生产单元布局
精益工厂布局
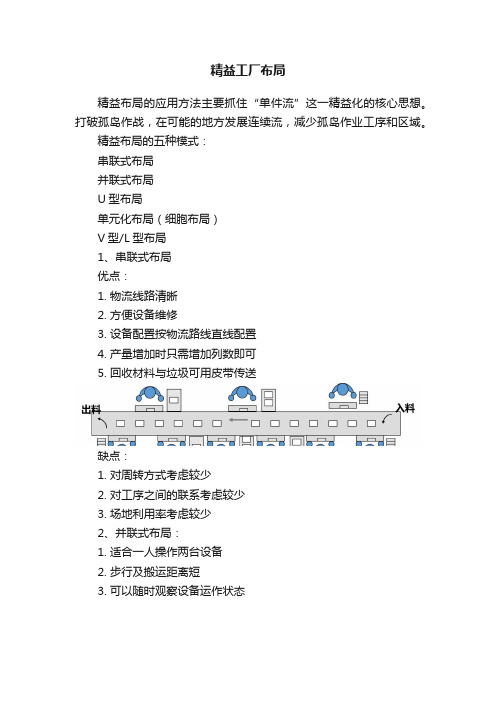
精益工厂布局精益布局的应用方法主要抓住“单件流”这一精益化的核心思想。
打破孤岛作战,在可能的地方发展连续流,减少孤岛作业工序和区域。
精益布局的五种模式:串联式布局并联式布局U型布局单元化布局(细胞布局)V型/L型布局1、串联式布局优点:1.物流线路清晰2.方便设备维修3.设备配置按物流路线直线配置4.产量增加时只需增加列数即可5.回收材料与垃圾可用皮带传送缺点:1.对周转方式考虑较少2.对工序之间的联系考虑较少3.场地利用率考虑较少2、并联式布局:1.适合一人操作两台设备2.步行及搬运距离短3.可以随时观察设备运作状态3、U型布局:优点:1.进料和出料口一致,异常信息可以及时传递2.一人操作3台以上的设备3.可以随时观察设备运作状况4.员工操作步行距离较近5.占用空间场地较小3、单元化布局:单元化生产布局,是精益生产的一个模块,是当代最新、最有效的生产线设置方式之一,为日本以及欧美企业所广泛采用。
这种方式使得小批多种生产残酷环境下的生产线几乎比流水线效果还好,因此被誉为“看不见的传送带”。
单元化生产方式单元化生产,是指将设备和厂房以特定的顺序安排,使材料和零件由1个或极少的作业者以最小的搬运完成部分或者全部生产过程。
•把4M进行合理的安排,进行更好的单件流生产;•只要有需要,可以进行单件流操作,1个员工也可以完成整个操作过程;•通常按产品族或者按工艺流程分组;•通常采用“U”型布局。
优点:•更有效的目视化管理;•生产过程头尾相接;•最小化走动的距离;•提高了工序间的平衡;•避免了孤岛操作。
•能够实行单人多工位操作;•加强了员工之间的交流;•更好的发现异常情况;•更容易实现高频率小批量物料补充需求;•适应节拍T/T的变化;•生产计划和人员配备的变化更容易实现。
布局的基本规则1.将设备与工位靠在一起;2.移走工作路径上的障碍物;3.单元里面的宽度大约为1.5m;4.排除可能产生WIP(标准在制品)的环节;5.流程的起点与终点靠得很近;6.在工作场所避免上上下下、前前后后往返传输;7.将一些基本的作业步骤安排在一起。
制造车间布局详解课件

设备设施布局
系统布置设计(Systematic Layout Planning )
P产品构成分析:
例:叉车产品分析
设备设施布局
系统布置设计(Systematic Layout Planning )
例:P—Q分析
设备设施布局
系统布置设计(Systematic Layout Planning )
在工业安全用色中,橙色表示危险,是警戒色。橙色非常明亮刺眼,如火车头,登山服装,背包,救生衣等。车间现场,橙色可用于安全警示标识,如安全帽、危险作业场所的工作服。
在工业安全用色中,黄色表示提醒注意。如交通号志上的黄灯,工程用的大型机器,学生用雨衣,雨鞋等,危险、保安设施。车间现场,黄色常被用作安全色,因为这极易被人发现,如室外作业的工作服,常用于警示标识,用于通道线、定置线。
图1 产品原则布置示意图
设备设施布局
(2)工艺布置原则(机群式)把同类型的设备和人员集中布置在一个地方。
图4 工艺原则布置示意图
设备设施布局
(3)固定式布置原则(项目布置)主要是工程项目和大型产品生产采用的一种布置形式。 它的加工对象位置,生产工人和设备都随加工产品所在的某一位置而转移。如工程建设、飞机厂、造船厂、重型机器厂等。
车间整体颜色选择
色彩的前后感
处在同一平面上的颜色,有的颜色使人感觉突出,有的颜色给人以退向后方的感觉。前者称前进色,后者称为后退色。由各种不同波长的色彩在人眼视网膜上的成像有前后,红、橙等光波长的色在内侧成像,感觉比较迫近;蓝、紫等光波短的色则在外侧成像,在同样距离内感觉就比较后退。实际上这是视错觉的一种现象,一般暖色、纯色、高明度色、强烈对比色、大面积色、集中色等有前进感觉,相反,冷色、浊色、低明度色、弱对比色、小面积色、分散色等有后退感觉。
工厂布置的四种基本形式

工厂布置是指在有限的工厂空间内,合理地安排生产设备、工作区域和物流路线,以提高生产效率、降低成本、提升工作环境和安全性。
工厂布置的四种基本形式包括:
1. 工艺布置(Process Layout):
工艺布置是按照生产工艺流程来安排工厂的布局。
这种布置方式强调的是生产流程的连续性和逻辑性,适合于流程式生产,如化工、炼油等工业。
其优点是生产流程清晰,易于管理和控制,但缺点是灵活性差,不易于适应产品种类的变化。
2. 产品布置(Product Layout):
产品布置是按照产品的生产顺序来安排工厂的布局。
这种布置方式强调的是产品的流动路径最短,适合于大量生产单一产品或类似产品,如汽车制造等。
其优点是生产效率高,运输距离短,但缺点是生产线一旦建立,不易于更改和适应新产品。
3. 混合布置(Mixed Layout):
混合布置是工艺布置和产品布置的结合,适用于生产多种产品的情况。
这种布置方式可以兼顾生产效率和灵活性,适合于中小型企业。
其优点是灵活性强,可以适应产品种类的变化,但缺点是管理复杂,需要更多的协调和规划。
4. 单元布置(Cellular Layout):
单元布置是将工厂划分为若干个独立的工作单元,每个单元负责完成产品的全部或大部分生产过程。
这种布置方式强调的是工作的灵活性和团队的协作,适合于多品种小批量生产,如电子组装等。
其优点是响应速度快,质量控制容易,但缺点是初始投资成本较高。
生产空间布置:生产空间布置设计,工厂空间、作业车间布置方案
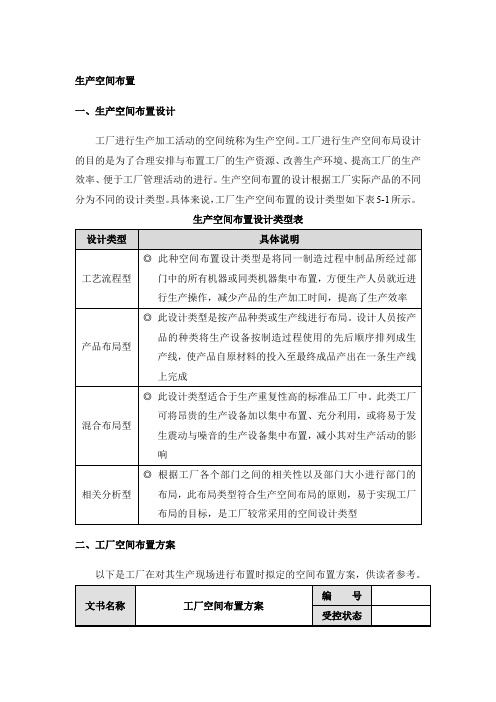
生产空间布置一、生产空间布置设计工厂进行生产加工活动的空间统称为生产空间。
工厂进行生产空间布局设计的目的是为了合理安排与布置工厂的生产资源、改善生产环境、提高工厂的生产效率、便于工厂管理活动的进行。
生产空间布置的设计根据工厂实际产品的不同分为不同的设计类型。
具体来说,工厂生产空间布置的设计类型如下表5-1所示。
生产空间布置设计类型表二、工厂空间布置方案以下是工厂在对其生产现场进行布置时拟定的空间布置方案,供读者参考。
工厂的车间及各种设施的相对位置,其步骤如下所述。
(1)根据原材料在制品在生产过程中的流向,初步布置各个生产车间和生产服务单位的相对位置,绘出初步物料图。
(2)统计车间之间的物料流量,制定物料运量表,如下表所示。
车间之间物料运量表单位:吨至 从0102030405总计01 6 5 2 3 16 02 6 1 7 03 4 5 2 11 04 7 1 8 05 3 3 合计1018116(3)按运量大小进行初始布置,将生产车间之间运输量大的安排在相邻位置,并考虑其他因素进行改进和调整。
最后的结果如下图所示,因为部门01和02、部门02和03、部门03和04之间的运量较大,所以应该相邻布置。
运量图2.活动关系图法是通过图解,判明组织各组成部分之间的关系,然后根据关系的密切程度加以布置,从而得出较优的总平面布置方案。
其绘制步骤如下。
01020304051吨运量2吨运量(1)绘制生产活动相关图。
下图是某工厂八个部门之间的生产活动关系图,表示各生产单位之间的联系程度。
生产活动相关图(2)从生产活动相关图可以方便地找到每一部门与其他七个部门单位的关系,图中每个菱形处于从两个部门发出的平行线的交汇区,在菱形对角线的上方填写两个部门的相关程度代号,对角线下方填写的数字表示两部门之间的相关的原因。
(3)图中最右边的菱形表示了材料库和办公室之间的相关关系,代号“I ”表示两者之间关系重要,数字“4”表示两部门间的人员联系密切,数字“5”表示两者之间的文件联系密切。
生产车间如何进行布局
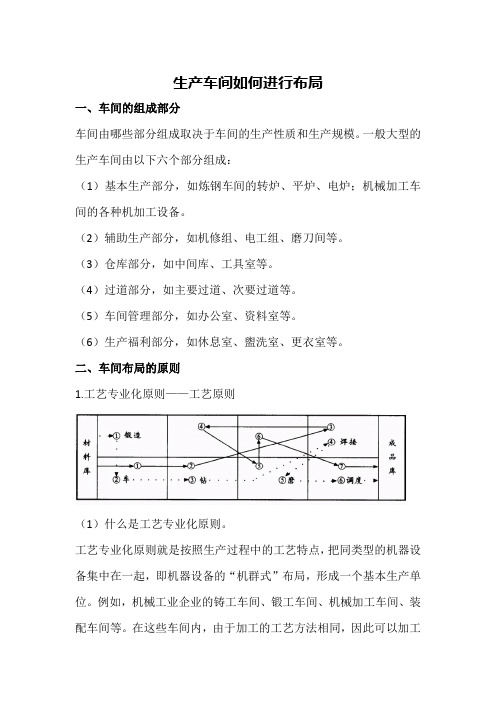
生产车间如何进行布局一、车间的组成部分车间由哪些部分组成取决于车间的生产性质和生产规模。
一般大型的生产车间由以下六个部分组成:(1)基本生产部分,如炼钢车间的转炉、平炉、电炉;机械加工车间的各种机加工设备。
(2)辅助生产部分,如机修组、电工组、磨刀间等。
(3)仓库部分,如中间库、工具室等。
(4)过道部分,如主要过道、次要过道等。
(5)车间管理部分,如办公室、资料室等。
(6)生产福利部分,如休息室、盥洗室、更衣室等。
二、车间布局的原则1.工艺专业化原则——工艺原则(1)什么是工艺专业化原则。
工艺专业化原则就是按照生产过程中的工艺特点,把同类型的机器设备集中在一起,即机器设备的“机群式”布局,形成一个基本生产单位。
例如,机械工业企业的铸工车间、锻工车间、机械加工车间、装配车间等。
在这些车间内,由于加工的工艺方法相同,因此可以加工多种多样的产品。
(2)工艺专业化原则的优点。
①车间对产品品种的适应性强。
②由于同种设备集中在一起,可以充分利用设备和生产面积,提高设备负荷系数。
③便于工艺管理。
④生产控制灵活性较强,便于生产任务连续进行。
(3)工艺专业化原则的缺点。
①当零件加工工序较多时,需要由不同的车间来完成,因而加工路线长,往返运输多,生产周期长。
②在制品数量增多,流动资金占用量增大。
③各车间之间的联系和协作关系复杂,影响各项管理工作的协调一致。
(4)适用范围。
按工艺专业化原则的车间工艺布局,多用于单件小批生产条件。
2.对象专业化原则——对象原则(1)什么是对象专业化原则。
对象专业化原则就是把加工对象的全部或大部分工艺过程集中在一个生产单位中,组成以产品或零件为对象的生产单位。
例如,机械工业企业的齿轮车间、标准件车间、发动机车间等。
(2)优点。
①机器设备按零件或产品的工艺流程布置,缩短了产品的加工路线,节约了运输费用,减少了仓库和生产面积。
②缩短了生产周期,减少了在制品数量和流动资金的占用量。
③减少了车间之间的联系,便于各项管理工作。
生产与运作管理四生产系统布局

生产与运作管理四生产系统布局生产与运作管理是一个有关于企业如何有效地组织和管理其生产和运作活动的领域。
生产系统布局是生产与运作管理中的一个重要方面,它涉及到如何安排和组织公司的生产设施和资源,以提高生产效率和降低成本。
下面将分别介绍传统生产系统布局、流水线生产系统布局、细胞生产系统布局和恶意生产系统布局。
传统生产系统布局是传统的生产布局方式,通常将不同的设备和工作站按照功能或者产品性质进行划分。
这种布局方式适用于生产种类繁多且工序独立的场景,例如传统的制造企业。
这种布局方式的优点是灵活性较高,容易适应生产需求的变化。
但是缺点是生产效率相对较低,因为产品在不同工作站之间需要频繁地转移,造成了生产的时间浪费和成本浪费。
流水线生产系统布局是一种将生产过程分成一系列有序的连续工位,将产品从一道工序推送到下一道工序的布局方式。
这种布局方式适用于生产需求稳定,产品工序相对简单的场景,例如汽车制造、手机组装等。
流水线生产系统布局的优点是生产效率高,能够实现快速高效的生产。
但是缺点是灵活性较低,不适合生产需求频繁变化的环境。
细胞生产系统布局是一种将生产设备和工作站组织成小型的细胞单元,在一个细胞单元内完成产品的加工和生产。
每个细胞单元是一个相对独立的实体,可以根据生产需求进行灵活组合和调整。
这种布局方式适用于生产小型批量定制的产品,例如家具制造、珠宝加工等。
细胞生产系统布局的优点是灵活性高,能够快速适应客户需求的变化。
但是缺点是相对复杂,需要较高的管理和协调能力。
恶意生产系统布局是一种将生产过程分成多个相互竞争的小组,每个小组都是一个完整的生产系统。
每个小组之间保持一定的独立性,通过竞争来提高生产效率和质量。
这种布局方式适用于生产需求高度个性化、追求创新和竞争的场景,例如时尚服装、高科技产品等。
恶意生产系统布局的优点是能够激发员工的创造力和竞争意识,促进产品质量和效率的提高。
但是缺点是管理难度较大,需要较高的协调和沟通能力。
生产与运作管理生产系统选址与布局
2021/8/25
1
• 生产什么,生产多少,在哪儿生产和以什么方式生 产,这些是生产运营系统设计的四个根本问题,是 需要公司高层慎重决策的长期生产方案问题。
• 为什么美国麦当劳公司吧它在中国的第一家快餐连 锁店开在北京王府井的街口?
• 为什么大型百货商场的一层大多是首饰和化装品柜 台?
代号
密切程度
A
绝对重要
E
特别重要
I
重要
O
一般
U
不重要
X
不予考虑
表1 关系密切程度分类表
2021/8/25
代号
1 2 3 4 5 6 7 8 9
关系密切原因
使用共同的原始记录 共用人员 共用场地
人员接触频繁 文件交换频繁 工作流程连续 做类似的工作
共用设备 其他
表2 关系密切原因表
26
1.材料库 2.成品库 3.工具库 4.生产车间 5.机修车间 6.半成品库 7.食堂 8.办公室
某企业有n个可供选择的厂址,需供给m个目标市场
设 Xi: i工厂的产量 (i=1‥‥‥ n)
Rj: j目标市场需求量 (j=1 ‥‥‥ m)
Xij: i工厂运往j目标市场的产品数量
Ci: i工厂的单位产品本钱
Dij: i工厂向j目标市场运输单位产品的费用
目标函数:
nm
CiXi
DijXij min
1、作业相关图 2、从——至〔from-to)表法 作业相关图法由穆德提出,它是根据企业各个
部门之间的活动关系密切程度布置其相互位 置。 首先将密切程度划分为A、E、I、O、U、X六个 等级,然后列出导致不同程度关系的原因。 使用这两种资料,将待布置的部门一一确定 出相互关系,根据相互关系重要程度,按重 2021要/8/25等级高的部门相邻布置的原那么,安排出25
单元生产方式
单元生产方式摘要:伴随着科学技术的发展,当今的企业面对的市场环境也是瞬息万变。
企业的生产运作需要更高的柔性来面对市场随时变化的需求环境,所以越来越多的企业采用了多品种小批量的生产方式。
本文就单元布局产生的背景;单元布局的优缺点;单元布局所采用的成组技术,特别是基于工艺流程的顺序聚类方法进行介绍。
关键字:单元布局;生产方式;成组技术;排序聚类法目录1.生产方式的演变 (2)1.1.基于工艺原则的单件生产 (2)1.2.基于标准化流水线的大量生产 (2)1.3.基于单元布局的多品种小批量生产方式 (2)2.单元生产方式介绍 (3)2.1.单元生产的几种常见形式 (3)2.1.1.屋台式 (3)2.1.2.逐兔式 (3)2.1.3.分割式 (3)2.2.单元生产的优缺点 (4)3.实现单元生产的成组技术 (4)3.1.基于生产流程分析的排序聚类法 (4)3.2.生产流程分析的排序聚类法实例 (5)4.结论 (7)生产方式主要经历了三个发展阶段:单件手工作业,大批量生产,柔性化、系统化和智能化的生产方式。
制造业被大批量生产方式主导了将近百年,其间世界各国工业化进程得到了极大发展,进而促进市场经济的形成。
随着科学技术的飞速发展、市场的高速变化和产品需求的多样化,市场对产品的需求已经从传统的刚性需求向高度定制化的柔性需求转化,这使得大批量生产方式的规模经济优势遭遇了前所未有的挑战。
1.生产方式的演变[1]1.1.基于工艺原则的单件生产单件生产方式是按照用户的要求进行生产,采用手动操作的通用机床。
由于无标准的计量系统,所以生产出来的产品规格只能达到近似要求,可靠性和一致性不能得到保证。
生产效率不高,产量很低,例如当时的汽车产量每年不超过1000辆,而且生产成本很高,也不随产品产量的增加而下降。
从业者通晓和掌握产品设计、机械加工和装配等方面的知识和操作技能,大多数人从学徒开始,最后成为制作整台机器的技师或作坊业主。
生产线布局(超详细)_图文
工艺原则布局
权重代码 密切程度
A
绝对必要
E
特别重要
I
重要
O
普通的
U
不重要的
X
不予考虑的
2020/8/6
线代号
29
工艺原则布局
▪ 医院相关图
1
3
5
2
4
6
2020/8/6
30
工艺原则布局
▪ 医院总体合理布局图
1
4
65
2
3
2020/8/6
31
工艺原则布局
▪ 布局方法 设部门或工艺有n个
布局方案=n!
▪ 使用范围:
• 批量小 • 体积大
▪ 布局特点
• 以产品为中心 • 不考虑物流成本和复杂程度
2020/8/6
18
工艺原则布局
▪ 定义:
• 将相似的设备或功能集中放在一起的布局方式 • 也称车间布局,如车床车间
▪ 使用范围
• 生产设备密集型 • 设备专业性 • 自动化程度高 • 资本密集型 • 产品重量轻
2020/8/6
次数
1 1 2 3 4 5 6 7 8
23 175 50
0
45 0 30 100 75 17 88
20
678 200 20 25 90 80 90 125 99 180 5 0 25 0 180 187
347 103 7
21
▪ 玩具厂各车间年物流成本示意图
2020/8/6
22
工艺原则布局
1. 采用了看板管理,拉动生产方式 2. 车间布局U型布局; 3. 不同类型的机器摆放在一块; 4. 实现了单件流的生产; 5. 机器小型化 ; 6. 工序中间很少甚至没有库存; 7. 实现了作业标准化; 8. 对工人实行了多技能培训; 9. 具有完善的作业改善活动制度
7种精益生产线布局
车间流水线布局的原则,可以概括为“两个遵守、两个回避”。
两个遵守:逆时针排布、出入口一致两个回避:孤岛型布局、鸟笼型布局1.流畅原则:各工序的有机结合,相关联工序集中放置原则,流水化布局原则。
2.最短距离原则:尽量减少搬运,流程不可以交叉,直线运行.3.平衡原则:工站之间资源配置,速率配置尽量平衡。
4.固定循环原则:尽量减少诸如搬运、传递这种Non—Value Added的活动。
5.经济产量原则:适应最小批量生产的情形,尽可能利用空间,减少地面放置原则.6.柔韧性的原则:对未来变化具有充分应变力,方案有弹性。
如果是小批量多种类的产品,优先考虑“U”型线布局、环形布局等。
7.放错的原则:生产布局要尽可能充分的考虑这项原则,第一步先从硬件布局上预防错误,减少生产上的损失。
1.逆时针排布主要目的是希望员工能够采用一人完结作业方式,能够实现一人多机。
一人完结与一人多机要求一个员工从头做到尾,因此员工是动态的,称之为“巡回作业”。
2.出入口一致是指原材料入口和成品出口在一起。
为什么要求出入口一致呢?首先,有利于减少空手浪费.假设出入口不一致,作业员要采用巡回作业,那么当一件产品生产完了,要去重新取一件原材料加工的话,作业员就会空手(手上没有材料可以生产)从成品产出口走到原材料投入口,这段时间是浪费.如果出入口一致的话,作业员立刻就可以去到新的原材料进行加工,从而避免了空手浪费。
第二,有利于生产线平衡。
由于出入口一致,布局必然呈现类似“U”的形状,这使得各工序非常接近,从而为一个人同事操作多道工序提供了可能,这就提高了工序分配的灵活性,从而取得更高的生产线平衡率。
3.避免孤岛型布局孤岛型布局把生产线分割成一个个单独的工作单元,其缺陷在于单元与单元之间互相隔离,无法互相协助.4.避免鸟笼型布局鸟笼型布局往往没有·考虑到物流、人流顺畅的结果,这种布局错误的用机器设备或者工作台把作业员围在中间,使得物流不顺畅,在制品增加,单元与单元之间的相互支援也变得几乎不可能。
- 1、下载文档前请自行甄别文档内容的完整性,平台不提供额外的编辑、内容补充、找答案等附加服务。
- 2、"仅部分预览"的文档,不可在线预览部分如存在完整性等问题,可反馈申请退款(可完整预览的文档不适用该条件!)。
- 3、如文档侵犯您的权益,请联系客服反馈,我们会尽快为您处理(人工客服工作时间:9:00-18:30)。
工艺专业化布局和产品专业化布局
生产设备的布置通常有两种形式,工艺专业化和产品专业化。
1. 工艺专业化布置形式
机群式布置,这个概念与厂区布置的工艺专业化是相同的,只是工艺的概念更小一些,指把同种类型的设备和人员集中布置在一个地方。
这种布置方式常常用于用同样的设备来制造和装配各种不同的部件。
比较是用于品种多产量小的生产类型。
其特点是:同类设备集中,加工技术单一,生产系统柔性大;加工对象多,工艺路线差别大,物料搬运有交叉,难以使工件搬动自动化;在各工序之间成批搬运,加工周期长;周转环节多,不易管理。
车间
门
工艺专业化布置车间
2. 产品专业化布置形式
流水线布置,按产品的加工过程顺序配置设施,布置成一条专门的加工生产线。
这种形式适合于品种少产量达的生产类型。
其特点是:生产效率高;生产流程连续性好,可缩短生产周期;降低搬运费用;计划管理简单,生产易控制;但加工线应变能力差,缺乏柔性。
输入
输出
产品专业化布置
除上述两种布置形式外还有混合布置,固定布置,存储布置,销售布置等。
需要注意的是在生产车间内部的布置也应该遵循工艺性、经济性和安全性原则,具体有以下要求:
1.尽可能保持生产过程的连续性;
2.工件加工中的运送路线要短;
3.车间内要留出足够的通到面积,通道要直;
4.充分保证生产用面积,提高利用率;
5.设备布置要保证安全。
传统生产线的弊端
直线型生产线的生产方式下,人员在一个周期内的来回时间及行走距离较多,如图2 所示。
某个单元生产周期不能够得到合理限制造成整个系统的周期过长,产品成本增加,如局部环节出现问题会影响整个生产线的连续性,形成在制品堆积的严重现象。
面向产品族的“制造单元”
制造单元是以柔性设备为核心的若干台设备的组合,将这些设备按照每一个产品“族”相类同的工艺顺序排列,在制造单元内完成制造这些产品/零件族的全部过程。
制造单元不是针对每一个零件的,这样就不是精益制造了。
制造单元起码有以下几个特征和功能:
a)面向一个“产品/零件族”。
“族”是一组形状和制造过程相同或相似的
零件。
因而精益的制造单元是柔性的,大大地减少了由于换型造成
的生产停滞。
b)制造单元内的设备顺序是按工艺流程排列的,考虑到零件进出单元
方向的一致性,经常排列成U形,所以又称其为U形单元,从而
保证了物流>物流的流程距离最短,而消除了多种形式的浪费。
工件在制造单元中按流程顺序自然流转,从而简化了管理,节省了
信息的传递和信息流距离。
c)制造单元内的工人是多能的,单元团队的成员之间是相互支持和相
互替代的,使更加发挥工人和团队的积极性,
所以建立制造单元是实行精益生产的关键步骤之一。
单元生产模式是一种基于追求无浪费理念,以工作单元(机械设备、生产人员和在制品的物流系统)为基本组成,对生产线合理布置,进行单一或多品种的生产方式。
单元式生产可根据人员配备情况将生产线分为单人、多人循环类型,即U 型布置。
单元生产方式的基本目的就是消除浪费,该生产模式主要消除七大浪费中的搬运浪费、等待浪费、生产线平衡浪费。
同时可有效的降低生产成本,提高质量及工作效率,增强系的柔性能力通常单元式生产线采用U 型或C 型生产线的模式,在这种生产线模式中设备和工作地点按照流程步骤的顺序紧密配置,这样能够减少不必要的人员走动和物料的搬运时间,使得生产线的运行更加顺畅,U 型生产线的最大特征就是实现生产线的平衡,该生产线为了减少工作人员由于生产线布局不当所造成的行走时间浪费现象,把生产的投入点,即原材料的放置点与半成品或成品的产出点的位置,尽可能的缩短其二者间距离,叫做“IO 一致”原则
构建制造单元需要有以下技术的支持:
利用成组技术(Group Technology)的相似性原则,将产品和零件分成为若干“族”。
在这个过程中,采用成组技术分类编码是必要的。
但是很多企业径直采用目测和经验的方法分类,也取得可行的效果。
利用工艺流程分析和聚类分析等方法形成与零件族工艺设备相对应的设备组。
这个过程可以凭经验完成,最好用专业的应用软件实现。
绘制产品族的价值流图(value stream mapping)。
价值流图是借鉴日本的经验在美国广泛应用的一种识别浪费的方法。
利用价值流图分析现行过程存在的过程停滞和浪费,计算不增值过程所占用的过程时间。
按照分析结果重新设计业务流程。
在车间现场按经过优化的族的工艺流程布置设备组,形成U形或直线的生产单元。
不断的进行工艺路线的改进和优化,不断的进行制造单元设备类型和位置的调整。
将工程技术人员的办公桌安放在各个制造单元的中央,加快对现场问题的反应速度
为了方便的构建和调整制造单元,布置精益制造单元的厂房采用整体地基,准备在任何地方安置设备,而设备也放在简易的可移动拖架上,多数并不与地面固定。
在美国和中国的许多实践打消了关于设备精度、安全和寿命的所有疑虑。
水、电、气的管道从设备上空下来。
设备的位置排列:
1. 单行排列:例:某金加工车间,加工ABCD四种零件,所需设备(工作地)单行排为:料库—铣床—钻床—刨床—车床—检验,各零件加工工艺路线如下:
A: 料—刨—铣—检
B: 料—车—铣—刨—检
C: 料—铣—车—刨—钻—检
D: 料—车—铣—车—铣—钻—检
2. 设备的多行排列:
柔性化的设备
,实现精益制造的设备是便于更换或调整的柔性化设备。
在柔性设备上,更换产品只需要很少的时间,以至于可以大大地降低所谓“经济规模”的阈值。
各种数控设备,特别是数控加工中心和柔性制造系统FMS是拉式生产系统首选的柔性设备。
注意首推数控设备并不是由于它们是“自动化”的,而是看中了它们“柔性化”的特征。
用普通的通用设备加日本式的快速换装的模具系统、或在前苏联推广过的成组夹具或组合夹具,也是效果很好的柔性化设备方案。
相反,刚性自动化设备最能体现大量生产方式的优势,但用他们进行精益的小批量甚至单件流生产、而又企图获得高效率和低成本是不可能的。
因而,在向精益企业转变过程中,体积庞大而不易搬动、需要按批量作业的“超大设备”成为新的浪费而失去它的生命力。
在国内外成功进行精益企业改造过程中,并没有一开始就进行大规模设备更新的案例。
但是必须不断地进行制造技术的改进,用新的柔性自动化的设备替代普通的通用设备,逐渐形成出面向“大规模定制生产”的敏捷制造环境。