表面缺陷无损检测方法的比较
介绍几种常见的无损检测技术及其优缺点

介绍几种常见的无损检测技术及其优缺点无损检测技术是一种在不破坏被检物理性能的情况下,对物体的内部或表面进行检测、评价和控制质量的方法。
它被广泛应用于工程、制造业、航空航天、能源、交通运输等各个领域。
本文将介绍几种常见的无损检测技术及其优缺点。
首先,超声波检测是一种常见的无损检测技术。
这种技术通过将超声波的脉冲传递到被检测物体中,然后测量超声波反射或传播速度的变化来检测物体的内部缺陷。
超声波检测具有检测深度大、分辨率高、对不同材料具有良好适应性等优点。
然而,它也存在着检测速度慢、对被检材料有一定要求等缺点。
其次,射线检测是另一种常见的无损检测技术。
射线检测主要利用X射线或γ射线穿透被检材料,通过感光材料或电子束探测器来测量射线的衰减情况,以检测物体的缺陷。
射线检测具有检测速度快、可以检测多种材料、对内部缺陷有较高的分辨率等优点。
但是,由于射线具有辐射危害,对操作人员保护要求较高。
电磁检测是第三种常见的无损检测技术。
电磁检测基于电磁感应原理,通过改变磁场来检测被测物体的内部缺陷。
这种技术具有非接触性、检测速度快、对复杂几何形状具有良好适应性的优点。
然而,电磁检测也存在着对导电材料的限制、对操作环境的电磁干扰敏感等缺点。
另外,磁粉检测是一种常用的无损检测技术。
这种技术通过在被检测物体表面涂覆磁粉或将磁粉溶解在液体中,在外部施加磁场的作用下,通过观察或测量磁粉在缺陷区域的积聚情况来检测缺陷。
磁粉检测具有对各种材料适用、操作简便、成本低等优点。
然而,它只能检测表面缺陷,对缺陷深度的评估能力较弱。
最后,涡流检测是一种常用的无损检测技术。
涡流检测基于涡流感应原理,通过感应导体中的涡流来检测被检测物体的缺陷。
这种技术具有对导电和磁性材料适用、对小缺陷具有高灵敏度、无需接触被检材料等优点。
然而,涡流检测也受到导体材料和几何形状的限制,对操作人员的技术要求较高。
总而言之,无损检测技术在各个领域中发挥着重要的作用。
超声波检测、射线检测、电磁检测、磁粉检测和涡流检测是常见的无损检测技术,每种技术都有其独特的优点和缺点。
金属材料缺陷检测与无损评估方法研究

金属材料缺陷检测与无损评估方法研究近年来,金属材料作为工业生产中不可或缺的材料,在各个领域广泛应用。
然而,金属材料在使用过程中可能会出现各种缺陷,如裂纹、腐蚀、疲劳等,这些缺陷会对金属材料的性能和寿命产生严重影响,甚至会引发事故。
因此,对金属材料的缺陷进行准确的检测和无损评估就显得尤为重要。
一、金属材料缺陷检测方法1. 目测检测方法:目测检测方法是最简单、直观的检测方法之一,适用于一些表面缺陷的检测。
通过肉眼观察金属材料的外观,如表面颜色、形状等,来判断是否存在缺陷。
这种方法操作简单、成本低,但只适用于检测一些比较明显的缺陷。
2. 超声波检测方法:超声波检测是一种常用的无损检测方法,能够全面、有效地检测金属材料内部的缺陷。
在超声波检测中,通过超声波发射和接收器件,对金属材料进行扫描,根据超声波在材料内部的传播速度和反射强度来判断是否存在缺陷。
这种方法具有高灵敏度、高准确性的特点,可以检测到微小的缺陷。
3. 磁粉检测方法:磁粉检测是一种常用的金属材料缺陷检测方法,适用于检测表面和近表层存在的裂纹、焊接缺陷等。
在磁粉检测中,通过在金属材料表面施加磁场,再撒上带有磁粉的粉末,通过观察磁粉在缺陷处的分布情况,来判断是否存在缺陷。
这种方法操作简单、成本较低,但只适用于表面和近表层的缺陷检测。
二、金属材料缺陷无损评估方法1. 声发射检测方法:声发射检测是一种通过检测材料在受力后产生的声波信号来评估缺陷的方法。
在金属材料受力或变形时,缺陷会引起局部应力集中,从而产生声波信号。
通过对这些声波信号的分析,可以评估材料的缺陷性质、位置和严重程度。
与其他方法相比,声发射检测具有非接触、实时、高灵敏度等优点。
2. 磁记忆检测方法:磁记忆检测是一种通过检测材料的磁矩分布变化来评估缺陷的方法。
在金属材料中存在缺陷时,缺陷会引起磁矩分布的变化,通过在材料表面布置磁传感器,可以监测磁场的变化,从而评估缺陷的位置和严重程度。
这种方法具有快速、高效、无损伤的特点,适用于对金属材料进行在线无损评估。
无损探伤方案

无损探伤方案无损探伤是一种非破坏性检测方法,通过使用物理学的原理和科学的仪器设备来检测物体的内部或表面缺陷、杂质、裂纹等。
它广泛应用于航空、航天、核能、军工、建筑、交通等领域。
本文将介绍无损探伤方案的几种常见方法。
一、磁粉探伤法磁粉探伤法是一种适用于铁、钢等金属表面、近表面缺陷的无损探伤方法。
其原理是在被检测物体表面均匀涂有铁磁性粉末,利用外加磁场引导粉末在裂纹、缺陷处留下磁纹,从而发现该处的缺陷。
磁粉探伤法灵敏度高、速度快、成本低,但只适用于铁、钢等铁磁性材料。
二、涡流探伤法涡流探伤法是一种适用于金属、导体等导电材料表面或近表面缺陷的无损探伤方法。
其原理是将交流电源通入探测器,电流在待检测金属或导体中产生涡流,从而形成磁场,利用磁场对探测器产生的信号进行检测,可以发现缺陷。
涡流探伤法灵敏度高、速度快、适用于各种导电材料。
三、超声波探伤法超声波探伤法是一种适用于大多数材料内部缺陷的无损探伤方法。
其原理是利用超声波在材料内部的传播和反射来检测材料内部缺陷。
可以通过探头的不同位置、不同方向进行检测,对材料内部的缺陷、尺寸、定位等都可以进行准确的检测。
超声波探伤法灵敏度高、适用范围广,但在检测厚度较大、表面不平整、材料吸音性较强时可能存在一定的局限性。
四、射线探伤法射线探伤法是一种适用于金属、非金属等大多数材料内部缺陷的无损探伤方法。
其原理是利用电磁波的作用直接透射材料,得到材料内部组织、缺陷等信息来实现无损检测。
射线探伤法灵敏度高、适用范围广,但需要射线源,且辐射可能对人体和环境造成危害,需要进行详细的安全措施。
五、热波探伤法热波探伤法是一种利用材料吸收热能散热规律来检测缺陷的无损探伤方法。
其原理是利用探测器对材料表面施加热源,通过测量热能的传播和分布情况来检测材料内部的缺陷。
热波探伤法适用范围广,可以检测小到几毫米的缺陷,但需要加热、冷却,操作比较繁琐。
综上所述,无损探伤方案是通过选择不同的探测方法和仪器设备,根据被检材料的不同特性来进行无损检测。
磁粉检测技术:磁粉检测与其它无损检测方法比较
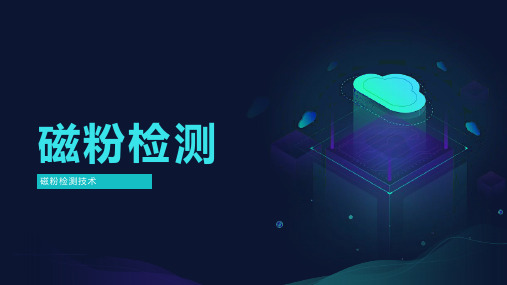
渗透检测(PT) 毛细渗透作用 表面开口缺陷
渗透液渗出形成缺陷显示 渗透液和显像剂 非松孔性材料
任何非多孔材料制成的零部件 及组合件,以及使用过的上述
零部件
裂纹、疏松、针孔
直观 较慢 探伤 较重
高
涡流检测(ET) 电磁感应作用 表面及近表面缺陷 检测线圈电压和相位发生变化 记录仪、电压表和示波器
磁粉检测
磁粉检测技术
磁粉检测与 其它无损检测
方法比较
一、几种无损检测方法的比较
方法原理 能检出的缺陷 缺陷表现形式
显示材料 适用材质
主要检验对象
主要检测缺陷 缺陷显示 检测速度 应用 污染 灵敏度
磁粉检测(MT) 缺陷漏磁场吸附磁粉
表面及近表面缺陷
磁粉附着在缺陷附件形成磁痕 磁粉
铁磁性材料
锻钢件、铸钢件、压延件、焊缝、管材、 棒材、机加工件以及使用中的钢材
导电材料
管材、线材、棒材等及零件可检 查缺陷,材料分选及厚度测量等
裂纹、材质变化、厚度变化
不直观 最快
探伤、材质分选、测厚 最轻 较低
二、与漏磁检测的主要区别:
漏磁场检测方法主要包括磁粉检测和检测元件检测。磁粉检测是利用磁粉 作为传感器,形成磁痕显示缺陷,而漏磁检测利用磁带、霍尔元件、磁敏 二极管或感应线圈作为磁场的传感器检测缺陷。
10-10
10-8
10-6 10-4
10-2
1
探头旋转式
钢管
照片来源:华中科技大学机电工程公司
管旋转检测方式
纵向检测系统 横向检测系统
漏磁检测的眼睛
探靴
磁化方式
• 1.交流磁化方式 • 2.直流磁化方式 • 3.永磁磁化方式 • 4.复合磁化方式 • 5.综合磁化法
表7.6五种常用无损检测方法的对照表

表7.6五种常用无损检测方法的对照表
在压力容器制造过程中,各种无损检测方法的选择,首先要满足国家的有关规程,标准的要求.也必须按照有关技术文件,如:图纸和技术协议的要求,满足其探伤的比例.合格等级检测时的检测时机等.
无损检测责任工程师在制造和检修工作中,除完成上述必要的检测项目外,有时必须根据工作需要增加检测方法和手段来进一步对缺陷进行判断.我们除应掌握常规无损检测方法各自的特点及其适应性,而且也必须了解其他检测方法和手段特点帮助我们来提高检测结果的可靠性.
无损检测所利用的基本原理都可以归纳为材料内部组织的不连续性和几何形状发生变化,会引起各种物理量的变化.反过来根据物理量的变化大小来推断试件内部组织的不连续性和几何形状的变化.然而,物理量的变化的原因很复杂,往往与试件内部的变化无法一一应对.所以我们必须综合考虑几种物理量的变化.才能对试件内部的异常作出正确的判断.我们有时应根据几种无损检测方法检测的结果进行综合分析判断,最终来确定缺陷,并对缺陷进行定性.
定量.定位分析.。
磁粉探伤

磁粉探伤磁粉探伤又称磁力探伤(MT、MPT,Magnetic Particle Testing),是一种通过磁粉在缺陷附近漏磁场中的堆积以检测铁磁性材料表面或近表面处缺陷的一种无损检测方法。
磁力探伤中对缺陷的显示方法有多种,有用磁粉显示的,也有不用磁粉显示的。
用磁粉显示的称为磁粉探伤,因它显示直观、操作简单、人们乐于使用,故它是最常用的方法之一。
不用磁粉显示的,习惯上称为漏磁探伤,它常借助于感应线圈、磁敏管、霍尔元件等来反映缺陷,它比磁粉探伤更卫生,但不如前者直观。
由于目前磁力探伤主要用磁粉来显示缺陷,因此,人们有时把磁粉探伤直接称为磁力探伤,其设备称为磁力探伤设备。
铁磁性材料被磁化后,其内部会产生很强的磁感应强度,磁力线密度增大到几百倍到几千倍,如果材料中存在不连续性,磁力线会发生畸变,部分磁力线有可能逸出材料表面,从空间穿过,形成漏磁场,漏磁场的局部磁极能够吸引铁磁物质。
如果在工件上撒上磁粉,漏磁场会吸附磁粉,形成与缺陷形状相近的磁粉堆积(磁痕),从而显示缺陷。
指示图案比实际缺陷要大数十倍,因此很容易便能找出缺陷。
磁粉探伤方法应用比较广泛,主要用以探测磁性材料表面或近表面的缺陷。
多用于检测焊缝,铸件或锻件,如阀门,泵,压缩机部件,法兰,喷嘴及类似设备等。
探测更深一层内表面的缺陷,则需应用射线检测或超声波检测。
在工业中,磁粉探伤可用来作最后的成品检验,以保证工件在经过各道加工工序(如焊接、金属热处理、磨削)后,在表面上不产生有害的缺陷。
它也能用于半成品和原材料如棒材、钢坯、锻件、铸件等的检验,以发现原来就存在的表面缺陷。
铁道、航空等运输部门、冶炼、化工、动力和各种机械制造厂等,在设备定期检修时对重要的钢制零部件也常采用磁粉探伤,以发现使用中所产生的疲劳裂纹等缺陷,防止设备在继续使用中发生灾害性事故。
磁粉探伤的工作原理磁粉探伤机是利用自然界中磁力线总能保持其连续性的原理。
当铁磁性工件放在使其饱和的磁场中时,磁力线便会被引导通过工件。
渗透检测1
二.渗透检测的发展简史
目前,尚未确切地查明渗透检测起源于何时。 目前,尚未确切地查明渗透检测起源于何时。 19世纪未期 , 铁道车轴、 车轮、 车钩的“ 19 世纪未期, 铁道车轴 、 车轮 、 车钩的 “ 油 世纪未期 白法”检查,公认为是渗透检测方法最早的应用。 白法”检查,公认为是渗透检测方法最早的应用。 这种方法是将重滑油稀释在煤油中, 这种方法是将重滑油稀释在煤油中,得到一种混和 体作为渗透剂; 把工件浸人渗透剂中, 一定时间后, 体作为渗透剂 ; 把工件浸人渗透剂中 , 一定时间后 , 用浸有煤油的布把工件表面擦净, 用浸有煤油的布把工件表面擦净,再涂上一种白粉 加酒精的悬浮液,待酒精自然挥发后, 加酒精的悬浮液,待酒精自然挥发后,如果工件表 面有开口缺陷。 面有开口缺陷。则在工件表面均匀的白色背景上出 现显示缺陷的深黑色痕迹。 现显示缺陷的深黑色痕迹。
渗透检测的基础知识 §1.2 渗透检测的基础知识
一.渗透检测的基本原理
渗透检测是基于液体的毛细作用(或毛细现象) 渗透检测是基于液体的毛细作用 ( 或毛细现象 ) 和固体 染料在一定条件下的发光现象。 染料在一定条件下的发光现象。 渗透检测的工作原理是 渗透检测的工作原理 是 : 工件表面被施涂含有荧光染 料或着色染料的渗透剂后,在毛细作用下,经过一定时间, 料或着色染料的渗透剂后,在毛细作用下,经过一定时间, 渗透剂可以渗入表面开口缺陷中; 渗透剂可以渗入表面开口缺陷中;去除工件表面多余的渗 透剂,经干燥后,再在工件表面施涂吸附介质—显像剂 显像剂; 透剂 , 经干燥后 , 再在工件表面施涂吸附介质 显像剂; 同样在毛细作用下,显像剂将吸引缺陷中的渗透剂, 同样在毛细作用下,显像剂将吸引缺陷中的渗透剂,即渗 透剂回渗到显像剂中;在一定的光源下(黑光或白光) 透剂回渗到显像剂中; 在一定的光源下 ( 黑光或白光) , 缺 陷处的渗透剂痕迹被显示(黄绿色荧光或鲜艳红色) 陷处的渗透剂痕迹被显示(黄绿色荧光或鲜艳红色),从而 探测出缺陷的形貌及分布状态。 探测出缺陷的形貌及分布状态。
无损检测知识
磁粉检测的原理磁粉探伤的原理是指有表面或近表面缺陷的工件被磁化后,当缺陷方向与磁场方向成一定角度时,由于缺陷处的磁导率的变化,磁力线逸出工件表面,产生漏磁场,吸附磁粉形成磁痕。
谈谈我对磁粉检测原理的认识:当铁磁性工件被磁化时,磁感应线(B线)从中透过,如果工件表面存在缺陷,就会有一部分磁感应线逸出工件表面,他们从缺陷的一侧穿出进入空气中,绕过缺陷,从缺陷另一侧又折回到工件中,于是在工件表面缺陷处就形成了漏磁场。
此时将磁粉(能在微弱磁场中被吸附的氧化铁粉末)施加于改漏磁场中。
每一颗细小的磁粉在漏磁场中被磁化而成为极小的磁极,并在漏磁场的作用下磁粉被吸向漏磁场最强区(即缺陷表面中心处)。
于是磁粉就在缺陷处堆积起来形成与缺陷形状类似的磁痕。
这样缺陷就被显示出来。
磁粉检测的适用范围磁粉检测的适用范围是什么?我厂生产的磁粉探伤机适合什么样的工件使用?不适合什么样的工件使用?我根据我厂多年来对客户提供需探伤的工件的资料进行了整理并结合自己多年来对磁粉探伤机的认识总结了以下几点。
1)磁粉检测适用于检测铁磁性材料工件表面和近表面尺寸很小,间隙狭窄(如可检测出长0.1mm、宽为微米级)的裂纹和目视难以看出的缺陷。
2)适用于检测马氏体不锈钢和沉淀硬化不锈钢材料,但不适用于检测奥氏体不锈钢材料(如1Cr18Ni9)和用奥氏体不锈钢焊条焊接的焊缝,也不适用于检测铜、铝、镁、钛合金等非磁性材料。
3)适用于检测钢管、棒材、板材、型材和锻钢件、铸钢件及焊接件。
4)适用于检测为加工的原材料(如钢坯)和加工的半成品、成品件及在役与使用过的工件。
5)适用于检测工件表面和近表面的裂纹、白点、发纹、折叠、疏松、冷隔、气孔和夹杂等缺陷,但不适用于检测工件表面浅而宽的划伤、针孔状缺陷、埋藏较深的内部缺陷和延伸方向与磁力线方向夹角小鱼20°的缺陷。
超声波检测中,产生和接收超声波的方法,通常是利用某些晶体的(c)a.电磁效应 b.磁致伸缩效应 c.压电效应 d.磁敏效应2.目前工业超声波检测应用的波型是(f)a.爬行纵波 b.瑞利波 c.压缩波 d.剪切波 e.兰姆波 f.以上都是3.工件内部裂纹属于面积型缺陷,最适宜的检测方法应该是(a)a.超声波检测 b.渗透检测 c.目视检测 d.磁粉检测 e.涡流检测 f.射线检测4.被检件中缺陷的取向与超声波的入射方向(a)时,可获得最大超声波反射:a.垂直 b.平行 c.倾斜45°d.都可以5.工业射线照相检测中常用的射线有(f):a.X射线 b.α射线 c.中子射线 d.γ射线 e.β射线 f.a和d6.射线检测法适用于检验的缺陷是(e)a.锻钢件中的折叠 b.铸件金属中的气孔 c.金属板材中的分层 d.金属焊缝中的夹渣 e.b和d7.10居里钴60γ射线源衰减到1.25居里,需要的时间约为(c):a.5年 b.1年 c.16年 d.21年8.X射线照相检测工艺参数主要是(e):a.焦距 b.管电压 c.管电流 d.曝光时间 e.以上都是9.X射线照相的主要目的是(c):a.检验晶粒度;b.检验表面质量;c.检验内部质量;d.以上全是10.工件中缺陷的取向与X射线入射方向(b)时,在底片上能获得最清晰的缺陷影像:a.垂直 b.平行 c.倾斜45°d.都可以11.渗透检测法适用于检验的缺陷是(a):a.表面开口缺陷 b.近表面缺陷 c.内部缺陷 d.以上都对12.渗透检测法可以发现下述哪种缺陷?(c)a.锻件中的残余缩孔 b.钢板中的分层 c.齿轮的磨削裂纹 d.锻钢件中的夹杂物13.着色渗透探伤能发现的缺陷是(a):a.表面开口缺陷 b.近表面缺陷 c.内部未焊透14.下面哪一条不是液体渗透试验方法的优点?(a)a.这种方法可以发现各种缺陷 b.这种方法原理简单,容易理解c.这种方法应用比较简单 d.用这种方法检验的零件尺寸和形状几乎没有限制15.下面哪一条不是渗透探伤的特点?(a)a.这种方法能精确地测量裂纹或不连续性的深度 b.这种方法能在现场检验大型零件c.这种方法能发现浅磁粉检测具有下列优点:1)能直观的显示出缺陷的位置、大小、形状和严重成都,并可大致确定缺陷的性质。
四种无损检测方法对比
四种无损检测方法对比无损检测就是利用声、光、磁和电等特性,在不损害或不影响被检对象使用性能的前提下,检测被检对象中是否存在缺陷或不均匀性,给出缺陷的大小、位置、性质和数量等信息,进而判定被检对象所处技术状态(如合格与否、剩余寿命等) 的所有技术手段的总称。
常用的无损检测方法:超声检测(UT)、磁粉检测(MT)、液体渗透检测(PT)及X射线检测(RT)。
磁粉检测首先来了解一下,磁粉检测的原理。
铁磁性材料和工件被磁化后,由于不连续性的存在,工件表面和近表面的磁力线发生局部畸变,而产生漏磁场,吸附施加在工件表面的磁粉,形成在合适光照下目视可见的磁痕,从而显示出不连续性的位置、形状和大小。
磁粉检测的适用性和局限性有:1、磁粉探伤适用于检测铁磁性材料表面和近表面尺寸很小、间隙极窄目视难以看出的不连续性。
2、磁粉检测可对多种情况下的零部件检测,还可多种型件进行检测。
3、可发现裂纹、夹杂、发纹、白点、折叠、冷隔和疏松等缺陷。
4、磁粉检测不能检测奥氏体不锈钢材料和用奥氏体不锈钢焊条焊接的焊缝,也不能检测铜铝镁钛等非磁性材料。
对于表面浅划伤、埋藏较深洞和与工件表面夹角小于20°的分层和折叠很难发现。
液体渗透检测液体渗透检测的基本原理,零件表面被施涂含有荧光染料或着色染料后,在一段时间的毛细管作用下,渗透液可以渗透进表面开口缺陷中;经去除零件表面多余的渗透液后,再在零件表面施涂显像剂,同样,在毛细管的作用下,显像剂将吸引缺陷中保留的渗透液,渗透液回渗到显像剂中,在一定的光源下(紫外线光或白光),缺陷处的渗透液痕迹被现实,(黄绿色荧光或鲜艳红色),从而探测出缺陷的形貌及分布状态。
渗透检测的优点有:1、可检测各种材料;2、具有较高的灵敏度;3、显示直观、操作方便、检测费用低。
而渗透检测的缺点有:1、不适于检查多孔性疏松材料制成的工件和表面粗糙的工件;2、渗透检测只能检出缺陷的表面分布,难以确定缺陷的实际深度,因而很难对缺陷做出定量评价。
常用无损检测方法的特点及应用
检测方法优点缺点应用射线检测 1.检测结果有直接记录——底片2.可以获得缺陷的投影图像,缺陷定性定量准确1.体积型缺陷检出率很高,而面积型缺陷的检出率受到多种因素影响2. 不适宜检验较厚工作。
3. 检测角焊缝效果较差,不适宜检测板材、楱材、锻件。
4. 对缺陷在工作中厚度方向的位置、尺寸(高度)的确定比较困难。
5. 射线对人体有伤害1.焊缝透照。
2.平板对接焊缝透照。
3.角形焊缝照射。
4.管件对接焊缝照射。
超声检测 1.面积型缺陷的检出率较高,而体积型缺陷的检出率较低。
2.适宜检验厚度较大的工件,不适宜检验较薄的工件。
3.应用范围广,可用于各种试件。
4.检测成本低、速度快,仪器体积小、重量轻,现场使用较方便5.对缺陷在工件厚度方向上的定位较准确。
1.无法得到缺陷直观图像,定性困难,定量精度不高。
2.检测结果无直接见证记录。
3.材质、晶粒度对检测有影响。
4.工件不规则的外形和一些结构会影响检测。
5.探头扫查面的平整度和粗糙度对超声检测有一定影响。
1.陶瓷气孔率的检测。
2.陶瓷表面缺陷检测。
3.钻孔灌注桩的无损检测磁粉检测 1.磁粉检测对工件中表面或近表面的缺陷检测灵敏度最高。
2.对裂纹、折叠、夹层和未焊透等缺陷较为灵敏,能直观地显示出缺陷的大小、位置、形状和严重程度,并可大致确定缺陷性质,检测结果的重复性好。
1.随着缺陷的埋藏深度的增加,其检测灵敏度迅速降低。
因此,它被广泛用于磁性材料表面和近表面的缺陷1.压力容器的探伤。
2.锻件探伤。
3.疲劳缺陷探伤。
渗透检测1.渗透检测可以用于除了疏松多孔性材料外任何种类的材料。
2.形状复杂的部件也可用渗透检测,并一次操作就可大致做到全面检测。
3.同时存在几个方面的缺陷,用一次检测操作就可完成检测。
4.不需要大型的设备,可不用水、电。
1.试件表面光洁度影响大,检测结果往往容易受操作人员水平的影响。
2.可以检出表面开口缺陷,但对埋藏缺陷或闭合型表面缺陷无法检出。
3.检测工序多,速度慢。
- 1、下载文档前请自行甄别文档内容的完整性,平台不提供额外的编辑、内容补充、找答案等附加服务。
- 2、"仅部分预览"的文档,不可在线预览部分如存在完整性等问题,可反馈申请退款(可完整预览的文档不适用该条件!)。
- 3、如文档侵犯您的权益,请联系客服反馈,我们会尽快为您处理(人工客服工作时间:9:00-18:30)。
主要检测缺陷
裂纹、发纹、白点、折叠、夹渣物、冷隔
裂纹、发纹、白点、折叠、夹渣物、冷隔
裂纹、白点、疏松、针孔、夹渣物
裂纹、材质变化、厚度变化
缺陷显示
直观
直观
直观
不直观
缺陷性质判断Байду номын сангаас
能大致确定
能大致确定
能基本确定
难以判断
灵敏度
高
高
高
较低
检测速度
较快
快
慢
很快
污染
较轻
无污染
较重
无污染
相对优点
可检测出铁磁性材料表面和近表面(开口和不开口)的缺陷。
能直接的观察出缺陷的位置、形状、大小和严重程度。
具有较高的检测灵敏度,可检测微米级宽度的缺陷。
单个工件的检测速度快、工艺简单,成本低、污染轻。
综合使用各种磁化方法,几乎不受工件大小和几何形状的影响。
检测缺陷重复性好。
可检测受腐蚀的在役情况。
a)易于实现自动化
b)较高的检测可靠性
c)可以实现缺陷的初步量化
d)在管道的检查中,在厚度高达30mm的壁厚范围內,可同时检测內外壁缺陷
e)高效、无污染,可以获得很高的检测效率.
可检测出任何非松孔性材料表面开口性缺陷。
能直接的观察出缺陷的位置、形状、大小和严重程度。
具有较高的灵敏度。
显示信息的器材
磁粉
计算机显示屏
渗透液、显像剂
记录仪、示波器或电压表
适用的材料
铁磁性材料
铁磁性材料
非多孔性材料
导电材料
主要检测对象
铸钢件、锻钢件、压延件、管材、棒材、型材、焊接件、机加工件在役使用的上述工件检测
铸钢件、锻钢件、压延件、管材、棒材、型材、焊接件、机加工件在役使用的上述工件检测
任何非多孔性材料、工件及在役使用过的上述工件检测
着色检测时不用设备,可以不用水电,特别适用于现场检验。
检测不受工件几何形状和缺陷方向的影响。
对针孔和疏松缺陷的检测灵敏度较高。
非接触法检测,适用于对管件、棒材和丝材进行自动化检测,速度快。
可用检测材料导电率代替硬度检测。了解材料的热处理状态和进行材料分选。
污染很小。
相对局限性
只能检测铁磁性材料及其制品,不能检测奥氏体材料及其焊接接头和非铁磁性材料。
表面缺陷无损检测方法的比较
方法
项目
磁粉检测(MT)
漏磁检测(MLF)
渗透检测(PT)
涡流检测(ET)
方法原理
磁力作用
磁力作用
毛细渗透作用
电磁感应作用
能检出的缺陷
表面和近表面缺陷
表面和近表面缺陷
表面开口缺陷
表面及表层缺陷
缺陷部位的显示形式
漏磁场吸附磁粉形成磁痕
漏磁场大小分布
渗透液的渗出
检测线圈输出电压和相位发生变化
对缺陷性质难以判断。
对铁磁性材料检测灵敏度,不如磁粉检测。
只能检测表面和近表面位置的缺陷。
表面的划伤,针孔缺陷等缺陷不易发现。
受几何形状影响,易产生非相关显示。
用通电法和触头法磁化时,易产生电弧烧伤工件,电接触的非导电覆盖层必须打磨掉。
只适用于铁磁材料。
检测灵敏度低。
缺陷的量化粗略。
受被检测工件的形状限制:由于采用传感器检测漏磁通,漏磁场方法不适合检测形形状复杂的试件。
漏磁探伤不适合开裂很窄的裂纹,尤其是闭合型裂纹。实验上发现,开裂很窄的疲劳裂纹,疲劳裂纹,磁粉探伤和漏磁探伤都没能产生伤显示和伤信号。:
只能检测表面开口性缺陷(表面开口性缺陷被堵塞时也检测不出来)。
单个工件检测效率低,成本高。
检测时缺陷的重复性不好。
污染较严重。
对表面下的较深的缺陷不能检测。
对形状较复杂的工件不适用,有边界效应影响。