稀土球化剂的质量与选用
优质稀土镁球化剂的生产与应用

( 3化 ຫໍສະໝຸດ 理 ( 4O.8 O
柱形 最利 于球化 吸 收 , 深度 应 使球化 剂及 覆盖 其
0.4 0
0.0 O
-
剂填充后高度低于凹坑顶沿 ;
() 5 尽量 缩短 装 球化 剂与 球化 处理 之 间的 时 间, 以防球化 剂氧 化及球 化 反应过早 ;
() a 不同炉次 w( ) Mg量波动 图
0.4 0
-
0.8 O 01 .2
—
() 6 球化 剂上 覆 盖一定 量 的覆 盖剂 或者 同牌
号球铁铁板 , 以延迟球化剂开始反应 的时间; () 7 快速 出铁 , 在球化剂反应前建立较高 的 铁液静压头 , 减少 M 汽化及温度损失 , g 提高球 化剂 M 吸收率 ; g () 8尽量选用盖包法取代传统冲入法进行球
关键词 : 钇基重稀土镁球化包 芯线 ; 喂线球化处理工艺 ; 抗球化衰退能力 中图分类号 :G 5 T 25 文献标识码 : B 文章编号 :0 3 84 (0 ) — 0 2 0 10 — 3 5 2 1 0 0 5 — 3 1 5
D :036 /i n10 — 3 52 1 . . 9 OI 1.9 9 .s. 3 8 4 . 0 0 js 0 015 0
摘要 : 细介 绍了喂线 处理 工艺和包 芯线 的规格 , 详 采用钇基重稀土镁球化 包芯线生产汽车加重桥壳球铁铸件 和风 电铸 件, 试验结果表明 :1 钇基重稀土高镁球化包芯线应用于 大断 面球 墨铸铁件生产 , () 具有较强的抗球 化衰退 能力 , 能保证 材料的质量要求 ;2 喂线法球化处理工艺是保证球铁材料质量 、 () 改善作业环境 的良好工艺。
率、 石墨球大小及铸件产生缩松 、 气孔 、 夹渣的倾 向等。 目前市场上稀土镁球化剂以其处理方式简 便、 球化质量稳定性 、 生产成本低而被广泛应用 。 优质球化剂必须具备 : 化学成分稳定 , 波动 小; 合金纯度高 , g M O含量低 ; 合金组织致密 , 无 气缩孑 ; L 粒度分布均匀 、 合理。
重稀土球化剂

超厚断面大吨位铸件用钇基重稀土球化剂(DY)一、产品特点及应用范围:该产品与轻稀土同类产品相比,具有抗衰退、抗石墨畸变、抗干扰元素能力强,无球化衰退之忧,能确保铸件性能表里如一,且适用的原料范围宽、不回硫、使磷共晶减少并弥散等特点。
是目前解决由于衰退引起的厚大断面铸件质量不高,特别是本体心部质量不高及质量不稳定,成品率低这一国际铸造难题理想的球化剂。
该产品适用于超厚大断面铸件的生产,其处理工艺与轻稀土球化剂基本一致,适用于铁液温度1400-1550℃,普通冲入法球化,加入量为1.0-1.8%(根据铁液杂质含量高低而定),球化剂入包后上面覆盖硅铁或铁屑、铁板,无需采取专门的脱硫、冷却措施。
球化反应后,无球化衰退现象,且球化率>80%,石墨圆整度好。
二、产品标准1、物理状态⑴产品断面应呈银灰色;⑵产品粒度范围为5-30mm,小于5mm和大于30mm,各不应超过总量的5%;⑶需方对化学成份和粒度有特殊要求,可由供需双方另行协商。
2、包装、标志和质量证明书⑴包装、标志:产品采用内衬塑料袋的双层编织袋包装,有明确的名称和数量标志,25kg/袋,也可根据用户要求选择包装方式;⑵质量证明书:出具符合用户要求并与产品相符的产品质量证明书。
风力发电机关键零部件专用重稀土球化剂(FD)一、产品特点及应用范围:◆抗球化衰退、抗石墨畸变及抗干扰元素能力显著,与公司配套孕育剂联合使用,确保断面>180mm铸件心部球化3级以内,石墨球数>200个/mm2,球化率>85%,可以提高抗低温冲击韧性和抗拉强度值;◆采用特殊工艺和高纯原料生产,元素偏差值小,纯度高,干扰球化的微量元素少而低;◆能适当放宽球墨铸造生铁原料要求,打破以往采用高纯生铁生产该类铸件的传统思路,简便地生产出表里如一的高品质铸件,从而大幅度节约成本;◆残余稀土的范围较普通稀土球化剂宽,具有白口倾向小的优势,且可简化加冷铁等强制冷却工艺;◆适用于电炉铁水工艺,最佳球化温度1420-1450℃,堤坝包冲入法球化,加入量为1.0-1.6%。
球墨铸铁用稀土硅镁球化剂
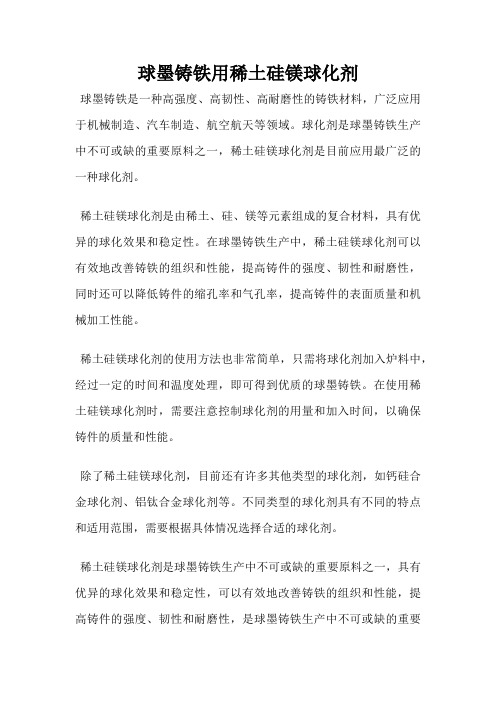
球墨铸铁用稀土硅镁球化剂
球墨铸铁是一种高强度、高韧性、高耐磨性的铸铁材料,广泛应用于机械制造、汽车制造、航空航天等领域。
球化剂是球墨铸铁生产中不可或缺的重要原料之一,稀土硅镁球化剂是目前应用最广泛的一种球化剂。
稀土硅镁球化剂是由稀土、硅、镁等元素组成的复合材料,具有优异的球化效果和稳定性。
在球墨铸铁生产中,稀土硅镁球化剂可以有效地改善铸铁的组织和性能,提高铸件的强度、韧性和耐磨性,同时还可以降低铸件的缩孔率和气孔率,提高铸件的表面质量和机械加工性能。
稀土硅镁球化剂的使用方法也非常简单,只需将球化剂加入炉料中,经过一定的时间和温度处理,即可得到优质的球墨铸铁。
在使用稀土硅镁球化剂时,需要注意控制球化剂的用量和加入时间,以确保铸件的质量和性能。
除了稀土硅镁球化剂,目前还有许多其他类型的球化剂,如钙硅合金球化剂、铝钛合金球化剂等。
不同类型的球化剂具有不同的特点和适用范围,需要根据具体情况选择合适的球化剂。
稀土硅镁球化剂是球墨铸铁生产中不可或缺的重要原料之一,具有优异的球化效果和稳定性,可以有效地改善铸铁的组织和性能,提高铸件的强度、韧性和耐磨性,是球墨铸铁生产中不可或缺的重要
原料之一。
球化剂的品质、选用与提示

球化剂的品质、选用与提示河北工业大学(天津300130)钱立张宏标【提要】列出了评判球化剂的4项内容,讨论了选用球化剂成分的依据,并对所称铸态用球化剂的含义和成分提出了看法。
关键词:球化剂球墨铸铁自由渗碳体金属基体当前球墨铸铁(以下简称球铁)生产中存在着两大问题:一是球化质量不稳定;二是球化剂选用不当。
前一个问题与球化剂品质有关,后一个问题则与用户对球化剂品种及成分的内涵不甚了解有关。
以下简述的是球化剂的品质要求和成分选择原则。
一、球化剂的品质要求衡量球化剂品质的因素有以下几点。
1、Mg和RE的波动值按国标规定,各个牌号中Mg和RE的含量允许偏差为±1%。
以FeSiMg8RE7为例,Mg的名义含量为8%,可变动于7%~9%;RE的名义含量为7%,可变动于6%~8%,上下限相差2%。
Mg含量差2%,Mg残可相差0 010%~0 015%,如再有铁水中含硫量,铁水温度及接铁量等波动因素叠加,Mg残的出入会更大。
因此,评价球化剂的首要内容是该球化剂中Mg、RE实际含量偏离名义含量的幅度大小。
一般好的球化剂,偏差应控制在±0 2%~0 3%以内。
2、MgO含量Mg易氧化,球化剂在熔炼过程中,不可避免地会有一部分Mg生成MgO,浇注成锭时,还有二次氧化,这些均构成了球化剂中MgO含量。
球化剂出厂单中所报为Mg总量,MgO量越多,Mg总量中所剩有效Mg量就越少。
1993年新国标中规定MgO<1%,每1%MgO,约损失0 6%的Mg。
MgO量高,不仅减少有效Mg,而且略提高球化剂熔点,妨碍吸收。
因此,MgO量高,会造成球化不良。
3、断口密实程度观察球化剂断口,可以直感球化剂的优劣。
凡是断口均匀,色灰兰略黄,密实者为上品。
而断口不均,有异物,致密性差的为下品,这种球化剂,从不同货位取样,其成分亦必参差不齐。
4 粒度在批量生产的铸工车间,球化处理工艺严密,对球化剂用量、粒度和包底装放规则都有明确规定。
球化剂
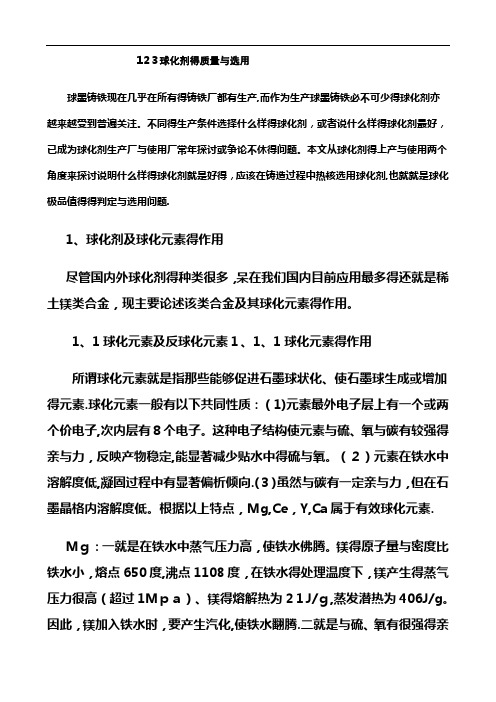
123球化剂得质量与选用球墨铸铁现在几乎在所有得铸铁厂都有生产,而作为生产球墨铸铁必不可少得球化剂亦越来越受到普遍关注。
不同得生产条件选择什么样得球化剂,或者说什么样得球化剂最好,已成为球化剂生产厂与使用厂常年探讨或争论不休得问题。
本文从球化剂得上产与使用两个角度来探讨说明什么样得球化剂就是好得,应该在铸造过程中热核选用球化剂,也就就是球化极品值得得判定与选用问题.1、球化剂及球化元素得作用尽管国内外球化剂得种类很多,呆在我们国内目前应用最多得还就是稀土镁类合金,现主要论述该类合金及其球化元素得作用。
1、1球化元素及反球化元素1、1、1球化元素得作用所谓球化元素就是指那些能够促进石墨球状化、使石墨球生成或增加得元素.球化元素一般有以下共同性质:(1)元素最外电子层上有一个或两个价电子,次内层有8个电子。
这种电子结构使元素与硫、氧与碳有较强得亲与力,反映产物稳定,能显著减少贴水中得硫与氧。
(2)元素在铁水中溶解度低,凝固过程中有显著偏析倾向.(3)虽然与碳有一定亲与力,但在石墨晶格内溶解度低。
根据以上特点,Mg,Ce,Y,Ca属于有效球化元素.Mg:一就是在铁水中蒸气压力高,使铁水佛腾。
镁得原子量与密度比铁水小,熔点650度,沸点1108度,在铁水得处理温度下,镁产生得蒸气压力很高(超过1Mpa)、镁得熔解热为21J/g,蒸发潜热为406J/g。
因此,镁加入铁水时,要产生汽化,使铁水翻腾.二就是与硫、氧有很强得亲与力。
所生成得MgO与MgS熔点高,密度也远小于铁,容易与铁水分离,因此镁处理后得铁水,硫与羊得含量都很低;三就是在铁水凝固过程中有偏析于石墨得倾向,当其在铁水中得残留量超过0、035%时,使末就可以球化,但当镁残留量超过0、07%时,一部分镁偏析于晶界,并于晶界中得碳、磷等发生放热反应,生成MgC2、Mg2C3、Mg3P2等。
残留镁量更多时,晶间碳化物增多。
Re:稀土族元素对石墨球化有显著作用得就是轻稀土元素中得铈与重稀土中得钇.一就是稀土元素得沸点均比镁高,加入铁水中时,不会引起铁水得翻腾与喷溅;二就是铈与钇基稀土元素有比镁更强得脱硫脱氧能力,生成得硫化稀土、氧化稀土等化合物熔点高、稳定性好;三就是,稀土元素与铁水中得球化干扰元素也能形成稳定得化合物,因此含稀土得球化剂比镁球化剂得抗干扰能力强.稀土元素残留量对石墨球化有明显得影响.轻稀土处理过共晶铁水,当残留铈含量0、04%时,石墨就可以球化,而且很稳定;处理亚共晶铁水时,轻稀土加入量要增加。
球化剂怎么选
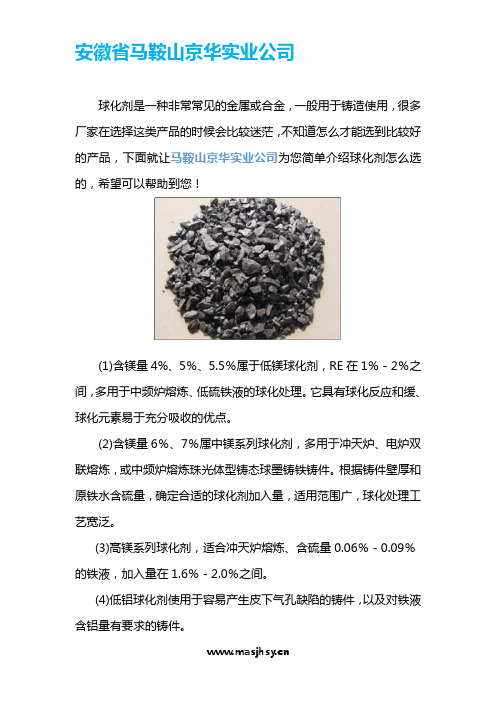
球化剂是一种非常常见的金属或合金,一般用于铸造使用,很多厂家在选择这类产品的时候会比较迷茫,不知道怎么才能选到比较好的产品,下面就让马鞍山京华实业公司为您简单介绍球化剂怎么选的,希望可以帮助到您!
(1)含镁量4%、5%、5.5%属于低镁球化剂,RE在1%-2%之间,多用于中频炉熔炼、低硫铁液的球化处理。
它具有球化反应和缓、球化元素易于充分吸收的优点。
(2)含镁量6%、7%属中镁系列球化剂,多用于冲天炉、电炉双联熔炼,或中频炉熔炼珠光体型铸态球墨铸铁铸件。
根据铸件壁厚和原铁水含硫量,确定合适的球化剂加入量,适用范围广,球化处理工艺宽泛。
(3)高镁系列球化剂,适合冲天炉熔炼、含硫量0.06%-0.09%的铁液,加入量在1.6%-2.0%之间。
(4)低铝球化剂使用于容易产生皮下气孔缺陷的铸件,以及对铁液含铝量有要求的铸件。
(5)纯Ce、纯La生产的球化剂,球化处理后铁液纯净夹杂物少、石墨球圆整。
钇基重稀土生产的球化剂适合于大断面铸件,延缓球化衰退、防止块状石墨。
含Sb球化剂用于珠光体型球墨铸铁。
(6)低硅球化剂适用于使用大量回炉料的铸造工厂;镍镁球化剂则用于高镍奥氏体球墨铸铁。
马鞍山京华实业公司是炼钢、铸造用增碳剂、煅后石油焦以及石墨化增碳剂,孕育剂,碳化硅等专业生产厂家。
公司能按增碳剂客户的要求加工成各种粒度规格的增碳剂,对产品高质量的追求户及对顾客称心满意的服务是马鞍山京华的经营宗旨。
马鞍山京华实业公司秉承着“凭质量铸造现在,靠信誉开拓未来”的经营理念,为客户提供最优质的增碳剂和贴心的服务。
如果您想进一步了解,可以直接点击官网马鞍山京华实业公司进行在线咨询。
新型稀土镁球化剂

新型稀土镁球化剂
随着工业化进程的不断推进,稀土元素在现代工业中的应用越来越广泛。
其中,稀土镁球化剂是一种新型稀土材料,具有独特的物理化学性质和广阔的应用前景。
稀土镁球化剂是由稀土元素和镁元素组成的一种新型功能材料。
它具有高强度、高硬度、高热稳定性、低抗氧化性和良好的耐腐蚀性等优点,能够广泛应用于冶金、化工、建材、电子、光学等领域。
在冶金行业中,稀土镁球化剂可作为铸造助剂,能够提高铸件的强度和耐磨性,减少气孔和缩孔等缺陷,提高铸件的质量和使用寿命。
在化工行业中,稀土镁球化剂可作为催化剂,能够提高反应速率和产品品质,降低生产成本和环境污染。
在建材行业中,稀土镁球化剂可作为填料和增强剂,能够提高材料强度和抗风化性能,提高产品的市场竞争力。
在电子、光学等领域中,稀土镁球化剂还可作为粉末冶金原料、光学玻璃添加剂、稀土发光材料等,具有广泛的应用前景。
随着稀土镁球化剂的广泛应用,其生产技术也在不断改进和创新。
目前,常用的生产方法包括溶剂热法、水热法、水煮法等。
这些方法具有生产周期短、成本低、产品质量稳定等优点,能够满足不同领域和行业的需求。
总之,稀土镁球化剂作为一种新型稀土材料,具有广泛的应用前景和市场潜力。
随着技术的不断进步和生产工艺的不断完善,相信它将在未来的工业发展中发挥越来越重要的作用。
- 1 -。
球化剂生产质量控制要点浅析
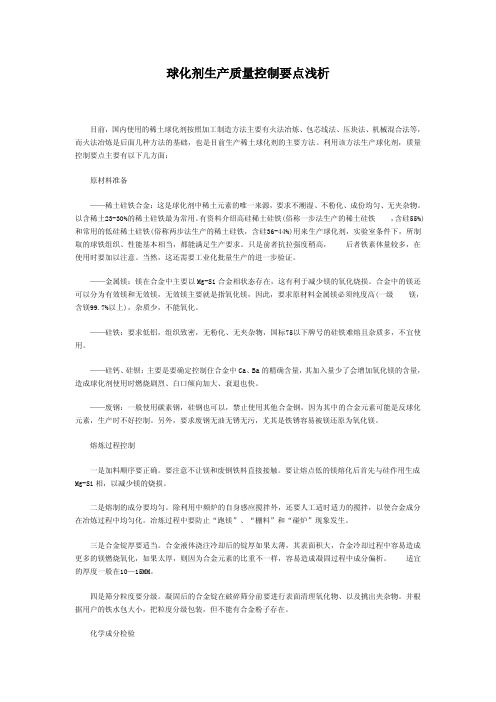
球化剂生产质量控制要点浅析目前,国内使用的稀土球化剂按照加工制造方法主要有火法冶炼、包芯线法、压块法、机械混合法等,而火法冶炼是后面几种方法的基础,也是目前生产稀土球化剂的主要方法。
利用该方法生产球化剂,质量控制要点主要有以下几方面:原材料准备——稀土硅铁合金:这是球化剂中稀土元素的唯一来源,要求不潮湿、不粉化、成份均匀、无夹杂物。
以含稀土23-30%的稀土硅铁最为常用。
有资料介绍高硅稀土硅铁(俗称一步法生产的稀土硅铁,含硅55%)和常用的低硅稀土硅铁(俗称两步法生产的稀土硅铁,含硅36-44%)用来生产球化剂,实验室条件下,所制取的球铁组织、性能基本相当,都能满足生产要求。
只是前者抗拉强度稍高,后者铁素体量较多,在使用时要加以注意。
当然,这还需要工业化批量生产的进一步验证。
——金属镁:镁在合金中主要以Mg-Si合金相状态存在,这有利于减少镁的氧化烧损。
合金中的镁还可以分为有效镁和无效镁,无效镁主要就是指氧化镁,因此,要求原材料金属镁必须纯度高(一级镁,含镁99.7%以上),杂质少,不能氧化。
——硅铁:要求低铝,组织致密,无粉化、无夹杂物,国标75以下牌号的硅铁难熔且杂质多,不宜使用。
——硅钙、硅钡:主要是要确定控制住合金中Ca、Ba的精确含量,其加入量少了会增加氧化镁的含量,造成球化剂使用时燃烧剧烈、白口倾向加大、衰退也快。
——废钢:一般使用碳素钢,硅钢也可以,禁止使用其他合金钢,因为其中的合金元素可能是反球化元素,生产时不好控制。
另外,要求废钢无油无锈无污,尤其是铁锈容易被镁还原为氧化镁。
熔炼过程控制一是加料顺序要正确。
要注意不让镁和废钢铁料直接接触。
要让熔点低的镁熔化后首先与硅作用生成Mg-Si相,以减少镁的烧损。
二是熔制的成分要均匀。
除利用中频炉的自身感应搅拌外,还要人工适时适力的搅拌,以使合金成分在冶炼过程中均匀化。
冶炼过程中要防止“跑镁”、“棚料”和“碰炉”现象发生。
三是合金锭厚要适当。
- 1、下载文档前请自行甄别文档内容的完整性,平台不提供额外的编辑、内容补充、找答案等附加服务。
- 2、"仅部分预览"的文档,不可在线预览部分如存在完整性等问题,可反馈申请退款(可完整预览的文档不适用该条件!)。
- 3、如文档侵犯您的权益,请联系客服反馈,我们会尽快为您处理(人工客服工作时间:9:00-18:30)。
·稀土球化剂的质量与选用(铸造球铁)摘要:本文探讨了球化剂及球化元素的作用机理,提出了球化剂成分的配置原则,并结合多年实际,强调了合金生产企业球化剂质量的生产控制要点,说明了球化剂质量的评价指标,阐述了球化剂如何选用、以及选用不当引起的铸造缺陷,同时还提出了稳定球化处理的综合配套措施。
球墨铸铁现在几乎在所有的铸铁厂都有生产,而作为生产球墨铸铁必不可少的球化剂亦越来越受到普遍关注。
不同的生产条件选择什么样的球化剂,或者说什么样的球化剂最好,已成为球化剂生产厂和使用厂常年探讨或争论不休的问题。
本文从球化剂的上产和使用两个角度来探讨说明什么样的球化剂是好的,应该在铸造过程中热核选用球化剂,也就是球化极品值得的判定和选用问题。
1、球化剂及球化元素的作用尽管国内外球化剂的种类很多,呆在我们国内目前应用最多的还是稀土镁类合金,现主要论述该类合金及其球化元素的作用。
1、1球化元素及反球化元素1、1、1球化元素的作用所谓球化元素是指那些能够促进石墨球状化、使石墨球生成或增加的元素。
球化元素一般有以下共同性质:(1)元素最外电子层上有一个或两个价电子,次内层有8个电子。
这种电子结构使元素与硫、氧和碳有较强的亲和力,反映产物稳定,能显著减少贴水中的硫和氧。
(2)元素在铁水中溶解度低,凝固过程中有显著偏析倾向。
(3)虽然和碳有一定亲和力,但在石墨晶格内溶解度低。
根据以上特点,Mg,Ce,Y,Ca属于有效球化元素。
Mg:一是在铁水中蒸气压力高,使铁水佛腾。
镁的原子量和密度比铁水小,熔点650度,沸点1108度,在铁水的处理温度下,镁产生的蒸气压力很高(超过1Mpa).镁的熔解热为21J/g,蒸发潜热为406J/g。
因此,镁加入铁水时,要产生汽化,使铁水翻腾。
二是与硫、氧有很强的亲和力。
所生成的MgO和MgS熔点高,密度也远小于铁,容易与铁水分离,因此镁处理后的铁水,硫和羊的含量都很低;三是在铁水凝固过程中有偏析于石墨的倾向,当其在铁水中的残留量超过0.035%时,使末就可以球化,但当镁残留量超过0.07%时,一部分镁偏析于晶界,并于晶界中的碳、磷等发生放热反应,生成MgC2、Mg2C3、Mg3P2等。
残留镁量更多时,晶间碳化物增多。
Re:稀土族元素对石墨球化有显著作用的是轻稀土元素中的铈和重稀土中的钇。
一是稀土元素的沸点均比镁高,加入铁水中时,不会引起铁水的翻腾和喷溅;二是铈和钇基稀土元素有比镁更强的脱硫脱氧能力,生成的硫化稀土、氧化稀土等化合物熔点高、稳定性好;三是,稀土元素与铁水中的球化干扰元素也能形成稳定的化合物,因此含稀土的球化剂比镁球化剂的抗干扰能力强。
稀土元素残留量对石墨球化有明显的影响。
轻稀土处理过共晶铁水,当残留铈含量0.04%时,石墨就可以球化,而且很稳定;处理亚共晶铁水时,轻稀土加入量要增加。
轻稀土处理得球铁,石墨圆整度比镁处理得球铁要差,并出现碎块状石墨;另外轻稀土处理得球铁白口倾向大,因此需要控制其加入量。
重稀土钇本身熔点高,其脱氧除硫产生的氧化物、硫化物在高温下比较稳定,因此其抗球化衰退能力很强。
1400度的铁水保温1小时,球化率降低不超过10%,含硫0.06% 的铁水,用钇基重稀土合金处理后,能得到完整的球状石墨。
铁水中残留钇0.10—0.15%,石墨球化良好;低于此限度,随钇量减少一次出现不规则石墨和蠕虫状石墨;残留钇超过0.15而低于0.30%时,白口倾向逐渐增大,石墨圆整度变差,并在更高残留量时出现YTe4。
Ca:钙在铁水中的溶解度很低,它对金相组织的影响是通过与氧和硫的结合而间接实现的。
与镁相比,钙与硫、氧的亲和力更强,能够有效的脱硫除氧。
钙残留量很低时,石墨分枝倾向增加,残留量较多时,可是使石墨尺寸减小,分枝倾向降低。
钙残留量达到0.2%时,白口倾向明显加大。
1、1、2反球化元素(球化干扰元素)的作用该类元素主要是指破坏和阻碍使石墨球化的元素,按其作用机理大概可以分三类:一是消耗型反球化元素,如硫、氧、硒、碲等,它们与镁、稀土元素生成化合物,通过消耗球化元素来阻止球状石墨的形成。
二是境界偏析的球化干扰元素,包括锡、锑、砷、铜、硼、钛、铝等,这些元素富集到晶界,促使碳在共晶后期结晶时,形成畸形的枝晶状石墨,如果这些元素含量较高,也可在共晶中期促成石墨畸变,形成团状或厚片状石墨。
三是一些中间球化干扰元素,如铝、铋,它们在含量较低时主演通过偏析作用促成石墨畸变,含量较高时也能消耗球化元素。
另外,反球化元素对球铁基体也有不同的影响。
Te\B强烈促进白口的形成,As\Sn\Sb\Pb\Bi 稳定珠光体,Al\Zr促进铁素体形成,Se无影响。
1、2球化元素的配置和球化剂的种类镁、稀土和钙,是目前公认的有促进石墨球化的能力,但如何结合工业生产实际来制备和使用,既保证球化剂的球化能力,又要在生产中容易制取,原料经济,使用方便,便成为配制和使用球化剂的的原则。
1、2、1球化元素的配置——成分配制原则和特点:要有强烈的球化能力,着显然要以镁为主,镁的沸点低,加入铁水中可以使铁水剧烈翻腾,反应上下均匀;配成合金后增加比重,使其在铁水中不易上浮,可以减少镁的氧化和烧损。
——消化中和反球化元素能力,稀土元素有有很强的脱硫除气、净化铁水和消除反球化元素的能力,而且我国稀土资源丰富,获取原料成本较低。
——球化剂反应平稳,易于操作。
钙虽然不能作为秋化剂单独使用,但用它和和镁、稀土配成复合球化剂,就既可以减少球化剂中MgO的含量,使球化处理平稳,还可以减少因稀土造成的较大白口倾向。
因此,配制球化剂成分的原则和特点,就是要发挥各种球化元素的长处,来提高球化效果,并通过调整球化元素的含量来满足不同生产条件、不同结构铸件的需求。
1、2、2球化剂的种类按照球化和反球化元素配置的原则,国内外曾先后开发了多种球化剂,大体上有以下几种:————纯镁:这是国外常用的球化剂,国内应用比较少。
压力加镁制取球铁,优点和缺点同样明显。
————铜镁、镍镁:我国早期使用的该合金,但成本高,回炉料中铜和镍积累难以控制,造成韧性下降。
————硅镁铁合金:一般镁含量最低3.5—4.5%,最高10—15%,常用的合金是镁5—10%、硅42—47%,其余为贴。
含镁量越低,球化反应越平稳,镁回收率越高(含镁4%的能比9%个合金镁回收率提高10%),但是低镁球化剂是铁水的增硅量加大。
该球化剂是用于处理硫和反球化元素含量较低的铁水,浇注中等断面厚度的铸件。
目前在国内要大批量用于制造球墨铸铁将会与我国铸造企业的生产条件和原材料采购产生一定的矛盾。
————稀土镁类合金:包括稀土硅镁、稀土钙镁、稀土铜镁等合金,是我国工程技术人员立足我国实际,在六十年代初研制开发的稀土镁类系列合金球化剂,它们综合了各种球化元素的优缺点,尤其是稀土镁钙合金,是目前国内应用量大面广的主要球化剂,从而走出了一条适合我国国情的球墨铸铁制造技术道路。
2、球化剂质量的生产控制要点目前,国内使用的稀土球化剂按照加工制造方法主要有火法冶炼、包芯线法、压块法、机械混合法等,而火法冶炼是后面几种方法的基础,也是生产稀土球化剂的主要方法。
利用该方法生产球化剂,质量控制要点主要有以下几方面:2、1原材料准备——稀土硅铁合金:这是球化剂中稀土元素的唯一来源,要求不潮湿、不粉化、成份均匀、无夹杂物。
以含稀土23-30%的稀土硅铁最为常用。
有资料介绍高硅稀土硅铁(俗称一步法生产的稀土硅铁,含硅55%)和常用的低硅稀土硅铁(俗称两步法生产的稀土硅铁,含硅36-44%)用来生产球化剂,实验室条件下,所制取的球铁组织、性能基本相当,都能满足生产要求。
只是前者抗拉强度稍高,后者铁素体量较多,在使用时要加以注意。
当然,这还需要工业化批量生产的进一步验证。
——金属镁:镁在合金中主要以Mg-Si合金相状态存在,这有利于减少镁的氧化烧损。
合金中的镁还可以分为有效镁和无效镁,无效镁主要就是指氧化镁,因此,要求原材料金属镁必须纯度高(一级镁,含镁99.7%以上),杂质少,不能氧化。
——硅铁:要求低铝,组织致密,无粉化、无夹杂物,国标75以下牌号的硅铁难熔且杂质多,不宜使用。
——硅钙、硅钡:主要是要确定控制住合金中Ca、Ba的精确含量,其加入量少了会增加无效氧化镁的含量,造成球化剂使用时燃烧剧烈、白口倾向加大、衰退也快。
——废钢:一般使用碳素钢,硅钢也可以,禁止使用其他合金钢,因为其中的合金元素可能是反球化元素,生产是不好控制。
另外,要求废钢无油无锈无污责,尤其是铁锈容易被镁还原为氧化镁。
2、2熔炼过程控制一是加料顺序要正确。
要注意不让镁和废钢铁料直接接触。
要让熔点低的镁熔化后首先与硅作用生成Mg-Si相,以减少镁的烧损。
二是熔制的成分要均匀。
除利用中频炉的自身感应搅拌外,还要人工适时适力的搅拌,以使合金成分在冶炼过程中均匀化。
冶炼过程中要防止“跑镁”、“棚料”和“碰炉”现象发生。
三是合金锭厚要适当。
合金液体浇注冷却后的锭厚如果太薄,其表面积大,合金冷却过程中容易造成更多的镁燃烧氧化,如果太厚,则因为合金元素的比重不一样,容易造成凝固过程中成分偏析。
适宜的厚度一般在10—15MM。
四是筛分粒度要分级。
凝固后的合金锭在破碎筛分前要进行表面清理氧化物、以及挑出夹杂物。
并根据用户的铁水包大小,把粒度分级包装,但不能有合金粉子存在。
2、3化学成分检验一个合格的球化剂,除了外观致密、没有夹杂物等之外,更重要的还是其化学成分的含量及均匀性。
球化剂中,除了常规的Re,Mg,Si,Ca等元素的分析之外,生产厂和使用厂常常忽略了对合金中MgO的分析。
这也与没有统一的MgO国家分析标准有关,同一种合金在不同的厂家用不同的分析方法,得出的成分结论不一样。
这就要求合金生产厂和铸造厂用户要达成一个统一的验收分析标准来共同遵守。
3、球化剂质量的评价什么样的球化剂是最好的?这往往会成为诸多铸造厂的常年话题。
其实,可以说,球化剂没有最好的,只有适合的,适合自己的就是最好的。
那么,到底该如何评价球化剂的质量哪?有资料从球化元素在铁液中的反应热力学、反应动力学和球化剂生产过程质量影响因素、铸造厂使用过程工艺影响因素,提出了判定球化剂质量的标准如下:(1)球化元素与铁水中硫、氧等元素的亲和力。
亲和力强,并与之形成化合物,作为铁液凝固过程中的外来核心,如稀土、镁、钙等球化元素。
(2)球化元素改变石墨形态由片状变为球状的能力。
(3)球化剂的密度、沸点均低于铁液。
密度小能够在铁液中自动上浮,沸点低于铁液处理温度,镁能在该处理温度下转化为气态,有自搅拌作用,从而改善球化效果。
(4)球化剂中氧化镁含量等于镁含量的10%左右。
(5)球化剂致密、无偏析、无缩孔缩松、不粉化。
(6)球化剂粒度分布均匀,无粉状合金,钝角多变形颗粒为好。