手机壳料检验标准
{生产管理知识}手机塑胶件来料检验标准手册

{生产管理知识}手机塑胶件来料检验标准手册一、引言手机塑胶件是手机外壳等关键组件,其质量直接影响手机的整体质量和性能。
为了保证手机塑胶件质量的稳定和一致性,需要进行来料检验。
本手册旨在制定手机塑胶件来料检验标准,以确保来料质量符合整体要求。
二、检验内容1.外观检验外观缺陷是目测可见的缺陷,包括但不限于模具毛刺、气泡、油污、划痕、凹陷等。
外观检验应参考手机外壳设计图纸,检查外观是否符合要求。
2.尺寸检验尺寸检验是对手机塑胶件的几何尺寸进行测量,以确定其与设计要求的偏差。
尺寸检验应按照设计图纸或者产品规格要求进行。
3.物理性能检验物理性能检验包括拉伸强度、冲击强度、硬度等。
拉伸强度测试需要使用拉力测试仪进行,冲击强度测试需要使用冲击试验机进行。
4.化学性能检验化学性能检验包括耐酸碱性、耐候性等。
可以使用化学品测试仪器对手机塑胶件进行相应测试,以确定其化学性能是否符合要求。
5.封装密封性检验封装密封性检验是对手机塑胶件的封装效果进行评估,目的是确保塑胶件能够有效防止外界物质对手机内部的侵入。
可以使用封装性测试仪器进行密封性测试。
三、检验方法1.外观检验方法外观检验应该使用肉眼进行,充分对比设计图纸,检查是否有外观缺陷。
2.尺寸检验方法尺寸检验可以使用数码测量仪器进行,根据设计图纸或产品规格要求进行测量,记录尺寸数据并与规格进行对比。
3.物理性能检验方法物理性能检验应使用专业测试仪器进行,在测试之前应进行仪器的校准。
测试结果应与设计要求进行对比。
4.化学性能检验方法化学性能检验可以使用专业测试仪器进行,测试之前需要对仪器进行校准。
测试结果应与规格要求进行对比。
5.封装密封性检验方法封装密封性检验需要使用专业的封装性测试仪器,在测试之前应对仪器进行校准。
测试结果应与规格要求进行对比。
四、检验标准1.外观检验标准外观检验标准应按照设计要求进行,包括模具毛刺、气泡、油污、划痕等外观缺陷的数量和质量等。
2.尺寸检验标准尺寸检验标准应参考设计图纸或产品规格要求,确定每个尺寸的容差范围。
手机外壳的测试标准
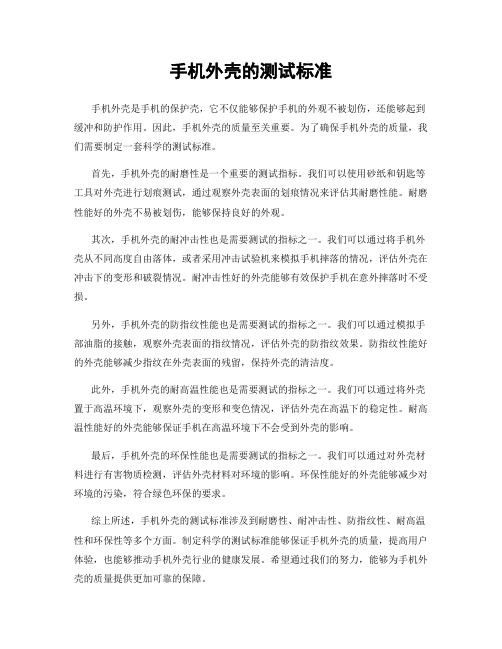
手机外壳的测试标准手机外壳是手机的保护壳,它不仅能够保护手机的外观不被划伤,还能够起到缓冲和防护作用。
因此,手机外壳的质量至关重要。
为了确保手机外壳的质量,我们需要制定一套科学的测试标准。
首先,手机外壳的耐磨性是一个重要的测试指标。
我们可以使用砂纸和钥匙等工具对外壳进行划痕测试,通过观察外壳表面的划痕情况来评估其耐磨性能。
耐磨性能好的外壳不易被划伤,能够保持良好的外观。
其次,手机外壳的耐冲击性也是需要测试的指标之一。
我们可以通过将手机外壳从不同高度自由落体,或者采用冲击试验机来模拟手机摔落的情况,评估外壳在冲击下的变形和破裂情况。
耐冲击性好的外壳能够有效保护手机在意外摔落时不受损。
另外,手机外壳的防指纹性能也是需要测试的指标之一。
我们可以通过模拟手部油脂的接触,观察外壳表面的指纹情况,评估外壳的防指纹效果。
防指纹性能好的外壳能够减少指纹在外壳表面的残留,保持外壳的清洁度。
此外,手机外壳的耐高温性能也是需要测试的指标之一。
我们可以通过将外壳置于高温环境下,观察外壳的变形和变色情况,评估外壳在高温下的稳定性。
耐高温性能好的外壳能够保证手机在高温环境下不会受到外壳的影响。
最后,手机外壳的环保性能也是需要测试的指标之一。
我们可以通过对外壳材料进行有害物质检测,评估外壳材料对环境的影响。
环保性能好的外壳能够减少对环境的污染,符合绿色环保的要求。
综上所述,手机外壳的测试标准涉及到耐磨性、耐冲击性、防指纹性、耐高温性和环保性等多个方面。
制定科学的测试标准能够保证手机外壳的质量,提高用户体验,也能够推动手机外壳行业的健康发展。
希望通过我们的努力,能够为手机外壳的质量提供更加可靠的保障。
手机塑胶外壳通用检验标准
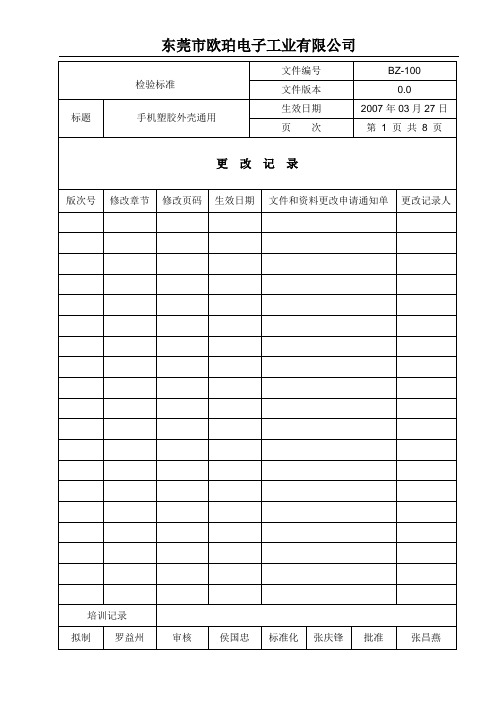
耐化妆品测试
先用棉布将产品表面擦拭干净,将凡士林护手霜(或SPF8的防晒霜)涂在产品表面上后,将产品放在恒温箱内(温度设定在60℃±5℃,湿度设定在为90%--98%),保持24h后将产品取出,用棉布将化妆品擦试干净.检查产品外观,并测试油漆的附着力。产品表面不出现异常,附着力≥4B则为合格:产品表面出现油膜有脱落、变色、裂痕、起皱、分离为异常。首次到料、每隔三个月每厂家抽测一次,每次检验两个。
10)丝印针孔(在应有印刷的区域出现点状油墨)的直径D>0.2,1个。
11)文字断线、边角漏印、文字残缺、模糊、残缺、毛边、积油、多划、少划。
12)丝印重影或二次丝印整体错位。
13)丝印文字留有指纹。
14)丝印表面异物(线屑状异物、印迹等),250mm-300mm目视距离分辩明显。
15)色薄(文字的颜色偏浅),250mm-300mm目视距离分辩明显。
2)弹性皮革漆:以同样的方法产品电池盖或平面标准试件上检测,以油漆不透底,露出底材,达到150个循环以上为合格。
每批到料中以颜色为准,每个颜色一个。
5)硬度
测试内容描述
备注
检验内容
铅笔硬度试验
用H铅笔(三菱UNI测试铅笔),将笔芯削成长5mm的圆柱形并在400目砂纸上磨平后,装在专用的铅笔硬度测试仪上(施加在笔尖上的载荷为1kg,铅笔与水平面的夹角为45°),推动铅笔向前滑动约5mm的长度,不同位置划3次(每个位置划一次),再用橡皮擦将铅笔痕擦拭干净。尽可能把测试胶件剪平成标准测试件,测试点应避开油漆断裂层2mm。产品表面有1条或1条以下划痕为合格,顶出时的剥落及陷下不作为观察对象。
7)其他
测试内容描述
备注
检验内容
弯折试验
某公司手机外壳塑胶件外观检验标准
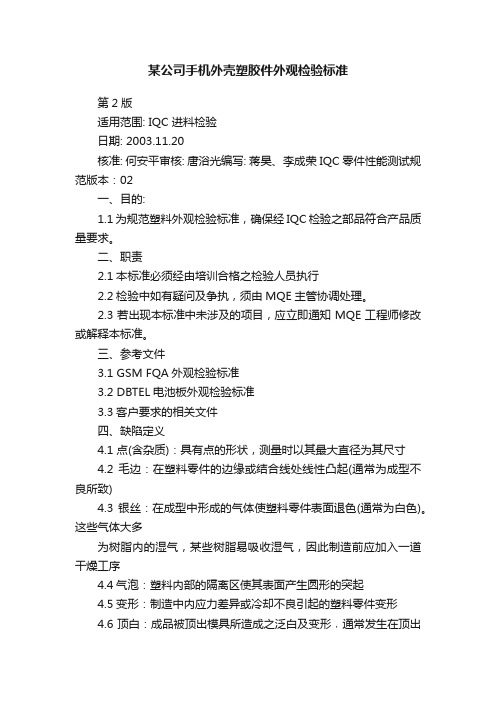
某公司手机外壳塑胶件外观检验标准第2版适用范围: IQC 进料检验日期: 2003.11.20核准: 何安平审核: 唐浴光编写: 蒋昊、李成荣IQC零件性能测试规范版本:02一、目的:1.1为规范塑料外观检验标准,确保经IQC检验之部品符合产品质量要求。
二、职责2.1本标准必须经由培训合格之检验人员执行2.2检验中如有疑问及争执,须由MQE主管协调处理。
2.3若出现本标准中未涉及的项目,应立即通知MQE工程师修改或解释本标准。
三、参考文件3.1 GSM FQA外观检验标准3.2 DBTEL电池板外观检验标准3.3客户要求的相关文件四、缺陷定义4.1 点(含杂质):具有点的形状,测量时以其最大直径为其尺寸4.2 毛边:在塑料零件的边缘或结合线处线性凸起(通常为成型不良所致)4.3 银丝:在成型中形成的气体使塑料零件表面退色(通常为白色)。
这些气体大多为树脂内的湿气,某些树脂易吸收湿气,因此制造前应加入一道干燥工序4.4气泡:塑料内部的隔离区使其表面产生圆形的突起4.5变形:制造中内应力差异或冷却不良引起的塑料零件变形4.6顶白:成品被顶出模具所造成之泛白及变形﹐通常发生在顶出稍的另一端(母模面)4.7缺料:由于模具的损坏或其它原因﹐造成成品有射不饱和缺料情形.4.8断印:印刷中由于杂质或其它原因造成印刷字体中的白点等情况。
4.9漏印:印刷内容缺划或缺角或字体断印缺陷大于0.3mm,也被认为有漏印。
4.10色差:指实际部品颜色与承认样品颜色或色号比对超出允收值。
4.11同色点: 指颜色与部品颜色相接近的点;反之为异色点。
4.12流水纹:由于成形的原因﹐在浇口处留下的热溶塑料流动的条纹4.13熔接痕:由于两条或更多的熔融的塑料流汇聚,而形成在零件表面的线性痕迹4.14装配缝隙:除了设计时规定的缝隙外,由两部组件装配造成的缝隙4.15细碎划伤:无深度的表面擦伤或痕迹(通常为手工操作时造成)4.16硬划伤:硬物或锐器造成零件表面的深度线性伤痕(通常为手工操作时造成)4.17凹痕缩水:零件表面出现凹陷的痕迹或尺寸小于设计尺寸(通常为成型不良所致)4.18颜色分离:塑料生产中,流动区出现的条状或点状色痕(通常由于加入再生材料引起)4.19不可见:指瑕疵直径<0.03mm为不可见,LENS透明区除外(依每部品材料所订定之检测距离)4.20碰伤:产品表面或边缘遭硬物撞击而产生的痕迹4.21油斑:附着在对象表面的油性液体4.22漏喷:应喷漆之产品表面部份因异常原因而导致油漆没有喷到露出底材之现象4.23修边不良:产品边缘处因人工修边而产生缺口等不规则形状4.24毛屑:分布在喷漆件表面的线型杂质。
壳料类测试标准
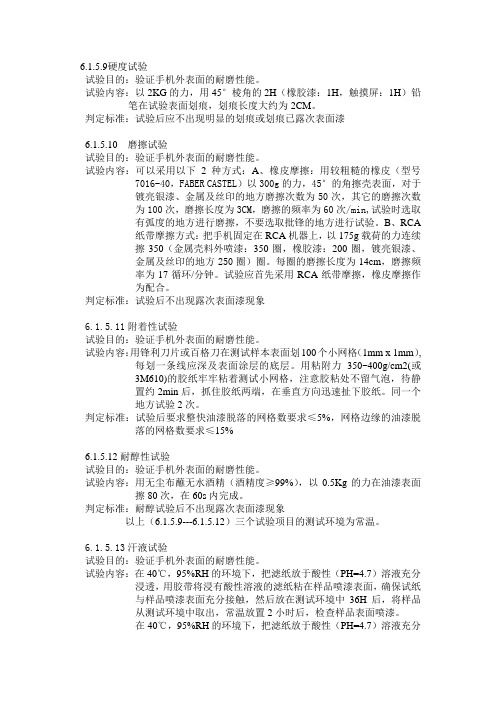
6.1.5.9硬度试验试验目的:验证手机外表面的耐磨性能。
试验内容:以2KG的力,用45°棱角的2H(橡胶漆:1H,触摸屏:1H)铅笔在试验表面划痕,划痕长度大约为2CM。
判定标准:试验后应不出现明显的划痕或划痕已露次表面漆6.1.5.10 磨擦试验试验目的:验证手机外表面的耐磨性能。
试验内容:可以采用以下2种方式:A、橡皮摩擦:用较粗糙的橡皮(型号7016-40,FABER CASTEL)以300g的力,45°的角擦壳表面,对于镀亮银漆、金属及丝印的地方磨擦次数为50次,其它的磨擦次数为100次,磨擦长度为3CM,磨擦的频率为60次/min,试验时选取有弧度的地方进行磨擦,不要选取批锋的地方进行试验。
B、RCA纸带摩擦方式:把手机固定在RCA机器上,以175g载荷的力连续擦350(金属壳料外喷漆:350圈,橡胶漆:200圈,镀亮银漆、金属及丝印的地方250圈)圈。
每圈的磨擦长度为14cm,磨擦频率为17循环/分钟。
试验应首先采用RCA纸带摩擦,橡皮摩擦作为配合。
判定标准:试验后不出现露次表面漆现象6.1.5.11附着性试验试验目的:验证手机外表面的耐磨性能。
试验内容:用锋利刀片或百格刀在测试样本表面划100个小网格(1mm x 1mm),每划一条线应深及表面涂层的底层。
用粘附力350~400g/cm2(或3M610)的胶纸牢牢粘着测试小网格,注意胶粘处不留气泡,待静置约2min后,抓住胶纸两端,在垂直方向迅速扯下胶纸。
同一个地方试验2次。
判定标准:试验后要求整快油漆脱落的网格数要求≤5%,网格边缘的油漆脱落的网格数要求≤15%6.1.5.12耐醇性试验试验目的:验证手机外表面的耐磨性能。
试验内容:用无尘布蘸无水酒精(酒精度≥99%),以0.5Kg的力在油漆表面擦80次,在60s内完成。
判定标准:耐醇试验后不出现露次表面漆现象以上(6.1.5.9---6.1.5.12)三个试验项目的测试环境为常温。
手机壳五金件检验规范标准

手机壳五金检验规一. 目的为规本公司生产的五金件产品检验作业,明确检验容和要求,有效管控材料与产品品质,确保 满足顾客和生产需要。
二. 围适用于公司通用五金件的检验。
(注:客户有特别要求的产品,按具体产品的检验指导书执行。
)三. 取样方案1.来料检验采用MIL-STD-iO5E 单次抽样,检查水平(IL )和接收质量(AQU 遵循如下规定:眼就可以感觉到色彩的变化了。
这种测试方法用于当顾客指定或接受某种颜色时,用以保证色彩一 致性的量度。
4.5毛边:由于机械冲压或切割后未处理好,导致加工件边缘或分型面处所产生的金属毛刺。
4.6划伤:由于在加工或包装、运输过程中防护不当导致产品表面出现的划痕、削伤。
4.7裁切不齐:由于产品在加工过程中定位或设备固定不当,导致产品边缘切割不齐。
4. 8变形:因加工设备调校不当或材料因应力而造成的产品平面形变。
4.9氧化生锈:因产品加工后未进行相应防锈处理或处理措施不当,而导致产品表面出现锈斑。
4. 10尺寸偏差:因加工设备的精度不够,导致产品尺寸偏差超过设计允许水平。
4. H''R 角”过大:产品因折弯或冲压设备精度不够,导致折弯处弧度过大。
4. 12表面凹痕:由于材料热处理不好或材料生锈,其部杂质导致金属表面形成的凹痕。
4. 13倒圆角不够:产品裁切边缘因切割或冲压原因产生的锐边未处理成圆弧状,易导致割手。
4. 14焊接疤痕:产品焊接后未经打磨刨光而残留的凸起疤痕。
4. 15色差:产品表面颜色与标准样品颜色有差异。
4. 16异色点:在产品表面出现颜色异于周围颜色的点。
4. 17破裂:因机加工损伤而造成产品的裂纹或细小开裂。
4. 18麻点:喷涂件表面上有附著的细小颗粒。
-DOC 资料.2.部生产过程首件检验、巡检及出货检验按每个产品具体的检查指导书执行。
四.定义A 面:指组装成整机后的正前面、上表面(在使用过程能直接看到的表面);B 面:指组装成整机后的侧面(需将视线偏转45° ~90°才能看到的四周边)。
手机壳体料检验标准

手机壳料检验规范1 适用范围本规定对手机外壳的测试项目、技术要求、试验方法、检验规则等要求做了相应的规定,本规定适合科健公司产品手机外壳的检验测试。
2 定义本规范采用下列定义:Weld line ——注塑成形时。
树脂空穴或中心周围不融合而形成扭曲的现象 Folw mark——模具内树脂流后以gate为中心的文线Sink mark——注塑成形时rib、boss 等部分的树脂冷却时产品表面出现凹进的现象Crazing ————固应力的柜裂现象Crack ————注塑成形时出现部分歪斜面或者表面龟裂的现象Deflection ——均匀的厚度中存在不均匀的厚度Brittleness ——成形产品时因机械强度比原来树脂所具有的机械强度弱而出现被破损的现象黑点————材料中混有异物而形成的瑕疵白花————成形时原材料的冲击或部件脱离时其它部位的干涉或部分应力增加而出现局部变白的现象异物质——产品表面所粘有的一些不必要的、有损外观的物质未成形——未满足试模成形条件,出现未填充而凝固的现象色像差——因原材料的差异、条件变动而引起的和样品有像异和错色气泡——表面产生的凸出现象变形——成形产品因各部位收缩率差异而形成的扭曲现象色稳不良——产品表面色泽不均匀状态剥离——成形品表面树脂呈层形,出现被拔出的现象原材料刮痕—原材料表面有刮痕,涂漆产生的细的刮纹3 测试部件a.前壳b.LCD 窗c.屏蔽盒d.后壳e.电池扣翻盖f.智能键壳4 测试方法4.1 前壳测试5 检验规则按照国标GB2828,正常抽样检验,检验水平:Ⅱ严重缺陷(MAJ):AQL=0.65轻微缺陷(MIN):AQL=1.5致命缺陷:Re:1 Ac:0尺寸S-3或指定抽样数量功能(如拉、扭力):3PCS 外观相关缺陷的管理基准以各类型的外观缺陷基准规范检验条件:30cm 距离,湿度60±2%,照明700Lux以上,正面(900 )检验条件是根据部件及制品的特性会有角度、湿度、距离等的不同检查者条件:矫正视力1.0以下,不允许有色盲,色弱者1、外观判断基准外观判断基准分三等级(A级、B级、C级)表面和三分类(轻缺陷、重缺陷、致命缺陷)缺陷。
手机壳件检验标准

2. 毛边:铁件或者塑胶件在成型時造成的粗糙尖锐边缘﹔3. 缺料﹕铁件或者塑胶件成型不当或产品结构问题造成表面产品某些部位未射饱;4. 间隙:組裝后两个不同部件在裝配时两接触面不能完全吻合而出现的裂缝.8. 顶白:因模具顶针問題造成塑胶制品顶针处外部出现白色圆弧。
5. 缩水﹕塑胶成型时﹐因外表面已冷却﹐但內部仍旧温热﹐冷却时表面內缩所产生的凹陷.6. 刮伤﹕塑胶件因与其他物品相摩擦造成的条狀或片狀痕迹.7. 汽泡:塑胶成形过程中包含空气或水汽的圆球、在透明件中尤为明显。
五﹑表面的定义四﹑产品缺陷定义1. 变形:物体失去应具备之形狀﹔三.检验条件位置: 产品置放于检验者正前面, 垂直于检验者。
目视時間: 10秒钟内确认缺陷。
目视距离:肉眼与被测物距离30cm至45cm. 目视角度:与被测物成30度至45度角范围内 工作场所灯光: 60W,距离检测者50cm.MSTIQC-07-008第1页共4页1.0文 件 编 号页 次版 次C面:指产品在使用过程中很少见或看不见的面(手机背面内部和电池门内)。
A面:指产品在使用过程中,直接在近处观看且暴露的主要面(正常观察时手机的前面)。
一﹑作业內容品质检验人員抽样计划依照MIL-STD-105E, 正常检验(Normal Inspection), Level II, 单次抽样。
如客戶有特殊要求﹐以客戶提供之抽样水准抽样。
品质检验允收水准(AQL): MA=0.4,MI=1.0。
抽样计划采用『分批检查, 分批验退』的方式。
二﹑缺点分类致命缺点 (Critical Defect, CR) 指由经验和判断表明产品对人体有害的产品缺陷。
严重缺点 (Major Defect, MAJ) 指影响产品正常使用功能,降低产品可靠性或严重影响产品外观的缺陷。
轻微缺点 (Minor Defect, MIN) 偏离限定标准,但不影响产品正常使用功能或外观缺陷不太明显的缺陷。
B面:指产品在使用过程中,不直接观看但暴露的次要面(手机的上下左右侧面和背面)。
- 1、下载文档前请自行甄别文档内容的完整性,平台不提供额外的编辑、内容补充、找答案等附加服务。
- 2、"仅部分预览"的文档,不可在线预览部分如存在完整性等问题,可反馈申请退款(可完整预览的文档不适用该条件!)。
- 3、如文档侵犯您的权益,请联系客服反馈,我们会尽快为您处理(人工客服工作时间:9:00-18:30)。
手机壳料检验标准
目的
本规范明确了本司手机壳料的质量检验标准,确保产品质量达到客户要求。
适用范围
本规范适用于我司手机所有来料壳料的质量检验和控制。
3.职责
品管管理员有责任依此标准培训和监督IQC的外观检测手段,并根据标准核实不良品,处理壳料不良问题
4程序:
4.1 定义:所有壳料包括(塑胶,五金)等结构件来料必须有样品及样品规格书,IQC根据样品及规格书进行检验。
4.2.1 检验条件
4.2.1 距离:人眼与被测物表面的距离为250mm-300mm。
4.2.2 时间:每件检查总时间不超过3s
4.2.3 位置:检视面与桌面成45°,上下左右转动15°,前后翻转。
4.2.4照明:100W冷白荧光灯,光源距零件表面500-
550mm,照度约
500-550Lux.
4.2.5温度23+/-3,湿度30%-70%
4.2.2检验标准:
1.采用MIL-STD-105E II表,正常检验、单次抽样计划,
AQL订定为CRI(0), MAJ (0.4)及MIN (1.0)
5..定义。
5.1.缺陷定义
严重缺陷:(CRITICAL)
不符合国家安全标准认定,对人身安全造成伤害或存在安全隐患的缺陷。
如机械材料之锐利批峰
主要缺陷:((MAJOR)
重要的质量特性和功能特性不符合部件规格。
不能达到使用效果,或严重影响外观收货标准及其它可能引起投诉的缺陷。
次要缺陷:(MINOR)
不影响使用功能,一般机械材料和金属材料的外观问题,不影响装配的轻微尺寸偏差。
5.2测量面定义:
A测量面:暴露在外,在使用过程中总能被客户看见的主要表面(如:前壳的正面,后壳的正面,。
这些表面不允许有可能导致一般客户不购买产品的外观缺陷。
B测量面:暴露在外在使用过程中常常被客户看见的部分(如:前壳后壳的侧面,这些表面允许有轻微不良,但是不致引起挑剔客户
不购买产品
C测量面:在使用过程中很少被客户注意到的表面部分(如:电池盖或背盖)
这些表面的外观缺陷应合理,而且不至于给客户觉得
该产品质量不过关。
D测量面:在使用过程中决不会被客户看见的表面部分(如:面、底壳内面)
5.3点缺陷定义
异色点:壳料表面出现的颜色异于周围的点。
同色点:壳料表面出现的颜色同于周围的点。
5.4塑胶件喷涂表面不良缺陷定义
颗粒:在喷漆件表面上附着的细小颗粒。
积漆:在喷漆件表面上出现局部的油漆堆积现象。
裂纹:漆层表面有裂开现象。
桔纹:在漆层表面出现桔子皮状皱痕。
透底:在漆层表面局部油漆层过薄而露出基体颜色的现象。
剥落:在漆层表面出现涂层脱落现象。
鱼眼:由于溶剂挥发速度不适而造成在喷漆件表面有凹陷或小坑。
划痕:在漆层表面有线状划伤现象
纤毛屑:油漆本身带有的或油漆未干时落在油漆表面而形成的纤维状毛屑。
色差:漆层颜色呈现与标准色板或客户样板的颜色差异。
5.5注塑件不良缺陷定义
气泡:由于原料未充分干燥,造成成成型后产品内部有缩孔。
缩水:塑件表面局部由于填充不足或注塑压力保持不够而形成的凹坑。
熔接线:塑料熔体在型腔中流动时,遇到阻碍物(型芯等物体)时,熔体在绕过阻碍物后不能很好的融合,而在塑料件的表面形成
一条明显的线。
顶白:由于塑料件的包紧力,顶杆区域受到顶出力所产生的白印或凸起。
裂纹:塑胶件由于环境老化而造成的在产品表面上有裂。
油渍:在塑料件表面残留的油污。
翘曲及变形:塑料件成型时由于受力不均或应力而造成塑料件的形变
毛边:由于注塑工艺或模具原因,造成在塑料件的边缘分型面处所产生的废边。
有感划伤:硬物磨擦而造成产品表面有浓度的划痕(且摸上去有明显的感觉)。
无感划伤:没有深度(且摸上去无感觉)的划痕。
凹凸点:由于模具的损坏等原因造成塑料件表面上出现的高低不平。
斑点:在塑料件表面和内部的细微粒和杂质
烧焦:在塑胶件表面出现的局部塑胶焦化发黑或发黄。
泽差异:漆层表面光泽度超出标准样品的光泽差异。
5.6.电镀件外观不良定义:
漏镀:偏出规范的非覆镀区域。
电镀毛边:电镀时在高电流密度镀层的过高堆积,过高的电流产生了粗糙(毛边)
气孔?气泡:在表层下,表层中或外表面(完整或破裂的)之可见气穴/泡(气体或流动物)
刮伤:表面内或表面上可视的摩损,凹痕或划痕。
斑点:局部的脏污。
色差:与标准样品有颜色上的差异。
光泽度差异:与规定的光泽度存在总体或局部的差异。
5.7.装配组件不良缺陷定义
段差:上下部件之间本应在同一平面或曲面之内光滑连接,但
由于生产制造过程中的误差使其产生前或后不同面。
间隙:部件之间由于尺寸公差、变形等原因造成配合不紧而产生的缝
隙。
变形:由于装配尺寸误差,毛边等原因而造成装配组合件变形现象。
5.8.密集缺陷:
两点缺陷.线缺陷.区块缺陷中心距离,<=15mm,则为密集缺陷,本标准中规定可接收缺陷但不允许密集。
6.检验内容
6.11.点缺陷判定标准:(D:直径 W:宽度 L:长度)
6.2.注塑件外观判定标准:
6.3.喷油件外观判定标准
6.4装配件判定标准:
6.5)电镀件外观判定标准:(D:直径 N:数量 W:宽度 L:长度 DS:距离)
6.6五金件外观判定标准
对不做要求的缺陷,如有很多,形成整体,影响到外观,拒收。
7.装配质量
前后壳电池盖等壳料与手机其它物料配合时要配合良好,前壳与后壳缝隙<=0.2mm,底壳与电池盖缝隙小于0.15mm,段差小于0.2mm..
8特性测试
此我司组装厂不作要求但壳料供应商需作并出具出货检验报告,项目为(百格测试,酒精测试,盐雾测试,高低温测试等详情请参考我司可靠性测试规范。
9包装方面
1来料物料编码,型号应与BOM一致。
2来数不允许有少装混装等不良现象
3来料必须附带出货检验报告。
4来料必须保证到我司工厂这边包装及物料未受损伤,否则我司有权拒收。