三角形内螺纹车削加工
普通内三角螺纹车削过程经验探讨

普通内三角螺纹车削过程经验探讨导言内三角螺纹是制造行业中常见的一种螺纹结构形式,主要应用于螺母和螺栓的对接连接中。
而内三角螺纹的车削加工是制造过程中的重要环节之一,其加工精度和效率直接关系到产品的质量和生产成本。
在日常工作中,我们经常会遇到内三角螺纹车削过程中的一些问题,本文基于实际工作经验,对内三角螺纹车削过程进行探讨,总结经验和技巧,希望能够对相关行业的从业人员提供一些参考和帮助。
一、内三角螺纹车削工艺流程内三角螺纹车削是利用车床进行加工的一种工艺,主要包括粗车、精车和螺纹车削三个环节。
在进行内三角螺纹车削之前,首先需要进行工件的装夹和刀具的选择设置。
接下来,我们将分别对粗车、精车和螺纹车削三个环节进行详细介绍。
1. 粗车在进行内三角螺纹车削时,首先需要进行粗车环节。
粗车的目的是将工件的直径加工到要求的尺寸,为后续的精车和螺纹车削做好准备。
在粗车过程中,要特别注意切削深度和进给速度的控制,以及刀具的选择和刀具刃部与工件的接触情况。
还需要确保车床的稳定性和刀具的稳定性,避免因为振动或者抖动导致的加工质量不稳定。
二、内三角螺纹车削经验探讨在实际工作中,我们发现内三角螺纹车削过程中会遇到一些常见问题,如切削过程中的振动、刀具的磨损、加工精度的不稳定等。
下面我们将结合实际经验,对这些问题进行分析探讨,并提出相应的解决方法。
1. 振动问题振动是内三角螺纹车削过程中常见的问题,它会导致切削质量的不稳定,影响加工精度和表面质量。
解决振动问题的关键在于对车床和刀具的加工参数进行合理设置,确保工件和刀具的稳定性。
还需要注意检查车床的机械结构是否存在松动或者变形,及时进行维护和更换,避免因为机床失稳导致的振动问题。
2. 刀具磨损刀具磨损是内三角螺纹车削过程中的另一个常见问题,它会导致切削质量的下降,加工效率的降低。
解决刀具磨损问题的关键在于选择合适的刀具材料和刀具型号,并严格按照生产工艺要求进行操作。
还需要注意定期对刀具进行检查和更换,及时修复和更换磨损严重的刀具,避免因为刀具磨损导致的加工质量下降。
普通内三角螺纹车削过程经验探讨
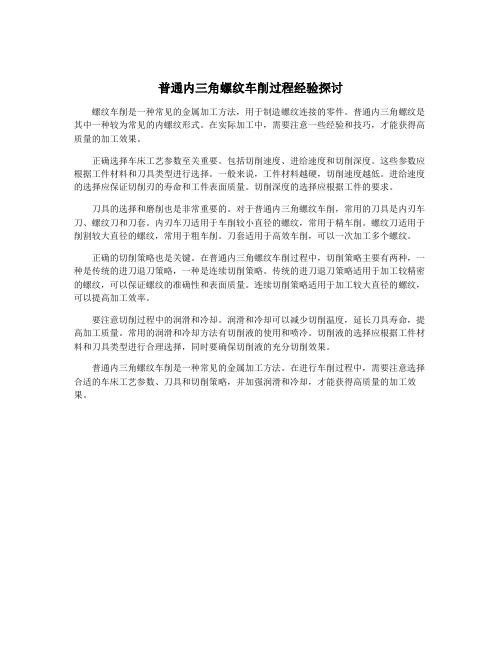
普通内三角螺纹车削过程经验探讨
螺纹车削是一种常见的金属加工方法,用于制造螺纹连接的零件。
普通内三角螺纹是其中一种较为常见的内螺纹形式。
在实际加工中,需要注意一些经验和技巧,才能获得高质量的加工效果。
正确选择车床工艺参数至关重要。
包括切削速度、进给速度和切削深度。
这些参数应根据工件材料和刀具类型进行选择。
一般来说,工件材料越硬,切削速度越低。
进给速度的选择应保证切削刃的寿命和工件表面质量。
切削深度的选择应根据工件的要求。
刀具的选择和磨削也是非常重要的。
对于普通内三角螺纹车削,常用的刀具是内刃车刀、螺纹刀和刀套。
内刃车刀适用于车削较小直径的螺纹,常用于精车削。
螺纹刀适用于削割较大直径的螺纹,常用于粗车削。
刀套适用于高效车削,可以一次加工多个螺纹。
正确的切削策略也是关键。
在普通内三角螺纹车削过程中,切削策略主要有两种,一种是传统的进刀退刀策略,一种是连续切削策略。
传统的进刀退刀策略适用于加工较精密的螺纹,可以保证螺纹的准确性和表面质量。
连续切削策略适用于加工较大直径的螺纹,可以提高加工效率。
要注意切削过程中的润滑和冷却。
润滑和冷却可以减少切削温度,延长刀具寿命,提高加工质量。
常用的润滑和冷却方法有切削液的使用和喷冷。
切削液的选择应根据工件材料和刀具类型进行合理选择,同时要确保切削液的充分切削效果。
普通内三角螺纹车削是一种常见的金属加工方法。
在进行车削过程中,需要注意选择合适的车床工艺参数、刀具和切削策略,并加强润滑和冷却,才能获得高质量的加工效果。
普通内三角螺纹车削过程经验探讨

普通内三角螺纹车削过程经验探讨内三角螺纹车削是机械加工中常见的一种加工方法,具有精度高、加工效率高等优点。
然而,在实际工作中,要想达到理想的加工效果,需要掌握一定的经验和技巧。
本文将从车刀的选择、车削参数的调整以及车削中应对常见问题等方面进行探讨。
一、车刀的选择:内三角螺纹车削需要使用专门的车刀(内三角螺纹车刀),其刀身侧面采用了特殊的形状,使其能够在内螺纹的壁面上做出精确的切削,同时也避免了刀身与工件碰撞。
在选择车刀时,需要根据工件材料、螺纹尺寸、切削深度等因素进行综合考虑。
一般情况下,螺纹直径越小,切削深度越浅,则需要选择尽量小的车刀,以保证精度和平稳性。
二、车削参数的调整:在进行内三角螺纹车削时,需要调整的车削参数包括:车削速度、切削深度、进给量等。
要想获得高精度的螺纹加工品质,需要根据具体情况合理调整这些参数。
1. 车削速度车削速度是指车刀在切削时在工件表面运动的平均速度。
车削速度的大小直接影响切削力、精度以及车刀的寿命。
在内三角螺纹车削中,车削速度一般较低,一般在200~500m/min左右。
当螺纹直径较小时,车削速度应适当提高,以增加切削速度,提高加工效率。
2. 切削深度切削深度是指车刀每次与工件表面接触时,切削刀口深度。
内三角螺纹车削时,切削深度一般不宜过大,一般在0.2~0.5mm之间。
若切削深度过大,则容易造成振动和剪切变形,影响切削精度和表面质量;若切削深度过小,则加工效率低,不能达到理想加工效果。
3. 进给量进给量是指车刀切削时运动的步进距离,在内三角螺纹车削中,进给量一般根据螺纹型号和材料进行调整。
一般情况下,进给量越小,加工表面越光滑,进给量越大则加工效率越高。
在车削过程中,应根据具体情况适当调整进给量,以保证加工精度和效率的平衡。
三、车削中应对常见问题的应对在内三角螺纹车削过程中,有时会出现一些常见问题,如振动、毛刺等,应及时进行应对,以保证加工质量。
1. 振动振动是内三角螺纹车削中常见的问题,主要原因是车刀切削过程中,经常发生振动,影响切削质量和工件表面质量。
普通内三角螺纹车削过程经验探讨

普通内三角螺纹车削过程经验探讨普通内三角螺纹车削是一种常用的车削过程,广泛应用于机械制造、汽车制造、航空航天等行业。
本文将对普通内三角螺纹车削过程进行经验探讨。
普通内三角螺纹车削过程中,为了获得理想的加工质量和效率,需要注意以下几个方面的因素。
合理选择刀具及切削参数。
对于普通内三角螺纹车削,一般选用的刀具是硬质合金螺纹刀具。
刀具的选择需要根据被加工的材料及工件规格来确定。
在切削参数的选择上,要根据材料的硬度和强度、切削深度、工件的材料和形状等进行综合考虑。
要注意合理选择切削速度、进给量和主轴转速等参数,以保证刀具的寿命和加工效率。
合理选择机床及夹具。
机床的精度和稳定性对于普通内三角螺纹车削来说至关重要。
一般来说,应选择高精度的数控车床,并确保机床的刚性和稳定性。
夹具的选择也需要根据工件的形状和尺寸来确定,以保证工件的位置和稳定性。
合理安排车削顺序。
在进行普通内三角螺纹车削时,要根据工件的形状和要求,合理安排车削的顺序。
一般来说,先进行轮廓车削,然后进行螺旋车削。
在车削过程中,要确保钻孔、中心孔等加工工序的准确性和精度,以保证后续车削过程的顺利进行。
注意刀具的保养和润滑。
刀具的保养对于普通内三角螺纹车削的加工质量和效率至关重要。
使用过程中要注意定期检查刀具的磨损情况,及时更换或修复磨损过大的刀具。
要定期对刀具进行润滑,以减少切削时的摩擦和磨损,延长刀具的使用寿命。
普通内三角螺纹车削是一种常见的车削过程,要想获得良好的加工质量和效率,需要注意刀具及切削参数的选择、机床及夹具的选择、车削顺序的安排以及刀具的保养和润滑等方面的因素。
通过不断的实践和经验积累,可以逐步提高普通内三角螺纹车削的加工质量和效率。
普通内三角螺纹车削过程经验探讨

普通内三角螺纹车削过程经验探讨普通内三角螺纹车削是一种常见的工艺,用于加工内螺纹零件。
在实际操作中,需要注意一些经验问题,以提高加工质量和效率。
选择合适的刀具是非常重要的。
刀具的选择应根据加工材料和螺纹尺寸来确定。
一般情况下,使用硬质合金刀具能够得到较好的切削效果。
同时还要注意刀具的磨损情况,及时更换磨损严重的刀具,以确保加工质量。
要合理设置机床的切削参数。
包括主轴转速、进给速度和切割深度等。
主轴转速应根据加工材料的硬度和刀具的直径来选择,进给速度则应根据切削深度和刀具的切削力来确定。
在车削过程中,要注意保持稳定的切削参数,避免剧烈波动导致加工质量下降。
正确选择刀具路径和切割方式也是很重要的。
根据实际情况选择初始切割点和刀具路径,可以提高加工效率和质量。
要注意切削速度和进给速度的匹配,以避免过大或过小的切屑产生。
在实际操作中,还要注意切削润滑和冷却。
适当的润滑和冷却能够减少切削温度,延长刀具寿命。
可以使用润滑剂或切削液进行冷却和润滑,确保切削过程的稳定性。
操作人员的经验和技能也是影响加工效果的重要因素。
操作人员需要熟悉机床的使用和刀具的安装,能够准确地控制切削参数,及时调整和修正。
在实际操作中,要密切观察切削情况,及时发现和解决问题,确保加工质量。
需要注意的是,普通内三角螺纹车削过程中存在一定的风险。
操作人员应遵守相关安全规定,佩戴好安全防护装备,确保人身安全。
普通内三角螺纹车削是一项常见但技术要求较高的加工工艺。
在实际操作中,需要注意刀具选择、切削参数设置、刀具路径和切割方式选择、切削润滑和冷却等经验问题。
操作人员的经验和技能也是影响加工质量的重要因素。
只有充分掌握这些经验和技巧,才能够更好地完成内螺纹零件的加工任务。
数控车床加工工艺编程-车削内三角螺纹
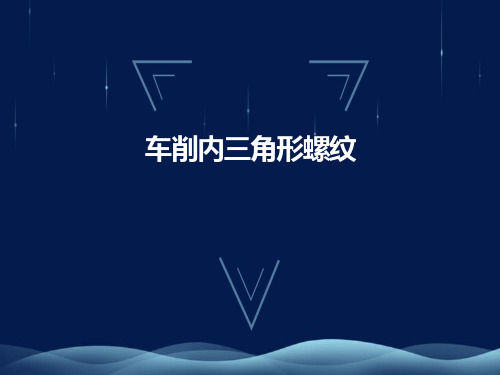
二、内螺纹车刀几何角度及安装
粗车刀
精车刀
内螺纹车刀的刃磨方法与外螺纹车刀基本相同,但是刃磨刀尖角时,要特别注意它的平分线必须与刀杆垂直,否则车内螺纹时会出现刀柄碰伤工件内孔的现象。
1.螺纹车刀的几何角度
二、内螺纹车刀几何角度及安装
外螺纹车刀的对刀方法
车刀
牙底
牙顶
四、车削内三角形螺纹注意事项
1、车内螺纹时,应将小滑板适当调紧些,以防车削过程中小滑板产生位移造成螺纹乱牙现象。 2、车内螺纹时,退刀要及时、准确。退刀过早螺纹未车完,在加工盲孔时退刀过迟车刀容易碰撞孔底。 3、精车时必须保持车刀锋利,否则容易产生‘让刀’,致使螺纹产生锥形误差,一旦产生锥形误差,不能盲目增加背吃刀量,而是应让螺纹车刀在原切削深度上反复进行无进给切削来消除误差。 4、工件在回转中不能用棉纱去擦内孔,更不允许用手指去摸内螺纹表面,以免发生人身事故。 5、在加工过程中,中途换刀必须重新对刀,以防造成乱牙。
车削内三角形螺纹
一、内、外三角形螺纹加工方法对比
车外螺纹
车内螺纹
工件
卡盘
车刀Βιβλιοθήκη 车三角形内螺纹的方法与车三角形外螺纹的方法基本相同,但进刀与退刀的方向正好相反。车内三角形螺纹时,尤其是直径较小的内螺纹,由于刀柄细长、刚度低、切屑不易排出、切削液不易注入及车削时不便于观察等原因,造成车内三角形螺纹比车外三角形螺纹要有难度。内三角形螺纹车刀的尺寸大小受到螺纹孔径尺寸限制,一般内螺纹车刀的刀头径向长度应比孔径小3~5mm,刀柄太细车削时容易产生振动,刀柄太粗退刀时会碰伤内螺纹牙顶,甚至不能车削。
内螺纹车刀的对刀方法
1.螺纹车刀的安装
二、内螺纹车刀几何角度及安装
6.2 车削三角形内螺纹
编程加工实例
O0002;(G32) T0101 M03 S600 G00 X24.5 Z3 G32 Z-22 F2 G00 X23
Z3 X25 G32 Z-22 F2 G00 X23 Z3 X25.5 G32 Z-22 F2 G00 X23 Z3 X25.8 G32 Z-22 F2 G00 X23
每次进给的背吃刀量用螺纹深度减精加工背吃刀量所得的差按递减规律分配。
O1004 M03 S600; T0101; G00 X30.0 Z3.0; X23.0; G32 Z-23.0 F1.5; G00 X30.0; Z3.0; X22.5; G32 Z-23.0 F1.5; G00 X30.0; Z3.0;
如果螺纹塞规通端正好可 旋入工件,而止端旋不进, 说明加工的螺纹符合精度要 求,反之工件不合格。
任务小结
一.内螺纹加工指令G32与G92的使用方法。 二.内螺纹实际加工中应注意的问题:
(1)控制螺纹车刀装刀的中心高,刀具转正,刀具伸出刀架长度满足螺纹加工的有效长度; (2)检查程序编写的正确性,螺纹底孔要加工正确; (3)螺纹车刀退刀时注意先选择X向退刀,再选择Z向退刀。
Z3 X26 G32 Z-22 F2 G00 X23
Z3 X26.05 G32 Z-22 F2 G00 X23 Z3 X26.1 G32 Z-22 F2 G00 X23 Z3 G00 Z100 X100 M30
三角形内螺纹的检测
检测三角形内螺纹一般采 用综合测量法。检测时,采 用螺纹塞规测量,如图 1212 所示。
课后作业
尝试编制下图所示轴类零件的加工程序。
Thanks
感谢您的聆听
普通三角形内螺纹孔径的确定
车普通三角形内螺纹时,内螺纹孔径车多大与工件材料性质、螺距
普通内三角螺纹车削过程经验探讨
普通内三角螺纹车削过程经验探讨1. 引言1.1 研究背景内三角螺纹是一种常见的螺纹结构,广泛应用于机械制造领域。
而内三角螺纹的加工过程中,车削是一种常见的加工方法。
对于普通内三角螺纹的车削过程,了解其基本过程、影响因素以及优化方法是非常重要的。
研究普通内三角螺纹车削的背景在于,加工精度要求不断提高的背景下,如何提高内三角螺纹车削的加工效率和质量成为了一个亟待解决的问题。
随着机械制造领域的发展,对于内三角螺纹的加工要求也在不断增加,因此有必要对内三角螺纹车削进行更深入的研究和探讨。
通过深入研究内三角螺纹车削的基本过程、影响因素以及优化方法,可以为提高内三角螺纹车削的加工效率和质量提供理论支持和技术指导。
研究普通内三角螺纹车削的过程经验具有非常重要的意义和价值。
1.2 研究目的研究目的是通过对普通内三角螺纹车削过程的深入探讨,分析影响内三角螺纹车削质量和效率的各种因素,找出优化车削过程的方法,并设计实验验证其效果。
通过研究,旨在提高内三角螺纹车削的加工精度和效率,降低成本,增强产品的竞争力。
探讨机床设备和刀具在内三角螺纹车削中的选择对加工效果的影响,为工程实践提供技术支持和参考依据。
通过本研究的开展,旨在总结内三角螺纹车削的关键技术要点,为工程领域的相关研究和生产实践提供指导和参考,推动内三角螺纹车削技术的进步和发展。
1.3 研究意义普通内三角螺纹车削是机械加工领域中常见的一种加工方法,具有广泛的应用领域。
研究普通内三角螺纹车削的意义在于提高加工效率,优化加工质量,降低生产成本,满足市场需求。
通过对内三角螺纹车削过程的深入研究,可以探讨和总结出影响加工精度和效率的因素,并提出优化加工过程的方法和技术。
这将有助于提高企业的竞争力,推动工业制造的发展。
研究内三角螺纹车削还可以促进机床设备和刀具技术的进步,推动整个加工领域的发展。
对普通内三角螺纹车削过程进行深入探讨具有重要的理论和实践意义,对于推动科技进步和产业发展具有积极作用。
普通内三角螺纹车削过程经验探讨
普通内三角螺纹车削过程经验探讨内三角螺纹车削是一种常见的车削工艺,广泛应用于机械加工领域。
在进行内三角螺纹车削的过程中,经验技巧的掌握对提高加工效率和保证加工质量起着至关重要的作用。
本文将围绕普通内三角螺纹车削过程中的经验探讨展开。
一、刃具的选择与磨制在进行内三角螺纹车削时,刃具的选择和磨制对加工结果影响很大。
一般情况下,内三角螺纹车削采用带刃固定刀片。
合适的刃片选择,可以保证加工的精度和表面质量。
刃片的刀尖角度和前角角度要与车削材料相匹配。
刃片的磨制需要掌握良好的技巧,保证刃片具有良好的刃口质量。
二、合理的切削参数切削参数的选择对内三角螺纹车削过程至关重要。
合理的切削速度、进给速度和切削深度可以保证车削过程的安全性和加工效率。
切削速度过高可能导致刀具磨损过快,切削速度过低可能导致切削力过大。
进给速度过高容易引起刀具振动,进给速度过低可能导致加工效率低下。
切削深度过大可能导致刀具磨损加剧,切削深度过小可能导致加工效率低下。
需要根据具体情况选择合适的切削参数。
三、保持稳定的切削过程内三角螺纹车削过程中需要保持稳定的切削过程,避免刀具振动和工件错位等问题。
在进行车削时,要注意切削盘的装夹,确保工件和刀具之间的配合良好。
在切削过程中,要保持稳定的切削力和切削速度,避免加工中出现大的冲击力。
在遇到刀具刃口磨损时要及时更换刀具,保证加工结果的稳定性。
四、合理的切削顺序和路径切削顺序和路径的选择对内三角螺纹车削的效果有着重要的影响。
一般情况下,应先进行粗车,再进行精车。
粗车时应选择较大的切削深度和进给速度,以快速去除多余的材料。
精车时应选择较小的切削深度和进给速度,以保证加工的精度和表面质量。
切削路径应从外到内,从轴向到径向,避免螺纹刀片出现跳动和刀具破碎的情况。
五、加工润滑与冷却内三角螺纹车削过程中,加工润滑和冷却至关重要。
加工润滑可以降低加工温度,减少切削力和磨损,提高加工质量。
常用的加工润滑方式有干削和液体润滑。
三角形内螺纹车削加工
5. 1切削过程基本规律与应用
• 2)刀具磨损的原因 • 刀具磨损原因很复杂,它与工件材料、刀具材料和切削条件等因素密
切相关,刀具磨损的主要原因有如下几个。 • (1)磨料磨损。 • 由于在工件材料中含有硬质点(如碳化物、氮化物和氧化物),在铸、
锻工件表面存在着硬夹杂物,在切屑和工件表面赫附着硬的积屑瘤残 片,这些硬质点的作用使刀具表面刻划出沟痕,致使刀具表面磨损。 磨料磨损又称机械磨损。 • (2)赫结磨损。 • 切削塑性材料时,在很大压力和强烈摩擦作用下,切屑,工件与前、 后刀面间的吸附膜被挤破,形成新的表面紧密接触,因而发生赫结现 象。刀具表面局部强度较低的微粒被切屑和工件带走,这样形成的磨 损称为赫结磨损。赫结磨损一般在中等偏低的切削速度下较严重。赫 结磨损又称冷焊磨损。
上一页 下一页 返回
5. 1切削过程基本规律与应用
• 3)影响切削力的主要因素 • 凡影响切削过程变形和摩擦的因素均影响切削力,其中主要包括工件
材料、切削用量和刀具几何参数等三个方面。 • (1)工件材料。 • 工件材料是通过材料的剪切屈服强度、塑性变形程度与刀具间的摩擦
条件影响切削力的。 • 一般来说,材料的强度和硬度愈高,切削力愈大。这是因为强度、硬
上一页 下一页 返回
5. 1切削过程基本规律与应用
• (2)切削用量。 • 当vc. , .f和ap增加时,由于切削变形和摩擦所消耗的功增大,故切削
温度升高。其中切削速度vc影响最大, vc增加一倍,切削温度约增加 30%;进给量f的影响次之,f增加一倍,切削温度约增加18%;背吃刀 量。l影响最小,ap增加一倍,切削温度约增加7%。上述影响规律的 原因是, vc增加使摩擦生热增多;f增加因切削变形增加较少,故热量 增加不多,此外,使刀一屑接触面积增大,改善了散热条件; ap增加 使切削宽度增加,显著增大了热量的传散面积。
- 1、下载文档前请自行甄别文档内容的完整性,平台不提供额外的编辑、内容补充、找答案等附加服务。
- 2、"仅部分预览"的文档,不可在线预览部分如存在完整性等问题,可反馈申请退款(可完整预览的文档不适用该条件!)。
- 3、如文档侵犯您的权益,请联系客服反馈,我们会尽快为您处理(人工客服工作时间:9:00-18:30)。
5. 1切削过程基本规律与应用
• (3)刀具几何参数。 • 在刀具几何参数中,刀具的前角γo和主偏角Kr.对切削力的影响较明
显。当加工钢时, γo增大,切削变形明显减小,切削力减小的较多。 Kr适当增大,使切削厚度久增加,单位面积上的切削力减小。在切削 力不变的情况下,主偏角大小将影响背向力和进给力的分配比例,当 Kr增大,背向力Fp减小,进给力凡增加;当Kr = 900时,背向力凡=0, 对防止车细长轴类零件时减小弯曲变形和振动十分有利。 • 2.切削热与切削温度 • 切削热和切削温度是切削过程中产生的另一个物理现象,它对刀具的 寿命、工件的加工精度和表面质量影响较大。
上一页 下一页 返回
5. 1切削过程基本规律与应用
• 1)切削热的产生和传散 • 在切削加工中,切削变形与摩擦所消耗的能量几乎全部转换为热能,
即切削热。切削热通过切屑、刀具、工件和周围介质(空气或切削液) 向外传散,同时使切削区域的温度升高。切削区域的平均温度称为切 削温度。 • 影响热传散的主要因素是工件和刀具材料的热导率、加工方式和周 围介质的状况。热量传散的比例与切削速度有关,切削速度增加时, 由摩擦生成的热量增多,但切屑带走的热量也增加,在刀具中热量减 少,在工件中热量更少。所以高速切削时,切屑温度很高,刀具和工 件温度较低,这有利于切削加工顺利进行。
上一页 下一页 返回
5. 1切削过程基本规律与应用
• 3)影响切削力的主要因素 • 凡影响切削过程变形和摩擦的因素均影响切削力,其中主要包括工件
材料、切削用量和刀具几何参数等三个方面。 • (1)工件材料。 • 工件材料是通过材料的剪切屈服强度、塑性变形程度与刀具间的摩擦
条件影响切削力的。 • 一般来说,材料的强度和硬度愈高,切削力愈大。这是因为强度、硬
度高的材料,切削时产生的抗力大,虽然它们的变形系数若相对较小, 但总体来看,切削力还是随材料强度、硬度的增大而增大。在强度、 硬度相近的材料中,塑性、韧性大的,或加工硬化严重的,切削力大。 例如不锈钢1 Cr18 Ni9Ti与正火处理的45钢强度和硬度基本相同,但 不锈钢的塑性、韧性较大,其切削力比正火45钢约高25 %。
上一页 下一页 返回
5. 1切削过程基本规律与应用
• 加工铸铁等脆性材料时,切削层的塑性变ห้องสมุดไป่ตู้很小,加工硬化小,形成 崩碎切屑,与前刀面的接触面积小,摩擦力小,故切削力就比加工钢 小。
• (2)切削用量。 • 切削用量三要素对切削力均有一定的影响,但影响程度不同,其中
背吃刀量ap和进给量f影响较明显。若f不变,当ap增加一倍时,切削 厚度ac不变,切削宽度aw增加一倍,刀具上的负荷也增加一倍,即切 削力增加约一倍;若ap不变,当f增加一倍时,切削宽度aw保持不变, 切削厚度ac曾加约一倍,在刀具刃圆半径的作用下,切削力只增加 68%一86%可见在同样切削面积下,采用大的f较采用大的ap省力和 节能。切削速度vc对切削力的影响不大,当vc > 500 m/min,切削塑 性材料时,vc增大,切削温度增高,使材料强度、硬度降低,剪切角 增大,变形系数减小,使得切削力减小。
工作任务5三角形内螺纹车削加工
• 5. 1切削过程基本规律与应用 • 5. 2三角形内螺纹车削加工 • 5. 3机械加工质量
5. 1切削过程基本规律与应用
• 5.1.1切削过程基本规律
• 1.切削力与切削功率 • 切削力是被加工材料抵抗刀具切入所产生的阻力。它是影响工艺系统
强度、刚度和加工工件质量的重要因素,是设计机床、刀具和夹具, 计算切削动力消耗的主要依据。 • 1)切削力的来源、合力与分力 • 刀具在切削工件时,由于切屑与工件内部产生弹、塑性变形抗力,切 屑与工件对刀具产生摩擦阻力,形成了作用在刀具上的合力F,如图 5. 2所示。切削时合力F作用在接近切削刃空间某方向,由于大小与 方向都不易确定,因此,为便于测量、计算和反映实际作用的需要, 常将合力F分解为三个分力。
上一页 下一页 返回
5. 1切削过程基本规律与应用
• 2)影响切削温度的主要因素 • 切削温度的高低主要取决于:切削加工过程中产生热量的多少和向外
传散的快慢。影响热量产生和传散的主要因素有:工件材料、切削用 量、刀具几何参数和切削液等。 • (1)工件材料。 • 工件材料主要是通过硬度、强度和导热系数影响切削温度的。 • 加工低碳钢,材料的强度和硬度低,导热系数大,故产生的切削温度 低;加工高碳钢,材料的强度和硬度高,导热系数小,故产生的切削 温度高。例如,加工合金钢产生的切削温度比加工45钢高30%;不锈 钢的导热系数是45钢的1 /3,故切削时产生的切削温度高于45钢40 %; 加工脆性金属材料产生的变形和摩擦均较小,故切削时产生的切削温 度比45钢低25 %。
上一页 下一页 返回
5. 1切削过程基本规律与应用
• (2)切削用量。 • 当vc. , .f和ap增加时,由于切削变形和摩擦所消耗的功增大,故切削
温度升高。其中切削速度vc影响最大, vc增加一倍,切削温度约增加 30%;进给量f的影响次之,f增加一倍,切削温度约增加18%;背吃刀 量。l影响最小,ap增加一倍,切削温度约增加7%。上述影响规律的 原因是, vc增加使摩擦生热增多;f增加因切削变形增加较少,故热量 增加不多,此外,使刀一屑接触面积增大,改善了散热条件; ap增加 使切削宽度增加,显著增大了热量的传散面积。
下一页 返回
5. 1切削过程基本规律与应用
• 切削力Fc(主切削力Fz)—在主运动方向上的分力; • 背向力Fp(切深抗力Fy )—在垂直于工作平面上的分力; • 进给力Ff(进给抗力Fx)—在进给运动方向上的分力。 • 背向力Fp与进给力Ff的合力是推力FD,推力FD作用在切削层平面上且
垂直于主切削刃。 • 合力F、推力FD与各分力之间关系:
上一页 下一页 返回
5. 1切削过程基本规律与应用
• 2)切削功率 • 在切削过程中消耗的功率叫切削功率尸门单位为kW,它是Fc, Fp, Ff
在切削过程中单位时间内所消耗的功的总和。一般来说, Ff相对Fe 所消耗的功率很小,可以略去不计,于是: • • 式中v—主运动的切削速度。 • 计算切削功率Pc是为了核算加工成本和计算能量消耗,并在设计机 床时根据它来选择机床电机功率。机床电机的功率PE可按下式计算: • • 式中ηc—机床传动效率,一般取ηc =0. 75一0. 85