MRP类型及MRP运行参数(优选.)
MRP培训教材基础知识
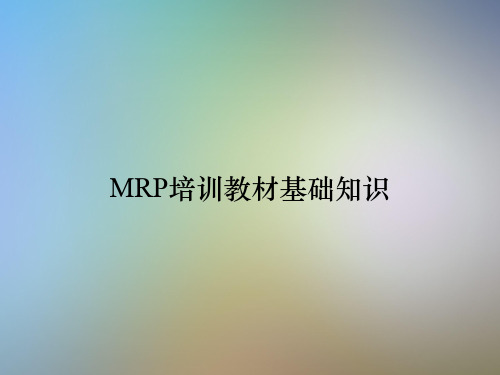
– 1、预测报表(Z1MR207-A)查询MRP数据设置情况 – 2、查询物料库存及在途情况(MD04) – 3、问题点讨论
20-апр-20
MRP Overview
MRP名词解释
• 常规材料(VM):是指经常性使用的材料,是由系统自动计 算材料的再订点和安全库存
• 关键材料(VB):是指必须在仓库备有最小库存,如果没有缺 料,生产就会发生问题,是手动计算材料的再订点和安全库存。 – 如特殊轴承,采购周期很长,不常用但不能缺货
2、点击“后台执行 ”
20-апр-20
1、输入相应的条件
26
SAP MRP Overview
后台执行
3.2、通过输出控制器(事务代码:SP02)来查看或者导出所需的数据 即可实现快速运行
双击
20-апр-20
27
SAP MRP Overview
3.2、通过输出控制器(事务代码:SP02)来查看清单
MRP主数据操作(ND)
备注:MRP2、MRP3、MRP4、预测等视图与S1 材料设置相同
20-апр-20
14
SAP MRP Overview
单项运行MRP ( MD03)
1: 输入料号和 工厂代码
2: 选定显示结果
20-апр-20
15
SAP MRP Overview
多项运行MRP ( MD01)
24
SAP MRP Overview
MRP呆滞料管控
2.2、MRP呆滞料管控——MRP呆滞料作业表单(HTT//:COCONUT/文件 管理/三阶文件/公用表单)
20-апр-20
25
3.1、当遇到S系A统P运M行R速P度O慢v时e可rv以ie通w过SAP“后台执行”,来实现快后速台查执询行功
主生产计划的功能以及其相关MRP类型参数

主生产计划的功能以及其相关MRP类型参数2.MRP运行方式3.MRP运行的先决条件4.客制化MRP参数的优先级别5.MRP的运算逻辑及低阶码的用途6.SAP PP MD02界面参数说明7.mrp操纵参数及未清期间8. SAP PP MRP视图中重要栏位的意义及功能作用主生产计划的功能与其有关MRP类型参数主生产计划实际相当于一个计划调节器,用主生产计划能够合理的调节企业资源配置与需求的矛盾,避免由于需求不稳固造成的产品未能按期交货,产品积压,资源浪费、超负荷运转等现象,提高企业对用户的服务水平。
通常MPS的计划对象为最终产品或者者关键重要部件,有的时候候也会对原材料做计划,比如造船行业。
原料品种比较少而产品品种比较多。
在SAP系统,与MPS有关的MRP类型有:M0 MPS,固定类型 -0-M1 MPS,固定方式 -1-M2 MPS,固定方式 -2-M3 MPS,固定方式 -3-M4 MPS,固定方式 -4-到后台去看这些参数的配置,发现只有确定的类型(Firming Tpyes)一个值不一样0 计划结果未被确认1 自动确定与订购建议被重新计划2 不含订购建议的自动确定3 手工确定与订单建议再计划4 手工确定不含订单建议为了弄清晰上面每个确定类型的含义,需要看下面的图:在时区1、2,某时刻到计划时界这个区间内计划订单是否被确定,新的需求的是否创建与创建的落点在那个区间,由这个确定类型参数确定,下面是它的全面解释。
tpye0 :需求不自动确定,新的需求在需求日期创建,不可能自动确定(计划时界内外都一样)。
tpye1 :需求自动确定,新的需求假如日期在计划时界内,那么在计划时界结束的位置创建需求。
type2 :需求自动确定,计划时界内的新需求不被考虑,缺料。
tpye3 :需求不自动确定,新的需求假如日期在计划时界内,那么在计划时界结束的位置创建需求。
tpye4 :需求不自动确定,计划世界内的新需求不被考虑,缺料。
基本MRP

2016/3/31
物料需求计划系统(MRP)
1. 引 言
1.2 MRP的发展经历
定货点法 MRP 闭环MRP MRP II
MRP / 基本MRP / 时段MRP
是针对定货点法的局限性提出的一种库存定货计划 主要的改进包括: ● 将物料需求区分为独立需求和非独立需求并分别加以处理 ● 对库存状态数据引入了时间分段的概念 ● 以确定的主生产计划为依据
预测量 合同量 毛需求 毛需求 计划接收量 8 预计库存量 净需求 净需求 计划产出量 计划投入量 可供销售量
5 12 12 10 6
5 8 8 8 7 10
5
5 2 5 13 2 10
销 售 计 划
5 7 7
5 6 6
5 5 5
5 13 13 12 13 20
5 5 5 7
5 5 12 3 10
5 2 5 7
2016/3/31
物料需求计划系统(MRP)
2. 基本MRP — 2.1
原理 MRP的目标与功能
目标:确定每项物料在每个时区内的需求量,以 便为正确进行生产库存管理提供必要的信息。
功能:
–
– – – –
减少库存投资 提高应变生产变化的灵敏度 可对每项物料提供未来的库存状态信息 面向生产作业的库存控制 强调需求、库存储备和订货作业的时间性
2016/3/31
物料需求计划系统(MRP)
1. 引 言
1.2 MRP的发展经历——定货点法
定货点法 MRP 闭环MRP MRP II
订货点法
一种按过去的经验预测未来的物料需求的方法
含义: 遵循“库存补充”的原则, 依靠对库存补充周期内的需求量预测, 并要求保留一定的安全库存储备,以应付需求的波动。 基本公式: 定货点=单位时区的需求量×定货提前期+安全库存量
MRP——精选推荐

物料需求计划(MRP)的编制物料需求计划(Material Requirements Planning,MRP)是ERP管理层的计划,MRP计划的运行是由ERP决策层的主生产计划(MPS)驱动的。
1MRP的概念1.1物料需求计划物料需求计划(MRP)是ERP的核心,是一种物料管理和生产方式,它建立在MPS的基础上。
根据产品的BOM、工艺路线、批量政策和提前期等技术和管理特征,生成原材料、毛坯、外购件的采购作业计划和零部件生产、装配计划,从而达到有效管理和控制企业物料流动的微观计划。
1.2物料需求计划(MRP)的作用MRP的作用就是利用有关书录信息,实现各计划时间段(计划周期)的采购计划(采购订单)和制造计划(生产订单)。
MRP主要解决以下5个问题:1)要生产(含采购或制造)什么?(这些数据从MPS获得)2)要用到什么?(这些数据根据BOM表展开获得。
)3)已经有了什么(包括已分配量和以订货量)?(这些数据根据物料库存信息获得。
)4)还缺什么?(这些数据根据MRP计算结果获得)。
5)何时安排(包括何时开始采购制造、何时完成采购制造)?(这些数据依据物料的提前期获得)。
1.3物料需求计划(MRP)在ERP中的层次关系对于ERP共有5个层次的计划中,物料需求计划处于第四层,属于管理层计划,它与其它计划间的关系详如下图所示。
注:BOM:分解各种物料的工具。
物料编码:识别、使用的依据。
工艺路线和工序:安排生产作业顺序的基础。
工作中心:把MRP与能力需求计划关联起来。
制造日历:有助于明确安排时间。
2.1 MRP的输入数据项主生产计划主生产计划说明一个企业在一个时期内(计划展望期内)计划生产的产品名称、数量和日期。
主生产计划作为MRP的输入数据项、主要解决“生产(含采购和制造)什么”,亦即“生产(含采购和制造)多少”问题。
这里的主生产计划的计划(或排产)对象是指企业的最种产品。
主生产计划是MRP最重要和最基本的数据,开始编制物料需求计划时,必须首先得到一个有效的主生产计划。
运行MRP工厂参数配置
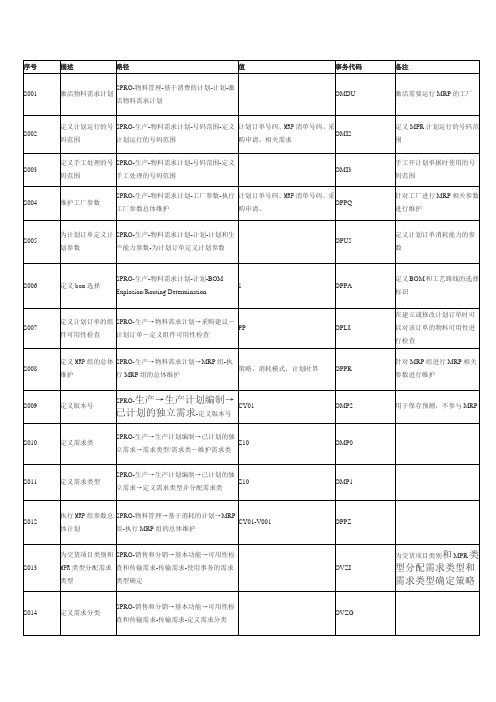
定义手工处理的号码范围
SPRO-生产-物料需求计划-号码范围-定义手工处理的号码范围
OMI3
手工开计划单据时使用的号码范围
S004
维护工厂参数
SPRO-生产-物料需求计划-工厂参数-执行工厂参数总体维护
计划订单号码、MRP清单号码、采购申请、
OPPQ
针对工厂进行MRP相关参数进行维护
S005
为计划订单定义计划参数
SPRO-生产-物料需求计划-计划-计划和生产能力参数-为计划订单定义计划参数
OPU5
定义计划订单消耗能力的参数
S006
定义bom选择
SPRO-生产-物料需求计划-计划-BOM Explosion/Routing Determination
1
OPPA
定义BOM和工艺路线的选择标识
序号
描述
路径
值
事务代码
备注
S001
激活物料需求计划
SPRO-物料管理-基于消费的计划-计划-激活物料需求计划
OMDU义计划运行的号码范围
SPRO-生产-物料需求计划-号码范围-定义计划运行的号码范围
计划订单号码、MRP清单号码、采购申请、相关需求
OMI2
定义MPR计划运行的号码范围
S007
定义计划订单的组件可用性检查
SPRO-生产→物料需求计划→采购建议-计划订单-定义组件可用性检查
PP
OPL8
在建立或修改计划订单时可以对该订单的物料可用性进行检查
S008
定义MRP组的总体维护
SPRO-生产→物料需求计划→MRP组-执行MRP组的总体维护
策略,消耗模式,计划时界
OPPR
针对MRP组进行MRP相关参数进行维护
MRP参数详细说明

MRP参数详细说明MRP(Material Requirements Planning)即物料需求计划,是一个用于确保企业生产和供应链运作平稳高效的计划方法。
MRP系统通过识别和计划所需的原材料、零部件和成品,以最低的成本和最高的效率满足生产和客户需求。
下面是MRP参数的详细说明。
1.生产订单参数:-订单数量:确定生产订单的数量,根据市场需求和销售预测进行调整。
-订单日期:指定生产订单的开始日期,以确保及时满足需求和安排生产资源。
2.计划时间参数:-计划时间框架:指定MRP计算所需的时间范围,通常根据企业的生产和物料供应周期而定。
-计划间隔:指定MRP计算的时间间隔,通常以天为单位,以确定物料需求和计划的更新频率。
3.物料参数:-物料编号:唯一标识物料的编码,用于识别和跟踪物料的需求和库存情况。
-物料描述:提供物料的详细说明,包括名称、规格、用途等信息。
-单位:指定物料的计量单位,如个、箱、千克等。
-安全库存:确定所需的最低库存水平,以应对供应链中的不确定性和突发情况。
4.计划参数:-提前期:指定在其需求产生之前所需要的时间,以便及时采购和安排生产。
-采购时间:确定预计采购物料到达的时间,以便安排生产和避免库存短缺。
-生产时间:确定预计完成生产的时间,以便满足客户需求和安排物料采购。
5.库存参数:-初始库存:指定MRP计算开始时的库存水平,以确保准确计算物料需求和采购计划。
-库存减少:确定库存减少的原因,如销售订单、工艺损耗、报废等。
6.供应商参数:-供应商编号:唯一标识供应商的编码,用于管理和识别不同的供应商。
-最小订购量:确定供应商要求的最小订单或采购量,以确保物料供应的经济性和可行性。
-交货时间:指定供应商预计交货的时间,以便安排生产和满足客户需求。
7.MRP运算参数:-引导时间:确定订单或需求在系统中引导到下级供应链环节的时间,以确保及时的物料供应。
-批量大小:确定批量制造或采购的物料数量,以满足成本和效率需求。
MRP参数详细说明
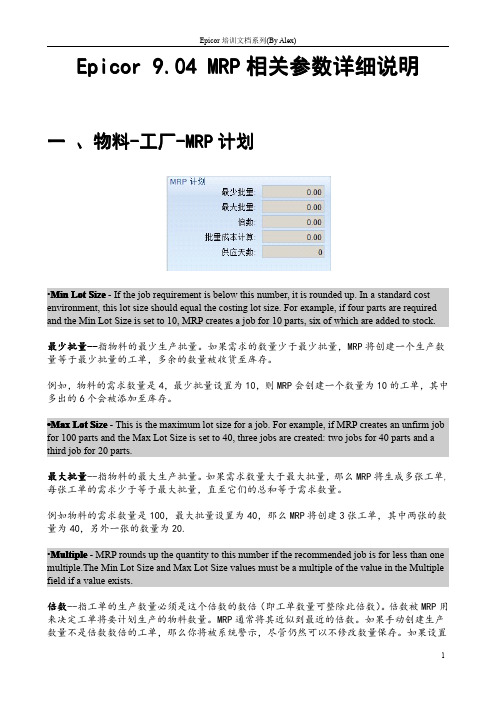
Epicor9.04MRP相关参数详细说明-MRP计划工厂-MRP、物料--工厂一、物料•Min Lot Size-If the job requirement is below this number,it is rounded up.In a standard cost environment,this lot size should equal the costing lot size.For example,if four parts are required and the Min Lot Size is set to10,MRP creates a job for10parts,six of which are added to stock.--指物料的最少生产批量。
如果需求的数量少于最少批量,MRP将创建一个生产数最少批量最少批量--量等于最少批量的工单,多余的数量被收货至库存。
例如,物料的需求数量是4,最少批量设置为10,则MRP会创建一个数量为10的工单,其中多出的6个会被添加至库存。
•Max Lot Size-This is the maximum lot size for a job.For example,if MRP creates an unfirm job for100parts and the Max Lot Size is set to40,three jobs are created:two jobs for40parts and a third job for20parts.最大批量--指物料的最大生产批量。
如果需求数量大于最大批量,那么MRP将生成多张工单,每张工单的需求少于等于最大批量,直至它们的总和等于需求数量。
例如物料的需求数量是100,最大批量设置为40,那么MRP将创建3张工单,其中两张的数量为40,另外一张的数量为20.•Multiple-MRP rounds up the quantity to this number if the recommended job is for less than one multiple.The Min Lot Size and Max Lot Size values must be a multiple of the value in the Multiple field if a value exists.倍数--指工单的生产数量必须是这个倍数的数倍(即工单数量可整除此倍数)。
MRP物料需求计划简介

三、企业生产类型
(三)混合型生产(Make to order& stock) (或者Configure to order)
该类商品和服务属于一些基本采购,需要指出较多的资金,但给 公司带来的风险并不高,包装物,紧固件,涂料等都属于此产品 瓶颈型:代表的是高风险,低成本的项目或服务,我们称为“瓶 颈型”, 该类产品成本较低,但进入潜在市场有困难,因而导致风险较高, 犹豫供应商数量少,到货时间长货无法交付货物等原因可能造成 采购额超支。 战略型:代表的是高风险,高成本的项目和服务。
它是通过BOM(bill of material 物料清单)文件来描述各零件 在产品中的层次关系和数量。它的重要功能之一,是根据产品设 计文件、工艺文件、物料文件和生产提前期等资料自动生成BOM 表。
MRP的基本思想,按反工艺顺序来确定零部件、毛坯到原材料的 需要数量和需要时间,
二、物料需求计划(MRP)
对于各个阶段产生的不良设立仓码(供应商来料不良,制程不良, 产程品不良,过保质期限的物料等分类管理库存)由责任部门定 期处理。
四、目前工作的改善建议
(三)制造BOM 的建立完善
现有BOM 格式的规范化,标准化。首先是BOM 的层次清晰,其 次是BOM 的使用量准确,原则上应该跟库存单位保持一致性。 最后是在某个范围内进行BOM 共享。使用人员严格遵守公司的 保密制度。
(2)库存周转率=产品销售成本/库存平均占用金额 (3)呆滞库存金额比率=呆滞库存金额/总库存金额 (4)EOL库存金额比率=EOL库存金额/总库存金额 (5)不良品在库金额比率=不良品在库金额/总库存金额
- 1、下载文档前请自行甄别文档内容的完整性,平台不提供额外的编辑、内容补充、找答案等附加服务。
- 2、"仅部分预览"的文档,不可在线预览部分如存在完整性等问题,可反馈申请退款(可完整预览的文档不适用该条件!)。
- 3、如文档侵犯您的权益,请联系客服反馈,我们会尽快为您处理(人工客服工作时间:9:00-18:30)。
最新文件---------------- 仅供参考--------------------已改成-----------word文本 --------------------- 方便更改
PP中的MRP类型:
前台设置是在 MRP1 视图中:
PP模块常用的MRP类型为主生产计划(M0)、物料需求计划(PD)或者无计划(ND). 具体的后台配置在物料需求计划中:
具体路径为:生产-物料需求计划-主数据-检查MRP类型
MRP类型的差距主要体现在控制参数中确定的类型(Firming types)上。
确定的类型主要反应两个问题:
1.已存在的计划时界(计划时界内)已什么形式体现(确认OR 不确认?)
2.有新的计划订单进入计划时界内怎么处理?
(确认:指实际中该订单是要被用来生产的,不能更改。
系统中,MRP元素数据中有* .在正常情况下,*根据计划时界中的内容确定,保护计划不受到MRP、MPS的破坏,跑MRP时,即不会更改和删除该订单。
)
确定的类型中的具体含义:
0.计划结果未被确认:
计划世界内的计划订单不是确认的,可以删除、增加或减少,若存在一个新订单,该在什么时候就在什么时候,类似于无计划时界概念。
1.自动确认和订购建议被重新计划:
计划时界中的计划订单是确认的,若有新订单,新订单产生的计划订单不在计划时界内,在计划时界后,即新单不影响计划时界里面的内容。
2.不含订购建议的自动确定:
计划时界中的计划订单是确认的,若有新单,新单不产生计划订单,表现方式是缺料的方式。
3.手工确定和订单建议再计划:
计划时界内的计划订单不会确认,若有新单,新单产生计划订单,计划订单在计划时界后面。
4.手工确定不含订单建议:
计划时界内的计划订单不会确认,若有新单,新单不产生计划订单,以缺料形式表现。
运行MRP时的控制参数:
处理代码:
CH N : 上一次跑MRP到现在,有变更的物料就会跑MRP(一般用)。
PL P : 在计划区间中有变化的物料会跑MRP.
3.NEUPL G: 全跑。
一般建议一个新的工厂,系统第一次上线事,一定要用NEUPL G 对全工厂跑一次MRP,作用为:
1)对所有的物料建立计划文件
2)对全部的物料跑MRP .
计划文件的用途:仅提供依据,哪些物料需要跑MRP,哪些物料不需要跑MRP,或者怎样跑的文件。
激活计划文件的两种方式:
1.建立计划文件(后台配置),路径为生产-物料需求计划-计划文件条目-激活MRP和建
立计划相关文件(OMDU)。
不建议采用。
2.运行MRP (NEUPL G ),全工厂运行。
最新文件---------------- 仅供参考--------------------已改成-----------word文本 --------------------- 方便更改。