精度控制在船舶分段建造中的应用
{生产工艺技术}船体结构装配总组船台分段定位精度管理应用工艺

{生产工艺技术}船体结构装配总组船台分段定位精度管理应用工艺船体结构装配总组是造船工艺中的重要环节,其质量与精度的控制对于船体结构的强度、刚度和平整度具有非常重要的影响。
船台分段定位精度管理应用工艺是船体结构装配总组的一项关键技术,下面将对其进行详细讨论。
船台分段定位精度管理应用工艺主要包括如下几个方面:首先是船台分段位置的准确标定。
船台作为船体结构装配的基础,其位置的准确标定对于后续的船体结构组装具有重要意义。
在船台分段制作过程中,需采取严格的工艺控制措施,确保船台分段位置的准确标定,包括使用高精度的测量设备和工具进行测量,以及制作标志和导线进行标定。
其次是船台分段定位的调整和校验。
船台分段在制造和装配过程中,经常需要进行调整和校验,以保证其位置的准确性。
调整和校验时,可以使用调整垫块、调整螺栓等方式进行,同时通过测量工具进行位置的验证,确保船台分段定位的精确度。
再次是船台分段的装配和固定。
船台分段装配时需要根据设计要求进行逐段拼装,确保各个船台分段的位置匹配和连接。
在装配过程中,应采用适当的装配夹具和工具,确保船台分段的定位精度。
同时,在装配完成后,需要进行固定,防止装配过程中位置的变动,可以采用焊接、螺栓固定等方式。
最后是船台分段定位精度的检验和测量。
在船体结构装配总组完成后,需要进行船台分段定位精度的检验和测量,以确保其满足设计要求和船舶建造规范。
检验和测量可以采用三坐标测量仪、激光测量仪等高精度测量设备进行,在实际操作中要注意测量点的选取和测量误差的控制,确保测量结果的准确性。
综上所述,船台分段定位精度管理应用工艺是船体结构装配总组的关键技术之一,通过准确标定、调整和校验、装配和固定以及检验和测量等环节的控制,可以确保船台分段位置的准确性,保证船体结构装配总组的质量和精度。
船体结构的装配质量与精度的提高,将为船舶的性能和可靠性提供坚实的保障。
船舶建造分段搭载精度的控制和优化

船舶建造分段搭载精度的控制和优化摘要:本文主要从船舶建造中分段搭载的精度控制实际发展趋势、船体分段三维测量及相关分析技术入手,对船舶建造中分段搭载的精度控制予以综合分析,进而对船舶建造中分段搭载的精度控制优化措施,进行了深度的分析及研究。
从而能够通过对船舶建造中分段搭载实际精度控制的合理优化,切实地保证船舶建造中分段搭载实际精度的有效性控制,为我国船舶建造业的持续性发展奠定基础。
关键词:船舶建造;分段搭载;精度;控制;优化;前言:船舶搭载(Ship carrying),是船舶建造的核心步骤,更是至关重要的环节。
船舶搭载,其自身具有着建筑时间短、劳动力强度低、建筑成本低、便于集中管理、提高狭小空间的质量等功能优势。
在一定程度上,伴随着船舶搭载相关技术日新月异的发展,可谓开启了我国船舶建造业发展的新空间,让我国船舶建造业可以稳步开创新的里程碑。
那么,基于在船舶搭载过程中,最为关键的就是分段搭载实际精度的控制。
为了能够更好的保证船舶搭载的效率及质量,就必须对船舶建造中分段搭载实际精度的控制予以深度分析,制定出较为科学的优化措施,以提升船舶建造中分段搭载实际精度控制的效果,促进我国船舶建造业的进一步发展。
1、精度控制发展趋势的分析在船舶建造中分段搭载的精度控制,是我国最具科学性的造船技术之一。
通过将其利用在船舶建造中,不仅能够将造船的周期予以缩短、将造船的成本有效降低,还能够极大的减轻劳动力的强度性,提高船舶建造的效率及质量。
那么,针对于我国船舶建造中分段搭载实际精度的控制技术,该项技术目前发展的趋势主要表现在以下几点:其一,船舶相关零件制造类设备逐渐向着自动化、数控化方向发展着,船舶相关零件制造的精度也相对愈加提升,对予船舶精度的控制也起着一定的正面作用。
例如,控水火弯性板机、数控的切割机、数控的卷板机等相继出现,让船舶相关零件制造的实际精度逐渐提升,能够适应于对精度要求相对较高的船舶建造;其二,自部分的加放精度性补偿量,逐渐向着全船舶建造均实现精度的补偿量来替代余量的方向不断发展着。
船舶建造分段搭载精度的控制和优化 王旭光

船舶建造分段搭载精度的控制和优化王旭光摘要:船舶建造分段搭载的传统测量方法效率低下,占用吊机时间较长;需要在现场对余量进行切割,需要对分段进行复位作业;很多分段需要进行二次定位,影响船台周期;传统的测量手段很难对船体分段在船体成型过程中的变化进行有效统计,为反变形的施放及无余量生产提供数据支持。
传统造船业采用的船舶建造测量手段比较落后,明显不适应现代造船对时间、精度的要求。
关键词:分段搭载;精度;控制前言:考虑到散货船舷侧分段总组搭载过程中产生的错位会对后续分段搭载产生一系列精度影响,分析产生问题的原因,采取统一测量标准,应用精度分析软件ECO-G2对测量数据进行分析,通过模拟搭载,大大提高了散货轮舷侧分段总组和搭载时的精度,能够明显缩短定位时间和提高吊装效率,缩短了船坞周期。
1船体分段建造的步骤船体分段建造的信息经过精心设计,分为4个步骤:①建造船体分段的小组件,板材的拼接、型材的切割或者弯制、T型面板的拼装和焊接。
②分段的建造,由小组件和T型材的组合拼接,形成一定的开放式分段。
③船体总段的建造:由前面完成的小组立、小分段拼装起来,骨架外面的外板挂装,形成相对独立的封闭总段。
④总段上的附属结构,部分小件的安装(桅杆,舱口,门,扶手栏杆等)。
2舷侧分段常见精度问题及影响2.1首尾带线型的舷侧分段错位问题1)外板线型错位。
2)肋骨前后错位。
3)小隔舱底脚肋板错位。
4)端面不同步。
此问题的产生,导致外板线型不光顺,现场定位耗时过长,不但影响吊车的使用效率,而且影响后续分段搭载定位。
2.2对小甲板的影响左右舷侧分段端面同步出现问题时,小甲板吊装时左右甲板面产生错位,还造成落脚与槽型舱壁的错位。
现象:508与408落脚前后错位70~100mm。
原因:508甲板错位是408整体直线度不好,中间在尾70mm,66/67N在前15mm。
累积造成错位。
对策:408组立阶段控制直线度,垂直度。
搭载控制精度,减少累积误差。
探讨船体分段建造的精度管理与控制措施
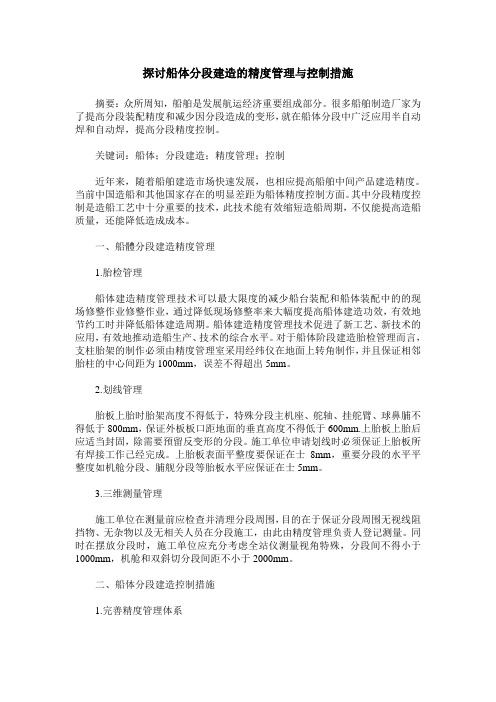
探讨船体分段建造的精度管理与控制措施摘要:众所周知,船舶是发展航运经济重要组成部分。
很多船舶制造厂家为了提高分段装配精度和减少因分段造成的变形,就在船体分段中广泛应用半自动焊和自动焊,提高分段精度控制。
关键词:船体;分段建造;精度管理;控制近年来,随着船舶建造市场快速发展,也相应提高船舶中间产品建造精度。
当前中国造船和其他国家存在的明显差距为船体精度控制方面。
其中分段精度控制是造船工艺中十分重要的技术,此技术能有效缩短造船周期,不仅能提高造船质量,还能降低造成成本。
一、船體分段建造精度管理1.胎检管理船体建造精度管理技术可以最大限度的减少船台装配和船体装配中的的现场修整作业修整作业,通过降低现场修整率来大幅度提高船体建造功效,有效地节约工时并降低船体建造周期。
船体建造精度管理技术促进了新工艺、新技术的应用,有效地推动造船生产、技术的综合水平。
对于船体阶段建造胎检管理而言,支柱胎架的制作必须由精度管理室采用经纬仪在地面上转角制作,并且保证相邻胎柱的中心间距为1000mm,误差不得超出5mm。
2.划线管理胎板上胎时胎架高度不得低于,特殊分段主机座、舵轴、挂舵臂、球鼻脯不得低于800mm,保证外板板口距地面的垂直高度不得低于600mm.上胎板上胎后应适当封固,除需要預留反变形的分段。
施工单位申请划线时必须保证上胎板所有焊接工作己经完成。
上胎板表面平整度要保证在士8mm,重要分段的水平平整度如机舱分段、脯舰分段等胎板水平应保证在士5mm。
3.三维测量管理施工单位在测量前应检查并清理分段周围,目的在于保证分段周围无视线阻挡物、无杂物以及无相关人员在分段施工,由此由精度管理负责人登记测量。
同时在摆放分段时,施工单位应充分考虑全站仪测量视角特殊,分段间不得小于1000mm,机舱和双斜切分段间距不小于2000mm。
二、船体分段建造控制措施1.完善精度管理体系船舶制造企业应在造船过程中编制《分段评级管理方案》、《分段精度管理及奖惩细则》、《流水线分段精度管理》、《内外场划线管理规定》等,同时编制《分段精度作业指导书》中明确规定:“精度管理安全生产规范”、“常见问题分析”、“仪器使用和保养规范”、“划线和完成检测管理及处罚规定”等。
船体分段建造的精度控制方法探究

船体分段建造的精度控制方法探究摘要:在船舶建造的过程当中,为了能够提高船体分段建造的精度,从而给船舶建造工程开展奠定基础,本文在探究船舶建造特点的同时,对全体生产设计质量现状以及精度控制方法进行了深入探讨。
关键词:船体工程;分段建造;精度控制引言在船体分段建造过程精度控制作为非常关键的一项内容,有效的控制方法可以提高船体建造的质量。
因此对精度控制方法进行全面分析,明确相关的控制要点所在,对推进各项工作开展有着积极作用。
1船舶建造的特点船舶建造过程非常复杂,有着系统性要求,必须加强整个建造过程的监督与管理,才能保证船舶的质量合格,满足航行的需要。
在船舶建造的过程中,由于规模比较大,所以要进行分段建造施工,主要是从钢材预处理、数控切割、加工等方面进行,每个工序都要全面的。
监督管控达到质量标准要求,在分段成型之后进行最后的精度测量。
船体分段建造的过程中,结合吊车能力、船舶结构等合理的进行分段,明确加工艺流程。
因为船舶结构内部非常的复杂,有些部件需要进行热处理、冷加工、焊接等,所以容易造成结构尺寸的偏差,影响船舶建造精度。
2船体生产设计质量现状船体生产设计的质量对于整个生产效果存在直接的影响,也会关系到船舶建造的进度。
因此,船体设计的环节提高设计水平,满足当前的船舶制造加工的需要。
因为船舶设计需要多个专业和部门共同进行,一份图纸需要多个部门和专业共同签字确认,比如船体分段工作图,需要提供结构图、装配图、工艺图、舾装托盘表等,这些图纸要分段在车间进行生产,还要进行整体的组装,所以各个单位需要加强每个部分的设计管控,保证总体设计水平合格,不会给现场的建造生产带来任何影响。
但是目前在船体生产设计环节,质量控制管控不到位,有些部分的设计方案不能达到生产的要求,进而造成严重的质量隐患和问题3精度控制重要意义经过对目前我国的造船企业实际情况调查发现,很多企业都非常重视船体建造过程中精度控制,这些企业将船体分段建造精度控制为主要的目标,采取精度控制技术,选择合适的建造工艺,实现各个分段结构的质量监督管控。
船体分段建造现场精度控制工艺分析
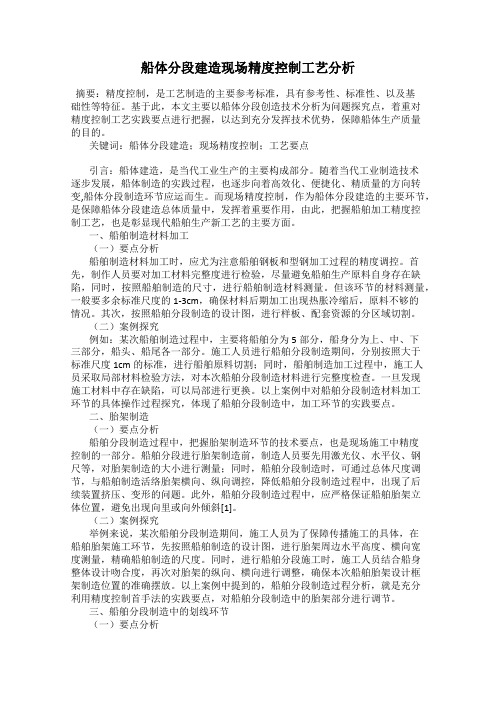
船体分段建造现场精度控制工艺分析摘要:精度控制,是工艺制造的主要参考标准,具有参考性、标准性、以及基础性等特征。
基于此,本文主要以船体分段创造技术分析为问题探究点,着重对精度控制工艺实践要点进行把握,以达到充分发挥技术优势,保障船体生产质量的目的。
关键词:船体分段建造;现场精度控制;工艺要点引言:船体建造,是当代工业生产的主要构成部分。
随着当代工业制造技术逐步发展,船体制造的实践过程,也逐步向着高效化、便捷化、精质量的方向转变,船体分段制造环节应运而生。
而现场精度控制,作为船体分段建造的主要环节,是保障船体分段建造总体质量中,发挥着重要作用,由此,把握船舶加工精度控制工艺,也是彰显现代船舶生产新工艺的主要方面。
一、船舶制造材料加工(一)要点分析船舶制造材料加工时,应尤为注意船舶钢板和型钢加工过程的精度调控。
首先,制作人员要对加工材料完整度进行检验,尽量避免船舶生产原料自身存在缺陷,同时,按照船舶制造的尺寸,进行船舶制造材料测量。
但该环节的材料测量,一般要多余标准尺度的1-3cm,确保材料后期加工出现热胀冷缩后,原料不够的情况。
其次,按照船舶分段制造的设计图,进行样板、配套资源的分区域切割。
(二)案例探究例如:某次船舶制造过程中,主要将船舶分为5部分,船身分为上、中、下三部分,船头、船尾各一部分。
施工人员进行船舶分段制造期间,分别按照大于标准尺度1cm的标准,进行船舶原料切割;同时,船舶制造加工过程中,施工人员采取局部材料检验方法,对本次船舶分段制造材料进行完整度检查。
一旦发现施工材料中存在缺陷,可以局部进行更换。
以上案例中对船舶分段制造材料加工环节的具体操作过程探究,体现了船舶分段制造中,加工环节的实践要点。
二、胎架制造(一)要点分析船舶分段制造过程中,把握胎架制造环节的技术要点,也是现场施工中精度控制的一部分。
船舶分段进行胎架制造前,制造人员要先用激光仪、水平仪、钢尺等,对胎架制造的大小进行测量;同时,船舶分段制造时,可通过总体尺度调节,与船舶制造活络胎架横向、纵向调控,降低船舶分段制造过程中,出现了后续装置挤压、变形的问题。
船舶建造分段搭载精度的控制和优化

船舶建造分段搭载精度的控制和优化摘要:船舶建造分段搭载的传统测量方法效率低下,占用吊机时间较长;需要在现场对余量进行切割,需要对分段进行复位作业;很多分段需要进行二次定位,影响船台周期;传统的测量手段很难对船体分段在船体成型过程中的变化进行有效统计,为反变形的施放及无余量生产提供数据支持。
传统造船业采用的船舶建造测量手段比较落后,明显不适应现代造船对时间、精度的要求。
关键词:船舶建造;分段搭载精度;控制;优化;引言船舶搭载(Shipcarrying),是船舶建造的核心步骤,更是至关重要的环节。
船舶搭载,其自身具有着建筑时间短、劳动力强度低、建筑成本低、便于集中管理、提高狭小空间的质量等功能优势。
在一定程度上,伴随着船舶搭载相关技术日新月异的发展,可谓开启了我国船舶建造业发展的新空间,让我国船舶建造业可以稳步开创新的里程碑。
那么,基于在船舶搭载过程中,最为关键的就是分段搭载实际精度的控制。
为了能够更好的保证船舶搭载的效率及质量,就必须对船舶建造中分段搭载实际精度的控制予以深度分析,制定出较为科学的优化措施,以提升船舶建造中分段搭载实际精度控制的效果,促进我国船舶建造业的进一步发展。
1.重要意义根据相关调研数据,目前大多数中国造船企业非常重视船体建造的精度控制技术。
这些企业以船体分段建造精度为控制目标,通过精度控制技术和适当的建造工艺实现对不同部件的控制。
此外,一部分中国造船企业还会学习国外先进造船技术和精度控制技术,在造船过程中进行更加全面的检查和验证,以保证船舶建造的安全性、可靠性和合理性。
研究精度控制技术,分析船舶建造过程中各钢板的使用误差和热变形,可有效节省造船的物力和财力,降低劳动生产率,提高造船质量。
加强对船舶精密控制技术的研究和应用,将船舶建造过程中产生的误差控制在要求范围内,确保船舶性能达到预期效果,提高船舶安全性。
将精度控制技术应用于船舶建造,可有效提高船舶的生产质量,减少操作过程中的差错和误差,保证船上旅客和货物的安全,提高船舶运行效率,为船东实现价值,有助于提高我国造船业在国际造船市场上的竞争优势。
船舶建造分段精度控制之反变形法的应用

船舶建造分段精度控制之反变形法的应用摘要:本文将以船坞搭载精度为目标,反变形方法应用为导向,分段制作阶段实施的路线,来介绍某船厂在8.2万吨散货船上利用反变形法对分段精度控制的研究实施,从而实现在船坞搭载阶段减少结构错位离空,提高船舶精度,缩短船坞周期,增加经济效益的目的。
关键词:精度控制分段建造反变形引言船舶建造中焊接引起的变形是诸多变形中最常见的现象,在变形达到一定程度之后就会超出精度标准范围,需要现场通过额外的弥补措施进行矫正,按照造船行业1:3:9的成本理论,越是后期进行矫正,所付出的代价越大。
通常情况下,焊接的变形我们可以在以下三个阶段进行控制:1、前期设计:合理的焊缝设计及焊接方法的选用;2、施工过程:制定合理的施工工艺,并对施工工艺严格执行,即现场工人按照设计的焊接电流、电压、焊接顺序、焊接速度进行施工;3、后期矫正:即变形后的补救措施,通过机械和火工进行变形矫正。
对于整个船舶建造环节,分段精度的控制是重中之重,分段因焊接产生的变形我们需两方面加以理解和区别对待,从而制定相应的措施进行控制,保证船坞分段搭载顺利进行。
1、分段完工状态目前船厂普遍的精度测量方法基本上是利用全站仪对分段相关点进行数据扫描,收集数据后用专用软件进行处理并与分段理论模型进行对比,尽量做到让实际分段与理论模型吻合。
在船舶实际建造中,常见的分段完工状态应该和理论模型一致,分段的变形需要进行矫正或制作胎架时释放一定反变形,让分段完工后朝着理论模型的方向变化。
另一种是该分段完工后产生的变形,虽然不能与理论模型数据吻合,但正是我们在船坞搭载阶段所需要的状态,或者认为在胎架制作时为让分段完工后达到与理论模型吻合所释放反变形反而不利于船坞搭载。
那么一个分段完工后究竟需要一个什么样的状态呢,这需要我们结合船坞的搭载时分段状态来判断,进而制定分段建造时分段反变形释放的方法。
下面将介绍两种不同分段状态要求下某造船厂分段反变形的释放应用。
- 1、下载文档前请自行甄别文档内容的完整性,平台不提供额外的编辑、内容补充、找答案等附加服务。
- 2、"仅部分预览"的文档,不可在线预览部分如存在完整性等问题,可反馈申请退款(可完整预览的文档不适用该条件!)。
- 3、如文档侵犯您的权益,请联系客服反馈,我们会尽快为您处理(人工客服工作时间:9:00-18:30)。
精度控制在船舶分段建造中的应用目录1引言................................................................................................................................................................... - 1 -2船舶分段建造精度测量仪器与操作 ............................................................................................................ - 2 -2.1船舶分段建造精度测量仪器 (2)2.2全站仪操作和使用要点 (2)3船舶分段建造精度标准 ................................................................................................................................. - 4 -4船舶分段精度控制和管理............................................................................................................................. - 5 -4.1船舶分段建造的精度控制 (5)4.1.1双层底分段结构及建造程序..................................................................................................................... - 6 -4.1.2双层底分段的测量控制.............................................................................................................................. - 6 -4.2船舶分段建造的精度管理 (8)结论.............................................................................................................................................................. - 10 -1引言船舶建造有很长的历史,传统造船方式无法对船舶制造过程中因焊接受热变形造成的尺寸不足和其他一些不利因素进行有效控制。
造船周期长、造船质量差、造船成本高是传统造船方式的最大问题。
为了最大化的减少这些因素对造船的影响,人们通过探索和研究,通过对一些建造过程的控制,从而达到缩短造船周期和减少成本的目的。
在船舶建造中,精度管理是造船技术的重要组成部分。
它主要是在分段建造的过程中以补偿量替代余量,通过合理的数据加放,对船体零件、部件和主尺度进行精度控制,提高了造船的质量,缩短了工期,从而达到减少成本的目的。
从上世纪60年代中期,我国开始从国外引入先进造船技术和精度管理的概念,但是我国因起步晚对船舶建造各方面缺少系统的认识,忽视了船舶建造精度管理各个方面的技术,只着重于工艺方面。
一直以来我国在船舶精度管理方面还没有形成一个完善的船体建造精度数据库和一整套船舶建造精度管理系统,国内许多船厂都只是尺寸方面的控制,精度管理基本还是处在事前加放余量的阶段,事后测量切割的状态,而且缺少对船舶建造精度管理的分析钻研能力。
传统分段测量和统计数据各个方面欠缺都体现在:(1)船舶分段建造过程精度控制问题,并不是数字化的精度测量,所测量的数据都是手动记录,而非数字化的记录,无益于问题的分系和研究,缺乏船舶建造过程当中数据的对比;所用测量工具的精度误差(钢尺等),而且非常不方便,对于一些较大,有线性的分段不能进行精确的测量;而且测量人员较多,耗费时间较长,非常不方便。
(2)在船舶建造中对于分段和总段精度控制问题,分段须得按照便于测量的方式放置,否则不好进行测量;数据的每一项统计和计算都需要人工来计算,无益于实际数据与设计数据的对比;耗费时间长,而且容易出现问题,极大的影响了工程周期;目前我国由于对分段的测量手段的落后和对分段建造的经验不足,目前还无法形成比较完善的的精度管理机制和精度数据利用循环。
(3)船台、船坞合拢的精度控制问题,之前传统的测量方法效力较低,占用吊车时候较长;在分段上船台后需要根据现场实际情况对余量进行切割,需要对分段进行重新定位作业;很多分段需要进行二次定位,极大的影响船台搭载周期;传统的测量和记录方式很难对船舶分段建造中的数据进行精度管理,难以对分段的无余量搭载模式提供可靠的数据统计与汇总。
在船舶建造精度管理方面,国外很多学者已经研究出大量成果,并且大多都被应用到实际建造中,但都因商业秘密考虑,所研究的成果很少被公开分享。
因此,具体船舶建造精度管理水平到什么程度只能从一个国家的船舶生产总量上大致看出。
目前,在我国先进的船舶建造精度管理技术在大型船厂已得到了较为广泛地运用,但在中小型造船企业中还未得到广泛地运用,还停留在运用余量加放来控制船舶精度的阶段。
对于立体分段的常规测量方法是首先将分段调整到方便分段测量的状态,然后利用各种非数字化的工具进行测量,这种方法的弊端是数据测量的速度比较慢,而且由于测量工具的准确性不高,无益于数据的系统分析和数据的整理。
为了使船舶建造精度管理技术在中小型造船企业得到广泛应用,在现代造船模式下,这种非数字化的测量方式已经不能为船舶分段建造提供方便。
最合适的方法是充分利用计算机技术生产设计出三维分段立体模型,通过三维分段立体测量仪器和测量软件,通过对分段主要点的测量和控制,然后通过专用船舶建造精度管理软件对实测点与设计点进行对比分析,最后对比实造分段各项数据进行修改。
这类方式有效的避免了传统使用方式的弊端,为进一步船舶建造精度管理水平奠定了可靠的基石。
2船舶分段建造精度测量仪器与操作2.1船舶分段建造精度测量仪器船舶建造精度控制中常用到的仪器主要有三种,分别是水准仪、经纬仪、全站仪,但因前两种仪器无论在使用还是测量精度上面都没有全站仪容易和精准,全站仪三维测量在人员、安全性、精度等方面优于传统测量方式。
所以,一些大型的船厂已逐渐使全站仪代替了前两种仪器。
2.2全站仪操作和使用要点全站型电子速测仪简称全站仪,如图1所示。
它是一种可以同时进行角度(水平角、竖直角)丈量、间隔(斜距、平距、高差)丈量和数据处理的周全仪器。
由于只需选好位置放置,就可以完成所有需要测量的工作,故被称为“全站仪”。
图1 全站仪全站仪的操作步骤和注意要点如下:不同型号的全站仪,其具体操作方法会有较大的差异。
以下简单介绍其操作方法和应注意的事项:(1)水平角的测量1)打开仪器后,按角度测量键,这时全站仪会处于角度测量模式,照准第一个目标A。
2)然后设置A方向的水平度盘读数为0°00′00〃。
3)照准第二个目标B,这时显示器上显示的便是两个点之间的角度。
(2)距离的测量架设好一起后,使目镜照准所测目标中心,按测距键,距离测量开始,测距完成时显示斜距、平距、高差。
(3)坐标测量1)进行坐标测量前,应先选择好比较有利的测量地点,尽量在不迁站的情况下把索要测量的点都测量完。
一般坐标测量都会有专门的软件,打开软件,设置文件编码,找到比较有利的测量点(注意仪器架设地面要比较稳定,不易晃动)。
2)建立三维空间坐标测量,既所测的第一个点,通常是原点即(0,0,0),然后依次测量别的点,点的测量没有先后顺序,可根据现场的情况选择优先测的点。
3)迁站,对于一些较大分段,而无法测量到的点,要进行迁站,有专用的迁站靶标,分段测量一般都是两点靶标迁站,具体情况按实际现场情况而言,注意两个迁站的靶标与仪器之间的夹角在90°最佳,角度不宜过大或太小,影响测量结果,迁站靶标的放置一般在1-1.5 倍的分段最大长度,大一些或小一些都可以,具体按照现场情况摆继续进行测量,所需要测的点测完为止。
(4)测量完以后仪器工具的收放,保证所有工具都已收集起来,不能漏掉。
全站仪在整个造船工程中占据的很重要的使用价值。
全站仪在造船中的应用很广泛,前期分段的制造,以及后期船台的搭载,船舶水线的绘制等等,尤其是船台中心线的确定,为后期船台搭载做出了基准。
全站仪的使用使得造船的精度,质量有了一个很大的提高。
3船舶分段建造精度标准船舶分段建造精度标准是整个船舶精度标准体系的一部分,既要反映本企业船体分段制作精度的质量水平,又要满足行业。
精度标准包括补偿量标准、精度检验标准、精度控制基准、精度测量表、基准线设计基准等。
精度补偿量包括切割补偿量、加工补偿量、装置补偿量和焊接补偿量等方面,要对以前分段建造的数据总结,反应在船体分段建造上,然后经由建造好的分段的现实数据和计划数据对比,确定所放补偿量的正确性,再形确定补偿量标准。
精度检验标准是根据精度目标细化到船体制作各工序阶段的精度要求。
精度工艺标准是对于一些精度容易出现问题的工序阶段制定专门的装焊工艺。
(1)精度标准按适用范围一般可分为,行业标准、企业标准和作业标准三类。
(2)行业标准是指同行业内通过讨论共同制定的标准。
(3)企业标准是企业根据自身各方面的情况所制定的标准。
(4)作业标准是船厂为控制误差在企业标准内而制定的各种标准。
分段建造精度标准按《中国造船质量标准》分为:(1)平面与曲面分段精度标准。
(2)立体分段装精度标准。
(3)含艉柱的立体分段精度标准。
(4)含主机座的分段精度标准。
船体精度标准的制定并不是一成不变的,根据船厂自身硬件和软件水平的提高和国际标准各的提高,以及船东对船舶建造提出的要求而改变。
船体建造精度的行业标准大多会两年进行一次改变,企业标准则是根据各个船厂的发展来进行制定。
为了正确表述船体精度标准,应对下列名词进行定义:(1)船体分段:为便利船体布局制作合理划分的布局单元,为大组立而构成的中心产物。
(2)余量:对船体零件、工件和中心产物经由过程加工、装焊、火工改正等多道工序,而发生的变形及缩短举行定性和定量分析后,加放的比现实变形及缩短略大的工艺量值,一样平常要在装置后割除。
(3)补偿量:对船体零件、工件和中心产物经由过程加工、装焊、火工改正等多道工序,而发生的变形及缩短举行定量分析后,加放相称现实变形和缩短的工艺量值,一样平常不需再切割。