汽车冲压件焊接检验指导书
冲压件检验指导书(二)
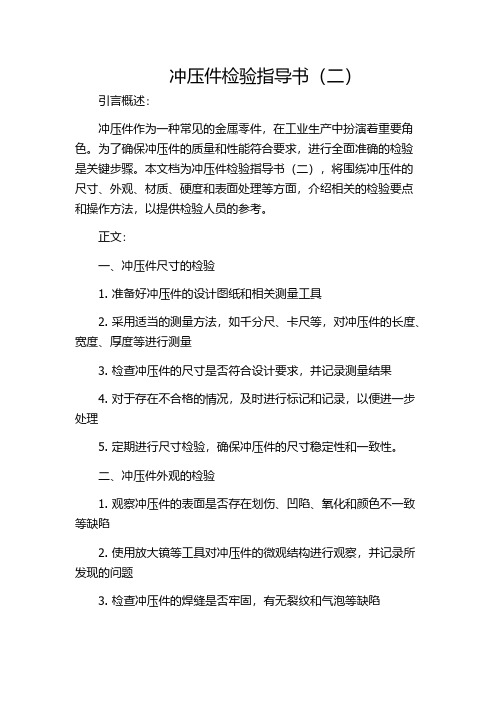
冲压件检验指导书(二)引言概述:冲压件作为一种常见的金属零件,在工业生产中扮演着重要角色。
为了确保冲压件的质量和性能符合要求,进行全面准确的检验是关键步骤。
本文档为冲压件检验指导书(二),将围绕冲压件的尺寸、外观、材质、硬度和表面处理等方面,介绍相关的检验要点和操作方法,以提供检验人员的参考。
正文:一、冲压件尺寸的检验1. 准备好冲压件的设计图纸和相关测量工具2. 采用适当的测量方法,如千分尺、卡尺等,对冲压件的长度、宽度、厚度等进行测量3. 检查冲压件的尺寸是否符合设计要求,并记录测量结果4. 对于存在不合格的情况,及时进行标记和记录,以便进一步处理5. 定期进行尺寸检验,确保冲压件的尺寸稳定性和一致性。
二、冲压件外观的检验1. 观察冲压件的表面是否存在划伤、凹陷、氧化和颜色不一致等缺陷2. 使用放大镜等工具对冲压件的微观结构进行观察,并记录所发现的问题3. 检查冲压件的焊缝是否牢固,有无裂纹和气泡等缺陷4. 对于外观不合格的冲压件,及时进行分类处理,避免出现混淆和错误使用的情况5. 定期进行外观检验,防止冲压件因外界因素损坏而影响其使用性能。
三、冲压件材质的检验1. 根据冲压件的设计要求,准备对应的材质检验工具和设备2. 通过化学分析或光谱分析等方法,对冲压件的材质成分进行检验和确认3. 检查冲压件的密度和硬度是否符合标准要求,并记录测试结果4. 对于材质未达到要求的冲压件,进行追溯调查和替换处理,以确保产品质量和安全性5. 定期进行材质检验,防止恶意替换或使用劣质材料导致的问题。
四、冲压件硬度的检验1. 根据冲压件的硬度要求,选择适当的硬度测量方法和仪器2. 对冲压件的不同位置进行硬度检测,并记录测试数据3. 检查冲压件的硬度是否均匀、稳定,符合设计要求4. 异常硬度的冲压件,需进行追踪分析,找出原因并进行处理5. 定期进行硬度检验,防止冲压件因材料变质或加工工艺问题导致硬度不符合要求。
五、冲压件表面处理的检验1. 对冲压件的表面处理工艺进行了解和研究,了解其要求和方法2. 观察冲压件表面处理是否平整光滑,达到要求的光洁度和平整度3. 检查冲压件的防锈涂层和涂装层是否均匀、牢固,不易脱落或剥落4. 对于出现表面处理缺陷的冲压件,进行清洗、修复或替换处理5. 定期进行表面处理的检验,确保冲压件的外观美观和防腐性能。
冲压件毛刺检验指导书
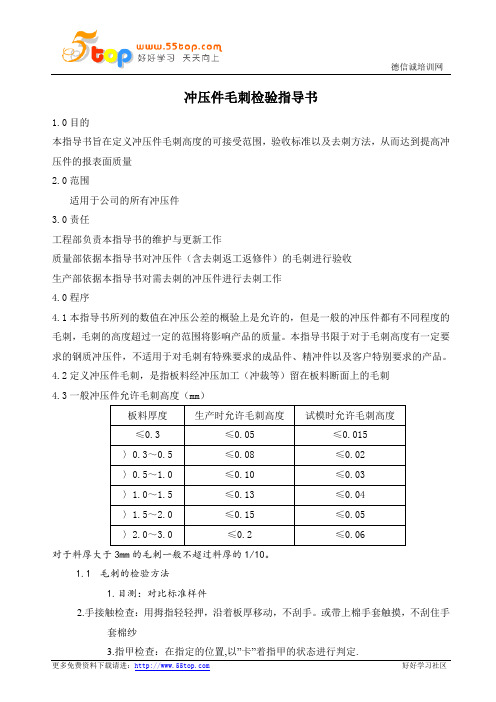
冲压件毛刺检验指导书1.0 目的本指导书旨在定义冲压件毛刺高度的可接受范围,验收标准以及去刺方法,从而达到提高冲压件的报表面质量2.0 范围适用于公司的所有冲压件3.0 责任工程部负责本指导书的维护与更新工作质量部依据本指导书对冲压件(含去刺返工返修件)的毛刺进行验收生产部依据本指导书对需去刺的冲压件进行去刺工作4.0 程序4.1 本指导书所列的数值在冲压公差的概验上是允许的,但是一般的冲压件都有不同程度的毛刺,毛刺的高度超过一定的范围将影响产品的质量。
本指导书限于对于毛刺高度有一定要求的钢质冲压件,不适用于对毛刺有特殊要求的成品件、精冲件以及客户特别要求的产品。
4.2 定义冲压件毛刺,是指板料经冲压加工(冲裁等)留在板料断面上的毛刺4.3 一般冲压件允许毛刺高度(mm)板料厚度生产时允许毛刺高度试模时允许毛刺高度≤0.3 ≤0.05 ≤0.015〉0.3~0.5 ≤0.08 ≤0.02〉0.5~1.0 ≤0.10 ≤0.03〉1.0~1.5 ≤0.13 ≤0.04〉1.5~2.0 ≤0.15 ≤0.05〉2.0~3.0 ≤0.2 ≤0.06对于料厚大于3mm的毛刺一般不超过料厚的1/10。
1.1毛刺的检验方法1.目测:对比标准样件2.手接触检查:用拇指轻轻押,沿着板厚移动,不刮手。
或带上棉手套触摸,不刮住手套棉纱3.指甲检查:在指定的位置,以”卡”着指甲的状态进行判定.确认位置以各表面进行.不可”卡”着指甲4.过纸检查:在指定的位置,以A4纸作R部,约45o倾斜,以前端部”卡”着状态移动,进行判定..前端不可”卡”着F5.卡尺测量(毛刺较大),4.5毛刺的清除1、对于小毛刺可以先用锉刀或刮刀修锉,然后用砂纸进行精砂;对于较大毛刺先采用旋转研磨机去除毛刺,然后用抛光轮抛光但注意造成零件的变形量,更不能伤到产品其它表面。
注意在使工具手工去刺时,工具防向要与毛刺方向成一定的倾角。
2、喷砂冲压件外观缺陷检验标准项目描述关键件判定(整车区域)A B C D裂纹1、封闭裂纹:长度≥50mm宽度≥3mm2、不封闭裂纹:长度≥30mm宽度≥2mm/所有件下同报废1、封闭裂纹:10mm≤长度<50mm宽度<3mm2、不封闭裂纹:10mm≤长度<30mm宽度<2mm是报废报废报废报废非报废返修返修返修1、封闭裂纹:长度<10mm宽度<3mm2、不封闭裂纹:长度<10mm宽度<2mm/ 返修返修返修返修缩颈缩颈部位材料厚度:厚度≥料厚的80%;缩颈部位长度≥60mm/ 报废缩颈部位材料厚度:料厚的50%≤厚度<料厚的80%;缩颈部位长度:30mm≤长度<60mm;是报废报废报废报废非报废报废返修返修缩颈部位材料厚度:厚度<料厚的50%缩颈部位长度:长度<30mm/ 返修坑包面积≥8m㎡;长度≥10mm;高度≥1.5mm/ 报废报废返修返修面积<8m㎡;长度L<10mm;高度<1.5mm/ 返修返修返修合格变形零件表面出现明显起伏;目视明显;严重影响外观及装配/ 报废零件表面出现起伏;目视不明显;手感/ 返修返修返修合格明显零件表面出现起伏;手感不明显;油石检验明显/ 返修返修合格合格麻点零件2/3面积上能看到麻点或小凸包/ 报废零件表面用油石磨件之前用手感觉明显的麻点或麻点群;麻点面积<2/3零件面积;/ 报废报废返修合格材料缺陷料厚明显不符合要求;表面有明显的桔皮滑移线、镀锌层疏松;锌脱落长度≥300mm;宽度≥5mm/ 报废报废报废合格轻微的材料缺陷;磨件后可见的材料缺陷;/ 返修返修合格合格锈蚀锈蚀厚度≥料厚的40%;锈蚀面积≥全部面积的25%;型面比较复杂无法消除锈迹;/ 报废锈蚀厚度:料厚的20%≤厚度<料厚的40%;锈蚀面积:全面积5%≤厚度<全面积25%;是报废非报废报废返修返修表面质量受锈蚀影响但可通过打磨修复;/ 返修起皱肉眼能看出的严重皱折、棱线错位,严重影响焊接及装配;/棱线、弧度不够清晰光顺;肉眼可见的皱纹、波纹、棱线错位;是报废报废返修返修非报废报废返修合格毛刺毛刺高度H大于料厚的40%;有操作危险性的粗毛刺;/ 返修毛刺高度:料厚的20%≤高度<料厚的40%;毛刺影响定位、装配、焊接、压一般孔合格定位孔装返修合的;配孔一般料边合格压合/焊接料边返修毛刺高度:高度<料厚的20%;/ 合格拉毛压痕划伤深度≥料厚的30%;宽度≥2mm;长度≥5mm;是报废非报废报废返修合格料厚的10%≤深度<料厚的30%;宽度<2mm;长度<5mm/ 返修返修返修合格深度<料厚的10%;/ 返修返修合格合格圆角不顺圆角半径不均匀,未达到要求;明显地不清晰、不光顺;配合间隙达2mm以上;/ 报废报废返修返修圆角半径不均匀,不够清晰光顺;配合间隙达2mm以下/ 返修返修合格合格叠料板料重叠宽度:宽度≥8mm / 报废板料重叠宽度:3mm≤宽度<8mm是报废非报废报废报废返修板料重叠宽度:宽度<3mm / 报废返修返修合格其他能引起严重功能障碍的缺陷报废对使用有明显影响的缺陷返修9.2尺寸缺陷检验判定标准尺寸缺陷检验判定标准项目描述零件与检具的间隙用d 表示, 平度用h 表示,单位mm判定结果压合料边面 定位面特殊料边面 -0.5≤h ≤0.5;2.5≤d ≤3.5 合格焊缝搭接边 -1.0≤h ≤1.0;2.0≤d ≤4.0点焊搭接边 涉及外观\装配面料边 -0.5≤h ≤0.5;2.0≤d ≤4.0 定位孔0≤直径≤0.2;-0.5≤d ≤0.5; -0.5≤圆心位置偏移量≤0.5; 装配孔-0.2≤直径≤0.2;-0.5≤d ≤0.5; -0.5≤圆心位置偏移量≤0.5; 一般过孔 -0.5≤直径≤0.5;-1.0≤d ≤1.0; -1.0≤圆心位置偏移量≤1.0 一般边缘 1.5≤d ≤4.5;-1.0≤h ≤1.0一般型面2.0≤d ≤4.0说明:1、表中数值为制件检具测量的平度、间隙大小。
冲压检验操作指导
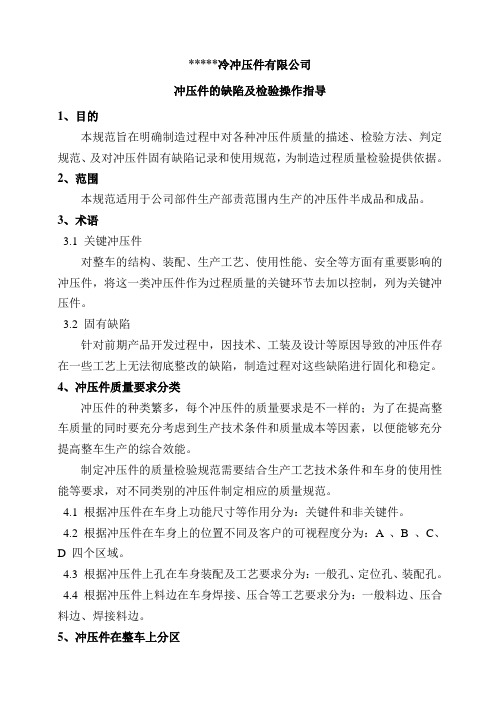
*****冷冲压件有限公司冲压件的缺陷及检验操作指导1、目的本规范旨在明确制造过程中对各种冲压件质量的描述、检验方法、判定规范、及对冲压件固有缺陷记录和使用规范,为制造过程质量检验提供依据。
2、范围本规范适用于公司部件生产部责范围内生产的冲压件半成品和成品。
3、术语3.1 关键冲压件对整车的结构、装配、生产工艺、使用性能、安全等方面有重要影响的冲压件,将这一类冲压件作为过程质量的关键环节去加以控制,列为关键冲压件。
3.2 固有缺陷针对前期产品开发过程中,因技术、工装及设计等原因导致的冲压件存在一些工艺上无法彻底整改的缺陷,制造过程对这些缺陷进行固化和稳定。
4、冲压件质量要求分类冲压件的种类繁多,每个冲压件的质量要求是不一样的;为了在提高整车质量的同时要充分考虑到生产技术条件和质量成本等因素,以便能够充分提高整车生产的综合效能。
制定冲压件的质量检验规范需要结合生产工艺技术条件和车身的使用性能等要求,对不同类别的冲压件制定相应的质量规范。
4.1 根据冲压件在车身上功能尺寸等作用分为:关键件和非关键件。
4.2 根据冲压件在车身上的位置不同及客户的可视程度分为:A 、B 、C、D 四个区域。
4.3 根据冲压件上孔在车身装配及工艺要求分为:一般孔、定位孔、装配孔。
4.4 根据冲压件上料边在车身焊接、压合等工艺要求分为:一般料边、压合料边、焊接料边。
5、冲压件在整车上分区5.1 (A区)车身腰线装饰条或防擦条的下边线、前翼\后翼轮罩边线等以上部位,不包括当车身前后风挡玻璃上边缘的顶盖和天窗区域。
5.2 (B 区)车身腰线装饰条或防擦条的下边线、前翼\后翼轮罩边线等以下部位,车身前后风挡玻璃上边缘的顶盖和天窗区域。
5.3 (C 区)打开车门上车时能看到的部位;坐在司机或乘客座位上,关上车门后能看得见的部位;车身发动机盖、行李盖打开后看得见区域;天窗窗框,油箱加注孔入口等其他区域。
5.4 (D 区)除A 、B 、C 三个可视区域,车身上被内饰件等覆盖的、客户一般所不能察觉或发现的部位。
冲压常规检验指导书

目视
√
√
烧焊或点焊时接头位的熔接痕;
a、用手触摸,明显刮手或凸起;
b、用手触摸,轻微刮手,但表面平顺;
漏打磨
目视
√
焊接点因有利边或利角需要磨平,但未磨到;
假焊
目视
√
焊接点未焊接上,轻微用力焊接位会裂开(1LBS内);
刮花痕
目视/卡尺
√
√
工件表面刮花痕迹;
a、刮花痕迹超过1CM;
b、刮花痕迹小于1CM;
披锋
目视
√
√
冲压时由于冲模未调整好(上下模不对位)或上下模冲刀不利;
a、后加工(抛光)不能抛平或严重刮手;
b、后加工(抛光)可以抛平且不刮手;
压伤
目视
√
冲刀屑掉在模具内将工件撞伤或排盆不当而将产品压伤;
毛边/卷边
目视
√
√
在冲压时工件边缘卷起;
a、后加工(抛光)不能抛平或严重刮手;
b、后加工(抛光)可以抛平且不刮手;
尺寸不良
卡尺
√
与签样、BOM表或图纸尺寸不相符;
形状不符
目视
√ቤተ መጻሕፍቲ ባይዱ
与签样样品形状不相符;
孔偏位
目视/卡尺
√
√
与签样比较孔位偏差大于1CM;
与签样比较孔位偏差小于1CM;
纹路冲反
目视
√
与签样不相符
压花深度不良
目视
√
与签样比对压花深度不符;
序号
制/修订说明
最新版本
制/修订人
日期
01
首次发行
A0
02
03
1.0目的
建立一套次品鉴定标准以便冲压QC能正确地鉴定次品内别。
汽车零部件冲压件作业指导书

⇒
检查注意事项 OP05注意边毛刺; OP10注意成型到位; OP20注意冲孔毛刺; OP30注意冲孔毛刺、孔数,上检具测量;
1 笔计数
9
3 重・开裂・缩颈
3 开裂
目视
无大差
5
变形
4 暗裂 目视、测定 料厚的30%
6 起皱□叠料
5
变形 触感、油石 无大差 首检
7
6
起皱、叠 料
目视 前次品以下
8
擦伤 边毛刺
7 擦伤 目视、触感 料厚的20%
8 边毛刺 9 孔毛刺
目视 目视
0.3mm以 下
0.3mm以 下
9
孔毛刺
10 废料压痕
11 拉延印记
10 尺寸欠缺 目视 基本一致
11 废料压痕 目视
料厚的 20%
2 抽检
3
开裂・暗裂
12 拉延印记
目视
能够识别 末件
2 ⇒ 12
同样件比较 白板笔检查 (从出毛刺的一面开始) 铅笔检查100mm间隔 从内侧看凸R部 油石・触感 (针对一类表面覆盖件)
目视 与样件对比 油石・触感・比较 (砂纸#240)(针对一类表面覆盖
公司冲压件检验、作业指导书
品质检查作业标准
车型
H13
零件号 零件名称
H13-5301751 前保上横梁中间安装板本体
制作部门 制作日期
检验性质
牌号
冲压件检验作业指导书

检查时间检查结论检查时间检查结论序号类别公差序号类别公差面±0.5面±0.5边±0.7边±0.5面±0.5边±0.7面±0.5Φ7.5+0.2边±0.70.6面±0.52-6.5X4.8+0.2边±0.50.6面±0.510.5X7.0+0.2边±0.50.6检查时间检查结论检查时间检查结论面±0.52-5.0X5.0+0.2首检边±0.50.6面±0.55-Φ8.5+0.2边±0.50.6面±0.5Φ7.0+0.1边±0.50面±0.57.0X10.0+0.1边±0.50面±0.5边±0.5首检面±0.5巡检边±0.5巡检面±0.5末检边±0.5检查记录检查记录检查记录检查记录检验项目检验项目边界轮廓检验内容实际合格率目标合格率 当班检验: 班长:车型检验项目工艺参数孔数孔位S21检验内容工作高度、气垫压力等目测检具零件编号要求必须在作业指导书要求范围内,若生产过程中工作高度变更,需要进行边界轮廓抽检点的复检共 18 孔是否有漏孔、多孔现象巡检巡检巡检末检表面质量压印点、棱线B11B12B1B2B3B4B5B6h3h4B7B8B9B10h6h7检验项目孔径孔位检验内容B13冲压件检验作业指导书6201101002-S21零件名称HC180B/0.7检具编号后门外板-右材质/料厚S21-44-6201101001-J01文件编号:表格编号:简图:要求要求检验内容要求检具状态h1h2定位顺序:按检具操作流程执行备注:清晰锈蚀、分层、划伤、凸包凹坑、压痕、严重拉毛、起皱、开裂、隐裂、缺边等按冲压件检验标准验收到底标识清晰毛刺高度h<0.20mm (极限样板)h5SS。
冲压件检验作业指导书(两篇)

引言概述:冲压件是一种常见的金属加工零部件,广泛应用于汽车、家电、机械等领域。
为了确保冲压件的质量,提高生产效率和产品可靠性,进行冲压件检验工作是至关重要的。
本文是冲压件检验作业指导书的第二部分,旨在提供详细的工作指导,帮助检验员正确执行冲压件检验任务。
正文内容:一、检验前准备1.准备检验设备和工具:包括显微镜、测量工具(卡尺、千分尺、测微计等)、外观检验工具(手电筒、放大镜等)等。
2.准备冲压件技术标准和图纸:检验员需要熟悉冲压件的技术标准和图纸,了解要求的尺寸、外观等要求。
3.准备检验记录表格:根据实际需求,准备相关的检验记录表格,方便记录检验结果。
二、尺寸检验1.测量尺寸:使用合适的测量工具,按照冲压件的技术标准和图纸上的要求,测量冲压件的各个尺寸。
2.校验测量工具:定期校验测量工具,确保其准确性。
校验工具时,可以使用已知尺寸的标准样品进行比对,校验结果应在允许范围内。
3.记录尺寸:将测量结果记录在检验记录表格中,及时发现异常尺寸并进行记录。
三、外观检验1.观察表面缺陷:使用手电筒、放大镜等工具,仔细观察冲压件表面是否存在破损、划痕、氧化等缺陷。
2.检测涂层质量:如冲压件表面有涂层,利用视觉和手感,观察涂层是否均匀、无起皱、无脱落等。
3.检查装配性能:如冲压件需要用于装配,可以进行装配试验,检查冲压件的装配性能,确保其能够正常使用。
四、材料检验1.材料标识检查:检查冲压件上的材料标识是否清晰、准确,与技术要求一致。
2.化学成分分析:根据需要可以进行化学成分分析,以验证材料的成分符合要求。
3.硬度检验:使用硬度测量仪器,对冲压件进行硬度检验,确认其硬度符合技术要求。
五、其他检验1.物理性能检验:如冲压件需要承受一定的载荷或振动,可以进行物理性能检验,包括强度、刚性等。
2.功能性能检验:如冲压件需要具备特定的功能,可以进行功能性能检验,确保其能够满足产品要求。
3.环境适应性检验:对于要求耐腐蚀等特殊环境要求的冲压件,需要进行相应的环境适应性检验。
冲压件检验作业指导书(一)2024

冲压件检验作业指导书(一)【引言概述】冲压件检验是在冲压件生产过程中必不可少的环节,其目的是确保产品的质量和一致性。
本作业指导书旨在指导操作人员进行冲压件检验工作,提供明确的操作流程和注意事项,以确保检验结果的准确性和可靠性。
【正文内容】一、检查冲压件外观1. 检查表面是否有明显的缺陷,如划痕、凸起、凹陷等。
2. 检查冲压件的尺寸是否符合图纸要求。
3. 检查冲压件的颜色、涂层等是否符合规定标准。
4. 检查冲压件的边缘是否整齐光滑,无毛刺、露铜等问题。
5. 检查冲压件的标志和标签是否清晰可辨认。
二、检测冲压件材料性能1. 使用金相显微镜检查冲压件的金相组织结构。
2. 进行硬度测试,确保冲压件的硬度符合标准要求。
3. 进行拉伸试验,检测冲压件的拉伸强度和延伸率。
4. 进行冲击试验,评估冲压件的抗冲击性能。
5. 进行化学成分分析,确保冲压件材料的成分符合标准要求。
三、检验冲压件的功能性能1. 进行装配试验,测试冲压件与其他零件的配合情况。
2. 进行泄漏测试,确保冲压件的密封性。
3. 进行开关试验,检验冲压件的开关性能和可靠性。
4. 进行负荷试验,评估冲压件的承载能力。
5. 进行振动测试,检测冲压件的耐振性能。
四、检验冲压件的可靠性1. 进行寿命试验,评估冲压件的使用寿命。
2. 进行可靠性验证,确保冲压件在规定的时间内正常工作。
3. 进行环境适应性测试,检查冲压件在不同环境条件下的工作稳定性。
4. 进行电磁兼容性测试,确保冲压件在电磁干扰下的正常工作。
5. 进行强度耐久性测试,评估冲压件在重复负荷下的耐久性能。
五、记录和处理检验结果1. 在检验过程中,及时记录冲压件的检验结果和相关数据。
2. 对于不合格的冲压件,及时进行标识和隔离,并记录不合格原因。
3. 对于合格的冲压件,进行标识和追溯,确保其质量可追溯。
4. 对于异常情况和重要的检验结果,及时向相关部门报告和处理。
5. 定期回顾和评估检验结果,以改进和优化冲压件生产和检验流程。
- 1、下载文档前请自行甄别文档内容的完整性,平台不提供额外的编辑、内容补充、找答案等附加服务。
- 2、"仅部分预览"的文档,不可在线预览部分如存在完整性等问题,可反馈申请退款(可完整预览的文档不适用该条件!)。
- 3、如文档侵犯您的权益,请联系客服反馈,我们会尽快为您处理(人工客服工作时间:9:00-18:30)。
汽车冲压件焊接检验指导书焊接检验指导书一、检验标准内容1、焊接质量检验方法2、外观检验标准3、焊点质量标准4、焊接尺寸精度二、焊接质量检验方法1、直观检查用普通、无辅助设备的视力观察,检查车身分总成的外观、焊点(缝)数量、位置和成形质量。
2、试片的性能试验用与正常生产相同的焊接参数,对与产品同材料、同厚度、同层次的试板进行焊接,试验完成后出具相关试验报告。
将试验报告提交至技术部、质量部存档,试验标准参见表3a、调试完成后,所有工位试板需进行试板的性能试验,并提供试验报告。
b、正式生产后,需每三个月提供一次所有工位试板5组的性能试验报告c、每次对焊钳进行参数调整,需提供相应焊钳的试板性能试验报告。
3、半破坏试验检查将专用的工具或装置插入焊接部件以及临近焊缝的部件之间,施加一个外力后,不破坏元部件,观察焊点(缝)的成形质量。
a、检查对象1) 焊接件焊点及关键焊点、易出现缺陷的焊点;2) 半破坏检查前先进行目视检查,检查焊接和工件是否异常。
b、检验频次:抽检:每批次1次,一次3件。
c、检验内容:将被检查的部件放至规定的检查区域:1)清点焊点个数;2)检查焊点位置;3)检查是否存在不可接受的焊点。
d、检验方法:对焊缝中具有特征代表性的焊接点进行检验,将专用凿子和锤子进行在离焊点规定处插入一定的深度(与被检查焊点内端齐平),到达要求的尺寸范围后,上下扳动凿子,直到焊接点材料屈服或严重弯曲,检查焊点是否松动。
f、检验注意事项:1)如果发现有焊点拉长而焊缝无断裂或损坏,应停止检验。
对于两个以上工件之间的焊缝,应在每对相邻工件之间进行检验。
对于两端焊点,必须检验。
2)当进行半破坏检查时应注意:别让凿子接至焊接部位,这可能会导致衔接部位被切断;3)当进行半破坏检查时,插入凿子的位置和深度做如下要求:A=1.0mm,2.0mm(尽量同焊接部位靠近),B=5.0mm以上。
半破坏检查的操作示意图;4)拔出凿子,用0.5,1镑锤子还原零件。
5)半破坏焊点检查的数量,不少于焊接焊点总量的30%。
g、记录1)如发现有异常焊点,在相应的焊点上做好异常状态记录,并将结果记录在《检验记录单》,并执行焊接质量问题处理流程2)缺陷焊点数量超过总数的1%,则焊接质量不合格。
h、修复1)破坏检查完成后在零件上标出标识,并在规定的区域存放,存放时间为半个工作日,到期后对检查部位加以(修正)点焊补焊后使用;2)焊点有损坏的,应用CO2焊补焊处理。
如果有缺陷,应按照指定方案修理并重新进行检查或者报废。
注1:下列焊点不适于进行半破坏检查:1) 凿子无法达到的焊点;2) 外表面,平整度要求较高的焊点(包括铜板焊接)。
4、破坏试验检查由专业人员用专用的工具或装置插入焊接部件以及临近焊缝的部件之间直到元部件彻底分离,观察焊点(缝)的成形质量。
a、检查对象焊接件焊点及关键焊点、易出现缺陷的焊点。
b、检验频次:在正常批量生产过程中,现场加工的所有焊缝应按检验周期(见下表1)进行破坏性检验。
序号每周生产数量频次备注 1 1-500 1次/2000 1次3件 2 501-1500 1次/3000 1次3件 3 1501-3000 1次/3000 1次3件 4 3001-6000 1次/3000 1次3件 5 6001-10000 1次/3000 1次3件c、检验内容:破坏检查前先进行目视检查,检查焊接和工件是否异常。
将被检查的部件放至规定的检查区域:a) 清点焊点个数;b) 检查焊点位置;c) 检查是否存在不可接受的焊点。
对焊缝中具有特征代表性的焊接点进行检验,将专用凿子或液压扩力钳对工件进行破检,工件撕裂要求在分离后的任意一个工件上焊接处形成一个圆孔,另一个上形成一个圆凸台,且焊点直径符合表3的规定,见表3。
如果两个工件上孔径小于标准,表示点焊试件不合格。
并将结果记录在《检验记录单》。
d、记录a)如发现有异常焊点,在相应的焊点上做好异常状态记录,并将结果记录在《检验记录单》,并执行焊接质量问题处理流程。
b)缺陷焊点数量超过总数的1%,则焊接质量不合格。
三、外观检验标准表2 外观检验标准序号检查项目检查方式检验工具检验标准不允许有记号笔痕、油污(允许少量浮油)、残胶 1 表面清洁目视不允许有目视可见铁屑、灰尘等异物 2 圆弧, 棱线目视不允许明显的轮廓不清晰 3 划伤碰伤目视手感不允许零件表面明显划伤 4 凸包/凹坑目视手感油石不允许目视可见、手感明显的凸包凹坑 5 麻点群目视手感油石无手感明显的麻点(群)6 材料缺陷目视测量游标卡尺不允许7 锈蚀目视不允许明显目视可见的锈斑 8 间隙目视测量间隙尺间隙不得超过0.8mm 9 裂纹目视不允许10 错位目视测量游标卡尺不允许明显可见装配错位 11 变形目视检具不允许12 打磨纹目视手感油石不允许13 缺胶目视按照工艺标准检查,不允许缺胶 14 错焊、漏焊目视不允许15 其它不允许有影响整车安全性能及明显影响整车外观的缺陷四、焊点质量标准1、点焊:a、焊点外观质量:焊点表面呈圆形或椭圆形,焊点数量、位置、尺寸应符合产品图样或工艺文件的要求,焊点目视无裂纹、气孔、脱焊、烧穿、过烧等缺陷;b、焊点直线度:焊点直线度之差左右位移量不大于3mm,c、压痕深度:不可大于板厚的20%;如果两工件的厚度比大于2:1,压痕深度可增大到20%,25%,任何压痕要抛光处理;d、焊透率:应为30-80%。
e、焊点熔核直径:工艺规程未注明焊点熔核直径的,根据表2检验,焊点直径误差允许-1~+2mm。
f、焊点强度:焊点抗剪强度要求见表3;g、焊点间距/边距:工艺规程未注明焊点边距和焊点间距的,根据表4检验,焊点须均布,焊点间距之差为?5mm,但不得积累。
当最后一个焊点间距不能满足要求时(间距过大或过小)须进行调节保证焊点均布,间距Ha>3d(d为核心直径)。
h、焊点数量:符合该工位《焊装标准作业指导书》的要求,工艺文件中规定的某个焊接边的焊点数为5个或者更少时,不允许出现有缺陷焊点或少焊点;工艺文件中规定的某个焊接边的焊点数为6个或者更多时,允许的缺陷焊点数量和多余的焊点数量见下表5。
i、如果一条焊接边允许有两处或者两处以上的缺陷焊点,那么缺陷焊点间应至少有一个好的焊点间隔,才可以看作合格;焊缝末尾的焊点不得有缺陷。
表3 焊点熔核直径及焊点抗剪强度要求抗剪强度(kN /序号板厚(mm) 熔核直径(mm) 焊透率点)1 0.8+0.8 4.5 ?4.02 1.0+1.0 5 ?5.43 1.2+1.2 5.5 ?6.8 注:4 1.5+1.56 ?9.3 1、焊透率应为30-80%。
2、二层点焊应按簿板计算。
5 1.6+1.6 6.3 ?10.93、薄板与厚板焊接,按薄板计算,6 1.8+1.8 6.7 ?11.4多层点焊分别按现两外层板计7 2.0+2.0 7.1 ?13.7 算。
8 2.5+2.5 7.9 ?17.79 3.0+3.0 8.1 ?18.5表4 点焊板厚与焊点位置要求板厚δ(mm) 最小点距e(mm) 边距b(mm) 备注0.5 10 ,4.50.8 12 ,5.01.0 12 ,6.01.2 14 ,6.51.5 14 ,7.02.0 16 ,8.02.5 18 ,9.03.0 20 ,10.0表5 有效焊点数量要求规定的焊点数有效焊点数Min 实施焊点数MAX1-5 n n6-10 n-1 n+111-20 n-2 n+221-30 n-3 n+331-40 n-4 n+441以上 (1-12%)?n (1+12%)?n 表6 点焊缺陷判断序号检查项目图示检查方式检验工具检验标准1、钢板被拉超过紧靠焊点周围的厚目视测1 拉痕度的两倍,就判定该焊点有缺陷。
量2、缺陷焊点数不得大于10%目视测1、母材扭曲变形超过焊接面30度 2 扭曲量 2、缺陷焊点数不得大于10%1、焊点不得超过焊接钢板的边缘 3 咬边目视2、缺陷焊点数不得大于10%1、脱离的焊点部位不能超过焊点直径的1/3; 目视测4 脱离 2、对于棱角、圆角部位,不容出现量脱离正确位置的焊点。
3、缺陷焊点数不得大于10%1、S=从熔核直径超过2.0mm以上的飞溅(焊为不良接面上焊目视测52、e=从熔核直径超过5.0mm以上的接液呈毛量为不良刺状)3、不允许超过总点数的15%1、被电极压的深度为较薄板的70%目视测以下时,但要求钣金的外部压锻为6 压痕过深量 90%以下时判为压痕过深2、不允许超过总点数的20%目视测1、A/B<0.8的情况为不良 7 焊接痕迹量 2、不允许超过总点数的20%A:窄处 B:宽处序号检查项目图示检查方式检验工具检验标准1、孔洞直径D=1.5mm以上为不良焊后 8 目视测量2、D?1.5mm的情况下不允许超过孔洞总点数的5%半破坏试1、无熔核或熔核过小,按表3检9 虚焊验/破坏试扁铲、锤子验验 2、缺陷焊点数量超过1% 10 焊穿目视缺陷焊点数不得大于10% 11 漏焊目视缺陷焊点数不得大于10% 12 开裂目视开裂焊点数不得大于1% 焊偏数?10%,偏离位置小于等于13 焊偏目测 3mm。
缺陷焊点数不得大于10%2、凸焊a、外观质量:无螺纹损伤、裂纹,允许有轻微飞溅和少量的金属挤出,但不影响螺栓拧入;不允许有漏焊、错焊、未焊透、焊接变形等缺陷。
b、凸焊螺母螺栓抗扭强度应符合要求,若不合格必须重新凸焊,或用CO2保护焊加固; c、关键零件凸焊螺母不允许有裂纹,一般零件凸焊螺母若有裂纹,允许用CO2保护焊补焊; d、检验方法说明:1)螺母螺纹检验法:选用与工件上凸焊螺母相配的螺纹螺栓,要求不能借用任何工具,直接用手能将螺纹螺栓顺利拧入螺母孔内,则为合格;反之螺纹螺栓或拧入困难,则为不合格。
2)螺栓螺纹检验法:选用与工件上凸焊螺栓相配的螺纹螺母,要求不能借用任何工具,直接用手能将螺纹螺母顺利拧入螺栓上,则为合格;反之螺纹螺母不或拧入困难,则为不合格。
3)产品强度检验:将工件固定在工作台上,把扭力扳手上的专用套筒套在螺母及螺栓上,用手扳动扭力扳手。
如工件上螺母及螺栓承受规定的扭力而不脱落,则为合格;如试片上螺母及螺栓承受的扭力未达到要求或达到要求后脱落,则为不合格。
表7 螺母凸焊抗扭强度参数:螺母规格 M5 M6 M8 M10 7/16″ M12 M14 扭矩(N?m) ?40 ?50 ?60 ?80 ?90 ?100 ?140 表8 承面凸焊螺栓抗扭强度参数: 承面凸焊螺栓规格 M4?L M5?L M6?L M8?L M10?L M12?L抗扭强度(N•m) ?6 ?10 ?25 ?50 ?90 100 e、检验频次:抽检:每批次1次,每次5件。
3、保护焊a、焊缝外观质量:焊缝表面均匀、光滑、平整,焊缝宽度均匀;b、焊缝质量缺陷判断见表9;焊缝出现下表所述质量问题,则分总成质量不合格。