精益单元化生产简介与案例
精益生产在中国成功的经典案例
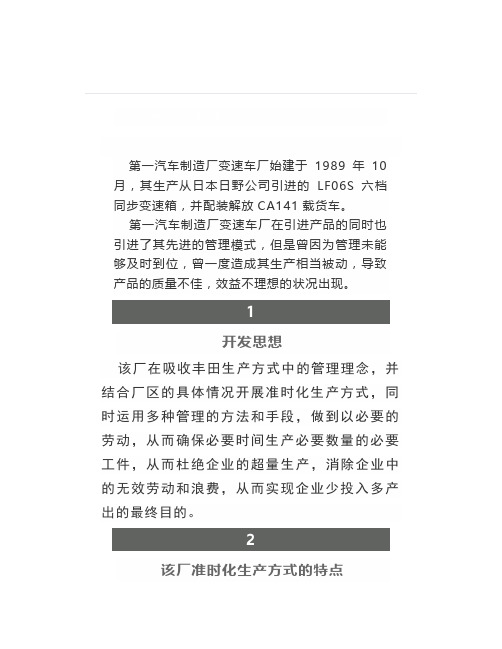
第一汽车制造厂变速车厂始建于1989年10月,其生产从日本日野公司引进的LF06S六档同步变速箱,并配装解放CA141载货车。
第一汽车制造厂变速车厂在引进产品的同时也引进了其先进的管理模式,但是曾因为管理未能够及时到位,曾一度造成其生产相当被动,导致产品的质量不佳,效益不理想的状况出现。
1开发思想该厂在吸收丰田生产方式中的管理理念,并结合厂区的具体情况开展准时化生产方式,同时运用多种管理的方法和手段,做到以必要的劳动,从而确保必要时间生产必要数量的必要工件,从而杜绝企业的超量生产,消除企业中的无效劳动和浪费,从而实现企业少投入多产出的最终目的。
2该厂准时化生产方式的特点01.目标明确,系统性强。
围绕提高产品质量,降低成本,满足市场需求的目标,进行“配套设计,同步实施”的开发与建议方式02.采用“拉动式”生产组织方式。
变“推动式”生产为“拉动式”生产组织方式,以市场需求为目标组织生产03.向工序间在制品为“0”进军。
04.实行“一人多机”操作。
实行U形生产设备布置,“一人多机”操作,大大提高劳动生产率05.工具定置集配,精度刀具强制换刀与跟踪管理。
06.“三为”现场管理。
强调观念更新,以生产现场为中心,生产工人为主体,车间主任为首的“三为”管理体制。
一切后方部门围绕准时化生产服务,使生产不停地创造附加价值07.生产现场实行“5S”活动——整顿、整理、清扫、清洁和素质。
08.实行“三自一控”、“创合格”、“深化工艺”、“五不流”和“产品创优”的“五位一体”的管理体系。
3实施效果经过1年多的实践,准时化生产方式使工厂面貌产生巨大变化。
1、生产能力大幅度提高,实现均衡生产原设计能力 6.8万台/年,92年实施准时化生产后实现8000台/月生产水平。
产品品种由原来1个基本型发展为18个改型产品。
2、产品质量稳步提高 91年废品率下降35%,一次装配合格率由80%提高到92%,市场占有率大幅度提高。
3、推行看板管理,在制品大幅度下降在制品流动资金占用从91年初的700万下降到年底的350万,下降了50%,92年月产量增加了25%,而流动资金下降到300万。
某汽车公司精益生产改善案例

某汽车公司精益⽣产改善案例某汽车公司精益⽣产改善案例某汽车零部件公司⽣产现状及精益⽣产改善⽅案⼀、某汽车零部件公司⽣产现状某汽车零部件公司为提⾼职⼯的⽣活⽔平,每年进⾏调薪并提供各种福利。
近⼏年随着国际能源价格的⾛⾼。
原材料价格也持续提⾼,但该公司产品价格没能同步反应,这导致该公司运营成本上升,利润率降低。
共次在产品上的竞争愈演愈烈,导致该公司争取新业务时需要更具竞争⼒的价格,更加影响了本已不多的利润空间。
利润空间的减少需要通过节约运营成本,提⾼⽣产效率来加以弥补。
.通过该公司的调查发现其主要⾯临以下问题:1、⽣产⽅式落后,统⼀下发⽣产计划进⾏推动式⽣产使各车间成为“孤岛”。
现场、库房存在⼤量库存,占⽤⼤量空间和资⾦,同时带来质量隐患;2、设备管理粗放,很少关⼼设备利⽤率,设备停机、换模时间较长;3、现场管理松散,⽣产效率低。
该公司要想⽣存和发展就必须开始进⾏持续改进和成本控制,要达到这⼀⽬的该公司需要优化调配⼈员、设备、资⾦等资源,使它们发挥最⼤效益。
“没有⼀个国家可以在低廉的⼯资基础上在全球竞争中建⽴长时间的绝对优势,但可以通过精益⽣产和精益理念来维系优势”。
⼆、该公司精益⽣产改善⽅案借助价值流图析法分析,价值流是当前产品通过其基本⽣产过程所要求的全部活动。
这些活动包括增加价值和不增加价值两部分,简单地说包括从供应商到⼯⼚制造再到顾客交付的过程。
.⾸先确定实施精益⽣产⽅式的产品线,然后对选取的产品线进⾏研究。
收集数据,绘制现阶段的价值流程图。
通过对现有价值流程图的分析,找到需要改进的地⽅并运⽤精益的改善⼯具提出改进⽅案。
绘制未来改进后的价值流程图,实施精益⽣产⽅式,验证改进效果。
通过对该公司精益⽣产的探索和研究,共对打公司的⽣产管理⽅式做了如下改善:1、⽬视化管理为了更⽅便的掌握⽣产情况,对该公司进⾏⽬视化管理。
设⽴控制中⼼,将需要的信息集中展⽰。
按照管理层级的不同将控制中⼼分为:⽣产单元控制中⼼、⼯⼚控制中⼼,运营控制中⼼。
单元化生产实施方案

单元化生产实施方案随着工业化和自动化水平的不断提高,单元化生产已经成为了现代制造业的主流趋势。
单元化生产是指将整个生产过程分解成多个独立的单元,每个单元负责特定的生产环节,通过协同合作完成整个产品的制造。
单元化生产可以提高生产效率、降低成本、提高产品质量,因此在各个行业都得到了广泛的应用。
本文将介绍单元化生产的实施方案,包括单元化生产的基本原理、实施步骤、关键技术和应用案例。
一、单元化生产的基本原理单元化生产的基本原理是将整个生产过程分解成多个独立的单元,每个单元负责特定的生产环节。
每个单元都是一个相对独立的生产单元,可以根据需要进行组合和拆分,从而适应不同的生产需求。
通过协同合作,各个单元共同完成整个产品的制造。
单元化生产的核心是将复杂的生产过程分解成简单的单元,通过协同合作实现高效生产。
二、单元化生产的实施步骤1. 制定单元化生产计划。
首先需要对整个生产过程进行分析,确定可以分解的单元和各个单元之间的协作关系。
然后制定单元化生产的实施计划,包括分解方案、组合方案、协作方案等。
2. 设计单元化生产系统。
根据单元化生产计划,设计单元化生产系统,包括单元化设备、单元化工艺、单元化控制系统等。
单元化设备需要具备灵活性和通用性,能够适应不同的生产需求。
单元化工艺需要简单可靠,易于操作和维护。
单元化控制系统需要实现各个单元之间的协作和协调。
3. 实施单元化生产系统。
根据设计方案,逐步实施单元化生产系统,包括采购单元化设备、调试单元化工艺、建立单元化控制系统等。
在实施过程中需要不断优化和调整,确保单元化生产系统能够稳定运行。
4. 进行单元化生产培训。
对生产人员进行单元化生产培训,包括单元化设备操作、单元化工艺流程、单元化控制系统操作等。
确保生产人员能够熟练掌握单元化生产技术,保证单元化生产系统的正常运行。
5. 完善单元化生产管理体系。
建立完善的单元化生产管理体系,包括单元化生产计划、单元化生产调度、单元化生产监控等。
《单元生产简介》课件

03
单元生产模式下的生产单元可以独立调整和优化,有助于企业实现资源节约、减少浪费,从而促进绿色生产和可持续发展。
单元生产模式能够提高企业的生产效率和灵活性,降低成本,从而增强企业的市场竞争力。
提高企业竞争力
促进企业组织变革
引领行业变革
单元生产模式要求企业组织结构更加扁平化、决策更加集中化,有助于企业实现组织变革和优化。
《单元生产简介》ppt课件
目录
单元生产概述单元生产的历史与发展单元生产的优势与挑战单元生产实施案例单元生产与精益生产的关系单元生产的前景展望
01
CHAPTER
单元生产概述
单元生产是一种将生产线划分为一系列独立的工作单元,每个工作单元配备相应的设备和人力,完成特定工序的生产方式。
单元生产定义
单元生产起源于日本,为了适应多品种、小批量、定制化生产的需要,提高生产效率和灵活性而发展起来的一种生产模式。
汽车制造业是单元生产应用最为广泛的领域之一,涉及冲压、焊接、涂装、总装等多个工艺环节。
汽车制造业
电子产品制造中,单元生产广泛应用于装配、检测、包装等环节,满足多品种、小批量的生产需求。
电子产品制造
机械制造业中,单元生产应用于各种零件的加工、装配和检测,提高生产效率和产品质量。
机械制造业
除了上述行业,单元生产还广泛应用于家具、服装、化工等其他行业,帮助企业实现高效、灵活的生产管理。
其他行业
02
CHAPTER
单元生产的历史与发展
单元生产起源于日本,最初是为了满足多品种、小批量生产的需求。
20世纪70年代,日本汽车制造商开始采用单元生产方式,以提高生产效率和灵活性。
单元生产的出现,解决了传统流水线生产方式在应对多品种、小批量生产时的局限性。
非常好的精益生产案例值得借鉴

非常好的精益生产案例值得借鉴前言精益生产是一种专注于提高效率和降低浪费的经营管理方法。
通过消除不必要的步骤和资源浪费,精益生产可以帮助企业实现更高的产出和更好的质量,从而获得竞争优势。
本文将介绍一些非常好的精益生产案例,展示出这种方法的实际应用和可行性,以供其他企业借鉴。
案例一:丰田汽车丰田汽车是精益生产的经典案例之一。
丰田公司以“丰田生产方式”(Toyota Production System,TSP)闻名于世。
TSP 的核心思想是通过限制生产速度来提高质量,消除浪费和降低成本。
丰田将员工视为最重要的资源,鼓励员工参与改进流程,并不断学习和提高。
通过实施流程改进和标准化操作,丰田成功地降低了库存水平、缩短了交付周期,并提高了产品的质量。
流程改进丰田汽车通过实施精细的生产计划和精确的生产控制来改进流程。
他们使用所谓的“拉动式生产”(Pull Systems),这意味着生产进程只会在下一阶段需要材料和部件时才会启动,以此保持生产流程的稳定性。
这种方式可以防止过度生产和库存积压,并减少浪费。
标准化操作丰田汽车非常注重标准化操作。
他们制定了详细的作业指导书,确保每位员工都能按照标准程序工作。
通过标准化操作,丰田能够减少错误和变量,并提高整体生产效率。
标准化操作还使得员工之间可以互相替代,以应对人员变动和流程变化。
持续改进丰田汽车秉持着“持续改进”的信念。
他们鼓励员工积极参与改进流程,并通过小改进和创新来不断提高生产效率和质量。
丰田实行所谓的“就地解决问题”(Genchi Genbutsu),即员工应该亲自去现场了解问题并找到解决方案。
这种方法帮助丰田构建了一个持续改进的文化,使得所有员工都在努力寻找问题并付诸行动。
案例二:美国空军美国空军也是一个非常成功的精益生产案例。
空军一直致力于在各个领域实施精益生产,以提高效率、降低成本,并最大限度地满足任务需求。
下面将以飞机维修作业为例,介绍空军如何运用精益生产方法改进维修流程:改进维修流程空军通过改进维修流程来提高效率。
精益生产案例

精益生产是一种以最大限度地减少运营成本为主要目标的生产方式精——少而精,不投入多余生产要素,只在适当时间生产必要的产品 益——所有经营活动有益有效,具有经济性特点:(1)消除一切浪费(2)追求精益求精和不断改善(3)去掉一切不增值的岗位核心:精简某企业的生产车间接到任务,要生产一组产品,需要经过铣、钻、磨、装配和打包等六道工序,每周生产3200件,所有这些产品的加工过程相似,需要的工人相同。
该企业每周工作5天,每天工作8小时。
生产指定产品每道工序的单位加工时间:工序 加工时间/s 工序 加工时间/s 铣 80 装配线1 80钻 30 装配线2 180磨 60 包装 30现对其进行精益化改造,经调查:1.铣、钻、磨床尚有剩余生产能力,因此在不影响其它生产条件下,可进行适当调整2.所有装配线和包装依靠手工完成,只需提供工作台和工具3.目前该生产单元按工艺专业化布置。
因为加工次序和优先级别不同,使生产很难达到应有的熟练程度,生产拖拖沓沓,有时还需推迟交货时间,要么经常加班加点才能完成任务。
生产成本高,顾客意见大 步骤1:计算单件产品生产时间步骤2:计算符合单件产品生产时间每小时的生产量步骤3:计算每道工序的每小时的生产能力,以及每道工序所需工作台的数目 包装unit s wunits m s h m w h /45/3200/60/60/40=⨯⨯h units unit s ms h m /80/45/60/60=⨯h units unit s m s h m /120/30/60/60=⨯167.0/120/80<=h units h units(取一个工作台,尚有生产能力剩余)装配线2(取4个工作台) 装配线1(取2个工作台,尚有生产能力剩余) 铣、钻、磨:这几道工序有长有短,必须平衡各道工序的劳动利用率。
设置一个微型加工单元,把铣、钻、磨有机地结合起来,并且只要一个工人完成这三项操作。
精益生产案例

精益生产案例引言精益生产是一种通过最大限度地减少浪费,提高生产效率和产品质量的方法。
它始于丰田生产系统,如今已经被广泛应用于各种行业和组织中。
本文将介绍三个精益生产的案例,以展示其在不同领域的应用。
案例一:汽车制造在汽车制造业中,精益生产被广泛用于提高生产效率和降低成本。
丰田汽车公司是精益生产的典型代表之一。
他们采用了精益生产的原则和技术,通过提高生产线的流程效率,使得汽车制造过程更加高效和可持续。
丰田的生产线采用了“单件流水线”模式,每个工人都负责完成整个工作过程,从而减少了不必要的等待和处理时间。
此外,丰田还推崇“质量至上”的原则,通过在每个生产环节中设置严格的质量控制标准,确保产品质量。
另一个值得注意的案例是日本的一个零件制造公司。
该公司通过消除浪费和优化工作流程,成功地提高了生产效率。
他们分析了原本复杂的生产流程,将其简化为一系列简单的步骤,让每个工人都能清楚地知道自己的工作内容和目标。
案例二:医疗服务精益生产同样适用于医疗服务行业。
一个典型的案例是德国某医院的急诊科。
该医院采用了精益生产的原则和工具,通过优化流程和增加资源的使用效率,将就医时间缩短了70%。
在过去,患者在急诊科等待就医时间往往较长。
该医院通过对患者流程进行重新设计,将患者按照病情严重程度进行分类,并在每个分类中设置不同的诊疗团队。
这样,医护人员可以更有效地处理患者,避免了等待时间过长的问题。
此外,该医院还引入了标准化的医疗流程,并充分利用ICT技术,提供了在线预约、电子病历等便捷服务。
这些措施不仅提高了医疗服务的质量,也提高了患者的满意度。
案例三:酒店管理精益生产的原则也可以应用于酒店管理领域。
一个例子是一家高端度假村酒店。
这家酒店通过精益生产的方法,优化了业务流程,提高了客户满意度,并在市场上取得了成功。
首先,酒店管理团队对酒店的工作流程进行了深入分析,并找出了其中的浪费和问题。
然后,他们采取了一系列措施,如优化客房清洁流程、提高服务质量等。
单元生产简介
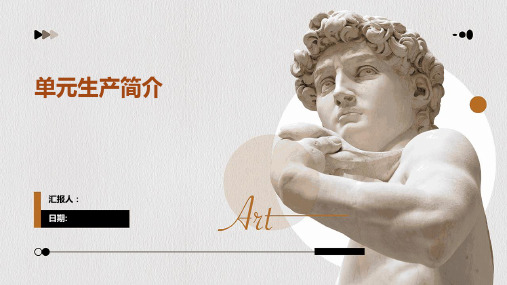
通过优化资源配置、提高生产效率等方式降低生产成本。
低成本
采用先进的生产管理方法和自动化设备,提高生产效率。
高效率
生产方式
生产效率
适用范围
资源配置
单元生产由于多品种、小批量的特点,生产效率相对较低,而批量生产通过规模化生产,具有较高的生产效率。
单元生产适用于多品种、小批量、定制化的生产需求,而批量生产适用于大批量、单一品种的生产需求。
绿色制造和环保是未来制造业的重要发展方向,单元生产也不例外。
智能化和自动化是未来制造业的重要特征,单元生产也不例外。
智能化和自动化技术的应用,将使单元生产更加高效、灵活和可靠,同时也可以提高生产的质量和精度,满足高端制造业的需求。
未来,单元生产的智能化和自动化将与信息化、网络化深度融合,实现更加智能、高效、可靠的生产。
单元生产采用精益生产中的拉动式生产、单件流、快速换模等核心方法,实现快速响应市场需求和高效利用资源。
改进生产流程
通过对生产流程进行分析和优化,消除浪费和瓶颈,提高生产效率和质量。
实施可视化管理
通过数据采集和分析,实时监控生产过程和质量,发现问题及时处理,提高管理效率和决策水平。
提升员工技能
加强员工技能培训和职业发展,提高员工的技能水平和综合素质,实现员工与企业的共同发展。
优化生产计划
采用拉动式生产方式,根据客户需求进行排产,避免过度生产和库存积压。
05
CHAPTER
人工智能、物联网、云计算等,将为单元生产带来更多的智能化和自动化,提高生产效率和降低成本。
单元生产作为制造业的重要生产方式,未来将更加注重持续改进与创新,以适应不断变化的市场需求和提高企业竞争力。
单元生产需要针对不同品种的产品进行资源优化配置,而批量生产由于规模化生产的特点,对资源配置的要求相对较低。
- 1、下载文档前请自行甄别文档内容的完整性,平台不提供额外的编辑、内容补充、找答案等附加服务。
- 2、"仅部分预览"的文档,不可在线预览部分如存在完整性等问题,可反馈申请退款(可完整预览的文档不适用该条件!)。
- 3、如文档侵犯您的权益,请联系客服反馈,我们会尽快为您处理(人工客服工作时间:9:00-18:30)。
Lops
All For Results
精益单元化流程生产概述
流程分工作业
个人独立作业
Lops
All For Results
单元化生产概述 二:单元化生产特点
1. 后续工序流程、批量生产及单个制作 2. 空间上的利用 (Spacing Saving) 3. 多能工化 (Skill up! Multi-job!) 4. 部件供应、产品输出
15.43 12.74 11.41 13.97 13.15 14.35
A、瓶颈工时=工位最长工 时26.73 B、两单元作业人数=10人 C、工序总时间=254.12S D、生产线平衡率=95.06%
1
2
3
4
5
6
7
8
9
10
30.00 25.00 20.00 15.00 10.00 5.00 0.00
讲师:郭锡兰/Terry Guo 日期:2006年12月21日
Lops
All For Results
现状与对策
现状
生产线平衡率不超过75%,但由于各工位作业周期较短(小于20 秒),难以在现有基础上直接改善平衡率 测试用老化架自动化程度不高,加水、升降火锅等动作皆需人工 作业,老化产能为216台/(每小时.架),成为总装效率进一步提升 的瓶颈 外箱、彩箱成型由作业员在隔楼完成,利用滑道滑至作业员旁, 但经常造成堆积,或外箱、彩箱数量不配套,造成短时缺料 生产时作业员位于“U”线内,组装所需物料无法被方便地送至适当 位置,导致作业员增加了非创造价值动作
Lops
All For Results
达成结果
20.00 18.00 16.00 14.00 12.00 10.00 8.00 6.00 4.00 2.00 0.00 18.25 13.69 12.98 10.86
A 、瓶颈工时 = 工位最长工 时18.25 B、流水线作业人数=10人 C、工序总时间=136.83S D、生产线平衡率=75%
备注:数据来源于总装车间综合日报表(10月16日~10月22日)
Lops
All For Results
达成结果
线体区域由32mX8m,优化为29mX6m, 每线可节少面积82m²
Lops
All For Results
达成结果
之前:“U”形线体
之后:“CELL”线
Lops
All For Results
继承了流水线的一切优点,同时能够适应 小批量、多品种的苛刻要求,被誉为“看不 见的传送带”
Lops
All For Results
单元化生产的实施程序
1. 分析适合单元生产的产品
1.根据市场预测,对相关产品按产值进行ABC分类,确定重要、关键产品 2.以重要产品为对象,为分析、优化、组合相关产品、工序、所需设备等
Lops
All For Results
零件组合加工
问题: 单种零件生产导致大量边料损失
解决方案: • 在CNC冲压上,多个零件配套同时冲压 • 在同一弯板机上,一次为多个产品设置弯板模具,以减少前置时间、 减少生产批量,并提高品质率 •加工程序按单元编制,并实时调整加工程序
Lops
All For Results
Lops
All For Results
精益单元化生产概述与案例
讲师:郭锡兰/Terry Guo 日期:2006年12月21日
Lops
All For Results
内容说明
精益单元化生产概述 精益单元化生产布局--钣金冲压 精益单元化总装线设计--生活家电
Lops
All For Results
典型钣金数控冲压制造单元 弯板 机
数控 冲床
制造单元
铆钉 机
Lops
All For Results
典型钣金数控冲压制造单元
Lops
All For Results
单元化生在钣金冲压行业的典型布局
1. 根据钣金加工特点,一生产单元一般配置1台数控冲床、2台弯板机作 为主要设备 2. 辅助设备类型及数量按工序需要进行配置,如铆钉机、攻丝机、钻床、 焊接机、打磨房、预装配线等 3. 每单元所需生产零件,预先指定,便于刀模设置、优化;生产计划安 排 4. 配置人员需经培训,适应多种工序操作,以适应单元生产。配置现场 作业人数为3名/单元。 5. 各单元设有备料区、废料区,方便物料集中处理 6. 注意零件表面防护,避免在输送过程中损伤 7. 计划板、指示灯及等
达成案例
单元化生产
生产单元计划板
闪烁黄灯:补料
刀具管理与维护LopsAll ForResults达成案例
可视化员工看板
单元状态显示灯:绿色表示正常;黄色 表示需补料;红色表示异常停机
生产计划信息板
Lops
All For Results
精益生产单元化总装线
美的电磁炉公司总装线单元化设计 --生活家电
2. 工程的同期化
1.作业标准化 2.及时EC导入 3.实时根据生产需求,优化或调整产品加工工艺及加工组合
Lops
All For Results
精益单元化制造生产布局
制造单元--钣金数控冲压典型单元布局
讲师:郭锡兰/Terry Guo 日期:2006年12月21日
Lops
All For Results
达成结果
之前:需滑道,造成堆积
之后:不需滑道,摆放整齐
Lops
All For Results
所用精益工具
精益单元化生产概念 模特法----员工作业动作分析 2箱系统----在线物料配送、补充 5S、目视化控制----火锅加水线 看板 ---- 在线物料需求信息传递 线平衡分析 …..
精益单元化流程生产概述
一:单元化生产定义
1. 单元化生产是精益生产的核心 2. 单元生产方式是强调进行工序的改善,建立并运用组装、零部件加工、 原材料三要素的协同生产体系 3. 目的是节约资源、缩短交付期、减少库存等 4. 已被美的、松下电器、戴尔计算机、佳能公司、奥林巴斯、理光公司 等广泛采用
Lops
All For Results
现状与对策
对策
导入单元作业理念,将测试前组装段设计成并行的两个作业单 元,以减少工位,适当放慢组装段员工作业节拍,最大限度提升 线平衡率 同时皆顾激光打码机、安全分析仪、打包机等设备的利用率,在 测试、包装段仍为一个单元的流程作业 重新设计老化架方案,增加老化产能,实现半自动化,如自动加 水功能、自动升降等 组装2单元中,员工面对面作业,方便物料员直接将物料 送至适当位置
25.42
25.3
25.37 24.92 26.12 26.73 24.31 24.13 25.77 26.05
生产线平衡 率提升18%
1.1
1.2
2.1
2.2
3.1
3.2
4.1
4.2
5.1
5.2
Lops
All For Results
达成结果
线别 2A 2B 4A 4B 5A 5B 7A 7B 11A 11B 12A 13A 17B 主要生产机型 EP192H EP192H EP186 EP186 EF197B EF197B EP192H EP192H SH2112 SH2112 SH2112 SP201C+EP186 SH2115 产能(PPH) 改善前 改善后 192 192 192 192 192 192 192 192 192 192 192 192 192 270 260 246 253 247 233 257 249 217 227 217 219 236 在线人数 改善前 改善后 28 28 28 28 28 28 28 28 28 28 28 28 28 28 28 28 28 28 28 28 28 27 27 27 27 27 PPO 提升百分点 改善前 改善后 6.88 6.88 6.88 6.88 6.88 6.88 6.88 6.88 6.88 6.88 6.88 6.88 6.88 9.64 9.30 8.79 9.05 8.81 8.33 9.19 8.89 8.02 8.42 8.05 8.09 8.75 40.06% 35.14% 27.75% 31.48% 28.12% 21.01% 33.65% 29.24% 16.56% 22.41% 16.95% 17.65% 27.19%
2. 工场布局
1.根据零件组工序要求,将相关设备按加工工序需要进行单元化布局,以 实现单元内“单件制造”,减少工序间般运 2.同时,根据市场信息、单位时间产能,进行产能分析,以确定对应单元 所需的数量和产能计划
3. 生产管理及计划
1.生产人员按单元生产需要进行分配、管理 2.生产计划以生产单元为单位进行统筹安排
4. 教育培训、意识……其他
1.员工技能提升,为实现“多能工” 2.团队合作,自我激励,等
Lops
All For Results
单元化生产提升效果的关键
1. 与供方共存、相互关联,竭力创建稳定无间断流程
1.客户或下道工序的真实需求通过系统拉动产品生产 2.库存即是浪费 3.上一道工序加工完的零件立即可进入下一道工序 4.看板传递工序间需求信息,且形式不限,关键在于传递信息 5.生产中节凑必须保持平衡(各工序对下工序准时交货) 6.计划实质上由各生产单元自已控制、完成
Lops
All For Results
单元化总装线达成目标
线平衡率由75%提升至95% 在线员工数量由30人/线减至28人/每线 老化产能由每小时216台,提升为每小时288台 老化架实现加水、升降自动化,节省了员工作时间, 虽然产能已大幅提升,但不需额外增加作业员 方便了在线物料配送,取消了原在线备料区,从而减 少了在线库存 线体区域由32mX8m,优化为29mX6m,每线可节少 面积82m²