丁苯橡胶SBR)是以丁二烯和苯乙烯为单体,采用自由基引发的乳液
丁苯橡胶的生产工艺及技术进展【精选】

丁苯橡胶的生产工艺及技术进展丁苯橡胶是丁二烯和苯乙烯两种单体经共聚合反应而生成的弹性体共聚物。
按聚合工艺方法可分为乳聚丁苯橡胶(ESBR)和溶聚丁苯橡胶(SSBR)两大类。
从聚合机理来看,ESBR是自由基聚合,而SSBR是采用阴离子活性聚合。
ESBR的发展已过鼎盛时期,而SSBR的发展目前正处于稳步上升阶段。
2.1 丁苯橡胶的分类及品种2.1.1 乳聚丁苯橡胶的生产工艺乳聚丁苯橡胶(ESBR)的生产历史悠久,乳聚丁苯橡胶是通过自由基聚合得到的,在20世纪50年代以前,均是高温丁苯橡胶,1937年由德国Farben公司首先实现工业化,它是当前合成橡胶中生产能力最大的品种。
50年代初才出现了性能优异的低温丁苯橡胶。
目前所使用的乳聚丁苯橡胶基本上为低温乳聚丁苯橡胶。
羧基丁苯橡胶是在丁苯橡胶聚合过程中加入少量(1~3%)的丙烯酸类单体共聚而制成。
其力学性能和耐老化性能等较丁苯橡胶好。
但这种橡胶吸水后容易早期硫化,工艺上不易掌握。
高苯乙烯丁苯橡胶是将苯乙烯含量为85~87%的高苯乙烯树脂胶乳与丁苯橡胶(常用SBR1500)胶乳以一定比例混合后经共凝得到的产品。
乳聚丁苯橡胶的工业生产方法有高温聚合(又称热法)和低温聚合(冷法)两种。
高温聚合所得产品的分子量较低、文化度较大,分子量分布较宽,在质量上都不如低温聚合产品,目前很少采用。
因此,这里只叙述低温连续法乳液聚合生产工艺。
1、工艺流程简述…图2.1 乳液聚合生产丁苯橡胶工艺流程图如生产充油胶,则需在胶乳中加入定量的高芳烃油或环烷烃油,充分混合后,送去凝聚,后续工序同上。
表2.1 典型低温乳液聚合生产丁苯橡胶配方表2、聚合配方及聚合工艺条件乳液聚合配方和工艺条件是决定橡胶质量最关键因素。
经过几十年的工业生产实践,乳聚丁苯橡胶的生产技术、工艺过程、聚合配方和品种牌号都具有相当程度的国际规范化。
当前的改进都侧重在节能、环保及自控方面,或是调整开发一些急需专用性品种,以满足市场需求。
丁苯橡胶SBR
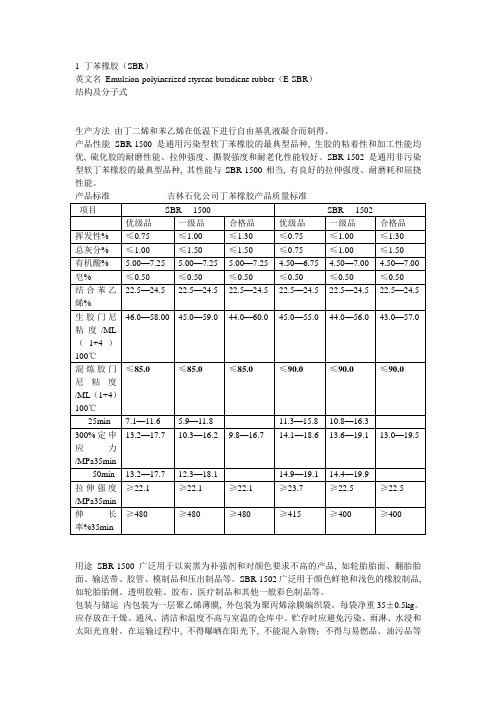
1 丁苯橡胶(SBR)
英文名Emulsion-polyinerized styrene butadiene rubber(E-SBR)
结构及分子式
生产方法由丁二烯和苯乙烯在低温下进行自由基乳液凝合而制得。
产品性能SBR-1500是通用污染型软丁苯橡胶的最典型品种, 生胶的粘着性和加工性能均优, 硫化胶的耐磨性能、拉伸强度、撕裂强度和耐老化性能较好。
SBR-1502是通用非污染型软丁苯橡胶的最典型品种, 其性能与SBR-1500相当, 有良好的拉伸强度、耐磨耗和屈挠性能。
产品标准吉林石化公司丁苯橡胶产品质量标准
用途SBR-1500广泛用于以炭黑为补强剂和对颜色要求不高的产品, 如轮胎胎面、翻胎胎面、输送带、胶管、模制品和压出制品等。
SBR-1502广泛用于颜色鲜艳和浅色的橡胶制品, 如轮胎胎侧、透明胶鞋、胶布、医疗制品和其他一般彩色制品等。
包装与储运内包装为一层聚乙烯薄膜, 外包装为聚丙烯涂膜编织袋。
每袋净重35±0.5kg。
应存放在干燥、通风、清洁和温度不高与室温的仓库中。
贮存时应避免污染、雨淋、水浸和太阳光直射。
在运输过程中, 不得曝晒在阳光下, 不能混入杂物;不得与易燃品、油污品等
堆放在一起。
运输车箱应保持清洁, 避免包装破损和杂物混入, 敞车运输要盖防雨布。
本产品保质期为两年。
生产企业吉林石化公司。
丁苯橡胶制备实验报告(3篇)

第1篇一、实验目的1. 了解丁苯橡胶的合成原理及制备方法。
2. 掌握乳液聚合反应的基本操作和实验技能。
3. 分析丁苯橡胶的性能及其影响因素。
二、实验原理丁苯橡胶(SBR)是一种合成橡胶,由丁二烯和苯乙烯在引发剂的作用下进行乳液聚合反应而成。
该反应过程为自由基聚合反应,具体原理如下:\[ n\text{C}_4\text{H}_6 + n\text{C}_6\text{H}_5\text{CH}=CH_2\rightarrow (\text{C}_6\text{H}_5\text{CH}-\text{CH}_2\text{C}_4\text{H}_6)_n \]其中,C4H6代表丁二烯,C6H5CH=CH2代表苯乙烯,n为聚合度。
三、实验仪器与试剂1. 仪器:搅拌器、反应釜、温度计、压力计、真空泵、乳液聚合反应装置等。
2. 试剂:丁二烯、苯乙烯、引发剂(过氧化氢、过硫酸铵等)、乳化剂(十二烷基硫酸钠等)、调节剂(十二烷基苯磺酸钠等)、去离子水等。
四、实验步骤1. 准备反应釜,加入适量的去离子水。
2. 加入引发剂,搅拌均匀,待引发剂完全溶解。
3. 加入乳化剂,搅拌均匀。
4. 加入苯乙烯和丁二烯,搅拌均匀。
5. 将反应釜加热至预定温度,维持一段时间。
6. 冷却反应釜,终止聚合反应。
7. 离心分离乳液,得到丁苯橡胶乳液。
8. 将乳液干燥,得到丁苯橡胶粉。
五、实验结果与分析1. 实验结果根据实验条件,我们制备了不同分子量的丁苯橡胶。
实验结果表明,随着聚合温度、聚合时间、单体浓度等条件的改变,丁苯橡胶的分子量、门尼粘度、抗拉强度等性能也会发生变化。
2. 结果分析(1)聚合温度:温度对丁苯橡胶的分子量有显著影响。
温度越高,分子量越小。
这是因为高温有利于自由基的生成和迁移,导致链增长反应加剧,从而降低分子量。
(2)聚合时间:聚合时间对丁苯橡胶的性能也有一定影响。
随着聚合时间的延长,分子量逐渐增大,抗拉强度和硬度也随之提高。
制备丁苯橡胶实验报告
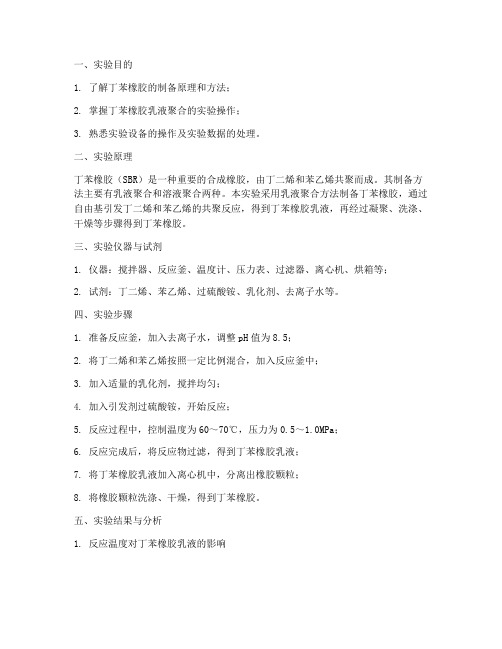
一、实验目的1. 了解丁苯橡胶的制备原理和方法;2. 掌握丁苯橡胶乳液聚合的实验操作;3. 熟悉实验设备的操作及实验数据的处理。
二、实验原理丁苯橡胶(SBR)是一种重要的合成橡胶,由丁二烯和苯乙烯共聚而成。
其制备方法主要有乳液聚合和溶液聚合两种。
本实验采用乳液聚合方法制备丁苯橡胶,通过自由基引发丁二烯和苯乙烯的共聚反应,得到丁苯橡胶乳液,再经过凝聚、洗涤、干燥等步骤得到丁苯橡胶。
三、实验仪器与试剂1. 仪器:搅拌器、反应釜、温度计、压力表、过滤器、离心机、烘箱等;2. 试剂:丁二烯、苯乙烯、过硫酸铵、乳化剂、去离子水等。
四、实验步骤1. 准备反应釜,加入去离子水,调整pH值为8.5;2. 将丁二烯和苯乙烯按照一定比例混合,加入反应釜中;3. 加入适量的乳化剂,搅拌均匀;4. 加入引发剂过硫酸铵,开始反应;5. 反应过程中,控制温度为60~70℃,压力为0.5~1.0MPa;6. 反应完成后,将反应物过滤,得到丁苯橡胶乳液;7. 将丁苯橡胶乳液加入离心机中,分离出橡胶颗粒;8. 将橡胶颗粒洗涤、干燥,得到丁苯橡胶。
五、实验结果与分析1. 反应温度对丁苯橡胶乳液的影响实验结果表明,反应温度对丁苯橡胶乳液的性能有较大影响。
随着反应温度的升高,丁苯橡胶乳液的分子量逐渐降低,聚合反应速率加快,但乳液稳定性变差。
因此,在实际生产中,应控制反应温度在60~70℃之间。
2. 反应压力对丁苯橡胶乳液的影响实验结果表明,反应压力对丁苯橡胶乳液的性能也有一定影响。
随着反应压力的升高,丁苯橡胶乳液的分子量逐渐降低,聚合反应速率加快。
但过高的压力会导致乳液稳定性变差,甚至出现暴聚现象。
因此,在实际生产中,应控制反应压力在0.5~1.0MPa之间。
3. 乳化剂种类对丁苯橡胶乳液的影响实验结果表明,不同种类的乳化剂对丁苯橡胶乳液的性能有较大影响。
其中,非离子型乳化剂具有较好的乳液稳定性,但乳液粘度较高;阴离子型乳化剂乳液粘度较低,但乳液稳定性较差。
丁苯橡胶
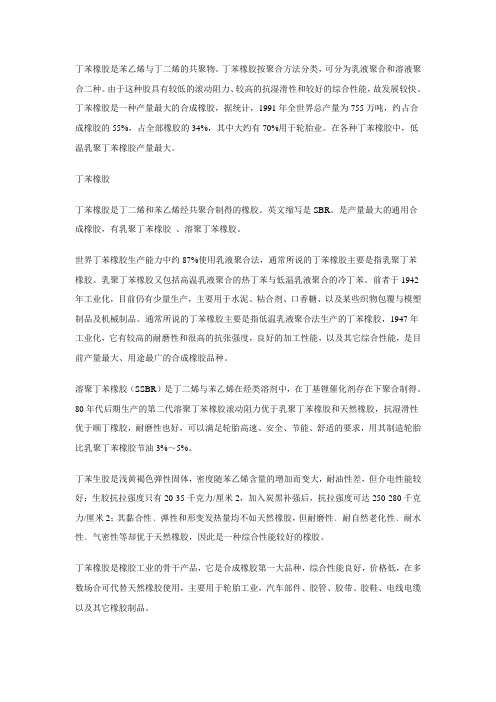
丁苯橡胶是苯乙烯与丁二烯的共聚物。
丁苯橡胶按聚合方法分类,可分为乳液聚合和溶液聚合二种。
由于这种胶具有较低的滚动阻力、较高的抗湿滑性和较好的综合性能,故发展较快。
丁苯橡胶是一种产量最大的合成橡胶,据统计,1991年全世界总产量为755万吨,约占合成橡胶的55%,占全部橡胶的34%,其中大约有70%用于轮胎业。
在各种丁苯橡胶中,低温乳聚丁苯橡胶产量最大。
丁苯橡胶丁苯橡胶是丁二烯和苯乙烯经共聚合制得的橡胶。
英文缩写是SBR。
是产量最大的通用合成橡胶,有乳聚丁苯橡胶、溶聚丁苯橡胶。
世界丁苯橡胶生产能力中约87%使用乳液聚合法,通常所说的丁苯橡胶主要是指乳聚丁苯橡胶。
乳聚丁苯橡胶又包括高温乳液聚合的热丁苯与低温乳液聚合的冷丁苯。
前者于1942年工业化,目前仍有少量生产,主要用于水泥、粘合剂、口香糖、以及某些织物包覆与模塑制品及机械制品。
通常所说的丁苯橡胶主要是指低温乳液聚合法生产的丁苯橡胶,1947年工业化,它有较高的耐磨性和很高的抗张强度,良好的加工性能,以及其它综合性能,是目前产量最大、用途最广的合成橡胶品种。
溶聚丁苯橡胶(SSBR)是丁二烯与苯乙烯在烃类溶剂中,在丁基锂催化剂存在下聚合制得。
80年代后期生产的第二代溶聚丁苯橡胶滚动阻力优于乳聚丁苯橡胶和天然橡胶,抗湿滑性优于顺丁橡胶,耐磨性也好,可以满足轮胎高速、安全、节能、舒适的要求,用其制造轮胎比乳聚丁苯橡胶节油3%~5%。
丁苯生胶是浅黄褐色弹性固体,密度随苯乙烯含量的增加而变大,耐油性差,但介电性能较好;生胶抗拉强度只有20-35千克力/厘米2,加入炭黑补强后,抗拉强度可达250-280千克力/厘米2;其黏合性﹑弹性和形变发热量均不如天然橡胶,但耐磨性﹑耐自然老化性﹑耐水性﹑气密性等却优于天然橡胶,因此是一种综合性能较好的橡胶。
丁苯橡胶是橡胶工业的骨干产品,它是合成橡胶第一大品种,综合性能良好,价格低,在多数场合可代替天然橡胶使用,主要用于轮胎工业,汽车部件、胶管、胶带、胶鞋、电线电缆以及其它橡胶制品。
锂离子电池粘结剂选择难题,终于有人能讲明白了
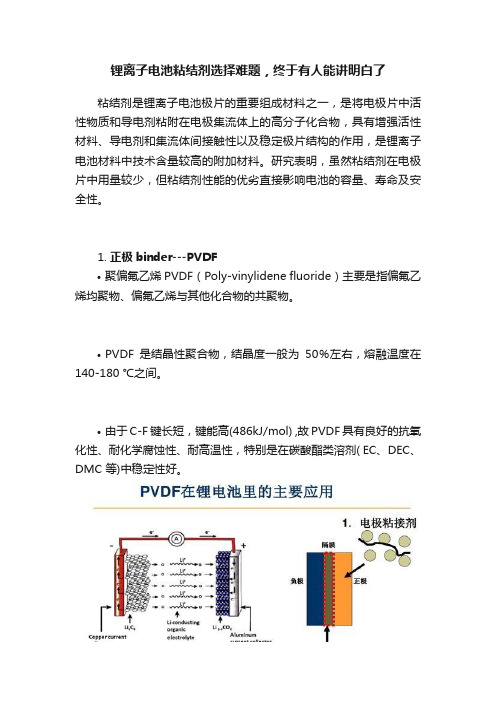
锂离子电池粘结剂选择难题,终于有人能讲明白了粘结剂是锂离子电池极片的重要组成材料之一,是将电极片中活性物质和导电剂粘附在电极集流体上的高分子化合物,具有增强活性材料、导电剂和集流体间接触性以及稳定极片结构的作用,是锂离子电池材料中技术含量较高的附加材料。
研究表明,虽然粘结剂在电极片中用量较少,但粘结剂性能的优劣直接影响电池的容量、寿命及安全性。
1.正极binder---PVDF•聚偏氟乙烯PVDF(Poly-vinylidene fluoride)主要是指偏氟乙烯均聚物、偏氟乙烯与其他化合物的共聚物。
•PVDF是结晶性聚合物,结晶度一般为50%左右,熔融温度在140-180 ℃之间。
•由于C-F键长短,键能高(486kJ/mol) ,故PVDF具有良好的抗氧化性、耐化学腐蚀性、耐高温性,特别是在碳酸酯类溶剂( EC、DEC、DMC 等)中稳定性好。
1.1 PVDF主要种类•均聚类PVDF,是VF2的均聚物,如HSV900, 5130等;•共聚物类PVDF,主要使用的是VF2(偏二氟乙烯)/HFP(六氟丙烯)的共聚物,如2801,LBG等。
1.2 PVDF合成方法通常由偏氟乙烯通过悬浮聚合或乳液聚合而成,反应方程式如下所示:CH2=CF2→(CH2CF2)n1.3 分子量对PVDF的影响•不同聚合度的VDF均聚物,其熔点温度差异不大;但PVDF分子量的大小会影响其在溶剂中的溶解难易程度。
•在一定分子量范围内,分子量的提高有助于粘结力和内聚力的提高;l改性对PVDF结晶度/溶胀度影响•掺杂的-HFP量越多,其结晶度越低,导致熔点相应降低;•结晶度降低,聚合物溶胀程度增大(甚至溶解)。
1.4 PVDF面临的问题与挑战过高分子量(>150W)对粘结力的提升效果不明显,但会造成更难溶解2. 负极binder---SBRSBR(丁苯橡胶乳液)由丁二烯及苯乙烯两种单体经自由基乳液聚合而成。
常用的锂离子电池SBR粘结剂除上述两种单体外,通常都引入了新的功能单体,用以提高其离子电导率或粘附力。
丁苯橡胶(SBR)是以丁二烯和苯乙烯为单体,采用自由基引发的乳液

丁苯橡胶(SBR)是以丁二烯和苯乙烯为单体,采用自由基引发的乳液聚合或阴离子溶液聚合工艺而得的,目前世界上产量最高,消费量最大的通用合成橡胶(SR)品种。
其物理机械性能、加工性能和制品的使用性能都接近于天然橡胶(NR),而且耐磨性、耐热性、耐老化性优于天然橡胶,并可与NR以及多种SR并用,广泛用于生产轮胎与轮胎制品、鞋类、胶管、胶带、医疗器械、汽车零部件、电线电缆以及其他多种工业橡胶制品。
按生产工艺,丁苯橡胶可以分为乳聚丁苯橡胶(ESBR)和溶聚丁苯橡胶(SSBR)两大类。
乳聚丁苯橡胶开发历史悠久,生产和加工工艺成熟,应用广泛,其生产能力、产量和消耗量在丁苯橡胶中均占首位。
溶聚丁苯橡胶是兼具多种综合性能的橡胶品种,其生产工艺与乳聚丁苯橡胶相比,具有装置适应能力强、胶种多样化、单体转化率高、排污量小、聚合助剂品种少等优点,是今后的发展方向。
1 世界丁苯橡胶的供需现状及发展前景1.1 生产现状近年来,世界丁苯橡胶的生产能力稳步增长。
2003年全世界丁苯橡胶的总生产能力为451.2万t/a,2006年增加到504.6万t/a,比2005年增长约6.5%,其中乳聚丁苯橡胶的生产能力为404.9万t/a,约占世界丁苯橡胶总生产能力的80.2%:溶聚丁苯橡胶的生产能力为99.7万t/a,约占总生产能力的19.8%。
北美、欧洲和亚洲地区是最主要的生产地区,生产能力分别约占世界总生产能力的22.2%、19.8%和38.6%。
美国固特异轮胎橡胶公司是目前世界上最大的丁苯橡胶生产厂家,2006年生产能力达到36.3万t/a,约占世界丁苯橡胶总生产能力的7.19%;其次是中国石油化工集团公司,生产能力为29.0万t/a,约占世界总生产能力的5.75%;再次是韩国锦湖石油化工公司,生产能力为27.5万t/a,约占世界总生产能力的5.45%;第4是日本合成橡胶公司,生产能力为26.8万t/a,约占世界总生产能力的5.31%。
我国丁苯橡胶的供需现状及发展建议

1生产现状
我 国丁苯 橡 胶 的研 究开 发始 于 2 世纪 5 o o年 代 中期 ,16 年 兰州 石油 化 工公 司 从前苏 联 引进 90
技术建成一套 13 . 万吨 /年乳聚丁苯橡胶生产装 置 。当时该装置只能生产热法乳聚丁苯橡胶,产 品质 量较 差, 需要 进行 热氧增 塑后才 能使 用 。
申华 公 司和 茂 名 石化 公 司都 可 以生 产 充油 产 品 。 齐鲁 石油 化工 公 司开 发的 S R 2 型 充油 丁苯橡 B1 7l 增 加 ,丁苯 橡胶 的进 口量 持续增 加 , 19 99年我 国 丁苯橡 胶 的进 口量达 为 l .3万吨 ,2 0 突破 4O 02年 2 O万吨 /年大关 ,达 到 2 .3万 吨, 同 比增 长 约 24
产量也不断增加。19 年我国丁苯橡胶的产量只 99
有 2 .2万 吨,2 0 年上 升到 3 .7万吨 ,20 93 01 48 03
量的年均增长率约为 9 8% 0 5年我国丁苯橡 .5 。2 0 胶的产量约为 5 . 万吨。 30
近 年来 我 国丁苯橡 胶 品种牌 号 不 断增 加 , 充
的 5 . 万吨 / 55 年,其中乳聚丁苯橡胶 的生产装置 4 套,生产能力合计为 4 . 万吨 / 95 年,约占我国 丁苯橡胶总生产能力的 8 .9 ; 9 1% 主要的生产厂家
有 齐鲁 石油 化 工 公司 、吉 林 石油 化 工 公 司 、兰州 石 油化 工 公司 和江 苏 南通 申华 公 司;溶 聚丁 苯 橡
维普资讯
・
1・ 6
我国丁者橡胶的供需现状及发展建议 .
我 国丁苯橡胶 的供需现状及发展建议
崔 小 明
( 北京燕 山石 化 公 司研 究院 ,12 5 ) 0 50
- 1、下载文档前请自行甄别文档内容的完整性,平台不提供额外的编辑、内容补充、找答案等附加服务。
- 2、"仅部分预览"的文档,不可在线预览部分如存在完整性等问题,可反馈申请退款(可完整预览的文档不适用该条件!)。
- 3、如文档侵犯您的权益,请联系客服反馈,我们会尽快为您处理(人工客服工作时间:9:00-18:30)。
丁苯橡胶(SBR)是以丁二烯和苯乙烯为单体,采用自由基引发的乳液聚合或阴离子溶液聚合工艺而得的,目前世界上产量最高,消费量最大的通用合成橡胶(SR)品种。
其物理机械性能、加工性能和制品的使用性能都接近于天然橡胶(NR),而且耐磨性、耐热性、耐老化性优于天然橡胶,并可与NR以及多种SR并用,广泛用于生产轮胎与轮胎制品、鞋类、胶管、胶带、医疗器械、汽车零部件、电线电缆以及其他多种工业橡胶制品。
按生产工艺,丁苯橡胶可以分为乳聚丁苯橡胶(ESBR)和溶聚丁苯橡胶(SSBR)两大类。
乳聚丁苯橡胶开发历史悠久,生产和加工工艺成熟,应用广泛,其生产能力、产量和消耗量在丁苯橡胶中均占首位。
溶聚丁苯橡胶是兼具多种综合性能的橡胶品种,其生产工艺与乳聚丁苯橡胶相比,具有装置适应能力强、胶种多样化、单体转化率高、排污量小、聚合助剂品种少等优点,是今后的发展方向。
1 世界丁苯橡胶的供需现状及发展前景1.1 生产现状近年来,世界丁苯橡胶的生产能力稳步增长。
2003年全世界丁苯橡胶的总生产能力为451.2万t/a,2006年增加到504.6万t/a,比2005年增长约6.5%,其中乳聚丁苯橡胶的生产能力为404.9万t/a,约占世界丁苯橡胶总生产能力的80.2%:溶聚丁苯橡胶的生产能力为99.7万t/a,约占总生产能力的19.8%。
北美、欧洲和亚洲地区是最主要的生产地区,生产能力分别约占世界总生产能力的22.2%、19.8%和38.6%。
美国固特异轮胎橡胶公司是目前世界上最大的丁苯橡胶生产厂家,2006年生产能力达到36.3万t/a,约占世界丁苯橡胶总生产能力的7.19%;其次是中国石油化工集团公司,生产能力为29.0万t/a,约占世界总生产能力的5.75%;再次是韩国锦湖石油化工公司,生产能力为27.5万t/a,约占世界总生产能力的5.45%;第4是日本合成橡胶公司,生产能力为26.8万t/a,约占世界总生产能力的5.31%。
2006年世界主要的丁苯橡胶生产厂家以及前10家丁苯橡胶生产厂家隋况分别见表1和表2。
2007-2011年期间,世界上将新增丁苯橡胶产能约120.0万t/a,新增装置主要集中在我国大陆、印度、韩国、德国以及美国等国家和地区,其中陶氏(Dow)公司已开始在德国施科保建6.0万t/a溶液丁苯橡胶(SSBR)新装置,计划在2008年下半年建成。
美国国际特种产品公司(ISP)计划在美国新建一套16.0万t/a丁苯橡胶生产装置,印度信赖工业公司计划在2009年新建一套10.0万t/a生产装置,印度石油天然气公司计划在2010年新建一套14.0万t/a生产装置,韩国锦湖石油化工公司拟于2008年新增加10.0万t/a生产能力。
预计到2011年,世界丁苯橡胶的生产能力将超过620.0万t/a,其中亚太地区、北美地区以及西欧地区仍将是世界最主要的丁苯橡胶的3个生产地区。
1.2 消费现状及发展前景1.2.1 消费现状2003年,全世界丁苯橡胶的总消费量为339.5万t,2005年消费量为363.0万t,2006年消费量为368.7万t,同比增长约1.6%。
亚洲、北美和西欧地区是主要的消费地区,2006年这3个地区丁苯橡胶的消费量合计达到271.9万t,约占世界丁苯橡胶总消费量的73.6%。
亚洲地区的消费量为155.8万t,约占总消费量的42.3%;北美地区的消费量为77.3万t,约占总消费量的21.0%;西欧地区的消费量为69.8万t,约占总消费量的18.9%。
近几年,世界丁苯橡胶消费量的增长并不显著,其原因主要有以下3点:(1)子午线胎普及率不断增加,与斜交胎相比,丁苯橡胶在于午线胎中的用量较少;(2)其他合成橡胶品种,如三元乙丙橡胶(EPDM)、丁腈橡胶(NBR)和聚丁二烯橡胶(BR)二元乙丙橡胶、丁腈橡胶和聚丁二烯橡胶增长较快,尤其是在非轮胎领域中的应用明显增长,一定程度上抑制了丁苯橡胶的增长;(3)合成橡胶与天然橡胶的价格竞争激烈。
2006年世界丁苯橡胶的总贸易量超过160万t,比2005年略有增长。
其中,中东欧地区是净出口量最大的地区,其次是北美地区。
除上述两个地区外,其他地区均为丁苯橡胶的净进口地区。
1.2.2 消费结构近两年在世界丁苯橡胶消费结构中,用于生产轮胎及汽车制品用橡胶零部件对丁苯橡胶的需求量约占总消费量的54.0%,非汽车用橡胶制品约占总消费量的12.5%,制鞋等其他方面约占总消费量的33.5%。
世界各个地区丁苯橡胶的消费结构有所不同。
在北美和西欧地区,由于其轮胎产业比较发达,用于生产轮胎及其制品的丁苯橡胶所占比例高于世界平均水平。
北美地区的比例高达72.0%,西欧地区为62.0%,而亚洲地区只有约50.0%。
1.2.3 发展前景今后几年,世界经济前景继续向好,丁苯橡胶各消费领域的需求将有所增加,但由于受原料价格高涨等因素的影响,增速将会趋缓。
预计今后几年,世界丁苯橡胶的消费量将以年均约5.4%的速度增长,到2011年总消费量将达到约480.0万t,其中亚洲地区的消费量增长最快,消费量的年均增长率将达到约5.5%。
2 我国丁苯橡胶的供需现状及发展前景2.1 生产现状2.1.1 生产能力自1960年兰州石油化工公司从前苏联引进技术,建成我国第一套1.3万t/a乳聚丁苯橡胶生产装置以来,我国丁苯橡胶的生产发展较快。
尤其是2003年以后,国内有多套丁苯橡胶新建或扩建装置建成投产。
2004年,中石油吉林石油化工公司将其乳聚丁苯橡胶装置生产能力增加到14.0万t/a,中石油兰州石油化工公司亦于2004年末将其生产能力扩增到5.5万t/a;江苏南通申华化工公司于2005年6月将其原来的12.0万t/a生产能力扩建到17.0万t/a;2006年8月22日,中石化高桥石油化工公司采用日本旭化成公司溶液法连续生产的10.0万t/a溶液丁苯橡胶装置建成投产。
2007年5月28日,南京扬子石化金浦橡胶有限公司(扬子石化股份有限公司和江苏金浦集团按照股比6:4组建的合资公司)采用国产化的低温生产技术建成的10.0万t/a乳聚丁苯橡胶装置打通全流程,产出合格产品,实现一次开车成功。
截止到2007年底,我国丁苯橡胶的生产厂家有8家,总生产能力为75.5万t/a。
其中,乳聚丁苯橡胶的生产厂家有中石化齐鲁石油化工公司、中石油吉林石油化工公司、中石油兰州石油化工公司、江苏南通申华化工公司和南京扬子石化金浦橡胶有限公司5家,生产能力合计为59.5万t/a,约占我国丁苯橡胶总生产能力的78.8%。
溶聚丁苯橡胶的生产厂家有中石化北京燕山石油化工公司、中石化茂名石油化工公司和中石化高桥石油化工公司3家,生产能力合计为16.0万t/a,约占我国丁苯橡胶总生产能力的21.2%。
其中,江苏南通申华化工公司是目前我国最大的丁苯橡胶生产厂家,生产能力约占全国丁苯橡胶总生产能力的22.5%,其次是中石油吉林石油化工公司,生产能力约占总生产能力的18.5%,再次是中石化齐鲁石油化工公司,生产能力约占总生产能力的17.2%。
2007年我国丁苯橡胶的主要生产厂家情况见表3。
2.1.2 产量随着生产能力的不断增加,我国丁苯橡胶的产量也不断增加。
1999年我国丁苯橡胶的产量只有29.32万t,2001年增加到34.87万t。
2003年产量首次突破40万t,达到40.79万t,2005年产量为51.42万t,比2004年增长约9.6%。
2006年我国丁苯橡胶的产量达到58.10万t,同比增长约13.0%,2001-2006年产量的年均增长率约为10.7%。
2007年1-10月份的产量为59.50万t,同比增长24.5%。
2.1.3 品种近年来我国丁苯橡胶产品品种牌号不断增加。
齐鲁石油化工公司开发出高结合苯乙烯的非污染型丁苯胶SBR1516,具有优异的抗湿滑、耐曲挠等性能,达到国外同类产品先进水平,在压敏胶粘剂、制鞋、轮胎三角胶等领域,具有广阔的应用前景。
SBR1714为高充油丁苯胶SBR1714,除具备普通充油丁苯胶加工性能好、生热低、低温屈挠寿命长,用作胎面胶时牵引力大的特点外,还具有优越的耐磨耗、抗湿滑等性能,可应用于轮胎胎面、胶管、胶带等领域,具有较好的社会效益和经济效益。
不含亚硝胺类物质的环保型丁苯胶SBR1721,已替代进口产品应用于轮胎生产中。
南京扬金橡胶公司顺利生产出了丁苯环保橡胶SBR-1712E和一种填充高芳香烃油的产品SBR-1712丁苯橡胶。
兰州石油化工公司开发出高门尼粘度粉末丁苯橡胶(PSBR)1712产品,申华化学工业有限公司开发成功填充低稠环芳烃油的丁苯橡胶SBR1723,该产品与SBR1712相比,生胶门尼粘度低、伸长率稍低、定伸应力稍高,开炼机混炼工艺性能稍好,两者基本物理性能没有明显的差异。
SBR1723能适用于环保要求较高的橡胶制品。
由吉林石化公司研究院与有机合成厂共同协作开发的一项具有自主知识产权的科研新成果——高转化率丁苯橡胶1502新技术,日前正式通过专家验收。
该项成果通过调整工艺配方,将丁苯橡胶聚合转化率由原有的62%提高到70%,达到了国内先进水平。
北京燕山石化公司研究院根据掌握的连续聚合SSBR分子调控技术,并开发出具有自主知识产权的新牌号,其中YL950为中苯乙烯、中乙烯基非充油牌号,YL951为相应的充油牌号,YL954为高苯乙烯基充油牌号,YL952为高乙烯基充油牌号。
此外,该院还研究开发出集成橡胶$IBR合成技术,利用该技术开发出星型高支化HB-SIBR新产品。
与偶联型SSBR相比,该产品同时具有较好的抗湿滑性能和优异的低滚动阻力性能(其tanδ(50℃)范围在0.0898-0.1019)。
由于SIBR的tanδ-温度曲线峰形较宽,使得集成橡胶的DMA 性能中,tanδ(0℃)和tamδ(50℃)能够扩大差距,两者比值达到4-5。
2.2 装置新建或扩建情况近几年,由于我国丁苯橡胶的产能还不能满足国内实际生产的需求,因而有多家企业新建或扩建生产装置。
除中石化扬子石油化工公司与南京金浦(GPRO)集团合资建设的10.0万t/a乳聚丁苯橡胶生产装置已经于2007年5月正式投产外,中石油兰州石油化工公司拟将现有乳聚丁苯橡胶生产能力扩建到10.0万t/a,预计2008年初投产。
普利司通公司与日本合成橡胶公司(JSR)近日签订了技术转让协议,将应用JSR 公司的丁苯橡胶专用技术在我国广东惠州新建一套5.0万t/a的乳聚丁苯橡胶生产装置,计划于2008年上半年建成投产。
中石油独山子石化公司拟于2009年建设一套10.0万t/a溶聚丁苯橡胶生产装置,中石化茂名石油化工公司将新建一套5.0万t/a丁苯橡胶生产装置,中石油抚顺石油化工公司计划新建一套10.0万t/a乳聚丁苯橡胶生产装置。