精密注塑模具解决方案
精密注塑件尺寸精度的解决方案

精密注塑件尺寸精度的解决方案一、背景介绍精密注塑件是一种在制造业中广泛应用的零部件,其尺寸精度对产品的质量和性能有着重要影响。
然而,在注塑件生产过程中,由于材料、模具、注塑机等因素的影响,注塑件的尺寸精度可能存在一定的偏差。
因此,为了解决精密注塑件尺寸精度的问题,我们需要采取相应的解决方案。
二、解决方案1. 优化模具设计模具是注塑件生产过程中最关键的因素之一。
通过优化模具设计,可以提高注塑件的尺寸精度。
具体措施包括:- 选择高精度的模具材料,如优质钢材,以确保模具的稳定性和耐磨性。
- 设计合理的模具结构,避免尺寸变形和偏差的产生。
- 采用先进的模具加工技术,如数控加工,以提高模具的加工精度和表面质量。
2. 优化注塑工艺参数注塑工艺参数的选择和调整对注塑件的尺寸精度有着重要影响。
以下是一些优化注塑工艺参数的建议:- 控制注塑机的注射速度和压力,以确保注塑料充填均匀,避免尺寸不一致。
- 控制注塑机的冷却时间和温度,以确保注塑件的收缩率和尺寸稳定性。
- 选择合适的熔融温度和保压时间,以确保注塑料的流动性和成型质量。
3. 引入精密测量设备精密测量设备可以帮助我们准确测量注塑件的尺寸,及时发现和纠正尺寸偏差。
以下是一些常用的精密测量设备:- 三坐标测量机:可以实现对注塑件各个尺寸的精确测量和比对。
- 光学投影仪:可以对注塑件的平面尺寸和轮廓进行快速测量。
- 厚度测量仪:可以测量注塑件的厚度,判断是否符合要求。
4. 严格质量控制和检验在注塑件生产过程中,严格的质量控制和检验是确保尺寸精度的关键。
以下是一些常用的质量控制和检验措施:- 制定严格的质量标准和工艺规范,确保每个环节都符合要求。
- 进行过程监控和数据分析,及时发现和纠正质量问题。
- 进行全面的尺寸检验,包括外观检查、尺寸测量等,确保注塑件的质量和尺寸精度。
三、案例分析以汽车零部件为例,通过采取上述解决方案,成功解决了精密注塑件尺寸精度的问题。
经过优化模具设计,采用高精度的模具材料和先进的模具加工技术,注塑件的尺寸稳定性得到了显著提高。
注塑粘模解决方案

注塑粘模解决方案注塑粘模是生产过程中常见的问题之一,它会降低生产效率,增加生产成本。
然而,通过采取一些有效的解决方案,我们可以解决这个问题,提高生产效率,降低成本。
首先,选择合适的模具材料是解决注塑粘模问题的关键。
模具材料应具有良好的耐磨性和耐腐蚀性,以避免模具因磨损或腐蚀而引起粘模现象。
常用的模具材料有优质钢和特殊合金钢,它们具有高硬度和耐腐蚀性能,适合长时间稳定工作。
其次,使用合适的模具润滑剂也是解决注塑粘模问题的重要因素之一。
模具润滑剂可以减少模具与注塑材料之间的摩擦力,降低粘附度,从而减少粘模现象的发生。
常见的模具润滑剂有固体蜡、液体硅油等,可以根据具体情况选择适合的润滑剂。
此外,合理调整注塑设备的温度和压力也能有效解决粘模问题。
过高的温度和压力会导致注塑材料在模具表面产生粘附现象。
因此,我们需要根据具体的注塑材料和产品要求,合理设置温度和压力,以减少粘模发生的概率。
另外,定期清洁和维护模具也是解决注塑粘模问题的重要措施之一。
定期清洗模具表面的残留物和污垢,可以防止其积聚和附着,从而减少粘模发生的可能性。
同时,及时修复模具表面的损伤和缺陷,可以提高模具的完整性,减少粘模的概率。
最后,尽量避免在注塑过程中产生过多的外力和振动,这也是解决粘模问题的一项重要措施。
外力和振动会使注塑材料在模具表面产生剪切力和挤压力,增加其粘模的可能性。
因此,我们需要通过合理的操作和设备维护,减少外力和振动的产生。
综上所述,注塑粘模问题可以通过选择合适的模具材料、使用合适的模具润滑剂、合理调整注塑设备的温度和压力、定期清洁和维护模具、避免外力和振动等多种有效措施来解决。
通过这些解决方案,我们可以提高生产效率,降低成本,最大程度地避免和减少注塑粘模的发生,为企业的发展带来更大的价值和竞争优势。
注塑过程中常见的问题及解决方案

注塑过程中常见的问题及解决方案一、飞边(披锋)1. 问题描述- 这飞边就像塑料偷偷长出来的小翅膀,在注塑件的边缘或者分型面那里冒出来,看着可闹心了。
就像好好的一块蛋糕,边缘突然多出了一些不规则的奶油坨坨。
2. 解决方案- 首先得检查模具的合模力。
要是合模力不够,那塑料就会像调皮的小孩从门缝里挤出来。
适当增加合模力,把模具紧紧抱住,让塑料乖乖待在该待的地方。
- 模具的磨损也会导致飞边。
就像穿破了的鞋子会漏脚指头一样,磨损的模具缝隙变大了。
这时候就得修模啦,把那些磨损的地方补一补或者磨平。
- 注塑压力也不能太大。
如果压力太大,塑料就像被大力士猛推的水,到处乱流。
降低注塑压力,找到一个合适的值,既能把模具填满,又不会让塑料溢出来。
二、短射(缺料)1. 问题描述- 短射就像给一个杯子倒水,结果没倒满一样。
注塑件看着不完整,有些地方该有塑料的却空着,就像一个没发育好的小怪物。
2. 解决方案- 先看看注塑压力是不是太小。
压力小的话,塑料就像没力气的小蚂蚁,爬不到模具的每个角落。
增加注塑压力,让塑料充满整个模具型腔。
- 塑料的流动性也很关键。
如果塑料太黏,就像浓稠的糨糊,很难流到模具的远端。
这时候可以提高料筒温度,让塑料变得稀一点,流动性更好,就像把糨糊加热变成稀粥一样,能顺利流到各个地方。
- 浇口尺寸也可能有问题。
要是浇口太小,就像一个小得可怜的水龙头,水流不出来多少。
适当扩大浇口尺寸,让塑料能畅快地流进模具。
三、气泡(气穴)1. 问题描述2. 解决方案- 注塑速度可能太快了。
塑料像一阵风呼呼地冲进模具,把空气都裹在里面了。
降低注塑速度,让塑料慢慢流进去,就像散步一样,这样空气就有机会跑出来了。
- 模具的排气也很重要。
如果模具没有排气孔或者排气不良,空气就被困在里面出不来。
在模具上开排气槽或者使用透气钢材料,给空气一条逃跑的路。
- 塑料干燥不彻底也会产生气泡。
如果塑料里有水份,加热的时候就会变成水蒸气,形成气泡。
精密注塑工艺与产品缺陷解决方案100例

精密注塑工艺与产品缺陷解决方案100例【导言】精密注塑工艺是一种高精度、高要求的注塑工艺,它在汽车、电子、医疗等行业有着广泛的应用。
然而,由于产品的特殊性,精密注塑工艺中常常会出现一些产品缺陷,如翘曲、气泡、热缩等,这不仅影响产品的美观和功能,还会影响产品的使用寿命和市场竞争力。
本文将从精密注塑工艺的角度出发,总结100例产品缺陷解决方案,帮助读者更全面地了解精密注塑工艺和解决产品缺陷的方法。
【一、精密注塑工艺概述】1.1 精密注塑工艺的定义精密注塑工艺是一种高精度、高稳定性的注塑技术,它主要应用于对产品精度、表面质量和材料要求极高的领域。
1.2 精密注塑工艺的应用领域精密注塑工艺广泛应用于汽车、电子、医疗器械等行业,例如汽车外饰件、无线终端壳体、医疗器械零部件等。
1.3 精密注塑工艺的特点精密注塑工艺具有高精度、高稳定性、高材料要求、高成本等特点,是一种技术含量高、门槛高的注塑工艺。
【二、产品缺陷解决方案】2.1 翘曲解决方案:优化模具结构,增加产品的冷却时间,控制注塑工艺参数。
2.2 气泡解决方案:选择适当的材料、改善模具设计、优化注塑工艺参数。
2.3 热缩解决方案:优化成型工艺、使用专业热缩材料、加强模具表面处理等。
【三、总结与展望】本文总结了100例精密注塑工艺产品缺陷解决方案,从模具设计、材料选用、工艺参数等方面提出了解决问题的方法。
未来,随着工艺技术的不断进步,相信会有更多更先进的产品缺陷解决方案出现,为精密注塑工艺的发展提供更坚实的保障。
【个人观点】作为一名资深的精密注塑工艺工程师,我深知产品缺陷对企业的影响之大。
解决产品缺陷是我们工程师的责任和使命。
通过不断学习和实践,我相信精密注塑工艺在解决产品缺陷方面一定会有更好的表现,为行业发展做出更大的贡献。
总结起来,精密注塑工艺是一门高技术含量的工艺,它在产品缺陷解决方案方面有着丰富的经验和成果。
希望本文的内容能够帮助读者更深入地了解产品缺陷的解决方法,为精密注塑工艺的发展和应用提供借鉴和参考。
注塑工艺与产品缺陷解决方案100例

注塑工艺与产品缺陷解决方案注塑工艺是一种常见的制造方法,用于生产各种塑料制品。
然而,在注塑过程中可能会出现一些产品缺陷。
以下是一些常见的注塑产品缺陷及其解决方案:1. 短射(Short Shot):指塑料注射不完整,导致产品部分或全部空洞。
解决方案包括:- 检查模具温度和压力,确保足够的塑料流动。
- 检查塑料熔融温度和压力,确保充分熔融。
- 检查模具设计,确保填充均匀。
2. 气泡(Air Traps):在产品内部形成气泡,影响外观和强度。
解决方案包括:- 调整注射速度和压力,以减少气体陷阱的形成。
- 优化模具通道和冷却系统,确保塑料充分流动并迅速冷却。
3. 热胀冷缩(Warping):产品在冷却后变形或扭曲。
解决方案包括:- 优化模具温度和冷却系统,确保均匀冷却。
- 调整注射速度和压力,避免内部应力积累。
- 使用合适的塑料材料,具有较低的热胀冷缩性能。
4. 流痕(Flow Marks):产品表面出现纹理或痕迹。
解决方案包括:- 调整注射速度和压力,确保塑料流动顺畅。
- 优化模具设计,减少填充阻力。
- 提高模具温度,增加塑料流动性。
5. 毛刺(Flash):产品边缘出现额外的塑料。
解决方案包括:- 检查模具关闭力,确保模具严密闭合。
- 检查模具设计,减少模具间隙。
- 控制注射速度和压力,避免过多的塑料溢出。
6. 熔接线(Weld Lines):由于塑料流动不畅导致的界面线。
解决方案包括:- 调整注射速度和压力,以减少熔接线形成。
- 优化模具设计,减少填充阻力。
- 提高模具温度,增加塑料流动性。
以上只是一些常见的注塑产品缺陷及其解决方案,具体解决方案还需要根据具体情况进行调整和优化。
为了确保产品质量,注塑过程中的工艺参数、模具设计以及塑料材料的选择都非常重要。
注塑缺陷原因分析与解决方案
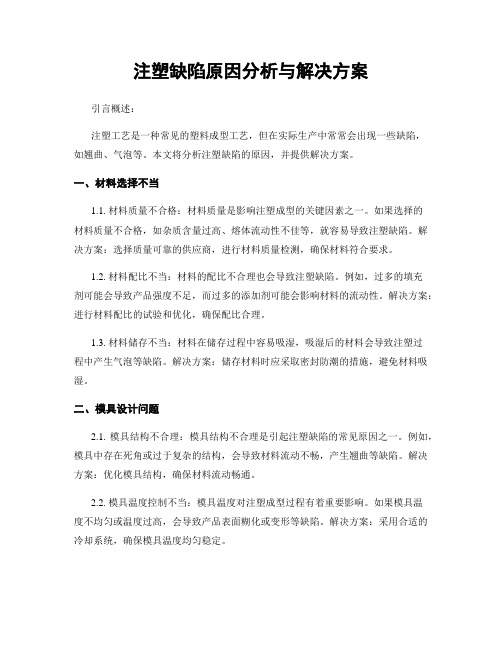
注塑缺陷原因分析与解决方案引言概述:注塑工艺是一种常见的塑料成型工艺,但在实际生产中常常会出现一些缺陷,如翘曲、气泡等。
本文将分析注塑缺陷的原因,并提供解决方案。
一、材料选择不当1.1. 材料质量不合格:材料质量是影响注塑成型的关键因素之一。
如果选择的材料质量不合格,如杂质含量过高、熔体流动性不佳等,就容易导致注塑缺陷。
解决方案:选择质量可靠的供应商,进行材料质量检测,确保材料符合要求。
1.2. 材料配比不当:材料的配比不合理也会导致注塑缺陷。
例如,过多的填充剂可能会导致产品强度不足,而过多的添加剂可能会影响材料的流动性。
解决方案:进行材料配比的试验和优化,确保配比合理。
1.3. 材料储存不当:材料在储存过程中容易吸湿,吸湿后的材料会导致注塑过程中产生气泡等缺陷。
解决方案:储存材料时应采取密封防潮的措施,避免材料吸湿。
二、模具设计问题2.1. 模具结构不合理:模具结构不合理是引起注塑缺陷的常见原因之一。
例如,模具中存在死角或过于复杂的结构,会导致材料流动不畅,产生翘曲等缺陷。
解决方案:优化模具结构,确保材料流动畅通。
2.2. 模具温度控制不当:模具温度对注塑成型过程有着重要影响。
如果模具温度不均匀或温度过高,会导致产品表面糊化或变形等缺陷。
解决方案:采用合适的冷却系统,确保模具温度均匀稳定。
2.3. 模具磨损严重:模具长时间使用后会出现磨损,磨损严重的模具会导致产品尺寸不准确或表面粗糙等缺陷。
解决方案:定期检查和维护模具,及时更换磨损严重的模具部件。
三、注塑工艺参数设置不当3.1. 注射压力过高或过低:注射压力是影响注塑成型的关键参数之一。
如果注射压力过高,会导致产品变形或开裂,而注射压力过低则会导致产品表面光洁度不高。
解决方案:根据产品要求和材料特性,合理设置注射压力。
3.2. 注射速度不合理:注射速度对产品的充填和冷却过程有着重要影响。
如果注射速度过快,会导致产品内部产生气泡或短射,而注射速度过慢则会导致产品表面瑕疵。
注塑试模10大问题及其解决方案
注塑试模10大问题及其解决方案试模中常见问题1:主浇道粘模解决问题的方法与顺序:1拋光主浇道→2喷嘴与模具中心重合→3降低模具温度4缩短注射时间→5增加冷却时间→6检查喷嘴加热圈→ 7拋光模具表面→8检查材料是否污染。
试模中常见问题2:塑件脱模困难解决问题的方法与顺序:1降低注射压力→2缩短注射时间→3增加冷却时间→4降低模具温度→5拋光模具表面→6增大脱模斜度→7减小镶块处间隙试模中常见问题3:尺寸稳定性差解决问题的方法与顺序:1改变料筒温度→2增加注射时间→3增大注射压力→4改变螺杆背压→5升高模具温度→6降低模具温度→7调节供料量→8减小回料比例试模中常见问题4:表面波纹解决问题的方法与顺序:1调节供料量→2升高模具温度→3增加注射时间→4增大注射压力→5提高物料温度→6增大注射速度→7增加浇道与浇口的尺寸试模中常见问题5:塑件翘曲和变形解决问题的方法与顺序:1降低模具→2降低物料温度→3增加冷却时间→4降低注射速度→5降低注射压力→6增加螺杆背压→7缩短注射时间试模中常见问题6:塑件脱皮分层解决问题的方法与顺序:1检查塑料种类和级别→2检查材料是否污染→3升高模具温度→4物料干燥处理→5提高物料温度→6降低注射速度→7缩短浇口长度→8减小注射压力→9改变浇口位置→10采用大孔喷嘴试模中常见问题7:银丝斑纹浇道粘模解决问题的方法与顺序:1降低物料温度→2物料干燥处理→3增大注射压力→4增大浇口尺寸→5检查塑料的种类和级别→6检查塑料是否污染试模中常见问题8:表面光泽差解决问题的方法与顺序:1物料干燥处理→2检查材料是否污染→3提高物料温度→4增大注射压力→5升高模具温度→6拋光模具表面→7增大浇道与浇口的尺寸试模中常见问题9:凹痕解决问题的方法与顺序:1调节供料量→2增大注射压力→3增加注射时间→4降低物料速度→5降低模具温度→6增加排气孔→7增大浇道与浇口尺寸→8缩短浇道长度→9改变浇口位置→10降低注射压力→11增大螺杆背压试模中常见问题10: :气泡解决问题的方法与顺序:1物料干燥处理→2降低物料温度→3增大注射压力→4增加注射时间→5升高模具温度→6降低注射速度→7增大螺杆背压。
注塑缺陷描述及解决方案
注塑缺陷描述及解决方案一、缺陷描述在注塑过程中,可能会出现各种缺陷,这些缺陷会影响产品的质量和外观。
以下是常见的注塑缺陷描述:1. 气泡缺陷:在注塑制品表面或内部出现气泡,影响产品的美观度和强度。
2. 热胀冷缩缺陷:注塑制品在冷却过程中,由于热胀冷缩不均匀,导致产品尺寸不准确或变形。
3. 短射缺陷:注塑模具中的塑料未能充满模腔,导致产品出现不完整或部分缺失。
4. 毛刺缺陷:注塑制品表面出现细小的毛刺,影响产品的外观质量。
5. 沉痕缺陷:注塑制品表面出现凹陷或凸起的痕迹,影响产品的美观度。
6. 热裂缺陷:注塑制品在冷却过程中,由于塑料内部应力过大,导致出现裂纹。
7. 毛躁缺陷:注塑制品表面出现粗糙的纹理或颗粒,影响产品的触感和外观。
二、解决方案针对以上注塑缺陷,可以采取以下解决方案:1. 控制注塑工艺参数:合理调整注塑机的注射速度、压力、温度等参数,确保塑料充满模腔,避免短射和气泡缺陷的发生。
2. 优化模具设计:对于容易出现热胀冷缩缺陷的产品,可以通过优化模具结构和冷却系统设计,平衡热胀冷缩过程,减少尺寸偏差和变形。
3. 选择合适的塑料材料:根据产品的要求和使用环境,选择适合的塑料材料,以提高产品的强度和耐用性,减少热裂和毛刺缺陷的发生。
4. 加工后处理:对于出现毛刺、沉痕和毛躁等缺陷的产品,可以采用打磨、抛光、喷涂等后处理方法,改善产品的外观质量。
5. 增加注塑模具的维护保养:定期清洁和保养注塑模具,确保模具表面光滑,减少缺陷的发生。
6. 引入质量控制措施:建立完善的质量控制体系,通过检测和测试,及时发现和解决注塑缺陷问题,确保产品质量符合要求。
总结:注塑缺陷的描述及解决方案是为了帮助生产企业更好地理解和解决注塑过程中可能出现的问题。
通过合理调整工艺参数、优化模具设计、选择合适的材料、加工后处理和加强质量控制,可以有效地解决注塑缺陷问题,提高产品质量和客户满意度。
注塑模模具水路堵塞处理方案和改善措施
注塑模模具水路堵塞处理方案和改善措施下载温馨提示:该文档是我店铺精心编制而成,希望大家下载以后,能够帮助大家解决实际的问题。
文档下载后可定制随意修改,请根据实际需要进行相应的调整和使用,谢谢!并且,本店铺为大家提供各种各样类型的实用资料,如教育随笔、日记赏析、句子摘抄、古诗大全、经典美文、话题作文、工作总结、词语解析、文案摘录、其他资料等等,如想了解不同资料格式和写法,敬请关注!Download tips: This document is carefully compiled by the editor. I hope that after you download them, they can help you solve practical problems. The document can be customized and modified after downloading, please adjust and use it according to actual needs, thank you!In addition, our shop provides you with various types of practical materials, such as educational essays, diary appreciation, sentence excerpts, ancient poems, classic articles, topic composition, work summary, word parsing, copy excerpts, other materials and so on, want to know different data formats and writing methods, please pay attention!标题:注塑模模具水路堵塞处理方案和改善措施引言注塑模模具在生产过程中,水路堵塞是一种常见而又令人头痛的问题。
CimatronE注塑模具CAD CAM集成解决方案
CimatronE注塑模具CAD/ CAM集成解决方案一、 注塑模具设计基础1、实体造型1.1 CimatronE11采用典型的混合造型理念,即实体和曲面相结合又可以相互转化的方式,使造型功能灵活快捷,高效而完备。
1.2 各功能基于参数化,变量化和特征化的特点,可以非常灵活地定义修改参数和约束,不受模型生成秩序的限制。
草图工具利用智能的导引技术来控制约束,简捷的交互意味着高效的设计和优化。
1.3 由于CimatronE11采用了混合造型核心系统,为大型复杂产品的设计提供了前所未有的强大功能,比如支持在开放实体的模型上进行实体设计与布尔运算,为用户提供了极大的灵活性。
2、曲面设计2.1 CimatronE的曲面造型工具是基于一些高级的算法,这些算法不仅能生成完整的几何实体,而且能对其灵活的控制和修改。
2.2 所有的曲面功能使用NURBS曲面来保证光顺性。
同时,系统优秀的布尔运算操作----支持实体间,实体与曲面间,曲面与曲面间的布尔运算等。
保证曲面创建的方便与灵活。
2.3 曲面编辑功能丰富。
具有强大的曲面混合,曲面过渡,多曲面裁剪,曲面修补,恢复原始曲面,草图修改曲面,曲面缠绕等独特的功能。
3、数据转换CimatronE具有读/写迅速而准确的数据接口,CimatronE支持当前业界的所有标准数据信息格式,这些接口包括:① IGES——国际标准的曲面模型信息交换格式;② VDA——多用于测量机测量信息表达的格式,如果用户的信息中含有曲线信息,在转换完成时就可得到现成的三维曲线模型;③ DXF——当前应用广泛的二维信息交换格式,最初来自于AutoCAD,后被人们广泛使用;④ STL——是面向激光立体成型的模型信息表达格式,CimatronE支持由三维模型生成STL信息,也可以读取STL信息进行数控编程;⑤ STEP——目前是国际上正在不断完善的三维产品信息交换模式;⑥ SAT——该接口是用来读取基于ACIS核心软件设计的三维产品模型;⑦ Parasolid——该接口还可以用于读取任何基于Parasolid核心而开发的CAD系统建立的三维模型。
- 1、下载文档前请自行甄别文档内容的完整性,平台不提供额外的编辑、内容补充、找答案等附加服务。
- 2、"仅部分预览"的文档,不可在线预览部分如存在完整性等问题,可反馈申请退款(可完整预览的文档不适用该条件!)。
- 3、如文档侵犯您的权益,请联系客服反馈,我们会尽快为您处理(人工客服工作时间:9:00-18:30)。
精密注塑模具解决方案
注塑模具的定义:塑料通过注塑机台注入非标工具内经冷却后成型的工具称之为模具,精密注塑模具在设计当中会出现各种各样的问题,以下是针对各种各样的问题对应的解决方案:
问题一:
精密塑胶模具的结构确定是关键,总体结构是关系到产品最终效果的体现:模具总体结构的确定,入水系统的确定,顶出系统的确定以及运水系统的确定等等这些要有利于产品的后加工取向。
问题二:
入水问题?首先我们会根据产品的结构,重量,体积以及成本选择合理的入水方案,既能满足客户的要求又要满足品质的要求,其次是要严格按照入水设计标准进行设计:水口排布要均匀主分流道横载面的大小胶口的形状以及大小。
问题三:
顶出问题?首先我们会根据产品的取向和结松确定顶出的方式,其次就是顶出平衡的评估以及与其它系统共存的问题,比如说与运水干涉以及环保标识等等。
问题四:
运水系统的设计基于四大要求(运水线路尽量均衡。
运水的线路不能干涉其它机构。
运水的设备要尽可能的满足客户标准和易于安装。
每条运水线路都要显示有进出标识。
问题五:怎样保证模具的加工精度,制品的精度,主要取决于模具型腔,入子以及模芯尺寸的精度,型腔定位准确或分型面精度是否合理将直接影响制品的尺寸;首先要制定加工工艺流程表每完成一道工序都必须全检并以文本的形式作出数据检测一览表;加工完成后对工件要作后处理加工以及维护。
塑胶模具分型面的设计也是很重要的一环,如果设计不合理,轻则塑件不易取出,重则损坏模具,下面介绍一下塑胶模具分型面的设计原则。
.
便于脱出塑件,简化塑胶模具结构,加压方向选定后,分型面的位置应尽量使塑件落在下模。
.
对同轴度精度高的塑件,分型面宜选在可将两直径(示图中及)同时放
在下模或上模的位置上。
.
塑件沿高度方向精度要求高时,宜采用半溢型腔,在分型面处形成横向飞边,则易保证高度精度,而不溢式型腔不易保证。
.
当径向尺寸精度较高时,应考虑飞边厚度对塑件精度的影响,如图所示。
若塑件取垂直分型而易保证,取水平型面则因飞边厚度不易控制,影响塑件精度。
.
保证塑件外观,应便于清理飞边,不易损坏外观,如图所示分型面产生的飞边便于清理,不易损坏塑件外观。
.
便于塑胶模具制作及成型零件的加工,改进后的分型面,使塑胶模具加工同心度要求低,便于制造,飞边也不损坏塑件外观。
.
保证成型零件的强度,如确定分型面时,避免成型零件出现薄壁及尖角。
塑料模具厂加工模具的分类及各种注意点要求
、塑料模具的种类分为很多种,大致可分为十大类。
根据零件材料、物理化学性能、机械强度、尺寸精度、表面光洁度、使用寿命、经济性等不同要求,选择不同类型的模具成形。
、精度要求高的塑料模具需要使用高精度的数控机床加工,而且模具材质、成形工艺都有严格要求,还需使用模具技术去设计、分析。
、有些零件由于成型时有特殊要求,塑料模具还需使用热流道,气辅成型,氮气缸等先进的工艺。
、塑料模具生产厂家应具备数控机床、电火花机床、线切割机床及数控仿型铣设备,高精度磨床,高精度三座标测量仪,计算机设计及相关软件等。
、一般大型冲压模具(如汽车复盖件模具)要考虑机床是否有压边机构,甚至边润滑剂、多工位级进等。
除冲压吨位还要考虑冲次、送料装置、机床及模具保护装置。
、上述塑料模具的制造手段及工艺不是每个企业都具备和掌握的。
在选择合作的塑料模具厂家时一定要了解它的加工能力,不但看硬件设备,还要结合管理水平、加工经验以及技术力量。
、对同一套模具,不同的模具厂家报价有时有很大差距。
你不该付出高于模具价值费用的同时,也不应该少于模具的成本。
塑料模具厂家像你一样,要在业务中取得合理的利润。
订制一套报价低得多的模具会是麻烦的开始。
用户须从自身要求出发,全面衡量。