各类焊接质量缺陷及措施
焊接中出现的问题和解决方案
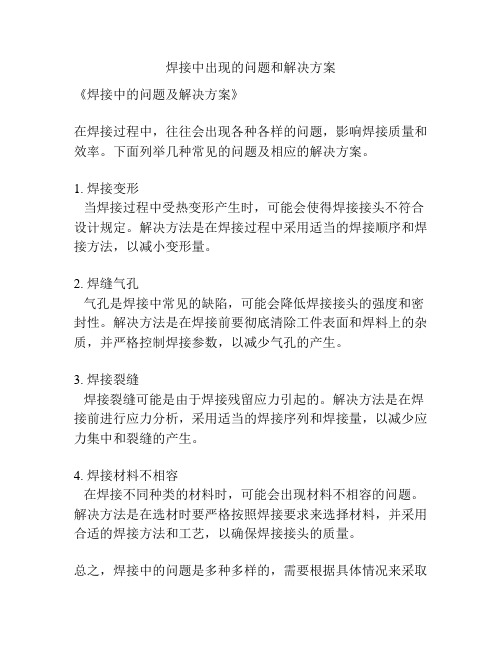
焊接中出现的问题和解决方案
《焊接中的问题及解决方案》
在焊接过程中,往往会出现各种各样的问题,影响焊接质量和效率。
下面列举几种常见的问题及相应的解决方案。
1. 焊接变形
当焊接过程中受热变形产生时,可能会使得焊接接头不符合设计规定。
解决方法是在焊接过程中采用适当的焊接顺序和焊接方法,以减小变形量。
2. 焊缝气孔
气孔是焊接中常见的缺陷,可能会降低焊接接头的强度和密封性。
解决方法是在焊接前要彻底清除工件表面和焊料上的杂质,并严格控制焊接参数,以减少气孔的产生。
3. 焊接裂缝
焊接裂缝可能是由于焊接残留应力引起的。
解决方法是在焊接前进行应力分析,采用适当的焊接序列和焊接量,以减少应力集中和裂缝的产生。
4. 焊接材料不相容
在焊接不同种类的材料时,可能会出现材料不相容的问题。
解决方法是在选材时要严格按照焊接要求来选择材料,并采用合适的焊接方法和工艺,以确保焊接接头的质量。
总之,焊接中的问题是多种多样的,需要根据具体情况来采取
相应的解决方法。
只有不断积累经验、改进技术,才能够提高焊接质量和效率。
常见焊接缺陷产生原因及防止措施
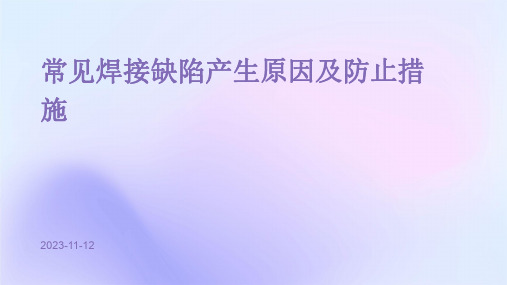
2023-11-12•焊接缺陷概述•常见焊接缺陷产生原因•焊接缺陷防止措施•焊接缺陷实例分析•焊接缺陷的检测方法与工具目录01焊接缺陷概述焊缝尺寸不符合要求焊缝宽度、高度、平整度等不符合设计要求,影响焊接质量和强度。
气孔焊接过程中熔融金属内产生的气泡未被充分排除,在焊缝表面形成气孔。
未焊透焊接过程中未能完全熔透金属,导致焊接接头强度降低。
未熔合焊接过程中焊缝金属与母材之间未能完全熔合,影响焊接接头强度。
夹渣焊接过程中熔渣残留在焊缝中,降低焊接质量。
咬边焊接过程中母材边缘被电弧烧蚀,形成的凹陷或沟槽。
焊接缺陷的类型降低焊接接头的强度和致密性,影响设备的安全运行和使用寿命。
引起应力集中,增加焊接接头的脆性,降低其抗冲击性能。
影响设备的外观质量,增加维修成本。
焊接缺陷的影响02常见焊接缺陷产生原因金属表面有水分、锈迹、油污等杂质,在焊接高温下形成气孔。
焊接前未将焊缝周围的杂质清理干净,导致焊接时气体被包裹在焊缝中。
焊接速度过快,气体未完全排出。
焊接操作不当,如电弧过长、电流过大等,导致气体进入焊缝。
焊接材料中存在杂质,如碳、硫、磷等元素含量过高,导致焊缝韧性不足,产生裂纹。
结构设计不合理,焊缝承受的应力过大,导致裂纹产生。
焊接过程中温度过高或冷却速度过快,导致焊缝热影响区产生裂纹。
焊接操作不当,如电弧过长、电流过大等,导致焊缝金属过热,产生裂纹。
夹渣焊接前未将焊缝周围的杂质清理干净,导致焊接时杂质被包裹在焊缝中。
焊接材料质量不好,含有杂质,导致焊缝中夹渣。
焊接速度过快,气体未完全排出,导致焊缝中夹渣。
焊接操作不当,如电流过小、电弧过长等,导致焊缝金属熔化不均匀,产生夹渣。
未焊透焊接速度过快,导致焊缝未完全熔合。
焊接材料质量不好,含有杂质,导致熔合不完全。
焊接电流过小,导致焊缝金属熔化不均匀。
焊缝角度不正确,导致熔合不完全。
焊接速度过快,导致焊缝未完全熔合。
焊缝角度不正确,导致熔合不完全。
焊接材料质量不好,含有杂质,导致熔合不完全。
焊接的六大缺陷及其产生原因、危害、预防措施

焊接的六大缺陷及其产生原因、危害、预防措施一、外观缺陷外观缺陷(表面缺陷)是指不用借助于仪器,从工件表面可以发现的缺陷。
常见的外观缺陷有咬边、焊瘤、凹陷及焊接变形等,有时还有表面气孔和表面裂纹。
单面焊的根部未焊透等。
A、咬边是指沿着焊趾,在母材部份形成的凹陷或者沟槽,它是由于电弧将焊缝边缘的母材熔化后没有得到熔敷金属的充分补充所留下的缺口。
产生咬边的主要原因:是电弧热量太高,即电流太大,运条速度太小所造成的。
焊条与工件间角度不正确,摆动不合理,电弧过长,焊接次序不合理等都会造成咬边。
直流焊时电弧的磁偏吹也是产生咬边的一个原因。
某些焊接位置( 立、横、仰 )会加剧咬边。
咬边减小了母材的有效截面积,降低构造的承载能力,同时还会造成应力集中,发展为裂纹源。
咬边的预防:矫正操作姿式,选用合理的规范,采用良好的运条方式都会有利于消除咬边。
焊角焊缝时,用交流焊代替直流焊也能有效地防止咬边。
B、焊瘤焊缝中的液态金属流到加热缺陷未熔化的母材上或者从焊缝根部溢出,冷却后形成的未与母材熔合的金属瘤即为焊瘤。
焊接规范过强、焊条熔化过快、焊条质量欠佳(如偏芯),焊接电源特性不稳定及操作姿式不当等都容易带来焊瘤。
在横、立、仰位置更易形成焊瘤。
焊瘤常伴有未熔合、夹渣缺陷,易导致裂纹。
同时,焊瘤改变了焊缝的实际尺寸,会带来应力集中。
管子内部的焊瘤减小了它的内径,可能造成流动物阻塞。
防止焊瘤的措施:使焊缝处于平焊位置,正确选用规范,选用无偏芯焊条,合理操作。
C、凹坑凹坑指焊缝表面或者反面局部的低于母材的部份。
凹坑多是由于收弧时焊条(焊丝)未作短期停留造成的(此时的凹坑称为弧坑),仰立、横焊时,常在焊缝反面根部产生内凹。
凹坑减小了焊缝的有效截面积,弧坑常带有弧坑裂纹和弧坑缩孔。
防止凹坑的措施:选用有电流衰减系统的焊机,尽量选用平焊位置,选用合适的焊接规范,收弧时让焊条在熔池内短期停留或者环形摆动,填满弧坑。
D、未焊满未焊满是指焊缝表面上连续的或者断续的沟槽。
焊接缺陷及防止措施
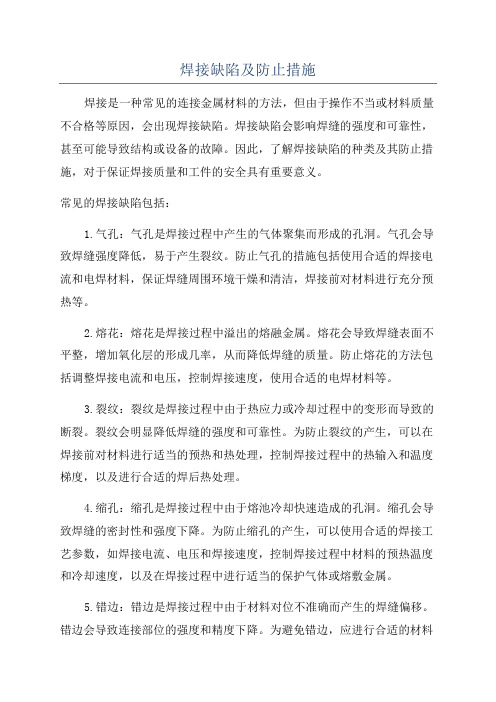
焊接缺陷及防止措施焊接是一种常见的连接金属材料的方法,但由于操作不当或材料质量不合格等原因,会出现焊接缺陷。
焊接缺陷会影响焊缝的强度和可靠性,甚至可能导致结构或设备的故障。
因此,了解焊接缺陷的种类及其防止措施,对于保证焊接质量和工件的安全具有重要意义。
常见的焊接缺陷包括:1.气孔:气孔是焊接过程中产生的气体聚集而形成的孔洞。
气孔会导致焊缝强度降低,易于产生裂纹。
防止气孔的措施包括使用合适的焊接电流和电焊材料,保证焊缝周围环境干燥和清洁,焊接前对材料进行充分预热等。
2.熔花:熔花是焊接过程中溢出的熔融金属。
熔花会导致焊缝表面不平整,增加氧化层的形成几率,从而降低焊缝的质量。
防止熔花的方法包括调整焊接电流和电压,控制焊接速度,使用合适的电焊材料等。
3.裂纹:裂纹是焊接过程中由于热应力或冷却过程中的变形而导致的断裂。
裂纹会明显降低焊缝的强度和可靠性。
为防止裂纹的产生,可以在焊接前对材料进行适当的预热和热处理,控制焊接过程中的热输入和温度梯度,以及进行合适的焊后热处理。
4.缩孔:缩孔是焊接过程中由于熔池冷却快速造成的孔洞。
缩孔会导致焊缝的密封性和强度下降。
为防止缩孔的产生,可以使用合适的焊接工艺参数,如焊接电流、电压和焊接速度,控制焊接过程中材料的预热温度和冷却速度,以及在焊接过程中进行适当的保护气体或熔敷金属。
5.错边:错边是焊接过程中由于材料对位不准确而产生的焊缝偏移。
错边会导致连接部位的强度和精度下降。
为避免错边,应进行合适的材料对位和夹持,控制焊接过程中的热输入和焊接速度,以及采用合适的焊接工艺。
针对以上不同类型的焊接缺陷,需采取相应的防止措施,如合理选择适用的材料、控制合适的焊接参数、确保焊缝周围环境条件良好等,以保证焊接质量。
此外,还应注意人员技术培训和操作规程的制定,提高焊接人员的技术能力和安全意识,从而减少人为因素对焊接缺陷产生的影响。
总之,焊接缺陷在焊接过程中是难免的,但通过合适的防止措施,可以降低焊接缺陷的发生概率,并提高焊接质量和工件的安全性。
常见焊接缺陷产生原因及防止措施
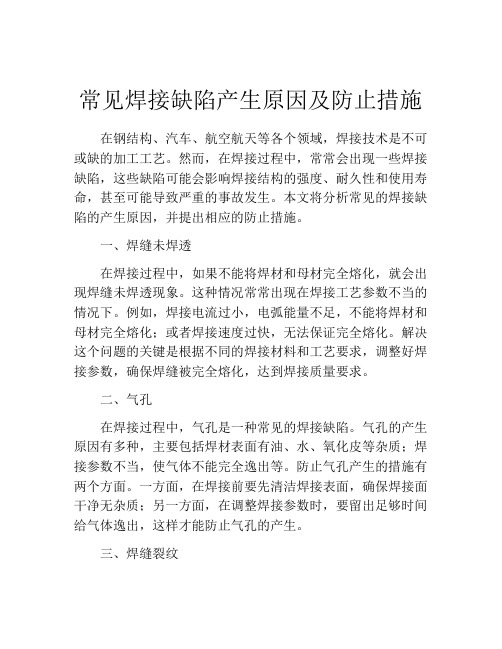
常见焊接缺陷产生原因及防止措施在钢结构、汽车、航空航天等各个领域,焊接技术是不可或缺的加工工艺。
然而,在焊接过程中,常常会出现一些焊接缺陷,这些缺陷可能会影响焊接结构的强度、耐久性和使用寿命,甚至可能导致严重的事故发生。
本文将分析常见的焊接缺陷的产生原因,并提出相应的防止措施。
一、焊缝未焊透在焊接过程中,如果不能将焊材和母材完全熔化,就会出现焊缝未焊透现象。
这种情况常常出现在焊接工艺参数不当的情况下。
例如,焊接电流过小,电弧能量不足,不能将焊材和母材完全熔化;或者焊接速度过快,无法保证完全熔化。
解决这个问题的关键是根据不同的焊接材料和工艺要求,调整好焊接参数,确保焊缝被完全熔化,达到焊接质量要求。
二、气孔在焊接过程中,气孔是一种常见的焊接缺陷。
气孔的产生原因有多种,主要包括焊材表面有油、水、氧化皮等杂质;焊接参数不当,使气体不能完全逸出等。
防止气孔产生的措施有两个方面。
一方面,在焊接前要先清洁焊接表面,确保焊接面干净无杂质;另一方面,在调整焊接参数时,要留出足够时间给气体逸出,这样才能防止气孔的产生。
三、焊缝裂纹焊缝裂纹是一种比较危险的焊接缺陷。
它常常由以下原因引起:焊接材料的拉伸强度不均,焊接接头部位过于脆弱,或者是焊接温度过高、冷却过快等。
为了防止焊缝裂纹的产生,可以采取以下措施。
一是控制焊接参数,避免过高的焊接温度和过快的冷却速度。
二是在焊接过程中,注意焊接的连续性,确保焊接成形完整。
三是在焊接过程中,采用预热的方法,改善焊接材料的拉伸强度,避免裂纹的出现。
四、过度熔深焊接过度熔深是由于焊接材料熔化过度,穿过母材嵌入焊接面内,使得焊缝结构松散,焊接强度降低。
过度熔深的原因有多种,如焊接电流过大,焊接速度过慢等。
预防过度熔深可以通过调整焊接参数、控制熔化深度和焊接速度等措施实现。
总之,焊接缺陷的产生原因可能有很多,需要针对具体情况采取相应的防止措施。
这需要焊接工艺人员有丰富的焊接经验和专业知识,对焊接材料和工艺有深入的了解,才能确保焊接质量达到要求。
焊接质量缺陷原因分析及预防、治理措施
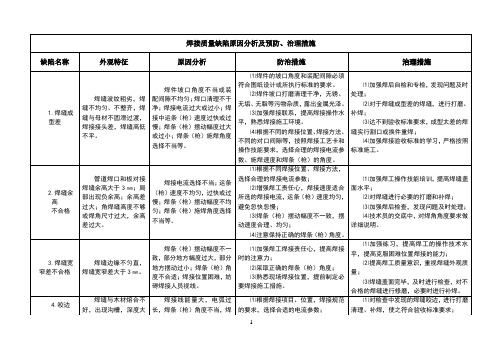
⑷根据自己的操作技能,选择合适的线能量、焊接速度和操作手法。
厚度符合标准要求;
⑵加强打底练习,熟练掌握操作手法以及对应的焊接线能量及焊接速度等。
18.管道焊口根部焊瘤、凸出、凹陷
⑷注意周围焊接施工环境,搭设防风设施,管子焊接无穿堂风;
⑸氩弧焊时,氩气纯度不低于%,氩气流量合适;
⑹尽量采用短弧焊接,减少气体进入熔池的机会;
⑺焊工操作手法合理,焊条、焊枪角度合适;
⑻焊接线能量合适,焊接速度不能过快;
⑼按照工艺要求进行焊件预热。
⑴严格按照预防措施执行;
⑵加强焊工练习,提高操作水平和责任心;
⑴严格按照规程和作业指导书的要求准备各种焊接条件;
⑵提高焊接操作技能,熟练掌握使用的焊接方法;
⑶采取合理的焊接顺序等措施,减少焊接应力等。
⑴针对每种产生裂纹的具体原因采取相应的对策;
⑵对已经产生裂纹的焊接接头,采取挖补措施处理。
11.焊缝表面不清理或清理不干净,电弧擦伤焊件
焊缝焊接完毕,焊接接头表面药皮、飞溅物不清理或清理不干净,留有药皮或飞溅物;焊接施工过程中不注意,电弧擦伤管壁等焊件造成弧疤。
⑶发现问题及时采取必要措施。
14.气孔
在焊缝中出现的单个、条状或群体气孔,是焊缝内部最常见的缺陷。
根本原因是焊接过程中,焊接本身产生的气体或外部气体进入熔池,在熔池凝固前没有来得及溢出熔池而残留在焊缝中。
⑴焊条要求进行烘培,装在保温筒内,随用随取;
⑵焊丝清理干净,无油污等杂质;
⑶焊件周围10~15㎜范围内清理干净,直至发出金属光泽;
⑴焊件的坡口角度和装配间隙必须符合图纸设计或所执行标准的要求。
常见焊接缺陷及防止措施和注意事项
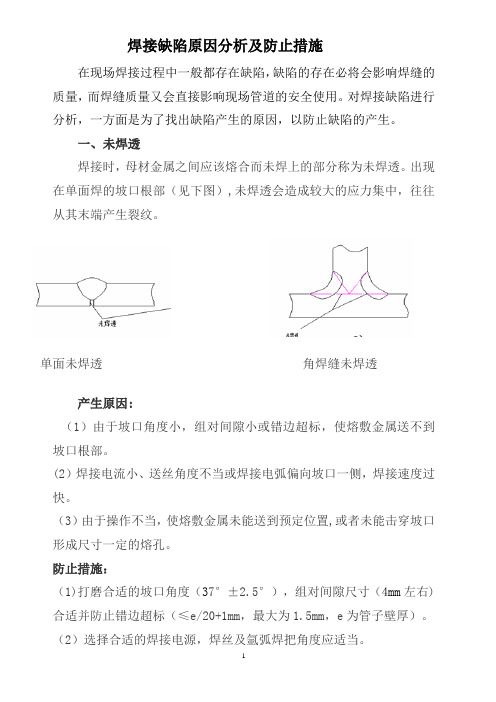
焊接缺陷原因分析及防止措施在现场焊接过程中一般都存在缺陷,缺陷的存在必将会影响焊缝的质量,而焊缝质量又会直接影响现场管道的安全使用。
对焊接缺陷进行分析,一方面是为了找出缺陷产生的原因,以防止缺陷的产生。
一、未焊透焊接时,母材金属之间应该熔合而未焊上的部分称为未焊透。
出现在单面焊的坡口根部(见下图),未焊透会造成较大的应力集中,往往从其末端产生裂纹。
单面未焊透角焊缝未焊透产生原因:(1)由于坡口角度小,组对间隙小或错边超标,使熔敷金属送不到坡口根部。
(2)焊接电流小、送丝角度不当或焊接电弧偏向坡口一侧,焊接速度过快。
(3)由于操作不当,使熔敷金属未能送到预定位置,或者未能击穿坡口形成尺寸一定的熔孔。
防止措施:(1)打磨合适的坡口角度(37°±2.5°),组对间隙尺寸(4mm左右)合适并防止错边超标(≤e/20+1mm,最大为1.5mm,e为管子壁厚)。
(2)选择合适的焊接电源,焊丝及氩弧焊把角度应适当。
(3)掌握正确的焊接操作方法,氩弧焊丝的送进应稳、准确、熟练地击穿尺寸适宜的熔孔,应把熔敷金属送至坡口根部。
二、未熔合这种缺陷常出现在坡口的侧壁、多层焊的层间及焊缝的根部(见下图)。
产生原因:(1)由于焊丝和氩弧焊把角度不当,电弧不能良好地加热坡口两侧母材金属,致坡口面母材母材金属未能充分熔化。
(2)在焊接时由于上侧坡口金属熔化后产生下坠,影响下侧坡口面金属的加热熔化,造成“冷接"。
(3)2GT位置操作时,在上、下坡口面击穿顺序不对,未能先击穿下坡口后击穿上坡口,或者在上、下坡口面上击穿熔孔位置未能错开一定的距离,使上坡口熔化金属下坠产生粘接,造成未熔合。
(4)氩弧焊时电弧两侧坡口的加热不均(线能量不同),或者坡口面存在污物等.防止措施:(1)选择适宜的焊丝和氩弧把角度。
(2)操作时注意观察坡口两侧金属熔化情况,使之熔合良好。
(3)2GT位置操作时,掌握好上、下坡口面的击穿顺序和保持适宜的熔孔位置和尺寸大小,焊丝的送进应熟练地从熔孔上坡口拉到下坡口。
焊接焊缝的缺陷与预防措施

焊接焊缝的缺陷与预防措施焊接是一种常见且广泛应用的金属连接方法,但焊接过程中会出现焊缝缺陷,对于焊接质量和强度产生不利影响。
因此,了解焊接焊缝的缺陷形式及其预防措施是至关重要的。
本文将介绍焊接焊缝的几种常见缺陷,并提出相应的预防措施。
1.气孔气孔是焊接中最普遍的缺陷之一。
气孔的形成是由于焊接过程中的气体未能完全排除,被困在焊缝内部形成的孔洞。
气孔的存在会导致焊缝强度降低,并可能在受力时产生应力集中,从而导致焊接断裂。
预防措施:- 检查焊接材料的表面,确保其干净无油、无水,以减少气孔的生成。
- 采用适当的焊接参数,控制焊接热输入,避免焊料表面温度过高,减少气孔的生成。
- 选择合适的焊接材料和焊接电极,以减少气孔的生成。
2.夹渣夹渣是指焊缝中存在的夹杂物,常见的有氧化物、矿物和其他金属颗粒等。
夹渣的存在会降低焊接接头的强度,甚至引发焊缝的开裂。
预防措施:- 清理工件和焊条的表面,确保无污染物和杂质,降低夹渣的产生。
- 采用正确的焊接技术和操作方法,确保焊接过程中夹渣容易浮起并排出。
- 检查焊接设备和工具的状态,确保其清洁和良好维护,以减少夹渣的生成。
3.裂纹焊接过程中的热应力和冷却过程中的收缩应力可能导致焊接接头出现裂纹。
裂纹的出现会降低焊接接头的强度和密封性。
预防措施:- 选择合适的焊接方法,控制焊接热输入和焊接速度,减少焊接产生的热应力。
- 采用适当的预热和后热处理工艺,以减小接头热应力和冷却收缩应力。
- 采用合适的焊接顺序,避免焊缝局部的过快冷却和热应力集中。
4.热裂纹热裂纹是焊缝在焊接过程中产生的一种裂纹,通常发生在高温下。
它是由于焊接过程中的热引起焊接材料在固态时的形变不均匀,产生内部应力而引起的。
预防措施:- 选择合适的焊接方法和工艺参数,避免焊接材料过多的热输入。
- 采用适当的焊接顺序,避免焊接接头局部过快冷却和热应力集中。
- 进行预热和后热处理,以减小热裂纹的发生。
总结:为了保证焊接接头的质量和强度,我们应该充分了解焊接焊缝缺陷的形成原因,并采取相应的预防措施。
- 1、下载文档前请自行甄别文档内容的完整性,平台不提供额外的编辑、内容补充、找答案等附加服务。
- 2、"仅部分预览"的文档,不可在线预览部分如存在完整性等问题,可反馈申请退款(可完整预览的文档不适用该条件!)。
- 3、如文档侵犯您的权益,请联系客服反馈,我们会尽快为您处理(人工客服工作时间:9:00-18:30)。
A :虚焊:无熔核或熔核直径尺寸小于白车身焊接强度检验控制方法规定尺寸的焊点。
原因:
1. 焊接电流小或焊接时间过短,焊接部位热量不足
2. 电极压力过大或过小
3. 工件或电极帽表面有油污或有氧化层,焊点加热的不一致
4. 焊接回路接触不良(焊枪分流或设备电缆老化)
5. 工件厚度材质差异过大
6. 电极帽未及时修磨或更换
7. 电极帽冷却不良
解决措施:
1. 编程器查看参数,根据实际情况增加焊接电流,延长焊接时间
2. 压力计检测焊枪压力:多层板焊接则增加焊枪压力;薄板焊接则降低焊枪压力。
所设压力值与焊接参数成比值。
3. 来料目检,清理工件或电极帽表面异物,稳定工件和电极帽的接触电阻
4. 大电流测试仪检测焊枪实际电流,检查焊枪绝缘处及电缆磨损程度
5. 根据板材分布情况,增设A 、B 档,设置预热电流、冷却电流、脉冲次数
6. 修磨或更换电极帽,复位步增按钮(电极帽顶端直径为φ6±1mm )
7. 检查焊枪循环水状况,电极臂内特弗容管是否正常(流量>2.5L/min )
B :裂纹:沿着焊点周围有裂纹的焊点。
车身焊接各类质量缺陷及解决措施
焊点表面 焊点侧面 可接受的裂纹
裂纹
原因:
1.焊接电流过大
2.电极压力过小
3.被焊金属本身缺陷
4.工件表面污物过多
5.焊枪上下电极不对中
解决措施:
1.编程器查看焊接参数,根据实际情况降低焊接电流(可增设冷却电流,延长保持时间)
2.压力计检测焊枪压力,增加焊枪压力(可调整焊接参数,延长预压、加压时间)
3.来料目检,检查来料是否存在缺陷(裂纹、拉伸印)
4.来料目检,清理工件或电极帽表面异物,稳定工件和电极帽的接触电阻
5.调整焊枪上下电极的对中度
C:烧穿:焊点内有贯穿于焊点的气孔。
原因:
1.焊接电流过大
2.电极压力不足
3.工件厚度材质差异过大
4.工件或电极表面污物过多
5.电极帽表面出现变形或扩大
6.被焊金属本身缺陷
解决措施:
1.编程器查看焊接参数,降低焊接电流(可增设冷却电流,延长保持时间)
2.压力计检测焊枪压力,增加焊枪压力(可调整焊接参数,延长预压、加压时间)
3.根据板材分布情况,设置相应焊接参数(可调整焊接参数,增设冷却电流及时间)
4.来料目检,清理工件或电极帽表面异物,稳定工件和电极帽的接触电阻
6.来料目检,检查来料是否存在缺陷(裂纹、拉伸印)
D:边缘焊点:没有包括钢板所有边缘部分的焊点。
不可接受
可接受
边缘焊点
原因:
1.焊枪焊接位置偏移
2.焊枪上下电极不对中
3.被焊金属本身缺陷,零件配合间隙过小
解决措施:
1.加强操作人员岗位操作培训
2.调整焊枪上下电极对中度
3.来料目检,检查来料是否存在缺陷(切边不均匀)
E:压痕过深:焊点压痕深度超过钢板厚度的50%的焊点。
材料厚度减少50% 压痕过深
原因:
1.预压时间短、焊接电流大,焊接时间长
2.加压力过大
3.电极帽端面直径过小或端面变形
4.焊枪上下电极不对中
5.焊接角度不垂直
解决措施:
1.查看焊接参数,增加预压时间、脉冲次数,降低焊接电流及焊接时间
2.压力计检测焊枪压力,降低焊枪压力
4.调整焊枪上下电极对中度
5.调整焊接姿态,保持与被焊工件表面垂直
F:位置偏差:与标准焊点位置的距离超过10mm的焊点。
实际焊点
标准位置焊点
位置偏差
原因:
1.焊枪焊接位置偏移;
解决措施:
1.加强人员岗位标准化操作培训
G:扭曲:母材扭曲变形超过焊接面30度的焊点。
变形超过30度
扭曲
原因:
1.焊接角度不垂直
2.焊枪上下电极不对中
3.被焊金属本身缺陷,表面扭曲
解决措施:
1.调整焊接姿态,保持与被焊工件表面垂直
2.调整焊枪上下电极对中度
H:漏焊:实际焊点数量少于理论焊点数量。
原因:
1.未按标准化进行操作
解决措施
2.加强人员岗位标准化操作培训
I. 飞溅:点焊、缝焊和凸焊时,由焊件贴合面或电极与焊件表面间喷出微细熔化金属颗粒的现象。
飞溅
原因:
1.预压时间短,焊接压力低,焊接电流高
2.工件或电极帽表面污物过多
3.工件配合间隙差
4.焊点接近板材边缘
5.焊枪动作滞后
6.焊接角度不垂直
7.工件厚度、材质差异过大
8.电极帽冷却不良
解决措施:
1.查看焊接参数,增加预压时间,焊接压力,降低焊接电流及时间
2.来料目检,清理工件或电极帽表面异物,稳定工件和电极帽的接触电阻
3.来料目检,将翘边工件敲平,使工件与工件之间完全贴合
4.调整焊接姿态,避免焊接边缘焊点
5.检查焊枪状态,焊枪气管、气缸是否有漏气现象
6.调整焊接姿态,保持与被焊工件表面垂直
7.根据板材分布情况,增设A、B档,设置预热电流、冷却电流、脉冲次数
8.检查焊枪循环水状况,电极臂内特弗容管是否正常(流量>2.5L/min)
J.粘铜:板材的表面粘有铜质。
原因:
1.预压时间短、焊接时间长、焊接电流大、保持时间短、焊接压力低
2.冷却水循环不通畅
3.板材表面附有异物
4.板材之间配合间隙差
5.焊枪动作滞后
6.焊接角度不垂直
7.焊枪上下电极对中性差
8.板材金属特性
解决措施:
1.查看焊接参数,增加预压时间、保持时间,降低焊接电流、焊接时间,调整焊接压力
2.检查焊枪循环水状况,电极臂内特弗容管是否正常(流量>2.5L/min)
3.来料目检,清理工件或电极帽表面异物,稳定工件和电极帽的接触电阻
4.来料目检,将翘边工件敲平,使工件与工件之间完全贴合
5.检查焊枪状态,焊枪气管、气缸是否有漏气现象
6.调整焊接姿态,保持与被焊工件表面垂直
7.调整焊枪上下电极对中度
8.根据板材分布情况,增设A、B档,设置预热电流、冷却电流
K.铜板焊接:对于有外观要求的焊点,加铜板焊接以避免表面出现压痕及缩孔的焊接方法。
铜板焊接出现焊接缺陷:
1.焊点缩孔
2.焊点扭曲
3.压痕过深
解决措施:
1.编辑焊接参数,采用软规范参数焊接方法:小电流,长时间
2.调整焊接姿态,保持与被焊工件表面垂直
3.增加修磨电极帽和打磨铜保护条频次,减少铜保护与工件、电极帽贴合不均匀的倾向。