水泥回转窑烘窑介绍
新型干法水泥回转窑系统

新型干法水泥回转窑系统1. 引言干法水泥生产是指在生产过程中不添加水分的一种水泥生产方法。
回转窑系统是干法水泥生产过程中的关键设备之一。
随着科技的不断进步,新型的干法水泥回转窑系统得到了广泛应用,带来了许多优势和创新。
本文将介绍新型干法水泥回转窑系统的构成、工作原理、优势以及应用范围,以帮助读者更好地了解和应用该系统。
2. 新型干法水泥回转窑系统的构成新型干法水泥回转窑系统由以下几个主要部分构成:2.1 窑体新型干法水泥回转窑系统的窑体采用高温耐火材料制作,能够耐受高温和化学腐蚀等恶劣条件。
窑体通常为圆筒形,具有一定的倾斜角度,倾斜角度的选择对于干法水泥生产的效果具有重要影响。
2.2 进料装置新型干法水泥回转窑系统的进料装置主要包括料斗和给料机构。
料斗用于储存原料,并通过给料机构将原料均匀地输送到回转窑系统中。
2.3 燃料装置新型干法水泥回转窑系统采用了先进的燃烧技术,能够利用多种不同的燃料,如煤炭、天然气或者油气。
燃料装置确保了系统的高效运行和能源利用率。
2.4 排出装置新型干法水泥回转窑系统的排出装置用于排出已经被煅烧和烧结的水泥熟料。
排出装置通常由滚筒、冷却器和排气系统组成。
2.5 辅助设备新型干法水泥回转窑系统还配备了一些辅助设备,如预热器、除尘设备等。
这些设备可以提高系统的热能利用率和环境保护效果。
3. 新型干法水泥回转窑系统的工作原理新型干法水泥回转窑系统的工作原理是将原料从进料口导入窑体中,通过窑体的旋转和倾斜,使原料逐渐移动向出料口的方向。
在这个过程中,燃料通过燃烧装置进行燃烧,释放热能,使窑体内部的温度升高。
原料在窑体中被加热和煅烧,逐渐形成水泥熟料。
随着窑体的旋转,熟料在窑体内部不断地翻动和混合,使得熟料能够充分烧结。
熟料最终通过排出装置排出,并经过冷却器进行冷却,然后进一步处理和细磨,最终得到水泥产品。
4. 新型干法水泥回转窑系统的优势新型干法水泥回转窑系统相比传统干法水泥回转窑系统具有以下几个优势:4.1 高效能新型干法水泥回转窑系统采用先进的燃烧技术和热交换设备,能够提供更高的热能利用效率,达到更高的生产能力。
新型干法水泥回转窑工艺及设备概述

⑦ 扩大分解炉用煤的品种。
同线型
(a):特点:分解炉所需助燃空气全部由窑内通过,无三次风管。 优点是可节省投资、操作简便、冷却机选型不 受限制。 缺点是过多的空气通过窑内,影响窑的操作。
(b): —目前常用形式 特点:分解炉所需助燃空气由三次风管提供,并在炉内与窑气混合。 (c):特点:分解炉所需助燃空气由三次风管提供,窑气不入炉。
c1 c5 c 4 c3 c 2
(2)各级旋风筒的表面散热损失
Lc5 Lc4 Lc3 Lc2 Lc1
(3)各级旋风筒的漏风量
Lokc5 Lokc4 Lokc3 Lokc2 Lokc1
1.2.5 各级旋风预热器串联级数的选择(P29)
1.2.6 旋风预热器分类以及几种典型的旋风预热器
8)入窑生料分解率: 两种表示方法
(1)表观分解率e: 指从窑尾取得入窑料样,分析其烧失量计算而得的分解率. 所取
样品即有预热生料又有窑尾循环飞扬的飞灰,是两种料的综合分解 率。
e 10000(L1 L2 ) (%) L1(100 L2 )
(2)真实分解率: 生料在预热器内预热和分解的真实数据,不考虑飞灰对所取
向 板,以便使旋风筒内的大部分循环气流由导向板直接 引入排气管,从而保证在不降低气固分离效率的前提
1.3 分解炉
1.3.1窑外分解技术
在悬浮预热器与回转窑之间增加一 个新热源——分解炉,将生料中碳 酸钙分解过程提到窑外进行,加快 其分解提高其分解率,如要分解率 课题高到85%-90%
预分解窑的特点(与其它窑相比)
② 改进分解炉的结构,使炉内具有合理的三位流场,力求提高炉 内气、固滞留时间比(τs/τg),延长生料在分解炉内的滞留时间。
水泥回转窑的烘窑和停窑
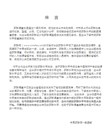
4、不换碱性砖而需停窑时,必须按适当的降温制度慢慢冷却窑衬,否则衬砖热面会迅速冷却,收缩过快,使砖内产生严重的破坏应力,甚至开裂,导致窑衬裂成两层,即砖的热面层与相结合的窑皮成为一层,下面残留砖体的另一层。再次开窑时,热面层往往随窑皮一起剥落,还会使窑衬内砖位扭曲,因此,应绝对禁止用冷风或平缓地用水来加速冷却窑衬。
水泥回转窑的烘窑和停窑
1、对于新窑(水泥回转窑),特别是预热器中的耐火材料充分干热应力易使窑衬剥落,故尽可能减小砖内温差应力,才能保证砖衬安全。所以“慢升温,不回头”是烘烤升温制度的基本指导原则。
3、烘烤期间从间歇到连续,从低速到正常窑速转动窑体极为重要,既可保持窑衬表面温度的均匀性,又可避免窑体中心线变歪及局部椭圆度增大,致使窑体变形。
回转窑简介

回转窑简介回转窑是一种用于煅烧原料的旋转设备,是干法水泥生产线中最重要的设备之一。
它特别适用于长时间连续煅烧,从而使原料充分发生化学反应,生产出高质量的水泥熟料。
回转窑的结构由筒体、支撑装置、驱动装置、轴承装置、密封装置和热交换设备等组成。
筒体通常为钢筋混凝土结构,内壁以耐火砖砌筑,以耐高温、耐磨和耐腐蚀的材料制成。
支撑装置通过轴承将筒体与基础连接,使其可以稳固地旋转。
驱动装置一般采用电动机和齿轮箱组成的传动装置,传递动力给筒体,使其顺时针或逆时针旋转。
轴承装置用于支撑和转动筒体,通常由滚动轴承和滑动轴承组成。
密封装置用于防止高温烟气和粉尘外泄,保证生产环境的清洁和安全。
热交换设备则用于将回转窑排出的烟气进行热能回收和利用,提高能源利用效率。
在回转窑的工作过程中,原料从入口处进入筒体,并随着筒体的旋转逐渐向出口处移动。
在煅烧过程中,原料经历一系列的物理和化学变化,最终转化为水泥熟料。
整个过程可以分为干燥区、预热区、煅烧区和冷却区四个阶段。
在干燥区,由于回转窑内部温度较低,原料中的水分得以蒸发,从而使原料脱水。
在预热区,高温烟气进入回转窑与原料进行热交换,使其逐渐升温。
在煅烧区,原料达到足够高的温度,使其发生化学反应,生成水泥熟料的主要成分。
在冷却区,较低温度的烟气冷却熟料,使其从高温状态恢复到室温。
最后,熟料从出口处排出,经过破碎和磨煤机加工后成为水泥成品。
回转窑具有许多优点,使其成为水泥生产线中不可或缺的设备。
首先,由于回转窑的连续运转特性,可以实现高效的大规模生产,提高生产能力。
其次,由于回转窑具有较大的热容量,能够有效地利用各种燃料的热能,降低能源消耗。
再者,回转窑内部温度和气氛可以进行精确控制,从而保证了水泥熟料的质量和稳定性。
最后,由于回转窑的结构紧凑,占地面积相对较小,可以适应各种场地条件。
然而,回转窑也存在一些问题和挑战。
首先,由于回转窑内部温度很高,对设备材料和热工性能要求较高,增加了设备的制造难度和成本。
水泥回转窑的工作原理和结构

水泥回转窑的工作原理和结构介绍水泥回转窑是水泥生产过程中的重要设备,它通过高温处理原料,在窑内进行物理化学反应,最终产生水泥熟料。
本文将详细介绍水泥回转窑的工作原理和结构。
工作原理水泥回转窑的工作原理如下: 1. 原料进料:原料(如石灰石、粉煤灰、铁矿石等)通过进料设备进入水泥回转窑。
2. 升温区:原料在水泥回转窑中自上而下地流动,经过升温区。
升温区内通常有燃料和燃烧空气,通过燃烧将原料加热到1500°C以上。
3. 煅烧区:在煅烧区,原料经过高温处理,发生物理化学反应,形成水泥熟料。
这个过程主要是熟化石灰石中的矿物,如石英,形成熟料矿物等。
4. 冷却区:煅烧后的水泥熟料通过冷却区进行冷却,以降低其温度,准备进入下一个工艺环节。
5. 出料:冷却后的水泥熟料从水泥回转窑的出料口流出,再经过破碎、磨粉等工序,最终制成水泥产品。
结构水泥回转窑主要由以下几个部分构成: 1. 窑筒:水泥回转窑的主体部分,通常为圆柱形。
窑筒由耐高温材料制成,以抵御高温和腐蚀。
2. 转子:位于窑筒内部并固定在回转窑的轴上,通过驱动装置带动窑筒转动。
转子通常由多个钢制齿轮组成,以确保窑筒的稳定转动。
3. 辊轮:固定在窑筒外侧,起到支撑窑筒和转子的作用。
辊轮通常由钢制制成,具有一定的承重能力。
4. 驱动装置:用于带动转子和窑筒的转动。
驱动装置通常由电机、减速器和联轴器等组成。
5. 进料装置:用于将原料输送到水泥回转窑中。
进料装置通常包括给料斗、螺旋输送机等设备。
6. 出料装置:用于将冷却后的水泥熟料从水泥回转窑中排出。
出料装置通常包括排料板、出料斗等设备。
水泥回转窑的优势水泥回转窑具有以下优势: 1. 高效性:水泥回转窑具有较大的传热面积和高温区的维持时间,能够高效地将原料加热到所需的温度。
2. 灵活性:水泥回转窑可以通过调整进料量、进料位置和窑转速来控制生产过程,以适应不同的原料和生产要求。
3. 稳定性:水泥回转窑具有良好的稳定性和可靠性,可以连续稳定地生产高质量的水泥熟料。
水泥回转窑
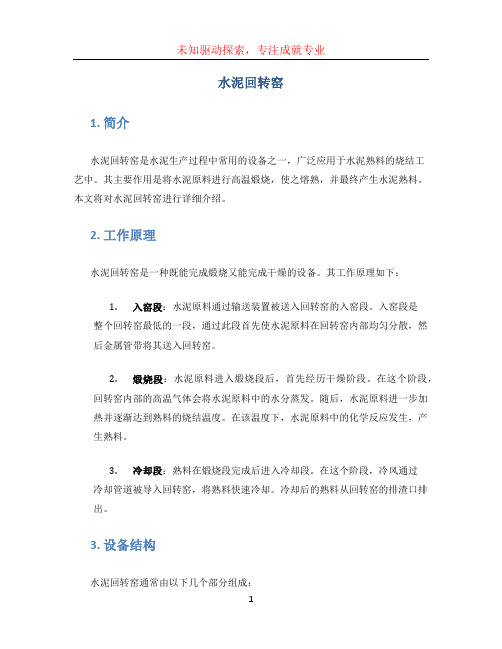
水泥回转窑1. 简介水泥回转窑是水泥生产过程中常用的设备之一,广泛应用于水泥熟料的烧结工艺中。
其主要作用是将水泥原料进行高温煅烧,使之熔熟,并最终产生水泥熟料。
本文将对水泥回转窑进行详细介绍。
2. 工作原理水泥回转窑是一种既能完成煅烧又能完成干燥的设备。
其工作原理如下:1.入窑段:水泥原料通过输送装置被送入回转窑的入窑段。
入窑段是整个回转窑最低的一段,通过此段首先使水泥原料在回转窑内部均匀分散,然后金属管带将其送入回转窑。
2.煅烧段:水泥原料进入煅烧段后,首先经历干燥阶段。
在这个阶段,回转窑内部的高温气体会将水泥原料中的水分蒸发。
随后,水泥原料进一步加热并逐渐达到熟料的烧结温度。
在该温度下,水泥原料中的化学反应发生,产生熟料。
3.冷却段:熟料在煅烧段完成后进入冷却段。
在这个阶段,冷风通过冷却管道被导入回转窑,将熟料快速冷却。
冷却后的熟料从回转窑的排渣口排出。
3. 设备结构水泥回转窑通常由以下几个部分组成:1.筒体:筒体是回转窑的主要部分,一般为圆筒形,由高强度钢材制成。
筒体由多个筒段组成,每个筒段都有不同的功能和结构。
2.传动装置:传动装置用于驱动回转窑的转动。
常见的传动装置包括齿轮传动、链条传动等。
3.燃烧装置:燃烧装置用于提供燃料,并产生高温气体。
常见的燃烧装置包括煤粉燃烧器、油燃烧器等。
4.冷却装置:冷却装置通过冷风或水进行冷却,将煅烧完成的熟料快速冷却。
5.排渣装置:排渣装置用于将煅烧后的熟料从回转窑中排出。
4. 设备优点水泥回转窑具有以下几个优点:1.高耐火性:由于水泥生产过程中需要高温环境,所以回转窑的材质通常选用高耐火材料制成,具有极高的耐火性能。
2.生产效率高:水泥回转窑是连续生产设备,能够实现自动化操作,生产效率高。
而且其设计合理,可以最大限度地利用燃料热能,提高能源利用效率。
3.产能大:水泥回转窑产能大,可以根据需要进行扩展和改造,适应不同规模的生产需求。
4.产品质量稳定:水泥回转窑能够提供稳定且高质量的水泥熟料。
水泥工艺介绍——烘窑篇 Microsoft Word 文档 (3)

水泥工艺介绍——烘窑篇对于窑的烘干,关键的一点既温度上升要均匀,采用逐步升温法,有利于保护窑砖和挂好窑皮。
同时也要注意根据温度的不同进行转窑,以防窑体变形。
不管是新窑、全部换砖或是局部换砖,都要进行24小时以上的烘干。
燃料只在窑头加入,预热机中的喷煤管只在进料后才进行喷煤。
窑体一般使用重油进行烘干,比较便宜,油的燃点在200-300度左右,煤的燃点在500-700度左右,重油比较容易点燃,燃烧也比较稳定。
但它的粘度大、杂质多,雾化效果不好。
在进油的油路上设有快速阀,它是利用电磁铁带动,当断电时快速阀马上关闭,与其配套的回油阀马上打开,防止油发生倒烧进入油库中。
喷煤嘴由四风道组成,由外到内分别是:外圈一次空气,煤粉圈,内圈一次空气,油管圈。
重油只在点火烘窑时才会用到,重油有一次油与二次油之分,一次油的压力要比二次油略高一些。
这主要是为了调节油量方便。
1.点火重油从油库,要经过加压、加温设备才进入到喷油管,然后经过喷油处的雾化器雾化后喷出,雾化后的油燃烧效率比较好。
点火前,将喷油系统开起,使重油加热加压循环,重油需要加压到36-40 bar,升温至80-110度左右,温度高其粘度小,雾化的效果也会好。
如果温度高过140度时,油就会有自燃得危险,电加热器则会自动跳闸断电。
烘窑点火是利用瓦斯或油布进行引燃。
点火前将瓦斯管或油布准备好,火可以是在外部点燃再伸入窑内,也可以伸入以后再点火。
利用一根单独的管子,从窑头HOOD旁边的观测孔中伸入,然后将瓦斯管或油布伸入喷油管的下方,此时要注意不要让一次空气将火焰吹灭。
在点火刚开始时的风压不宜太高,因为开初窑内的温度较低,容易将火吹灭。
经烧手检查确认,将重油系统切换到窑头,进行喷油点火。
2. 燃料的供应喷油嘴由内外圈组成,主要是为了调节方便,内圈的油是旋转喷出,外圈的油则是直接喷出,点火时先点内圈油,外圈的油根据内圈油进行调节。
一般内圈的压力要比外圈高1.5bar左右。
水泥行业回转窑的详细结构及工作原理
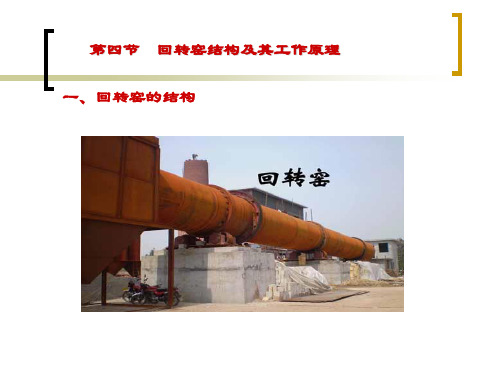
在对回转窑内物料运动的规律进行分析和模拟试验后,得出 很多计算回转窑内物料运动的速度的公式其中最为常用的一般公 式为:
vm
Di n Di n L , (m / s ) , (m / min) 60 m 60 1.77 1.77
式中:
vm
m
—物料在窑内运动的速度,m/s; L—窑的长度,m; —物料在窑内停留的时间:
影响窑内火焰长度的因素:有很多。主要有:燃烧速度和窑 内气体的流速。 燃烧速度:
粉煤的细度、煤粉与空气混合情况、一、二次风的温度
等因素有关。
煤粉粉愈细,或在喷煤管内加装风翅,以加还煤与空气
的混合,或提高一、二次空气的温度,均能提高燃烧速度, 而使火焰短。
风煤的混合速度和均匀程度也是影响燃烧速度的关键。
第四节
回转窑结构及其工作原理
一、回转窑的结构
海螺水泥厂
回转窑齿圈
托
轮
挡
轮
窑筒体轴向位移
窑筒体
轮带 挡轮
图2-72
轮带与挡轮
轮
带
回转窑轮带的润滑
Байду номын сангаас
轮 带 节
迷宫式密封装置是利用空气多次通过曲折通道增 大流动阻力而防止漏风的。
固定迷宫环
活动迷宫环 窑筒体
图2-73
迷宫式密封装置示意图
燃料燃烧的火焰温度要达到1600~1800℃;(保持高温) 火焰要有适当的长度;(保持物料高温时间) 处于适当的位置。(适合 C3 S 的形成的反应)
2、回转窑对入窑煤粉和助燃空气的要求
(1)对入窑煤粉的质量要求
低热值:
g QDW 20600 kJ / kg
挥发份:
灰分: 水分:
- 1、下载文档前请自行甄别文档内容的完整性,平台不提供额外的编辑、内容补充、找答案等附加服务。
- 2、"仅部分预览"的文档,不可在线预览部分如存在完整性等问题,可反馈申请退款(可完整预览的文档不适用该条件!)。
- 3、如文档侵犯您的权益,请联系客服反馈,我们会尽快为您处理(人工客服工作时间:9:00-18:30)。
水泥回转窑烘窑介绍
对于窑的烘干,关键的一点既温度上升要均匀,采用逐步升温法,有利于保护窑砖和挂好窑皮。
同时也要注意根据温度的不同进行转窑,以防窑体变形。
不管是新窑、全部换砖或是局部换砖,都要进行24小时以上的烘干。
燃料只在窑头加入,预热机中的喷煤管只在进料后才进行喷煤。
窑体一般使用重油进行烘干,比较便宜,油的燃点在200-300度左右,煤的燃点在500-700度左右,重油比较容易点燃,燃烧也比较稳定。
但它的粘度大、杂质多,雾化效果不好。
在进油的油路上设有快速阀,它是利用电磁铁带动,当断电时快速阀马上关闭,与其配套的回油阀马上打开,防止油发生倒烧进入油库中。
喷煤嘴由四风道组成,由外到内分别是:外圈一次空气,煤粉圈,内圈一次空气,油管圈。
重油只在点火烘窑时才会用到,重油有一次油与二次油之分,一次油的压力要比二次油略高一些。
这主要是为了调节油量方便。
1.点火
重油从油库,要经过加压、加温设备才进入到喷油管,然后经过喷油处的雾化器雾化后喷出,雾化后的油燃烧效率比较好。
点火前,将喷油系统开起,使重油加热加压循环,重油需要加压到36-40 bar,升温至80-110度左右,温度高其粘度小,雾化的效果也会好。
如果温度高过140度时,油就会有自燃得危险,电加热器则会自动跳闸断电。
烘窑点火是利用瓦斯或油布进行引燃。
点火前将瓦斯管或油布准备好,火可以是在外部点燃再伸入窑内,也可以伸入以后再点火。
利用一根单独的管子,从窑头HOOD旁边的观测孔中伸入,然后将瓦斯管或油布伸入喷油管的下方,此时要注意不要让一次空气将火焰吹灭。
在点火刚开始时的风压不宜太高,因为开初窑内的温度较低,容易将火吹灭。
经烧手检查确认,将重油系统切换到窑头,进行喷油点火。
2. 燃料的供应
喷油嘴由内外圈组成,主要是为了调节方便,内圈的油是旋转喷出,外圈的油则是直接喷出,点火时先点内圈油,外圈的油根据内圈油进行调节。
一般内圈的压力要比外圈高1.5bar左右。
由于开窑时温度较低,喷油量在700L/H,只需开内圈的空气就可以满足要求,在喷煤嘴的外圈空气及煤粉圈只要加入少量的空气进行冷却。
烘窑用喷油嘴的流孔板不可采用大直径,否则在烘窑时很难将油量减小,当喷油嘴的喷油量降到最低时,油还是会从油管中流出。
如果喷油管直径太小,在烘窑过程中需要提高喷油量时,加到最大,窑内温度还是达不到要求。
点火以后,要注意观查火焰形状。
若火焰向上飘动,则油量过多或风量不够,说明不稳定。
火焰比较稳定时可以考虑加油,通过调节一次油及二次油的用量来达到。
油量的调节主要参考火焰形状、窑尾CO与O2的含量等,使重油能完全燃烧。
喷油量的大小还要根据旋窑系统的温升速度来调节。
在点火的初期只要使用内圈的空气就可以满足燃烧的需求,但在外圈中还是要通入一部份冷空气来冷却风管。
当喷油量逐渐增大后,就要将外圈的空气打开帮助燃烧。
内圈风量的调节利用出风机处的档板开度调节,外圈是采用窑头喷煤处的放风阀进行处理。
喷煤嘴位置一般与窑头出料处平齐。
喷油嘴喷煤管的相对位置要特别注意,油管要与喷煤端平齐。
如果过于靠内部,就会使油雾化不好,造成滴油并且燃烧的效果也不行。
过于靠外就会造成喷油嘴温度较高,磨损较快。
喷煤管外圈空气孔不是垂直端面,而是有一定的角度,这样可以使风旋转,使燃料与空气混合较好,还可以带动二次空气进行混合。
在烘窑点火后6~8小时,随着窑温的上升,当到达600-700度左右时,在喷煤嘴中逐渐地加入一部份煤粉进行油煤混烧。
随着温度的提高逐渐增加煤的用量,减少喷油量,直至完全停掉喷油,然后用压缩空气将喷油管中的残留油吹出,以防余集。
目前,停止喷油都是在进料以后,窑内的烧成比较稳定才会停止。
准备煤、油混燃之前,开起煤粉计量站进料输送系统,将煤粉进入到窑头煤粉斗。
要开煤粉计量站前,要由现场激活大煤斗的收尘机,在中控室中激活窑头饲煤煤粉斗的输送系统,然后在试运转煤磨。
3. 烘窑时升温控制
在烘窑的开始,由于窑温比较低,可以不进行转窑,随着燃料的不断喷入窑内温度也不断上升,但是温度的上升速率不能太快,否则会造成窑砖暴热膨胀不均匀而被破裂。
在胎环处的窑壳升温速率比胎
环增大更快,窑壳的膨胀会受到胎环的限制。
窑进口温度维持约40℃/h稳定上升,不可超过50℃/h。
在加热的过程中要测窑内的温度比较困难。
目前有两种方法去判断窑内温度。
一是测进料室的气体温度去推测窑内的温度。
根据经验,进料室的温度每增加20度,窑内烧成带的温度就要增大30度,也就是说如果在进料室是800度,窑内烧成带就有1200度。
另一中方法就是根据窑壳的温度去推测窑内的温度,这种方法不能马上获得答案,同时窑壳的温度受外界的影响也比较大。
预热机风车进口温度不得超过350度。
当到达200度时,要主动联系T/G人员配合关起SP挡板。
烘窑时要注意预热机出口O2、CO的含量及电收尘的工作情况。
同时也要注意火焰的形状,不要让它熄火或伤害到窑砖。
4.转窑
窑的转速一般都通过C4的进口风温进行调整,在烘窑过程中按温度用寸动马达进行转窑。
如果转窑太早或者是转窑次数多,窑砖容易松动或变形。
转窑太迟或次数太少,窑体单边受热容易变形。
或者是当C4温度达到600℃时以寸动马达连续转窑。
1. 当其温度到达200度时,每半小时用辅助马达传1/4圈左右。
2. 到达400度时,每15分钟转1/4圈。
3. 到达600度以上则要用辅助马达连续转窑,将各托轮以及止推滚轮的冷却水系统激活,通知电仪组将窑尾的O2分析器插入
到其中使用。
5. 烘窑时的注意事项
烘窑时还要根据一些具体的情况去进行调整,例如烘窑时,在二段旋风筒出口处,温度达到100度时就要将进料皮带机以及转饲机开动起来,由于带运机与旋风筒间的距离较短,旋风筒的热辐射会造成带运机的温度过高而损坏。
在点火时将进料室中的通料口微微打开,防止在预热机中有易燃性气体的聚集(因为是用瓦斯点燃,如果是用气体燃料时更要注意,不完全燃烧所产生的CO),当温度过高时可能有爆炸的危险。
在烘窑时,冷却机风车都没有打开,只是预热机风车抽而以。
在烘窑加热的过程中,预热机中所有的观测孔、清料孔及人孔都要关闭。
在烘窑的过程中,窑内最好不要有保护层,如生料。
因为在这种保护层的下部,耐火砖的升温速度慢,当窑翻转时,温度较低的部份就会露出接触高温,引起耐火砖热振而破碎。
烘窑时三次风管及下料管都关闭,因为在窑尾气体上升管道中有高温气体的通过,所以在三次风管的喷煤嘴中风车还是要打开,对风管进行冷却。