浅析采煤机控制系统的发展
浅析煤矿机电一体化技术的现状和发展趋势
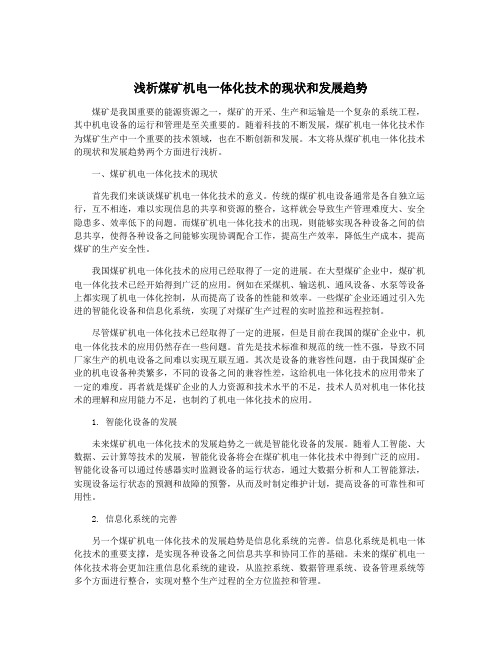
浅析煤矿机电一体化技术的现状和发展趋势煤矿是我国重要的能源资源之一,煤矿的开采、生产和运输是一个复杂的系统工程,其中机电设备的运行和管理是至关重要的。
随着科技的不断发展,煤矿机电一体化技术作为煤矿生产中一个重要的技术领域,也在不断创新和发展。
本文将从煤矿机电一体化技术的现状和发展趋势两个方面进行浅析。
一、煤矿机电一体化技术的现状首先我们来谈谈煤矿机电一体化技术的意义。
传统的煤矿机电设备通常是各自独立运行,互不相连,难以实现信息的共享和资源的整合,这样就会导致生产管理难度大、安全隐患多、效率低下的问题。
而煤矿机电一体化技术的出现,则能够实现各种设备之间的信息共享,使得各种设备之间能够实现协调配合工作,提高生产效率,降低生产成本,提高煤矿的生产安全性。
我国煤矿机电一体化技术的应用已经取得了一定的进展。
在大型煤矿企业中,煤矿机电一体化技术已经开始得到广泛的应用。
例如在采煤机、输送机、通风设备、水泵等设备上都实现了机电一体化控制,从而提高了设备的性能和效率。
一些煤矿企业还通过引入先进的智能化设备和信息化系统,实现了对煤矿生产过程的实时监控和远程控制。
尽管煤矿机电一体化技术已经取得了一定的进展,但是目前在我国的煤矿企业中,机电一体化技术的应用仍然存在一些问题。
首先是技术标准和规范的统一性不强,导致不同厂家生产的机电设备之间难以实现互联互通。
其次是设备的兼容性问题,由于我国煤矿企业的机电设备种类繁多,不同的设备之间的兼容性差,这给机电一体化技术的应用带来了一定的难度。
再者就是煤矿企业的人力资源和技术水平的不足,技术人员对机电一体化技术的理解和应用能力不足,也制约了机电一体化技术的应用。
1. 智能化设备的发展未来煤矿机电一体化技术的发展趋势之一就是智能化设备的发展。
随着人工智能、大数据、云计算等技术的发展,智能化设备将会在煤矿机电一体化技术中得到广泛的应用。
智能化设备可以通过传感器实时监测设备的运行状态,通过大数据分析和人工智能算法,实现设备运行状态的预测和故障的预警,从而及时制定维护计划,提高设备的可靠性和可用性。
浅谈我国采煤机发展现状及趋势

浅谈我国采煤机发展现状及趋势摘要:采煤机作为综合机械化采煤设备的主要设备之一,它扮演了重要角色。
本文简述了现阶段采煤机的发展历程及目前我国采煤机发展现状,指出了我国采煤机的发展前景和主攻方向着重在于发展采煤机的可靠性和自动化技术以及大功率等。
关键词:采煤机;种类;现状;发展趋势.1采煤机的发展历程20世纪40年代初,英国和前苏联相继研制出了链式采煤机,这种采煤机是通过截链截落煤,在截链上安装有被称为截齿的专用截煤工具,其工作效率低。
同时德国研制出了用刨削方式落煤的刨煤机。
50年代初,英国和德国相继研制出了-滚筒式采煤机,在这种采煤机上安装有截煤滚筒,这是一种圆筒形部件,其上安装有截齿,用截煤滚筒实现落煤和装煤。
这种采煤机与可弯曲输送机配套,奠定了煤炭开采机械化的基础。
这种采煤机的主要缺点有二点:其一是截煤滚筒的高度不能在使用中调整,对煤层厚度及其变化适应性差;其二是截煤滚筒的装煤效果不佳,限制了采煤机生产率的提高。
进入60年代,英国、德国、法国和前苏联先后对采煤机的截割滚筒做出革命性改进。
其一是截煤滚筒可以在使用中调整其高度,完全解决对煤层赋存条件的适应性;其二是把圆筒形截割滚筒改进成螺旋叶片式截煤滚筒,即螺旋滚筒,极大地提高了装煤效果。
这两项关键的改进是滚筒式采煤机称为现代化采煤机械的基础。
可调高螺旋滚筒采煤机或刨煤机与液压支架和可弯曲输送机配套,构成综合机械化采煤设备,使煤炭生产进入高产、高效、安全和可靠的现代化发展阶段。
从此,综合机械化采煤设备成为各国地下开采煤矿的发展方向。
自70年代以来,综合机械化采煤设备朝着大功率、遥控、遥测方向发展,其性能日臻完善,生产率和可靠性进一步提高。
工矿自动检测、故障诊断以及计算机数据处理和数显等先进的监控技术已经在采煤机上的到应用。
2国内外采煤机技术差距我国采煤机械技术经历了近半个世纪的发展,已在国际采煤机械领域占取一席之地,形成了自主知识产权的开采范围1.1~5.5m的滚筒式采煤机系列产品,我国采煤机械部分技术已处于国际领先地位。
采煤机自动控制系统分析
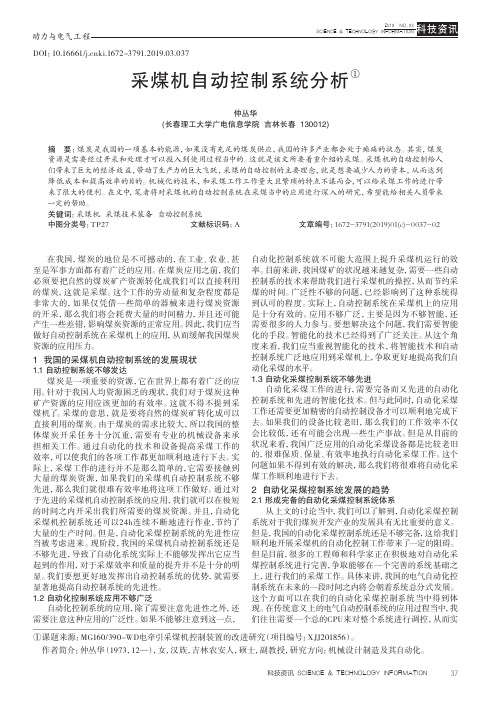
37科技资讯 SCIENCE & TECHNOLOGY INFORMATIONDOI:10.16661/ki.1672-3791.2019.03.037采煤机自动控制系统分析①仲丛华(长春理工大学广电信息学院 吉林长春 130012)摘 要:煤炭是我国的一项基本的能源,如果没有充足的煤炭供应,我国的许多产业都会处于瘫痪的状态。
其实,煤炭资源是需要经过开采和处理才可以投入到使用过程当中的。
这就是该文所要着重介绍的采煤。
采煤机的自动控制给人们带来了巨大的经济效益,带动了生产力的巨大飞跃,采煤的自动控制的主要理念,就是想要减少人力的资本,从而达到降低成本和提高效率的目的。
机械化的技术,和采煤工作工作量大且繁琐的特点不谋而合,可以给采煤工作的进行带来了很大的便利。
在文中,笔者将对采煤机的自动控制系统在采煤当中的应用进行深入的研究,希望能给相关人员带来一定的帮助。
关键词:采煤机 采煤技术装备 自动控制系统中图分类号:TP27 文献标识码:A 文章编号:1672-3791(2019)01(c)-0037-02①课题来源:MG160/390-WD电牵引采煤机控制装置的改进研究(项目编号:XJJ201856)。
作者简介:仲丛华(1973,12—),女,汉族,吉林农安人,硕士,副教授,研究方向:机械设计制造及其自动化。
在我国,煤炭的地位是不可撼动的,在工业、农业、甚至是军事方面都有着广泛的应用。
在煤炭应用之前,我们必须要把自然的煤炭矿产资源转化成我们可以直接利用的煤炭,这就是采煤。
这个工作的劳动量和复杂程度都是非常大的,如果仅凭借一些简单的器械来进行煤炭资源的开采,那么我们将会耗费大量的时间精力,并且还可能产生一些差错,影响煤炭资源的正常应用。
因此,我们应当做好自动控制系统在采煤机上的应用,从而缓解我国煤炭资源的应用压力。
1 我国的采煤机自动控制系统的发展现状1.1 自动控制系统不够发达煤炭是一项重要的资源,它在世界上都有着广泛的应用。
浅析煤矿机电一体化技术的现状和发展趋势

浅析煤矿机电一体化技术的现状和发展趋势煤矿机电一体化技术是以机电一体化为基础,结合计算机、网络通信等先进技术,实现煤矿设备和系统之间的智能化互联互通,从而提高生产效率、保障安全生产、节约能源、减少人工成本,是煤矿现代化生产的重要手段。
本文就煤矿机电一体化技术的现状和发展趋势展开分析。
一、煤矿机电一体化技术的现状1. 技术在煤矿生产中的应用目前,煤矿机电一体化技术已广泛应用于煤矿生产中的各个环节,包括采矿、洗选、运输等各个环节。
在采煤过程中,通过自动化采煤机等设备的应用,实现对煤矿开采过程的自动化控制,减少人工操作,提高作业效率,降低事故风险。
在煤矿的洗选环节,利用机电一体化技术实现对洗煤厂设备的自动监控和调控,提高洗选效率,保障产品质量。
在煤矿运输环节,通过自动化输送带和搬运机器人等设备的应用,实现煤矿内部的物料运输自动化,提高运输效率,降低物料损耗。
2. 技术发展趋势目前,随着信息技术和通信技术的快速发展,煤矿机电一体化技术也在不断向智能化、网络化方向发展。
未来,煤矿机电一体化技术将更加注重对设备之间的信息互通和智能化控制,实现设备之间的自动协同作业。
随着人工智能技术的逐渐成熟,煤矿机电一体化技术将更加注重对设备的智能化感知和决策能力,实现对设备状态的实时监控和智能故障诊断。
随着5G、物联网等新一代通信技术的广泛应用,煤矿机电一体化技术将更加注重对设备之间的无线互联,实现对煤矿整个生产过程的实时监控和智能调度。
1. 深度融合人工智能技术随着人工智能技术的迅速发展,煤矿机电一体化技术将更加注重对设备的智能化控制和决策能力。
未来,煤矿机电一体化技术将利用机器学习、深度学习等人工智能技术,实现对煤矿设备状态的智能感知和预测,实现对设备运行过程的自主调控和故障预警。
2. 智能化互联网化未来,煤矿机电一体化技术将更加注重对设备之间的信息互通和智能化协同。
通过无线传感器网络、物联网等新一代通信技术,实现对煤矿所有设备的实时监控和远程控制。
采煤机电控系统介绍及发展方向

采煤机电控系统介绍及发展方向作者:邓耀来源:《中国科技博览》2013年第23期[摘要]鹤矿集团综采系统电牵引采煤机电控系统,电力拖动系统取代液压传动系统,其电控设备都安装在采煤机身中部的电控部内。
由于电控箱内的干扰电场、干扰磁场过于强大常常造成主控系统工作失常。
针对这种情况,在采煤机电控部的结构设计以及在电控系统的安装过程中采取了以下几项措施。
[关键词]电控系统;干扰磁场;信息传输系统中图分类号:G354.4 文献标识码:A 文章编号:1009-914X(2013)23-0054-01我国的滚筒式采煤机从60年代开始自行研制,70年代初研制成功第1台用于普采工作面的DY150型液压牵引采煤机,到90年代我们已经有了大功率交流电牵引采煤机MG400/920-WD型,整个技术水平得到了较大发展。
总的看来,滚筒式采煤机总体技术的发展过程经历了:牵引方式从液压牵引到电牵引、驱动方式从单电机到多电机、总体结构从纵向布置到横向布置。
采煤机的电控技术也随之逐步发展,从引进仿制到自行设计,从分立元件组成到集成化、PLC和微机控制,逐步走向成熟,赶超国际同行先进水平。
随着我国基础工业特别是电力电子工业技术水平的不断提高,近年来国产采煤机越来越多的采用电牵引形式。
电牵引采煤机较液压牵引采煤机具有许多优点,如液压牵引采煤机液压牵引部件有许多难以克服的故障和燃油着火的危险;电牵引采煤机可以获得很高的牵引速度;电牵引采煤机结构简单,维护方便,运行稳定、可靠;电牵引采煤机的使用成本低、操作简便。
液压牵引采煤机的故障不易检查出来,而电牵引采煤机易于装备故障诊断,故障报警、故障保护及工况显示齐全等。
正因如此,电牵引采煤机的使用逐步得到了普及。
目前,国外生产的采煤机已经完成了由液压牵引形式向电牵引形式的转换过程,国内采煤机除机身较薄的机型,以及部分用户要求使用液压牵引形式的以外,其它采煤机产品,特别是用于中厚、厚煤层的产品均为电牵引形式。
采煤机速度自动控制系统探究
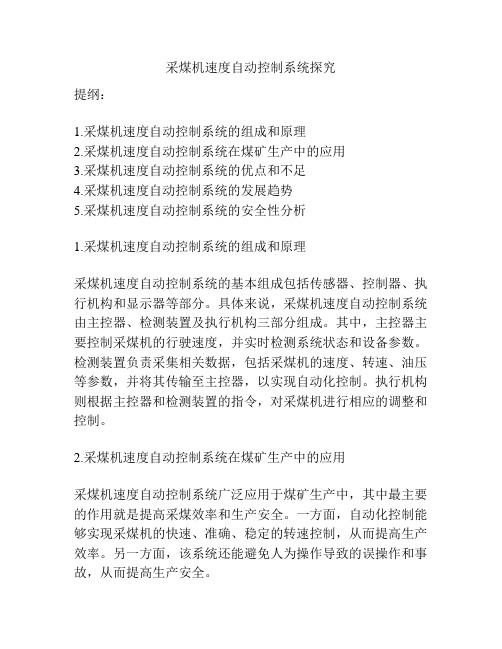
采煤机速度自动控制系统探究提纲:1.采煤机速度自动控制系统的组成和原理2.采煤机速度自动控制系统在煤矿生产中的应用3.采煤机速度自动控制系统的优点和不足4.采煤机速度自动控制系统的发展趋势5.采煤机速度自动控制系统的安全性分析1.采煤机速度自动控制系统的组成和原理采煤机速度自动控制系统的基本组成包括传感器、控制器、执行机构和显示器等部分。
具体来说,采煤机速度自动控制系统由主控器、检测装置及执行机构三部分组成。
其中,主控器主要控制采煤机的行驶速度,并实时检测系统状态和设备参数。
检测装置负责采集相关数据,包括采煤机的速度、转速、油压等参数,并将其传输至主控器,以实现自动化控制。
执行机构则根据主控器和检测装置的指令,对采煤机进行相应的调整和控制。
2.采煤机速度自动控制系统在煤矿生产中的应用采煤机速度自动控制系统广泛应用于煤矿生产中,其中最主要的作用就是提高采煤效率和生产安全。
一方面,自动化控制能够实现采煤机的快速、准确、稳定的转速控制,从而提高生产效率。
另一方面,该系统还能避免人为操作导致的误操作和事故,从而提高生产安全。
3.采煤机速度自动控制系统的优点和不足采煤机速度自动控制系统的优点主要有以下几个方面:首先,由于自动控制,可以减少人为操作错误,提高生产效率和生产安全;其次,采煤机速度自动控制系统还能够在各种恶劣工况下工作,如高温、高湿度等环境;最后,该系统具有灵活性和可调节性,可以根据实际需要进行调整。
然而,采煤机速度自动控制系统也存在一些不足之处。
首先,该系统需要大量的进口部件,成本较高;其次,系统的可靠性和稳定性还需要进一步改进,以便更好地满足煤矿生产的实际需求。
4.采煤机速度自动控制系统的发展趋势未来采煤机速度自动控制系统的发展趋势主要有以下几个方面:一方面,该系统将更加智能化,能够自主进行判断和决策;另一方面,系统将更加普及、应用更为广泛。
此外,随着科技不断进步,该系统还能够更好地满足人们的实际需求。
浅析煤矿机电一体化技术的现状和发展趋势

浅析煤矿机电一体化技术的现状和发展趋势煤矿机电一体化技术是以机电产品技术为基础,融合自动化、信息化、软件技术等多种技术于一体,实现煤炭采掘全过程的数字化、智能化、无人化、安全化和高效化的一种高新技术。
煤矿机电一体化技术的现状和发展趋势是重要的研究课题,以下对其进行浅析。
一、现状目前,我国煤矿机电一体化技术取得了显著进展,已成为国内外矿井采掘技术发展的重要方向之一。
煤矿机电一体化技术主要涉及到采掘机械、输送机械、通风机械、水泵、控制系统等方面。
在采掘机械方面,煤矿机电一体化技术的应用主要体现在智能化和自动化上,如无人驾驶采煤机和无人驾驶绞车等。
在输送机械方面,煤矿机电一体化技术的应用主要解决了高速输送、大量输送和长距离输送等方面的问题。
在通风机械方面,煤矿机电一体化技术的应用主要解决了通风系统的效率和安全性问题。
在水泵方面,煤矿机电一体化技术的应用主要解决了水利工程和矿井排水等方面的问题。
在控制系统方面,煤矿机电一体化技术的应用主要实现了生产过程全程的信息化和数字化,提高了生产过程的准确性、精度和效率。
二、发展趋势(1)更加智能化和自动化煤矿机电一体化技术的发展趋势是更加智能化和自动化。
随着人工智能和大数据技术的迅速发展,煤矿机械将更加智能化,自动化程度也会更高。
未来,采煤机械将会实现全人工智能化控制,而非常规的数字化、自动化控制,从而提高生产效率、质量和安全性。
(2)更加数字化和集成化煤矿机电一体化技术的发展趋势是更加数字化和集成化。
煤矿系统将实现数字化操作、数字化编程和数字化控制。
未来,整个煤矿生产系统将会形成数字化、信息化和智能化的生产模式,从而提高信息传递的效率和生产过程的准确性和可靠性。
(3)更加节能和环保煤矿机电一体化技术的发展趋势是更加节能和环保。
未来,煤矿机电产品将会节能、减排、循环利用,以实现绿色开采、循环发展的目标。
此外,煤矿机电一体化技术将针对煤矿生产过程中的环境污染问题进行研究和解决,如机械噪声、粉尘等污染问题,从而更好地保护矿工和环境。
《采煤机智能调高控制理论与技术》范文

《采煤机智能调高控制理论与技术》篇一一、引言采煤业作为国家经济发展的重要支柱,随着技术的进步,传统的人工操作模式逐渐向智能化和自动化方向转变。
在采煤过程中,智能调高控制技术尤为重要,因为它直接影响着煤炭的开采效率和安全。
本文将探讨采煤机智能调高控制的理论基础、技术发展及其在实践中的应用。
二、采煤机智能调高控制理论基础1. 控制系统架构采煤机智能调高控制系统主要由传感器、控制器和执行器三部分组成。
传感器负责实时感知采煤机的位置、速度、负载等信息;控制器则根据这些信息做出决策,并通过执行器实现控制。
这种闭环控制系统可以保证采煤机在各种工况下都能稳定运行。
2. 控制算法智能调高控制算法是采煤机控制系统的核心。
常见的算法包括PID控制、模糊控制、神经网络控制等。
这些算法可以根据采煤机的实际工况,实时调整控制参数,以达到最佳的开采效果。
三、采煤机智能调高控制技术发展1. 传感器技术传感器是采煤机智能调高控制系统的关键组成部分。
随着技术的发展,传感器逐渐向高精度、高稳定性的方向发展。
例如,激光雷达、红外传感器等的应用,使得采煤机能够更准确地感知周围环境。
2. 控制器技术控制器是采煤机智能调高控制系统的“大脑”。
随着计算机技术和人工智能技术的发展,控制器逐渐向高性能、高集成度的方向发展。
例如,采用FPGA(现场可编程门阵列)的控制器可以实现更快的处理速度和更高的可靠性。
3. 执行器技术执行器是采煤机智能调高控制系统的“手脚”。
随着电机和液压技术的进步,执行器逐渐向高效、低能耗的方向发展。
例如,采用永磁直流电机的执行器具有较高的效率和较长的寿命。
四、实践应用采煤机智能调高控制在实践中有着广泛的应用。
通过实时感知采煤机的位置、速度、负载等信息,控制系统可以自动调整采煤机的切割高度,以保证煤炭的开采效率和安全。
此外,智能调高控制还可以实现远程监控和故障诊断,进一步提高采煤机的可靠性和维护效率。
五、未来展望随着技术的不断进步,采煤机智能调高控制技术将进一步向高效、智能、环保的方向发展。
- 1、下载文档前请自行甄别文档内容的完整性,平台不提供额外的编辑、内容补充、找答案等附加服务。
- 2、"仅部分预览"的文档,不可在线预览部分如存在完整性等问题,可反馈申请退款(可完整预览的文档不适用该条件!)。
- 3、如文档侵犯您的权益,请联系客服反馈,我们会尽快为您处理(人工客服工作时间:9:00-18:30)。
浅析采煤机控制系统的发展
发表时间:2019-09-03T17:00:11.337Z 来源:《科学与技术》2019年第07期作者:李建新1 尹动2
[导读] 但是由于采煤机在井下的工作环境极复杂恶劣,增加了采煤机控制系统自动化的实现难度,更加阻碍了新型技术在采煤机系统上的应用。
1.新汶矿业集团有限责任公司翟镇煤矿机电安装队 271200
2.新汶矿业集团有限责任公司翟镇煤矿机电安装队 271200
在我国现代化煤矿中始终将高产高效作为第一要务,生产实践的经验表明,煤矿生产中只有实施综合机械化才是实现高效安全开采的有效途径。
而与煤炭生产直接相关的是工作面配套的采煤机等关键设备,是由电气、机械、液压等多个独立系统构成的,系统结构比较复杂。
采煤机的电气控制系统是采煤机割煤工作执行过程中的控制中枢,电气控制系统的性能的好坏与煤炭生产的产量和效率直接相关,关系着重大的经济效益问题。
但是由于采煤机在井下的工作环境极复杂恶劣,增加了采煤机控制系统自动化的实现难度,更加阻碍了新型技术在采煤机系统上的应用。
关键词:采煤机;控制系统;发展
(一)采煤机控制系统结构特点
采煤机电控系统的控制对象是一种在特殊环境下,实时运动的机电液一体化的重型设备,采煤机电控系统各部分间存在着相互作用的反馈调节,对控制系统的实时性,提出了相当高的要求。
煤矿电气控制系统通常采用的技术是以计算机为核心的,利用嵌入式系统来实现的控制系统,是以独立的计算机为控制中枢的集中控制系统,另一种是分布式控制系统。
传统集中控制系统通过现场总线等方式将采集的信号送到控制计算机,现场总线传输的信息发送至距离执行装置较近的输出模块,至此完成了信号的输出。
采煤机集中控制系统的一个显著优点就是可以简化现场接线模式,通过数字信号的有效传输,对增强信号的抗干扰能力有一定支持,提高了信号传输的质量。
分布式集中控制系统增强了系统可靠性,简化了现场控制信号走线,有助于简化控制对象结构设计。
(二)采煤机电气控制系统特殊要求
1、采煤机是一种特殊的工业设备,井下工作环境恶劣,周围含有瓦斯和煤尘等爆炸性气体,因此要求控制系统必须具备防爆特性,符合煤矿安全要求。
2、电牵引技术在采煤机中广泛使用,使得电气控制系统故障越来越多。
由于井下电气控制系统故障难处理,直接影响设备的开机率,导致生产效率降低,甚至可能使采煤机失控造成人身伤亡和设备的严重损坏。
为避免此类事件的发生,应在入井设计开发前做好研究,使系统软硬件能够限制或隔离故障对其影响,从而保证系统的操作运行。
3、随着现代化工业技术的发展,对于现代化矿井要求采煤机的自动化程度不断提高,采煤机的功率不断增大,这就要求采煤机电气控制系统在满足操作和系统保护的基本功能需求以外,更应考虑为煤矿新技术设备的应用提供足够的硬件平台支持。
4、煤矿电气控制系统的自身结构应坚固、具有实用性、耐用等特点,还应在尽可能的情况下采取高级别的抗电磁冲击和机械振动冲击的防治措施。
5、煤矿特殊的工作环境下,对采煤机的性能要求也不尽相同,在采煤机电气控制系统中应注意系统的硬件配置的灵活性和扩展性,尽量按照用户的需求定制系统。
(三)采煤机控制系统的抗干扰技术
1、采煤机电控系统的抗干扰技术
煤矿井下电控系统抗电磁干扰一方面来自系统外部电磁干扰,还有就是电路系统工作时产生的对系统本身的干扰。
解决电磁干扰应尽量切断干扰的传播途径,对于传导干扰,可采取尽量减少对外部引线,合理布置外部引线,增强受干扰影响大的敏感电路干扰承受能力,对干扰源采取屏蔽接地、输出端加装 EMI 滤波器、远离敏感电路布置等。
2、采煤机电控系统的可靠性
由于采煤机长时间工作在恶劣环境下,采煤机自身及周围机电设备都是很强的电磁干扰源,对电气控制系统的可靠性和抗干扰能力有重要影响。
采煤机电气控制系统的硬件可靠性往往取决于控制电子电路及元器件的可靠性。
在元器件选择上尽量选择成熟的器件,应注重质量保证及生产制造工艺。
再设计早期对元器件的热操作特性、发热和散热需求进行工程对比分析。
(四)主控部分的具体功能实现
1、主回路
主回路主要是由隔离开关QSI,QSZ,截割电机,牵引电机,变频器箱等组成。
煤机送电。
首先把隔离开关QSI,QSZ旋转到“合”的位置上,然后把煤机工作开关SAI顺时针旋转到启动位置维持数秒,先导回路导通,控制前级磁力启动器接通,开始向煤机供电。
具体过程为:隔离开关QSI合上后,变频器箱上电,载波(通讯)接收模块开始工作,准备接收位于采煤机中的载波(通讯)发送模块的控制信号;煤机工作开关SAI旋转到启动位置,载波(通讯)发送模块检测到此动作后,以载波或通讯方式向载波(通讯)接收模块发送煤机启动控制信号,载波(通讯)接收模块接收到启动控制信号后,闭合串联在先导回路中的煤机启动继电器,先导回路导通,前级磁力启动器启动,煤机上电。
煤机上电后截割电机即开始运行。
若想切断采煤机电源则需将开关SAI逆时针旋转到停止位置松手。
注:隔离开关严禁带负荷操作。
2、控制部分
a.控制变压器TCI。
TCI将主电源 1140V变成 110V,100V,25V,其中25V给主控器箱供电,110V和10OV经整流桥VCI,VCZ整流后给电磁制动器线圈供电。
b.主控器箱。
主控器采集电机电流、温度,瓦斯含量等各种工况信息,接收来自端头站和遥控器的控制信息,进行逻辑判断,控制系统运行,并在端头站和工控机屏幕上显示系统运行状态。
c.端头站。
为本安型操作站,由主控器本安12V供电。
端头站与主控器之间通过串口通讯方式传递数据。
操作人员通过端头站可以进
行牵引,急停,工况信息和故障查询,参数设置等操作。
d.遥控器。
为本安型操作站,由电池供电,与内置在电控箱中的接收装置组成无线遥控系统,可实现对煤机的牵引,急停等操作。
3、变频器
本电控系统为机外载交流变频调速系统,变频器箱供电电压为 1140V,变频器输出频率和电压可变的电流驱动牵引电机,实现煤机的牵引调速。
4、传感器
电控系统中使用了电流互感器,甲烷传感器等各种检测设备,它们将电流,瓦斯含量等信息变成电信号送入主控器,由主控器进行数据处理,实现控制和保护功能。
5、电控系统功能
操作控制功能完成煤机开启,牵引控制,急停等操作,通过端头站或遥控器实现。
结语:本文先对采煤机智能化控制系统主要构成及其设计进行了研究,然后对采煤机智能化监控系统的识别技术进行了阐述,并对采煤机智能控制系统的总体结构设计进行了探究,希望可以为同行业提供一定的借鉴。
参考文献:
[1]梁延召.采煤机智能化控制系统研究与设计[J].建筑工程技术与设计,2018, (25):814.
[2]李涛.采煤机自动控制系统与关键因素分析[J].内蒙古煤炭经济,2018, (10):62.
[3]路染妮.采煤机智能化控制系统研究与设计[J].煤矿机械,2018, 39(2):23.。