橡胶硫化剂的研究进展
氟橡胶硫化机理的研究进展

base
CH - CF
C =C
HF
②双亲核试剂 Nu - R - Nu通过亲核加成反应 ,
加成到双键上形成交联 。
2 硫化种类及其机理
氟橡胶的种类繁多 ,其化学交联也各不相同 ,但 其交联机理却可以归结为以下两种 :离子型和自由 基型 。离子型包括胺类硫化和双酚类硫化 ,而自由 基型包括有机过氧化物硫化和辐射交联硫化 。目前 工业上常用的硫化配合有二胺及其衍生物硫化体
2)二元胺通过迈克尔加成反应加成到 - CH = CF - 双键上形成了交联 。
3)在二段硫化过程中 ,从交联点上继续脱去
HF形成 - N = C 双键 。
如果在氧气氛围中长时间加热 ,容易脱硫 ,即发 生以下热分解反应 [ 9 ] :
2. 1. 2 双酚类硫化体系 [ 3, 5, 8 ] 双酚硫化系统是在 20世纪 60年代末期发展起
过氧化物交联是一种自由基交联方式 ,它包括 以下两个过程 :一 、通过加热使过氧化物分解而产生 自由基 ,然后吸收聚合物链中叔碳原子上的 H 或交 联点单 体 ( CSM ) 上 的 活 性 点 (如 B r、I等 卤 素 离 子 ) ,形成聚合物自由基 。二 、聚合物自由基直接或 者通过自由基捕捉剂的媒介作用来形成交联键 。由 于链节间活动性很小 ,为此大部分聚合物基团不能 直接形成交联键 ,而是失去活性 ,如氧 、杂质的相互 作用或由于主链破坏的不均性等 。为了消除以上不 良过程和提高交联的有效性 ,所以添加了在聚合物 中活动性较强和能很快地在它的双键上接上基团中 心的自由基接受体 。其交联机理如图 4所示 [ 3, 10 ] 。
由于偏氟乙烯类氟橡胶在胺类及双酚类硫化过
程中产生的 HF等酸性气体会腐蚀设备及对人体产
橡胶绿色交联策略研究进展--应对硫化污染问题及废橡胶的高值回收
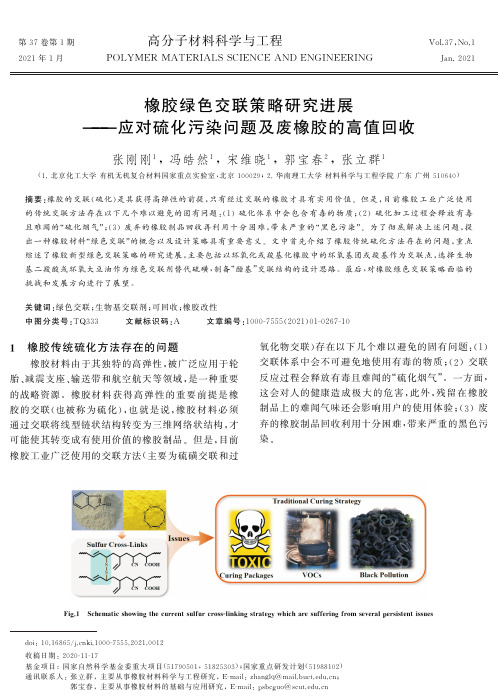
第37卷第1期高分子材料科学与工程V o l .37,N o .1 2021年1月P O L YM E R MA T E R I A L SS C I E N C E A N DE N G I N E E R I N GJ a n .2021橡胶绿色交联策略研究进展应对硫化污染问题及废橡胶的高值回收张刚刚1,冯皓然1,宋维晓1,郭宝春2,张立群1(1.北京化工大学有机无机复合材料国家重点实验室,北京100029;2.华南理工大学材料科学与工程学院广东广州510640)摘要:橡胶的交联(硫化)是其获得高弹性的前提,只有经过交联的橡胶才具有实用价值㊂但是,目前橡胶工业广泛使用的传统交联方法存在以下几个难以避免的固有问题:(1)硫化体系中会包含有毒的物质;(2)硫化加工过程会释放有毒且难闻的 硫化烟气 ;(3)废弃的橡胶制品回收再利用十分困难,带来严重的 黑色污染 ㊂为了彻底解决上述问题,提出一种橡胶材料 绿色交联 的概念以及设计策略具有重要意义㊂文中首先介绍了橡胶传统硫化方法存在的问题,重点综述了橡胶新型绿色交联策略的研究进展,主要包括以环氧化或羧基化橡胶中的环氧基团或羧基作为交联点,选择生物基二羧酸或环氧大豆油作为绿色交联剂替代硫磺,制备 酯基 交联结构的设计思路㊂最后,对橡胶绿色交联策略面临的挑战和发展方向进行了展望㊂关键词:绿色交联;生物基交联剂;可回收;橡胶改性中图分类号:T Q 333 文献标识码:A 文章编号:1000-7555(2021)01-0267-10d o i :10.16865/j.c n k i .1000-7555.2021.0012收稿日期:2020-11-17基金项目:国家自然科学基金委重大项目(51790501,51825303);国家重点研发计划(51988102)通讯联系人:张立群,主要从事橡胶材料科学与工程研究,E -m a i l :z h a n g l q@m a i l .b u c t .e d u .c n ;郭宝春,主要从事橡胶材料的基础与应用研究,E -m a i l :p s b c gu o @s c u t .e d u .c n 1 橡胶传统硫化方法存在的问题橡胶材料由于其独特的高弹性,被广泛应用于轮胎㊁减震支座㊁输送带和航空航天等领域,是一种重要的战略资源㊂橡胶材料获得高弹性的重要前提是橡胶的交联(也被称为硫化),也就是说,橡胶材料必须通过交联将线型链状结构转变为三维网络状结构,才可能使其转变成有使用价值的橡胶制品㊂但是,目前橡胶工业广泛使用的交联方法(主要为硫磺交联和过氧化物交联)存在以下几个难以避免的固有问题:(1)交联体系中会不可避免地使用有毒的物质;(2)交联反应过程会释放有毒且难闻的 硫化烟气㊂一方面,这会对人的健康造成极大的危害,此外,残留在橡胶制品上的难闻气味还会影响用户的使用体验;(3)废弃的橡胶制品回收利用十分困难,带来严重的黑色污染㊂F i g .1 S c h e m a t i c s h o w i n g t h e c u r r e n t s u l f u r c r o s s -l i n k i n g s t r a t e g y w h i c ha r e s u f f e r i n g f r o ms e v e r a l pe r s i s t e n t i s s u e s1.1硫化剂对于硫磺硫化体系而言,其中的促进剂和活化剂是必不可少的㊂它们的主要作用有:降低硫磺用量,加快硫化速率,降低硫化温度,同时可以提高硫化程度及改善橡胶制品的物理力学性能等㊂橡胶硫化促进剂按化学结构分,主要有次磺酰胺类㊁噻唑类㊁胍类㊁秋兰姆类㊁硫脲类和二硫代氨基甲酸盐类等[1]㊂目前,综合性能最好且使用最广泛的促进剂为次磺酰胺类㊂但是,促进剂的合成过程往往会伴随非常严重的污染㊂促进剂M是噻唑类促进剂的重要品种,也是生产下游苯并噻唑类和次磺酰胺类促进剂的原料(比如促进剂D M和促进剂C Z㊁促进剂N S等)㊂然而,促进剂M合成过程时间长㊁生产效率低㊁能耗高, 三废 污染严重,且难治理[2,3]㊂另外,在硫化反应过程中,一些常用的促进剂会产生致癌物 N-亚硝胺㊂例如,含仲胺结构的次磺酰胺类促进剂首先会产生仲胺,进而与氮氧化物(N O x)反应,生成稳定的致癌物 N-亚硝胺[4]㊂除此之外,一些促进剂本身有毒且容易分解,例如,促进剂D P G会在170ħ开始分解;促进剂C Z会使人的皮肤产生过敏反应㊂氧化锌(Z n O)作为硫化活化剂,可以催化硫化反应,提高硫化胶的交联密度,改善硫化胶的耐老化性能等[5,6]㊂因此,Z n O在硫磺硫化体系中有着举足轻重的地位㊂但是,Z n O会对水生生物产生极强的毒性[7,8]㊂一些研究人员指出,轮胎磨损颗粒和Z n O生产企业可能是锌污染的主要来源[9~11]㊂早在2004年,欧盟2004/73/E C法规就开始限制Z n O在橡胶制品(尤其是轮胎)中的应用㊂此外,在2016年初,美国加州提出一项类似的法案(S B1260),限制Z n O的使用㊂1.2硫化烟气硫磺硫化是一个非常复杂的反应过程㊂因此,在橡胶材料的硫化工序中会产生大量的 硫化烟气 粉尘和有毒且难闻的挥发性有机物(V O C s)㊂硫化烟气的成分十分复杂,其中的污染因子主要是胺类化合物㊁二硫化碳(C S2)㊁羰基硫化物等[12]㊂例如,一些含氮促进剂(如促进剂C Z)在硫化反应过程会释放胺类化合物;硫磺在高温下会产生大量的含硫化合物㊂因此,硫磺等用量越多,硫化温度越高,硫化反应越容易产生大量的硫化烟气㊂此外,这些硫化过程产生的含硫化合物和胺类化合物等大多具有刺激性的恶臭,气味阈值很低,也就是说,空气中有极少量的这些物质就会令人恶心㊁呕吐㊂最重要的是,硫化烟气是诱发职业性肿瘤的罪魁祸首[13]㊂这些难闻且有毒V O C s会一直伴随着橡胶制品,是橡胶制品难闻气味的主要来源㊂尤其是橡胶制品(如汽车密封条)在密闭的环境中使用时,不仅会对用户的健康产生极大的危害,而且还会使其产生强烈不适感[14]㊂除了硫磺硫化体系,过氧化物硫化体系也会产生大量有毒且难闻的V O C s,比如,常用的过氧化二异丙苯(D C P)硫化反应过程中会产生有毒且难闻的分解产物 苯乙酮[15]㊂1.3 黑色污染橡胶材料广泛使用的硫化方法为硫磺硫化或过氧化物硫化,硫化最终形成的交联键(主要为C-S, C-C键等)是典型的不可逆共价键㊂橡胶交联后,就会变得 不溶不熔 ,不能再次重复加工使用㊂同时,废橡胶制品的回收利用非常困难,造成严重的 黑色污染 [16~18]㊂目前,全球每年废橡胶的产生量约为3ˑ107t,其中大部分被焚烧回收热能或经粉碎制成胶粉㊂还有一部分废橡胶可以被用于制备再生胶,即通过打开废橡胶交联键中的C-S-C,C-S-S-C 或C-S x-C键,破坏其中的网络结构,得到再生胶[17]㊂但是传统的脱硫技术打开交联键不具选择性,同时也会造成橡胶分子链被破坏,从而导致再生胶性能较差;另外脱硫工艺还存在能耗大和污染严重等问题[19,20]㊂2橡胶材料新型绿色交联体系的设计针对橡胶传统硫化方法存在的上述问题,北京化工大学张立群教授在国际上提出了橡胶材料 绿色交联 的概念以及设计策略[21]㊂在进行新型绿色交联体系的设计时,该研究团队将交联反应落脚于环氧基团与羧基之间的反应,主要原因可以归结于以下几个方面:(1)环氧与羧基之间有着比较合适的反应活性,非常适合于橡胶的硫化加工过程,从而可以得到一种兼顾焦烧安全性和交联效率的交联体系;(2)环氧化和羧基化橡胶比较容易实现工业化制备,并且已经有商品化的产品,如环氧化天然橡胶(E N R)和羧基化丁腈橡胶(X N B R);(c)基于环氧基团与羧基之间的反应,可以构建一个 酯基 交联网络结构㊂在酸或碱的催化下,交联结构中的 酯基 被选择性地断开,从而得到一种温和且高效的橡胶回收再利用的方法(F i g.2)㊂因此,该新型绿色交联策略可以使橡胶材料实现绿色且高效的交联,还能有利于废橡胶高效回收再利用㊂862高分子材料科学与工程2021年F i g .2G r e e n c u r i n g s t r a t e g y f o r d i e n e r u b b e r b a s e d o n e s t e r l i n k a ge 2.1 生物基二羧酸绿色交联环氧化橡胶大多数二烯烃橡胶的官能化改性都是建立在改变不饱和双键的思路之上,以双键作为反应位点,对其进行氢化㊁环氧化和羧基化等[22]㊂其中,环氧化改性是橡胶改性中最简单㊁易操作的方法,几乎适用于所有的二烯烃橡胶,因此具有非常好的应用前景[23]㊂目前,已经报道的比较常见的环氧化橡胶有E N R [24,25]㊁环氧化丁苯橡胶[26]等㊂因此,可以以环氧化橡胶中的环氧基团作为交联点,选择生物基㊁绿色无毒的二羧酸作为交联剂替代硫磺或过氧化物;基于环氧基团与羧基之间的反应,构建含 酯基 的交联网络结构㊂早在2010年,P i r e 等[27,28]选择十二烷二酸(D A )作为E N R 的交联剂,基于E N R 中环氧基团与D A 中羧基之间的反应,成功地实现了E N R 的交联㊂但是,由于E N R 中的环氧基团活性较低,导致交联效率较低,硫化反应时间过长;此外,最终形成的交联结构含有大量的悬挂链,即D A 上只有1个羧基反应,未能形成有效的交联㊂因此,在随后的研究中,该研究团队发现以1,2-二甲基咪唑(D M I)作为催化剂,能够有效地提高D A 对E N R 的交联效率,其中催化机理是羧基与D M I 形成羧基咪唑金翁盐,然后再进攻环氧基团进行开环反应(F i g.3)[29,30]㊂但是,D M I 往往会伴随着难闻的气味㊂此外,这一系列工作并未对二羧酸交联环氧化橡胶的可回收性能进行研究㊂F i g .3 (a )C r o s s -l i n k i n g o fE N Rb y d o d e c a n e d i o i c a c i d (D A ),(b )g r a f tD A :d i f f e r e n t s e c o n d a r yi n t e r a c t i o n s i n d u c e db y f r e e c a r b o x y l i c g r o u ps F i g .4 I m i d a z o l i u md i c a r b o x y l a t e p r o p o s e da s q u a n t i t a t i v e i n t e r m e d i a t e i n t h e a c c e l e r a t i o nm e c h a n i s mo f c r o s s -l i n k i n gG u o 等[31]通过巯基-烯点击化学的方法,在溶聚丁苯橡胶(S S B R )分子链上引入羟基作为交联点;然后利用氧杂-迈克尔反应,羟基官能化的S S B R 可被多种丙烯酸酯快速交联㊂硫化胶的力学性能和交联962 第1期张刚刚等:橡胶绿色交联策略研究进展应对硫化污染问题及废橡胶的高值回收密度等可以通过改变硫化温度㊁羟基官能化S S B R中羟基含量㊁交联剂丙烯酸酯的官能度或用量等来调节(F i g.5)㊂但是,通过巯基-烯点击化学制备的羟基官能化S S B R中会残存有未反应的巯基乙醇;在硫化过程中,它容易造成橡胶的焦烧(早期交联)㊂此外,该工作也没有关注新型交联橡胶的可回收再利用性能㊂F i g.5(a)M o l e c u l a r s t r u c t u r e s o f c r o s s l i n k e r sw i t hd i f f e r e n t f u n c t i o n a l i t i e s,(b)t h i o l-e n e a d d i t i o nb e t w e e nM Ea n dS S B R[31]近期,张立群教授团队设计合成了一种高活性的环氧化丁苯橡胶,即在乳聚丁苯橡胶(E S B R)的聚合体系中,引入含有环氧基团的第3单体 甲基丙烯酸缩水甘油酯(GMA),成功制备了一系列不同环氧化程度的环氧化乳聚丁苯橡胶(E S B R-GMA)㊂然后,基于E S B R-GMA中环氧基团与二羧酸中羧基之间的反应,构建了 酯基 交联网络结构㊂笔者系统研究了生物基二羧酸的种类和用量以及环氧化橡胶的环氧化程度对E S B R-GMA交联性能的影响(F i g.6)㊂最终,得到了一种简单㊁无催化且高效的绿色交联方法[32]㊂F i g.6(a)P r e p a r a t i o no fE S B R-G M Av i a e m u l s i o n p o l y m e r i z a t i o na n d(b)p r o p o s e d c r o s s-l i n k e ds t r u c t u r e o fE S B R-G M Ac u r e d t h r o u g h e p o x y-a c i d r e a c t i o n s[32]首先,选用不同链长的饱和二羧酸作为交联剂㊂由于饱和二羧酸的p K a值会随链长增加而增加,因此丁二酸(S A)的酸性最大,D A的酸性最小㊂随着二羧酸酸性的提高,E S B R-GMA/C B橡胶复合材料的交联速率㊁交联密度和力学性能等都呈现显著地增加㊂因此,生物基S A表现出最佳的综合性能㊂此072高分子材料科学与工程2021年外,通过研究S A 用量的影响发现,随着S A 用量的增加,样品的交联密度和定伸应力等显著增大,同时交联速率和拉伸强度变化不大(F i g.7)㊂因此,E S -B R -GMA 的力学性能可以通过简单地控制二羧酸的用量等来调节㊂在未加入其它任何助剂的情况下,1ph r S A 就可以使E S B R -GMA /C B 橡胶复合材料获得优异的交联性能和力学性能㊂众所周知,橡胶中的交联点数目也是影响其交联性能的重要因素之一㊂因此,在E S B R -GMA 聚合中,通过调节环氧单体GMA 的比例,从而获得一系列不同GMA 含量的E S B R -GMA ㊂然后,研究E S B R -GMA 的环氧化程度对E S B R -GMA 交联性能的影响㊂结果发现,随着E S B R -GMA 分子链中环氧基团含量增加,样品的交联速率㊁交联密度和定伸应力等显著增大㊂F i g .7 (a )C u r i n g c u r v e s (t =180ħ),(b )t y p i c a l s t r e s s -s t r a i n c u r v e s ,(c )c r o s s -l i n k i n g d e n s i t y,a n d (d )t a n δo f E S B R -G M A /C Bc o m po s i t e sw i t hd i f f e r e n t S Ac o n t e n t s [32] 由于环氧基团与羧酸的反应,在橡胶的交联网络结构中引入了可水解的 酯基 ㊂在强酸或者强碱的催化下,可选择性地将 酯基 水解,从而可以使交联网络中的交联键断开,得到线型回收橡胶㊂如F i g.8所示,二羧酸交联的E S B R -GMA 的交联结构中主要有2种酯基:(1)环氧基团与羧酸交联反应产生的酯基;(2)GMA 单体单元中的酯基㊂在酸或碱的催化下,酯基可以被水解断开,最终可以得到线型羧基化丁苯橡胶㊂这为解决废橡胶带来的 黑色污染 问题提供了新思路㊂综上所述,绿色交联S B R 有望应用在大宗的轮胎制品和橡胶输送带上,帮助轮胎企业降低V O C s 排放,以及降低轮胎产品的气味㊂ F i g .8 S c h e m a t i c i l l u s t r a t i o no f t h e r u b b e r -r e c y c l i n gpr o c e s s o f S A -c u r e dE S B R -G M A [32]172 第1期张刚刚等:橡胶绿色交联策略研究进展应对硫化污染问题及废橡胶的高值回收三元乙丙橡胶(E P D M )具有耐热性能㊁耐老化性能㊁抗冲击性能和低温性能良好等优点,E P D M 最重要的应用领域之一是汽车密封条㊂但是,采用硫磺硫化或过氧化物硫化的E P D M 密封条,会散发出有毒且难闻的V O C s,从而对人的身体健康产生危害㊂近期,张立群教授团队提出对E P D M 进行环氧化改性,然后开发一种新型的绿色交联体系的设计思路[33]㊂首先,通过绿色高效的原位环氧化改性法,成功地制备了环氧化三元乙丙橡胶(e -E P D M )㊂然后,采用生物基D A 作为交联剂,基于e -E P D M 中的环氧基团与生物基D A 中的羧基之间的反应,构建了含β-羟基酯键的共价交联网络结构(F i g .9)㊂该交联体系避免了使用有毒的化学物质,大大降低了硫化过程有毒且难闻V O C s 的释放㊂此外,D A 交联的e -E P -D M /C B 橡胶复合材料具有优异的力学性能,拉伸强度可以达到20M P a 以上㊂从F i g .10可以看到,D A 交联的e -E P D M /C B 橡胶复合材料的拉伸强度与硫磺硫化样品的拉伸强度相近,比D C P 硫化样品的拉伸强度要高得多㊂这个现象的原因可以归结于D A 交联体系的交联网络结构要比D C P 硫化体系的交联网络更均匀㊂综上所述,绿色交联E P D M 有望应用在汽车密封条上,从而推动密封条向 绿色无毒㊁低气味 方向发展㊂F i g .9 (a )P r e p a r a t i o n o f e p o x y g r o u p -f u n c t i o n a l i z e dE P D Mb y i n s i t u e p o x i d a t i o n r e a c t i o n ,(b )t h e c r o s s -l i n k i n gs t r u c t u r e o f e -E P D Mc u r e db y e p o x y-a c i d r e a c t i o n s [33]F i g .10 T y p i c a ls t r e s s -s t r a i nc u r v e so fe -E P D M /C B c o m po s i t e s b a s e d o nd i f f e r e n t c u r i n g s ys t e m s [33]2.2 生物基环氧大豆油绿色交联羧基化橡胶近期,张立群教授团队提出了第2种绿色交联策略,即以羧基化橡胶中的羧基基团作为交联点,以生物基的环氧分子作为交联剂[34]㊂羧基化橡胶在生活中也比较常见㊂目前,已经有商品化的羧基化橡胶,比如羧基丁腈橡胶(X N B R )㊁羧基丁苯橡胶(X S B R )等㊂此外,最重要的是,将交联结构中的酯基水解后,可以重新得到羧基化橡胶,实现羧基化橡胶的 闭环回收㊂该团队以价格低廉的生物基环氧大豆油(E S O )作为商品化X N B R 的绿色交联剂,使X N B R 实现简单㊁有效且绿色的交联㊂基于羧基与环氧基团之间的反应,构建 酯基 交联网络结构㊂该绿色交联方法不使用任何有毒的化学物质,有效降低了硫化过程有毒且难闻V O C s 的释放㊂此外,在发生交联反应前,油状的生物基E S O 还可以大幅度降低X N B R 的门尼黏度,起到增塑作用,有着 一剂多用 的效果(F i g .11)㊂通过调整E S O 的用量,可以实现对X N B R 的交联速率㊁交联密度和力学性能等的调控;E S O 交联的X N B R /C B 橡胶复合材料的力学性能可以在较大的范围内进行调节,尤其是300%定伸应力可以在2.4M P a 到14.1M P a 的范围内调节(F i g.12)㊂这说明该绿色交联体系的力学性能具有优异的可调性,表现出良好的应用前景㊂272高分子材料科学与工程2021年F i g .11 D e s i g n o f n e x t g e n e r a t i o n c r o s s -l i n k i n g s t r a t e g y b a s e do nE S Of o rX N B Rv i a e p o x y-a c i d r e a c t i o n [34]F i g .12 (a )F T -I Rs p e c t r ao fX N B R ,E S O ,X N B R /E S Oc o m p o u n da n d E S O -c u r e d X N B Rc o m p o s i t e ,(b )c u r i n g cu r v e so fX N B R /C B c o m p o u n dw i t hd i f f e r e n t c o n t e n t s o fE S O (t =180ħ),(c )t y p i c a l s t r e s s -s t r a i nc u r v e s a n d (d )c r o s s -l i n k i n g d e n s i t y ofX N B R /C B c o m po s i t e sw i t hd i f f e r e n t c o n t e n t s o fE S O [34]此外,在交联体系中加入少量的Z n O 作为交联反应的催化剂,可以显著地促进环氧-羧基交联反应的进行,加快交联速率和提高交联程度㊂同时,锌离子与羧基形成的离子对或者离子簇可作为增强点,从而可以提高X N B R 的力学性能㊂特别地,当加入2p h r Z n O 时,X N B R /C B 橡胶复合材料的拉伸强度和300%定伸应力分别增加了26.7%和71.1%(F i g.13)㊂T a b .1 M o l e c u l a rw e i g h t o f t h e o r i gi n a l X N B R a n d r e c yc l e dX N B R [33]S a m p l e M n ˑ10-4M w ˑ10-4P D IX N B R9.826.82.72R e c yc l e dX N B R 9.128.93.16在硫酸的催化下,交联结构中的 酯基 被水解成羟基和羧基,重新得到了线型X N B R (F i g.14)㊂372 第1期张刚刚等:橡胶绿色交联策略研究进展应对硫化污染问题及废橡胶的高值回收回收后橡胶的相对分子质量与原始的X N B R 相对分子质量非常接近(T a b .1)㊂从F i g.15中可以发现,再加工后样品的强度得到了很好的恢复㊂再加工后样品的拉伸强度㊁定伸应力和断裂伸长率等都能够恢复到接近初始样品的水平㊂因此,利用该方法,X N -B R 可以被多次循环使用,得到一种高效的 闭环回收 方法㊂综上所述,绿色交联X N B R 有望应用在印刷胶辊以及橡胶手套上,帮助企业降低成本㊂F i g .13 (a )C u r i n g c u r v e s ,(b )t y p i c a l s t r e s s -s t r a i n c u r v e s o fE S O -c u r e dX N B R /C Bc o m po s i t e sw i t hd i f f e r e n t c o n t e n t s o fZ n Ow h i l e t h e c o n t e n t o fE S Ow a s s e t a s 12.0p h r[34]F i g .14 C h e m i c a l r e c y c l i n gpr o c e s s e s o fE S O -c u r e dX N B R (a )o r i g i n a l ,(b )p o s t -s w e l l i n g ,(c )p o s t -r e c y c l i n g r e a c t i o n ,a n d (d )p o s t -c o a g u l a t i n g o f t h eE S Oc u r e dX N B Rs a m pl e [34]F i g .15 (a )F T -I Rs p e c t r a o f t h e o r i g i n a l X N B Ra n d r e c y c l e dX N B R ,(b )t y pi c a l s t r e s s -s t r a i n c u r v e s o f t h e o r i g i n a l a n d r e c y c l e dX N B R /C Bc o m po s i t ew i t h12.0p h rE S O [34]3 展望目前,新型绿色交联橡胶材料的设计㊁制备和性能研究取得了一定的进展,展现出实际应用的潜力㊂但同时也存在许多难题和挑战:(1)与传统硫化体系相比,新型绿色交联体系的硫化温度更高,硫化速率较低;(2)由于交联体系比较简单,新型绿色交联体系的硫化动力学控制,不如硫磺硫化体系灵活;(3)由于交联结构中 酯基 是相对较弱的化学键, 酯基 可能易被破坏,从而可能造成交联橡胶较差的耐老化及耐候性㊂因此,在今后的研究中,如何通过交联体系的设计,实现高硫化速率与焦烧安全性的兼顾,将会是一个重要的研究方向㊂此外,汽车轮胎是橡胶材472高分子材料科学与工程2021年料消耗量最大的橡胶制品;因此,将这种绿色交联方法应用到轮胎制品中,具有重要的科学意义和应用前景㊂参考文献:[1]杨清芝.实用橡胶工艺学[M].北京:化学工业出版社,2005.[2]肖军.我国橡胶助剂三废治理述评[J].化学工业,2011,29(6):38-41.X i a o J.R u b b e r a d d i t i v e s t h r e ew a s t e s t r e a t m e n t i nC h i n a[J].C h e m i c a l I n d u s t r y,2011,29(6):38-41.[3]唐志民,夏海洋,李世伍.橡胶防老剂中间体4-A D P A与促进剂M绿色生产工艺[J].上海化工,2013,38(2):28-32.T a n g Z M,X i a H Y,L iS W.G r e e n p r o d u c t i o n p r o c e s s e so f r u b b e r a n t i o x i d a n t i n t e r m e d i a t e4-A D P Aa n da c c e l e r a n t M[J].S h a n g h a i C h e m i c a l I n d u s t r y,2013,38(2):28-32. [4]张刚刚,梁宽,史金炜,等.橡胶制品生产过程低V O C s技术进展:从材料到工艺[J].高分子通报,2019(2):81-89.Z h a n g GG,L i a n g K,S h i JW,e t a l.R e c e n t a d v a n c e i n r e d u c i n g V O C s e m i s s i o n i nr u b b e r p r o d u c t sm a n u f a c t u r i n g i n d u s t r y[J].P o l y m e rB u l l e t i n,2019(2):81-89.[5] H e i d e m a nG,D a t t aRN,N o o r d e r m e e r JW M,e t a l.A c t i v a t o r s i na c c e l e r a t e d s u l f u r v u l c a n i z a t i o n[J].R ub b e r C h e m i s t r y a n dT e c h n o l o g y,2004,77:512-541.[6] K o o d z i e j c z a k-R a d z i m s k aA,J e s i o n o w s k iT.Z i n c o x i d e-f r o ms y n t h e s i s t o a p p l i c a t i o n:a r e v i e w[J].M a t e r i a l s,2014,7:2833-2881.[7] A d a m sL K,L y o nD Y,A l v a r e zPJ.C o m p a r a t i v ee c o-t o x i c i t yo f n a n o s c a l eT i O2,S i O2,a n dZ n Ow a t e r s u s p e n s i o n s[J].W a t e r R e s e a r c h,2006,40:3527-3532.[8] F r a n k l i nN M,R o g e r sNJ,A p t e SC,e t a l.C o m p a r a t i v e t o x i c i t y o fn a n o p a r t i c u l a t e Z n O,b u l k Z n O,a n d Z n C l2t o a f r e s h w a t e r m i c r o a l g a:t h e i m p o r t a n c eo f p a r t i c l es o l u b i l i t y[J].E n v i r o n m e n t a l S c i e n c e&T e c h n o l o g y,2007,41:8484-8490.[9] C o u n c e l lTB,D u c k e n f i e l dK U,L a n d aER,e t a l.T i r e-w e a rp a r t i c l e s a s a s o u r c e o f z i n c t o t h e e n v i r o n m e n t[J].E n v i r o n m e n t a l S c i e n c e&T e c h n o l o g y,2004,38:4206-4214.[10] R h o d e sEP,R e nZ,M a y sDC.Z i n c l e a c h i n g f r o mt i r e c r u m br u b b e r[J].E n v i r o n m e n t a lS c i e n c e&T e c h n o l o g y,2012,46: 12856-12863.[11]S m o l d e r sE,D e g r y s eF.F a t e a n d e f f e c t o f z i n c f r o mt i r e d e b r i si ns o i l[J].E n v i r o n m e n t a lS c i e n c e&T e c h n o l o g y,2002,36:3706-3710.[12]丁学锋,张慧君,曹睿.浅议轮胎企业有机废气排放因子[J].环境科学导刊,2013,32(5):14-16.D i n g X F,Z h a n g H J,C a o R.D i s c u s s i o n o nt h ee m i s s i o nf a c t o r so ft h e o rg a n i c e xh a u s t g a s o fti r e e n t e r p r i s e s[J].E n v i r o n m e n t a l S c i e n c eS u r v e y,2013,32(5):14-16.[13]黄荣征.硫化烟气危害与治理的研究进展[J].中国职业医学,1995(4):46-47.H u a n g RZ.R e s e a r c h p r o g r e s so nt h eh a r m a n dt r e a t m e n to fs u l f i d e f l u e g a s[J].C h i n a O c c u p a t i o n a l M e d i c i n e,1995(4):46-47.[14] C h e n g H,H uY,R e i n h a r d M.E n v i r o n m e n t a l a n dh e a l t h i m p a c t so f a r t i f i c i a l t u r f:a r e v i e w[J].E n v i r o n m e n t a l S c i e n c e&T e c h n o l o g y,2014,48:2114-2129.[15] N a s k a rK.T h e r m o p l a s t i c e l a s t o m e r s b a s e d o nP P/E P D Mb l e n d s b yd y n a m i cv u l c a n i z a t i o n[J].R u b be r C h e m i s t r y a n d T e c h n o l o g y,2007,80:504-519.[16]I m b e r n o nL,N o r v e zS.F r o ml a n d f i l l i n g t ov i t r i m e r c h e m i s t r y i nr u b b e r l i f ec y c l e[J].E u r o p e a nP o l y m e r J o u r n a l,2016,82:347-376.[17] T a n g Z H,L i uYJ,H u a n g Q Y,e t a l.Ar e a l r e c y c l i n g l o o p o fs u l f u r-c u r e d r u b b e r t h r o u g h t r a n s a l k y l a t i o ne x c h a n g e o fC-Sb o n d s[J].G r e e nC h e m i s t r y,2018,20:5454-5458.[18] K o j i m aM,T o s a k a M,I k e d aY.C h e m i c a l r e c y c l i n g o f s u l f u r-c u r e dn a t u r a l r u b b e r u s i n g s u p e r c r i t i c a l c a r b o n d i o x i d e[J].G r e e nC h e m i s t r y,2004,6:84-89.[19]S h i JW,J i a n g K,R e nD Y,e t a l.S t r u c t u r e a n d p e r f o r m a n c e o fr e c l a i m e dr u b b e ro b t a i n e d b y d i f f e r e n t m e t h o d s[J].J o u r n a lo fA p p l i e dP o l y m e r S c i e n c e,2013,129:999-1007.[20]S h iJ,Z o u H,D i n g L,e ta l.C o n t i n u o u s p r o d u c t i o no f l i q u i dr e c l a i m e dr u b b e rf r o m g r o u n dt i r er u b b e ra n di t sa p p l i c a t i o na sr e a c t i v e p o l y m e r i c p l a s t i c i z e r[J].P o l y m e r D e g r a d a t i o n a n dS t a b i l i t y,2014,99:166-175.[21]Z h a n g G G,Z h o uX X,Z h a n g L Q.C u r r e n t i s s u e s f o rr u b b e rc r o s s l i n k i n g a nd i t s f u t u re t r e n d sofg r e e nch e mi s t r y s t r a t e g y[J].E x p r e s s P o l y m e rL e t t e r s,2019,13:406-406.[22]储俊峰,于丽,刘超豪,等.橡胶环氧化改性的研究进展[J].化工新型材料,2016,44(10):28-29.C h u JF,Y u L,L i u C H,e ta l.R e s e a r c h p r o g r e s so fr u b b e re p o x i d a t i o nm o d if i c a t i o n[J].N e w C h e m i c a l M a t e r i a l s,2016,44(10):28-29.[23]M e n g Y,C h uJF,X u e J J,e t a l.D e s i g na n ds y n t h e s i so fn o n-c r y s t a l l i z a b l e,l o w-T g p o l y s i l o x a n e e l a s t o m e r s w i t h f u n c t i o n a le p o x y g r o u p st h r o u g h a n i o n i cc o p o l y m e r i z a t i o n a n d s u b s e q u e n te p o x i d a t i o n[J].R S CA d v a n c e s,2014,4:31249-31260.[24]何灿忠,彭政,钟杰平,等.环氧化天然橡胶的研究进展[J].高分子通报,2012(2):86-95.H eCZ,P e n g Z,Z h o n g J P,e t a l.R e s e a r c h p r o g r e s s o n e p o x i d i z e dn a t u r a l r u b b e r[J].P o l y m e r B u l l e t i n,2012(2):86-95. [25] Z h a n g X,N i u K,S o n g W,e ta l.T h ee f f e c to fe p o x i d a t i o no ns t r a i n-i n d u c e d c r y s t a l l i z a t i o n o f e p o x i d i z e d n a t u r a lr u b b e r[J].M a c r o m o l e c u l a rR a p i dC o m m u n i c a t i o n s,2019,40:1900042.[26] Q i a oH,C h a oM Y,H u i D,e t a l.E n h a n c e d i n t e r f a c i a li n t e r a c t i o n a n d e x c e l l e n t p e r f o r m a n c e o f s i l i c a/e p o x y g r o u p-f u n c t i o n a l i z e d s t y r e n e-b u t a d i e n e r u b b e r(S B R)n a n o c o m p o s i t e sw i t h o u t a n y c o u p l i n g a g e n t[J].C o m p o s i t e sP a r tB:E n g i n e e r i n g, 2017,114:356-364.[27] P i r eM,N o r v e zS,I l i o p o u l o s I,e t a l.E p o x i d i z e dn a t u r a l r u b b e r/d i c a r b o x y l i ca c i dse l f-v u l c a n i z e db l e n d s[J].P o l y m e r,2010,51:5903-5909.[28] P i r e M,O i k o n o m o u E K,I m b e r n o n L,e ta l.C r o s s l i n k i n g o f572第1期张刚刚等:橡胶绿色交联策略研究进展 应对硫化污染问题及废橡胶的高值回收e p o x i d i z e dn a t u r a l r u b b e rb y d i c a r b o x y l i ca c i d s:a na l t e r n a t i v e t os t a n d a r d v u l c a n i z a t i o n[J].M a c r o m o l e c u l a r S y m p o s i a,2013,331:89-96.[29]P i r eM,L o r t h i o i rC,O i k o n o m o uEK,e t a l.I m i d a z o l e-a c c e l e r a t e d c r o s s l i n k i n g o f e p o x i d i z e dn a t u r a l r ub b e r b y d ic a r b o x y l i ca c i d s:a m e c h a n i s t i ci n v e s t i g a t i o n u s i n g N M R s p e c t r o s c o p y[J].P o l y m e rC h e m i s t r y,2012,3:946-953.[30]P i r eM,N o r v e z S,I l i o p o u l o s I,e t a l.I m i d a z o l e-p r o m o t e da c c e l e r a t i o n o f c r o s s l i n k i n g i n e p o x i d i z e d n a t u r a l r ub b e r/d ic a r b o x y l i ca c i db l e n d s[J].P o l y m e r,2011,52:5243-5249.[31]Z h a n g X,T a n g Z,G u oB.R e g u l a t i o n o fm e c h a n i c a l p r o p e r t i e s o fd ie n er u b b e r c u r e d b y o x a-M i c h a e l R e a c t i o n v i a m a n i p u l a t i n gn e t w o r k s t r u c t u r e[J].P o l y m e r,2018,144:57-64.[32]Z h a n g G,L i a n g K,F e n g H,e t a l.D e s i g n o f e p o x y-f u n c t i o n a l i z e d s t y r e n e-b u t a d i e n e r u b b e rw i t hb i o-b a s e dd i c a r b o x y l i ca c i d a s a c r o s s-l i n k e r t o w a r d t h e g r e e n-c u r i n g p r o c e s s a n dr e c y c l a b i l i t y[J].I n d u s t r i a l&E n g i n e e r i n g C h e m i s t r y R e s e a r c h, 2020,59:10447-10456.[33]Z h a n g G,Z h o uX,L i a n g K,e t a l.M e c h a n i c a l l y r o b u s t a n dr e c y c l a b l e E P D M r u b b e r c o m p o s i t e s b y a g r e e n c r o s s-l i n k i n g s t r a t e g y[J].A C SS u s t a i n a b l eC h e m i s t r y&E n g i n e e r i n g,2019,7: 11712-11720.[34]Z h a n g G,F e n g H,L i a n g K,e t a l.D e s i g n o f n e x t-g e n e r a t i o n c r o s s-l i n k i n g s t r u c t u r ef o re l a s t o m e r st o w a r d g r e e n p r o c e s sa n dar e a l r e c y c l i n g l o o p[J].S c i e n c eB u l l e t i n,2020,65:889-898.P r o g r e s s o nG r e e nC r o s s-L i n k i n g S t r a t e g i e s o fR u b b e r:C o p i n g w i t hV u l c a n i z a t i o nP o l l u t i o n a n dH i g h-V a l u eR e c o v e r y o fW a s t eR u b b e rG a n g g a n g Z h a n g1,H a o r a nF e n g1,W e i x i a oS o n g1,B a o c h u nG u o2,L i q u nZ h a n g1(1.S t a t eK e y L a b o r a t o r y o f O r g a n i c-I n o r g a n i cC o m p o s i t e s,B e i j i n g U n i v e r s i t y o fC h e m i c a lT e c h n o l o g y,B e i j i n g100029,C h i n a;2.D e p a r t m e n t o f P o l y m e rM a t e r i a l s a n dE n g i n e e r i n g,S o u t hC h i n aU n i v e r s i t y o f T e c h n o l o g y,G u a n g z h o u510640,C h i n a)A B S T R A C T:T h ec o v a l e n tc r o s s-l i n k i n g o fe l a s t o m e r si st h e m o s ti m p o r t a n ts t e p f o ra c h i e v i n g h i g he l a s t i c i t y.H o w e v e r,t h e r eh a v eb e e ns e v e r a l i n h e r e n t i s s u e s c a u s e db y t r a d i t i o n a l c r o s s-l i n k i n g m e t h o d s.F i r s t,s o m e c u r i n g a d d i t i v e s h a v e c a u s e d g r e a t t r o u b l e f o r t h e e n v i r o n m e n t.S e c o n d,s o m e c u r i n g a d d i t i v e s t e n d t o r e l e a s e t o x i c v o l a t i l e o r g a n i c c o m p o u n d s(V O C s)a c c o m p a n i e db y u n p l e a s a n t s m e l l d u r i n g s u l f u rv u l c a n i z a t i o n p r o c e s s e s.F u r t h e r m o r e, t h e c o v a l e n t l y c r o s s-l i n k e de l a s t o m e r sa r e i n h e r e n t l y d i f f i c u l t t ob er e c y c l e da n dr e p r o c e s s e d,r e s u l t i n g i ns e r i o u s e n v i r o n m e n t a l p r o b l e m s a n d r e s o u r c ew a s t e a t t h e i r e n d o f l i f e.T oo v e r c o m e t h e a b o v e-m e n t i o n e d i n h e r e n t i s s u e s,i t i s o f g r e a t s i g n i f i c a n c e t o p u t f o r w a r d t h e c o n c e p t a n dd e s i g n s t r a t e g y o f g r e e n c r o s s-l i n k i n g s y s t e m.I n t h i s r e v i e w, t h e p r o b l e m s o f t r a d i t i o n a l v u l c a n i z a t i o nm e t h o d sw e r e i n t r o d u c e d f i r s t,a n d f o c u s e d o n t h e r e s e a r c h p r o g r e s s o n g r e e n c r o s s-l i n k i n g s t r a t e g i e so fr u b b e r.I t m a i n l y i n c l u d e dt h es t r a t e g y a b o u tt h ed e s i g no fc r o s s-l i n k e dd i e n e-t y p e d e l a s t o m e r s b a s e do nh y d r o l y z a b l ee s t e r c r o s s-l i n k s.T h e c r o s s-l i n k i n g s i t e s c o u l db eb a s e do nt h ee p o x yg r o u p so r c a r b o x y l g r o u p s r a t h e r t h a n t h e d o u b l e b o n d s,w h i l e b i o-b a s e d a n d g r e e nd i c a r b o x y l i c a c i do r e p o x i d i z e d s o y b e a no i l c o u l d s e r v e a s c r o s s-l i n k e r i n s t e a d o f s u l f u r,r e s u l t i n g i n c r o s s l i n k i n g n e t w o r k s c o n t a i n i n g e s t e r l i n k a g e s.F i n a l l y,t h e c h a l l e n g e s a n d f u t u r e p r o s p e c t s i n t h i s n e w l y e m e r g i n g f i e l dw e r e p r o s p e c t e d.K e y w o r d s:g r e e n c r o s s-l i n k i n g;b i o-b a s e d c r o s s-l i n k e r;r u b b e r r e c y c l i n g;r u b b e rm o d i f i c a t i o n672高分子材料科学与工程2021年。
橡胶的硫化硫磺作用
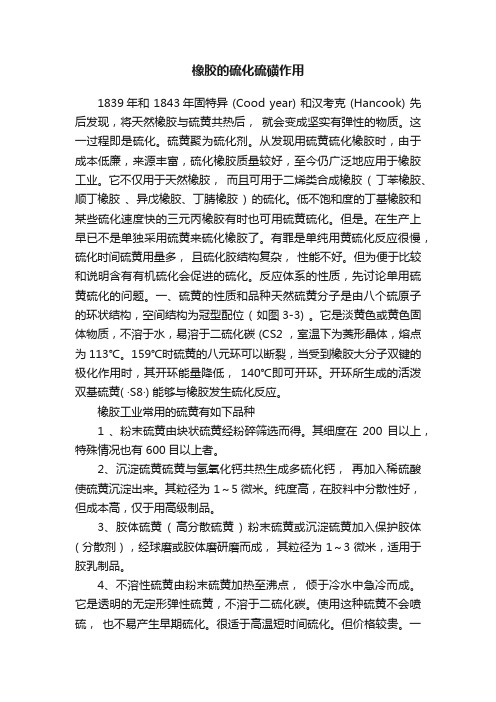
橡胶的硫化硫磺作用1839年和 1843年固特异 (Cood year) 和汉考克 (Hancook) 先后发现,将天然橡胶与硫黄共热后,就会变成坚实有弹性的物质。
这一过程即是硫化。
硫黄聚为硫化剂。
从发现用硫黄硫化橡胶时,由于成本低廉,来源丰富,硫化橡胶质量较好,至今仍广泛地应用于橡胶工业。
它不仅用于天然橡胶,而且可用于二烯类合成橡胶( 丁苯橡胶、顺丁橡胶、异戊橡胶、丁腈橡胶) 的硫化。
低不饱和度的丁基橡胶和某些硫化速度快的三元丙橡胶有时也可用硫黄硫化。
但是。
在生产上早已不是单独采用硫黄来硫化橡胶了。
有罪是单纯用黄硫化反应很慢,硫化时间硫黄用量多,且硫化胶结构复杂,性能不好。
但为便于比较和说明含有有机硫化会促进的硫化。
反应体系的性质,先讨论单用硫黄硫化的问题。
一、硫黄的性质和品种天然硫黄分子是由八个硫原子的环状结构,空间结构为冠型配位 ( 如图3-3) 。
它是淡黄色或黄色固体物质,不溶于水,易溶于二硫化碳 (CS2 ,室温下为菱形晶体,熔点为 113℃。
159℃时硫黄的八元环可以断裂,当受到橡胶大分子双键的极化作用时,其开环能量降低,140℃即可开环。
开环所生成的活泼双基硫黄( ·S8·) 能够与橡胶发生硫化反应。
橡胶工业常用的硫黄有如下品种1 、粉末硫黄由块状硫黄经粉碎筛选而得。
其细度在200 目以上,特殊情况也有 600目以上者。
2、沉淀硫黄硫黄与氢氧化钙共热生成多硫化钙,再加入稀硫酸使硫黄沉淀出来。
其粒径为 1~5 微米。
纯度高,在胶料中分散性好,但成本高,仅于用高级制品。
3、胶体硫黄( 高分散硫黄) 粉末硫黄或沉淀硫黄加入保护胶体( 分散剂 ) ,经球磨或胶体磨研磨而成,其粒径为 1~3 微米,适用于胶乳制品。
4、不溶性硫黄由粉末硫黄加热至沸点,倾于冷水中急冷而成。
它是透明的无定形弹性硫黄,不溶于二硫化碳。
使用这种硫黄不会喷硫,也不易产生早期硫化。
很适于高温短时间硫化。
动态硫化三元乙丙橡胶聚丙烯热塑性弹性体的研究进展
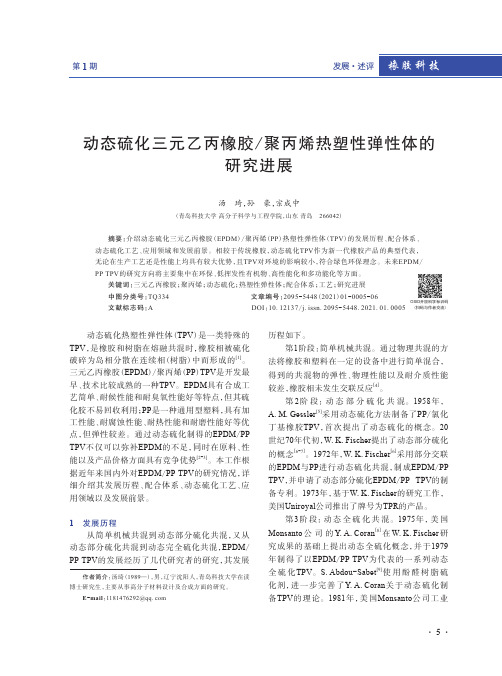
动态硫化三元乙丙橡胶/聚丙烯热塑性弹性体的研究进展汤 琦,孙 豪,宗成中(青岛科技大学高分子科学与工程学院,山东青岛 266042)摘要:介绍动态硫化三元乙丙橡胶(EPDM)/聚丙烯(PP)热塑性弹性体(TPV)的发展历程、配合体系、动态硫化工艺、应用领域和发展前景。
相较于传统橡胶,动态硫化TPV作为新一代橡胶产品的典型代表,无论在生产工艺还是性能上均具有较大优势,且TPV对环境的影响较小,符合绿色环保理念。
未来EPDM/ PP TPV的研究方向将主要集中在环保、低挥发性有机物、高性能化和多功能化等方面。
关键词:三元乙丙橡胶;聚丙烯;动态硫化;热塑性弹性体;配合体系;工艺;研究进展中图分类号:TQ334 文章编号:2095-5448(2021)01-0005-06文献标志码:A DOI:10.12137/j.issn.2095-5448.2021.01.0005动态硫化热塑性弹性体(TPV)是一类特殊的TPV,是橡胶和树脂在熔融共混时,橡胶相被硫化破碎为岛相分散在连续相(树脂)中而形成的[1]。
三元乙丙橡胶(EPDM)/聚丙烯(PP)TPV是开发最早、技术比较成熟的一种TPV。
EPDM具有合成工艺简单、耐候性能和耐臭氧性能好等特点,但其硫化胶不易回收利用;PP是一种通用型塑料,具有加工性能、耐腐蚀性能、耐热性能和耐磨性能好等优点,但弹性较差。
通过动态硫化制得的EPDM/PP TPV不仅可以弥补EPDM的不足,同时在原料、性能以及产品价格方面具有竞争优势[2-3]。
本工作根据近年来国内外对EPDM/PP TPV的研究情况,详细介绍其发展历程、配合体系、动态硫化工艺、应用领域以及发展前景。
1 发展历程从简单机械共混到动态部分硫化共混,又从动态部分硫化共混到动态完全硫化共混,EPDM/ PP TPV的发展经历了几代研究者的研究,其发展历程如下。
第1阶段:简单机械共混。
通过物理共混的方法将橡胶和塑料在一定的设备中进行简单混合,得到的共混物的弹性、物理性能以及耐介质性能较差,橡胶相未发生交联反应[4]。
橡胶与金属的硫化粘结详解
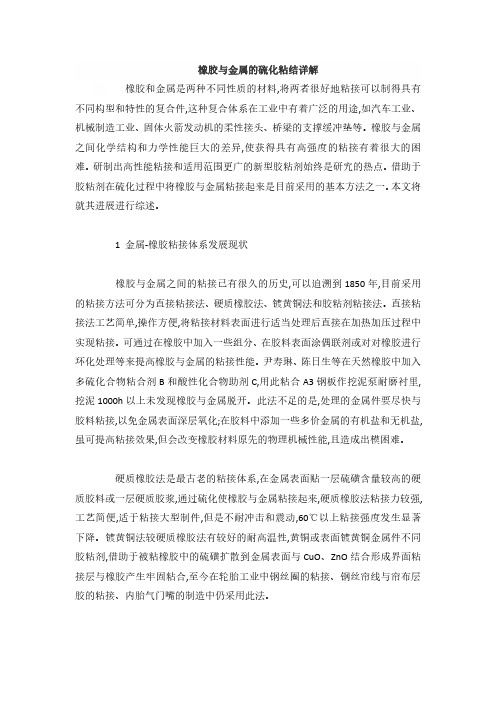
橡胶与金属的硫化粘结详解橡胶和金属是两种不同性质的材料,将两者很好地粘接可以制得具有不同构型和特性的复合件,这种复合体系在工业中有着广泛的用途,如汽车工业、机械制造工业、固体火箭发动机的柔性接头、桥梁的支撑缓冲垫等。
橡胶与金属之间化学结构和力学性能巨大的差异,使获得具有高强度的粘接有着很大的困难。
研制出高性能粘接和适用范围更广的新型胶粘剂始终是研究的热点。
借助于胶粘剂在硫化过程中将橡胶与金属粘接起来是目前采用的基本方法之一。
本文将就其进展进行综述。
1金属-橡胶粘接体系发展现状橡胶与金属之间的粘接已有很久的历史,可以追溯到1850年,目前采用的粘接方法可分为直接粘接法、硬质橡胶法、镀黄铜法和胶粘剂粘接法。
直接粘接法工艺简单,操作方便,将粘接材料表面进行适当处理后直接在加热加压过程中实现粘接。
可通过在橡胶中加入一些组分、在胶料表面涂偶联剂或对对橡胶进行环化处理等来提高橡胶与金属的粘接性能。
尹寿琳、陈日生等在天然橡胶中加入多硫化合物粘合剂B和酸性化合物助剂C,用此粘合A3钢板作挖泥泵耐磨衬里,挖泥1000h以上未发现橡胶与金属脱开。
此法不足的是,处理的金属件要尽快与胶料粘接,以免金属表面深层氧化;在胶料中添加一些多价金属的有机盐和无机盐,虽可提高粘接效果,但会改变橡胶材料原先的物理机械性能,且造成出模困难。
硬质橡胶法是最古老的粘接体系,在金属表面贴一层硫磺含量较高的硬质胶料或一层硬质胶浆,通过硫化使橡胶与金属粘接起来,硬质橡胶法粘接力较强,工艺简便,适于粘接大型制件,但是不耐冲击和震动,60℃以上粘接强度发生显著下降。
镀黄铜法较硬质橡胶法有较好的耐高温性,黄铜或表面镀黄铜金属件不同胶粘剂,借助于被粘橡胶中的硫磺扩散到金属表面与CuO、ZnO结合形成界面粘接层与橡胶产生牢固粘合,至今在轮胎工业中钢丝圈的粘接、钢丝帘线与帘布层胶的粘接、内胎气门嘴的制造中仍采用此法。
胶粘剂法是目前应用最广和最有效的方法,已经历了酚醛树脂、多异氰酸酯、卤化橡胶、特种硫化剂的卤化橡胶、硅橡胶和水基胶粘剂等不同的发展阶段。
橡胶硫化促进剂氧化技术研究进展

橡胶硫化促进剂氧化技术研究进展王飞濮阳蔚林化工股份有限公司摘要:介绍了绿色环保型橡胶硫化促进剂DM、NS和CBS的主要生产方法,包括采用亚硝酸钠、氯气、次氯酸钠为氧化剂的传统工艺和采用双氧水、氧气为氧化剂以及电解氧化法的新工艺。
完善和推广双氧水、氧气为氧化剂的技术路线,降低“三废”排放,实现节能减排,是我国橡胶助剂行业当下的重中之重。
关键词: 促进剂绿色氧化前言随着全球低碳经济的兴起,“绿色生产”成为我国橡胶工业可持续性发展的重要战略方针之一,加大产业结构调整,大力发展清洁生产工艺是“绿色生产”的根本。
橡胶助剂行业是橡胶工业十分重要的配套产业,其产品结构和市场形势与整个橡胶工业的发展休戚相关。
近年来,我国橡胶助剂行业坚持走绿色化工之路,并取得了一定成效。
一是产品绿色环保化。
不断调整产品结构,以绿色产品取代有毒有害产品。
2008年,防老剂D和促进剂NOBS已经被列入国家高污染和高环境风险产品目录,所占比例逐步下降,其生产基本得到控制。
二是生产工艺清洁化,其重大成果就是对苯二胺类防老剂中间体RT-培司(四氨基二苯胺)清洁工艺的突破,采用硝基苯和苯胺为原料,成功开发了催化氧化新工艺,产成品全部原材料利用率达98%,基本实现了“原子经济”的生产模式,实现了零排放。
硫化促进剂是是橡胶助剂产量最大的品种,占其总量的40%以上,而噻唑类和次磺酰胺类促进剂是促进剂中产量和用量最大的品种(表1为近年来我国噻唑类和次磺酰胺类促进剂产量),但在生产过程中仍然是传统工艺,采用亚硝酸钠、次氯酸钠、氯气作为氧化剂得到最终产品,产生大量废水,每吨产品产生6-8吨高含盐废水,难以直接生化处理,因此,开发双氧水氧化或氧气氧化清洁工艺对助剂行业绿色化工起着重要的带动作用。
2l世纪是绿色环保世纪,随着环保费用和压力越来越高,环境污染问题将成为制约我国橡胶助剂及中间体发展的“瓶颈”之一,今后在加强末端治理的同时,环境污染治理的根本出路在于开发与推广应用清洁工艺,将污染消灭在合成工艺中,如何改进工艺,推广普及“清洁工艺”将成为未来竞争的关键。
橡胶硫化促进剂的研究和开发进展
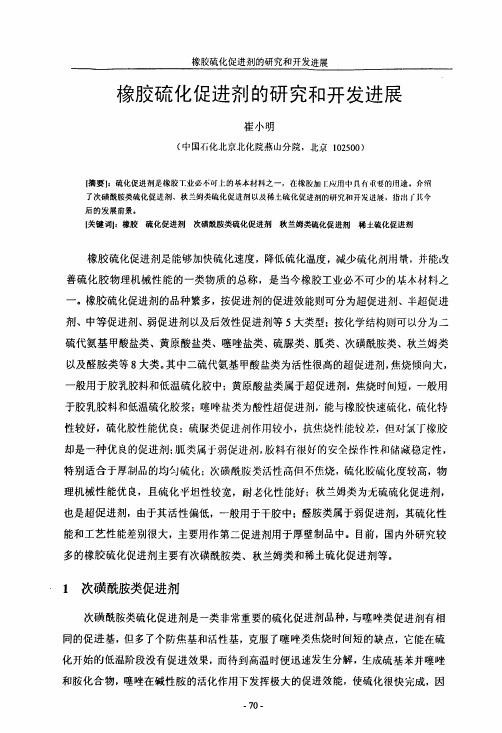
华南师范大学章伟光等【_7】发明了一种二硫代氨犀甲酸稀土硫化促进剂及其制备
方法。该方法首先以二苄胺、氢氧化钠和二硫化碳(CS2)为原料制备成配体,再将 配体与氯化稀土反应制备出二苄基二硫代氨基甲酸稀士配合物中间体,最后将中间体
与六次甲基磷酰胺反应制得所需要的产物。该发明产品原料来源广泛、性能好、反应 条件温和,无需惰性气体保护,成本低、使用安全,发展前景好。 广东轻工职业技术学院林新花等【8】将O,O,-二辛基二硫代磷酸镨(PrDODP)用 作NR硫磺硫化的促进剂。研究结果表明,PrDODP对天然橡胶有显著的促进作用,
进剂,但近年来发现它们在硫化时会产生亚硝酸铵,因此,人们积极丌发出性能更加
优异且不会产生致癌物质的新型秋兰姆类硫化促进剂。Crompton公司14l丌发成功烷基 化三亚乙基四胺二硫化秋兰姆(TATD),其结构类似于其它秋兰姆二硫化物,只是它
含有高分子量的长键烷基不同于其它二硫化秋兰姆。其分子量高于其它二硫化秋兰姆
适合于橡胶厚制品。TATD的另外一个大特点是它在三元乙丙橡胶中的溶解度约是乙丙橡
胶挤出制品和海绵制品。三元乙丙橡胶不饱和度很低,有极好的耐热和耐老化性能。
一些要求表面质量高的产品其表面不允许有喷霜现象。一些性能好的促进剂用于乙丙
一72.
状CBS能完全取代粉状产品,对橡胶的硫化性能没有不良影响。
2秋兰姆类硫化促进剂
秋兰姆类促进剂包括一硫化秋兰姆、二硫化秋兰姆和多硫化秋兰姆。其中二硫化 秋兰姆和多硫化秋兰姆在常规硫化温度下易释放出活性硫,使胶料不加硫磺即可进行 硫化即称为“无硫硫化”。用二硫化秋兰姆作硫化促进剂时多采用二硫化四甲基秋兰 姆(促进剂TMTD)、二硫化四乙基秋兰姆(促进剂TETD)以及二硫化甲基苯基秋 兰姆(MPhTD)等。 一硫化四甲基秋兰姆(TMTM)和TMTD都是性能较好的秋兰姆类橡胶硫化促
稀土橡胶硫化促进剂的研究和开发进展

物,采用液一 液合成法合成了二丁基二硫代氨基 甲酸镧,作为硫化促进剂应用于丁苯橡胶的基础
配方 中。研究结果表明,合成的二丁基二硫代氨
基甲酸斓配合物应用于丁苯橡胶,能明显延长其
焦烧时间,提高胶料的物理机械性能;添加二丁 基二硫代氨基甲酸斓配合物的硫化胶在拉伸 的过
程 中能阻止裂纹的发展 ,二丁基二硫代氨基 甲酸
《 广东橡胶 》2 1年 第 1 期 0 1 0
1 3
稀 土橡 胶硫化促进剂 的研究和开发进展
崔 小明
橡胶硫化促进剂是一类能够加快硫化速度, 降低硫化温度,减少硫化剂用量,并能改善硫化
胶物理机械性能的物质的总称,它是当今橡胶工
ห้องสมุดไป่ตู้
来,该领域研究最为活跃的是其与稀土配合物所
形成的二硫代氨基 甲酸类稀土硫化促进剂。
1 二硫 代氨 基 甲酸类 稀土 硫 化促进 剂
条件温和,无需惰性气体保护,成本低、使用安
,
发展前景好 。
广东轻工职业技术学院轻化工程系林新花等
将0 ,0 L二辛基二硫代磷酸镨 ( r O P P D D )用作
天然橡胶 ( R N )硫磺硫化的促进剂。研究结果表
明,P D D ) 天然橡胶有显著的促进作用,硫化 r O P{  ̄ 动力学研究表明,含P D D 的天然橡胶的硫化反 r OP 应活化能E 72 Jm l 为8 .k / 0 ;当P D P 的质量分数 rOD
华南师范大学 张启 交等研究 了在天然橡胶
使用特点,与传统促进剂N B 、c a- 苄基二硫 OS z r 代氨基甲酸金属配合物进行 了比较。结果表明,
二苄基二硫代氨基 甲酸钕稀土配合物除具有较好 的硫化促进性能和优 良的硫化胶综合物理机械性
- 1、下载文档前请自行甄别文档内容的完整性,平台不提供额外的编辑、内容补充、找答案等附加服务。
- 2、"仅部分预览"的文档,不可在线预览部分如存在完整性等问题,可反馈申请退款(可完整预览的文档不适用该条件!)。
- 3、如文档侵犯您的权益,请联系客服反馈,我们会尽快为您处理(人工客服工作时间:9:00-18:30)。
橡胶硫化剂的研究进展。
普通硫磺硫化的橡胶在停放时,易出现喷霜,且有焦烧倾向,极大影响最终产品的性能。
为弥补硫磺的不足,人们开始了硫磺的改性研究,成功的例子是聚合态硫磺或不溶硫(Insoluble Sulfur),简称IS,该硫磺为不溶於二硫化碳的线性高分子聚合硫,是硫的μ型体。
这种聚合态的硫磺平均分子量很大,经过不断验证,人们普遍认为其分子量为30000~40000。
不溶性硫磺在使用时通常分为充油型和未充油型两大类,而工业中使用的绝大多数(*99%)是充油型。
与普通硫磺相比,不溶性硫磺具有以下优点﹕(1)胶料在存放期内不会出现喷霜;(2)在胶料中无迁移现象(特别是在顺丁橡胶和丁基橡胶胶料中);(3)可减少混炼和存放过程中的焦烧现象;(4)有利於橡胶与其它材料的粘合;(5)可缩短硫化时间、减少硫磺用量。
不溶性硫磺可以通过硫磺的高温气相法或低温的熔融法制备,也可以通过硫化氢的氧化法制备。
低温熔融法是指普通硫磺在温度高於临界聚合温度(159℃)下按照反应机理(图2)开环聚合而成,反应结束後形成两端为自由基的链状分子,如果自由基不能被俘获,该活性中间体存在解聚的可能,这一过程为可逆聚合反应。
图2硫磺低温熔融聚合反应历程图与液相熔融不同,高温气相法是将硫磺加热至444.6℃以上,液硫沸腾气化,按自由能最小原理,气相硫的分子结构较小,主要是S8,S6,和S2。
温度越高,分子中的硫原子越少,当温度高於1000℃,硫主要以S2的方式存在。
低分子的硫反应活性很高,在快速降温的过程中很快聚合成份子量很大的聚合硫,其反应过程如下:通过上述方法制备的不溶性硫磺均属於亚稳态,稳定性较差,特别在较高硫化温度下很容易返还成普通硫磺,这将极大影响硫化胶的性能,也限制了它的应用。
因此提高不溶硫的稳定性是目前研究的重点。
国外做得最早也是最为成熟的是富莱克斯公司生产的Crystex样品,其高品位不溶硫的质量分数在90%以上,而且在高温条件下不溶硫的保持率也较高。
图3硫磺高温气相聚合反应历程图由於不溶性硫磺稳定性较差的原因可能是自由基的存在,所以人们设想用一种化学稳定剂耦合聚合硫双端自由基,减缓其返原作用。
目前可采用的化学稳定剂有卤素或卤化物及不饱和有机化合物。
王亚池等人在他们的专利中提到,由聚异戊二烯、二异丙烯基黄原酸二酯和芳烃油(质量比为10:45:45)组成的复合稳定剂可使生产的不溶性硫磺的质量分数达到96%~98%,其热稳定性经过高温(105℃,15min)仍较高,达到国际先进水平。
中科院大连化学物理研究所王复东等人采用由稳定剂A及稳定剂B组成的复合稳定剂(质量比为1:(20~180)),在50~80℃下对不溶性硫磺产品加热0.5~3h的稳定化处理,可得到不溶性硫磺质量分数为97%~98%;在110℃、15min条件下,不溶性硫磺的质量分数仍高达85%~89%。
硫磺给予体为了提高硫磺在硫化过程中的有效利用率,改善硫磺与其它助剂的配合,人们开始对硫磺有机化处理的研究,并合成出更加高效的含硫化合物,即硫磺给予体。
硫磺给予体又称硫载体,在硫化过程中可析出活性硫,使橡胶发生交联。
硫磺给予体的主要品种是秋兰姆、含硫吗啡衍生物、多硫聚合物、烷基苯酚硫化物及其它类型硫化物等,橡胶工业最常用的是秋兰姆和吗啡衍生物。
随着硫化工艺的发展,特别是半有效硫化体系SemiEV和有效硫化体系EV的出现,硫磺给予体作为硫磺类硫化剂的生力军,不断有新的产品出现,以满足实际生产的需要。
1、工业化的秋兰姆和吗啡衍生物常用的秋兰姆类硫化剂,由於它们的化学结构和所含的硫磺量不同,所以硫化胶的综合性能也不相同。
以TMTD(二硫化四甲基秋兰姆)为例,由於具有焦烧倾向小、硫化平坦性好等特点,所以应用越来越广。
但无硫配合时,硫化速度慢,硫化胶的综合性能较差,因此,可采取低硫配合或并用少量促进剂M、DM等来增加硫化体系的活性,改善硫化胶性能。
与秋兰姆相比,吗啡的TDM和MDB防焦烧性较好,且具有良好的操作安全性,但单独使用硫化速度较慢,因此一般是DTDM/TMTD并用,或用次磺酰胺或噻唑促进剂来调整焦烧期和硫化速度。
随着人们环保观念的增强及对健康的关注,人们发现硫化剂DTDM和秋兰姆产品在硫化温度下会裂解释放出仲胺基分子残片,而这些残片可与亚硝基供给体结合产生致癌性亚硝胺物质,因此硫化剂DTDM和秋兰姆产品的生产和应用受到欧美国家及环境法规的限定与警告。
目前新型硫化剂DTDC(N,N-二(ε-己内酰胺)二硫化物)因在硫化过程中不产生亚硝胺而备受国际关注,被认为是硫化剂DTDM和二硫化或六硫化秋兰姆的最佳替代品,用其等量替代硫化剂DTDM,无需改变胶料的配方和工艺。
2、含硫聚合物这里的含硫聚合物也就是一般意义的多硫化合物(polysulfide),其分子量往往较小,但富含的硫原子在半导体、涂料及橡胶硫化等领域有着广泛的应用前景。
含硫聚合物种类较多,合成方法也不尽相同,主要有缩聚、加聚及催化加成等。
Ganesh K.等人通过1,2-二溴乙苯与Na2S2/Na2S4水溶液缩合聚合已成功合成聚苯乙烯四硫化物(PST)和聚苯乙烯二硫化物(PSD),用红外、核磁、紫外及质谱等进行了详细的表徵,并将其作为链转移剂,实现乙烯基聚合或作为新合成单体完成与其它单体的共聚,图4即为缩聚反应历程图。
图4PST/PSD合成反应历程图加成聚合,即利用传统的自由基聚合方式实现单体与硫磺的共聚,实验操作更为简便。
早在上世纪80年代就有苯乙烯与硫磺共聚的报道,并从动力学角度分析得出单体共聚倾向性要优於自聚。
加成-聚合硫PAS-80催化加成,可通过选择不同的催化剂来实现结构可控。
据Mieko A报道,钌金属化合物能催化完成二硫化物的交换反应,并通过改变不同的金属和配体来控制硫原子在化合物的位置(含硫化合物和硫磺之间),如图5所示。
除了线性多硫化合物,环状多硫化合物和其他类型的多硫化合物也有许多相关报道。
图5钌催化硫原子间的交换反应目前,国内也有许多关於含硫聚合物的报道,如上海京海化工有限公司开发了一种加成-聚合硫PAS-80。
从结构特徵中可看出,硫化剂PAS-80可以看作是硫磺给予体和不溶性硫磺的结合。
与不溶性硫磺相比,硫化剂PAS-80中含硫部分为短链结构,稳定性相对较好。
其次,独特的烃类化学键合封端结构,又体现了硫磺给予体的特徵,因此在实际中PAS-80既结合不溶性硫磺不易喷霜、防焦烧的特性,又体现硫磺给予体耐热的动态性能,适用於许多橡胶制品的生产。
值得一提的是,这种新型硫化剂的独特结构,还将赋予该类硫化剂更加独特的性能,硫链部分在有机基团的携带作用下能更好地分散在基体中,而含有的烃类部分可与橡胶基体产生相互作用,硫磺与有机链的连接使得硫磺不易迁出表面,减少喷霜;高温硫化後,烃类部分的端基对橡胶可产生进一步交联,从而更加有效地发挥硫化作用。
这种双重硫化作用将对橡胶硫化後的性能产生巨大影响,因此该类硫化剂有望成为硫化剂未来研究的热点,成为下一代高效、功能化硫化剂的典范。
3、其它类型的硫磺给予体Si-69(双(3-三乙氧基甲矽烷基丙基)四硫化物)作为补强型硫化剂主要用於平衡硫化体系,往往与硫磺促进剂并用。
由於它与白炭黑表面的活性基团可产生化学结合,因此提高了非极性橡胶基体与填料间的界面作用,有助於改善硫化胶的机械性能。
图6Si-69(双(3-三乙氧基甲硅烷基丙基)四硫化物)橡胶硫化剂双-1,6-(二乙基硫代氨甲酰-二硫化)己烷(分子结构如图7所示)是一种新型硫化剂。
其独特的化学结构在满足快速高效硫化的同时,还能改善部分胶料的抗硫化返原性,并提高形成交联键多硫化物的耐屈挠性(常规半有效和有效硫化体系不具备)。
实验结果表明,这种新型硫化剂硫化後的橡胶在保证物理机械性能良好的同时,确实体现出优异的抗硫化返原性和动态疲劳性能。
图7双-1,6-(二乙基硫代氨甲酰-二梳化)己烷非硫磺体系随着橡胶品种的不断增加,对橡胶的功能性要求不断提高,作为橡胶硫化剂中的硫磺系列已经不能一统天下,因此其它非硫硫化剂及新型硫化体系得到迅速发展,如过氧化物、金属氧化物等。
过氧化物对於不饱和键含量较低或饱和体系的硫化而言,过氧化物是一类重要的硫化剂。
过氧化物类硫化剂主要包括烷基过氧化物、二酰基过氧化物和过氧酯三种,其中二烷基过氧化物应用较为广泛。
如DCP(过氧化二异丙苯)和DBP(二叔丁基过氧化物)在含炭黑补强的胶料中使用,可得到优良的硫化胶。
过氧化物除了用来交联二烯类橡胶,NR、SBR等外,其主要用来硫化各种饱和橡胶,PE、EPM以及硫化杂链橡胶,如甲基矽橡胶。
实际应用中,为了提高交联效率,往往加入助交联剂,如三元乙丙橡胶中,硫磺是最有效的助交联剂,它不但能增加EPM和EPDM的交联密度,而且在0.2~0.4范围内,可明显改善硫化胶的性能。
近年来,人们研究发现利用过氧化物(叔丁基过氧化物)预硫化天然胶乳(PPVL),不需使用硫化促进剂就能得到性能较好的橡胶,这样就可避免硫磺硫化体系中因使用促进剂所引起的亚硝胺问题,而且硫化在较低的温度下进行,工艺简单。
该工艺可替代传统硫磺硫化胶乳体系,应用於医用制品。
金属氧化物对於一些特种橡胶(主要指氯丁橡胶、卤化丁基橡胶及羧基丁橡胶等)来说,金属氧化物也可以作为硫化剂。
常用的金属氧化物主要指氧化锌、氧化镁、氧化钙及氧化铅等,其中以氧化锌和氧化镁应用较多。
作为硫化剂,两者均可单独硫化氯丁橡胶,但并用效果最佳,两者可充分发挥各自硫化时的优势,使得生成的硫化胶既有较好的防焦性能和贮存安全性,又能保证较快的硫化速度和平坦硫化性。
在使用金属氧化物作硫化剂时,为了改善硫化胶的性能,往往不单独使用金属氧化物,而是与其它硫化剂并用。
如在羧基丁橡胶的硫化过程中,硫磺/金属氧化物硫化体系制得的XNBR 硫化胶不仅综合物理机械性能较好,而且耐磨性、耐老化性及压缩永久变形性均优於其它硫化体系。
树脂化合物及醌类衍生物在橡胶加工过程中,树脂化合物间的交联反应也是制备功能性橡胶的重要方法。
Leicht研究发现,若在胶料中加入适量的酚醛树脂,则可改善胶料的加工性能,又保持胶料的硬度和刚度。
这类硫化体系硫化时实际上是形成了互穿网络的高分子合金,硫化胶有优越的耐热性能,压缩变形小。
硫化体系中的树脂化合物主要指酚醛类,而橡胶一般为天然橡胶、丁苯橡胶、丁基橡胶和丁橡胶,尤其适用於丁基橡胶。
这类硫化剂硫化速度一般较慢,因此硫化要求在高温下进行,通常硫化温度为160~190℃,有时硫化温度可高达300℃。
在粉末NBR/高聚合度PVC热塑弹性体及丙烯-丁二烯共聚物/丁橡胶/高苯乙烯树脂(AS/NBS/HSB)三元共混体系中,加入一定量酚醛树脂进行动态硫化,结果表明,共混体系的力学性能如拉伸强度和扯断伸长率得到很好的平衡。