锯片铣刀切削振动分析与研究
金属切削过程中的刀具振动与切削质量关系探讨

金属切削过程中的刀具振动与切削质量关系探讨刀具振动是金属切削过程中一个重要的问题,它直接影响着切削质量和生产效率。
因此,对刀具振动与切削质量之间的关系进行深入探讨对于提高金属切削加工的质量和效率具有重要意义。
刀具振动是指切削过程中刀具主动或被动地产生的摆动或往复振动。
刀具振动的主要原因包括:切削力、刀具强度、刀具几何状况、切削参数、切削条件、切削材料等多个因素的综合作用。
振动会使切削过程中的刀具失去初始正常的状态,造成切削力的不稳定和切屑的形态不规则,进而影响切削质量和刀具寿命。
首先,刀具振动与切削质量之间存在着明显的关系。
刀具振动会导致加工表面粗糙度的增加、尺寸精度的降低以及表面质量的恶化。
振动引起的表面粗糙度增加是由于振动会使刀具在切削过程中产生较大的摩擦,进而增加工件表面的摩擦热,导致较大的表面粗糙度。
另外,振动还会使得切削过程中产生的切屑形状不规则,进一步影响加工表面的质量。
同时,振动还会导致刀具与工件之间的相对位置不稳定,从而影响工件的尺寸精度。
其次,振动还会对刀具寿命产生负面影响。
刀具振动会引起刀具的磨损加剧和断裂的风险增加,从而降低刀具的寿命。
振动会使切削过程中切削力的分布不均匀,导致刀具的局部负荷增加,进而加速刀具的磨损。
此外,振动还会导致刀具受到冲击载荷,使得刀具的断裂风险增加,严重影响刀具的使用寿命。
接下来,我将介绍一些可以减小刀具振动的方法,从而提高切削质量和刀具寿命。
首先,合理选择刀具材料和刀具几何形状。
刀具材料应具有良好的刚性和抗振性能,能够抵抗切削过程中产生的振动力。
同时,刀具的几何形状应该设计合理,以减小切削过程中的振动。
其次,合理选择切削参数和切削条件。
切削参数的选择应以减小振动为目标,例如选择合适的进给量和切削速度。
此外,切削条件的选择也非常重要,如确保刀具和工件之间的准确安装和刀具夹紧力的合理。
最后,加强刀具的检修和维护,及时更换磨损的刀具,确保刀具的正常运转。
金属切削过程中的振动对加工质量的影响分析

金属切削过程中的振动对加工质量的影响分析引言:随着工业的发展,金属切削成为了制造过程中常用的方法之一。
然而,金属切削过程中的振动问题一直以来都是一个困扰制造业的难题。
振动不仅会对加工质量造成负面影响,还会导致工具磨损、机械失效、甚至对操作者的健康造成威胁。
因此,深入分析金属切削过程中振动对加工质量的影响,对于提高制造业的效率和质量至关重要。
1. 振动引起的切削质量问题金属切削过程中的振动主要表现为切削面粗糙度增加、切削刃磨损加剧、切削力增大、切削面失真等问题。
振动会使切削刀具发生剧烈振动,导致对工件的切削不稳定,进而影响加工表面的精度。
振动还可能导致刀具切削边缘的磨损加剧,从而缩短刀具的使用寿命。
此外,振动还会在切削过程中产生附加切削力,增加了工件上的切削力,使加工效率降低。
最后,振动还会使金属切削过程中的加工表面发生形变,导致工件的尺寸失准和表面质量下降。
2. 振动的产生机理振动产生的机理包括不平衡力、共振效应、弹性变形和切削参数选择不合理等。
不平衡力是最主要的振动产生机理之一。
不平衡的刀具或工件会在高速旋转时产生力的不平衡,导致振动。
共振效应指的是系统在特定频率下振幅增大的现象,当切削频率接近刚性结构的固有频率时,共振效应会引发严重的振动问题。
弹性变形是由于工件和刀具之间的接触力引起的,当接触面不均匀时会产生振动。
切削参数选择不合理也是引发振动的原因之一,过大或过小的进给量和转速都会导致振动的发生。
3. 减振方法和技术为了降低金属切削过程中的振动对加工质量的影响,需要采取一系列的振动减振方法和技术。
其中包括:a) 刀具结构设计优化:通过设计合适的刀具结构,减少切削过程中产生的不平衡力,降低振动的发生。
b) 切削参数优化:合理选择进给量和转速,避免因切削参数选择不当而引发振动。
c) 刀具磨损监测与更换:定期检查和更换磨损严重的刀具,减少切削过程中的振动。
d) 切削稳定性改善:采用稳定的切削方式,如切削过程中使用软刦等方法,降低振动的发生。
铣削振动的分析和解决方案 PPT

如果镗刀的刀尖产生160公斤的切削力,直径32毫米的
14
镗刀杆悬伸320毫米时产生的刀杆前端弹变为1.6毫米
提高刀杆的静态刚性(StaticToughness)
这样的刀片在镗削或铣削中的切削
pos. 楔入角最小,切削当然轻快。在车 削与镗削中,7度和11度后角是最
常见的刀片,刀片为螺钉夹持的最
neg..
多;在20mm以下的孔镗削中,即便
不存在振动问题,也通常选择11度
后角的刀片,例如山特维克可乐满
的TPMT,DPMT,VCEX的刀片(V型刀
片后角为7度或11度)。后角以7或
11
2、如何应对系统刚性差—— 薄壁工件的铣削用90度主偏角的刀具。
薄壁工件铣削发生振动的原因完全来自于工件,这种工件 一般是箱式或者碗式零件。
改善工件夹持。如:增加合适的辅助支撑点,在夹具和机 床工作台面之间加装一层木板,用粗大的橡皮条或者弹簧 勒在壳体的外面,在箱体内部充满湿沙子等等,奇思妙想 不一而足。
铣削
通用的 HRC40 以上的合金钢刀杆,刀杆从主轴端部向外悬深 与刀杆直径比大于 3 到 4; 模块化刀杆的模块接口磨损影响定位或者接口类型不适合铣削 加工; 刀杆的模块化接口之间拉紧力不够。
3
切削振动的三个分类
似起皱的丝绸
小直径细长刀杆或者薄壁工件 进行高转速切削
被定义为细长轴的零件外圆车削,通常由尾部顶尖支撑但是没 有跟刀架
内孔车、镗削
通用的 HRC40 以上的合金钢刀杆,刀杆夹持悬深与刀杆直径 比大于 4; 同时刀杆夹紧采用螺拴侧压,定位采用 V 型铁或孔柱间隙配 合; 刀尖偏离孔中心线 0.1mm 以上。
2
机夹刀片车镗刀与铣刀的切削振动条件
金属切削中的振动现象对刀具磨损的影响

金属切削中的振动现象对刀具磨损的影响切削加工是一种常见的金属加工方法,其通过通过刀具对工件进行削除材料的过程。
然而,在金属切削中,振动现象常常会对刀具产生负面影响,导致刀具的磨损加剧。
本文将讨论振动现象对刀具磨损的影响,并探讨可能的解决方案。
首先,振动现象在金属切削过程中可能引起刀具的不均匀磨损。
振动会导致刀具与工件之间的相对运动受到干扰,使得刀具无法均匀地接触工件表面。
当刀具在振动状态下工作时,刀具的切削力和切削温度会发生变化。
这种不均匀的切削力分布将导致刀具表面的磨损不均匀,使刀具的寿命大大缩短。
其次,振动还可能引起刀具的疲劳破裂。
由于振动会导致刀具产生应力集中,这些应力集中区域容易形成裂纹。
随着切削过程的持续,裂纹将逐渐扩展并最终导致刀具的疲劳破裂。
疲劳破裂会导致刀具的可用寿命大大降低,并且对于高强度材料的切削加工来说尤其严重。
另外,振动还会对切削表面质量产生负面影响。
振动导致切削力的不稳定变化,这将导致切削表面产生不规则的纹理和凹凸不平的表面。
对于需要高精度加工的工件来说,这种表面质量的损坏是无法容忍的。
那么,如何减轻振动现象对刀具磨损的影响呢?首先,优化切削条件是减轻振动现象的关键。
合适的切削速度、进给量和切削深度能够减少切削力的变化,从而降低振动的程度。
此外,选择合适的刀具材料和几何形状也能够减轻振动现象对刀具磨损的影响。
采用具有抗振动能力的刀具材料,如硬质合金,以及刀具几何形状设计上的优化,可以显著降低刀具的磨损。
其次,刀具的装夹和刀具路径的设计也是减轻振动现象的重要因素。
正确的刀具装夹能够减少刀具的振动,并提高切削稳定性。
同时,针对工件和刀具的几何形状特点,设计合理的切削路径也能够减轻振动现象的产生。
采用合理的路径能够平衡切削力,降低振动的风险。
最后,使用先进的切削工具和技术也是减轻振动现象的有效手段。
近年来,先进的切削工具如超硬刀具和复合刀具的发展为减轻振动带来了新的解决方案。
锯切时夹盘圆锯片横向振动特性研究

锯切时夹盘圆锯片横向振动特性研究随着夹盘圆锯片在生产实践中得到广泛地应用以及原材料成本的提高,锯片本身的厚度和横向振动所带来的锯路损失引起了更多的关注,锯路损失降低了出材率,加大了生产的成本。
在锯片结构一定的情况下,如何降低锯切时的横向振动成为研究的热点。
为了更好的实现横向振动的控制,就需要深入了解锯片横向振动的机理。
这方面的研究屡见不鲜,但研究的内容大多集中在空载、谐波激励和径向、切向力作用下的横向振动特性,对于锯切工作时侧刃横向力作用下的横向振动机理的研究较少。
本文研究的主要目的就是探寻锯切时在侧刃横向力作用下的圆锯片横向振动机理。
推导发现,侧刃横向激励作用与振动的位移变量有关,形成横向振动方程中的带周期性参数的位移参数激励项。
考虑到实际工作时,会受到外部干扰激励的影响,横向振动的方程中加入了与转频和空气激励有关的外激励项。
因此,问题转化为对空载和锯切状态下横向受迫振动方程的分析探讨。
利用状态矢量法对横向振动方程进行变换,基于Matlab对状态方程进行数值计算,分别获得空载和锯切状态下不同情况的横向受迫振动响应的时域和频域图谱,结合图谱中的具体数值和分布特点,归纳总结了相应的变化规律。
最后,对与前面对应的情况进行验证分析,主要包括两部分的内容,一是通过试验模态分析,验证运动方程的可靠性,结果表明,理论计算和试验测试得到的固有模态频率基本一致,说明运动方程是正确合理的;二是利用带有非接触式电涡流位移传感器的测试系统对空载和切削过程中的横向振动响应进行实时的监测,与前面的数值分析结论进行对照,分析表明,实测与理论及数值计算结果基本一致。
研究结论如下: 1.数值计算说明,锯切时夹盘圆锯片的横向振动表现出非线性。
2.实验测试说明,锯切时的非线性较弱,属于弱非线性特征。
3.锯切时的横向振动响应幅值比空载时要小,并随着转速的增加,非线性的倍频响应的倍数逐渐减小。
4.横向振动与切削材料有关,实验中柳桉、中密度纤维板和杨木的幅值逐渐变小,频率分布也基本一致。
切削过程中刀具振动对切削质量的影响研究

切削过程中刀具振动对切削质量的影响研究切削是现代制造工艺中常见的金属加工方法,对刀具振动的研究一直是学术界和工程界关注的焦点。
刀具振动对切削质量有直接的影响,它会导致加工表面粗糙度增加、尺寸偏差加大、切削力增加、刀具寿命缩短等问题。
因此,研究刀具振动对切削质量的影响具有重要的工程意义。
首先,刀具振动会导致加工表面粗糙度增加。
刀具振动会使得切削力在时间轴上发生波动,从而导致加工表面出现波纹状纹路,表面粗糙度增加。
实验研究表明,刀具振动频率与加工表面粗糙度呈正相关关系,即振动频率越高,表面粗糙度越大。
因此,在切削加工中,降低刀具振动是提高加工表面质量的重要措施之一。
其次,刀具振动会导致加工尺寸偏差加大。
由于刀具振动的存在,刀具与工件之间无法保持稳定的切削过程,会使得切削量不均匀,进而导致加工尺寸偏差增加。
切削尺寸偏差的大小与振动频率、振幅及刀具与工件之间的相对运动速度有关。
因此,减小刀具振动、提高切削稳定性是降低加工尺寸偏差的关键方法。
刀具振动还会导致切削力增加。
刀具振动会使切削力发生波动,并在振动周期内出现临界值。
当刀具振动频率接近工件固有振动频率时,切削力会达到最大值,从而导致切削能量损失增加。
这不仅会增加对切削机床的负载,还会使工件变形,降低切削效率。
因此,减小刀具振动能够有效地降低切削力,提高切削效率。
此外,刀具振动对刀具寿命也有重要影响。
刀具振动会导致刀具的应力变化剧烈,从而引起刀具表面的应力集中和疲劳破坏,进而缩短刀具的使用寿命。
实验研究表明,刀具振动会使刀具的磨损速度加快,刀具寿命减少。
因此,减小刀具振动对于提高刀具的使用寿命具有关键意义。
为了降低刀具振动对切削质量的影响,研究者们提出了多种方法和技术。
首先,优化刀具结构可以减小刀具振动。
改善刀具的材质、减小刀具的质量、提高刀具的刚性等方式可以有效降低刀具振动频率,提高切削稳定性。
其次,优化切削参数也是降低刀具振动的常用手段。
通过合理选择切削速度、切削深度、进给速度等参数,可以使切削过程更加稳定,降低刀具振动的发生。
机械加工过程中机械振动的原因及对策分析

机械加工过程中机械振动的原因及对策分析机械振动在机械加工过程中是一种常见的现象,它由多种原因引起。
机械振动不仅会影响加工精度和加工质量,还会对机床和工具设备造成损坏,因此需要采取相应的对策来减小机械振动。
机械振动的原因可以归结为以下几点:1. 切削力导致的机械振动:在机械加工过程中,切削力是产生振动的主要原因之一。
加工过程中的突然切削力、不平衡切削力以及刀具的不良使用等都会导致机械振动的产生。
2. 构件的材质和形状对机械振动的影响:构件的材质和形状也会对机械振动产生一定的影响。
如果构件的刚度不够,容易产生共振现象,进而引起机械振动。
3. 机床刚度不足:机床刚度不足也是机械振动的原因之一。
如果机床的刚度不够,加工过程中的力量无法得到有效的传递,会引起机械振动现象。
针对机械振动的原因,可以采取以下对策来减小机械振动:1. 优化刀具的设计和选择:合理选择刀具并进行刀具的定期检查和更换,以保证刀具的质量和使用寿命。
还可以根据具体的加工需求,优化刀具的设计,减小切削力的大小。
2. 提高机床的刚度:增加机床的刚度,可以有效地减小机床振动。
可以采取增加机床整体重量、加强机械结构的刚度,以及增加机床的支撑点等方法来提高机床的刚度。
3. 选用减振材料:在机床的结构中采用减振材料,如橡胶减振垫、弹簧减振装置等,可以有效地减小机械振动。
4. 控制切削参数:合理调整切削参数,如切削速度、进给量和切削深度等,可以降低切削力的大小,进而减小机械振动。
5. 加强工件固定:在加工过程中,合理固定工件,以减小工件的共振现象,从而减小机械振动。
机械振动是机械加工过程中常见的问题,但通过优化刀具的设计和选择、提高机床的刚度、选用减振材料、控制切削参数以及加强工件的固定等措施,可以有效地减小机械振动的发生,提高加工精度和加工质量。
锯片铣刀切削振动分析与研究
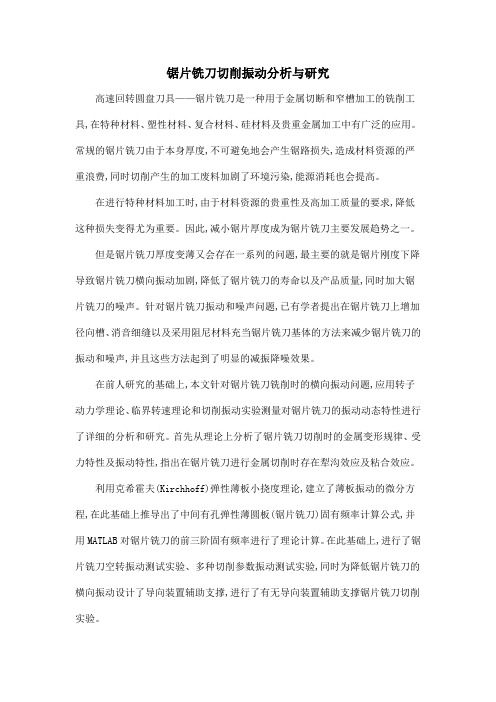
锯片铣刀切削振动分析与研究高速回转圆盘刀具——锯片铣刀是一种用于金属切断和窄槽加工的铣削工具,在特种材料、塑性材料、复合材料、硅材料及贵重金属加工中有广泛的应用。
常规的锯片铣刀由于本身厚度,不可避免地会产生锯路损失,造成材料资源的严重浪费,同时切削产生的加工废料加剧了环境污染,能源消耗也会提高。
在进行特种材料加工时,由于材料资源的贵重性及高加工质量的要求,降低这种损失变得尤为重要。
因此,减小锯片厚度成为锯片铣刀主要发展趋势之一。
但是锯片铣刀厚度变薄又会存在一系列的问题,最主要的就是锯片刚度下降导致锯片铣刀横向振动加剧,降低了锯片铣刀的寿命以及产品质量,同时加大锯片铣刀的噪声。
针对锯片铣刀振动和噪声问题,已有学者提出在锯片铣刀上增加径向槽、消音细缝以及采用阻尼材料充当锯片铣刀基体的方法来减少锯片铣刀的振动和噪声,并且这些方法起到了明显的减振降噪效果。
在前人研究的基础上,本文针对锯片铣刀铣削时的横向振动问题,应用转子动力学理论、临界转速理论和切削振动实验测量对锯片铣刀的振动动态特性进行了详细的分析和研究。
首先从理论上分析了锯片铣刀切削时的金属变形规律、受力特性及振动特性,指出在锯片铣刀进行金属切削时存在犁沟效应及粘合效应。
利用克希霍夫(Kirchhoff)弹性薄板小挠度理论,建立了薄板振动的微分方程,在此基础上推导出了中间有孔弹性薄圆板(锯片铣刀)固有频率计算公式,并用MATLAB对锯片铣刀的前三阶固有频率进行了理论计算。
在此基础上,进行了锯片铣刀空转振动测试实验、多种切削参数振动测试实验,同时为降低锯片铣刀的横向振动设计了导向装置辅助支撑,进行了有无导向装置辅助支撑锯片铣刀切削实验。
通过理论分析和实验结果分析,可得到以下结论:1.锯片铣刀为中心带孔的薄板圆盘,其固有振动形式有扭转振动、径向振动和横向振动。
在实践中,横向振动最为突出,并且是构成噪声的最重要的辐射源。
因此,控制圆盘或锯片铣刀的振动与噪声,关键是控制铣刀的横向振动。
- 1、下载文档前请自行甄别文档内容的完整性,平台不提供额外的编辑、内容补充、找答案等附加服务。
- 2、"仅部分预览"的文档,不可在线预览部分如存在完整性等问题,可反馈申请退款(可完整预览的文档不适用该条件!)。
- 3、如文档侵犯您的权益,请联系客服反馈,我们会尽快为您处理(人工客服工作时间:9:00-18:30)。
锯片铣刀切削振动分析与研究
高速回转圆盘刀具——锯片铣刀是一种用于金属切断和窄槽加工的铣削工具,在特种材料、塑性材料、复合材料、硅材料及贵重金属加工中有广泛的应用。
常规的锯片铣刀由于本身厚度,不可避免地会产生锯路损失,造成材料资源的严重浪费,同时切削产生的加工废料加剧了环境污染,能源消耗也会提高。
在进行特种材料加工时,由于材料资源的贵重性及高加工质量的要求,降低这种损失变得尤为重要。
因此,减小锯片厚度成为锯片铣刀主要发展趋势之一。
但是锯片铣刀厚度变薄又会存在一系列的问题,最主要的就是锯片刚度下降导致锯片铣刀横向振动加剧,降低了锯片铣刀的寿命以及产品质量,同时加大锯片铣刀的噪声。
针对锯片铣刀振动和噪声问题,已有学者提出在锯片铣刀上增加径向槽、消音细缝以及采用阻尼材料充当锯片铣刀基体的方法来减少锯片铣刀的振动和噪声,并且这些方法起到了明显的减振降噪效果。
在前人研究的基础上,本文针对锯片铣刀铣削时的横向振动问题,应用转子动力学理论、临界转速理论和切削振动实验测量对锯片铣刀的振动动态特性进行了详细的分析和研究。
首先从理论上分析了锯片铣刀切削时的金属变形规律、受力特性及振动特性,指出在锯片铣刀进行金属切削时存在犁沟效应及粘合效应。
利用克希霍夫(Kirchhoff)弹性薄板小挠度理论,建立了薄板振动的微分方程,在此基础上推导出了中间有孔弹性薄圆板(锯片铣刀)固有频率计算公式,并用MATLAB对锯片铣刀的前三阶固有频率进行了理论计算。
在此基础上,进行了锯片铣刀空转振动测试实验、多种切削参数振动测试实验,同时为降低锯片铣刀的横向振动设计了导向装置辅助支撑,进行了有无导向装置辅助支撑锯片铣刀切削实验。
通过理论分析和实验结果分析,可得到以下结论:1.锯片铣刀为中心带孔的薄板圆盘,其固有振动形式有扭转振动、径向振动和横向振动。
在实践中,横向振动最为突出,并且是构成噪声的最重要的辐射源。
因此,控制圆盘或锯片铣刀的振动与噪声,关键是控制铣刀的横向振动。
2.对锯片铣刀设计时应综合考虑锯片铣刀的几何结构参数对固有频率的影响。
锯片铣刀的固有频率随锯片厚度呈线性增加,但厚度增加会增大锯路损失。
可通过减少锯片铣刀的直径来提高锯片铣刀的固有频率,从固有频率计算公式可知,锯片铣刀直径减小10%,固有频率可提高21%。
3.刀杆的旋转不平衡及机床振动对锯片铣刀的横向振动有一定影响,但相对切削所引起的振动而言,影响较小。
4.铣削金属时,刀具的切削速度和切削厚度对锯片铣刀的振动有很大影响,进给速度对锯片铣刀的振动影响不明显。
因此,在锯片铣刀实际工作时,可选用较小的切削速度和切削厚度。
5.锯片铣刀的切削参数的改变并不改变锯片铣刀以其固有频率振动的事实,锯片铣刀以其固有频率振动是最主要的振动形式。
因此,使锯片铣刀的切削频率远离刀具系统的固有频率能够有效控制和减弱振动和噪声。
6.锯片铣刀切削金属的切削频率是产生振动的主要原因。
切削频率等于锯片铣刀固有频率或是固有频率的整数倍时,刀具系统会发生共振。
7.在锯片铣刀上加装导向装置辅助支撑对刀具系统的振动抑制明显。
为此,建议在木工锯机和石材锯机上加装该装置,能起到很好的控制振动的效果。