水玻璃精密铸造
硅酸乙酯-水玻璃复合型壳在精密铸造中的应用
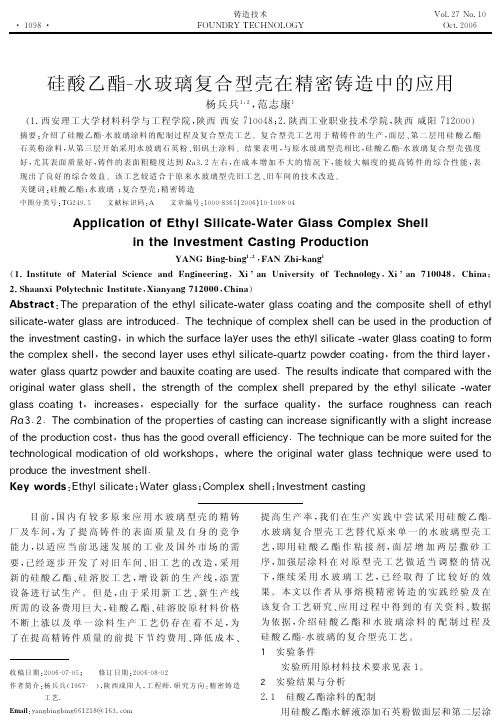
$ ! " # $ % & ’ $ ( + )? & ) / & / 0 1 " $" 2 0 + )) 0 + , 3 1 , 1 * / 0 ) < 4 / 0 ) &, / 3 3* " / 0 1 $ $ %0 + )* " . " 3 1 0 )3 + ) , ," 2) 0 + , ? ’ -/ ? ’ 3 1 , 1 * / 0 ) < 4 / 0 ) &, / 3 3/ & ) 1 $ 0 & " % # * ) % > ( + ) 0 ) * + $ 1 # )" 2 * " . , ) H3 + ) , , * / $F )# 3 ) % 1 $ 0 + )? & " % # * 0 1 " $" 2 V ? # 1 $4 + 1 * + 0 + )3 # & 2 / * ) , / ) & # 3 ) 3 0 + )) 0 + , 3 1 , 1 * / 0 ) < 4 / 0 ) & , / 3 3* " / 0 1 $ 0 " 2 " & . 0 + )1 $ E ) 3 0 . ) $ 0 * / 3 0 1 $ ’ ’ # # # 0 + )3 ) * " $ % , / ) & # 3 ) 3) 0 + , 3 1 , 1 * / 0 ) < # / & 0 A? " 4 % ) & * " / 0 1 $ 2 & " .0 + ) 0 + 1 & % , / ) & 0 + )* " . , ) H3 + ) , , ’ ’ V ’ ? 4 / 0 ) &, / 3 3V # / & 0 A? " 4 % ) & / $ %F / # H 1 0 )* " / 0 1 $ & )# 3 ) % > ( + ) & ) 3 # , 0 3 1 $ % 1 * / 0 ) 0 + / 0 * " . / & ) %4 1 0 + 0 + ) -/ ? # 0 + )3 0 & ) $ 0 +" 2 0 + )* " . , ) H3 + ) , ,? & ) / & ) %F + )) 0 + ,3 1 , 1 * / 0 )< 4 / 0 ) & " & 1 1 $ / ,4 / 0 ) &, / 3 33 + ) , , ? ? ’0 ’ # #) # , / 3 3* " / 0 1 $ 1 $ * & ) / 3 ) 3 3 ) * 1 / , , " &0 + )3 # & 2 / * )V # / , 1 0 0 + )3 # & 2 / * )& " # + $ ) 3 3* / $& ) / * + -0 ? ’2 ’ ! " 5> 7> ( + )* " . F 1 $ / 0 1 " $" 2 0 + )? & " ) & 0 1 ) 3" 2 * / 3 0 1 $ / $ 1 $ * & ) / 3 )3 1 $ 1 2 1 * / $ 0 , 1 0 +/3 , 1 + 0 1 $ * & ) / 3 ) ? -* ’4 # " 2 0 + )? & " % # * 0 1 " $* " 3 00 + # 3 + / 3 0 + )" " %" E ) & / , , ) 2 2 1 * 1 ) $ * > ( + ) 0 ) * + $ 1 # )* / $F ). " & )3 # 1 0 ) % 2 " & 0 + ) ’ V #4 + ) & )0 + )" & 1 1 $ / ,4 / 0 ) &, / 3 30 ) * + $ 1 # )4 ) & )# 3 ) %0 " 0 ) * + $ " , " 1 * / ,. " % 1 * / 0 1 " $" 2" , %4 " & 8 3 + " 3 V ? & " % # * ) 0 + ) 1 $ E ) 3 0 . ) $ 0 3 + ) , , > ? $ % % % ( ) , % #\ 0 + , 3 1 , 1 * / 0 )T / 0 ) &, / 3 3 Q " . , ) H3 + ) , , D $ E ) 3 0 . ) $ 0 * / 3 0 1 $ *+ ’ ? 国内有较多原来应用水玻璃型壳的精铸 !! 目 前 # 厂及车间# 为了提高铸件的表面质量及自身的竞争 能力# 以适应 当 前 迅 速 发 展 的 工 业 及 国 外 市 场 的 需 要# 已经逐步 开 发 了 对 旧 车 间’ 旧 工 艺 的 改 造# 采用 新的硅酸乙 酯’ 硅 溶 胶 工 艺# 增 设 新 的 生 产 线# 添置 由于采用新工艺’ 新生产线 设备进行试生产(但是# 所需的设备费用巨大# 硅酸乙酯’ 硅溶胶原材料价格 不断上涨以 及 单 一 涂 料 生 产 工 艺 仍 存 在 着 不 足# 为 了在提高精铸件质量的前提下节约费用’ 降低成本’ 提高生产率# 我们在生产实践中尝试采用硅酸乙酯 $ 水玻璃复合型壳工艺替代原来单一的水玻璃型壳工 艺# 即用 硅 酸 乙 酯 作 粘 接 剂# 面层增加两层撒砂工 序# 加强层涂 料 在 对 原 型 壳 工 艺 做 适 当 调 整 的 情 况 下# 继续 采 用 水 玻 璃 工 艺# 已经取得了比较好的效 果(本文以作者从事熔模精密铸造的实践经验 及 在 该复合工艺研究’ 应用过程中得到的有关资料’ 数据 为依据# 介绍 硅 酸 乙 酯 和 水 玻 璃 涂 料 的 配 制 过 程 及 硅酸乙酯 水玻璃的复合型壳工艺( $ =! 实验条件 实验所用原材料技术要求见表 &( 7! 实验结果与分析 !) &! 硅酸乙酯涂料的配制 用硅酸乙酯水解液添加石英粉做面层和第二层涂
水玻璃铸造工艺
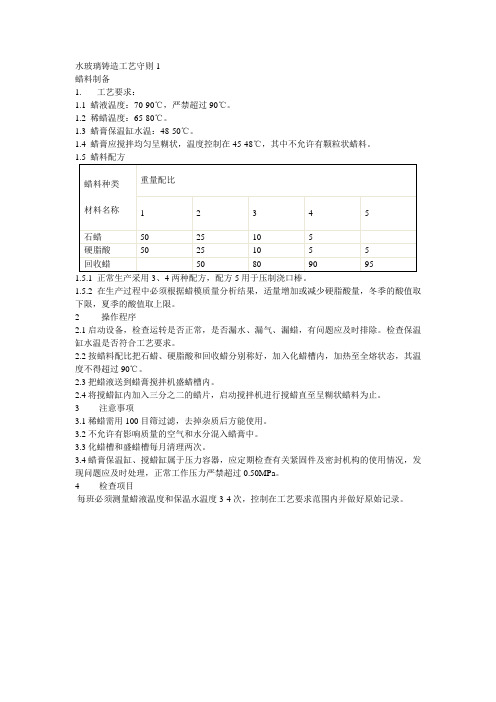
水玻璃铸造工艺守则1蜡料制备1. 工艺要求:1.1 蜡液温度:70-90℃,严禁超过90℃。
1.2 稀蜡温度:65-80℃。
1.3 蜡膏保温缸水温:48-50℃。
1.4 蜡膏应搅拌均匀呈糊状,温度控制在45-48℃,其中不允许有颗粒状蜡料。
1.5.1 正常生产采用3、4两种配方,配方5用于压制浇口棒。
1.5.2 在生产过程中必须根据蜡模质量分析结果,适量增加或减少硬脂酸量,冬季的酸值取下限,夏季的酸值取上限。
2 操作程序2.1 启动设备,检查运转是否正常,是否漏水、漏气、漏蜡,有问题应及时排除。
检查保温缸水温是否符合工艺要求。
2.2 按蜡料配比把石蜡、硬脂酸和回收蜡分别称好,加入化蜡槽内,加热至全熔状态,其温度不得超过90℃。
2.3 把蜡液送到蜡膏搅拌机盛蜡槽内。
2.4 将搅蜡缸内加入三分之二的蜡片,启动搅拌机进行搅蜡直至呈糊状蜡料为止。
3 注意事项3.1 稀蜡需用100目筛过滤,去掉杂质后方能使用。
3.2 不允许有影响质量的空气和水分混入蜡膏中。
3.3 化蜡槽和盛蜡槽每月清理两次。
3.4 蜡膏保温缸、搅蜡缸属于压力容器,应定期检查有关紧固件及密封机构的使用情况,发现问题应及时处理,正常工作压力严禁超过0.50MPa。
4 检查项目每班必须测量蜡液温度和保温水温度3-4次,控制在工艺要求范围内并做好原始记录。
蜡模制造1 工艺要求1.1 室温:16-28℃(最高不超过30℃)。
1.2 蜡膏压注温度:45~48℃,压力:0.3~0.5 MPa,保压时间:3~10秒。
1.3 压蜡冷却水温,14~24℃,冷却时间:20~100秒。
1.4蜡模冷却水温,14~24℃,冷却时间:10~60min。
1.5蜡模清洗液温度,20~28℃,清洗液中加入0.01% JFC。
1.6 脱模剂:ZF201.1.7蜡模表面光洁度,形状完整,轮廓清洗,尺寸合格,不允许有缩陷,凸包裂纹等缺陷。
2 操作程序2.1 手工制模2.1.1检查压型的分型面、型腔、脱模机构、定位销、紧固件应完整清洁。
精密铸造常识及详解

6.铸件后清理
将清理好的铸件按照客户的包装要求进行包装
入库即可
Copy Right By ZYC
11
What Shall We Talk…? 主要内容
Copy Right By ZYC
28
4
铸件尺寸影响因素分析
熔化收缩(焙烧和凝固)
1、模壳的焙烧温度和时间 2、浇注温度 3、浇注速度 4、补浇冒口操作 5、合金成分 6、浇后冷却方式 7、出壳到浇注结束的时间 8、合金的净化处理质量 9、环境温度
Copy Right By ZYC 29
5
铸件冶金质量影响因素分析
Copy Right By ZYC 17
3绍
3 三种蜡料系统和三种粘结剂系统介
三种蜡料系统
1、低温蜡料 以蜡基模料为主。熔点小于70度,主 要用于小件和尺寸及表面要求不高的零 件,膏状压制,能回用。与水玻璃粘结 剂多一起使用。用热水直接脱蜡。
Copy Right By ZYC
18
3绍
3 三种蜡料系统和三种粘结剂系统介
脱除。脱出的蜡料经回收处理后可重复使用。
Copy Right By ZYC
8
4.焙烧
为了进一步去除型壳中的水分、残蜡及其它杂
质,在金属浇注之前,必须将型壳送入加热炉内加热
到950℃左右进行焙烧2h左右。通过焙烧,型壳强度
增高,型腔更为干净。
Copy Right By ZYC
9
5.浇铸
为提高合金的充型能力,防止浇不足和冷隔缺
水玻璃法精密铸造工艺规程
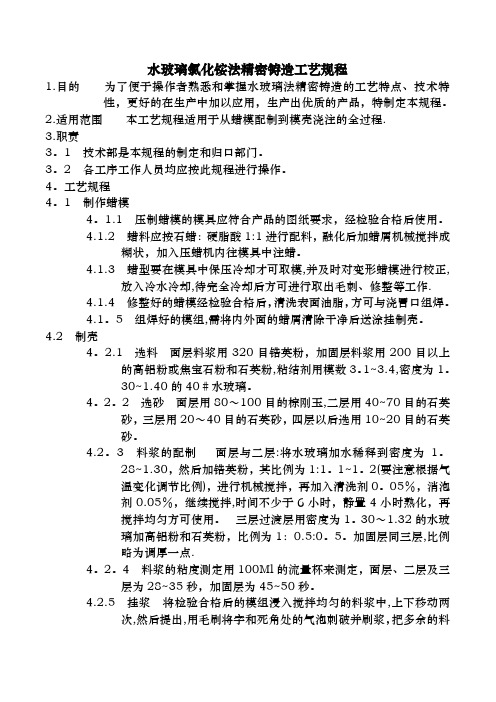
水玻璃氯化铵法精密铸造工艺规程1.目的为了便于操作者熟悉和掌握水玻璃法精密铸造的工艺特点、技术特性,更好的在生产中加以应用,生产出优质的产品,特制定本规程。
2.适用范围本工艺规程适用于从蜡模配制到模壳浇注的全过程.3.职责3。
1 技术部是本规程的制定和归口部门。
3。
2 各工序工作人员均应按此规程进行操作。
4。
工艺规程4。
1 制作蜡模4。
1.1 压制蜡模的模具应符合产品的图纸要求,经检验合格后使用。
4.1.2 蜡料应按石蜡:硬脂酸1:1进行配料,融化后加蜡屑机械搅拌成糊状,加入压蜡机内往模具中注蜡。
4.1.3 蜡型要在模具中保压冷却才可取模,并及时对变形蜡模进行校正,放入冷水冷却,待完全冷却后方可进行取出毛刺、修整等工作.4.1.4 修整好的蜡模经检验合格后,清洗表面油脂,方可与浇冒口组焊。
4.1。
5 组焊好的模组,需将内外面的蜡屑清除干净后送涂挂制壳。
4.2 制壳4。
2.1 选料面层料浆用320目锆英粉,加固层料浆用200目以上的高铝粉或焦宝石粉和石英粉,粘结剂用模数3。
1~3.4,密度为1。
30~1.40的40#水玻璃。
4。
2。
2 选砂面层用80~100目的棕刚玉,二层用40~70目的石英砂,三层用20~40目的石英砂,四层以后选用10~20目的石英砂。
4.2。
3 料浆的配制面层与二层:将水玻璃加水稀释到密度为1。
28~1.30,然后加锆英粉,其比例为1:1。
1~1。
2(要注意根据气温变化调节比例),进行机械搅拌,再加入清洗剂0。
05%,消泡剂0.05%,继续搅拌,时间不少于6小时,静置4小时熟化,再搅拌均匀方可使用。
三层过渡层用密度为1。
30~1.32的水玻璃加高铝粉和石英粉,比例为1:0.5:0。
5。
加固层同三层,比例略为调厚一点.4。
2。
4 料浆的粘度测定用100Ml的流量杯来测定,面层、二层及三层为28~35秒,加固层为45~50秒。
4.2.5 挂浆将检验合格后的模组浸入搅拌均匀的料浆中,上下移动两次,然后提出,用毛刷将字和死角处的气泡刺破并刷浆,把多余的料浆刷掉,整个模组要求挂浆均匀,无遗漏,五堆积,然后即可挂砂,整个挂浆过程时间不可过长,以免表面自然硬化,而无法挂砂。
水玻璃精密铸造工艺流程

水玻璃精密铸造工艺流程一、模具制作。
做水玻璃精密铸造呀,模具制作那可是第一步呢。
这模具就像是一个小房子的框架,要是框架歪了或者不好看,那后面的“装修”可就麻烦啦。
我们得根据要铸造的零件形状来设计模具。
一般是用一些特殊的材料,像木头或者金属,把它精心地加工成我们想要的形状。
这个过程可得仔细,一点点的小失误,可能就会让最后的铸件长得奇奇怪怪的呢。
比如说,如果是做一个小齿轮的模具,每个齿的形状、大小和间距都得拿捏得死死的,不然铸造出来的齿轮可能就没法好好工作啦。
二、水玻璃的配制。
模具做好了,就轮到水玻璃出场喽。
水玻璃就像是一种神奇的胶水,它能帮助我们把铸造材料粘在一起。
配制水玻璃也有讲究呢。
要按照一定的比例把水玻璃和其他的添加剂混合起来。
这个比例就像做饭时放调料一样,多了少了都不行。
如果水玻璃太稀,就像汤太淡了,可能就没法很好地固定铸造材料;要是太稠呢,就像面糊糊太干了,操作起来就很困难。
而且在配制的时候,还得慢慢地搅拌,就像搅拌蛋糕面糊一样,要让各种成分均匀地混合在一起。
三、蜡模制造。
有了调好的水玻璃,接下来就是做蜡模啦。
蜡模就像是一个临时的小演员,它的任务就是在铸造过程中占据一个位置,最后又华丽退场。
我们把融化的蜡注入到之前做好的模具里,等蜡冷却凝固了,再把它小心地取出来。
这个过程就像是从一个精致的小盒子里拿出一件宝贝一样。
蜡模的表面要光滑,不能有小坑洼或者气泡,不然就会影响后面铸件的质量。
就像一个人的皮肤要是不光滑,那看起来就不那么漂亮啦。
四、水玻璃涂料涂覆。
蜡模做好了,就要给它穿上一层水玻璃涂料的“衣服”啦。
这层“衣服”可是很重要的哦。
它可以让铸造材料更好地附着在蜡模上。
涂覆的时候呢,要轻轻地、均匀地把水玻璃涂料涂在蜡模的表面。
不能涂得太厚,不然会干得很慢,还可能会出现裂缝;也不能太薄,不然就起不到很好的保护和附着作用。
这就像是给小宝贝穿衣服,穿得太厚太热,穿得太薄又会着凉。
五、撒砂。
涂了水玻璃涂料之后,还要撒砂呢。
免硬化解决分层水玻璃精密铸造制壳面层、过渡层新工艺

划时代的水玻璃精密铸造制壳工艺面层、过渡层新型工艺和配方各位精密铸造行业的专家、企业家们,衷心的请您耐心认真的了解本文介绍的内容,相信您一定可以感受到即将到来的呼之欲出的精铸工艺革命!我国传统的水玻璃精密铸造工艺,面层、过渡层以水玻璃为粘结剂,辅以石英粉,适当添加消泡剂、渗透剂配浆以后,将蜡模模组进行蘸浆、洒砂、风干,然后用氯化铵、或者氯化铝、氯化铝氯化镁混合作为硬化剂,浸泡,待水玻璃和氯化铵反应以后,起到硬化的作用,硬化以后仍需等待模组干燥,然后再进入到下一层的操作。
多年来,我国一直用氯化铵作水玻璃型壳的硬化剂。
以后又逐步发展为用氯化铝:氯化镁作硬化剂。
无论用何种硬化剂,都免不了需要硬化,都有其不可克服的缺点。
氯化铵虽能在较短时间内硬化型壳,但焙烧后型壳强度差,作高强度型壳的硬化,显然不行,加之硬化时有氨气逸出,散发出刺鼻的气味,故工作环境条件差,导致招工难,留人难。
用氯化铝,还是氯化铝和氯化镁混合溶剂硬化,又有铸件表面质量差,清砂困难等缺点。
为客服上述传统工艺的各种缺陷,我公司技术人员经过多年的生产实践和摸索,经历了无数次的试验失败和不断尝试,研究出一种新型工艺和配方(该工艺和配方已经进入了国家实用型专利的申请流程),利用量身定做的配浆设备、配浆配方、脱蜡装置等重要工艺因素,让水玻璃精密铸造工艺取得飞跃的进步。
本文介绍的新工艺,主要是体现在型壳的面层、过渡层制作彻底告别硬化时代,使铸件的表面质量得到很大的提高,其光洁度甚至可以与硅溶胶精铸工艺生产出来的铸件媲美。
避免了传统的制壳工艺带来的表面分层、表面粘砂,橘子皮等缺陷。
同时,由于没有了氯化铵挥发出来的氨味,工作环境得到明显的改善,同时工艺参数要求、操作要求没有传统的硬化工艺那么复杂和严格,操作简单,一般工人均可上手,减少了由于熟练工流失,新工人上岗时的废品损失,稳定了工厂的正常生产效率。
成本方面,制壳材料成本比传统硬化工艺非但没有增加,而且明显减少了铸件后处理的焊补打磨抛丸处理,大大降低了生产成本,提高了良品率,缩短了生产周期,提升了利润空间的同时,大大提升了客户满意度。
熔模铸造水玻璃工艺

熔模铸造水玻璃工艺技术管理文件水玻璃铸造工艺守则文件编号:RMZZ/QG-JS-01版本:A修改状态:O受控状态:编制:日期:2004-3-1蜡料制备1.工艺要求:1.1蜡液温度:70-90℃,严禁超过90℃。
1.2稀蜡温度:65-80℃。
1.3蜡膏保温缸水温:48-50℃。
1.4蜡膏应搅拌均匀呈糊状,温度控制在45-48℃,其中不允许有颗粒状蜡料。
1.5蜡料配方蜡料种类材料名称重量配比 1 2 3 4 5 石蜡 50 25 10 5 ? 硬脂酸 50 25 10 5 5 回收蜡 ? 50 80 90 95 1.5.1正常生产采用3、4两种配方,配方5用于压制浇口棒。
1.5.2在生产过程中必须根据蜡模质量分析结果,适量增加或减少硬脂酸量,冬季的酸值取下限,夏季的酸值取上限。
2操作程序2.1?启动设备,检查运转是否正常,是否漏水、漏气、漏蜡,有问题应及时排除。
检查保温缸水温是否符合工艺要求。
2.2?按蜡料配比把石蜡、硬脂酸和回收蜡分别称好,加入化蜡槽内,加热至全熔状态,其温度不得超过90℃。
2.3?把蜡液送到蜡膏搅拌机盛蜡槽内。
2.4?将搅蜡缸内加入三分之二的蜡片,启动搅拌机进行搅蜡直至呈糊状蜡料为止。
3注意事项3.1?稀蜡需用100目筛过滤,去掉杂质后方能使用。
3.2?不允许有影响质量的空气和水分混入蜡膏中。
3.3?化蜡槽和盛蜡槽每月清理两次。
3.4?蜡膏保温缸、搅蜡缸属于压力容器,应定期检查有关紧固件及密封机构的使用情况,发现问题应及时处理,正常工作压力严禁超过0.50MPa。
4检查项目每班必须测量蜡液温度和保温水温度3-4次,控制在工艺要求范围内并做好原始记录。
蜡模制造1?工艺要求1.1室温:16-28℃(最高不超过30℃)。
1.2蜡膏压注温度:45~48℃,压力:0.3~0.5MPa,保压时间:3~10秒。
1.3压蜡冷却水温,14~24℃,冷却时间:20~100秒。
1.4蜡模冷却水温,14~24℃,冷却时间:10~60min。
水玻璃铸造工艺(3篇)

第1篇一、引言水玻璃铸造工艺是一种传统的铸造方法,它利用水玻璃作为铸造材料,具有熔点低、流动性好、易于脱模等优点。
随着我国铸造工业的不断发展,水玻璃铸造工艺在铸造领域得到了广泛应用。
本文将从水玻璃的制备、铸造工艺流程、质量控制等方面对水玻璃铸造工艺进行详细介绍。
二、水玻璃的制备1. 水玻璃的原料水玻璃的原料主要有硅砂、碱金属氧化物、碱土金属氧化物等。
其中,硅砂是水玻璃的主要成分,其质量直接影响水玻璃的性能。
2. 水玻璃的制备方法(1)熔融法:将硅砂、碱金属氧化物、碱土金属氧化物等原料按照一定比例混合,加热熔融后,加入适量水冷却、固化,得到水玻璃。
(2)水解法:将硅砂、碱金属氧化物、碱土金属氧化物等原料按照一定比例混合,加入适量水,搅拌、加热,使原料水解,得到水玻璃。
(3)沉淀法:将硅砂、碱金属氧化物、碱土金属氧化物等原料按照一定比例混合,加入适量水,搅拌、加热,使原料发生化学反应,生成沉淀,经过过滤、洗涤、干燥等工序,得到水玻璃。
三、水玻璃铸造工艺流程1. 原料准备将硅砂、碱金属氧化物、碱土金属氧化物等原料按照一定比例混合,经过筛选、烘干等工序,确保原料的质量。
2. 水玻璃制备按照一定的工艺参数,将原料进行熔融、水解或沉淀等制备过程,得到符合要求的水玻璃。
3. 模具准备根据铸件形状、尺寸、材料等要求,选择合适的模具。
模具应具有良好的脱模性能、耐磨性和耐腐蚀性。
4. 铸造将水玻璃倒入模具中,进行凝固、硬化。
根据铸件形状、尺寸、材料等要求,选择合适的铸造温度、时间、压力等参数。
5. 脱模在铸件凝固、硬化后,进行脱模操作。
脱模过程中应避免对铸件造成损伤。
6. 后处理对铸件进行打磨、抛光、热处理等后处理工序,提高铸件质量。
四、质量控制1. 原料质量:严格控制原料质量,确保水玻璃的性能稳定。
2. 水玻璃制备:按照一定的工艺参数,确保水玻璃的制备质量。
3. 模具质量:选择合适的模具,确保模具的脱模性能、耐磨性和耐腐蚀性。
- 1、下载文档前请自行甄别文档内容的完整性,平台不提供额外的编辑、内容补充、找答案等附加服务。
- 2、"仅部分预览"的文档,不可在线预览部分如存在完整性等问题,可反馈申请退款(可完整预览的文档不适用该条件!)。
- 3、如文档侵犯您的权益,请联系客服反馈,我们会尽快为您处理(人工客服工作时间:9:00-18:30)。
水玻璃精密铸造蜡料制备1.工艺要求:1.1 蜡液温度:70-90℃,严禁超过90℃。
1.2 稀蜡温度:65-80℃。
1.3 蜡膏保温缸水温:48-50℃。
1.4 蜡膏应搅拌均匀呈糊状,温度控制在45-48℃,其中不允许有颗粒状蜡料。
1.5 蜡料配方1.5.2 在生产过程中必须根据蜡模质量分析结果,适量增加或减少硬脂酸量,冬季的酸值取下限,夏季的酸值取上限。
2操作程序2.1 启动设备,检查运转是否正常,是否漏水、漏气、漏蜡,有问题应及时排除。
检查保温缸水温是否符合工艺要求。
2.2 按蜡料配比把石蜡、硬脂酸和回收蜡分别称好,加入化蜡槽内,加热至全熔状态,其温度不得超过90℃。
2.3 把蜡液送到蜡膏搅拌机盛蜡槽内。
2.4 将搅蜡缸内加入三分之二的蜡片,启动搅拌机进行搅蜡直至呈糊状蜡料为止。
3注意事项3.1 稀蜡需用100目筛过滤,去掉杂质后方能使用。
3.2 不允许有影响质量的空气和水分混入蜡膏中。
3.3 化蜡槽和盛蜡槽每月清理两次。
3.4 蜡膏保温缸、搅蜡缸属于压力容器,应定期检查有关紧固件及密封机构的使用情况,发现问题应及时处理,正常工作压力严禁超过0.50MPa。
4检查项目每班必须测量蜡液温度和保温水温度3-4次,控制在工艺要求范围内并做好原始记录。
蜡模制造1 工艺要求1.1 室温:16-28℃(最高不超过30℃)。
1.2 蜡膏压注温度:45~48℃,压力:0.3~0.5 MPa,保压时间:3~10秒。
1.3 压蜡冷却水温,14~24℃,冷却时间:20~100秒。
1.4蜡模冷却水温,14~24℃,冷却时间:10~60min。
1.5蜡模清洗液温度,20~28℃,清洗液中加入0.01% JFC。
1.6 脱模剂:ZF201.1.7蜡模表面光洁度,形状完整,轮廓清洗,尺寸合格,不允许有缩陷,凸包裂纹等缺陷。
2操作程序2.1 手工制模2.1.1检查压型的分型面、型腔、脱模机构、定位销、紧固件应完整清洁。
涂擦分型剂,装配并紧固压型。
2.1.2注蜡:把蜡抢嘴对准压型的注蜡孔,旋开阀门使蜡膏注入型腔并保压3~10s,关闭阀门,移走蜡枪。
2.1.3冷却:把注满蜡膏的压型濅入水内或放在工作台上冷却,冷却时间视蜡模形状与质量要求具体掌握,一般冷却20~100s。
2.1.4取模:拆开冷却过的压型,取出蜡模并及时放入水中继续冷却。
有特殊要求的蜡模应放在专用夹辅具上冷却。
2.1.5清型:用压缩空气吹除型腔、型芯上的水和蜡渣,视取模状况涂擦脱模剂。
2.1.6合型:装配清理干净的压型,按3.1.2~3.1.5的程序再次制模。
2.1.7交班:工作完毕应把压型清理干净,打扫工作环境后交班,若不在生产时,压型应及时交还压型库保管。
2.2 机械制模2.2.1检查压蜡机的润滑,电器、气动系统是否正常,调整限位,顶模机构,调节循环水系统和蜡膏输送系统。
根据不同产品的压型注蜡孔,调整固定压蜡抢嘴的位置。
2.2.2用压缩空气吹除压型型腔内的水和蜡渣,吹刷分形剂,启动压蜡机。
2.2.3压蜡机按自控程序完成:取出蜡模,按要求放置冷却。
2.2.4按3.2.2~3.2.4的程序连续制模。
2.2.5工作完毕应用压缩空气清除压蜡和压型上的水和蜡渣,水槽中的蜡渣和注蜡道必须清理干净,打扫工作环境后交班,并作好交接班记录。
2.3蜡模修整2.3.1用修模刀除去分型面上的披缝和其他不应有的凸起(包括注蜡残余),用稀蜡填补缺陷并修饰光滑。
2.3.2修整合格的蜡模在清洗槽中用清洗液进行清洗,清除分型剂,用压缩空气吹除蜡模表面上的蜡屑和水分。
2.3.3清洗干净的蜡模按品种整齐摆放在规定的器具中交检查员进行验收。
3 注意事项3.1压型应定期用煤油清洗,进行必要的保养。
3.2蜡模在运输、贮存中应轻拿轻放,不得整盘倾倒,防止变形和碰伤。
3.3蜡模贮存、时间不得超过15天,超时间的蜡模应重新检查。
4检查项目:自检蜡模质量应符合1.7的规定要求,自检合格后按规定填写交检单,并注明零件号(名称)、交检数量、制造日期。
蜡浇口棒制造1 工艺要求1.1温室:16~28℃(最高不超过30℃)1.2蜡高温度:48~50℃;压力0.20~0.40MPa。
1.3蜡膏保温水温度:50~54℃。
1.4蜡棒的表面应光滑平整,不得有孔洞、凹陷、裂纹、披缝。
2操作过程2.2将注蜡抢嘴对准棒压型中心,打开阀门使蜡膏注入棒压型内。
控制蜡膏注入量,待蜡膏到浇口杯与直浇道交接处时关闭阀门,然后将芯棒插入蜡膏中,以棒压型顶部为准,多余的蜡膏用铲子除去,不足的用蜡膏补平。
2.3蜡棒在制棒机中冷却5~15min后取出,放在水槽中继续冷却5~10min,然后按规格分类摆放在蜡棒小车内。
3注意事项3.1棒芯表面应清洁干净,不允许带砂及杂物。
3.2蜡棒浇口顶面应平整,不得有凸起和孔洞。
4检查项目4.1每班测量蜡膏保温水温度2~4次,严格控制在工艺要求范围内。
4.2蜡棒按规格分类验收,检查标准按2.4和2.5规定执行。
蜡模组装1工艺要求1.1室温:16~28℃(最高不得超过30℃)。
1.2模组最小压头:60mm,尾段最小余头:10mm。
1.3蜡模间最小间隙:6mm。
1.4蜡模的内浇口与蜡棒之间焊接要严密,不得有尖角与小缝。
1.5组装的蜡模应均匀,不得有蜡滴、蜡渣、灰尘杂物。
2操作程序2.1检查电烙铁(或电炉)是否漏电、完好,然后送电,备用。
2.2检查蜡棒、蜡模完整与清洁,不准组装不合格的蜡模。
2.3按有关工艺参数和要求进行组装。
2.4修整好的模组,质检合格后按品种分类挂在专用模组小车(架)上。
3注意事项3.1不合格的蜡棒与蜡模不允许组装。
3.2组装好的模组不允许放在地面上,应挂在蜡模小车(架)上,并停放在规定位置。
4检查项目4.1模组符合有关工艺参数之后,必须按2.2-2.5的规定进行100%的检查。
4.2组装好的模组不允许掉件,掉件的模组补上后方为合格。
涂料配置1工艺要求1.1工艺材料主要技术参数b.室内高于30℃,涂层粘度应降低:表面层应降低2~3s,加固层应降低1~2s。
c.手工制壳的涂料粘度应增加:表面层应提高5~10s,加固层应提高2~3s。
2操作程序2.1检查涂料搅拌机运转是否正常,按1.2的规定分别计算水玻璃、粉料、JFC 的加入量,并准确称量。
2.2按1.1.1的规定,水玻璃加水处理合格后一次性加入涂料搅拌机中,加JFC 搅匀,粉料应分2~3次加入,边加边搅拌至全部完成,再搅拌60~90min。
可间断搅拌每次搅拌时间不得小于30min。
2.3配好的涂料应静置4~8h,使用前应充分搅拌,达到2.3的规定后方能使用。
3注意事项3.1若在表面层与加固层之间增加过渡层,其涂料粘度应在表面层的基础降低5~10s。
3.2涂料配比作为一次性配料的工艺要求,最终按室温调整到工艺规定的粘度。
4检查项目4.1水玻璃、耐火粉料按进货批次进行检验,检验结果应符合2.1和有关材料标准要求。
4.2涂料粘度采用体积100ml,流出孔φ6±0.02mm的标准流杯,每班测定1~2次,测定结果应符合2.3的规定。
4.3期采用不锈钢涂片或玻璃片测定涂料的覆盖性(涂料厚度及均匀性),要求达到涂料无堆积、涂层均匀。
4.4水玻璃模数、涂料的粘度和覆盖性的测定方法,按JB4007——85《熔模铸造涂料试验方法》的规定进行。
制壳1范围本标准规定了制造型壳(以下简称制壳)的工艺要求、操作程序、注意事项和检查项目。
本标准适用于水玻璃、石英砂、铝矾土砂、高岭石系列砂等材料的型壳制造。
2工艺要求2.1室温:15~32度,湿度40%~60%.2.2工艺材料主要技术参数2.2.1水玻璃涂料应符合标准CICBA/B02.07。
2.2.2撤砂2.2.2.1石英砂2.2.3硬化剂42.2.3.3氯化镁硬化剂:MgCl 2含量(%)30~40;1.26~1.30g/cm 3。
氯化铵硬化,3~4层以后为结晶氯化铝硬化或氯化镁化。
氯化镁硬化的工艺参数同氯化铵硬化。
b如增加过渡层,其硬化、干燥工艺参数同表面层,撤砂粒度30#(0.600)。
c涂料层数按铸件单重选择。
一般铸件单重≤0.4kg的涂四层半,>0.40~1.00kg 的五层半,>1.00kg的涂六层半。
特殊铸件如:多孔复杂铸件,单重>2.5kg铸件定位手工制壳,其涂料层次参照一般铸件要求执行并增加涂料层次。
2.4手工制壳工艺参数2.4.1硬化温度与时间等效采用制壳工艺参数。
2.4.2自然风干时间:25~30min。
2.4.3室温低于5℃或阴雨天应适当延长硬化时间与风干时间,以保证型壳质量为准。
3制壳线操作程序3.1检查所有设备运转是否正常。
3.2现将涂料充分搅拌均匀,测量涂料展度、硬化剂参数,启动干燥时设备,测量风温,使所有的指标都控制在工艺要求的范围内。
3.3制壳线撤砂方式有两种,一种是沸腾式撤砂,另一种是雨淋式撤砂。
启动撤砂机,把撤砂效果调整到最佳状态。
3.4开动制壳线,将合格的模组挂在吊具上,按上涂料-撤砂-硬化-干燥程序即铸件规定的层次制壳。
3.5在涂料、撤砂工序中,要切实负责,对一、二层难涂之处,需用排刷点刷或用压缩空气吹,消除气泡。
必须勤加砂子,确保撤砂机有一定量的砂子,每涂一层筛去一次砂疙瘩。
3.6制壳完毕,浇口杯顶部用专用工具打平,浮砂、壳皮用压缩空气吹干净。
然后把模组从吊具上取下,按品种存放在专用的模组小车(筐、架)上。
4手工制壳操作程序4.1将当班生产的模组全部挂在硬化槽上方的吊架上,按3.1~3.3的有关程序作好制壳前的准备工作。
4.2从吊架上取出模组,按2.4的规定手工进行上涂料-撤砂-硬化-风干等操作程序及铸件规定的层次与3.6的有关规定完成制壳。
5注意事项5.1水玻璃型壳的撤砂,一般表面层、过渡层、加固层全部用石英砂,也可以从第三层开始用铝矾土砂或高岭石系列砂。
应因地制宜最低的成本保证最佳的型壳质量选择型壳用砂。
5.2在生产过程中,应保证涂料粘度、撤砂效果、硬化温度、干燥温度、干燥时间符合工艺要求,若检查不符合要求时,应立即停止生产,调整合格后再生产。
5.3工作中要经常检查硬化槽内是否有模组或零件掉入并及时捞出。
5.4模组掉件处应补上足够的层次,掉件大于三分之一者不再继续涂制。
5.5模组存放应按品种摆放整齐,不允许堆层加码。
5.6硬化槽、干燥室、涂料槽、撤砂机应定期清理,保证良好状态。
6检查项目6.1涂料粘度、硬化温度、干燥温度每班检测3~4次,做好原始记录。
6.2每周化验一次结晶氯化铝硬化液中Al2O3含量,B(碱化度)含量。
6.3每周化验三次氯化铵硬化液中NH4Cl含量。
6.4每周化验二次氯化镁硬化液中MgCl2含量。
6.5每周化验一次混合硬化液中AlCl3·6H2O含量,NH4Cl含量。
热水脱蜡1范围本标准规定了模组热水脱蜡的工艺要求、操作程序、注意事项和检查项目。