传动轴机械加工工艺过程卡
齿轮传动轴加工工艺及过程

设计任务:
• 了解齿轮传动轴的加工过程
零件的结构分析
• 1.合理的零件尺寸 • 为保证设计基准与工艺基准的重合并符合 尺寸链最短原则,使零件在被加工过程中 能直接保证尺寸精度要求,并保证装配时 累积误差最小,零件的尺寸标注不封闭, 避免从一个加工表面确定几个非加工表面 的位置。 • 2.合理的零件结构 • 轴的相邻表面间留 • 有退刀槽。
• 粗车 20° • 精车/半精 • 车 20° •
7°
11°
60°
60°
5°
5°
7°
5°
加工阶段的划分
• 此传动轴在结构上可大致分为四个部分整个轴段的表面 粗糙度为0.8两个尺度不同的键槽。在加工上大致分为粗 车半精车精车 铣削,以得到不同要求的加工面。 • 1.粗加工阶段 在这一阶段中要对整个圆棒料毛坯切除大量 的加工余量,使毛坯在形状和尺寸上尽快接近成品,得到 的已加工表面的表面粗糙度要达到12,为半精加工提供精 基准。 • 2.半精加工阶段 在这一阶段中应为主要表面的精加工做 好准备并完成一些 • 次要表面的加工在完成这一步时所加工表面的表面粗糙 度要求达到3.2。 • 3.精加工阶段 保证各主要表面达到或基本达到图样规定的 质量要求完成表面粗糙度0.8的加工。
一、选择毛坯
• 此传动轴采用综合力学性能优异且价格较 为便宜的45钢这种材料在经过 • 热处理后能得到一个较好的切屑性能、较 高强度及需要的韧度在加工中非常适合 各种加工的需要。 • 由于此传动轴为单件小批生产且精度不是 很高故此传动轴采用圆棒料毛坯圆棒 • 料毛坯成本较低加工方面也较方便。 • 得毛坯尺寸选取 长度250mm根据半精车及 粗车端面余量算得 • 240+2x2+2x2=248mm接近的是 • 250mm故此长度选择250mm。 • 查《实用机械制造工艺设计手册》表2-11
加工轴的工艺流程及路线分析

加工轴的工艺流程及路线分析1.零件图样分析;2.确定毛坯;3.确定主要表面的加工方法;4.确定定位基准;5.划分阶段;6.热处理工序安排;7.加工尺寸和切削用量;8.拟定工艺过程;9.传动轴机械加工工艺过程工序简图下料→车两端面,钻中心孔→粗车各外圆→调质→修研中心孔→半精车各外圆,车槽,倒角→车螺纹→划键槽加工线→铣键槽→修研中心孔→磨削→检验。
1.零件图样分析图所示零件是减速器中的传动轴。
它属于台阶轴类零件,由圆柱面、轴肩、螺纹、螺尾退刀槽、砂轮越程槽和键槽等组成。
轴肩一般用来确定安装在轴上零件的轴向位置,各环槽的作用是使零件装配时有一个正确的位置,并使加工中磨削外圆或车螺纹时退刀方便;键槽用于安装键,以传递转矩;螺纹用于安装各种锁紧螺母和调整螺母。
根据工作性能与条件,该传动轴图样规定了主要轴颈M,N,外圆P、Q以及轴肩G、H、I有较高的尺寸、位置精度和较小的表面粗糙度值,并有热处理要求。
这些技术要求必须在加工中给予保证。
因此,该传动轴的关键工序是轴颈M、N和外圆P、Q的加工。
2.确定毛坯该传动轴材料为45钢,因其属于一般传动轴,故选45钢可满足其要求。
本例传动轴属于中、小传动轴,并且各外圆直径尺寸相差不大,故选择¢60mm的热轧圆钢作毛坯。
3.确定主要表面的加工方法传动轴大都是回转表面,主要采用车削与外圆磨削成形。
由于该传动轴的主要表面M、N、P、Q的公差等级IT6较高,表面粗糙度Ra值Ra=0.8 um较小,故车削后还需磨削。
外圆表面的加工方案可为:粗车→半精车→磨削。
4.确定定位基准合理地选择定位基准,对于保证零件的尺寸和位置精度有着决定性的作用。
由于该传动轴的几个主要配合表面Q、P、N、M及轴肩面H、G对基准轴线A-B均有径向圆跳动和端面圆跳动的要求,它又是实心轴,所以应选择两端中心孔为基准,采用双顶尖装夹方法,以保证零件的技术要求。
粗基准采用热轧圆钢的毛坯外圆。
中心孔加工采用三爪自定心卡盘装夹热轧圆钢的毛坯外圆,车端面、钻中心孔。
传动轴机械加工工艺实例分享

检验
6
车
双顶尖装夹
1
车M24mm×l.5mm~6g至尺寸
车床
调头,双顶尖装夹
2
车M24mm×1.5mm~6g至尺寸
3
检验
7
钳
划两个键槽及一个止动垫圈槽加工线
8
铣
用V形虎钳装夹,按线找正
1
铣键槽12mm×36mm,保证尺寸41~41.25mm
立铣
2
铣键槽8mm×l6mm,保证尺寸26~26.25mm
3
铣止动垫圈槽6mm×l6mm,保证20.5mm至尺寸
4
检验
9
钳
修研两端中心孔
车床
10
磨
1
磨外圆¢35±0.008mm至尺寸
外圆磨床
2
磨轴肩面I
3
磨外圆¢30±0.0065mm至尺寸
4
磨轴肩面H
调头,双顶尖装夹
5
磨外圆P至尺寸
6
磨轴肩面G
7
磨外圆N至尺寸
8
磨轴肩面F
9
检验
传动轴加工工序简图:
传动轴机械加工工艺实例
零件图样分析
图A-1 传动轴
加工工艺技术方案如下:
下料→车两端面,钻中心孔→粗车各外圆→调质→修研中心孔→半精车各外圆,车槽,倒角→车螺纹→划键槽加工线→铣键槽→修研中心孔→磨削→检验。
传动轴机械加工工艺卡:
机械工程学院
机械加工工艺卡
产品名称
图 号
零件名称
传动轴
共1页
第1页
毛坯种类
12
检验
3
热
调质处理220~240HBS
4
钳
修研两端中心孔
工序卡片(参考)

详图见附图一机械加工工序卡片产品型号零件图号产品名称零件名称传动轴共22 页第 1 页车间工序号工序名称材料牌号1车削毛坯种类毛坯外形尺寸每毛坯可制件数每台件数铸件11设备名称设备型号设备编号同时加工件数数控车床CK6136S1夹具编号夹具名称切削液三爪卡盘工位器具编号工位器具名称工序工时(分) 准终单件工步号工步内容工艺装备主轴转速切削速度进给量切削深度进给次数工步工时r/min m/min mm/r mm 机动辅助1 车端面55°车刀800 163.280.020.5 1设计(日期)校对(日期)审核(日期)标准化(日期)会签(日期)详图见附图二机械加工工序卡片产品型号零件图号产品名称零件名称传动轴共22 页第 2 页车间工序号工序名称材料牌号2 车削毛坯种类毛坯外形尺寸每毛坯可制件数每台件数1 1设备名称设备型号设备编号同时加工件数数控车CK6136S 1夹具编号夹具名称切削液三爪卡盘工位器具编号工位器具名称工序工时(分)准终单件工步号工步内容工艺装备主轴转速切削速度进给量切削深度进给次数工步工时r/min m/min mm/r mm 机动辅助1 车Φ63 55°车刀800 162.5 0.152 12 车Φ62 55°车刀800 161.3 0.15 1 1设计(日期)校对(日期)审核(日期)标准化(日期)会签(日期)车间工序号工序名称材料牌号4 车销毛坯种类毛坯外形尺寸每毛坯可制件数每台件数1 1设备名称设备型号设备编号同时加工件数数控车CK6136S 1 夹具编号夹具名称切削液三爪卡盘工位器具编号工位器具名称工序工时(分) 准终单件工步号工步内容工艺装备主轴转速切削速度进给量切削深度进给次数工步工时r/min m/min mm/r mm 机动辅助1 精车Φ58.2 53°车刀1200 161.3 0.01 0.3 12 精车Φ58 53°车刀1200 161.3 0.01 0.2 13设计(日期)校对(日期)审核(日期)标准化(日期)会签(日期)车间工序号工序名称材料牌号3 车削毛坯种类毛坯外形尺寸每毛坯可制件数每台件数1 1设备名称设备型号设备编号同时加工件数数控车CK6136S 1 夹具编号夹具名称切削液三爪卡盘工位器具编号工位器具名称工序工时(分) 准终单件工步号工步内容工艺装备主轴转速切削速度进给量切削深度进给次数工步工时r/min m/min mm/r mm 机动辅助1 半精车Φ60 53°车刀1000 161.2 0.01 2 12 半精车Φ59 53°车刀1000 161.1 0.01 1 13 半精车Φ58.553°车刀1000 161.1 0.01 0.5 1设计(日期)校对(日期)审核(日期)标准化(日期)会签(日期)车间工序号工序名称材料牌号5 车削毛坯种类毛坯外形尺寸每毛坯可制件数每台件数设备名称设备型号设备编号同时加工件数数控车CK6136S 1 夹具编号夹具名称切削液三爪卡盘工位器具编号工位器具名称工序工时(分) 准终单件工步号工步内容工艺装备主轴转速切削速度进给量切削深度进给次数工步工时r/min m/min mm/r mm 机动辅助1 粗车Φ54 55°车刀800 161.1 0.012 22 粗车Φ53 55°车刀800 160.8 0.01 1 13设计(日期)校对(日期)审核(日期)标准化(日期)会签(日期)车间工序号工序名称材料牌号6 车削毛坯种类毛坯外形尺寸每毛坯可制件数每台件数1 1设备名称设备型号设备编号同时加工件数数控车CK6136S 1 夹具编号夹具名称切削液三爪卡盘工位器具编号工位器具名称工序工时(分) 准终单件工步号工步内容工艺装备主轴转速切削速度进给量切削深度进给次数工步工时r/min m/min mm/r mm 机动辅助1 半精车Φ49 53°车刀1000 160.5 0.012 22 半精车Φ48 53°车刀1000 160.1 0.01 1 1设计(日期)校对(日期)审核(日期)标准化(日期)会签(日期)车间工序号工序名称材料牌号7 车削毛坯种类毛坯外形尺寸每毛坯可制件数每台件数1 1设备名称设备型号设备编号同时加工件数数控车CK6136S 1 夹具编号夹具名称切削液三爪卡盘工位器具编号工位器具名称工序工时(分) 准终单件工步号工步内容工艺装备主轴转速切削速度进给量切削深度进给次数工步工时r/min m/min mm/r mm 机动辅助1 半精车Φ46 53°车刀1000 159 0.01 1 2半精车Φ45 53°车刀1000 159 0.01 0.5 2设计(日期)校对(日期)审核(日期)标准化(日期)会签(日期)车间工序号工序名称材料牌号8 车削毛坯种类毛坯外形尺寸每毛坯可制件数每台件数设备名称设备型号设备编号同时加工件数数控车CK6136S 1 夹具编号夹具名称切削液三爪卡盘工位器具编号工位器具名称工序工时(分) 准终单件工步号工步内容工艺装备主轴转速切削速度进给量切削深度进给次数工步工时r/min m/min mm/r mm 机动辅助粗车Φ43 55°车刀800 158 0.01 2 1粗车Φ41 55°车刀800 158 0.01 2 1粗车Φ40 55°车刀800 158 0.01 1 1设计(日期)校对(日期)审核(日期)标准化(日期)会签(日期)车间工序号工序名称材料牌号10 车削毛坯种类毛坯外形尺寸每毛坯可制件数每台件数设备名称设备型号设备编号同时加工件数数控车CK6136S 1 夹具编号夹具名称切削液三爪卡盘工位器具编号工位器具名称工序工时(分) 准终单件工步号工步内容工艺装备主轴转速切削速度进给量切削深度进给次数工步工时r/min m/min mm/r mm 机动辅助精车Φ36.6 53°车刀1000 158 0.01 0.6 1精车Φ36 53°车刀1000 158 0.01 0.3 2设计(日期)校对(日期)审核(日期)标准化(日期)会签(日期)车间工序号工序名称材料牌号9 车削毛坯种类毛坯外形尺寸每毛坯可制件数每台件数设备名称设备型号设备编号同时加工件数数控车CK6136S夹具编号夹具名称切削液三爪卡盘工位器具编号工位器具名称工序工时(分) 准终单件工步号工步内容工艺装备主轴转速切削速度进给量切削深度进给次数工步工时r/min m/min mm/r mm 机动辅助半精车Φ38.2 53°车刀1000 157 0.01 1.8 2半精车Φ37.2 53°车刀1000 155 0.01 1.0 2设计(日期)校对(日期)审核(日期)标准化(日期)会签(日期)车间工序号工序名称材料牌号车削毛坯种类毛坯外形尺寸每毛坯可制件数每台件数11设备名称设备型号设备编号数控车CK6136S夹具编号夹具名称切削液三爪卡盘工位器具编号工位器具名称工序工时(分) 准终单件工步号工步内容工艺装备主轴转速切削速度进给量切削深度进给次数工步工时r/min m/min mm/r mm 机动辅助粗车Φ34 55°车刀800 155 0.01 2 1粗车Φ32 55°车刀800 154 0.01 2 1设计(日期)校对(日期)审核(日期)标准化(日期)会签(日期)车间工序号工序名称材料牌号12 车削毛坯种类毛坯外形尺寸每毛坯可制件数每台件数设备名称设备型号设备编号同时加工件数数控车CK6136S夹具编号夹具名称切削液三爪卡盘工位器具编号工位器具名称工序工时(分) 准终单件工步号工步内容工艺装备主轴转速切削速度进给量切削深度进给次数工步工时r/min m/min mm/r mm 机动辅助半精车Φ31.5 53°车刀1000 154 0.01 0.5设计(日期)校对(日期)审核(日期)标准化(日期)会签(日期)车间工序号工序名称材料牌号车削毛坯种类毛坯外形尺寸每毛坯可制件数每台件数13设备名称设备型号设备编号同时加工件数数控车CK6136S夹具编号夹具名称切削液三爪卡盘工位器具编号工位器具名称工序工时(分) 准终单件工步号工步内容工艺装备主轴转速切削速度进给量切削深度进给次数工步工时r/min m/min mm/r mm 机动辅助半精车Φ30.5 53°车刀1000 152 0.01 1.0 4半精车Φ30 53°车刀1000 152 0.01 0.5 2设计(日期)校对(日期)审核(日期)标准化(日期)会签(日期)车间工序号工序名称材料牌号15 切槽毛坯种类毛坯外形尺寸每毛坯可制件数每台件数设备名称设备型号设备编号同时加工件数数控车CK6136S夹具编号夹具名称切削液三爪卡盘工位器具编号工位器具名称工序工时(分) 准终单件工步号工步内容工艺装备主轴转速切削速度进给量切削深度进给次数工步工时r/min m/min mm/r mm 机动辅助切Φ24的槽5X30切槽刀800 153 0.01 6 2设计(日期)校对(日期)审核(日期)标准化(日期)会签(日期)车间工序号工序名称材料牌号切槽毛坯种类毛坯外形尺寸每毛坯可制件数每台件数16设备名称设备型号设备编号同时加工件数数控车CK6136S夹具编号夹具名称切削液三爪卡盘工位器具编号工位器具名称工序工时(分) 准终单件工步号工步内容工艺装备主轴转速切削速度进给量切削深度进给次数工步工时r/min m/min mm/r mm 机动辅助切Φ53的槽5X30切槽刀800 141 0.01 5 1车间工序号工序名称材料牌号14 车削毛坯种类毛坯外形尺寸每毛坯可制件数每台件数设备名称设备型号设备编号同时加工件数数控车CK6136S夹具编号夹具名称切削液三爪卡盘工位器具编号工位器具名称工序工时(分) 准终单件工步号工步内容工艺装备主轴转速切削速度进给量切削深度进给次数工步工时r/min m/min mm/r mm 机动辅助加工圆弧53°车刀1000 140 0.01 1设计(日期)校对(日期)审核(日期)标准化(日期)会签(日期)标记处数更改文件号签字日期标记处数更改文件号签字日期标记处数更改文件号签字日期标记处数更改文件号签字日期机械加工工序卡片产品型号零件图号产品名称零件名称传动轴共22 页第17 页车间工序号工序名称材料牌号17 车螺纹毛坯种类毛坯外形尺寸每毛坯可制件数每台件数设备名称设备型号设备编号同时加工件数数控车CK6136S夹具编号夹具名称切削液三爪卡盘工位器具编号工位器具名称工序工时(分) 准终单件工步号工步内容工艺装备主轴转速切削速度进给量切削深度进给次数工步工时r/min m/min mm/r mm 机动辅助粗加工M30X1.5的螺纹60°螺纹车刀80 7.5 1 1机械加工工序卡片产品名称零件名称传动轴共22 页第18 页车间工序号工序名称材料牌号18 车螺纹毛坯种类毛坯外形尺寸每毛坯可制件数每台件数设备名称设备型号设备编号同时加工件数数控车CK6136S夹具编号夹具名称切削液三爪卡盘工位器具编号工位器具名称工序工时(分) 准终单件工步号工步内容工艺装备主轴转速切削速度进给量切削深度进给次数工步工时r/min m/min mm/r mm 机动辅助半精加工M30X1.5的螺纹60°螺纹车刀80 0.7 0.7 1机械加工工序卡片产品名称零件名称传动轴共22 页第19 页车间工序号工序名称材料牌号19 车螺纹毛坯种类毛坯外形尺寸每毛坯可制件数每台件数设备名称设备型号设备编号同时加工件数数控车CK6136S夹具编号夹具名称切削液三爪卡盘工位器具编号工位器具名称工序工时(分) 准终单件工步号工步内容工艺装备主轴转速切削速度进给量切削深度进给次数工步工时r/min m/min mm/r mm 机动辅助精加工M30X1.5的螺纹60°螺纹车刀80 7.5 0.9 3机械加工工序卡片产品型号零件图号产品名称零件名称传动轴共22 页第20 页车间工序号工序名称材料牌号20 车端面毛坯种类毛坯外形尺寸每毛坯可制件数每台件数设备名称设备型号设备编号同时加工件数夹具编号夹具名称切削液三爪卡盘工位器具编号工位器具名称工序工时(分) 准终单件工步号工步内容工艺装备主轴转速切削速度进给量切削深度进给次数工步工时r/min m/min mm/r mm 机动辅助粗车至125 55°车刀800 145 0.01 5 2设计(日期)校对(日期)审核(日期)标准化(日期)会签(日期)产品名称零件名称传动轴共22 页第21 页车间工序号工序名称材料牌号21 车端面毛坯种类毛坯外形尺寸每毛坯可制件数每台件数设备名称设备型号设备编号同时加工件数夹具编号夹具名称切削液三爪卡盘工位器具编号工位器具名称工序工时(分) 准终单件工步号工步内容工艺装备主轴转速切削速度进给量切削深度进给次数工步工时r/min m/min mm/r mm 机动辅助半精车至120.5 53°车刀800 145 0.01 4.5 3设计(日期)校对(日期)审核(日期)标准化(日期)会签(日期)产品名称零件名称传动轴共22 页第22 页车间工序号工序名称材料牌号22 车端面毛坯种类毛坯外形尺寸每毛坯可制件数每台件数设备名称设备型号设备编号同时加工件数夹具编号夹具名称切削液三爪卡盘工位器具编号工位器具名称工序工时(分) 准终单件工步号工步内容工艺装备主轴转速切削速度进给量切削深度进给次数工步工时r/min m/min mm/r mm 机动辅助精车至120 53°车刀1000 145 0.01 0.5 2设计(日期)校对(日期)审核(日期)标准化(日期)会签(日期)。
机械加工工艺过程及工序卡片模板

机械加工工艺过程及工序卡片模板一、工艺规划工艺规划是在设计任务和制造要求的基础上,确定产品的加工工艺和加工工序的流程,具体步骤如下:1.了解产品的使用功能、要求以及材料的特性,确定最佳的加工方法和加工工艺。
2.绘制产品的工艺流程图,包括加工工序、顺序和设备选择等。
3.制定加工工艺卡,记录每个加工工序的详细信息,包括工具刀具的选择、加工参数等。
二、技术准备技术准备包括原材料准备、机床设备准备和工装量具准备等,具体步骤如下:1.检查原材料的规格、质量和数量是否符合要求,如有问题及时采取补救措施。
2.检查机床设备的运行状态和性能,确保设备正常运行。
3.准备需要的工装量具,确保其准确性和可靠性。
三、加工操作加工操作是根据工艺规划和技术准备的要求,对原材料进行加工操作,具体步骤如下:1.根据工艺流程图和加工工艺卡,按照预定的顺序进行加工工序。
2.调整和选择合适的机床设备,安装和装夹好加工零件。
3.根据加工工艺卡的要求,合理设置机床的工作参数和工装量具的位置。
4.进行切削、剪切、钻孔、磨削等加工操作,确保加工质量和加工效率。
四、检验与维护在加工过程中,需要进行产品质量的检验和设备维护,具体步骤如下:1.进行零件的尺寸和表面质量的检验,确保零件的几何精度和表面质量符合要求。
2.检查机床设备的工作状态和性能,及时发现和解决问题,确保设备的正常运行。
3.根据机床设备的维护手册,定期对设备进行清洁、润滑和维护保养,延长设备的使用寿命。
以上是机械加工工艺过程的一般步骤和主要内容。
下面是一个工序卡片的模板,供参考:工序卡片工序名称:(填写工序名称)主要工艺参数:1.切削速度:(填写切削速度,单位)2.进给速度:(填写进给速度,单位)3.切削深度:(填写切削深度,单位)刀具/工具:1.刀具名称:(填写刀具名称)2.刀尖半径:(填写刀尖半径,单位)3.刀具材料:(填写刀具材料)4.工具冷却方式:(填写工具冷却方式)夹具/工装:1.夹具类型:(填写夹具类型)2.夹具安装位置:(填写夹具安装位置)3.工装定位方式:(填写工装定位方式)检验要求:1.尺寸精度:(填写尺寸精度要求)2.表面质量:(填写表面质量要求)3.其他检验要求:(填写其他检验要求)注意事项:1.在操作中注意安全,佩戴必要的防护设备。
齿轮传动轴加工工艺及过程
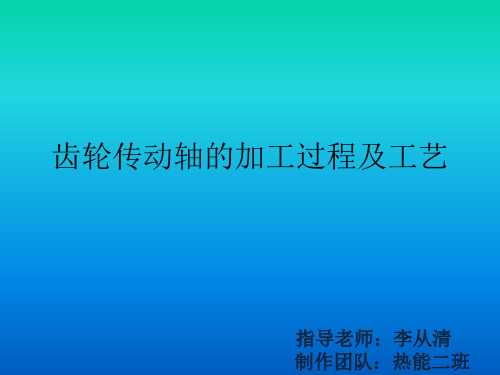
加工后的立体图形
参考文献:
• 机械制造技术基础(韩秋实 王红军主编 机械工业出版社)
• 实用机械制造工艺设计手册(王凡主编 机 械工业出版社)
• 机械制造工艺学(王宪逵)
•
•
•
前角 后角 主偏角 副偏角 刃倾角
• 粗车 20° 7° 60° 5° 7° • 精车/半精 • 车 20° 11° 60° 5° 5°
•
加工阶段的划分
• 粗糙度为0.8
• 1.粗加工阶段 在这一阶段中要对整个圆棒料毛坯切除大量 的加工余量,使毛坯在形状和尺寸上尽快接近成品,得到 的已加工表面的表面粗糙度要达到12,为半精加工提供精 基准。
钻中心孔 三爪夹持
粗车φ25外圆及φ30右端面 三爪夹持
粗车φ30外圆φ35右端面 三爪夹持
粗车左端面 三爪一顶
粗车φ30及φ35左端面
三爪一顶
半精车φ30及φ35左端面 三爪一顶
半精车φ25外圆及φ30右端面
半精车φ30外圆φ35右端面 三爪一顶
倒角、切槽 三爪夹持
铣键槽
精车φ30 三爪一顶
精车φ35 三爪一顶
车11车右端面三爪夹持?毛坯外圆?2钻中心孔三爪夹持?毛坯外圆?3粗车25外圆及30右端面三爪夹持?毛坯外圆?4粗车30外圆35右端面三爪夹持?毛坯外圆?2调头1粗车左端面三爪一顶?2粗车30及35左端面三爪一顶?3车11半精车30及35左端面三爪一顶?2调头1半精车25外圆及30右端面三爪一顶?2半精车30外圆35右端面三爪一顶?4车倒角切槽三爪夹持?5铣铣键槽?6车11精车30三爪一顶?2调头1精车35三爪一顶?2精车30三爪一顶?3精车25三爪一顶?7钳工去毛刺四铣?铣床可以加个平面沟槽螺旋型表面以及齿轮还可以加个回转体表面内孔等
1传动轴加工工艺过程
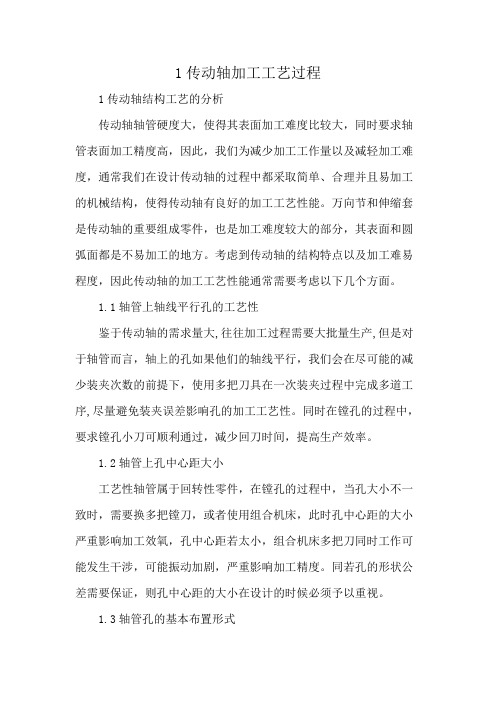
1传动轴加工工艺过程1传动轴结构工艺的分析传动轴轴管硬度大,使得其表面加工难度比较大,同时要求轴管表面加工精度高,因此,我们为减少加工工作量以及减轻加工难度,通常我们在设计传动轴的过程中都采取简单、合理并且易加工的机械结构,使得传动轴有良好的加工工艺性能。
万向节和伸缩套是传动轴的重要组成零件,也是加工难度较大的部分,其表面和圆弧面都是不易加工的地方。
考虑到传动轴的结构特点以及加工难易程度,因此传动轴的加工工艺性能通常需要考虑以下几个方面。
1.1轴管上轴线平行孔的工艺性鉴于传动轴的需求量大,往往加工过程需要大批量生产,但是对于轴管而言,轴上的孔如果他们的轴线平行,我们会在尽可能的减少装夹次数的前提下,使用多把刀具在一次装夹过程中完成多道工序,尽量避免装夹误差影响孔的加工工艺性。
同时在镗孔的过程中,要求镗孔小刀可顺利通过,减少回刀时间,提高生产效率。
1.2轴管上孔中心距大小工艺性轴管属于回转性零件,在镗孔的过程中,当孔大小不一致时,需要换多把镗刀,或者使用组合机床,此时孔中心距的大小严重影响加工效氧,孔中心距若太小,组合机床多把刀同时工作可能发生干涉,可能振动加剧,严重影响加工精度。
同若孔的形状公差需要保证,则孔中心距的大小在设计的时候必须予以重视。
1.3轴管孔的基本布置形式轴管孔多数为通孔,同时两端与万向节连接处偶有阶梯孔,因此不司的孔径比折射出不同的工艺性能。
当孔径比大于1但是小于1.5时,属于短圆柱孔,该类孔的工艺性能较好:当孔径比大于1.5时,属于深孔,深孔的加工难度大,因此工艺性较差。
阶梯孔的工艺性也受孔径比的影响,其中孔径比快接近通孔时,加工难度容易,工艺性能较好,但孔径比远离通孔孔径比时,加工难度较大,工艺性能差。
2传动轴零件加工工艺分析传动轴的零件包括轴管、伸缩套、万向节,加工工艺直接影响零件的装配精度、零件的使用寿命,因此对于加工工艺的分析显得尤为重要。
万向节在传动轴中的作用相当于大脑作用,没有万向节的连接作用加辅助支撑以及旋转的作用,传动轴将无法正常工作。
典型零件加工工艺流程
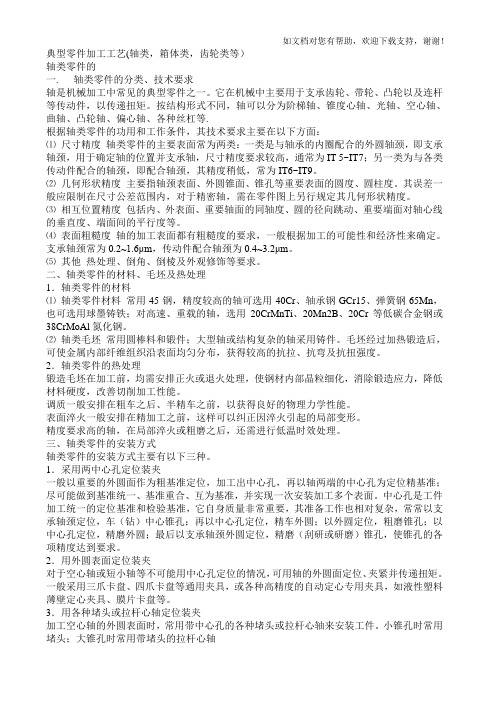
典型零件加工工艺(轴类,箱体类,齿轮类等)轴类零件的一. 轴类零件的分类、技术要求轴是机械加工中常见的典型零件之一。
它在机械中主要用于支承齿轮、带轮、凸轮以及连杆等传动件,以传递扭矩。
按结构形式不同,轴可以分为阶梯轴、锥度心轴、光轴、空心轴、曲轴、凸轮轴、偏心轴、各种丝杠等.根据轴类零件的功用和工作条件,其技术要求主要在以下方面:⑴尺寸精度轴类零件的主要表面常为两类:一类是与轴承的内圈配合的外圆轴颈,即支承轴颈,用于确定轴的位置并支承轴,尺寸精度要求较高,通常为IT 5~IT7;另一类为与各类传动件配合的轴颈,即配合轴颈,其精度稍低,常为IT6~IT9。
⑵几何形状精度主要指轴颈表面、外圆锥面、锥孔等重要表面的圆度、圆柱度。
其误差一般应限制在尺寸公差范围内,对于精密轴,需在零件图上另行规定其几何形状精度。
⑶相互位置精度包括内、外表面、重要轴面的同轴度、圆的径向跳动、重要端面对轴心线的垂直度、端面间的平行度等。
⑷表面粗糙度轴的加工表面都有粗糙度的要求,一般根据加工的可能性和经济性来确定。
支承轴颈常为0.2~1.6μm,传动件配合轴颈为0.4~3.2μm。
⑸其他热处理、倒角、倒棱及外观修饰等要求。
二、轴类零件的材料、毛坯及热处理1.轴类零件的材料⑴轴类零件材料常用45钢,精度较高的轴可选用40Cr、轴承钢GCr15、弹簧钢65Mn,也可选用球墨铸铁;对高速、重载的轴,选用20CrMnTi、20Mn2B、20Cr等低碳合金钢或38CrMoAl氮化钢。
⑵轴类毛坯常用圆棒料和锻件;大型轴或结构复杂的轴采用铸件。
毛坯经过加热锻造后,可使金属内部纤维组织沿表面均匀分布,获得较高的抗拉、抗弯及抗扭强度。
2.轴类零件的热处理锻造毛坯在加工前,均需安排正火或退火处理,使钢材内部晶粒细化,消除锻造应力,降低材料硬度,改善切削加工性能。
调质一般安排在粗车之后、半精车之前,以获得良好的物理力学性能。
表面淬火一般安排在精加工之前,这样可以纠正因淬火引起的局部变形。
- 1、下载文档前请自行甄别文档内容的完整性,平台不提供额外的编辑、内容补充、找答案等附加服务。
- 2、"仅部分预览"的文档,不可在线预览部分如存在完整性等问题,可反馈申请退款(可完整预览的文档不适用该条件!)。
- 3、如文档侵犯您的权益,请联系客服反馈,我们会尽快为您处理(人工客服工作时间:9:00-18:30)。
卧式车床
80
精车
调头精车Φ70外圆留磨
卧式车床
90
检验
100 画线
画两处键槽线
画线钳台
110 铣
铣削两处键槽并去毛刺
立式铣床
120 磨 130 检验
用两顶尖装夹,磨
、6000..002141 、54.400.05 到规定尺寸 万能外圆磨床
按图样检验各部分尺寸
工序号 工序名称 工序内容
机床设备
10
下料
棒料Φ90*385 mm
锯床
20
粗车
粗车一端面打中心孔,粗车各外圆,留余量
卧式车床
30
粗车
调头车另一端面打中心孔,粗车各 外圆,留余量
卧式车床
40
检验
50
热处理 调质并检验,28~32HRC
60
钳
修研中心孔
卧式车床
70
精车
精车Φ70、Φ88外圆到规定尺寸,其余各圆留磨