液压阀块工艺优化
控制阀在液压系统中的优化设计

控制阀在液压系统中的优化设计液压系统是一种基于液压传动的工程技术,广泛应用于各个领域。
而其中的关键组件之一就是控制阀。
控制阀在液压系统中负责调节和控制液压传动的压力、流量和方向。
因此,优化设计控制阀对于提高液压系统的工作效率和性能至关重要。
首先,对于液压系统的优化设计,需要从控制阀的选择入手。
不同的液压系统在工作压力、流量和工况环境等方面都会有所差异,这就要求我们根据具体情况选择合适的控制阀。
可以通过考虑控制阀的流量特性、压力损失、质量和可靠性等方面来进行综合评估和选择。
此外,还可以通过模拟和仿真等手段来验证所选控制阀的适用性。
其次,控制阀的布置和连接方式也是优化设计的关键。
液压系统中控制阀的布置应符合工程设计的要求,以保证液压系统的紧凑性和通用性。
同时,在控制阀的连接方式上,应选用合理的接口和连接件,以确保控制阀与其他部件的密封性和可靠性。
此外,还需要注意控制阀的安装和维护位置,以便于后续的调试和维修工作。
在控制阀的设计和制造过程中,需要注重提高其性能和可靠性。
一方面,控制阀的流量特性和稳定性是评价其性能的重要指标。
设计中应注意控制阀的流道形状和尺寸,以提高流量的控制精度和稳定性。
此外,还可以采用先进的加工工艺和材料,以提高控制阀的耐磨性、密封性和可靠性。
另一方面,控制阀的灵活性和响应速度也是需要优化的方面。
可通过优化液压系统的传动结构和增加控制信号的反馈机制来提高控制阀的灵活性和响应速度。
当液压系统需要进行性能调整或维护时,控制阀的调试和维修工作也显得十分重要。
在控制阀的调试过程中,可以通过监测和分析液压系统的工作参数来判断控制阀的工作状态和性能。
通过调整控制阀的参数和特性,可以实现液压系统的工作效率和性能的最优化。
在控制阀的维修过程中,应遵循正确的维修规范和方法,以确保控制阀的可靠性和使用寿命。
总结而言,控制阀在液压系统中的优化设计是提高液压系统性能和工作效率的关键环节。
通过合理选择控制阀、优化控制阀的布置和连接方式、提高控制阀的性能和可靠性,以及注意控制阀的调试和维修工作,可以实现液压系统的最优化设计和运行。
提升阀门装配调试效率的实用技术方法介绍

提升阀门装配调试效率的实用技术方法介绍阀门是工业生产中不可或缺的设备,其装配和调试是确保阀门正常运行的重要环节。
然而,由于阀门种类繁多、结构复杂,装配和调试过程中常常出现一些问题,导致效率低下。
为了提升阀门装配调试效率,本文将介绍一些实用的技术方法。
1. 优化工艺流程优化工艺流程是提高阀门装配调试效率的关键。
首先,需要对装配和调试的流程进行详细的分析和规划,确定每个步骤的时间和顺序。
其次,根据实际情况,合理分配人力资源,确保每个环节都有足够的人手。
最后,建立一套完善的工艺标准和作业指导书,对每个步骤进行详细说明,以提高操作的准确性和效率。
2. 使用专用工具和设备在阀门的装配和调试过程中,使用专用工具和设备可以大大提高效率。
例如,使用扭矩扳手可以确保螺栓的紧固力度符合要求,使用液压泵可以快速完成阀门的压力测试。
此外,还可以根据具体情况选择适合的辅助设备,如吊装机械、气动工具等,以提高操作的便捷性和效率。
3. 加强培训和技能提升阀门装配和调试是一项技术活,需要操作人员具备一定的专业知识和技能。
因此,加强培训和技能提升是提高效率的重要手段。
可以通过组织内部培训、邀请专家讲座等形式,提高操作人员的专业水平和技术能力。
同时,还可以鼓励员工参加相关的培训课程和考取相关的证书,以不断提升自身的竞争力和专业素养。
4. 引入信息化管理系统引入信息化管理系统是提高阀门装配调试效率的重要途径。
通过建立数据库和信息平台,可以实现对装配和调试过程的全程监控和管理。
操作人员可以通过电脑或移动终端随时查看任务进度、工艺标准和作业指导书,提高工作的协同性和准确性。
此外,还可以通过数据分析和挖掘,发现问题和瓶颈,及时进行调整和优化,提高整体效率。
5. 加强沟通和协作在阀门装配和调试过程中,加强沟通和协作是提高效率的关键。
不同环节之间需要紧密配合,及时交流信息和问题,确保任务的顺利进行。
可以通过定期召开会议、建立沟通渠道等方式,促进各个环节之间的协作和信息共享。
优化液压阀体安全阀孔加工工艺

莫克公 司特有的液压 阀体加 工理 念
及相应 的刀具技术 。通过采用此 种
刀具优 化方案 ,不仅 可以提高孔 的 加 工质量 ,而且可以大 大提高加 工 效率 ,从而 降低单件 的总体加工成
本。
液压 阀体 安全阀孔加工 难 点及原 工艺 分析
图1 为典 型 的液 压 阀体 安全 阀 孔 ,材料 为HT 5 ,为 无预铸孔加 20 图1 液压阀体安全阀孔
轴 度和 圆度要 求 ,并使孔 内壁保持 1u , m的粗 糙度 ,是个 比较大 的难 6
题 。但 只 有 保 证这 样 的公 差 要 求 才 能生产 出性能 优越的 阀体产 品。 而 且 ,客 户产量 每年 达到 1 0 0 0 5 0
件 ,要求生产节 拍也很高 ,效 率必
须得 到提 高。
低到11 .。
() 1m /1mm 三 刃阶梯 钻加 工 5 和 8 m孔 ,一步成形 , 1  ̄ 5 m ̄ 8 1mm 1m
包括倒角等 ,如 图2 所示 。
v =1 5 s c 4 m/ .Fn 0 4.n= 9 0 / n = . 20r mi
( ) 有 效 提 高 了 加 工 效 4 率 ,减 少 了加 工节 拍 。整 个 孔
工 。从 图中可以看 出 ,它对表面粗
糙度 、直径 公差都有很 高的要求 。
客户的加工工艺分析如下 :
( )中心钻。 1
因为客 户原来加工 的阀体装 配后 , 总有很大 的噪声 ,整机 内泄严重 ,
所 以 客 户 还对 8 mm/ 9  ̄ mm有 同
( )0 48 2 1. mm预锄 1mm和 5
( )整个 阀体性 能 得到 很 3
尤尼莫克的优化方案及特点
液压阀块加工工艺以及检测内部毛刺的方法
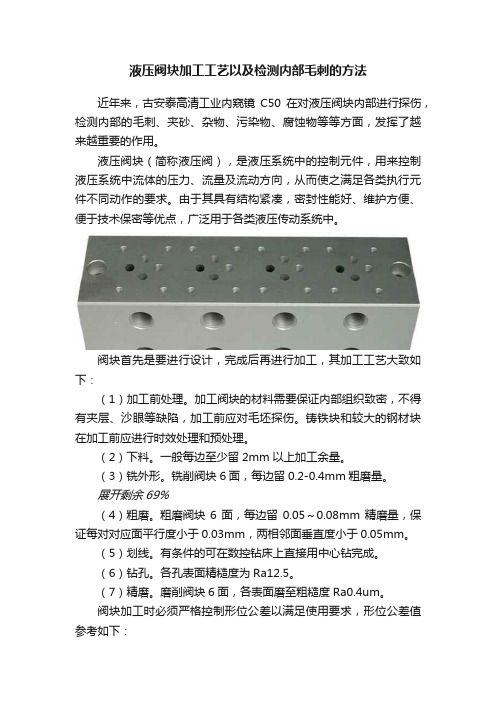
液压阀块加工工艺以及检测内部毛刺的方法近年来,古安泰高清工业内窥镜C50在对液压阀块内部进行探伤,检测内部的毛刺、夹砂、杂物、污染物、腐蚀物等等方面,发挥了越来越重要的作用。
液压阀块(简称液压阀),是液压系统中的控制元件,用来控制液压系统中流体的压力、流量及流动方向,从而使之满足各类执行元件不同动作的要求。
由于其具有结构紧凑,密封性能好、维护方便、便于技术保密等优点,广泛用于各类液压传动系统中。
阀块首先是要进行设计,完成后再进行加工,其加工工艺大致如下:(1)加工前处理。
加工阀块的材料需要保证内部组织致密,不得有夹层、沙眼等缺陷,加工前应对毛坯探伤。
铸铁块和较大的钢材块在加工前应进行时效处理和预处理。
(2)下料。
一般每边至少留2mm以上加工余量。
(3)铣外形。
铣削阀块6面,每边留0.2-0.4mm粗磨量。
展开剩余69%(4)粗磨。
粗磨阀块6面,每边留0.05~0.08mm精磨量,保证每对对应面平行度小于0.03mm,两相邻面垂直度小于0.05mm。
(5)划线。
有条件的可在数控钻床上直接用中心钻完成。
(6)钻孔。
各孔表面精糙度为Ra12.5。
(7)精磨。
磨削阀块6面,各表面磨至粗糙度Ra0.4um。
阀块加工时必须严格控制形位公差以满足使用要求,形位公差值参考如下:阀块6个面相互之间的垂直度公差为0.05mm;相对面的平行度公差为O.03mm;各面的平面度公差为0.02mm;螺纹与其贴合面之间垂直度公差0.05mm;所有孔与所在端面垂直度的允差为如0.05mm为了保证液压系统的清洁度,液压阀块必须进行去毛刺。
目前很多厂家仍然采用毛刷进行人工去毛刺,也有采用甲烷爆破法去毛刺的。
液压阀块去毛刺完成后需通过工业内窥镜检验,以确保毛刺清理完毕。
最后对阀块进行清洗。
清除附着在阀块表面的各种颗粒污染物、腐蚀物、油脂等。
为了确保阀块在使用中不会过早的生锈,必须进行防锈处理。
阀块的内部油道可采用酸洗磷化,外表面防锈处理工艺主要有发蓝、镀镉、镀锌、镀镍等表面处理。
压力阀块加工工艺
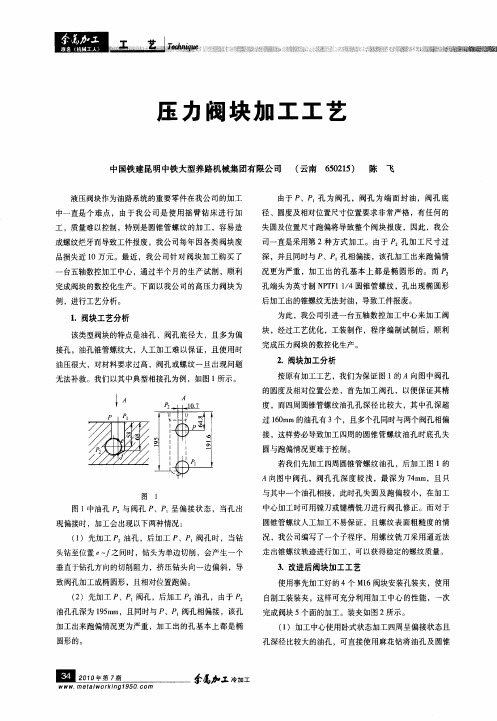
与其 中一个油孔相接 , 此时孔失 圆及 跑偏较小 ,在加工
中心加工时可用镗刀或键槽铣 刀进行 阀孔修正。而对于
图 1中油孑 : 阀孔 P、P 呈偏接 状态 ,当孔 出 L 与 P 现偏接时 ,加工会出现以下两种情况 : ( )先加工 P 油孑 ,后加工 P 阀孔 时,当钻 1 : L 、P 头钻至位置 e f 间时 ,钻头为单边切削 ,会产生一个 ~之
2 .阀块加工分析
按原有加工工艺,我们为保证 图 1的 A向图中阀孑 L
的圆度及相对位置公差 ,首先加工 阀孔 ,以便保证其精
J
度 ,而四周 圆锥管螺纹油孔孔深径 比较 大 , 中孔深超 其
过 10 m的油孔有 3个 ,且多个孔 同时与两个 阀孔相偏 6m 接 ,这样 势必导致加工 四周 的圆锥管螺纹油孔 时底孔 失 圆与跑偏情况更难于控制 。 若我们先加工 四周 圆锥管螺纹油 孔 ,后加 工图 1的 A向图中阀孔 ,阀孔孔深 度较 浅 ,最深 为 7 m 4 m,且 只
圆
管螺纹底孔加工至尺寸。在加工阀块卧式状态、其余 四
周偏接孔时 , 必须遵循钻一扩一镗 ( 或铣 )方式 ,以便 将加工失圆的孔修正 。 排屑通畅。
( )使用 圆锥管螺纹铣 刀加工各螺纹孔 。此 时应 注 5 意清除油孔 内残 留切屑 ,保证铣削时不会 被切屑将螺 纹
拉伤。我公司使用的是德国 WA T R公司生产的螺纹铣 LE
一
由于 P 为 阀孔 ,阀孔 为端 面封 油 ,阀孔 底 、P 孔 径、圆度及相对位置尺寸位 置要求 非常严格 ,有任何的
失圆及位置尺寸跑偏将导致整个 阀块报废 ,因此 ,我公
司一直是采用第 2 种方式 加工 。由于 P 孔 加工尺 寸过 : 深, 并且 同时与 P . 、P 孔相偏接 , 该孔加工 出来跑偏情
液压集成块智能优化算法概述
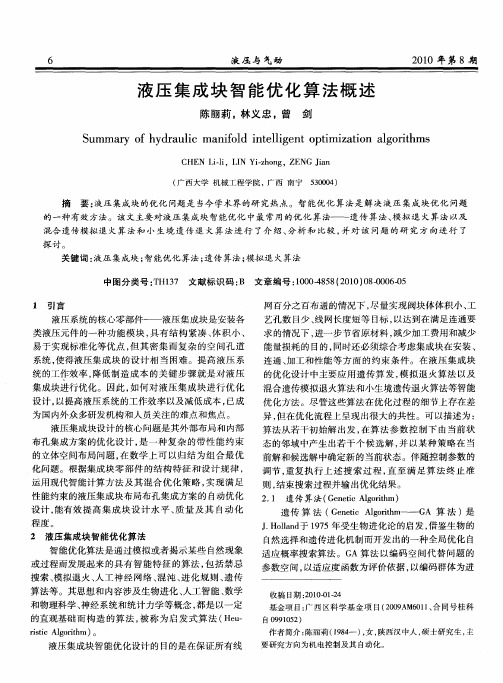
液 压 与 气动
21 0 0年 第 8期
Hale Waihona Puke 液 压 集 成 块 智 能 优 化 算 法 概 述
陈 丽 莉 , 义 忠 ,曾 林 剑
S mma y o y r u i n f l n e l e to tmia in ag r h u r fh d a l ma i d i t l g n p i z to l o i ms c o i t
21 0 0年 第 8期
液 压 与 气动
7
化基础 , 以对群 体 中个 体 位 串 的遗 传 操 作 实 现 选择 和
遗传机 制 , 建立 起 一个迭 代 的过 程 。在这 一 过程 中 , 通 过随 机重 组编 码位 串 中重 要 的 基 因 , 使新 一 代 的 位 串 集 合优 于 老一代 的位 串集合 , 体 的个体 不 断进 化 , 群 逐 渐接 近最 优 解 , 终 达 到 求 解 问 题 的 目的 。G 最 A算 法
关键 词 : 液压集 成块 ; 能优化 算 法 ; 智 遗传 算 法 ; 拟退 火算 法 模
中图分类 号 : H 3 文献 标识码 : 文章 编号 :0 04 5 ( 0 0 0 -0 60 T 17 B 10 -8 8 2 1 )80 0 -5
1 引 言
网百分 之百 布通 的情况 下 , 量实 现阀块 体体积 小 、 尽 工 艺孔数 目少 、 网长度短 等 目标 , 线 以达到在 满足连 通要
C HEN L — ,L N Yiz o g EN Ja i i I —h n ,Z G in l
( 西大学 机械工程学 院, 西 南宁 广 广
5 00 ) 30 4
摘
要: 液压 集成块 的优化 问题 是 当今 学 术界 的研 究热点 。智 能优 化 算 法是 解决 液 压集 成 块优 化 问题
液压阀块设计
液压阀块设计方法1.1液压阀块的结构特点按照结构和用途划分,液压阀块有条形块、小板块,盖板、夹板、阀安装底板、泵阀块、逻辑阀块、叠加阀块、专用阀块、集流排管和连接块等多种形式。
实际系统中的液压阀块是由阀块体以及其上安装的各种液压阀、管接头、附件等元件组成。
(1)阀块体阀块体是集成式液压系统的关键部件,它既是其它液压元件的承装载体,又是它们油路连通的通道体。
阀块体一般都采用长方体外型,材料一般用铝或可锻铸铁。
阀块体上分布有与液压阀有关的安装孔、通油孔、连接螺钉孔、定位销孔,以及公共油孔、连接孔等,为保证孔道正确连通而不发生干涉有时还要设置工艺孔。
一般一个比较简单的阀块体上至少有40-60个孔,稍微复杂一点的就有上百个,这些孔道构成一个纵横交错的孔系网络。
阀块体上的孔道有光孔、阶梯孔、螺纹孔等多种形式,一般均为直孔,便于在普通钻床和数控机床上加工。
有时出于特殊的连通要求设置成斜孔,但很少采用。
(2)液压阀液压阀一般为标准件,包括各类板式阀、插装阀、叠加阀等,由连接螺钉安装在阀块体上,实现液压回路的控制功能。
(3)管接头管接头用于外部管路与阀块的连接。
各种阀和阀块体组成的液压回路,要对液压缸等执行机构进行控制,以及进油、回油、泄油等,必须与外部管路连接才能实现。
(4)其它附件包括管道连接法兰、工艺孔堵塞、油路密封圈等附件。
1.2液压阀块的布局原则阀块体外表面是阀类元件的安装基面,内部是孔道的布置空间。
阀块的六个面构成一个安装面的集合。
通常底面不安装元件,而是作为与油箱或其它阀块的叠加面。
在工程实际中,出于安装和操作方便的考虑,液压阀的安装角度通常采用直角。
液压阀块上六个表面的功用(仅供参考):(1)顶面和底面液压阀块块体的顶面和底面为叠加接合面,表面布有公用压力油口P、公用回油口O、泄漏油口L、以及四个螺栓孔。
(2)前面、后面和右侧面(a)右侧面:安装经常调整的元件,有压力控制阀类,如溢流阀、减压阀、顺序阀等:流量控制阀类,如节流阀、调速阀等。
液压阀块的工艺优化,示例说明液压阀块的加工。
液压阀块的工艺优化,示例说明液压阀块的加工。
转载是一种美德1 液压阀块加工过程中的技术分析与工艺改进[摘要]介绍了液压阀块的加工工艺,解决了液压阀在加工过程中所遇到的一些技术难点,通过对刀具及工艺的改进为企业提高了生产效率的同时降低了企业加工成本。
[关键词]液压阀块、加工中心、三坐标测量仪、滚压刀一、简介液压阀块在液压系统中的重要性已被越来越多的人们所认识,其应用范围也越来越广泛。
液压阀块的使用不仅能简化液压系统的设计和安装,而且便于实现液压系统的集成化和标准化,有利于降低制造成本,提高精度和可靠性。
随着液压系统复杂程度的提高,对液压阀块的要求也越来严格,提高了液压阀块生产制造和加工检验的难度,若加工工艺考虑不周,就会造成加工成本提高、原材料浪费、生产效率底等一系列问题。
所以本文以一典型液压阀块为课题进行深入研究,对加工工艺、工装夹具、刀具选用等方面进行合理优化,从而发现并解决了液压阀块在生产中的效率底、成本高、尺寸精度不稳定等一系列难题。
二、液压阀块概述2.1液压阀块的作用液压阀是一种用压力油操作的自动化元件,它受配压阀压力油的控制,通常与电磁配压阀组合使用,可用于远距离控制水电站油、气、水管路系统的通断。
而液压阀的核心部件即为液压阀块,液压阀块在液压阀中起到控制液流的方向、压力和流量的重要作用。
2.2加工精度液压阀块上安装阀、法兰的表面粗糙度应达到Ra0.4,末端管接头的密封面的表面粗糙度应达到Ra3.2。
另外,安装管接头的螺孔与其外贴合面之间的垂直度允差至少应为8级。
阀块上所有螺孔应有加工精度要求,一般选7H,螺纹式插装阀的安装孔的加工精度应附合产品样本的要求,插装阀安装孔的粗糙度为Ra0.8,此外,还要有尺寸公差和形位公差要求。
0型圈沟槽的表面粗糙度为Ra3.2,一般流道的表面粗糙度为Ra12.5。
2.3材料选择高压阀块最好采用35 锻钢,一般的阀块采用A3钢或球墨铸铁,在用气割从板材上裁制阀块材料时,应留有足够的加工余量,最好将阀块的毛坯进行锻造后再加工。
新型液压阀的优化设计
新型液压阀的优化设计随着产业的发展,越来越多的机械设备开始采用液压系统进行控制。
液压系统具有结构简单、功率密度高、响应灵敏等优点,因此被广泛应用于工业生产。
其中,液压系统的核心部件就是液压阀。
液压阀的设计优化对于机械系统的性能和寿命具有极为重要的影响。
本文就新型液压阀的优化设计进行探讨。
一、液压阀的结构液压阀主要包括:阀体、阀芯、弹簧、密封圈等部分。
其中阀体是阀的主体部分,承受着液压力的作用;阀芯则是阀门打开或关闭的主要部分;弹簧则根据需要提供开启或关闭的力量;密封圈则起到密封作用。
二、优化设计的目标液压阀的优化设计目标主要是针对其工作时存在的一些缺陷和不足,如:流量损失较大、能耗高、振动噪声等问题,进行改善。
首先,要尽量减少液压阀的流量损失,提高其工作效率。
流量损失是液压系统中最主要的能量损失形式,而液压阀是导致流量损失的关键部件。
设计上要注意减少内部通道长度和过渡段,优化阀门的孔形式和位置,减小阀门启闭时的泄压量。
其次,要尽量降低液压阀的能耗。
目前,国内很多液压系统仍然存在能耗高的问题。
要想实现液压系统能耗的降低,就必须对液压阀进行优化设计。
常用的技术手段有:采用先进的液压技术和材料、以及优化阀门的结构和控制电路等。
最后,要尽量减少液压阀的振动噪声。
在液压系统的工作过程中,液压阀的振动会产生噪声,影响人体健康以及机器的精度和寿命。
液压阀的结构设计应该从减小阀门惯性力、缩小流量孔口和增加缓冲结构等方面入手,降低其振动噪声。
三、优化设计的具体方法1、减少阀门内部流失针对阀门内部流失造成的流量损失问题,可以采用以下措施:合理分配流路;减少过渡段长度;精确控制公称通径;选择阀门的孔形式;采用细节设计等。
2、提高阀门的控制精度为了减少能耗并提高系统的灵敏度和稳定性,阀门的控制精度至关重要。
因此,在阀门的设计中,需要考虑采用响应性更好的新型定位元件和精度更高的加工技术,以提高阀门的控制精度。
3、优化阀门的材质和加工工艺使用新型高分子材料代替传统金属材料可降低系统能耗。
液压阀块数控加工工艺的实践探析
机电信息工程液压阀块数控加工工艺的实践探析陈文升(广东省佛山职业技术学院,广东佛山528137)摘要:本文通过分析液压阀块加工工艺特征,阐述液压阀块孔径的加工方式,分析多轴加工、斜孔加工等不同的方式加工,为液压阀块的数控加工提供&关键词:液压阀块;数控加工;工艺实践;分析1液压阀块的工艺的材料根据耐压性能可以选择多种,比、段铸铁、钢件,如果对压力选择非常,则可以选。
为了安装、连通各门和油路,该部件一般为六面体,在各个面布不式的孔,这里进行简单。
(1)安装孔:安的主要作用在系统之上,同时在安不、盖板。
在实作当中其实加工方式很简单,型号多为M5〜M16,公 纹孔。
加工的时候需要注意攻丝过程中丝断的风险。
为降低该风险,因此选择柔性、挤压丝加以避免作者简介:陈文升(1980-),男,广东佛山人,本科,机械助理实验师,研究方向:机械工程及自动化&控加工方面的知识与机械制造企业的实际情况结合在一起,继而为数控加工的高效应用和人才。
其次,加强内部。
机械业可以从数控加工技术人才中选拔人才,然后为其提供研学机会,在有的进对性的教学,让其形的,运用最新的数控加技术来更好维和管理机械数控加工系统。
从人进到人养,只有在高素人才支下,数控加在机械中发应有的价值和作用。
3.2优化机械制造流程,开展精细化管理优化机械制造流程,开展精细化管理,也是促进数控加工在机械制造中应用的重要路径。
尽管数控加有监控功能,但是有序的机械够有效提升数控加工应用效率,让机械生产线高效的。
在这一中,机械业需要生产线上的责任人,将生产监督责实到个人,要求被折断的风险。
挤压丝锥不需要排屑,而且加工质量很好&精度方面有要求。
(2)接口孔:油口孔和管接头孔的主要作用P口、T口油路。
在孔口位置要求使用管螺纹,方便与油管连接。
口没有螺纹,在孔口端面常常以O形圈来进行密封,因此在加工的中对孔口位置度有一定要求。
在加工完成之、清洗、去毛刺的中要非常小心,避免划伤以及影响密封性能。
- 1、下载文档前请自行甄别文档内容的完整性,平台不提供额外的编辑、内容补充、找答案等附加服务。
- 2、"仅部分预览"的文档,不可在线预览部分如存在完整性等问题,可反馈申请退款(可完整预览的文档不适用该条件!)。
- 3、如文档侵犯您的权益,请联系客服反馈,我们会尽快为您处理(人工客服工作时间:9:00-18:30)。
液压阀块加工过程中的技术分析与工艺改进
[摘要]介绍了液压阀块的加工工艺,解决了液压阀在加工过程中所遇到的一些技术难点,通过对刀具及工艺的改进为企业提高了生产效率的同时降低了企业加工成本。
[关键词]液压阀块、加工中心、三坐标测量仪、滚压刀
一、简介
液压阀块在液压系统中的重要性已被越来越多的人们所认识,其应用范围也越来越广泛。
液压阀块的使用不仅能简化液压系统的设计和安装,而且便于实现液压系统的集成化和标准化,有利于降低制造成本,提高精度和可靠性。
随着液压系统复杂程度的提高,对液压阀块的要求也越来严格,提高了液压阀块生产制造和加工检验的难度,若加工工艺考虑不周,就会造成加工成本提高、原材料浪费、生产效率底等一系列问题。
所以本文以一典型液压阀块为课题进行深入研究,对加工工艺、工装夹具、刀具选用等方面进行合理优化,从而发现并解决了液压阀块在生产中的效率底、成本高、尺寸精度不稳定等一系列难题。
二、液压阀块概述
2.1液压阀块的作用
液压阀是一种用压力油操作的自动化元件,它受配压阀压力油的控制,通常与电磁配压阀组合使用,可用于远距离控制水电站油、气、水管路系统的通断。
而液压阀的核心部件即为液压阀块,液压阀块在液压阀中起到控制液流的方向、压力和流量的重要作用。
2.2加工精度
液压阀块上安装阀、法兰的表面粗糙度应达到Ra0.4,末端管接头的密封面的表面粗糙度应达到Ra3.2。
另外,安装管接头的螺孔与其外贴合面之间的垂直度允差至少应为8级。
阀块上所有螺孔应有加工精度要求,一般选7H,螺纹式插装阀的安装孔的加工精度应附合产品样本的要求,插装阀安装孔的粗糙度为Ra0.8,此外,还要有尺寸公差和形位公差要求。
0型圈沟槽的表面粗糙度为Ra3.2,一般流道的表面粗糙度为Ra12.5。
2.3材料选择
高压阀块最好采用35 锻钢,一般的阀块采用A3钢或球墨铸铁,在用气割从板材上裁制阀块材料时,应留有足够的加工余量,最好将阀块的毛坯进行锻造后再加工。
加工阀块的材料须要保证内部组织致密,不得有夹层、沙眼等缺陷,必要时应对毛坯探伤。
铸铁块和较大的钢材块在加工前应进行时效处理和预处理。
本文中的工件材料为QT400-18。
三、液压阀块加工难点分析
难点1、加工效率低
首先是装夹较繁琐,此零件的重点是在B—B剖视图(见下图)相交孔的加工方法上,正常情况下加工三侧面就需要三次装夹,再加上Φ4斜孔就是四次装夹,而且不容易保证孔与孔间的相互位置关系。
其次是加工过程中所需刀具较多,如图纸所示X、Y、V、U局部视图(见下图)中的孔口相当复杂,比如X视图中的45°、15°、R0.1在加工过程中就占用了三把专用刀,而且粗糙度以及形位公差不容易满足图纸要求,影响加工效率。
难点2、形位公差较高
如下图所示,图纸要求中心孔圆度及圆柱度要保证在0.005mm之内,并且要求Φ14孔与Φ15孔的同轴度在0.1mm之内,如何保证加工后的零件满足图纸要求,是关系到整个零件加工后是否合格的重中之重。
难点3、粗糙度要求较高
如下图所示,要求中心Φ14H7孔在满足以上严格的行为公差的同时粗糙度好要保证在Ra0.8以下,这样使中心孔的加工难度有提高了一级,对工艺人员的工艺安排及刀具选用提出了更加苛刻的要求。
四、难点解决方案
1、工装的设计
通过对图纸的认真分析,决定将B—B剖视图中的相交孔放在带回转轴的立式加工中心上加工,以减少工件装夹次数,同时解决了Φ4斜孔的角度问题。
工装设计如下图所示,工件采用一面三销定位,符合六点定位原则(一面限定工件3个自由度,两长销限定工件2个自由度,一短销限定工件1个自由度),一次装夹两个零件,图中①为工件紧固螺钉孔,通过图纸C—C剖所示的四个通孔将工件紧固与工装之上;图中②为定位销,其中中间两个为长销(外露长度15mm左右),左右两侧为短销(外露长度小于3mm ),以防止在加工过程中与刀具产生干涉问题;图中③为紧固螺钉孔,通过次孔将工装紧固与加工中心回转轴花盘上。
需要注意的是工装四角经过认真处理过,四段圆弧是以工装回转中心相一致的向心弧,它的作用就是解决每次装夹工装时的重复定位问题(每次装夹工装时,用百分表找四段圆弧的跳动,小于0.02mm
即可)。
工装设计简图(虚线为工件轮廓)
2、复合刀具的选用
复合刀具是将两把或两把以上的同类或不同类的孔加工刀具组合成一体的专用刀具,它能在一次加工的过程中,完成钻孔、扩孔、铰孔、锪孔和镗孔等多工序不同的工艺复合,具有高效率、高精度、高可靠型的成形加工特点。
为了减少加工X、Y、V、U局部视图的所需刀具,我们选用了复合刀具,通过定制硬质合金复合刀具,减少了刀具的使用量,一把刀具可同时加工出螺纹底孔、45°、15°、R0.1倒角以及外侧沉孔,极大的提高了加工效率。
复合刀具设计如下:
G1/4复合刀
G1/8复合刀
G3/8复合刀
3、中心阀芯孔的工艺解决方案
为了达到图纸要求,H7的公差等级、圆度0.005mm、圆柱度0.005mm、粗糙度Ra0.8、两孔同轴度0.1mm,我们采用了钻、镗、铰、滚压的加工工艺,首先通过合金钻头将底孔加工至Φ13去处加工量;其次用Φ13.8和Φ15.1粗镗刀双向镗孔,以确保孔的位置精度;再次用
,粗糙Φ13.99的合金铰刀稳定孔径(一般铰孔后的孔径为Φ14+0.002
-0.002
度为Ra1.6);最后通过可微调滚压刀保证孔的尺寸精度,同时达到图纸所要求的粗糙度值。
滚压刀
五、工艺改进成果
通过工艺改进后加工出来的工件,经过检测全部合格,其中阀芯孔尺寸为Φ14.013mm,圆度和圆柱度经过三坐标测量分别为0.002mm和0.004mm,粗糙度经过粗糙度仪测量为Ra0.3,加工时间由原来的90分钟(加工中心所用时间)缩短为20分钟,尺寸稳定性大幅提高。
经过对比,工艺改进后的刀具成本上升了10%,加工时间降低了45%,
产品废品率由原来的5% 降低到现在的0.5%,虽然刀具成本有略微升高,但是整体加工成本比原来降低了50%。
六、结束语
液压阀块的投入使用对液压系统的集成有了质的飞跃,同时简化了系统的安装,增加系统运行的可靠性。
目前国内液压生产厂家已经设计、制造出用于各种液压系统的液压阀块,并且渐趋形成定型化,标准化产品。
而面对传统工艺加工方法,不仅加工精度难以保证,同时加工效率极低,只有不断创新、钻研、优化加工工艺才能使加工设备得以充分的发挥,提高加工效率、降低加工成本。
参考文献 [1]《机械设计手册》联合编写组编.机械设计手册.北京:机械工业出版社,1998。