各种添加剂对低温陶瓷结合剂性能的影响
添加剂对釉浆性能的影响

添加剂对釉浆性能的影响作者:毛旭琼来源:《佛山陶瓷》2013年第07期摘要:本文主要针对目前陶瓷砖生产中容易出现与釉浆性能相关的各种问题,从理论与实践的角度,详细阐述各种添加剂的性能、对釉浆的影响,以及其在陶瓷砖生产中的作用。
实践表明,釉料的工艺性能仅靠原材料配方的调整是很难达到最佳使用效果的,必须通过合适的添加剂来进行合理的调节与改善才能实现。
关键词:添加剂;陶瓷砖;釉浆性能;控制;改善1 前言经过数十年的摸索与沉淀,如今,陶瓷砖的生产工艺已趋于稳定。
尤其在釉浆性能等方面得到了较好的改善,这主要得益于各种新型添加剂的推广和应用。
新型添加剂的引入,可让陶瓷釉浆性能得到显著的提高,并保持稳定。
虽然其加入量很少,但能起到优化工艺、提高产品质量的作用。
衡量釉浆性能好坏的主要指标有以下几方面:釉浆的粘性、流动性、保水性、悬浮性、分散性、干水速度、保存时间、釉面强度等。
另外,还要保证辊筒、丝网印花的各种印刷性能等。
必须说明的是,以上有些性能不是独立的,具有统一性。
2 添加剂对釉浆性能的影响2.1 甲基与三聚磷酸钠对釉浆性能的影响2.1.1釉浆沉淀及处理方法在大生产过程中,釉浆在静置或搅拌速度较慢时,会出现分层及沉淀现象。
有的沉淀不严重,搅动后其性能又可恢复;有的沉淀较严重,很难搅起,就算搅起后在很短一段时间内又会重新沉淀,严重影响线上的使用性能。
尤其是颜色较深的釉,分层与沉淀会导致颜色的不均匀,产生色差与色边等缺陷。
这一般是由塑性粘土、CMC及三聚磷酸钠的种类与添加的配比不合适引起的。
就CMC而言,我们宜选用分子链较长的中、高粘类型产品,与三聚磷酸钠搭配,其添加量也需经过反复实验来确定。
若CMC加入量过多,会导致生产线上因釉浆比重低、干水速度慢,而不利于二次烧的淋釉工艺。
尤其是辊筒印花,釉面太湿会加剧白边、白点,以及后辊粘前辊的问题;添加量太少又会导致釉浆悬浮性不够而出现沉淀。
总之,CMC 的添加量与比例不能随意而定,要在保证釉浆不沉淀的条件下,具有较高的比重与较好的流动性。
在95瓷中普遍采用CaO
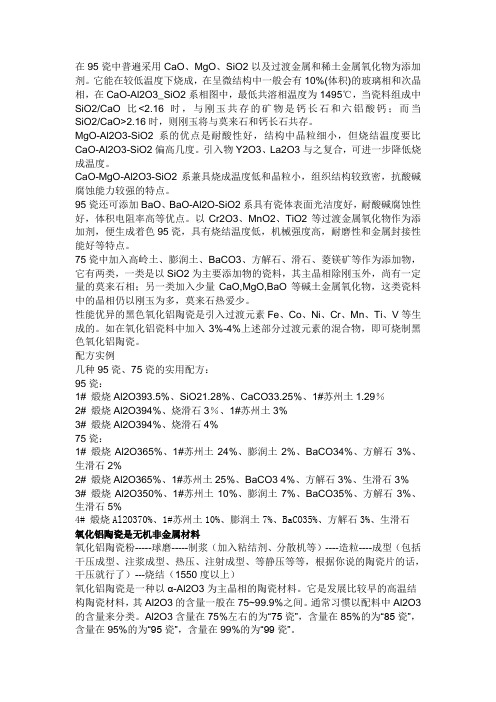
在95瓷中普遍采用CaO、MgO、SiO2以及过渡金属和稀土金属氧化物为添加剂。
它能在较低温度下烧成,在呈微结构中一般会有10%(体积)的玻璃相和次晶相,在CaO-Al2O3_SiO2系相图中,最低共溶相温度为1495℃,当瓷料组成中SiO2/CaO比<2.16时,与刚玉共存的矿物是钙长石和六铝酸钙;而当SiO2/CaO>2.16时,则刚玉将与莫来石和钙长石共存。
MgO-Al2O3-SiO2系的优点是耐酸性好,结构中晶粒细小,但烧结温度要比CaO-Al2O3-SiO2偏高几度。
引入物Y2O3、La2O3与之复合,可进一步降低烧成温度。
CaO-MgO-Al2O3-SiO2系兼具烧成温度低和晶粒小,组织结构较致密,抗酸碱腐蚀能力较强的特点。
95瓷还可添加BaO、BaO-Al2O-SiO2系具有瓷体表面光洁度好,耐酸碱腐蚀性好,体积电阻率高等优点。
以Cr2O3、MnO2、TiO2等过渡金属氧化物作为添加剂,便生成着色95瓷,具有烧结温度低,机械强度高,耐磨性和金属封接性能好等特点。
75瓷中加入高岭土、膨润土、BaCO3、方解石、滑石、菱镁矿等作为添加物,它有两类,一类是以SiO2为主要添加物的瓷料,其主晶相除刚玉外,尚有一定量的莫来石相;另一类加入少量CaO,MgO,BaO等碱土金属氧化物,这类瓷料中的晶相仍以刚玉为多,莫来石热爱少。
性能优异的黑色氧化铝陶瓷是引入过渡元素Fe、Co、Ni、Cr、Mn、Ti、V等生成的。
如在氧化铝瓷料中加入3%-4%上述部分过渡元素的混合物,即可烧制黑色氧化铝陶瓷。
配方实例几种95瓷、75瓷的实用配方:95瓷:1# 煅烧Al2O393.5%、SiO21.28%、CaCO33.25%、1#苏州土1.29%2# 煅烧Al2O394%、烧滑石3%、1#苏州土3%3# 煅烧Al2O394%、烧滑石4%75瓷:1# 煅烧Al2O365%、1#苏州土24%、膨润土2%、BaCO34%、方解石3%、生滑石2%2# 煅烧Al2O365%、1#苏州土25%、BaCO3 4%、方解石3%、生滑石3%3# 煅烧Al2O350%、1#苏州土10%、膨润土7%、BaCO35%、方解石3%、生滑石5%4# 煅烧Al2O370%、1#苏州土10%、膨润土7%、BaCO35%、方解石3%、生滑石氧化铝陶瓷是无机非金属材料氧化铝陶瓷粉-----球磨-----制浆(加入粘结剂、分散机等)----造粒----成型(包括干压成型、注浆成型、热压、注射成型、等静压等等,根据你说的陶瓷片的话,干压就行了)---烧结(1550度以上)氧化铝陶瓷是一种以α-Al2O3为主晶相的陶瓷材料。
Y_2O_3添加剂对SiC复相多孔陶瓷烧结性能和力学性能的影响
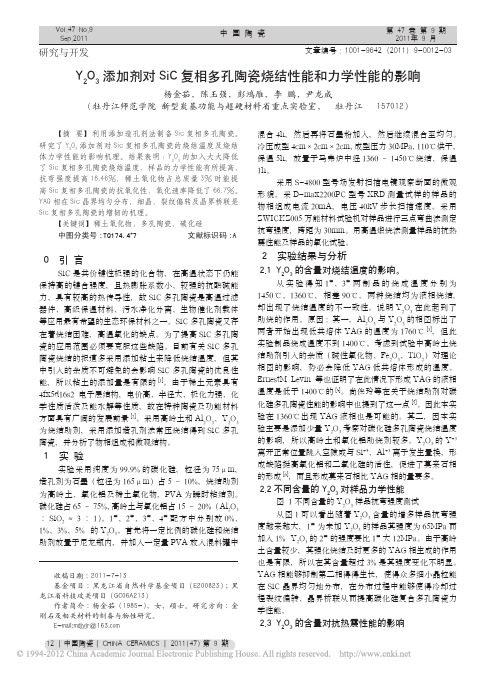
【摘 要】利用添加造孔剂法制备SiC 复相多孔陶瓷。
研究了Y 2O 3添加剂对SiC 复相多孔陶瓷的烧结温度及烧结体力学性能的影响机理。
结果表明:Y 2O 3的加入大大降低了SiC 复相多孔陶瓷烧结温度,样品的力学性能有所提高,抗弯强度提高18.46%,稀土氧化物占总质量3%时能提高SiC 复相多孔陶瓷的抗氧化性,氧化速率降低了66.7%。
YAG 相在SiC 晶界均匀分布,细晶,裂纹偏转及晶界桥联是SiC 复相多孔陶瓷的增韧的机理。
【关键词】稀土氧化物,多孔陶瓷,碳化硅中图分类号:TQ174.4+7 文献标识码:A0 引 言SiC 是共价键性极强的化合物,在高温状态下仍能保持高的键合强度,且热膨胀系数小、较强的抗酸碱能力、具有较高的热传导性,故SiC 多孔陶瓷是高温过滤器件、高级保温材料、污水净化分离、生物催化剂载体等应用最有希望的生态环保材料之一。
SiC 多孔陶瓷又存在着烧结困难,高温氧化的缺点。
为了提高SiC 多孔陶瓷的应用范围必须要克服这些缺陷。
目前有关SiC 多孔陶瓷烧结的报道多采用添加粘土来降低烧结温度,但其中引入的杂质不可避免的会影响SiC 多孔陶瓷的优良性能,所以粘土的添加量是有限的[1]。
由于稀土元素具有4fx5d16s2 电子层结构,电价高、半径大、极化力强、化学性质活泼及能水解等性质,故在特种陶瓷及功能材料方面具有广阔的发展前景[2]。
采用高岭土和Al 2O 3、Y 2O 3为烧结助剂,采用添加造孔剂法常压烧结得到SiC 多孔陶瓷,并分析了物相组成和微观结构。
1 实 验实验采用纯度为99.9%的碳化硅,粒径为75μm,造孔剂为石墨(粒径为165μm)占5~10%,烧结助剂为高岭土、氧化铝及稀土氧化物,PVA 为瞬时粘结剂。
碳化硅占65~75%,高岭土与氧化铝占15~20%(Al 2O 3 ∶SiO 2≈3∶1)。
1#、2#、3#、4#配方中分别放0%、1%、3%、5% 的Y 2O 3。
氧化铝陶瓷低温烧结助剂研究概述

氧化铝陶瓷低温烧结助剂研究概述氧化铝陶瓷是一种重要的结构陶瓷材料,具有优异的耐磨性、耐腐蚀性、抗高温性等特点,在工业生产和科研领域有着广泛的应用。
然而,氧化铝陶瓷的低温烧结难度较大,需要添加一定的助剂才能够实现良好的烧结效果。
本文将对氧化铝陶瓷低温烧结助剂的研究进展进行概述。
1. 氧化铝陶瓷低温烧结助剂的分类氧化铝陶瓷低温烧结助剂主要分为有机助剂和无机助剂两类。
有机助剂包括聚乙烯醇(PVA)、聚丙烯酸(PAA)、聚乙烯酮(PVP)等;无机助剂包括碳酸钙、硼酸、氧化钙、氢氧化钠等。
2. 有机助剂在氧化铝陶瓷低温烧结中的应用有机助剂可以在氧化铝陶瓷低温烧结过程中起到增强材料粘结力、促进颗粒成核、调节材料微观结构等作用。
其中,PVA 是一种常用的有机助剂,可以有效地提高氧化铝陶瓷的烧结密度和力学性能。
PAA则可以在低温下促进氧化铝颗粒的成核和晶粒生长,提高材料的致密性和硬度。
PVP则可以增加氧化铝陶瓷的塑性变形能力,降低其断裂韧性。
3. 无机助剂在氧化铝陶瓷低温烧结中的应用无机助剂可以在氧化铝陶瓷低温烧结过程中起到促进颗粒成核、调节晶体生长速率、防止晶体生长过快等作用。
其中,碳酸钙可以促进氧化铝陶瓷颗粒的成核和晶粒生长,提高材料的致密性和硬度;硼酸则可以防止氧化铝陶瓷晶体生长过快而导致材料开裂;氢氧化钠则可以调节氧化铝陶瓷晶体生长速率,提高材料的致密性和强度。
4. 氧化铝陶瓷低温烧结助剂的优化为了进一步提高氧化铝陶瓷低温烧结助剂的效果,需要对其进行优化。
目前,主要采用的方法包括改变助剂添加量、改变助剂种类、采用复合助剂等。
其中,复合助剂是一种较为有效的优化方法,可以充分发挥不同助剂的作用,提高氧化铝陶瓷的致密性和力学性能。
综上所述,氧化铝陶瓷低温烧结助剂是实现氧化铝陶瓷低温烧结的关键因素之一,其种类和添加量对于材料的致密性和力学性能具有重要影响。
未来,我们还需要进一步深入研究不同助剂的作用机制,以及如何优化氧化铝陶瓷低温烧结助剂的配方,为其在工业生产和科学研究中的应用提供更为可靠的技术支持。
纯相陶瓷烧结助剂

纯相陶瓷烧结助剂
纯相陶瓷烧结助剂,也被称为助烧剂,是在陶瓷烧结过程中加入的用于促进烧结致密化的氧化物或非氧化物。
由于纯陶瓷材料有时很难烧结,所以在性能允许的前提下,常常添加一些烧结助剂以降低烧结温度。
这可以降低能耗,使烧结成本降低。
根据烧结助剂作用机理的差异,SiC烧结可以分为固相烧结和液相烧结。
在固相烧结中,一种常见的助剂体系是Al-B-C-B4C。
此外,研究还发现,如十二烷基苯磺酸钠、氢氧化钠以及NaA分子筛残渣等添加剂均有助于提高支撑体的气体渗透性、抗弯强度和耐热震性。
特别是添加NaA分子筛残渣这种烧结助剂,制备出的碳化硅多孔陶瓷表现出优良的各项性能:气体渗透率高达1300 m³/(m²·h·kPa),强度可达27 MPa,且具有良好的抗热震性能。
还有一种具有三元层状的Y3Si2C2材料,该材料可作为碳化硅陶瓷新型的烧结助剂,其具有低温液相存在和高温相分解的特性,能起到促进碳化硅陶瓷高温烧结过程中晶粒重排和晶界处重结晶的效果。
合适的烧结助剂能有效降低烧结温度,增强陶瓷材料的致密性,提高其性能表现。
造孔剂对低温制备多孔SiC陶瓷性能的影响

造孔剂对低温制备多孔SiC陶瓷性能的影响
解玉鹏;徐俊
【期刊名称】《大学物理实验》
【年(卷),期】2023(36)1
【摘要】以三元体系Al 2O 3-Y 2O 3-SiO 2作为SiC粉末的烧结助剂,石墨烯、淀粉、鳞片石墨为造孔剂,低温制备高孔隙率的多孔碳化硅陶瓷。
探讨了造孔剂的种类对多孔碳化硅陶瓷的体积密度、气孔率和弯曲强度的影响,分析了多孔碳化硅陶瓷的相组成和显微结构。
研究结果表明:(1)该体系中石墨烯的造孔效果优于淀粉和鳞片石墨的造孔效果,且以石墨烯为造孔剂的多孔SiC陶瓷的抗弯强度要高于以鳞片石墨为造孔剂的多孔SiC陶瓷,低于以淀粉为造孔剂的多孔SiC陶瓷。
(2)在1400℃下以不同的造孔剂烧结制得多孔SiC陶瓷的孔隙率在53.34%~56.82%范围内,其抗弯强度为14.86~17.47 MPa。
(3)使用不同的造孔剂并未改变碳化硅陶瓷物相组成。
【总页数】6页(P35-40)
【作者】解玉鹏;徐俊
【作者单位】吉林化工学院理学院;吉林化工学院材料科学与工程学院
【正文语种】中文
【中图分类】TM285
【相关文献】
1.助烧剂和造孔剂对真空烧结SiC多孔陶瓷性能的影响
2.炭粉作造孔剂制备工艺对多孔羟基磷灰石陶瓷性能的影响
3.造孔剂对氧化物结合SiC多孔陶瓷性能的影响
4.造孔剂对SiC多孔陶瓷材料性能的影响
5.造孔剂对氧化物结合SiC多孔陶瓷性能的影响
因版权原因,仅展示原文概要,查看原文内容请购买。
以MnO2-TiO2-MgO为添加剂注浆成型低温烧结Al2O3陶瓷
以MnO2-TiO2-MgO为添加剂注浆成型低温烧结Al2O3陶瓷采用注浆成型方法,通过加入MnO2-TiO2-MgO复相添加剂,在1350℃空气气氛中常压烧结,获得了相对密度最大为95.7%的氧化铝陶瓷。
研究了MnO2-TiO2-MgO复相添加剂对氧化铝陶瓷显微结构与力学性能的影响。
在添加质量分数为3%MnO2,0.5%MgO的情况下,比较添加不同质量分数的TiO2(1.0~3.0%)对氧化铝陶瓷烧结性能的影响。
通过对比发现,该复相添加剂能有效降低氧化铝陶瓷的烧结温度,在同一温度下,随着TiO2的增加,烧结体密度也随之增加,强度也有明显差别。
结果表明,1350℃下Al2O3+0.5%MgO+3%MnO2+1.5%TiO2体系烧结效果最好,断口为沿晶断裂,无明显气孔,晶粒分布均匀,平均粒径为2μm,无晶粒异常长大现象。
烧结体密度达到3.80g/cm^3,抗弯强度为243MPa。
结果表明,添加TiO2 5%、在1300oC时的常压烧结密度可达到理论值的97%.固定CuO(0.4%)和TiO2(4%)的添加量、改变TiO2(0--32%)和CuO(0--3.2%)的添加量(质量分数, 下同), 研究了CuO--TiO2复合助剂对氧化铝陶瓷烧结性能、微观结构、物相组成以及烧结激活能的影响, 以揭示复合助剂的低温烧结机理。
结果表明, 在1150--1200℃TiO2固溶入Al2O3生成Al2Ti7O15相, 并生成大量正离子空位提高了扩散系数, 从而以固相反应烧结的作用机理促进了氧化铝陶瓷的致密化; TiO2在Al2O3中的极限固溶度为2%--4%, 超过固溶极限的TiO2对陶瓷烧结没有促进作用; 添加适量的CuO(0.4%)可将TiO2在Al2O3中的固溶温度降低到1100℃以下, 并以液相润湿作用促进氧化铝陶瓷的致密烧结。
陶瓷烧结激活能的计算结果定量地印证了上述烧结机理; 当在Al2O3中添加4%的TiO2和2.4%的CuO,可将烧结激活能降低到54.15 kJ ? mol-1。
金属及合金粉对低温陶瓷结合剂性能影响
摘 要 :在低 温陶瓷结合 剂 中添加适量金 属或合金粉 , 就会对结合 剂的耐火度 、 动性 、 流 热膨胀 系数 、 强度 等
性 能 产 生 影 响 。通 过 试 验 分 析 , 金 粉 的加 入 能 改 善 结 合 剂 的 强 度 及 韧 性 。 合
维普资讯
第3 8卷第 4期
20 0 2年 8月
中 国 陶
CH 『 A a囹
瓷
ⅡCS
Vn . 8 No 4 3 1
Au 2 0 g 0 2
金 属 及 合 金 粉 对 低 温 陶 瓷 结合 剂 性 能 影 响
侯 永 改 , 王 改 民 ,荆 运 杰
维普资讯
・
1 ・ 4
中 国 陶
ห้องสมุดไป่ตู้瓷
20 02年 第 4期
加入 A 后 , 2 2 j 在 5 ℃就 出现 一 个放 热峰 , 但是 氧化后 生 成 的 A23 l 覆盖在粉 末表 面阻止 反 应进行 , 以产 生放 0 所
加入, 混合均匀后 , 制作成待测 锥 , 与标准锥 一起放入耐 火度测定炉 内 , 要求 的升 温 曲线 下 , 定 出结合 剂 的 在 测
均 匀 , 别 制 成 测 定 耐 火 度 的 三 角 锥 , 1 X1m 的 圆 分 5 5 m
3 实 验 结 果
3. 加 入 不 同 添 加 剂 时 结 合 剂 差 热 分 析 1
柱体测 定 流 动 性 ,) X2 m 的 圆柱 体 测 定 热 膨 胀 系 日 5 m 4 数。再将结合 剂与磨料 ( C和金刚石 ) G 按磨 具 配 比要求 进行配料 、 料 、 型 、 混 成 干燥 、 成 , 成 10×6×8 m 烧 制 0 m
一种低温陶瓷结合剂及其制备方法[发明专利]
专利名称:一种低温陶瓷结合剂及其制备方法专利类型:发明专利
发明人:不公告发明人
申请号:CN201611059809.7
申请日:20161129
公开号:CN108115580A
公开日:
20180605
专利内容由知识产权出版社提供
摘要:本发明公开了一种低温陶瓷结合剂及其制备方法,该陶瓷结合剂由下列重量分数的物质组成:SiO36~45份,BO 23~33份,FeO 30~40份,CaO 2~8份,LiCO 7~10份,KNO3~5
份,NaO 6~9份。
将所有原料在球磨机中充分混合,在加入水,球磨10~15h,然后静置3~4h,将水倒出,在90~105℃条件下烘干,再球磨、过筛制备得到陶瓷结合剂。
本发明所制备的陶瓷结合剂具有耐火度低、强度高的特点。
申请人:房世俊
地址:224222 江苏省盐城市东台市三仓镇新农村五组78号
国籍:CN
更多信息请下载全文后查看。
加入TaC对Ti3SiC2陶瓷材料性能的影响
T i , S i C , 材料 既有金 属 的特 性 , 又 具有 陶瓷材 料
行 星式球 磨 机 中湿 混 4 h , 干 燥 后 置 于石 墨磨 具 内 进行热 压烧结 , 烧结 温度 分别 为 1 5 0 0 o C, 1 5 5 0  ̄ C, 1 6 0 0 o C, 升温 速率 为 1 0 ℃/ mi n , 热压 压力 为 2 5 M P a , 保 温时 间为 3 h , 气 氛条 件为真 空 。 氧化性 试样 为 4 m m x 4 m m ×1 0 m m 块体 , 表 面最 终用 8 0 0 # S I C砂 纸研 磨 , 在酒 精 中 以超 声 波 方 法 清洗 。热重 分 析在 T G A一 1 6 . 2 0 P热 重分 析 仪 中进 行, 以1 0 o C / m i n升温 至预 定温 度保温 2 0 h, 以获得 不 同温度 下 氧化增 重 随时间变 化 的曲线 。 采用 阿基 米德法 测试 试样 的显 气孔 率和体 积 密
第3 3卷 第 1 期
2 0 1 3年 2月
航
空
材
料
学
报
Vo 1 . 33,No . 1
J O URNA L O F AER ONAU T I C AL MAT E RI A L S
Fe b r u a r y 2 01 3
加入 T a C对 T i 3 S i C 2陶瓷 材 料 性 能 的影 响
d o i : 1 0 . 3 9 6 9 / j . i s s n . 1 0 0 5 — 5 0 5 3 . 2 0 1 3 . 1 . 0 1 0
中图 分 类 号 : T B 3 3
文献标识码 : A
文 章 编 号 :1 0 0 5 — 5 0 5 3 ( 2 0 1 3 ) 叭- 0 0 5 6 - 0 5
- 1、下载文档前请自行甄别文档内容的完整性,平台不提供额外的编辑、内容补充、找答案等附加服务。
- 2、"仅部分预览"的文档,不可在线预览部分如存在完整性等问题,可反馈申请退款(可完整预览的文档不适用该条件!)。
- 3、如文档侵犯您的权益,请联系客服反馈,我们会尽快为您处理(人工客服工作时间:9:00-18:30)。
温度∕℃
∕℃
4.92 5.59 8.09 第三组石条烧成曲线
10.09
温度∕℃
∕℃
实验结果一
氧化铅
实验结果二
氧化锌
实验结果三
硼酸
实验分析一 分析添加剂对低温陶瓷结合剂性能的影响
低温陶瓷结合剂耐火度随添加剂加入的变化 PbO 840 820 800 780 760 740 720 700 680 660 640 620 1 2 3 编号 4 5 ZnO 硼酸
◆目前国内外超硬磨料陶瓷磨具大多采用1000℃以下低温烧成。超硬材
料陶瓷磨具以结合剂磨耗为主,所以磨具的磨削性能及耐用度较差。
◆ 低温陶瓷结合剂有节约能源,降低烧成燃料成本缩短生产周期提高生
产效率提高磨具的外观和内在质量,减少烧成废品可防止磨料性能 因高温作用而产生的性能劣化等优势。
研究意义
低温陶瓷磨具生产中容易产生的一些问题:磨 具坯体的强度差、磨具强度、硬度不易控制,不易 生产高硬度的磨具;因此为了改善结合剂本身性能 可以通过研究添加剂对低温陶瓷结合剂性能的影响
论文题目:
各种添加剂对低温陶瓷结合剂性能的影响
LOGO
实验纲要
◆实验研究背景 ◆实验研究意义 ◆实验过程 ◆实验结果及分析
◆实验结论
◆致谢
研究背景
◆陶瓷结合剂磨具被广泛用于机械、汽车制造业、电子行业、建筑业、
航空航天等许多行业和领域,其用量在磨具总用量中占50%以上。 其中陶瓷结合剂超硬材料加工工具得到发展和应用。
温度∕℃
制作耐火锥、耐火台→干燥→按上图升温曲线烧
烧成→观察锥倒情况并记录相应数据
实验过程六:抗折强度的测定
为制定石条烧成曲线依据耐火度不同将结合剂分为三组烧成:
小石条标准:6㎜×6 ㎜×28㎜ 密度: 2.38g∕ ㎝3 计算得每个小石条质 量M=2.4g
从已混好的试样结合 剂中各称取2.4g,做 15种石条, 每 样 石 条制作4个→混料→ 压制成型→干燥→按 下图烧成曲线烧成→ 取出后测定抗折强度 并记录相关数据
抗折强度的影响
实验过程 二
粘土 长石 混合 过筛 混均匀 基础结合剂 测耐火度 硼玻璃
实验流程图:
氧化铅
氧化锌 混合、加粘结剂
硼酸
三角锥成型、干燥
成型、干燥、烧成
测洛氏硬度
测抗折强度
实验过程 三
实验操作内容
配制糊精液→计算结合剂添加量→制定升温
曲线→制作耐火锥、耐火台→干燥→测耐火
度→压制试样条→制定烧结曲线→烧结→抗 折强度强度的测试。
硼酸:B2O3作为网络形成体,能够使网络结构更加致密,提高 网络的联接强度,使结合剂自身的强度得到提高,从而也可提
高磨具的整体强度;但是B2O3的加入量过多时,会使结合剂的
热膨胀系数增大,导致结合剂和磨粒之间不能有效地结合,即 降低了结合强度。
氧化锌:在高温条件下,ZnO和硼形成硼锌玻璃,添加适量的
∕℃
一组 二祖 三组
1-3 1-2 1-1
1-4 3-1
1-5 3-2
3-5 3-3 2-2 3-4 2-3
2-1 3-1 2-4 2-5
第一组石条烧成曲线 800 700 600 500 400 300 200 100 0 0 0.67 1.34 3.01 3.67 时间∕h 4.5 5.17 6.67 8.67
温度∕℃
石条烧成曲线
第二组石条烧成曲线 900 800 700 600 500 400 300 200 100 0 0 0.67 1.34 3.01 3.67 时间∕h
900 800 700 600 500 400 300 200 100 0 0 0.67 1.34 3.01 3.67 时间∕h 5.34 6.01 8.5 10.5
ቤተ መጻሕፍቲ ባይዱ
实验分析二分析添加剂对低温陶瓷结合剂抗折强度的影响
低温陶瓷结合剂抗折强度随添加剂加入量的变化 PbO 30 25 ZnO 硼酸
抗折强度(MPa)
20 15 10 5 0 1 2 3 编号 4 5
◆
氧化铅:适量的PbO的加入可以提高结合剂中玻璃相的含量,增强结
合剂对磨粒的把持力,从而达到增加强度的目的;过多时,液相量过多, 这就会使磨具在磨削高温的条件下发生变形、发泡等问题,而降低磨具的 强度。
ZnO,可增大陶瓷结合剂的碱用量,起到很好的助熔作用,可 促使液相产生,大幅度降低陶瓷结合剂的熔融温度,而且能够
改善对磨粒的润湿性,促使结合剂与磨粒有力的结合,从而提
高抗折强度。
实验结论
氧化铅的加入显著降低了结合剂得耐火度,适量的 氧化铅可以提高结合剂的抗折强度。 氧化锌的加入在一定程度上增加了结合剂的耐火度 且随着添加剂量的加入结合剂耐火度逐渐上升;加
耐火度∕℃
◆氧化铅:PbO作为助熔材料引入结合剂,PbO
本身的耐火度就较低,并且PbO和SiO2在较低的 温度下会生成固溶体,而这种固溶体的熔点更低 进一步起到助熔作用,因此, PbO的加入会显 著降低结合剂的耐火度。
硼酸:B2O3的熔点很低,为460℃,硼可以与陶瓷中的 SiO2形成熔点较低的玻璃体。但是有资料表明,结合剂中 B2O3含量的增加,结合剂的耐火度不会一直降低,反而有 可能升高,当含量低时,结合剂的耐火度也可能很低。在 基础结合剂中就有硼玻璃的加入,已提供一定量的B2O3, 所以对研究B2O3的加入对结合剂耐火度的影响,要综合考 虑各种因素的影响。 氧化锌:氧化锌的加入在一定程度上增加了结合剂的耐火 度但影响不大。
入氧化铅后抗折强度有一定的增加。
加入一定量硼酸可降低低温陶瓷结合剂的耐火度但 要注意考虑各种因素;适量的硼酸则提高结合剂的 抗折强度
实验过程四
计算添加剂各量的多少:
表一:结合剂中基础结合剂与添加剂的质量百 分数(%)
编号 基础结合 剂 100 0 氧化铅% 氧化锌% 硼酸%
1
0
0
2
3 4
100
100 100
3
6 9
3
6 9
3
6 9
5
100
12
12
12
实验过程五:耐火度的测定
耐火度测定升温曲线
升温曲线 900 800 700 600 500 400 300 200 100 0 0 0.56 1.56 2.56 3.56 时间∕h 4.67 5.67 7.34 9.34 ∕℃
近而改善低温陶瓷结合剂性能,提高磨具的强度韧
性、耐磨性。
实验过程 一 基础结合剂和添加剂的选定: 本实验使用以粘土-长石-硼玻璃系统 基础结合剂,选定的低温陶瓷结合剂:粘 土、长石、硼玻璃配比30:20:50 ,添加 剂选择三种分别为氧化铅、氧化锌、硼酸。 研究三种添加剂单次添加量分别为3℅6℅ 9℅ 12℅时对基础结合剂耐火度和结合剂