橡胶撕裂综述
橡胶材料的抗撕裂性能
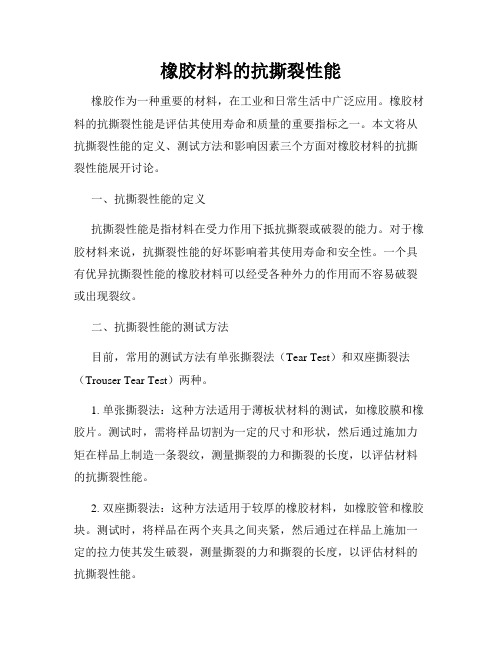
橡胶材料的抗撕裂性能橡胶作为一种重要的材料,在工业和日常生活中广泛应用。
橡胶材料的抗撕裂性能是评估其使用寿命和质量的重要指标之一。
本文将从抗撕裂性能的定义、测试方法和影响因素三个方面对橡胶材料的抗撕裂性能展开讨论。
一、抗撕裂性能的定义抗撕裂性能是指材料在受力作用下抵抗撕裂或破裂的能力。
对于橡胶材料来说,抗撕裂性能的好坏影响着其使用寿命和安全性。
一个具有优异抗撕裂性能的橡胶材料可以经受各种外力的作用而不容易破裂或出现裂纹。
二、抗撕裂性能的测试方法目前,常用的测试方法有单张撕裂法(Tear Test)和双座撕裂法(Trouser Tear Test)两种。
1. 单张撕裂法:这种方法适用于薄板状材料的测试,如橡胶膜和橡胶片。
测试时,需将样品切割为一定的尺寸和形状,然后通过施加力矩在样品上制造一条裂纹,测量撕裂的力和撕裂的长度,以评估材料的抗撕裂性能。
2. 双座撕裂法:这种方法适用于较厚的橡胶材料,如橡胶管和橡胶块。
测试时,将样品在两个夹具之间夹紧,然后通过在样品上施加一定的拉力使其发生破裂,测量撕裂的力和撕裂的长度,以评估材料的抗撕裂性能。
以上两种测试方法都能够准确评估橡胶材料的抗撕裂性能,选择合适的测试方法取决于材料的形状和厚度。
三、影响橡胶材料抗撕裂性能的因素橡胶材料的抗撕裂性能受多种因素的影响,在材料的选择和设计中需要考虑以下因素:1. 材料的硬度:硬度是指橡胶材料抵抗外力的能力。
一般来说,硬度较高的橡胶材料具有较好的抗撕裂性能。
2. 材料的弹性模量:弹性模量是指材料在弹性变形范围内的刚度。
弹性模量越高,橡胶材料的抗撕裂性能越好。
3. 添加剂的种类和用量:在橡胶材料的制备过程中,添加剂的种类和用量对其抗撕裂性能起着重要影响。
常用的添加剂有增塑剂、交联剂等,它们可以增加橡胶材料的柔软性和韧性,从而提高其抗撕裂性能。
4. 结构设计:在橡胶制品的设计中,合理的结构设计可以降低材料的受力程度,从而提高其抗撕裂性能。
橡胶的撕裂

橡胶的撕裂橡胶的撕裂是由于材料中的裂纹或裂口受力时迅速扩大开裂而导致破坏的现象。
橡胶的撕裂一般是沿着分子链数目最少,即阻力最小的途径发展。
因此,裂口的发展途径是选择内部结构较弱的路线进行的。
通过结构中的某些弱点间隙形成不规则的撕裂路线,从而促进了撕裂破坏。
撕裂强度的真正含义是撕裂能。
橡胶撕裂所需要的能量称为撕裂能,定义为每单位厚度的式样产生单位裂口所需要得到能量。
撕裂能包括材料表面能、塑性流动耗散的能量以及不可逆粘弹过程所耗散的能量。
所有这些能量的变化皆正比于裂口长度的增加,与试样形状无关。
应该指出的是,橡胶的撕裂强度与拉伸强度之间没有直接的关系。
例如,我们比较两种不同的橡胶,第一种拉伸强度高,扯断伸长率和粘弹损耗很低,第二种拉伸强度低,但扯断伸长率和粘弹损耗却很高。
比较这两种胶料可以发现,第二种橡胶有较高的撕裂强度。
所以拉伸强度低但粘弹损耗较大的胶料会有较高的撕裂强度。
(一)不同橡胶的撕裂强度常温下NR和CR的撕裂强度较高,这是由于产生诱导结晶后使应变能大大提高。
但CR在高温下的撕裂强度明显降低。
IIR的炭黑填充胶料,由于内耗较大也有较高的撕裂强度,特别是高温下撕裂强度较大。
(二)撕裂强度与硫化体系的关系1、多硫键具有较高的撕裂强度2、随交联密度增加,撕裂强度会有所下降(三)撕裂强度与填充体系的关系1、各种合成橡胶用炭黑补强时,撕裂强度明显改善。
随炭黑粒径减小,撕裂强度增加,在粒径相同的情况下,能赋予硫化胶高伸长率的炭黑,亦能提高撕裂强度。
2、使用各向同性的填料,如炭黑、白艳华、立德粉、氧化锌等,耐撕裂效果较好3、使用各向异性的填料,如陶土、碳酸镁等不会获得高的撕裂强度。
-。
橡胶生产工艺简介
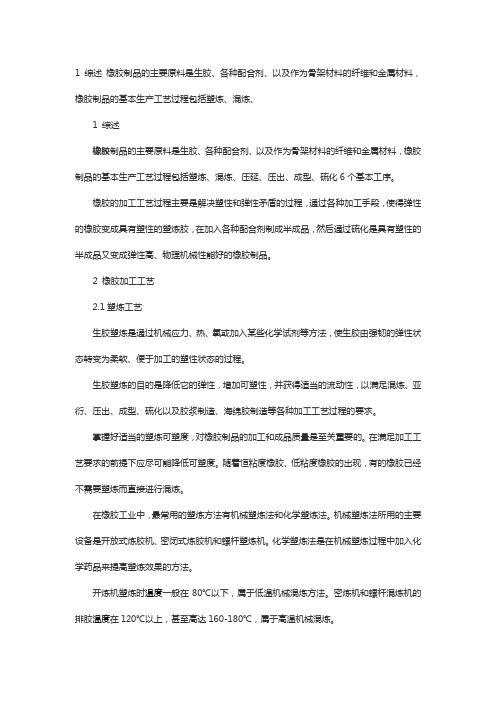
1 综述橡胶制品的主要原料是生胶、各种配合剂、以及作为骨架材料的纤维和金属材料,橡胶制品的基本生产工艺过程包括塑炼、混炼、1 综述橡胶制品的主要原料是生胶、各种配合剂、以及作为骨架材料的纤维和金属材料,橡胶制品的基本生产工艺过程包括塑炼、混炼、压延、压出、成型、硫化6个基本工序。
橡胶的加工工艺过程主要是解决塑性和弹性矛盾的过程,通过各种加工手段,使得弹性的橡胶变成具有塑性的塑炼胶,在加入各种配合剂制成半成品,然后通过硫化是具有塑性的半成品又变成弹性高、物理机械性能好的橡胶制品。
2 橡胶加工工艺2.1塑炼工艺生胶塑炼是通过机械应力、热、氧或加入某些化学试剂等方法,使生胶由强韧的弹性状态转变为柔软、便于加工的塑性状态的过程。
生胶塑炼的目的是降低它的弹性,增加可塑性,并获得适当的流动性,以满足混炼、亚衍、压出、成型、硫化以及胶浆制造、海绵胶制造等各种加工工艺过程的要求。
掌握好适当的塑炼可塑度,对橡胶制品的加工和成品质量是至关重要的。
在满足加工工艺要求的前提下应尽可能降低可塑度。
随着恒粘度橡胶、低粘度橡胶的出现,有的橡胶已经不需要塑炼而直接进行混炼。
在橡胶工业中,最常用的塑炼方法有机械塑炼法和化学塑炼法。
机械塑炼法所用的主要设备是开放式炼胶机、密闭式炼胶机和螺杆塑炼机。
化学塑炼法是在机械塑炼过程中加入化学药品来提高塑炼效果的方法。
开炼机塑炼时温度一般在80℃以下,属于低温机械混炼方法。
密炼机和螺杆混炼机的排胶温度在120℃以上,甚至高达160-180℃,属于高温机械混炼。
生胶在混炼之前需要预先经过烘胶、切胶、选胶和破胶等处理才能塑炼。
几种胶的塑炼特性:天然橡胶用开炼机塑炼时,辊筒温度为30-40℃,时间约为15-20min;采用密炼机塑炼当温度达到120℃以上时,时间约为3-5min。
丁苯橡胶的门尼粘度多在35-60之间,因此,丁苯橡胶也可不用塑炼,但是经过塑炼后可以提高配合机的分散性顺丁橡胶具有冷流性,缺乏塑炼效果。
橡胶疲劳断裂形态

橡胶疲劳断裂形态橡胶是一种具有优异机械性能和耐磨耐腐蚀特性的弹性材料,广泛应用于各个领域。
然而,在长期使用过程中,橡胶材料可能会出现疲劳断裂现象。
疲劳断裂是指材料在受到重复加载作用下,由于应力集中和损伤累积,最终导致断裂失效。
橡胶疲劳断裂形态多种多样,常见的有裂纹扩展型、剪切型和磨损型。
下面将详细介绍这些形态。
裂纹扩展型是指在橡胶材料中出现裂纹,并随着加载次数的增加逐渐扩展。
这种疲劳断裂形态常见于高应力和高应变下的橡胶材料,如橡胶密封件和橡胶弹簧等。
裂纹扩展型的疲劳断裂通常呈现出断裂口较为平整和光滑的特点,裂纹呈尖锐形状,断裂面较为干净。
裂纹扩展型的疲劳断裂是由于材料内部的微观缺陷和损伤导致的,随着裂纹的扩展,材料的强度逐渐降低,最终导致断裂失效。
剪切型是指在橡胶材料中出现剪切变形,并伴随着裂纹的形成和扩展。
剪切型的疲劳断裂常见于橡胶材料在剪切应力作用下的情况,如橡胶管道和橡胶密封圈等。
剪切型疲劳断裂通常表现为断裂面上有明显的剪切纹路,呈现出类似撕裂的特征。
剪切型疲劳断裂的形成是由于橡胶材料在受到剪切应力作用下,发生内部断裂和相对滑移,造成裂纹的形成和扩展。
磨损型是指橡胶材料在长期使用过程中,由于摩擦和磨损作用,最终导致断裂失效。
磨损型的疲劳断裂常见于橡胶轮胎和橡胶密封件等应用场景。
磨损型疲劳断裂通常表现为断裂面上有明显的磨损痕迹和划痕,呈现出类似磨损的特征。
磨损型疲劳断裂的形成是由于橡胶材料在受到摩擦和磨损作用下,表面逐渐磨损,最终导致断裂失效。
总结起来,橡胶疲劳断裂形态包括裂纹扩展型、剪切型和磨损型。
裂纹扩展型的疲劳断裂主要是由于材料内部的微观缺陷和损伤导致的,呈现出断裂口平整光滑的特点。
剪切型的疲劳断裂主要是由于橡胶材料在受到剪切应力作用下发生内部断裂和相对滑移,呈现出撕裂的特征。
磨损型的疲劳断裂主要是由于橡胶材料在长期使用过程中受到摩擦和磨损作用,表面逐渐磨损,呈现出磨损的特征。
了解橡胶疲劳断裂形态对于预防和控制疲劳断裂失效具有重要意义。
橡胶材料的抗撕裂性能测试方法
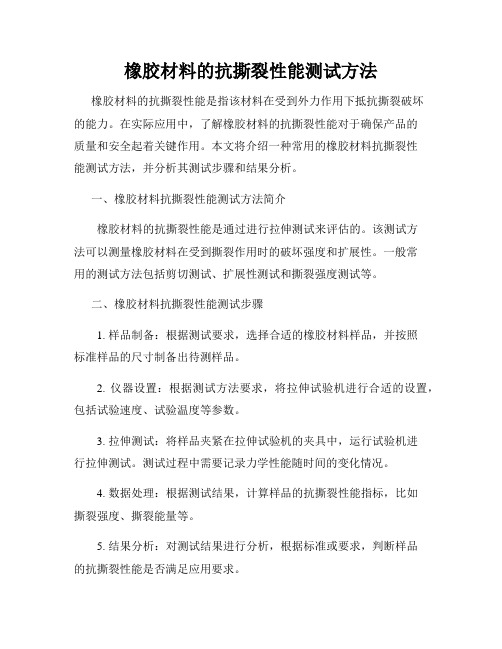
橡胶材料的抗撕裂性能测试方法橡胶材料的抗撕裂性能是指该材料在受到外力作用下抵抗撕裂破坏的能力。
在实际应用中,了解橡胶材料的抗撕裂性能对于确保产品的质量和安全起着关键作用。
本文将介绍一种常用的橡胶材料抗撕裂性能测试方法,并分析其测试步骤和结果分析。
一、橡胶材料抗撕裂性能测试方法简介橡胶材料的抗撕裂性能是通过进行拉伸测试来评估的。
该测试方法可以测量橡胶材料在受到撕裂作用时的破坏强度和扩展性。
一般常用的测试方法包括剪切测试、扩展性测试和撕裂强度测试等。
二、橡胶材料抗撕裂性能测试步骤1. 样品制备:根据测试要求,选择合适的橡胶材料样品,并按照标准样品的尺寸制备出待测样品。
2. 仪器设置:根据测试方法要求,将拉伸试验机进行合适的设置,包括试验速度、试验温度等参数。
3. 拉伸测试:将样品夹紧在拉伸试验机的夹具中,运行试验机进行拉伸测试。
测试过程中需要记录力学性能随时间的变化情况。
4. 数据处理:根据测试结果,计算样品的抗撕裂性能指标,比如撕裂强度、撕裂能量等。
5. 结果分析:对测试结果进行分析,根据标准或要求,判断样品的抗撕裂性能是否满足应用要求。
三、橡胶材料抗撕裂性能测试结果分析根据橡胶材料的抗撕裂性能测试结果,可以得出以下几个方面的分析:1. 撕裂强度:撕裂强度是指橡胶材料在受到撕裂作用时所承受的最大应力。
撕裂强度越高,表示材料的抗撕裂性能越好。
2. 撕裂能量:撕裂能量是指橡胶材料在受到撕裂作用时所吸收的能量。
撕裂能量越大,表示材料具有更好的抵抗撕裂破坏的能力。
3. 撕裂韧性:撕裂韧性是指材料在受到撕裂作用时的抗裂纹扩展能力。
撕裂韧性越高,表示材料在撕裂时具有更强的韧性和延展性。
4. 撕裂模式:根据撕裂测试结果,可以观察和分析材料的撕裂模式,如纵向撕裂、横向撕裂等。
这能够帮助我们进一步了解材料的性能和破坏机制。
四、橡胶材料抗撕裂性能测试的意义橡胶材料的抗撕裂性能是产品使用寿命和安全性的重要指标之一。
通过进行抗撕裂性能测试,可以评估材料的耐用性和抗破坏性能,进而选取更合适的材料用于产品制造。
乙丙橡胶撕裂强度
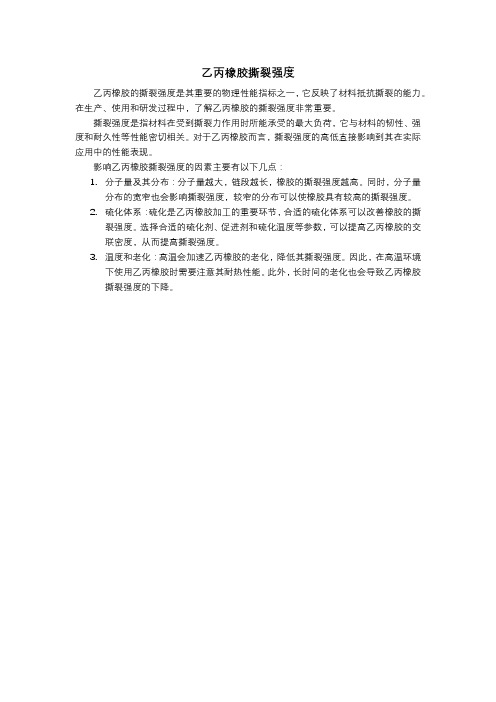
乙丙橡胶撕裂强度
乙丙橡胶的撕裂强度是其重要的物理性能指标之一,它反映了材料抵抗撕裂的能力。
在生产、使用和研发过程中,了解乙丙橡胶的撕裂强度非常重要。
撕裂强度是指材料在受到撕裂力作用时所能承受的最大负荷,它与材料的韧性、强度和耐久性等性能密切相关。
对于乙丙橡胶而言,撕裂强度的高低直接影响到其在实际应用中的性能表现。
影响乙丙橡胶撕裂强度的因素主要有以下几点:
1.分子量及其分布:分子量越大,链段越长,橡胶的撕裂强度越高。
同时,分子量
分布的宽窄也会影响撕裂强度,较窄的分布可以使橡胶具有较高的撕裂强度。
2.硫化体系:硫化是乙丙橡胶加工的重要环节,合适的硫化体系可以改善橡胶的撕
裂强度。
选择合适的硫化剂、促进剂和硫化温度等参数,可以提高乙丙橡胶的交
联密度,从而提高撕裂强度。
3.温度和老化:高温会加速乙丙橡胶的老化,降低其撕裂强度。
因此,在高温环境
下使用乙丙橡胶时需要注意其耐热性能。
此外,长时间的老化也会导致乙丙橡胶
撕裂强度的下降。
抗撕裂橡胶实验报告(3篇)

第1篇一、实验目的本次实验旨在研究抗撕裂橡胶的性能,了解其制备方法、材料选择以及性能特点。
通过对比不同配方和工艺条件下的抗撕裂橡胶性能,为实际应用提供理论依据。
二、实验材料与设备1. 实验材料:- 天然橡胶(NR)- 硫磺- 促进剂- 抗撕裂剂- 填料- 油脂- 混炼设备- 硫化设备- 拉伸试验机- 撕裂试验机2. 实验设备:- 密炼机- 开炼机- 模压机- 真空干燥箱- 拉伸试验机- 撕裂试验机三、实验方法1. 混炼:将天然橡胶、硫磺、促进剂、抗撕裂剂、填料、油脂等原料按一定比例投入密炼机中,在密炼机中混炼至均匀。
2. 硫化:将混炼好的胶料放入模具中,进行硫化处理。
3. 制样:将硫化后的胶料切割成标准试样。
4. 性能测试:- 抗撕裂性能:采用撕裂试验机测试试样的抗撕裂性能,记录撕裂强度和撕裂伸长率。
- 抗拉性能:采用拉伸试验机测试试样的抗拉性能,记录拉伸强度和断裂伸长率。
四、实验结果与分析1. 抗撕裂性能:- 不同抗撕裂剂用量对橡胶抗撕裂性能的影响:实验结果表明,随着抗撕裂剂用量的增加,橡胶的抗撕裂性能逐渐提高。
当抗撕裂剂用量达到一定值后,抗撕裂性能趋于稳定。
- 不同硫化时间对橡胶抗撕裂性能的影响:实验结果表明,随着硫化时间的延长,橡胶的抗撕裂性能逐渐提高。
但当硫化时间过长时,抗撕裂性能反而下降。
- 不同硫化温度对橡胶抗撕裂性能的影响:实验结果表明,在一定温度范围内,随着硫化温度的升高,橡胶的抗撕裂性能逐渐提高。
但当温度过高时,抗撕裂性能反而下降。
2. 抗拉性能:- 不同抗撕裂剂用量对橡胶抗拉性能的影响:实验结果表明,随着抗撕裂剂用量的增加,橡胶的抗拉性能逐渐提高。
但当抗撕裂剂用量过多时,抗拉性能反而下降。
- 不同硫化时间对橡胶抗拉性能的影响:实验结果表明,随着硫化时间的延长,橡胶的抗拉性能逐渐提高。
但当硫化时间过长时,抗拉性能反而下降。
- 不同硫化温度对橡胶抗拉性能的影响:实验结果表明,在一定温度范围内,随着硫化温度的升高,橡胶的抗拉性能逐渐提高。
各种橡胶的抗撕裂强度

各种橡胶的抗撕裂强度
橡胶是一种常见的弹性材料,具有良好的抗撕裂强度。
不同类
型的橡胶具有不同的抗撕裂强度,下面我将从不同角度来回答你的
问题。
首先,橡胶的抗撕裂强度与其材料的特性有关。
例如,天然橡
胶由橡胶树中提取,具有较高的弹性和抗撕裂强度。
合成橡胶通常
由石油化工产品制成,其抗撕裂强度取决于具体的合成方法和原材料。
其次,橡胶的抗撕裂强度也受到其结构和添加剂的影响。
例如,硫化橡胶通过硫化处理可以提高其抗撕裂强度。
此外,添加填料和
增强剂(如碳黑、纤维等)也可以改善橡胶的抗撕裂性能。
另外,不同用途的橡胶制品具有不同的抗撕裂强度要求。
例如,汽车轮胎需要具有较高的抗撕裂强度以应对复杂的路面和载重要求,而橡胶密封垫则需要具有良好的抗撕裂性能以确保密封效果。
此外,橡胶制品的抗撕裂强度还受到温度、湿度、紫外线等环
境因素的影响。
在不同的工作环境中,橡胶制品的抗撕裂强度表现
也会有所不同。
总的来说,橡胶的抗撕裂强度是一个综合性能指标,受到多种因素的影响。
针对不同的需求和环境,可以选择合适的橡胶材料和加工工艺来满足其抗撕裂强度的要求。
- 1、下载文档前请自行甄别文档内容的完整性,平台不提供额外的编辑、内容补充、找答案等附加服务。
- 2、"仅部分预览"的文档,不可在线预览部分如存在完整性等问题,可反馈申请退款(可完整预览的文档不适用该条件!)。
- 3、如文档侵犯您的权益,请联系客服反馈,我们会尽快为您处理(人工客服工作时间:9:00-18:30)。
定量关系式: Gc=Ub*d
说明:
1、Thomas提出定量关系式,Gc与裂纹的尖锐度有关。 2、试验证明Ub几乎不受外界影响,Gc在一定范围内,也 可视为常数。 3、关系式说明裂纹生长过程实质是裂纹变钝过程。
能量密度Ub一般可视为常数, 不受外界条件影响。
d--裂纹尖端直径,表征裂纹锐度
撕裂机理
局部单元撕裂其本质为线弹性断裂力学现象
Griffith理论
能量平衡理论 拉伸储存的弹性应变能释放
Irwin理论
应力强度理论 材料所受应力
产生新裂纹表面所需消耗的能量
材料承受应力
释放形变能,撕裂引发 储存形变能,累计至撕裂引发能
受力,发生弹性变形
撕裂引发
撕裂
撕裂生长 撕裂引发后 受力,弹性形变 储存形变能,累计至撕裂生长能 释放形变能,裂纹生长
撕裂机理
弹性体疲劳失效现象
弹性体材料受力一定程度后,弹性失效而材料遭到破坏。 Lake和Lindley对此现象做出以下解释:(能量方面) 弹性体撕裂生长过程中,弹性体材料具有一个最小撕裂能T0,低于T0,材 料不会发生撕裂。弹性体撕裂包括下列3个阶段:
1
2
3
T0
材料发生形变, 储存形变能至 T0,此时能量 得以释放,裂 纹增长且表面
多用Ring II of DIN53504,两切口对立分布 在内部边缘。测试时不旋转。
Goodrich-Winkelmann
撕裂的分类
(2)、按撕裂方式的不同可以分为: I 直接撕裂 II垂直撕裂
III成角度撕裂(取决于合应力)
撕裂的分类
(3)按撕裂后的形状分
a
b
cknotty撕裂sawtoth撕裂DIN53507
Semperit-Probe
a类试样:(沿切口方向进行撕裂,外力作用于部分试样)
规格类型
撕裂方式
备注说明
使用早于DIN53507,试样 便于狭口设备夹持。
切口在条形试样前部中心, 撕裂时垂直切口90°撕裂。
区别于DIN53507,主要用 于硫化后试样检测。
Trousers-Probe (裤型试样)
厚度较薄2mm,切口垂直于长度方向,由 薄刀片裁制而成。
剪切试样 (Shear testpiece)
试样较宽,狭口宽度上夹持撕裂,适用于 撕裂能的测试。
代尔夫特试样 (Delft testpiece)
直角撕裂试样 (Angle testpiece)
新月形撕裂试样 (Crescent testpiece)
核心:材料承受不了此方向应力,则该位置上结构遭破坏被撕裂。
❖ 瑕疵累积说:
C.M.Roland等人认为当材料被拉伸后,会存在很多微观裂纹(或材 料本身存在)。而裂纹的生长是由许多微观裂纹衍生出来的,并不是所加 应力直接作用的结果。
微观裂纹
宏观裂纹
撕裂路线杂乱无规
另外,可反映出材料本身瑕疵(裂纹尖端周围环境)是影响撕裂强度之一。 反映出撕裂的复杂性。
撕裂的分类
(1)按照撕裂生长决定因素分类:
a.由外界施加的拉伸或撕裂速度决定裂纹的生长速度的撕裂---撕裂 降低内应力,使内外应力趋于平衡。
b.裂纹在受力下,自发进行生长的撕裂---结构中应力达到某承受临 界点自发断裂生长。按此方法,撕裂试样分为以下两类:
撕裂的分类
试样名称 Fan testpiece (扇形试样)
生长。之后应力迅速降低,撕裂停止。 此时裂纹尖端应力也得到释放,应力
当材料再次被拉伸,材料再次取向, 降低,撕裂停止。再次被拉伸时,再
上述撕裂过程重复进行。从而获得上 次一定程度取向,上述撕裂过程再次
述Knotty撕裂。
重复进行,从而获得saw-tooth撕裂。
平滑撕裂
当外界拉伸速度较快时,材 料来不及取向,整个撕裂过 程的完成就在同一个力下完 成。 拉伸试样的两狭口距离非常 近的时候会出现的一种撕裂; 裤型撕裂等经常出现。
Marzetti (马泽蒂试样)
Greensmith、Thomas试验 用试验,厚度仅1
撕裂的分类
试样名称
Fan testpiece (扇形试样)
a类试样:(沿切口方向进行撕裂,外力作用于部分试样)
规格类型
撕裂方式
备注说明
使用早于DIN53507,试样 便于狭口设备夹持。
DIN53507
切口在条形试样前部中心, 撕裂时垂直切口90°撕裂。
Semperit-Probe
区别于DIN53507,主要用 于硫化后试样检测。
Trousers-Probe (裤型试样)
Marzetti (马泽蒂试样)
Greensmith、Thomas试验 用试验,厚度仅1
撕裂的分类 b类试样:(切口与拉伸方向垂直,外部应力作用于整个试样)
名称
试样规格
备注说明
条形试样 (strip testpiece)
形成主要是低拉伸速度下,分子链发 拉伸速度升至一定后,分子链取向、
生充分取向,在拉伸方向的抗撕裂能 不充分,则撕裂生长所需要的力也有
力增强(需获得更大的力进行撕裂生 一定程度的增加。裂纹在微撕裂后,
长),裂纹在微撕裂后,撕裂生长发 撕裂生长发生一定程度的偏转(30°-
生大偏移,沿着分子链方向进行裂纹 50°),沿分子链方向进行裂纹生长。
粗糙
T
持续周期进 行,裂纹逐渐
增大
Tc
裂纹切口足够 大,形变能达 到Tc.裂纹生长 既快且光滑。
撕裂机理
❖ 现象:撕裂路线杂乱无章 ❖ Irwin理论解释撕裂过程:
当弹性体材料受力后,在材料结构中产生应力,若在该应力方向上,所 受力结构承受不了此应力(高于该结构所能承受的最大应力),则发生撕 裂破坏。内部结构的复杂性与内部应力分布的共同作用,最终导致无规则 的撕裂路线。
橡胶撕裂综述
大冢材料科技(上海)有限公司 青岛创智恒业新材料有限公司
内容
➢橡胶撕裂定义 ➢撕裂机理 ➢撕裂的分类 ➢影响撕裂因素 ➢常见橡胶的撕裂 ➢提高撕裂的配合方法 ➢相关技术发展
橡胶撕裂定义
撕裂:是橡胶等弹性体材料中的裂纹,由于受力而
导致裂纹扩大的现象。过程中会伴有大的弹性形变。
撕裂强度:表征材料抵抗撕裂的能力,用撕
环形撕裂试样 Ring testpiece of Pohle
Nijveld发明使用,切口在试样中部,垂直 于试样长轴。
目前试验室使用较多,其凹处为直角,有 有切口和无切口之分。(ASTM D 624 Method C)
直角撕裂的普及,涵盖较多撕裂情况,切 口在凹处中心内边缘。(ASTM D 624 Method B有介绍)