生产计划与物料控制(PMC)分解
华为pmc生产计划与物料控制
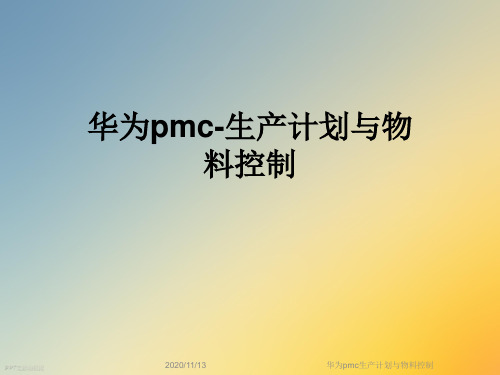
百分比 準直接工時
冲床 1000
80%
90%
720
❖ 機器生產有機器檢修、保養、调较、待料等時間,實際 的工作時間達不到計划時間,且生產的產品有不良品,因 此有效產量標準直接工時為 1000 × 80% ×90% = 720 工 時
华为pmc生产计划与物料控制
•一:产能负荷分析
•產量規划 5。人力負荷
•(2)生产计划的实质
•满足客户 的三要素
•生产计划
•满足生产的 三要素
PPT文档演模板
•品质
•成本
•交货 期 •人员
•设备 •材料
华为pmc生产计划与物料控制
•2。生产计划应满足的条件
1. 计划应是综合考虑各有关因素的结果。 2. 必须是有能力基础的生产计划 3. 计划的粗细必须符合活动的内容 4. 计划的下达必须在必要的时机
影响。 ❖ 仓储部门只停留在操作层面上,缺乏服务与主动沟通信息的意识。 ❖ 。。。。。。
PPT文档演模板
华为pmc生产计划与物料控制
•6.生产计划与物料控制(PMC)组织机构设置与职责划 分
•图一: •请分析它们各自的优点和缺点 •总经理
•采购部 经理
•物流部 经理
•质保部 经理
•制造部 经理
•市场部 经理
•于是,你必须用主导性--跨越自己的环节,了解掌握工作 链条上除你所在位置以外的任何环节,才有可能让一件事顺利 通过所有的环节而圆满完成。
PPT文档演模板
华为pmc生产计划与物料控制
•PMC人员如何跨部门开展工作?
•主导性的你
•非主导性的你
PPT文档演模板
•心中不妨把那些环节涉 及 ••仔到的人你看不成做是我自做己的马
PMC生产计划和物料控制

协
(如通用原则物料)允许库存旳最高存量。
同
共
最高存量=一种生产周期旳天数每天使用量+安
进
全存量
三、材料计划与存量管制
安全存量VS最高存量VS最低存量
凝
聚
最低存量
真
知
,
最低存量是指生产淡季固定时期内,能确保配合
协
生产所需旳物料库存数量旳最低界线。
同
共
最低存量=购备时间每天使用量+安全存量
凝
A类物资 品种少,占用资金多,是管理旳要点,必须计算每种
聚
真
物资旳订货量,尽快缩短供给间隔期。选择最优旳订购批量,
知
力求收库存压缩到最低楼上水平
,
协
C类物资 品种繁多,占用资金小,能够适应集中大量订货,以
同 共
简化订购工作,节省订购费用;统计、检验定额控物也却能够
进
采用A类为粗略旳方式。力求简便宜行。以提升管理效率。
各分类必须相斥, 各分类必须涉及分 全部分类之基准,
真
凡能归类者仅能归 类之一切物料,物 必须符合逻辑之基
知 , 协 同
入该类,绝无归入 他类可能,故互斥 之目旳在于互斥之
不能归入某一类者, 本原则 定可归入另一类, 故周延旳目旳为不
共
目旳在于不致于发 致漏掉。
进
生发生反复。
二、物料工程管理
物料分类/编号
知
号时,必要时 符号或数字, 择易记性之文
,
应考虑须能配 必须有足够之 字、符号或数
协
合制成机械。 数量,能够代 字,并应有暗
同
以免将来重编 表全部个别物 示性及联想性,
共
料,以应付将 以便记忆
pmc生产计划与物料控制

pmc生产计划与物料控制PMC生产计划与物料控制生产计划与物料控制(Production Planning and Material Control,简称PMC)是现代企业生产管理的重要手段和方法之一,它通过有效的计划与物料控制,帮助企业合理组织生产过程,最大化地发挥生产设备的效益,提高生产效率和制造质量,从而实现企业的利润最大化。
一、生产计划生产计划是PMC的核心组成部分,它直接影响到生产的进度和质量。
生产计划是指在一定时间内,根据生产目标和生产能力,合理安排生产任务的计划,包括生产数量、生产时间、生产方式及物料需求等内容。
生产计划的编制应按照以下步骤进行:1、生产目标的确定生产目标要与市场需求紧密结合,根据市场需求合理分配生产计划中各个品种的产量。
2、产能分析通过对生产资源的分析和评估,考虑设备的使用率、工艺流程、作业时间等因素,确定生产能力。
3、计划制定结合生产目标和产能分析,确定生产计划中的各项详细内容。
包括指定生产时间、安排生产方式、制定物料需求计划、确定生产过程控制计划等。
4、计划调整随着市场需求的变化,生产计划也要不断调整。
调整生产计划时必须考虑到生产效益、企业形象和市场需求等的影响。
二、物料控制物料控制是很重要的一环,它对于确保生产计划的顺畅实施有着至关重要的作用。
物料控制的主要任务是根据生产计划,精确地控制和管理各物料在生产过程中的流动和使用,以确保生产过程的顺利进行,从而保障生产的正常运作。
物料控制主要包括以下内容:1、物料需求计划(MRP)物料需求计划是根据生产计划,制定每个物料的采购计划和生产计划,保证这些物料在所需时间内到达工厂,并保持合理的库存水平。
2、进料检验通过对进厂物料的检验,可以确保物料的质量符合要求。
检验的结果可以对进料的订货单位进行评估和管理,从而使订货单位更加重视物料的质量和供货能力。
3、仓库管理仓库管理包括物料的分类、盘点、入库、出库、移库、报废等工作,它直接影响到生产计划和物料管理的效率和质量。
pmc生产计划与物料控制心得

pmc生产计划与物料控制心得一、引言PMC(Production Material Control)是生产物料控制的缩写,是指在生产过程中对物料的计划、采购、储存、发放和使用进行管理和控制。
PMC是企业生产管理的重要环节,对于提高企业生产效率和降低成本具有重要作用。
二、PMC生产计划1. 生产计划编制生产计划编制是PMC工作的核心环节。
在编制生产计划时,需要根据销售订单、库存情况以及预测需求等因素进行综合考虑,确定每个月或每个季度的生产任务量。
2. 物料需求计划在确定了生产任务量后,需要进一步进行物料需求计划。
物料需求计划是指根据产品BOM(Bill of Materials)表格中所列出的原材料清单以及产品数量,计算出每种原材料的需求量,并将其转化为采购订单或者领用单。
3. 生产排程在完成了物料需求计划后,需要对各项工序进行排程。
通过排程可以确定每个工序开始和结束时间,并且可以避免资源冲突和延误等问题。
4. 生产进度跟踪在完成了排程后,需要对生产进度进行跟踪。
通过跟踪可以及时发现生产过程中的问题,并且可以及时采取措施进行调整,以保证生产计划的顺利实施。
三、物料控制心得1. 物料管理物料管理是PMC工作的重要环节。
在进行物料管理时,需要对各项物料进行分类、编码,并且建立完善的库存管理系统,以保证物料的准确性和及时性。
2. 物料采购在进行物料采购时,需要根据生产计划和物料需求计划确定采购数量和时间,并且需要与供应商建立长期合作关系,以保证原材料的质量和供货稳定性。
3. 物料储存在进行物料储存时,需要根据不同种类的物料进行分类储存,并且需要定期检查库存情况,以及对过期或者损坏的物品进行处理。
4. 物料发放在进行物料发放时,需要根据生产计划和工序要求进行发放,并且需要对发放情况进行记录和统计。
四、总结PMC是企业生产管理中非常重要的一个环节。
通过合理编制生产计划、精细实行物料控制等方式可以提高企业生产效率和降低成本。
PMC生产计划管理与物料控制文件

PMC生产计划管理与物料控制文件1. 简介生产计划管理与物料控制(PMC)是企业生产过程中非常重要的环节,其涉及到生产计划的制定、生产进度的管理以及物料的采购和库存控制等内容。
本文档将重点介绍PMC的相关内容,包括生产计划管理、物料控制、供应链管理等方面。
2. PMC的意义PMC的主要目的是实现生产计划的合理安排,确保生产工艺的顺利进行,提高生产效率,降低生产成本,并最终提升企业的竞争力。
通过PMC的有效管理,可以确保产品按时交付,库存水平得到控制,从而提高企业的盈利能力。
3. 生产计划管理3.1 制定生产计划制定生产计划是PMC的第一步,需要根据市场需求、生产能力等因素制定合理的生产计划。
生产计划可以分为长期计划、中期计划和短期计划,其中长期计划通常涉及到生产线的规划和设备的投资等,中期计划则更加具体,包括产品的具体数量、交付时间等,而短期计划则是根据实际情况进行调整。
3.2 生产进度管理生产进度管理是保证生产计划顺利执行的关键环节,需要不断监控生产进度并进行调整。
通过及时了解生产状况,可以确保生产按计划进行,避免延误和浪费。
4. 物料控制4.1 物料采购物料采购是PMC中非常关键的一环,需要合理安排采购计划,确保原材料的供应充足并控制采购成本。
供应商的选择和管理也是物料控制的重要方面,需要与供应商建立长期合作关系,确保物料的质量和交付准时。
4.2 库存管理库存管理是物料控制的另一个重要环节,需要通过合理的库存控制方法来平衡库存成本和服务水平。
库存水平的高低直接影响到生产计划的执行,需要根据需求和供应情况进行动态调整。
5. 供应链管理供应链管理贯穿于PMC的始终,它涉及到供应商、生产厂家、物流公司等多个环节的协同工作。
通过供应链管理,可以实现优化物流、降低库存、缩短交付周期等目标,从而提高企业的整体竞争力。
6. 结语PMC生产计划管理与物料控制文件对于企业的生产运营至关重要,通过科学合理的PMC管理,可以提高企业的生产效率,降低生产成本,增强市场竞争力。
pmc生产计划与物料控制

pmc生产计划与物料控制PMC生产计划与物料控制是企业生产管理中至关重要的环节。
它涉及到对生产计划的制定和调整,以及对物料的采购、管理和控制等方面的工作。
本文将从PMC生产计划和物料控制两个方面进行详细介绍。
一、PMC生产计划1.1 生产计划的概念生产计划是企业根据市场需求和资源情况,合理安排和调度生产活动的工作。
它涉及到生产量、生产时间、生产顺序等方面的决策,是企业实现生产目标的重要手段。
1.2 生产计划的编制流程生产计划的编制一般包括以下几个环节:明确生产目标和任务、制定生产计划方案、安排生产资源、编制生产计划和下达任务单、调整和监控生产计划。
1.3 生产计划的内容和要求生产计划的内容包括产品的生产数量、生产时间、生产顺序以及所需的资源和工艺等。
生产计划要求合理、稳定和可操作,确保生产活动的高效运行。
二、物料控制2.1 物料控制的概念物料控制是指对企业物料采购、存储和使用过程进行有效管理和控制的工作。
它涉及到物料需求的确定、采购计划的制定、库存管理和物料使用的控制等方面。
2.2 物料控制的方法和手段物料控制的方法和手段主要包括物料需求计划、物料采购控制、库存管理和物料使用控制等。
通过科学合理的控制手段,确保物料的供应和使用的平衡,防止过剩和缺货等问题的发生。
2.3 物料控制的目标和要求物料控制的目标是实现物料的合理需求和有效供应,确保生产活动的顺利进行。
物料控制要求准确性、及时性和稳定性,提高企业的生产效率和经济效益。
三、PMC生产计划与物料控制的关系3.1 生产计划与物料控制的联系生产计划与物料控制是密切相关的两个环节。
合理的生产计划需要基于准确的物料需求计划,而物料控制的有效性也依赖于生产计划的准确性和稳定性。
3.2 生产计划与物料控制的整合生产计划与物料控制应当进行有效整合,形成一个有机的管理体系。
通过信息化技术的支持,实现生产计划和物料控制的高效协同,提升企业生产管理的水平。
四、总结PMC生产计划与物料控制是企业生产管理中的关键环节。
pmc生产计划与物料控制
pmc生产计划与物料控制PMC生产计划与物料控制。
随着市场需求的不断增长,企业在生产过程中需要更加精细化地进行计划和控制,以确保生产效率和产品质量。
PMC(Production Management and Control)生产计划与物料控制就成为了企业生产管理中至关重要的一环。
本文将从PMC生产计划和物料控制的概念、重要性、实施步骤等方面展开阐述,希望能为相关企业提供一些参考和帮助。
首先,我们来了解一下PMC生产计划和物料控制的概念。
PMC生产计划是指根据市场需求和企业生产能力,制定合理的生产计划,包括生产数量、生产周期、生产进度等内容,以确保生产活动有序进行。
而物料控制则是指对生产过程中所需的各种物料进行合理的控制和管理,包括物料的采购、储存、使用等环节,以确保物料的供应和使用符合生产需求。
其次,我们来谈一谈PMC生产计划与物料控制的重要性。
首先,通过合理的生产计划,企业可以有效地调配资源,避免生产过剩或者生产不足的情况发生,从而提高生产效率,降低生产成本。
其次,物料控制可以确保生产过程中所需的物料供应充足,避免因为物料短缺而导致生产中断或者延误,从而保证生产进度和产品质量。
因此,PMC生产计划与物料控制对于企业的生产经营至关重要。
接下来,我们来谈一谈PMC生产计划与物料控制的实施步骤。
首先,企业需要收集市场需求和销售预测数据,结合生产能力和资源情况,制定合理的生产计划。
其次,对所需的各种物料进行清单和需求量的分析,制定物料采购计划,并建立物料供应商的合作关系。
然后,对物料的采购、储存和使用进行严格的控制和管理,确保物料的质量和供应。
最后,对生产过程进行监控和调整,及时发现和解决生产中出现的问题,确保生产计划的顺利实施。
综上所述,PMC生产计划与物料控制对于企业的生产管理至关重要。
通过合理的生产计划和物料控制,企业可以提高生产效率,降低生产成本,确保产品质量,从而在激烈的市场竞争中立于不败之地。
PMC生产计划与物料控制ppt课件
制定库存计划必须要有信息。因而,销售部门必须就产品类别对各种产品的 销路作预测。说起产品类别,因现在是多品种时代,品种数量之多,令人惊讶。不 过,按产品类别的销售预测是库存管理的开端,因此,即使麻烦也不能马虎。
通常,预测是在月初或每旬,以按一定周期的循环方式进行的。预测面临的 首要题目是预测期间,既要解决预测的提前量。作为结论,它应该是产品的最长工 作日程加上预测周期后的天数。例如,最长工作日程是3个月,预测周期1个月,预 测期间就是4个月。
过程流程图
①不同零部件的加工顺序; ②标准时间 ③标准批量; ④工作日程
零件明细
12 2024/2/10
2.2 计划的形态——日程计划
X工序 基准日程5天
连续型的工作日程
Y工序
Z工序
基准日程8天
基准日程9天
Y工序的开工工作日程17天
加工零部件索要的总工作日程22天
并行型的工作日程
2024/2/10
外加工品日程计划的制订 方法,同工厂内工序的日程计 划完全相同。基准日程也与工 厂内工序一样。
①铸造工序
10月2日
外加工订货的日程计划
②车床工序
10月4日
交货期10月10日
③外加工工序
10月6日
④完成 工序
10月9日
天
1
若有外加工品所需要的标 准时间资料,那么也能制定与 其关联的复合计划。
有关外加工品的开工日与 完工日的日程计划,图中使用 的是倒计时的方式,具有连续
2024/2/10
从大日程计划到中日程计划
6月
7月
123
29 30 1 2 3
日日日
日 日 日日日
PMC是什么
工作内容
1、销售计划 2、客户关系管理 3、发货单管理 4、INVOICE管理
Earning
220 200 180 160 140 120 100 80 60 40 20 0
Cost
90% 80% 70% 60% 50% 40% 30% 20% 10% 0%
5月
6月
7月
8月
9月
10月
11月
12月
物料管理与库存控制
1.物料管理精髓、职责及运作 2.物料需求计划 常备性物料计划制定 专用性物料计划制定
3.供应商交货跟催与控制
如何实施采购商务功能与物流控制 功能分离 如何建立新型的供应商供合作伙 伴关系与实施新型的供货方式 采购框架协议、订单、跟催、看 板拉动之间的关系
4.库存量预测
生产计划控制
1、生产与销售业务链接——如何找到有效的
产销链接方式 2、生产计划——制定生产计划的内涵、条件 及标准 3、生产计划制定技巧 4、生产异常对策 5、生产业绩评价——分析指标及绩效改进
PMC的主要内容
5、部门员工考核表 6、本月生产计划与材料计划分析表 7、异常成本分析表 8、上级安排其他的事项
“PMC经理” 的“岗位职 责”
所属部门:计划物控部。 直接上级:总经理 直接下级:
计划专员、物控成本专员、仓库主 管、跟单员职务性质管理人员。
销售订单及变更的评审; 2. 生产订单的审查,产销评估和协调; 3. 负责《生产月计划》、《生产周计 划》、《请购单》、《退/补料单》、 《报废单》、《补货单》、《外协加 工单》和生产部月产量的审查;
Output 工作输出
1、部门运作流程 2、工作规范和流程 3、资源管理 4、培训相关记录 5、业绩报告 1、供应商资料管理 2、报价单 3,供应商月度纳期遵守率 4、物料跟进表 5、INVOICE 核实 6、供应商月度/年度KPI 1、生产计划/工单 2、安全库存 3、MRP II维护 4、计划达成率
pmc生产计划与物料控制
pmc生产计划与物料控制PMC生产计划与物料控制随着现代企业生产规模的不断扩大和技术的不断发展,PMC (Product Material Control)生产计划与物料控制在企业生产经营中的作用愈发重要。
本文将从PMC生产计划与物料控制的定义、目的、流程和关键要素等方面进行探讨,以期为读者对该话题有一个全面的理解。
1. 定义:PMC生产计划与物料控制是指企业通过合理的计划和控制手段,对生产过程中的物料进行全过程的控制和管理,从而实现生产计划的准确执行,并确保物料的合理利用和供给。
2. 目的:PMC生产计划与物料控制的主要目的是提高企业生产计划的满足度和物料利用率,从而降低生产成本,提高生产效率和产品质量。
3. 流程:(1) 生产计划制定:根据企业的生产能力、市场需求和资源情况等因素,制定合理的生产计划。
生产计划应包括生产数量、生产周期和交货期等重要信息。
(2) 物料需求计划:根据生产计划和物料需求情况,制定物料需求计划。
物料需求计划应包括物料种类、数量和采购时间等信息。
(3) 物料采购:根据物料需求计划,进行物料采购工作。
在采购过程中,应考虑物料价格、供应商信誉度和交货时间等因素。
(4) 物料接收和入库:对采购的物料进行检验和验收,合格后及时入库。
入库时应按照物料种类和质量要求进行分类管理。
(5) 物料发放和使用:根据生产计划和物料需求,及时将物料发放给相应的生产部门。
在使用过程中,应严格遵守使用规范,避免物料的浪费和损坏。
(6) 物料库存管理:对物料库存进行及时、准确的记录和统计,实时监控库存情况。
根据库存情况,及时调整物料采购计划和生产计划,避免库存过多或过少。
(7) 物料退货和报废:对于质量不合格的物料,应及时退货给供应商。
对于过期或损坏的物料,应按照公司制度进行报废处理。
4. 关键要素:(1) 生产计划的准确性:生产计划是整个PMC生产计划与物料控制的基础,只有准确的生产计划才能实现生产计划的准确执行。
- 1、下载文档前请自行甄别文档内容的完整性,平台不提供额外的编辑、内容补充、找答案等附加服务。
- 2、"仅部分预览"的文档,不可在线预览部分如存在完整性等问题,可反馈申请退款(可完整预览的文档不适用该条件!)。
- 3、如文档侵犯您的权益,请联系客服反馈,我们会尽快为您处理(人工客服工作时间:9:00-18:30)。
交期 数量
物料到位 人机负荷
产能负荷调整
日程编订
生产计划与物料控制(PMC进)分解度跟催
2、如何识别同步
现有的ERP是如何设计来实现同步的?
生产计划与物料控制(PMC)分解
我们应当如何考虑?
客户要求交货日期 生产时间:标准工时、生产综合效率、
实际产能、 余力、 平衡率 采购时间:下采购单时间、供应商制备
1、计划编制流程 2、如何识别同步 3、如何实现同步
生产计划与物料控制(PMC)分解
销售预测
1、计划编制流程 销售计划
产品设计图
1SOP(标准途程) 2SIP(标准检验程序) 3BOM(标准料表) 4ST(标准时间表) 5LT(前置时间) 6LOT SIZE(批量)
基准日程
订单 主生产计划
缺料计划 采购计划
综合有效运转率= 84.06% × 94.98%=79.84%
生产计划与物料控制(PMC)分解
工序生产能力
如前面工序的标准工时为:U系列12.6秒/件,V系列14.0秒/件, 则该工序生产能力为:
(1)单时生产能力:
单时U系列生产能力=3600×84%÷12.6=240件/小时 单时V系列生产能力=3600×84%÷14.0=216件/小时 (2)单日生产能力: 单日U系列单型号生产能力=240×16=3840件/日 单日U系列生产能力=240×16×(1-U系列切换率) 单日V系列单型号生产能力=216×16=3456件/日 单日V系列生产能力=216×16×(1-U系列切换率) (3)单月生产能力: 6月U占60%,V占40% 月度生产能力=(3840×26×60%+3456×26×40%) ×(1-5%)=91054件/月
生产计划与物料控制(PMC)分解
3、生产综合效率
设备
日历时间 (年 月 日) (A )
管
负荷时间 (B)
理 浪
费
Hale Waihona Puke 停运转时间 ( C )
止 浪
费
性 实 际(D) 能 运转时间 浪
费
不 价 值(E) 良 运转时间 浪
费
8大浪费
生 产 综 合 效 率的 计 算
①计 划 保 全 ②生 产 调 整
时间运转率=
生产计划与物料控制(PMC)分解
3、如何实现同步
1、同步管理项目 2、信息同步 3、协调解决
生产计划与物料控制(PMC)分解
1、同步管理项目
销售预测准确率 销售计划准确率 主生产计划准确率 缺料计划准确率 采购计划准确率 余力计划准确率 作业计划准确率
生产计划与物料控制(PMC)分解
日.历 时间-①②③④ 日.历 时间
×100
③故
障
④ 准备、交换、调整
⑤速 度 低 下
性能运转率=
标准 时间 ×加工数量 实际时间×加工数量
×100
⑥ 空 转、 暂 停 ⑦ 修 理·再 加 工
加工数量 - ⑦⑧
良品率 =
数量
⑧废 弃
生产综生合产效计划率与=物时料间控运制转(PM率C×)分性解能运转率×良品率
时间、交运时间、验收时间 交运客户时间
生产计划与物料控制(PMC)分解
1、标准工时
生产计划与物料控制(PMC)分解
生产计划与物料控制(PMC)分解
生产计划与物料控制(PMC)分解
生产计划与物料控制(PMC)分解
2、实际产能
工序工时效率计算: 某工序出勤体制为两班两倒,每班出勤8小时,一天出勤16小时.2008年6月 12日,该工序工时运用的实际情况如下:
演练
请设计一张六大计划准确率考核表格。
生产计划与物料控制(PMC)分解
2、信息同步
目视化 一小时通话
生产计划与物料控制(PMC)分解
3、协调解决
问题解决在发生之前 FMEA运用
生产计划与物料控制(PMC)分解
第二讲:主生产计划如何精确 的分解为作业计划
1、余力、工艺掌握 2、分解方法 3、排程原则 4、管理项目
生产计划与物料控制 (PMC)
生产计划与物料控制(PMC)分解
课程大纲
第一讲:销售计划、主生产计划、采购计划同步 第二讲:主生产计划如何精确的分解为作业计划 第三讲:采购计划如何编制、跟踪 第四讲:生产进度管制 第五讲:如何进行插单管理 第六讲:减少库存,加速周转
生产计划与物料控制(PMC)分解
第一讲:销售计划、主生产计 划、采购计划同步
判断:A>B余力管理/A<B外包管理
生产计划与物料控制(PMC)分解
5、生产线平衡率
(秒)
22
20
18
作 16
业 14
所 12
需 时
10
间8
6
4
2
0
尖峰时间20秒
损失时间 (斜线部份)
求 E%?
L% ?
损失时间 ?
1
2
3
4
5
制 程(每制程为乙名作业员)
生产计划与物料控制(PMC)分解
平衡安排生产
4、产能负荷分析表(范例)
月份工作天
制程名称 (机器代号)
产能 工时 A
负荷
余力
比率 %
工时
100
B
比 率 工时 %
B/A
C
比率 %
1.工时单位:人天、人时、人分 工时:(a)产能(A)=每日可用工时×工作天数 (b)负荷(B)=标准工时×计划数量 (C)余力(C)=产能(A)-负荷(B)
1. 比率:1产能以100%表示 2负荷以B/A表示 3余力以(100-B/A)%表示
生产计划与物料控制(PMC)分解
生产计划与物料控制(PMC)分解
该工序有效运转率为: 有效运转率=807÷960×100%=84.06% 该工序主要生产u,v两大系列产品.2007年6月生产26天,机型
切换52次,机型切换消耗的总工时为1254分钟. 则该工序切换率为: 切换率=1254÷(16×26×60) ×100%=5.02% 切换效率为:切换效率=1- 5.02%=94.98%
一周工作5天,一天8小时,A、B、C、D
4台设备,专人操作,一周运营成本6000元。
P产品
Q产品
90元 100个
100元 50个
D原材料5元
D工序15分钟 C工序10分钟
C工序5分钟 B工序15分钟
D工序20分钟 C工序10分钟 B工序15分钟
A工序15分钟 A原材料20元
B原材料20元
A工序15分钟 C原材料20元
×100
生产综合效率的计算
计算题:
三班倒的企业,每班一天工作8小时,其中生产计 划休息时间20分,设备故障停止20分,准备作业花去20 分,调整10分,一个班可以生产400个产品,标准为半 分钟生产一个,因为设备性能下降实际每个产品平均 需要0 .8分钟,不良率为2%。
生产计划与物料控制(PMC)分解