第三节 球化处理工艺
第三节 球墨铸铁知识

第三节球墨铸铁一、组织和性能经过球化处理的铸铁液,浇注后石墨结晶球状,获得球墨铸铁,从而提高了铸铁的力学性能。
[组织]:基体+球状石墨,基体的组织有多种,常见的如图所示。
[性能]:球墨铸铁的强度、塑性与韧性都大大优于灰铸铁,力学性能可与相应组织的铸钢相媲美。
缺点是凝固收缩较大,容易出现缩松与缩孔,熔铸工艺要求高,铁液成分要求严格。
二、热处理铸态下的球墨铸铁基体组织一般为铁素体与珠光体,采用热处理方法来改变球墨铸铁基体组织,可有效地提高力学性能。
常用的热处理方法如下:[退火]:球墨铸铁的退火分为去应力退火、低温退火和高温退火。
去应力退火工艺与灰铸铁相同。
低温退火和高温退火的目的是使组织中的渗碳体分解,获得铁素体球墨铸铁,提高塑性与韧性,改善切削加工性能。
[正火]:球墨铸铁正火的目的是增加基体中珠光体的数量,或获得全部珠光体的基体,起细化晶粒,提高铸件的强度和耐磨性能的作用。
正火分为低温正火和高温正火。
[调质处理]:将铸件加热到860~920℃,保温2~4小时后油中淬火,然后在550~600℃回火2~4小时,得到回火索氏体加球状石墨的组织,具有良好的综合力学性能,用于受力复杂和综合力学性能要求高的重要铸件,如曲轴与连杆等。
[等温淬火]:将铸件加热到850~900℃,保温后迅速放入250~350℃的盐浴中等温60~90分钟,然后出炉空冷,获得下贝氏体基体加球状石墨的组织,使综合力学性能良好,用于形状复杂,热处理易变形开裂,要求强度高、塑性和韧性好、截面尺寸不大的零件。
三、球墨铸铁的牌号及用途[牌号表示]:是由“QT”(“球铁”两字汉语拼音字首)后附最低抗拉强度σb值(MPa)和最低断后伸长率的百分数表示。
例如牌号QT700—2表示最低抗拉强度为600MPa、最低断后伸长率δ为2%的球墨铸铁。
[应用场合]:球墨铸铁的力学性能优于灰铸铁,与钢相近,可用它代替铸钢和锻钢制造各种载荷较大、受力较复杂和耐磨损的零件。
球化过程及主要缺陷分析 文档
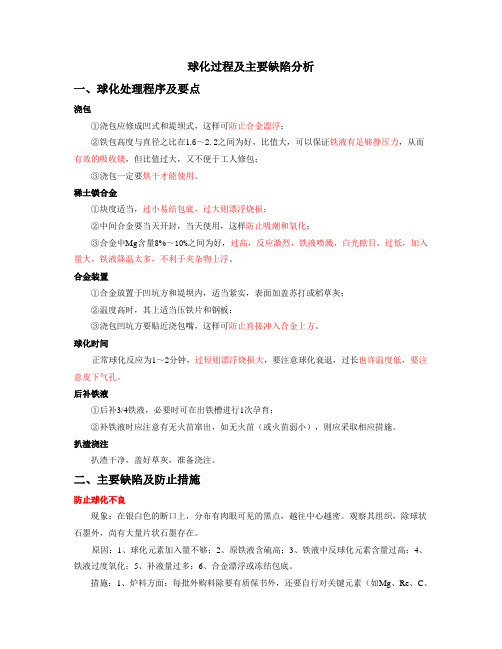
球化过程及主要缺陷分析一、球化处理程序及要点浇包①浇包应修成凹式和堤坝式,这样可防止合金漂浮;②铁包高度与直径之比在1.6~2.2之间为好,比值大,可以保证铁液有足够静压力,从而有效的吸收镁,但比值过大,又不便于工人修包;③浇包一定要烘干才能使用。
稀土镁合金①块度适当,过小易结包底,过大则漂浮烧损;②中间合金要当天开封,当天使用,这样防止吸潮和氧化;③合金中Mg含量8%~10%之间为好,过高,反应激烈,铁液喷溅,白光眩目。
过低,加入量大,铁液降温太多,不利于夹杂物上浮。
合金装置①合金放置于凹坑方和堤坝内,适当紧实,表面加盖苏打或稻草灰;②温度高时,其上适当压铁片和钢板;③浇包凹坑方要贴近浇包嘴,这样可防止直接冲入合金上方。
球化时间正常球化反应为1~2分钟,过短则漂浮烧损大,要注意球化衰退,过长也许温度低,要注意皮下气孔。
后补铁液①后补3/4铁液,必要时可在出铁槽进行1次孕育;②补铁液时应注意有无火苗窜出,如无火苗(或火苗弱小),则应采取相应措施。
扒渣浇注扒渣干净,盖好草灰,准备浇注。
二、主要缺陷及防止措施防止球化不良现象:在银白色的断口上,分布有肉眼可见的黑点,越往中心越密。
观察其组织,除球状石墨外,尚有大量片状石墨存在。
原因:1、球化元素加入量不够;2、原铁液含硫高;3、铁液中反球化元素含量过高;4、铁液过度氧化;5、补液量过多;6、合金漂浮或冻结包底。
措施:1、炉料方面:每批外购料除要有质保书外,还要自行对关键元素(如Mg、Re、C、S、As等)进行检测。
自制合金也要随机抽样化验,并要做到当天熔制当天破碎和使用。
2、熔炼方面:严格按照操作指导书的要求配制铁水,各元素的最终成分应该在一定的变化范围内。
3、处理方面:球化剂不可压得过紧和过松,并且放入包内时间越短越好。
一定要做到定量出液,特别要防止包内进渣,处理后要及时搅拌,扒净浮渣,盖好草灰。
防止皮下气孔现象:经常在铸件上表面的表层内,一般位于表面下0.5m m~3mm处,形成分散细小的圆形或椭圆形光滑孔洞,直径多在1~3mm左右。
铸铁的球化处理
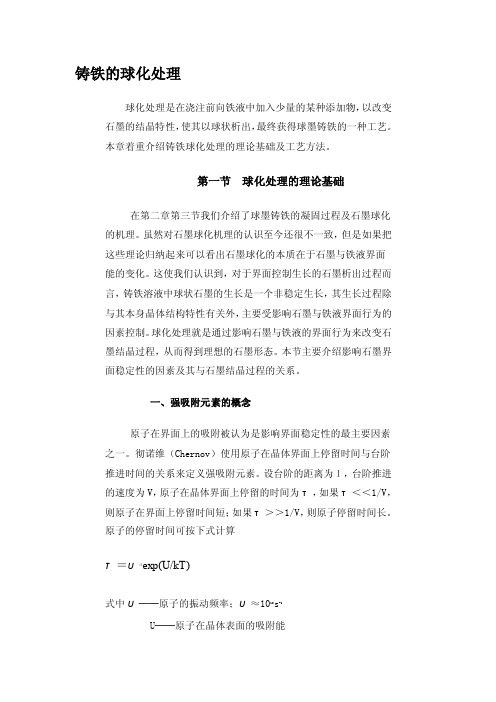
铸铁的球化处理球化处理是在浇注前向铁液中加入少量的某种添加物,以改变石墨的结晶特性,使其以球状析出,最终获得球墨铸铁的一种工艺。
本章着重介绍铸铁球化处理的理论基础及工艺方法。
第一节球化处理的理论基础在第二章第三节我们介绍了球墨铸铁的凝固过程及石墨球化的机理。
虽然对石墨球化机理的认识至今还很不一致,但是如果把这些理论归纳起来可以看出石墨球化的本质在于石墨与铁液界面能的变化。
这使我们认识到,对于界面控制生长的石墨析出过程而言,铸铁溶液中球状石墨的生长是一个非稳定生长,其生长过程除与其本身晶体结构特性有关外,主要受影响石墨与铁液界面行为的因素控制。
球化处理就是通过影响石墨与铁液的界面行为来改变石墨结晶过程,从而得到理想的石墨形态。
本节主要介绍影响石墨界面稳定性的因素及其与石墨结晶过程的关系。
一、强吸附元素的概念原子在界面上的吸附被认为是影响界面稳定性的最主要因素之一。
彻诺维(Chernov)使用原子在晶体界面上停留时间与台阶推进时间的关系来定义强吸附元素。
设台阶的距离为l,台阶推进的速度为V,原子在晶体界面上停留的时间为τ,如果τ<<1/V,则原子在界面上停留时间短;如果τ>>1/V,则原子停留时间长。
原子的停留时间可按下式计算τ=υ-1exp(U/kT)式中υ──原子的振动频率;υ≈1012s-1U──原子在晶体表面的吸附能例如某原子在晶体表面的吸附能U≈20J/mol,则可由上式计算出其室温下在晶体表面的停留时间τ≈10-8s,此时原子的吸附能是弱的,原子在晶体表面的停留时间很短,该原子被认为是弱吸附原子。
根据彻诺维的计算,强吸附原子的U值在50~60J/mol 之间。
二、强吸附元素引起的动力学过冷卡布雷拉(Cabrera)认为,强吸附元素吸附在晶体表面上时会在晶体表面形成一个网络,形成网络的原子之间的距离影响着晶体长大所要求的过冷度。
如图4-1所示,如果形成网络的原子之间的距离小于晶体中台阶在所处温度下的临界形核尺寸2ρc,则台阶向前推移受到网络的阻碍。
《球化处理工艺》课件

合作与交流
强调了加强国际合作与 交流,共同推动球化处 理工艺技术的发展和应
用的重要性。
THANKS
[ 感谢观看 ]
生产过程的自动化与智能化
总结词
通过自动化与智能化技术,可以提高生产效率、降低 能耗、减少人工干预,进一步优化球化处理工艺。
详细描述
随着自动化与智能化技术的不断发展,越来越多的企 业开始将这些技术应用于球化处理工艺中。通过自动 化技术,可以实现生产过程的自动化控制,提高生产 效率;通过智能化技术,可以对生产过程进行实时监 控和预测,及时发现和解决潜在问题,降低能耗和减 少人工干预。这些技术的运用,可以进一步优化球化 处理工艺,提高企业的生产效率和产品质量。
球化处理工艺的应用范围
球化处理工艺广泛应用于铸铁 制品的生产,如机床、汽车、 拖拉机等机械制造业中。
由于球化处理工艺可以提高铸 铁制品的力学性能和耐磨性, 因此可以延长其使用寿命,提 高产品质量。
此外,球化处理工艺还可以应 用于其他金属材料的处理,如 钢、铝合金等。
CHAPTER 02
球化处理工艺流程
预处理
去除杂质
在球化处理前,需要对原材料进 行严格筛选,去除其中的杂质和 有害元素,以确保球化处理的质 量和效果。
破碎与筛分
对于大块的原材料,需要进行破 碎和筛分,使其达到合适的粒度 和分布,以便于后续的球化处理 。
球化剂的选择与配置
根据原材料性质选择合适的球化剂
不同的原材料需要不同的球化剂,选择合适的球化剂是保证球化处理效果的关 键。
CHAPTER 06
案例分析
某公司球化处理工艺的应用实例
案例概述
工艺流程
某公司在生产过程中采用了球化处理工艺 ,有效地提高了产品质量和生产效率。
第三节 球化处理工艺
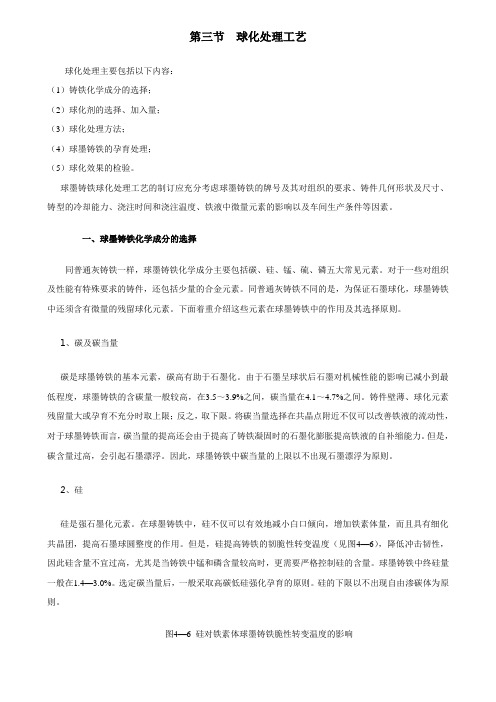
第三节球化处理工艺球化处理主要包括以下内容:(1)铸铁化学成分的选择;(2)球化剂的选择、加入量;(3)球化处理方法;(4)球墨铸铁的孕育处理;(5)球化效果的检验。
球墨铸铁球化处理工艺的制订应充分考虑球墨铸铁的牌号及其对组织的要求、铸件几何形状及尺寸、铸型的冷却能力、浇注时间和浇注温度、铁液中微量元素的影响以及车间生产条件等因素。
一、球墨铸铁化学成分的选择同普通灰铸铁一样,球墨铸铁化学成分主要包括碳、硅、锰、硫、磷五大常见元素。
对于一些对组织及性能有特殊要求的铸件,还包括少量的合金元素。
同普通灰铸铁不同的是,为保证石墨球化,球墨铸铁中还须含有微量的残留球化元素。
下面着重介绍这些元素在球墨铸铁中的作用及其选择原则。
1、碳及碳当量碳是球墨铸铁的基本元素,碳高有助于石墨化。
由于石墨呈球状后石墨对机械性能的影响已减小到最低程度,球墨铸铁的含碳量一般较高,在3.5~3.9%之间,碳当量在4.1~4.7%之间。
铸件壁薄、球化元素残留量大或孕育不充分时取上限;反之,取下限。
将碳当量选择在共晶点附近不仅可以改善铁液的流动性,对于球墨铸铁而言,碳当量的提高还会由于提高了铸铁凝固时的石墨化膨胀提高铁液的自补缩能力。
但是,碳含量过高,会引起石墨漂浮。
因此,球墨铸铁中碳当量的上限以不出现石墨漂浮为原则。
2、硅硅是强石墨化元素。
在球墨铸铁中,硅不仅可以有效地减小白口倾向,增加铁素体量,而且具有细化共晶团,提高石墨球圆整度的作用。
但是,硅提高铸铁的韧脆性转变温度(见图4—6),降低冲击韧性,因此硅含量不宜过高,尤其是当铸铁中锰和磷含量较高时,更需要严格控制硅的含量。
球墨铸铁中终硅量一般在1.4—3.0%。
选定碳当量后,一般采取高碳低硅强化孕育的原则。
硅的下限以不出现自由渗碳体为原则。
图4—6 硅对铁素体球墨铸铁脆性转变温度的影响球墨铸铁中碳硅含量确定以后,可用图4—7进行检验。
如果碳硅含量在图中的阴影区,则成分设计基本合适。
球墨铸铁球化处理方法
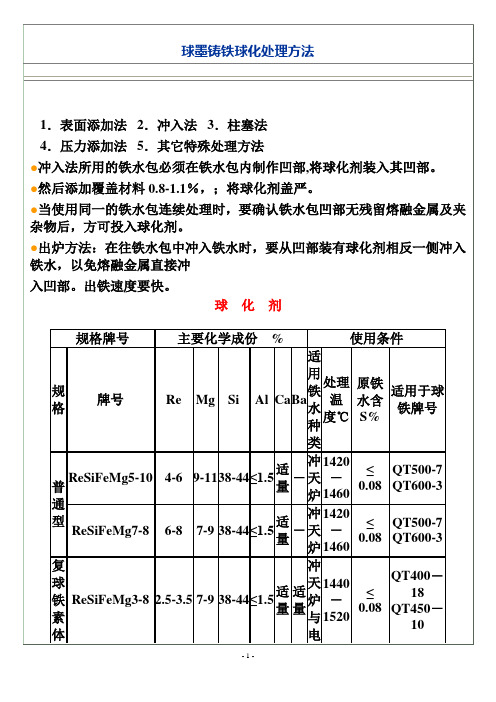
2.1 炉料选择
球铁球化剂的加入效果条件是:高碳、低硅、大孕育量。
为了稳定化学成分和有效地控制促进白口化元素和反球化元素,保证熔炼铁水的质量,选用张钢Z14生铁,其化学成分:C>3.3%,Si 1.25%~1.60%,P≤0.06%,
S≤0.04%。
2.2 球化剂的选择
球化剂的选用应根据熔炼设备的不同,即出铁温度及铁液的纯净度(如含硫量、氧化程度等)而定。
我国最常用的是稀土镁硅铁球化剂,采用这种球化剂处理时,由于合金中含硅量较高,可显著降低镁处理时反应的剧烈程度。
同时也能因增硅而有些孕育作用。
电炉生产时,因温度相对较高,所用球化剂的化学成分见表1。
表1 球化剂FeSiMg8Re7化学成分
项目
出铁温度
/℃S %
球化剂成分/%
Mg Re Si
电炉1420~1480≤0.047.0~9.0 6.0~8.0≤44.0
3 炉前控制
3.1 化学成分选择
球铁原铁液应高碳、低硅、低硫、低磷。
控制好硫的含量,是生产球铁的一个重要条件。
几种牌号的球铁的化学成分见表2。
3.2 球化和孕育处理
球化剂加入量应根据铁液成分、铸件壁厚、球化剂成分和球化处理过程的吸收率等因素分析比较确定。
一般为1.6%~2.0%,若球化剂放置时间较。
铸造合金熔炼之球化处理工艺介绍
提高产品质量:球化处理工艺可以提高产品的机械性能和耐磨性,从而提高产品质量。
减少环境污染:球化处理工艺可以减少生产过程中的废气和废水排放,从而减少环境污染。
04
谢谢
02
温度控制:控制熔融金属的温度,使球化剂充分反应
03
球化处理时间:控制球化处理的时间,使球状组织充分形成
04
球化处理后处理:球化处理后进行脱氧、脱硫等处理,提高金属性能
05
球化处理工艺流程
原材料准备
准备铸造合金材料,如铁、碳、硅等
准备球化剂,如镁、稀土等
准备孕育剂,如硅铁、硅钙等
准备脱氧剂,如铝、钛等
04
球化处理可以改善金属的加工性能,提高生产效率。
球化处理的目的
改善合金的组织结构,提高其力学性能
01
降低合金的脆性,提高其韧性和延展性
02
改善合金的耐磨性和耐腐蚀性
03
提高合金的加工性能,便于加工成型
04
球化处理的方法
球化剂加入:将球化剂加入熔融金属中,使金属形成球状组织
01
搅拌:通过搅拌使球化剂均匀分布,形成球状组织
02
03
04
球化温度的控制
球化温度是球化处理工艺的关键因素之一
球化温度过高会导致球化不良,影响合金性能
球化温度过低会导致球化不完全,影响合金的力学性能
球化温度需要根据合金的成分和生产工艺进行精确控制,以保证合金的性能和品质
01
02
03
04
球化时间的控制
01
球化时间的长短直接影响球化效果
02
球化时间过短,球化效果不佳,影响产品质量
浇铸:将熔融的铁合金倒入模具中,冷却成型
球化处理作业指导书
受控号:汽车配件制造有限公司球化处理作业指导书编号:Q/YL(J)-JS-006-2010编制:审核:批准:此文件自年月日起执行。
目的:规范球化处理的操作与指导。
适用范围:适用于本厂树脂砂及潮模砂造型工艺的球化处理。
1、炉前控制成分应严格执行《配料单》和《化学成分控制范围》2、出铁温度潮模1550-1580℃;树脂砂:1470-1550℃。
3、炉前检验当铁水熔化完毕后炉前工应及时取样,进行炉前检验,确认铁水合格后,方可进行球化处理。
4、球化处理冲入法球化,工艺如下:4.1球化前准备检查球化包尺寸是否符合要求,是否已烘干,球化剂和孕育剂是否干燥。
4.2冲入球化法:1、球化包形式:球化包筑成坝式。
2、球化剂加入量一般为:0.8-1.6%,粒度为10-25mm,一次孕育剂加入量一般为0.2-0.6%,二次孕育(依据配料单要求)粒度为3-8mm;铁豆加入量为7-10Kg详细按照配料单和当炉的含硫量、含硅量、出炉温度等确认。
3、加料顺序及方法球化剂放入坝中,一次孕育剂放在球化剂上面,再用铁豆或专用盖板盖好,准备出铁水。
4、出铁要求每次出铁分为两次,第一次出铁约为铁水总量的2/3,当包内的铁水约为铁水总量的2/3左右时,开始起爆反应。
反应快结束时将剩余铁水加入包内;遇到不起反应情况时,应用长铁棍捅开球化剂,使其反应;当反应过于强烈时应在球化包中加入面包铁以缓解球化反应的程度,根据此次情况调整下炉的铁豆的加入量。
5、球化完后应立即进行至少两次拔渣操作。
6、孕育处理:即二次孕育。
1)浇包形式:浇包为茶壶式浇包。
2)孕育方法:采用冲入法进行孕育。
3)铁水量根据铸型的大小而定。
4)二次孕育剂加入量:按照配料单的要求数量加入。
一般为0.3-0.5%,粒度为3-8mm。
7、球化过程中应时刻注意反应飞溅铁豆溅入眼内或衣服内烫伤。
8、球化过程应紧凑,力争缩短时间,以防降温及出现球化不良。
一般从球化开始到浇注结束控制在8分钟内9、记录《配料单》、《浇注记录》。
球化处理工艺
球化处理工艺1.熔炼设备选择1.1熔炼设备的选用首先是在满足生产需要的前提下,遵循高效、低耗的原则。
感应电炉的优点是:加热速度快,炉子的热效率较高,氧化烧损较轻,吸收气体较少。
因此,用中频电炉熔炼,可避免增硫、磷问题,使铁水中P不大于0.07%、S不大于0.05%。
1.2 球化包的确定为了提高球化剂的吸收率,增加球化效果,球化处理包应比一般铁液包深。
球化包的高度与直径之比确定为2:1。
2 原材料选择2.1 炉料选择球铁球化剂的加入效果条件是:高碳、低硅、大孕育量。
为了稳定化学成分和有效地控制促进白口化元素和反球化元素,保证熔炼铁水的质量,选用张钢Z14生铁,其化学成分:C>3.3%,Si1.25%~1.60%,P≤0.06%,S≤0.04%。
2.2 球化剂的选择球化剂的选用应根据熔炼设备的不同,即出铁温度及铁液的纯净度(如含硫量、氧化程度等)而定。
我国最常用的是稀土镁硅铁球化剂,采用这种球化剂处理时,由于合金中含硅量较高,可显著降低镁处理时反应的剧烈程度。
同时也能因增硅而有些孕育作用。
电炉生产时,因温度相对较高,所用球化剂的化学成分见表1。
表1 球化剂FeSiMg8Re7化学成分电炉项目球化剂成分/%出铁温度/℃S Mg Re Si1420~1480 ≤0.047.0~9.0 6.0~8.0 ≤44.03 炉前控制3.1 化学成分选择球铁原铁液应高碳、低硅、低硫、低磷。
控制好硫的含量,是生产球铁的一个重要条件。
几种牌号的球铁的化学成分见表2。
3.2 球化和孕育处理球化剂加入量应根据铁液成分、铸件壁厚、球化剂成分和球化处理过程的吸收率等因素分析比较确定。
一般为1.6%~2.0%,若球化剂放置时间较长,则应适量多加。
球化反应控制的关键是镁的吸收率,温度高,反应激烈,时间短,镁烧损多,球化效果差;温度低,反应平稳,时间长,镁吸收率表2 球铁化学成分%牌号 C Si Mn S PQT400~18球化前3.6~4.1 0.9~1.2 ≤0.4≤0.05≤0.07球化后 3.5~4.0 2.6~3.2 ≤0.02QT450~10球化前3.6~4.1 0.9~1.2 ≤0.4≤0.05≤0.07球化后3.5~3.9 2.5~3.0 ≤0.02QT600~3球化前3.6~3.9 0.9~1.2 0.6~0.8 ≤0.05≤0.07球化后3.5~3.8 2.2~2.6 ≤0.02QT700~2球化前3.6~3.9 0.9~1.2 0.6~0.8 ≤0.05≤0.07球化后 3.5~3.8 2.1~2.5 ≤0.02温度高,球化效果好。
球化工艺过程
球化工艺过程球化工艺是一种常见的金属加工工艺,主要用于改善金属的力学性能和耐磨性。
它通过加热和冷却的方式,使金属材料在一定温度范围内发生相变,从而改善材料的晶体结构和性能。
球化工艺的基本步骤包括加热、保温和冷却三个阶段。
首先,将待处理的金属材料放入加热炉中,使其达到一定的加热温度。
加热过程中,金属内部的晶粒逐渐长大,形成大尺寸的晶粒。
这是因为高温下,金属的晶界迁移速率增加,晶界能降低,从而使晶粒长大。
此时,晶粒的形状呈现出圆球状,因此称为球化。
接下来,将加热后的金属材料放入保温炉中,保持一定的温度和时间。
在保温过程中,晶粒内部的应力逐渐释放,晶粒的形状得到进一步改善,并且晶粒之间的晶界也得到调整。
这一过程主要是为了使晶粒的尺寸和形状更加均匀,提高金属的塑性和韧性。
将保温后的金属材料进行冷却处理。
冷却过程中,金属材料的温度逐渐降低,晶粒继续调整和固定,最终形成球状的晶粒结构。
通过球化工艺,金属材料的晶界面积增加,晶粒尺寸减小,晶粒形状更加均匀,从而提高材料的强度、韧性和耐磨性。
球化工艺的应用非常广泛,特别是在钢铁行业中。
例如,球化处理可以提高钢材的塑性和韧性,减少冷脆性,提高钢材的冷加工能力。
此外,球化处理还可以改善钢材的耐磨性,延长使用寿命。
在汽车制造、机械制造和航空航天等领域,球化工艺也被广泛应用于各种金属材料的处理。
总结一下,球化工艺是一种通过加热、保温和冷却的方式,使金属材料的晶粒发生相变,形成球状晶粒结构的工艺。
它可以改善金属材料的力学性能和耐磨性,提高材料的塑性和韧性。
球化工艺在金属加工和材料制备中具有重要的应用价值,对于提高金属材料的性能和品质具有重要意义。
- 1、下载文档前请自行甄别文档内容的完整性,平台不提供额外的编辑、内容补充、找答案等附加服务。
- 2、"仅部分预览"的文档,不可在线预览部分如存在完整性等问题,可反馈申请退款(可完整预览的文档不适用该条件!)。
- 3、如文档侵犯您的权益,请联系客服反馈,我们会尽快为您处理(人工客服工作时间:9:00-18:30)。
第三节球化处理工艺球化处理主要包括以下内容:(1)铸铁化学成分的选择;(2)球化剂的选择、加入量;(3)球化处理方法;(4)球墨铸铁的孕育处理;(5)球化效果的检验。
球墨铸铁球化处理工艺的制订应充分考虑球墨铸铁的牌号及其对组织的要求、铸件几何形状及尺寸、铸型的冷却能力、浇注时间和浇注温度、铁液中微量元素的影响以及车间生产条件等因素。
一、球墨铸铁化学成分的选择同普通灰铸铁一样,球墨铸铁化学成分主要包括碳、硅、锰、硫、磷五大常见元素。
对于一些对组织及性能有特殊要求的铸件,还包括少量的合金元素。
同普通灰铸铁不同的是,为保证石墨球化,球墨铸铁中还须含有微量的残留球化元素。
下面着重介绍这些元素在球墨铸铁中的作用及其选择原则。
1、碳及碳当量碳是球墨铸铁的基本元素,碳高有助于石墨化。
由于石墨呈球状后石墨对机械性能的影响已减小到最低程度,球墨铸铁的含碳量一般较高,在3.5~3.9%之间,碳当量在4.1~4.7%之间。
铸件壁薄、球化元素残留量大或孕育不充分时取上限;反之,取下限。
将碳当量选择在共晶点附近不仅可以改善铁液的流动性,对于球墨铸铁而言,碳当量的提高还会由于提高了铸铁凝固时的石墨化膨胀提高铁液的自补缩能力。
但是,碳含量过高,会引起石墨漂浮。
因此,球墨铸铁中碳当量的上限以不出现石墨漂浮为原则。
2、硅硅是强石墨化元素。
在球墨铸铁中,硅不仅可以有效地减小白口倾向,增加铁素体量,而且具有细化共晶团,提高石墨球圆整度的作用。
但是,硅提高铸铁的韧脆性转变温度(见图4—6),降低冲击韧性,因此硅含量不宜过高,尤其是当铸铁中锰和磷含量较高时,更需要严格控制硅的含量。
球墨铸铁中终硅量一般在1.4—3.0%。
选定碳当量后,一般采取高碳低硅强化孕育的原则。
硅的下限以不出现自由渗碳体为原则。
图4—6 硅对铁素体球墨铸铁脆性转变温度的影响球墨铸铁中碳硅含量确定以后,可用图4—7进行检验。
如果碳硅含量在图中的阴影区,则成分设计基本合适。
如果高于最佳区域,则容易出现石墨漂浮现象。
如果低于最佳区域,则容易出现缩松缺陷和自由碳化物。
图4—7 球墨铸铁中碳硅含量3、锰由于球墨铸铁中硫的含量已经很低,不需要过多的锰来中和硫,球墨铸铁中锰的作用就主要表现在增加珠光体的稳定性,促进形成(Fe、Mn)3C。
这些碳化物偏析于晶界,对球墨铸铁的韧性影响很大。
锰也会提高铁素体球墨铸铁的韧脆性转变温度,锰含量每增加0.1%,脆性转变温度提高10~12℃。
因此,球墨铸铁中锰含量一般是愈低愈好,即使珠光体球墨铸铁,锰含量也不宜超过0.4~0.6%。
只有以提高耐磨性为目的的中锰球铁和贝氏体球铁例外。
4、磷磷是一种有害元素。
它在铸铁中溶解度极低,当其含量小于0.05%时,固溶于基体中,对力学性能几乎没有影响。
当含量大于0.05%时,磷极易偏析于共晶团边界,形成二元、三元或复合磷共晶,降低铸铁的韧性。
磷提高铸铁的韧脆性转变温度,含磷量每增加0.01%,韧脆性转变温度提高4~4.5℃。
因此,球墨铸铁中磷的含量愈低愈好,一般情况下应低于0.08%。
对于比较重要的铸件,磷含量应低于0.05%。
5、硫硫是一种反球化元素,它与镁、稀土等球化元素有很强的亲合力,硫的存在会大量消耗铁液中的球化元素,形成镁和稀土的硫化物,引起夹渣、气孔等铸造缺陷。
球墨铸铁中硫的含量一般要求小于0.06%。
6、球化元素目前在工业上使用的球化元素主要是镁和稀土。
镁和稀土元素可以中和硫等反球化元素的作用,使石墨按球状生长。
镁和稀土的残留量应根据铁液中硫等反球化元素的含量确定。
在保证球化合格的前提下,镁和稀土的残留量应尽量低。
镁和稀土残留量过高,会增加铁液的白口倾向,并会由于它们在晶界上偏析而影响铸件的机械性能。
表4—2 球墨铸铁推荐化学成分(%)基体组织C Si Mn P S Mg RE Cu Mo铸态铁素体3.5~2.5≤0.3≤0.07≤0.020.03~0.02~3.9 ~3.0.06 0.04退火铁素体3.5~3.92.~2.7≤0.6≤0.07≤0.020.03~0.060.02~0.04铸态珠光体3.6~3.82.1~2.50.3~0.5≤0.07≤0.020.03~0.060.02~0.040.5~1.00~0.2表4—2给出了不同组织球墨铸铁的化学成分,供参考。
二、球化剂的选择在选用球化剂时,应考虑以下几个因素:(1)对铸件铸态组织的要求。
•铸态铁素体球墨铸铁选用低稀土球化剂,铸态珠光体球墨铸铁选用含铜或镍的球化剂。
(2)铁液中干扰元素的含量。
如果干扰元素,诸如钛、钒、铬、锡、锑、铅、锌等含量较高,须选用稀土含量较高的球化剂。
如果干扰元素含量较低(总量小于0.1%),可选用纯镁或镁合金球化剂。
(3)铁液含硫量。
硫含量较高时,一般采用稀土和镁含量较高的球化剂,如有条件,可进行脱硫处理。
硫含量较低时,可选用低稀土低镁的稀土硅铁镁球化剂。
(4)铸件冷却条件。
冷却速度较快的金属型铸造条件下,可选用低稀土球化剂。
冷却速度较慢的大型厚断面铸件可选用钇基重稀土球化剂。
三、球化处理方法球化处理方法主要指球化剂的加入方法。
球化处理方法不同,球化剂被铁液吸收率不同,球化效果就大不一样。
目前常用的球化处理方法主要有冲入法、自建压力加镁法、转包法、盖包法、型内法、钟罩法、密封流动法以及型上法等。
下面简要介绍其中常用工艺方法的特点及适用范围。
1、冲入法将球化剂破碎成小块,放入处理包底部一侧,或在处理包底部设置堤坝或凹坑,将球化剂放在堤坝内侧或凹坑内,然后在球化剂上面覆盖孕育剂、无锈铁屑、或草灰、苏打、珍珠岩集渣剂等,然后冲入1/2~2/3铁液,待铁液沸腾结束时,再冲入其余铁液。
处理完毕后加集渣剂彻底扒渣。
冲入法要求处理包的深度与内径之比在1.5~1.8之间,处理包要预热到600~800℃,铁液温度应高于1400℃。
冲入法的优点是设备简单,操作简单。
缺点是镁的吸收率低,一般只有30~40%,而且烟尘闪光较严重。
目前这种方法广泛应用于各种温度和含硫量的各种生产规模的球墨铸铁件生产。
2、自建压力加镁法镁的沸点与压力呈正比,如果铁液中有6~8个大气压时,镁的沸点就会提高到1350~1400℃。
在这样的条件下加镁,就可以避免镁的沸腾。
自建压力法是在密封的条件下将装有镁的钟罩压入铁液,使镁在铁液中有控制的沸腾,从而提高镁的回收率,稳定球化质量。
自建压力加镁法要求有安全可靠的处理设备,以防止铁液喷射出来。
处理包深度与内径之比应为1.5~2,加镁钟罩压入铁液后距包底的距离应为包深的10%。
自建压力加镁法镁的吸收率可达到70~80%,•并且处理效果稳定,无镁光,无烟尘,但设备费用高,操作繁琐。
这种方法适用于大型厚断面铸件,铸态高韧性铁素体铸件以及大量生产要求控制镁量的铸件。
3、转包法转包法原理如图图4—8所示。
反应室内装入纯镁或镁焦,转包横卧,接受铁液,然后转包立起,使铁液通过反应室的处理网孔进入反应室与镁反应。
这种方法镁的吸收率可达到60~70%,烟尘及镁光较轻,可处理含硫高达0.15%的铁液。
其缺点是需要专门的处理设备,操作较冲入法复杂。
图4—8 转包法示意图1—反应室2—球化剂3—安全盖4—铁液入口5—处理网4、盖包法盖包法是在冲入法的基础上发展起来的球化处理方法。
其方法如图4—9所示,在冲入法的处理包上部安装一个中间包将其密封,处理包与中间包之间仅通过经过严格计算的浇口连接。
预先将球化剂放在处理包内,然后用中间包承接铁液,靠由中间包流入处理包的铁液使处理包处于密闭状态,从而减少反应烟尘和镁光外逸,提高镁的利用率。
4—9 盖包法示意图这种方法与冲入法比镁的吸收率高,烟尘及镁光减少,操作复杂程度和设备费用增加不多,因此可以广泛应用。
5、型内法把球化剂放置在浇注系统中专门设计的反应室内,在浇注过程中铁液流经反应室时与球化剂发生反应进行球化处理。
为保证球化处理稳定,减少烧损,要严格计算反应室及浇注系统尺寸。
一般情况下,反应室设置于直浇道下的横浇道中,浇口杯到冒口前的系统应处于充满状态,冒口和铸件型腔保持开放。
具体尺寸可参阅有关手册。
这种方法镁吸收率高,可达70~80%,无镁光,无烟尘,无球化衰退。
其不足之处是对铁液温度、含硫量、球化剂成分、球化剂块度、反应室尺寸、浇注系统设计都有严格要求,这些因素的微小变化都会引起球化效果的变化。
此外,这种方法易产生夹渣。
这种方法适合于机械造型的大量流水生产,以及高强度高韧性球墨铸铁的生产。
四、球墨铸铁的孕育处理由于球化剂的加入,球墨铸铁的过冷倾向增大。
为避免碳化物的析出,促进析出大量细小圆整的石墨球,往往在球化处理后需要对球墨铸铁进行孕育处理。
对于球墨铸铁的孕育处理,孕育剂一般采用硅铁。
硅铁在刚刚溶解的时候其孕育效果最好,大约在8min 后出现孕育衰退现象,20~30min后孕育完全衰退。
因此,球铁的孕育以瞬时孕育效果最好。
生产实践证明,随流孕育和型内孕育效果比较理想。
但是由于操作方便,冲入孕育法(冲入法球化处理时将孕育剂覆盖在球化剂上)、倒包孕育法、浇口杯孕育法也在生产中经常使用。
图4—10为75FeSi孕育剂不同加入量、不同孕育方法时产生的不同孕育效果。
不难看出,在铸件壁厚小于40mm的情况下随流孕育效果明显优于包内孕育,只有当铸件壁厚大于45mm时,由于二者都出现严重的孕育衰退,孕育剂加入量较大的包内孕育法效果才略好。
图4—10 75FeSi随流孕育与包内孕育效果比较孕育的初期效果及其衰退速度与孕育剂中所含有的微量元素有关。
图4—11是用十种含有不同微量元素的硅铁孕育剂孕育处理球墨铸铁中石墨球数量随时间的变化情况,试棒直径为22mm。
就初期效果而言,含锶硅铁最好。
而从抗衰退能力看,Si-Mn-Ba硅铁最有效。
图4—11 不同成分硅铁孕育剂孕育处理的球墨铸铁中石墨球数量与孕育处理后时间的关系五、球化效果的检验球化效果的检验应包括炉前铁液成分的快速分析,炉前工艺试块检验,以及金相组织和力学性能的检验。
在条件许可的情况下还可以通过测定热分析曲线测定球化率。
此外,由于石墨形态对超声波、音频的传播有影响,近年来利用超声波和音频对球墨铸铁件进行无损检测也被用于生产中。
在球铸铁的生产中,及时检验铁液化学成分是否符合要求,尤其是在球化处理前预知铁液中碳、硅及硫含量对于及时调整成分,确定球化剂和孕育剂的加入量是十分重要的。
铁液化学成分的快速检验方法请参阅本书第三章中孕育效果的检验一部分内容。
下面着重介绍球墨铸铁的炉前工艺试块检验法。
球化和孕育处理后搅拌扒渣,从金属液表面下取铁液浇入长150mm、宽25mm、高50mm的三角试样铸型中,待其冷凝至表面呈暗红色时取出,底面向下淬入水中冷却,然后将其打断,观察断口。
也可采用直径15~30mm的园棒试样。