1组_汽车发动机缸体生产技术及制造工艺
汽车缸体铸造工艺

汽车缸体铸造工艺一、缸体材料车用发动机缸体缸盖的材质主要有灰铸铁,铝合金,蠕墨铸铁等。
传统的发动机无论是缸体还是缸盖都是采用铸铁的,但是铸铁有着许多先天的不足,例如重量大、散热性差、摩擦系数高等等。
所以,许多发动机厂商都在寻找更适合的材料制造发动机的构成部件,比如密度小的铝。
铝的比重轻,单位体积的铝结构强度要小于铸铁,所以铝缸体通常体积反而大些。
但铝容易和燃烧时产生的水发生化学作用,耐腐蚀性不及铸铁缸体,尤其对温度压强都更高的增压引擎更是如此。
铸铁缸体和铝缸体各有其优缺点,所以所以高增压的引擎很多都采用铸铁缸体,小型车的缸体则更多向铝缸体发展。
金属中的元素组成会对金属材料的性能产生较大的影响,就钢铁而言,钢中含碳量增加,屈服点和抗拉强度升高,但塑性和冲击性降低,当碳量0.23%超过时,钢的焊接性能变坏,因此用于焊接的低合金结构钢,含碳量一般不超过0.20%。
碳量高还会降低钢的耐大气腐蚀能力,在露天料场的高碳钢就易锈蚀;此外,碳能增加钢的冷脆性和时效敏感性。
不同的缸体元素配比也是有差别的。
合肥江淮铸造有限责任公司缸体化学成分要求化学成分(%)C Si Mn P S Cr Cu Ti Sn Pb下限 3.25 1.95 0.60 0.00 0.06 0.25 0.30 0.00 0.06 0.00 0上限 3.40 2.10 0.90 0.06 0.10 0.35 0.50 0.03 0.09 0.00 4二、原材料熔炼熔炼设备选用:中频感应保温电炉:生产效率10t/h,外水冷长炉龄大排距冲天炉:生产效率7t/h。
1、原材料原材料一般为回炉料,废钢和生铁。
回炉料是厂家的常备材料,在使用时必须注意其本身的干净程度。
回炉料的加入量必须严格按一定比例,否则会导致铁水的Si、S含量不易控制。
江淮生产的缸体铸件回炉料使用量一般不超过20%。
在江淮的缸体生产中,废钢的使用量超过50%。
这是由于生铁本身含有粗大石墨,而石墨熔点较高,在2000℃以上,在熔炼中不能熔尽,使得结晶过程中石墨变得粗大。
汽车发动机缸体加工工艺分析
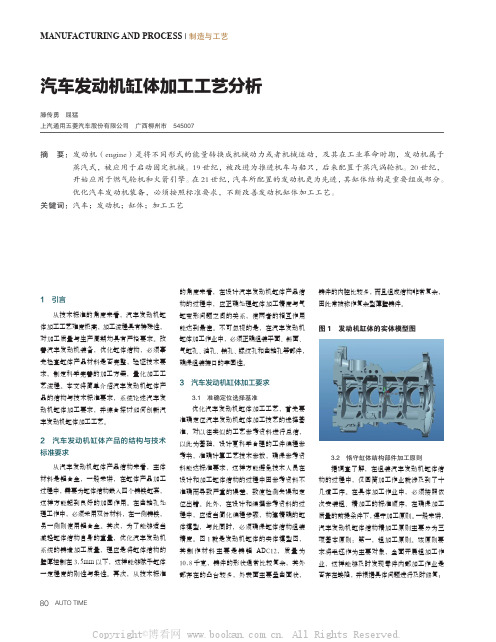
80AUTO TIMEMANUFACTURING AND PROCESS | 制造与工艺汽车发动机缸体加工工艺分析滕传勇 屈猛上汽通用五菱汽车股份有限公司 广西柳州市 545007摘 要: 发动机(engine)是将不同形式的能量转换成机械动力或者机械运动,及其在工业革命时期,发动机属于蒸汽式,被应用于启动固定机械。
19世纪,被改进为推进机车与船只,后来配置于蒸汽涡轮机。
20世纪,开始应用于燃气轮机和火箭引擎。
在21世纪,汽车所配置的发动机更为先进,其缸体结构是重要组成部分。
优化汽车发动机装备,必须按照标准要求,不断改善发动机缸体加工工艺。
关键词:汽车;发动机;缸体;加工工艺1 引言从技术标准的角度来看,汽车发动机缸体加工工艺难度极高,加工流程具有特殊性,对加工质量与生产周期均具有严格要求。
改善汽车发动机装备,优化缸体结构,必须事先检查缸体产品材料是否完整,验证技术要求,制定科学完善的加工方案,量化加工工艺流程。
本文将简单介绍汽车发动机缸体产品的结构与技术标准要求,系统论述汽车发动机缸体加工要求,并综合探讨如何创新汽车发动机缸体加工工艺。
2 汽车发动机缸体产品的结构与技术标准要求从汽车发动机缸体产品结构来看,主体材料是铝合金,一般来讲,在缸体产品加工过程中,需要为缸体结构嵌入四个铸铁缸套,这样方能起到良好的加固作用。
在曲轴孔处理工作中,必须采用双份材料,在一侧铸铁,另一侧则使用铝合金。
其次,为了能够适当减轻缸体结构自身的重量,优化汽车发动机系统的铸造加工质量,理应是将缸体结构的壁厚控制在3.5mm 以下,这样能够赋予缸体一定程度的刚性与柔性。
再次,从技术标准的角度来看,在设计汽车发动机缸体产品结构的过程中,应正确处理缸体加工精度与气缸变形问题之间的关系,使两者的相互作用能达到最佳。
不可忽视的是,在汽车发动机缸体加工作业中,必须正确组装平面、斜面、气缸孔、油孔、销孔、螺纹孔和曲轴孔等部件,确保组装接口的牢固性。
汽车发动机缸体制造工艺
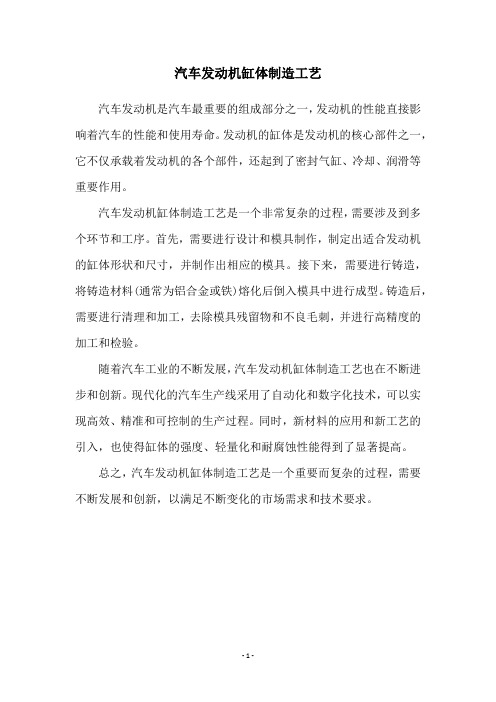
汽车发动机缸体制造工艺
汽车发动机是汽车最重要的组成部分之一,发动机的性能直接影响着汽车的性能和使用寿命。
发动机的缸体是发动机的核心部件之一,它不仅承载着发动机的各个部件,还起到了密封气缸、冷却、润滑等重要作用。
汽车发动机缸体制造工艺是一个非常复杂的过程,需要涉及到多个环节和工序。
首先,需要进行设计和模具制作,制定出适合发动机的缸体形状和尺寸,并制作出相应的模具。
接下来,需要进行铸造,将铸造材料(通常为铝合金或铁)熔化后倒入模具中进行成型。
铸造后,需要进行清理和加工,去除模具残留物和不良毛刺,并进行高精度的加工和检验。
随着汽车工业的不断发展,汽车发动机缸体制造工艺也在不断进步和创新。
现代化的汽车生产线采用了自动化和数字化技术,可以实现高效、精准和可控制的生产过程。
同时,新材料的应用和新工艺的引入,也使得缸体的强度、轻量化和耐腐蚀性能得到了显著提高。
总之,汽车发动机缸体制造工艺是一个重要而复杂的过程,需要不断发展和创新,以满足不断变化的市场需求和技术要求。
- 1 -。
汽车发动机制造工艺介绍
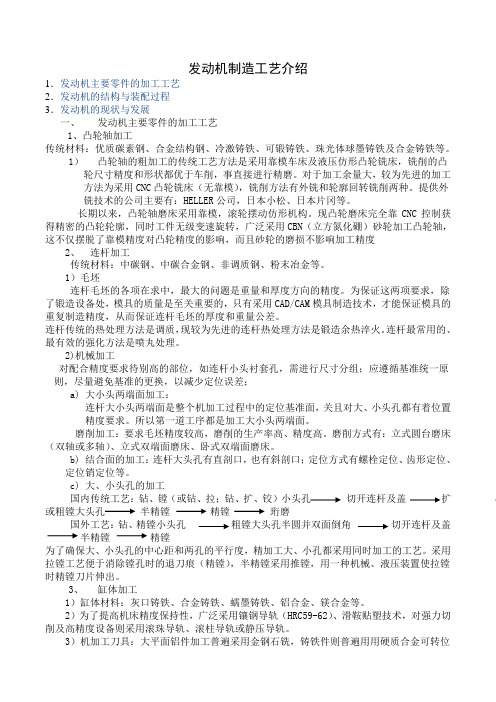
发动机制造工艺介绍1.发动机主要零件的加工工艺2.发动机的结构与装配过程3.发动机的现状与发展一、发动机主要零件的加工工艺1、凸轮轴加工传统材料:优质碳素钢、合金结构钢、冷激铸铁、可锻铸铁、珠光体球墨铸铁及合金铸铁等。
1)凸轮轴的粗加工的传统工艺方法是采用靠模车床及液压仿形凸轮铣床,铣削的凸轮尺寸精度和形状都优于车削,事直接进行精磨。
对于加工余量大,较为先进的加工方法为采用CNC凸轮铣床(无靠模),铣削方法有外铣和轮廓回转铣削两种。
提供外铣技术的公司主要有:HELLER公司,日本小松、日本片冈等。
长期以来,凸轮轴磨床采用靠模,滚轮摆动仿形机构。
现凸轮磨床完全靠CNC控制获得精密的凸轮轮廓,同时工件无级变速旋转,广泛采用CBN(立方氮化硼)砂轮加工凸轮轴,这不仅摆脱了靠模精度对凸轮精度的影响,而且砂轮的磨损不影响加工精度2、连杆加工传统材料:中碳钢、中碳合金钢、非调质钢、粉末冶金等。
1)毛坯连杆毛坯的各项在求中,最大的问题是重量和厚度方向的精度。
为保证这两项要求,除了锻造设备处,模具的质量是至关重要的,只有采用CAD/CAM模具制造技术,才能保证模具的重复制造精度,从而保证连杆毛坯的厚度和重量公差。
连杆传统的热处理方法是调质,现较为先进的连杆热处理方法是锻造余热淬火。
连杆最常用的、最有效的强化方法是喷丸处理。
2)机械加工对配合精度要求待别高的部位,如连杆小头衬套孔,需进行尺寸分组;应遵循基准统一原则,尽量避免基准的更换,以减少定位误差;a)大小头两端面加工:连杆大小头两端面是整个机加工过程中的定位基准面,关且对大、小头孔都有着位置精度要求。
所以第一道工序都是加工大小头两端面。
磨削加工:要求毛坯精度较高,磨削的生产率高、精度高。
磨削方式有:立式圆台磨床(双轴或多轴)、立式双端面磨床、卧式双端面磨床。
b) 结合面的加工:连杆大头孔有直剖口,也有斜剖口;定位方式有螺栓定位、齿形定位、定位销定位等。
c) 大、小头孔的加工国内传统工艺:钻、镗(或钻、拉;钻、扩、铰)小头孔切开连杆及盖扩或粗镗大头孔半精镗精镗珩磨国外工艺:钻、精镗小头孔粗镗大头孔半圆并双面倒角切开连杆及盖半精镗精镗为了确保大、小头孔的中心距和两孔的平行度,精加工大、小孔都采用同时加工的工艺。
论发动机缸体的加工工艺

环球市场/理论探讨-176-论发动机缸体的加工工艺朱广波 史晓龙上汽通用五菱汽车股份有限公司青岛分公摘要:汽车制造业作为国民经济的支柱产业,多年来为我国经济发展做出了非常突出的贡献。
然而,在经历了突飞猛进的高增长之后,我国汽车工业面临着越来越多的问题和压力。
如何在我国人口红利逐渐消失、企业竞争力日益下降的今天,进一步降低生产成本,同时不断提高产品质量,实现绿色制造,应对市场对产品提出的日新月异的需求尤其重要。
在此背景下本文将着重分析探讨发动机缸体的加工工艺要点,以期能为以后的实际工作起到一定的借鉴作用。
关键词:发动机;缸体;加工1、发动机缸体加工工艺性分析发动机缸体毛坯制作成坯后,上下缸体的6个面都需要采用金属切削加工的工艺方法最终加工成缸体成品,在加工过程中还要穿插气密检测、清洗、珩磨缸孔等工艺方法。
金属切削加工发动机缸体主要包括:铣面、铣孔、钻孔、镗孔、铰孔和攻丝等。
发动机缸体的加工一般情况下可划分为两个阶段,一是分体加工阶段,二是组件加工阶段。
分体加工阶段主要是将上下缸体上的精度要求不太高的一般结构特征、组合后不便加工的结构特征及关系到合缸的结构特征加工到位或去除大部余量,主要包括合缸面、合缸定位销孔、进排气两侧的安装面与孔系、止推面及轴瓦槽等特征。
发动机缸体的重要结构特征,如曲轴孔、气缸孔、缸盖面、前后端的定位销孔等必须安排在发动机缸体合缸后进行精加工。
发动机缸体试制加工的工艺流程安排可视企业设备现状进行合理安排,一般来讲,采用立式加工中心进行加工,装夹较为方便,但工序会相对分散,需要投入的工艺装备较多,会加大试制的加工成本。
采用卧式加工中心进行加工,可以使工序相对集中,投入的工装较少,可降低试制加工成本。
2、发动机缸体加工工艺要点2.1 缸体加工自动线汽车缸体加工自动线是汽车制造行业中的一种高效设备。
自动线又分为刚性自动线和柔性自动线。
在我国,加工缸体最多的当属组合机床自动线,其输送形式有棘爪输送、摆杆式输送和抬起步伐输送等,都属于刚性自动线。
汽车发动机缸体的铸造工艺

汽车发动机缸体的铸造工艺汽车发动机的发展离不开发动机铸造工艺的进步,而发动机铸造的核心在于汽车发动机缸体的铸造工艺。
汽车发动机缸体作为发动机的核心部件,除了承载发动机部件外,还需具有良好的散热和密封性能。
因此,发动机缸体的铸造工艺对发动机整体性能和稳定性有着至关重要的作用。
本文将从铸造材料、铸造工艺、铸造缺陷、铸造后处理等方面对汽车发动机缸体的铸造工艺进行详细探讨。
一、铸造材料发动机缸体通常采用铸铁材料,主要分为灰铸铁和球墨铸铁。
灰铸铁通常用于较低功率和低转速的汽车发动机,而球墨铸铁则适用于高性能、高功率、高转速的汽车发动机。
球墨铸铁在强度、塑性、耐磨性等方面均优于灰铸铁,且在重量、散热、强度均有更好的表现。
同时,球墨铸铁具有更好的冲击吸能性能,能够有效地防止发动机在碰撞时的损坏。
二、铸造工艺1. 铸型制作铸型制作是铸造过程中的重要环节,它直接影响到铸体的质量和缺陷率。
一般采用砂型铸造,其制作包括砂型模板制作、芯制作、脱模、修型等步骤。
对于汽车发动机缸体的铸造,为了保证制品的精度和质量,通常采用分型铸造法,即把模型分成几个部分分别制作再组装成模型,以保证铸体的准确度。
2. 熔炼与倒铸铸型制作完成后,便进入了熔炼与倒铸环节。
熔炼时,为了保证铸体的质量,一般采用先熔化高温点低融点的材料,然后在熔化过程中加入低温点高融点的材料,并在熔融过程中进行剧烈搅拌,以使铸材充分混合。
倒铸时,应尽量减小流型和鼓包缺陷的产生,避免气孔、夹渣等缺陷产生。
3. 铸后处理铸造完成后,需要进行铸后处理,以进一步提高铸体的性能与质量。
铸后处理主要包括清除毛边、磨光、修整、冷却采取等环节。
其中,清除毛边和磨光是保证表面光洁度的必要环节,而修整和冷却采取是保证铸体的准确度和性能的关键环节。
三、铸造缺陷由于铸造工艺的复杂性和铸造材料的不均匀性等原因,汽车发动机缸体在铸造过程中通常会出现各种类型的缺陷,如气孔、夹渣、热裂、鼓包、孔眼等。
缸体加工工艺
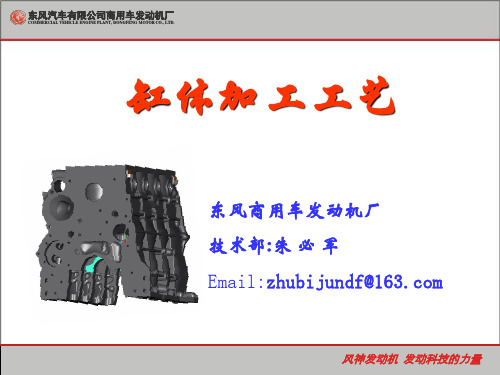
六、缸体工艺分析
(一)、面的加工:
大面一般采用刚性铣床,为保证设备的柔性,铣头采用CNC三维控制,小面一般用加工 中心铣削。对于铝合金材料,一般采用高速加工中心。 加工顺序:粗铣---半精铣----精铣 加工特点:余量大,噪音大,刀具损耗快; 加工机床:加工中心、数控铣床、组合机; 加工刀具: 铣刀; 量检具: 粗糙度用粗糙度仪,距离:三坐标
东风汽车有限公司商用车发动机厂
COMMERCIAL VEHICLE ENGINE PLANT, DONGFENG MOTOR CO., LTD.
六、缸体工艺分析
(二):螺纹孔加工:
螺纹孔大多是和螺栓配合,起紧固作用,故对其形位公差要求较低(位置度 大多在0.4mm左右)但对螺扣要求严格,必须能承受规定的力矩,不能乱扣。 加工特点:数量多,位置度容易保证,刀具比较贵,占节拍较长。 加工顺序:钻底孔---倒角----攻丝 加工机床:高速加工中心或多轴组合机; 加工刀具:钻头、倒角刀、丝锥; 量检具: 螺纹规、三坐标;
优点:柔性好,适用于加工小型缸体 缺点:(1) 刀库容量小,对刀长限制严格;(2)每次只能加工一个孔,加工节拍慢; (3)夹具回转,加工精度相对较低。
2、专用机床:用于加工大面和部分孔
优点(1)刀具大小、长度相对不受限制;(2)可以多个主轴同时加工,节拍快;(3) 刚性好,加 工质量稳定 缺点:柔性差,无法切换加工别的品种。
风神发动机 发动科技的力量
东风汽车有限公司商用车发动机厂
COMMERCIAL VEHICLE ENGINE PLANT, DONGFENG MOTOR CO., LTD.
六、缸体工艺分析
风神发动机 发动科技的力量
东风汽车有限公司商用车发动机厂
汽车发动机缸体模具设计及低压铸造工艺

汽车发动机缸体模具设计及低压铸造工艺摘要:目前,对于汽车铝合金发动机缸体采用压力铸造的方法较为广泛。
因此,压铸造工艺在汽车发动机缸体铸造中的应用过程,通过缸体模型合理的设计,调整与优化相关工艺参数,可以达到提高合格率的目的。
关键词:汽车发动机;模具设计;低压铸造工艺引言下缸体是汽车发动机上的重要零件,其上部与气缸体、下部与油底壳相连;气缸体与下缸体之间安装有曲轴。
下缸体在发动机工作过程中的特点是:处于高温状态下工作,承受较大的热冲击作用和承受较大的力,工作条件较为恶劣。
下缸体对气密性要求较高。
另外,此铸件在缸体的螺栓孔处及水泵孔凸台处较为厚大,极易产生铸造缺陷。
选择低压铸造工艺方法,采用合理的工艺参数、模具结构及局部快冷生产此铸件,不仅能解决铸件上厚大部位铸造缺陷的问题,同时也能满足此铸件组织致密性的要求。
1汽车发动机缸体结构本次研究以GM-L850发动机下缸体为例,铸件重为10.3 kg,轮廓尺寸为471 mm,371 mm和91mm,壁厚平均为4.0 mm。
材质是铝合金,这种材料具有力学性能好以及铸造工艺性能好的特点,因此,在汽车发动机铸造中应用比较广泛。
为了满足具体的工艺条件,在结构设计中进行的主要措施有两个:①在曲轴孔半圆处对工艺余量增加,以能够在下部形成一个厚大部位;②为了能够对模具结构简化,可以不铸出产品机械加工斜孔。
发动机铸件结构如图1。
2发动机缸体铸造模具设计铸造模具设计中所采用的是UG软件CAD模块,依照具体的工艺和产品毛坯三维模型,实施分型拆模,从而得到模具型芯、型腔、滑块以及镶块等,之后将这些模具分型与标准或者是非标准零件结合实施装配,经过一系列干涉检查、成型分析等流程之后,也就能够获取模具。
在进行模具三维设计中,重点是要表而形成分模成型特征,其他特征则较易实现。
汽车发动机缸体模具工作流程如图2.3模具设计3.1模具结构形式为了顺利开模,模具分型要采用多分型面,模具有6个方向开模,分别是:底模、顶模、右模、左模、前模及后模(具体模具结构见图3)。
- 1、下载文档前请自行甄别文档内容的完整性,平台不提供额外的编辑、内容补充、找答案等附加服务。
- 2、"仅部分预览"的文档,不可在线预览部分如存在完整性等问题,可反馈申请退款(可完整预览的文档不适用该条件!)。
- 3、如文档侵犯您的权益,请联系客服反馈,我们会尽快为您处理(人工客服工作时间:9:00-18:30)。
主要是铸造 汽车发动机缸体缸盖消失模铸造技术
三、缸体生产技术
缸体加工工艺流程
1.毛坯外观检查,上料; 2.利用毛坯初级基准定位。粗镗曲轴孔,粗铣前 后端面、开档面,钻主油道孔,钻铰过渡基准孔, 半精铣定位面; 3.利用加工的过渡基准定位。粗镗缸孔,钻曲轴 斜油孔,钻水套斜冷却孔,钻缸盖、主盖螺栓孔, 加工工艺基准孔; 4.工艺销孔定位。钻攻进排气侧各螺栓孔系,前 后端面部分孔系; 5.工艺销孔定位。镗水泵孔及喇叭孔,铣止推面、 锁瓦槽; 6.中间清洗、烘干;
气缸体应具有足够的强度和刚度,根据气缸体与油底 壳安装平面的位置不同,通常把气缸体分为以下三种 形式:
(1) 一般式气缸体: 其特点是油底壳安装平 面和曲轴旋转中心在同 一高度。这种气缸体的 优点是机体高度小,重 量轻,结构紧凑,便于 加工,曲轴拆装方便; 但其缺点是刚度和强度 较差
(2) 龙门式气缸体: 其特点是油底壳安装 平面低于曲轴的旋转 中心。它的优点是强 度和刚度都好,能承 受较大的机械负荷; 但其缺点是工艺性较 差,结构笨重,加工 较困难。
连接
1组 汽车构造~发动机运转.flv
7.中间试漏。采用内视法测试主油道、水道、曲轴 箱有无压力泄露,前两项10cc/min,后一项 30cc/min; 8.安装框架/主盖(下缸体); 9.合箱后采用上缸体和下缸体的工艺销孔定位。加 工前后端面各螺纹孔系,精铣顶面、前后端面,精 镗曲轴孔、缸孔、前后油封孔; 10.缸孔、曲轴孔衍磨; 11.最终清洗。浪涌清洗、定点定位、翻转、真空 干燥、冷却; 12.压装堵盖,密封试漏(外试); 13.测量打号; 14.外观检查,下线。
(3) 隧道式气缸体: 这种形式的气缸体曲轴的主轴承孔 为整体式,采用滚动轴承,主轴承孔 较大,曲轴从气缸体后部装入。其优 点是结构紧凑、刚度和强度好,但其 缺点是加工精度要求高,工艺性
较差,曲轴拆装不方便。 为了 能够使气缸内表面在高温下正
常工作,必须对气缸和气缸盖进行适 当地冷却。冷却方法有两种,一种是 水冷,另一种是风冷。水冷发动机的 气缸周围和气缸盖中都加工有冷却水 套,并且气缸体和气缸盖冷却水套相 通,冷却水在水套内不断循环,带走 部分热量,对气缸和气缸盖起冷却作 用。
二、缸体加工
气缸体
气缸体 水冷发动机的气缸体和上曲轴箱常铸 成一体,称为气缸体——曲轴箱,也可称为 气缸体。气缸体一般用灰铸铁铸成,气缸体 上部的圆柱形空腔称为气缸,下半部为支承 曲轴的曲轴箱,其套和 润滑油道等。
汽缸体示意图
2.4L汽缸体
汽车发动机
缸体生产技术及制造工艺
由五班第一组全体组员 共同制作
一、发动机缸体材料
目前制造汽车发动机缸体的材料主要有铸铁和铝合 金。
铸铁 铝合金
缸体的发展方向
由于缸体材料需要高强度,重量轻以及优良的热疲劳性能。 其发展方向如下图:
下图为铸铁发动机在国内乘用车自主品牌发动机的应用。 由下图看一看出铝合金材料正在逐年上涨