车架焊接标准
汽车车架焊接过程焊接变形控制方法
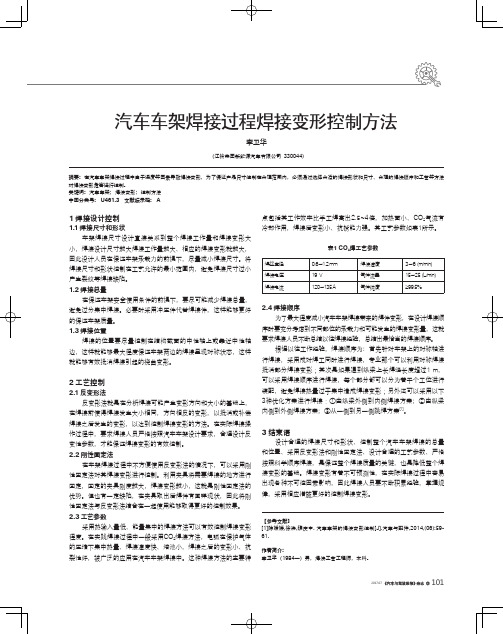
焊接的位置要尽量控制在结构截面的中性轴上或靠近中性轴 边,这样就能够最大程度保证车架两边的焊接呈现对称状态,这样 就能够有效抵消焊接引起的挠曲变形。
语
设计合理的焊接尺寸和形状、控制整个汽车车架焊接的总量 和位置、采用反变形法和刚性固定法、设计合理的工艺参数、严格 按照科学顺序焊接,是保证整个焊接质量的关键,也是降低整个焊 接变形的基础。焊接变形有着不可预测性,在实际焊接过程中容易 出现各种不可控因素影响,因此焊接人员要不断积累经验,掌握规 律,采用相应措施更好的控制焊接变形。
【参考文献】 [1]陈嫒媛,徐浩,魏庆丰. 汽车车架的焊接变形控制[J].汽车与配件,2014,(06):5961.
作者简介: 李卫华(1984—)男,焊接工艺工程师,本科。
2017.07
101
反变形法就是在分析焊接可能产生变形方向和大小的基础上, 在焊接前使得焊接发生大小相同,方向相反的变形,以抵消或补偿 焊接之后发生的变形,以达到控制焊接变形的方法。在实际焊接操 作过程中,要求焊接人员严格按照汽车车架设计要求,合理设计反 变性参数,才能保证焊接变形的有效控制。 2.2 刚性固定法
在车架焊接过程中不方便使用反变形法的情况下,可以采用刚 性固定法对其焊接变形进行控制。利用夹具将需要焊接的地方进行 固定,固定的夹具刚度越大,焊接变形越小,这就是刚性固定法的 优势。但也有一定缺陷,在夹具取出后焊件有回弹现状,因此将刚 性固定法与反变形法结合在一起使用能够取得更好的控制效果。 2.3 工艺参数
1 焊接设计控制 1.1 焊接尺寸和形状
车架焊接尺寸设计直接关系到整个焊接工作量和焊接变形大 小,焊接设计尺寸越大焊接工作量越大、相应的焊接变形就越大, 因此设计人员在保证车架承载力的前提下,尽量减小焊接尺寸。将 焊接尺寸和形状控制在工艺允许的最小范围内,避免焊接尺寸过小 产生裂纹等焊接缺陷。 1.2 焊接总量
车架焊接工艺规范

8~11
8.2工艺参数按下表规定执行。
编制 (日 期)
校对 (日 期)
审核 (日 期)
标准 化 (日 期)
会签 (日 期)
批准 (日 期)
标 处 更改文 记 数 件号
签字 (日 期)
奔驰汽车股
第5页
份有限公司
北京 车架装焊通用工艺
汽车
守则
共6页
厂
8.3电流极性采用直流反接。 8.4工艺参数的监控与检查:
续焊,两端15mm不焊。 7.8.7管状横梁平板件(如变速操纵支架、消音器支架等)的
焊接:采用双面对称角焊缝。 7.8.8板簧吊耳的焊接:采用圆周焊。
7.8.9管状横梁与纵梁的焊接:均采用单面圆周焊。 7.8.10本守则中未注明的焊接方法在作业指导书中体现。 8 焊接规范参数
8.1车架车间生产用焊丝牌号为H08Mn2SiA,直径为Ф1.0或
9.3.10驾驶室支架安装尺寸位置度公差不大于2.0。 9.3.11驾驶室支架安装基准面至车架上平面高度尺寸公差不大 于1.2。 9.3.12发动机前支架托板中心距车架上平面高度尺寸公差应不 大于1.5,左、右跨距公差应不大于1.5。 9.3.13小汽三车架车头管中心线与板簧支架中心线的对称度不 大于3.0。 9.4 9.2中规定内容为车架检查工位必检内容,任一项不符合要 求该车架视为不合格车架。
编制 校对 审核 标准 会签 批准
(日 (日 (日 化 (日 (日 期) 期) 期) (日 期) 期)
期)
标 处 更改文 记 数 件号
签字 (日 期)
奔驰汽车股
第6页
份有限公司
北京 车架装焊通用工艺
汽车
守则
共6页
厂
9.3.5车架各横梁应垂直于车架纵向对称平面,垂直度1000范 围内不大于2.0。
汽车车架的铆接和焊修技术
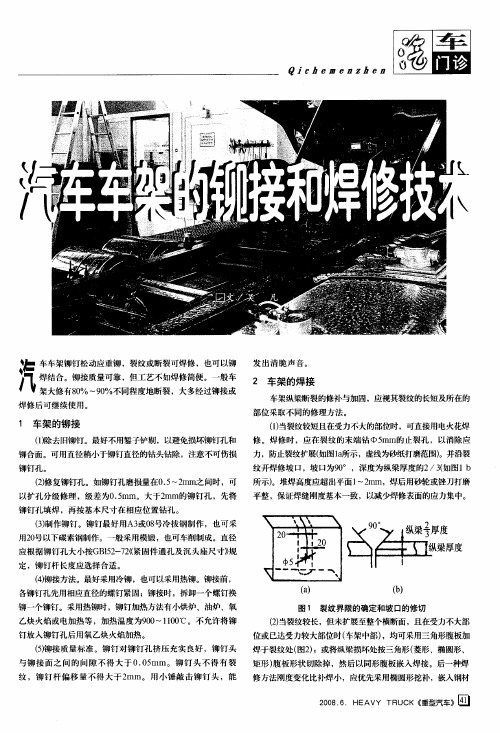
大多经过铆接或
车架纵梁断裂的修补与加固,应视其裂纹的长短及所在的 部位采取不同的修理方法。 () 1当裂纹较短且在受力不大的部位时,可直接用电火花焊
修 。焊修时 ,应在裂纹的末端钻 ①5 mm的止裂孔 ,以消除应
1 车架 的铆 接
() 1 除去旧铆钉。最好不用錾子铲剔,以避免损坏铆钉孔和 铆合面。可 用直径稍小于铆钉直径的钻头钻除 ,注意不可伤损
修方法刚度变化比补焊小 ,应优先采用椭圆形挖补,嵌入钢材
1 71 " 1 7
(铆接质量标 准。铆钉对铆钉 孔挤压充实 良好 ,铆钉头 5 )
与铆接 面 之 间的 间隙 不得 大于 0. 5 m。铆 钉头 不 得 有裂 0r a
纹 ,铆钉 杆偏 移量 不得 大于 2 m。用 小锤敲 击铆 钉头 ,能 a r
() 1 若在受力大的部位焊加强腹板,要注意焊接应力对纵梁 的影响,可采用 图5 的方法。加强板比纵梁边缘宽 出25( .t 为车 t 架纵梁厚度) ,并把焊缝焊成 凹形。
() 2车架上焊缝长度大时 ,应采用断续分段焊法(n 所 I 图6
示) 。每段焊缝长度和间距请参阅下表 。
图2 三角形加强腹板 的厚度 、材质应与纵梁材质相 同。
() 6寒冷季节,应将焊接部位预热至2 ~5  ̄ 0 0 C,以防炸裂; 图 3 角钢切角 图 4 弯角圆弧半径 焊后缓慢冷却,清除焊渣 ,用砂轮、锉刀等工具修整焊缝 。
黼 ■ 鬻 ■ 一 黧 ■ 麓 一 麓 ● 麓 一 麓 ■ 臻 ■ 鞠 ■ ■ 一 ■ 瓣 一 鬃 一 辫 一 鞭 一 一 ■ ■ 一 一 一 一 ■ 一 ■ 一 曩 一 一 ■
为了减小应力集中,加强板的端部应做成逐渐减小的斜角 形( ) 图3。加强板的形状如 图4 所示 ,其弯角圆弧半径应不大于
常见副车架(厚板件)焊接基本技术
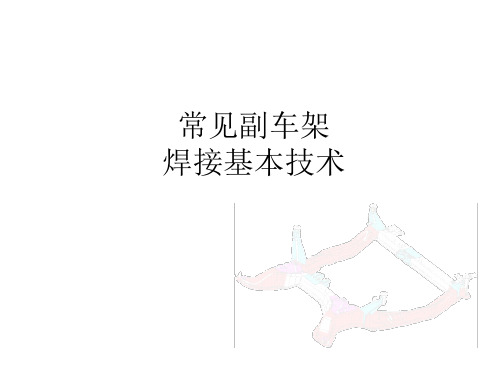
焊接的本质
焊接实质上利用局部加热或局部加压,或两者兼用的方法,使被连接的金属 融化或达到塑性状态,以促使两种金属的原子相互渗合并接近到一定的金属晶格距离, 原子之间的结合力就可以把两个分离的金属构件连接成一体。
熔化焊一般都要经历下列几个过程,加热-------熔化-------冶金反应------结晶-----固态相变------形成接头。
焊点结构如图所示:
R总
电极
ew w c
w
被焊工件
ew
电极
焊点结构示意图
δ——焊件板厚,d——电极直径, dn——熔核直径,dr——塑性环直径, hn——熔核高度,△——压痕深度。
点焊的原理图
其中R总——焊接区总电阻 Rew——电极与焊件之间接触电阻 Rw——焊件内部电阻 Rc——焊件之间接触电阻 电阻焊产生的热量公式:Q=I2Rt
1)焊条电弧焊:外部涂有涂料的焊丝熔化,产生熔渣漂浮于 熔池的表面,防止焊缝金属与周围气体相互作用.熔渣还有 一个重要的作用是可以添加合金元素改善焊缝性能.
2)熔化极气体保护电弧焊:焊丝本身充当电极,被电弧热熔 化,焊炬喷嘴喷出气体保护焊接区域.根据所喷气体的不同 又分为:MIG(一般是惰性气体氩气),MAG(惰性气体氩气与 氧化气体的混合物),CO2气体保护焊(熔池较其他保护气体 熔池宽.但易引起飞溅,焊缝不美观);氩气与CO2的理想配 比是1:4,既能得到理想的熔化宽度又可以得到较好的工件 外管)
点焊接头必须以搭接基本形式(如图),有两个或两个以上等厚或 不等厚的工作组件组成。点焊设计应考虑一下几方面内容:
点焊的基本接头形式 其中b——边距,c——搭接量,e——点距
点焊工艺参数参考表
板厚(mm)
汽车车架焊接工艺分析及工装设计
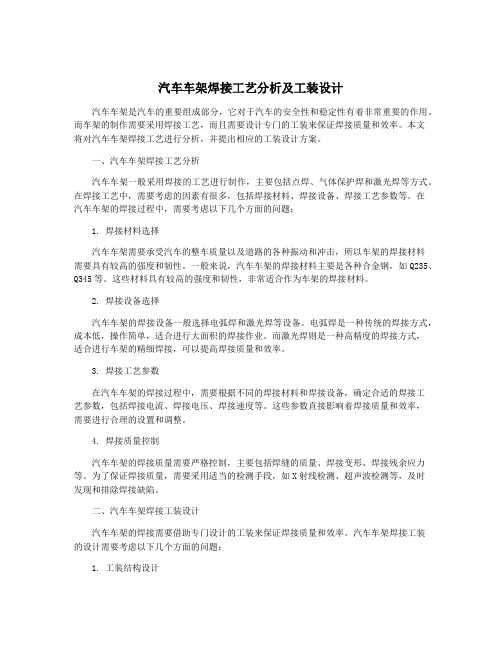
汽车车架焊接工艺分析及工装设计汽车车架是汽车的重要组成部分,它对于汽车的安全性和稳定性有着非常重要的作用。
而车架的制作需要采用焊接工艺,而且需要设计专门的工装来保证焊接质量和效率。
本文将对汽车车架焊接工艺进行分析,并提出相应的工装设计方案。
一、汽车车架焊接工艺分析汽车车架一般采用焊接的工艺进行制作,主要包括点焊、气体保护焊和激光焊等方式。
在焊接工艺中,需要考虑的因素有很多,包括焊接材料、焊接设备、焊接工艺参数等。
在汽车车架的焊接过程中,需要考虑以下几个方面的问题:1. 焊接材料选择汽车车架需要承受汽车的整车质量以及道路的各种振动和冲击,所以车架的焊接材料需要具有较高的强度和韧性。
一般来说,汽车车架的焊接材料主要是各种合金钢,如Q235、Q345等。
这些材料具有较高的强度和韧性,非常适合作为车架的焊接材料。
2. 焊接设备选择汽车车架的焊接设备一般选择电弧焊和激光焊等设备。
电弧焊是一种传统的焊接方式,成本低,操作简单,适合进行大面积的焊接作业。
而激光焊则是一种高精度的焊接方式,适合进行车架的精细焊接,可以提高焊接质量和效率。
3. 焊接工艺参数在汽车车架的焊接过程中,需要根据不同的焊接材料和焊接设备,确定合适的焊接工艺参数,包括焊接电流、焊接电压、焊接速度等。
这些参数直接影响着焊接质量和效率,需要进行合理的设置和调整。
4. 焊接质量控制汽车车架的焊接质量需要严格控制,主要包括焊缝的质量、焊接变形、焊接残余应力等。
为了保证焊接质量,需要采用适当的检测手段,如X射线检测、超声波检测等,及时发现和排除焊接缺陷。
二、汽车车架焊接工装设计汽车车架的焊接需要借助专门设计的工装来保证焊接质量和效率。
汽车车架焊接工装的设计需要考虑以下几个方面的问题:1. 工装结构设计汽车车架焊接工装的设计需要充分考虑车架的形状和结构,采用合适的夹具和模具来固定和支撑车架,在焊接过程中保证车架的稳定性和一致性。
工装的结构设计还需要考虑操作方便、维修方便等因素。
中华人民共和国国家标准汽车车架修理技术条件
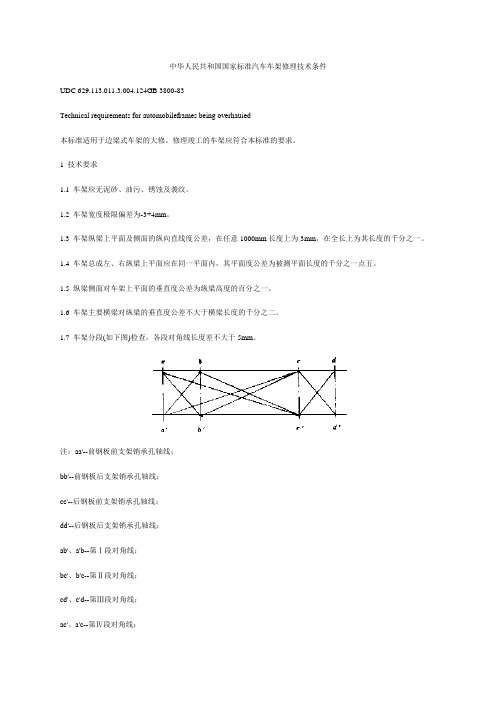
中华人民共和国国家标准汽车车架修理技术条件UDC 629.113.011.3.004.124GB 3800-83Technical requirements for automobileframes being overhauied本标准适用于边梁式车架的大修。
修理竣工的车架应符合本标准的要求。
1 技术要求1.1 车架应无泥砂、油污、锈蚀及袭纹。
1.2 车架宽度极限偏差为-3+4mm。
1.3 车架纵梁上平面及侧面的纵向直线度公差,在任意1000mm长度上为3mm,在全长上为其长度的千分之一。
1.4 车架总成左、右纵梁上平面应在同一平面内,其平面度公差为被测平面长度的千分之一点五。
1.5 纵梁侧面对车架上平面的垂直度公差为纵梁高度的百分之一。
1.6 车架主要横梁对纵梁的垂直度公差不大于横梁长度的千分之二。
1.7 车架分段(如下图)检查,各段对角线长度差不大于5mm。
注:aa'--前钢板前支架销承孔轴线;bb'--前钢板后支架销承孔轴线;cc'--后钢板前支架销承孔轴线;dd'--后钢板后支架销承孔轴线;ab'、a'b--第Ⅰ段对角线;bc'、b'c--第Ⅱ段对角线;cd'、c'd--第Ⅲ段对角线;ac'、a'c--第Ⅳ段对角线;1.8 左右钢板弹簧固定支架销孔应同轴,其同轴度公差为φ2.0mm(按GB 1958-80《形状和位置公差检测规定》检测方法5-1进行检测)。
前后固定支架销孔轴线间的距离左、右相差:轴距在4000mm及其以下的应不大于2mm,轴距在4000mm以上的应不大于3mm。
1.9 车架的焊接应符合焊接规范。
焊缝应平整、光滑、无焊瘤、弧坑,咬边深度不大于0.5mm,咬边长度不大于焊缝长度的百分之十五,并不得有气孔、夹渣等缺陷。
1.10 车架挖补或截修的焊缝方向,除特殊车架外,不允许与棱线垂直、重叠;焊缝及其周围基体金属上,不应有裂纹。
汽车车架焊接标准

汽车车架焊接标准一、焊接材料要求1.选用的焊接材料应符合汽车车架材质和厚度要求,并具备相应的力学性能指标。
2.焊接材料应具备良好的可焊性和稳定性,以减少焊接过程中出现的裂纹、气孔等问题。
3.焊接材料应保持干燥,避免使用受潮或受污染的材料。
二、焊接前的准备工作1.对待焊接的汽车车架进行清理,去除油污、铁锈、氧化皮等杂质。
2.对待焊部件进行装配和定位,确保焊接过程中不会发生移动或变形。
3.准备所需的焊接设备和材料,如焊机、焊条、保护气体等。
三、焊接设备的选择和校准1.根据汽车车架的材质和厚度,选择适合的焊接设备,如手工电弧焊、气体保护焊等。
2.对所选的焊接设备进行校准,确保其输出电压、电流、保护气体流量等参数符合焊接要求。
3.定期检查和维护焊接设备,确保其正常运行和安全性。
四、焊接工艺和操作规范1.根据汽车车架的材质和厚度,制定相应的焊接工艺,包括焊接电流、电压、速度等参数。
2.进行焊接操作时,应严格遵守操作规范,如保持安全距离、避免手部触摸电极等。
3.在焊接过程中,应注意观察熔池的形成、焊缝的成型等情况,及时调整焊接参数。
五、焊接质量检查与检验1.对完成的焊接部位进行外观检查,确保焊缝平直、饱满,无裂纹、气孔等缺陷。
2.进行焊缝尺寸检查,如焊缝宽度、高度、间隙等是否符合要求。
3.对重要的焊接部位进行无损检测,如超声波探伤、射线探伤等,确保焊缝内部无缺陷。
4.对不合格的焊接部位进行返修或补焊,确保达到质量要求。
六、焊接安全与防护1.进行焊接操作时,应佩戴齐全的劳动防护用品,如防护面罩、手套、工作服等。
2.在焊接过程中,应注意防止火星飞溅引起的火灾或烫伤事故。
3.在焊接作业区域设置安全警示标识和围栏,避免非作业人员进入。
4.对长期暴露在恶劣环境下的汽车车架进行定期维护和保养,确保其正常运转。
车架及车厢焊接工作规定

车架及车厢焊接工作规定
为了提高车架及车厢焊接质量,严格工作纪律,现特对焊接车间工作提出如下规定:
一、工作环境
1、工作地面要经常洒水,始终保持地面无尘土浮起,地面无垃圾和烟头。
2、工作用料及其它辅料和半成品要分类摆放整齐,并划区标识,避免混用。
二、工作行为方面
1、焊接工艺应严格按照《车厢及车架的焊接工艺》进行焊接,每道工序在进行前、进行
中、进行后都要首先自检,然后接受检验人员的检验,不经检验员同意,不得进行下道工序操作。
2、焊接工应严格按照胎具定位焊接,不准随意改动胎具和车架(领导批准除外)。
三、检验工作
1、日起对所有规格的车架、车厢的焊接过程实行全检,即对对每个车厢车架的每道工序都要进行检验,成品车厢和车架要加盖检验印章或标签,检验员要作好检验记录备查。
2、检验员应严格按照《车厢及车架的焊接检验规程》进行检验,不得有漏检项目。
着重部位,重点检查。
3、检验员要从严求,及时制止焊接过程中的每项违规行为。
对不听劝止的有权进行处罚。
四、资励办法
1、对操作工严格按照工艺操作,连续焊接200个车架或车厢,无任何质量问题的,经质检部人员认定并有记录可查的,奖励操作工班组100元。
2、焊接车间转入装配车间的车架及车厢合格率达到100%且当月无用户。
- 1、下载文档前请自行甄别文档内容的完整性,平台不提供额外的编辑、内容补充、找答案等附加服务。
- 2、"仅部分预览"的文档,不可在线预览部分如存在完整性等问题,可反馈申请退款(可完整预览的文档不适用该条件!)。
- 3、如文档侵犯您的权益,请联系客服反馈,我们会尽快为您处理(人工客服工作时间:9:00-18:30)。
电动车车架焊缝外观质量要求
1 主题内容与适用范围
本标准规定了对电动车车架焊缝的外观质量要求。
本标准适用于钢质电动车车架、铝合金电动车车架及电动车护杠、扶手支架、靠背支架、车筐支架、车把、车梯、衣架等焊缝外观质量检验。
2 焊缝外观质量检验
2.1 车架结构的所有焊缝都应进行外观质量检验,焊缝表面成型应均匀致密,焊道与焊道,焊道与母材之间应平滑过渡,不应有突然变化的截面。
2.2 外观质量检验应在把焊缝表面及两侧附近的焊渣、飞溅物及污物清除干净的前提下进行。
焊缝在外观检验合格之前不得涂漆。
我公司要求的外露位置焊接质量要求如第本标准第5页图1、2、3、4。
外露部位为:前叉、护杠、简易车把、扶手支架、靠背支架、车筐支架、支架(车梯),车架的外露位置以车架图为准,车架图纸上标注的鱼鳞焊纹要求即为外露位置。
2.3 焊缝外观质量主要靠目测及使用焊缝焊角检验尺,必要时可以借助放大镜检验。
2.4 在外观目测检验合格后,方可对焊缝的内部质量进行检验。
3 角焊缝
3.1角焊缝的剖面形状见图1
图1
在满足焊喉h值的情况下,图1中三种型式都允许采用。
其中以微凸型角焊缝(有焊缝增强的)推荐采用。
3.2 对角焊缝剖面尺寸的要求见表1。
项目图示范围允许极限说明
焊脚高K,焊喉厚
度h,增强焊厚度
E,mm
K-实际焊脚高度
Ko-设计焊脚高度
h-实际焊喉厚度
ho-设计焊喉厚度
ho= 0.7Ko
E-增强焊厚度0.9Ko<K≤Ko+2
h> 0.9ho
(h>0.63 Ko)
E≤2 mm
K>0.9Ko
h=0.9ho
(h=0.63Ko)
1. K成0- 9K。
时,
必须修正。
2. 0.9Ko>K或
0.9ho>h的所有焊
缝的长度总和不得
超过焊缝全长10%
且每段连续长度不
得超过300 mm。
3. K>Ko+2,可不
修正,但要加强管
理。
4.焊脚,焊喉尺寸
不宜过大尤其是薄
板。
5.增强焊厚度E不
应大干2mm 。
焊缝侧面角θθ< 90°θ≥90°必须修正。
间断焊缝每段焊缝的有效长度,mm L,e—间断焊实际的
焊段长度及间距尺寸
Lo,e。
- 设计焊段长度
及间距尺寸
1. L。
< L<L。
+10
2. e。
-5<e<e。
+5
1. L。
+5<L<L。
+ 10
2. e。
-5<e<e。
+10
1.当L>Lo+10或
e<e。
-10不必修正,
但要加强管理。
2.当L<L。
-5或e>e。
+10且各段总和超
过该焊缝全长20%
时应修正,不超过
20%可不修正但应
加强管理。
包角焊长度L,mm 1.包角焊的长度应
符合设计要求
或L≥75mm。
2.焊脚高度应符合
设计要求。
双面间断焊或单面连续焊的立板端部应作包角焊,包角焊各边的长度l≥75mm。
4 对接焊缝
对接焊缝的形状和尺寸要求见表2
项目图示范围允许极限说明
增高量hm 母材厚小于
10
h= 0~2.5 0<h≤3.5 在任意25mm焊缝
长度上,增高量的
差不大于2mm。
母材厚大于
10
h= 0~2.5 0< h≤4.5
m
焊缝宽度C 焊缝在焊道每边覆
盖的宽度为
2~4mm
在任意10 mm焊
缝长度上,宽度的
差应不超过5mm
应尽量避免窄而高
的焊缝。
焊缝侧面角θB< 90°θ≥90°时必须修
正。
5 焊缝表面缺陷及其修正
见表3
项目图示范围允许极限说明备注
严重咬边深度dmm 母材厚度
≤6时
d<0.3 d<0.5连续
长度不大于
100mm
1.超过允许极限应修
正。
2.咬边深度d在标准范
围和允许极限之间,且
各段总和不超过该焊
缝全长的25%可不修
正,超过25%则应修
正。
母材厚
度>6时
d<0.5 d<0.8连续
长度不大于
100mm
裂纹不允许存在 1.碳弧气刨将裂缝全部
清除后补焊。
2.在同一位置焊补次数
不得超过2次。
例:
表面夹渣
不允许存在不允许存在碳弧气刨后补焊
表面气孔只数P 对接焊缝P = 0 P = 0 超过允许极限应碳弧
气刨后补焊
角
焊
缝
水密
部分
P = 0 P = 0
非水
密部
分
P=1只/0.5m 气孔直径Φ≤1.5mm,深
度≤1. 0 mm
弧坑长度L及深度S,mm L≤3
S≤1
L≤5
S≤2
超过允许极限应用碳
弧气刨刨后补焊
飞船壳外表及不允许有飞溅飞溅物应全部清除例:
溅上层建筑暴
露处图5 图9
其他部位在100 mm
长度
范围内每侧
不
得多于5个超过允许极限应修正磨平
焊瘤只数P 车架焊缝P=0 超过允许极限应修正
磨平
例:
图5
图6
图7 其他焊缝P=1只/m
多层焊焊波间沟深
S,mm
S≤1.5 超过允许极限要修正
6 焊缝修正
6.1 所有完工的焊缝表面,若存在上述缺陷时,应在焊缝内部质量检验和可靠试验之前修补完毕。
6.2 在车架酸洗、磷化后发现焊缝缺陷,应在上烤漆线加工之前,修补完毕。
这里的修补是检查焊接质量,不合求的缺陷焊接件必需清理出来。
对焊接部位外露的,有飞溅、过度不平滑、焊瘤、焊疤、夹渣、毛剌、飞边必须上烤漆线前打磨,本标准第5页、第6页有图示标准。
6.3 焊缝修正后必须进行再次检验,再次检验仍需符合本标准要求。
附加说明:
本标准由****电动车制造有限公司天津分公司品质部提出。
本标准由****电动车制造有限公司天津分公司技术部负责起草。
本标准主要起草人:***
附图页
图1 图2
图3 图4
图1、2、3、4焊接比较好,焊缝均匀饱满,表面过渡区域比较平滑没有漏焊、虚焊、夹渣、气孔、裂纹可视部分没有飞溅物等缺陷。
图5 图6 图7 图8
图9 图10
图11 图12
图5、6、7 所示位置不符合焊接要求,焊接表面堆积成块形成焊瘤,焊纹没有平滑过渡,表面凹凸不平。
对此类焊接应在烤漆之前对其进行打磨处理,使焊接表面过渡光滑。
图8焊接点不符合要求,在焊接位置出现了气孔。
图5、9所示位置不符合焊接要求,焊接位置附近出现飞溅物,影响车架表面的光滑度和外观。
对此类焊接应该在烤漆之前对其表面进行打磨处理。
图10、11所示位置不符合要求,在焊接位置出现了漏焊现象。
图12所示位置不符合要求,焊接位置出现焊穿现象。