光学镜片外观检作业规范
光学镜片表面外观检测标准

光学镜片表面外观检测标准您的光学工厂一.定义:表面缺陷标准:依据美国军用标准MIL-O-13830B用两组数字表示表面缺陷大小。
例如40/20(或40-20)前者限制划痕大小,后者限制麻点大小。
道子、亮路、伤、擦痕都统称为划痕。
斑点、坑点、点子都称为麻点。
规定长与宽的比大于4:1的为划痕;长与宽的比小于4:1的为麻点。
当元件的不同区域表面光洁度要求不一样时,等效直径的计算以区域进行:表面质量要求高的内区域其等效直径以内区域为准(如有效孔径的区域),表面质量要求低的外区域计算的是整体元件的等效直径。
如下图元件表面质量要求不同,则在判定A区是否符合要求时,应取内圆直径进行计算。
而B区则取整个元件的圆直径划痕:以美国军用标准《MIL-O-13830》的表面质量划痕样板作为各级数划痕的比对标准。
(注意:美军标未指明划痕的计量单位也即未确定划痕的宽度和深度,只能以实际观察样版为标准。
)这里的划痕级数就是通常的划痕号数,标准样版有10#、20#、40#、60#、80# 5个级。
1.当元件的划痕级数超过表面质量要求的划痕级数时,元件不合格。
例如:元件的表面质量要求为60—40,则代表元件的划痕必须≤60#,如果元件有>60#的划痕,则元件不合格。
2.当元件的划痕级数未超过表面质量要求的级数,但元件存在最大划痕时,所有最大划痕的长度之和应不超过元件直径的1/4。
例如:有一长30mm宽10mm的元件,元件的表面质量要求为60—40,有2条60#长为3 mm划痕。
它的等效直径为20mm1/4D为1/4×20=5mm最大划痕的长度和为:3mm+3mm=6mm6mm>5mm元件最大划伤痕的长度和超过元件直径的1/4。
所以元件不合格。
下图是看到的样品(图片是放大的不是实际尺寸)图中的划痕为20#,且长度>1/4D。
对于表面质量要求20-10该产品不合格。
但本次样品未提出表面质量要求,而是要大家自已决定光洁度等级。
玻璃镜片测试规范
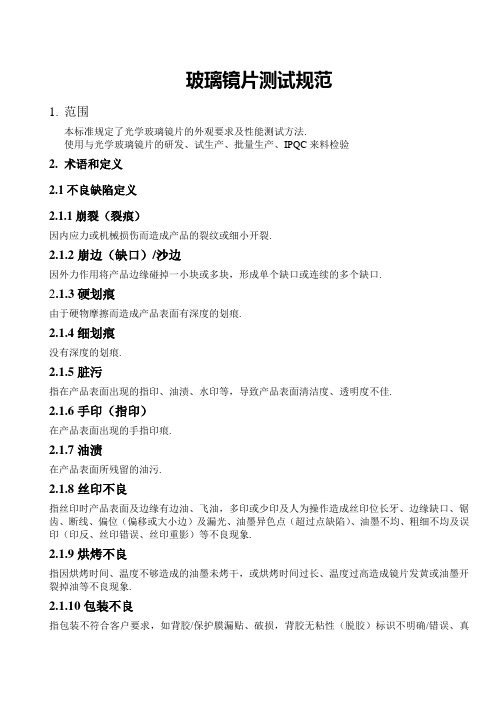
玻璃镜片测试规范1.范围本标准规定了光学玻璃镜片的外观要求及性能测试方法.使用与光学玻璃镜片的研发、试生产、批量生产、IPQC来料检验2.术语和定义2.1不良缺陷定义2.1.1崩裂(裂痕)因内应力或机械损伤而造成产品的裂纹或细小开裂.2.1.2崩边(缺口)/沙边因外力作用将产品边缘碰掉一小块或多块,形成单个缺口或连续的多个缺口.2.1.3硬划痕由于硬物摩擦而造成产品表面有深度的划痕.2.1.4细划痕没有深度的划痕.2.1.5脏污指在产品表面出现的指印、油渍、水印等,导致产品表面清洁度、透明度不佳.2.1.6手印(指印)在产品表面出现的手指印痕.2.1.7油渍在产品表面所残留的油污.2.1.8丝印不良指丝印时产品表面及边缘有边油、飞油,多印或少印及人为操作造成丝印位长牙、边缘缺口、锯齿、断线、偏位(偏移或大小边)及漏光、油墨异色点(超过点缺陷)、油墨不均、粗细不均及误印(印反、丝印错误、丝印重影)等不良现象.2.1.9烘烤不良指因烘烤时间、温度不够造成的油墨未烤干,或烘烤时间过长、温度过高造成镜片发黄或油墨开裂掉油等不良现象.2.1.10包装不良指包装不符合客户要求,如背胶/保护膜漏贴、破损,背胶无粘性(脱胶)标识不明确/错误、真空包装漏气等.2.2不合格的分类按程度不同分为A类不合格、B类不合格、C类不合格三类.2.2.1 A类不合格易导致不安全因素的项目以及导致其基本功能失效的项目.1)镜片破碎2)性能测试不良:抗冲击、附着力、装配.3)尺寸不符:与客户图纸要求不符,影响装配功能.2.2.2 B类不合格可能导致功能失误或降低原有使用功能的项目.外观检测项目内容:如崩边、崩裂、细硬划痕、点缺陷、脏污、烘烤不良、丝印不良、漏光、透光性、色泽、倒边不符要求等.2.2.3C类不合格指对产品的使用性能没有影响或只有轻微影响的项目.1)包装方式不符合客户要求,包装内有异物等.2)标识不全或不符.3)有漏装、多装或错装产品.4)检验记录填写不全或有误.2.3不合格品的定义按不合格类型分为A类不合格品、B类不合格品、C类不合格品.2.3.1 A类不合格品有一个或一个以上A类不合格品,也可能还有B类和C类不合格的单位产品.2.3.2 B类不合格品有一个或一个以上的B类不合格,也可能还有C类不合格的单位产品,但不包含A类不合格的单位产品.2.3.3C类不合格品有一个或一个以上的C类不合格,但不包含A类和B类不合格的单位产品2.4缺陷代码对照表缺陷代码对照表见表1.表1缺陷代码对照表3.外观检验条件及环境的要求.a)距离:人眼与被测无表面的距离为200mm-300mm.b)时间:每片检查时间不超过5-10s(10s内检验不出来的缺陷可以不计)c)检验方法:目视,且监视面与桌面成45°;上下左右转动15°,(透明清晰度、漏光须对光检测,即与灯光呈平行目视检测)d)照明:35w冷白荧光灯,光源距被测物表面400mm-500mm(照度达800Lux-1200Lux).4.检验操作注意事项a)操作人员工作前必须洁净双手,严格执行检验标准,不能误判、漏检.b)产品必须轻拿轻放,按指定的位置放置,标识清楚,随时注意防潮防尘遮盖(无论良品或不良品)c)工作台面必须随时保持干净、整洁.必须以合格的产品转序.5.抽样检验规则1)正常检验批量检查采用GB 2828-87中的一次抽样方案,如批量总数为150片,则样本数位20片.批合格质量水平(AQL)如下所示:AQL取值:— A类不合格品为0.65(性能/尺寸样本数以总样本数的值采用特殊检验水平S-3级正常一次抽样方案)—B类不合格品为1.0(样本数以批量数取样本值,一般检验水平Ⅱ级正常一次抽检方案)—C类不合格品为0.65(样本数以抽样包装箱、袋数取样本值,一般检验水平Ⅱ级正常一次抽检方案)2)加严检验当正常检验时,在连续5批中有两批检验不合格,则从下批起转到加严检验(母体数是150片,抽样32片)3)从加严检验转为正常检验当进行加严检验时,若连续5批检验合格时,则从下批起转到正常检验。
3D镜片检测规范
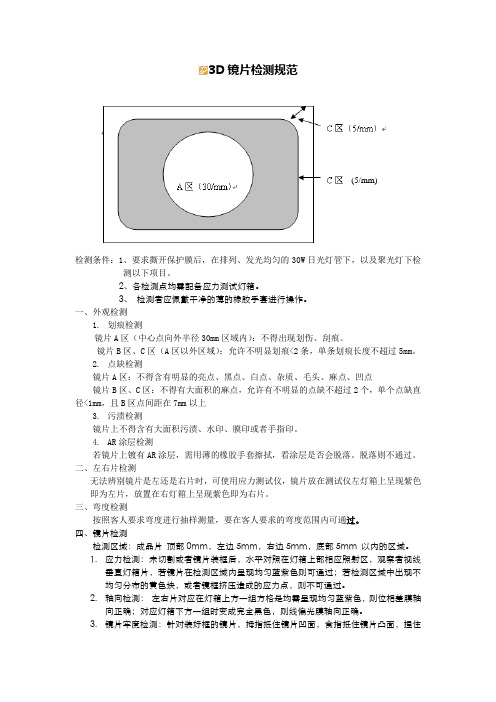
3D镜片检测规范检测条件:1、要求撕开保护膜后,在排列、发光均匀的30W日光灯管下,以及聚光灯下检测以下项目。
2、各检测点均需配备应力测试灯箱。
3、检测者应佩戴干净的薄的橡胶手套进行操作。
一、外观检测1.划痕检测镜片A区(中心点向外半径30mm区域内):不得出现划伤、刮痕。
镜片B区、C区(A区以外区域):允许不明显划痕<2条,单条划痕长度不超过5mm。
2.点缺检测镜片A区:不得含有明显的亮点、黑点、白点、杂质、毛头、麻点、凹点镜片B区、C区:不得有大面积的麻点,允许有不明显的点缺不超过2个,单个点缺直径<1mm,且B区点间距在7mm以上3.污渍检测镜片上不得含有大面积污渍、水印、膜印或者手指印。
4.AR涂层检测若镜片上镀有AR涂层,需用薄的橡胶手套擦拭,看涂层是否会脱落。
脱落则不通过。
二、左右片检测无法辨别镜片是左还是右片时,可使用应力测试仪,镜片放在测试仪左灯箱上呈现紫色即为左片,放置在右灯箱上呈现紫色即为右片。
三、弯度检测按照客人要求弯度进行抽样测量,要在客人要求的弯度范围内可通过。
四、镜片检测检测区域:成品片顶部0mm,左边5mm,右边5mm,底部5mm 以内的区域。
1.应力检测:未切割或者镜片装框后,水平对照在灯箱上部相应照射区,观察者视线垂直灯箱片,若镜片在检测区域内呈现均匀蓝紫色则可通过;若检测区域中出现不均匀分布的黄色块,或者镜框挤压造成的应力点,则不可通过。
2.轴向检测:左右片对应在灯箱上方一组方格是均需呈现均匀蓝紫色,则位相差膜轴向正确;对应灯箱下方一组时变成完全黑色,则线偏光膜轴向正确。
3.镜片牢度检测:针对装好框的镜片,拇指抵住镜片凹面,食指抵住镜片凸面,捏住镜片捻转并大力向内外推拉,若镜片轻易掉落则不能通过。
4.颗粒检测:直径≤0.3mm5.刮伤检测:宽度≤0.5mm,长度≤2mm6.气泡检测:直径≤0.3mm7.纤维丝检测:宽度≤0.5mm,长度≤2mm8.明显的缺陷:直径≤1.5mm(例如污点、水渍等等)9.指纹印/模糊印:清晰的镜片上不能有指纹印或模糊印。
光学镜片外观检作业规范
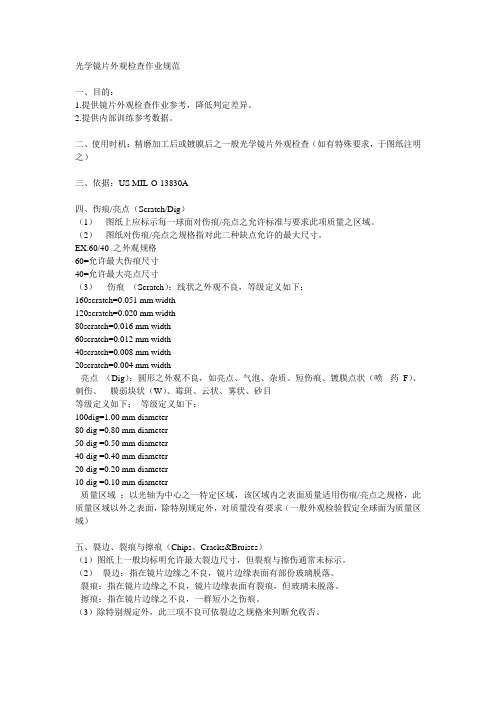
光学镜片外观检查作业规范一、目的:1.提供镜片外观检查作业参考,降低判定差异。
2.提供内部训练参考数据。
二、使用时机:精磨加工后或镀膜后之一般光学镜片外观检查(如有特殊要求,于图纸注明之)三、依据:US MIL-O-13830A四、伤痕/亮点(Scratch/Dig)(1)图纸上应标示每一球面对伤痕/亮点之允许标准与要求此项质量之区域。
(2)图纸对伤痕/亮点之规格指对此二种缺点允许的最大尺寸。
EX.60/40 之外观规格60=允许最大伤痕尺寸40=允许最大亮点尺寸(3)--伤痕(Scratch):线状之外观不良,等级定义如下:160scratch=0.051 mm width120scratch=0.020 mm width80scratch=0.016 mm width60scratch=0.012 mm width40scratch=0.008 mm width20scratch=0.004 mm width--亮点(Dig):圆形之外观不良,如亮点、气泡、杂质、短伤痕、镀膜点状(喷-药F)、刺伤、膜弱块状(W)、霉斑、云状、雾状、砂目等级定义如下:等级定义如下:100dig=1.00 mm diameter80 dig =0.80 mm diameter50 dig =0.50 mm diameter40 dig =0.40 mm diameter20 dig =0.20 mm diameter10 dig =0.10 mm diameter--质量区域:以光轴为中心之一特定区域,该区域内之表面质量适用伤痕/亮点之规格,此质量区域以外之表面,除特别规定外,对质量没有要求(一般外观检验假定全球面为质量区域)五、裂边、裂痕与擦痕(Chips、Cracks&Bruises)(1)图纸上一般均标明允许最大裂边尺寸,但裂痕与擦伤通常未标示。
(2)--裂边:指在镜片边缘之不良,镜片边缘表面有部份玻璃脱落。
光学镜片标准
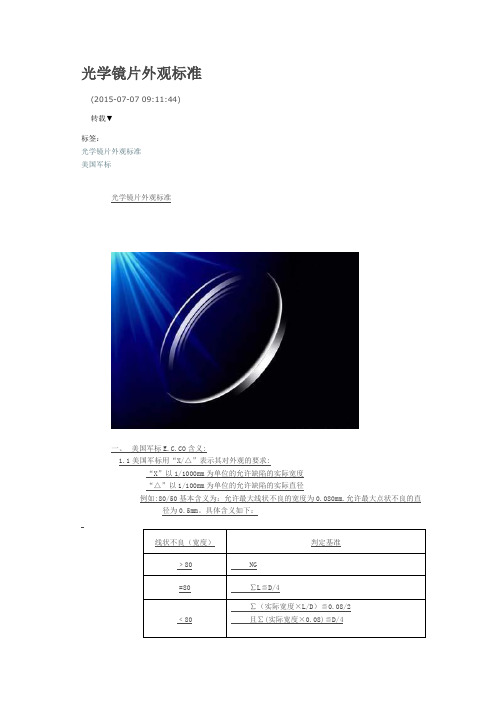
光学镜片外观标准(2015-07-07 09:11:44)转载▼标签:光学镜片外观标准美国军标光学镜片外观标准一、美国军标E.C.CO含义:1.1美国军标用“X/△”表示其对外观的要求:“X”以1/1000mm为单位的允许缺陷的实际宽度“△”以1/100mm为单位的允许缺陷的实际直径例如:80/50基本含义为:允许最大线状不良的宽度为0.080mm.允许最大点状不良的直径为0.5mm。
具体含义如下:线状不良(宽度)判定基准﹥80 NG=80∑L≦D/4﹤80∑(实际宽度×L/D)≦0.08/2且∑(实际宽度×0.08)≦D/4以上字母的含义:L:线状不良的长度D:圆形镜片D=光线有效直径方形镜片=2√长(有效径)﹒宽(有效径)/II棱镜线状不良:D=2√∑各个面积(有效径)/II点状不良:D=2√面积(有效径)/IIN=允许的不良个数一、美国军标的含义:例如:80/50基本含义为:允许最大线状不良的宽度为0.080mm.允许最大点状不良的直径为0.5mm。
2.1.1伤痕:线状划伤的外观不良.2.1.2斑孔:圆点状凹坑之外观不良.2.1.3品质区域:以光轴为中心的一个圆形区域。
在该区域内、表面品质适用伤痕/斑孔的要求。
在此区域外,除特别规定外,无对表面品质之要求。
2.2伤痕的判定基准:2.2.1仅有标准的最大伤痕时:L=1/4*D2.2.2同时有最大伤痕与较小伤痕时:L=1/4*D L+L′=1/2*D2.2.3仅有较小标准的伤痕时: L′=D说明: L:允许最大伤痕总长度D:镜片表面直径L′较小的伤痕换算成最大等值伤痕长度L′∑(实际伤痕/标准最大伤痕)*实际伤痕的长度例1:标准为80/40,镜片直径40mm的镜片,检查镜片表面后发现伤痕如下:#80 伤痕8mm判定:L8mm﹤1/4*40mm=10mm 本片允收例2:标准为80/40,镜片直径40mm的镜片,检查镜片表面后发现伤痕如下:#80 伤痕8mm ; #60 伤痕4mm ; #40 伤痕6mm 判定:L=8mmL=(60/80)*4mm+(40/80)*6mm =6mmL+L=14mm﹤1/2*40mm 本片允收例3:标准80/40,镜片直径40mm的镜片,检查镜片表面后发现伤痕如下:#60 伤痕8mm; #40 伤痕6mm; #20 伤痕8mm判定:L=(60/80)*8mm +(40/80)*6mm+(20/80)*8mm=11mm﹤40mm 本片允收注意:镀膜后膜层上的伤痕标准依图面,伤痕/斑孔的规定应单独计算,不与加工的不良混合。
光学透镜检验标准
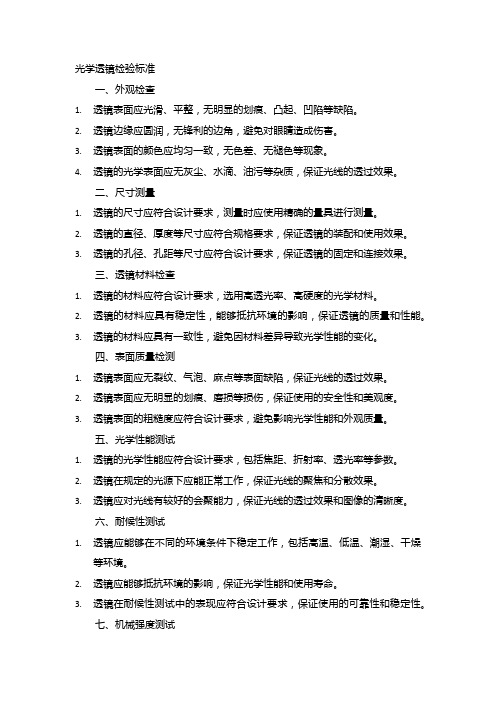
光学透镜检验标准一、外观检查1.透镜表面应光滑、平整,无明显的划痕、凸起、凹陷等缺陷。
2.透镜边缘应圆润,无锋利的边角,避免对眼睛造成伤害。
3.透镜表面的颜色应均匀一致,无色差、无褪色等现象。
4.透镜的光学表面应无灰尘、水滴、油污等杂质,保证光线的透过效果。
二、尺寸测量1.透镜的尺寸应符合设计要求,测量时应使用精确的量具进行测量。
2.透镜的直径、厚度等尺寸应符合规格要求,保证透镜的装配和使用效果。
3.透镜的孔径、孔距等尺寸应符合设计要求,保证透镜的固定和连接效果。
三、透镜材料检查1.透镜的材料应符合设计要求,选用高透光率、高硬度的光学材料。
2.透镜的材料应具有稳定性,能够抵抗环境的影响,保证透镜的质量和性能。
3.透镜的材料应具有一致性,避免因材料差异导致光学性能的变化。
四、表面质量检测1.透镜表面应无裂纹、气泡、麻点等表面缺陷,保证光线的透过效果。
2.透镜表面应无明显的划痕、磨损等损伤,保证使用的安全性和美观度。
3.透镜表面的粗糙度应符合设计要求,避免影响光学性能和外观质量。
五、光学性能测试1.透镜的光学性能应符合设计要求,包括焦距、折射率、透光率等参数。
2.透镜在规定的光源下应能正常工作,保证光线的聚焦和分散效果。
3.透镜应对光线有较好的会聚能力,保证光线的透过效果和图像的清晰度。
六、耐候性测试1.透镜应能够在不同的环境条件下稳定工作,包括高温、低温、潮湿、干燥等环境。
2.透镜应能够抵抗环境的影响,保证光学性能和使用寿命。
3.透镜在耐候性测试中的表现应符合设计要求,保证使用的可靠性和稳定性。
七、机械强度测试1.透镜应具有一定的抗冲击能力,能够在一定程度的冲击下不发生破裂或变形。
2.透镜的固定方式应牢固可靠,能够保证透镜在使用中的稳定性和安全性。
3.透镜的机械强度应符合设计要求,保证使用的耐久性和稳定性。
八、防尘防水测试1.透镜应具有较好的防尘防水性能,能够在一定的尘埃和水分环境下正常工作。
2.透镜的密封性能应符合设计要求,保证使用的可靠性和安全性。
镜片检验作业指导书
4.2.16包边不良:针对镜片四周边缘的油漆覆盖不够,造成边缘不够油漆的现象。
检验项目
抽样方案
检查水平
AQL
判定数组
6.3.1
6.3.2.4
6.3.2.5
GB/T2828.1正常检验一次抽样
Ⅱ
A(0,1)
B=1.0
C=2.5
7
6.3.2.3
定数抽样
n=3,B类不合格:Ac=0,Re=1
序号
缺陷名称
检验条件及判定标准
允收数
A区
B区
C区
1
注点
D<0.2,S<0.3,DS>30
0
1
2
0.3<D<0.5,0.3<S<0.5,DS>30
0
1
1
2
硬划伤
不允许
3
软划伤
L<2,W<0.2,DS>30
0
0
1
2<L<3,0.2<W<0.3,DS>30
0
0
1
4
飞油
L<0.3或参照限度样品。
不允许
5
色差
6.3.2.2
定数抽样
n=10,B类不合格:Ac=0,Re=1
n=10,C类不合格:Ac=1,Re=2
5、抽样方案
6、检验项目,技术要求及判定标准
6.1、相关规定
6.1.1外观检验条件
6.1.1.1光源:物件距光源0.65~1.0m的40W日光灯下
6.1.1.2目视距离:30-40cm
6.1.1.3目视角度:检测面与人眼方向成45°~90°
光学镜片外观检作业规范
光学镜片外观检查作业规范一、目的:1.提供镜片外观检查作业参考,降低判定差异。
2.提供内部训练参考数据。
二、使用时机:精磨加工后或镀膜后之一般光学镜片外观检查(如有特殊要求,于图纸注明之)三、依据:US MIL-O-13830A四、伤痕/亮点(Scratch/Dig)(1)图纸上应标示每一球面对伤痕/亮点之允许标准与要求此项质量之区域。
(2)图纸对伤痕/亮点之规格指对此二种缺点允许的最大尺寸。
EX.60/40 之外观规格60=允许最大伤痕尺寸40=允许最大亮点尺寸(3)--伤痕(Scratch):线状之外观不良,等级定义如下:160scratch=0.051 mm width120scratch=0.020 mm width80scratch=0.016 mm width60scratch=0.012 mm width40scratch=0.008 mm width20scratch=0.004 mm width--亮点(Dig):圆形之外观不良,如亮点、气泡、杂质、短伤痕、镀膜点状(喷-药F)、刺伤、膜弱块状(W)、霉斑、云状、雾状、砂目等级定义如下:等级定义如下:100dig=1.00 mm diameter80 dig =0.80 mm diameter50 dig =0.50 mm diameter40 dig =0.40 mm diameter20 dig =0.20 mm diameter10 dig =0.10 mm diameter--质量区域:以光轴为中心之一特定区域,该区域内之表面质量适用伤痕/亮点之规格,此质量区域以外之表面,除特别规定外,对质量没有要求(一般外观检验假定全球面为质量区域)五、裂边、裂痕与擦痕(Chips、Cracks&Bruises)(1)图纸上一般均标明允许最大裂边尺寸,但裂痕与擦伤通常未标示。
(2)--裂边:指在镜片边缘之不良,镜片边缘表面有部份玻璃脱落。
光学外观40_20检验标准
光学外观40_20检验标准
一、表面平整度
1.外观表面应平整,无明显的凹凸不平、波纹、变形等现象。
2.表面粗糙度应在Ra 0.2以下。
二、表面光洁度
1.外观表面应光洁,无明显的麻点、划痕、锈蚀等现象。
2.表面光泽度应在50%以上。
三、表面色彩均匀性
1.外观表面的色彩应均匀,无明显的色差、色斑等现象。
2.色彩应符合设计要求。
四、反光性
1.外观表面应具有一定的反光性能,但不能过于强烈,以免影响视觉舒适度。
2.反光性能应符合设计要求。
五、表面污染物
1.外观表面应清洁,无灰尘、油污、指纹等污染物。
2.清洁度应符合相关标准要求。
六、表面划痕
1.外观表面不应有明显的划痕,如有轻微划痕,应在可接受范围内。
2.对于硬质材料的外观表面,如玻璃、金属等,划痕深度不得超过0.05mm。
七、形状尺寸精度
1.外观形状应符合设计要求,尺寸精度应在公差范围内。
2.对于有特殊形状要求的外观,如球面、非球面等,形状精度应符合相关标
准要求。
八、角度精度
1.对于有角度要求的外观表面,角度精度应在公差范围内。
2.角度精度包括但不限于倾斜角、旋转角等。
九、光学性能测试
1.外观表面应具有一定的透光性能,透光率应在设计要求范围内。
2.对于具有光学功能的外观,如反射镜、棱镜等,应测试其光学性能是否符
合设计要求。
十、防紫外线性能
1.外观表面应具有一定的防紫外线性能,能有效阻挡紫外线穿透。
2.防紫外线性能应符合相关标准要求。
光学镜片检验标准国标
光学镜片检验标准国标光学镜片是日常生活中常见的光学元件之一,广泛应用于眼镜、相机、显微镜等光学设备中。
为了保证光学镜片的质量,确保其在使用过程中具有良好的成像效果和可靠性,制定了一系列的光学镜片检验标准国标。
本文将详细介绍光学镜片检验的相关标准和方法,并提供具体的实例说明。
一、光学镜片检验标准国标的基本概念和定义1.1 光学镜片光学镜片是用于将光线聚焦或分散的一种光学元件,包括凸透镜、凹透镜、平面镜等。
1.2 光学镜片检验光学镜片检验是针对光学镜片的光学性能、物理性能、外观缺陷等方面进行的一系列检测和评估工作。
国标是指由中国标准化组织制定的标准,用于统一产品质量要求和检验方法的技术规范。
二、光学镜片检验标准国标的主要内容2.1 光学性能检验光学性能检验是评估光学镜片成像效果的重要指标。
国标规定了光学镜片的球差、色差、畸变等性能参数的检验方法和标准值。
2.1.1 球差检验球差是指光线通过透镜时由于折射率的差异而导致的不同焦距的现象。
国标规定了球差的数值范围,通常使用经验公式和检验仪器进行评估和检验。
2.1.2 色差检验色差是指透镜在不同波长光线下折射率的差异,导致成像时产生的色差现象。
国标规定了色差的范围和评价方法,常用的检验仪器包括分光光度计和色差仪等。
2.1.3 畸变检验畸变是指光线通过透镜后,由于透镜形状或透镜表面曲率不均匀而导致成像时的畸变现象。
国标规定了畸变的检验方法和标准,常用的检验手段包括透镜曲率半径仪和光线追迹仪等。
2.2 物理性能检验物理性能检验是评估光学镜片的耐磨性、耐冲击性等力学性能的重要标准。
国标规定了光学镜片在耐磨、耐冲击、耐温变化等方面的检验方法和标准。
2.2.1 耐磨性检验耐磨性是指光学镜片在使用条件下抵抗表面划伤和磨损的能力。
国标规定了耐磨性检验的方法和标准,包括磨损试验机、针尖硬度计等设备的使用。
2.2.2 耐冲击性检验耐冲击性是指光学镜片在受到外力撞击时不会破裂或产生裂纹的能力。
- 1、下载文档前请自行甄别文档内容的完整性,平台不提供额外的编辑、内容补充、找答案等附加服务。
- 2、"仅部分预览"的文档,不可在线预览部分如存在完整性等问题,可反馈申请退款(可完整预览的文档不适用该条件!)。
- 3、如文档侵犯您的权益,请联系客服反馈,我们会尽快为您处理(人工客服工作时间:9:00-18:30)。
光学镜片外观检查作业规范
一、目的:
1、提供镜片外观检查作业参考,降低判定差异。
2、提供内部训练参考数据。
二、使用时机:精磨加工后或镀膜后之一般光学镜片外观检查(如有特殊要求,于图纸注明之)
三、依据:US MIL-O-13830A
四、伤痕/亮点(Scratch/Dig)
(1)图纸上应标示每一球面对伤痕/亮点之允许标准与要求此项质量之区域。
(2)图纸对伤痕/亮点之规格指对此二种缺点允许的最大尺寸。
EX、60/40 之外观规格
60=允许最大伤痕尺寸
40=允许最大亮点尺寸
(3) --伤痕(Scratch):线状之外观不良,等级定义如下:
160scratch=0、051 mm width
120scratch=0、020 mm width
80scratch=0、016 mm width
60scratch=0、012 mm width
40scratch=0、008 mm width
20scratch=0、004 mm width
--亮点(Dig):圆形之外观不良,如亮点、气泡、杂质、短伤痕、镀膜点状(喷-药F)、刺伤、膜弱块状(W)、霉斑、云状、雾状、砂目
等级定义如下: 等级定义如下:
100dig=1、00 mm diameter
80 dig =0、80 mm diameter
50 dig =0、50 mm diameter
40 dig =0、40 mm diameter
20 dig =0、20 mm diameter
10 dig =0、10 mm diameter
--质量区域:以光轴为中心之一特定区域,该区域内之表面质量适用伤痕/亮点之规格,此质量区域以外之表面,除特别规定外,对质量没有要求(一般外观检验假定全球面为质量区域)
五、裂边、裂痕与擦痕(Chips、Cracks&Bruises)
(1)图纸上一般均标明允许最大裂边尺寸,但裂痕与擦伤通常未标示。
(2)--裂边:指在镜片边缘之不良,镜片边缘表面有部份玻璃脱落。
--裂痕:指在镜片边缘之不良,镜片边缘表面有裂痕,但玻璃未脱落。
--擦痕:指在镜片边缘之不良,一群短小之伤痕。
(3)除特别规定外,此三项不良可依裂边之规格来判断允收否。
六、脏污或霉斑(Stain)
(1)脏污或霉斑:指镜片表面变色的区域,如水痕、口水、泡沫状、雾状、云状、刺孔状…等等,由于镀膜前镜片表面不干净而覆盖于膜下。
(2)可由透视法或反射法发现
<і>一般依照伤痕/亮点之规格来判断允收否。
<іі>水痕之边线依照伤痕之规格来判断允收否。
七、外观检验应具备事项:
(1)图纸:标示外观要求之规格与区域。
(2)标准板:标示外观之标准伤痕/亮点之参考样板。
(3)检验条件:20W 的日光灯(或100W 的灯泡)。
(4)检验环境:前、上、下、左、右均为黑色之不反光物。
(5)放大镜(4 倍):检查#60 或#60 以下之伤痕。
八、检查方式:
(1)透视法:镜片置于光源前四方形孔之前3 公分偏下,稍微倾斜镜片检验的检验方法。
(2)反射法:镜片置于灯光下的桌面上,前后稍微摇晃镜片的检验方法。
不论透视法或反射法,被测面均朝向检查员。
九、伤痕(Scratch)之判断标准:
(1)只有最大伤痕时:
L’=≦1/4×D 允收
(2)同时有最大伤痕与较小伤痕时:
L’=Σ【(W/N)×L】≦1/2×D 允收
(3)只有较小伤痕时:
L’=Σ【(W/N)×L】≦D 允收
L’=伤痕换算之总长度
W=伤痕宽度
N=要求之伤痕规格
L=该级伤痕长度
D=镜片表面直镜
(4) EX、1:规格为80/50,镜片直径40mm 的镜片,检查镜片表面后,发现伤痕如下:
#80 伤痕8mm
L’=8mm≦1/4×40=10mm=>允收
EX、2:规格为80/50 镜片直径8、2mm 的镜片检查镜片表面后,发现伤痕如下:
#80 伤痕8mm,#60 伤痕4mm,#40 伤痕6mm
L’=(80/80)×8+(60/80)×4+(40/80)×6=14mm≦【1/2×40=20mm】=>允收
EX、3:规格为80/50,镜片直径40mm 的镜片,检查镜片表面后,发现伤痕如下:
#60 伤痕8mm,#40 伤痕6mm,#20 伤痕8mm
L’=(60/80)×8+(40/80)×6+(20/80)×8=10mm≦40mm=>允收L’=(60/80)×8+(40/80)×6+(20/80)×8=10mm≦40mm=>允收
(5)镀膜后之反射膜的伤痕标准依照图纸”伤痕/亮点”之规格判定。
十、亮点(Dig)之判断标准:
(1)只有最大亮点时:
N’≦D/(20mm)
允收
D/(20mm)<1 时以D/(20mm)=1 计算(即镜片表面直径<20mm)
(2)同时有最大亮点与较小亮点时: N’=Σ【(d’/d×N)】≦2×(D/(20mm))允收
N’=亮点换算之最多允许个数d=亮点大小
d=要求之亮点规格
N=该级亮点个数
D=镜片表面直径
(3)EX、1:规格为80/50,镜片直径12mm 的镜片,检查镜片表面后,发现亮点如下:
#50 亮点1 个
N’=1 个=(12/20=1 个) 允收
EX、2:规格为80/50,镜片直径40mm 的镜片,检查镜片表面后,发现亮点如下: #50 亮点1 个
N’=1 个≦(40/20=2 个) 允收
EX、3:规格为80/50,镜片直径40mm 的镜片,检查镜片表面后,发现亮点如下: #50 亮点1 个,#40 亮点1 个,#20 亮点3 个
N’=(50/50)×1+(40/50)×1+(20/50)×3=3 个≦2×(40/20)=4 个=>允收EX、4:规格为80/50,镜片直径40mm 的镜片,检查镜片表面后,发现亮点如下: #50 亮点0 个,#40 亮点2 个,#20 亮点5 个
N’=(50/50)×0+(40/50)×2+(20/50)×5=3、6 个≦2×(40/20)=4 个=>允收
(4)镀膜后反射检查膜上之亮点标准依照图纸伤痕/亮点的规格
(5)计算等值亮点时,0、002mm 至0、005mm 的亮点可忽略
十一、简易换算表:
(1)伤痕(Scratch)
最大伤痕→
伤痕规格↓
#120
#80
#60
#40
#20
#10
#120
1/4D
1、5D
2、0D
3、0D
6、0D
12、0D
#80
1/4D
1、3D
2、0D
4、0D
8、0D
#60
1/4D
1、5D
3、0D
6、0D
#40
1/4D
2、0D
4、0D
#20
1/4D
2、0D
#10
1/4D
(2)亮点(Dig)
直径(mm)
允收最大亮点数
允收最大等值亮点数0-20
1
2
20-40
2
4
40-60
3
6
60-80
4
8
80-100
5
10
100-120
6
12
120-140
7
14。