低温渗氮技术的类型
低温化学热处理方法——离子渗氮

低温化学热处理方法——离子渗氮1、原理简述离子渗氮时,首先用真空泵向炉内抽气,当真空度达到1.33Pa后,通入氨、氮混合气体,至炉压升至约70Pa时接通电源,在阴极(工件)与阳极间施加直流电压,使炉内气体放电,其伏安特性曲线如下图所示。
当阴阳极电压升到下图中c点对应的数值时,工件上开始产生辉光,这个电压称为辉光点燃电压。
起辉后极间电压陡降,随后电流在电源电压增加而极间电压基本不变的情况下不断增大。
此时工件上辉光的覆盖面迅速增大,至图中d点工件表面完全被辉光覆盖,cd段称为正常辉光区。
超过d点时电流再增加,阴阳电压也上升。
极间电压达到e点后又开始陡降,此时开始发生弧光放电。
de段称为异常辉光区,e点以后称为弧光放电区。
离子渗氮通常是在异常辉光区进行。
在这个区段可通过控制电压调节电流,从而控制工件的加热温度,但注意避免弧光放电。
电源控制系统应能在发生弧光时自动切断电源熄灭弧光,然后自动点燃辉光,继续工作。
▲气体放电的伏安特性曲线在真空离子渗氮炉中,氮氢混合气体中的氮被电离成离子,它们轰击钢件表面,使之溅射出铁原子,并与等离子区的氮原子及电子结合形成化合物FeN,FeN吸附在工件表面后,又在离子轰击作用下逐步分解为低价氮化物和氮原子,使之渗入工件内部。
因此,氮由气相转入固相而实现渗氮主要是通过碰撞离解产生的大量活性氮原子渗入工件来实现的。
2、离子渗氮层性能(1)渗氮层的硬度渗层的硬度及其分布,是衡量渗氮效果和使用性能的主要指标。
离子渗氮与常规渗氮工艺相比,在硬度方面无明显差别。
但离子渗氮可以通过调节工艺参数来控制渗层组织,获得理想的、平缓的硬度分布。
碳钢、铸铁的化合物层薄,硬度低(<800HV),主要靠固溶强化,扩散层的硬度仅比心部略高(300~500HV)。
含合金氮化物形成元素的钢,如结构钢、工具钢、高速钢等经离子渗氮后,由于高硬度的合金氮化物弥散强化作用,而使得表面具有很高的硬度。
(2)耐磨性足够厚的化合物层,具有较好的抗腐蚀、耐磨损的能力。
渗氮

渗氮求助编辑渗氮,是在一定温度下一定介质中使氮原子渗入工件表层的化学热处理工艺。
常见有液体渗氮、气体渗氮、离子渗氮。
传统的气体渗氮是把工件放入密封容器中,通以流动的氨气并加热,保温较长时间后,氨气热分解产生活性氮原子,不断吸附到工件表面,并扩散渗入工件表层内,从而改变表层的化学成分和组织,获得优良的表面性能。
如果在渗氮过程中同时渗入碳以促进氮的扩散,则称为氮碳共渗。
常用的是气体渗氮和离子渗氮。
目录编辑本段一般以提高金属的耐磨性为主要目的,因此需要获得高的表面硬度。
它适用于38CrMoAl等渗氮钢。
渗氮后工件表面硬度可达HV850~1200。
渗氮温度低,工件畸变小,可用于精度要求高、又有耐磨要求的零件,如镗床镗杆和主轴、磨床主轴、气缸套筒等。
但由于渗氮层较薄,不适于承受重载的耐磨零件。
气体参氮可采用一般渗氮法(即等温渗氮)或多段(二段、三段)渗氮法。
前者是在整个渗氮过程中渗氮温度和氨气分解率保持不变。
温度一般在480~520℃之间,氨气分解率为15~30%,保温时间近80小时。
这种工艺适用于渗层浅、畸变要求严、硬度要求高的零件,但处理时间过长。
多段渗氮是在整个渗氮过程中按不同阶段分别采用不同温度、不同氨分解率、不同时间进行渗氮和扩散。
整个渗氮时间可以缩短到近50小时,能获得较深的渗层,但这样渗氮温度较高,畸变较大。
还有以抗蚀为目的的气体渗氮,渗氮温度在 550~700℃之间,保温0.5~3小时,氨分解率为35~70%,工件表层可获得化学稳定性高的化合物层,防止工件受湿空气、过热蒸汽、气体燃烧产物等的腐蚀。
正常的气体渗氮工件,表面呈银灰色。
有时,由于氧化也可能呈蓝色或黄色,但一般不影响使用。
编辑本段离子渗氮又称辉光渗氮,是利用辉光放电原理进行的。
把金属工件作为阴极放入通有含氮介质的负压容器中,通电后介质中的氮氢原子被电离,在阴阳极之间形成等离子区。
在等离子区强电场作用下,氮和氢的正离子以高速向工件表面轰击。
最全的渗碳和渗氮区别整理表格
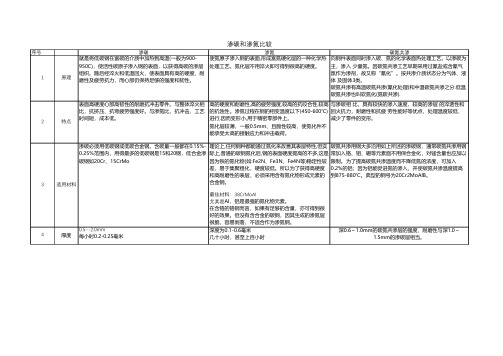
序号渗碳和渗氮比较12特点表面高硬度心部高韧性的耐磨抗冲击零件。
与整体淬火相比,抗挤压、抗弯疲劳强度好。
与渗氮比,抗冲击,工艺时间短,成本低。
高的硬度和耐磨性,高的疲劳强度,较高的抗咬合性,较高的抗蚀性。
渗氮过程在钢的相变温度以下(450-600℃)进行,因而变形小,用于精密零部件上。
氮化层较薄,一般0.5mm、且脆性较高,使氮化件不能承受太高的接触应力和冲击载荷。
渗碳渗氮就是将低碳钢在富碳的介质中加热到高温(一般为900-950C),使活性碳原子渗入钢的表面,以获得高碳的渗层组织。
随后经淬火和低温回火,使表面具有高的硬度、耐磨性及疲劳抗力,而心部仍保持足够的强度和韧性。
使氮原子渗入钢的表面,形成富氮硬化层的一种化学热处理工艺。
氮化层不用淬火即可得到很高的硬度。
原理碳氮共渗向钢件表面同时渗入碳、氮的化学表面热处理工艺。
以渗碳为主,渗入 少量氮。
因碳氮共渗工艺早期采用过氰盐或含氰气氛作为渗剂,故又称“氰化”。
按共渗介质状态分为气体、液体 及固体3类。
碳氮共渗有高温碳氮共渗(氰化处理)和中温碳氮共渗之分.低温碳氮共渗也叫软氮化(氮碳共渗).与渗碳相 比,具有较快的渗入速度,较高的渗层 的淬透性和回火抗力,耐磨性和抗疲 劳性能好等优点,处理温度较低,减少了零件的变形。
3适用材料渗碳必须用低碳钢或低碳合金钢。
含碳量一般都在0.15%-0.25%范围内,用得最多的低碳钢是15和20钢,低合金渗碳钢如20Cr、15CrMo理论上,任何钢种都能通过氮化来改善其表层特性,但实际上,普通的碳钢氮化后,钢的表面硬度提高的不多,这是因为铁的氮化物(如:Fe2N、Fe3N、Fe4N等)稳定性较差,易于集聚粗化,硬度较低。
所以为了获得高硬度和高耐磨性的表层,必须采用含有氮化物形成元素的合金钢。
最佳材料:38CrMoAl尤其是AI,铝是最强的氮化物元素。
在含铬的铬钢而言,如果有足够的含量,亦可得到很好的效果。
但没有含合金的碳钢,因其生成的渗氮层很脆,容易剥落,不适合作为渗氮钢。
盘点生产中最常用的渗氮工艺
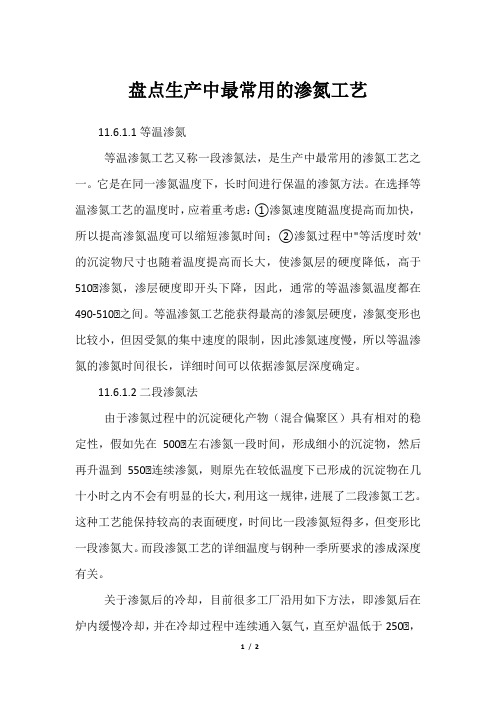
盘点生产中最常用的渗氮工艺11.6.1.1等温渗氮等温渗氮工艺又称一段渗氮法,是生产中最常用的渗氮工艺之一。
它是在同一渗氮温度下,长时间进行保温的渗氮方法。
在选择等温渗氮工艺的温度时,应着重考虑:①渗氮速度随温度提高而加快,所以提高渗氮温度可以缩短渗氮时间;②渗氮过程中"等活度时效'的沉淀物尺寸也随着温度提高而长大,使渗氮层的硬度降低,高于510℃渗氮,渗层硬度即开头下降,因此,通常的等温渗氮温度都在490-510℃之间。
等温渗氮工艺能获得最高的渗氮层硬度,渗氮变形也比较小,但因受氮的集中速度的限制,因此渗氮速度慢,所以等温渗氮的渗氮时间很长,详细时间可以依据渗氮层深度确定。
11.6.1.2二段渗氮法由于渗氮过程中的沉淀硬化产物(混合偏聚区)具有相对的稳定性,假如先在500℃左右渗氮一段时间,形成细小的沉淀物,然后再升温到550℃连续渗氮,则原先在较低温度下已形成的沉淀物在几十小时之内不会有明显的长大,利用这一规律,进展了二段渗氮工艺。
这种工艺能保持较高的表面硬度,时间比一段渗氮短得多,但变形比一段渗氮大。
而段渗氮工艺的详细温度与钢种一季所要求的渗成深度有关。
关于渗氮后的冷却,目前很多工厂沿用如下方法,即渗氮后在炉内缓慢冷却,并在冷却过程中连续通入氨气,直至炉温低于250℃,甚至150℃才出炉。
其动身点是避开冷却时工件变形,以及避开工件表面氧化,保持银灰色的外观。
但这种传统的渗氮后冷却方法有值得商榷之处。
1)渗氮零件变形主要不是发生在渗后冷却阶段。
渗氮温度并不高,即使渗后出炉空冷,甚至油冷,大多数零件也不至于变形超差。
为了掌握畸变而规定炉冷至250℃,一般而言是不合理的。
2)渗氮后提前出炉,会在工件表面消失氧化色,但只是形成一层很薄的氧化膜,并不会影响渗氯层的性能。
最近的讨论还表明,氧化膜具有减小摩擦系数的作用,所以要求渗氮零件表面保持银灰色也是不必要的。
3)在低温下,特殊是在400 ℃以下,炉冷的速度非常缓慢,到250℃以下,需要几十小时,采纳炉冷低温出炉的工艺使生产效率和设备利用率显著降低,氨的消耗量增加。
低温渗氮工艺

低温渗氮工艺
低温渗氮是一种常用的金属表面处理工艺,它可以显著改善材料的硬度、耐磨性和耐腐蚀性能。
该工艺主要适用于钢材和铸铁等金属材料,通过在低温条件下将氮气与金属表面进行反应,使氮原子渗透到材料表面形成氮化物层。
这个层具有极高的硬度和耐磨性,能够有效地提高金属材料的使用寿命与性能。
低温渗氮工艺分为硬化渗氮和氮化渗氮两种方式。
硬化渗氮主要适用于低碳钢和合金钢材料,它通过将材料加热至渗氮温度以下,然后用氨气反应使氮原子渗入材料表面,形成氮化物层。
而氮化渗氮工艺则适用于高碳钢和铸铁等材料,其渗氮温度一般较低,可以防止材料退火和热变形的发生。
低温渗氮工艺具有以下优点:
1. 渗氮温度较低,不会引起较大的热变形和退火现象,可以保持材料的原有尺寸和形状。
2. 渗氮层硬度高、耐磨性好,能够有效提高材料的机械性能和使用寿命。
3. 渗氮层的耐腐蚀性能优越,能够在一定程度上提高材料的抗腐蚀性。
4. 渗氮工艺简单,操作方便,能够适应不同材料和工件的处理需求。
需要注意的是,在进行低温渗氮工艺时,必须注意控制温度和气氛的稳定性,避免过渡渗氮或渗氮不足的情况发生。
同时,还需注意保护工艺中的耐火材料和设备,以确保渗氮工艺的顺利进行。
总之,低温渗氮工艺是一种重要的金属表面处理方式,通过渗氮可以有效改善材料的性能,延长其使用寿命。
在实际应用中,应根据具体材料的要求选择合适的渗氮方式和条件,以获得最佳的处理效果。
碳氮共渗与氮碳共渗的区别

渗碳:渗碳后的工件经淬火和低温回火,使表面具有高硬度和耐磨性,而心部仍保持良好的塑性和韧性,从而满足工件外硬内韧的使用要求。
渗氮:零件渗氮后表面形成一层氮化物,不需要淬火就可以具有高的硬度、耐磨性、抗疲劳性和一定的腐蚀性,而且变形也很小。
三者比较而言以等离子效果最佳,气体渗氮次之,碳氮共渗最差。
碳氮共渗:又称氰化。碳氮共渗是将钢件表面同时渗入碳原子和氮原子,形成碳氮共渗层,以提高工件的硬度、耐磨性和疲劳强度的处理方法。
等离子氮化由于其温度低、渗氮周期短(温度为500-520℃,时间为12至15小时)组织由ε相、γ相组成,基本不含有脆性ξ相,从而使热应力和组织应力大为降低,变形量小,不易开裂,可作为最终工序。
气体渗氮温度一般为500~560看出温度虽然不高,但时间很长,其热应力就大。组织由ε相、γ相组成,处理不好时有脆性ξ相。
气体软氮化(碳氮共渗)温度常用560-570℃,因该温度下氮化层硬度值最高。氮化时间常为2-3小时,因为超过2.5小时,随时间延长,氮化层深度增加很慢。 可以看出碳氮共渗的温度最高,其组织由ε相、γ相和含氮的渗碳体Fe3(C,N)所组成,所以热应力和组织应力都较前两者大,再者渗层薄,所以不能承受重载。但这种处理也有优点,由于软氮化层不存在脆性ξ相,故氮化层硬而具有一定的韧性,不容易剥落。
低温渗氮技术更节约热处理能源
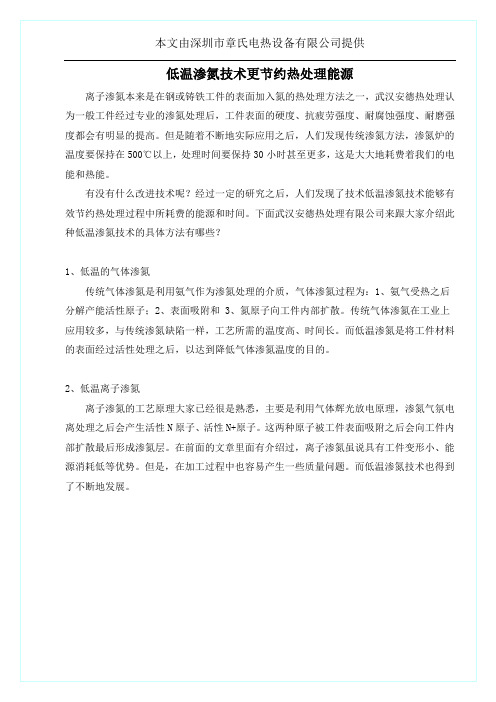
1、低温的气体渗氮
传统气体渗氮是利用氨气作为渗氮处理的介质,气体渗氮过程为:1、氨气受热之后分解产能活性原子;2、表面吸附和3、氮原子向工件内部扩散。传统气体渗氮在工业上应用较多,与传统渗氮缺陷一样,工艺所需的温度高、时间长。而低温渗氮是将工件材料的表面经过活性处理之后,以达到降低气体渗氮温度的目的。
2、低温离子渗氮
离子渗氮的工艺原理大家已经很是熟悉,主要是利用气体辉光放电原理,渗氮气氛电离处理之后会产生活性N原子、活性N+原子。这两种原子被工件表面吸附之后会向工件内部扩散最后形成渗氮层。在前面的文章里面有介绍过,离子渗氮虽说具有工件变形小、能源消耗低等优势。但是,在加工过程中也容易产生一些质量问题。而低温渗氮技术也得到了不断地发展。
低温渗氮技术更节约热处理能源
离子渗氮本来是在钢或铸铁工件的表面加入氮的热处理方法之一,武汉安德热处理认为一般工件经过专业的渗氮处理后,工件表面的硬度、抗疲劳强度、耐腐蚀强度、耐磨强度都会有明显的提高。但是随着不断地实际应用之后,人们发现传统渗氮方法,渗氮炉的温度要保持在500℃以上,处理时间要保持30小时甚至更多,这是大大地耗费着我们的电能和热能。
低温渗氮技术的类型
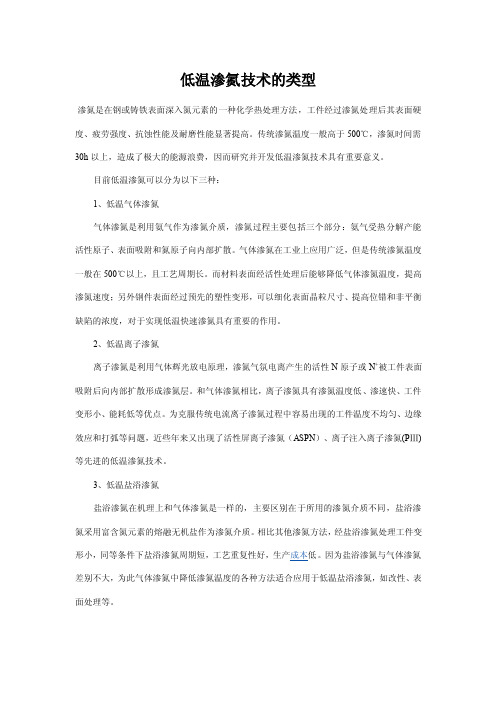
低温渗氮技术的类型渗氮是在钢或铸铁表面深入氮元素的一种化学热处理方法,工件经过渗氮处理后其表面硬度、疲劳强度、抗蚀性能及耐磨性能显著提高。
传统渗氮温度一般高于500℃,渗氮时间需30h以上,造成了极大的能源浪费,因而研究并开发低温渗氮技术具有重要意义。
目前低温渗氮可以分为以下三种:1、低温气体渗氮气体渗氮是利用氨气作为渗氮介质,渗氮过程主要包括三个部分:氨气受热分解产能活性原子、表面吸附和氮原子向内部扩散。
气体渗氮在工业上应用广泛,但是传统渗氮温度一般在500℃以上,且工艺周期长。
而材料表面经活性处理后能够降低气体渗氮温度,提高渗氮速度;另外钢件表面经过预先的塑性变形,可以细化表面晶粒尺寸、提高位错和非平衡缺陷的浓度,对于实现低温快速渗氮具有重要的作用。
2、低温离子渗氮离子渗氮是利用气体辉光放电原理,渗氮气氛电离产生的活性N原子或N+被工件表面吸附后向内部扩散形成渗氮层。
和气体渗氮相比,离子渗氮具有渗氮温度低、渗速快、工件变形小、能耗低等优点。
为克服传统电流离子渗氮过程中容易出现的工件温度不均匀、边缘效应和打弧等问题,近些年来又出现了活性屏离子渗氮(ASPN)、离子注入离子渗氮(PⅢ)等先进的低温渗氮技术。
3、低温盐浴渗氮盐浴渗氮在机理上和气体渗氮是一样的,主要区别在于所用的渗氮介质不同,盐浴渗氮采用富含氮元素的熔融无机盐作为渗氮介质。
相比其他渗氮方法,经盐浴渗氮处理工件变形小,同等条件下盐浴渗氮周期短,工艺重复性好,生产成本低。
因为盐浴渗氮与气体渗氮差别不大,为此气体渗氮中降低渗氮温度的各种方法适合应用于低温盐浴渗氮,如改性、表面处理等。
目前低温渗氮技术已得到了工业应用,但仍存在着一些问题,如低温条件下的渗氮速度,另外一些预先处理,如活性、表面处理的附加的渗氮成本,这些将是今后的研究方向。
- 1、下载文档前请自行甄别文档内容的完整性,平台不提供额外的编辑、内容补充、找答案等附加服务。
- 2、"仅部分预览"的文档,不可在线预览部分如存在完整性等问题,可反馈申请退款(可完整预览的文档不适用该条件!)。
- 3、如文档侵犯您的权益,请联系客服反馈,我们会尽快为您处理(人工客服工作时间:9:00-18:30)。
低温渗氮技术的类型
渗氮是在钢或铸铁表面深入氮元素的一种化学热处理方法,工件经过渗氮处理后其表面硬度、疲劳强度、抗蚀性能及耐磨性能显著提高。
传统渗氮温度一般高于500℃,渗氮时间需30h以上,造成了极大的能源浪费,因而研究并开发低温渗氮技术具有重要意义。
目前低温渗氮可以分为以下三种:
1、低温气体渗氮
气体渗氮是利用氨气作为渗氮介质,渗氮过程主要包括三个部分:氨气受热分解产能活性原子、表面吸附和氮原子向内部扩散。
气体渗氮在工业上应用广泛,但是传统渗氮温度一般在500℃以上,且工艺周期长。
而材料表面经活性处理后能够降低气体渗氮温度,提高渗氮速度;另外钢件表面经过预先的塑性变形,可以细化表面晶粒尺寸、提高位错和非平衡缺陷的浓度,对于实现低温快速渗氮具有重要的作用。
2、低温离子渗氮
离子渗氮是利用气体辉光放电原理,渗氮气氛电离产生的活性N原子或N+被工件表面吸附后向内部扩散形成渗氮层。
和气体渗氮相比,离子渗氮具有渗氮温度低、渗速快、工件变形小、能耗低等优点。
为克服传统电流离子渗氮过程中容易出现的工件温度不均匀、边缘效应和打弧等问题,近些年来又出现了活性屏离子渗氮(ASPN)、离子注入离子渗氮(PⅢ)等先进的低温渗氮技术。
3、低温盐浴渗氮
盐浴渗氮在机理上和气体渗氮是一样的,主要区别在于所用的渗氮介质不同,盐浴渗氮采用富含氮元素的熔融无机盐作为渗氮介质。
相比其他渗氮方法,经盐浴渗氮处理工件变形小,同等条件下盐浴渗氮周期短,工艺重复性好,生产成本低。
因为盐浴渗氮与气体渗氮差别不大,为此气体渗氮中降低渗氮温度的各种方法适合应用于低温盐浴渗氮,如改性、表面处理等。
目前低温渗氮技术已得到了工业应用,但仍存在着一些问题,如低温条件下的渗氮速度,另外一些预先处理,如活性、表面处理的附加的渗氮成本,这些将是今后的研究方向。