煤制天然气工艺简介(最新终极版)
天然气化工技术(最终版)
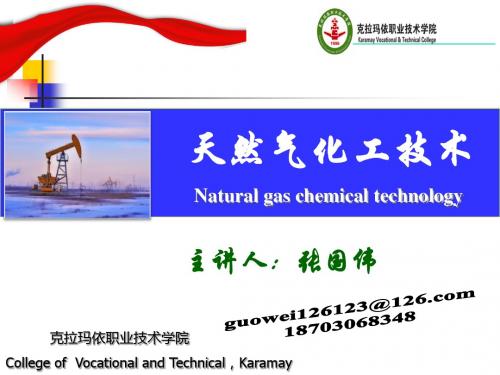
LNG,NGLs,CNG,GTL和LPG的典型组成
天然气主要成分是%以上的甲烷,还含有乙烷以及少量氮、硫、磷等。 天然气主要成分是%以上的甲烷,还含有乙烷以及少量氮、硫、磷等。
1.2 天然气资源的蕴藏形式 (1) 气田:天然气单独蕴藏,主要成分是甲烷,有的甲烷含 量高达99%以上。油田气中C5以上烷烃能以“气体汽油 ”形式分离出来,称为凝析油。 (2) 油田气或油田伴生气:天然气与石油共生,多为湿气。 其中丙烷、丁烷能以“液化气体”的形式分离出来,称 “液化石油气”(Liquefied Petroleum Gas, LPG)。
及其衍生产品是用天然气和天然气凝析液为原料的。
许多天然气转化的化学品不仅是重要的化工基础原料而且也是新的清洁燃 料。在经济、环境与能源问题的驱动下,生产环境友好清洁燃料成为天然
气化工技术的新命题。其中,氢、甲醇、二甲醚(DME) 和天然气制合成
油(GTL) 等新技术日益受到人们的关注。
中国天然气加工工艺路线
西气东输
西气东输,我国距离最长、口径最大的输气管道,西起塔里木盆地的轮南,东至上 海,全长4200千米。全线采用自动化控制,供气范围覆盖中原、华东、长江三角洲 地区。自新疆塔里木轮南油气田,向东经过库尔勒、吐鲁番、鄯善、哈密、柳园、 酒泉、张掖、武威、兰州、定西、宝鸡、西安、洛阳、信阳、合肥、南京、常州等 地区,仅以一、二线工程每年输送的天然气量计算,就可以少烧燃煤12千万吨,减 少CO2排放2亿吨、减少SO2排放226万吨。
开发步伐,为天然气的化工利用开辟更大的发展空间。
传统的天然气化工利用主要是用天然气制备合成气,并进一步加工成其它下 游产品。
由合成气制备甲醇、合成氨、DME等化学品的工艺革新与优化仍然是国际上 重要的研究课题,特别是着眼于新型催化剂研制与工艺节能降耗。
煤制天然气工艺过程
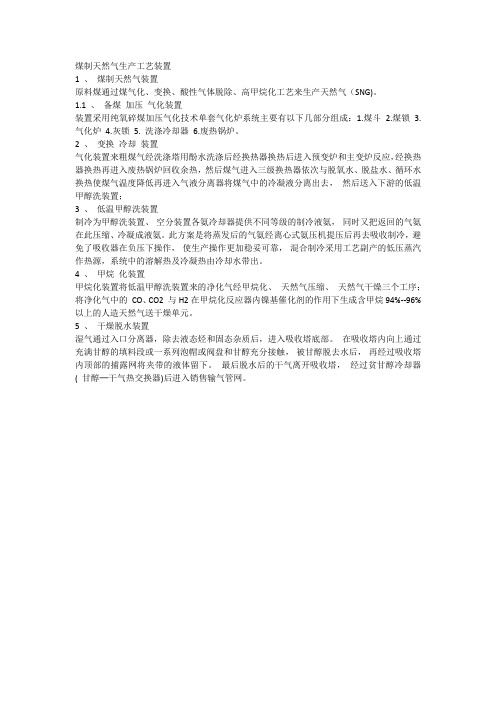
煤制天然气生产工艺装置
1 、煤制天然气装置
原料煤通过煤气化、变换、酸性气体脱除、高甲烷化工艺来生产天然气(SNG)。
1.1 、备煤加压气化装置
装置采用纯氧碎煤加压气化技术单套气化炉系统主要有以下几部分组成:1.煤斗 2.煤锁 3.气化炉4.灰锁5. 洗涤冷却器6.废热锅炉。
2 、变换冷却装置
气化装置来粗煤气经洗涤塔用酚水洗涤后经换热器换热后进入预变炉和主变炉反应,经换热器换热再进入废热锅炉回收余热,然后煤气进入三级换热器依次与脱氧水、脱盐水、循环水换热使煤气温度降低再进入气液分离器将煤气中的冷凝液分离出去,然后送入下游的低温甲醇洗装置;
3 、低温甲醇洗装置
制冷为甲醇洗装置、空分装置各氨冷却器提供不同等级的制冷液氨,同时又把返回的气氨在此压缩、冷凝成液氨。
此方案是将蒸发后的气氨经离心式氨压机提压后再去吸收制冷,避免了吸收器在负压下操作,使生产操作更加稳妥可靠,混合制冷采用工艺副产的低压蒸汽作热源,系统中的溶解热及冷凝热由冷却水带出。
4 、甲烷化装置
甲烷化装置将低温甲醇洗装置来的净化气经甲烷化、天然气压缩、天然气干燥三个工序;将净化气中的CO、CO2 与H2在甲烷化反应器内镍基催化剂的作用下生成含甲烷94%--96%以上的人造天然气送干燥单元。
5 、干燥脱水装置
湿气通过入口分离器,除去液态烃和固态杂质后,进入吸收塔底部。
在吸收塔内向上通过充满甘醇的填料段或一系列泡帽或阀盘和甘醇充分接触,被甘醇脱去水后,再经过吸收塔内顶部的捕露网将夹带的液体留下。
最后脱水后的干气离开吸收塔,经过贫甘醇冷却器( 甘醇─干气热交换器)后进入销售输气管网。
【推荐下载】煤制天然气生产工艺 煤制天然气发展前景
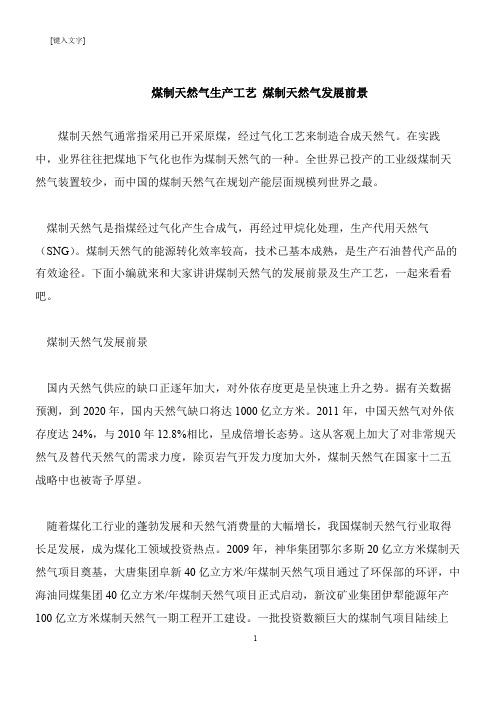
[键入文字]
煤制天然气生产工艺煤制天然气发展前景
煤制天然气通常指采用已开采原煤,经过气化工艺来制造合成天然气。
在实践中,业界往往把煤地下气化也作为煤制天然气的一种。
全世界已投产的工业级煤制天然气装置较少,而中国的煤制天然气在规划产能层面规模列世界之最。
煤制天然气是指煤经过气化产生合成气,再经过甲烷化处理,生产代用天然气(SNG)。
煤制天然气的能源转化效率较高,技术已基本成熟,是生产石油替代产品的有效途径。
下面小编就来和大家讲讲煤制天然气的发展前景及生产工艺,一起来看看吧。
煤制天然气发展前景
国内天然气供应的缺口正逐年加大,对外依存度更是呈快速上升之势。
据有关数据预测,到2020年,国内天然气缺口将达1000亿立方米。
2011年,中国天然气对外依存度达24%,与2010年12.8%相比,呈成倍增长态势。
这从客观上加大了对非常规天然气及替代天然气的需求力度,除页岩气开发力度加大外,煤制天然气在国家十二五战略中也被寄予厚望。
随着煤化工行业的蓬勃发展和天然气消费量的大幅增长,我国煤制天然气行业取得长足发展,成为煤化工领域投资热点。
2009年,神华集团鄂尔多斯20亿立方米煤制天然气项目奠基,大唐集团阜新40亿立方米/年煤制天然气项目通过了环保部的环评,中海油同煤集团40亿立方米/年煤制天然气项目正式启动,新汶矿业集团伊犁能源年产100亿立方米煤制天然气一期工程开工建设。
一批投资数额巨大的煤制气项目陆续上
1。
煤基天然气的开发与利用
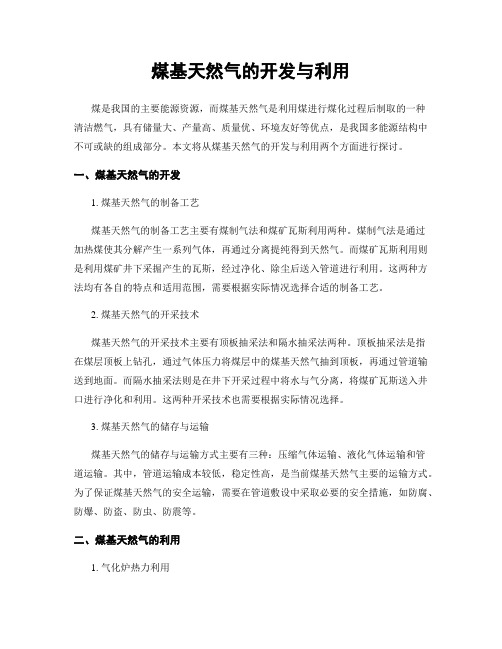
煤基天然气的开发与利用煤是我国的主要能源资源,而煤基天然气是利用煤进行煤化过程后制取的一种清洁燃气,具有储量大、产量高、质量优、环境友好等优点,是我国多能源结构中不可或缺的组成部分。
本文将从煤基天然气的开发与利用两个方面进行探讨。
一、煤基天然气的开发1. 煤基天然气的制备工艺煤基天然气的制备工艺主要有煤制气法和煤矿瓦斯利用两种。
煤制气法是通过加热煤使其分解产生一系列气体,再通过分离提纯得到天然气。
而煤矿瓦斯利用则是利用煤矿井下采掘产生的瓦斯,经过净化、除尘后送入管道进行利用。
这两种方法均有各自的特点和适用范围,需要根据实际情况选择合适的制备工艺。
2. 煤基天然气的开采技术煤基天然气的开采技术主要有顶板抽采法和隔水抽采法两种。
顶板抽采法是指在煤层顶板上钻孔,通过气体压力将煤层中的煤基天然气抽到顶板,再通过管道输送到地面。
而隔水抽采法则是在井下开采过程中将水与气分离,将煤矿瓦斯送入井口进行净化和利用。
这两种开采技术也需要根据实际情况选择。
3. 煤基天然气的储存与运输煤基天然气的储存与运输方式主要有三种:压缩气体运输、液化气体运输和管道运输。
其中,管道运输成本较低,稳定性高,是当前煤基天然气主要的运输方式。
为了保证煤基天然气的安全运输,需要在管道敷设中采取必要的安全措施,如防腐、防爆、防盗、防虫、防震等。
二、煤基天然气的利用1. 气化炉热力利用气化炉是煤基天然气生产的核心设备,其废热可以用来供暖、发电等方面。
目前,很多工厂和热电联产项目都利用气化炉废热进行能源回收,提高能源利用效率。
2. 气化燃烧发电气化燃烧发电是利用煤基天然气发电的一种方式,其具有环保、高效、资源可持续利用等优点。
同时,煤基天然气发电技术已经逐渐成熟,具备大规模商业化应用的条件。
3. 气化替代燃料煤基天然气可以替代传统燃料,如天然气、燃油、煤等,用于民用热水、供暖和工业生产等方面。
利用煤基天然气替代传统燃料可以大幅度降低能源消耗和环境污染。
煤制天然气工艺

注:上述反应为吸热反应,氧气作用是燃烧部分碳 提供过程所需热能。
(b) 气体的净化,主要是脱除酸性气体CO2和含硫化合物。 (c) 利用水煤气变换反应调节H2 / CO 大约为 3 : 1。
CO + H2O CO2 + H2 ΔH = - 41 kJ / mol (d) 甲烷化反应
CO + 3H2 CH4 + H2O ΔH = - 206 kJ / mol CO2 + 4H2 CH4 + 2H2O ΔH = - 165 kJ / mol
➢ 2008 年11 月,新奥集团煤基甲烷项目投料的试车成功(产品甲烷含 量达95. 67 %) 表明煤基甲烷化的可行性,为日后建设大型煤基甲 烷生产装置积累了宝贵的经验。
概况
❖ 市场供不应求投资天然气利润巨大
➢ 2000~2008年,我国天然气消费量 年均增长16.2%。
➢ 以同等热值计算,天然气目前价格 均低于油、电、液化气的价格,价 格与价值不相符。
➢ 丹麦托普索公司1978 年在美国建成7.2万m3/d 的合成天然气厂, 1981 年由于油价降低,被迫关停。最近, 托普索公司为美国某公司 完成了一个420万m3/d合成天然气工厂的前期工作。
➢ 1984 年美国大平原建成389万m3/d 的煤制天然气工厂, 产品气含甲 烷96%, 该厂建成至今, 正常运行20 多年。
煤直接甲烷化
➢ 煤在一定的温 度和压力下用煤 直接制产品富甲 烷气的工艺。
基本原理
❖ 煤间接甲烷化过程
(a) 在水蒸汽和氧气存在下, 气化煤来生产合成气(H2 + CO)。
C + H2O CO + H2
ΔH = 135 kJ / mol
煤制天然气

在气提塔内进行,液 硫被通过其中的空气
十单击一此、处编煤辑母制版天标题然样式气
概述
1
煤制天然气工艺
2
天然气脱硫
3
4
Page 1
第单击一此节处编、辑概母版述标题样式
煤制天然气是指煤经过气化产生合成气,再经过甲烷 化处理,生产代用天然气(SNG)。
是生产石油
优
替代产品
势
的有效途径
Page 2
耗水量较低 转化效率较高 环境影响较小
1000Nm3甲烷需要4.8吨煤作为原料和燃料。
三、甲烷化
主要反应:
CO + 3H2 = CH4 + H2O CO2 + 4H2 = CH4 + 2H2O
1. 反应热的撤热问题 2. 甲烷化工艺回路(稀释法、冷激法) 3. 多级反应器串联(三级甲烷化) 4. 甲烷合成的压力(高压力利于甲烷化和缩小设备体积) 5. 甲烷化反应的产物( 大量CH4、微量N2,H2,CO,CO2 ) 6. 甲烷化催化剂(还原镍、RHM-266, M-349, MCR-2X)
反应 机理
工艺 流程
化学 药剂
Page 8
最重要,保证溶液的稳定性和 操作的连续性。有利于硫磺的生 成和沉降,抑制副反应的发生。
第单击三此节处编、辑天母版然标气题样脱式硫
一、天然气脱硫与硫磺回收结合新工艺
H2S(g)+
OH- = 细菌
HS-
+
H2O2.
生物脱硫技术
HS- + 1/2O2 = S0 + OH-
第单击一此节处编、辑概母版述标题样式
一、煤制天然气的必要性
我国的能源消费情况和能源格局 煤化工行业发展及天然气消费量增长 能源效率最高,是最有效的煤炭转化利用方式
煤是怎样变成天然气的
相关知识:煤是怎样变成天然气的
煤制天然气通常指采用已开采原煤,经过气化工艺来制造合成天然气,在实践中,通常把煤气化产生合成气,再经过甲烷化处理,生产代用天然气。
煤制天然气主要包括三个工艺过程构成:
一是煤气化,原料煤在煤气化装置中与空分装置来的高纯氧气和中压蒸汽进行反应制得粗煤气;
二是粗煤气净化,粗煤气经一定的装置脱硫脱碳后,制成所需的净煤气;
三是甲烷化,净煤气进入甲烷化装置处理,生产出优质的天然气。
煤制气热值比天然气热值低,但其制取方便,可自备设备自行生产,在我国天然气供应不足的当前是不可替代的一种热源气体。
煤制气因其诸多优势,被广大工矿企业应用,并且也被用做生活用气。
第十一章 煤制天然气
反应温度对H2S转化率的影响: 1)高温区域: 2)低温区域: 3)硫磺的存在方式
Page
12
单击此处编辑母版标题样式 第三节、天然气脱硫——硫磺回收工艺 各种不同的实现方式区别在于脱硫装置的酸气质量 我们根据不同的酸气组成,设计不同的酸气进料方式。 ④.过程气再热方式 ①.直流法
优先选择
特点: ⑴ 燃烧炉 ⑵ 一级催化剂 ⑶ 二级催化剂
一、天然气脱硫与硫磺回收结合新工艺
1. Lo-cot工艺
证溶液的稳定性和 操作的连续性。有利于硫磺的生 成和沉降,抑制副反应的发生。
Page
9
单击此处编辑母版标题样式 第三节、天然气脱硫
一、天然气脱硫与硫磺回收结合新工艺
H2S(g)+ OH- = HS- + H2O 细菌 HS- + 1/2O2 = S0 + OH-
Lurgi 气化技术, 煤制天然气装置的 投资为:1亿Nm3 甲烷的投资大约为 5-7亿元 Lurgi 气化技术, 煤制天然气装置的 过程能量利用率为 56.6%,比较高 (主产业链较短)
Page
4
成本
投资
能耗
单击此处编辑母版标题样式 第二节、煤制天然气工艺
一、工艺组成:
煤气化、空分、部分变换、净化(低温甲醇洗)、甲烷化
Page 7
单击此处编辑母版标题样式 三级甲烷化工艺流程图
第一级:650-700℃;第二级:500℃左右;第三级:350℃左右
Page 8
单击此处编辑母版标题样式 第三节、天然气脱硫
H2S的吸收:H2S + H2O = H2S(水相)+ H2O 一步电离: H2S(水相)=H+ + HS二步电离: HS- = H+ + S2吸收(氧化)反应:2Fe3+ + S2- = 2Fe2+ + S0 氧气吸收: O2 + H2O = 2O(水相)+ H2O 再生(还原):2Fe2+ + O(水相)+ H+ =2Fe3+ + H2O 总反应:H2S +1/2 O2 = H2O + S0 总副反应:2HS- +3/2 O2 = H2S2O3
煤制气项目主要技术介绍
生产加工建筑材料
专业公司回收
主要技术介绍——三废处理
含硫气体
低温甲醇洗,克劳 斯硫回收等工艺回
收利用硫元素
废气
二氧化碳
碳捕集后用于工业生 产如石油驱采剂
主要技术介绍——三废处理
含有酚氨物质
青岛科技大技术 华南理工技术 赛鼎公司技术
鲁奇技术 经过萃取,汽提以及 生物发酵等工段回收 分解大部分有机物质
优点: 气化压力高最高可达8.5MPa,气化温度高 因而粗煤气中不含酚和焦油类物质
缺点: 对煤炭成浆性有要求,耐火砖、喷嘴寿命 低,渣阀磨损严重,黑水含固量高易发生 堵塞,冷煤气效率低
专利技术商:美国通用公司
GE气化炉示意图
运行案例:运行案例较多,据不完全统 计国内外有20多个项目采用GE气化炉
主要技术介绍——对置多喷嘴气化炉
对原料煤的要求以及优缺点与GE类似,只 是喷嘴对置,避免喷嘴更换或损坏带来的 停车,操作连续性高
专利技术商:华东理工大学
运行案例:在国内煤化工领域有较多应用业绩
对置多喷嘴气化炉示意图
主要技术介绍——多元料浆气化炉
对原料煤的要求以及优缺点与GE类似,只 是煤浆有单一的煤水混合物扩大为含碳的 固液混合物
BGL气化炉示意图
优点: 熔融排渣,气化用水蒸气量、污水量较鲁奇少
缺点: 粉煤率高,存在偏烧,污水中酚含量较鲁奇高
专利技术商:上海泽马克
运行案例:云南解化,金新化工,中煤图克
主要技术介绍——GE气化炉
原料煤要求: 发热量大于25MJ/Kg,灰分含量低于15% 最好低于12%,挥发分大于25%(wt),内水 ≤8%,灰熔点低于1300℃,可磨性好
项目 煤制天然气
项目能效 基本 先进值 要求 ≥56% ≥60%
煤气化加氢制天然气的原理
煤气化加氢制天然气的原理煤气化加氢制天然气是利用煤炭资源进行气化,然后通过一系列的反应步骤,生成并提纯天然气的一种工艺方法。
煤气化是将固态煤炭在高温和缺氧或氧不足的情况下转化为气体燃料的过程。
在煤气化过程中,首先需要将煤炭粉末与一定量的氧气或气化剂混合,然后通过加热使混合物发生化学反应,产生煤气。
在这一步骤中,煤炭中的有机物质被分解成一系列气体组分,如一氧化碳、氢气、二氧化碳、甲烷等。
这些气体组分共同组成了煤气。
接下来,煤气需要进一步处理,除去其中的灰尘、硫化物、氮化物等不纯物质,以保证后续反应的进行。
处理方法主要包括煤气净化和煤气脱硫等工艺。
净化过程中,常用的方法是通过引导煤气通过过滤器,将其中的固体颗粒和灰尘去除。
而脱硫则是使用吸收剂将煤气中的硫化物吸收,并与之发生化学反应,从而去除硫化物。
处理过后的煤气进入加氢反应器,进行加氢反应。
在加氢反应中,煤气与一定量的氢气反应,生成更多的甲烷和水蒸气。
加氢反应是通过将煤气中的一氧化碳和二氧化碳转化为甲烷和水蒸气,来增加甲烷含量和提高天然气质量。
加氢反应需要催化剂的存在,常用的催化剂有镍基和铁基催化剂。
经过加氢反应后,生成的气体混合物被送入分离装置进行分离。
分离装置通常采用冷却和压力变化的方法,将煤气中的水蒸气和杂质分离出来。
通过这种方式,可以得到高纯度的天然气。
分离后的天然气可以通过压缩和液化等方式进行储存和运输。
煤气化加氢制天然气的原理基本上是将煤炭粉末在高温和缺氧的条件下进行气化,生成煤气,然后对煤气进行净化、脱硫、加氢等处理,提高甲烷含量和天然气质量,最后通过分离装置分离和提纯天然气。
这种工艺能够有效利用煤炭资源,将其转化为天然气,是一种具有潜力的替代化石燃料的方法。
- 1、下载文档前请自行甄别文档内容的完整性,平台不提供额外的编辑、内容补充、找答案等附加服务。
- 2、"仅部分预览"的文档,不可在线预览部分如存在完整性等问题,可反馈申请退款(可完整预览的文档不适用该条件!)。
- 3、如文档侵犯您的权益,请联系客服反馈,我们会尽快为您处理(人工客服工作时间:9:00-18:30)。
• (三)变换冷却
• 变换冷却装置为两系列,单系列变换包括1台 洗涤塔、2台预变换炉、1台主变换炉等设备。 • 其工艺原理是通过钴钼催化剂使一氧化碳与水 蒸气反应生成二氧化碳和氢气,从而降低一氧 化碳含量和提高氢气含量(即调整氢碳比), 目的是使煤气组分符合甲烷合成的要求。
• 具体工艺是:煤经由煤锁加入气化炉,自中压 蒸汽管网来的蒸汽与空分装置提供的氧气混合 后作为气化剂,通过气化炉底部的旋转炉篦上 的分布孔进入气化炉内;煤在气化炉内由上向 下移动,而气化剂由下向上流动与煤逆流接触 ,在此过程中煤经干燥、干馏、气化和氧化后 ,只有灰渣残留下来形成灰渣层(可大致的由 上至下将其划分为干燥区、干馏区、气化区、 氧化区和灰区),灰渣经旋转炉篦排入灰锁, 再由灰锁经泄压后排至水力除渣系统。
备煤装置工艺流程示意图
汽 运 原 料 煤
10~50mm
10mm以下
• (二)气化
• 气化装置分为两系列,单系列为8台气化炉(7 开1备),正常运行时单台气化炉氧负荷为 6777Nm3/h,炉压为4.0MPa,单台气化炉产 粗煤气气量为49000 Nm3/h,汽氧比通常在 5—6之间。
• 气化装置主要由气化炉、洗涤冷却器、废热锅 炉、煤斗、煤锁、灰锁、灰膨胀冷却器及水力 除渣系统等组成。
• 出气化炉的粗煤气首先进入洗涤冷却器,利 用高压喷射煤气水对粗煤气进行洗涤冷却, 除去大部分的煤粉、焦油、酚氨等杂质并冷 却到200℃之后进入废热锅炉,在废锅内粗煤 气与脱盐水换热使煤气温度降至180℃后(压 力为3.9MPa)送往变换装置,同时副产 0.6MPa的低压蒸汽进入低压蒸汽管网。洗涤 冷却器下部的液体排至废锅,与废热锅炉下 部的冷凝液一同送往煤气水分离装置。
• 主生产装置中,气化采用纯氧固定床碎煤加压气化技术,以 氧气和蒸汽作为气化剂与原料煤发生复杂的气化反应产生粗 煤气(主要成分包括甲烷、氢气、一氧化碳、二氧化碳以及 氨酚、焦油、中油、石脑油等),经酚水喷淋洗涤除去煤尘 、氨酚、焦油、中油再经废锅冷却后进入变换装置。
• 变换装置是通过钴钼催化剂使一氧化碳与水蒸气反应生成二氧 化碳和氢气,从而降低一氧化碳含量和提高氢气含量(即调整 氢碳比),目的是使煤气组份符合甲烷合成的要求。其主要工 艺流程就是粗煤气经换热器预热后进入预变炉和主变炉(炉内 均装有钴钼催化剂)进行变换反应,反应后的煤气经换热器冷 却后送入煤气冷却装置。 • 煤气冷却就是通过换热器利用脱氧水、脱盐水和循环水逐级对 煤气进行冷却后送入低温甲醇洗。 • 粗煤气中含带的氨、酚、焦油、中油等被酚水洗涤吸收后进入 煤气水分离装置,利用泄压闪蒸的原理将煤气水中的气体解吸 出去,然后利用重力沉降的原理将焦油和中油分别分离出去, 剩下的酚水送入酚回收装置。 • 酚水进入酚回收装置先经预净化脱除酸性气体,然后进入脱氨 塔脱除氨并送往氨回收;之后酚水再进入萃取塔用二异丙基醚 作为萃取剂将酚萃取出来,之后再通过精馏塔将二异丙基醚和 酚分离出来从而得到产品粗酚,二异丙基醚作为萃取剂循环使 用;脱酚后废水送往污水处理。 • 来自酚回收装置的氨水进入氨回收装置先经过预处理,然后进 入氨精馏塔进行精馏,从而得到产品液氨,脱氨后废水送往污 水处理。
• 水处理车间
• 热电车间 • 电气车间 • 仪表车间 • 化机车间
• 化验车间ຫໍສະໝຸດ 全厂总流程方块图电能供全厂
蒸汽 液 氨 粗煤气 副线
煤 气 水
氨 气
粗煤气 空气 硫化氢
净煤气
天 然 气 天 然 气
氧气
酚水
氨水
天然气首站
全厂电气主接线示意图
国网
110KV母线
1 号主变
2 号主变
35KV母线
1号发 电机 60000 KW
煤制天然气工艺简介
新疆庆华能源集团有限公司 2011.10
• 一、概述
全厂工艺流程简述
• 本项目为年产55亿立方米煤制天然气工程,共 分为四期。全部建成后共有四系列备煤装置( 两座12万吨圆形储煤仓)、 64台气化炉、8套变换冷却、16套煤气水分离 、8套酚回收、4套氨回收、8套低温甲醇洗、 8套混合制冷、4套硫回收、2座全厂火炬、4 套甲烷化、4套压缩干燥、8套五万立空分、 10台锅炉、7台汽轮发电机组等装置。
•
•
二、各装置具体工艺流程
• (一)备煤 • 备煤装置为两系个列,单系列处理能 力为2000T/H,圆形储煤仓的储存能 力为12万吨(可供一期装置正常运行 7天)。
• 由汽车运来的原料煤进入汽车卸煤槽,经叶轮给煤机 送入带式输送机,然后煤通过电液动三通分料器可分 为两路运送,一路送入圆形储煤仓(煤可通过堆取料 机由输煤皮带送入破碎筛分楼),另一路送入破碎筛 分楼,经分级破碎机破碎后进入驰张筛进行筛分,筛 下物(≤10mm的碎煤)通过输煤皮带送往热电锅炉, 而筛上物(粒度在10mm—50mm之间)通过输煤皮 带送往气化。当热电锅炉用煤和气化用煤量不匹配, 且锅炉用煤量不能满足要求时,则一部分煤不进入驰 张筛,而是直接进入四齿辊破碎机,破碎后的煤与驰 张筛的筛下物混合送往热电锅炉。
气化装置工艺流程示意图
煤
蒸 汽 去 管 网 粗煤气去变换
煤气水
灰
去 煤 气 水 分 离
煤锁和灰锁加煤、排灰示意图
煤 来 自 煤 斗
煤锁泄压气
灰 来 自 气 化 炉
灰锁泄压气
充压用二氧化碳
充压用中压蒸汽
煤 去 气 化 炉
灰 去 渣 池
煤锁加煤过程:
• 粒度为10-50mm的原料煤通过皮带加入煤 斗,煤锁泄压完成后打开煤锁上锥阀,煤 进入煤锁至正常料位后关闭煤锁上锥阀。 • 打开煤锁充压阀,用来自低温甲醇洗的二 氧化碳进行充压,直至煤锁压力与气化炉 内压力相同,然后关闭煤锁充压阀。
• 一期工程消耗煤炭641T/h,512.8万吨/年 (其中原料煤365.6万吨,燃料煤147.2万 吨)
• 一期工程用水量2000T/h,1600万吨/年
• 一期工程用电8.5万KWh(其中自发电7.5万 KWh,受网电1万KWh)
一期工程年产焦油49600吨、中 油55360吨、石脑油19200吨、 粗酚20160吨、硫磺13667吨、 硫铵30880吨。
•
因低温甲醇洗使用的是低温甲醇,所以必须由外部装置提供冷量。 混合制冷装置的作用就是为低温甲醇洗提供冷量;其工艺流程就是 利用蒸气透平离心式压缩机将来自低温甲醇洗的氨气压缩后进入吸 收器用贫氨水吸收后变为浓氨水,之后再进入精馏塔进行精馏,得 到的纯氨气经冷却后变为液氨,然后将液氨送到低温甲醇洗作为制 冷剂。液氨经蒸发制冷后变为氨气再重新回到压缩机进行压缩,如 此往复循环使用。
本装置采用的主要工艺技术:
• 纯氧碎煤加压气化(鲁奇技术) • 粗煤气耐油耐硫变换 • 低温甲醇洗 • 混合制冷
• 超优克劳斯硫回收
• 甲烷化(引进丹麦托普索技术) • 内压缩空气分离 • 循环流化床锅炉(一期为循环流化床,二、三、四期 为粉煤锅炉) • 生化污水处理
本项目生产车间设置:
• 气化车间 • 净化车间 • 甲烷化车间 • 空分车间
来自低温甲醇洗的硫化氢气体作为生产硫磺的原料送入硫回收装置 ,其工艺技术采用超优克劳斯工艺。主要工艺流程是原料硫化氢气 体先进入主燃烧室,将其中三分之一的硫化氢燃烧后转变为二氧化 硫,然后硫化氢与二氧化硫再反应生成单质硫;为进一步提高硫的 转化率和保证排放尾气达到国家环保标准,出主燃烧室的工艺气经 废锅冷却后还要经过内部装有催化剂的克劳斯反应器、选择性催化 还原反应器以及部分氧化催化反应器等工序,从而将硫化氢转变为 产品硫磺。 来自低温甲醇洗的净煤气作为合成原料送入甲烷合成,其工艺技术 采用丹麦托普索的镍基催化剂SNG合成技术。主要工艺流程为原 料净煤气经压缩机压缩后进入甲烷化第一反应器,然后再依次进入 甲烷化第二、第三、第四和第五反应器,其反应原理是一氧化碳( 包括少量二氧化碳)与氢气在镍基催化剂的作用下发生甲烷化反应 ,生成甲烷和水。之后甲烷气体经天然气压缩机压缩升压后送入三 甘醇脱水装置进行物理脱水干燥,富含水分的三甘醇富液经再生塔 蒸馏再生脱除水分后变为三甘醇贫液,作为吸收干燥剂送回吸收塔 循环使用。而干燥后的合格天然气送入天然气首站。
• 本装置采用纯氧固定床(移动床)碎煤加压气 化技术,以氧气和蒸汽作为气化剂,与原料煤 发生复杂的气化反应生产粗煤气,最主要的反 应包括C+O2→CO2、C+O2→CO、 C+H2O→CO+H2、C+H2→CH4等,煤气成 分包括甲烷、氢气、一氧化碳、二氧化碳以及 硫化氢、氧硫化碳、氨酚、焦油、中油、石脑 油等。
• 其中一期工程主要包括: • 两系列备煤装置(1座12万吨圆形储 煤仓)、16台气化炉、2套变换冷却 、4套煤气水分离、2套酚回收、1套 氨回收、2套低温甲醇洗、2套混合制 冷、1套硫回收、1座全厂火炬、1套 甲烷化、1套压缩干燥、2套五万立空 分、5台锅炉、2台汽轮发电机组等装
• 一期工程生产天然气171875 Nm3/h, 13.75亿Nm3/年
• 来自气化装置的3.9MPa、180℃的粗煤气, 首先进入洗涤塔由来自煤气水分离装置的高 压煤气水进行洗涤,粗煤气中的灰尘及焦油 被洗涤下来,之后洗涤水送往煤气水分离装 置;粗煤气经气-气换热器加热至240℃后进 入预变换炉(一部分煤气不进入预变和主变 而直接走副线),出来的变换气(300℃)再 进入主变换炉进一步进行变换反应,出口变 换气(375℃)进入气-气换热器降温至230℃ 后进入低位余热回收器,煤气被冷却至175℃ (同时副产0.7MPa低压蒸汽)。
• 打开煤锁下锥阀,将煤加入气化炉内,然 后关闭煤锁下锥阀。
• 打开煤锁泄压阀,将煤锁泄压完成后再重 复上述的加煤过程。