成形条件设定方法
成型条件设定技巧

成型條件設定技巧生產優質注射制品所涉及的因素很多.一般說來,當提出一件新制品的使用性能和其它有關要求后,首先就應在經濟合理和技術可行的原則下,選擇最適合的原材料,生產方式、生產設備及模具結構.在這些條件確定之后,成型條件的選擇和控制就是主要考慮的因素.一.模腔溫度(Cavity Wall Temperature)當設定模腔溫度時,從預期之低溫開始,然后增高模腔溫度,其結果是:1.增加結晶度和得到均勻的結構;2.減少成型之后收縮和增加成型時的收縮;3.減少產品內部應力;4.減少塑料流動的方向性;5.減少產品之翹曲;6.減少塑料流動阻力;7.增加產品表面光潔度(減少玻纖外露)8.銳增冷卻時間;(每攝氏度約2%)9.成品尺寸變大.很重要的是不但模腔溫度,而且甚至模腔之冷卻因相同溫度分布在模腔的不同位置,結果產生不平衡收縮而造成不同的內部應力,使零件發生翹曲.模腔溫度應根據不同的原材料,模具結構而選擇不同的控制方式,常用的如接冰水,常溫水,模溫機,加熱器等.二.融膠溫度(Melt Temperature)在設定材料溫度時,應先按原料廠商推薦值設定,再依據狀況修正,但通常更改不必超過正負五攝氏度.另外,融膠溫度將受到料管溫度,背壓,螺杆轉速等因素的影響.增加融膠溫度,其結果是:1.降低材料溫度.2.減少可見之熔接痕.3.增加材料結晶度,4.減少流向.5.在噴嘴或澆口處之系統因熔解時撕開分子鏈而減少機械應力,或因通過模具內狹窄通道流動的翹曲.6.輕微增加冷卻時間(約每攝氏度為0.3%)熔膠溫度若太低,則熔膠粘度變大,此時必須用高射壓,高射速來充填,往往易造成模仁損傷;若太高,熔膠粘度變小,則易造成回流,流涕等現象,且由于熱分解易導致成型品三.背壓(Back Pressure)背壓是螺杆在進料的塑化期間時,螺杆前端融膠的反向壓力,其作用如下:1由剪切熱無法熔解的特殊粒狀材料和熱融膠之均質化;2.機械性的均質化使集中的顏料和玻纖平均分布;3.去除料管內空氣;4.平衡軸向融膠產生的溫度曲線及其他因螺杆有效長度太短的計量.背壓增加時塑化能力將降低,且將增加流涕的可能性,故在開始設定時應使用較低的背壓值.四.螺杆轉速(Screw Speed)螺杆轉速是每分鍾內螺杆的回轉速度.(角速度,單位r/min)螺杆圓周速度是以螺杆的圓周乘以回轉速度.(線速度,單位m/s)V=D*N成型之塑膠粒的熔解是由螺杆的旋轉造成的,而標準的回轉速是螺杆的圓周速度.較低的螺杆轉速將使計量時間變長,但計量較趨穩定;較高的螺杆轉速將導致:1.由于剪切力作用,融膠溫度變高,易使融膠過熱;2.螺杆止動時由于慣性而使計量不穩定;3.截短玻纖;4.增加料管和螺杆的磨損;5.計量時間變短.若在背壓不能降低的情況下,為避免塑化時間影響到成型周期,宜選用深紋螺杆及較大螺杆,直徑以增加塑化率減少塑化時間.對精密成型,一般認為螺杆轉速應慢→快→慢;對一般連接器成型,可只用一般轉(150~200 R.P.M);對精密連接器成型,可選用三段速(50-80 R.P.M →5mm, 150~200 R.P.M→middle, 50-80 R.P.M →last 5mm).五.保壓切換點.(V-P Changing Point)保壓之切換可由行程,計量,時間,油壓壓力及模穴壓等控制;從切換流動進料壓力進料系統,就是從射出壓轉為保壓的過程.若保壓切換點選擇不當將產生發下缺點:切換太遲:1.不必要之尖峰壓力;2.毛邊;3.過重;4.較高的內應力,;5.模仁損傷;6.鎖模系統承受大應力.切換太早:1.壓力降大;2.充填不足;3.重量不足及不穩;4.射流紋;5.合模線不良;6.較大的縮陷.當設定機台的保壓切換點時應選擇較高的保壓切換點,然后漸漸降低使每一射出量之模穴的充填完全.一般壓力位置點為充填到型腔之90~95%之處較為合適.另外我們一般設定緩沖點為5mm左右,若太小,則造成成型不穩定,太大則由于原料熱分解使成型品之機械性能變差.六.鎖模力(Clamping Pressure)作用在Tie Bar上張應力的總其力量稱為鎖模力,增加鎖模力將造成:1.不必依賴成型上來減少零件尺寸;2.減少零件尺寸變動;3.減少模具變形;4.減少模具損傷時之毛頭;5.射出時減少透氣能力;6.增加鎖模機構各肘節的磨損.七.射出速度(Injection Speed)在型腔內充填速度是由模腔的幾何形狀至前端融膠的流動速度和螺杆射出速度合成之結果.增加射出速度可:1.減少結合線;2.增加成型品表面光潔度;3.增加在模腔內之融膠溫度;4.減少流動方向性;5.更好的融接效果;6.增加毛邊的可能性;7.型膠內氣體較難排除,易導致產品燒焦或成型品內氣孔.八.射出壓力.(Injection Pressure)即噴嘴處所產生之最大壓力,射壓若太低,則無法達到所需求的射出速度,易產生充填不足,且低速將使融膠粘度增加,沖擊較小的模仁使之受損,射壓若太高,則易產生毛邊.九.保壓時間(Dwell Pressure Time)保壓之作用主要在於穩定成型品尺寸及重量.保壓時間信賴於料溫,模溫及主流道和澆口的大小,保壓時間若不足,將產生以下結果:1.收縮下陷;2.空隙;3.重量不足;4.尺寸較小及變動較大;5.融膠倒流;6.翹曲增加.理想的保壓時間可以從較緩慢的降低開始的放大保壓時間來決定. 十.保壓壓力.(Dwell Pressure)保壓壓力應用在融膠的緩沖,而且由螺杆在保壓時間內補償融膠在模具內冷卻時的體積收縮.也因此決定密度與成品之特性關系,在保壓時間內,壓力應逐漸增加一直到澆口充分的凝固,需求緩沖行程應該是計量的5%~10%.成型常見不良及原因分析一.充填不足(不飽模)1.計量不足;2.料管,模具溫度太低;3.射壓太低,保壓時間不足;4.射速太慢;5.流道或澆口太小,澆口數目不夠;6.排氣不良;7.注射時間太短;8.螺杆止逆環磨損;9.成型品內厚不均或太薄;10.噴嘴堵塞;11.原料潤滑劑不足;12.噴嘴與引料接頭間漏料;13.保壓切換過早.二.毛邊1.鎖模力不足;2.原料干燥不充分或受污染;3.射出太高,保壓過大;4.加料量太多;5.保壓切換太遲;6.射速過快;7.溫度太高;8.模仁損傷;9.排氣孔阻塞;10.模板剛性不夠;11.流道及流道尺寸不適當;12.鎖模力不均勻.三.縮水1.熔膠量不足;2.射壓太低;3.保壓壓力,時間不足;4.射出時間太短,射速太慢;5.澆口不對稱;6.料溫過高,模溫不當;7.冷卻時間不夠;8.排氣不良;9.螺杆止逆環磨損;10.成型品內厚不均.四.成型品粘模1.射壓太高,注射時間太長;2.模溫太高;3.澆口尺寸太大和位置不當;4.模腔光潔度不夠;5.脫模斜度太小;6.頂出位置結構不合理,;7.進料不均使部分過飽;8.冷卻時間不足;9.多穴模進澆口不平衡;10.深件脫模排氣設計不良;五.主流道粘模.1.料溫太高;2.冷卻時間太短,主流道尚未凝固;3.噴嘴溫度太低;4.主流道無冷料穴;5.主流道光潔度差;6.噴嘴孔徑太於主流道直徑;7.主流道襯套弧度與噴嘴弧度不吻合;8.主流道斜度不夠;9.無澆道抓鎖六.起泡1.塑料干燥不夠,含有水分,單體,溶劑和揮發性氣體;2.料溫太高,受熱時間太長,塑料分解;3.射速太快;4.模溫太低;5.排氣不良;6.從加料端混入空氣;7.背壓不夠;8.保壓材料不足,時間太短;9.螺杆直徑過大;10.松退過長;11.螺杆,料管磨損嚴重;12.原料顆粒密度差異過大,次料太粗或添加過多;七.熔接痕1.料溫太低,塑料流動性差,背壓過低或螺杆轉速過慢;2.射壓太小,射速太慢;3.模溫太低,脫模劑過量;4.排氣不良;5.澆口位置不當;6.澆口及流道太小;7.原料不清或混料;8.潤滑劑不足;9.產品部分肉厚太薄.八.包風1.料溫過高,射速太快;2.原料中含有水分;3.塑料有分解;4.螺杆轉速太快,背壓太高;5.原料污染過帶進雜質;6.模具排氣不良;7.料管內有空氣→降低后段溫度;8.澆口太小.九.成品變形1.模溫過高,冷卻時間不足,料溫過高;2.成型品形狀及厚薄不均;3.澆口位置不當,數量不夠;4.頂出位置不當,受力不均;5.填料過多;6.模溫不均;7.脫模斜度不夠或不均衡;8.融膠在料管內時間過長以致分解;9.保壓不均勻;10.開模速度太快.。
第43:注塑成型条件设定方法

第43问注塑成型条件设定方法一、开合模参数的设定方向:连续生产中,必须考虑工艺在今后生产中的稳定性,所以,开关模的参数设定必须保证开合模动作平稳设备不晃荡。
在产品取出方便的条件下,开关模位置越短越好。
低压保护设定,保证产品在模腔里合模起不到高压而报警,确保模具不会被压坏;高压锁模力最好设定低些,保证PL面不出披锋为止;设定太高,相反会有一定的坏处。
锁模力太高,易损坏模具;PL面排气不良,产品易困气烧焦;产品内应力大,出模后才可弃放;影响产品尺寸等。
具体的设定技巧:1.合模参数设定:以高压、慢速起步,短行程;中压、快速运行,导柱惯性到导套前;低压、匀速靠近腔面前;微压、低速惯性接触母模;高压、中速起高压合模。
有行位的模具,开模速度不可太快;2.开模参数设定:以高压、慢速离开母模;中压、快速运行惯性至终点前;高压、低速到开模终点。
3.低压保护位置与低压压力值的设定:接触模具的低压、低速设定必须能推动模具(特别是有弹簧或有行位的模具),但力量不能大于压坏产品的力(产品厚度被压至到原来的4/5所需要的力量);低压保护要调好,因为新模成品的形状与脱模情况不太了解;有抽蕊以及绞芽的模具,要先行手动试验,功能正常后方可用自动;4.高压锁模位置与高压锁模力的设定:高压位置设定方法。
(先不设定高压锁模力值,用前面设定的所有参数合模,模具会停在一个位置上,显示位置值将是实际的高压位置,在这位置上加上0.5㎜~1㎜就行)。
确认合模力是否充足:合模力(g)≥成形面投影面积(cm²)×模具内的平均压力(通常为400kg/cm²)。
合模力的大小计算可按《合模力设定方法》进行。
直压式机台需注意锁模力是否足够,肘节式机台注意十字头是否伸直,以防射出时模具后退,而出现大毛边涨坏模具;锁模力设定依据:最小锁模力=最高射出压力×(产品的投影面积+流道的投影面积);实际锁模力=最小锁模力×(1+5%~20%),再慢慢加到不出现毛边为止,闭模到30~50mm时,速度要转为慢速。
LENS成型条件设定程序

LENS成型条件设定程序1:成形条件假设:以目标周期,树脂特性来假定成型条件:目标周期:60S,模具温度:90℃,冷却时间:30S,树脂温度:240℃,螺杆回转数:90RPM,背压:5KGF/CM2 2:树脂温度设定:1)让成形机喷嘴和模具脱离;2)清料后,观察从喷嘴出来的原料状况;3)确认树脂的熔融度及流出是否顺畅,NG提高树脂温度10℃左右;4)OK确认树脂射出时是否有气泡在内(分解);NG降低树脂温度10℃左右;5)OK确认树脂是否有变色,是否有黑色异物;NG降低树脂温度10℃左右;6)让成形机喷嘴接触模具.3:计量值,速度,PV切换设定:1)设成日本**的条件:STROKE=成型品重量*10/(螺杆径*比重*射出率)+5MMVP切换压力大概假定为30KGF/CM2射出速度假定为以下值:S1 25MM/S S2 25 MM/S S3 5 MM/S S4 20 MM/S S5 20 MM/SS1—S2切换位置–30MM S4—S5切换位置–32MM页脚内容1保压全部设定为”0”2)一模成形;3)通过短射来确定通过流道时的螺杆位置;4)S2—S3,S3—S4的切换位置要符合流道通过位置;*浇口通过尽量控制速度;*注意是否有流痕5)成形6)确认制品是否有90%被充填7)OK确认速度是在80%以下吗?8)OK则速度提升10%(每次只能改变一个地方),NG则切换压力提升3KG(迟一点切换) 4:保压设定1)保压先假设成以下的时间:G1(P1 1.5S P2 1.0S P3 2.0S P4 2.0S)G2(P1 3.0S P2 2.0S P3 2.0S P4 2.0S)保压先假设成以下值:T1 30KGF/CM2 5.0S T2 25KGF/CM2 3.0S T32)浇口部是否缩水?NG则T2的压力上升5KGF;页脚内容23)产品干涉条纹是否OK? NG则T1的压力上升5KGF;4)确定残量是否在5~10MM之间?NG则将计量~速度切换,VP改为同一值.5:安定性测试(振幅测试)1)根据以下条件对设定值进行变更(一个一个项目地进行),各成形50模,取最后10模作为样品:温度(树脂温度±2℃(缩水,断裂)模具温度±2℃(断裂,毛边,波面))压力(保压1 ±10KGF(缩水,毛边,断裂,波面)背压±15KGF(气泡,变色))时间(冷却时间±1S(变形) 射出速度±1MM/S(S3会影响流痕))切换位置(计量位置±2MM速度切换位置±2MM(流痕))2)观察波面,条纹要在3本以内,如果有超过该值,变更最初设定值,从1)开始;3)确认检查重点都必须没问题,如有问题从1)开始.成型参数中;以射出速度影响光学质量为主要因素,依序为模具温度、保压压力、塑料温度,成型参数对于发光强度有较大影响程度,对于发光角度并没有太大影响,聚焦角度都约在4°左右。
成型条件分析与设定课件
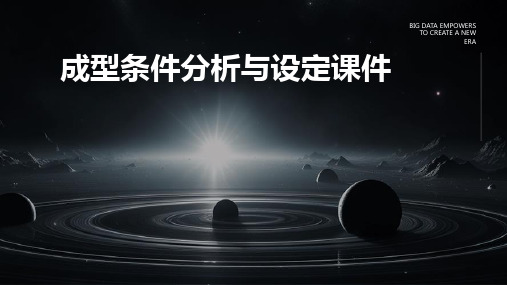
01
成型条件分析的重要性
BIG DATA EMPOWERS TO CREATE A NEW
ERA
定义与特点
成型条件分析是指对产品制造过程中各种因素的影响程度进行分析,以确定最佳的 成型工艺和条件。
成型条件分析需要考虑材料、工艺、设备、环境等因素,以及它们之间的相互作用 。
成型条件分析的特点包括系统性、综合性、实践性等。
05
成型条件与模具设计的关系
BIG DATA EMPOWERS TO CREATE A NEW
ERA
模具类型与成型条件的关系
注塑模具
适用于热塑性塑料,可快速生产 ,但模具成本高,不合适小批量
生产。
压铸模具
适用于铝合金、锌合金等金属材 料,生产效率高,但模具成本也
较高。
挤出模具
适用于塑料、橡胶等材料的连续 生产,成本低,但生产效率相对
公道安排生产计划
根据设备能力和生产需求,公道安排生产计划,避免设备闲置和过 度使用。
提高员工技能水平
通过培训和技能提升,提高员工的操作技能水平,减少操作失误和设 备故障。
07
成型条件与产品成本的关系
BIG DATA EMPOWERS TO CREATE A NEW
ERA
材料成本的控制方法
优化产品设计
成型条件分析与设定课件
BIG DATA EMPOWERS TO CREATE A NEW
ERA
• 成型条件分析的重要性 • 成型条件分析的方法 • 成型条件对产品性能的影响 • 成型条件的设定与调整 • 成型条件与模具设计的关系 • 成型条件与生产效率的关系 • 成型条件与产品成本的关系
目录
CONTENTS
优化模具设计和成型工艺条件,以提 高制品的表面质量和光洁度。对于外 观要求高的制品,可以采用抛光、喷 涂、贴膜等后处理工艺来提高其美观 度和使用感受。同时,注意控制原材 料的质量和稳定性,以避免因原材料 波动导致的产品外观问题。
成型条件设定技巧【收藏】

成型条件设定技巧【收藏】生产优质注射制品所涉及的因素很多.一般说来,当提出一件新制品的使用性能和其它有关要求后,首先就应在经济合理和技术可行的原则下,选择最适合的原材料,生产方式、生产设备及模具结构.在这些条件确定之后,成型条件的选择和控制就是主要考虑的因素.一模腔温度(Cavity WallTemperature)当设定模腔温度时,从预期之低温开始,然后增高模腔温度,其结果是:增加结晶度和得到均匀的结构;减少成型之后收缩和增加成型时的收缩;减少产品内部应力;减少塑料流动的方向性;减少产品之翘曲;减少塑料流动阻力;增加产品表面光洁度(减少玻纤外露)锐增冷却时间;(每摄氏度约2%)成品尺寸变大.很重要的是不但模腔温度,而且甚至模腔之冷却因相同温度分布在模腔的不同位置,结果产生不平衡收缩而造成不同的内部应力,使零件发生翘曲.模腔温度应根据不同的原材料,模具结构而选择不同的控制方式,常用的如接冰水,常温水,模温机,加热器等.二融胶温度(MeltTemperature)在设定材料温度时,应先按原料厂商推荐值设定,再依据状况修正,但通常更改不必超过正负五摄氏度.另外,融胶温度将受到料管温度,背压,螺杆转速等因素的影响.增加融胶温度,其结果是:降低材料温度.减少可见之熔接痕.增加材料结晶度,减少流向.在喷嘴或浇口处之系统因熔解时撕开分子链而减少机械应力,或因通过模具内狭窄通道流动的翘曲.轻微增加冷却时间(约每摄氏度为0.3%)熔胶温度若太低,则熔胶粘度变大,此时必须用高射压,高射速来充填,往往易造成模仁损伤;若太高,熔胶粘度变小,则易造成回流,流涕等现象,且由于热分解易导致成型品三背压(Back Pressure)背压是螺杆在进料的塑化期间时,螺杆前端融胶的反向压力,其作用如下:1由剪切热无法熔解的特殊粒状材料和热融胶之均质化;2.机械性的均质化使集中的颜料和玻纤平均分布;3.去除料管内空气;4.平衡轴向融胶产生的温度曲线及其他因螺杆有效长度太短的计量.背压增加时塑化能力将降低,且将增加流涕的可能性,故在开始设定时应使用较低的背压值.四螺杆转速(Screw Speed)螺杆转速是每分钟内螺杆的回转速度.(角速度,单位r/min)螺杆圆周速度是以螺杆的圆周乘以回转速度.(线速度,单位m/s)V=D*N成型之塑料粒的熔解是由螺杆的旋转造成的,而标准的回转速是螺杆的圆周速度.较低的螺杆转速将使计量时间变长,但计量较趋稳定;较高的螺杆转速将导致:由于剪切力作用,融胶温度变高,易使融胶过热;螺杆止动时由于惯性而使计量不稳定;截短玻纤;增加料管和螺杆的磨损;计量时间变短.若在背压不能降低的情况下,为避免塑化时间影响到成型周期,宜选用深纹螺杆及较大螺杆,直径以增加塑化率减少塑化时间.对精密成型,一般认为螺杆转速应慢→快→慢;对一般连接器成型,可只用一般转(150~200 R.P.M);对精密连接器成型,可选用三段速(50-80 R.P.M →5mm, 150~200 R.P.M→middle, 50-80 R.P.M →last 5mm).五保压切换点.(V-P ChangingPoint)保压之切换可由行程,计量,时间,油压压力及模穴压等控制;从切换流动进料压力进料系统,就是从射出压转为保压的过程.若保压切换点选择不当将产生发下缺点:切换太迟:不必要之尖峰压力;毛边;过重;较高的内应力,;模仁损伤;锁模系统承受大应力.切换太早:压力降大;充填不足;重量不足及不稳;射流纹;合模线不良;较大的缩陷.当设定机台的保压切换点时应选择较高的保压切换点,然后渐渐降低使每一射出量之模穴的充填完全.一般压力位置点为充填到型腔之90~95%之处较为合适.另外我们一般设定缓冲点为5mm左右,若太小,则造成成型不稳定,太大则由于原料热分解使成型品之机械性能变差.六锁模力(Clamping Pressure)作用在Tie Bar上张应力的总其力量称为锁模力,增加锁模力将造成:不必依赖成型上来减少零件尺寸;减少零件尺寸变动;减少模具变形;减少模具损伤时之毛头;射出时减少透气能力;增加锁模机构各肘节的磨损.七射出速度(Injection Speed)在型腔内充填速度是由模腔的几何形状至前端融胶的流动速度和螺杆射出速度合成之结果.增加射出速度可:减少结合线;增加成型品表面光洁度;增加在模腔内之融胶温度;减少流动方向性;更好的融接效果;增加毛边的可能性;型胶内气体较难排除,易导致产品烧焦或成型品内气孔.八射出压力.(Injection Pressure)即喷嘴处所产生之最大压力,射压若太低,则无法达到所需求的射出速度,易产生充填不足,且低速将使融胶粘度增加,冲击较小的模仁使之受损,射压若太高,则易产生毛边.九保压时间(Dwell Pressure Time)保压之作用主要在于稳定成型品尺寸及重量.保压时间信赖于料温,模温及主流道和浇口的大小,保压时间若不足,将产生以下结果:收缩下陷;空隙;重量不足;尺寸较小及变动较大;融胶倒流;翘曲增加.理想的保压时间可以从较缓慢的降低开始的放大保压时间来决定.十保压压力.(Dwell Pressure)保压压力应用在融胶的缓冲,而且由螺杆在保压时间内补偿融胶在模具内冷却时的体积收缩.也因此决定密度与成品之特性关系,在保压时间内,压力应逐渐增加一直到浇口充分的凝固,需求缓冲行程应该是计量的5%~10%.。
注塑成形条件设定

注塑成型技术成形条件设定目录第一章安装模具1,理论锁模力计算 (3)2,模具相关尺寸确认 (7)3,模具安装 (11)第二章温度设定1,料筒温度设定 (13)2,模具温度设定 (13)3,干燥温度设定 (14)第三章计量设定1,理论计量值计算 (16)2,计量值设定 (17)第四章压力设定1,填充压力设定 (20)2,保压设定 (21)3,背压设定 (25)4,锁模压力设定 (27)第五章速度设定1,填充速度设定 (29)2,保压速度设定 (32)3,计量减压速度设定 (33)4,开合模顶出速度设定 (34)第六章位置设定1,V—P位置设定 (37)2,速度切换位置设定 (39)3,开合模及顶出位置设定 (40)第七章时间设定1,射出时间设定 (42)2,冷却时间设定 (43)3,计量时间控制 (45)4,周期时间控制 (47)第一章 安装模具一, 理论锁模力计算当融体注入模具型腔时,注射压力通过融体液压传递到模具型腔内,此时,需要一定的力来保证模具的闭合维持现状,这个力就是锁模力。
通常我们的注塑机就是按锁模力的大小来分类的,比如30吨,即锁模力就是30吨。
那么,在我们的实际生产中,锁模力合不合适呢,还需计算才知道。
产品实际所需锁模力大于机台锁模力时,可能会出现披锋现象,产品实际所需锁模力一定要小于机台锁模力方可量产,当然,若过小则造成资源浪费,也不合适,在此,将介召一下理论锁模力的计算方法;计算公式;F = K × P × A × 10F-----锁模力(吨)K-----安全系数(1-1.2)P-----模腔平均压力(kg )A-----产品和浇注系统在分型面上的最大投影面积(cm )2 -3单位转换;• 吨 ----- Kg ----- N1吨=1000Kg = 9.8kn1Kg=9.8N1N=(1/9.8)Kg=0.102Kg1kn=102Kg=0.102吨• Mp ----- PaPa=1N/mMPa=10 Pa=1000000Pa1m =10 cm1Mp=10 N/m =10 N/cm =100 N/cm =10.2Kg/cm模腔平均压力;当融体注入模具型腔时,注射压力通过射嘴,主流道,分流道与浇口后,压力液压传递到模具型腔内的压力已有一定的压力损失,那么模腔平均压力肯定会比螺杆的射出压力小,压力损失的太小与模具结构,材料特性,机器特性及其条件设定有关。
Fanuc成型条件设定与调整精品PPT课件
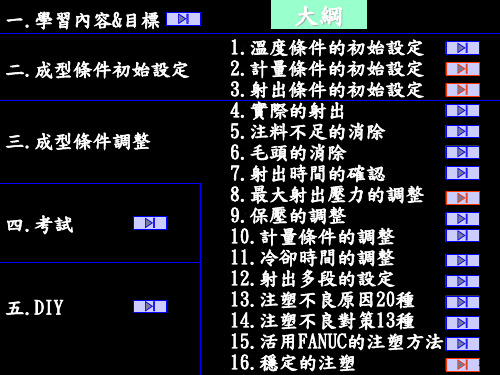
大綱
1.溫度條件的初始設定
2.計量條件的初始設定
3.射出條件的初始設定
4.實際的射出
5.注料不足的消除
6.毛頭的消.保壓的調整
10.計量條件的調整
11.冷卻時間的調整
12.射出多段的設定
10
2.計量條件的初始設定 2.5.減壓設定
設定減壓距離(松退量).減壓速度(松退速度). 2.5.1.減壓距離:2~10 mm左右 For LCP, is about 5 ~ 10 mm 2.5.2.減壓速度:10~50 mm/s左右 2.5.3.原則上設定在松退中不會混入空氣的距離和速度,
但也要注意樹脂的垂滴和拉絲. 2.5.4.請一邊觀察射出開始時的壓力現在值顯示,
一邊以下降到O MPa附近的壓力距離為基本標准 設定減壓距離.
Monitor the pressure and adjust the distance
11
2.計量條件的初始設定 2.6.冷卻時間
設定冷卻時間.請設定適合于注塑品的值. 冷卻時間會根据包括料筒溫度.澆口.流道在內的注塑品的厚度 而發生較大的變化.進行充分的冷卻可以減少注塑品變形.但是 這樣會延長注塑循環,且會影響到注塑品脫開模具.相反,如果冷 卻時間很短,注塑品則還沒有完全固化,因而會受脫模時的外部 力量的影響而變形.這樣不僅會影響到尺寸的穩定,而且還有可 能在開模時變形.基于上述情形,作為冷卻時間,要設定注塑品在 脫模時自然脫落且不會導致變開的時間.
請以50~100rpm/min作為基本標准予以設定.當旋轉數有充
裕時,設定比冷卻時間快1~2秒鐘就結束計量的旋轉數.
9
射出机成形条件之设定
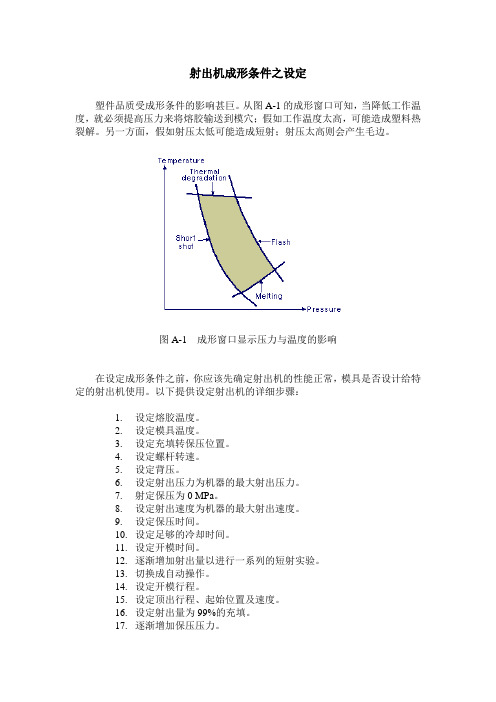
射出机成形条件之设定塑件品质受成形条件的影响甚巨。
从图A-1的成形窗口可知,当降低工作温度,就必须提高压力来将熔胶输送到模穴;假如工作温度太高,可能造成塑料热裂解。
另一方面,假如射压太低可能造成短射;射压太高则会产生毛边。
图A-1 成形窗口显示压力与温度的影响在设定成形条件之前,你应该先确定射出机的性能正常,模具是否设计给特定的射出机使用。
以下提供设定射出机的详细步骤:1.设定熔胶温度。
2.设定模具温度。
3.设定充填转保压位置。
4.设定螺杆转速。
5.设定背压。
6.设定射出压力为机器的最大射出压力。
7.射定保压为0 MPa。
8.设定射出速度为机器的最大射出速度。
9.设定保压时间。
10.设定足够的冷却时间。
11.设定开模时间。
12.逐渐增加射出量以进行一系列的短射实验。
13.切换成自动操作。
14.设定开模行程。
15.设定顶出行程、起始位置及速度。
16.设定射出量为99%的充填。
17.逐渐增加保压压力。
18.最小化保压时间。
19.最小化冷却时间。
步骤1. 设定熔胶温度熔胶温度是成形条件最重要的参数之一。
熔胶温度太低,使塑料无法完全熔化,或太黏而无法流动;熔胶温度太高,可能使塑料裂解,特别是POM或PVC 树脂更是如此。
熔胶与模具的建议温度可以请树脂供货商提供,或是使用表A-1的建议值。
大部份的树脂因为螺杆在料筒内旋转产生摩擦热而熔化。
料筒上通常会3~5组加热区域或加热片,主要功用是维持树脂在适当的温度。
设定加热片温度的规则为:●应该让温度从喷嘴到料斗附近逐渐降低。
●最接近料斗的加热片设定温度应该比计算之熔胶温度低40~50℃(72~80 °F),使塑料颗粒于塑化过程仍可以顺利地输送。
在喷嘴区的加热片应设定为计算之熔胶温度,并且保持均匀的温度。
设定不当的加热片温度会导致喷嘴处垂涎、塑料裂解或变色,特别是PA材料。
例如,C-mold软件建议使用235 ℃(455 °F)为PA材料的熔胶温度,则可以设定加热片的温度如下:●喷嘴区235 ℃(455 °F)●前段235 ℃(455 °F)●第一中段210 ℃(410 °F)●第二中段195 ℃(383 °F)●后段180 ℃(356 °F)因为旋转螺杆的摩擦热及背压对于熔胶的影响,真实的熔胶温度(或空射温度)通常比加热片的设定温度高。
- 1、下载文档前请自行甄别文档内容的完整性,平台不提供额外的编辑、内容补充、找答案等附加服务。
- 2、"仅部分预览"的文档,不可在线预览部分如存在完整性等问题,可反馈申请退款(可完整预览的文档不适用该条件!)。
- 3、如文档侵犯您的权益,请联系客服反馈,我们会尽快为您处理(人工客服工作时间:9:00-18:30)。
チックが冷 えて固まり 入らないこ とがありま す。そこで その箇所 を入れる 間だけ、プ ラスチック を入れる 速度を早く しその後 は又通常 の速度で 入れる と いうふうに 多段射出 を使用しま す。
5 . 固 め る ( 冷 却 )
充填で溶 けたプラス チックを金 型内に入 れたので すが、これ を金型内 を巡回す る水等で 冷却し固 めます。 この時、成 形品を金 型内に入 れておく時 間を冷却 時間といい 、長ければ 長いほど 成形品は 冷え固まり ます。
単に、50 mmから20 mmまでは 速度30 mm/秒で 移動させる と設定す れば良い だけです。
ここで又再 度注意し て欲しいの は、成形 機の力は とても強い のでいつも 全開で速 度30mm/ 秒を出そう と したら金型 を壊す可 能性があ るというこ とです。具 体的には 金型内に 異物がつ まり、プラ スチックを
図7
その後、溶 かすつまり スクリュー 回転の項 目にあるよ う図8、9の ようにスク リューを回 転させ、そ の後、 糸引き防 止のため サックバッ ク(図10参 考)します 。
図8
図9
次に充填 するの射 出項目に 沿って図 11、12、13 のように可 動した後、 保圧項目 に従って図 14、15の
つまり、細 長い供給 部でプラス チックをシ リンダ内に 落とし、段 々太くなる 圧縮部で プを圧ラス縮チしッ溶 かしていき 、太い計量 部で必要 なプラスチ ックの量を 計量すると いう訳です 。
よって基本 的には温 度は圧縮 部を中心 にプラスチ ックが溶け る温度より 少し高い 温度にしま す。 そして、計 量部は糸 引き対策 のため供 給部はホ ッパー下 が溶けた プラスチッ クで詰らな い様に圧 縮部より 少し低い 温度にしま す。
1 . プ ラ ス チ ッ ク の 成 形 方 法
プラスチッ クを役に立 つような形 に成す方 法(成形方 法)には射 出成形、 押出成形 等様々な ものがあり ます。 押出成形 とはマヨネ ーズをチュ ーブから出 すとその 口の形に 沿った形 状のもの 例えば星 型なら星 型 がの できも続の ける。その ような方法 でパイプや シートを作 る方法で すそし。てこれ から説明 する射出 成形とは 市販のチョ コレートを 溶かしそ れをハート 型等の容 器(射出成 ではこれを 金型と言 います)に 入れ、冷 やしハート 型のチョコ レートを作 る方法に 似ていま す。
いのです。 今 もし仮 にシリンダ の直径が とても大き かった場 合、少々 の力では スクリュー は動かな いかも しれません し、逆に小 さい直径で したら小さ な力でも簡 単に動くか もしれませ ん。そこで 、1cm2あ たり どれだけ 力がかか っているか 、つまりス クリューの 動かす力 をシリンダ の断面積 で割れば スクリュー が簡単
⑤ サ ッ ク バ ッ ク
ノズル先 端に樹脂 が沢山詰 まっていま すとノズル 先端から プラスチッ クが漏れ て出てくる ことがあり ます。 これをたれ もしくはド ローリング といいます 。これを防 止するた め計量停 止後スクリ ューを回転 させずに そのまま わずかに スクリュー を後退させ ノズル先 端のプラス チックにゆ とりをもた らせること が これあをりサますッ クバック と言います 。
もし、この 背圧という 力がなけ れば図5 のようにシ リンダ内に はプラスチ ックの他に 空気が混 入します。
これを背圧 をかけるこ とにより図 6のように 空気を除 去できるの です。 ここで、何 故、空気 が入ると良 くないかと 言 1う と計量 値にバラ つきが生じ る 2 空気 が成形品 表面に現 れ、銀条 等になる
ことからも わかると思 います。つ まり、速度 と力は互 いに関係し 、ある速度 を出したい ならこれだ けの力が
必要と自 然に決まり ますし、あ る力を出し たいなら、 この速度 でないとい けない と いうことが 決まる ということ です。この 、どれだけ の力が必 要かという こと等は、 成形機が 自動的に やってくれ 、私たちは
30mm/秒 で40mm から20mm までは 速 度10mm/ 秒のように 位置によっ て速度を 変える制 御方法 のことです 。何故、速 度を変化さ せて入れ るかと言う と成形品 の形状が 違うためそ れに適した 速度で入 れる ということ です。具体 的には 成 形品に狭 い箇所が ある場合、 そこを ゆ っくり入れ ていたら先 端のプラス
2 . 射 出 成 形 と は
射出成形 は、溶かす 、充填する 、固めるの 3つの工程 (段階)で 成り立って います。 溶かすと は溶けた プラスチッ クを必要 量作ること で充す填。すると は溶かす で作った溶 けたプラス チックを金 型の中に 入れること です。 固める と は 金型 内にある 溶けた状 態のプラス チックを冷 却し固める ことです。
① ス ク リ ュ ー 回 転
この値が 大きいとス クリューが 速く回転し 、速くプラ スチックを 前に送るこ とができま す。 しかしなが ら、速く回 転させると 、どうして も乱雑にな り混練が 良くないた め、ゆっく り回転させ た ほうがいい です。 ② 温 度
スクリュー は大げさ に書くと以 下のような 形をしてい ます。
プラスチッ クを入れ 込みます。 このスクリ ューの前 進の仕方 にコツがあ り、それで 良い成形 品がつくれ ることもあ ります。
② 射 出 保 圧 と は
ここで少し 思い出して ほしいので すが、カバ ンに何か 多くのもの を詰め込 まなけれ ばならなく なった時、 普通最初 は広いた めさっさと 入れ込む ことができ (速度)狭く なると隙間 に詰め込 むため力 で押し込む と思います 。
の場合20 mmを射出 保圧切換 え位置と 言います。
③ 力 と 速 度
射出は速 度で保圧 は力で制 御すると書 いたので すが、注意 してほしい のは、力 が弱けれ ば早くスク リューを
前進させる ことができ ないという ことです。 これは、力 の弱い人 が 重たい ものを持っ て走ること ができない
シリンダ2 185
シリンダ1 170
スクリュー回転
段 回転数 背圧 位置
1
50 10 70
2
30 5 80
サックバック
速度 20 ストローク 2
射出
冷却時間 18
8 35 60
段 圧力 時間
2 3
88 88
25 15
20
射出‐保圧 切替位置
8
1 33 1 2 22 2
まず、温度 の項目に あるように 図7のよう にシリンダ の温度が 上がります 。
50㎞/hを 出すことも 難しいかも 知れませ ん。つまり 力だけで は動かす ものが分 からなけれ ば、それが
どれ位の 速度で動 かすことが できるかど うか分から ないという ことです。
さて、今私 たちが動 かしたいも のはシリン ダ内にあ る溶けたプ ラスチック でこれをス クリューで 押し出した
4 . 充 填 す る
① 充 填 と は
溶かすで 成形に必 要な量の 溶けたプラ スチックが 用意できま した。今度 は充填す るで、用意 できたプラ スチックを金 型に入れ 込まないと いけませ んこれ。 は、注 射器で体 内に薬を 入れるよう に後ろに 下がったス クリューを 前進させる ことによっ て金型内
3 . 溶 か す
溶かすに 使うものは 以下の通 りです。
また、溶か すで知って ほしいこと は"スクリ ューを回転 させると その溝に あるものは スクリュー の溝に
そって前 もしくは後 ろに運ば れる"とい うことです 。(仮にス クリューが 右ねじでし たるとら前 右に回 左回転さ せると後ろ に下がりま すそし) て、こ の性質を 利用してホ ッパーにあ るプラスチ ックを熱を 持ったシリ ンダ内に 運ぶことに よ徐っ々てにプラ スチックを 溶かします 。それでは、 その工程 をするため に どのよ うな制御を しているか 見てみま す。
射出成形 も同様で、 最初は速 度で制御 し(これを 射出 と言 います)そ してある程 度詰まって きたら今度
は力で(こ れを保圧 と言いま す)で押し 込みます。
具体的に は、50mm までさがっ たスクリュ ーを20 mmまでは 速度30 mm/秒で、 それ以降 は10Kef
の力でスク リューを前 進させるこ のような制 御を行い ます。この 時、射出と 保圧の変 化する位 置、この例
しかし、長 すぎると1 つの成形 品を作る のに時間 がかかる ため、品質 に問題が 生じない程 度の時間 金型内に 入れます。
6 . ま と め
今、以下 のような条 件があっ たとします 。 このとき、 成形機が どのように 動くか見て みます。
温度
ノズル 180
シリンダ4 190
シリンダ3 200
込むことが できない状 態の時に、 無理に30 mm/秒で 樹脂を入 れようとす ると大きな バリが発 生し、ひい
ては金型 が壊れて しまいます 。そこで これ以上 の力を出し てはいけ ない とい う項目射 出圧力を 設けます。 当然、30 mm/秒を 出すのに 設定した 射出圧力 を越えるほ どの力が 必要な場 合、成形 機は設定 し上た限射の出力 で出せれ るだけの 速度でスク リューを前 進させます 。
からです。 しかし、背 圧をかけ すぎますと 、スクリュ ーが後ろ に下がらな くなったり します。
④ 計 量 完 了 位 置
スクリュー が計量完 了位置ま で後ろに 下がった 時、スクリ ューは回 転を止め まつすまり。 1個 の成形品 を作るの に必要な 溶けたプラ スチックが 出来たとい うことです 。 注意して ほしいの は1個の 成形品を 作るのに 必要なプラ スチックの 量とは、ラ ンナと成形 品及びいく らか 余分な量 を加えたも のです。こ の余分な 量を 残量 といいます 。(クッショ ン) この残量 があること によって外 の温度や 粉砕の混 入量の変 化による 計量した 量のバラ つき等に 対応します