模流分析成型条件设定依据
模流分析(MOLDFLOW)

一. 压力條件对产品的影响1.高保压压力能夠降低產品收縮的機會补充入模穴的塑料越多,越可避免產品的收縮高保压压力通常會造成产品不均勻收縮,而导致產品的翹曲变形对薄殼產品而言,由於壓力降更明顯,上述之情況更加嚴重2.Over packing 過保壓保壓壓力高,澆口附近體積收縮量少遠離澆口處保壓壓力低且體積收縮量較大導致產品翹曲變形,產品中央向四周推擠形成半球形(Dome Shape)3. Under packing 保壓不足澆口附近壓力低遠離澆口處壓力更低導致產品翹曲變形,產品中央向四周拉扯形成馬鞍形Twisted shape保壓時間如果夠長,足夠使澆口凝固,則可降低體積收縮的機會澆口凝固後,保壓效果就無效果一、澆口位置的要求:1.外观要求(浇口痕跡, 熔接线)2.產品功能要求3.模具加工要求4.產品的翹曲变形5.澆口容不容易去除二、对生产和功能的影响:1.流長(Flow Length)決定射出壓力,鎖模力,以及產品填不填的滿流長縮短可降低射出壓力及鎖模力2.澆口位置會影響保壓壓力保壓壓力大小保壓壓力是否平衡將澆口遠離產品未來受力位置(如軸承處)以避免殘留應力澆口位置必須考慮排氣,以避免積風發生不要將澆口放在產品較弱处或嵌入处,以避免偏位(Core Shaft)三、选择浇口位置的技巧1.將澆口放置於產品最厚處,從最厚處進澆可提供較佳的充填及保壓效果。
如果保壓不足,較薄的區域會比較厚的區域更快凝固避免將澆口放在厚度突然變化處,以避免遲滯現象或是短射的發生2.可能的話,從產品中央進澆將澆口放置於產品中央可提供等長的流長流長的大小會影響所需的射出壓力中央進澆使得各個方向的保壓壓力均勻,可避免不均勻的體積收縮射出量/切换点的影响射出量可由螺杆行程距离的設定決定射出量包括了填滿模穴需要的塑胶量以及保压時須填入模穴的塑膠量切換點是射出機由速度控制切換成壓力控制的點螺桿前进行程過短(切換點過早)會導致保壓壓力不足假如保压压力比所需射出壓力還低,產品可能发生短射PVT特性p –压力; v –比容; T –溫度描述塑胶如何随着压力及溫度的变化而发生体积上的变化。
模流分析资料

塑料流动行为一、塑料如何充填模穴射出成型射出成型的过程可分为三个阶段:●充填阶段;●加压阶段;●补偿阶段。
1、充填阶段充填阶段时塑料被射出机的螺杆挤入模穴中直到正好填满。
当我们要设计一个产品必须要使用到射出成型的制程时,最重要的是了解塑料充填的过程。
当塑料进入模穴时,塑料接触模壁时会很快的凝固,这会在模壁和熔融塑料之间形成凝固层。
下列的图显示塑料波前如何随着塑料往前推挤时而产生的扩张。
当流动波前到达模壁并凝固时,塑料分子在凝固层中没有很规则排列,一旦凝固,排列的方向性也无法改变。
红色箭头代表熔融塑料的流动方向,蓝色层代表凝固层,而绿色箭头代表熔融塑料向模具的传热方向。
2、加压阶段:在模穴充填满之后紧接着是加压阶段,虽然所有的流动路径在上一个阶段都已经充填完成,但其实边缘及角落都还有空隙存在。
为了完全充填整个模穴,所以必须在这个阶段加大压力将额外的塑料挤入模穴。
在下列图标中显示,模穴在充填阶段未期及加压阶段未期的差异,我们可以在左图的蓝色圆圈内看到未充填的死角。
注意:有时候“Confidence of Fill”的结果不能正确地预测短射,仍然显示良好的充填品质,但事实上可能有些区域不能被完全的充填。
这是因为浇口位置不适当而不能使全部的区域都能得到足够的保压。
3、补偿阶段:塑料从熔融状态冷凝固到固体时,会有大约25%的高收缩率,因此必须将更多的塑料射入模穴以补偿因冷却而产生的收缩,这是补偿阶段。
二、产品肉厚如何影响塑料流动“A flow leader and A flow deflector”定义:“A flow leader” 是指增加流动路径的肉厚以增加该路径的塑料流速。
“A flow deflector” 是指减少流动路径的肉厚以减少该路径的塑料流速。
Flow leaders 和Flow deflectors:Flow leaders 及Flow deflectors常常用来使模穴内各流动路径能在相同的时间内充填完(即流动平衡)。
成型条件设定与分析

三.射塑能力(Working Capacity)
unit:Kg:cm=射膠壓力(p Kg cm 2 )*行程容積
四.射出率:CM3/SEC
8/23
五.螺杆
三 二 一
47% 計量段
33% 壓縮段
19% 進料段
9/23
五.螺杆
螺杆應有一足夠長度以保証塑料的塑化均勻以 及為熱敏感材料保持一漸進之溫度差,一般L/D比為 16-22,較高之L/D比帶來額外之時間能源浪費,L/D 比小具有 效長度受影響,會影響塑化之均勻效果.
四.容模量
開模行程再加模具厚度即容模量
6/23
射出系統介紹
一.射塑量
實際射膠量=理論射膠量*行程效率(P) P 0.8-0.95(依塑膠流動性而言)
另止逆閥也無法達到100%的功能
一般成型制品重量約為最大注射量之30%-70%
二.射塑壓力
對相同之油壓系統而言,小螺杆之射壓高於大螺杆之 射壓.
7/23
上課對象﹕成型加工與模具維修職系師4以下人員
講 師:模具維修師1(含)以上資位 職系 上課時間:共2小時 課程特色:成型條件設定的基本觀念,成型條件的優化.
3/23
成型系統介紹
成型四要素:
成型品
鎖模體統
模具
材料
射出系統
電控系統
4/23
鎖模系統介紹
一.鎖模力(Clamping Force)
鎖模力F=P1*投影面積 鎖模力F=P1*投影面積
七.螺杆轉速
塑料供應商一般均會提供適當之RPM以供參考,而螺 杆之尺寸大小也會影響RPM的選擇. 小螺杆:槽深較淺所以塑料吸收熱源快,足夠促使逆料 在壓縮段段的軟化.另螺杆與料管壁間摩擦熱能低.所以可 用較高的RPM增加塑化能力. 大螺杆:反之,不適合高RPM應免塑化不均勻及造成過 大摩擦熱. 11/23
模流分析(CAE)管理制度

5-3-2. 模具设计阶段的分析优化流程5-3-3. 注塑成型阶段的分析优化流程5-4. 制作模流分析报告分析优化结束后,需将分析结果及改善建议,以Powerpoint的格式制作成《模流分析报告》,以供相关人员查阅和参考。
5-4-1. 报告的主要内容标准的模流分析报告一般应包含以下内容:5-4-1-1.报告封面:需注明产品名称、模具编号、CAE工程师、报告日期,并附产品图片;5-4-1-2. 分析说明:需注明分析目的、分析内容,以及分析所使用的塑胶材料名称;5-4-1-3. 产品介绍:需对产品做详细的壁厚分析,并提出设计不合理的地方;5-4-1-4. 材料介绍:需详细列出材料物性的各项数据;5-4-1-5. 浇注系统:进浇位置、浇口类型、流道排布情况;5-4-1-6. 冷却系统:水路温度、水路排布情况;5-4-1-7. 成型条件:温度设定、充填设定、保压设定;5-4-1-8. 充填时间:产品成型时的流动情况(须为动画图档);5-4-1-9. 最大注射压力:产品成型时所需的最大注射压力;5-4-1-10. 熔胶波前温度:产品成型时熔胶波前温度的分布情况;5-4-1-11.注射压力曲线:注射咀位置压力变化曲线;5-4-1-12.锁模力曲线:锁模力变化曲线;5-4-1-13.顶出时体积收缩:产品成型后顶出时的体积收缩大小;5-4-1-14.困气:产品成型后的困气位置;5-4-1-15.熔接线:产品成型后的熔接线位置;5-4-1-16.变形:产品成型后的变形大小和方向;5-4-1-17.总结:将所有的分析结果进行概括总结,并指出各方案的优劣;5-4-1-18.建议:明确提出建议方案,针对相关问题点提出改善建议。
5-4-2. 报告的命名规则模具编号(如:H1001)+产品名称+版次(如:A、B、C…)5-4-3. 报告的存放路径文件服务器\CAE\模具编号\5-5. 案例统计每个分析任务结束后,需将《CAE分析需求单》装订存档,并及时更新《CAE分析案例统计表》,以便今后对其进行查询和跟踪。
塑料零件模流分析教程
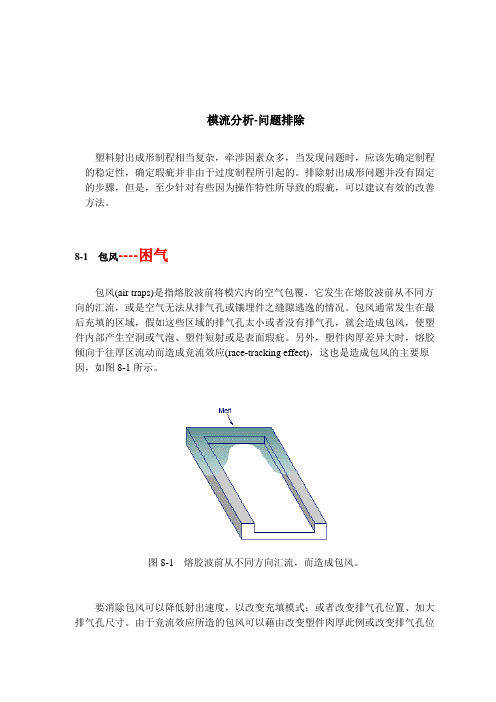
模流分析-问题排除塑料射出成形制程相当复杂,牵涉因素众多,当发现问题时,应该先确定制程的稳定性,确定瑕疵并非由于过度制程所引起的。
排除射出成形问题并没有固定的步骤,但是,至少针对有些因为操作特性所导致的瑕疵,可以建议有效的改善方法。
8-1 包风----困气包风(air traps)是指熔胶波前将模穴内的空气包覆,它发生在熔胶波前从不同方向的汇流,或是空气无法从排气孔或镶埋件之缝隙逃逸的情况。
包风通常发生在最后充填的区域,假如这些区域的排气孔太小或者没有排气孔,就会造成包风,使塑件内部产生空洞或气泡、塑件短射或是表面瑕疪。
另外,塑件肉厚差异大时,熔胶倾向于往厚区流动而造成竞流效应(race-tracking effect),这也是造成包风的主要原因,如图8-1所示。
图8-1 熔胶波前从不同方向汇流,而造成包风。
要消除包风可以降低射出速度,以改变充填模式;或者改变排气孔位置、加大排气孔尺寸。
由于竞流效应所造的包风可以藉由改变塑件肉厚此例或改变排气孔位置加以改善排气问题。
包风的改善方法说明如下:(1)变更塑件设计:缩减肉厚比例,可以减低熔胶的竞流效。
(2) 应变更模具设计:将排气孔设置在适当的位置就可以改善排气。
排气孔通常设在最后充饱的区域,例如模具与模具交接处、分模面、镶埋件与模壁之间、顶针及模具滑块的位置。
重新设计浇口和熔胶传送系统可以改变充填模式,使最后充填区域落在适当的排气孔位置。
此外,应确定有足够大的排气孔,足以让充填时的空气逃逸;但是也要小心排气孔不能太大而造成毛边。
建议的排气孔尺寸,结晶性塑料为0.025厘米(0.001英吋),不定形塑料为0.038厘米(0.0015英吋)。
(3)调整成形条件:高射出速度会导致喷射流,造成包风。
使用较低的射出速度可以让空气有充足的时间逃逸。
8-2 黑斑、黑纹、脆化、烧痕、和掉色黑斑(black specks)和黑纹(black streaks)是在塑件表面呈现的暗色点或暗色条纹,如图8-2所示。
Moldflow成型条件设定
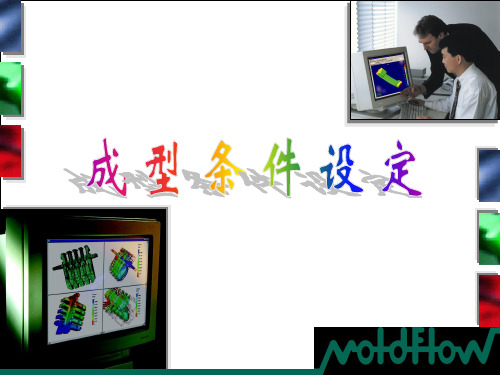
产品内外表面的冷却不均,导致产品产生翘曲,减小此翘曲的方法是使 公母模的冷却均匀,解决方法: 调整冷却水管排布 调整冷却液温度 在积热的地方加强冷却
收 缩 不 均
产品不同区域的收缩大小不一,所以不同区域之间产生内应力,致使产 品产生翘曲。
中间收缩大于四周,产生马鞍形翘曲。
产品各区域收缩不均导致变形, 解决方法: 调整保压曲线 修改产品设计
判断结果
在Buckling和Automatic的分析结果Screen out中会给出一个叫 Lambda的参数,根据这个参数,按照下列原则就可以判断材料是否 屈服:
Lambda<1: 材料出现屈服,用Large Deflection Lambda>1: 材料未出现屈服,用Small Deflection
•Flow - Cool - Flow - Warp (FCFW)
–冷却分析采用料到达此元素时的即时温度做为初始的 料温
–即时温度是用假设的恒定及统一的模温计算出来的
最佳分析序列
哪个序列是最佳的分析序列?
•FCFW 在流动分析的初始时假设恒定的模温
•CFW 假设冷却分析时的初始料温为常温 •对于翘曲的预测,假设恒定的料温比假设恒定模 温预测的更精确
变形的原因
塑料在成形过程中,由于温度、压力等因素 的影响,在材料分子之间产生很大的内应力,在 这种内应力的作用下,产品就产生了变形翘曲。 在应力和应变之间存在着一种特定的关系, 每种材料都不相同。 下面首先从理论上讲述一下应力和应变的关 系。
理想弹性变形
材料在受到应力的作用下会发 生变形,理想的弹性材料应力-应变 如右图所示,应变随着应力的增大 而增大,且成正比(线性)关系。
–因此CFW 是首选的运行序列
Moldflow设计原则

注塑成型流动行为设计原则注塑成型流动行为设计原则注射成型注射成型注塑成型机注塑成型机锁模单元液压单元Hopper 漏斗Screw (Ram)螺杆Barrel 料筒Heaterbands电热器来自外部单元的模具冷却在料筒和模具之间的喷嘴Nozzle (不显示)冷却时间开模时间充填时间保压时间注塑成型周期注塑成型周期周期时间充填时间保压时间冷却时间开模时间22秒19102注塑成型周期注塑成型周期充填Filling–模具闭合,螺杆快速向前移动,在模穴壁形成凝固塑料皮层保压Packing(保持Holding)–模穴填满,保压开始,冷却开始漏斗料筒螺杆模具螺杆对熔融塑料施加一定的压力使更多的塑料进入模穴内,这也称为“补偿阶段”。
注塑成型过程注塑成型过程冷却Cooling–保压完成,浇口凝固关闭,冷却继续–螺杆快速后移,开始为下一次注射塑炼树脂 开模Mold Open –冷却完成,模具打开注塑成型过程注塑成型过程注塑模具注塑模具固定侧可动侧流动行为流动行为在注塑模具中一个塑料分子会做些什么?充填阶段加压阶段补偿阶段Filling ,计量的充填模穴Pressurization ,建立模穴压力Compensation ,挤入额外的塑料以减少收缩成型各阶段成型各阶段喷泉流动喷泉流动描述塑料在一个模具中的流动现象首先进入的材料出现在浇口附近的表面最后进入模穴的材料,在中心层的熔融塑料下游出现对分子和在产品表面的纤维配向有直接的影响分子配向由剪切流动引起。
在凝固层剪切量高,因此导致最高的配向。
流动截面/分子配向流动截面/分子配向剪切率最小最大张力张力低配向高配向由剪切流动产生的热输入和进入模具的热损失之间应该是平衡的。
冷的模具热的熔融塑料热损失进入模具高剪切率热输入塑料流凝固层较快的注射速率较慢的注射速率对比流动截面/热交换流动截面/热交换注射时间/凝固层厚度注射时间/凝固层厚度较短的注射时间将会生产较薄的凝固层及较大的流动通道。
模流分析实验报告(3篇)
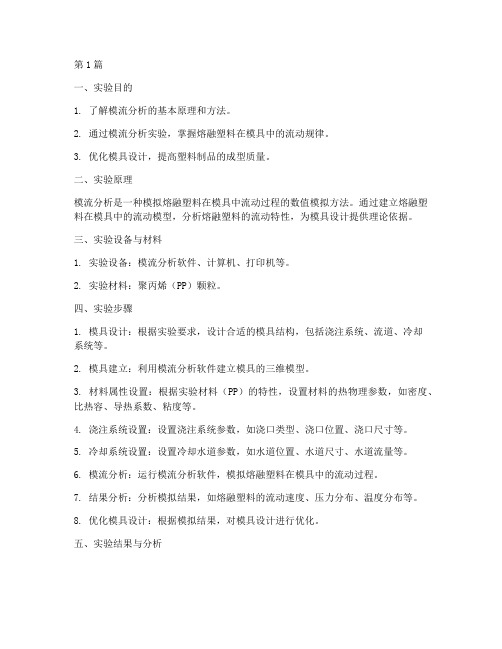
第1篇一、实验目的1. 了解模流分析的基本原理和方法。
2. 通过模流分析实验,掌握熔融塑料在模具中的流动规律。
3. 优化模具设计,提高塑料制品的成型质量。
二、实验原理模流分析是一种模拟熔融塑料在模具中流动过程的数值模拟方法。
通过建立熔融塑料在模具中的流动模型,分析熔融塑料的流动特性,为模具设计提供理论依据。
三、实验设备与材料1. 实验设备:模流分析软件、计算机、打印机等。
2. 实验材料:聚丙烯(PP)颗粒。
四、实验步骤1. 模具设计:根据实验要求,设计合适的模具结构,包括浇注系统、流道、冷却系统等。
2. 模具建立:利用模流分析软件建立模具的三维模型。
3. 材料属性设置:根据实验材料(PP)的特性,设置材料的热物理参数,如密度、比热容、导热系数、粘度等。
4. 浇注系统设置:设置浇注系统参数,如浇口类型、浇口位置、浇口尺寸等。
5. 冷却系统设置:设置冷却水道参数,如水道位置、水道尺寸、水道流量等。
6. 模流分析:运行模流分析软件,模拟熔融塑料在模具中的流动过程。
7. 结果分析:分析模拟结果,如熔融塑料的流动速度、压力分布、温度分布等。
8. 优化模具设计:根据模拟结果,对模具设计进行优化。
五、实验结果与分析1. 熔融塑料的流动速度:在模具入口处,熔融塑料的流动速度较大,随着流动距离的增加,流动速度逐渐减小。
在模具的狭窄部位,流动速度较大,而在宽大部位,流动速度较小。
2. 压力分布:在模具的狭窄部位,压力较大,而在宽大部位,压力较小。
在浇口处,压力最大。
3. 温度分布:在模具的冷却水道附近,温度较低,而在模具的加热部位,温度较高。
4. 优化模具设计:根据模拟结果,对模具设计进行优化,如调整浇口位置、改变冷却水道尺寸等。
六、实验结论1. 模流分析实验能够有效地模拟熔融塑料在模具中的流动过程,为模具设计提供理论依据。
2. 通过对模拟结果的分析,可以优化模具设计,提高塑料制品的成型质量。
3. 模流分析实验有助于缩短新产品开发周期,降低产品开发成本。