中国现有乙烯装置及其技术水平讲解
武汉万吨乙烯装置技术及特点讲课文档
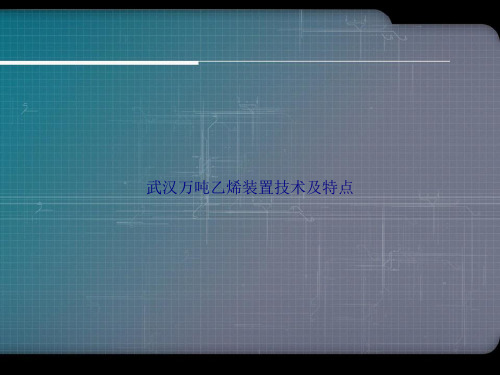
5.0裂解炉
4.2气体炉特点
(1)单辐射段单对流段结构
(2)采用2-1-1-1型炉管并加扭曲片强化传热。 (3)高温裂解气线性急冷锅炉
(4)底部与侧壁联合供热,底部占70% (5)热效率高:93~94% (6)引风机采用变频调速
现在十九页,总共三十四页。
6.0分离系统-总流程图
现在二十八页,总共三十四页。
8.0设备-设备汇总
设备类型
裂解炉 塔 压缩机/膨胀机 干燥器/反应器 罐 换热器 引风机 泵 其它
合计
设备台数
8 18 4 15 76 183(冷箱1台) 8 87 82
481
现在二十九页,总共三十四页。
8.0设备-关键塔
名称
内件
急冷油塔
固阀+挡板
急冷水塔
填料
碱洗塔
现在六页,总共三十四页。
1.0项目概况
装置组成:
布置图包括 变配电室
仪表机柜室 不在乙烯装置界区内的系统
清焦空气压缩机
原料及中间罐区 火炬水封罐及火炬筒
消防水排放池
现在七页,总共三十四页。
2.0项目进展
2007年7月底曹总主持武汉乙烯工程会议,确定乙烯装置裂解炉和分离全面国产化。 2007年9月27-28日,工程部召开总体协调会,明确乙烯装置“裂解炉采用SL-1M技术,分离采用LECT技术”,并确定只按一个工况设计。 2007年11月1日,SEI召开工艺包开工会。 2007年11月29-30日,第一次专家审查会 2007年12月27日,与沈鼓讨论三机条件及效率 2008年4月1日,裂解原料发生变化,增加一个工况 2008年6月24-26日,第二次专家审查 2008年8月7日,通过总部验收 2009年3月30日-4月3日,发展计划部主持召开了武汉分公司80万吨/年乙烯工程总体设计审查会。 2009年11月18-19日,工程部组织召开了基础设计协调会,明确乙烯装置设计基础不变,但要满足加工40万吨/年轻烃原料要求。 2009年11月20-21日,与SEI召开烯烃包基础工程设计开工会,明确乙烯装置设计时考虑处理40万吨/年轻烃的要求,并将轻烃过热系统与装置本身乙烷、丙烷分开设
乙烯装置技术水平分析及节能措施

乙烯装置技术水平分析及节能措施近年来,随着新的乙烯装置建设及老装置的扩能改造,新技术、新工艺及相关系统的设计优化的应用,我国乙烯装置能耗显著下降,随着国家“节能、降耗、减排”的要求提高,作为石油工企业耗能大户的乙烯装置将面临更大的节能降耗压力。
乙烯企业应严格控制工艺参数、工况条件,保证装置平稳运行、延长运行周期;通过用能数据、产品收率的对比分析以及对工艺单元的模拟计算,提出具体节能增效的措施。
乙烯企业应减少非计划停工事故发生,并结合装置特点逐步降低负荷、逐台有序停炉,尽可能回收物料,实现乙烯装置的无排放开停工。
标签:乙烯装置;综合能耗;节能措施1乙烯装置节能增效措施的研究1.1裂解炉系统优化原料的裂解性能在很大程度上决定了乙烯生产的能耗水平,但乙烯装置原料的优化和其上游炼厂的配制有很大关系。
大炼油小乙烯的配制,乙烯装置的原料就有很大的灵活性,相反小炼油或自身没有炼厂的乙烯装置其对原料就没有多少选择的余地。
我国优化裂解原料的重要措施就是实行“煉油化工一体化”,采用“宜烯则烯,宜芳则芳”的原则,它有利于炼厂和乙烯装置之间的原料互供和优化。
1.2装置精细化管理和无排放开停工创建节约型企业是企业增强核心竞争力的根本要求,石油化工企业通过精细化管理来实现节能增效具有重要的现实意义。
乙烯生产具备流程长、设备多、工艺机理复杂等特点,装置工艺指标约有上百个关键指标,因此在乙烯实际生产过程中,实施精细化管理、不断提升管理水平显得尤为重要。
乙烯企业应严格控制工艺参数、工况条件,例如裂解炉单元应加强烟道气氧含量、炉出口温度、炉管出口温度偏差、排烟温度及燃烧状况等工艺指标的管理,保证装置平稳运行、延长运行周期,为装置节能增效打下坚实基础。
例如独山子乙烯装置通过进细化管理和操作,裂解炉出口温度偏差保持在±2℃之间,双烯收率平均提高0.59%,经济效益显著。
同时应对重点耗能单元制订能耗消减措施,对易波动的工艺指标实行跟踪监控;通过用能数据的对比分析以及产品收率的对比评估,以及应用如Aspon等化工辅助模拟软件对工艺单元进行模拟计算,提出具体节能增效的措施。
武汉万吨乙烯装置技术及特点
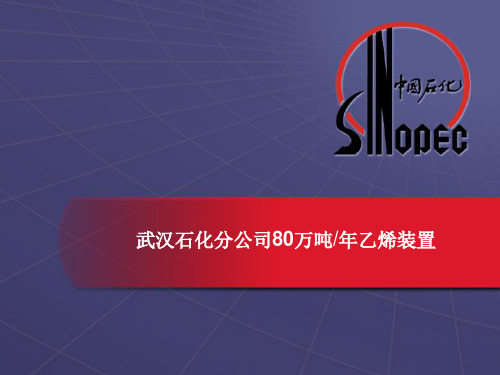
5.0裂解炉
4.2气体炉特点 (1)单辐射段单对流段结构 (2)采用2-1-1-1型炉管并加扭曲片强化传热。 (3)高温裂解气线性急冷锅炉 (4)底部与侧壁联合供热,底部占70% (5)热效率高:93~94% (6)引风机采用变频调速
6.0分离系统-总流程图
QO塔
QW塔
CGC1~4
HP DeC3
能量转换系 数单位
MJ/Mkcal MJ/t MJ/t MJ/t MJ/t MJ/t MJ/kwh
能量转换 系数
4186.8 3851.8 3684.4
3182 2763.2
4.19 11.84
能量消耗MJ/h
2259000 638628.44 -352228.6
-202057 -158055 180421.4 88563.2 2454272.4 100.66 24381.804
规模(万吨/年)
80
55 14 40 30 30 40 8/3 6/30
1.0项目概况
乙烯装置
产量80万吨聚合级乙烯 产量40万吨聚合级乙烯 年操作时间8000小时 操作弹性70-110% 占地:9.96公顷
1.0项目概况
装置位置图
1.0项目概况
技术来源: 裂解炉:中石化与Lummus合作技术SL-1M 分离: 中石化LECT
171
加氢尾油
69.69
LPG 8.28
4.0总物料平衡
乙 烯 装 置
循环丙烷2.73 循环乙烷14.48
氢气 2.45 聚合级乙烯 80 聚合级丙烯40 混合碳四 25.87 粗裂解汽油 51.88 裂解燃料油 12.68
综合收率:32.13
单位:万吨/年
乙烯教材之二:万吨乙烯装置情况介绍
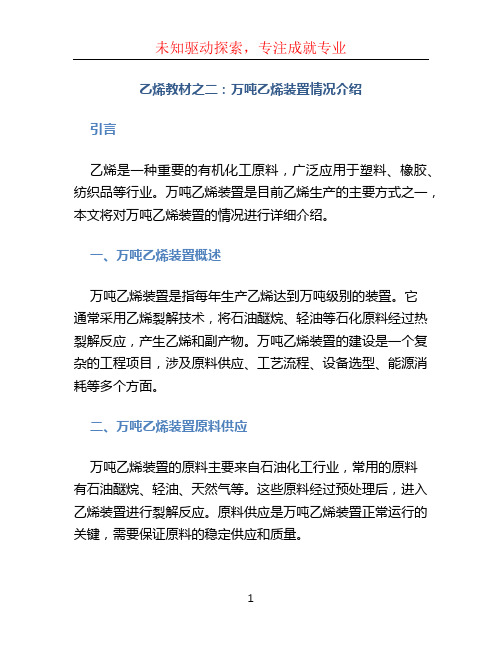
乙烯教材之二:万吨乙烯装置情况介绍引言乙烯是一种重要的有机化工原料,广泛应用于塑料、橡胶、纺织品等行业。
万吨乙烯装置是目前乙烯生产的主要方式之一,本文将对万吨乙烯装置的情况进行详细介绍。
一、万吨乙烯装置概述万吨乙烯装置是指每年生产乙烯达到万吨级别的装置。
它通常采用乙烯裂解技术,将石油醚烷、轻油等石化原料经过热裂解反应,产生乙烯和副产物。
万吨乙烯装置的建设是一个复杂的工程项目,涉及原料供应、工艺流程、设备选型、能源消耗等多个方面。
二、万吨乙烯装置原料供应万吨乙烯装置的原料主要来自石油化工行业,常用的原料有石油醚烷、轻油、天然气等。
这些原料经过预处理后,进入乙烯装置进行裂解反应。
原料供应是万吨乙烯装置正常运行的关键,需要保证原料的稳定供应和质量。
万吨乙烯装置的工艺流程通常包括原料预处理、热裂解反应、分离和精制等步骤。
原料预处理主要是去除杂质和硫化物,确保原料的纯度。
热裂解反应是乙烯生产的核心步骤,通过高温和催化剂的作用,将原料分解为乙烯和副产物。
分离和精制则是将产物进行分离和净化,得到高纯度的乙烯产品。
四、万吨乙烯装置设备选型万吨乙烯装置的设备选型直接影响到装置的产能和运行效率。
常见的设备包括裂解炉、分离塔、蒸汽压缩机等。
这些设备需要具备高效、耐腐蚀、稳定可靠的特点,以应对高温、高压等严苛的工艺条件。
五、万吨乙烯装置能源消耗万吨乙烯装置的能源消耗是一个重要的指标,对于提高装置的经济效益和环境友好型至关重要。
常见的能源消耗包括电力、蒸汽、水等。
通过优化工艺流程、改进设备和采用先进的节能技术,可以降低能源消耗,提高装置的能源利用率。
万吨乙烯装置的运行情况直接关系到乙烯产能和产品质量。
装置运行时需要监测和调控各个环节的参数,保证装置的安全稳定运行。
常见的运行指标包括乙烯产率、负荷率、设备故障率等,通过不断优化运行参数,可以提高装置的生产效率和产品质量。
结论万吨乙烯装置是乙烯生产的重要方式之一,具有生产规模大、设备复杂、能源消耗高等特点。
乙烯装置简介和重点部位及设备
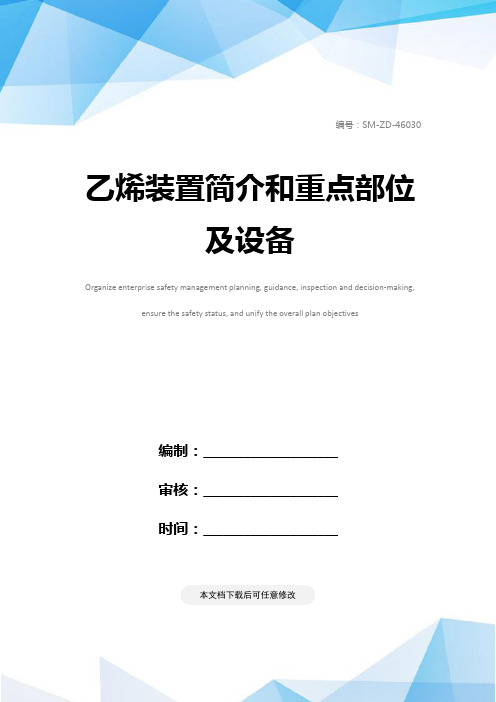
编号:SM-ZD-46030乙烯装置简介和重点部位及设备Organize enterprise safety management planning, guidance, inspection and decision-making, ensure the safety status, and unify the overall plan objectives编制:____________________审核:____________________时间:____________________本文档下载后可任意修改乙烯装置简介和重点部位及设备简介:该安全管理资料适用于安全管理工作中组织实施企业安全管理规划、指导、检查和决策等事项,保证生产中的人、物、环境因素处于最佳安全状态,从而使整体计划目标统一,行动协调,过程有条不紊。
文档可直接下载或修改,使用时请详细阅读内容。
一、装置简介(一)装置发展及其类型1.装置发展乙烯是石油化工的重要基础原料,乙烯装置是石油化工生产有机原料的基础,是石油化工的龙头,它的规模、产量、技术,标志着一个国家的石油化学工业的发展水平。
乙烯生产装置起源于1940年,美孚公司建成了第一套以炼厂气为原料的乙烯生产装置,开创了以乙烯装置为中心的石油化工历史。
50年代,德国、日本、英国、前苏联、意大利等国家相继建立了石油化工企业。
1960年世界乙烯产量为2910kt,1970年为19760kt,1980年达到34020kt,1990年为56300kt,到1997年世界乙烯生产能力接近86900kt,产量达78500kt。
目前世界上乙烯生产的主要技术是管式炉蒸汽热裂解和深冷分离流程。
我国第一套乙烯装置是1962年兰州化学工业公司合成橡胶厂5.25kt/a的乙烯生产装置,以炼厂气为原料,采用方箱管式裂解炉,油吸收法分离,生产化学级乙烯。
1962年底由我国自行建设了高桥化工厂2.0kt/a乙烯装置,1964年试车成功。
中国现有乙烯装置及其技术水平讲解
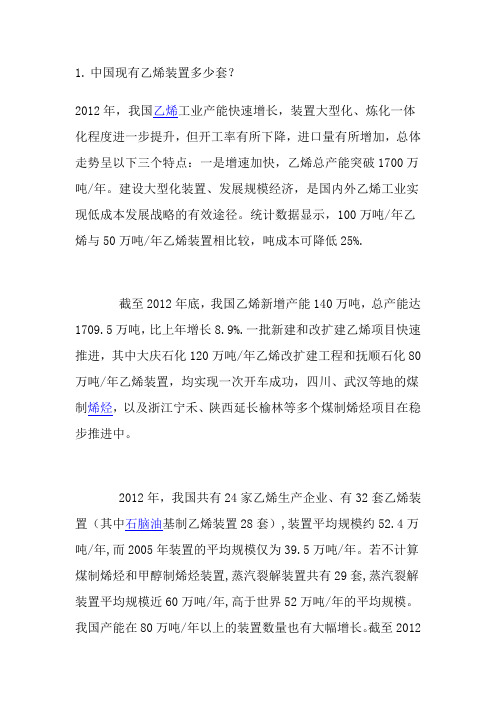
1.中国现有乙烯装置多少套?2012年,我国乙烯工业产能快速增长,装置大型化、炼化一体化程度进一步提升,但开工率有所下降,进口量有所增加,总体走势呈以下三个特点:一是增速加快,乙烯总产能突破1700万吨/年。
建设大型化装置、发展规模经济,是国内外乙烯工业实现低成本发展战略的有效途径。
统计数据显示,100万吨/年乙烯与50万吨/年乙烯装置相比较,吨成本可降低25%.截至2012年底,我国乙烯新增产能140万吨,总产能达1709.5万吨,比上年增长8.9%.一批新建和改扩建乙烯项目快速推进,其中大庆石化120万吨/年乙烯改扩建工程和抚顺石化80万吨/年乙烯装置,均实现一次开车成功,四川、武汉等地的煤制烯烃,以及浙江宁禾、陕西延长榆林等多个煤制烯烃项目在稳步推进中。
2012年,我国共有24家乙烯生产企业、有32套乙烯装置(其中石脑油基制乙烯装置28套),装置平均规模约52.4万吨/年,而2005年装置的平均规模仅为39.5万吨/年。
若不计算煤制烯烃和甲醇制烯烃装置,蒸汽裂解装置共有29套,蒸汽裂解装置平均规模近60万吨/年,高于世界52万吨/年的平均规模。
我国产能在80万吨/年以上的装置数量也有大幅增长。
截至2012年,共有10套80万吨以上的蒸汽裂解装置,合计产能达988万吨/年,占总产能的58.9%。
单套最大规模为上海赛科119万吨/年的乙烯装置。
乙烯生产企业平均规模74.1万吨/年,比2011年的68万吨/年增加了6.1万吨/年;乙烯装置平均规模57万吨/年,比2011年的56.1万吨/年上升了0.9万吨/年,高于世界52万吨/年的平均规模。
若不计算煤制烯烃和甲醇制烯烃装置,我国石脑油裂解乙烯装置的平均规模为59.2万吨/年,单套规模达80万吨/年以上的装置有8套,合计产能774万吨/年,占总产能的45%;单套规模60万吨/年以下的装置降至12套,产能合计263.5万吨/年,占总产能的16%.据美国《油气杂志》最新统计数据显示,当前全球十大乙烯生产商排名情况如下:排名第一的是埃克森美孚公司,共有19套装置,总产能1251.5万吨/年;排名第二的是陶氏化学,共有18套装置,产能1214.48万吨/年;排名第三的是沙伯公司,共有13套装置,产能1084.22万吨/年;排名第四的是壳牌化学,共有13套装置,产能935.84万吨/年;排名第五的是中国石化集团公司,共有12套装置,产能637.5万吨/年;排名第六的是道达尔公司,共有11套装置,产能593.3万吨/年;排名第七的是利安德巴赛尔公司,共有8套装置,产能520万吨/年;排名第八的是伊朗国家石化公司,共有7套装置,产能473.4万吨/年;排名第九的是英力士公司,共有6套装置,产能465.6万吨/年;排名第十的是台湾石化公司,共有5套装置,产能447.6万吨/年。
我国乙烯生产现状
我国乙烯生产技术水平
近年来我国乙烯及其下游加工装置在规模化水平、技术进步、 近年来我国乙烯及其下游加工装置在规模化水平、技术进步、节能 降耗、技术开发和创新等方面取得长足的进步,整体实力明显增强: 降耗、技术开发和创新等方面取得长足的进步,整体实力明显增强: 七套大型乙烯装置在2006年前后完成二轮改造后,平均规模达 年前后完成二轮改造后, 七套大型乙烯装置在 年前后完成二轮改造后 73.3万吨 年,虽大多数装置由二个系列组成,但整体规模已达世界 万吨/年 虽大多数装置由二个系列组成, 万吨 尤其是下游聚乙烯、聚丙烯装置,新建基本都在20万吨 年以上; 万吨/年以上 级,尤其是下游聚乙烯、聚丙烯装置,新建基本都在 万吨 年以上; 节能降耗效果明显, 年乙烯的平均能耗在730万大卡 吨乙烯 万大卡/吨乙烯 节能降耗效果明显,2003年乙烯的平均能耗在 年乙烯的平均能耗在 万大卡 左右,大型乙烯平均能耗691.8万大卡 吨乙烯,吉化乙烯能耗595 万大卡/吨乙烯 左右,大型乙烯平均能耗691.8万大卡/吨乙烯,吉化乙烯能耗595 万大卡/吨乙烯 为国内最佳,全国乙烯原料消耗平均为3.2吨/吨烯, 吨乙烯, 吨烯, 万大卡 吨乙烯,为国内最佳,全国乙烯原料消耗平均为 吨 吨烯 由于我国乙烯原料较重,轻烃比例小( ),石脑油 由于我国乙烯原料较重,轻烃比例小(占5~6%),石脑油(占 ),石脑油( 60%左右)供应不足,重质原料柴油和加氢尾油占 左右) 左右 供应不足,重质原料柴油和加氢尾油占24%~27%的 的 比重。乙烯原料耗量较高;石油化工技术在多年来引进、消化、 比重。乙烯原料耗量较高;石油化工技术在多年来引进、消化、吸收 的基础上,通过开发创新, 的基础上,通过开发创新,已形成了一批具有自主知识产权并可应用 于工业化的技术成果,包括10万吨 年能力的裂解炉, 万吨/年能力的裂解炉 于工业化的技术成果,包括 万吨 年能力的裂解炉,聚丙烯高效催 化剂和环管二代聚丙烯成套技术以及石化装置的催化剂国产化等等。 化剂和环管二代聚丙烯成套技术以及石化装置的催化剂国产化等等。
乙烯装置节能技术进展
乙烯装置节能技术进展摘要:从原料优化、改善裂解选择性、提高裂解炉热效率等方面介绍了近年来乙烯装置各系统的节能技术的进展情况,指出应加大对成熟技术的推广应用和节能降耗新工艺及新技术的开发力度,以进一步降低乙烯装置的能耗。
关键词:乙烯装置;原料优化;选择性;节能;裂解乙烯是石化工业最重要的基础原料之一,约有75%的石油化工产品由乙烯生产,乙烯工业的发展水平从总体上代表了一个国家石化工业的实力。
目前管式炉蒸汽裂解技术仍是乙烯生产的主导技术,世界上约98%的乙烯产量由该技术生产制得[1,2]。
裂解炉作为乙烯生产装置的关键设备,它的燃料消耗占全装置能耗的75%一80%,扣除部分外送蒸汽,能源消耗占装置总能耗的42%左右。
因此,降低裂解炉的能耗是降低乙烯装置能耗的重要途径之一。
近年来通过优化乙烯原料、改善裂解选择性、高裂解炉热效和延长裂解炉运行周期等措施使裂解炉的能耗得到显著降低。
本文就国内外近年来较为关注的乙烯装置节能技术的进展情况作一介绍。
1 原料优化原料的裂解性能在很大程度上决定了乙烯生产的能耗水平,据2003年度乙烯装置平均能耗的统计,采用重质原料时,装置的综合能耗为30.98GJ/t;以石脑油为原料时,装置的综合能耗为28.89GJ/t;以乙烷为原料时,装置的综合能耗仅为22.48GJ/t[3]。
原料中芳烃类物质的含量,还会大大加速高温裂解过程中炉管的结焦速度,影响传热效果,极大地降低了能源利用率。
由此可见,有效地提高原料的质量,对裂解炉的节能降耗有着重要的作用。
1.1 原油的选择与加工在石油烃裂解过程中,正构烷烃最易生成乙烯等目的产物,其次是五个碳以上的异构烷烃,再次为环烷烃,而芳烃的C一C共扼键键能高达611kJ/mol,很难裂解。
因而优化原油的选择和加工方案,调整原料结构,增加烷烃尤其是正构烷烃含量高、关联指数(BMCI)值低的优质裂解原料,可以在提高乙烯收率的同时,减少设备结焦,降低装置能耗。
探析乙烯装置分离技术及国产化开发
探析乙烯装置分离技术及国产化开发近几年,我国工业得到了快速发展,这在一定程度上也促进了我国乙烯装置分离技术的提高,对于整个行业的发展也能够起到一定促进作用。
首先,阐述了研究乙烯装置分离技术的意义;其次,介绍了乙烯装置分离技术;最后对国产化乙烯分离装置研究进展情况进行总结。
标签:乙烯装置;分类技术;反应装置;反应参数乙烯的产能情况标志着一个国家石油化化工行业的整体水平,近几年,我国工业的飞速发展,这在一定程度上提高了我国乙烯产能,促进了行业的发展。
1 研究乙烯装置分离技术的意义研究乙烯分离装置技术时,要先对乙烯生产期间的各项内容进行深入研究,并且在该过程中,乙烯生产中就是轻质烃进行MTO反应。
通过对乙烯分离装置进行应用,将启始剂装置中加入乙烯分离装置中,可以在一些分离装置中通过分离获取到较纯的乙烯物质,这些物质在应用期间具有不错的工业价值,其也可以作为精细化工作生产中的一项关键原材料,通过对其的合理应用,在一定程度上可以促进我国工业的发展,具有较高的工业价值[1]。
而从我国的经济、工业发展情况来看,人们对于乙烯的需求量不断增多,因此,在日后研究期间,应加强对乙烯装置分离技术的研究,尽快研究出更加先进的技术,通过对该项技术的合理应用,使乙烯装置在应用期间的生产效率能够得到进一步提高,满足人们对乙烯需求量日益增多的具体需求。
2 乙烯装置分离技术应用乙烯分离装置期间,相应的工作人员应当充分意识到乙烯装置分离技术其是一类特殊分离提纯反应,在采用乙烯装置分离技术期间,要对轻质烃具有的化学性质进行合理利用,同时,在设计乙烯分离装置期间,提高对乙烯分离装置自身安全性的设计,确保装置在实际应用过程中的安全性,以免生产过程中,出现安全问题,引发安全事故,对生产工作造成不良影响[2]。
同时,在设计乙烯分离装置期间,要全面结合MTO反应过程中涉及的动力学公式,以及MTO反应期间涉及到的压力參数、传递方面、温度参数等多项数值,只有保证各项参数内容准确无误,才能确保乙烯分离装置在应用中,可以正常运行,以免出现生产事故。
乙烯装置简介和重点部位及设备
【本文为word版,下载后可修改、打印,如对您有所帮助,请购买,谢谢。
】乙烯装置简介和重点部位及设备一、装置简介(一)装置发展及其类型1.装置发展乙烯是石油化工的重要基础原料,乙烯装置是石油化工生产有机原料的基础,是石油化工的龙头,它的规模、产量、技术,标志着一个国家的石油化学工业的发展水平。
乙烯生产装置起源于1940年,美孚公司建成了第一套以炼厂气为原料的乙烯生产装置,开创了以乙烯装置为中心的石油化工历史。
50年代,德国、日本、英国、前苏联、意大利等国家相继建立了石油化工企业。
1960年世界乙烯产量为2910kt,1970年为19760kt,1980年达到34020kt,1990年为56300kt,到1997年世界乙烯生产能力接近86900kt,产量达78500kt。
目前世界上乙烯生产的主要技术是管式炉蒸汽热裂解和深冷分离流程。
我国第一套乙烯装置是1962年兰州化学工业公司合成橡胶厂5.25kt/a的乙烯生产装置,以炼厂气为原料,采用方箱管式裂解炉,油吸收法分离,生产化学级乙烯。
1962年底由我国自行建设了高桥化工厂2.0kt/a乙烯装置,1964年试车成功。
70年代,我国先后从国外引进了一批技术先进、规模较大的乙烯装置,分别建成了燕山、大庆、齐鲁、扬子、金山等年产300kt/a的乙烯装置。
特别是近几【本文为word版,下载后可修改、打印,如对您有所帮助,请购买,谢谢。
】年来,全国乙烯行业有了飞跃性的发展,原有老装置经过配套平衡、技术改进,生产能力进一步发挥,2004年我国乙烯生产能力已达到6266kt。
随乙烯工业的迅速发展,原料种类和加工工艺均有了巨大的变化。
根据地域和资源的不同,原料分布从乙烷、丙烷、天然气、石脑油到柴油甚至到HAGO、HVAO和常三减一线油和蜡下油等。
加TI.艺有管式炉裂解制乙烯、甲醇制乙烯、甲烷制乙烯、催化裂解和由合成气制乙烯等方法。
其中以管式炉裂解制乙烯工艺最为成熟,世界乙烯产量的99%左右均由管式炉裂解法生产。
- 1、下载文档前请自行甄别文档内容的完整性,平台不提供额外的编辑、内容补充、找答案等附加服务。
- 2、"仅部分预览"的文档,不可在线预览部分如存在完整性等问题,可反馈申请退款(可完整预览的文档不适用该条件!)。
- 3、如文档侵犯您的权益,请联系客服反馈,我们会尽快为您处理(人工客服工作时间:9:00-18:30)。
1.中国现有乙烯装置多少套?2012年,我国乙烯工业产能快速增长,装置大型化、炼化一体化程度进一步提升,但开工率有所下降,进口量有所增加,总体走势呈以下三个特点:一是增速加快,乙烯总产能突破1700万吨/年。
建设大型化装置、发展规模经济,是国内外乙烯工业实现低成本发展战略的有效途径。
统计数据显示,100万吨/年乙烯与50万吨/年乙烯装置相比较,吨成本可降低25%.截至2012年底,我国乙烯新增产能140万吨,总产能达1709.5万吨,比上年增长8.9%.一批新建和改扩建乙烯项目快速推进,其中大庆石化120万吨/年乙烯改扩建工程和抚顺石化80万吨/年乙烯装置,均实现一次开车成功,四川、武汉等地的煤制烯烃,以及浙江宁禾、陕西延长榆林等多个煤制烯烃项目在稳步推进中。
2012年,我国共有24家乙烯生产企业、有32套乙烯装置(其中石脑油基制乙烯装置28套),装置平均规模约52.4万吨/年,而2005年装置的平均规模仅为39.5万吨/年。
若不计算煤制烯烃和甲醇制烯烃装置,蒸汽裂解装置共有29套,蒸汽裂解装置平均规模近60万吨/年,高于世界52万吨/年的平均规模。
我国产能在80万吨/年以上的装置数量也有大幅增长。
截至2012年,共有10套80万吨以上的蒸汽裂解装置,合计产能达988万吨/年,占总产能的58.9%。
单套最大规模为上海赛科119万吨/年的乙烯装置。
乙烯生产企业平均规模74.1万吨/年,比2011年的68万吨/年增加了6.1万吨/年;乙烯装置平均规模57万吨/年,比2011年的56.1万吨/年上升了0.9万吨/年,高于世界52万吨/年的平均规模。
若不计算煤制烯烃和甲醇制烯烃装置,我国石脑油裂解乙烯装置的平均规模为59.2万吨/年,单套规模达80万吨/年以上的装置有8套,合计产能774万吨/年,占总产能的45%;单套规模60万吨/年以下的装置降至12套,产能合计263.5万吨/年,占总产能的16%.据美国《油气杂志》最新统计数据显示,当前全球十大乙烯生产商排名情况如下:排名第一的是埃克森美孚公司,共有19套装置,总产能1251.5万吨/年;排名第二的是陶氏化学,共有18套装置,产能1214.48万吨/年;排名第三的是沙伯公司,共有13套装置,产能1084.22万吨/年;排名第四的是壳牌化学,共有13套装置,产能935.84万吨/年;排名第五的是中国石化集团公司,共有12套装置,产能637.5万吨/年;排名第六的是道达尔公司,共有11套装置,产能593.3万吨/年;排名第七的是利安德巴赛尔公司,共有8套装置,产能520万吨/年;排名第八的是伊朗国家石化公司,共有7套装置,产能473.4万吨/年;排名第九的是英力士公司,共有6套装置,产能465.6万吨/年;排名第十的是台湾石化公司,共有5套装置,产能447.6万吨/年。
2.中国目前的乙烯生产能力及其技术水平如何?经过数十年的发展,特别是在“十一五”期间,我国乙烯工业取得了举世瞩目的进步,同期世界新建的乙烯装置大多集中在中国。
随着一系列乙烯装置的建成投产,到2010年底我国乙烯总产能达到1494.9×104t/a,成为全球仅次于美国(2755.4×104t/a)的第二大乙烯生产国。
设备国产化程度提升,乙烯原料趋向多元化。
从装置国产化程度上看,乙烯生产工艺中所用的大型裂解炉、裂解气压缩机等关键设备已实现了国产化。
2012年10月,大庆石化年产120万吨乙烯改扩建工程龙头项目已生产出合格产品,实现了国内大型乙烯技术工艺包采用完全自主知识产权并实现完全国产化的目标。
在抚顺石化大乙烯建设中,国产设备达到72%,实现了关键设备乙烯压缩机组的国产化,使我国成为世界上少数几个掌握这一技术的国家之一。
从乙烯原料上看,受资源限制,目前我国乙烯使用的原料以石脑油为主,其次是轻柴油、加氢尾油等。
其中,石脑油占64%、加氢尾油占10%、轻柴油占10%,90%乙烯原料来自炼厂。
原料的构成在目前或将来都不占优势。
丰富的煤炭资源加上烯烃市场巨大的需求量,使煤制烯烃项目具有一定的市场竞争力。
随着神华包头等多个示范项目的投产,我国以煤等非石油基原料制乙烯的技术取得突破性进展。
截至2012年底,我国共有煤制烯烃、甲醇制烯烃工业化装置4套,合计烯烃产能218万吨,生产聚乙烯56万吨,聚丙烯162万吨。
2009年8月28日,国家乙烯工业新原料来源示范项目———沈阳石蜡化工有限公司50×104t/a催化热裂解(CPP)制乙烯项目(以下简称CPP项目)在沈阳投产。
该项目采用中国石化石油化工科学研究院研发的重油深度催化裂解制乙烯技术,以重质渣油为原料富产乙烯和丙烯,这是该技术首次工业化应用。
由于操作条件缓和、设备材料要求低、投资相对较小以及主要原料常压渣油价格较低,与国内现有的乙烯装置相比,CPP项目生产的乙烯成本可降低20%。
我国西部大开发标志性工程、国内最大的炼化一体化工程———独山子石化千万吨炼油百万吨乙烯工程于2009年9月21日建成投产,该工程包括100×104t/a乙烯。
辽宁华锦化工集团公司500×104t/a油化工程(即乙烯原料工程)、扩能45×104t/a乙烯工程于2009年10月中旬投产,16×104t/a乙烯能力不变,再增加一套45×104t/a装置,产能达到61×104t/a。
2.1.22010年新建和扩能乙烯项目随着几个百万吨级乙烯装置的投产,2010年我国乙烯产能达到1494.9×104t/a,“十一五”期间5年的产能增长接近前10个五年计划的总和。
2010年1月16日,天津石化100×104t/a乙烯装置产出合格产品,项目主要包括100×104t/a乙烯和1000×104t/a 炼油。
由于采用新工艺和新技术,乙烯综合能耗和炼油综合能耗达到国际先进水平。
该项目的建成投产使天津石化炼油一次加工能力达到1500×104t/a,乙烯生产能力达到120×104t/a,成为全国最大的乙烯生产企业之一和华北地区最大的炼油加工基地。
辽宁华锦化工集团“十一五”工程于2010年2月5日全面投产,其中包括45×104t/a乙烯。
2010年4月20日,镇海炼化公司100×104t/a乙烯裂解装置成功投产,标志着这个目前国内单套规模最大、技术最先进、国产化率最高的乙烯工程投产成功,镇海炼化也自此拥有2300×104t/a原油综合加工能力和100×104t/a乙烯生产能力,成为我国最大的炼化一体化企业。
镇海炼化100×104t/a乙烯工程是国家建设项目,主要包括乙烯裂解等10套生产装置及配套公用工程,其中100×104t/a乙烯裂解、45×104t/a聚乙烯、65×104t/a环氧乙烷/乙二醇和28.5×104t/a环氧丙烷/62×104t/a苯乙烯等装置,在世界同类装置中规模最大。
在工艺技术上,大部分装置采用国产技术,其中6套装置采用中国石化自有技术,乙烯综合能耗达到国际水平。
中海壳牌石油化工股份有限公司是壳牌化学公司与中国海洋石油总公司各持股50%的合资企业,该公司于2010年3月在惠州大亚湾石化联合装置实施扩能。
扩建前乙烯裂解装置的产能为80×104t/a,扩建后产能达到95×104t/a。
通过结构调整,“十一五”期间我国乙烯布局优化取得成效,在长三角、环渤海、珠三角和西部等地区形成了一批世界级乙烯生产基地。
2010年乙烯产能按地区分,华东占42.4%、东北占16.4%、中南占12.5%、西北占13.3%、华北占15.5%,西南地区也正在建设乙烯装置,即将实现零的突破。
2009年8月28日,国家乙烯工业新原料来源示范项目———沈阳石蜡化工有限公司50×104t/a催化热裂解(CPP)制乙烯项目(以下简称CPP项目)在沈阳投产。
该项目采用中国石化石油化工科学研究院研发的重油深度催化裂解制乙烯技术,以重质渣油为原料富产乙烯和丙烯,这是该技术首次工业化应用。
由于操作条件缓和、设备材料要求低、投资相对较小以及主要原料常压渣油价格较低,与国内现有的乙烯装置相比,CPP项目生产的乙烯成本可降低20%。
我国西部大开发标志性工程、国内最大的炼化一体化工程———独山子石化千万吨炼油百万吨乙烯工程于2009年9月21日建成投产,该工程包括100×104t/a乙烯。
辽宁华锦化工集团公司500×104t/a油化工程(即乙烯原料工程)、扩能45×104t/a乙烯工程于2009年10月中旬投产,16×104t/a乙烯能力不变,再增加一套45×104t/a装置,产能达到61×104t/a。
2.1.22010年新建和扩能乙烯项目随着几个百万吨级乙烯装置的投产,2010年我国乙烯产能达到1494.9×104t/a,“十一五”期间5年的产能增长接近前10个五年计划的总和。
2010年1月16日,天津石化100×104t/a乙烯装置产出合格产品,项目主要包括100×104t/a乙烯和1000×104t/a 炼油。
由于采用新工艺和新技术,乙烯综合能耗和炼油综合能耗达到国际先进水平。
该项目的建成投产使天津石化炼油一次加工能力达到1500×104t/a,乙烯生产能力达到120×104t/a,成为全国最大的乙烯生产企业之一和华北地区最大的炼油加工基地。
辽宁华锦化工集团“十一五”工程于2010年2月5日全面投产,其中包括45×104t/a乙烯。
2010年4月20日,镇海炼化公司100×104t/a乙烯裂解装置成功投产,标志着这个目前国内单套规模最大、技术最先进、国产化率最高的乙烯工程投产成功,镇海炼化也自此拥有2300×104t/a原油综合加工能力和100×104t/a乙烯生产能力,成为我国最大的炼化一体化企业。
镇海炼化100×104t/a乙烯工程是国家建设项目,主要包括乙烯裂解等10套生产装置及配套公用工程,其中100×104t/a乙烯裂解、45×104t/a聚乙烯、65×104t/a环氧乙烷/乙二醇和28.5×104t/a环氧丙烷/62×104t/a苯乙烯等装置,在世界同类装置中规模最大。
在工艺技术上,大部分装置采用国产技术,其中6套装置采用中国石化自有技术,乙烯综合能耗达到国际水平。
中海壳牌石油化工股份有限公司是壳牌化学公司与中国海洋石油总公司各持股50%的合资企业,该公司于2010年3月在惠州大亚湾石化联合装置实施扩能。