控轧控冷1
材料的控轧控冷工艺

材料的控轧控冷工艺
材料的控轧控冷工艺是一种通过控制轧制和冷却过程来改善材料的性能和结构的工艺。
这种工艺通常用于金属材料的加工,如钢铁等。
控轧是指在轧制过程中通过调节轧制温度、变形量和变形速度等参数,以控制材料的晶粒尺寸、组织结构和相变行为。
控轧可以使材料获得较细小的晶粒、均匀的组织和良好的力学性能。
控冷是指在轧制后通过冷却过程来控制材料的组织和性能。
控冷可以通过快速冷却或退火处理来改变材料的硬度、韧性和晶粒尺寸等特性。
控冷可以用于控制材料的相变行为,如马氏体转变和析出行为。
控轧控冷工艺的主要目的是优化材料的性能和结构,以适应特定的应用要求。
这种工艺可以改善材料的硬度、韧性、强度和耐腐蚀性等性能,并提高材料的加工性能和可焊性。
控轧控冷工艺广泛应用于金属制造、建筑、汽车、航空航天等领域,以满足不同材料对性能和结构的要求。
该工艺的应用可以提高材料的品质和成本效益,并推动材料的技术进步和创新。
控轧控冷1

控制轧制与控制冷却
奥氏体状态控制 奥氏体状态: 晶粒尺寸:大?小?
奥氏体状态:蓄积能量
内含能量:高?低? 内部缺陷:多?少?
铁素体、珠光体相变 贝氏体相变 马氏体相变 铁素体、贝氏体相变
相变方向 奥氏体相变条件的控制(阀门) 冷却条件的控制:冷却速度、 开始冷却温度、终止冷却温度、 冷却模式
TMCP的特征
微合金化元素在钢中的主要作用
1.2 控轧控冷强韧化机理
对钢的性能要求越来越高,不仅要求具有高的强度,并且要 具有良好的塑韧性、低的韧脆转变温度以及优异的加工性能 (焊接性能、冷成形性能等)。除对钢材性能的全面要求提 高之外,在钢材的使用上,不断要求降低材料用量、减少工 艺环节、削减生产成本。 在钢材应用上,其室温屈服强度σs、抗拉强度和韧脆转变温 度TC 是钢材的几项基本的力学性能指标。 在大多数条件下σs 和TC是设计选材的最基本标准。因此, 提高钢的σs和降低TC 一直是钢铁材料研究和开发的重点。
1.3 传统TMCP工艺的三个阶段
(1)奥氏体再结晶区变形阶段 t≥950℃ 对加热时粗化的奥氏体晶粒 反复进行轧制并反复再结晶 后使之得到细化 (2)奥氏体未再结晶区变形阶 2 段 t=950℃ r3 950℃~A 奥氏体晶粒沿轧制方向伸长、 压扁,晶内产生形变带,这 种加工硬化状态的奥氏体具 有促进铁素体相变形核作用 (3)奥氏体+铁素体两相区变 形阶段 t<Ar3 相变后为大角度晶粒和亚晶 粒的混合组织 图1 TMCP工艺的三阶段及其组织变化
通常研究的结构材料在室温工作条件下, 通常研究的结构材料在室温工作条件下,最需要考 虑的是屈服强度和断裂强度。 虑的是屈服强度和断裂强度。
屈服强度 σb≥σk 脆性材料 脆性材料的强度 通常以σ 通常以σk表示 断裂强度 σb≤σk 塑性材料 塑性材料的强度 通常以σ 通常以σb表示
控轧控冷工艺的发展及应用

控轧控冷工艺的发展及应用摘要控轧控冷工艺是把钢坯加热到适宜的温度,轧制时控制变形量和变形温度及轧后按工艺要求来冷却钢材。
控轧主要用于轧制细晶粒结构钢,主要原理是在终轧后当钢板在轧机上运行至“再结晶”完成的温度时,选用合适水冷方式获得理想延展性和韧性。
关键词变形量变形温度再结晶1 前言1.1 控轧控冷就是控制轧制和控制冷却,也叫TMCP(热机械变形轧制)+ACC。
比较适合于低碳微合金钢,特别是Nb、V 、Ti复合的。
1.2 控制轧制:是在调整钢的化学成分的基础上,通过控制加热温度、开轧温度,轧制过程温度、变形制度等工艺参数,控制奥氏体状态和相变产物的组织状态,从而达到控制钢材组织性能的目的.1.3 控制冷却:是通过控制热轧钢材轧后的冷却条件来控制奥氏体组织状态、控制相变条件、控制碳化物析出行为、控制相变后钢的组织和性能。
1.4 TMCP:控制轧制和控制冷却技术结合起来,能够进一步提高钢材的强韧性和获得合理的综合性能,并能够降低合金元素含量和碳含量,降低生产成本。
通过控轧控冷生产工艺可以使钢板的抗拉强度和屈服强度平均提高约40~60MPa,在低温韧性、焊接性能、节能、降低碳当量、节省合金元素以及冷却均匀性、保持良好板形方面都有无可比拟的优越性。
2 发展历程2.1 控轧控冷工艺主要是用于生产板材的技术。
该技术的核心是在轧制过程中通过控制加热温度、轧制过程、冷却条件等工艺参数,改善钢材的强度、韧性、焊接性能。
2.2 控制轧制工艺主要用于含有微量元素的低碳钢种,钢中常含有铌、钒、钛,其总量一般小于0.1%。
依据《塑性变形和轧制原理》控制轧制的内容是控制轧制参数,包括温度、变形量等,以控制再结晶过程,获得所要求的组织和性能。
根据塑性变形、再结晶和相变条件,控制轧制可分为三阶段,如下所述。
(1)在奥氏体再结晶区控制轧制:适用于轧制低碳优质钢普通碳素钢低合金高强度钢。
(2)在奥氏体未再结晶区控制轧制:适用于轧制含有微量合金元素的低碳钢,如含铌钛钒得低碳钢。
钢材控轧控冷工艺的原理
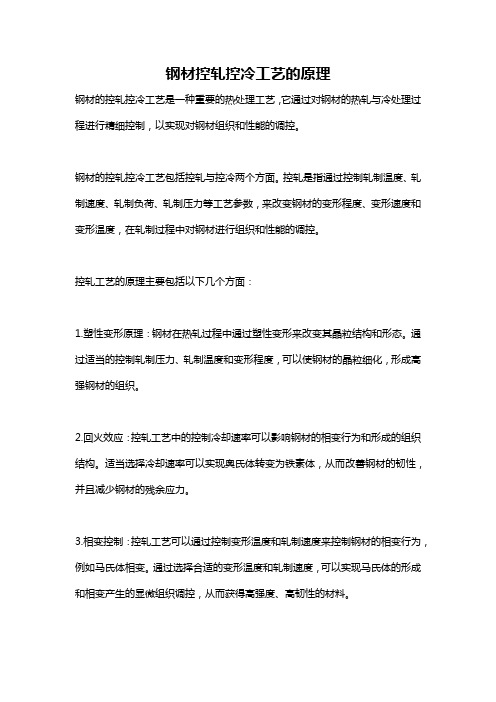
钢材控轧控冷工艺的原理钢材的控轧控冷工艺是一种重要的热处理工艺,它通过对钢材的热轧与冷处理过程进行精细控制,以实现对钢材组织和性能的调控。
钢材的控轧控冷工艺包括控轧与控冷两个方面。
控轧是指通过控制轧制温度、轧制速度、轧制负荷、轧制压力等工艺参数,来改变钢材的变形程度、变形速度和变形温度,在轧制过程中对钢材进行组织和性能的调控。
控轧工艺的原理主要包括以下几个方面:1.塑性变形原理:钢材在热轧过程中通过塑性变形来改变其晶粒结构和形态。
通过适当的控制轧制压力、轧制温度和变形程度,可以使钢材的晶粒细化,形成高强钢材的组织。
2.回火效应:控轧工艺中的控制冷却速率可以影响钢材的相变行为和形成的组织结构。
适当选择冷却速率可以实现奥氏体转变为铁素体,从而改善钢材的韧性,并且减少钢材的残余应力。
3.相变控制:控轧工艺可以通过控制变形温度和轧制速度来控制钢材的相变行为,例如马氏体相变。
通过选择合适的变形温度和轧制速度,可以实现马氏体的形成和相变产生的显微组织调控,从而获得高强度、高韧性的材料。
4.微量元素控制:在控轧工艺中,添加适量的微量合金元素可以改变钢材的组织和性能。
例如添加微量的硼元素可以细化晶粒,改善钢材的塑性和韧性。
控冷工艺是控制钢材在冷却过程中的温度和冷却速度,以实现对钢材组织和性能的调控。
控冷工艺的原理主要包括以下几个方面:1.相变控制:钢材的冷却速率会影响其相变行为和相变产物的组织结构。
通过控制冷却速率,可以实现奥氏体向铁素体的转变,形成细小的铁素体晶粒和均匀的组织结构。
2.马氏体相变控制:通过控制冷却速率,可以控制钢材从奥氏体向马氏体的相变行为。
适当调节冷却速度、冷却温度和冷却介质,可以实现马氏体的形成和马氏体组织的调控,从而获得高强度、高硬度的材料。
3.淬火与回火控制:控冷工艺还可以通过控制钢材的淬火和回火工艺参数,来调控钢材的组织和性能。
适当的淬火工艺可以实现钢材的高强度、高硬度,而回火工艺可以降低钢材的脆性和残余应力。
控轧控冷工艺基本原理
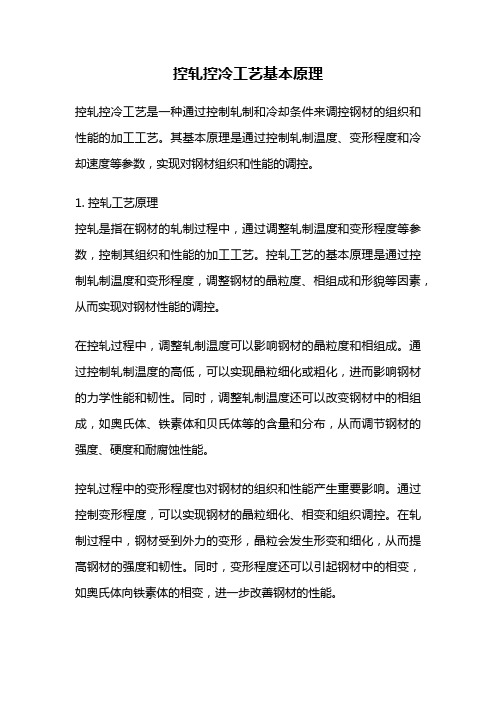
控轧控冷工艺基本原理控轧控冷工艺是一种通过控制轧制和冷却条件来调控钢材的组织和性能的加工工艺。
其基本原理是通过控制轧制温度、变形程度和冷却速度等参数,实现对钢材组织和性能的调控。
1. 控轧工艺原理控轧是指在钢材的轧制过程中,通过调整轧制温度和变形程度等参数,控制其组织和性能的加工工艺。
控轧工艺的基本原理是通过控制轧制温度和变形程度,调整钢材的晶粒度、相组成和形貌等因素,从而实现对钢材性能的调控。
在控轧过程中,调整轧制温度可以影响钢材的晶粒度和相组成。
通过控制轧制温度的高低,可以实现晶粒细化或粗化,进而影响钢材的力学性能和韧性。
同时,调整轧制温度还可以改变钢材中的相组成,如奥氏体、铁素体和贝氏体等的含量和分布,从而调节钢材的强度、硬度和耐腐蚀性能。
控轧过程中的变形程度也对钢材的组织和性能产生重要影响。
通过控制变形程度,可以实现钢材的晶粒细化、相变和组织调控。
在轧制过程中,钢材受到外力的变形,晶粒会发生形变和细化,从而提高钢材的强度和韧性。
同时,变形程度还可以引起钢材中的相变,如奥氏体向铁素体的相变,进一步改善钢材的性能。
2. 控冷工艺原理控冷是指在钢材的冷却过程中,通过调整冷却速度和冷却方式等参数,控制其组织和性能的加工工艺。
控冷工艺的基本原理是通过控制冷却速度,调整钢材的组织和性能。
在控冷过程中,调整冷却速度可以影响钢材的相组成和组织形貌。
通过控制冷却速度的快慢,可以实现钢材中相的相变和组织的调控。
当冷却速度较快时,钢材中的相变会受到限制,从而形成细小的相和均匀的组织。
相反,当冷却速度较慢时,钢材中的相变会较为充分,形成较大的相和不均匀的组织。
不同的冷却速度会影响钢材的强度、硬度和韧性等性能。
控冷过程中的冷却方式也会对钢材的组织和性能产生影响。
不同的冷却方式,如空冷、水冷、油冷等,具有不同的冷却速度和冷却效果。
通过选择合适的冷却方式,可以实现钢材组织的定向调控,从而达到钢材性能的要求。
3. 控轧控冷工艺的应用控轧控冷工艺广泛应用于钢材的生产和加工过程中。
控轧控冷1
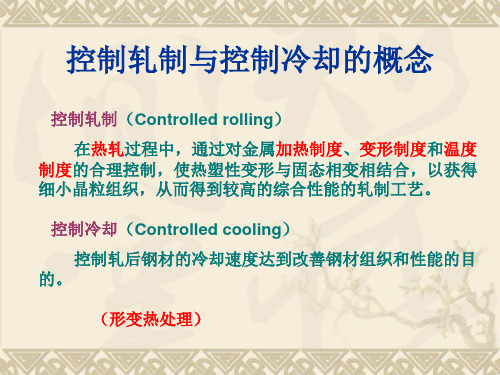
L0
拉伸性能
❖ 断面收缩率ψ: ❖ 断面收缩率ψ是评定材料塑性的主要指标。
AK A0 100%
A0
低碳钢的工程应力一工程应变曲线
true strain-stress line
2.0
Stress / MPa
1.5
Pm
Pb
1.0
0.5
0.0
0.0
0.5
1.0
1.5
2.0
载荷P压入被测材料表面,保持一定时间后卸除载荷,测出压 痕直径d,求出压痕面积F计算出平均应力值,以此为布氏硬度 值的计量指标,并用符号HB表示。
标注:D/P/T如120HB/10/3000/10,即表示此硬度值120 在D=10mm,P=3000kgf,T=10秒的条件下得到的。
简单标注:200~230HB
布氏硬度测定主要适用于各种未经淬火的钢、退火、
正火状态的钢;结构钢调质件;铸铁、有色金属、质地 轻软的轴承合金等原材料。
布氏硬度试验只可用来测定小于450HB的金属材料,
②洛氏硬度(HR)
基本原理—洛氏硬度属压入法洛氏硬度测定时需 要先后施加二次载荷(予载荷P1和主载荷P2)预 加载荷的目的是使压头与试样表面接触良好以保 证测量结果准确。洛氏硬度就是以主载荷引起的
对微量塑性变形的抗力
E /e
拉伸性能
❖ 抗拉强度b: ❖ 定义为试件断裂前所能承受的最大工程应力,
以前称为强度极限。取拉伸图上的最大载荷,即 对应于b点的载荷除以试件的原始截面积,即得抗 拉强度之值,记σ为b=b Pmax/A0
拉伸性能
延伸率: 材料的塑性常用延伸率表示。测定方法如下:拉伸
试验前测定试件的标距L0,拉伸断裂后测得标距为Lk, 然而按下式算出延伸率
控轧控冷
六十年代初:英国斯温顿研究所提出,铁素体珠光体钢中显 微组织与性能之间的定量关系。
著名的Petch关系式明确表明了热轧时晶粒细
化的重要性。
六十年代中期:英国钢铁研究会进行了一系列
研究:降碳改善塑性和焊接性能,利用Nb、V 获得高强度,Nb对奥氏体再结晶的抑制作用以 及细化奥氏体晶粒的各种途径。
六十年代后期:美国采用控制轧制工艺生产出σs> 422MPa的含Nb钢板,用来制造大口径输油钢管。日 本用控制轧制工艺生产出强度高,低温韧性好的钢板, 并开发出一系列新的控制轧制工艺,提出了相应的控 制轧制理论。这期间人们重视奥氏体再结晶行为的研 究,开始认识到未再结晶区轧制的重要性。 七十年代:完成了控轧三阶段,Nb、V、Ti应用逐步 完善。
1.再结晶热轧
2.板材加速冷却
水——钢的最有效的合金化添加剂
1. 控轧工艺分哪几类?控轧实践中最常用的
是哪种工艺?分别画出示意图。 2.Ⅰ型控轧与Ⅱ型控轧相比,哪种工艺轧材 的性能更好些?为什么?
3.如何理解“水是最有效的合金化添加剂”这
句话.
4. 对结构钢的要求有哪些要素?
2.钢的热加工金属学基础
工程应力 ζ=P/A0
工程应变 ε=(l-l0)/l0
A’: 比例极限
A:弹性极限
B:屈服强度
C:抗拉强度
7
6
7 8
真应变:e=lnl/l0
ε=(l-l0)/l0=l/l0-1
l/l0 =ε+1
e= lnl/l0= ln (ε+1)
从上式看出: ε较小时, e≈ ε,随ε↑,其
差别显著 e<ε
Nb钢的晶粒比Si-Mn钢要细,见图2--34.
3.初始晶粒直径
r0↓,再结晶晶粒也越小
钢材控制轧制和控制冷却技术
A F
——转换比,化学成分对转化比有影响。
③、通常热轧通过形变再结晶克使A体晶
粒细化20~40 m,转变后的F体可
细化20 (m8级)
§2控轧控冷理论
(2)、部分再结晶A体晶粒 F体晶粒
①、由两部分组成 1)再结晶细小在其晶界上析出F体晶粒细小。 2)未再结晶晶粒受变形拉长, 由于A没细化,F成核少,易形成粗大的F体和针状 组织——不均匀组织对韧性影响大。
§2控轧控冷理论
(2)常温组织以珠光体为主的钢材 ①、0.43%C,1.4%Mn钢实验 1)普通热轧 2)控轧,再结晶区轧制。 ②、043%C,1.38%Mn,0.023%Nb 控轧 由于Nb加入而处于未再结晶区,在伸长A体 晶界处生成极细F体组织,但在伸长A体晶粒 内形成粗大P体。
§2控轧控冷理论
③、这种钢种最好A体再结晶内充分轧制, 尽量细化A体晶粒,可获细小均匀F体和珠光体。 1)该钢中,在未再结晶区轧制对珠光体等 轴状起不到有效作用
2)加Nb钢在低温轧制时有时反而不利。
§2控轧控冷理论
(3)共析钢 ①、共析钢那样高碳钢的组织为单一P体。 ②、其控制轧制只是细化珠光体团。 ③、希望在A体再结晶区轧制,使A体晶粒细小。 这样既可使珠光体球团变小,又可使析出的网状 碳化物变薄。
三、控轧控冷工艺优点
1、控轧 2、控冷
§2控轧控冷理论
2、强化机制对韧性的影响 (1)固溶强化 (2)位错强化。对塑性和韧性双重影响 (3)沉淀强化 (4)晶界强化
细小均匀的晶粒既可提高强度又可改善塑性和韧性——是控轧的 基本目标。 (5)相变强化 3、冷脆系数
KT表K 示各S 强化机理和成分对强度和韧性的影响
§2控轧控冷理论
3、中高碳钢组织与力学性能的关系 (1)中高碳钢组织对性能的影响
控轧控冷1
• 变形带也是提供相变时的形核地点,因而相变后的铁素体晶粒更 加细小均匀。
• 5 .4在(y+a)两相区的控轧 • Y相由于变形而继续伸长并在晶内形成变形带,在a晶粒内形成 大量的位错,在高温下形戎亚晶,因而强度有所提高,脆性转变 温度降低。(r+a)相轧后形成较强的织构,故在断口上平行于轧制 面出现层状撕裂裂口。
5控轧和控冷工艺在中厚板和带钢生 产中的应用
• 5. 1板钢控轧类型 • 根据轧制过程中再结晶状态和相变机制不同可分为:奥氏体再结 晶型控轧、奥氏体未再结晶型控轧、(r+a)两相区控轧。 • 5. 2再结晶型控轧 • 轧件变形温度较高,一般在功1000℃以上,道次变形量必须大于 奥氏体再结晶变形量。普碳钢的临界变形量比较小,而含铌钢的 临界变形量较大。轧后停留时间长则晶粒长大,形成粗大的奥氏 体晶粒。再结晶控轧主要是利用静态再结晶过程去细化晶粒。 • 5. 3未再结晶型控轧 • 主要是在轧制中不发生奥氏体再结晶过程。一般是在950 C ~Ar3范围内变化,变形使奥氏体晶粒长大、压扁并在晶粒中形成 变形带。奥氏体晶粒被拉长将阻碍铁素体晶粒长大。随着变形量 的加大,变形带的数量增加,分布更加均匀。
•
4控轧和控冷技术的理论基础
• 4.1钢的奥氏体化过程 • 所谓奥氏体化是指在加工前将钢加热到奥氏体区,是形核、长大 均匀化过程。对亚共析钢来说,加热到Ac,以上,进行保温、形 核、长大、剩余渗碳体(Fe3C)溶解和奥氏体均匀化。对于共析钢 和过共析钢来说,加热到Ac,以上,使珠光体变为奥氏体。进一 步加热到Acm以上,保温足够时间,使铁素体或渗碳体溶解,获 得单相奥氏体。 • 4.2钢的变形再结晶 • 变形后的金属加热发生再结晶,根据温度不同有回复、再结晶和 晶粒长大。回复仍为拉长的晶粒,但储存能降低,为前阶段。而 再结晶是新晶粒的形核及长大过程,不是相变,无畸变能。核心 的产生一是原晶界的某部位变为核心。
钢材控制轧制和控制冷却技术PPT课件
一、控制轧制
在热轧过程中通过对金属的加热制度、变形制度和温度制度的合 理控制,使塑性变形与固态相变结合以获得细小的经理组织,使钢材 具有优异的综合力学性能(强度、韧性和焊接性能等)的轧制工艺。
二、控制冷却
控制轧后钢材的冷却速度以达到改善组织性能的目的。
三、控轧控冷工艺优点
1、控轧 2、控冷
第31页/共72页
§2控轧控冷理论
(3)细化F体晶粒 细化F体效果:Nb最显著,Ti次之,V最差。
(4)影响钢的强韧性能 ①、铌:在控轧时,产生显著的晶粒细化和中等沉淀强化。 ②、钛:随Ti含量增加,发生强烈沉淀强化,晶粒细化中 等。 ③、钒:产生中等程度沉淀强化和比较弱的 晶粒细化。
第32页/共72页
①、 增s 加
②、产生织构—强度的方向性,并使高阶冲击能(韧性 状态下冲击能)有所降低。
第20页/共72页
§2控轧控冷理论
6、三种类型的控制轧制 (1)促进F体细化的途径
①、细化A体晶粒 ②、控轧控冷 (2)控轧 ①、第一阶段,A体再结晶区轧制
1)通过反复形变—再结晶,使A晶粒细化 2)实际生产中动态再结晶有困难,主要发生静态再结晶。 3)实际生产中每道次都发生完全再结晶是困难的,存在部分 再结晶轧制,应避免产生混晶的临界压下量(10%)
第13页/共72页
§2控轧控冷理论
④、总变形量和道次变形量要大。
1)总变形量应 45%,可得F体晶粒 5m(12~13级)
2)一道次压下率越大,越易产生变形带,越易获得均匀组织。
⑤、未再结晶区材料强度由固溶强化( sh)和F体晶粒尺寸(d)
等决定。
1
s sh K y d 2
第14页/共72页
- 1、下载文档前请自行甄别文档内容的完整性,平台不提供额外的编辑、内容补充、找答案等附加服务。
- 2、"仅部分预览"的文档,不可在线预览部分如存在完整性等问题,可反馈申请退款(可完整预览的文档不适用该条件!)。
- 3、如文档侵犯您的权益,请联系客服反馈,我们会尽快为您处理(人工客服工作时间:9:00-18:30)。
回 火
3、回火过程的组织变化: 第一阶段(室温~250℃):马氏体中的过饱和碳原 子析出,形成碳化物FexC,得到回火马氏体组织。 第二阶段(230~280℃):马氏体继续分解,同时 残余奥氏体转变为过饱和固溶体与碳化物,得到回火
马氏体组织。
回 火
3、回火过程的组织变化: 第三阶段(260~360℃):马氏体继续分解,碳
鞍钢1700中薄板坯连铸连轧工艺流程
100-150mm厚的板坯经中薄板坯连铸机(1台)铸出并切断后, 直接热装进步进式加热炉(2座)加热,加热好的板坯经炉后 高压水除鳞箱除鳞,进入粗轧机,轧出的20-30mm 厚的中间 坯经辊道输送,进入热卷箱进行空心卷取,经切头飞剪切头, 精轧前高压水除鳞箱除鳞,进入精轧机组轧制,经带钢层流冷 却装置冷却后,由卷取机卷成成品钢卷,再经步进梁、爬坡链、 地面运输链组成的钢卷运输系统运至成品库堆冷、存放、包装、 发货。
为防止低温回火脆性,通常的办法是避免在脆化 温度范围内回火。防止高温回火脆性的方法是加 热后快冷。
第一章 钢材的性能要求
本章内容
第一节 金属材料的性能 第二节 钢的强化机制
第三节 材料的韧性
第一节 金属材料的性能
金属材料的性能
金属材料的性能包含工艺性能和使用性能。
使用性能:是指金属材料在使用条件下所 表现出来的性能。如:力学/机械性能、物 理性能、化学性能。 工艺性能:是指制造工艺过程中材料适应 加工的性能。如:铸造性、锻造性、焊接 性、切削加工性、热处理工艺性。
淬 火
3、钢在淬火时的组织和性能变化 4)马氏体的力学性能 马氏体的硬度主要取决于马氏体的含碳量, 通常情况是随含碳量的增加而升高。 马氏体的塑性和韧性主要取决于它的亚结构。 在相同屈服强度条件下,板条(位错)型马氏体 比片状(孪晶)型马氏体的韧性好得多。
淬 火
3、钢在淬火时的组织和性能变化 5)小结 马氏体转变是典型的无扩散性相变。马氏体 是碳在α —Fe中的过饱和固溶体,具有非常高的 强度和硬度所以,马氏体转变是强化金属的重要 途径之一。
为了保证获得所需淬火组织,又要防止变
5、常用淬火冷却方法
形和开裂,必须采用已有的淬火介质再配以各
种冷却方法才能解决。
淬 火
5、常用淬火冷却方法 通常的淬火方 法包括单液淬 火、双液淬火、
分级淬火和等
温淬火等,如
图所示。。
淬 火
钢的淬透性是指钢在淬火时获得马氏体的
6、钢的淬透性和淬硬性
能力。其大小通常用规定条件下淬火获得淬透 层的深度(又称有效淬硬深度)的距离作为淬 透层深度。
临界切应力
滑移只能在切应力的作用下发生, 使滑移系开动(产生滑移)的最 小切应力称为临界切应力.
c s cos cos
cosψcosλ称取向因子(或Schmid因子)
位错强化
1、完全无位错存在时,在外力 作用下,没有可以发生运动的位 错,材料表现极高的强度。 例如铜,理论计算的临界切应力 约为1500MPa,而实际测出的仅 为0.98MPa。 但制造这种材料非常困难,目前 只能在很小尺寸的晶体中实现 (晶须),用于研究型的复合材料 中。
扩散 退火 再结晶 退 火 去应力 退 火
正 火
正火的应用:
① 用正火作为性能要求的一般结构件的最终热 处理。 ② 亚共析钢采用正火来调整硬度,改切削加工 性能。 160-230HB切削性能最好,低-粘刀,高-废刀
③ 过共析钢的正火可消除网状碳化物。
淬 火
2、淬火的必要性
经过退火或正火的工件只能获得一般的强度
ቤተ መጻሕፍቲ ባይዱ
致,可选用淬透性大的钢。
(4)当要求工件表面硬度高,而心部韧性好时,可选
用低淬透性钢。
淬 火
6、钢的淬透性和淬硬性 钢的淬硬性是指淬火后马氏体所能达到的最高硬 度,淬硬性主要决定于马氏体的碳含量。
回 火
1、定义:回火是把淬火后的钢件,重新加热到A1以
下某一温度,经保温后空冷至室温的热处理工艺。 2、目的:淬火钢件经回火可以减少或消除淬火应力, 稳定组织,提高钢的塑性和韧性,从而使钢的强度、 硬度和塑性、韧性得到适当配合,以满足不同工件 的性能要求。
控轧控冷技术
主讲教师:张峻巍
引
言
人类社会的不断发展和人们日益增长 的物质与文化方面的需求,促进了科学技 术的长足进步。人们不仅在积极地开发新 材料、新工艺和新能源,也在努力地去挖 掘钢铁等传统材料的潜力,提高它们各方 面性能,使其焕发新的生命力。
控制轧制与控制冷却的概念
控制轧制(Controlled rolling)
原子继续析出使过饱和α 固溶体转变为铁素体;
回火马氏体中的FexC 转变为稳定的粒状渗碳体,
得到铁素体和极细渗碳体的机械混合物,即回火
屈氏体。
回 火
3、回火过程的组织变化: 第四阶段(400℃以上):碳化物聚集长大,温度
越高碳化物越大,得到粒状碳化物与铁素体的机
械混合物,即回火索氏体。
回 火
和硬度,对于许多需要高强度、高耐磨条件下工
作的零件则必须淬火与回火处理。
淬 火
3、钢在淬火时的组织和性能变化 1)获得马氏体的条件 (a)通过加热使钢具有奥氏体组织; (b)冷却速度超过临界冷却速度; (c)在Ms~Mf温度范围使过冷奥氏体发生马氏 体转变。
淬 火
3、钢在淬火时的组织和性能变化
降低硬度,改善切削 加热到AC1+20~ 片 状 珠 光 体 和 共 析 、 过 共 性能,提高塑性韧性,40℃,然后缓冷 网 状 渗 碳 体 组 析 钢 及 合 金 为淬火作组织准备 织转变为球状 钢的锻件、 轧件等 改善或消除枝晶偏析,加 热 到 Tm-100 ~ 粗 大 组 织 ( 组 合 金 钢 铸 锭 使成分均匀化 200 ℃,先缓冷,织严重过烧) 及大型铸钢 后空冷 件或铸件 消除加工硬化,提高 加 热 到 再 结 晶 温 变 形 晶 粒 变 成 冷 变 形 加 工 塑性 度,再空冷 细小的等轴晶 的制品 消除残余应力,提高 加热到500~650 尺寸稳定性 ℃ 缓 冷 至 200 ℃ 空冷 无变化 铸、锻、焊、 冷压件及机 加工件
铁碳相图
钢的热处理相变温度
钢在加热时,实际 转变温度往往要偏离平 衡的临界温度,冷却时 也是如此。随着加热和 冷却速度的增加,滞后 现象将越加严重。通常 把加热时的临界温度标 以字母“C”,如AC1 、 AC3 、ACcm 等;把冷却 时的临界温度标以字母 “ r” , 如 Ar1 、 Ar3 、 Arcm等。
淬 火
生产中也常用临界淬火直径表示钢的淬透性。
6、钢的淬透性和淬硬性
所谓临界淬火直径,是指圆棒试样在某介质中淬
火时所能得到的最大淬透直径(即心部被淬成半
马氏体的最大直径),用Do 表示。在相同冷却条
件下,Do越大,钢的淬透性越好。
淬透性的应用: (1)淬透性大的工件易淬透,组织和性能均匀一致; (2)淬火性大的工件在淬火时,可选用冷却能力较小 的淬火介质以减小淬火应力。 (3)对受力大而复杂的工件,为确保组织性能均匀一
马氏体形成过程示意图
淬 火
3、钢在淬火时的组织和性能变化
3)马氏体的组织形态
马氏体有两种基本形态:板条马氏体和片状马氏体。 W(C)≤0.20%时:基本上形成板条状马氏体(也称 低碳马氏体),板条马氏体内有高密度的位错缠结的 亚结构,又称为位错马氏体。
淬 火
3、钢在淬火时的组织和性能变化
板条马氏体
位错强化
1、完全无位错存在时,在外力 作用下,没有可以发生运动的位 错,材料表现极高的强度。 例如铜,理论计算的临界切应力 约为1500MPa,而实际测出的仅 为0.98MPa。 但制造这种材料非常困难,目前 只能在很小尺寸的晶体中实现 (晶须),用于研究型的复合材料 中。
滑移是塑性变形的主要 方式,材料中位错密度 对材料的强度的影响
淬 火
4、钢的淬火工艺 2)淬火保温时间 淬火保温时间主要根据钢的成分特点、加热介
质和零件尺寸来确定。 (a)含碳量越高,含合金元素越多,导热性越差,
则保温时间就越长; (b)零件尺寸越大,保温时间越长; (c)生产中常根据经验确定保温时间。
淬 火
4、钢的淬火工艺 3)淬火冷却速度 淬火冷却介质选择的原则: (a)为保证获得马氏体组织,要求V冷却≥V临界; (b)为保证零件不因淬火应力而开裂,要求V冷却 不应太大,应该选择合适的冷却介质。
4、回火的种类: 1)低温回火(150~250℃) 回火的目的是降低应力和脆性,获得回火马氏 体组织,使钢具有高的硬度、强度和耐磨性。低温 回火一般用来处理要求高硬度和高耐磨性的工件,
如刀具、量具、滚动轴承和渗碳件等。(HRC≥60)
回 火
4、回火的种类: 2)中温回火(350~500℃) 回火的目的是获得回火屈氏体,具备高的弹
在热轧过程中,通过对金属加热制度、变形制度和温度 制度的合理控制,使热塑性变形与固态相变相结合,以获得 细小晶粒组织,从而得到较高的综合性能的轧制工艺。
控制冷却(Controlled cooling) 控制轧后钢材的冷却速度达到改善钢材组织和性能的目 的。 (形变热处理)
轧 制
轧制是通过两个或两个以上旋转轧辊间的轧件产生压缩变形,使其横 断面面积减小与形状 改变,而纵向长度增加的一种加工方法。
淬 火
4、钢的淬火工艺 将钢加热到Ac1或Ac3以上,保温一定时间,
然后快速冷却以获得马氏体组织的热处理工艺称 为淬火。
淬 火
4、钢的淬火工艺 1)淬火加热温度
淬火加热温度的选择应以得到细而均匀的奥
氏体晶粒为原则,以便冷却后获得细小的马氏体