船体分段划分图设计规范
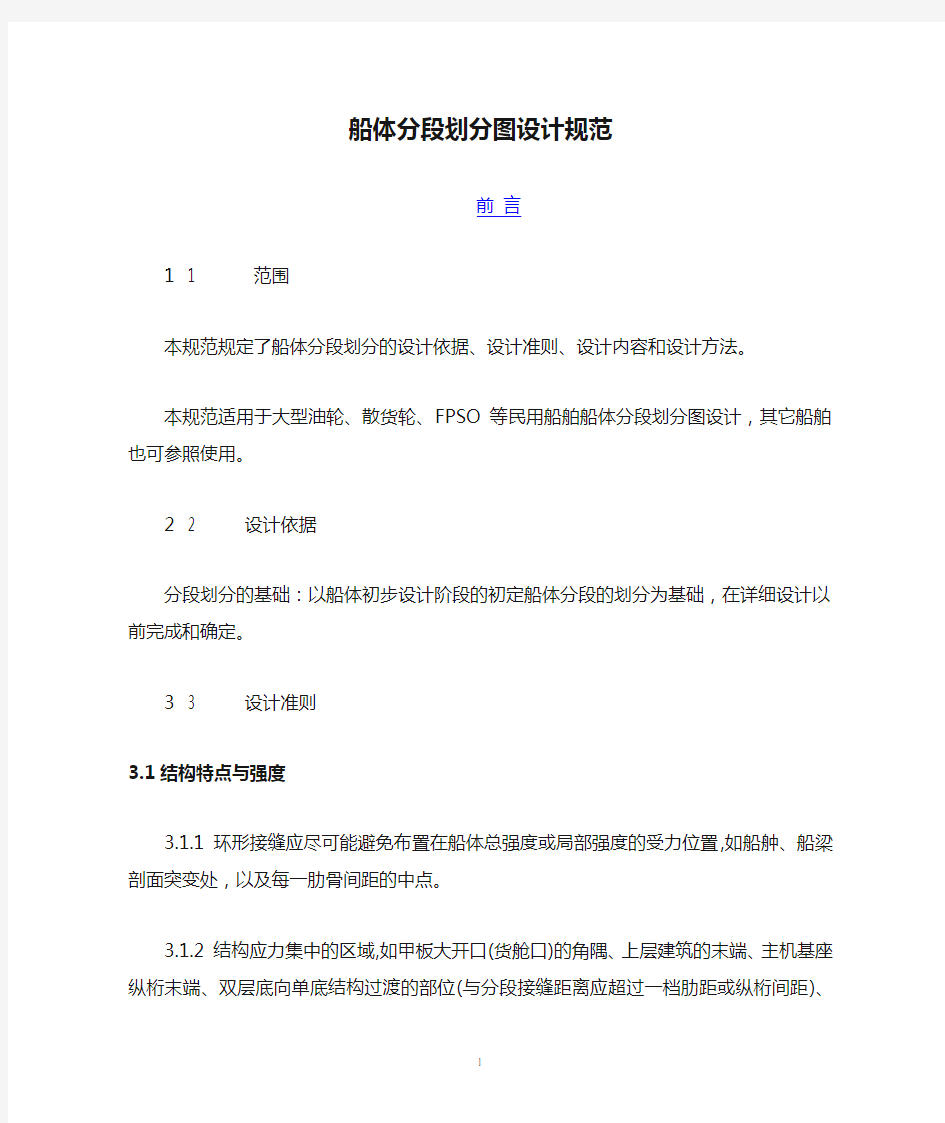

船体分段划分图设计规范
前言
11范围
本规范规定了船体分段划分的设计依据、设计准则、设计内容和设计方法。
本规范适用于大型油轮、散货轮、FPSO等民用船舶船体分段划分图设计,其它船舶也可参照使用。
22设计依据
分段划分的基础:以船体初步设计阶段的初定船体分段的划分为基础,在详细设计以前完成和确定。
33设计准则
3.1结构特点与强度
3.1.1环形接缝应尽可能避免布置在船体总强度或局部强度的受力位置,如
船舯、船梁剖面突变处,以及每一肋骨间距的中点。
3.1.2 结构应力集中的区域,如甲板大开口(货舱口)的角隅、上层建筑的末
端、主机基座纵桁末端、双层底向单底结构过渡的部位(与分段接缝距离应超过一档肋距或纵桁间距)、机舱海水箱,应避免布置分段接缝(参见图
A.1)。
3.1.3对纵骨架式的船体,应尽可能减少横向分段接缝的数目;为保持一定
的长度,必要时可将分段作纵向划分。对横骨架式的船体,一般尽可能减少纵向划分,以保持结构的连续性。
3.1.4 对同类型结构,如横向封闭型结构(如边水舱、双层底)、甲板或舷
侧的平面板架结构等,应尽可能采用同一的划分方法(参见图B.2、图C.4)。
3.1.5 分段接缝应尽可能选择在结构原有板缝或节点零件(如肘板)的连接
部位。尽量采用优化设计使分段的长度与结构强度要求的分布区域相匹配,达到减少钢板拼缝的目的。
3.1.6分段应具有足够的刚性,使不致因焊接、火工校正及翻身吊运而引起
较大的变形。
3.2工艺和施工条件
3.2.1 货舱区平行舯体部分,要充分利用平直分段流水线,满足平直分段流水线的生产工艺要求,并保证平直分段的重量和尺寸在平直分段流水线的生产能力范围之内(尺寸在20米×20米以内,高度在5米以内,少量分段高度可在7米以内);上下边水舱分段主要考虑尺寸和形状,同时也要考虑加强和翻身吊运的方便性,要满足曲面生产中心的生产能力(尺寸在20米×20米以内,少量分段可超长,高度在12米以内);艏、艉分段以结构合理性划分。
3.2.2 分段应尽可能根据钢板的尺度划分(长度和宽度,但主要是长度。钢板的常用尺寸为4米×20米,单张板重量在20吨以内,最佳长度取19970毫米。但公司可流转钢板的最大规格为
4.5米×22.5米),以减少对接缝,提高钢材利用率。
3.2.3 分段的划分应考虑装配和焊接的方便性。尽量在大接缝处创造比较良好的操作空间,同时考虑舾装、涂装的方便性。分段尽量形成开敞式,以便出砂、搭脚手架,检查和涂装作业等(参见图A.2、图C.4)。
3.2.4 分段的划分应有利于最大限度地采用自动和半自动焊接。为此,船体平行舯体以及平直部分的分段尺寸,可划得大些,艏艉部位曲型较大的分段则可划得小些。同时,曲度较大不能采用自动焊的部分,应尽可能不要与平直部分划在同一分段内。
3.2.5 单一产品的分段,应尽可能利用结构上的特点,减少或简化制造分段所需的工艺装备(如胎架、加强材等)。
3.2.6 分段接缝的位置,应为船舶预舾装和涂装作业创造有利条件。如充分考虑相邻分段安装件的布置,分段内的舾装单元与结构的配合,尽量减少接缝处的管子接头,使分段具有单独进行密性试验的条件。尽量保证封闭型舱室涂装的完整性,减少焊缝对舱室涂装的破坏等。
3.2.7 分段接缝处结构的参差(即板与骨架的相对位置),应考虑船坞装配的程序及操作的方便性。目前采用的接缝处参差的形式有两种:“阶梯形”和“平断面形”(即“一刀齐”)。阶梯形结构应设在同一肋骨间距内,以利操作和控制焊接变形。
3.3生产计划和劳动量
分段划分的分段数量应考虑工厂的劳动组织及场地面积。尽量使装配工序作业量的变动要少。若平直中心生产能力较大,而曲面中心、船坞较紧张时,则可划分较多的平面分段(如散货船顶边水舱,可划分为甲板、舷侧及内斜侧三个平面分段),减少密闭区域内和高空脚手架上作业,将平面分段合成立体、半立体分段或总段,然后吊上船坞安装,以利劳动力的展开和船坞周期的缩短。
3.4起重运输能力
公司的起重运输能力是决定分段尺寸和重量的主要因素。所谓起重能力,是指平直中心和曲面中心装配焊接区域的起重能力、制造部运出分段时的输送条件和方法、船坞起重能力(如平直中心流水线的两台升高台车负载能力在250吨以内、曲面中心两台150吨吊车负载能力在270吨以内、大型平车的负载能力378吨、船坞门式起重机使用吊排时总段重量控制在550吨以内、无吊排时总段重量控制在600吨以内),以及分段翻身的条件和能力等。比较理想的分段重量,应接近制造部和船坞区域的最大起重量;
分段尺寸则应在起重运输条件允许范围之内。在决定分段的重量时,还应考虑到分段的临时加强材料和预舾装的重量。
4设计内容
4.1 分段要素表:总段名及组成总段的有关分段名、以及各分段的重量、尺寸(参
见附录B)。
4.2 分段划分图
4.2.1中纵剖面视图:标明分段横接缝肋位、分段长度、外板纵接缝高度、
分段名(参见图A.1、图C.1)。
4.2.2主甲板、舱底、平台等剖面视图:标明分段横接缝位置、分段纵接缝
距舯尺寸、分段名(参见图A.1、图A.2、图C.1、图C.2、图C.3)。
4.2.3典型横剖面视图:标明分段纵接缝距舯尺寸、外板及舱壁纵接缝高度、
分段名(参见图A.2、图C.4)。
4.3 总组分段
分段划分图完成后,要参考单个分段的形状和重量来决定总组分段,以缩短船坞周期,使在船坞内合拢的分段尽可能的少。在分段划分图上,由几个分段组成的总段应用点划线交叉表示出总段(参见图A.1、图A.2)。
5 设计方法
5.1底部分段
5.1.1分段长度
根据船舶类型和平直中心流水线的生产能力, 最大不许超过22.5米。当采用纵向划分时,比较理想的分段长度在(18~20)米范围内(参见图A.1)。
5.1.2 分段的横向划分
双层底一般均划成环形分段,两端应尽可能带有实肋板。
分段接缝处的外板、内底板及骨架,通常以平断面形接头为宜。
5.1.3 分段纵向划分
当大型船舶的底部为纵骨架式时,可采用纵向划分,以减少纵向结构的对接接头,并有利于船坞装配时调节分段的高度和半宽。但对横骨架式,应尽量避免作纵向划分,以减少对接工作量。
分段纵向接缝的位置,当划为两个分段时,应在中桁材附近;当划为三个分段时,应在旁桁材附近;同时,接缝处的结构应呈阶梯形布置,或平断面形。
5.1.4分段高度的划分
平直的双层底分段在平直中心的流水线上反造,出流水线后翻身焊接,所以分段须保证内底板是个平面,双层底分段的高度即为内底板高度。
单底分段的高度,一般不宜超过肋板上缘(200~300)毫米,并考虑平直中心可通过分段的允许高度。
5.2上下边水舱分段
5.2.1分段的长度
分段的长度可根据钢板规格,一般取(18~20)米,长度应与底部分段一致。
5.1.2 分段的横向划分
分段的端接缝应尽量布置在曲率变化较小的部位。当采用总段或半立体分段建造时,分段接缝应与甲板分段接缝在同一平面内。
5.1.3 分段的纵向划分
当具有两层或两层以上甲板而又必须将舷侧分为上、下两个分段时,其纵向接缝应位于中间甲板(或平台)以上(100~150)毫米,且最好带有中间甲板的
边板,以利安装。
上下边水舱分段连接处的接缝,应考虑下列因素:
a)a)骨架与板避免错开过多;
b)b)分段翻身吊运可靠;
c)c)便于分段在船坞内的安装。
5.1.4 分段高度的划分
除边水舱、边油舱等立体分段外,一般的舷侧分段仅包括舷侧骨架——肋骨、强肋骨和舷侧纵桁。对纵骨架式的舷侧分段,还可带有横舱壁边板和甲板边板,以增加分段的刚性。但限于涂装中心涂装房的高度,分段进涂装房时的高度一般不许大于12米。
5.3甲板分段
5.3.1分段的长度
根据钢板规格,一般取(12~20)米,最长不超过22.5米。
5.3.2分段的横向划分
分段的端接缝应避免位于舱口角隅或将舱口割开。
分段的端接缝应尽量布置在横舱壁附近,以利船坞装配。
分段接缝处板和骨架的参差,可根据工艺上的考虑采用阶梯形或平断面形。
5.3.3 分段的纵向划分
当中间甲板的边板具有折角形式时,则甲板分段的边接缝可取在折角线处,并将折角板划入舷侧分段内。如折角线接近船舯部位,应将两侧的折角线划入中间甲板分段,以方便舷侧分段制造。
5.3.4 分段高度的划分
一般的甲板分段仅包括甲板骨架——横梁、强横梁和甲板纵桁等。当纵骨架式的甲板纵桁和甲板纵骨贯穿横舱壁,或甲板分段的长度跨及两道横舱壁时将横舱壁的上部作为围槛板形式划入甲板分段。甲板间轻围壁的围槛板,也应划入甲板分段内。舱壁和轻围壁的围槛板的高度,一般约(300~500)毫米,也可取为甲板纵桁或连接肘板的高度。
5.4舱壁分段
在多层甲板的船体中,一般应使舱壁在甲板处切断,而使甲板连续通过。
甲板间的舱壁,原则上应保持一个完整的独立分段,不宜再作分割,以减少船坞内的对接工作量。但对纵骨架式船舶,其边缘部分可作为边板(围槛板)分别划入甲板分段和舷侧分段,以利安装。
对单底船,若舱壁(包括纵、横舱壁)直接座于底部外板上,且不位于底部分段间的连接处,则舱壁分段的下部可划入底部分段(可高出肋板约100毫米)。
大型船舶的槽形舱壁,可以分左右舱壁分段和中间舱壁分段。当左右舱壁分段参加舷侧总段总组时可增加总段强度,并简化槽形舱壁在船坞搭载时的对接焊工作。划分中间舱壁分段时可连上下墩座,上墩座的面板也连在舱壁分段,以方便搭载时的焊接工作(参见图A.2)。
5.5艏、艉总段
5.5.1 艏、艉部分在重量和尺寸允许的情况下,应尽量划分为总段。艏总段的横向接缝宜设在艏尖舱壁后1/4肋骨间距处,艉总段的横向接缝宜设在艉尖舱壁前1/4肋骨间距处(参见图A.1)。
5.5.2 当艏、艉总段的重量或尺寸超过起重能力时,可再将总段沿高度划成(3~6)个半立体分段,其边接缝一般取在中间甲板或平台以上(150~200)毫米,同时也可将肋骨设计成不连续的上下部分。
5.5.3 球鼻部分可单独划为带有舱壁和平台的封闭的球鼻艏分段。
5.6上层建筑分段
上层建筑(包括甲板室)分段的高度均按甲板层划分,即为其本身的高度(参见图A.1、图C.1)。
由于上层建筑结构较弱,刚性不足,当长度较大时,可在横向划分为若干段。通常上层建筑分段不作纵向划分。
本公司对上层建筑的舾装有完整性要求,当上层建筑分段单独完成后,可在平台区总组成多层上层建筑的立体总段,以利进行上层建筑整体舾装。为此,当上层建筑分段横向划分时,上层建筑各层的横向接缝,最好布置于同一船体横剖面上。
附录 A
(资料性附录)
175000DWT船体划分图
内容见图A.1~A.2
图A.1 中纵剖面和主甲板船体分段划分图
图A.2 舱底、三平台、二平台和典型横剖面船体分段划分图
分 段 划 分 图
H U L L B L O C K D I V I S I O N
F r 106+600183607000501F r 46+150
F r 47+150F r 46+150
1790018300
F r 14+20012200 A /B
7400 A /B
15200 A /B
18800 A /B
110111
F r 5+100
182/92
112
183/93
3000 A /B
F r 30-200913
907
912
911
142/52
144/54
143/53
904
903
905
906
122/32
902
124/34
123/33
901102
101
8050
F r 37+100F r 14+200
620183
193
F r 30-200F r 30-2005600
4400
144
154
F r 24+200
620
109
R100124
134
F r 41-200
18960262/72622/32561/71621/31
511621F r 66+760261/71623/33512562/72263/73
17280F r 87+610622623
521561571
5316634502522532631
5335625729000503523632
633
577269/79517
629/3919970
F r 170+660U P P E R D E C K P L A N
19970中 纵 剖 面C E N R E R L I N E E L E V A T I O N
19970265/75625/35563/73624/34513F r 126+760
264/74626/36514564/74266/76F r 148+710主 甲 板525
563524
53457390005045355645749000505526
53619970566/76565/75515627/37
56019970267/77F r 192+610628/38516F r 214+560268/7852756557553790005065075285665385769000567529539653
F r 298-790643
1741018760
F r 258+150567/77568/78
518641/5119660
F r 236+510281/91642/52569-79
643/53
519
F r 278+710
282/92
642
283/93
9000568508541
5785517250542
509
552543
569
553
579
652
9800 A /B
5000 A /B
19400 A /B
14600 A /B
822/32823/33
824/34
825/35803
810
811
F r 315-200
F r 310+600
10000801
835
825200
7200510811
总 长:289.00M 垂线间长:279.00M 型 宽: 45.00M 型 深: 24.50M 设计吃水: 16.50M 分段数量: 209
B R E A D T H (M L D )分 段 划 分 图
H U L L B L O C K D I V I S I O N
L E N G T H B .P .L E N G T H O .A .P R I N C I P A L P A R T I C U L A R S
主 尺 度
B .L .278238
T Y P I C A L T R A N S V E R S S E C T I O N 2
三 平 台
3R D P L A T F R O M
110
152
142
200F r 14+101
102261221
222
262
271
231272
232
200
122
132
F r 30-200
二 平 台2N D P L A T F R O M
143
153
200
123
133
3100
F r 30-200
F r 14+
1400
235225265T Y P I C A L T R A N S V E R S S E C T I O N 1典型横剖面一223263233273224264274234275(425)(435)
(405)890015065
15580
11340
9000F r 159F R 130,F R 188,F R 216,F R 244
526424S
266
626B .L .
(433)(423)(403)226
505(436)(426)(406)236
2655
L
C 404
P .D .S
536
(437)
(427)(407)276
434舱 底典型横剖面二D O U B L E B O T T O M P L A N
226266
27623622726727723712960
622636B .L .522262
421B .L .
232
65345026634
F r 74
L
C P .
D .401222
2655
532
431
272
T Y P I C A L T R A N S V E R S S E C T I O N 4
292
438
D E S I G N D R A F T B L O C K N U M B E R D E P T H (M L D )T Y P I C A L T R A N S V E R S S E C T I O N 3
典型横剖面三228268229269279239241
281291251223
890015065
15580
113409000
632
B .L .
623S
523
422503
F r 102
L
C P .
D .402
2655
533
423233
242282243
283
292
252
293
253
200
100
典型横剖面四12960
642
1700
S
B .L .1400
633
542
282B .L .
428509
P .D .F r 272
71507250
2655
C L
408652552
B .L .
(资料性附录)
FPSO船体划分图
内容见图C.1~C.4
图C.1 侧视图和主甲板船体分段划分图
图C.2 舱底和中纵舱壁船体分段划分图
图C.3 艏楼甲板和A、B、C、16330平台船体分段划分图图C.4 典型横剖面船体分段划分图
1997019300
100
16430
6970
18025100
8725
8725
19970
19970199701997018470199701943019970100
16700
22200
861519470
16500
8200100
100
100
7000
10075
75
10000
2570
15090
21600 75
船体分段吊装工艺
船体通用工艺------船体分段吊装工艺 船体分段吊装工艺 一、适用范围 1、适用于各种分段的吊装、翻身、移位、运输。 2、上建的整体吊装另见有关上层建筑整体吊装工艺。 二、工艺内容 随着生产规模不断扩大发展,所有工艺规程、施工细则、操作步骤、实施方法均应该制定相应的工艺文件。以保证文明生产、提高产品质量。船体的建造通常采用构件小组装、中组装(分段建造)、大组装(分段大合拢)的建造方式,有关建造中的吊装、翻身、移位、运输的起重工作须制定相应工艺文件,以保证船体建造和安全生产。 有关分段吊装、翻身、移位、运输工艺如下: 1.分段所采用的吊装、翻身眼板应进行专门的三化设计、即系列化、标准化、通用化。 并具有互换性和多次使用性,并有足够的强度和安全系数。 2.分段的划分,首先考虑分段的实际吊重(分段重量加上临时加强辅助材重量),应 符合吊车的许用负荷。不得超过起重设备吊车的许用负荷。 3.在分段图中,标明吊装眼板、翻身眼板规格大小、安装位置及其数量。 4.眼板的焊接必须由二类以上的焊工施工。焊接材料应用碱性焊条如结507及CO2 焊丝。检验,验收。 5.分段吊装、翻身、移位、运输、堆放、上船台等起重工作均按照生产计划与作业场 地安排。 6.分段吊离胎架前,须检查,验收。分段的实际吊重(分段重量加上临时加强辅助材 重量),应符合吊车的许用负荷,才可进行吊运工作。 7.分段起吊前,应检查分段吊运周围环境,人员情况,以确保安全,然后起吊。 8.分段到达堆放场地,要按照分段实际形状确定垫墩高度及垫墩位置,其最低高度不 低于600mm。垫墩布置在分段有强构件结构位置,以避免分段变形、损坏。 9.分段翻身眼板确定,应预先在图纸中表明,并按下列要求进行: a、根据分段尺寸、结构情况确定分段翻身方向(横翻、纵翻)。 b、翻身眼板位置要要考虑钢索与外板的相关位置,不损坏钢索。 c、吊车的安排,一般要根据生产场地设备配置情况而定。 -- 1 --
典型船体结构术语
典型船体结构术语
1典型船体结构术语 图1:单壳油船—典型横剖面图 single hull oil —typical transverse section (transverse adj.横向的, 横断的) 1.强力甲板板strength deck plating (strength n.力, 力量, 力气, 实力, 兵力, 浓度) 2.甲板边板stringer plate 3.舷顶列板sheerstrake (strake n.束紧车轮用的轮铁, 船底板,列板) 4.舷侧板side shell plating (shell n.贝壳, 外形, 炮弹;vt.去壳,炮轰;vi.剥落, 脱壳) 5.舭板bilge plating 6.底部外板bottom shell plating 7.龙骨板keel plate 8.甲板纵骨deck longitudinals 9.甲板纵桁deck girders 10.舷顶列板纵骨sheerstrake longitudinals 11.纵舱壁顶列板longitudinal bulkhead top strake 12.船底纵骨bottom longitudinals 13.船底纵桁bottom girders 14.舭纵骨bilge longitudinals 15.纵舱壁底列板longitudinal bulkhead lower strake (bulkhead n.隔壁, 防水壁) 16.舷侧纵骨side shell longitudinals 17.纵舱壁板longitudinal bulkhead plating (remainder) 18.纵舱壁纵骨longitudinal bulkhead longitudinals 25.甲板横材(中央舱)deck transverse (centre tank ) 26.肋板(中央舱)bottom transverse (centre tank ) 27.甲板横材(边舱)deck transverse (wing tank ) 28.舷侧垂直桁材side shell vertical web 29.纵舱壁垂直桁材longitudinal bulkhead vertical web 30.肋板(边舱)bottom transverse wing tank 31.横撑材struts 31.桁材面板transverse web face plate 图一
船体分段吊耳制作安装技术要求
大连中远船务工程有限公司企业标准 Q/DZY JS/S- 006-2007 船体分段吊耳制作安装技术要求 Fabrication &Installation Technology Requirement Of Lifting Eye For Hull Block 2007– 07–发布试用 大连中远船务工程有限公司
前言 为适应公司生产发展的需要,保证船体建造过程中吊装作业的安全,满足分段(结构)吊装工艺设计、吊耳制作安装及检验的要求,使船体分段(结构)吊耳的使用逐步走向标准化,特统一制定本技术要求,并通过在公司范围内一段时间的推广应用,逐步加以完善。 本技术要求适应于我公司承建(修)的船舶产品及结构的分段吊装设计、现场施工、管理、安全等工作。 本技术要求主要规定了吊耳的系列型式、制作安装要求等。 本标准由大连中远船务工程有限公司标准化工作组提出。 本标准由大连中远船务工程有限公司技术部归口。 本标准起草单位:大连中远船务工程有限公司技术部。 本标准编制人:张平
1 范围 1.1本技术要求规定了吊耳系列的选用、制作及检验技术要求。 1.2本技术要求适用于公司范围内修造产品的吊装作业及管理。非船产品结构可以参照。 2 引用文件 参照国内有关船厂多年应用的吊装作业标准及结合公司状况汇总编制。; 3 吊耳系列 3.1吊耳类型、示意图形及尺寸标注、安装基准见表1:
3.2 吊耳系列型号及结构型式示意图 3.2.1 A型吊耳系列,其制作安装形式见图1,规格尺寸见表2:
3.2.2 B型吊耳系列,其制作安装形式见图2,规格尺寸见表3:
船舶产品设计要点
船舶产品信息建模 1 船舶产品设计阶段概述 船舶设计分为初步设计、详细设计和生产设计三个阶段。 1 初步设计(又称合同设计) 初步设计是在深入分析船舶技术任务书和调查研究的基础上,对船舶总体性能和主要技术指标动力装置、各种系统进行设计,并通过理论设计、资料对比和必要的模型试验来确定产品的基本技术形态、工作原理、主要参数、结构形式和主要设备选型等重大技术问题。初步设计阶段从按照客户提出的要求设计开始,到与客户签订合同为止。 1-1初步设计类图 2详细设计 详细设计的依据是造船合同和经审查通过的初步设计文件。任务是在初步设计的基础上,根据合同约定的技术文件,以完成技术文件送审和最终确定船舶全部技术性能的目的。
1-2详细设计类图 3 生产设计 生产设计是对造船施工的各种工程技术问题进行分析研究,对制造方法和有关技术措施作出决策,并用图、表和技术文件等方式表达出来,作为编制生产计划和指导现场施工的依据。 按专业分,生产设计分为船体生产设计、舾装生产设计、轮机和电气生产设计四部分。 生产设计从设绘分段结构图和舾装区域综合布置图开始,到完成全部施工文件设计为止。 生产设计 船生产设计体 舾装生产设计 轮机生产设计 电气生产设计 涂装生产设计 管系生产设计 通风生产设计 1-3生产设计类图
2 船体设计 船体设计类图 2.1 船体参数设计 船舶作为一种外形庞大的工业产品,一个复杂的空间几何体,它的大小也用尺寸标注来表示。如同某些产品标注其外形尺寸一样,这些表征船舶大小的尺寸称为船舶的主要尺度。船的主尺度有:总长、型宽、型深、设计水线长、设计水线宽、型吃水 从船舶主尺度的比值可以看出船舶长短肥瘦的形状特征。主尺度比值:长度宽宽比、型宽吃水比、长度吃水比、型深吃水比、长度型深比 船型系数表示船舶下水部分的丰满程度,还能进一步表明船体水下部分的形状特征。船型系数:面积系数中剖面系数、体积系数、
大型船舶船体建造识图
2. 图线及其应用: 表2-1 图线及其应用(续) 序号名称型式(宽度)应用范围示例 1 粗 虚 线 (b) 不可见板材简化线(不包括 规定采用轨道线表示的情况) 轨 道 线 (b) 主船体结构图内不可见水 密板材简化线(肋骨型线图、分 段划分图等除外) 2 细 虚 线 (
表2-1 图线及其应用(续) 序号名称型式(宽度)应用范围示例 7 细 双 点 划 线 (
3. 图形符号: 图形符号按表1-4规定。 表1-4 图形符号 序号名称符号示例1 吃水符号 2 船中符号 3 轴系剖面符号 4 端 接 缝 和 边 接 缝 符 号 一 般 接 缝 分 段 接 缝 5 连续符号 6 间断符号 7 视向符号 8 肋位符号FR
表1-4 图形符号(续) 序号名称符号示例 9 小 开 口 剖 面 符 号 (无扁钢开口) (有扁钢开口) 9 (续) 小 开 口 剖 面 符 号 (无面板) (有面板) 舱底 10 剖切符号
船体分段装配图设绘要领
Q/SWS 52-003-2005 船体分段装配图设绘要领 1 范围 本标准规定了船体分段装配图的设计依据、内容要点、图面要求和校审要点。 本标准适用于各类船舶的船体生产设计。 2 规范性引用文件 Q/SWS 12-001-2001 船体制图 Q/SWS 41-003-2004 船舶结构焊接与坡口型式选用规定 Q/SWS 52-012-2003 船体结构流水孔、透气孔和通焊孔形式 3 设计依据 3.1 船舶建造方针 3.2 分段划分图 3.3 肋骨型线图 3.4 船舶结构焊接与坡口型式选用规定 3.5 船体结构理论线图 3.6 结构详细设计退审图(包括船东退审图、船检退审图) 3.7 焊接规格表 3.8 金属船体制图 3.9 船体余量布置图 3.10 船体临时通道及临时工艺孔图 3.11 船体节点详图 3.12 船体结构流水孔、透气孔和通焊孔形式 3.13 船体强力构件开孔及补强 4 内容要点 4.1 设计要点 4.1.1 分段装配图应准确反映分段所有的结构及精度、焊接等工艺信息,还应当包括标准舾 1
Q/SWS 52-003-2005 装件、其它专业提出的结构加强和预开孔等内容。其内容通过封面、组立树、分段重量重心、组立顺序图、安装材料及预舾装品目录、支柱胎架图、胎架二次划线图、外板展开图、甲板平面图、纵剖面图、横剖面图、局部剖面图和节点详图等方式进行表明。 4.1.2 船体分段装配图总体设计要领 4.1.2.1 内容要求 a) 船体分段装配图中除特记外,必须包括图号、页数、比例; b) 船体分段装配图中必须完整反映船体各类构件的组立名、零件号、板厚、材质等信息,必要时须标注几何尺寸; c) 组立内主要型材大小、板厚及材质等信息应标注在组立名下,剖面内可不需再次标注; d) 船体分段装配图中应标明在施工过程中的临时工艺孔; e) 对于可以做成永久性吊环的结构,应在装配图中反映出来; f) 装配图必须标明分段余量及余量切割阶段符号,焊接补偿量符号; g) 装配图需反映与其它专业的协调问题,其中包括:其它专业提供的通过结构的管子、风管、电缆、放水塞及人孔盖的预开孔和孔加强;参照舾装图纸确认与舾装有关联 的基座垫板,确认甲板(平台)上面有没有安装柱子和垫板,并确认这些垫板与甲 板(平台)下型材的通气孔、流水孔是否有干涉; 垫板 参照舾装图纸标明有舾装用途的管子支柱的安装精度要求; h) 结构图必须标明倾斜构件的安装角度。装配角度是指两个零件装配面与面形成的角度,只在不等于90o时才在图纸上标记。由于梁拱或舷弧完全相等而在零件之间发生 装配角度时,在形成锐角的方向标记装配角度; 2
船体分段吊耳制作安装技术要求
Q/DZY 大连中远船务工程有限公司企业标准 Q/DZY JS/S- 006-2007 船体分段吊耳制作安装技术要求 Fabrication & Installation Technology Requirement Of Lifting Eye For Hull Block 2007– 07– 发布试用 大连中远船务工程有限公司
前 言 为适应公司生产发展的需要,保证船体建造过程中吊装作业的安全,满足分段(结构)吊装工艺设计、吊耳制作安装及检验的要求,使船体分段(结构)吊耳的使用逐步走向标准化,特统一制定本技术要求,并通过在公司范围内一段时间的推广应用,逐步加以完善。 本技术要求适应于我公司承建(修)的船舶产品及结构的分段吊装设计、现场施工、管理、安全等工作。 本技术要求主要规定了吊耳的系列型式、制作安装要求等。 本标准由大连中远船务工程有限公司标准化工作组提出。 本标准由大连中远船务工程有限公司技术部归口。 本标准起草单位:大连中远船务工程有限公司技术部。 本标准编制人:张平
1 范围 1.1本技术要求规定了吊耳系列的选用、制作及检验技术要求。 1.2本技术要求适用于公司范围内修造产品的吊装作业及管理。非船产品结构可以参照。 2 引用文件 参照国内有关船厂多年应用的吊装作业标准及结合公司状况汇总编制。; 3 吊耳系列 3.1吊耳类型、示意图形及尺寸标注、安装基准见表1:
3.2 吊耳系列型号及结构型式示意图 3.2.1 A型吊耳系列,其制作安装形式见图1,规格尺寸见表2:
3.2.2 B型吊耳系列,其制作安装形式见图2,规格尺寸见表3:
《船体结构与制图》课程标准
《船体结构与制图》课程标准 一.前言 (一)课程的性质和作用: 《船体结构与船体图识绘》是船舶工程技术专业的一门核心专业课程,是学生学习船舶工程技术的专业基础课,也是学生职业岗位能力的基本能力训练课程。其功能在于让学生通过一系列船体结构的模型、实船、船体图样的识读及船舶图样的绘制,认识船体结构的形式、构件种类、构件名称,掌握船体制图的有关标准、规则和船体图样的绘制方法,从而具备船体加工与装配、造船生产设计、生产组织与管理等职业岗位所需要的基本能力,为学生顶岗就业夯实基础;同时培养学生认真细致、精益求精的工作作风,并为后续专业课程的学习作好前期准备。 后续课程是“船体放样”、“船体建造工艺”、“船舶质量检验与管理”等。 (二)课程基本理念: 本课程的功能是通过对船体结构和船体制图的基础知识,使学生掌握识读和绘制船体图样的基本技能,和把图纸转化为模型的过程,提高学生船体结构分析能力和识图、制图能力,为学生的后续课程打下坚实的基础,同时也为今后在船舶企业从事船舶生产设计、船体检验、计划调度、编制建造工艺等岗位打下基础,使学生具备胜任船体检验员、计调员、船体工艺员等工作岗位的基本知识和能力。 (三)课程设计思路: 本课程的总体设计思路是以船舶工程技术专业(船体方向)在船体结构的认知及识图、绘图相关工作任务和职业能力分析为依据确定课程目标、设计课程内容,以工作任务为线索构建任务引领型课程。 课程结构以识读和绘制船体图样的任务为线索,以“必需、够用,兼顾发展”为原则,包括船体结构、船体图识读和绘制、船体结构节点的模型制作及型线图、分段结构图等图样的手工及计算机绘制,将船体结构的认识和船体图识读与绘制融为一体,让学生用纸板制作船体结构用型材、板材和结构节点模型,加强对对船体结构的认识,理解船体结构的视图表达,让学生通过识读、绘图等活动,增强各种图样识读和绘制的实践技能,掌握型线图、分段结构图等的手工和计算机绘制方法,形成相应的职业能力。课程内容的选取,围绕完成相应的工作任务,按照培养目标和学生的实际状况,重点突出识读、绘图能力的培养。以工作任务为中心,密切结合专业能力要求,采取课堂教学与现场教学交替的形式,实现教学做一体。积极开发学习资源,为学生提供多种学习媒体与学习机会,教学效果重点评价学生识读、绘制船体图样、船体结构节点的模型制作及型线图的绘制方面的职业能力。 本课程建议课时数为80学时。 二.课程目标 (一)课程总体目标: 通过本课程的学习,使学生在读图、绘图的训练过程中,逐步掌握船体结构的分析能力与识读
船体分段划分图设计规范
船体分段划分图设计规范 11范围 本规范规定了船体分段划分的设计依据、设计准则、设计内容和设计方法。 本规范适用于大型油轮、散货轮、FPSO等民用船舶船体分段划分图设计,其它船舶也可参照使用。 22设计依据 分段划分的基础:以船体初步设计阶段的初定船体分段的划分为基础,在详细设计以前完成和确定。 33设计准则 3.1结构特点与强度 3.1.1环形接缝应尽可能避免布置在船体总强度或局部强度的受力位置,如船舯、船梁剖面突变处,以及每一肋骨间距的中点。 3.1.2 结构应力集中的区域,如甲板大开口(货舱口)的角隅、上层建筑的末端、主机基座纵桁末端、双层底向单底结构过渡的部位(与分段接缝距离应超过一档肋距或纵桁间距)、机舱海水箱,应避免布置分段接缝(参见图 A.1)。 3.1.3对纵骨架式的船体,应尽可能减少横向分段接缝的数目;为保持一定的长度,必要时可将分段作纵向划分。对横骨架式的船体,一般尽可能减少纵向划分,以保持结构的连续性。 3.1.4 对同类型结构,如横向封闭型结构(如边水舱、双层底)、甲板或舷侧的平面板架结构等,应尽可能采用同一的划分方法(参见图B.2、图C.4)。 3.1.5 分段接缝应尽可能选择在结构原有板缝或节点零件(如肘板)的连接部位。尽量采用优化设计使分段的长度与结构强度要求的分布区域相匹配,达到减少钢板拼缝的目的。 3.1.6分段应具有足够的刚性,使不致因焊接、火工校正及翻身吊运而引起较大的变形。 3.2工艺和施工条件
3.2.1 货舱区平行舯体部分,要充分利用平直分段流水线,满足平直分段流水线的生产工艺要求,并保证平直分段的重量和尺寸在平直分段流水线的生产能力范围之内(尺寸在20米×20米以内,高度在5米以内,少量分段高度可在7米以内);上下边水舱分段主要考虑尺寸和形状,同时也要考虑加强和翻身吊运的方便性,要满足曲面生产中心的生产能力(尺寸在20米×20米以内,少量分段可超长,高度在12米以内);艏、艉分段以结构合理性划分。 3.2.2 分段应尽可能根据钢板的尺度划分(长度和宽度,但主要是长度。钢板的常用尺寸为4米×20米,单张板重量在20吨以内,最佳长度取19970毫米。但公司可流转钢板的最大规格为 4.5米×22.5米),以减少对接缝,提高钢材利用率。 3.2.3 分段的划分应考虑装配和焊接的方便性。尽量在大接缝处创造比较良好的操作空间,同时考虑舾装、涂装的方便性。分段尽量形成开敞式,以便出砂、搭脚手架,检查和涂装作业等(参见图A.2、图C.4)。 3.2.4 分段的划分应有利于最大限度地采用自动和半自动焊接。为此,船体平行舯体以及平直部分的分段尺寸,可划得大些,艏艉部位曲型较大的分段则可划得小些。同时,曲度较大不能采用自动焊的部分,应尽可能不要与平直部分划在同一分段内。 3.2.5 单一产品的分段,应尽可能利用结构上的特点,减少或简化制造分段所需的工艺装备(如胎架、加强材等)。 3.2.6 分段接缝的位置,应为船舶预舾装和涂装作业创造有利条件。如充分考虑相邻分段安装件的布置,分段内的舾装单元与结构的配合,尽量减少接缝处的管子接头,使分段具有单独进行密性试验的条件。尽量保证封闭型舱室涂装的完整性,减少焊缝对舱室涂装的破坏等。 3.2.7 分段接缝处结构的参差(即板与骨架的相对位置),应考虑船坞装配的程序及操作的方便性。目前采用的接缝处参差的形式有两种:“阶梯形”和“平断面形”(即“一刀齐”)。阶梯形结构应设在同一肋骨间距内,以利操作和控制焊接变形。 3.3生产计划和劳动量
船体分段装配
船体分段装配 船体是分段的集成体,而分段是集中材料最多,物品最齐,耗时最大,技术难度最高的“中间产品”。它是船体装配工艺程序中的重要组成部分。在船体建造中,它直接影响船舶产品的质量,建造周期、制造成本和企业的品牌和形象。 分段区域分为船尾区、机舱区、货油区、船艏区和上层建筑区。船艉区由轴架立体分段、舵臂立体分段组成。机舱区由机座底部分段,一、二、三半立体分段组成。货油舱区由底部分段、边水舱分段、舷侧分段、顶边舱甲板分段、中心甲板分段和纵横舱壁分段组成。船艏区由球鼻底部分段、压载舱立体分段、锚链舱立体分段和帆缆舱立体分段及前楼甲板分段。上层建筑区由艇甲板、多层居室甲板、驾驶甲板、罗经甲板等立体分段组成。 分段按形态可分为四大类:平直分段(包括平面分段和曲面分段)、立体分段、球型艏、艉分段和基座(主机座)联体底部分段。船体分段制造装配工艺的叙述按由船艉至船艏方向排序的有代表性的典型分段进行。 第一节船艉框架分段“AB02”分段制造装配 随着造船工业的不断发展和造船技术的不断提高,我国承建的船舶越造越大,随着航运业的发展,高附加值、高技术含量的船舶越造越多。而这些大型运输船舶的艉部多为球艉柱(见示图8—1),其型线变化特别大。正看像似一个瘦颈花瓶。它的结构不再是中小型船舶的铸钢组合段拼焊而成。而是用艉轴壳铸钢件和钢板结构的组合艉柱。艉柱框架分段“AB02”的艉柱由五部分装焊而成,型线柱包板(包括鞍型板、虾壳板和蚌壳板),艉轴壳、舵臂过渡板、水平隔板及纵桁隔板。 示图8—1 1、“AB02”分段制造要领 (1)建造方式:以艉尖舱横隔壁为基面卧造。轴壳在托架竖装全拢、艉柱小分段以左侧为基面侧造。 (2)胎架形式:轴壳总组竖造“井”字托架。艉柱侧造胎架,分段合拢平面胎架。 (3)制造顺序:横舱壁铺板→前、后轴壳总合拢→球艉柱胎架制造→艉柱小分段装焊→艉柱小分段吊装→贴装外板→吊环及加强装焊→施焊→完工测量→提交船检及船东。 (4)要领:球艉框架分段的制造是采用片段分离装焊。然后以艉尖舱水密舱壁的基面进行组合而成。 2、托架及专用胎架制造 胎架,已在胎架的章节中作过陈述,而球艉框架分段属于特殊胎架,故作专用叙述。胎架共分三种形式,即轴壳合拢托架、球艉柱特殊胎架和分段平台胎架。 (1)托架制作
船体主要构件结构图
船体结构图 船舶各部位名称如图所示。船的前端叫船首(stem);后端叫船尾(stern);船首两侧船壳板弯曲处叫首舷(bow);船尾两侧船壳板弯曲处叫尾舷(quarter);船两边叫船舷(ships side);船舷与船底交接的弯曲部叫舭部(bilge)。 连接船首和船尾的直线叫首尾线(fore and aft line center line,centre line)。首尾线把船体分为左右两半,从船尾向前看,在首尾线右边的叫右舷(starboard side);在首尾线左边的叫左舷(port side)。与首尾线中点相垂直的方向叫正横(abeam),在左舷的叫左正横;在右舷的叫右正横。 船体水平方向布置的钢板称为甲板,船体被甲板分为上下若干层。最上一层船首尾的统长甲板称上甲板(upper deck)。这层甲板如果所有开口都能封密并保证水密,则这层甲板又可称主甲板(main deck),在丈量时又称为量吨甲板。
少数远洋船舶在主甲板上还有一层贯通船首尾的上甲板,由于其开口不能保证水密,所以只能叫遮蔽甲板(shelter deck)。 主甲板把船分为上下两部分,在主甲板以上的部分统称为上层建筑;主甲板以下部分叫主船体。 在主甲板以下的各层统长甲板,从上到下依次叫二层甲板、三层甲板等等。在主甲板以上均为短段甲板,习惯上是按照该层甲板的舱室名称或用途来命名的。如驾驶台甲板(bridge deck)、救生艇甲板(life-boat deck)、等等。 在主船体内,根据需要用横向舱壁分隔成很多大小不同的舱室,这些舱室都按照各自的用途或所在部位而命名,如图1-18所示,从首到尾分别叫首尖舱、锚链舱、货舱、机舱、尾尖舱和压载舱等。在货舱中两层甲板之间所形成的舱间称甲板间舱(tween deck),也叫二层舱或二层柜。
船舶分段片体吊运结构一体化设计
船舶分段片体吊运结构一体化设计 发表时间:2018-06-19T17:17:48.537Z 来源:《基层建设》2018年第7期作者:罗碧辉[导读] 摘要:35000DWT散货船为我公司继成功建造57000DWT散货船系列船后的另一种船型,采用分段建造工艺。参考船舶制造的常规吊装工艺,优化35000DWT散货船的吊装工艺。 广东中远海运重工有限公司东莞 523146 摘要:35000DWT散货船为我公司继成功建造57000DWT散货船系列船后的另一种船型,采用分段建造工艺。参考船舶制造的常规吊装工艺,优化35000DWT散货船的吊装工艺。抓住吊装过程每个细节,节省吊环的使用量,节约吊环的制作材料,达到吊耳孔与结构一体化;并减少对船体母材及油漆的破坏,满足PSPC要求,减少过程浪费,源头上改进吊装起重技术工艺。 关键词:结构片体;吊耳;吊运;设计计算 1 概述 35000DWT散货船为我公司继成功建造57000DWT散货船系列船后的另一种船型,采用分段建造工艺。35000DWT散货船分段吊装进行设计以公司目前的建造流程装配工艺为前提,结合IMO强制性船舶涂层性能标准PSPC生效。分段吊运是船体建造中的一个重要工序,为了保证施工的安全性、制造费用经济性,对吊装工艺必须认真考虑计算,根据公司实际场地和设备,选择最优吊装工艺。 2 主要参数 本船为单机单桨柴油机驱动,无限航区,主船体结构为钢质船体,主要用于运输散装的干货,包括粮食、煤、铁矿石、钢制线材,钢管等,能运输几种指定品种的危险货物,甲板上不堆放货物;驾驶楼、生活区及机舱在艉部,机舱为24小时无人机舱;本船设计满足IACS 共同规范要求。 3 分段吊装设计主要依据 3.1分段装配制作搭载工序 小组片体 → 片体中组 → 大组 → 总组(搭载) 3.2分段吊装设计应用 分段片体吊运、翻身、定位装配 分段脱胎、移运、翻身、总组、搭载 3.3新规范要求 IMO 涂层性能标准PSPC(performance standard of protactive coting) 4 分段吊装设计介绍 吊装运用在船舶制造各道工序中,从分段装配制作到搭载合拢,对各类吊设计进行优化。公司现有的硬件设施为前提,根据新标准,采用新工艺,保证高质量的产品,选择造价经济最优的吊装施工方案。 5 35000DWT散货船分段吊装设计实例分析 吊装吊点结构强度直接决定吊装作业的安全性,认真做好吊耳设计才能避免施工事故的发生。一般情况,吊装施工吊耳的形式以及承载能力参照国家标准和企业标准,碰到特殊情况,需要自行设计吊耳,吊耳结构强度必须经过有限元分析和强度计算公式分析,确保有足够的吊耳强度和焊缝强度。有限元强度分析计算机软件建模受力分析,对硬件要求相对较高,一般采用简化的强度计算公式对吊耳进行强度评估,并按照企业施工标准取一个安全系数。 5.1本文所讨论的吊耳的结构强度按下列公式进行计算评估。 5.1.1承压验算 在载荷P的作用下,卸扣销轴与孔壁产生挤压,验算吊耳孔承压强度σa: 5.1.2剪切验算 在载荷P的作用下,平行于P方向最小受力截面受剪,即加强腹板面受剪τa:
船体主要构件结构图
船舶各部位名称如图所示。船的前端叫船首(stem);后端叫船尾(stern);船首两侧船壳板弯曲处叫首舷(bow);船尾两侧船壳板弯曲处叫尾舷(quarter);船两边叫船舷(ships side);船舷与船底交接的弯曲部叫舭部(bilge)。 连接船首和船尾的直线叫首尾线(fore and aft line center line,centre line)。首尾线把船体分为左右两半,从船尾向前看,在首尾线右边的叫右舷(starboard side);在首尾线左边的叫左舷(port side)。与首尾线中点相垂直的方向叫正横(abeam),在左舷的叫左正横;在右舷的叫右正横。
船体水平方向布置的钢板称为甲板,船体被甲板分为上下若干层。最上一层船首尾的统长甲板称上甲板(upper deck)。这层甲板如果所有开口都能封密并保证水密,则这层甲板又可称主甲板(main deck),在丈量时又称为量吨甲板。 少数远洋船舶在主甲板上还有一层贯通船首尾的上甲板,由于其开口不能保证水密,所以只能叫遮蔽甲板(shelter deck)。 主甲板把船分为上下两部分,在主甲板以上的部分统称为上层建筑;主甲板以下部分叫主船体。 在主甲板以下的各层统长甲板,从上到下依次叫二层甲板、三层甲板等等。在主甲板以上均为短段甲板,习惯上是按照该层甲板的舱室名称或用途来命名的。如驾驶台甲板(bridge deck)、救生艇甲板(life-boat deck)、等等 。 在主船体内,根据需要用横向舱壁分隔成很多大小不同的舱室,这些舱室都按照各自的用途或所在部位而命名,如图1-18所示,从首到尾分别叫首尖舱、锚链舱、货舱、机舱、尾尖舱和压载舱等。在
(完整word版)分段划分原则
分段划分原则 1.0目的 为了规范公司以后船舶类项目的分段命名,便于工人在施工的过程中能更好、更方便的识别分段。根据公司体系要求,编制此文件。 2.0适用范围 本规则适用于所有船舶类项目。 3.0命名规则 主船体分段的分段命名由五位数组成,如下所示: 分段左右舷标识 分段流水号个位 分段流水号十位 分段位置标识 分段区域标识 其它附属分段的分段命名由四位数组成,如下所示: 分段流水号 分段名缩写 4.0主船体分段的命名说明: 4.1分段区域标识: 分段区域主要指船舶主船体和上建区域按照区域划分,用字母A、E、H、F、L表示。 具体表示如下: A 表示尾部分段是AFT的缩写
E 表示机舱分段是ENGINE ROOM的缩写 H 表示中部船体分段是HULL的缩写 F 表示首部分段是FORE的缩写 L 表示上建分段是LIVING ACCOMMODATION的缩写 4.2分段位置标识: 分段位置指的是分段在区域的具体方位。具体分层位置和区域位置两类。 层位置表示方法适用于A尾部分段、E机舱分段、F首部分段、L上建分段,指的是分段所在的层,用数字1-9表示。从下向上进行排序,最下方的一个分段用‘1’表示,从下向上第二个分段用‘2’,第三个分段用‘3’表示,以此类推。 区域位置表示方法适用于H中部船体分段,分段的位置用分段所在的区域英文缩写表示,具体如下: B 双层底分段或底部分段BOTTOM的缩写 S 外板分段或舷侧分段SHELL的缩写 D 主甲板分段DECK的缩写 T 横舱壁分段TRANSVERSE BULKHEAD的缩写 L 纵舱壁分段LONGITUDINAL BUKLHEAD的缩写 P 平台分段PLATFORM 缩写 4.3分段流水号十位: 分段流水号十位的作用有两种:第一种是表示分段在所在层的具体方位;第二种是当分段流水号个位编号超过9后,用于个位向前进位。 第一种适用于A尾部分段、E机舱分段、F首部分段、L上建分段,指的是分段在所在层的横向位置,用数字0-9表示。从船中向舷侧进行排列,船中的系列分段用‘0’表示,从船中向舷侧的第一系列分段用‘1’表示,第二系列分段用‘2’表示,以此类推。 第二种适用于H中部船体分段,当分段个位编号超过9后,自动向十位进一位。例如:09分段后是10,19后面是20。同时分段流水号十位还可以用来区分该分段在所在区域的具体位置,具体如下: 在B 双层底分段、D 主甲板分段、P 平台分段三个区域,当分段横向超过三个分段时:‘0,1’表示中部第一系列分段。‘2,3’表示从船中向舷外的第二列分段;4,5表示第三列分段,以此类推。每两个数字代表一列分段,也就是说单列分段最多可划分20个分段。 在S 外板分段、L 纵舱壁分段两个区域,当分段垂向超过两个分段时:‘0,1’表示从下向上的第一列分段;‘2,3’表示第二列分段;4,5表示第三列分段,以此类推。每两个数字代表一列分段,也就是说单列分段最多可划分20个分段。 在T 横舱壁分段区域时:‘1’表示从机舱前壁开始,向船艏方向的第一道横舱壁;‘2’表示第二道横舱壁;‘3’表示第三道横舱壁;以此类推。 4.4分段流水号个位: 分段流水号个位的作用是表示分段在所在系列分段里面的具体方位;用数字1-9表示。编号原则如下: 在A 尾部分段、E 机舱分段、L 上建分段三个区域,编号原则是从船艏向船艉依次编号。
船体板材套料切割草图
板材套料数控切割草图与生产资料 1套料的条件 ⑴ 构件的建模工作全部完成,零件的形状、规格以及工艺属性正确、全齐,特别是板材坡口的类型和方向等都应符合要求。零件分离成功。外板零件展开,曲面板架也创建正确。 ⑵ 装配计划编制结束并确认,保证零件代码全名的正确性。 ⑶ 初次进入套料模块前,最好重新进行零件分离。确保扁钢零件已转换成板材零件。 ⑷ 熟悉钢板订货清单的尺度、材质和数量。 ⑸ 本船的原材料使用记录表和余料登记表的初始化。 ⑹ 如果没有材料订货清单,以套料草图作为订货资料,那么要分批汇总。 2 生产所需的套料完工文件 ⑴ 板材套料的数控切割草图。 封面选用A3横式。 FORM名: HDNEST31 切割草图用A3横式。FORM名: HDNEST32 (已设定) ⑵ 板材数控切割草图的.gen文件。 文件路径名:<工程代码>/nc/…… /<数控切割草图名>.gen ⑶ TRIBON 系统的gen文件,或者无坡口的数控切割指令。 ⑷ 板材用料统计表,列在封面中。 ⑸ 原材料使用记录表。分生产阶段发送。 表的路径名:/<工程代码>/nest/<工程代码>***板材使用统计表.xls ⑹ 余料登记和再利用记录表。分生产阶段发送。 表的路径名:/<工程代码>/nest/<工程代码>***余料登记表.xls 3 套料的批次 ⑴ 以总段为一个批次单位,根据生产部门的进度计划进行批次套料。如果缺乏具体的进度计划的资料,可参考”总段船台吊装顺序图”。 ⑵ 工厂为优化作业流程,曾推荐按制造阶段的区域以下列顺序的批次套料(适宜批量生产的后制产品) ① #2字组机舱和#1字组艉部区 ② #9字组上层建筑 ③ 主甲板以上的结构件,例如舱口围等 ④ #8字组艏部区 ⑤ #3字组货仓区(作为工程进度的调节) ⑶ 每一个批次中按工艺项目分三个类型的板材独立套料。即 ① 外板板,特别需要加工的板。 ② 要自动焊大拼板的甲板与纵横舱壁。
船体加工图设计指南
REF. NO. 船体加工图设计指南书 PLAN HISTORY NO. DATE DESCRIPTION DWN. APP. 1 渤海船舶重工有限公司 BOHAI SHIPBUILDING HEAVY INDUSTRY CO.,LTD
目录 章节项章别 PAGE 一般加工图纸1 概要 1 概念 4 2 加工图纸上须表示的事项 4 3 加工图纸的种类 5 2 加工图纸相关标准工程表 6 3 加工图检查清单7 4 图纸整理基准 1 加工图纸整理基准8 2. 切割加工图纸设绘指南1 数切(套料)加工图 1 数切加工系列9 2 数切加工图制作顺序9 3 零件配置基准10~12 4 其他事项12 5 过桥及起割点选定方法13 6 数控自动切割坡口适用范围13 2 F/P加工图 1 F/P 加工系列14 3 板材手工加工图 1 板材手工加工系列15 4 板条加工图 1 适用范围16 2 切割系列16 3 SX,SY,SZ 图纸制作顺序16 4 注意事项16 5 型材加工图 1 适用范围17 2 切割系列17 3 图纸制作基准17~19 4 注意事项19 6 甲板室加工图 1 概要20 2 波形壁套料20~21 3 一般事项21
章节项章别 PAGE 3. 曲加工图纸设绘指南1 内部构件曲加工(面 板等)加工流向 1 1000吨,600吨门式油压机22 2 制作图纸时应遵守的事项22 2 型材加工 1 肋骨冷弯机23 2 功能23 3 折角及波形壁加工 1 1000吨,600吨门式油压机、 长三辊卷(压)机 24 2 加工范围24 3 作成图纸时遵守事项24 4 波形壁绘图基准2 5 4 板材卷(压)加工 1 长三辊卷(压)板机26 2 加工范围26 3 制作图纸时应遵守的事项26~28 5 自然弯曲范围 1 定义29 2 选定平铁自然弯曲范围29 3 自然弯曲下垂计算方法29 4 自然弯曲表30 4.图样示例31~39 5.船体钢材 余料管理 规定1 适用范围40 2 目的40 3 关于用语说明40 4 责任和权限40 5 余料种类及管理基准40~41 6 余料编号构成图41~42 7 余料形象标记基准42~43 8 余料登录时注意事项43 9 设计部门对余料的登录报告书及再使用管理和记录。43~44
船舶分段设计
大连海事大学 毕业论文二○年月
船舶分段设计 学院:大连海事大学 专业:船舶海洋工程 姓名: 张学驹 指导教师:
引言 船舶工业是为水上交通、海洋开发和国防建设等行业提供技术装备的现代综合性产业,也是劳动、资金、技术密集型产业,对机电、钢铁、化工、航运、海洋资源勘采等上、下游产业发展具有较强带动作用,对促进劳动力就业、发展出口贸易和保障海防安全意义重大。我国是一个水路资源比较丰富的国家,可用来作为水路运输的江、河总长达十万公里。我国对外贸易货物的百分之九十是依靠海运来完成。船舶工程是研究、设计和制造水上交通运输工具的一项大型综合性系统工程,其主要研究对象是研究船舶的经济性、快速性、可靠性、安全性和舒适性。 我国的海洋资源比较丰富,其专属海洋经济开发区的面积接近500万平方公里,几乎是我国陆地面积的百分之五十。随着陆地石油及其它稀有资源的逐步减少直至最终枯竭,人们已经并将把未来石油及其它稀有资源的开发转向海洋。海洋工程是研究、设计和建造海洋资源开发工作平台和工具,比如离岸石油钻井平台、海上施工船舶等。 船舶工业是现代大工业的缩影,是关系到国防安全及国民经济发展的战略性产业。就现在来看,船舶工业也将要成为我国的一个支柱产业。经过改革开放后二十多年的快速发展,船舶工业已成为我国为数不多的几个具备了较强国际竞争能力的外向型产业之一,成为世界船舶工业的一支重要力量。
目录 一船舶的种类及其用途 (5) 二船体结构 (7) 三船舶分段的分类 (9) 四船模制作的必要性 (10) 五具体船模分段的设计与制作 (11) 六我国船舶工业发展现状及未来展望 (18) 七总结及参考文献 (20)
船体建造原则工艺规范汇总
船体建造原则工艺规范 前言 1 范围 本规范规定了船体建造过程中船体建造的工艺要求及过程。 本规范适用于散货船及油轮的船体建造,其他船舶也可参考执行。 2 规范性引用文件 Q/SWS42-027-2003 船舶焊接原则工艺规范 Q/SWS60-001.2-2003 船舶建造质量标准建造精度 3 基本要求 3.1要求 3.1.1船体理论线:船体构件安装基准线。 3.1.2船体检验线:以分段为基本单位设计全船统一的肋骨检验线、中心线、直剖线、水线对合线等。 3.2船体建造精度原则 3.2.1从设计、放样开始,零件加工应为无余量、少余量。 3.2.2以加放补偿量逐步取代各组立阶段零部件的余量。 3.2.3线形复杂涉及冷热加工的零件,加工时必须加放余量。加工结束后按要求进行二次划线、切割工作。 3.2.4施工单位需对精度造船中的余量、补偿量实施结果、板材收缩值等及时向精度管理小组反馈。 3.3分段作业图具备的主要资料与文件的信息:常规信息、纵、横、平、侧视图、节点详图、主要结构型值、胎架图、组立图、装焊工艺顺序、焊接工艺、吊环加强图、重心重量坐标、完工测量图表(包括补偿量、收缩原始测量记录表)、零件明细表、零件流程编码等等。 3.4分段建造实施密性舱室角焊缝气密检测试验。 3.5 船体焊接工艺按Q/SWS42-027-2003《船舶焊接原则工艺规范》,分段完工主尺度应符合Q/SWS 60-001.2-2003《船舶建造质量标准建造精度》。 3.6尾轴管等的制作需经内场加工、装焊、再机加工等多道工序,设计部对该零件单独绘制加工、装焊、机加工图。
3.7对大型铸件,设计部按计划按时出图、编制工艺文件。 3.8切割要求 3.8.1钢材材质的控制 3.8.1.1钢材进入喷丸流水线前,须按设计要求核对供货钢材所标签的材料信息表。 3.8.1.2切割中心将有关钢材信息:材质、规格、船级社钢级、数量、以及检验合格编号、生产炉批号等输入计算机系统以备跟踪、抽查。 3.8.1.3钢材的质量标准按Q/SWS60-001.2-2003《船舶建造质量标准建造精度》,生产中发现不符合质量标准的钢材不得流入下道工序。 3.8.1.4预处理喷丸质量、涂膜厚度必须符合质量标准和有关技术要求,未经预处理的材料不得流入工位。 3.8.2 材质的跟踪与传递以分段为单元(具体情况参见全船结构验收项目表)。 3.8.2.1 切割中心负责炉批号汇总(品质保证部负责炉批号传递和提交)。 3.8.2.2 切割中心须将有关材质、规格移植到钢板余料上。 3.8.3零件切割下料 3.8.3.1零件流程编码必须齐全,对合线、矫正线、构架线数控划线必须清晰,零件的坡口形式、企口上下、首尾、正反、左右等零件加工符号、尺寸、标注必须正确无误。 3.8.3.2下料后零件的减轻孔、人孔、透气孔、漏水孔、切口、面板的自由边都必须打磨。 3.8.3.3切割下料零件,严格按分段小组立、中组立、大组立、散装件、标准件等,分阶段配套、堆放,确保分段零件配套完整及零件分流正确。 3.8.3.4切割材料严格按下料工艺单要求,材料规格材质不准擅自替代。 3.8.4型材加工必须控制其直线度、水平度、角尺度及焊接质量。 3.8.5拼板切割零件其直线度精度、对角线精度达到质量标准。 3.8.6数控切割、门式切割、光电跟踪切割等设备的操作人员须每天上下班做好起始点检测保养,从而确保零件切割精度。 3.8.7板材的吊装严禁直接用钢丝绳捆扎。 3.8.8操作人员应根据设计要求做好切割下料实动工时的原始记录。
船体分段制作工艺规范
方圆船舶 船体分段制作工艺规范 编制:张松华 方圆造船有限公司 2011年9月28日
船体分段制造工艺规范 1.目的: 为缩短造船周期,提高生产效率,加强产品施工制作过程中的质量自主控制和管理,上道工序为下道工序提供合格、优良的零部件和产品,确保船体分段施工准确无误和管、电、铁舾件在分段制作期间一次完成。特制订本工艺规范。2.适用范围: 适用于产品的设计、下料、加工及分段制造,总组全过程的质量、精度控制。3.部门职能: 3.1、设计部从设计的角度研究如何缩短分段建造周期及船台合拢周期,为提高分段的建造精度而优化设计图纸。 3.2、项目部船体科负责工艺文件的消化及技术指导,实施过程中的监控和检查,同时对外包施工队、施工小组工艺文件执行,进行教育及监控。 3.3、质检科负责精度控制自零部件加工至分段制造、中组合拢的约束过程的精度检查,记录考核信息反馈,对各重要环节实施现场测控和数据确认,并建立各产品数据库,同时还要对现场制造进行过程跟踪监控。 3.4、建立船体建造精度质量管理与控制组织机构(设立二名专职精度管理员),各部门科长、主管负责对精度、质量管理与精度控制组织机构的领导,并对其工作组织检查。 3.5、各科主管、外包队队长负责按图纸和工艺要求,工艺纪律进行施工对建造精度质量进行自主控制为主原则,同时配合质检科、精控人员进行检测和控制。4.实施: 4.1、精度管理员工作要求 4.1.1、根据项目部下发生产任务分布情况,将工作范围从准备下料开始到船舶合拢结束,覆盖于整个施工全过程。在零部件控制工序,分段建造控制工序,分段
总组工序过程。要在主管支持、领导下,精控人员进行认真制作过程监控工作,要多到现场进行指导。发现不符合工艺规范、工艺纪律施工情况,要立即进行指正,并且指导他们用什么方法整改为最佳,必要时发出整改意见书。同时也要求相关施工队中的人员积极配合,及时整改,确保把质量事故隐患消灭在萌芽状态。使制造的分段成为合格产品后才能流到下道工序。同时复测数据由施工者、精控员、检验员按规定表格的要求测量,三者都要进行认真记录,做到实事求是和准确无误,严禁弄虚作假记录发生。 4.2精度控制要点: 4.2.1、精度管理人员要严格验收基准肋骨检验线、余量线和对合基准水线、纵剖线,做到万无一失,基准肋骨检验线驳移后须有三组以上洋冲眼标志。 4.2.2、精度管理人员认真对待完工测量,尤其对无余量加工的分段要加强测量和检验,确保分段在允许的误差范围内,对超出公差范围应及时反馈,进行整改。 4.2.3、施焊人员应对称均匀分布,严格按照焊接程序施焊。 4.2.4 本部门要加强精度、质量自主控制领导机构,并且有机构网络图。组长由主管担任,各劳务队长任副组长;做到每一周召开一次分析会,以便于沟通和管理,确保产品质量的提高。 4.3内业号料加工施工工艺要点及规定: 4.3.1钢材及型材号料时,领用记号笔或色漆清楚地写明工程编号、分段号、材料规格加工码和加工符号,号料时零件刨边余量留放,零件号料精度控制要求,都要按工艺要求、精度标准来执行。 4.3.2数控切割机操作工每天开机后的第一件事是检测数控切割机对角线的方整度,在调整到5米为对角线≤2mm的规定范围内后才能进行正式切割。切割前还需检查割边“留余”不小于规定数,“留余”规定如下:6~25mm板留余量10mm,26~40mm 留余量15mm,41mm以上留余15~20mm。数控切割矩形板改为半自动手工切割时,