铣削加工中工件变形仿真预测方法研究
基于ABAQUS的典型薄壁件加工变形仿真与试验研究
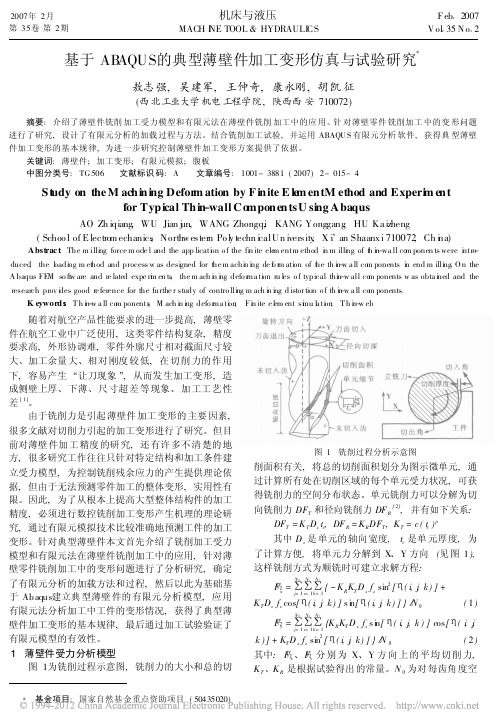
S tudy on the M ach in ing D eform ation by F in ite E lem en tM ethod and Experim en t
由于铣削力是引起 薄壁件 加工 变形的 主要 因素, 很多文献对切削力引起的加工变形进行了研究。但目 前对薄壁 件加 工 精度 的研 究, 还 有许 多不 清 楚的 地 方, 很多研究工作往往只针对特定结构和加工条件建 立受力模型, 为控制铣削残余应力的产生提供理论依 据, 但由于无法预测零件加工的整体变形, 实用性有 限。因此, 为了从根本上提高大型整体结构件的加工 精度, 必须进行数控铣削加工变形产生机理的理论研 究, 通过有限元模拟技术比较准确地预测工件的加工 变形。针对典型薄壁件本文首先介绍了铣削加工受力 模型和有限元法在薄壁件铣削加工中的应用, 针对薄 壁零件铣削加工中的变形问题进行了分析研究, 确定 了有限元分析的加载方法和过程, 然后以此为基础基 于 Ab aqu s建立典 型薄壁 件的 有限元 分析 模型, 应 用 有限元法分析加工中工件的变形情况, 获得了典型薄 壁件加工变形的基本规律, 最后通过加工试验验证了 有限元模型的有效性。
为了计算 Z 向 力, 首 先引 入轴 向 单元 力 计算 表
达式:
DFA = KA DF t tanAhx
其中: DFA 表 示 单元 的轴 向切 削 力, Ahx 为刀 具螺 旋 角, KA 为轴向常量, 这样得到 Z向平均力表达式:
NH Nz Nf
F½z
=
E
j= 1
基于stl模型的铣削加工仿真算法

基于stl模型的铣削加工仿真算法
### 采用的基本思路
1. 对于每一个铣削器,使用逆求解原理计算出新的切入点点位。
2. 将新的切入点点位用射线将STL模型分割成一块一块的,前一次切入点和后一次切入点之间的射线,有若干个在射线上的点,可以将这样的射线对应切削深度采用梯度下降方法计算射线切削深度。
3. 铣削处理时,使用O((N)^2)算法迭代射线技术,并采用平移式分割,根据铣削器的特点将STL模型分割成若干区域。
4. 对每一个新的铣削层,增加一层新的射线,将新的铣削层加入到计算结果中。
5. 用一种改进的分簇算法实现高效的射线技术,将最优的解决方案与射线分簇算法相结合,实现高效的射线技术。
6. 针对铣削器每一次切入层,计算并依据原本不处理的部分由上放模式来进行扩充,生成新的体素,以此达到减少算力的目的。
7. 最后,将计算结果导出用于机器加工的信息,通过存储的机器加工数据完成切削加工的信息转化。
### 主要优势
1. 采用了射线实现高效的分割,大大减少了计算复杂度;
2. 采用了改进分簇算法实现了高效的射线,减少了计算空间;
3. 通过应用逆求解原理计算出新的切入点点位,并使用平移式分割把STL模型分割成若干区域,大大提高了计算效率;
4. 用一种改进的分簇算法实现高效的射线技术,将最优解决方案与射线分簇算法相结合,提高了技术的效率;
5. 将最终计算结果转换成机器加工数据,简化了数据的转换过程,提高了切削加工的效率。
薄壁件铣削加工变形有限元仿真分析

经 验 交 流
T c i a m mUn c t s e hn c ICo iai on
Ⅸ 动 化 技 术 与 应 用 》2 0 自 0 7年 第 2 6卷 第 1 2期
薄 壁 件 铣 削 加 工 变 形 有 限 元 仿 真 分 析
苑 辉 . 隋秀 凛 . 亚 萍 . 文 强 郑 军 强 王 陈
数学公式的基础上 , 利用矩阵简化法 , 建立了基于材料 77 一, 05 I ' 6
的数控铣削力经验模型【。 中 为切 向铣削力 ; 为径 向铣削 其 力; F 为轴向力。
{ . 07 :8d. ・1 、 2・ k F =3 9・w8・ ・15 0 , 0 Z・ 8 9 0 0 6
{ v 7 1 8 ・: .08 枷 ・ 2・ ・ F = . ・ o 兜 d. . , 0 Z k 1 6 9 9 5 z 2 4 0 ・p d. ・ 0 ・10・ lF = . ・w2 0 ・08 15,03z 5 . 8 3 8 9 4 5 o
收 稿 日期 : 0 —0 — 2 0 07 8 3
强大 的 ME ( S 机械事件仿真 )可以动态的模拟薄壁在不 同时刻 受到铣削力作用下的变 形情 况和应力分布 。所以本文基于 AL — GR 0 软件进行分析 , 根据要仿真的条件 , 建立了铣削加工变形有 限 元分析流程 , 图 l 如 所示 :
Ab t a t Th n t lm e t s r c : e f ie ee n d l fmi i g ma h n n r o so h n wa l a t se t b ih d b h a g n t lm e t n l ss i mo e l n c i i g e r r fat i — l p r sa ls e y t el r e f iee e n a y i o l i i a s f r o t e ALGOR 0 An e ma h n n ro sc u e y t e c t n o c r r dit d v a t e d n mi a i u a i n wa V2 . d t c i i g e r a s d b h u t g f r ea ep e c e i y a cl d sm l t . h i h o o Ke o ds t i — l p r; n t l me t m a h n n r o s d n m i i l t n y W r : h n wa l a f i e e n ; c i i g e r ; y a c s mu ai t i e o
铣削加工过程动力学建模仿真技术研究进展

起刀具 、零件显著的加工变形 ,导致 了加工表面与期 望值之 间存在较 大偏差 。对 于弱 刚性工 艺系统 来讲 ,
颤振时有发生 ,因此在实际加工时往往采用试切后 的
日益激烈 ,怎样充分发挥铣削加工机床 、刀具 的最大 利用 率 ,满足在提高零件加工质量 的同时尽可能地缩 短加工时间和降低生 产成本 一直是 值得 深究 的课题 。 传统 的 C D C M 软件均是基于零件 的理想几 何形状 A/A 来确 定切削策略和规划刀轨 ,然而它们对影 响加工质 量 的显著 因素 ( 铣削 力和 颤振 ) 却无 能 为力 。铣 削 力仿 真在物理仿真 中占有非常重要 的地位 ,它不仅是 物理仿 真的主要 内容 ,又是颤振预报 、加工表面形貌
铣 削加 工 过程 动 力学 建模 仿真 技 术研 究 进 展
吴春桥 ,张胜 文 ,仝永海 ,方喜峰
( 江苏科技 大学现 代制 造技 术研 究所 ,江 苏镇 江 2 20 ) 103
摘要 :从数控 铣削加工过程铣削力建模仿 真、颤振 离线预测 出发 ,分 析 了铣 削力 建模方法 、颤振产 生的机理 。论述 了 铣削力仿真 、预测 Байду номын сангаас制颤振 的重要性和必要性 以及 国内外的研究现状 ,并指 出了该领域今后 主要的研究方 向。 关键 词 :铣 削加工 ;动力学建模 ;铣削力 ;颤振 中图分 类号 :T S 11 G 0 . 文献标识码 :A 文章编 号 :10 — 8 1 (0 1 9—1 1 5 0 1 3 8 2 1 )1 2 —
铣 削加工是一种重要 的机械加工工艺 ,在整个机
就必须对切削加工 中发生 的振动特别是颤振 的原 因及
其 防治方法进行深入研究 。铣削过程 中的铣削力会引
加工变形行为的数值模拟与应用

加工变形行为的数值模拟与应用一、引言加工变形是指在零件制造过程中,由于外力作用和加工参数不断调整,使工件不断发生变形。
改善加工变形问题,提高零件精度和加工效率是制造业发展中的一项重要课题。
基于数值模拟技术进行加工变形分析,已成为解决该问题的一种重要方法。
本文将从数值模拟技术的基础、加工变形分析原理和方法、数值模拟在机械零件加工中的应用等方面进行介绍。
二、数值模拟技术的基础数值模拟技术是指基于数值计算的建模模拟方法。
它将实际问题抽象成数学问题,通过计算机数值计算的方法,对实际问题进行仿真模拟,分析问题的本质和规律。
数值模拟技术应用广泛,不仅包括加工变形分析,还包括流体力学、电磁场、结构力学和热传导等领域。
数值模拟技术的基本流程如下:1.建立数学模型建立数学模型是数值模拟的第一步。
通过数学公式和表述,将实际问题建模成数学模型,将实际问题的复杂性简化为数学问题的简单性。
2.数值离散数值离散是将实际问题的连续性离散化,将求解区域划分成若干个区域,将区域内的数值用静态的数值代替,将求解问题转化为计算机可以处理的数值问题。
3.数值计算数值计算是将离散化的数值通过数值计算求解,得到问题的解答。
数值计算包括数值差分、数值积分和求解方程组等方法,通过计算机实现。
4.结果分析结果分析是数值模拟的最后一步,对模拟结果进行分析和验证,通过分析结果,可以帮助我们更好地理解实际问题的本质和规律。
三、加工变形分析原理和方法加工变形是指在机械加工过程中,由于加工力、切削热等因素的作用,使得工件产生形变的现象。
加工变形问题对零件加工精度和加工效率都有很大的影响。
因此,加工变形的分析和模拟是非常必要的。
加工变形分析的原理和方法是在模型基础上,采用有限元方法,模拟加工过程中的应力和变形过程,通过求解有限元方程,计算出零件加工过程中的应力分布和变形情况。
具体分为以下几个步骤:1.建立有限元模型建立有限元模型是分析加工变形的第一步。
根据零件的结构和加工工艺,建立零件的三维模型,并对其进行离散化处理,得到零件的有限元模型。
基于人工神经网络的铣削加工变形预测模型

中 图 分 类 号 : P 8 ;T 1 1 T 13 H 6 文献标 志码 : A 文 章 编 号 : 0 01 9 ( 0 0 0 .1 00 1 0 — 3 2 1 ) 81 3 - 0 4
第3 1卷 第 8期
20 10年 8月
兵
工
学
报
V0 . No 8 1 3l .
Aug . 20Βιβλιοθήκη 0ACTA ARMAM ENTARI I
基 于 人 工 神 经 网络 的 铣 削加工 变 形预 测模 型
辛 民 ,解 丽静 王 西彬 一 , ,石 文 天 ,杨 洪建
( . c olo c a ia n hc lrE gn eig ejn n tueo e h ooy,B in 0 0 ,C ia 1Sh o f Me h nc l dVe iua n ie r ,B i gIsi t fT c n lg a n i t ej g1 0 8 i 1 hn ;
td b sn c — o a a in n u a ewo k a d t k n h x e i e td t s i ri i g e a l s e y u ig a Ba k Pr p g t e r ln t r n a i g t e e p rm n aa a t tan n x mp e . o s
线预 测方 法 , 过正 交试 验方 法设计 试验 方案 , 行 了不 同铣 肖 参 数 条件 下 的铣 削试 验 , 通 进 0 以试 验 数 据为 训练样 本建 立 了基 于 B P神经 网络 的铣 削加工 变形 与铣 削参 数关 系 的预 测模 型 。通 过 生产试
金属切削变形过程的有限元仿真初探
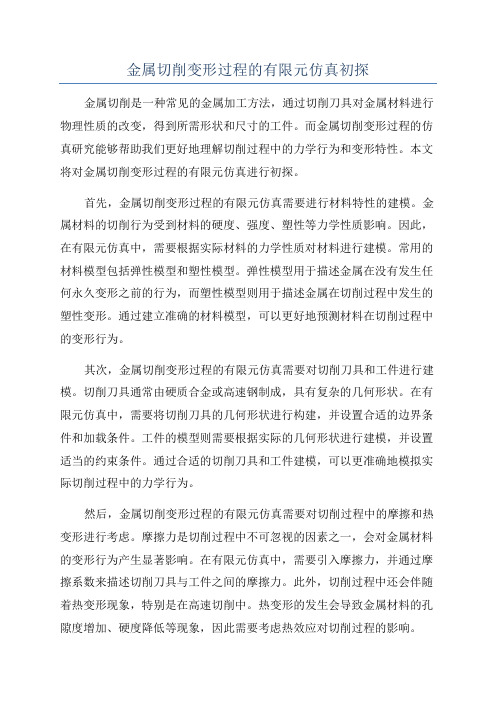
金属切削变形过程的有限元仿真初探金属切削是一种常见的金属加工方法,通过切削刀具对金属材料进行物理性质的改变,得到所需形状和尺寸的工件。
而金属切削变形过程的仿真研究能够帮助我们更好地理解切削过程中的力学行为和变形特性。
本文将对金属切削变形过程的有限元仿真进行初探。
首先,金属切削变形过程的有限元仿真需要进行材料特性的建模。
金属材料的切削行为受到材料的硬度、强度、塑性等力学性质影响。
因此,在有限元仿真中,需要根据实际材料的力学性质对材料进行建模。
常用的材料模型包括弹性模型和塑性模型。
弹性模型用于描述金属在没有发生任何永久变形之前的行为,而塑性模型则用于描述金属在切削过程中发生的塑性变形。
通过建立准确的材料模型,可以更好地预测材料在切削过程中的变形行为。
其次,金属切削变形过程的有限元仿真需要对切削刀具和工件进行建模。
切削刀具通常由硬质合金或高速钢制成,具有复杂的几何形状。
在有限元仿真中,需要将切削刀具的几何形状进行构建,并设置合适的边界条件和加载条件。
工件的模型则需要根据实际的几何形状进行建模,并设置适当的约束条件。
通过合适的切削刀具和工件建模,可以更准确地模拟实际切削过程中的力学行为。
然后,金属切削变形过程的有限元仿真需要对切削过程中的摩擦和热变形进行考虑。
摩擦力是切削过程中不可忽视的因素之一,会对金属材料的变形行为产生显著影响。
在有限元仿真中,需要引入摩擦力,并通过摩擦系数来描述切削刀具与工件之间的摩擦力。
此外,切削过程中还会伴随着热变形现象,特别是在高速切削中。
热变形的发生会导致金属材料的孔隙度增加、硬度降低等现象,因此需要考虑热效应对切削过程的影响。
最后,金属切削变形过程的有限元仿真需要进行切削参数的优化。
切削参数包括切削速度、进给量和切削深度等,它们会直接影响到金属切削过程中的力学行为和变形特性。
通过对切削参数进行优化,可以获得更理想的切削效果和更大的加工效率。
在有限元仿真中,可以通过改变切削参数的数值来模拟不同的切削条件,并通过参数优化来确定最佳的切削参数组合。
基于神经网络的薄壁件加工变形预测方法_秦国华

收稿日期: 2012 - 03 - 26 基金项目: 国家自然科学基金项目( 51165039 ) ; 航空科学基金项目( 2010ZE56014 ) ; 江西省自然科学基金项目( 2009GZC0104 ) ; 江西省科 技支撑计划重点项目( 2010BGB00300 ) ; 江西省省教育厅科学技术研究基金项目( GJJ10521 ) ; 无损检测技术教育部重点实验室 开放基金项目( ZD201029004 ) mail: qghwzx@ 126. com 作者简介: 秦国华( 1970 —) , 男, 教授, 博士后。E-
网络输入特征预测工件加工变形。 而刘新玲等
[5 ]
根据切削刃对工件作用时间的先后对已加工表面上 卸载, 利用载荷步方法对动态切 相应节点进行加载、 削力引起的工件变形进行有限元分析, 通过 BP 神 经网络算法建立了摆线轮铣削力与加工变形的预测 模型。上述工件变形的预测方法仅考虑了铣削工艺 参数的影响, 而忽略了刀具的几何参数。 薄壁件切削加工过程中引起加工变形的影响因 素多种多样, 多个影响因素的组合则更是成千上万 。 显然, 仅仅根据加工变形的影响因素利用有限元方 法分析计算工件的加工变形, 是不切实际的。为此, 本文针对薄壁件铣削过程建立了加工变形的有限元 仿真模型, 分析了刀具几何参数对加工变形的影响 1. 2 1. 2. 1
C 0. 005 m 1. 80 θm / ħ 600 θ0 / ħ 20 ε0 0. 001
D 达到 1. 0 时, 材料失效, 实现被切单元与工件脱 离。其失效准则是把每个工件单元定义为等效塑性 应变, 即 D=
p f
Constants of the JohnsonCook constitutive model
∑
- 1、下载文档前请自行甄别文档内容的完整性,平台不提供额外的编辑、内容补充、找答案等附加服务。
- 2、"仅部分预览"的文档,不可在线预览部分如存在完整性等问题,可反馈申请退款(可完整预览的文档不适用该条件!)。
- 3、如文档侵犯您的权益,请联系客服反馈,我们会尽快为您处理(人工客服工作时间:9:00-18:30)。
进 给 量 的 减 小 而 增 大 。 当 进 给 量 减 小 到 一 定 值 时 但
( . 0 3mm/r , 劳 强 度 几 乎 保 持 不 变 。 给 量 太 大 , )疲 进 滚
压不 充分 ; 给量 太小 , 于重 复滚 压 , 果 适得 其反 。 进 等 效
实 际 生 产 中 一 般 为 0 1~0 3mm/ . . r。
7 结 论
复 合 镗 滚 油 缸 内孔 为 一 种 先 进 制 造 工 艺 , 工 质 量 加
及 生 产 效 率 较 传 统 滚 压 3 艺 大 幅度 提 高 , 量 生 产 质 量 2 批
稳 定 。 公 司 采 用 该 新 型 工 艺 加 工 HS 型 3 程 油 缸 , 某 G 2 材
铣 削 加 工 中 工 件 变 形 仿 真 预 测 方 法 研 究
口 李 目 口 陈蔚芳
1 南 京 航 空航 天 大 学 机 电 学 院 南 京 2 0 1 . 10 6
2 北京航空精密机械研 究所 北京 10 7 . 006
摘 要 : 准 确 地 数 值 模 拟铣 削加 工过 程 , 控 制 工 件 加 工 变 形 、 高 加 工 精 度 有 实 际的 意 义 。 于 热 一 耦 合 弹 塑 对 提 基 机
的 热 传 导 , 现 了更 为 准 确 的 工 件 铣 削 变 形 的 预 测 。 实
能影 响很 大 , 滚 压深度 一 定 的条件 下 , 劳 强度 随着 在 疲
② 滚 压 前 精 镗 孔 粗 糙 度 一 般 为 R 3 2~ R 5, J . 预 J n 3 表 面粗糙 度 低 , 压 后粗糙 度 -低 。 2 滚 t g ③滚 压 只能 提高 加工 表 面物 理机 械性 能 和表 面粗
性有 限元 方 法 , 用 A A U 采 B Q S有 限 元 仿 真 软 件 , 建 了铣 削加 工过 程 的 三 维有 限元 模 型 , 测 了工 件 在 铣 削力 和 铣 削热 耦 创 预
合作用下的变形情 况。 研究结果表明 , 数值模拟计算与实验结果比较吻合 , 从而证 明了该仿真预测方法的可行性与有效性。
件 转 动 惯 性 大 , 起 振 动 , 工 质 量 也 不 高 。 压 速 度 引 加 滚
一
般 控制 在3 5~4 0m/mi 。 n
5 切 削 Байду номын сангаас
复 合 镗 滚 产 生 的 切 屑 必 须 从 镗 头 前 面 流 出 , 屑 切 的清 除 主 要 靠 低 压 、 流 量 的切 削 液 冲 洗 , 时 滚 压 时 大 同
关键词 : 削 铣 切削力 切削热 变 形 预 测
中 图分 类 号 :C 4 T 5
文献标识码 : A
文 章 编 号 :0 0—4 9 (0 0 0 —05 — 4 10 9 82 1 ) 1 0 1 0
金 属 切 削 加 3 变 形 是 机 械 制 造 业 普 遍 存 在 的 问 2 题 , 重 影 响 着 产 品 的 质 量 和 加 3 效 率 , 直 受 到 业 严 2 一 内人 士 的 广 泛 关 注 I 。 理 有 效 地 运 用 有 限 元 软 件 对 1 合 1 铣 削 加 工 过 程 进 行 仿 真 , 预 测 出 加 工 变 形 , 仅 为 并 不
仿 真 都 是 先 通 过 实 验 等 手 段 得 到 铣 削 力 模 型 和 铣 削 温 度 模 型 , 后 将 力 载 荷 和 温 度 载 荷 加 到 离 散 单 元 然
的 相 应 节 点 上 , 疑 使 得 仿 真 结 果 与 实 际 加 工 结 果 无
相差较大 。
实 际 加 工 的 智 能 化 提 供 了 有 利 条 件 , 时 也 为 切 削 同
个 较 复 杂 的过 程 , 时伴 有 进 给运 动 和 旋 转 运 动 , 同
收稿 日期 :0 9 9 2 0 年 月
载 荷 周 期 性 地 加 载 在 工 件 上 进 行 切 削 。 往 的 铣 削 以
机 耦 合 分 析 场 , 虑 了 摩 擦 生 热 以及 刀 具 与 工 件 之 间 考
一
产 生 的 大 量 热 量 也 要 靠 切 削 液 带 走 。 般 采 用 机 械 油 一
或5 %硫 化油 加5 %柴 油作 为切 削 液 。 O 0
参 数 优 化 和 路 径 补 偿 提 供 了 有 效 数 据 。 削 加 2 是 铣 ] 2
一
在通 常 的铣 削加 工过 程 中, 其对 弱 刚度 工件 , 尤 切 削 力 和 切 削 热 对 加 2 精 度 的 影 响 最 大 。 者 利 用 1 2 笔 ABAQU 软 件 建 立 铣 削 过 程 的 有 限 元 模 型 , 用 热 ~ S 采
质 为 4 钢 热 轧 无 缝 管 料 , 缸 内 孔 西l O 5 油 O H8, 13 5 长 6 mm , 批 量 生 产 验 证 , 件 表 面 粗 糙 度 可 达 R 0 2 圆 经 零 . ,
度 为0 0 . 4 mm,批 量 生 产 滚 压 质 量 稳 定 , 率 高 , 寸 效 尺
4. 4 滚 压速度
糙 度 , 不能 提高 工件 的几何形 状 精度 , 件 的几何形 而 工 状 精 度 只能依 靠滚 压前 的 预加工 来 保证 。 ④ 滚 柱 转 动 必 须 灵 活 , 排 滚 柱 直 径 方 向 上 差 值 每 不 得 大 于 0 0 5 mm, 则 会 挤 伤 工 件 或 引 起 振 动 甚 至 .0 否
损 坏 滚压 头 。
滚 压 速 度 是 指 滚 压 工 件 旋 转 的 线 速 度 , 压 速 度 滚 的 高 低 , 仅 影 响 生 产 率 , 且 关 系 到 滚 压 质 量 的 好 不 而 坏 。 度 太 低 , 柱 的 滚 动 不 灵 活 而 成 为 滑 动 , 于 是 速 滚 等 挤 压 ; 度 太 高 , 工 表 面 塑 性 变 形 不 充 分 , 时 , 工 速 加 同 因