【推荐下载】技术-利用钢厂停产小高炉改建熔融钢渣协同处理尘泥、冶炼渣等固废危废新思路
冶金废渣的处理方法
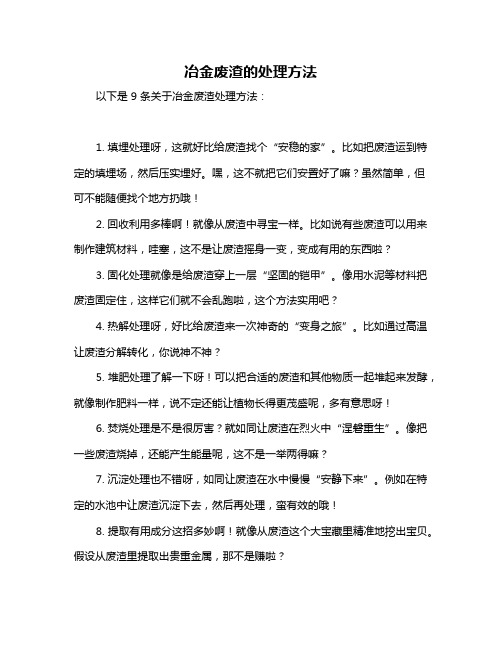
冶金废渣的处理方法
以下是 9 条关于冶金废渣处理方法:
1. 填埋处理呀,这就好比给废渣找个“安稳的家”。
比如把废渣运到特定的填埋场,然后压实埋好。
嘿,这不就把它们安置好了嘛?虽然简单,但可不能随便找个地方扔哦!
2. 回收利用多棒啊!就像从废渣中寻宝一样。
比如说有些废渣可以用来制作建筑材料,哇塞,这不是让废渣摇身一变,变成有用的东西啦?
3. 固化处理就像是给废渣穿上一层“坚固的铠甲”。
像用水泥等材料把废渣固定住,这样它们就不会乱跑啦,这个方法实用吧?
4. 热解处理呀,好比给废渣来一次神奇的“变身之旅”。
比如通过高温让废渣分解转化,你说神不神?
5. 堆肥处理了解一下呀!可以把合适的废渣和其他物质一起堆起来发酵,就像制作肥料一样,说不定还能让植物长得更茂盛呢,多有意思呀!
6. 焚烧处理是不是很厉害?就如同让废渣在烈火中“涅磐重生”。
像把一些废渣烧掉,还能产生能量呢,这不是一举两得嘛?
7. 沉淀处理也不错呀,如同让废渣在水中慢慢“安静下来”。
例如在特定的水池中让废渣沉淀下去,然后再处理,蛮有效的哦!
8. 提取有用成分这招多妙啊!就像从废渣这个大宝藏里精准地挖出宝贝。
假设从废渣里提取出贵重金属,那不是赚啦?
9. 微生物处理很新奇吧!就像是让小微生物们来当“清洁工”。
比如利用一些微生物分解废渣,哇,大自然的力量真神奇呀!
我觉得呀,这些方法各有各的好,都值得我们去好好研究和利用,把冶金废渣处理好,既保护环境又能创造价值,何乐而不为呢!。
钢铁行业含锌冶金尘泥资源化利用现状与研究进展究
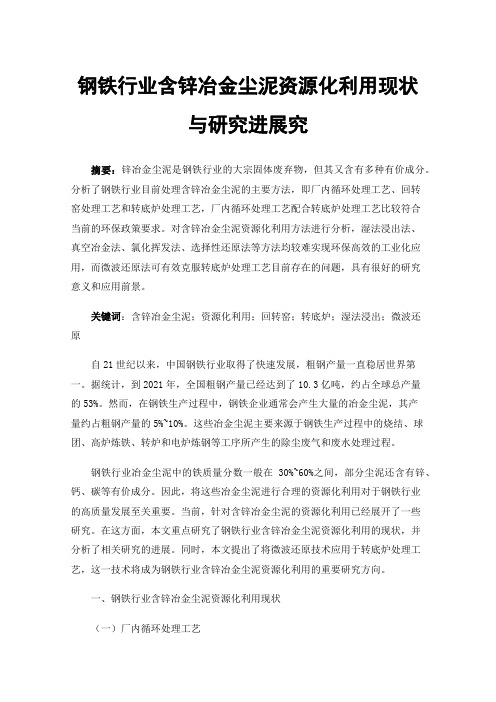
钢铁行业含锌冶金尘泥资源化利用现状与研究进展究摘要:锌冶金尘泥是钢铁行业的大宗固体废弃物,但其又含有多种有价成分。
分析了钢铁行业目前处理含锌冶金尘泥的主要方法,即厂内循环处理工艺、回转窑处理工艺和转底炉处理工艺,厂内循环处理工艺配合转底炉处理工艺比较符合当前的环保政策要求。
对含锌冶金尘泥资源化利用方法进行分析,湿法浸出法、真空冶金法、氯化挥发法、选择性还原法等方法均较难实现环保高效的工业化应用,而微波还原法可有效克服转底炉处理工艺目前存在的问题,具有很好的研究意义和应用前景。
关键词:含锌冶金尘泥;资源化利用;回转窑;转底炉;湿法浸出;微波还原自21世纪以来,中国钢铁行业取得了快速发展,粗钢产量一直稳居世界第一。
据统计,到2021年,全国粗钢产量已经达到了10.3亿吨,约占全球总产量的53%。
然而,在钢铁生产过程中,钢铁企业通常会产生大量的冶金尘泥,其产量约占粗钢产量的5%~10%。
这些冶金尘泥主要来源于钢铁生产过程中的烧结、球团、高炉炼铁、转炉和电炉炼钢等工序所产生的除尘废气和废水处理过程。
钢铁行业冶金尘泥中的铁质量分数一般在30%~60%之间,部分尘泥还含有锌、钙、碳等有价成分。
因此,将这些冶金尘泥进行合理的资源化利用对于钢铁行业的高质量发展至关重要。
当前,针对含锌冶金尘泥的资源化利用已经展开了一些研究。
在这方面,本文重点研究了钢铁行业含锌冶金尘泥资源化利用的现状,并分析了相关研究的进展。
同时,本文提出了将微波还原技术应用于转底炉处理工艺,这一技术将成为钢铁行业含锌冶金尘泥资源化利用的重要研究方向。
一、钢铁行业含锌冶金尘泥资源化利用现状(一)厂内循环处理工艺1.厂内循环处理工艺是目前钢铁企业处理低锌冶金尘泥(锌质量分数小于1%)广泛采用的方法之一。
该工艺的主要原理是将低锌含铁尘泥作为原料返回钢铁厂内的烧结或球团工序进行配料使用。
由于冶金尘泥在烧结或球团配料中的比例通常在5%以下,并且低锌冶金尘泥中锌含量极少,因此对高炉生产和冶炼设备的影响很小。
回转窑法处理含锌冶金尘泥洁净生产工艺研究

M etallurgical smelting冶金冶炼回转窑法处理含锌冶金尘泥洁净生产工艺研究王志红摘要:鉴于钢铁企业规模的不断扩大,致使钢铁废弃物的排放量也在逐年增多,对企业周边的生产与生活环境造成严重的影响。
为了使钢铁企业绿色可持续发展,需要对钢铁废弃物进行有效地处理,使其能够被合理的回收与利用。
在钢铁冶炼中产出了一种含铁、碳、锌较高的固体物质—尘泥,这种物质在很多钢铁厂得到回收与利用,使经济效益和社会效益都显著提高。
但含锌尘泥中的锌元素大量聚集在高炉中,使高炉一直在高锌负荷的状态下运行,对高炉的生产造成了影响。
基于此,本篇文章对回转窑法处理含锌冶金尘泥洁净生产工艺进行研究,以供参考。
关键词:回转窑法;含锌冶金尘泥;洁净生产工艺钢铁行业密集着大量的资源和能源,它在生产过程中不仅会消耗大量的能源,而且也会排出大量的废弃物,通过相关数据可以得出,钢铁行业的固体废弃物产量在整个工业中固废产量是最高的,而整体的利用率却保持在70%左右,虽然大部分的固体废弃物实现了循环再利用,但是,仍有一些问题困扰着钢铁企业的发展,比如钢渣和含锌尘泥的处理问题。
因此,就要把研究方向放到尘泥脱锌的内容上,对含锌尘泥做好处理工作,使其能够被充分的循环再利用。
含锌含铁尘泥利用的关键是先行脱除锌元素,脱锌的工艺较多,主要分为火法和湿法脱锌工艺两类,湿法脱锌多存在成本高、二次污染等问题,火法工艺处理效率较高,是目前含锌尘泥资源化利用的主要途径。
1 概述1.1 钢铁冶金尘泥特性在钢铁冶金尘泥中,最常见的尘泥有五种,分别是烧结灰、高炉尘泥、转炉尘泥、轧钢粉尘以及电炉粉尘,这些尘泥会在不同的工序生成不同的化学成分。
为了能够把这些冶金尘泥循环再利用,就先要对尘泥的物理性质和化学反应做一些相应的了解。
可以根据尘泥化学成分表展开分析:一是含铁粉尘中存在着大量的铁元素,其中有效含量高达46.79%,有非常可观的利用价值,因此,对于这类粉尘的回收要把主要目标放在铁回收上,对其存在的元素也要进行有效的回收。
钢渣的处理方式
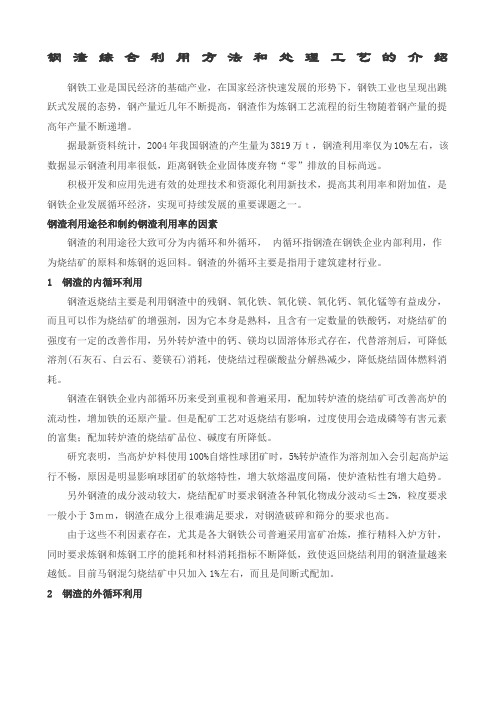
钢渣综合利用方法和处理工艺的介绍钢铁工业是国民经济的基础产业,在国家经济快速发展的形势下,钢铁工业也呈现出跳跃式发展的态势,钢产量近几年不断提高,钢渣作为炼钢工艺流程的衍生物随着钢产量的提高年产量不断递增。
据最新资料统计,2004年我国钢渣的产生量为3819万t,钢渣利用率仅为10%左右,该数据显示钢渣利用率很低,距离钢铁企业固体废弃物“零”排放的目标尚远。
积极开发和应用先进有效的处理技术和资源化利用新技术,提高其利用率和附加值,是钢铁企业发展循环经济,实现可持续发展的重要课题之一。
钢渣利用途径和制约钢渣利用率的因素钢渣的利用途径大致可分为内循环和外循环,内循环指钢渣在钢铁企业内部利用,作为烧结矿的原料和炼钢的返回料。
钢渣的外循环主要是指用于建筑建材行业。
1 钢渣的内循环利用钢渣返烧结主要是利用钢渣中的残钢、氧化铁、氧化镁、氧化钙、氧化锰等有益成分,而且可以作为烧结矿的增强剂,因为它本身是熟料,且含有一定数量的铁酸钙,对烧结矿的强度有一定的改善作用,另外转炉渣中的钙、镁均以固溶体形式存在,代替溶剂后,可降低溶剂(石灰石、白云石、菱镁石)消耗,使烧结过程碳酸盐分解热减少,降低烧结固体燃料消耗。
钢渣在钢铁企业内部循环历来受到重视和普遍采用,配加转炉渣的烧结矿可改善高炉的流动性,增加铁的还原产量。
但是配矿工艺对返烧结有影响,过度使用会造成磷等有害元素的富集;配加转炉渣的烧结矿品位、碱度有所降低。
研究表明,当高炉炉料使用100%自熔性球团矿时,5%转炉渣作为溶剂加入会引起高炉运行不畅,原因是明显影响球团矿的软熔特性,增大软熔温度间隔,使炉渣粘性有增大趋势。
另外钢渣的成分波动较大,烧结配矿时要求钢渣各种氧化物成分波动≤±2%,粒度要求一般小于3mm,钢渣在成分上很难满足要求,对钢渣破碎和筛分的要求也高。
由于这些不利因素存在,尤其是各大钢铁公司普遍采用富矿冶炼,推行精料入炉方针,同时要求炼钢和炼钢工序的能耗和材料消耗指标不断降低,致使返回烧结利用的钢渣量越来越低。
不锈钢渣资源再生利用技术的研究
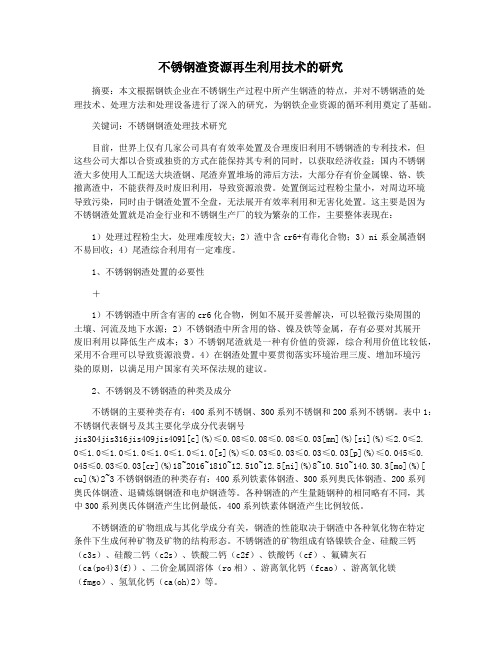
不锈钢渣资源再生利用技术的研究摘要:本文根据钢铁企业在不锈钢生产过程中所产生钢渣的特点,并对不锈钢渣的处理技术、处理方法和处理设备进行了深入的研究,为钢铁企业资源的循环利用奠定了基础。
关键词:不锈钢钢渣处理技术研究目前,世界上仅有几家公司具有有效率处置及合理废旧利用不锈钢渣的专利技术,但这些公司大都以合资或独资的方式在能保持其专利的同时,以获取经济收益;国内不锈钢渣大多使用人工配送大块渣钢、尾渣弃置堆场的滞后方法,大部分存有价金属镍、铬、铁撤离渣中,不能获得及时废旧利用,导致资源浪费。
处置倒运过程粉尘量小,对周边环境导致污染,同时由于钢渣处置不全盘,无法展开有效率利用和无害化处置。
这主要是因为不锈钢渣处置就是冶金行业和不锈钢生产厂的较为繁杂的工作,主要整体表现在:1)处理过程粉尘大,处理难度较大;2)渣中含cr6+有毒化合物;3)ni系金属渣钢不易回收;4)尾渣综合利用有一定难度。
1、不锈钢钢渣处置的必要性+1)不锈钢渣中所含有害的cr6化合物,例如不展开妥善解决,可以轻微污染周围的土壤、河流及地下水源;2)不锈钢渣中所含用的铬、镍及铁等金属,存有必要对其展开废旧利用以降低生产成本;3)不锈钢尾渣就是一种有价值的资源,综合利用价值比较低,采用不合理可以导致资源浪费。
4)在钢渣处置中要贯彻落实环境治理三废、增加环境污染的原则,以满足用户国家有关环保法规的建议。
2、不锈钢及不锈钢渣的种类及成分不锈钢的主要种类存有:400系列不锈钢、300系列不锈钢和200系列不锈钢。
表中1:不锈钢代表钢号及其主要化学成分代表钢号jis304jis316jis409jis409l[c](%)≤0.08≤0.08≤0.08≤0.03[mn](%)[si](%)≤2.0≤2.0≤1.0≤1.0≤1.0≤1.0≤1.0≤1.0[s](%)≤0.03≤0.03≤0.03≤0.03[p](%)≤0.045≤0. 045≤0.03≤0.03[cr](%)18~2016~1810~12.510~12.5[ni](%)8~10.510~140.30.3[mo](%)[ cu](%)2~3不锈钢钢渣的种类存有:400系列铁素体钢渣、300系列奥氏体钢渣、200系列奥氏体钢渣、退磷炼钢钢渣和电炉钢渣等。
科技成果——烟气磁化熔融炉处理钢铁尘泥及有价元素回收技术

科技成果——烟气磁化熔融炉处理钢铁尘泥及有价元素回收技术技术类别减碳技术所属领域钢铁行业适用范围适用于钢铁行业烧结、炼铁、炼钢和轧制工序含锌、铁尘泥等固体废物处理及综合利用。
应用情况传统处理钢铁行业烧结、炼铁、炼钢和轧制工序含锌、铁尘泥等固体废物多采用转底炉和回转窑工艺,产品为金属球团和次氧化锌。
烟气磁化熔融炉处理钢铁尘泥技术可回收尘泥中多种有价金属元素,比转底炉工艺减碳约15.98%、比回转窑工艺减碳约19.59%。
该回收技术及应用研究目前处于起步阶段,具有较广阔应用前景和市场空间。
成果简介(1)技术原理该技术以钢铁行业烧结、炼铁、炼钢和轧制工序含锌、铁尘泥等固体废物为原料,通过热熔造块和熔融炉高温还原工艺回收尘泥中的铁、锌、钾、钠、银、铟等有价金属元素,主要产品为再生生铁、硫酸锌、氯化钾、氯化钠、再生金/银/锌原料、硅酸盐炉渣及熔融炉法氧化锌粉。
(2)关键技术1、钢铁尘泥固废配比工艺技术根据冶金固废来源、物理化学特性,以及冶金固废制备特性,通过调整原料配比、工艺参数、混合方式,得到低成本、低消耗、高品质的热造块。
2、熔融炉及烟气磁化设备根据炉缸冶炼状态,优化熔融炉耐材、焦炭、布料方式及炉缸安全监测系统,消除有害元素循环富集对熔融炉操作及成本的影响。
3、有价金属分离富集技术分析有价元素在熔融炉内、提纯体系的转变行为,建立不同元素的循环富集计算模型。
根据有价元素的来源与赋存状态,分布、沉积规律等,形成有价金属元素高效梯级提纯技术。
4、有价金属提纯技术与设备根据有价金属理化成分、理化特性及元素迁移分配和逸出规律以及稀贵金属含量低的特性,确定有价元素定向分离与纯化技术,并配套设计相关装备和自动化控制系统。
(3)工艺流程物料→煤气→蒸汽烟气磁化熔融炉处理钢铁尘泥及有价元素回收技术工艺流程图主要技术指标钢铁尘泥按铁锌钾钠碳元素配比,热熔造块指标要求:Fe≥45%;Zn1-2%;转鼓强度60-65;碱度 1.5-1.7,碱金属(Na2O+K2O)0.3-0.5%;熔融还原炉内气体CO/(CO+CO2)比值为20-40%;磁化温度为600-800℃。
回转窑处理含锌尘泥技术现状及改进方向
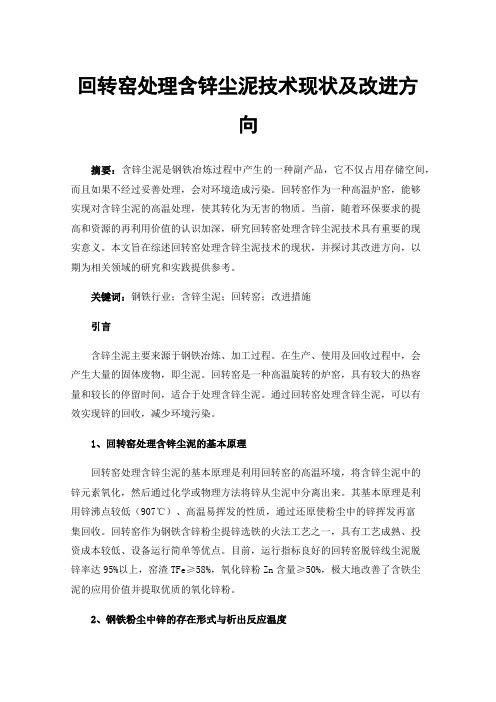
回转窑处理含锌尘泥技术现状及改进方向摘要:含锌尘泥是钢铁冶炼过程中产生的一种副产品,它不仅占用存储空间,而且如果不经过妥善处理,会对环境造成污染。
回转窑作为一种高温炉窑,能够实现对含锌尘泥的高温处理,使其转化为无害的物质。
当前,随着环保要求的提高和资源的再利用价值的认识加深,研究回转窑处理含锌尘泥技术具有重要的现实意义。
本文旨在综述回转窑处理含锌尘泥技术的现状,并探讨其改进方向,以期为相关领域的研究和实践提供参考。
关键词:钢铁行业;含锌尘泥;回转窑;改进措施引言含锌尘泥主要来源于钢铁冶炼、加工过程。
在生产、使用及回收过程中,会产生大量的固体废物,即尘泥。
回转窑是一种高温旋转的炉窑,具有较大的热容量和较长的停留时间,适合于处理含锌尘泥。
通过回转窑处理含锌尘泥,可以有效实现锌的回收,减少环境污染。
1、回转窑处理含锌尘泥的基本原理回转窑处理含锌尘泥的基本原理是利用回转窑的高温环境,将含锌尘泥中的锌元素氧化,然后通过化学或物理方法将锌从尘泥中分离出来。
其基本原理是利用锌沸点较低(907℃)、高温易挥发的性质,通过还原使粉尘中的锌挥发再富集回收。
回转窑作为钢铁含锌粉尘提锌选铁的火法工艺之一,具有工艺成熟、投资成本较低、设备运行简单等优点。
目前,运行指标良好的回转窑脱锌线尘泥脱锌率达95%以上,窑渣TFe≥58%,氧化锌粉Zn含量≥50%,极大地改善了含铁尘泥的应用价值并提取优质的氧化锌粉。
2、钢铁粉尘中锌的存在形式与析出反应温度根据化验分析,钢铁粉尘中锌的可能存在形式主要包括ZnO、ZnS、ZnSO4、ZnO·Fe2O3等,它们的理论析出反应温度如下表所示。
根据钢铁粉尘中锌的各种可能存在形式,理论上锌的析出反应温度均<1050℃,这一温度同时也满足钢铁粉尘中的Fe2O3在CO还原气体作用下阶梯式还原反应的温度要求—Fe2O3高温下在CO还原气体作用下,有可能被还原成FeO (380~800℃)与金属Fe(800~850℃)。
炉渣的处理与利用
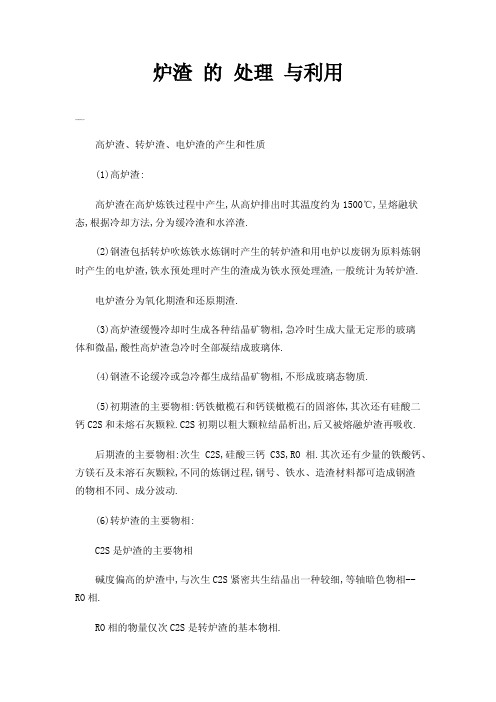
炉渣的处理与利用高炉渣、转炉渣、电炉渣的产生和性质(1)高炉渣:高炉渣在高炉炼铁过程中产生,从高炉排出时其温度约为1500℃,呈熔融状态,根据冷却方法,分为缓冷渣和水淬渣.(2)钢渣包括转炉吹炼铁水炼钢时产生的转炉渣和用电炉以废钢为原料炼钢时产生的电炉渣,铁水预处理时产生的渣成为铁水预处理渣,一般统计为转炉渣.电炉渣分为氧化期渣和还原期渣.(3)高炉渣缓慢冷却时生成各种结晶矿物相,急冷时生成大量无定形的玻璃体和微晶,酸性高炉渣急冷时全部凝结成玻璃体.(4)钢渣不论缓冷或急冷都生成结晶矿物相,不形成玻璃态物质.(5)初期渣的主要物相:钙铁橄榄石和钙镁橄榄石的固溶体,其次还有硅酸二钙C2S和未熔石灰颗粒.C2S初期以粗大颗粒结晶析出,后又被熔融炉渣再吸收.后期渣的主要物相:次生C2S,硅酸三钙C3S,RO相.其次还有少量的铁酸钙、方镁石及未溶石灰颗粒,不同的炼钢过程,钢号、铁水、造渣材料都可造成钢渣的物相不同、成分波动.(6)转炉渣的主要物相:C2S是炉渣的主要物相碱度偏高的炉渣中,与次生C2S紧密共生结晶出一种较细,等轴暗色物相--RO相.RO相的物量仅次C2S是转炉渣的基本物相.钢渣中未溶解或过饱和析出的CaO称为自由氧化钙,它是影响钢渣稳定性的重要物相.转炉渣特点:①FeO含量高②残留的石灰(自由氧化钙)电炉炼钢过程中精炼方法和所炼钢种的不同产生的渣也不同,主要可分为电炉溶化期和氧化精炼期发生的氧化渣以及还原精炼期和钢包精炼产生的还原渣.氧化渣由于吹氧时产生,氧化铁较多.还原渣中CaO和S较多.4.2炉渣处理技术4.2.1高炉渣处理技术(1)高炉渣用不同的处理方法可以得到四种产品:缓冷高炉渣膨化和泡沫高炉渣:与缓冷渣的区别在于其相对高的孔隙度和低的体积密度.球状高炉渣:冷却速度越快,玻璃相越多,结晶越少.粒状高炉渣:其水硬性很适合作水泥的添加剂.(2)我国高炉渣水淬处理方法:①Ocp法:滤渣法②Rasa法:搅拌槽法特点:冲渣水闭路循环,渣速为6t/min时,补充水量为5.08m3/min,约占冲渣水量的9%.水淬后的渣浆用管道输送到离高炉较远的地方脱水.渣水比为1:10,渣浆及渣浆输送管道易磨损,渣泵寿命1年到1年半,中级泵寿命约为4年,排泥泵约1.5年,渣浆管道约为2年.耗电量较多不能完全避免浮渣的产品,处理较为复杂③Tyna法:粒化轮法工艺过程:高炉渣由渣沟流下,落到有一定高差的粒化轮上,当渣粒和粒化轮相碰时,因机械作用使熔渣粒化,被粒化的渣粒在短时间内被喷水冷却,渣与水一起落入脱水转鼓.装有水渣混合物的滤斗,在转动过程中逐步脱水,当达到安装位置的上部时,过滤脱水基本结束,渣粒落入导向漏斗,由外部皮带机运至渣场.脱出的水进入转鼓下方的上水槽,通过溢流管流入下水槽.溢流口保证上水槽的水位使转鼓下部浸入水中一定深度,以便继续冷却转鼓.下水槽设计有水位计和冲渣水泵,冲渣水泵将下水槽的水往粒化轮上下的喷水口供冷却、粒化熔渣用.补充水维持下水槽的水位.下水槽沉积的残渣有一套气动提升装置使其返回转鼓脱水器,减少其对冲渣泵的磨损.技术指标:表4-6特点:a.运行安全b.作业率高c.脱水转鼓小巧灵活d.循环水量小、动力消耗少e.粒化轮渣含水量少f.装置占地面积小④INBA法:是高炉熔渣经水淬粒化--脱水--运输全系统的循环.粒化过程:熔炼通过渣道流至喷水箱上方,在水流作用下粒化,然后水渣经过水渣通道到脱水转鼓脱水.当粒化水与熔渣接触时,渣流被破碎成片状和线状,进一步沿水渣通道前进,变成渣滴.在水渣通道上只有少部分渣被粒化,多数在撞击到接收仓的挡板时或者落入接收仓后才完全粒化.只有部分水流是用来粒化高炉渣的,从喷水箱喷出的水流有一部分用来冷却水渣通道的耐磨保护板.粒化槽的作用:槽中有一定量的水,为粒化过程提供补充水.炉渣在粒化槽中湍流水的作用下比在水渣通道上粒化快.被喷水推进粒化槽内的炉渣与粒化槽中水的热交换过程也被强化.高炉渣中含有1%~2%的硫,硫在渣中的存在形式主要是CaS.粒化过程中高温的高炉渣与水和空气发生反应,释放出H2S和SO2气体.CaS+H2O=H2S+CaOCaS+3/2O2=SO2+CaO采用冷水冲渣加上蒸汽冷凝系统可以减少H2S的排放.4.2.2钢渣的处理工艺钢渣中自由氧化钙的存在不利于钢渣的利用.钢渣破碎(热拔、盘泼水冷、水淬、风淬等)→与水作用使氧化钙转变为氢氧化钙→钢渣处理间进行破碎、筛分、磁选等工艺处理,回收铁粒.钢渣"焖渣"处理工艺及设备①首钢钢渣处理工艺及设备②鞍钢钢渣加工工艺及设备③武钢钢渣加工工艺及设备④唐钢钢渣加工工艺及设备盘泼水冷(ISC法)浅盘水淬法的优点:用水强制快速冷却,处理时间短整个过程采用喷水和水池浸泡,减少粉尘对环境污染改变了渣的稳定性减少分段破碎、筛分加工工序采用分段水冷却处理、蒸汽可自由扩散,操作安全整个处理工序紧凑,劳动条件好.缺点:产生蒸汽量较多,蒸汽对厂房设备有影响,对起重机寿命有影响.钢渣水淬工艺指熔融的钢渣在流出、下降过程中,被压力水分割、击碎.再加上熔渣遇水急冷收缩产生应力集中而破裂,使熔渣粒化.工艺特点:用压力水粒化液态钢渣,既能满足在瞬间快速排渣,又能实现加工渣粒产品的目的.工艺形成:渣罐倾翻池内水淬工艺渣罐孔流沟内水淬工艺直接水淬工艺不论采用何种工艺形式,其流程基本相同:液态钢渣→压力水粒化器水淬钢渣→水淬集渣池→抓斗抓出→送往用户关于钢渣水淬产生中的爆炸问题物理现象引起"爆炸"的成因均是因大量的高温液态熔渣(成固融状态)把水覆盖包住,产生局部过热高温区,形成"封闭系统",水迅速汽化变成过热饱和蒸汽,体积急速膨胀,甚至可以达到几千倍,一旦内部压力达到冲破"封闭系统"阻力的临界压力时,瞬间以冲击波的形式将能量放出,形成"爆炸".消除"爆炸":钢渣水淬中"水"要限制液态钢渣既能深入水幕之中,而又不超过水幕之外,在水力集中点上把钢渣击碎、粒化,使之不形成局部过热高温区,就可以消除"爆炸"现象和事故发生.钢渣水淬工艺设计生产要点a.钢渣具有良好的流动性是实现钢渣水淬的前提.b.保证供水是防止和消除"爆炸"的关键.c.有效地控制渣流量是防止"爆炸"的重要手段.d.严格操作水淬渣的用途a.因急冷,潜在较多的内孔,并抑制了C2S的晶型转变及C2S分解,使其性能稳定.b.呈颗粒状、粒度均匀、无粉尘、不需要再加工,产品质量好,为综合利用提供了非常方便的条件.c.烧结料层透气性好,显著提高了烧结矿强度及烧结机产量.d.制造水泥加工简便、强度高、性能稳定e.生产农用肥,磷、钙等有益成分容易被植物所吸收f.既可以代替河沙又可用于喷砂除锈g.既可筑路又可方便回收钢锭水淬工艺的特点a.简化了工艺b.炼钢排渣速度快c.钢渣水淬工艺要求水淬点尽量靠近排渣点,因而其工艺环节紧凑,占地面积小.d.基建投资省、运行成本低e.水淬钢渣质量好,利用价值高,可满足多种途径利用钢渣的要求,经济效益好.钢渣水淬工艺生存条件a.具有掌握"钢渣水淬工艺"生产的技术力量b.钢渣性能好c.有用户要求水淬钢渣可以用于制作渣砖、水泥,也可以作烧结矿添加剂,在有此类需求的情况下,水淬钢渣就有市场.(4)辊筒--水池热淬法操作过程:从炉内放出的液态渣通过渣罐倒入安装在对辊上方的中间罐,钢渣从中间罐下口按一定速度流到对辊之间,由于对辊旋转,形成薄层渣,并逐渐落入水池中急冷.有的采用单辊式.(5)风淬法①经风淬而形成微粒的转炉渣,可做建筑材料②工艺流程:前处理段、风淬段、热回收段、后处理段③优点:处理钢渣的同时,可回收钢渣显热的41%.这种处理方法液态钢渣不与水接触,无爆炸危险,整个过程在罩式锅炉内,操作环境好;排出的热空气和热渣的热量还可以进一步回收.④工艺参数a.工作压力:0.35~0.6MPa(压缩空气)b.耗气量:35m3/t渣(标态)c.处理能力:2~2.5t/mind.对钢渣流动性的要求:能倒入中间包,并能从中间包流出即可.⑤主要设备及构筑物a.风淬钢渣平台及倾翻装置,220-Ⅱ-Ⅰ型渣罐车的渣罐倾翻传动装置b.压缩空气管网及自动控制系统c.粒化器,外形尺寸:650mm*360mm*120mm,布有φ8mm、φ10mm的27个喷吹孔d.中间包,11m3渣罐e.固定渣罐座f.10t桥式抓斗起重机,1.5m3抓斗g.粒化钢渣冷却池14.5m*6m*4.2mh.水幕系统⑥特点a.技术成熟、工艺简单、投资少b.占场地小,同时需水量少,完全做到循环使用不外排c.粒化彻底、处理能力大d.节约渣罐、经济效应明显(6)钢渣粉化处理粉化方式:自然老化、温水老化及蒸汽老化自然老化:利用雨水、空气中的水分或人工洒水对钢渣进行自然水和,需较大的渣场,处理时间约2年.温水老化:处理时间1周,设备成本高,微粒成分偏析蒸汽老化:2天(7)选择钢渣处理方法的原则①处理能力大②处理后的成品状态适合于应用③处理后的成品应用效果好,经济效益高④生产工艺流程和设备简单⑤安全易行⑥处理成本低4.3炉渣的资源化途径与存在的问题4.3.1高炉渣利用途径(1)粒化高炉渣做水泥混合材(2)粒化高炉渣矿粉做水泥和混凝土掺和料(3)粒化高炉渣做砖(4)高炉渣做硅肥(5)缓冷渣做混凝土骨料、道路材料(6)膨胀矿渣珠做混凝土轻骨料(7)做矿渣棉、铸石、微晶玻璃材料4.3.2钢渣利用途径(1)钢渣利用途径:做水泥、做砖和砌块、作炼铁烧结矿原料、道路基层材料,配烧水泥熟料等.(2)钢渣的厂内循环再利用和冶金功能:A.用作烧结矿溶剂:(代替石灰石等)优点:①提高烧结矿强度,改善烧结矿质量②有利于提高烧结矿产量③有利于降低燃料消耗④有利于降低烧结矿的生产成本B.钢渣用作高炉溶剂优点:①提高铁水含锰量,在某些特定条件下还能富集钒、铌等有益元素,提高了资源综合利用程度②利用钢渣中的铁,取代部分铁矿石,降低了生产成本③代替石灰石,减少碳酸盐分解热,有利于降低焦比④钢渣中的MnO、MgO有利于改善高炉渣的流动性(3)筑路和建筑材料A.建筑材料:降低膨胀性B.铺筑道路优点:①防滑性好,不易开裂、拉裂(钢渣沥青路面)②承重层变形小,道路工作寿命长(轮碾试验)③抗冻解冻性,适应寒冷气候开放道路的使用(4)钢渣用于农业钢渣是一种以钙、硅为主含有多种成分的具有速效又有后劲的复合矿物质肥料.钢渣磷肥对酸性、中性和碱性土壤都有用,同时渣中丰富的CaO和SiO2等也有不同程度的肥效.(5)钢渣作水泥由于C2S的含量较多,水泥的后期强度持续增长优点:良好的耐磨性、耐腐蚀性、抗冻融性、水化热低、收缩率小等一系列特点.不足:水泥细度难以保证,细度不够影响水泥早期强度,水泥性能不稳定,尽量减少水泥中的MgO的含量.(6)钢铁渣作水泥的生态意义①水泥的制造过程采用石灰石配烧熟料,在高温下分解为CaO和CO2,直接参与反应的是CaO,而CO2排放到大气中,同时带走大量的热能,水泥的生产需要能耗大量的能源.能源的巨大消耗意味着大量CO2的排放因此在水泥生产中应愈来愈多地使用其他有水硬性能的原材料,至今为止最重要的是钢铁渣作为水泥的部分替代原料用钢铁渣配料则无CaCO3的分解,也不存在CO2污染大气现象,对水泥工业节能降耗、保护环境都有重要作用.(7)钢渣资源化所受的限制①CaO和MgO的存在使钢渣的体积不稳定②CaSiO4由α相向γ相的转变使钢渣容易粉化③其中氟和重金属有被雨水、浸出污染环境的危险④铁氧化物含量较高⑤与其他天然材料的市场竞争⑥钢渣直接返回冶金流程中再利用时磷会逐渐富集到铁中⑦某些含有有价元素如Cr、V等的钢渣还没有很好地开发利用(8)其他利用途径如果能除去钢渣中的P2O5,其余成分皆可作为炼钢溶剂循环使用.转炉渣在缓慢冷却凝固时,其中所含有的P2O5大部分固溶于初晶相Ca2SiO4-Ca3(PO4)2中,渣炉渣中的磷有98%进入初晶相Ca2SiO4-Ca3(PO4)2中.将转炉渣用碳质还原剂进行还原,可以将炉渣中的Fe、Mn、V、P等元素还原得到碳饱和铁,炉渣冷却后可回收铁粒.脱出了Fe、Mn、V、P等元素的转炉渣则主要含有CaO、SiO2、MgO等成分,很适合作冶金熔剂或其他材料.还原过程可以在转炉出渣时进行,利用高温炉渣的潜热,可以减少能量消耗.转炉渣高温碳热还原,不需添加任何溶剂,金属和氧化物容易分离,除磷彻底,如果在热态下进行,还可以充分利用转炉渣的热能,不失为转炉渣资源化的一个新途径.4.4少渣冶炼钢渣量增加的解决方法:减少钢渣的发生量促进钢渣的有效利用4.4.1日本几个钢铁公司的少渣冶炼工艺(1)新日铁的少渣冶炼工艺A.转炉双联法:一座转炉专用于脱磷,另一座用来脱碳B.同炉出铁排渣MSN空间完美搬家到新浪博客!。
- 1、下载文档前请自行甄别文档内容的完整性,平台不提供额外的编辑、内容补充、找答案等附加服务。
- 2、"仅部分预览"的文档,不可在线预览部分如存在完整性等问题,可反馈申请退款(可完整预览的文档不适用该条件!)。
- 3、如文档侵犯您的权益,请联系客服反馈,我们会尽快为您处理(人工客服工作时间:9:00-18:30)。
[键入文字]
技术|利用钢厂停产小高炉改建熔融钢渣协同处理尘泥、冶炼渣等固废危废新思
路
北极星固废网讯:一、钢铁工业尘泥、冶炼渣处理现状
钢铁厂内部每天产生大量的含有容易循环富集的钾钠锌等有害元素的高炉布袋瓦斯
灰、烧结机头灰和炼钢污泥等固废得不到处理,每天产出量更大的转炉钢渣因含有害
元素磷,同样不便在烧结生产环节消纳利用。湖南建鑫公司研究开发了利用钢厂泰科
钢铁等高温熔体协同处理尘泥、冶炼渣固废危废分离回收整体解决方案的两项专利技
术,发表了《含锌瓦斯灰、除尘灰、污泥及冶金渣等固废协同处理整体解决方案探
讨》、《利用钢厂高温熔融钢渣协同处理钢铁及有色化工尘泥、冶炼渣等固废危废新技
术》两篇文章,引起了业内同行的关注。其中,熔融钢渣的液态下采用处理炉处理,
如何实施是大家关心的问题,本文结合现有大钢厂拆小建大,将停产的小高炉改建成
处理熔融钢渣与钢厂及有色化工固废危废的类似高炉进行钢渣固废处理生产,不失为
一条新的路子。
处理含铁含锌尘泥固废,国内有物理分选法、回转窑及转底炉法(固态)、国内引进
的太钢 OxyCup 竖炉法(液态)和宝钢 Corex、山东墨龙 HIsmelt 熔融还原法(液态)
也能处理部分尘泥固废。其中,OxyCup 竖炉法工艺---类似于一个直筒炉型的小高炉,
借鉴了高炉炼铁的一些技术,将各种含铁废料做成含碳压块加入竖炉内,直接产出铁
水和炉渣,并且在煤气除尘系统收集到含锌的烟灰或除尘泥。但不便大量循环利用的
含磷有害元素的转炉钢渣的处理大多停留在传统热拨、热闷等冷态处理上,未见有新
的钢渣固废处理技术出现。
OxyCup 竖炉法工艺实际上就是一个专门用来处理固废加废钢的半化铁半炼铁高炉工
艺,在处理固废方面具有一定的合理性。太钢引进的德国帝森-克虏伯 OxyCup 竖炉
1