abfkxp加成型热固化硅橡胶使用中常见原因及解决办法
硅酮胶常见问题及处理方法

硅酮玻璃胶施工问题硅酮胶常见问题及处理方法摘要:硅酮玻璃胶施工中常会遇到如,胶缝起泡、中性透明胶变黄、中性瓷白胶变粉红、有些玻璃胶打出来时有盐粒般大小的粒状,而固化后有些粒状又会自动化解等问题。
那么,导致这些问题的原因的是什么?玻璃胶施工问题硅酮胶常见问题及处理方法一、耐侯胶胶缝起泡原因及预防方法针对某用户使用耐候胶时,胶缝出现较严重的起泡现象,经技术专家的研究,得出了以下起泡原因分析:1、施工时各种操作的影响可能造成起泡1)胶缝及基材湿度较大,有雨水;2)施工时不小心把泡沫棒划破;3)泡沫棒选择不对,泡沫不能采用低密度的,必须符合相关规范的闭口式泡沫棒;4)施胶的厚度不够、太薄;以上这些因素都是可以避免的,在施工时一定要保证胶缝及基材是干燥,清洁的,注意操作时不能把泡沫棒划伤,根据接缝大小选择合适的泡沫棒。
2、温差过大会造成胶缝起泡。
首先说夏天的情况,在夏天,白天温度很高,湿度很大,如果在上午或午后施工特别容易起泡,因为硅酮耐候胶是在一定温度条件下靠吸收空气中的水份进行固化的。
当在上午或午后施胶后,这时硅胶的固化速度很快,硅酮胶固化过程中会释放出化学物质形成气体,聚集在一起不能立即逸出胶体。
这样会造成起泡现象,一般这种情况发生在幕墙阳面和幕墙组件尺寸长的一侧胶缝,在傍晚太阳下山时施胶,可以缓解这种现象。
由于冬天昼夜温差过大,温度低,气候较干燥就可能引起这一现象。
冬天胶体固化需较长时间,胶体施工后在末完全固化时,幕墙各单元组件本身有一定位移,加之昼夜温差过大产生更大的位移量胶体未完全硫化时抗位移能力较差,这样便形成耐候胶缝起鼓现象。
以上现象仅仅只给部分幕墙胶缝的美观造成影响,但对胶体的性能指标不产生任何不良结果,该现象随着温差变小会有所缓解。
因硅酮耐候胶具有卓越的耐候性能和极强的耐高低温性,建议在符合以下条件下可以施工:1、请避开雨天天气施工,注意施胶这段时间的天气情况,最好无雨天。
2、在施胶时必须得让胶缝及胶所接触基材是干燥的。
ab硅胶灌封时气泡解决方案

ab硅胶灌封时气泡解决方案AB硅胶灌封时气泡解决方案背景在AB硅胶灌封过程中,常常会出现气泡问题,这不仅会影响灌封效果和产品质量,还可能导致产品失效。
因此,我们需要一套解决方案来减少甚至消除气泡的产生。
解决方案以下是一些可行的方案来解决AB硅胶灌封时的气泡问题:1.原料筛选和处理:–选用较低粘度的AB硅胶,以降低其在灌封过程中产生气泡的可能性。
–对硅胶进行充分搅拌,以减少其中悬浮颗粒和气体的存在。
–过滤硅胶,以去除其中的杂质和颗粒。
2.设备优化:–确保灌封设备的密封性良好,避免外界空气进入。
–定期检查和维护设备,确保其正常工作,避免因设备问题导致气泡产生。
3.灌封操作优化:–控制灌封速度和压力,避免过快或过大的压力造成气泡。
–采用低压、恒定压力的灌封方式,以减少气泡的产生。
–避免在注射过程中产生剧烈的流动和湍流,以降低气泡的形成。
4.环境控制:–在灌封区域保持相对稳定的温度和湿度,避免环境因素对灌封过程产生影响。
–减少灰尘和颗粒等异物的存在,以减少其与硅胶反应产生气泡的可能性。
结论通过以上方案的综合应用,可以有效地解决AB硅胶灌封时的气泡问题。
然而,需要注意的是,不同生产环境和产品特性可能需要针对性地调整方案,以达到最佳效果。
因此,在实施方案之前,建议进行充分的实验和验证,以确保方案的适用性和可行性。
方案实施步骤为了有效地解决AB硅胶灌封时的气泡问题,可以按照以下步骤进行方案实施:1.调研和分析:–针对产品特性和生产环境,对气泡问题进行调研和分析。
–确定气泡产生的原因和可能影响因素。
2.制定方案:–根据调研和分析结果,制定适合本次案例的方案。
–综合考虑原料调配、设备优化、操作控制和环境控制等方面,提出具体的解决方案。
3.方案实施:–根据方案,采取相应的措施对AB硅胶灌封过程进行调整和优化。
–对原料进行筛选和处理,确保其质量符合要求。
–对设备进行检查、维护和调整,以确保其正常工作。
–对操作流程进行培训和指导,确保操作人员能够正确执行方案。
703硅橡胶加速固化的方法

703硅橡胶加速固化的方法
硅橡胶的固化速度取决于多种因素,包括温度、湿度、催化剂等。
为了加速硅橡胶的固化,可以采用以下几种方法:
1. 加热固化:通过提高温度来加速硅橡胶的固化过程。
通常可以将硅橡胶制品放入烘箱或加热器中加热,温度越高,固化速度越快。
但需注意,不同类型和品牌的硅橡胶有不同的耐热性能和固化温度范围,因此应按照厂家建议的温度进行加热。
2. 添加催化剂:某些硅橡胶需要添加催化剂才能加速固化。
可以根据硅橡胶的种类选择合适的催化剂,并在制作过程中加入。
但需注意,催化剂过多可能导致硅橡胶提前固化,而催化剂过少则可能无法有效加速固化。
3. 增加湿度:硅橡胶在潮湿的环境下可以更快地固化。
可以在硅橡胶制品上喷洒水雾或将其放置在潮湿的环境中,以增加湿度并加速固化。
4. 紫外线固化:某些硅橡胶可以通过紫外线照射来加速固化。
这种方法通常需要使用特殊的紫外线灯或光固化机。
但需注意,紫外线照射可能影响硅橡胶的颜色和耐久性。
需要注意的是,加速硅橡胶固化的方法应根据具体情况选择,并且应遵循厂家建议的操作方法和条件。
过度加热、使用不合适的催化剂或长时间暴露在紫外线下可能会影响硅橡胶的性能和寿命。
ab胶固化后表面不平的原因

ab胶固化后表面不平的原因胶水不固化:这可能是由于固化剂放得太少或太多(配比相差很大)、A胶储存时间较长用前未搅拌或未搅拌均匀所导致的。
本应为硬胶的胶水固化后是软的:这可能是由于胶水配比不正确,例如未按重量比配比或偏差较大(固化剂多了或少了都会有可能有此情况)、A胶储存时间较长用前未搅拌或未搅拌均匀所导致的。
有些胶水固化了,有些胶水没有固化或固化不完全:这可能是由于搅拌不均匀、A胶储存时间较长用前未搅拌或未搅拌均匀所导致的。
固化后胶水表面很不平整或气泡很多:这可能是由于固化太快、加温固化温度过高、接近或超过操作时间灌封点胶所导致的。
固化后胶水表面有油污状:这可能是由于灌胶过程有水、过于潮湿、A胶储存时间较长用前未搅拌或未搅拌均匀所导致的。
气温偏低或变化异常时环氧树脂组份可有一定机率会出现结晶现象,此时只需将结晶组份放于60-80度环境中加温30-60分钟后搅拌均匀即可使用。
拓展资料:ab胶固化后不平整处理方法一、胶结不均匀导致不平整在施工过程中,如果胶液没有充分混合均匀,或者涂敷不够均匀,就会导致胶固化后的表面不平整。
这种情况下,需要重新涂敷胶,并且在涂敷前,将胶液充分搅拌均匀,保证胶液的均匀性。
二、温度和湿度影响胶固化结构胶的固化速度和质量受到环境温度和湿度的影响。
如果温度过低或者湿度过高,都会影响固化质量,导致不平整的表面。
为了解决这个问题,可在施工前检查天气情况,确保环境温度和湿度适宜施工。
如果已经出现不平整的情况,可以使用加热或者通风的方式来改善环境条件,提供固化质量。
三、胶固化后修剪不平整表面如果以上两种措施都没有解决问题,就需要对不平整表面进行修剪。
先用工具清理掉表面杂质,然后使用粗砂纸或其他研磨工具研磨表面,直至表面光滑均匀。
注意不要过度研磨,避免影响胶的固化质量。
四、合理施工预防不平整预防结构胶固化后不平整的最好方法是合理施工。
在涂敷胶液之前,清理基材表面,确保其干燥清洁;涂敷过程中,加强操作规范,保证涂敷均匀;固化后,检查表面情况,及时予以修正。
导热硅胶片的热老化变硬问题

导热硅胶片的热老化变硬问题导热硅胶片的热老化变硬问题导热硅胶片在电子产品、汽车零部件和工业设备中被广泛应用,其优异的导热性能使其成为热管理领域不可或缺的材料。
然而,随着使用时间的增加,导热硅胶片可能会出现热老化变硬的问题,影响其导热性能和使用寿命。
本文将深入探讨导热硅胶片的热老化变硬问题,分析其成因和影响,并提出相应的解决方案。
1. 热老化变硬问题的成因导热硅胶片的热老化变硬问题主要由以下几个因素导致:1.1 温度影响:长期高温环境下,导热硅胶片中的有机成分易发生氧化、聚合等化学反应,导致材料结构变硬。
1.2 材料质量:导热硅胶片的制造工艺和原材料质量对热老化变硬问题有着重要影响,质量不合格的材料容易在高温下失去弹性。
1.3 应力影响:导热硅胶片在使用过程中受到机械应力影响,如挤压、拉伸等,容易导致材料变形和变硬。
2. 热老化变硬问题的影响导热硅胶片的热老化变硬问题会严重影响其导热性能和使用寿命,具体表现在以下几个方面:2.1 导热性能下降:材料变硬后,其导热性能会受到较大影响,导致热管理效果降低。
2.2 机械性能减弱:材料变硬后,弹性模量下降,易导致材料在挤压、拉伸等应力下发生破裂或变形。
2.3 使用寿命缩短:热老化变硬会加速导热硅胶片的老化过程,缩短其使用寿命,降低产品的可靠性。
3. 解决热老化变硬问题的方案针对导热硅胶片的热老化变硬问题,可以从以下几个方面进行解决:3.1 材料改进:优化导热硅胶片的配方和生产工艺,提高材料的耐热老化性能和机械性能。
3.2 温度管理:在实际使用中,合理设计散热系统,控制导热硅胶片的工作温度范围,减少热老化变硬的影响。
3.3 应力管理:在安装和使用导热硅胶片时,注意避免过大的机械应力,减少材料的变形和破裂。
4. 个人观点和总结导热硅胶片的热老化变硬问题是一个需要高度重视的技术难题,解决这一问题对于提高导热硅胶片的可靠性和使用寿命至关重要。
通过不断改进材料质量、优化设计和加强管理,可以有效降低导热硅胶片热老化变硬的风险,为电子产品和工业设备的稳定运行提供保障。
某公司橡胶模压制品常见缺陷及解决方法

橡胶模压制品常见缺陷及解决方法喷霜混炼胶或硫化胶内部的液体或固体配合剂因迁移而在橡胶制品表面析出形成云雾状或白色粉末物质的现象。
这是由于硫、石蜡、某些防老剂、软化剂的使用量超出了它们在橡胶中的溶解度而引起的。
为防止喷霜,上述各种配合剂用量要适当,对常见的硫黄喷霜可采用不溶性硫黄加以防止。
在橡胶中适当加入松焦油,液体古马隆等可增加胶料对上述配合剂的溶解度,以减少喷霜现象。
喷霜-定义和由来喷霜又名喷出(blooming),是橡胶加工过程中常见的质量问题,它是指未硫化胶或硫化胶中所含的配合剂迁移到表面并析出的现象。
有时,这种喷出物呈霜状结晶物,故习惯上称“喷霜”。
较多见的喷霜物为硫,因为硫黄是通用橡胶中应用最广泛的硫化剂,且在橡胶中的溶解度低因而容易产生喷霜。
其实从喷出物外观来看,也未必都呈霜状,也有呈油状(软化剂、增塑剂)或粉粒状(多为填充剂、防老剂、促进剂等)的物质喷出,甚至炭黑喷出也有所见。
喷霜-防霜剂硅胶也会有喷霜现象,采用双二四硫化剂(通常用在挤出成型工艺)高温分解后会产生低分子量的酸性物质,其与硅橡胶不相容,在存放过程中会转移到硅胶表面结晶从而出现喷霜。
防霜剂主要成分为碱性物质,通过酸碱中和反应来达到防霜的目的。
高硬度的硅胶往往加入比较多的内脱模剂,遇水也会喷白,水的酸性对此有遏制作用硅橡胶模具制作方法及注意事项模具是快速模具里的一种最为简单的方法,一般是用硅胶将RP原型进行复模,但寿命很短,只有10-30件左右!他具有很好的弹性和复制性能,用硅橡胶复制模可不用考虑拔模斜度,不会影响尺寸精度,有很好的分割性,不用分上下模可直接进行整体浇注。
再沿预定的分模线进行切割取出母模就可以了!室温硫化硅橡胶又分为加成型和缩合型两种!原料及配方采用专用模具硅橡胶,该品系以双包装形式出售,A组份是胶料,B组份是催化剂。
配制时要考虑室温、模具的强度和硬度,以此来确定AB组份的重量配制比例。
室温在20-25度时,A:B=100:1.5。
ab硅胶凝固条件

ab硅胶凝固条件ab硅胶是一种常见的胶凝材料,广泛应用于工业生产和科研实验中。
要使ab硅胶凝固,需要满足一定的条件。
本文将围绕ab硅胶凝固条件展开讨论,以便更好地理解和应用这一材料。
温度是ab硅胶凝固的重要条件之一。
在一般情况下,ab硅胶在室温下即可凝固。
但对于某些特殊的应用场景,可能需要调整温度以加快或延缓凝固速度。
在制备ab硅胶产品时,通常会在一定温度范围内进行加热或降温处理,以控制其凝固时间和硬度。
固化剂的添加量也是影响ab硅胶凝固的重要因素。
ab硅胶通常由两部分组成,即主胶和固化剂。
在制备过程中,需要按照一定的配比将两者混合均匀。
固化剂的添加量与凝固速度和硬度密切相关。
一般而言,固化剂的添加量越多,凝固速度越快,硬度也越大。
因此,在实际操作中,需要根据具体的需求和要求来确定固化剂的添加量。
搅拌是促使ab硅胶凝固的重要手段之一。
通过搅拌可以使主胶和固化剂充分混合,使其反应更加均匀。
在搅拌过程中,一般需要使用专用的搅拌器或搅拌设备,以确保混合均匀度和反应效果。
搅拌的时间和速度也需要根据具体情况来确定,以避免过度或不足的搅拌对凝固效果造成影响。
环境湿度也对ab硅胶的凝固有一定的影响。
在干燥的环境中,ab硅胶的凝固速度通常较快。
而在潮湿或高湿度的环境中,凝固速度则可能变慢。
因此,在实际应用中,需要对环境湿度进行控制,以确保ab硅胶能够在适当的时间内凝固。
压力也可以影响ab硅胶的凝固效果。
在一些特殊的应用场景中,需要通过施加一定的压力来促进ab硅胶的凝固。
这种压力可以通过机械设备或其他手段施加,以确保ab硅胶在凝固过程中能够充分填充和固化。
ab硅胶的凝固条件包括温度、固化剂的添加量、搅拌、环境湿度和压力等因素。
合理控制这些条件,可以实现ab硅胶的有效凝固,从而满足不同领域的应用需求。
在实际操作中,需要根据具体情况进行调整和优化,以获得最佳的凝固效果。
通过深入了解和研究ab 硅胶凝固条件,我们可以更好地应用这一材料,推动相关领域的发展和创新。
混炼硅橡胶平板硫化一段模压常见的问题及解决办法
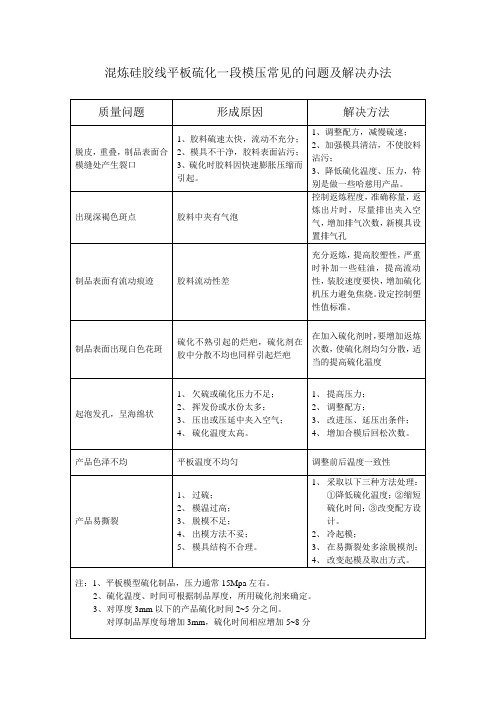
混炼硅胶线平板硫化一段模压常见的问题及解决办法
平板硫化二段模压常见的问题及解决办法
二段硫化目的:
1、消除一段硫化中所分解产生的一些低分子物质,以避免对制品产生老化催化作用。
2、稳定硫化制品的基本物性。
(硬度、拉伸强度、伸长率),改善压缩永久变形。
3、防止低分子挥发物污染接触的介质。
(如食品、医疗等用途的硅胶制品)
二段硫化条件:
1、可根据制品大小而定,制品愈厚升温速度愈慢,时间愈长。
2、高强度、高抗撕的制品,二段硫化温度以200℃为宜。
3、通常采用的二段硫化条件为
1~5mm 厚制品:150℃×1h、180℃×1h、200℃×1h
5~10mm 厚制品:150℃×1h、180℃×1h、200℃×2h
10~20mm 厚制品:150℃×2h、200℃×2h
常压热空气连续硫化中常见问题及解决办法。
- 1、下载文档前请自行甄别文档内容的完整性,平台不提供额外的编辑、内容补充、找答案等附加服务。
- 2、"仅部分预览"的文档,不可在线预览部分如存在完整性等问题,可反馈申请退款(可完整预览的文档不适用该条件!)。
- 3、如文档侵犯您的权益,请联系客服反馈,我们会尽快为您处理(人工客服工作时间:9:00-18:30)。
1 / 7 -+ 懒惰是很奇怪的东西,它使你以为那是安逸,是休息,是福气;但实际上它所给你的是无聊,是倦怠,是消沉;它剥夺你对前途的希望,割断你和别人之间的友情,使你心胸日渐狭窄,对人生也越来越怀疑。
—罗兰加成型热固化硅橡胶使用中常见原因及解决办法 A、胶不固化 出现问题的原因: 加成胶中的催化剂中毒或过期失效;固化温度不够或时间不够造成固化不完全。
造成问题的原因可能是: 因为计量器具误差或人为的因素造成配胶比例错误;产品超过了储存期或接近储存期造成失效、效能降低;储存时因储存不当造成产品中催化剂失效或效能降低;使用时的环境中有使催化剂中毒的因素,如含磷、硫、氮的有机化合物,或与加成硅胶同时使用聚氨酯、环氧树脂、不饱和聚脂、缩合型室温硫化硅橡胶等产品;固化温度不够或时间不够造成固化不完全。
解决办法: 计量器具必须定期校验;双组分配胶时采用双人制度;保证生产厂家要求的储存条件,并注意储存期,使用时遵循“先进先出”原则,保证在尽可能短的有效期内使用完毕。工作场所远离其它可能有害的有机化合物,严禁吸烟后立即使用胶料。
B、与基材的粘接性差 出现问题的原因: 加成硅橡胶的自身缺陷;未对所粘接的材料进行表面的处理;或基材材质更改。
造成问题的原因可能是: 2 / 7
未选择粘接性的产品牌号;因为计量器具失效或人为的偶然误差造成双组分配胶比例错误;产品超过了储存期而失效或效能降低;储存时因储存不当造成产品中催化剂失效或效能降低;使用时未能选择适当的增粘底涂剂;升温过高和固化速度过快,产生因温度变化而发生的膨胀系数不同造成的粘接性差;单组分从冰柜取出立即使用,而未放置一段时间“回温”。
解决办法: 选择增粘型的加成硅胶产品;计量器具必须定期校验;双组分配胶时采用双人制度;注意储存期,遵循“先进先出”原则;正确按照要求储存,保证胶的有效性;为保证粘接性,尽量在使用时选择使用配套的增粘底涂剂;固化时,为避免高温下固化速度过快而产生的内应力,尽量采用分阶段固化的方式,避免高温过快固化;单组分产品从冰柜取出后不立即使用,而是放置一段1~2小时,使胶与环境达到温度平衡再使用。
C、粘度有变化 原因: 加成胶的配方或生产不稳定;或超过储存期而变化。 造成的原因可能是: 因为计量器具失效或人为的偶然误差造成双组分配胶比例错误;单组分胶过了储存期或接近储存期而失效;储存时因储存不当造成;使用时,双组分一次配胶太多,超过允许操作时间,使前半部分的胶料粘度偏低,而后半部分的胶料粘度偏高;单组分则在使用环境温度下,放置时间过长,尤其是夏天未用完部分;使用时的环境温度过高;生产厂家的批次不稳定,超出了规定允许的粘度波动范围;所选择的产品规格型号不符合所需要使用的产品。
解决办法: 严格控制生产的批次稳定性在指标的许可范围内;计量器具必须定期校验;双组分配胶时采用双人制度;注意储存期,先进先出;正确按照要求储存,保证胶的有效性;使用环境温度尽量恒温,保证产品使用的环境温度具有一致性,但应注意,如果生产环境无条件恒温,则注意根据环境温度的变化来调 3 / 7
节。在夏天,单组分使用完毕后,立即送到冰柜保存;双组分则减少每一次的配胶量,而采用少量多批次配制的方法;冬天,对于粘度高的双组分产品,还可以采用A/B两组分分别升温至30~50℃预先热处理以降低其粘度后,再进行配胶的方法降低胶料粘度,但应注意此时的操作时间会随温度的升高而减少;当然也可以使用添加适量的有机溶剂(注意:
不得有水或其他杂质,最好为试剂级)来降低粘度来处理,但是,不推荐使用此方法!首先必须注意选择适合的产品型号规格才是关键!
D、固化物表面发粘 ●原因: 加成胶催化剂中毒或过期失效;或超过储存期而变化。造成的原因可能是:
因为计量器具误差或人为的偶然误差造成双组分配胶比例错误;单组分胶过了储存期而失效;储存时因储存不当造成;使用时,双组分一次配胶太多,超过允许操作时间,常温下放置时间过长,胶中的催化剂为空气中的一些物质所毒化失效;单组分则在使用中,固化温度过低或固化时间不足所致;使用时制品的表面涂层厚度过薄,使胶中的催化剂为空气中的一些物质所毒化失效;生产厂家的批次不稳定所致;所选择的产品规格型号不符合所需要使用的产品;使用环境有使催化剂中毒的因素,如含磷、硫、氮的有机化合物,或与加成硅胶同时使用或同一环境中使用聚氨酯、环氧树脂、不饱和聚脂、缩合型室温硫化硅橡胶等产品。
解决办法: 严格控制生产的批次稳定性在指标的许可范围内;计量器具必须定期效验;双组分配胶时采用双人制度;注意储存期,先进先出,在尽可能短的有效期内使用完;正确按照要求储存,保证胶的有效性;使用环境条件下,涂复或灌封的产品尽量减少常温的存放期,进入烤箱升温固化,以保证胶中的催化剂活性;双组分则减少每一次的配胶量,而采用少量多批次配置的方法;冬天,对于粘度高的双组分产品,还可以采用A/B两组分分别升温至30~50℃预先热处理以降低其粘度后,再配胶的方法使用,但应注意此时的操作时间会随温度的 4 / 7
升高而减少;使用环境不得有使胶可能中毒的含磷、硫、氮的有机化合物,或与加成硅胶同时使用或同一环境中使用聚胺脂、环氧树脂、不饱和聚脂、缩合型室温硫化硅橡胶等产品;所选择灌封或涂复的产品尽量大于1㎜的厚度。
E、其他问题 1.导热性及影响因素: 有机硅材料本身的影响: 首先,有机硅材料(silicones)由于是由无机硅(结晶硅的导热系数为 1.4W/M.K、熔点为1420℃、二氧化硅的熔点1710℃;硅在地壳中占~ 25.8%)与有机物的结合产物----主链含有--[-S-O-]n-的含硅-碳键的化合物,所以他兼具有二者的许多共性,即,有机硅材料既具有无机硅的许多特性,又具有有机物的许多特性,它是合成高分子材料中的特种高分子材料。一般有机物的导热系数都比较小,而无机物的导热系数都比有机物要大,所以有机硅硅橡胶的导热系数(一般为
0.2~ 0.3W/M.K)都比普通的高分子聚合物橡胶的导热系数高2倍左右。 填充物或助剂的影响: 综上所述,尽管,有机硅材料的导热系数高于一般合成高分子材料,但是单独作为导热材料使用,尚无法满足电子元器件的散热需要。一般电子元件对传热材料的导热性要求都在
0.5W/M.K以上,当然是导热系数越高越好!加成型导热液体硅橡胶一般是由金属氧化物和加成硅橡胶的基础材料经过特殊的工艺加工而成的。所以添加的导热材料的性能高低和工艺性决定了最终加成型导热液体硅橡胶的导热性能指标。
填充物的选择与工艺技术的影响: 5 / 7
加成型导热液体硅橡胶的另外的要求是电气绝缘性能要好,而此项指标与导热性能指标有相互冲突之处。一般电气绝缘性好的材料,导热性都比较差,如:
PP、P E、PET等;而导热性好的材料则导电性好,即电气绝缘性差。如: 铜、铝、金、银及其氧化物;所以选择适当的导热材料作为填充物是生产厂家的产品性能能否兼顾的技术关键。
施工粘度或流动性与导热性之间关系的影响: 一般来讲,在配方恒定的情况下,导热性越高,胶的粘度越大,流动性越差;反之,则导热性小,流动性好,胶料的粘度也小;当然也与填料和加工工艺有关。
其次使用时,如果胶料未能充分搅拌就直接混合使用,也必然导致同一桶胶的前半部分粘度小,后半部分粘度变大,不好使用。也会导致同一桶胶料性能差异。
施工方法与储存的影响: 一般导热性的硅橡胶,如上所述,都添加有导热性填料或助剂,储存放置一段时间之后,这些导热性填料或助剂会沉淀,放置的时间越长,沉淀越严重,使用时必须搅拌均匀,方能使用,尤其是双组分更是如此,所以储存了一段时间的导热硅橡胶使用前,必须充分搅拌均匀才能使用。
否则使用了上半部分的导热性就差,粘度也偏小;下半部分的导热性好,但是粘度偏大而造成施工困难。
所以,对于选择涂覆方法施工的双组分加成型导热硅橡胶来讲,此项必须加以注意!否则测试导热性时必然会发生不稳定现象!
综上所述,导热性的影响因素较多,只要注意了解上述所说的导热性能与影响因素,正确使用和选择适宜的产品牌号,产品质量必然会稳定和保证。 6 / 7
2.电性能(在很宽的频率和温度范围内变化很小,甚至浸入水中,电性能也变化很小);
体积电阻率: ~1×(1014~1016)Ω.cm 表面电阻率: ~1×(1012~1014)Ω.cm 介质损耗角正切: <10-3 耐电弧性: ≥180S(丁基橡胶则为72S) 介电强度:18~36KV/m 介电系数(50HZ/25℃): 2.7~ 3.3 耐电晕性(3kv下的寿命): >35600 hr(PP仅为24hr) 耐漏电起痕性能(蚀深度/mm): 0.064(丁基橡胶则为 0.342mm) 爬电性:10~30min(特殊可达 3.5kv/6h) 7 / 7
影响电性能的因素较多,其中主要有;硅橡胶的配方和组成,生产工艺方法的差异,产品的选择型号是否恰当合适,产品的使用条件或环境影响,使用产品时的工艺条件是否与所选产品性能匹配,最终产品的性能与固化是否充分。所以必须针对不同的硅橡胶和使用条件及要求按照以上的影响因素,进行具体分析判定!
3.耐热性(高温) 150℃下,其物理机械性能基本不变,可半永久使用。 &nb