新钢2500m3高炉采用的新技术
沙钢集团2500m3高炉热风炉烘炉方案介绍

沙钢公司 2500m3高炉热风炉烘炉方案1、意义和目的热风炉砌筑完成后,在高炉投产前,对其进行烘炉作业,主要目的是为了脱去耐火砌体的水份,并使其升温,具备向高炉输送热风的能力,为保证烘炉时使水脱尽以及气体在受热膨胀时不影响砌体的稳固,升温过程应迟缓进行,特别对采纳硅砖的热风炉而言,因硅砖内剩余石英的晶体变换过程中,其膨胀系数较大,致使硅砖的强度消弱,若升温不合理,极易破坏砌体,影响到热风炉此后的寿命,所以,对热风炉的烘炉从升温曲线到拟订升温的控制均有严格的要求。
2、烘炉时间确立热风炉烘炉的开始时间宜安排在高炉投产前约50 天,详细时间按沙钢高炉投产计划表履行,热风炉烘炉结束后,如不可以赶快投入生产,将给热风炉的保温工作带来较大困难,所以,在 950℃时可变换为高炉煤气。
3、热风炉的烘炉方案3.1 热风炉本体烘烤采纳逐炉点火烘烤方法进行,(依据烟囱抽力状况定和沙钢高炉投产计划表)。
3.2 热风炉烘烤方法将燃用轻质柴油的内燃式烘炉器备用 3 台,已备煤气不稳准时备用。
备用的燃油系统的设备一定备到现场,如油灌、油泵、鼓风系1统供油系统等。
3.2.4 现场的安装图在判定合同后,依据现场实测绘制完成后供应给甲方。
4、烘炉的必需条件4.1 外头公用设备4.1.1 相关介质管网(包含烘炉用暂时介质管道)所有安装完成并经检查试验合格。
4.1.2 热风炉冷却水系统投入正常运行,水量、水压均达到烘炉所需要求。
4.1.3 各样动力(蒸气、压缩空气、 N2等)保障供应,用量、压力均达到烘炉所需要求。
4.1.4 烘炉用焦炉煤气,压力8Kpa;流量, 3000~4000m3/h。
4.1.5 高炉外头公用设备、各联系系统已经具全。
4.1.6 热风炉地区环境整顿洁净,通道通畅。
4.2 热风炉机械设备4.2.1 热风炉及各工艺管道打压合格。
4.2.2 热风炉系统联动试车完成、PLC 系统调试完成(已经过192 小时联动、正常)。
马钢2500m3高炉喷煤技术的进步

2003年 5月
徽 T RONM AK[ NG
僻
V. I . 22
. 2 S u 0 p p 0 l 3
马钢 2 5 0 0 m 3 高炉喷煤技术的进步
邓新民 汪百友 干 承 孙 泉
( 马鞍 山钢铁股份有 限公 司第 四炼 铁厂J
摘 要 从制粉系统改造, 喷吹系统改造以及高炉操作等方面, 对马钢 2 5 0 0 - 0 高炉喷煤技术的进步
3 . 2 制粉 系统
( 1 ) 两个系列共用 1 个烟气炉。制粉系 统的 2 座烟气炉分别为两个系列提供N度为 1 0 0 0 C 、 烟气量为 I 1 0 0 0 m ' / h的热烟气 混 合 后 的温 度 为 2 0 0 - 3 0 0 C, 流量 为 5 6 0 0 0 m ' / h 。经过技术论证后. 在不改变生 产工艺的情况下, 采取了在两条烟气管道上 增加连通管的方案, 并增加了相应的烟气切
( 3 ) 用N : 作为操作及流化气源。 针对压 缩空气脱水效果差, 含油、 水偏高的实际情 况, 通过改造, 将操作及流化用气改为 N z , 从
而有效地解决 了流化孔板堵塞及换 向阀无法
( 5 ) 配加贫瘦煤 , 采用混合煤喷吹 为了 改善煤粉质量 , 提高制粉出力和煤粉的燃烧 率. 改善喷吹效果, 在无烟煤中配加了贫瘦煤 ( 现最大比例为 3 3 %, 其中贫瘦煤的挥发分 为1 5 叼左右) , 这就要求制粉系统采取相应 的安全措施, 为此我们对制粉系统进行了改 造: 增加了N 保安, 排除系统积粉死角, 操 作L 严格控制混合煤的挥发分和系统各点的
1 0 0 m ' 的储气罐, 同时要求空压站在原有供
气压力为 。 . 5 5 士。 . 0 5 MP a的基础上把压缩 空气压力提 高至 。 . 7 5 上。 . 0 5 MP a , 有效地 解决了正常生产中的系统压力波动问题 < 2 ) 提高煤粉浓度 , 增加喷吹量, 减少压 缩空气消耗, 降低生产成本。 在现有的工艺设
2500高炉初步设计

1 总论1.1 设计依据·《A钢铁有限公司2500m3高炉工程方案设计》—武汉钢铁设计研究总院编制。
(2002年10月)·A钢铁有限公司筹建指挥部与武汉钢铁设计研究总院2002年11月24日的《设计结合会议纪要》。
·《中标通知书》—A钢铁有限公司筹建指挥部。
(2002年11月25日)1.2 建设规模及工程内容本工程按照整体规划,分期实施,最终形成3座现代化大型高炉,生产600万t/a铁水的总目标进行炼铁系统的配套设计。
一期工程:新建1座2500m3高炉,年产铁水量200万t/a。
二期工程:新建1座2500m3高炉,2座高炉年产铁水量400万t/a。
三期工程:新建1座2500m3高炉,3座高炉年产铁水量600万t/a。
1.3 主要设计原则及指导思想1)高炉建设总的指导思想是:“优质、高产、低耗、长寿、环保”。
高炉一代炉龄15年以上,热风炉寿命25年以上。
2)高炉采用“精料、高压、高温、富氧、高喷煤”的冶炼工艺及相关的技术装备。
新建高炉的主要技术经济指标、装备水平达到-1-国内同类高炉的先进水平。
3)认真贯彻执行国家有关政策、法规、规程、规范、标准和行业政策,特别是环保、能源、安全卫生、消防等政策和法规。
4)充分利用北仑卸矿海港优势,建设一座以现代化大型高炉和氧气转炉为主体的冶炼工艺流程,海港与钢厂合一、大船大港大厂为一体,最终规模为550万t/a钢的海洋钢铁厂。
1.4 原燃料条件1.4.1. 烧结矿质量TFe≥58.5%;FeO≤8.0%;转鼓指数≥78%。
1.4.2球团矿质量TFe≥65%;常温耐压强度≥2000N/个球;转鼓指数≥90%。
1.4.3块矿成分(%)TFe≥65%1.4.4 焦炭质量M40≥82%;M10≤7%;灰分≤12%;硫≤0.5%1.4.5 喷吹原煤性能烟煤:灰分≤12%;S≤0.7% ;挥发分≥23%无烟煤:灰分≤12%;S≤0.7%;挥发分≤10%1.4.6 炉料结构分期建设3座2500 m3现代大型高炉,采用适合原料条件的炉料结-2-构:高碱度烧结矿80% + 酸性球团矿10% + 块矿10%,综合矿入炉品位T Fe 60%。
昆钢2500m3高炉泥炮开口机遥控操作实践
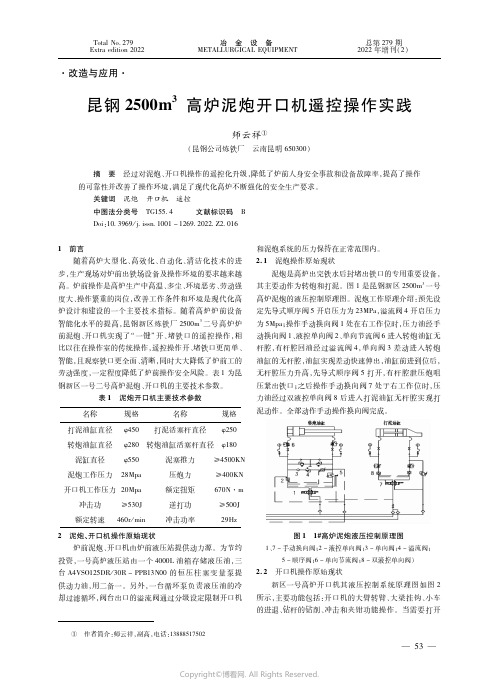
·改造与应用·昆钢2500m3高炉泥炮开口机遥控操作实践师云祥①(昆钢公司炼铁厂 云南昆明650300)摘 要 经过对泥炮、开口机操作的遥控化升级,降低了炉前人身安全事故和设备故障率,提高了操作的可靠性并改善了操作环境,满足了现代化高炉不断强化的安全生产要求。
关键词 泥炮 开口机 遥控中图法分类号 TG155.4 文献标识码 BDoi:10 3969/j issn 1001-1269 2022 Z2 0161 前言随着高炉大型化、高效化、自动化、清洁化技术的进步,生产现场对炉前出铁场设备及操作环境的要求越来越高。
炉前操作是高炉生产中高温、多尘、环境恶劣、劳动强度大、操作繁重的岗位,改善工作条件和环境是现代化高炉设计和建设的一个主要技术指标。
随着高炉炉前设备智能化水平的提高,昆钢新区炼铁厂2500m3二号高炉炉前泥炮、开口机实现了“一键”开、堵铁口的遥控操作,相比以往在操作室的传统操作,遥控操作开、堵铁口更简单、智能,且观察铁口更全面、清晰,同时大大降低了炉前工的劳动强度,一定程度降低了炉前操作安全风险。
表1为昆钢新区一号二号高炉泥炮、开口机的主要技术参数。
表1 泥炮开口机主要技术参数名称规格名称规格打泥油缸直径φ450打泥活塞杆直径φ250转炮油缸直径φ280转炮油缸活塞杆直径φ180泥缸直径φ550泥塞推力≥4500KN泥炮工作压力28Mpa压炮力≥400KN开口机工作压力20Mpa额定扭矩670N·m冲击功≥530J逆打功≥500J额定转速460r/min冲击功率29Hz2 泥炮、开口机操作原始现状炉前泥炮、开口机由炉前液压站提供动力源。
为节约投资,一号高炉液压站由一个4000L油箱存储液压油,三台A4VSO125DR/30R-PPB13N00的恒压柱塞变量泵提供动力油,用二备一。
另外,一台循环泵负责液压油的冷却过滤循环,阀台出口的溢流阀通过分级设定限制开口机和泥炮系统的压力保持在正常范围内。
2500m3高炉鼓风自动拨风工艺改造及应用.pdf

3)" 自动拨风 " 回路一旦接通就自保持 , 只能通
过复位按钮或转换开关才能将其断开 , 如果此时揿 下 " 停止拨风 " 按钮 , 则出现停止拨风和拨风同时动 作现象 ,系统出现混乱 。 因此将停止拨风中间继电器 常闭接点串入拨风控制回路 , 确保 " 停止拨风 " 回路 一接通 ,拨风控制回路立即断开 。
5
效果
自动拨风工艺现已成了马钢 2500 m3 高炉风机
5) 运行机组能力控制器 " 自动转手动 " 信号 。 这
是确保拨风时运行机组 ( 被拨风机组 )静叶稳定的条 件。 只有在以上条件全部满足时 , 拨风装置才能立 即投入运行 。
房生产上的一项重大安全技术保障 , 改造成功后 , 极 大地缓解了高炉风机的保产压力 , 同时也避免了因 风机故障停机而造成高炉断风事故 , 为高炉稳定 、 高 产发挥了重要作用 。 2005 年 8 月 29 日 ,1# 风机由于
3
3.1
改造技术方案
拨风装置的现场设置 在 2# 大高炉建成投产后 , 高炉鼓风站站内供风
管系相应形成了两路母管 (1#、2#), 两台机组通过各 自的两只 DN1400 送 风 阀 门 分 别 与 1#、2# 母 管 相 联 通 , 在正常生产中 , 两台机组分别向两座高炉供风 , 相互隔离 , 互不影响 。 在 1#、2# 母管之间安装一联通 管及一套拨风阀组 , 两只 DN700 电动 蝶 阀 , 一 只
3.2
拨风工艺条件的确定 不可能在任何情况下 , 只要一台机组发生了故
障停机或安全运转 ,拨风装置就能立即投运 。 既要保 证拨风工艺的可靠性 , 同时又要绝对保证风机设备 的安全性 , 这是拨风工艺设计改造工作最为关键的 技术问题 。 为此经过多次探讨和调研 ,确定拨风工艺 条件如下 :
承钢新2500m 3高炉操作优化实践
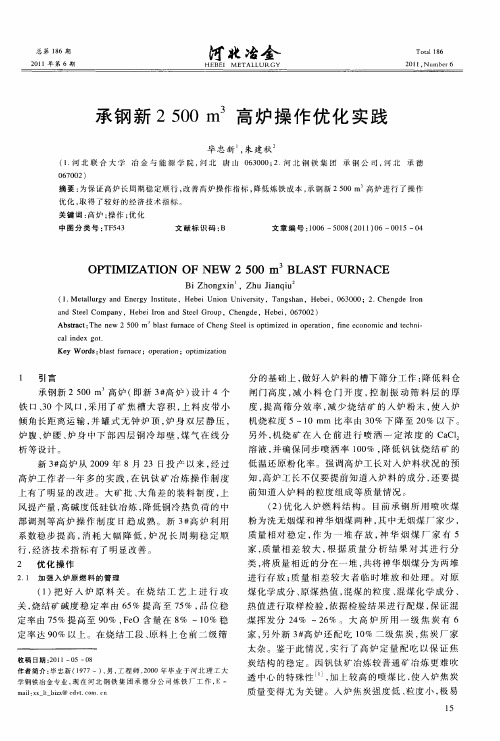
BiZ o g i ,Zh in i J n xn  ̄ u Ja q u
Absr c : e n w 00 m bl s ur a e o e g S e l i pt i e n o r to ta t Th e 2 5 a t f n c f Ch n t e s o i z d i pe a i n,fn c n m i e e o omi n e h i ca d tc n - c li d x go . a n e t Ke o d : l s u na e;o e a i n;o i i a i n y W r s b a tf r c p r to pt z to m
上 有 了 明 显 的改 进 。 大 矿 批 、 角 差 的 装 料 制 度 , 大 上
溶 液 , 确保 同步喷 洒率 10 , 并 0 % 降低 钒钛 烧 结矿 的 低 温还原 粉化率 。强调 高炉工 长对入 炉料状 况 的预 知, 高炉工 长不仅 要提前 知道人 炉料 的成分 , 要 提 还
( . ealry a d E eg n tue 1 M tl g n n ry I s tt ,He e in Unv ri u i b iUno iest y,T n sa a g h n,He e,0 3 0 b i 6 0 0;2. e g eIo Ch n d rn a d Se l mp n n te Co a y,He e Io n te o p,Ch n d ,He e,0 7 0 ) b i rna dSe l Gru eg e b i 6 0 2
煤气干法除尘在宣钢1#2500m3高炉应用实践

煤气干法除尘在宣钢1#2500m3高炉应用实践我国高炉煤气干法除尘目前还处于起步阶段,中小型高炉起步较早,覆盖率至今只有60%左右,并且装备水平不高,运行效果参差不齐,在1000m3以上的大中高炉推广冶只有4~5年的历史,只占该类型高炉的30%左右。
高炉煤气除尘根据除尘工艺的不同分为湿法除尘和干法除尘两大类,传统的煤气除尘系统采用湿法除尘工艺,由重力除尘器塔文(双文)或重力除尘器+环缝除尘器组成。
干法除尘与湿法除尘工艺相比有以下优点:1)节约用水、用电;2)可提高煤气温度80℃左右,用于热风炉燃烧可提高风温40℃;3)提高TRT发电量30%以上;4)除尘效果好,净煤气含量可达到<5mm/m;5)煤气含水少,提高煤气热值。
煤气干法除尘系统在宣钢300m3级小高炉应用了较长时间也有着较为丰富的使用经验,在大高炉上使用干法除尘系统还是首次。
经过3年多的应用实践,逐步完善,干法除尘工艺优势逐渐显现出来,运行中遇到的多种问题,也陆续得以解决。
1宣钢1#高炉煤气干法除尘工艺流程图(见图1)2宣钢1#高炉干法除尘主要技术参数(见表1)3宣钢1#高炉干法除尘系统工艺操作滤袋在过滤状态时,荒煤气进口气动蝶阀及净煤气出口气动蝶阀均打开,随着布袋外壁上的积灰逐渐增多,布袋阻力不断增大,当荒、净煤气主管压差达到4lkPa时,进行反吹。
反吹形式为脉冲反吹,反吹介质为氮气。
当所有布袋反吹完毕后,立即启动机械化除灰系统进行清灰。
每日反吹次数根据实际情况确定,一般情况下反吹10~12次,每次反吹约需15min~20 min。
干法除尘系统主要包括:反吹系统、输灰系统、卸灰系统。
3.1反吹基本情况1号高炉干法除尘共有12个除尘箱体和1个大灰仓,每个箱体都设有17个脉冲阀,每一个脉冲阀控制除尘器内一排滤袋的反吹。
24v直流电接通后第一个脉冲阀启动,脉冲阀工作时间小于0.3s(时间可在上位画面设定),向第一排滤袋喷射氮气,完成一排滤袋的反吹清灰;第一个脉冲阀喷吹后间隔5s~20s(时间可在上位画面设定)第二个脉冲阀动作,直到全部17个脉冲阀动作,完成一个箱体的反吹工作;再自动或手动进行第二个箱体的反吹,直至所有工作箱体完成喷吹。
八钢2500m3B高炉开炉炉料填充

八钢 2500m3 B 高炉开炉炉料填充摘要对八钢2500m3高炉开炉的主要操作经验进行了总结,八钢2500m3高炉采用了串罐物料钟炉顶,联合软水密闭循环冷却,在铁口、炉腹、炉腰及炉身下部采用铜冷却壁,陶瓷杯加水冷炭砖薄炉底炉缸结构,INBA炉渣处理系统、3座旋切顶燃式热风炉、煤气干法布袋除尘等多项技术。
通过开炉前的精心准备,制定合理的开炉方案,选择合适的送风参数,通过合理控制煤气流的分布,顺利实现了炉况快速恢复的目标。
关键词大型高炉开炉达产操作1 概述八钢2500m3B B高炉于2009年2月28日点火投产。
高炉设计有效容积2500m3,本体设计寿命大于15年,热风炉一代寿命大于30年。
高炉高径比Hu/D=2.3175,设30个风口,3个铁口,采用串罐无料钟炉顶装料设备。
在高炉的铁口、炉腹、炉腰及炉身下部采用铜冷却壁,炉喉钢砖采用水冷,使炉体实现100%冷却。
炉体采用软水密闭循环冷却系统,强化冷却。
炉底、炉缸耐材采用炭砖与陶瓷杯结合的结构。
炉底共5 层碳砖,2 层刚玉莫来石陶瓷垫,铁口以上为半石墨碳砖,陶瓷杯壁为刚玉莫来石。
采用储铁式主沟。
采用3 座旋切顶燃式热风炉,设置余热回收系统,预热助燃空气和煤气。
2021年9月份开始长周期检修作业,2022年2月13日开炉。
2 高炉开炉前的准备能够如此快速地实现高炉顺产,与开炉前的各项准备工作充分,组织管理工作到位是分不开的;与设备调试、试运转,把设备存在的问题集中解决在开炉之前,在开炉过程中较少的出现设备故障,确保了开炉过程能按计划顺利进行;尤其是对各种可能出现的设备事故做了充分的处理预案,确保了开炉过程遇到设备事故时沉着应对,平稳过渡,避免了事故的扩大;开炉装料方案和送风方案的确定,为顺利开炉奠定了坚实的基础。
2.1选择优质的开炉原料八钢2500m3B B高炉开炉料成分见表1,焦炭性能见表2。
表1B高炉开炉料成分:表2 B高炉焦炭性能:2.2 填充料方案确定(1)填充料总体上是按照设定方案进行的,高炉物料填充见表3。
- 1、下载文档前请自行甄别文档内容的完整性,平台不提供额外的编辑、内容补充、找答案等附加服务。
- 2、"仅部分预览"的文档,不可在线预览部分如存在完整性等问题,可反馈申请退款(可完整预览的文档不适用该条件!)。
- 3、如文档侵犯您的权益,请联系客服反馈,我们会尽快为您处理(人工客服工作时间:9:00-18:30)。
新钢2500m3高炉采用的新技术
摘要 高炉采用长寿、一罐制、皮带机上料、trt发电、小块焦
回收及矿石混装入炉节能新工艺、焦炭中子测水技术、顶燃式热风
炉、处理采用明特法渣处理技术。
关键词 长寿;一罐制;顶燃式热风炉;明特法渣处理
中图分类号tf54 文献标识码a 文章编号 1674-6708(2011)
37-0189-01
新钢2 500m3高炉是江西省内首座2 500m3级现代化大型高炉,设
计年产生铁能力210万t/座,采用刚性“一罐制”技术、长寿高效
高炉综合技术、带式运输机上料技术、明特法渣处理技术、焦炭中
子测水技术和小块焦回收及矿石混装入炉工艺等一大批国内外先
进技术和工艺,二座高炉开炉以来一直保持着极好的顺稳状态,生
铁产量在受控中稳步提升。目前,二座高炉日产已稳定在6 500t
以上,最高日产达到7 000t,各项主要经济技术指标均达到或好于
设计要求,达到了国内同行的先进水平,其中风温1 230℃以上、
入炉焦比320kg/t以下,双双进入了国内同类型高炉的领先行列。
本文对高炉所应用的新工艺、新技术进行了简要介绍。
1 采用长寿高效高炉综合技术
高炉本着“先进、实用、可靠、经济、环保”的原则,结合现代高
炉炼铁技术的特点,在高炉炉体设计中采用了一系列先进、长寿的
技术,特别是在高炉冷却设备、冷却系统、高炉内衬的选用及各种
检测手段的设计上更加完善、合理,为实现高炉一代炉役(不中修、
不喷补、不更换冷却设备)寿命达到15年,为高炉一代寿命内单
位炉容产铁量大于12 000t创造了条件。
1)冷却设备采用铜冷却壁与铸铁冷却壁结合的全冷却壁设备配置。
在现代高炉普遍采用诸如优质陶瓷杯、微孔炭砖之类的技术使得炉
底、炉缸寿命得以基本解决的情况下,冷却设备寿命直接决定了一
代高炉的寿命。随着砖壁合一、薄壁内衬技术、铜冷却壁技术以及
软水密闭循环冷却技术的应用和发展,全冷却壁的冷却形式已广泛
应用于现代大中型高炉,高炉采用的就是最新的砖壁合一技术,具
有冷却面积大、冷却均匀、维护炉型好、投资省、安装方便等诸多
优点。
2)冷却系统采用联合软水密闭循环冷却系统。高炉所采用的是并
联加串联的方式将3个独立软水系统联合起来形成的联合软水密闭
循环冷却系统,可充分发挥软水不结垢、能适当提高水温差的优点,
从而达到节省投资、减少水量、节约能源的目的,将对高炉冷却壁、
炉底、风口及热风阀等进行冷却保护,系统循环水总量为3 740m3/h,
循环率可达99.95%,较国内其他各种软水密闭循环冷却系统总循
环水量节省45%~50%,投资省18%~20%,运行成本每年节省30%
~50%。
3)高炉内衬采用砖壁合一、薄壁内衬结构。炉底炉缸耐材依照“内
堵外疏”的原则,内侧采用导热性低的陶瓷材料,外侧采用导热性
高的炭质材料;风口区采用刚玉莫来石质大块组合砖砌筑,以加强
结构的稳定性;铁口通道采用大块和小块相结合特殊组合砖结构以
抵抗渣铁侵蚀和冲刷;炉腹及其以上区域采用薄内衬结构。
2 采用刚性”一罐制”技术
“一罐制”也称“一包到底”,是国际钢铁新近发展起来的一种全
新的铁水供应技术,公司新建成的高炉、转炉之间所采用的铁钢生
产“刚性一罐制”工艺,这样,大大提高了生产工序连接效率,保
持了生产节奏的稳定结构,车间布置也更加紧凑,铁钢流程的动态
匹配和有序运行实现了高效化,这在国内冶金行业中尚属首创。该
运行模式使铁水温度提高70℃~80℃,仅此一项,就可为企业每年
节约标煤5万余吨,降低生产成本数千万元。由于铁水温度损失小,
在铁水进炉之前可采用kr搅拌脱硫工艺进行铁水深脱硫处理,为企
业生产高附加值产品,打造三大精品基地提供了先决条件。
3 采用双矩形出铁场
二座高炉均是省内汽车可以直接上出铁场平台的高炉,每座高炉采
用无沙层完全平坦化矩形出铁场,设置南北两个出铁场,北2南1
共三个出铁口,正常情况下,两个铁口轮换出铁,一个备用,且首
次采用了摆动流嘴出铁。各产尘点都有除尘吸风口,环保条件较好。
4 采用带式运输机上料技术
高炉采用高强度带式运输机上料,不设集中转运站,避免二次粉碎,
同时节省投资。其主要优点有3点:1)上料能力大,上料能力每
小时达2 700t,且具有连续性,可充分满足大型高炉的供料要求;
2)可将原燃料系统布置在距高炉较远的地区,为高炉车间合理布
置创造了条件;3)简化炉顶装置,设备维修简便。
5 采用干式trt发电技术
高炉率先将干式trt发电技术应用于2 500m3级大型高炉。高炉煤
气余压发电装置是通过高炉冶炼的副产品,高炉所采用的bdc干法
除尘净化工艺大大提高了透平入口煤气温度,使透平功率比湿式除
尘系统高30%~50%,同时节约耗电量60%~70%。
6 采用小块焦回收及矿石混装入炉节能新工艺
将焦槽槽下焦炭筛筛除物中10mm~25mm的小块焦回收,与矿石混装
入炉,具有良好的冶炼效果,约一年左右即可收回该系统的投资,
环境和经济效益明显。
7 采用焦炭中子测水技术
高炉引进并采用了焦炭中子测水技术测定高炉入炉焦炭水分,测量
准确及时,并能将测定结果传输到高炉计算机控制系统,实现焦炭
水分自动补偿。
8 采用顶燃式热风炉
高炉热风炉采用的是当前最为先进的顶燃式热风炉,其结构简单、
占地面积少,风温水平高,利用废气余热预热煤气和助燃空气可使
煤气完全燃烧,能节省大量风和煤气,又可使风温最高提升到1
250℃,一年就可收回1.4亿元的投资成本。
9 渣处理采用明特法渣处理技术
该技术装备具有投资小、占地面积小、脱水效率高、水渣处理能力
大,而且同时节省了生产成本、安全环保、寿命长等特点。生产出
的高炉水渣粒度均匀、脱水效果好、玻璃化程度高,是生产水泥、
渣砖、轻质混凝土砌块或凝石等建材产品的优质原料。另外该工艺
还具有环保节水的优点,循环水利用率可达到80%以上。