首钢京唐1号高炉铁水含硫高的分析
首钢京唐介绍
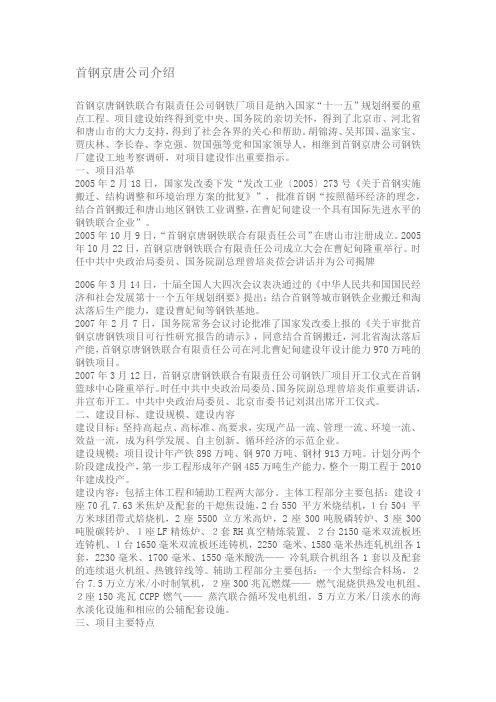
首钢京唐公司介绍首钢京唐钢铁联合有限责任公司钢铁厂项目是纳入国家“十一五”规划纲要的重点工程。
项目建设始终得到党中央、国务院的亲切关怀,得到了北京市、河北省和唐山市的大力支持,得到了社会各界的关心和帮助。
胡锦涛、吴邦国、温家宝、贾庆林、李长春、李克强、贺国强等党和国家领导人,相继到首钢京唐公司钢铁厂建设工地考察调研,对项目建设作出重要指示。
一、项目沿革2005年2月18日,国家发改委下发“发改工业〔2005〕273号《关于首钢实施搬迁、结构调整和环境治理方案的批复》”,批准首钢“按照循环经济的理念,结合首钢搬迁和唐山地区钢铁工业调整,在曹妃甸建设一个具有国际先进水平的钢铁联合企业”。
2005年10月9日,“首钢京唐钢铁联合有限责任公司”在唐山市注册成立。
2005年l0月22日,首钢京唐钢铁联合有限责任公司成立大会在曹妃甸隆重举行。
时任中共中央政治局委员、国务院副总理曾培炎莅会讲话并为公司揭牌2006年3月14日,十届全国人大四次会议表决通过的《中华人民共和国国民经济和社会发展第十一个五年规划纲要》提出:结合首钢等城市钢铁企业搬迁和淘汰落后生产能力,建设曹妃甸等钢铁基地。
2007年2月7日,国务院常务会议讨论批准了国家发改委上报的《关于审批首钢京唐钢铁项目可行性研究报告的请示》,同意结合首钢搬迁,河北省淘汰落后产能,首钢京唐钢铁联合有限责任公司在河北曹妃甸建设年设计能力970万吨的钢铁项目。
2007年3月12日,首钢京唐钢铁联合有限责任公司钢铁厂项目开工仪式在首钢篮球中心隆重举行。
时任中共中央政治局委员、国务院副总理曾培炎作重要讲话,并宣布开工。
中共中央政治局委员、北京市委书记刘淇出席开工仪式。
二、建设目标、建设规模、建设内容建设目标:坚持高起点、高标准、高要求,实现产品一流、管理一流、环境一流、效益一流,成为科学发展、自主创新、循环经济的示范企业。
建设规模:项目设计年产铁898万吨、钢970万吨、钢材913万吨。
首钢京唐特大型高炉料仓和无中继站上料系统
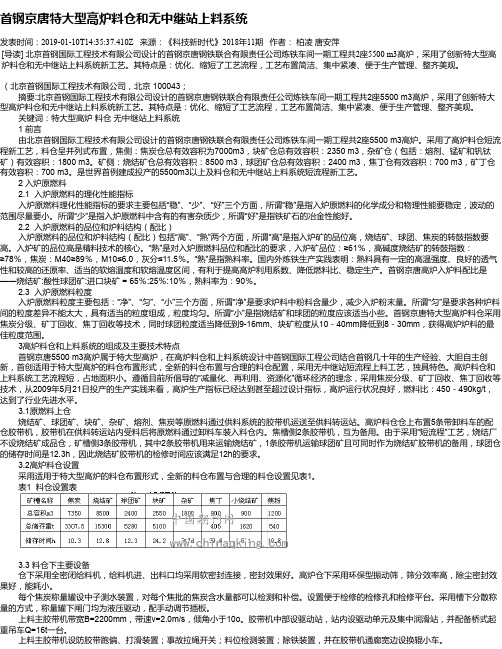
首钢京唐特大型高炉料仓和无中继站上料系统发表时间:2019-01-10T14:35:37.410Z 来源:《科技新时代》2018年11期作者:柏凌唐安萍[导读] 北京首钢国际工程技术有限公司设计的首钢京唐钢铁联合有限责任公司炼铁车间一期工程共2座5500 m3高炉,采用了创新特大型高炉料仓和无中继站上料系统新工艺。
其特点是:优化、缩短了工艺流程,工艺布置简洁、集中紧凑、便于生产管理、整齐美观。
(北京首钢国际工程技术有限公司,北京 100043;摘要:北京首钢国际工程技术有限公司设计的首钢京唐钢铁联合有限责任公司炼铁车间一期工程共2座5500 m3高炉,采用了创新特大型高炉料仓和无中继站上料系统新工艺。
其特点是:优化、缩短了工艺流程,工艺布置简洁、集中紧凑、便于生产管理、整齐美观。
关键词:特大型高炉料仓无中继站上料系统1 前言由北京首钢国际工程技术有限公司设计的首钢京唐钢铁联合有限责任公司炼铁车间一期工程共2座5500 m3高炉。
采用了高炉料仓短流程新工艺,料仓呈并列式布置,焦侧:焦炭仓总有效容积为7000m3,块矿仓总有效容积:2350 m3,杂矿仓(包括:熔剂、锰矿和钒钛矿)有效容积:1800 m3。
矿侧:烧结矿仓总有效容积:8500 m3,球团矿仓总有效容积:2400 m3,焦丁仓有效容积:700 m3,矿丁仓有效容积:700 m3。
是世界首例建成投产的5500m3以上及料仓和无中继站上料系统短流程新工艺。
2 入炉原燃料2.1 入炉原燃料的理化性能指标入炉原燃料理化性能指标的要求主要包括“稳”、“少”、“好”三个方面,所谓“稳”是指入炉原燃料的化学成分和物理性能要稳定,波动的范围尽量要小。
所谓“少”是指入炉原燃料中含有的有害杂质少,所谓“好”是指铁矿石的冶金性能好。
2.2 入炉原燃料的品位和炉料结构(配比)入炉原燃料的品位和炉料结构(配比)包括“高”、“熟”两个方面,所谓“高”是指入炉矿的品位高,烧结矿、球团、焦炭的转鼓指数要高。
高炉铁水有害元素分析与控制
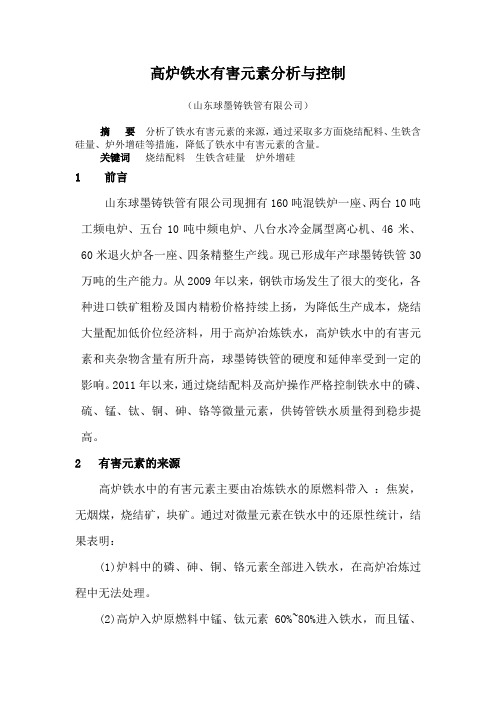
高炉铁水有害元素分析与控制(山东球墨铸铁管有限公司)摘要分析了铁水有害元素的来源,通过采取多方面烧结配料、生铁含硅量、炉外增硅等措施,降低了铁水中有害元素的含量。
关键词烧结配料生铁含硅量炉外增硅1 前言山东球墨铸铁管有限公司现拥有160吨混铁炉一座、两台10吨工频电炉、五台10吨中频电炉、八台水冷金属型离心机、46米、60米退火炉各一座、四条精整生产线。
现已形成年产球墨铸铁管30万吨的生产能力。
从2009年以来,钢铁市场发生了很大的变化,各种进口铁矿粗粉及国内精粉价格持续上扬,为降低生产成本,烧结大量配加低价位经济料,用于高炉冶炼铁水,高炉铁水中的有害元素和夹杂物含量有所升高,球墨铸铁管的硬度和延伸率受到一定的影响。
2011年以来,通过烧结配料及高炉操作严格控制铁水中的磷、硫、锰、钛、铜、砷、铬等微量元素,供铸管铁水质量得到稳步提高。
2 有害元素的来源高炉铁水中的有害元素主要由冶炼铁水的原燃料带入:焦炭,无烟煤,烧结矿,块矿。
通过对微量元素在铁水中的还原性统计,结果表明:(1)炉料中的磷、砷、铜、铬元素全部进入铁水,在高炉冶炼过程中无法处理。
(2)高炉入炉原燃料中锰、钛元素60%~80%进入铁水,而且锰、钛元素在铁水中含量与高炉铁水含硅量呈正相关性关系。
原始生铁含硅量的提高有助于有害元素含量的升高。
3 不同元素对铸铁管的危害供铸管铁水中一些元素达到一定值会对铸铁管的退火产生一定的影响,进而降低对铸铁管的产品质量:磷是铸铁中的常存元素,它对球墨铸铁的机械性能,尤其是冲击韧性和塑性有明显的不良影响,因此总是作为有害元素对待。
其主要原因是共晶团晶界产生的磷共晶脆相,磷共晶呈多角状分布于共晶团边界,急剧恶化球墨铸铁的力学性能,使球墨铸铁韧性下降;其次是磷阻碍珠光体的分解,又能固溶于铁素体中,这些都能降低韧性。
磷的质量分数每增加0.01%时,脆性转变温度升高4.0~4.5℃。
当磷的质量分数超过0.16%时,脆性转变温度已在室温以上,冲击断口出现脆性断裂。
钢铁冶炼中的高硫铁矿熔炼技术

钢铁冶炼中的高硫铁矿熔炼技术随着钢铁工业的不断发展,矿石资源的质量也越来越受到关注。
高硫铁矿通常是指硫含量在1-2%以上的矿石,在钢铁冶炼中使用率逐渐提高。
但是,高硫铁矿熔炼技术却是一个研究热点和难点。
高硫铁矿在熔炼过程中会产生大量的硫化物,其中的二氧化硫是造成环境污染的主要因素之一。
因此,如何有效地降低高硫铁矿在钢铁冶炼中的使用成本、提高回收率、降低污染是研究人员需要解决的问题。
目前,高硫铁矿熔炼技术一般采用焙烧还原、热还原、湿法冶金等方法。
其中,焙烧还原是最常用的方法。
该方法是指将高硫铁矿在高温和含氧气氛下进行热解(焙烧),使其产生一定的金属硫化物和熔渣,然后在还原条件下还原出金属。
这种方法具有工艺简单、操作容易等优点。
但同时,还存在硫化物回收效率低的问题,部分硫酸盐会被热分解,从而造成中毒和污染物排放。
热还原法是一种新型的高硫铁矿熔炼技术。
该方法是将高硫铁矿和还原剂一起熔炼,使其在高温还原条件下实现高硫铁矿硫还原成元素硫。
与焙烧还原法相比,该方法不需要对矿石进行热解,可以节约大量的能源,同时由于直接还原硫是一种“干燥”过程,因此不会出现硫酸盐分解的问题,也不会造成硫化氢中毒。
该方法还具有精细控制熔炼条件、节能、污染物排放较少等优点,但需要使用高铝砖和高级斜拉炉等特殊设备,其成本也较高。
湿法冶金在高硫铁矿熔炼中也有一定应用。
该方法是指以水或其他溶剂为介质,在氧气等气体存在下,将高硫铁矿进行还原反应,将硫溶解在水中或其他溶剂中,并转化为含有一定氧化性的化学物质。
该方法具有高硫铁矿还原率高、污染物排放少、回收硫酸盐、硫化物全都比较充分等优点。
但与其他方法相比,湿法冶金的能耗较高,设备、占地面积和建造成本等都比较大。
综上所述,钢铁冶炼中高硫铁矿熔炼技术的研究和应用是一个不断探索的领域。
各种方法都各有利弊,如何切实降低矿石的成本、提高其回收率、控制熔炼污染是需要研究者不断探索和解决的问题。
炼铁过程延迟硫磺析出技术

探索与其他节能减排技术的结合,进一步降低炼铁过程中的能耗和污 染物排放。
04
关注国际上相关技术的发展动态,积极引进先进技术,提高我国钢铁 行业的国际竞争力。
THANKS
感谢观看
实验设计和方法
实验材料
采用高硫铁矿和低硫铁矿 作为原料,通过不同的炼 铁工艺进行实验。
实验设备
采用高炉、转炉等炼铁设 备,模拟实际炼铁过程。
实验方法
对比不同炼铁工艺下硫磺 的析出规律,分析不同因 素对硫磺析出的影响。
实验结果和数据分析
实验结果表明,采用适当的炼铁工艺可以有效地延迟硫磺的析出,降低高炉渣中 的硫含量。
XX矿业公司
通过优化原料配比和反应条件,有效控制了硫磺的析出,降低了生铁中的硫含量,提高了生铁的合格 率。
技术推广和未来发展
1 2
推广应用
随着环保要求的提高和产品质量标准的提升,延 迟硫磺析出技术将在更多钢铁企业得到推广和应 用。
技术创新
未来将进一步研究炼铁过程中硫磺析出的机制, 探索更有效的延迟硫磺析出技术和方法。
技术优势和局限性
技术实施成本较高,需要投入大量资金和人力。
需要进一步研究不同原料和工艺条件下的应用效果。
对未来研究的建议和展望
01
深入研究不同原料和工艺条件下硫磺析出的规律和机制,为优化技术 提供理论支持。
02
加强与其他钢铁企业的合作,推广应用延迟硫磺析出技术,提高整个 行业的环保水平和产品质量。
02
高硫含量的铁水会导致钢材脆化 、热加工性能变差,对后续的轧 制和锻造过程产生不利影响。
硫磺析出问题的严重性
硫磺析出会导致高炉结瘤,影响高炉 的正常运行,甚至引发安全事故。
硫磺的大量析出还会增加炼铁过程的 能耗和生产成本,降低企业的经济效 益。
准确获取铁水中硫含量的方法
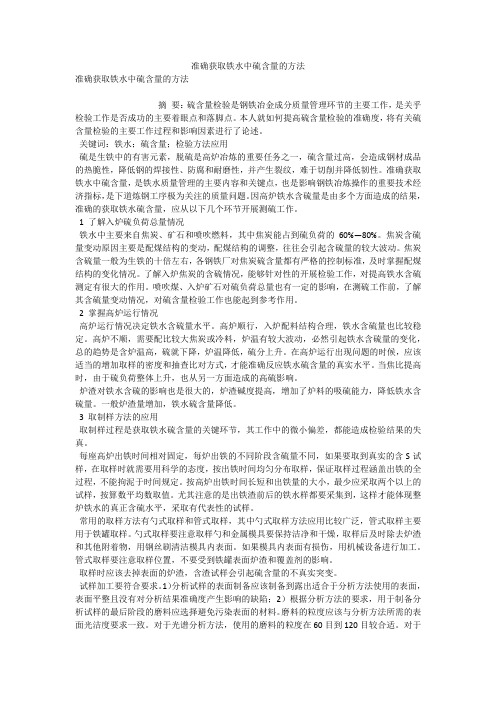
准确获取铁水中硫含量的方法准确获取铁水中硫含量的方法摘要:硫含量检验是钢铁冶金成分质量管理环节的主要工作,是关乎检验工作是否成功的主要着眼点和落脚点。
本人就如何提高硫含量检验的准确度,将有关硫含量检验的主要工作过程和影响因素进行了论述。
关键词:铁水;硫含量;检验方法应用硫是生铁中的有害元素,脱硫是高炉冶炼的重要任务之一,硫含量过高,会造成钢材成品的热脆性,降低钢的焊接性、防腐和耐磨性,并产生裂纹,难于切削并降低韧性。
准确获取铁水中硫含量,是铁水质量管理的主要内容和关键点,也是影响钢铁冶炼操作的重要技术经济指标,是下道炼钢工序极为关注的质量问题。
因高炉铁水含硫量是由多个方面造成的结果,准确的获取铁水硫含量,应从以下几个环节开展测硫工作。
1 了解入炉硫负荷总量情况铁水中主要来自焦炭、矿石和喷吹燃料,其中焦炭能占到硫负荷的60%―80%。
焦炭含硫量变动原因主要是配煤结构的变动,配煤结构的调整,往往会引起含硫量的较大波动。
焦炭含硫量一般为生铁的十倍左右,各钢铁厂对焦炭硫含量都有严格的控制标准,及时掌握配煤结构的变化情况。
了解入炉焦炭的含硫情况,能够针对性的开展检验工作,对提高铁水含硫测定有很大的作用。
喷吹煤、入炉矿石对硫负荷总量也有一定的影响,在测硫工作前,了解其含硫量变动情况,对硫含量检验工作也能起到参考作用。
2 掌握高炉运行情况高炉运行情况决定铁水含硫量水平。
高炉顺行,入炉配料结构合理,铁水含硫量也比较稳定。
高炉不顺,需要配比较大焦炭或冷料,炉温有较大波动,必然引起铁水含硫量的变化,总的趋势是含炉温高,硫就下降,炉温降低,硫分上升。
在高炉运行出现问题的时候,应该适当的增加取样的密度和抽查比对方式,才能准确反应铁水硫含量的真实水平。
当焦比提高时,由于硫负荷整体上升,也从另一方面造成的高硫影响。
炉渣对铁水含硫的影响也是很大的,炉渣碱度提高,增加了炉料的吸硫能力,降低铁水含硫量。
一般炉渣量增加,铁水硫含量降低。
首钢京唐公司高炉有害元素分布与控制

首钢京唐公司高炉有害元素分布与控制I. 导论A. 研究背景与意义B. 研究目的与方法C. 文章结构II. 高炉焦炭中有害元素分布与控制A. 高炉焦炭中的有害元素含量及来源B. 高炉焦炭中有害元素的影响C. 高炉焦炭中有害元素控制的方法III. 铁矿石中有害元素分布与控制A. 铁矿石中的有害元素含量及来源B. 铁矿石中有害元素的影响C. 铁矿石中有害元素控制的方法IV. 高炉渣中有害元素分布与控制A. 高炉渣中的有害元素含量及来源B. 高炉渣中有害元素的影响C. 高炉渣中有害元素控制的方法V. 高炉烟气中有害元素分布与控制A. 高炉烟气中的有害元素含量及来源B. 高炉烟气中有害元素的影响C. 高炉烟气中有害元素控制的方法VI. 结论与展望A. 结论总结B. 下一步研究方向注:此提纲仅供参考,可以根据具体情况进行修改和完善。
I.导论A. 研究背景与意义高炉是钢铁生产的核心设备,不仅直接决定钢铁生产的效益和质量,也是造成环境污染的主要来源之一。
高炉生产过程中会产生大量有害元素,如重金属、多环芳烃、氮氧化物等,对环境和人体健康造成不同程度的影响。
因此,研究高炉有害元素分布与控制对于保障工人健康、减少环境污染、提高钢铁生产效益具有重要意义。
首钢京唐公司是中国钢铁行业的重要生产基地,拥有世界一流的高炉设备和先进的环境治理技术。
本文以首钢京唐公司高炉为研究对象,系统研究高炉中有害元素的分布规律和控制方法,旨在为其他钢铁企业提供参考和借鉴,为环保事业做出贡献。
B. 研究目的与方法本文旨在研究首钢京唐公司高炉中有害元素的分布规律和控制方法,具体包括高炉焦炭、铁矿石、高炉渣和烟气等四个方面。
通过对高炉生产中这四个环节的样品采集和分析,研究有害元素在高炉各个环节中的分布规律及其来源,并提出相应的控制方法和技术措施。
本文采用实地调研与采样、原位分析、实验室分析和文献资料分析等方法,将采集的样品进行多种单一和综合的物理、化学和生物学分析,得出高炉中有害元素的分布规律和控制方法。
现代大型高炉工艺特点
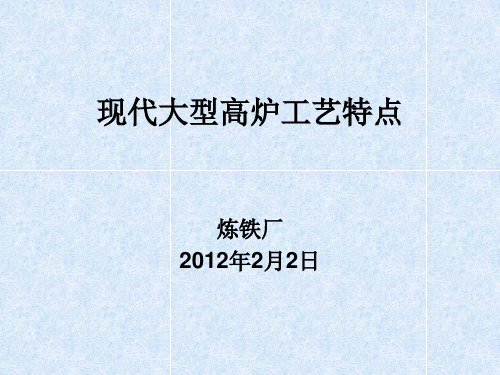
首钢京唐公司1号高炉采用成熟的水冷气封并罐式 首钢京唐公司 号高炉采用成熟的水冷气封并罐式 无料钟炉顶设备,实现了布料调剂的灵活性。 无料钟炉顶设备,实现了布料调剂的灵活性。在 炉顶设置了2个容积为 个容积为80m3料罐,炉顶压力设计 料罐, 炉顶设置了 个容积为 料罐 值为0.28MPa。 值为 。 4、综合鼓风系统 、 首钢京唐公司1号高炉和在建的 号高炉共配备了3 号高炉和在建的2号高炉共配备了 首钢京唐公司 号高炉和在建的 号高炉共配备了 台全静叶可调轴流式鼓风机(2用1备),最大风 台全静叶可调轴流式鼓风机(2用1备),最大风 量为9300m3/min,最大风压为 量为 ,最大风压为0.55MPa,并配 , 备脱湿装置。冷风管道设有富氧系统和加湿系统, 备脱湿装置。冷风管道设有富氧系统和加湿系统, 富氧率设计值为3.5%。 富氧率设计值为 。 5、热风系统高风温长寿 、 首钢京唐公司高炉配套建设有四座BSK顶燃式热 首钢京唐公司高炉配套建设有四座 顶燃式热 风炉和两座预热炉,预热炉是小型化的热风炉。 风炉和两座预热炉,预热炉是小型化的热风炉。
6)出铁场系统:2个宽敞明亮的、无填沙层、完 )出铁场系统: 个宽敞明亮的、无填沙层、 个宽敞明亮的 全平坦的矩形出铁场,设置3个铁口 个铁口, 个出铁场 全平坦的矩形出铁场,设置 个铁口,2个出铁场 下共设置6条铁路线 宽敞的风口平台, 条铁路线, 下共设置 条铁路线,宽敞的风口平台,设置了 上出铁场和上风口平台的通道,引进TMT液压泥 上出铁场和上风口平台的通道,引进 液压泥 炮和液压开口机,悬挂式国产液压揭盖机, 炮和液压开口机,悬挂式国产液压揭盖机,新型 结构的电动备手动的摆动流槽, 结构的电动备手动的摆动流槽,完善的通风除尘 设施。 设施。 7)铁水运输:沙钢 ×2500m3高炉,在国内最先 高炉, )铁水运输:沙钢2× 采用了一罐到底的技术,本高炉仍然采用180t铁 采用了一罐到底的技术,本高炉仍然采用 铁 水包的一罐到底的铁水运输技术, 水包的一罐到底的铁水运输技术,出铁场下铁水 包称量精度达到± 。 包称量精度达到±1t。 8)渣处理系统:采用新型全国产环保转鼓渣处理 )渣处理系统: 系统,2套双驱动转筒式水渣过滤装置,改进型 系统, 套双驱动转筒式水渣过滤装置, 套双驱动转筒式水渣过滤装置 冷凝塔,完善的供回水管路系统。 冷凝塔,完善的供回水管路系统。
- 1、下载文档前请自行甄别文档内容的完整性,平台不提供额外的编辑、内容补充、找答案等附加服务。
- 2、"仅部分预览"的文档,不可在线预览部分如存在完整性等问题,可反馈申请退款(可完整预览的文档不适用该条件!)。
- 3、如文档侵犯您的权益,请联系客服反馈,我们会尽快为您处理(人工客服工作时间:9:00-18:30)。
冶金之家网站 首钢京唐1号高炉铁水含硫高的分析 曹锋,霍吉祥 (首钢京唐钢铁联合有限责任公司炼铁部,河北 唐山 063200) 摘 要:从原燃料质量、炉渣成分、炉缸状态、炉况稳定性等方面,对首钢京唐1号高炉铁水含硫高进行了分析,原燃料质量恶化是铁水含硫高的重要原因,渣铁温度偏低、炉缸活性较差、炉况波动是铁水含硫高的主要原因,在改善原燃料质量的基础上,优化造渣制度,活跃炉缸,稳定煤气流,可降低铁水含硫。 关 键 词:高炉;铁水;硫;分析 首钢京唐公司产品定位于生产高端精品钢,对铁水质量有较高的要求。2011年以来,首钢京唐1号高炉铁水含硫有较大幅度的上升,对炼钢工序的脱硫作业带来一定的困难,分析导致铁水含硫升高原因,对稳定降低铁水含硫量、提高铁水质量、满足下道工序要求有重要意义。 1 概述 首钢京唐公司1号高炉容积为5500m3,年产铁水近450万t。近1a来,首钢京唐1号高炉所产铁水含硫情况见表1。首钢京唐1号高炉所用原燃料为自产高碱度烧结矿、自产酸性球团矿、澳块矿、自产干熄焦和主要由阳泉煤、潞安煤、焦作煤、神华煤按比例混合而成的喷吹煤。表2为首钢京唐1号高炉所用原燃料的含硫量情况,表3为首钢京唐1号高炉冶炼1t铁水由炉料带入的硫量。
2 铁水含硫上升的原因 2.1 原燃料质量恶化 铁水中的硫来源于入炉料,炉料含硫的升高,势必会导致(同样脱硫能力情况下)铁水含硫的上升。近年来,首钢京唐1号高炉入炉原燃料的含硫都趋于上升趋势。从表3可看出,烧结矿和燃料带入的硫占入炉炉料带入总硫的98%以上,其中入炉焦炭带入的硫占入炉总硫量的78%以上,是硫的主要来源,故焦炭含硫对铁水含硫影响较大。焦炭带入的硫增加,会明显增加铁水含硫量。表4为焦炭、煤粉的含硫变化情况。此外,焦炭灰分高且波动大,矿料成分波动频繁且趋坏,引起热制度、造渣制度的波动,在一定程度上也导致了铁水含硫上升,总的来说,原燃料质量的整体恶化,是首钢京唐高炉铁水含硫升高的重要原因。 冶金之家网站 2.2 炉渣对铁水含硫的影响 在原燃料含硫高的条件下,炉渣脱硫能力是直接影响铁水质量的重要因素之一。脱硫反应是在液态渣铁间界面处进行离子迁移的过程,即在铁水中呈中性的硫原子,在渣铁界面处吸收熔渣中的电子变成硫负离子进入炉渣,炉渣中的氧负离子在界面处失去电子变成中性的原子进入铁水,然后与铁水中的碳化合生成一氧化碳排出。影响高炉炉渣脱硫能力的因素很多,炉渣的成分和温度对铁水脱硫有着重要的影响。 适宜的炉渣碱度(ω(CaO)/ω(SiO2))是保证炉渣脱硫的最主要条件,炉渣碱度过低或过高都会引起其流动性变差,导致Ls值降低,对脱硫不利。首钢京唐1号高炉的入炉炉料碱度虽有波动,但通过日常操作调整,保证了渣碱度的相对稳定,表5为近1 a来首钢京唐1号高炉的炉渣成分。
合适的渣中MgO质量分数,可降低炉渣的熔化温度和黏度,改善渣的流动性、稳定性,能加速反应产物CaS的扩散,使脱硫反应加快进行。文献指出[1-11],随着渣中MgO质量分数的增加,炉渣黏度下降,流动性改善,稳定性提高,利于炉渣脱硫。这是因为增加渣中MgO质量分数的比率,可以带入较多的O2-离子,因而减少了Si-O,Al-O阴离子团的聚合度,破坏了它们的网状结构,形成了简单的单、双四面体结构;同时还能与Al2O3生成一系列低熔点物质,改善炉渣的流动性。而CaO-SiO2-Al2O3-MgO四元系等温线-初晶区相图也反映出,渣中MgO可有效地扩大渣相中黄长石(2CaO·MgO·2SiO2)区,在该区域内,熔化温度较低,等温线分布较稀疏,炉渣的热稳定性和化学稳定性好。但渣中MgO不应大于13%,一般来说,较为适宜的渣中MgO质量分数为9%~12%。目前首钢京唐1号高炉渣中MgO平均质量分数为7.33%,渣中MgO质量分数偏低,脱硫效果差。 随着炉渣中Al2O3质量分数升高[6-13],炉渣的黏度和熔化性温度均提高,炉渣的流动性变差,脱硫能力降低,铁水硫质量分数将明显升高。炉渣中的Al2O3质量分数提高后,炉渣中的(AlO4)5-离子团数量有所增加,同时炉渣中高熔点的复杂化合物也容易形成,炉渣的内 冶金之家网站 部结构呈现复杂化,从而使炉渣的黏度和熔化性温度提高,恶化了炉渣脱硫反应的动力学条件。另一方面炉渣中的Al2O3会吸收炉渣中的自由氧离子,降低炉渣中CaO和MgO的活度,从而降低了炉渣脱硫能力。为使炉渣获得较好的脱硫能力,通常应控制炉渣中Al2O3的质量分数不超过15%。 虽然Al2O3质量分数上升导致炉渣熔化性温度、黏度上升,但MgO质量分数增加对炉渣熔化性23温度、黏度上升起着明显的缓解作用。在炉渣温度较高时,Al2O3质量分数对炉渣黏度影响较大;随温度下降,炉渣黏度增大时,MgO缓解黏度增大的作用比Al2O3对炉渣的影响要大。而对于Al2O3质量分数比较高的炉渣,其MgO质量分数也不宜控制太高,原因是在高Al2O3的炉渣中,当MgO质量分数增至13%以上时,MgO和Al2O3容易形成一些高熔点的化合物,炉渣中会出现难溶的尖晶石(MgO·Al2O3)和方镁石(MgO)等高熔点物质,炉渣的黏度、熔化性温度都将大幅度提高,流动性变差,从而严重恶化了脱硫反应的动力学条件。常规四元渣系中,控制MgO质量分数在9%~12%,Al2O3质量分数不大于15%是较为适宜的。在MgO平均质量分数为7.33%条件下,首钢京唐1号高炉渣中的Al2O3偏高(见表5),对铁水脱硫不利。 炉渣中FeO增加,不仅增加了炉缸内直接还原热量的消耗,而且会促使更多的S—与Fe++结合进入铁水,对脱硫反应是十分不利的。目前首钢京唐1号高炉渣中FeO质量分数平均在0.51%左右,最高达1.24%,渣中FeO质量分数偏高,使铁水含硫增加。 炉缸热量不足,渣温低,不利于反应向脱硫方向进行,炉渣黏度大、流动性差,也影响硫从铁水向炉渣的扩散速度,在同一碱度下,硫分配系数Ls降低,炉渣脱硫能力不足。图1为首钢京唐1号高炉近1a来的铁水温度与硫分配系数Ls相关关系曲线。由图可见,硫分配系数与铁水温度有较强的相关性,铁水温度高时,脱硫效果好些。生产实践表明,首钢京唐高炉渣铁温度在1500℃以上时,炉渣脱硫效果较好。1号高炉的铁温略显偏低,不利于降低铁水含硫。
2.3 炉缸工作对铁水含硫的影响 当炉缸堆积时,尽管炉温不低,由于炉渣不能在炉缸内自由流动,脱硫效果不好,从而降低炉渣的脱硫能力。2011年1号高炉计划和非计划停风次数较多,高炉长期休、慢风,引起了炉缸堆积,使炉缸在较长一段时间内处于不活跃状态,炉缸工作性能变差,使脱硫效率大大降低,铁水含硫上升。炉缸活性差,渣中FeO不能被充分还原,也导致了渣中FeO高,影响炉渣的脱硫效果。 经过治理,炉缸的活性有阶段性的改善,图2为首钢京唐1号高炉近年来的炉芯温度。但炉缸活性、均匀性仍显欠缺,热制度极不稳定,炉缸温度不均匀,渣铁温度偏低且波动大,引起铁水含硫升高。图3为1号高炉2012年3个月的铁温日统计曲线。 冶金之家网站 2.4 炉况波动 1a多来,首钢京唐1号高炉的技术经济指标取得了巨大的进步,但由于对大高炉的冶炼技术还需要一个逐步摸索的认识过程,炉况的稳定性有待进一步提高,特别是前期的治理恢复过程中,炉况稳定性差,渣皮脱落频繁,冷却壁水温差变化大,煤气流的稳定性差,易发生管道行程,在一定程度上也导致了铁水含硫较高。图4为1号高炉冷却壁水温差波动情况,图5为1号高炉煤气利用率情况。 冶金之家网站 3 结语 1)炼铁原燃料含硫高、渣铁温度偏低、炉缸活跃程度差、煤气流稳定性差、渣皮脱落频繁是首钢京唐1号高炉铁水含硫高的原因。 2)在目前原燃料含硫量较高条件下冶炼,可通过适当提高炉温,稳定炉温,促进炉缸工作均匀活跃,进一步提升炉况的顺行稳定程度,提高炉渣的脱硫能力,来改善铁水质量。 参 考 文 献: [1] 何环宇.MgO含量对高炉渣黏度影响的实验研究[J].武汉科技大学学报:自然科学版,2002,25(4):340. [2] 何环宇,王庆祥,韩秋影.MgO含量对高炉渣性能的影响研究[J].武汉科技大学学报:自然科学版,2006,29(1):5. [3] 郭志刚.三安高炉高Al2O3炉渣冶炼实践[J].炼铁,2006,25(2):24. [4] 谢振华,丁毅.新钢一铁厂高炉铁水一级品率攻关实践[J].炼铁技术通讯,2008(1):10. [5] 马利科,何红斌.降低铁水含硫量途径的探讨[J].炼铁技术通讯,2001(5):2. [6] 安为杰,胡宾生.马钢2500m3高炉渣的冶金性能[J].华东冶金学院学报,1998,15(1):11. [7] 李贵阳,魏志江,胡滨生.宣钢高炉炉渣脱硫能力的研究[J].炼铁技术通讯,2006(11):5. [8] 郁庆瑶,张龙来,林成城.高炉渣流动性的实验研究[J].宝钢技术,2002(3):37. [9] 杨金福.济钢高炉炉渣性能的研究与应用[J].中国冶金,2006,16(5):14. [10] 俞晓林.降低铁水中硫的实践[J].中国冶金,2007,17(11):21. [11] 王再义,刘德军,张伟,等.鞍钢高炉炉渣黏度的研究与优化[J].中国冶金,2009,19(10):40. [12] 李福民,吕庆,胡宾生,等.高炉渣的冶金性及造渣制度[J].钢铁,2006,41(4):20.[13]吴长生,李玉华,邱金龙,等.梅钢高炉渣流动性能的实验研究[J].冶金丛刊,2009(5):1.