拨叉夹具设计
CA6140车床拨叉(831006)夹具设计

课程设计报告题目CA6140车床拨叉(831006)夹具设计课程名称机制工艺课程设计目录序言 (2)第1章零件的工艺分析及生产类型的确定 (3)1.1零件的作用 (3)1。
2拨叉的技术要求 (3)1。
3零件的工艺性分析和零件图的审查 (4)1.4确定拨叉的生产类型 (4)第2章选择毛坯,确定毛坯尺寸,设计毛坯图 (5)2。
1 确定毛坯的成形方法 (5)2.2 铸件结构工艺性分析和铸造工艺方案的确定 (6)第3章选择加工方法,制定工艺路线 (7)3.1定位基准的选择 (7)3。
2各表面加工方案的选择 (7)3.3制定机械加工工艺路线 (8)第4章确定机械加工余量和工序尺寸 (11)第5章确定切削用量及时间定额 (15)第6章夹具设计 (22)设计心得.......................................................................................................... .25参考文献 (26)序言《机械制造工程学》课程设计是培养学生综合运用机械制造工程原理及专业课程的理论知识。
在此次课程设计中我结合金工实习中学到的实践知识,独立地分析和解决机械加工工艺问题,初步具备中等零件工艺规程的能力.我本次设计的是CA6140机床的拨叉831006,通过这个设计让我直观地了解了拨叉831006的作用,随着科学技术的发展,各种新材料、新工艺和新技术不断涌现,机械制造工艺正向着高质量、高生产率和低成本方向发展。
各种新工艺的出现,已突破传统的依靠机械能、切削力进行切削加工的范畴,可以加工各种难加工材料、复杂的型面和某些具有特殊要求的零件,使工艺过程的自动化达到了一个新的阶段。
了解这些尤为重要的是巩固综合了大学三年以来学习的专业课知识,温故知新。
通过课程设计我增强了空间想象能力和结构构造能力,提前为以后的毕业设计打下了基础。
在机械设计制造工艺中每个环节毛坯的设计,夹具的方案一次次的修改成最后的方案无不是我日思夜想的成果,对于方案抱有严谨挑剔的态度这个是我在设计中的最大的收获,也是不断地改进设计优化方案的最大动力。
拨叉(831008)的加工工艺及钻20孔的夹具设计

拨叉(831008)的加工工艺及钻20孔的夹具设计本文描述了CA6140车床拨叉(型号)零件的机械加工工艺规程及加工φ20孔的钻床夹具设计。
首先介绍了课程设计的重要性和个人的期望。
然后对零件进行了分析, 包括零件的作用和材料特性, 以及加工表面之间的位置要求。
接着设计了工艺规程, 包括毛坯的制造形式和基面的选择。
最后介绍了钻床夹具的设计和加工工艺过程综合卡片。
在零件的分析部分, 对拨叉的作用和结构进行了详细介绍, 并提出了加工表面位置精度要求。
在工艺规程设计部分, 选择了木摸手工砂型铸件毛坯, 并选用铸件尺寸公差等级为CT-12.在钻床夹具设计部分, 设计了一种可靠的夹具, 并提供了加工工艺过程综合卡片, 以确保加工精度和效率。
1.粗、精加工基准的选择为了保证零件的加工精度和装夹准确方便, 我们需要选择合适的基准。
根据“基准重合”原则和“基准统一”原则, 我们以粗加工后的上底面为主要的定位精基准, 以两个小头孔外圆柱表面为辅助的定位精基准。
2.制定工艺路线根据零件的几何形状、尺寸精度及位置精度等技术要求,以及加工方法所能达到的经济精度, 在生产纲领已确定的情况下, 我们考虑采用万能性机床配以专用工卡具, 并尽量使工序集中来提高生产率。
除此之外, 还应当考虑经济效果, 以便使生产成本尽量下降。
根据《机械制造工艺设计简明手册》, 我们选择以下工艺路线方案:1.粗、精铣Φ32的上端面, 以Φ32的外圆面为粗基准, 采用X51立式铣床加专用夹具;2.钻、扩、铰、精铰Φ20孔, 以Φ32的上端面为基准, 采用Z525立式钻床加专用夹具;3.粗、精铣Φ32和Φ72的下端面, 以Φ32的内圆面为基准。
采用X51立式铣床加专用夹具;4.粗、精铣Φ72的上端面, 以Φ32的下端面为基准。
采用X51立式铣床加专用夹具;5.铣断, 采用X60卧式铣床加专用夹具;6.粗、精镗Φ50孔, 以Φ32的下端面为基准;7.钻Φ4通孔, 钻M6孔;8.用三面刃铣刀铣斜槽面;3.机械加工余量、工序尺寸及毛皮尺寸的确定针对“CA6140车床拨叉”零件材料为HT200, 硬度200HBW, 毛坯重量1.2KG, 生产类型大中批量, 铸造毛坯的情况, 我们需要确定各加工表面的机械加工余量、工序尺寸及毛坯尺寸。
CA6140车床拨叉831003 夹具设计说明书

课程设计说明书设计题目:设计“CA6140车床拔叉”零件的机械加工工艺规程及工艺装备(大批生产)设计者XXX指导教师XXX前言通过所学的专业课知识(《公差与配合》、《工程材料》、《机械原理》、《机械设计制造》、《机械制造技术基础》等)和金工实习使我们对机械设计制造有了一定的感性和理性认识。
这次机床工艺及夹具设计让我们对所学的专业课得以复习、巩固和应用。
是理论和实践相结合的有效手段。
不仅为大四的毕业设计做准备,而且为以后的工作打下一定的基础。
在这次设计中,我们主要设计C6140拨叉的夹具。
在设计中阅读大量的参考资料并且得到老师的指导由于能力有限在设计中难免有不足之处,恳请各位老师、同学批评指正。
一、零件的分析(一)零件的作用题目给定的零件是C6140拨叉(见附图1)它位于车床变速机构中,主要其换挡作用。
通过拨叉的拨动使车床滑移齿轮与不同的齿轮啮合从而达到要求的主轴转速。
宽度为30mm的面的尺寸精度要求很高,在拨叉工作工程中,和如果拨叉和槽的配合尺寸精度不高或者它们之间的空隙很大时。
滑移齿轮就达不到很高的定位精度,这样滑移齿轮就不能很好的与其他齿轮进行正确有效的啮合。
从而影响整个传动系统的工作。
所以拨叉宽度为30mm的面和槽之间要达到很高的配合精度。
(二)零件的工艺分析CA6140拨叉共有两组加工表面:1、这一组加工表面包括:A端面和轴线与A端面相垂直的花键底孔2、这一组加工表面包括: 六个方齿花键孔,及Φ25mm花键底孔两端的2×75°倒角。
对于两组加工表面可先加工一组表面,再用专用夹具加工另一组表面。
二、工艺规程设计(一)确定毛坯的制造形式此次所设计的拨叉材料为HT200,根据材料成型工艺可知用金属型铸造。
该零件能够承受较大载荷和冲击载荷,能够满足使用要求。
因为生产纲领为大批量生产。
因为零件形状简单故毛坯形状需与零件的形状尽量接近,又因内孔很小,可不铸出。
毛坯零件图见附图2。
课程设计:拨叉机械加工工艺规程及夹具设计

70
H
3.0 孔,降一级,单侧加工
3、画零件毛坯图(图附后)
四、 机械加工工艺过程设计
(一)选择定位基准 (1)、选择粗基准 为了方便装夹,以及依据以不加工表面为基准和毛坯表 面质量较好者为基准的原则,选底端面为粗基准。 (2)、选择精基准 依据基准重合原则,应选用统一的基准有利于保证零件 的精度。多用“一面两孔”的定位方式定位,所以选择小头孔轴线和底面为精基 准。 (二)制订工艺过程 1、根据各表面加工要求和各种加工方法所能达到的经济精度(查表 15-32、 15-33、15-34),选择加工方法: (1)、上端面 T1:粗铣(R6.3)——精铣(R3.2) (2)、上端面 T2:粗铣(R6.3)——精铣(R3.2) (3)、底端面 T3:粗铣(R6.3)——精铣(R3.2) (4)、切断面 T4:粗铣(R6.2) (5)、小端头孔 D1:扩孔(R6.3、IT10)——铰孔(R1.6、IT7)
优良,但塑性较差,脆性高,不适合磨削。 2、该零件主要加工表面及技术要求分析如下: (1)、零件上端面及孔φ50H13 的上下端面与孔φ22H7 的垂直度公差等级为
9-10 级。表面粗糙度为 Ra≤3.2um。加工时应以上端面与孔φ22H7 的内表面为基 准。又由于上端面须加工,根据“基准先行”的规则,故应先加工上端面,再加 工孔φ22H7,最后加工孔φ50H13 的上下端面。
1
表面 基本尺 加工余 加工余 代号 寸(mm) 量等级 量(mm)
说明
T1
40
H
3.5 顶面,降一级,单侧加工
T2
70
H
3.0
顶面,单侧加工
T3
70
H
3.0
底面,单侧加工
D1
倒档拨叉专用夹具设计(钻Φ18孔夹具的设计)

优秀设计制造工艺学夹具课程设计《倒档拨叉专用夹具说明书》姓名:学号:班级:指导老师:设计时间:目录一、设计题目 (3)二、零件图及加工工序分析 (4)三、设计方案 (6)1、夹具设计方案2、夹紧装置的设计3、导向装置的设计及其他装置结构.夹具体的确定4、绘制夹具结构图5、确定夹具技术要求和有关尺寸,公差配合四、夹具零部件的结构 (10)五、定位误差的计算 (14)六、致谢 (15)七、参考文献 (16)一、设计题目“倒档拨叉”专用夹具设计二、零件图及加工工序分析1、倒档拨叉零件图如图1所示:图1 倒档拨叉零件图倒档拨叉材料为QT450-10,即球墨铸铁,最小抗拉强度为450MPa,最低延伸率为10。
根据机械加工材料等相关资料可以知道:球墨铸铁既有灰铸铁的优点,即具有高的抗压强度、优良的耐磨性和消震性,低的缺口敏感性。
同时具有与中碳钢媲美的抗拉强度、弯曲疲劳强度及良好的塑性与韧性,此外,还可以通过合金化及热处理来改善与提高它的性能,所以生产上已用球墨铸铁代替中碳钢及中碳合金钢制造发动机的曲轴、连杆、凸轮轴和机床的主轴等。
QT450-10主要用于汽车、拖拉机底盘零件等。
由于该倒档拨叉外形复杂,又是薄壁零件,属于大批量生产,故毛坯采用金属型铸造。
加工机床部分采用通用机床,部分采用专用机床;按零件分类,部分布置成流水线,部分布置成机群式;广泛采用专用夹具,可调夹具;按零件产量和精度,部分采用通用刀具和量具,部分采用专用刀具和量具;部分采用划线找正装夹,广泛采用通用或专用夹具装夹;有较详细的工艺规程,用工艺卡管理生产。
根据零件图可知,零件整体要求精度较高。
其中Φ18孔中心线和叉脚开档脚面有垂直度要求,并且Φ18孔中心线自身有直线度要求,被测槽面与Φ8.7孔中心线有对称度要求。
Φ26圆柱的上下端面粗糙度要求为Ra2.5,槽内面两侧的粗糙度要求为Ra12.5,槽面粗糙度要求为Ra2.5,叉脚开档脚面的粗糙度要求为Ra6.3,脚面内侧的粗糙度要求为Ra12.5,操纵槽端面的粗糙度要求为Ra2.5。
拨叉工艺规程及铣端面的工装夹具设计
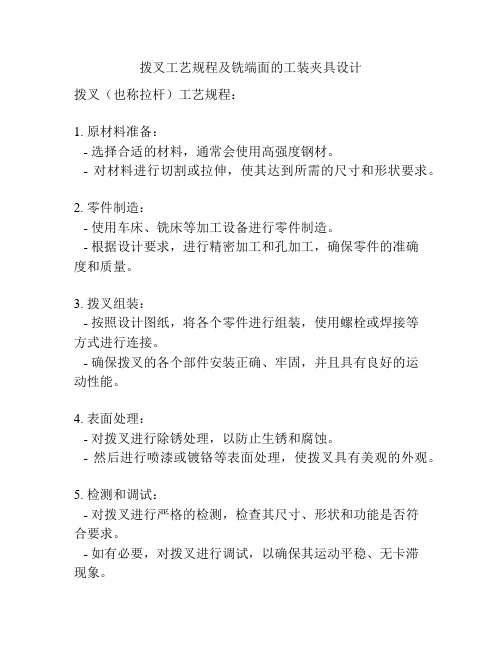
拨叉工艺规程及铣端面的工装夹具设计拨叉(也称拉杆)工艺规程:1. 原材料准备:- 选择合适的材料,通常会使用高强度钢材。
- 对材料进行切割或拉伸,使其达到所需的尺寸和形状要求。
2. 零件制造:- 使用车床、铣床等加工设备进行零件制造。
- 根据设计要求,进行精密加工和孔加工,确保零件的准确度和质量。
3. 拨叉组装:- 按照设计图纸,将各个零件进行组装,使用螺栓或焊接等方式进行连接。
- 确保拨叉的各个部件安装正确、牢固,并且具有良好的运动性能。
4. 表面处理:- 对拨叉进行除锈处理,以防止生锈和腐蚀。
- 然后进行喷漆或镀铬等表面处理,使拨叉具有美观的外观。
5. 检测和调试:- 对拨叉进行严格的检测,检查其尺寸、形状和功能是否符合要求。
- 如有必要,对拨叉进行调试,以确保其运动平稳、无卡滞现象。
铣端面的工装夹具设计:1. 确定夹具类型:- 根据铣削端面的形状和尺寸,选择合适的夹具类型,如机械夹具、气动夹具等。
2. 设计夹具结构:- 根据铣削端面的特点和工艺要求,设计夹具的结构。
- 确定夹具的定位装置、夹紧装置和支撑装置等部件,并确保其具有足够的刚性和稳定性。
3. 定位装置设计:- 根据铣削端面的形状和尺寸,设计合适的定位装置,以确保工件在夹具中的准确定位。
- 可使用V型槽或定位销等装置来实现准确定位。
4. 夹紧装置设计:- 根据铣削端面的形状和尺寸,设计夹紧装置来夹紧工件。
- 可使用夹紧螺钉、夹紧卡等装置,并确保夹紧力均匀、稳定。
5. 支撑装置设计:- 为了防止工件在铣削过程中发生振动或变形,设计适当的支撑装置。
- 可使用支撑块、支撑杆等装置,并确保其对工件施加适当的支撑力。
6. 安全考虑:- 在夹具设计中,必须考虑到安全因素,确保夹具的使用过程中不会对操作人员或设备造成危险。
- 可使用防护罩、安全开关等措施来提高安全性。
以上是拨叉工艺规程及铣端面的工装夹具设计的概述,具体的规程和设计细节可以根据具体情况进行调整和补充。
拨叉机械加工工艺规程及夹具设计
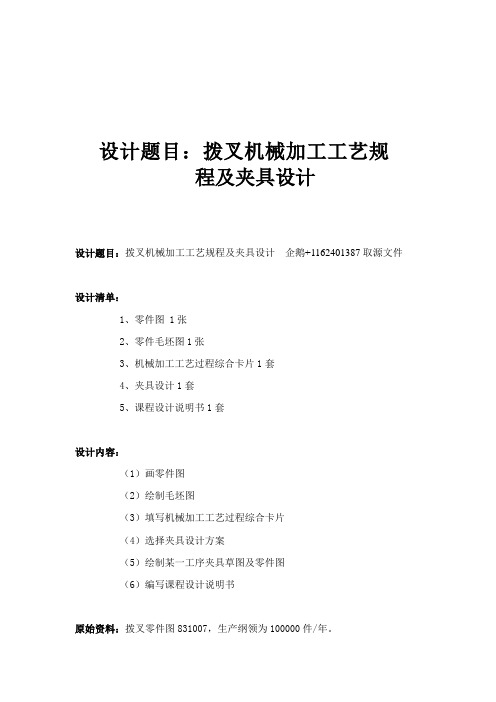
设计题目:拨叉机械加工工艺规程及夹具设计设计题目:拨叉机械加工工艺规程及夹具设计企鹅+1162401387取源文件设计清单:1、零件图 1张2、零件毛坯图1张3、机械加工工艺过程综合卡片1套4、夹具设计1套5、课程设计说明书1套设计内容:(1)画零件图(2)绘制毛坯图(3)填写机械加工工艺过程综合卡片(4)选择夹具设计方案(5)绘制某一工序夹具草图及零件图(6)编写课程设计说明书原始资料:拨叉零件图831007,生产纲领为100000件/年。
一、分析零件图(一)零件作用拨叉是传动系统中用来拨动滑移齿轮,以实现系统调速、转向的零件。
其小头通过与轴的过盈配合来传递凸轮曲线槽传来的运动;大头的内部突起处与滑移齿轮的凹槽配合。
(二)零件的工艺分析1、零件选用材料为HT200,俗称灰口铸铁。
灰铸铁生产工艺简单,铸造性能优良,但塑性较差,脆性高,不适合磨削。
2、该零件主要加工表面及技术要求分析如下:(1)、零件上端面及孔φ50H13的上下端面与孔φ22H7的垂直度公差等级为9-10级。
表面粗糙度为Ra≤3.2um。
加工时应以上端面与孔φ22H7的内表面为基准。
又由于上端面须加工,根据“基准先行”的规则,故应先加工上端面,再加工孔φ22H7,最后加工孔φ50H13的上下端面。
(2)、尺寸30、20、65、φ50、φ70都有其公差要求,加工时需要保证这些尺寸。
使其满足30-0.24+0.084、20-0.21-0.07、65-0.190φ50+0.46φ70+0.46。
(3)、φ22H7孔内表面Ra≤1.6,需要进行精铰。
φ70H13孔内表面Ra≤6.3,铣端面时就可以保证。
φ20H13内孔表面Ra≤3.2只需半精镗即可。
(4)、M8 的孔只需要钻孔与攻丝,可放在后期工序中。
(5)、φ8锥销孔只要求加工一半,故可以与M8孔同时钻出。
(6)、花键方向保持与图样一致。
两件铸在一起表面应无夹渣、气孔。
根据各加工方法的经济精度及一般机床所能达到的位置精度,该零件没有很难加工的表面尺寸,上述表面的技术要求采用常规加工工艺均可以保证。
拨叉的加工工艺及夹具设计
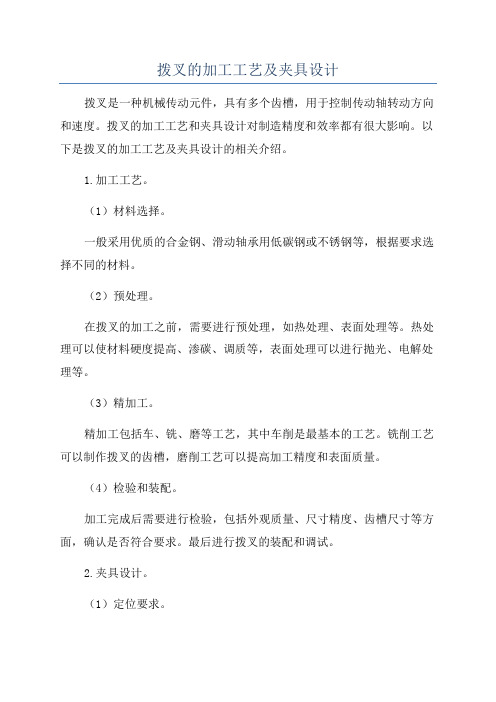
拨叉的加工工艺及夹具设计
拨叉是一种机械传动元件,具有多个齿槽,用于控制传动轴转动方向和速度。
拨叉的加工工艺和夹具设计对制造精度和效率都有很大影响。
以下是拨叉的加工工艺及夹具设计的相关介绍。
1.加工工艺。
(1)材料选择。
一般采用优质的合金钢、滑动轴承用低碳钢或不锈钢等,根据要求选择不同的材料。
(2)预处理。
在拨叉的加工之前,需要进行预处理,如热处理、表面处理等。
热处理可以使材料硬度提高、渗碳、调质等,表面处理可以进行抛光、电解处理等。
(3)精加工。
精加工包括车、铣、磨等工艺,其中车削是最基本的工艺。
铣削工艺可以制作拨叉的齿槽,磨削工艺可以提高加工精度和表面质量。
(4)检验和装配。
加工完成后需要进行检验,包括外观质量、尺寸精度、齿槽尺寸等方面,确认是否符合要求。
最后进行拨叉的装配和调试。
2.夹具设计。
(1)定位要求。
夹具设计的第一个要求是准确定位,保证加工精度。
可以采用中央定位孔、三点定位、夹具块定位等方法。
(2)夹紧方式。
夹具要采用可靠的夹紧方式,避免工件滑动或变形,常用的夹紧方式有机械夹紧、气动夹紧等。
(3)切削力。
在夹具设计中要考虑切削力大小和方向,以保证加工过程中的稳定性和安全性。
(4)材料选择和加工精度。
夹具的材料选择应符合要求,一般采用高强度钢材或铸铁等,夹具的加工精度也需要达到高精度。
总之,拨叉的加工工艺和夹具设计都需要进行精细的规划和调整,以达到高质量、高效率的加工要求。
- 1、下载文档前请自行甄别文档内容的完整性,平台不提供额外的编辑、内容补充、找答案等附加服务。
- 2、"仅部分预览"的文档,不可在线预览部分如存在完整性等问题,可反馈申请退款(可完整预览的文档不适用该条件!)。
- 3、如文档侵犯您的权益,请联系客服反馈,我们会尽快为您处理(人工客服工作时间:9:00-18:30)。
目录 目录 ......................................................................... 1 摘要 ......................................................................... 2 一、分析零件图 ............................................................... 3 1.1零件作用 ............................................................................................ 错误!未定义书签。 1.2零件的工艺分析................................................................................. 错误!未定义书签。 二、确定毛坯 ........................................................................................... 错误!未定义书签。
三、工艺规程设计 ............................................. 错误!未定义书签。 3.1基面的选择 ........................................................................................ 错误!未定义书签。 3.2精基准的选择.................................................................................................................... 7 四 工序加工计算..................................................................................................................... 8
五、夹具的设计 ............................................... 错误!未定义书签。 5.1定位误差分析...................................................................................... 错误!未定义书签。 5.2工件的夹紧 ........................................................................................ 错误!未定义书签。
5.2.1. 加紧位置的组成 ........................................................................... 错误!未定义书签。 5.2.2. 加紧力的方向 ............................................................................................................ 18 5.2.3. 加紧力的作用点 ........................................................................................................ 18 5.2.4. 加紧力的大小 ............................................................................... 错误!未定义书签。 5.2.5. 夹具的精度分析 ........................................................................................................ 21 参考文献 ............................................................... 22 新疆大学机械制课程设计
- 2 - 任 务 书
1、分析零件图 1.1零件作用 拨叉是传动系统中用来拨动滑移齿轮,以实现系统调速、转向的零件。其小头通过与轴的过盈配合来传递凸轮曲线槽传来的运动;大头的内部突起处与滑移齿轮的凹槽配合。
1.2零件的工艺分析
1、零件选用材料为ZG310-570。ZG310-570生产工艺简单,铸造性能优良,但塑性较差,脆性高,不适合磨削。
图1-1拨叉 2、该零件主要加工表面及技术要求分析如下: 零件上端面及孔φ160的上下端面与孔φ52H8的垂直度公差等级为8级。表面粗糙度为Ra≤3.2um。加工时应以上端面与孔φ52H8的内表面为基准。又由于上端面须加工,根据“基准先行”的规则,故应先加工上端面,再加工孔φ52H8,最后加工孔φ160,新疆大学机械制课程设计 - 3 - 然后加工其上下端面。
2、确定毛坯 2.1、确定毛坯种类 根据零件材料确定毛坯为铸件。并依其结构形状、尺寸大小和生产类型,毛坯的铸造方法选用砂型铸造,机器造型。
图2-1零件毛坯图 2.2、确定毛坯基本尺寸 通过零件分析可知孔为双侧加工,小头孔端面为单侧加工, 根据毛坯基本尺寸的计算公式可得下表: 表2-1 项目 小头孔端面 52孔 160孔
公差等级CT 9 9 9
加工面基本尺寸 52 26 80
铸件尺寸公差 2 1.7 2 机械加工余量等级 F F F RMA 1.5 1.5 1.5
毛坯基本尺寸 52.5 15 85 新疆大学机械制课程设计
- 4 - 3、工艺路线:
表3-1 工序号 工序名称 工序内容 工艺装备 1 铸 精密铸造,两件合铸(工艺需要) 2 热处理 退火 3 划线 划各端面及三个孔的线 4 车 以外形及下端面定位,按线找正,四爪单动卡盘装夹(或专用工具)工件。车160孔至图样尺寸,并车孔的两侧面,保证尺寸80和9及尺寸要求。 CA6140专用工具
5 铣 以两段50内孔及外部端定位,装夹工件,铣50上端面,保证两端面距离尺寸80mm和9及精度要求 X5030A组合夹具
6 铣 以两边的50内孔外端定位定位,反过来装夹工件,铣50的另一端面,保证两段面尺寸80mm X5030A组合夹具
7 钻 以50内孔的两段外部端面定位,装夹工件,钻,扩铰50孔,孔口倒角C1 Z5132A组合夹具
8 钻 M6的螺纹孔按精度要求达到尺寸标准 Z5132A组合夹具
9 检验 按图样要求检查各部件尺寸 及精度 10 入库 入库
3.1、基面的选择 粗基准的选择: 以零件的小头上端面为主要的定位粗基准,以两个小头孔外圆表面为辅助粗基准。加工两小孔端面时,以底面和两外圆表面定位是合理的,此时应选择两V型块作为定位元件,这样比较容易实现。若选择底面和两小孔作为定位基准,则由于小孔铸造时的误差太大,很难与心轴、菱形销配合良好。以加工后的小孔端面为粗基准来加工两小孔。再以加工后的小孔和小孔端面为粗基准来加工中间孔,以及中间孔上下端面。这样做是保证零件垂直度误差的前提。
3.2、精基准的选择
加紧装置的组成: 拨叉的铣断面装置如下图所示的 工序的确定: 按给定的尺寸和精度要求我重复的考虑吧拨叉的工业路线和夹具设计。 因工件的加工的表面和空比较多加工工序分给几组的同学,按分给我的加工工序我设计好了拨叉两端面铣的加工工序和夹具的设计。我用两个工件同时加工的方法来设计了拨叉的夹具。这样就可以提升加工量和加工速度,加工过程中可以避免拨叉的加工新疆大学机械制课程设计 - 5 - 误差。两个拨叉零件平行放着夹具的中间部分也就是前后放着。铣拨叉两端面的夹具体主要是固定v形块和活动v形块的加紧方案,因前后放着的v形块高度不一样,我设计的支撑钉的高度也不一样但上面部分和下部分的螺纹长度和宽度都一样的,前面的零件下面使用的是尺寸小的支撑钉,后面的零件下面使用的是尺寸大的支撑钉,一共有四个支撑钉。固定v形块有俩个,前面和后面的零件各自用一个。活动v形块也是两个,配对固定v形块使用的。活动v形块外套有两个,盖上活动v形块上面部分。连杆也有两个是活动v形块的不可分离的一部分。对刀块用一个安装在后面零件的旁边。
装配图:
图5-1夹具图 整个铣断面装置的夹具的主要部分是固定和活动v形块。我们通过仔细的分析才决定了铣断面装置的夹具。主要用的是毛胚零件要两个,平行放着铣。
V形块: V型块是一种比较特殊的定位元件。它虽然是一个单独定位元件,但它的定位基面的结构要素却不是单一的,有两个定位平面,从某种意义上来讲这种形式的定位可看作是两个平面的组合定位。因此,它的定位基准的确定就不能象分析单一定位基面那样简单。 大多数定位元件的定位基准都是定位基面本身或者是由其形成的点、面、线,如单一平面、球心、孔和轴的中心线等。根据这个道理,笔者认为,V型块的定位基准应有