拨叉(831008)的加工工艺及钻20孔的夹具设计
拨叉(831008)的加工工艺及钻20孔的夹具设计

拨叉(831008)的加工工艺及钻20孔的夹具设计本文描述了CA6140车床拨叉(型号)零件的机械加工工艺规程及加工φ20孔的钻床夹具设计。
首先介绍了课程设计的重要性和个人的期望。
然后对零件进行了分析, 包括零件的作用和材料特性, 以及加工表面之间的位置要求。
接着设计了工艺规程, 包括毛坯的制造形式和基面的选择。
最后介绍了钻床夹具的设计和加工工艺过程综合卡片。
在零件的分析部分, 对拨叉的作用和结构进行了详细介绍, 并提出了加工表面位置精度要求。
在工艺规程设计部分, 选择了木摸手工砂型铸件毛坯, 并选用铸件尺寸公差等级为CT-12.在钻床夹具设计部分, 设计了一种可靠的夹具, 并提供了加工工艺过程综合卡片, 以确保加工精度和效率。
1.粗、精加工基准的选择为了保证零件的加工精度和装夹准确方便, 我们需要选择合适的基准。
根据“基准重合”原则和“基准统一”原则, 我们以粗加工后的上底面为主要的定位精基准, 以两个小头孔外圆柱表面为辅助的定位精基准。
2.制定工艺路线根据零件的几何形状、尺寸精度及位置精度等技术要求,以及加工方法所能达到的经济精度, 在生产纲领已确定的情况下, 我们考虑采用万能性机床配以专用工卡具, 并尽量使工序集中来提高生产率。
除此之外, 还应当考虑经济效果, 以便使生产成本尽量下降。
根据《机械制造工艺设计简明手册》, 我们选择以下工艺路线方案:1.粗、精铣Φ32的上端面, 以Φ32的外圆面为粗基准, 采用X51立式铣床加专用夹具;2.钻、扩、铰、精铰Φ20孔, 以Φ32的上端面为基准, 采用Z525立式钻床加专用夹具;3.粗、精铣Φ32和Φ72的下端面, 以Φ32的内圆面为基准。
采用X51立式铣床加专用夹具;4.粗、精铣Φ72的上端面, 以Φ32的下端面为基准。
采用X51立式铣床加专用夹具;5.铣断, 采用X60卧式铣床加专用夹具;6.粗、精镗Φ50孔, 以Φ32的下端面为基准;7.钻Φ4通孔, 钻M6孔;8.用三面刃铣刀铣斜槽面;3.机械加工余量、工序尺寸及毛皮尺寸的确定针对“CA6140车床拨叉”零件材料为HT200, 硬度200HBW, 毛坯重量1.2KG, 生产类型大中批量, 铸造毛坯的情况, 我们需要确定各加工表面的机械加工余量、工序尺寸及毛坯尺寸。
831008拨叉 设计说明书
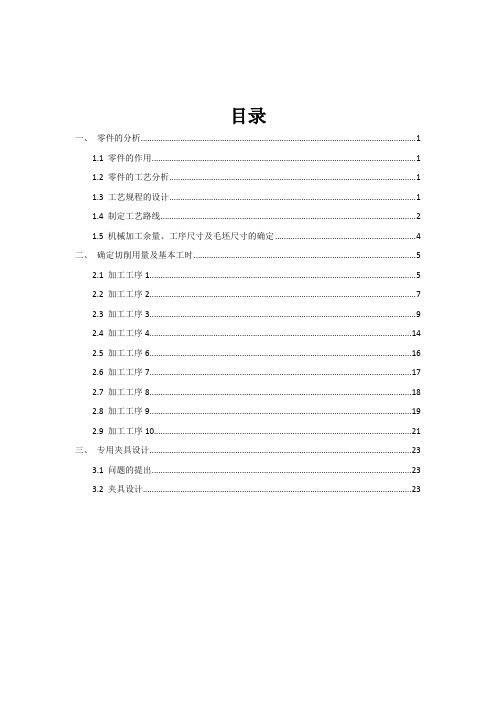
工序5粗、半精铣Φ50mm孔上端面。
工序6粗、半精铣Φ50mm孔下端面。
工序7钻Φ4mm孔(装配时钻铰锥孔)。
工序8钻Φ5mm孔,攻M6螺纹。
工序9铣47°平面。
工序10铣断。
工序11终检。
③工艺方案的比较与分析
上述两个工艺方案的特点在于:方案一的加工效率比较高,但是同时加工三个孔对设备和夹具的精度要求比较高,并且在把零件铣断后钻侧壁孔会使工件难以固定从而导致夹具的复杂化。方案二的加工效率比方案一低,不符合大批量加工的要求,并且加工Φ50mm孔使用钻床加工的时间比镗床加工的时间长,综合考虑以后,加工工艺路线如下所示:
工序5以Φ20mm孔为精基准,粗、半精镗Φ50mm孔,保证尺寸 mm。选用T612卧式镗床。
工序6以Φ20mm孔为精基准,粗、半精铣Φ50mm孔上端面。选用XA6132万能升降台铣床。
工序7以Φ20mm孔为精基准,铣47°平面。选用XA6132万能升降台铣床。
工序8以Φ20mm孔为精基准,钻Φ4mm孔。选用Z525立式钻床。
②精基准的选择。精基准的选择主要应该考虑基准重合的问题。当设计基准与工序基准不重合时,应该进行尺寸换算。
ቤተ መጻሕፍቲ ባይዱ1.4
由于生产类型为大批量生产,故采用万能机床配以专用工夹具,并尽量使工序集中来提高生产率。除此以外,还应降低生产成本。
①工艺路线方案一:
工序1粗、半精铣Φ20mm孔上端面。
工序2钻、扩、绞、精绞Φ20mm、Φ50mm孔。
= = =0.89
= = =1
故 = =96.6m/min
则 = = =384.4r/min
采用XA6132铣床,根据《切削手册》P111,表3.30,机床说明书,取 =375r/min,故实际切削速度为:
工艺课程设计--拨叉80-08的加工工艺规程设计
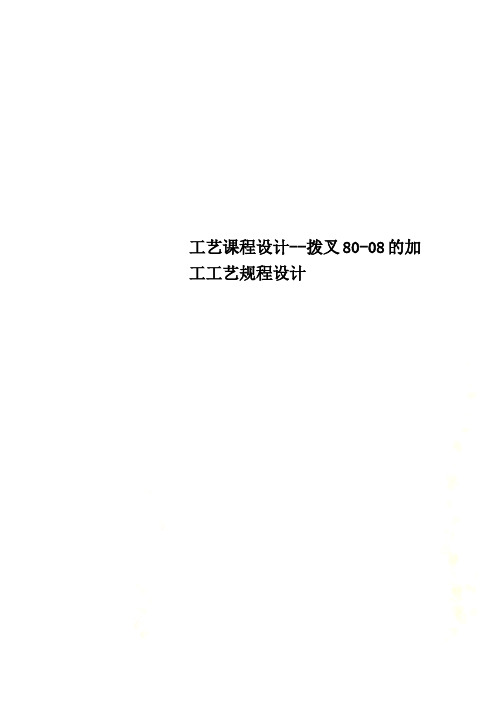
工艺课程设计--拨叉80-08的加工工艺规程设计1绪论1.1课题背景随着科学技术的发展,各种新材料、新工艺和新技术不断涌现,机械制造工艺正向着高质量、高生产率和低成本方向发展。
各种新工艺的出现,已突破传统的依靠机械能、切削力进行切削加工的范畴,可以加工各种难加工材料、复杂的型面和某些具有特殊要求的零件。
数控机床的问世,提高了更新频率的小批量零件和形状复杂的零件加工的生产率及加工精度。
特别是计算方法和计算机技术的迅速发展,极大地推动了机械加工工艺的进步,使工艺过程的自动化达到了一个新的阶段。
“工欲善其事,必先利其器。
”工具是人类文明进步的标志。
自20世纪末期以来,现代制造技术与机械制造工艺自动化都有了长足的发展。
但工具(含夹具、刀具、量具与辅具等)在不断的革新中,其功能仍然十分显著。
机床夹具对零件加工的质量、生产率和产品成本都有着直接的影响。
因此,无论在传统制造还是现代制造系统中,夹具都是重要的工艺装备。
1.2夹具的发展史夹具在其发展的200多年历史中,大致经历了三个阶段:第一阶段,夹具在工件加工、制造的各工序中作为基本的夹持装置,发挥着夹固工件的最基本功用。
随着军工生产及内燃机,汽车工业的不断发展,夹具逐渐在规模生产中发挥出其高效率及稳定加工质量的优越性,各类定位、夹紧装置的结构也日趋完善,夹具逐步发展成为机床—工件—工艺装备工艺系统中相当重要的组成部分。
这是夹具发展的第二阶段。
这一阶段,夹具发展的主要特点是高效率。
在现代化生产的今天,各类高效率,自动化夹具在高效,高精度及适应性方面,已有了相当大的提高。
随着电子技术,数控技术的发展,现代夹具的自动化和高适应性,已经使夹具与机床逐渐融为一体,使得中,小批量生产的生产效率逐步趋近于专业化的大批量生产的水平。
这是夹具发展的第三个阶段,这一阶段,夹具的主要特点是高精度,高适应性。
可以预见,夹具在不一个阶段的主要发展趋势将是逐步提高智能化水平。
1.3小结一项优秀的夹具结构设计,往往可以使得生产效率大幅度提高,并使产品的加工质量得到极大地稳定。
拨叉零件机械加工工艺规程及其夹具设计(课程设计)

课程设计(论文)任务及评语目录第一章零件工艺性分析 0第二章生产纲领计算及生产类型的确定 0第三章毛坯种类及制造方法 0第四章拟定工艺路线 (1)4.1定位基准确定 (1)4.2各表面加工方案确定 (1)4.3工序安排 (1)第五章计算各工序的加工余量、工序尺寸及公差 (3)5.1粗铣,半精铣,精铣右端面工序尺寸及公差确定 (3)5.2粗铣,半精铣,精铣左端面工序尺寸及公差确定 (3)5.3Φ20孔工序尺寸及公差确定 (4)5.4拨叉脚内表面工序尺寸及公差确定 (4)5.5Φ5销孔工序尺寸及公差确定 (5)第六章各工序机床、刀具、量具、夹具的选择 (6)第七章工序切削用量和时间定额计算 (7)7.1粗铣,半精铣,精铣右端面 (7)7.2粗铣,半精铣,精铣右端面 (9)7.3粗扩,精扩,铰Φ20孔 (9)7.4粗铣、半精铣拨叉脚内表面 (11)7.5钻,粗铰,精铰Φ5孔 (12)第八章工艺规程的编制 (15)第九章专用夹具设计 (15)9.1方案分析 (15)9.2定位误差的计算: (15)9.3夹紧力的计算: (15)第十章设计体会 (16)参考文献 (16)附录 (17)第一章零件工艺性分析拨叉零件的作用:用在变速箱换挡机构中,通过叉轴孔Φ20安装在变速叉轴上,销钉经拨叉上Φ5孔与叉轴固定,齿轮在拨叉脚内,操纵拨叉头部带动拨叉使拨叉脚内表面拨动齿轮换挡≥745MPa ,硬度HB 231-304。
本题目零件材料为球墨铸铁Q745-5,其力学性能:σb毛坯形式为铸件,轻型零件,生产纲领为大量批生产。
分析零件图,此零件需加工表面为拨叉两端面,Φ20通孔,Φ5销孔以及拨叉脚内表面。
拨叉两端面和拨叉内表面加工精度可由铣削加工保证,Φ20孔和Φ5销孔加工精度可由钻,扩,铰一次加工就可以达到要求,所有加工表面都可在正常生产条件下,采用较经济的方法保质保量地加工出来。
由此可见,该零件的工艺性很好。
第二章生产纲领计算及生产类型的确定生产纲领:N=Qn(1+a%)(1+b%)=10000×(1+0.001)(1+0.001)=10020.01 件/年生产类型:查《机械制造基础课程设计指导教程》∵质量0.15kg<4kg∴由表1-4知该零件属于轻型零件(P5)∵10020大于5000∴由表1-5知该零件属于大批生产第三章毛坯种类及制造方法毛坯材料为球墨铸铁Q745-5,根据零件生产类型,制造精度,原材料,加工余量等综合选择砂型铸造,因为是大批生产,采用砂型机器铸造。
拨叉零件的机械加工工艺规程设计

拨叉零件的机械加工工艺规程设计一、工艺流程及工序划分拨叉是一种常见的机械零件,用于传递和转换运动,同时也具有一定的强度和刚度要求。
拨叉零件的机械加工工艺规程设计主要包括以下几个工序:材料准备、车削、铣削、钻孔、热处理、车磨、组装等。
二、材料准备选用的材料应满足零件的强度、刚度和耐磨性要求。
常用的材料有碳钢、合金钢等。
在材料准备阶段,需要根据零件的要求,选择合适的材料,并按照规格要求切割或剪断原材料到适当尺寸。
三、车削工序1.车削工序主要用于零件的外轮廓形状加工和螺纹加工。
根据零件的图纸和要求,确定车削工序中的主要参数,包括刀具选择、切削速度、进给量、切屑厚度等。
同时,需考虑零件材料的硬度和刀具的耐磨性,选择合适的切削参数。
根据加工的不同要求,可以采用车削粗加工和车削精加工两种切削工艺。
四、铣削工序1.铣削工序主要用于零件表面的平面加工和槽加工。
根据零件的工艺要求和图纸,确定铣削工序的主要参数,包括刀具的选择、切削速度、进给量、切削层厚度等。
根据加工的要求,可以选择平面铣削、立铣、端铣等不同的铣削方式。
五、钻孔工序1.钻孔工序主要用于拨叉零件的孔加工。
根据零件的需求和图纸,确定钻孔工序的主要参数,包括钻头的选择、切削速度、进给量等。
根据加工的要求,可以选择不同精度的钻孔操作,包括铰孔、镗孔等。
六、热处理工序1.热处理工序主要用于提高零件的硬度和耐磨性。
根据零件的材料和工艺要求,选择合适的热处理工艺,包括淬火、回火等。
同时,需根据工艺要求,控制加热温度和保温时间,以保证零件的性能满足要求。
七、车磨工序1.车磨工序主要用于零件的精密加工和表面粗糙度的改善。
根据零件的要求和图纸,确定车磨工序的主要参数,包括磨削刀具的选择、磨削速度、进给量、切削深度等。
根据加工的要求,可以选择不同精度的车磨操作,包括车削、磨削等。
八、组装工序1.组装工序主要用于将加工好的零件进行组装,使之成为完整的产品。
在组装工序中,需要使用合适的工具和设备,如螺丝刀、扳手等,确保零件的安装和连接的质量。
拨叉的加工工艺及钻20孔的夹具设计
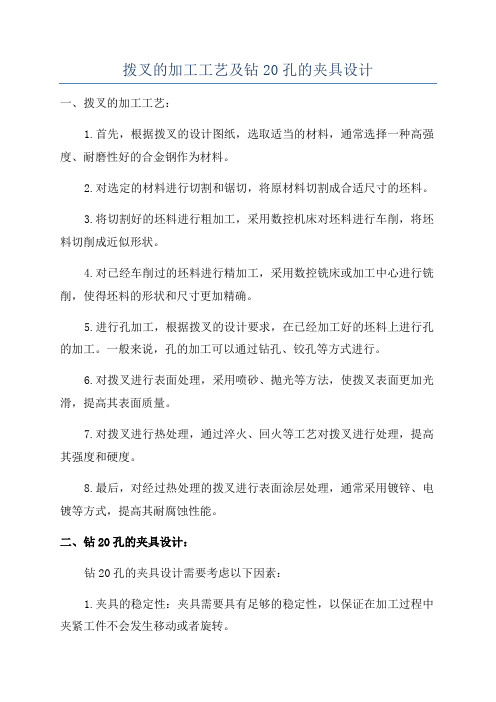
拨叉的加工工艺及钻20孔的夹具设计一、拨叉的加工工艺:1.首先,根据拨叉的设计图纸,选取适当的材料,通常选择一种高强度、耐磨性好的合金钢作为材料。
2.对选定的材料进行切割和锯切,将原材料切割成合适尺寸的坯料。
3.将切割好的坯料进行粗加工,采用数控机床对坯料进行车削,将坯料切削成近似形状。
4.对已经车削过的坯料进行精加工,采用数控铣床或加工中心进行铣削,使得坯料的形状和尺寸更加精确。
5.进行孔加工,根据拨叉的设计要求,在已经加工好的坯料上进行孔的加工。
一般来说,孔的加工可以通过钻孔、铰孔等方式进行。
6.对拨叉进行表面处理,采用喷砂、抛光等方法,使拨叉表面更加光滑,提高其表面质量。
7.对拨叉进行热处理,通过淬火、回火等工艺对拨叉进行处理,提高其强度和硬度。
8.最后,对经过热处理的拨叉进行表面涂层处理,通常采用镀锌、电镀等方式,提高其耐腐蚀性能。
二、钻20孔的夹具设计:钻20孔的夹具设计需要考虑以下因素:1.夹具的稳定性:夹具需要具有足够的稳定性,以保证在加工过程中夹紧工件不会发生移动或者旋转。
2.工件的定位:夹具设计需要考虑工件的定位,使得工件能够准确的被定位在正确的位置。
3.加工的精度:夹具设计需要保证加工的精度,使得钻孔的位置和尺寸能够满足设计要求。
4.工件的夹持:夹具设计需要确保工件能够被牢固的夹持,不会产生松动或者震动。
5.加工的效率:夹具设计需要考虑加工的效率,确保能够高效的完成钻孔任务。
基于以上因素,可以设计一个简单的夹具:该夹具由一个底座和两个夹紧板组成。
底座上有20个孔,用于定位工件。
夹紧板上也有20个相对应的孔,用于夹持工件。
在夹紧板上安装夹持装置,通过旋转夹持装置,可以实现夹紧和松开工件。
在夹持板和底座之间设置弹簧,以确保夹持板能够向下施加足够的压力,夹紧工件。
夹具的底座和夹持板可以采用合金钢材料制作,以确保足够的强度和耐磨性。
完整_拨叉80-08的加工工艺
摘要本次设计是车床变速箱中拔叉零件的加工工艺规程及一些工序的专用夹具设计。
此拔叉零件的结构较为复杂,其加工的地方主要是孔和平面。
本设计先加工孔后加工面。
将孔与平面的加工明确划分成粗加工和精加工阶段以保证它们的加工精度。
基准选择以拔叉右面的最大的平面作为粗基准,来加工中间的通孔,然后以此加工过的孔作为精基准。
主要加工工序安排是先以中心孔定位加工出顶平面和右侧平面以及下面的大孔的两平面,再以中心孔定位加工出下端的大孔。
加工时是用镗床镗孔。
最后以这两个孔为基准,分别加工右侧的槽和顶面的螺纹底孔。
整个加工过程选用了钻床、铣床和镗床。
工件在机床上定位夹紧选用专用夹具,夹紧方式为手动夹紧,夹紧可靠,操作方便。
因此生产效率较高,适用于大批量、流水线上加工。
能够满足设计要求。
关键词:加工工艺,定位,夹紧,专用夹具目录1 绪论 (1)1.1课题背景 (1)1.2夹具的发展史 (1)1.3小结 (1)2 拨叉80-08的加工工艺规程设计 (3)2.1零件的分析 (3)2.2确定生产类型 (3)2.3确定毛坯 (3)2.4工艺规程设计 (4)2.5确定切削用量及基本工时 (8)2.6本章小结 (20)3 专用夹具设计 (21)3.1镗孔夹具设计 (21)3.1.1问题的提出 (21)3.1.2夹具的设计 (21)3.2铣槽夹具设计 (24)3.2.1问题的提出 (24)3.2.2夹具的设计 (24)3.3钻孔夹具设计 (28)3.3.1问题的提出 (28)3.3.2夹具的设计 (28)3.4本章小结 (33)结论 (34)致谢 (35)参考文献 (36)1 绪论1.1课题背景随着科学技术的发展,各种新材料、新工艺和新技术不断涌现,机械制造工艺正向着高质量、高生产率和低成本方向发展。
各种新工艺的出现,已突破传统的依靠机械能、切削力进行切削加工的范畴,可以加工各种难加工材料、复杂的型面和某些具有特殊要求的零件。
数控机床的问世,提高了更新频率的小批量零件和形状复杂的零件加工的生产率及加工精度。
拨叉类零件加工工艺和夹具设计
拨叉类零件加工工艺和夹具设计任务书1.设计的主要任务及目标对零件进行工艺分析,熟悉零件图制定零件的机械加工工艺路线工艺装备设计及编写设计说明书2.设计的基本要求和内容分析课题要求,查阅相关知识方面的论文,拟定开题报告;查找设计题目相关的资料;制定零件的机械加工工艺路线;绘制装配图及零件图撰写设计说明书一份(约40页10000字左右)。
3.主要参考文献《机械制造工艺学》、《机械制造基础》、《优化设计》、《机械设计手册》、《机床夹具设计》、《数控机床加工工艺》等参考书4.进度安排拨叉类零件加工工艺和夹具设计摘要:本次毕业设计是拔叉零件加工工艺设计,及加工夹具设计。
该拨叉位于车床变速机构中,主要起换挡、使主轴回转运动按照工作者的要求工作,获得所需的速度和扭矩的作用。
此拨叉零件的结构较为复杂,其加工的地方主要是孔和平面。
本设计一共十三道工序,以先孔后面为原则。
将孔与平面的加工明确划分成粗加工和精加工阶段以保证它们的加工精度。
基准选择以拨叉右面的最大平面作为粗基准,来加工中间的通孔,然后以此加工过的孔为精基准。
主要加工工序安排是先以中心孔定位加工出顶平面和右侧平面以及下面的大孔的两平面,再以中心孔定位加工出下端的大孔。
最后以这两个孔为基准,分别加工右侧的槽和顶面的螺纹底孔。
整个加工过程选用了钻床、铣床和镗床。
因此生产效率较高,适用于大批量流水线上加工。
专用夹具的设计是针对工序精铣槽16H11的设计,夹具结构简单,便于操作,降低成本,提高夹具性价比。
关键词:拔叉,加工工艺,夹具,设计Transmission fork parts processing technology and fixturesdesignAbstract:This graduation design is transmission fork parts processing technology and fixtures design.The fork is located lathe gear mechanism, the role is shift and spindle rotary motion in accordance with requirements of workers, access to the required speed and torque.Part of this configuration is more complicated fork,its mainly processing place is holes flat.The design process has thirteen,the principle is “first hole and the surface”.Put the hole and surface clearly divided into roughing and finishing stages to ensure their precision.The largest surface to the right of the fork as a rough benchmark,then process the through hole in the middle,and this hole is fine benchmark.The principal processes arrangement is process the surface on the top and the surface on the right side and the surface of the following hole,then process the following hole. Finally,with reference to these two holes, processed slot on the right side and top of surface pilot hole for tapping separately.The whole process is selected drilling, milling and boring machines.Therefore it has higher productivity and apply to the processing of high-volume assembly line.Special fixture is designed for the twelfth slot 16H11 finishing processes of design. Fixture structure is simple,easy to operate,lower costs, good value.Keyword: transmission fork,processing technology,fixture,design目录1前言 (1)2零件的分析 (2)2.1零件的作用 (2)2.2零件的技术要求 (2)2.3零件的工艺分析 (3)3工艺规程的设计 (4)3.1生产类型的确定 (4)3.2确定毛坯的制造形式 (5)3.3基面的选择 (5)3.3.1粗基准的选择 (5)3.3.2精基准的选择 (5)3.4制定工艺路线 (6)3.4.1制定多种工艺路线 (6)3.4.2工艺方案的分析与比较 (7)3.5拨叉工艺路线及设备、工装的选用 (8)3.6机械加工余量、工序尺寸及毛坯尺寸的确定 (8)3.7确立切削用量及基本工时 (10)4夹具设计 (17)4.1问题的提出 (17)4.2工序设计专用夹具的优点 (17)4.3夹具设计 (17)4.3.1定位基准的选择 (17)4.3.2切削力和夹紧力的计算 (18)4.3.3定位误差分析 (19)4.3.4夹具设计及操作的简要说明 (20)结论 (21)附录 (22)附录1拨叉零件图 (22)附录2 夹具零件图 (23)附录3 机械加工工艺过程卡片 (24)附录4 机械加工工序卡片 (25)参考文献 (26)致谢 (27)1 前言机械制造工业是国民经济最重要的部门之一,是一个国家或地区经济发展的支柱产业,其发展水平标志着该国家或地区的经济实力、科技水平、生活水平和国防实力。
831008 拨叉的 工艺过程卡
立式铣床
X52K
面铣刀
游标卡尺
3
钻扩两孔φ20
定位:1)以φ20外圆③2)以底面③
工序尺寸:钻,扩两个φ20的孔至20.021-20mm、Ra1.6μm
摇臂钻床
Z3025
麻花钻、扩孔钻
内径千分尺
4
粗镗孔φ50
定位:1)以φ32两圆柱外圆柱面③;2)底面③工序尺寸:粗镗孔φ50至φ50.50-φ50.25、Ra3.2μm
摇臂钻床
Z525
麻花钻
内径千分尺
12
攻螺纹m6
丝锥
13
半精铰两孔φ20
定位:1)以φ50内孔④;2)底面②
工序尺寸:半精铰两孔φ20至20.021mm-20mm
摇臂钻床
Z535
铰刀
内径千分尺
14
精铰两孔φ20
定位:1)以φ50内孔④;2)底面②
工序尺寸:精铰两孔φ20至20.021mm-20mm、Ra1.6μm
卧式铣镗床
T611
镗刀
卡尺,塞规
5
半精镗孔φ50
定位:1)以φ32两圆柱外圆柱面③;2)底面③工序尺寸:半精镗镗孔φ50至φ50.50-φ50.25、Ra3.2μm
卧式铣镗床
T611
镗刀
卡尺,塞规
6
粗铣孔φ50端面
定位:1)以底面③;2)两φ20孔③
工序尺寸:粗铣孔φ50端面至11.994mm-11.982mm
面铣刀
游标卡尺
9
半精铣φ32端面
定位:1)以底面③;2)两φ20孔③
工序尺寸:半精铣φ32端面至30mm,Ra3.2μm
卧式铣床
拨叉加工工艺路线制定及夹具设计
拨叉加工工艺路线制定及夹具设计摘要拨叉是一种常用的齿轮传动部件,广泛应用于工程机械、汽车等领域。
拨叉的加工工艺路线的制定及夹具设计对于提高生产效率、保证产品质量至关重要。
本文将介绍拨叉加工工艺路线的制定过程,包括工艺规程、加工工序、工艺参数的确定,并重点探讨拨叉加工夹具的设计原则和方法。
一、拨叉加工工艺路线的制定过程拨叉加工工艺路线的制定是基于产品的设计要求和工艺性能的分析,旨在确定具体的加工工序和工艺参数,以实现产品的高效加工和优质制造。
1. 工艺规程的确定工艺规程是加工工艺路线制定的基础,它是根据产品的设计要求和工艺性能,确定的各个加工工序和工艺参数的详细规定。
具体包括以下内容:•拨叉加工工序的排列顺序:根据产品的结构特点和加工工序之间的依赖关系,确定拨叉加工的工艺流程,确保加工工序之间的合理衔接和协调。
•加工工序的分解与组合:将拨叉的加工过程分解为若干个子工艺,并确定各个子工艺之间的顺序关系。
同时,要考虑到工序之间的依赖关系和可能存在的并行加工过程。
•工艺参数的设定:根据产品的设计要求和材料的特性,确定拨叉加工过程中的各个工艺参数,如加工速度、切削深度、进给速度等。
同时,要根据实际情况进行综合考虑,以保证产品质量和加工效率的平衡。
2. 加工工序的确定加工工序的确定是基于工艺规程的要求,考虑到产品的结构特点和加工工艺的特点,确定拨叉加工的具体工序。
一般包括以下几个方面:•材料的准备和加工前处理:包括原材料的检验、切割和清洗等工作,确保原材料的质量符合要求。
•切削加工:采用切削方式对拨叉进行加工,包括铣削、车削、钻孔等工序。
根据工艺规程,确定各个工序中的刀具选择、切削速度和进给速度等工艺参数。
•热处理:对拨叉进行热处理,以提高其硬度和强度,常用的热处理方法包括淬火、回火等。
•表面处理:对拨叉进行表面处理,如研磨、抛光等,以提高其表面质量和光洁度。
•检验和组装:对加工后的拨叉进行检验,以确保其质量符合要求。
- 1、下载文档前请自行甄别文档内容的完整性,平台不提供额外的编辑、内容补充、找答案等附加服务。
- 2、"仅部分预览"的文档,不可在线预览部分如存在完整性等问题,可反馈申请退款(可完整预览的文档不适用该条件!)。
- 3、如文档侵犯您的权益,请联系客服反馈,我们会尽快为您处理(人工客服工作时间:9:00-18:30)。
拨叉(831008)的加工工艺及钻20孔的夹具设计本文描述了CA6140车床拨叉(型号)零件的机械加工工艺规程及加工φ20孔的钻床夹具设计。
首先介绍了课程设计的重要性和个人的期望。
然后对零件进行了分析,包括零件的作用和材料特性,以及加工表面之间的位置要求。
接着设计了工艺规程,包括毛坯的制造形式和基面的选择。
最后介绍了钻床夹具的设计和加工工艺过程综合卡片。
在零件的分析部分,对拨叉的作用和结构进行了详细介绍,并提出了加工表面位置精度要求。
在工艺规程设计部分,选择了木摸手工砂型铸件毛坯,并选用铸件尺寸公差等级为CT-12.在钻床夹具设计部分,设计了一种可靠的夹具,并提供了加工工艺过程综合卡片,以确保加工精度和效率。
1.粗、精加工基准的选择为了保证零件的加工精度和装夹准确方便,我们需要选择合适的基准。
根据“基准重合”原则和“基准统一”原则,我们以粗加工后的上底面为主要的定位精基准,以两个小头孔外圆柱表面为辅助的定位精基准。
2.制定工艺路线根据零件的几何形状、尺寸精度及位置精度等技术要求,以及加工方法所能达到的经济精度,在生产纲领已确定的情况下,我们考虑采用万能性机床配以专用工卡具,并尽量使工序集中来提高生产率。
除此之外,还应当考虑经济效果,以便使生产成本尽量下降。
根据《机械制造工艺设计简明手册》,我们选择以下工艺路线方案:1.粗、精铣Φ32的上端面,以Φ32的外圆面为粗基准,采用X51立式铣床加专用夹具;2.钻、扩、铰、精铰Φ20孔,以Φ32的上端面为基准,采用Z525立式钻床加专用夹具;3.粗、精铣Φ32和Φ72的下端面,以Φ32的内圆面为基准。
采用X51立式铣床加专用夹具;4.粗、精铣Φ72的上端面,以Φ32的下端面为基准。
采用X51立式铣床加专用夹具;5.铣断,采用X60卧式铣床加专用夹具;6.粗、精镗Φ50孔,以Φ32的下端面为基准;7.钻Φ4通孔,钻M6孔;8.用三面刃铣刀铣斜槽面;3.机械加工余量、工序尺寸及毛皮尺寸的确定针对“CA6140车床拨叉”零件材料为HT200,硬度200HBW,毛坯重量1.2KG,生产类型大中批量,铸造毛坯的情况,我们需要确定各加工表面的机械加工余量、工序尺寸及毛坯尺寸。
1.外圆表面延轴线方向长度方向的加工余量及公差(φ20,φ50端面)根据《机械制造工艺设计简明手册》表2.2~2.5,我们取φ20、φ50端面长度余量均为2(双边加工)。
铣削加工余量为:粗铣1mm,精铣1mm。
2.内孔(φ50已铸成孔)根据《机械制造工艺设计简明手册》表2.2~2.5,我们取φ50已铸成孔长度余量为2,即铸成孔直径为φ46mm。
工序尺寸加工余量为:钻孔R9mm,扩孔0.125mm,粗铰0.035mm,精铰0.015mm。
3.其他尺寸直接铸造得到由于本设计规定的零件为大批量生产,应该采用调整加工。
因此在计算最大、最小加工余量时应按调整法加工方式予以确认。
加工尺寸及公差:离,零件尺寸为34mm。
加工前尺寸为34mm,加工后尺寸为30mm,18mm,19.7mm,19.8mm,19.94mm。
加工余量(单边)为2.0mm和0.85mm,加工公差(单边)为+0.021/0和0.07mm。
确定切削用量及基本工时:工序1为粗、精铣Φ32的上端面,以Φ32的外圆面为粗基准。
粗铣Φ32上端面的加工条件如下:1.工件材料为HT200,σb=170~240MPa,铸造;工件尺寸为aemax=72mm,L=176mm;加工要求为粗铣φ20孔上端面,加工余量1mm;机床为X51立式铣床;刀具为YG6硬质合金端铣刀。
铣削宽度ae≤90,深度ap≤6,齿数z=12.根据《机械制造工艺设计简明手册》(后简称《简明手册》)表3.1,取刀具直径dw=125mm。
根据《切削用量手册》(后简称《切削手册》)表3.16,选择刀具前角γ=0°后角α=8°,副后角α’=10°,刃倾角λs=-10°,主偏角Kr=60°,过渡刃Krε=30°,副偏角Kr’=5°。
2.切削用量1)确定切削深度ap,因为余量较小,故选择ap=1mm,一次走刀即可完成。
2)确定每齿进给量fz,由于本工序为粗加工,尺寸精度和表面质量可不考虑,从而可采用不对称端铣,以提高进给量提高加工效率。
根据《切削手册》表3.5,使用YG6硬质合金端铣刀加工,机床功率为4.5kw(据《简明手册》表4.2-35,X51立式铣床)时,fz=0.09~0.18mm/z。
故选择fz=0.18mm/z,f=fz*z=2.16mm/r。
3)确定刀具寿命及磨钝标准,根据《切削手册》表3.7,铣刀刀齿后刀面最大磨损量为1.5mm;由于铣刀直径dw=125mm,故刀具使用寿命T=180min(据《简明手册》表3.8)。
4)计算切削速度vc和每分钟进给量vf,根据《切削手册》表3.16,当dw=125mm,Z=12,ap≤7.5,fz≤0.18mm/z时,vt=98m/min,nt=250r/min,vft=471mm/min。
各修正系数为:kMV=1.0,kSV=0.8.切削速度计算公式为:vc≥cvd*wqvpvkvmTa*pxvfz*yv。
根据给定的数据,我们可以确定机床主轴转速为600r/min。
根据《简明手册》表4.2-36,选择nc300r/min,vfc390mm/min,因此实际进给量为118m/min。
根据《切削手册》表3.24,近似为Pcc=3.3kw,根据机床使用说明书,主轴允许功率Pcm=4.5×0.75kw=3.375kw>Pcc,校验合格。
最终确定ap4.0mm,nc300r/min,vf390mm/s,vc118m/min,fz0.1mm/z。
对于精铣Φ20上端面,我们选择YG6硬质合金端铣刀,机床为X51立式铣床。
根据《切削手册》表3.5,进给量f z可取0.5~1.0mm/min,我们选择f=6mm/r。
参考有关手册,确定切削速度为124m/min,dw为125mm,z为12,则可计算出ns316r/min。
由于我们采用的是X51立式铣床,根据《简明手册》表4.2-36,我们选择nw300r/min。
因此,实际切削速度为117.75m/min。
当nw300r/min时,工作台每分钟进给量为fmfzz×nw。
最后,我们可以根据给定的数据计算出基本工时为0.55min,其中L=176mm,y+Δ=40mm。
精铣时,每分钟的进给速度为1800mm,但我们将其取为980mm/min。
在精铣时,y+Δ=32+20×2=72(mm)。
因此,基本工时为t=72/980=0.07分钟。
接下来,我们需要进行钻孔和扩孔的工序。
在钻孔之前,需要选择合适的钻头。
我们使用Z525立式钻床,并根据《切削手册》表 2.1.2.2选择高速钢麻花钻钻头。
在粗钻时,钻头的直径为18mm。
此外,钻头采用双锥后磨横刀,后角αo=12°,二重刃长度bε=3.5mm,横刀长b=2mm,宽l=4mm,棱带长度l1=1.5mm,2Φ=100°,β=30°。
接下来,需要确定切削用量。
首先,我们需要确定进给量。
根据加工要求,进给量应为f=0.43~0.53mm/r,而ld=30/18=1.67<3.根据《切削手册》表2.7,系数为0.5,则f=(0.43~0.53)×0.5=(0.215~0.265)mm/r。
根据钻头强度和机床进给机构强度选择,我们得出受限制的进给量为0.215~0.265mm/r。
根据《简明手册》表4.2-16,最终选择进给量为f=0.22mm/r。
根据《切削手册》表2.19,钻孔时轴向力Ff=2500N,轴向力修正系数为1.0,因此Ff=2500N。
根据Z525立式钻床使用说明书,机床进给机构允许的最大轴向力为8830N>Ff,所选进给量可用。
接下来,需要确定钻头磨钝标准及寿命。
后刀面最大磨损限度(查《简明手册》)为0.6mm,寿命T=45min。
最后,需要确定切削速度。
根据《切削手册》表2.30,切削速度计算公式为:cv=dzv/(mxvTa*pfyv*kv)(m/min)。
其中,Cv=9.5,d=18mm,zv=0.25,m=0.125,ap=9,xv=0,yv=0.55,f=0.22.查得修正系数:kTv=1,kv=0.85,ktv=1.因此,实际的切削速度为9.5×18.25/(0.125×0.85)=9.5m/min。
此时,转速为168r/min,但工艺手册要求为184r/min。
最后,需要检验机床扭矩及功率。
2.计算铣削参数根据工件材料和加工要求,选择合适的切削参数。
查《切削手册》表2.12,当切削深度ap≤2mm时,选用铣削切削力系数Kc=1.07,修正系数均为1.0,故铣削切削力Fc=Kc·ap·ae·f=1.07·2·72·0.2=30.912N。
根据机床使用说明书,功率系数Kp=0.75,故铣削功率Pc=Fc·vc·η·Kp=30.912·0.35·0.85·0.75=5.18W。
3.计算工时根据工件尺寸和加工要求,确定铣削长度为L=72mm,加工余量为1mm,故铣削长度为L1=71mm。
根据铣削进给量f=0.2mm/r,计算铣削速度vc=fn·z·π·dw=0.2·2·3.14·32=40.192mm/min。
根据铣削长度和铣削速度,计算铣削工时tm=L1/vc=71/40.192=1.766min。
4.精铣Φ32、Φ72下端面1.加工条件工件材料、尺寸和加工要求同上。
2.计算铣削参数根据工件材料和加工要求,选择合适的切削参数。
查《切削手册》表2.12,当切削深度ap≤0.5mm时,选用铣削切削力系数Kc=0.8,修正系数均为1.0,故铣削切削力Fc=Kc·ap·ae·f=0.8·0.5·72·0.1=2.88N。
根据机床使用说明书,功率系数Kp=0.75,故铣削功率Pc=Fc·vc·η·Kp=2.88·0.35·0.85·0.75=0.343W。
3.计算工时根据工件尺寸和加工要求,确定铣削长度为L=72mm,加工余量为0.2mm,故铣削长度为L1=71.8mm。
根据铣削进给量f=0.1mm/r,计算铣削速度vc=fn·z·π·dw=0.1·2·3.14·32=20.096mm/min。