辊压机水泥半终粉磨工艺系统调试
钢铁渣辊压机终粉磨系统关键参数调试与优化

钢铁渣辊压机终粉磨系统关键参数调试与优化
耿鹏浩;田俊琪;邵明凯;代伟林
【期刊名称】《新世纪水泥导报》
【年(卷),期】2024(30)1
【摘要】辊压机终粉磨系统粉磨钢铁渣(钢渣+矿渣),调试期间关键控制参数有V 型选粉机出口温度、工艺收尘器出口温度、加湿搅拌机喷水量、中间仓仓重等,关键指标参数有辊缝、辊子电流、V型选粉机、动态选粉机压差、成品比表面积及活性等。
对这些重要参数进行调整及优化,最终使产品比表面积稳定在440
m^(2)/kg,系统产量稳定在100 t/h(干基),粉磨系统电耗小于39 kWh/t,系统热耗小于401280 kJ/t。
【总页数】3页(P35-37)
【作者】耿鹏浩;田俊琪;邵明凯;代伟林
【作者单位】中信重工工程技术有限责任公司
【正文语种】中文
【中图分类】TQ172.632
【相关文献】
1.辊压机生料终粉磨系统的推广及生产调试
2.辊压机终粉磨系统生产钢铁渣粉工艺设计及优化
3.辊压机终粉磨系统在生产钢铁渣微粉上的应用
4.生料辊压机终粉磨系统的调试与优化探讨
5.TRP220-160辊压机半终粉磨系统粉磨水泥运转调试
因版权原因,仅展示原文概要,查看原文内容请购买。
辊压机终粉磨工艺

辊压机终粉磨工艺辊压机是一种常用的粉磨设备,它通过辊子的相互挤压和磨擦,将原料磨成所需细度的粉末。
在辊压机的终粉磨工艺中,主要包括以下几个方面:1. 原料配料终粉磨的原料配比要根据所需产品规格和质量要求进行调整。
一般情况下,终粉磨的原料主要包括水泥熟料、矿渣、石膏和适量的掺合料。
在原料配料时,要根据原料的性质和特点进行合理搭配,保证所配制的原料能够满足终粉磨的要求。
2. 清洗和检查辊子在进行终粉磨前,应清洗和检查辊子。
清洗辊子的目的是去除表面的沉淀物和杂质,从而避免对磨辊的磨损和影响产品质量。
检查辊子的目的是查看辊子是否存在磨损、裂纹等缺陷,从而及时进行维护和更换。
3. 调节磨辊压力和间隙磨辊压力和间隙对于终粉磨的质量和效率有很大的影响。
一般情况下,磨辊的压力应该适中,不宜过大或过小。
太大会使得磨辊的磨损加剧,太小会影响磨辊的磨磨能力和产品的细度。
同时,磨辊间隙也需要根据产品的要求进行调节,以保证产品能够满足规格和质量要求。
4. 控制辊压机运行参数在终粉磨的过程中,需要对辊压机的运行参数进行控制,以保证产品的质量稳定和生产效率。
具体而言,需要控制的参数包括磨辊转速、进料速度、加热温度等。
5. 对成品进行筛分和风送终粉磨完成后,需要对成品进行筛分和风送。
筛分是为了控制产品粒度和分布;风送是为了将成品送入收集器或储存罐中。
同时,也需要对成品进行化验和检查,以确认产品的质量符合要求。
总之,辊压机终粉磨工艺是一个比较复杂和关键的过程,需要对各个环节进行精心设计和控制,以保证产品质量和生产效率。
同时,在进行终粉磨时,还需要注意安全生产和节能减排,以实现可持续发展。
小型辊压机联合粉磨系统改为半终粉磨系统的经验

小型辊压机联合粉磨系统改为半终粉磨系统的经验浙江胥口有一条2500t/d 水泥熟料生产线和一条GLF140-65辊压机+直径3.8×13m 球磨机双闭路联合水泥粉磨系统。
胥口于2014年2月将水泥磨联合粉磨工艺改为水泥磨半终粉磨工艺,取得了较好的增产节能效果。
1、技改前的基本情况 1.1 工艺流程及主机设备粉磨系统采用的是国内水泥企业较为普遍的双闭路联合粉磨工艺,工艺流程图见图1,主机设备见表1。
图1 改造前的双闭路联合粉磨工艺表1:技改前主机设备 1.2、存在的主要问题参照国内其他厂家的改造经验,检查胥口南方粉磨系统实际情况,该系统中主要存在以下问题:1、辊压机预磨系统的旋风收尘器入磨的物料中存在有20-30%的30μm 及以下的合格品,在磨内产生过粉磨现象,降低了磨机的粉磨效率。
序号 设备名称 规格、型号及主要参数1 水泥磨机 Ø3.8×13m 两仓水泥磨,电机功率2800kw2 辊压机 GLF140-65 , 通过能力380-480t/h ,电机功率 2×500kw3 V 型选粉机 VX5810,能力450t/h , 处理风量 15000m3/h4辊压机 循环风机 处理风量150000 m3/h ,全压4000Pa, 电机功率200kw5 O-Sepa 选粉机 N2500,处理能力90-150 t/h ,电机功率132kw 6磨内通风风机处理风量50000 m3/h ,全压4000Pa, 电机功率110kw2、磨内物料细度(0.08mm筛筛余)从磨头的20.98%到磨尾的8.12%,只降低了13%;比表面积从磨头的135m2/kg到磨尾的156m2/kg,只增加了21m2/kg,显然粉磨效率是比较低的。
2、改造措施2.1 基本思路采取半终粉磨工艺,在保证水泥质量的前提下,将预粉磨系统中的部分合格细粉通过选粉机分选出来,直接通过斜槽输送入水泥库。
按照其它厂家的经验,采取半终粉磨工艺时,辊压机的装机功率与磨机装机功率的比要大于0.6,而该系统中辊压机的装机功率与磨机装机功率的比只有0.357。
水泥粉磨系统辊压机操作控制的几点经验

平 均 采 购价 格 37 4 / 算 ,购 买 助磨 剂 费 用 为 4 冗 t 计 197 万元 。抵 消液 体 助磨 剂成 本及 研 发成 本 等费 4. 6 用 后 ,全年 可增 加直接 经 济效益 5.4 02万元 。
观察 ,发 现边 料溜 子物 料多 且下不 及 ,物料堆 积 到
分料 阀转 轴 附近 ,从分 料 阀的转 轴下部 串人成 品溜
子。
动辊 固定辊
/ /
动 、定 辊
图 1 动 辊 侧 挡 料 调 节 板 的 原 位 置
动辊侧 挡料 调节 板
/ \ ) / /
l\/
辊 缝 的 限制 ,液压 缸 内 的液压 油 的体 积 是一 定 的 , 辊 缝 增大 ,液压缸 被 压缩 ,油 压也 达不 到 作压 力 丁 一
82 M Pa。 .
量提高了1. 31 %,系统粉磨电耗降低 了1. 6 %。 6
( 收稿 日期 :2 1— 10 ) 020— 8
由于初 始辊缝 决定 液压缸 的体积 ,初始 辊缝 确定为1 r  ̄ 0mn ,液压缸体积不变 ,工作辊缝一般 N 为2 m~ 8m 6m 2 m,变化不大。因此我们认为初 始
经 过辊 压 机 动 、定 辊 碾 压 的物 料 形 成 料饼 , 在 两 辊 间 的下 部 出来 ,由于 两 辊 间 进 料 充 分 ,物 料被 碾压 的效 果好 ,边 部 的物料碾 压效 果不及 中部
物料 , 分料阀的作用是将碾压效果好与不好的物料
进 行 分离 ( 3)。由于 一 直认 为 分料 阀开度 越 小 图 越 好 ,故一 度将 分料 阀开度 调整 到2 %,结果 成 品 0 中一直 含有 1 左 右 的粗 物料 。打 开辊 压机 侧 门 0mm
辊压机联合粉磨工艺系统分析

辊压机联合粉磨工艺系统分析辊压机联合粉磨(或半终粉磨)工艺系统,其技术核心在本质上属于“分段粉磨”。
目前,国内水泥制成工序广泛应用由辊压机+打散分级机(动态分级设备)或V型选粉机(静态分级设备)+管磨机开路(或配用高效选粉机组成双闭路)组成的联合粉磨工艺系统(或由辊压机+V型选粉机(静态分级设备)+高效选粉机+管磨机组成的半终粉磨工艺系统),在实际运行过程中,由于各线生产工艺流程及设备配置、物料粉磨特性、水份等方面因素不尽相同,导致系统产量、质量及粉磨电耗等技术经济指标也参差不齐,本文拟对水泥联合粉磨单闭路(管磨机为开路)及双闭路系统(或半终粉磨系统)中各段常出现的工艺技术与设备故障模式进行探讨分析,并提出了相应的解决办法,仅供粉磨工程技术人员在日常工作中参考,文章中谬误之处恳望予以批评指正:一、辊压机系统故障模式:辊压机挤压效果差故障原因1:1. 被挤压物料中的细粉过多,辊压机运行辊缝小,工作压力低影响分析:辊压机作为高压料床(流动料床)粉磨设备,其最大特点是挤压力高(>150Mpa),粉磨效率高,是管磨机的3-4倍,预处理物料通过量大,能够与分级和选粉设备配置用于生料终粉磨系统。
但由于产品粒度分布窄、颗粒形貌不合理及凝结时间过快、标准稠度需水量大与混凝土外加剂相容性差等工作性能参数方面的原因,国内水泥制备工艺未采用辊压机终粉磨系统,辊压机只在水泥联合粉磨系统中承担半终粉磨(预粉磨)的任务,经施以双辊之间的高压力挤压后的物料,其内部结构产生大量的晶格裂纹及微观缺陷、<2.0mm及以下颗粒与<80um细粉含量增多(颗粒裂纹与粒度效应),分级后的入磨物料粉磨功指数显著下降(15-25%),易磨性明显改善;因后续管磨机一仓破碎功能被移至磨前,相当于延长了管磨机细磨仓,从而大幅度提高了系统产量,降低粉磨电耗。
但辊压机作业过程中对入机物料粒度及均匀性非常敏感,粒状料挤压效果好、粉状料挤压效果差,即有“挤粗不挤细”的料床粉磨特性;当入机物料中细粉料量多时会造成辊压机实际运行辊缝小,主电机出力少,工作压力低,若不及时调整,则挤压效果会变差、系统电耗增加。
洪堡RPZ10140110辊压机系统的优化调整

刘广铎,等:洪堡R P-Z10-140/11辊压机系统的优化调整工艺装备中图分类号:TQ172& 文献标志码:(文章编号=1007-0389 (2019) 01-61-02 【D01】10.13697/ki.32-1449/tu.2019.01.025洪堡RP-Z10-140/110辊压机系统的优化调整刘广铎,于海涛(河北金隅鼎鑫水泥有限公司,河北石家庄050200)0前言我公司水泥磨2003年投产,拥有两条双闭路粉 磨系统。
2012年拆除原有设计六管旋风收尘器,增 加TAS3000侧进风选粉机,将系统更改为半终粉磨 系统。
由于洪堡辊压机投入使用较早,应用水泥系 统存在一定缺陷,加之窑系统超产等原因熟料易磨 性相对不稳定,结粒普遍较差,并且熟料温度年均 180+以上,辊压机做功一直偏差;磨机型号为4.2 mxl1.短磨,有效利用率偏低,造成系统能耗一 直偏高。
2017年8月我公司通过一系列调整使辊压 机做功显著好转,系统台时得到大幅度提高。
1系统改造前存在的问题该系统工艺流程及主要设备表见图1表1。
我 公司辊压机大部分时间运行功率仅为设计能力的 50%,加之辊压机设计能力相较于磨机本身偏小,不 能很好的发挥联合粉磨的优势,此外磨机规格长径 比偏小,做功死角占比偏大。
通过对系统长期观察 摸索,总结问题如下。
设备名称规格型号设计能力电机功率/kW 辊压机RP-Z10-140/110490 〜600t/h2x710V型选粉机VS96/20入磨选粉机TAS3000330 t/h155磨机94.2mXllm140 t/h28高效动态选粉机N3000〇-sepa140 t/h16系统排风机Y6-40-11180000m3/h63循环风机Y4-73-11180 000 m3/h28(1)喂料投影的位置不合理。
我公司用洪堡辊压机为设计较早的型号,采用偏定辊设计,物料完全落在定辊上,通过辊子转动将物料带入拉入角,喂料插板通过两条螺旋丝杠进行上下垂直调节,改造前后见图2。
不同水泥粉磨系统调试及改进效果
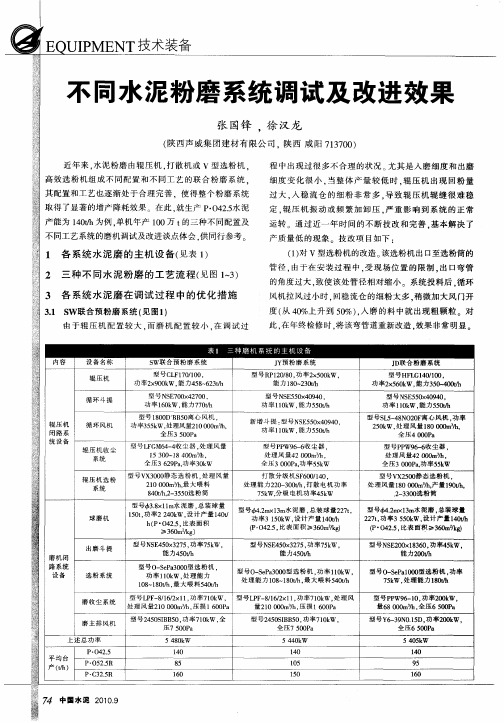
能 力 10 20/ 8 ~ 3t h
型 号 N E 5 x 04 S 5 0 4 9 0. 功率 1O W . 力5 0/ lk 能 5t h 新增 斗 提 型 号NS 5 0 4 9 0. E5 ̄04
:
功 率2 5 0 W 。 力 3 0 4 0/ x6k 能 5~0t h
型号 N E 5  ̄ 0 4 S 5 0 4 9 0. 功 率 1O W . 力 50/ lk 能 5t h
循 环 斗 提 型号 N E 0 x 2 0 . S 7 0 4 7 0 功 率 10 W . 力 7 0/ 6k 能 7t h 型号 1 0 D B 5 离心 风 机 . 80 B0 功 率3 5 W. 5 k 处理 风量2 0O 0 S 1 m/ 0 h 全 压 35 0 a 0 P
全压 3O0 a 率 5 k 0 P . 功 5 W
型号V 20静态选粉机 . X 50 处 理 风 量 10O 0 S , 8 0 m/ 产 ̄'9 t , h 10 h / .- 3 0 粉 筒 230选 型号 似 .m 1 m 泥 磨 , 装球 量 2 ̄3水 总 2 7 , 率350 W . 计 产 量 10/ 2 t功 5k 设 4t h ( 0 25 比表面积 >30 /g P。 4 ., _ 6mZ ) - k  ̄ - S 2 0 13 0 功 率4 k 。 N E 0x86 , 5W 能 力2 0/ 0t h
,
取得 了显著 的增产 降耗效 果 。在 此 , 就生 产 P 0 2 水 泥 ・4. 5 产能 为 10 h 例 , 机年 产 10万 t 三种 不 同配 置 及 4t 为 / 单 0 的 不 同工艺 系 统 的磨机 调试 及 改进 谈 点体 会 , 同行 参考 。 供
辊压机及其挤压粉磨工艺系统的操作

辊压机及其挤压粉磨工艺系统的操作1 前言挤压粉磨工艺是国际八十年代中期新开发的新型节能粉磨技术。
自1990年江苏省江阴市水泥厂国内第一台辊压机投产以来,在我国生产实际中应用已有多年的历史。
截止1995年11月的不完全统计,国内销售近二百台辊压机,已投产也有一百多台。
正如所有的新技术那样,辊压机在推广应用初期无论从设备还是工艺,都存在逐步认识与完善的过程,而经过几年的使用,经验得到积累,技术日臻完善。
随着辊面结构的改进和新技术新材料的应用,辊面磨损修复问题已逐步得到解决。
伴随着不同工艺系统的研究开发,挤压粉磨工艺的各项技术经济指标大幅度提高。
辊压机的操作方式也由于不同工艺流程,不同的物料情况,不同的设备配置方式而发生较大的变化,其突出特点之一就是在相同主电机功率条件下,辊压机液压系统的操作压力,料饼的厚度以及各种回料循环量等参数间的调节。
由压力和物料循环量的不同形成低压大循环和高压小循环为特征的操作方式。
辊压机设计参数之一就是单位辊宽线压力值,对Φ1000辊径的辊压机,单位辊宽线压力设计值为100kN/cm,正常操作在(40-80)kN/cm之间。
所谓低压一般为(40~60)kN/cm,高压为(60-80)kN/cm。
本文就不同情况下辊压机及其在不同工艺系统中的操作方式谈一些体会,以供使用辊压机的厂家参考。
2 辊压机操作参数的调整及其影响当一台辊压机应用于具体的工艺生产线中时,其规格参数,包括辊面形状、辊宽、线速度、装机功率以及液压系统最大操作压力均已确定。
喂入辊压机新鲜物料的物性,包括物料的形状、强度、温度、最大粒度、平均粒径及颗粒分布状况都已基本定型。
因而此时辊压机可以调整的参数,实际只有液压系统压力和辊压机出料的料饼厚度(即通过量)。
为不使主电动机的运行电流超过其额定电流,还必须对这两个参数的调整加以控制。
如果假设辊压机主电机电流保持不变,则液压系统的压力与料饼厚度呈反比例关系。
即增大通过量,增大料饼厚度,就必须降低液压系统的操作压力。
- 1、下载文档前请自行甄别文档内容的完整性,平台不提供额外的编辑、内容补充、找答案等附加服务。
- 2、"仅部分预览"的文档,不可在线预览部分如存在完整性等问题,可反馈申请退款(可完整预览的文档不适用该条件!)。
- 3、如文档侵犯您的权益,请联系客服反馈,我们会尽快为您处理(人工客服工作时间:9:00-18:30)。
辊压机水泥半终粉磨工艺系统增产调试 邹伟斌 中国建材工业经济研究会水泥专业委员会(100024) 邹 捷 南京工业大学粉体科学与工程研究所 (210009)
题要:本文总结了ZC公司5000t/d新型干法水泥熟料生产线,水泥制成工序采用辊压机、V型静态选粉机、双分离高效选粉机、双仓管磨机组成的半终粉磨闭路工艺系统增产调试过程,调整中以“分段粉磨”理论及系统工程方法为指导依据,并对粉磨系统中各段存在的技术问题进行了诊断分析,制定并实施了相应的改进措施,充分挖掘粉磨系统中每一段生产潜力,最终达到增产、降耗的目的。 关键词:辊压机 半终粉磨系统 双分离高效选粉机 增产调试
1. 水泥粉磨工艺线基本概况 ZC公司5000t/d新型干法水泥熟料生产线,两套水泥成品制备系统均配用160-140辊压机+V型静态分级机(V型选粉机)+双分离高效选粉机+Φ4.2×13m双仓管磨机组成的半终粉磨闭路工艺;其具体工艺流程为:物料经过配料站由高速板链斗式提升机输送至稳流称重仓,进入辊压机挤压后通过V型选粉机分级出细粉(<80um以下颗粒占70%-85%、<45um以下水泥成品颗粒所占比例约为55%以上),V型选粉机细粉出口联接下进风的双分离高效选粉机(负压抽吸式进入高浓度布袋收尘器收集成品),首先分离出由辊压机挤压过程中产生的成品,分选出成品后的粗粉输送至管磨机粉磨,出磨物料经输送设备由上部喂入双分离高效选粉机再次分选。在辊压机、管磨机两段正常运行后,双分离高效选粉机承受下部(V选出口)及上部(由管磨机磨尾输送的)两股料流,同时进行分选。我们可以将辊压机水泥半终粉磨工艺系统理解为:它是传统联合粉磨工艺系统的另一个变种,辊压机半终粉磨工艺系统与辊压机联合粉磨工艺系统各有其技术特点、均可使粉磨系统增产能力达到70%-200%甚至200%以上、节电幅度达20%-30%。 该半终粉磨工艺系统与传统联合粉磨工艺系统相比,须采用一台物料处理能力较大的辊压机和一台喂料、分选能力大的下进风双分离高效选粉机,V型选粉机与双分离高效选粉机则共用一台系统风机,取消了联合粉磨系统中一台循环风机与旋风收尘器(双旋风筒或单旋风筒)及部分管道和输送设备,减少了设备数量及维护点,维修成本降低。此外,该半终粉磨系统中直接采用高浓度布袋收尘器收集由辊压机段挤压所产生的及管磨机段粉磨后生产的水泥成品,避免了大量<45um细粉进入管磨机内部,导致细磨仓出现“过粉磨”所引起的研磨体及衬板表面严重粘附现象,使管磨机系统始终保持较高而稳定的粉磨效率。 由于水泥成品经过高浓度布袋收尘器收集,后续管道与系统风机中的粉尘浓度显著降低,彻底消除了传统联合粉磨工艺系统中导致管道与循环风机叶轮磨损严重的因素,降低了系统设备磨损并减少了装机功率,设备磨耗量明显降低、整个系统粉磨电耗低。 该系统的管磨机段既可由闭路粉磨流程转换为开路粉磨流程、亦可由开路粉磨流程转换为闭路粉磨流程,实现了一套粉磨系统可开、可闭的灵活转换与调节,转换操作简单、快捷。 在辊压机水泥半终粉磨工艺系统中,当后续管磨机系统为开路方式操作时,即辊压机段创造的成品与开路管磨机粉磨系统生产的成品共同混合入库,成品颗粒级配范围比闭路操作时要宽; 当后续管磨机系统为闭路方式操作时,即辊压机段创造的成品与闭路管磨机粉磨系统生产的成品共同混合入库,成品颗粒级配范围仍然比开路操作时要窄,且由辊压机制造的水泥颗粒球形度非常低,其颗粒形貌多呈不规则的长条状、多角形等;采用辊压机高效率料床粉磨设备制得的水泥颗粒分布范围相对集中(窄),即颗粒粒径更均匀,均匀性系数n值增大,颗粒之间空隙增多,水泥粉体颗粒堆积密度就小,难以形成最紧密堆积,当达到相同流动度时需要多加水,水则变成了填充物,充填于水泥颗粒之间的空隙、穴道,导致水泥标准稠度需水量增大;水泥制成系统的粉磨效率越高,对增产、节电越有利,但成品水泥需水量增大现象则会越突出,这就是造成半终粉磨闭路工艺系统水泥标准稠度需水量偏大的主要原因之一;此外,该系统因辊压机段挤压生产的水泥中≤5um以下微细颗粒含量较高、成品水泥比表面积与抗压强度一般均偏高,为综合利用工业废弃物,大掺量制备复合水泥、降低水泥生产成本创造了先决条件,但该粉磨系统应用中须权衡水泥使用性能与系统高效、增产、节电等几个方面的关系,并对系统中相关控制参数、管磨机内部结构以及所用混合材料品种等做出相应调整,以使水泥成品性能满足混凝土制备技术要求。 该系统中管磨机磨尾配置有单独的通风、收尘设备,收尘风机采用变频调速控制,便于生产过程中磨内通风量的调节与操作。(系统工艺流程见图一) 辊压机水泥半终粉磨工艺系统主辅、机设备配置及技术性能参数见表1: 表1 水泥半终粉磨工艺系统主、辅机设备配置及技术性能参数 主、辅机设备名称 设备技术性能参数 辊压机 型号160-140、辊径1600mm、辊宽1400mm、物料通过量≥780t/h,、主电机功率1120kw×2、入料粒度≤50mm(≥95%) V型选粉机 喂料能力≥960t/h、选粉风量240000-260000m3/h、风压1.5-2.0KPa 双分离高效选粉机 喂料能力≥680t/h、选粉能力≥200t/h、主电机功率200kw
高速板链提升机 型号NSE900P、提升能力≥950t/h、电机功率160kw 高速链式提升机 型号NSE900、提升能力750t/h-1000t/h、电机功率160kw 系统风机 风量280000m3/h-310000m3/h、风压7800Pa、风机电机功 率900kw 管磨机 规格Φ4.2×13m(双滑履中心传动)、筒体工作转速15.6r/min、设计研磨体装载量234t、主电机功率10KV-3550KW(额定电流243A、配置进相器)、设计产量180t/h 主减速器 型号JS150B、速比i=47.295:1 磨尾提升机 型号ZYL1100,物料提升量690t/h,功率110KW
磨尾收尘风机 型号Y5-48NO12.5D 、风量59000 m3/h 、全压4000Pa 、风机电机功率110kW(变频调速) 磨尾袋收尘器 型号LFGM96-9、处理风量60000 m3/h、总过滤面积836㎡ 气箱脉冲收尘器 型号LFGM128-2×16、总过滤面积5100m2、处理风量290000m3/h、人口浓度≤1300g/Nm3、出口浓度30≤mg/Nm3 成品入库提升机 型号NSE300、提升能力>250t/h、电机功率45kw
图一 水泥半终粉磨闭路工艺系统流程图 2. 生产调试中遇到的问题 2.1辊压机工作辊缝较小 投产调整初期,由于入辊压机熟料中含有较多黄心、粉料,导致工作辊缝偏小,只有28mm左右,辊压机主电机工作电流较低(46A左右),即使调节入料斜插板比例(75%左右),工作电流变化不大,辊压机挤压出力能力较差。 2.2辊压机工作压力偏低 受辊压机工作辊缝偏小的影响,工作压力上不去,挤压效果较差,辊压机工作压力在8.5MPa左右波动,挤压后细粉明显偏少。 2.3脱硫石膏水份大 由于入辊压机的脱硫石膏水份达到8%-12%不易下料、计量,称重仓粘附、挂壁现象严重,甚至造成挤压后的料饼进入V型选粉机内部不易散开,影响分级效果。 2.4管磨机做功能力差 由双分离高效选粉机分离出成品后的入磨物料(粗粉)比表面积平均在100m2/kg(95m2/kg ---105m2/kg)左右,而在管磨机有效长度12.5m范围内研磨体做功少,出磨水泥比表面积仅在185m2/kg左右,计算得知:每米研磨体粉磨出的比表面积为185m2/kg-100m2/kg/12.5m=6.8m2/kg/m,说明管磨机段研磨能力不足; 一般来讲,带有双分离高效选粉机的水泥半终粉磨系统,由于预先分离出成品,入磨物料中的细粉量极大地减少,较好地避免了细粉在磨内产生的“过粉磨”与细磨仓研磨体与衬板表面粘附现象,研磨体磨细做功能力提高,每米研磨体创造出磨物料比表面积能力至少应≥10m2/kg/m; 2.5两台选粉机用风量小 因处于设备磨合期,辊压机段与管磨机段做功能力均不理想,即挤压处理与研磨两段的成品量不足,以致不能增加V选与双分离高效选粉机拉风量,一般在80%-85%左右。中控操作增加系统风机风量时,造成水泥成品比表面积低、细度粗;由此判断:辊压机与管磨机两段创造成品量低时,系统风机拉风量必须降低,最终导致系统产量低、电耗较高; 3. 技术分析及处理措施 3.1辊压机工作压力及辊缝 高压、慢速、过饱和喂料是辊压机料床挤压粉磨技术特性,除国外粉磨生产线设计、应用辊压机水泥终粉磨工艺(国内目前只应用于生料终粉磨,节电效果显著),在国内水泥制成工序辊压机只是在水泥联合粉磨系统中承担半终粉磨(或预粉磨)的任务,经施以双辊之间的高压力(≥150MPa)挤压后的物料,其内部结构产生大量的晶格裂纹及微观缺陷、<2.0mm及以下颗粒达到65%以上,其中<80um、<45um以下细粉含量增多(颗粒裂纹与粒度效应),分级后的入磨物料粉磨功指数显著下降(15%-25%),易磨性明显改善;因后续管磨机一仓破碎功能被移至磨前,相当于延长了管磨机细磨仓,可充分发挥研磨体对物料的磨细能力,从而大幅度提高了系统产量,降低系统粉磨电耗。 辊压机水泥半终粉磨工艺系统(或联合粉磨工艺系统)的共同特点是:辊压机及分级设备的投入,实现了系统中的“分段粉磨”,必须充分发挥辊压机系统料床粉磨的技术优势及其较大的处理能力,辊压机段做功越多,对系统增产节电越有利;辊压机的吸收功耗越多,后续管磨机段节电效果越显著;辊压机吸收功耗一般在7.5kwh/t-13kwh/t,在此范围内吸收功耗越多,管磨机段节电幅度越大。基本规律是:辊压机吸收功多投入1kwh/t,则后续管磨机系统节电1.5kwh/t--2kwh/t; 在相对稳定的工艺条件下,辊压机工作压力越大,挤压处理物料过程中产生的粉料越多,成品量显著增加,被分离出的合格品也越多。 首先,对入辊压机熟料采取多库搭配措施,多采用颗粒状、减少粉状料;其次,称重仓必须保持一定的仓容,料位比例一般控制在70%-80%,以有效形成入机料压,实现过饱和喂料,确保挤压效果;同时将辊压机工作压力由8.0MPa-9.0MPa,调整至10.0MPa-11.0MPa;辊压机工作辊缝由原27mm--29mm,调整至30mm--34mm;入料斜插板比例拉开至85%以上,以实现过饱和喂料;调整后辊压机主电机工作电流(额定电流76A)由44A--50A(58%-66%)提高至54A--60A(71%--79%)挤压做功能力显著提高,经由V型选粉机分级后的物料R80um、R45um筛余量明显减少,比表面积提高,合格品比例大幅度增加。 3.2脱硫石膏水份及下料处理 进厂脱硫石膏水份较大,实施入堆棚预先存放措施、分批周转取用。将存放较长时间且含有一定水份(<5%)的脱硫石膏与颗粒较大的石灰石按照一定比例搭配(1:1)混匀入配料库,库壁内锥体及筒体内壁部分采用表面光洁度优良、耐磨性能良好的超高分子量聚乙烯板敷贴,处理后库壁光滑、物料不粘壁,下料效果较好; 3.3V型选粉机及双分离高效选粉机用风量, 在半终粉磨系统中,由于V型选粉机与双分离高效选粉机两台粗、细分级设备共用一台高浓度布袋收尘器和一台系统风机,在满足水泥质量控制指标的前提下,应尽量采用大风操作方式,最大程度上将辊压机段及管磨机段创造的成品分选出来,系统风机的拉风比例由原85%提高至90%以上(根据实际生产状况,在V型选粉机入料口上方增设打散棒,以形成均匀、分散的料幕;同时关闭了最上部一排进、出风导流板,有效延长物料分级路线与分级时间,提高V选出口物料的比表面积)。 3.4管磨机研磨体级配及通风参数 管磨机的特点是磨细能力有余而粗碎能力较差,而由辊压机+V型静态分级设备组成的磨前预粉磨系统,能够充分发挥辊压机高效率料床粉磨优势,高压挤