煤矿用钻杆断裂原因解决措施
非开挖导向、定向钻杆的失效原因

非开挖导向、定向钻进用钻杆的失效原因及解决措施前言钻杆最可怕的失效形式是钻杆的断裂。
钻杆在导向、定向钻进铺管过程中一旦断裂,将会对工程造成严重影响,不仅是经济上的损失,而且影响工期,失去信誉,后果不堪设想。
因此,作为施工企业,一定要学会如何正确地选择和使用钻杆;而作为钻杆生产厂家,要知道非开挖工程对钻杆的特殊要求,生产出高强度、高弹性和高可靠性的钻杆。
笔者在1994年至1998年间曾带队做过多项导向钻进非开挖铺管工程,尽管当时的钻杆质量非常差,但在施工过程中从未遇到断钻杆事故。
后来,笔者从事非开挖工艺和钻具的研究、设计工作,此期间也是我国非开挖铺管技术迅猛发展的时期,时常有施工单位报告钻杆断裂事故,总觉得有些费解。
于是,笔者亲身在施工现场调查了多起事故原因,同时设计了多种结构形式的钻杆进行试验。
通过多年的事故分析和试验研究,总结出一些钻杆失效(主要是断裂)产生的原因:除钻杆自身质量问题外,施工中不当的操作是使钻杆失效的主要原因。
笔者撰写此文旨在避免施工企业重复走弯路,也算作为我国非开挖技术的发展做一点贡献。
一、钻杆主要失效形式及原因分析非开挖导向、定向钻进用钻杆往往在受到较大拉力和扭力作用的同时,还受到弯曲力的作用。
钻杆通过曲线段时,钻杆被迫弯曲,弧线内侧受压应力作用,弧线外侧受拉应力作用。
当钻杆在曲线段旋转时,杆体就受到拉压交变应力的作力,而钻孔曲率半径越小交变应力就越大。
研究表明这个交变应力达到一定值后,就极容易使钻杆产生疲劳裂纹。
钻杆刚开始产生的疲劳裂纹非常微小,肉眼很难发现,但疲劳裂纹发展速度极快,最后表现为突然的脆性断裂。
试验证明,钻杆受交变应力作用而疲劳断裂是非开挖钻杆断裂失效的主要原因。
很多钻杆在施工导向孔时发生断裂事故就佐证了这一结论。
目前我国的非开挖施工队伍有很多是经验丰富素质高的专业公司,但更多的是临时拼凑起来的没有任何施工经验和技术的队伍,他们往往连钻杆(或钻孔)的曲率半径都没听说过,让他们来指挥非开挖施工是造成钻杆断裂的人为方面的主要原因。
钻具常见失效形式
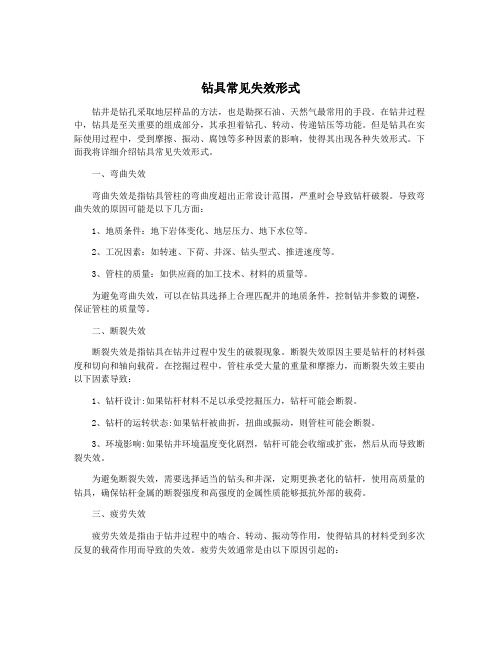
钻具常见失效形式钻井是钻孔采取地层样品的方法,也是勘探石油、天然气最常用的手段。
在钻井过程中,钻具是至关重要的组成部分,其承担着钻孔、转动、传递钻压等功能。
但是钻具在实际使用过程中,受到摩擦、振动、腐蚀等多种因素的影响,使得其出现各种失效形式。
下面我将详细介绍钻具常见失效形式。
一、弯曲失效弯曲失效是指钻具管柱的弯曲度超出正常设计范围,严重时会导致钻杆破裂。
导致弯曲失效的原因可能是以下几方面:1、地质条件:地下岩体变化、地层压力、地下水位等。
2、工况因素:如转速、下荷、井深、钻头型式、推进速度等。
3、管柱的质量:如供应商的加工技术、材料的质量等。
为避免弯曲失效,可以在钻具选择上合理匹配井的地质条件,控制钻井参数的调整,保证管柱的质量等。
二、断裂失效断裂失效是指钻具在钻井过程中发生的破裂现象。
断裂失效原因主要是钻杆的材料强度和切向和轴向载荷。
在挖掘过程中,管柱承受大量的重量和摩擦力,而断裂失效主要由以下因素导致:1、钻杆设计:如果钻杆材料不足以承受挖掘压力,钻杆可能会断裂。
2、钻杆的运转状态:如果钻杆被曲折,扭曲或振动,则管柱可能会断裂。
3、环境影响:如果钻井环境温度变化剧烈,钻杆可能会收缩或扩张,然后从而导致断裂失效。
为避免断裂失效,需要选择适当的钻头和井深,定期更换老化的钻杆,使用高质量的钻具,确保钻杆金属的断裂强度和高强度的金属性质能够抵抗外部的载荷。
三、疲劳失效疲劳失效是指由于钻井过程中的啮合、转动、振动等作用,使得钻具的材料受到多次反复的载荷作用而导致的失效。
疲劳失效通常是由以下原因引起的:1、超负荷:如果管柱承受超出其载荷极限的应力,随着时间的推移,它们将在高载荷情况下疲劳。
2、变形:如果管柱在钻井过程中出现变形,如扭曲、振动等,其疲劳极限会降低。
3、环境因素:诸如温度、酸碱性等环境因素可能导致钻具的材料受到损害。
为了避免疲劳失效,以下是几个重要的措施:1、选择尽可能高的钻杆金属强度。
2、控制切削转速,减少外部载荷情况下的功率。
钻具失效断裂浅谈
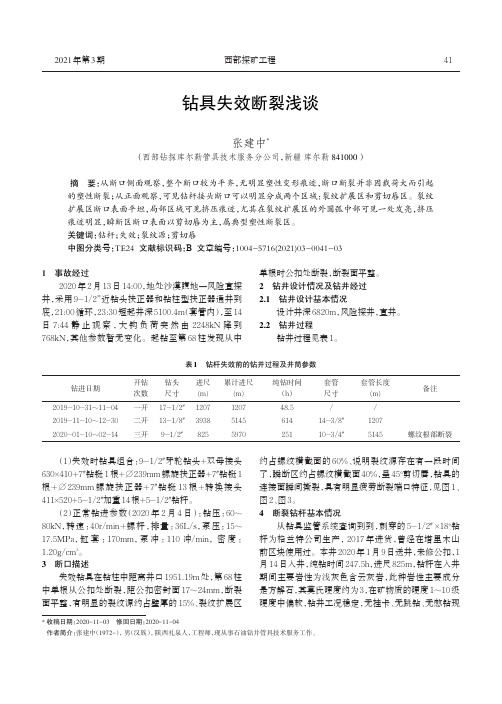
杆为格兰特公司生产,2017 年进货,曾经在塔里木山
1.20g/cm 。
前区块使用过。本井 2020 年 1 月 9 日送井,未修公扣,1
3
月 14 日入井,纯钻时间 247.5h,进尺 825m,钻杆在入井
3
断口描述
失效钻具在钻柱中距离井口 1951.19m 处,第 68 柱
期间主要岩性为浅灰色含云灰岩,此种岩性主要成分
图 3,且表面疲劳台阶明显;瞬断区断口表面以剪切唇
为主,属典型塑性断裂区。根据钻杆接头以上断口特
征,该钻杆接头根部断裂应为典型的疲劳断裂。
(4)接头断裂部位位于螺纹根部,从断口表面裂纹
源区域可以看到,该区域断口颜色发亮,与附近端 5 口
表面颜色明显不同,且该区域挤压痕迹明显,见图 3。
根据裂纹源处的宏观特征,和该钻具入井时间和钻井
设计井深 6820m,风险探井,
直井。
2.2
768kN,其他参数暂无变化。起钻至第 68 柱发现从中
表1
钻井设计情况及钻井经过
钻井过程
钻井过程见表 1。
钻杆失效前的钻井过程及井筒参数
开钻
钻头
进尺
累计进尺
纯钻时间
套管
套管长度
次数
尺寸
(m)
(m)
(h)
尺寸
(m)
2019-10-31~11-04
一开
17-1/2″
液沉淀浓度(0.1~0.4mL/100mL)配合连续法加电同
时施加配置好的磁悬液,尤其适应于钻具公螺纹表面
和近表面的缺陷检测。
7 预防措施
钻具公扣螺纹根部为应力集中区,应力得不到及
时释放加之复杂工况下的拉应力和弯曲应力交变,容
抽油杆断脱分析与防治对策
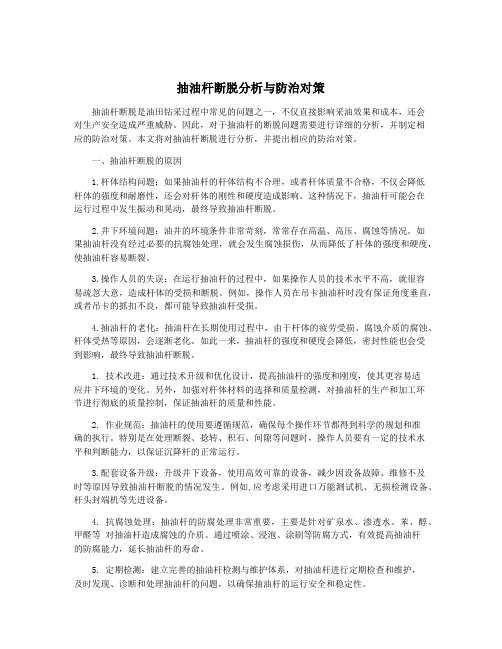
抽油杆断脱分析与防治对策抽油杆断脱是油田钻采过程中常见的问题之一,不仅直接影响采油效果和成本,还会对生产安全造成严重威胁。
因此,对于抽油杆的断脱问题需要进行详细的分析,并制定相应的防治对策。
本文将对抽油杆断脱进行分析,并提出相应的防治对策。
一、抽油杆断脱的原因1.杆体结构问题:如果抽油杆的杆体结构不合理,或者杆体质量不合格,不仅会降低杆体的强度和耐磨性,还会对杆体的刚性和硬度造成影响。
这种情况下,抽油杆可能会在运行过程中发生振动和晃动,最终导致抽油杆断脱。
2.井下环境问题:油井的环境条件非常苛刻,常常存在高温、高压、腐蚀等情况。
如果抽油杆没有经过必要的抗腐蚀处理,就会发生腐蚀损伤,从而降低了杆体的强度和硬度,使抽油杆容易断裂。
3.操作人员的失误:在运行抽油杆的过程中,如果操作人员的技术水平不高,就很容易疏忽大意,造成杆体的受损和断脱。
例如,操作人员在吊卡抽油杆时没有保证角度垂直,或者吊卡的抓扣不良,都可能导致抽油杆受损。
4.抽油杆的老化:抽油杆在长期使用过程中,由于杆体的疲劳受损、腐蚀介质的腐蚀、杆体受热等原因,会逐渐老化。
如此一来,抽油杆的强度和硬度会降低,密封性能也会受到影响,最终导致抽油杆断脱。
1. 技术改进:通过技术升级和优化设计,提高抽油杆的强度和刚度,使其更容易适应井下环境的变化。
另外,加强对杆体材料的选择和质量检测,对抽油杆的生产和加工环节进行彻底的质量控制,保证抽油杆的质量和性能。
2. 作业规范:抽油杆的使用要遵循规范,确保每个操作环节都得到科学的规划和准确的执行。
特别是在处理断裂、捻转、积石、间隙等问题时,操作人员要有一定的技术水平和判断能力,以保证沉降杆的正常运行。
3.配套设备升级:升级井下设备,使用高效可靠的设备,减少因设备故障、维修不及时等原因导致抽油杆断脱的情况发生。
例如,应考虑采用进口万能测试机、无损检测设备、杆头封端机等先进设备。
4. 抗腐蚀处理:抽油杆的防腐处理非常重要,主要是针对矿泉水、渗透水、苯、醇、甲醛等对抽油杆造成腐蚀的介质。
抽油机井杆断脱原因分析与预防对策

抽油机井杆断脱原因分析与预防对策抽油机井杆是油田开采中重要的设备之一,其主要功能是将地下油层中的油井液抽上地面进行处理。
该设备由多根钢管组成,通常有数百根钢管堆叠而成,联合起来形成一个井杆。
然而,在实际生产中,经常出现井杆断裂和脱落的情况,给生产带来极大的影响。
因此,本文将分析抽油机井杆断脱原因,并提出预防对策。
一、原因分析1. 断裂原因分析(1)重负荷当井杆处于长时间重负荷状态时,会因过度负荷而导致井杆断裂。
比如,在冬季因为冻土等原因,泥浆的密度急剧上升,泥浆的黏度增大,会形成较大的剪切力,导致井杆常压断裂。
(2)腐蚀损耗井杆长期处于地下,极易受到井内油气、水、气vapour等介质的侵蚀,导致井杆表面腐蚀,从而减少了井杆的强度。
当井杆表面腐蚀严重时,容易出现断裂。
(3)拉伸应力太大井杆在运行过程中,会受到地下油气动态载荷的作用,导致井杆变形产生拉伸应力,当拉伸应力超过井杆的抗拉极限时,井杆就会发生断裂。
(1)偏心原因井杆堆叠不规范,容易造成井杆偏心,导致井杆脱落。
(2)井杆接口质量差井杆接口连接形式复杂,容易出现接口间隙大、连接不紧等情况,使井杆处于松散状态,从而导致井杆脱落。
此外,如果接口处使用的螺纹不均匀,也会导致井杆脱落。
(3)地震和冲击地震和冲击容易损坏井杆接口,导致井杆脱落。
二、预防对策1. 技术措施(1)加强井杆管理对钻出井杆进行检测和试验,发现井杆出现变形、裂缝、腐蚀和损耗等情况,在未造成事故前及时进行更换。
同时,对于新的井杆要严格检测和试验,保证其质量符合标准要求。
(2)修补螺纹的均匀性对井杆螺纹进行修整,保证螺纹精度和均匀性,减少螺纹运动时的摩擦和损耗。
(3)改进井杆结构加强井杆的整体试验,改进井杆的结构,减少井杆数量,增加井杆长度,减少接口数量,有视情况采取更牢靠的接口形式。
2. 管理措施(1)加强机器设备的维修和保养加强设备的维护,清除井口、井筒和地面的杂物,防止井杆因为被异物打断而丧失支持。
螺杆桩机钻杆断裂形式及原因分析

螺杆桩机钻杆断裂形式及原因分析作者:张宗媛来源:《硅谷》2015年第02期摘要介绍螺杆桩机钻具的主要组成部分,通过螺杆桩钻具在实际生产中出现的几种失效现象,针对钻杆主要失效形式经过计算及现场考察逐个列举并分析原因,对失效原因提出解决方案。
关键词螺杆桩机;螺杆钻具;失效形式中图分类号:TU67 文献标识码:A 文章编号:1671-7597(2015)02-0239-02理论上在相同承载力的情况下螺杆挤土桩投入的成本比长螺旋灌注桩、沉管预制桩相对较低,国内建筑桩机(桩工机械)螺杆挤土桩施工正逐渐取代长螺旋灌注桩施工。
螺杆挤土桩应用螺杆钻具在加压装置的协同作用下挤土形成螺纹孔,既避免了返土现象,又增加了桩体的承载力,响应了国家节能减排的号召,并改善了施工环境。
螺杆钻具第一节为梯形螺纹节,其余各节为光杆。
由于恶劣的工作环境和复杂的受力情况,螺杆桩机钻杆易出现破坏断裂现象,主要为疲劳断裂和扭转变形,极少发生钻杆失稳导致的弯曲变形。
因此,为了避免生产事故,针对钻杆断裂失效原因进行分析,并找出解决办法。
1 螺杆桩机钻杆的介绍螺杆钻具主要由钻头、梯形螺纹钻杆、光钻杆、泥浆管等组成。
使用内、外六方接头通过销体连接,部分使用内、外八方接头通过销体紧固,钻具内设有泥浆管,作为输送混凝土的通道。
钻头用于完成钻进过程中破土和碎石的工作,因此它必须有足够的强度和硬度。
为防止钻头被动力头旋转产生的过大扭矩撕裂,要求钻头钻进过程中受力均衡,设计时选用两侧对称的钻头叶片方式。
螺纹钻杆部分主要由叶片和中心管组成。
根据所需的钻具直径大小来选定中心管。
中心管的直径加上二倍叶片宽度即为所设计钻具的直径。
叶片采用分段铸造成型,每个螺距分3段铸造。
可以根据所需的螺纹形状及螺纹深度大小设计叶片的具体形式。
中心管选用无缝钢管。
中心管与叶片通过焊接结合在一起。
在螺杆部分中间设有泥浆管,方便混凝土灌注,且能预防泥浆滞留造成钻杆阻塞。
钻杆部分由内部泥浆管和外部中心管组成,通过内六方或内八方接头连接,并通过销轴紧固。
反井钻机承载接头断裂事故处理技术探讨

反井钻机承载接头断裂事故处理技术探讨摘要:煤矿使用反井钻机,因产品质量因素,以及现场过倾斜煤层、地质变化带等情况,扩孔钻头受偏载影响,存在一个附加弯矩,可能造成承载接头断裂或钻杆断裂等事故发生。
通过承载接头断裂事故的处理办法,提高现场事故处理能力,确保设备快速处理,防止对生产的中断事故延长,具有一定的借鉴意义。
关键词:反井钻机承载接头工装一、概述太平煤矿+700m 水平南一采区2#溜煤井ZFYP2.5-80-200反井钻机于该钻机系2018年11月出厂,2018 年12 月25日安装完成并试运转成功,同时投入钻小孔作业,于2019年1月9日完成钻小孔作业,钻井深度95m,随即完成扩孔器安装,截止1月18日,完成扩孔深度5m。
1月18日14:30,2名钻机司机正常作业,当扩孔到标尺1.2m处时,钻机承载接头突然断裂,断裂的棘轮套下落到底板上,导致底板变形严重,2个主推缸∮80销轴、16颗底板固定M20螺栓全部断裂。
事故造成ZFYP2.5-80-200反井钻机全部停止运行。
二、现场检验情况钻机承载接头断列事故发生后,18日下午及19日,太平矿副总工程师组织各部门人员,生产厂家技术人员赴现场查看事故现场,承载接头断裂情况如下图:图一作业现场承载拉头断裂位置。
三、事故原因分析1、直接原因经太平煤矿、生产厂家售后服务人员现场测量分析,承载接头内部有伤,受伤面积大约为接头断面的三分之二,扩孔到标尺1.2m处时,突然断裂,是此次事故的直接原因。
2、间接原因:(1)经生产厂家检测,隐患系在该设备生产过程中,材料选择及质量管理不到位,导致产品质量存在缺陷,不能满足生产需要。
(2)该产品系较新产品,前期使用经验及试验参数不足。
四、事故处理方法(一)技术方案1.钻机扩孔钻头安置处理:将钻机扩孔钻头固定在混凝土基础面上,钻机扩孔钻头悬吊在导孔中。
1.1制作专门起吊工装,发往现场。
1.2拆除断裂的主推缸销轴,重新装入略细的销轴。
焦炭塔钻杆断裂失效分析及防范措施
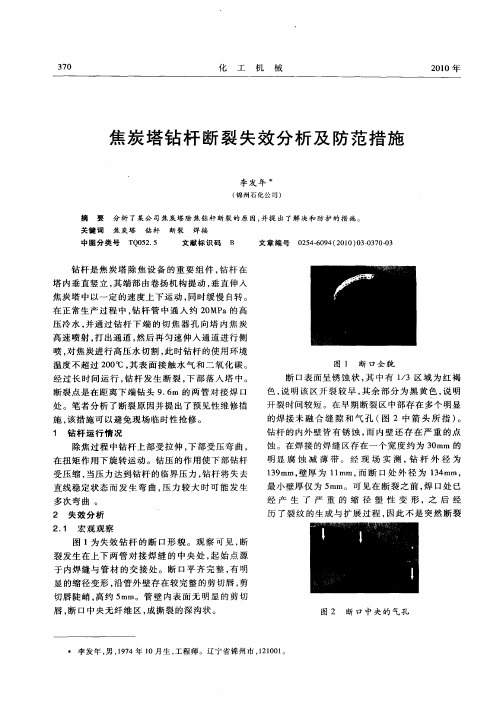
文章编号
0 5 —0 4 2 1 ) 3 3 7 —3 2 4 6 9 ( 0 0 0 d3 00
钻 杆是 焦炭 塔 除 焦 设备 的重 要 组 件 , 杆 在 钻 塔 内垂直 竖立 , 端部 由卷 扬机 构提 动 , 直伸 入 其 垂 焦炭塔 中以一定 的速 度上 下运 动 , 同时缓 慢 自转 。 在正 常生产 过程 中 , 钻杆 管 中 通入 约 2 bP 0 la的 高
缝 与母 材 的熔 合 线 上 , 即管 头 的 内坡 口上 管 头 在
焊 接前 开有 V形坡 口, 图 3中 A处 ) 焊 材 金 属 ( , 与 内坡 口已经发 生 了剥 离 , 说 明管 母 材 与 焊 材 这
钻杆 材料 具有 较 高 的强 度 与 硬 度 , 对 接 两 但 管 的焊缝 区却 是 力 学性 能 的 薄弱 区 , 强 度 与 硬 其 度 明显低 于管 材 。在 管头 与焊缝 的交界 处存 在硬 度 的陡 降 , 应该 是在 拉应 力 的作用 下 , 这 造成 焊缝 区缩 径变形 和焊缝 材料 与母 材 剥离 的直 接原 因 。
料抗 拉强 度值 。按 标 准 进行 换 算 , 出管材 平 得
均 抗 拉 强 度 为 9 3 a 焊 缝 区 抗 拉 强 度 为 7 MP ;
7 5M Pa。 0
缝 金属 明显 比母 材 金属腐 蚀 严重 。外 壁焊 缝 的断
裂 点产 生在 焊缝 的 中部 , 内壁 断裂 点 出现 在 焊 而
压 冷 水 , 通 过 钻 杆 下 端 的 切 焦 器 孔 向 塔 内 焦 炭 并
高速 喷射 , 出通 道 , 打 然后再 匀 速伸入 通道 进行 侧 喷, 对焦炭 进行 高压 水切 割 , 时钻杆 的使 用环 境 此
- 1、下载文档前请自行甄别文档内容的完整性,平台不提供额外的编辑、内容补充、找答案等附加服务。
- 2、"仅部分预览"的文档,不可在线预览部分如存在完整性等问题,可反馈申请退款(可完整预览的文档不适用该条件!)。
- 3、如文档侵犯您的权益,请联系客服反馈,我们会尽快为您处理(人工客服工作时间:9:00-18:30)。
煤矿用钻杆断裂原因及解决措施浅析 【摘 要】 安全一直是煤矿井下施工的重中之重,在煤矿井下瓦斯抽采、煤矿探放水钻孔等施工过程中,钻杆是钻孔装备的重要组成部分,钻杆在钻进过程中的受力状态复杂,实际工况要求钻杆具备良好的性能。在实际的煤矿施工中如果钻杆断裂,必定会对造成安全事故,本文分析了煤矿钻孔用钻杆材质、加工工艺与质量、现场使用时钻进工艺等产生钻杆断裂的原因,并提出了如何提高并稳定钻杆质量、减少防止钻杆施工过程中发生断裂事故的措施。 【关键词】 钻杆 煤矿坑道钻机 钻杆断裂 原因分析 解决措施 在煤矿井下瓦斯抽采、探放水的钻孔施工中,经常使用煤矿坑道钻机,钻杆作为钻机的重要组成部分,在钻孔施工现场大量使用。实际钻进过程中,钻杆处于孔内复杂的工作状态,通常承受拉、压、弯、剪扭、液力、振动等交变载荷,并伴随着液体的冲刷,钻进时经常出现钻杆断裂现象。钻杆断裂不仅影响正常生产,而且还因打捞困难使事故恶化,造成人力、财力的损失,给煤矿的施工安全带来很大影响。因此,正确客观分析钻杆的断裂原因,提前采取有效预防措施,提高控制钻杆质量,降低钻孔事故率,有重要的意义。 1 煤矿勘探用全液压动力头式钻机介绍 分体式全液压动力头式煤矿坑道钻机现已成为国内普遍生产的一种矿用回转式钻机。在煤矿井下钻孔施工中被广泛应用,其结构分主机、泵站、操纵台三大部分,适用于回转和冲击回转给进,主要用于煤矿瓦斯抽采、煤矿井下探放水、探地质构造、探煤层厚度、煤层注浆注水及管棚等各类工程钻孔的施工。 其解体性好,搬迁方便,机械式拧卸钻具,卡盘、夹持器与油缸之间,回转器与夹持器之间可联动操作,自动化程度高,工作效率高,操作简便,工人劳动强度小;采用双泵系统,回转参数与给进参数独立调节,提高了钻机对各种不同钻机工艺的适应能力,用支撑油缸调整机身倾角方便省力,回转器采用通孔结构,钻杆长度不受给进行程的限制,操作台集中操作,人员可远离孔口,有利于人身安全。 2 煤矿用钻杆介绍 在煤矿瓦斯抽放、对煤层注水等钻孔施工过程中,钻杆是必不可少的设备,作为钻机的配套设备,钻杆质量的好坏就直接影响施工的安全与进度,然而由于煤矿中钻杆需要承受的压力、材质、以及加工工艺的不同,使得钻杆存在一些质量的问题,这必将影响煤矿施工的进度。下图是直径为42毫米的钻杆结构图,不仅包括外锥螺纹接头、无缝地质钢管还包括内锥螺纹接头,这个就是矿用钻杆的最基本结构。因此我们要想提高钻杆的质量,就要先从钻杆断裂的原因着手,从而找到对钻杆质量安全的控制对策(如图1)。 3 煤矿用钻杆断裂原因的分析 3.1 钻杆的断裂形式 钻杆在实际施工过程中主要有几下集中断裂的形式:(1)螺纹接头焊缝处断裂;(2)内螺纹接头端部变形成喇叭口或彻底开裂;(3)外螺纹接头处大端螺纹尾部断裂;(4)外螺纹接头螺纹脱扣滑扣或断裂;(5)钻杆杆体钢管中间处断裂。 3.2 钻杆断裂原因分析 3.2.1 杆体母材材质质量缺陷 钻杆常用母材无缝钢管在冶炼加工中本身存在裂纹、结疤等质量问题。加之对钻杆母材经常进行抽样的质量检测,没有对全部母材进行控制,母材材质问题便成为钻杆质量残疵的源头,在现场使用中,因钻杆母材材质的质量问题导致经常发生钻杆扭曲变形、焊缝断裂、螺纹接头大端螺纹尾部断裂等现象。 3.2.2 加工工艺与质量 公母螺纹接头与钢管连接工艺;第一、摩擦焊接工艺与质量:目前钻杆的公母接头与钻杆杆体主要通过摩擦焊接连接。这种工艺方法是两种材料在高挤压力作用下强力接触并相对旋转,通过接触面摩擦产生高温,将接触部分的材料加热到塑性状态,使两者紧紧地挤压连接在一起。这种焊接方式焊缝承载能力较高,而且焊接缺陷相对较少,但焊缝接触面积的大小会影响到其承载能力,且在实际焊接工艺中,因为摩擦焊机挤压力、温度等参数未调好造成钻杆从焊缝处断裂的事故时有发生。第二、接头与钢管采用先螺纹联接而后手工普通焊接的工艺与质量;钻杆螺纹公母接头与钻杆杆体通过普通焊接连接时,焊接人员水平、焊接过程中对于焊条、焊缝的宽度与焊接方式选择执行不到位,都会造成焊接质量的问题;焊接温度的不稳定导致焊缝中的奥氏体组织转化成马氏体组织,使焊缝脆化,马氏体组织还会以条状的形态留在焊缝中,当受到强烈荷载时,钻杆就会产生焊缝裂纹,另外中碳钢可焊性差,手工焊接夹渣、气孔等焊接缺陷难以避免。加之联接螺纹并不能加强接头焊缝的承载能力。当焊缝因承载过大出现裂纹时,联接螺纹只能加快焊缝裂纹扩大,最终导致钻杆的断裂。目前很多小企业钻杆加工现场经常采用这种方法。 3.2.3 钻杆连接接头的尺寸精度误差 第一、连接螺纹加工精度达不到要求;由于螺纹锥度、牙形等的加工误差,导致两根钻杆连接时,尽管公扣、母扣接头端的径向松动。造成在钻进施工过程中,钻杆高速旋转承受径向冲击载荷,导致接头螺纹尾部发生断裂;由于螺纹中径精度误差控制不好,钻杆连接时接头端间隙达不到技术要求。使得钻杆所承受的弯曲、扭转载荷全部由螺纹承受,这样钻杆在螺纹联接处易发生疲劳裂纹,导致螺纹滑扣脱扣。第二、接头螺纹同轴度超差;由于材料、工艺方法、人员失误等原因,两端公扣、母扣螺纹同轴度超差导致钻杆在连接处发生弯曲。这样在钻进过程中,钻杆不但要承受正常的轴向负荷,而目螺纹连接处还要承受很大的径向载荷。 3.2.4 钻杆危险断而应力集中 钻杆公扣、母扣接头端台肩根部应有r>0.5的圆角,圆角过小或者没有圆角会导致钻杆在使用过程中产生应力集中现象,最终疲劳断裂。 3.2.5 机加工质量 钻杆的杆体的外表面一般用车床加工加工,由于车削加工造成钻杆表面有大的裂纹缺陷,也是造成钻杆断裂的原因之一。同时很深的机加工刀痕本身是一个尖锐的缺口,存在较大的应力集中,在应力集中区很容易萌生疲劳裂纹,导致钻杆断裂。 3.3 钻杆现场的不合理使用和突发事件 施工现场钻杆的管理混乱、分级不明、钻机故障、钻进参数的设置不合理、选配不当等现场因素都会造成钻杆的断裂。钻进过程中钻杆突然受到极为苛刻的交变扭矩和顶力,譬如遇到硬的岩石、地质塌陷、卡钻、跳钻等突发变化,也容易使钻杆瞬间受力过载导致断裂。 4 防止钻杆断裂的预防解决对策 4.1 加强钻杆母材钢管的质量控制 从源头保障,加强钻杆母材的定货和到货的质量检验与管理工作,必要时对母材取样做理化检验、金相分析和力学性能试验等,使其机械强度、材料等符合要求。 4.2 加强钻杆生产线质量控制与成品钻杆的试验 (1)严格按照设计图样加工钻杆,加强钻杆生产线与关键工艺与成品的质量监控,确保成品钻杆的质量过关,不断改进工艺手段和工艺方法,建议对钻杆管材通过改变成分或增加回火工序,消除马氏体组织,提高材料的韧性,最终提高钻杆质量。(2)在钻杆的焊接过程中,对杆体和接头的材料进行分析,选择适合匹配的焊接方法、焊材和焊接温度、时间等参数;严格控制摩擦焊机压力、温度等参数。(3)对于成品钻杆的关键连接尺寸公差严格把控,对螺纹部位、杆体和手工焊缝和摩擦焊缝进行无损探伤,对于和合格的产品返修或者报废。(4)对成品钻杆进行整体的强度试验,譬如进行弯曲、扭转、扭转疲劳、弯扭拉复合疲劳强度试验等,掌握实验数据,为钻杆的现场试用和研发生产提供数据支撑。 4.3 加强钻杆的现场使用管理 (1)加强施工现场钻杆的分级管理、做到分级实时明晰、统一调配使用,避免新旧混用。严格执行钻杆的使用制度,保护好内涂层钻杆的涂层。(2)实时注意钻机的维护维修,加强责任心,严格执行各项操作规程,在打钻中尽量避免卡钻、跳钻等突发变化,降低钻机故障和力突变带来的钻杆断裂事故;在遇到地质情况复杂且经常突变的岩层时,施工人员可根据经验,在设备中增加限扭矩控制仪,以免钻杆超载。(3)钻进参数的设置不合理、选配不当等现场因素都会造成钻杆的断裂。钻进过程中钻杆突然受到极为苛刻的交变扭矩和顶力,譬如遇到硬的岩石、地质塌陷、,也容易使钻杆瞬间受力过载导致断裂。(4)钻杆的工作环境比较恶劣,在其长期的服役过程中,会产生很多的缺陷。建议每批钻杆每次使用前后尽量通过探伤方法掌握其缺陷及损伤程度,并根据不同裂纹作针对性处理,提高钻杆使用的可靠性。(5)针对不同岩性、钻孔深度和钻孔直径的要求,合理选用钻进参数,防止钻杆过载。 5 结语 本文列举了煤矿坑道钻机用钻杆在钻孔施工过程中常见的断裂形式,分析了钻杆不同断裂形式产生的原因,并就如何提高稳定钻杆的质量,如何预防、避免、减少钻杆断裂事故的发生率从不同角度提出了改进的措施方法,从而减少由于钻杆断裂造成的煤矿井下事故的发生率,提高煤矿生产的安全性。 参考文献: [1]潘小叶.王志红.钻机钻孔时钻杆振动的有限元分析[j].煤矿机械,2009,(01). [2]蒲天一.李克松.煤矿近水平定向钻进钻头侧向力计算与分析[j].煤炭工程,2013,(04). [3]赵万里.李莞歆.路金萍.松软煤层瓦斯抽采高强螺旋钻杆的研制与应用[j].煤炭工程,2013,(01). [4]张巨川.段隆臣.王红波.基于ansys的煤田地质勘探钻杆振动模态分析[j].煤炭科学技术.2009,(08). [5]刘鸿文.材料力学[m].北京:高等教育出版社,1993. [6]徐晓军.提高钻杆强度及使用寿命的几点意见[j].探矿机械,1998(5):24-27.