齿轮载荷修正系数计算方法的研究_李杰

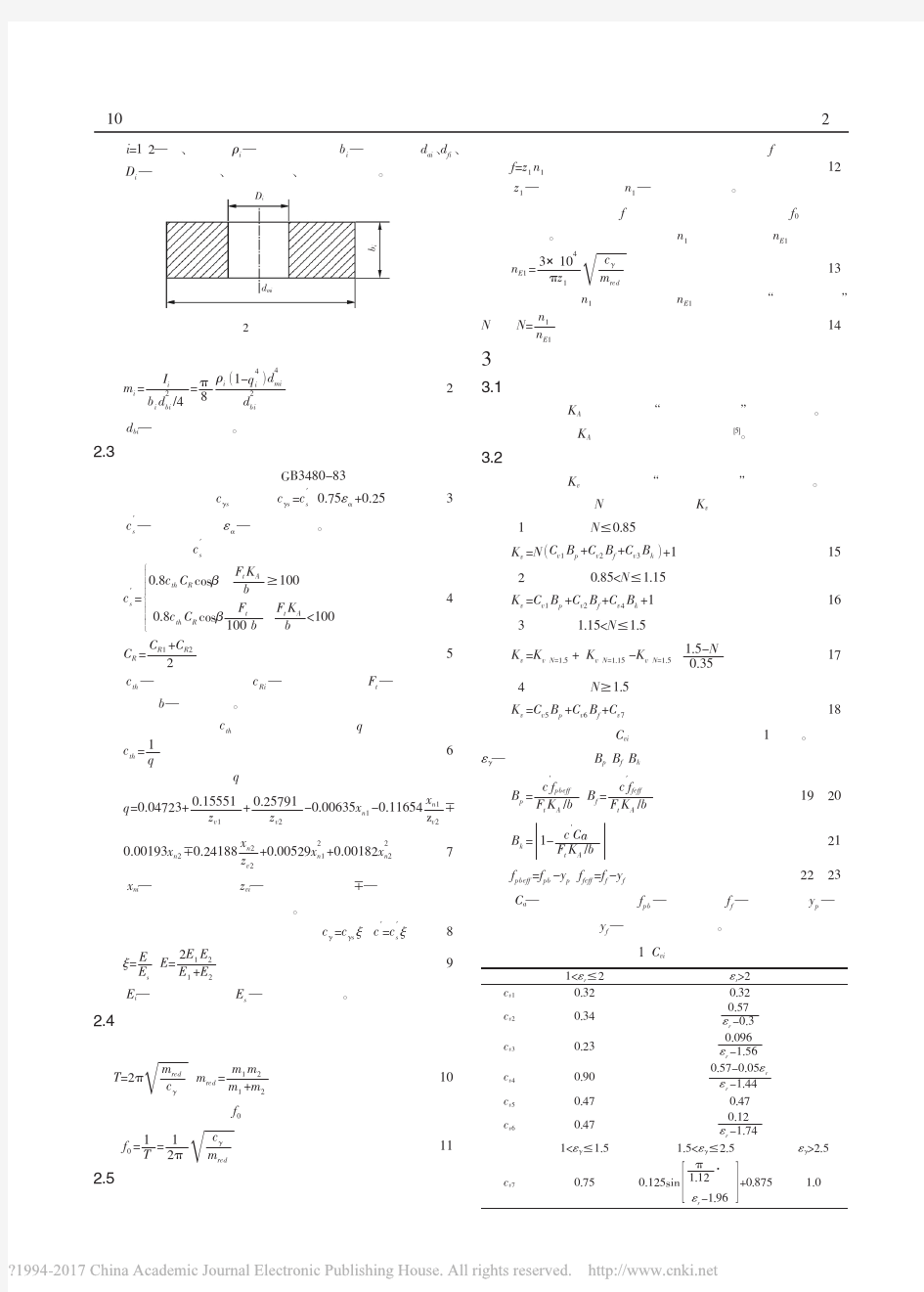
机械设计基础-10. 4齿轮传动的计算载荷
第四节 齿轮传动的计算载荷 齿轮传动强度计算中所用的载荷,通常取沿齿面接触线单位长度上所受的载荷进行计算。沿齿面接触线单位长度上的平均载荷p(单位为N/mm)为,即: F n 为轮齿所受的公称法向载荷。 实际传动中由于原动机、工作机性能的影响以及制造误差的影响,载荷会有所增大,且沿接触线分布不均匀。接触线单位长度上的最大载荷为: K 为载荷系数,其值为:K =K A K v K α K β 式中:K A ─使用系数 K α─齿间载荷分配系数 K v ─动载系数 K β─齿向载荷分布系数 1、KA--使用系数 使用系数KA 是考虑齿轮啮合时外部因素引起的附加动载荷影响的系数。 这种动载荷取决于原动机和工作机的特性,质量比,联轴器类型以及运行状态等。KA 的使用值应针对设计对象,通过实践确定。表10-2 2、Kv--动载系数 动载系数Kv 是考虑齿轮副本身的啮合误差(基节误差、齿形误差、轮齿受载变形等)所引起的啮入、啮出冲击和振动而产生内部附加动载荷影响的系数。 影响动载系数Kv 的主要因素: 1)基节误差和齿形误差 由于制造及装配的误差,轮齿受载后弹性变形的影响,使啮合轮齿的法向齿距Pb1与Pb2不相等,因而轮齿就不能正确的啮合传动,瞬时传动比就不是定值,从动齿轮在运转中就会产生角加速度,于是引起了动载荷或冲击。 L F p n =L KF Kp p n ca ==
2)轮齿变形和刚度大小的变化 对于直齿轮传动,轮齿在啮合过程中,不论是由双对齿啮合过 渡到单对齿啮合,或是由单对齿啮合过渡到双对齿啮合的期间,由 于啮合齿对的刚度变化,也要引起动载荷。为了计及动载荷的影响, 引入了动载系数Kv。 3)齿轮转速的高低及变化 齿轮的制造精度及圆周速度对轮齿啮合过程中产生动载荷的大小影响很大。 减小动载荷的措施: 1)提高制造精度,以减小基节误差和齿形误差,减小齿轮直径以 降低圆周速度; 2)对轮齿进行修缘,以减小轮齿的啮入、啮出冲击; 对轮齿进行齿顶修缘,即把齿顶的小部分齿廓曲线(分度圆压 力角α=20°的渐开线)修正成α>20°的渐开线。因Pb2>Pb1,则 后一对轮齿在未进入啮合区时就开始接触,从而产生动载荷。为此 将从动轮2进行齿顶修缘,图中从动轮2的虚线齿廓即为修缘后的齿廓,实线齿廓则为未经修缘的齿廓。 由图明显地看出,修缘后的轮齿齿顶处的法节P'b2
圆柱齿轮受力分析
轮齿的受力分析 1. 直齿圆柱齿轮受力分析 图为直齿圆柱齿轮受力情况,转矩T1由主动齿轮传给从动齿轮。若忽略齿面间的摩擦力,轮齿间法向力Fn的方向始终沿啮合线。法向力Fn在节点处可分解为两个相互垂直的分力:切于分度圆的圆周力Ft 和沿半径方向的径向力Fr 。 式中:T1-主动齿轮传递的名义转矩(N·mm),,Pl为主动齿轮传递的功率(Kw),n1为主动齿轮的转速(r/min); d1-主动齿轮分度圆直径(mm); α-分度圆压力角(o)。 对于角度变位齿轮传动应以节圆直径d`和啮合角α`分别代替式(9.44)中的d1 和α。 作用于主、从动轮上的各对力大小相等、方向相反。从动轮所受的圆周力是驱动力,其方向与从动轮转向相同;主动轮所受的圆周力是阻力,其方向与从动轮转向相反。径向力分别指向各轮中心(外啮合)。 2. 斜齿轮受力分析 图示为斜齿圆柱齿轮受力情况。一般计算,可忽略摩擦力,并将作用于齿面上的分布力用作用于齿宽中点的法向力Fn 代替。法向力Fn 可分解为三个相互垂直的分力,即圆周力Ft 、径向力Fr 及轴向力Fa 。它们之间的关系为
式中:αn-法向压力角(°); αt-端面压力角;(°) β-分度圆螺旋角(°); 作用于主、从动轮上的各对力大小相等、方向相反。圆周力Ft 和径向力Fr 方向的判断与直齿轮相同。轴向力Fa 的方向应沿轴线,指向该齿轮的受力齿面。通常用左右手法则判断:对于主动轮,左旋时用左手(右旋时用右手),四指顺着齿轮转动方向握住主动轮轴线,则拇指伸直的方向即为轴向力Fa1 的方向。 2 计算载荷和载荷系数 名义载荷上述所求得的各力是用齿轮传递的名义转矩求得的载荷。 计算载荷由于原动机及工作机的性能、齿轮制造及安装误差、齿轮及其支撑件变形等因素的影响,实际作用于齿轮上的载荷要比名义载荷大。因此,在计算齿轮传动的强度时,用载荷系数K对名义载荷进行修正,名义载荷与载荷系数的乘积称为计算载荷。
齿轮的基本参数和计算公式
齿轮的基本参数和计算 公式 -CAL-FENGHAI.-(YICAI)-Company One1
87一基本参数 表示;齿顶圆:轮齿齿顶所对应的圆称为齿顶圆,其直径用d齿根圆:齿轮的齿槽底部所对应的圆称为齿根圆,直径用df表示。 齿厚:任意直径dk的圆周上,轮齿两侧齿廓间的弧长称为该圆上的齿厚,用sk表示;齿槽宽:任意直径dk的圆周上,齿槽两侧齿廓间的弧长称为该圆上的齿槽宽,用ek表示; 齿距:相邻两齿同侧齿廓间的弧长称为该圆上的齿距,用表示。设z为齿数,则根据齿距定义可,故。 齿轮不同直径的圆周上,比值不同,而且其中还包含无理数 k也是不等的。又由渐开线特性可知,在不同直径的圆周上,齿廓各点的压力角 分度圆:为了便于设计、制造及互换,我们把齿轮某一圆周上的比值规定为标准值(整数或较完整的有理数),并使该圆上的压力角也为标准值,这个圆称为分度圆,其直径以d表示。 表示,我国国家标准规定的标准压力角为20°压力角:分度圆上的压力角简称为压力角,以 模数:分度圆上的齿距p对的比值称为模数,用m表示,单位为mm,即。模数是齿轮的主要参数之一,齿轮的主要几何尺寸都与模数成正比,m越 大,则p越大,轮齿就越大,轮齿的抗弯能力就越强,所以模数m又是轮齿抗弯能力的标志。 顶隙:顶隙c=c*m是指一对齿轮啮合时,一个齿轮的齿顶圆到另一个齿轮的齿根圆的径向距离。顶隙有利于润滑油的流动。 表示;齿顶高:轮齿上介于齿顶圆和分度之间的部分称为齿顶,其径向高度称为齿顶高,用h 齿根高:轮齿上介于齿根圆和分度之间的部分称为齿根,其径向高度称为齿根高,用hf 表示
标准齿轮:标准齿轮:分度圆上齿厚与齿槽宽相等,且齿顶高和齿根高为标准值的齿轮为标准齿轮。因此,对于标准齿轮有 模数和齿数是齿轮最主要的参数。在齿数不变的情况下,模数越大则轮齿越大,抗折断的能力越强,当然齿轮轮坯也越大,空间尺寸越大;模数不变的情况下,齿数越大则渐开线越平缓,齿顶圆齿厚、齿根圆齿厚相应地越厚; 齿轮计算公式
直齿锥齿轮传动计算例题
例题10-3试设计一减速器中的直齿锥齿轮传动。已知输入功率P=10kw,小齿轮转速n1=960r/min,齿数比u=3.2,由电动机驱动,工作寿命15年(设每年工作300天),两班制,带式输送机工作平稳,转向不变。 [解]1.选定齿轮类型、精度等级、材料及齿数 (1)选用标准直齿锥齿轮齿轮传动,压力角取为20°。 (2)齿轮精度和材料与例题10-1同。 (3)选小齿轮齿数z1=24,大齿轮齿数z2=uz1=3.224=76.8,取z2=77。 2.按齿面接触疲劳强度设计 (1)由式(10-29)试算小齿轮分度圆直径,即 1) =1.3 计算小齿轮传递的转矩。 9.948 选取齿宽系数=0.3。 查得区域系数 查得材料的弹性影响系数。 [] 由图 由式( , 由图10-23查取接触疲劳寿命系数 取失效概率为1%,安全系数S=1,由式(10-14)得 取和中的较小者作为该齿轮副的接触疲劳许用应力,即
2)试算小齿轮分度圆直径 (2) 1 3.630m/s ②当量齿轮的齿宽系数 0.342.832mm 2) ①由表查得使用系数 ②根据级精度(降低了一级精度) ④由表 由此,得到实际载荷系数 3)由式(10-12),可得按实际载荷系数算得的分度圆直径为 及相应的齿轮模数 3.按齿根弯曲疲劳强度设计 (1)由式(10-27)试算模数,即
1)确定公式中的各参数值。 ①试选 ②计算 由分锥角 由图 由图 由图查得小齿轮和大齿轮的齿根弯曲疲劳极限分别为 由图取弯曲疲劳寿命系数 ,由式(10-14)得 因为大齿轮的大于小齿轮,所以取 2)试算模数。 =1.840mm
渐开线圆柱齿轮传动的动载荷系数分析
万方数据
第34卷第1期渐开线圆柱齿轮传动的动载荷系数分析35 速时,简化方法确定的动载荷系数偏大;而在高速时,简化方法确定的动载荷系数偏小。为此本文中我们给出了一般方法确定动载荷系数的实用曲线和数据表。 1确定动载荷系数的一般方法 在亚临界区工作的齿轮,其动载荷系数Ky的表达式为[1]118—119[2】11—12 Kv=NK+1(1)K=GlBp+G2BS+C口3Bk(2)式(1)、式(2)中,Gl、G2和G3分别为考虑齿轮重合度影响的系数;8。、Bj,和仇分别为考虑齿距偏差、齿形偏差和轮齿修缘影响的系数;N为临界转速比,对于亚临界区Ⅳ≤0.85,其表达式为Ⅳ:藉(3)式(3)中,mred为齿轮副诱导质量,单位kg/mm。对于一般外啮合传动,诱导质量可按下式计算m捌=詈(等)2—11(4) (1一g{)lDl。(1一q{)lD2“2式(3)中的c,为齿轮的啮合刚度,N/(mm?/.an),其表达式为 门,’门 勺=(o.75E.+o.25)半cosp×1.05(5) 式(5)中,g’为齿轮柔度的最小值,单位mm?tan,标准齿轮可按下式确定 q’=0.04723+(0.15551+0.25791/u)/磊l(6)上面各式中其他参数的含义及取值详见参考文献[3]9一ll。 由以上各式可知,齿轮动载荷系数岛与齿轮的齿数zl、齿数比//,、小齿轮转速nl、诱导质量mred等参数有关,确定过程复杂,不便于工程应用。为此新国标给出了确定动载荷系数凰的简化方法。 2确定动载荷系数的简化方法 新国标[3]14。5和文献[4]给出了用简化方法确定 动载荷系数凰的表达式 Kv=[A+瓜200v/A]日 =[A+ ̄/j占(7)A=106—56B(8)召=0.25(C一5.O)o-667(9)式(7).式(9)中,移为齿轮的节线速度,单位m/s;C为齿轮传动精度系数C=6—12。 根据式(6),新国标给出了岛的线图,如图l所示。 新国标指出,简化方法是基于经验数据,主要考虑齿轮制造误差和节线速度的影响。曲线范围内没有考虑共振的影响,此方法主要适用于缺乏详细资料的初步设计阶段。目前,各种机械设计教材给出的都是这种简化的岛曲线。那么,该简化方法与一般方法确定的动载荷系数差异有多大,我们通过下面的实例计算加以分析。 齿轮节线速度v/(m/s) 图1齿轮动载荷系数岛‘ 3一般方法的动载荷系数计算与分析 3.1一般方法的动载荷系数计算 为了用一般方法确定动载荷系数的大小,设一对标准正常齿制直齿圆柱齿轮传动,小齿轮的齿数Z-l-25,模数m=4.0mm,小齿轮宽度b1_65mm,大齿轮宽度b2=60ram,实心式结构(式(3)中gl=q2=0)。两齿轮材料皆为40M11B(P1=P2=7.8×10“kg/mm3),热处理为表面淬火,接触疲劳极限盯liIn=1060MPa。各级精度齿轮的单个齿距偏差和齿廓总偏差按GB/T10095.1—2008确定。 厶=o.3(%+o.4“+4)×2(cr2-2.5’(tan)圪=(3.2厂磊+0.22^+o.7)×2(∽-2.5)(/.an)上式中,d.为齿轮的分度圆直径,r肿。 由(1)式可知,动载荷系数K。是临界转速比Ⅳ的函数。把式(3)、式(4)代入式(1),并设齿轮分度圆直径约等于平均直径,则有 red】/7,l玎厶111,1,,^、口。丽丽2丽丽t川,一对材料相同的实心齿轮,式(1)经整理后变为Kv=而7.1"0伽√彘南K+l(… 由式(11)可知,动载荷系数胁是2Iv/100的函数。因此,在给定齿轮精度等级的条件下可以绘制出琊的曲线(详见GB/T3480—1983)。但是实际上嘶还与齿数比/3,、单位齿宽载荷杨E/6(影响式(11)中的K)等其他参数有关。对于7级精度的齿轮,取不同齿数比和单位齿宽载荷,计算的动载荷系数K如图2所示。可见齿数比和单位齿宽载荷对动载荷系数都有较明显的影响。因此,GB/T3480—1983中简化方法确定的动载荷系数的曲线在GB/T3480一1997中被取消 了。如前所述,新国标中简化方法确定动载荷系数的 万方数据
齿轮基本计算公式
齿轮基本计算公式-CAL-FENGHAI.-(YICAI)-Company One1
齿轮计算公式 节圆柱上的螺旋角:L d /tan 00?=πβ 基圆柱上的螺旋角:n g αββcos sin sin 0?= 齿厚中心车角:Z θ/90?= 销子直径:m 728.1dp ?= 中心距离增加系数:)1cos /(cos )2/)((y b 021-?+=ααZ Z 标准正齿轮的计算(小齿轮①,大齿轮②) 1. 齿轮齿 标准 2. 工齿齿形 直齿 3. 模数 m 4. 压力角 c αα=0 5. 齿数 21,Z Z 6. 有效齿深 m 2h e ?= 7. 全齿深 c m h +=2 8. 齿顶隙 m 35.0,m 25.0,m 2.0c ???= 9. 基础节圆直径 m d 0?=Z 10. 外径 m )2(d k ?+=Z 11. 齿底直径 c 2m )2(d r ?-?-=Z 12. 基础圆直径 0g cos m d αZ ??= 13. 周节 m t 0?=π 14. 法线节距 0e cos m t απ??= 15. 圆弧齿厚 2/m S 0?=π 16. 弦齿厚 )2sin(m S 1 j Z π Z ???= 17. 齿轮油标尺齿高 m m h j +Z ?-??Z =)2cos 1()2/(π
18. 跨齿数 5.0)180/(0m ??=Z αZ 19. 跨齿厚 ])5.0([cos 0o m inva m m S Z ?-?Z ??=πα 20. 销子直径 m 728.1d ?= 21. 圆柱测量尺寸 d m d m +?Z =)cos /cos (0φα (偶数齿) d )]90(cos )cos /cos m [(d 0m +? ??=Z φαZ (奇数齿) 其中, 00)2 cos (1απαφinv m d inv +-?Z 22. 齿隙 f 移位正齿轮计算公式(小齿轮①,大齿轮②) 1. 齿轮齿形 转位 2. 工具齿形 直齿 3. 模数 m 4. 压力角 c αα=0 5. 齿数 Z 6. 有效齿深 m 2h e ?= 7. 全齿深 c m )]x x (y 2[h 21+??-+= 或 c m 2h +?= 8. 齿隙 c 9. 转位系数 x 10. 中心距离 m y x ?+=αα 11. 基准节圆直径 m d 0?=Z 12. 啮合压力角 02 12 10b inv )x x ( tan 2inv αZ Z αα+++?= 13. 啮合节圆直径 )( x 2d 2 11 b Z Z Z α+??= 14. 外径 m )x y (2m )2(d 21k ?-?+?+=Z 15. 齿顶圆直径 h 2d d 1k r ?-= 16. 基圆直径 0cos t g m d α??Z =
齿轮参数计算公式
齿轮参数计算公式 节圆柱上的螺旋角: 基圆柱上的螺旋角: 齿厚中心车角: 销子直径: 中心距离增加系数: 一、标准正齿轮的计算(小齿轮①,大齿轮②)1.齿轮齿标准 2.工齿齿形直齿 3.模数 m 4.压力角 5.齿数 6.有效齿深 7.全齿深 8.齿顶隙 9.基础节圆直径 10.外径 11.齿底直径 12.基础圆直径 13.周节 14.法线节距 15.圆弧齿厚 16.弦齿厚
17.齿轮油标尺齿高 18.跨齿数 19.跨齿厚 20.销子直径 21.圆柱测量尺寸(偶数齿) (奇数齿)其中, 22.齿隙 ? 二、移位正齿轮计算公式(小齿轮①,大齿轮②) 1.齿轮齿形转位 2.工具齿形直齿 3.模数 4.压力角 5.齿数 6.有效齿深 7.全齿深或 8.齿隙 9.转位系数 10.中心距离 11.基准节圆直径 12.啮合压力角 13.啮合节圆直径
14.外径 15.齿顶圆直径 16.基圆直径 17.周节 18.法线节距 19.圆弧齿厚 20.弦齿厚 21.齿轮游标尺齿高 22.跨齿数 23.跨齿厚 24.梢子直径 25.圆柱测量尺寸(偶数齿) (奇数齿) 三、标准螺旋齿的计算公式(齿直角方式)(小齿轮①,大齿轮②) 1.齿轮齿形标准 2.齿形基准断面齿直角 3.工具齿形螺旋齿 4.模数
5.压力角 6.齿数 7.螺旋角方向(左或右)8.有效齿深 9.全齿深 10.正面压力角 11.中心距离 12.基准节圆直径 13.外径 14.齿底圆直径 15.基圆直径 16.基圆上的螺旋角 17.导程 18.周节(齿直角) 19.法线节距(齿直角) 20.圆弧齿厚(齿直角)21.相当正齿轮齿数 22.弦齿厚
齿轮传动的载荷和应力
1. 齿轮传动的载荷计算 (1) 直齿圆柱齿轮传动的受力分析 圆周力: 径向力: 法向力: o d1——小齿轮的分度圆直径mm oα——分度圆压力角 o T1——小齿轮传递的名义转矩(N.m) o P1为小齿轮所传递的功率(KW) o n1为小齿轮转速(rpm) 作用在主动轮和从动轮上的力大小相等,方向相反。主动轮上的圆周力是阻力,其方向与它的回转方向相反;从动轮上的圆周力是驱动力,其方向与它的回转方向相同;两轮所受的径向力分别指向各自的轮心。 齿面上的总法向力方向则为啮合点的法向方向,对于渐开线齿廓即为通过啮合点与基圆相切的啮合线方向。 (2) 斜齿圆柱齿轮传动的受力分析
圆周力: 径向力: 轴向力: 法向力: ?αt——端面分度圆压力角; ?αn——法向分度圆压力角; ?β——分度圆螺旋角; ?βt——基圆螺旋角。 (3) 直齿锥齿轮传动的受力分析 法向力Fn集中作用在齿宽节线中点处,则Fn可分解为互相垂直的三个分力。
圆周力: 径向力: 轴向力: dm1——小齿轮齿宽中点分度圆直径mm;δ1——小锥齿轮分度圆锥角 圆周力和径向力的方向判别与直齿圆柱齿轮判别方法相同,轴向力方向分别指向各自的大端。由于锥齿轮传动两轴的空间交角为90°,因此存在以下关系:;。负号表示方向相反。 (4) 齿轮传动的计算载荷 齿轮承受载荷常表现为其传递的力矩或圆周力。由上述力的分析计算所得出的圆周力为齿轮传动的名义圆周力。实际工作中,由于各种因素的影响,齿轮实际承受的圆周力要大于名义圆周力。考虑各种因素的影响,实际圆周力Ftc为: Ftc也称为计算载荷。 1)KA——使用系数。2)KV——动载系数。3) KHα和KFα——齿间载荷分配系数。4) KHβ和KFβ——齿向载荷分布系数。 2. 齿轮传动应力分析 齿轮传动工作过程中,相啮合的轮齿受到法向力Fn的作用,主要产生两种应力:齿面接触应力和齿根弯曲应力。 (1) 齿面接触应力σH 齿轮传动工作中,渐开线齿面理论上为线接触,考虑齿轮的弹性变形,实际上为很小的面接触。在接触面上,产生齿面接触应力。对于相啮合齿轮上的一对特定轮齿,工作齿廓上的各对应接触部位仅仅在接触的瞬间产生接触应力,过此瞬间脱离接触之后,该部位的接触应力随即消失。因此,不论轮齿承受稳定载荷或不稳定载荷,传动运动方式如何,齿面接触应力总是按脉动循环变化的变应力。 齿面接触应力的数值,与载荷大小、接触点的变形、材料性能等因素有关,可按弹性力学理论和轮齿表面的具体情况予以确定;齿面接触应力的变化次数,与齿轮的预期工作寿命及转速等因素有关。 (2) 齿根弯曲应力σF
齿轮基本计算公式
齿轮计算公式 节圆柱上的螺旋角:L d /tan 00?=πβ 基圆柱上的螺旋角:n g αββcos sin sin 0?= 齿厚中心车角:Z θ/90?= 销子直径:m 728.1dp ?= 中心距离增加系数:)1cos /(cos )2/)((y b 021-?+=ααZ Z 标准正齿轮的计算(小齿轮①,大齿轮②) 1. 齿轮齿 标准 2. 工齿齿形 直齿 3. 模数 m 4. 压力角 c αα=0 5. 齿数 21,Z Z 6. 有效齿深 m 2h e ?= 7. 全齿深 c m h +=2 8. 齿顶隙 m 35.0,m 25.0,m 2.0c ???= 9. 基础节圆直径 m d 0?=Z 10. 外径 m )2(d k ?+=Z 11. 齿底直径 c 2m )2(d r ?-?-=Z 12. 基础圆直径 0g cos m d αZ ??= 13. 周节 m t 0?=π 14. 法线节距 0e cos m t απ??= 15. 圆弧齿厚 2/m S 0?=π 16. 弦齿厚 )2sin( m S 1 j Z π Z ???= 17. 齿轮油标尺齿高 m m h j +Z ?-??Z =)2cos 1()2/(π 18. 跨齿数 5.0)180/(0m ??=Z αZ
19. 跨齿厚 ])5.0([cos 0o m inva m m S Z ?-?Z ??=πα 20. 销子直径 m 728.1d ?= 21. 圆柱测量尺寸 d m d m +?Z =)cos /cos (0φα (偶数齿) d )]90(cos )cos /cos m [(d 0m +? ??=Z φαZ (奇数齿) 其中, 00)2 cos (1απαφ inv m d inv +-?Z 22. 齿隙 f ? 移位正齿轮计算公式(小齿轮①,大齿轮②) 1. 齿轮齿形 转位 2. 工具齿形 直齿 3. 模数 m 4. 压力角 c αα=0 5. 齿数 Z 6. 有效齿深 m 2h e ?= 7. 全齿深 c m )]x x (y 2[h 21+??-+= 或 c m 2h +?= 8. 齿隙 c 9. 转位系数 x 10. 中心距离 m y x ?+=αα 11. 基准节圆直径 m d 0?=Z 12. 啮合压力角 02 12 10b inv )x x ( tan 2inv αZ Z αα+++?= 13. 啮合节圆直径 )( x 2d 2 11 b Z Z Z α+??= 14. 外径 m )x y (2m )2(d 21k ?-?+?+=Z 15. 齿顶圆直径 h 2d d 1k r ?-= 16. 基圆直径 0cos t g m d α??Z = 17. 周节 m t 0?=π 18. 法线节距 00cos m t απ??=
齿轮传动的计算载荷
齿轮传动的计算载荷 songli2010-01-21 14:06 齿轮传动的计算载荷 为了便于分析计算,通常取沿齿面接触线单位长度上所受的载荷进行计算。沿齿面接触线单位长度上的平均载荷p(单 位为N/mm)为 p=Fn/L 式中:Fn——作用于齿面接触线上的法向载荷,N; L——沿齿面的接触线长,mm。 法向载荷Fn为公称载荷,在实际传动中,由于原动机及工作机性能的影响,以及齿轮的制造误差,特别是基节误差和 齿形误差的影响,会使法向载荷增大。此外,在同时啮合的齿 对间,载荷的分配并不是均匀的,即使在一对齿上,载荷也不 可能沿接触线均匀分布。因此在计算齿轮传动的强度时,应按 接触线单位长度上的最大载荷,即计算载荷pca(单位为N/mm) 进行计算。即Pca=Kp=KFn/L
式中,K为载荷系数;Fn、L的意义和单位同前。 计算齿轮强度用的载荷系数K,包括使用系数KA、动载系数Kv、齿间载荷分配系数Kα及齿向载荷分布系数Kβ,即K= KAKvKαKβ (一)使用系数KA 使用系数KA是考虑齿轮啮合时外部因素引起的附加载 荷影响的系数。这种附加载荷取决于原动机和从动机械的特性、质量比、联轴器类型以及运行状态等。KA的实用值应针对设计对象,通过实践确定。表10-2所列的KA值可供参考。
(二)动载系数鬈, 齿轮传动不可避免地会有制造及装配的误差,轮齿受载后还要产生弹性变形。这些误差及变形实际上将使啮合轮齿的法节pb1与ph2不相等(参看图10-6和10-7),因而轮齿就不能正确地啮合传动,瞬时传动比就不是定值,从动齿轮在运转中就会产生角加速度,于是引起了动载荷或冲击。对于直齿轮传动,轮齿在啮合过程中,不论是由双对齿啮合过渡到单对齿啮合,或是由单对齿啮合过渡到双对齿啮合的期间,由于啮合齿对的刚度变化,也要引起动载荷。为了计及动载荷的影响,引入了动载系数KA。
直齿圆柱齿轮传动的受力分析和载荷计算
直齿圆柱齿轮传动的受力分析和载荷计算 直齿圆柱齿轮传动的受力分析: 图 9-8为一对直齿圆柱齿轮,若略去齿面间的摩擦力,轮齿节点处的法向力F n 可分解为两个互相垂直的分力:切于分度圆上的圆周力F t 和沿半径方向的径向力F r 。 (1)各力的大小 图 9 - 8直齿圆柱齿轮受力分析 圆周力 (9-1) 径向力 (9-2)
法向力 (9-3) 其中转矩 (9-4) 式中:T1 ,T2 是主、从动齿轮传递的名义转矩,N.mm ;d1 ,d2 是主、从动齿轮分度圆直径, mm ;为分度圆压力角;P是额定功率, kW ;n1 ,n2 是主动齿轮、从动轮的转速, r/min 。作用在主动轮和从动轮上的各对应力大小相等,方向相反。即: ,, (2)各力的方向 主动轮圆周力的方向与转动方向相反;从动轮圆周力的方向与转动方向相同;径向力F r 分别指向各自轮心 ( 外啮合齿轮传动 ) 。 9.4.2 计算载荷 前面齿轮力分析中的F n 、F t 和F r 及F a 均是作用在轮齿上的名义载荷。原动机和工作机性能的不同有可能产生振动和冲击;轮齿在啮合过程中会产生动载荷;制造安装误差或受载后轮齿的弹性变形以及轴、轴承、箱体的变形,会使载荷沿接触线分布不均,而同时啮合的各轮齿间载荷分配不均等,因此接触线单位长度的载荷会比由名义载荷计算的大。所以须将名义载荷修正为计算载荷。进行齿轮的强度计算时,按计算载荷进行计算。
(9-4) 计算载荷(9 - 5) 载荷系数 (9- 6) 式中:K是载荷系数;K A 是使用系数;K v 是动载系数; 是 齿向载荷分布系数;是齿间载荷分配系数。 1 .使用系数K A 使用系数K A 是考虑由于齿轮外部因素引起附加动载荷影响的系数。其取决于原动机和工作机的工作特性、轴和联轴器系统的质量和刚度以及运行状态。其值可按表 9 - 3选取。 表 9-3使用系数K A 工作 机的 工作 特性 工作机器 原动机的工作特性及其示例电动 机、均 匀运转 的蒸气 机、燃 气轮机 (小 的,启 蒸气 机、燃 气轮机 液压装 置电动 机(经 常启动 启动转 多 缸 内 燃 机 单缸 内燃 机
(完整版)齿轮齿条传动设计计算.docx
1. 选定齿轮类型、精度等级、材料级齿数 1)选用直齿圆柱齿轮齿条传动。 2)速度不高,故选用 7 级精度( GB10095-88)。 3)材料选择。由表 10-1 选择小齿轮材料为 40Cr(调质 ),硬度为 280HBS ,齿条 材料为 45 钢(调质)硬度为 240HBS 。 4)选小齿轮齿数 Z 1 =24,大齿轮齿数 Z 2 = ∞。 2. 按齿面接触强度设计 由设计计算公式进行计算,即 3 K t T 1 u + 1 Z E d 1t ≥ 2.32 √ ?( ) 2 φd u [ σ ] H (1) 确定公式内的各计算数值 1)试选载荷系数 K t =1.3。 2)计算小齿轮传递的转矩。 (预设齿轮模数 m=8mm,直径 d=160mm ) T 1 = 95.5 ×105 P 1 = 95.5 ×105 ×0.2424 n 1 7.96 = 2.908 ×105 N ?mm 3) 由表 10-7 选齿宽系数 φ = 0.5。 d 1 4)由表 10-6 查得材料的弹性影响系数 Z E = 189.8MPa 2 。 5)由图 10-21d 按齿面硬度查得小齿轮的接触疲劳强度极限 σ = 600MPa;齿 Hlim1 条的接触疲劳强度极限 σ = 550MPa 。 Hlim2 6)由式 10-13 计算应力循环次数。 N 1 = 60n 1 jL h = 60 × ( 2× 0.08× 200 × ) = × 4 7.96 ×1 × 4 6.113 10 7)由图 10-19 取接触疲劳寿命系数 K HN1 = 1.7。 8)计算接触疲劳许用应力。 取失效概率为 1%,安全系数 S=1,由式( 10-12)得 [ σH ] 1 = K HN1 σHlim1 ×600MPa = 1020MPa = 1.7 S (2) 计算 1)试算小齿轮分度圆直径 d ,代入 [σ ] 。 t1 H 1
标准直齿圆柱齿轮传动强度计算
§8-5 标准直齿圆柱齿轮传动的强度计算 一.齿轮传动承载能力计算依据 轮辐、轮缘、轮毂等设计时,由经验公式确定尺寸。若设计新齿,可参《工程手册》20、22篇,用有限元法进行设计。 轮齿的强度计算: 1.齿根弯曲强度计算:应用材料力学弯曲强度公式W M b = σ进行计算。数学模型:将轮齿看成悬臂梁,对齿根进行计算,针对齿根折断失效。
险截面上,γcos ca p --产生剪应力τ,γsin ca p 产生压应力σc ,γcos .h p M ca =产生弯曲应力σF 。分析表明,σF 起主要作用,若只用σF 计算齿根弯曲疲劳强度,误差很小(<5%),在工程计算允许范围内,所以危险剖面上只考虑σF 。 单位齿宽(b=1)时齿根危险截面的理论弯曲应力为 2 20cos .66 *1cos .S h p S h p W M ca ca F γγσ=== 令α cos ,,b KF L KF p m K S m K h t n ca S h = ===,代入上式,得 ()αγαγσcos cos 6.cos cos ..622 0S h t S h t F K K bm KF m K b m K KF == 令 αγc o s c o s 62 S h Fa K K Y = Fa Y --齿形系数,表示齿轮齿形对σF 的影响。Fa Y 的大小只与轮齿形状有关(z 、h *a 、c *、
α)而与模数无关,其值查表10-5。 齿根危险截面理论弯曲应力为 bm Y KF Fa t F = 0σ 实际计算时,应计入载荷系数及齿根危险剖面处的齿根过渡曲线引起的应力集中的影响。 bm Y Y KF Sa Fa t F = σ 式中:Sa Y --考虑齿根过渡曲线引起的应力集中系数,其影响因素同Fa Y ,其值可查表10-5。 2.齿根弯曲疲劳强度计算 校核公式 []F Fa Sa Sa Fa t F Y Y bmd KT bm Y Y KF σσ≤== 1 1 2 MPa 令1 d b d = φ,d φ--齿宽系数。 将111,mz d d b d ==φ代入上式 设计公式 [])(.23 211mm Y Y z KT m F Sa Fa d σφ≥
齿轮传动的强度设计计算
1. 齿面接触疲劳强度的计算 齿面接触疲劳强度的计算中,由于赫兹应力是齿面间应力的主要指标,故把赫兹应力作为齿面接触应力的计算基础,并用来评价接触强度。齿面接触疲劳强度核算时,根据设计要求可以选择不同的计算公式。用于总体设计和非重要齿轮计算时,可采用简化计算方法;重要齿轮校核时可采用精确计算方法。 分析计算表明,大、小齿轮的接触应力总是相等的。齿面最大接触应力一般出现在小轮单对齿啮合区内界点、节点和大轮单对齿啮合区内界点三个特征点之一。实际使用和实验也证明了这一规律的正确。因此,在齿面接触疲劳强度的计算中,常采用节点的接触应力分析齿轮的接触强度。强度条件为:大、小齿轮在节点处的计算接触应力均不大于其相应的许用接触应力,即: ⑴圆柱齿轮的接触疲劳强度计算 1)两圆柱体接触时的接触应力 在载荷作用下,两曲面零件表面理论上为线接触或点接触,考虑到弹性变形,实际为很小的面接触。两圆柱体接触时的接触面尺寸和接触应力可按赫兹公式计算。 两圆柱体接触,接触面为矩形(2axb),最大接触应力σHmax位于接触面宽中线处。计算公式为: 接触面半宽:
最大接触应力: ?F——接触面所受到的载荷
?ρ——综合曲率半径,(正号用于外接触,负号用于内接触) ?E1、E2——两接触体材料的弹性模量 ?μ1、μ2——两接触体材料的泊松比 2)齿轮啮合时的接触应力 两渐开线圆柱齿轮在任意一处啮合点时接触应力状况,都可以转化为以啮合点处的曲率半径ρ1、ρ2为半径的两圆柱体的接触应力。在整个啮合过程中的最大接触应力即为各啮合点接触应力的最大值。节点附近处的ρ虽然不是最小值,但节点处一般只有一对轮齿啮合,点蚀也往往先在节点附近的齿根表面出现,因此,接触疲劳强度计算通常以节点为最大接触应力计算点。 参数直齿圆柱齿轮斜齿圆柱齿轮 节点处的载荷为
齿轮强度计算公式
第7节 标准斜齿圆柱齿轮的强度计算 一. 齿面接触疲劳强度计算 1. 斜齿轮接触方式 2. 计算公式 校核式: 设计式: 3. 参数取值说明 1) Z E ---弹性系数 2) Z H ---节点区域系数 3) ---斜齿轮端面重合度 4) ---螺旋角。斜齿轮:=80~250;人字齿轮=200~350 5) 许用应力:[H ]=([H1]+[H2])/2[H2] 6) 分度圆直径的初步计算 在设计式中,K 等与齿轮尺寸参数有关,故需初步估算: a) 初取K=K t b) 计算d t c) 修正d t 二. 齿根弯曲疲劳强度计算 1. 轮齿断裂 2. 计算公式校核式: 设计式: 3. 参数取值说明 1) Y F a 、Y Sa ---齿形系数和应力修正系数。Z v =Z/cos 3 Y Fa 、Y Fa 2) Y ---螺旋角系数。 3) 初步设计计算 在设计式中,K 等与齿轮尺寸参数有关,故需初步估算: d) 初取K=K t e) 计算m nt f) 修正m n [] H t H E H u u bd KF Z Z σεσα≤±=1 1[] 3 2 1112??? ? ??±≥H H E d Z Z u u KT d σεψα[]3 2 1112 ??? ? ??±≥H H E d t t Z Z u u T K d σψ311t t K K d d ≥[]F n sa Fa t F bm Y Y Y KF σεσα β ≤=[]3 2121cos 2F sa Fa d n Y Y z Y KT m σεψβα β≥3t t n n K K m m ≥[] 3 2121cos 2F sa Fa d t nt Y Y z Y T K m σεψβα β≥
齿轮齿条传动设计计算
齿轮齿条传动设计计算 Revised as of 23 November 2020
1. 选定齿轮类型、精度等级、材料级齿数 1) 选用直齿圆柱齿轮齿条传动。 2) 速度不高,故选用7级精度(GB10095-88)。 3) 材料选择。由表10-1选择小齿轮材料为40Cr(调质),硬度为280HBS ,齿条材料 为45钢(调质)硬度为240HBS 。 4) 选小齿轮齿数Z 1=24,大齿轮齿数Z 2=∞。 2. 按齿面接触强度设计 由设计计算公式进行计算,即 d 1t ≥2.32√K t T 1d u +1(Z E [H ])23 (1) 确定公式内的各计算数值 1) 试选载荷系数K t =。 2) 计算小齿轮传递的转矩。(预设齿轮模数m=8mm,直径d=160mm ) T 1=95.5×105P 1n 1=95.5×105×0.24247.96 =2.908×105N?mm 3) 由表10-7选齿宽系数φd =0.5。 4)由表10-6查得材料的弹性影响系数Z E =189.8MPa 12 。 5)由图10-21d 按齿面硬度查得小齿轮的接触疲劳强度极限σHlim1=600MPa ;齿条的接触疲劳强度极限σHlim2=550MPa 。 6)由式10-13计算应力循环次数。 N 1=60n 1jL h =60×7.96×1×(2×0.08×200×4)=6.113×104 7)由图10-19取接触疲劳寿命系数K HN1=1.7。 8)计算接触疲劳许用应力。 取失效概率为1%,安全系数S=1,由式(10-12)得 [σH ]1=K HN1σHlim1S =1.7×600MPa =1020MPa
齿轮基本尺寸计算公式知识分享
齿轮基本尺寸计算公 式
齿轮参数计算公式 节圆柱上的螺旋角: 基圆柱上的螺旋角: 齿厚中心车角: 销子直径: 中心距离增加系数: 一、标准正齿轮的计算(小齿轮①,大齿轮②)1.齿轮齿标准 2.工齿齿形直齿 3.模数 m 4.压力角 5.齿数 6.有效齿深 7.全齿深 8.齿顶隙 9.基础节圆直径 10.外径 11.齿底直径 12.基础圆直径 13.周节 14.法线节距 15.圆弧齿厚 16.弦齿厚
17.齿轮油标尺齿高 18.跨齿数 19.跨齿厚 20.销子直径 21.圆柱测量尺寸(偶数齿) (奇数齿)其中, 22.齿隙 ? 二、移位正齿轮计算公式(小齿轮①,大齿轮②) 1.齿轮齿形转位 2.工具齿形直齿 3.模数 4.压力角 5.齿数 6.有效齿深 7.全齿深或 8.齿隙 9.转位系数 10.中心距离 11.基准节圆直径 12.啮合压力角 13.啮合节圆直径
14.外径 15.齿顶圆直径 16.基圆直径 17.周节 18.法线节距 19.圆弧齿厚 20.弦齿厚 21.齿轮游标尺齿高 22.跨齿数 23.跨齿厚 24.梢子直径 25.圆柱测量尺寸(偶数齿) (奇数齿) 三、标准螺旋齿的计算公式(齿直角方式)(小齿轮①,大齿轮②) 1.齿轮齿形标准 2.齿形基准断面齿直角 3.工具齿形螺旋齿 4.模数 5.压力角
6.齿数 7.螺旋角方向(左或右)8.有效齿深 9.全齿深 10.正面压力角 11.中心距离 12.基准节圆直径 13.外径 14.齿底圆直径 15.基圆直径 16.基圆上的螺旋角 17.导程 18.周节(齿直角) 19.法线节距(齿直角) 20.圆弧齿厚(齿直角)21.相当正齿轮齿数 22.弦齿厚 23.齿轮游标尺齿深
圆柱齿轮传动的计算载荷和受力分析
1 轮齿的受力分析 1. 直齿圆柱齿轮受力分析 图为直齿圆柱齿轮受力情况,转矩T1由主动齿轮传给从动齿轮。若忽略齿面间的摩擦力,轮齿间法向力Fn的方向始终沿啮合线。法向力Fn在节点处可分解为两个相互垂直的分力:切于分度圆的圆周力Ft 和沿半径方向的径向力Fr 。 式中:T1-主动齿轮传递的名义转矩(N·mm),,Pl为主动齿轮传递的功率(Kw),n1为主动齿轮的转速(r/min); d1-主动齿轮分度圆直径(mm); α-分度圆压力角(o)。 对于角度变位齿轮传动应以节圆直径d`和啮合角α`分别代替式(9.44)中的d1 和α。 作用于主、从动轮上的各对力大小相等、方向相反。从动轮所受的圆周力是驱动力,其方向与从动轮转向相同;主动轮所受的圆周力是阻力,其方向与从动轮转向相反。径向力分别指
向各轮中心(外啮合)。 2. 斜齿轮受力分析 图示为斜齿圆柱齿轮受力情况。一般计算,可忽略摩擦力,并将作用于齿面上的分布力用作用于齿宽中点的法向力Fn 代替。法向力Fn 可分解为三个相互垂直的分力,即圆周力Ft 、径向力Fr 及轴向力Fa 。它们之间的关系为 式中:αn-法向压力角(°); αt-端面压力角;(°) β-分度圆螺旋角(°);
作用于主、从动轮上的各对力大小相等、方向相反。圆周力Ft 和径向力Fr 方向的判断与直齿轮相同。轴向力Fa 的方向应沿轴线,指向该齿轮的受力齿面。通常用左右手法则判断:对于主动轮,左旋时用左手(右旋时用右手),四指顺着齿轮转动方向握住主动轮轴线,则拇指伸直的方向即为轴向力Fa1 的方向。 2 计算载荷和载荷系数 名义载荷上述所求得的各力是用齿轮传递的名义转矩求得的载荷。 计算载荷由于原动机及工作机的性能、齿轮制造及安装误差、齿轮及其支撑件变形等因素的影响,实际作用于齿轮上的载荷要比名义载荷大。因此,在计算齿轮传动的强度时,用载荷系数K对名义载荷进行修正,名义载荷与载荷系数的乘积称为计算载荷。 法向计算载荷Fnc 为: 式中:K -载荷系数 KA-使用系数
机械设计齿轮传动设计答案解析
题10-6 图示为二级斜齿圆柱齿轮减速器,第一级斜齿轮的螺旋角1β的旋向已给出。 (1)为使Ⅱ轴轴承所受轴向力较小,试确定第二级斜齿轮螺旋角β的旋向,并画出各轮轴向力 、径向力及圆周力的方向。 (2) 若已知第一级齿轮的参数为:Z 1=19,Z 2=85,m n =5mm,020=n α,a=265mm, 轮1的传动功率P=,n 1=275 r/min 。试求轮1上所受各力的大小。 解答: 1.各力方向:见题解10-6图。 2.各力的大小:m N 045.217m N 27525.6 955095501 11?=??= ?= n P T 148.11,9811.0265 2) 8519(52)(cos 211==?+?=+= ββa z z n m ; mm 83.96cos 1 1==βz n m d ; N 883tan ,N 1663cos tan ,N 448320********* 1 1====== ββαt a t r t F F n F F d T F ; 题10-7 图示为直齿圆锥齿轮-斜齿圆柱齿轮减速器,为使Ⅱ轴上的轴向力抵消一部分,试确定一对斜齿圆柱齿轮螺旋线的方向;并画出各齿轮轴向力、径向力及圆周力的方向。 解答:齿轮3为右旋,齿轮4为左旋; 力的方向见题解10-7图。 题解10-6图 题10-6图
题10-9 设计一冶金机械上用的电动机驱动的闭式斜齿圆柱齿轮传动, 已知:P = 15 kW,n 1 =730 r/min,n 2 =130 r/min,齿轮按8级精度加工,载荷有严重冲击,工作时间t =10000h,齿轮相对于轴承为非对称布置,但轴的刚度较大,设备可靠度要求较高,体积要求较小。(建议两轮材料都选用硬齿面) 解题分析:选材料→确定许用应力→硬齿面,按轮齿的弯曲疲劳强度确定齿轮的模数→确定齿轮的参数和几何尺寸→校核齿轮的接触疲劳强度→校核齿轮的圆周速度 解答:根据题意,该对齿轮应该选用硬齿面,其失效形式以轮齿弯曲疲劳折断为主。 1. 选材料 大、小齿轮均选用20CrMnTi 钢渗碳淬火([1]表11-2),硬度为56~62HRC ,由[1]图 11-12 和[1]图11-13查得:MPa 1500,MPa 430lim lim ==H F σσ 2.按轮齿弯曲疲劳强度进行设计 (1)确定FP σ 按[1]式(11-7 P227)计算,取6.1,2min ==F ST S Y ;齿轮的循环次数: 8111038.41000017306060?=???==at n N ,取11=N Y ,则: 538MPa MPa 16 .124301m in lim 1=??== N F ST F FP Y S Y σσ (2)计算小齿轮的名义转矩T 1