数控立铣刀切削条件相关参数刃数及特点及磨削计算公式
切削加工常用计算公式
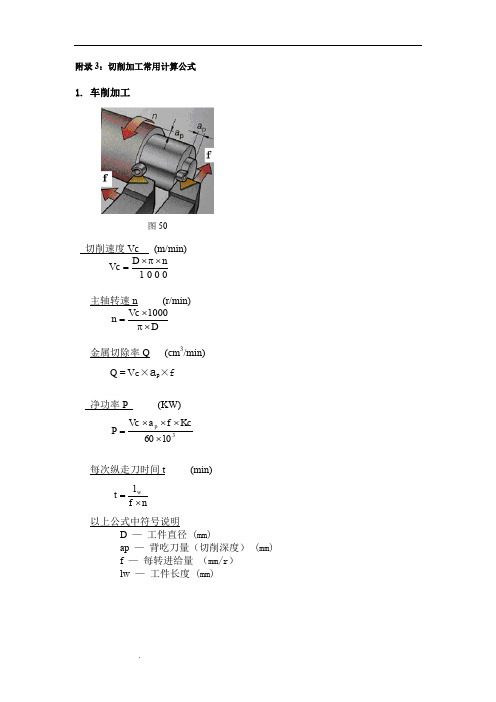
附录3:切削加工常用计算公式1.切削速度Vc (m/min)1000nD Vc ⨯π⨯=主轴转速n (r/min)D 1000Vc n ⨯π⨯=金属切除率Q (cm 3/min)Q = V c ×a p ×f净功率P (KW)3p 1060Kcf a V c P ⨯⨯⨯⨯=每次纵走刀时间t (min)n f l t w⨯=以上公式中符号说明D — 工件直径 (mm)ap — 背吃刀量(切削深度)(mm)f — 每转进给量 (mm/r )lw — 工件长度 (mm)铣削速度Vc (m/min)1000nD Vc ⨯π⨯=主轴转速n (r/min)D 1000Vc n ⨯π⨯=每齿进给量fz (mm)z n Vffz ⨯=工作台进给速度Vf (mm/min)z n fz Vf ⨯⨯=金属去除率Q (cm 3/min)1000Vfae ap Q ⨯⨯=净功率P (KW)61060KcVf ae ap P ⨯⨯⨯⨯=扭矩M (Nm)n 1030P M 3⨯π⨯⨯= 以上公式中符号说明D — 实际切削深度处的铣刀直径(mm ) Z — 铣刀齿数a p — 轴向切深 (mm)a e — 径向切深 (mm)切削速度Vc (m/min)1000n d Vc ⨯π⨯=主轴转速n (r/min)d1000Vc n ⨯π⨯=每转进给量f (mm/r)nVf f =进给速度Vf (mm/min)n f Vf ⨯=金属切除率Q (cm 3/min)4Vc f d Q ⨯⨯=净功率P (KW)310240kc d Vc f P ⨯⨯⨯⨯=扭矩M (Nm)n1030P M 3⨯π⨯⨯=以上公式中符号说明:d — 钻头直径 (mm)kc1 — 为前角γo=0、切削厚度hm=1mm 、切削面积为1mm 2时所需的切削力。
(N/mm 2)mc — 为切削厚度指数,表示切削厚度对切削力的影响程度,mc 值越大表示切削厚度的变化对切削力的影响越大,反之,则越小γo — 前角 (度)。
铣刀修磨次数计算公式

铣刀修磨次数计算公式铣刀是一种常用的切削工具,用于金属加工、木工和其他材料的切削加工。
随着铣刀的使用,刀具会逐渐磨损,需要定期进行修磨以保持刀具的切削性能和使用寿命。
而对于工程师和操作人员来说,如何准确地计算铣刀的修磨次数是非常重要的,因为这将直接影响到生产效率和成本控制。
铣刀修磨次数的计算公式是一个关键的工程参数,它可以帮助工程师和操作人员准确地预测铣刀的使用寿命,合理安排刀具的更换和修磨计划,从而保证生产线的连续运转和产品的质量稳定。
在本文中,我们将介绍铣刀修磨次数的计算公式及其相关的工程知识,希望能够为相关行业的专业人士提供一些参考和帮助。
首先,我们需要了解铣刀的磨损规律。
一般来说,铣刀的磨损是一个逐渐累积的过程,主要包括刀尖磨损、刀身磨损和刀具断裂等。
这些磨损会导致刀具的切削性能下降,同时也会增加工件的表面粗糙度和加工质量的不稳定性。
因此,及时进行修磨是非常重要的。
其次,我们需要了解铣刀修磨次数的计算方法。
一般来说,铣刀的修磨次数可以通过以下公式进行计算:修磨次数 = 刀具使用寿命 / 刀具修磨量。
其中,刀具使用寿命是指刀具在正常工作条件下能够连续加工的工件数量,通常以件或小时为单位;刀具修磨量是指每次修磨后刀具的磨损量,通常以毫米或厘米为单位。
通过这个公式,我们可以比较准确地预测铣刀的修磨次数,从而合理安排刀具的更换和修磨计划。
在实际应用中,我们还需要考虑一些其他因素。
例如,刀具的材料、刀具的结构、切削参数、加工材料等都会对修磨次数产生影响。
因此,在具体计算时,我们需要结合这些因素进行综合考虑,以确保计算结果的准确性和可靠性。
铣刀修磨次数的计算公式是一个非常重要的工程参数,它直接关系到生产效率和成本控制。
在实际应用中,我们需要充分考虑刀具的磨损规律和相关因素,合理地进行计算和预测,从而保证生产线的连续运转和产品的质量稳定。
希望本文能够对相关行业的专业人士提供一些参考和帮助,同时也希望在未来的工程实践中能够进一步完善和优化这个计算公式,以满足不同行业的需求。
铣削参数计算方法

Ks 数值
190 210 240 190 245 93 120 70
Ks × W × fZ × Z × N × d 6120000 ×
PHP =
6120 4500
× PKW
Ks : 比切削阻力值 [kgf/mm2] η : 机械效率 (0.7 ~ 0.8)
青铜、黄铜
● 切屑排出量
Q= W×F×d 1000
技术资料 计算式
● 切削速度
V=
× D × N
V : 切削速度 [m/min] D : 铣刀盘径 [mm] N : 主轴旋转数 [min-1]
d D
铣削加工
1000
● 工作台进给量与进刀量
fz = F Z ×N
fz : 进刀量 [mm/ 刃 ] F : 工作台进给量 [mm/min] Z : 铣刀盘刃数 N : 主轴旋转数 [min-1]
D L′ F L
549
技术资料 计算式
● 真斜角
tanT = tanR × cosC + tanA × sinC
C I T A (+)
铣削加工
● 刃斜角
tanI = tanA × cosC - tanR × sinC
A : 轴向斜角 A.R. [° ] (-90° < A < 90°) R : 径向斜角 R.R. [° ] (-90° < R < 90°) C : 侧切刃角 [° ] (0° < C < 90°) T : 直斜角 [° ] (-90° < T < 90°) I : 刃倾角 [° ] (-90° < I < 90°)
=
Pkw =
D 20
×
数控铣削加工参数的确定原则
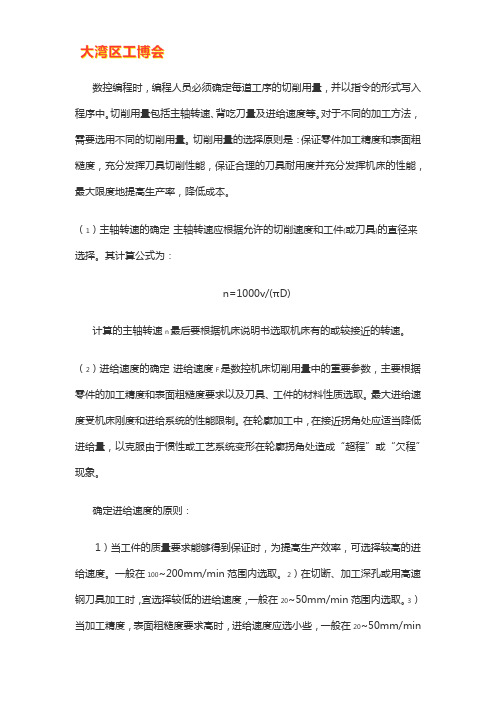
数控编程时,编程人员必须确定每道工序的切削用量,并以指令的形式写入程序中。
切削用量包括主轴转速、背吃刀量及进给速度等。
对于不同的加工方法,需要选用不同的切削用量。
切削用量的选择原则是:保证零件加工精度和表面粗糙度,充分发挥刀具切削性能,保证合理的刀具耐用度并充分发挥机床的性能,最大限度地提高生产率,降低成本。
(1)主轴转速的确定主轴转速应根据允许的切削速度和工件(或刀具)的直径来选择。
其计算公式为:n=1000v/(πD)计算的主轴转速n最后要根据机床说明书选取机床有的或较接近的转速。
(2)进给速度的确定进给速度F是数控机床切削用量中的重要参数,主要根据零件的加工精度和表面粗糙度要求以及刀具、工件的材料性质选取。
最大进给速度受机床刚度和进给系统的性能限制。
在轮廓加工中,在接近拐角处应适当降低进给量,以克服由于惯性或工艺系统变形在轮廓拐角处造成“超程”或“欠程”现象。
确定进给速度的原则:1)当工件的质量要求能够得到保证时,为提高生产效率,可选择较高的进给速度。
一般在100~200mm/min范围内选取。
2)在切断、加工深孔或用高速钢刀具加工时,宜选择较低的进给速度,一般在20~50mm/min范围内选取。
3)当加工精度,表面粗糙度要求高时,进给速度应选小些,一般在20~50mm/min范围内选取。
4)刀具空行程时,特别是远距离“回零”时,可以选择该机床数控系统给定的最高进给速度。
(3)背吃刀量确定背吃刀量(a p)根据机床、工件和刀具的刚度来决定,在刚度允许的条件下,应尽可能使背吃刀量等于工件的加工余量,这样可以减少走刀次数,提高生产效率。
为了保证加工表面质量,可留0.2~0.5mm精加工余量。
选择切削参数和常用计算公式

每加工一个零件的时间=100/(0.2x976)=0.51分钟 车削功率P=(230x3x0.2x2900)/60037.2=6.7千瓦
Vc xap xfr xkc P= 60037.2
车削力=2900 x0.2 x3=1740牛顿=177.5公斤 车削扭矩T=1740 x37.5=65牛顿米
T= F力 x(D/2) =P x9549/RPM
铣削三要素
Cutting data formulas
Power consuming and Torque force
Torque (Nm) = kW (nett) x 9549 RPM
面铣刀直径80mm, 6个刀片刃口,铣削的材料分别为铸 铝合金(kc:800) 和奥氏体不锈钢(kc:2400), 若刀片的切 削速度为600m/min和150m/min, 每齿进刀为fz=0.2mm/z, 切深ap=4mm, 切宽ae=60mm, 问他们的铣削功率和扭矩
F力=Kc xfr xap
Vc
1/2Vc
Vc
举例:镗削奥氏体不锈钢,工件硬度HB200, 工 件直径75mm,切深3mm,走刀量0.2mm/r, 切削速 度115m/min, 材料单位切削力为2900N/mm2,加 工长度为100mm RPM=(115X1000)/(3.14X75)=488转每分钟 金属去除率V=115x2x0.2=46 立方厘米每分钟
�=0.9,计算钻削功率和扭矩。
d: core diamerer
D: hole diameter
扭矩 T=1.2 �9549/636=18NM
转速 n=40 �1000/3.14 �20=636rpm
钻削功率P=4500 � 0.07 �40 �20/240000 �0.9=1.2KW
(16)立加编程—如何计算切削参数

(16)立加编程—如何计算切削参数在实际加工中经常有一个问题困扰我们,就是当拿到一把新刀具时,刀具在编程时的转速、进给怎么给,这不仅涉及到工件的加工效率而且对刀具的寿命有很大影响,一旦给的不合适,刀具的尖叫声整个车间都能听见,今天我们就来聊聊在加工中心上常用铣刀的参数如何计算。
先了解几个加工参数中的概念,见图示(1):图示(1)铣削加工中常用到的两个公式如下:图示(2)图示(2)中的 n 就是我们编程中的 S ,Vc为线速度;π是常数,按3.14代入即可;Dm是刀具直径,而Vf就是编程中的F ,Fz为每齿进给量,Zc为刀具参与切削的齿数。
从以上参数可以得知,只有两个数值是未知的,分别为线速度Vc和每齿进给量Fz。
下面咱们就分类了解一下常用刀具的这两个参数怎么给:第一种、可转位面铣刀类图示(3)使用以上面铣刀加工钢制品时,Vc=120-250加工45#钢,Vc=180加工Q235钢,Vc=250加工模具钢,Vc=120加工铸铁,Vc=150相当于材料硬度高时,线速度Vc就小一些,材料硬度软时,线速度Vc就给高一些。
每齿进给量Fz=0.05-0.25加工45#钢,Fz=0.15加工Q235钢,Fz=0.25加工模具钢,Fz =0.1加工铸铁,Fz =0.25加工不锈钢时,Vc=80-180我一般用Vc=120每齿进给量Fz=0.05-0.15我一般用Fz =0.1加工钛合金时,Vc=60-150我一般用Vc=60每齿进给量Fz=0.05-0.15我一般用Fz =0.1加工高温合金时,Vc=30-60我一般用Vc=40每齿进给量Fz=0.05-0.15我一般用Fz =0.05加工铝合金,Vc=300-1000我一般用Vc=400-500米,同时看机床最高转速,如最高转速8000时,刀具转速我给5000每齿进给量Fz=0.05-0.5我一般用Fz =0.3当需要较高表面粗糙度时,Fz可以给0.05假如我们用D50面铣刀加工45#,刀具齿数5时,它的转速进给为:S=N=(180*1000)/(3.14*50)≈1150F=Vf=0.15*5*1150≈860像普通刀具咱们转速、进给精确到十位即可,不必精确到个位!以上刀具参数前提是使用相对应的加工刀片。
切削条件计算公式
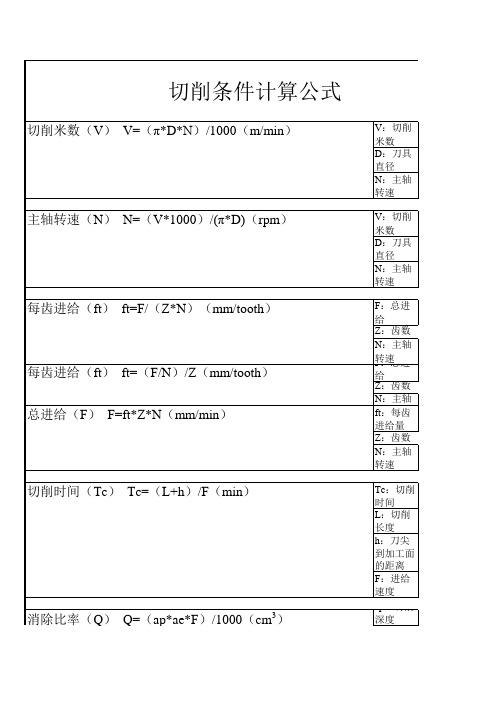
表面粗糙度(h) h=ft2/(40*D)
切削马力(HP) HP=(ap*ae*F*kc)/(60*106*η)(KW)
砂轮线速度的转换公式
Vc:切削米数
切削米数(Vc): Vc=(π*D*n)/1000*60(m/s) 转速(n): n=(Vc*1000*60)/π*D(RPM)
D:砂轮直径 n:主轴转速 Vc:切削米数 D:砂轮直径 n:主轴转速
主轴转速(N) N=(V*1000)/(π*D)(rpm)
每齿进给(ft) ft=F/(Z*N)(mm/tooth) 每齿进给(ft) ft=(F/N)/Z(mm/tooth) 总进给(F) F=ft*Z*N(mm/min)
切削时间(Tc) Tc=(L+h)/F(min)
消除比率(Q) Q=(ap*ae*F)/1000(cm3)
切削米数正常为1~3mm/MIN
V:切削米数 D:刀具直径 N:主轴转速 V:切削米数 D:刀具直径 N:主轴转速 F:总进给
主轴转速(N) N=(V*1000)/(π*D)(rpm) 每转进给(ft) ft=转速*螺距
每转进给(ft) ft=转速*螺距
N:主轴转速
导程的转换公式
导程(L) L=(π*D)/(Tanα)
钻头速度的转换公式
切削米数(V) V=(π*D*N)/1000(m/min)
V:切削米数 D:刀具直径 N:主轴转速 V:切削米数 D:刀具直径 N:主轴转速 F:总进给 N:主轴转速
主轴转速(N) N=(V*1000)/(π*D)(rpm) 每转进给(ft) ft=F/N(mm/tooth)
丝锥速度的转换公式
切削条件计算公式砂轮线速度的转换公式钻头速度的转换公式丝锥速度的转换公式切削米数vvdn1000mminv
切削速度计算公式

切削速度计算公式切削速度是切削加工中一个十分重要的参数,它表示刀具在切削过程中每分钟切削的长度。
切削速度的计算公式可以通过根据工件材料、切削刀具和刀具直径来确定。
以下是常见的切削速度计算公式。
1.单刃铣刀的切削速度计算公式:Vc=π*Dc*n其中,Vc表示切削速度(单位:m/min),Dc表示刀具直径(单位:mm),n表示主轴转速(单位:rpm)。
2.钢材的切削速度计算公式:Vc=(π*Dc*n)/1000其中,Vc表示切削速度(单位:m/min),Dc表示刀具直径(单位:mm),n表示主轴转速(单位:rpm)。
3.车削加工中的切削速度计算公式:Vc=(π*Dc*n)/1000其中,Vc表示切削速度(单位:m/min),Dc表示刀具直径(单位:mm),n表示主轴转速(单位:rpm)。
4.钻削加工中的切削速度计算公式:Vc=(π*Dc*n)/1000其中,Vc表示切削速度(单位:m/min),Dc表示刀具直径(单位:mm),n表示主轴转速(单位:rpm)。
5.铣削加工中的切削速度计算公式:Vc = nc * fz * z其中,Vc表示切削速度(单位:mm/min),nc表示铣削系数(单位:mm/z),fz表示进给速度(单位:mm/min),z表示齿数。
需要注意的是,以上计算公式中的单位可能有所不同,具体应根据实际情况进行转换。
切削速度的选择直接影响到加工效率和工件表面质量,因此在具体应用中需要综合考虑工件材料特性、刀具耐磨性和工艺要求等因素,选择合适的切削速度。
同时,切削过程中应注意刀具的冷却润滑,以减少切削热量对刀具和工件的损伤。