TBM刀具
刀具检查规程

刀具检查规程TBM共有51把刀具,其中中心刀8把(1#~8#)、边刀8把(44#~51#)、正滚刀35把(9#~43#)。
掘进过程中由于受围岩条件、刀具的布置、掘进参数、机械状况和司机的操作习惯等多种因素的影响,每把刀的使用寿命迥然不同;即使同一部位的刀具,也无法预测出精确的寿命;而且随着机械的剧烈振动和掘进推力的急剧变化,即使是新换的刀具,时常会出现预想不到的挡圈脱落、刀刃崩落、偏磨、刀圈移位、密封漏油和轴承破损等非正常损伤。
刀具损伤只有通过准确的检查才能及时发现。
通过检查,可以摸索刀具在各类围岩下的磨损规律;指导司机选择最佳掘进参数、正确调向、柔和操作,达到减轻磨损、节省刀具的目的。
一、刀盘检查掘进中刀盘上的刀具作业工况十分恶劣,既要承受巨大的载荷和振动、石碴与水的冲击、又要承受剧烈的摩擦和温度升高的考验,刀盘的掘进性能状态不断变化,为此,必须定期进行检查,按要求对刀具状态进行判定,对发现的问题及时进行调整、更换和维修,恢复刀盘的掘进性能,保证刀盘在预期内能连续掘进。
刀盘上的51把刀,若有一把刀损坏都必须停机检查更换,尤其是边刀,更要严格检查、及时更换。
刀盘和刀具的检查、整备,是TBM施工中的首要工作,它关系到当日是否能连续掘进和后期的施工安排。
负责刀盘的技术和管理人员应根据当前的地质条件、掘进参数、刀具和刮碴板的状态等安排好当日刀盘的整备内容和计划好后期要进行的刀盘维修工作。
刀盘检查和整备工作的基本要求,首先是在预期掘进时间内,不因检查整备不当,发生掘进中刀具状态失常的停机故障。
第二是要尽可能减少占用掘进工班时间进行刀盘作业,以提高机器的利用率。
二、检查周期1、检验时机(1)在最初掘进的500英尺(150m)每隔4小时检查一次刀具。
(2)在保证最初500英尺(150m)的刀具检查之后,这种检查可以延长到每天一次。
不过通常是每班检查一次。
连续两个掘进工班后,必须对掘进后的刀具运用情况作全面彻底的检验;(3)更换新刀后的例行检查中,当发现刀盘区出现异常情况或石渣中发现钢的磨损颗粒时,应立即进行检验;硬岩条件下,当发现每两个掘进循环的洞壁结合面呈显著的波浪形或调向过大时,应考虑到边刀偏磨和漏油的可能性,及时安排检查。
国产双护盾TBM刀具失效形式及刀具使用管理
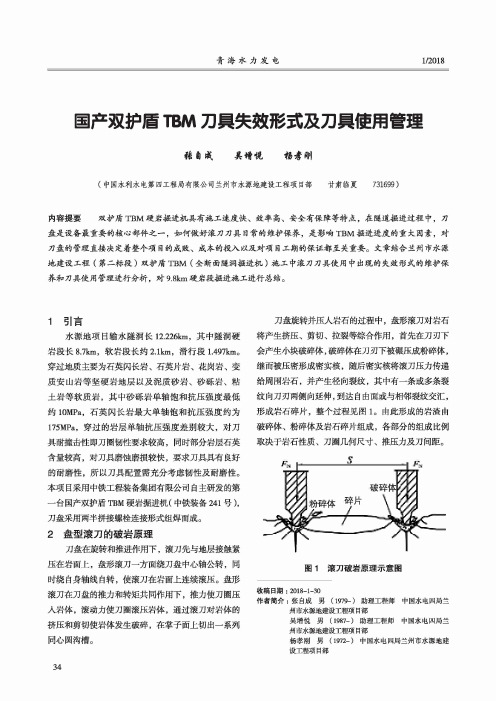
国产双护盾TBM刀具失效形式及刀具使用管理成 具靖说杨考剛(中国水利水电第四工程局有限公司兰州市水源地建设工程项目部 甘肃临夏 731699)内容提要双护盾TBM硬岩掘进机具有施工速度快、效率高、安全有保障等特点,在隧道掘进过程中,刀盘是设备最重要的核心部件之一,如何做好滚刀刀具日常的维护保养,是影响TBM掘进进度的重大因素,对 刀盘的管理直接决定着整个项目的成败、成本的投入以及对项目工期的保证都至关重要。
文章结合兰州市水源地建设工程(第二标段)双护盾TBM (全断面隧洞掘进机)施工中滚刀刀具使用中出现的失效形式的维护保 养和刀具使用管理进行分析,对9.8km硬岩段掘进施工进行总结。
1引言水源地项目输水隧洞长12.226km,其中隧洞硬 岩段长8.7km,软岩段长约2.1km,滑行段1.497km。
穿过地质主要为石英闪长岩、石英片岩、花岗岩、变 质安山岩等坚硬岩地层以及泥质砂岩、砂砾岩、粘 土岩等软质岩,其中砂砾岩单轴饱和抗压强度最低 约lOMPa,石英闪长岩最大单轴饱和抗压强度约为 175MPa,穿过的岩层单轴抗压强度差别较大,对刀 具耐撞击性即刀圈韧性要求较高,同时部分岩层石英 含量较髙,对刀具磨蚀磨损较快,要求刀具具有良好 的耐磨性,所以刀具配置需充分考虑韧性及耐磨性。
本项目采用中铁工程装备集团有限公司自主研发的第 一台国产双护盾TBM硬岩掘进机(中铁装备241号),刀盘采用两半拼接螺栓连接形式组焊而成。
2盘型滚刀的破岩原理刀盘在旋转和推进作用下,滚刀先与地层接触紧 压在岩面上,盘形滚刀一方面绕刀盘中心轴公转,同时绕自身轴线自转,使滚刀在岩面上连续滚压。
盘形 滚刀在刀盘的推力和转矩共同作用下,推力使刀圈压 入岩体,滚动力使刀圈滚压岩体,通过滚刀对岩体的 挤压和剪切使岩体发生破碎,在掌子面上切出一系列 同心圆沟槽。
刀盘旋转并压人岩石的过程中,盘形滚刀对岩石 将产生挤压、剪切、拉裂等综合作用,首先在刀刃下 会产生小块破碎体,破碎体在刀刃下被碾压成粉碎体,继而被压密形成密实核,随后密实核将滚刀压力传递 给周围岩石,并产生径向裂纹,其中有一条或多条裂 纹向刀刃两侧向延伸,到达自由面或与相邻裂纹交汇, 形成岩石碎片,整个过程见图1。
TBM的主要构造

TBM的主要构造:
1、刀盘:包括刀盘内圈、铲斗、大轴承、刀具等。
2、刀盘支撑装置:由支撑壳体、前支撑、侧支撑、护盾及挡坐板。
3、传动系统:由四台150kw电动机通过联轴节、二级行星齿轮减速器和末级齿轮、驱动大齿圈带动刀盘旋转。
此外,机器上还装有一套刀盘液压启动装置。
4、机架和机尾:支撑水平框架的机架,由上下大梁和前后立柱组成空间框架。
5、除尘系统:设置旋风水膜除尘器和轴流通风机,将流过粉尘离析的空气送出洞外。
同时另有一路进风管路,将新鲜空气送到机器旁边,保证操作人员的环境卫生。
6、液压系统:由供油及操作系统组成。
7、润滑系统:包括稀油和干油两部分。
8、电气系统:
9、激光指向:机器上装有固定的前靶和后靶,根据激光束在两靶上位置的差别,判断机器方位的偏差。
10、机器方位调整:掘进坡度调整和水平方位调整。
TBM滚刀刀圈材料合金成分对组织和耐磨性能的影响
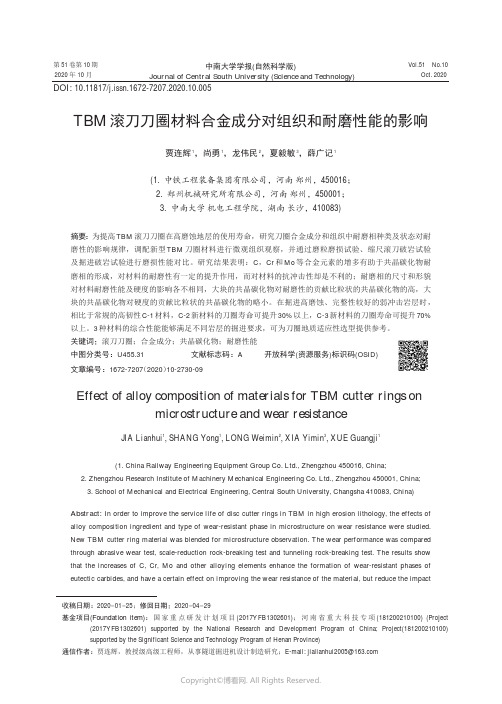
第51卷第10期2020年10月中南大学学报(自然科学版)Journal of Central South University (Science and Technology)V ol.51No.10Oct.2020TBM 滚刀刀圈材料合金成分对组织和耐磨性能的影响贾连辉1,尚勇1,龙伟民2,夏毅敏3,薛广记1(1.中铁工程装备集团有限公司,河南郑州,450016;2.郑州机械研究所有限公司,河南郑州,450001;3.中南大学机电工程学院,湖南长沙,410083)摘要:为提高TBM 滚刀刀圈在高磨蚀地层的使用寿命,研究刀圈合金成分和组织中耐磨相种类及状态对耐磨性的影响规律,调配新型TBM 刀圈材料进行微观组织观察,并通过磨粒磨损试验、缩尺滚刀破岩试验及掘进破岩试验进行磨损性能对比。
研究结果表明:C ,Cr 和Mo 等合金元素的增多有助于共晶碳化物耐磨相的形成,对材料的耐磨性有一定的提升作用,而对材料的抗冲击性却是不利的;耐磨相的尺寸和形貌对材料耐磨性能及硬度的影响各不相同,大块的共晶碳化物对耐磨性的贡献比粒状的共晶碳化物的高,大块的共晶碳化物对硬度的贡献比粒状的共晶碳化物的略小。
在掘进高磨蚀、完整性较好的弱冲击岩层时,相比于常规的高韧性C-1材料,C-2新材料的刀圈寿命可提升30%以上,C-3新材料的刀圈寿命可提升70%以上。
3种材料的综合性能能够满足不同岩层的掘进要求,可为刀圈地质适应性选型提供参考。
关键词:滚刀刀圈;合金成分;共晶碳化物;耐磨性能中图分类号:U455.31文献标志码:A开放科学(资源服务)标识码(OSID)文章编号:1672-7207(2020)10-2730-09Effect of alloy composition of materials for TBM cutter rings onmicrostructure and wear resistanceJIA Lianhui 1,SHANG Yong 1,LONG Weimin 2,XIA Yimin 3,XUE Guangji 1(1.China Railway Engineering Equipment Group Co.Ltd.,Zhengzhou 450016,China;2.Zhengzhou Research Institute of Machinery Mechanical Engineering Co.Ltd.,Zhengzhou 450001,China;3.School of Mechanical and Electrical Engineering,Central South University,Changsha 410083,China)Abstract:In order to improve the service life of disc cutter rings in TBM in high erosion lithology,the effects of alloy composition ingredient and type of wear-resistant phase in microstructure on wear resistance were studied.New TBM cutter ring material was blended for microstructure observation.The wear performance was compared through abrasive wear test,scale-reduction rock-breaking test and tunneling rock-breaking test.The results show that the increases of C,Cr,Mo and other alloying elements enhance the formation of wear-resistant phases of eutectic carbides,and have a certain effect on improving the wear resistance of the material,but reduce the impactDOI:10.11817/j.issn.1672-7207.2020.10.005收稿日期:2020−01−25;修回日期:2020−04−29基金项目(Foundation item):国家重点研发计划项目(2017YFB1302601);河南省重大科技专项(181200210100)(Project(2017YFB1302601)supported by the National Research and Development Program of China;Project(181200210100)supported by the Significant Science and Technology Program of Henan Province)通信作者:贾连辉,教授级高级工程师,从事隧道掘进机设计制造研究;E-mail:**********************第10期贾连辉,等:TBM滚刀刀圈材料合金成分对组织和耐磨性能的影响resistance of the material.The effect of the size and morphology of the wear-resistant phase on the wear resistance and hardness of the material is also rge eutectic carbides contribute more to wear resistance than the granular eutectic carbides,and large eutectic carbides contribute slightly less to the hardness than the granular eutectic carbides.In driving high abrasion and weak integrity rock formations,compared with the conventional high toughness C-1material,the life of the cutter ring of the new C-2material can be increased by more than30%, and C-3new material ring life can be increased by more than70%.The comprehensive performance of the three materials can meet the requirements of different rock formations,which provides reference for the geological adaptability selection of cutter ring.Key words:disc cutter ring;alloy composition;eutectic carbide;wear-resisting performance岩石隧道掘进机(tunnel boring machine,TBM)掘进过程中伴随刀盘转动,刀盘上安装的盘形滚刀刀圈直接与岩体相互作用,滚刀贯入岩体滚动挤压,岩石表面产生局部变形并出现微观裂纹,随着挤压力增大,微观裂纹发展成为主裂纹并贯通,形成岩片破碎[1−2]。
TBM滚刀磨损研究现状及展望
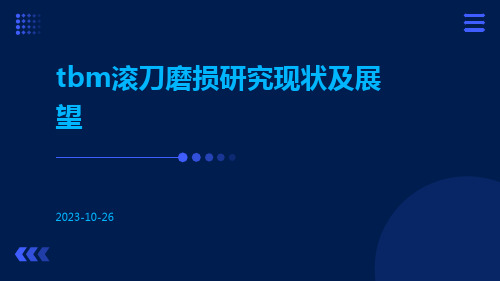
03
随着隧道施工向高速度、高效率、高精度方向发展,对TBM滚刀磨损的研究显得尤为重要。
通过对TBM滚刀磨损的研究,可以深入了解滚刀磨损的机理和规律,为优化滚刀设计和提高隧道施工效率提供理论支持。
对于隧道施工单位而言,通过研究滚刀磨损规律,可以制定更为合理的维护和更换滚刀的策略,提高施工经济效益。
改进滚刀结构设计
利用传感器和监测系统,实时监测滚刀的磨损状态和地下岩层的分布情况,为调整施工参数和预防性维护提供依据。
发展智能监测技术
THANKS
感谢观看
tbm滚刀磨损研究现状及展望
2023-10-26
目录
contents
研究背景和意义tbm滚刀磨损研究现状滚刀磨损对tbm性能的影响展望与挑战结论与建议
01
研究背景和意义
01
TBM(Tunnel Boring Machine)是一种先进的隧道施工设备,广泛应用于全球各地的隧道建设中。
研究背景
02
开发了基于图像识别、振动分析、声发射等技术的在线监测系统,用于实时监测滚刀的磨损状态。
滚刀磨损监测技术
建立了滚刀磨损数据共享平台,汇集了不同地质条件下的滚刀磨损数据,为工程实践提供参考。
滚刀磨损数据库建设
滚刀磨损研究起步较晚
工程应用与理论研究结合
创新性研究成果
国的影响
研究结论
滚刀磨损的主要原因是岩石的硬度、裂隙发育程度、地下水等因素,这些因素在不同地层条件下是不断变化的。
滚刀磨损的后果包括刀具损坏、更换频繁、施工周期延长和成本增加等,对隧道施工和工程安全造成不利影响。
目前,针对滚刀磨损的研究主要集中在材料、热处理和结构设计等方面,虽然取得了一定的成果,但仍存在许多亟待解决的问题。
TBM开仓换刀施工
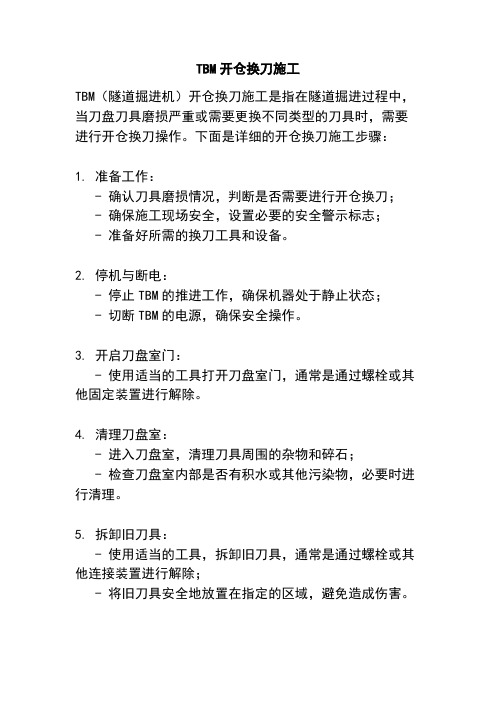
TBM开仓换刀施工TBM(隧道掘进机)开仓换刀施工是指在隧道掘进过程中,当刀盘刀具磨损严重或需要更换不同类型的刀具时,需要进行开仓换刀操作。
下面是详细的开仓换刀施工步骤:1. 准备工作:- 确认刀具磨损情况,判断是否需要进行开仓换刀; - 确保施工现场安全,设置必要的安全警示标志;- 准备好所需的换刀工具和设备。
2. 停机与断电:- 停止TBM的推进工作,确保机器处于静止状态;- 切断TBM的电源,确保安全操作。
3. 开启刀盘室门:- 使用适当的工具打开刀盘室门,通常是通过螺栓或其他固定装置进行解除。
4. 清理刀盘室:- 进入刀盘室,清理刀具周围的杂物和碎石;- 检查刀盘室内部是否有积水或其他污染物,必要时进行清理。
5. 拆卸旧刀具:- 使用适当的工具,拆卸旧刀具,通常是通过螺栓或其他连接装置进行解除;- 将旧刀具安全地放置在指定的区域,避免造成伤害。
6. 安装新刀具:- 将新刀具按照正确的顺序和位置进行安装;- 使用适当的工具,确保新刀具与刀盘正确连接,并进行紧固。
7. 检查刀具安装:- 检查新刀具的安装情况,确保刀具安全可靠;- 检查刀具与刀盘的配合是否良好,避免出现松动或偏移现象。
8. 关闭刀盘室门:- 关闭刀盘室门,确保门的密封性和安全性;- 使用适当的工具,将刀盘室门紧固。
9. 恢复电源与启动:- 恢复TBM的电源供应;- 启动TBM,进行必要的测试和调试,确保刀具更换后的正常运行。
以上就是TBM开仓换刀施工的详细步骤。
在进行该操作时,需要严格按照相关规范和安全要求进行操作,确保施工过程的安全和顺利进行。
TBM刀具

TBM刀具检修工艺的完善中铁十八局集团有限公司隧道工程公司周雁领齐梦学TBM(隧道掘进机)作为长大隧道施工最有效的大型综合机械,使用刀盘直接接触掌子面进行破岩,因此安装在刀盘上的刀具的使用和维修情况直接影响了隧道施工的进程,同时,刀具的消耗也是TBM施工成本中所占比例最大的项目之一,要从维修刀具的可靠性来提高掘进速度、从降低消耗来降低掘进成本。
原技术文件中的检修工艺过于简单,必须根据施工中出现的各种情况,具体问题,具体分析,区别对待,对TB880E型掘进机17"盘形滚刀的检查和维修继续进行全面而深入的研究与总结,并用以指导TBM掘进施工。
一、刀具检查维修要达到的目的刀具经检查维修后,达到安装后在掘进过程中不出现因检修不当产生的故障,造成停机更换。
从统计角度讲,维修刀具产生故障的比例不应超过5%,以减少对TBM利用率和掘进速度的影响。
1、通过对刀具的检查与维修,分析刀具及其零件的生产质量、前期检修的质量、刀具安装存在的问题、地质变化和TBM操作等因素对刀具损坏的影响,及时提出分析及反馈意见。
2、刀具维修中,不可盲目更换零部件,对损坏的零件要修复,既要保证维修刀具的质量,又要严格零件报废条件,作到物尽其用、节约成本。
二、维修前的刀具清理与检查从刀盘上更换下的刀具,要及时进行清理,将表面粘渣,尤其是对内六角扳手孔内的粘渣及滑动密封腔内的灰渣要仔细进行清理。
清理完成后进行以下项目的检查,其结果记录在《刀具维修检查》表中:①查刀具编号,并按编号进行登记,不清晰者,确认后补作。
②检查外表,是否有漏油、刀圈偏磨、端盖螺栓松动或丢失、挡圈丢失和断裂、M24螺孔损坏和螺栓断裂等异常情况存在。
③检查刀圈的磨损量,用专用刀具卡规测量,倾斜状磨损的刀圈要测出最大与最小值。
④检查刀具轴承扭矩大小和转动是否均匀。
检查扭矩前,一定要将密封腔内的渣土用高压风清理干净,检查扭矩应转动360度以上,凡有手感振动者为转动不均匀。
三、刀具维修检查项目的制定根据刀具使用卡片(记录每把刀上机掘进过程和刀具的维修过程)、刀盘日常检查记录(记录刀具在刀盘上工作中发生过的漏油、螺栓松动等异常情况)和刀具维修前的检查记录制定各刀具的维修项目,并标记在刀具上。
TBM开仓换刀施工
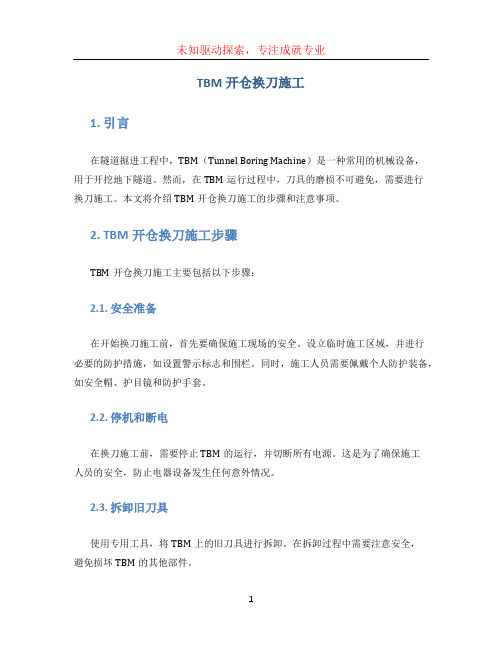
TBM开仓换刀施工1. 引言在隧道掘进工程中,TBM(Tunnel Boring Machine)是一种常用的机械设备,用于开挖地下隧道。
然而,在TBM运行过程中,刀具的磨损不可避免,需要进行换刀施工。
本文将介绍TBM开仓换刀施工的步骤和注意事项。
2. TBM开仓换刀施工步骤TBM开仓换刀施工主要包括以下步骤:2.1. 安全准备在开始换刀施工前,首先要确保施工现场的安全。
设立临时施工区域,并进行必要的防护措施,如设置警示标志和围栏。
同时,施工人员需要佩戴个人防护装备,如安全帽、护目镜和防护手套。
2.2. 停机和断电在换刀施工前,需要停止TBM的运行,并切断所有电源。
这是为了确保施工人员的安全,防止电器设备发生任何意外情况。
2.3. 拆卸旧刀具使用专用工具,将TBM上的旧刀具进行拆卸。
在拆卸过程中需要注意安全,避免损坏TBM的其他部件。
2.4. 清洁工作区在安全拆卸旧刀具后,需要对工作区进行清洁。
清除旧刀具留下的残渣和污垢,以确保新刀具能够正确安装并正常运行。
2.5. 安装新刀具按照TBM厂家提供的说明书,正确安装新的刀具。
确保刀具与TBM的其他部件正确连接,并紧固螺丝。
2.6. 检查和测试安装完新刀具后,进行必要的检查和测试。
检查刀具是否正确安装,各个部件是否完好,并进行简单的功能测试。
2.7. 启动TBM当确认所有步骤都完成并通过测试后,启动TBM,开始下一轮的掘进工作。
3. 注意事项在TBM开仓换刀施工过程中,有几个注意事项需要特别注意:3.1. 安全第一换刀施工前,务必确保施工现场的安全。
施工人员应严格遵守安全操作规程,佩戴个人防护装备,并严禁违章操作。
3.2. 按照说明书操作在拆卸旧刀具和安装新刀具时,务必按照TBM厂家提供的说明书进行操作。
不得擅自修改或忽略任何步骤,以免造成损坏或安全风险。
3.3. 定期维护保养除了换刀施工,定期维护保养也是确保TBM正常运行的关键。
定期检查刀具的磨损情况,并根据需要进行及时维修或更换。
- 1、下载文档前请自行甄别文档内容的完整性,平台不提供额外的编辑、内容补充、找答案等附加服务。
- 2、"仅部分预览"的文档,不可在线预览部分如存在完整性等问题,可反馈申请退款(可完整预览的文档不适用该条件!)。
- 3、如文档侵犯您的权益,请联系客服反馈,我们会尽快为您处理(人工客服工作时间:9:00-18:30)。
TBM刀具检修工艺的完善中铁十八局集团有限公司隧道工程公司周雁领齐梦学TBM(隧道掘进机)作为长大隧道施工最有效的大型综合机械,使用刀盘直接接触掌子面进行破岩,因此安装在刀盘上的刀具的使用和维修情况直接影响了隧道施工的进程,同时,刀具的消耗也是TBM施工成本中所占比例最大的项目之一,要从维修刀具的可靠性来提高掘进速度、从降低消耗来降低掘进成本。
原技术文件中的检修工艺过于简单,必须根据施工中出现的各种情况,具体问题,具体分析,区别对待,对TB880E型掘进机17"盘形滚刀的检查和维修继续进行全面而深入的研究与总结,并用以指导TBM掘进施工。
一、刀具检查维修要达到的目的刀具经检查维修后,达到安装后在掘进过程中不出现因检修不当产生的故障,造成停机更换。
从统计角度讲,维修刀具产生故障的比例不应超过5%,以减少对TBM利用率和掘进速度的影响。
1、通过对刀具的检查与维修,分析刀具及其零件的生产质量、前期检修的质量、刀具安装存在的问题、地质变化和TBM操作等因素对刀具损坏的影响,及时提出分析及反馈意见。
2、刀具维修中,不可盲目更换零部件,对损坏的零件要修复,既要保证维修刀具的质量,又要严格零件报废条件,作到物尽其用、节约成本。
二、维修前的刀具清理与检查从刀盘上更换下的刀具,要及时进行清理,将表面粘渣,尤其是对内六角扳手孔内的粘渣及滑动密封腔内的灰渣要仔细进行清理。
清理完成后进行以下项目的检查,其结果记录在《刀具维修检查》表中:①查刀具编号,并按编号进行登记,不清晰者,确认后补作。
②检查外表,是否有漏油、刀圈偏磨、端盖螺栓松动或丢失、挡圈丢失和断裂、M24螺孔损坏和螺栓断裂等异常情况存在。
③检查刀圈的磨损量,用专用刀具卡规测量,倾斜状磨损的刀圈要测出最大与最小值。
④检查刀具轴承扭矩大小和转动是否均匀。
检查扭矩前,一定要将密封腔内的渣土用高压风清理干净,检查扭矩应转动360度以上,凡有手感振动者为转动不均匀。
三、刀具维修检查项目的制定根据刀具使用卡片(记录每把刀上机掘进过程和刀具的维修过程)、刀盘日常检查记录(记录刀具在刀盘上工作中发生过的漏油、螺栓松动等异常情况)和刀具维修前的检查记录制定各刀具的维修项目,并标记在刀具上。
刀具维修分为解体维修和不解体维修,刀圈切割更换与不更换及特殊部位的损坏(如螺栓孔损坏等)修理等几类。
1、刀圈的更换标准①正刀刀圈磨损量>30mm、磨损量<30mm但移位>5mm,边刀及中心刀磨损量>20mm,刀圈断裂、崩刃,更换新刀圈;②正刀刀圈磨损量<30mm、边刀及中心刀磨损量<10mm的刀圈应保留再使用。
留用刀圈的刀具,若挡圈有丢失、断裂者,应进行相应的维修。
焊接正、边刀挡环时,要使用铜垫,用3.2mm焊条小电流进行焊接,焊加强铁时,要与刀圈有3mm的间隙。
2、刀具的不解体检查维修条件具备以下条件的刀具可不进行拆卸检查维修:①正、边刀扭矩在30N.m至80 N.m的正常范围内,转动均匀;②正刀轴承运转小于900h,边刀轴承运转小于300h;③上次拆卸检查后正刀运转小于300h,边刀运转小于150h;③正、边刀的挡圈、端盖螺栓、M24螺孔等均完好。
3、刀具的解体检查维修条件①正刀轴承运转≥900h、边刀轴承运转≥300h时,拆卸更换轴承;②上次拆检后正刀运转≥300h,边刀运转≥150h,再次进行拆卸检查维修;③正、边刀扭矩小于30N.m或大于80N.m,转不动或转动不均匀者,都应拆卸检查修理;④刀具漏油的,应拆卸检查原因,进行修理;⑤端盖固紧螺栓松动或断裂及M24螺孔损坏和有断螺栓不能取出者,要拆卸检查维修;⑥中心刀正常磨损一个刀圈后,都要进行拆卸检查,轴承报废视检测损坏情况而定。
具备以上条件的刀具要进行拆卸检查维修。
刀具拆卸后,要进行全面检查,更换不可靠零件、橡胶圈和润滑油,恢复轴承扭矩,提高刀具性能的可靠度。
拆卸检查过程中,每拆卸一个零件,都应对零件进行检查,对异常损坏要进行分析和维修或更换,并进行记录。
4、端面密封环的检查维修与润滑油的更换拆开刀具后,首先检查刀具的油量和油中是否有铁末等杂物,把刀具内的油量分为油满、有油,油尽(油干)几种状态。
油满而油中无铁末者,说明端面密封处于良好状态,可继续使用,但要更换橡胶圈。
对油中有铁末和油已经有流失的密封状态,其密封的金属环不能直接使用,修理后可再使用,橡胶圈则应报废。
对刀具拆卸后刀体腔内有石渣、泥浆且密封金属环已断裂或碎为几段、橡胶圈撕裂的情况,端面密封报废,并应仔细分析其损坏原因。
根据施工中得出的经验,正常使用的刀具换油周期定为300小时,这样可使换油和密封环及轴承的检查同时进行;对异常损坏的刀具,如漏油、偏磨等情况每次拆卸修理时都要更换新油。
在加入润滑油的同时,还应加入3~5ml异味剂,这对刀具在掘进中漏油有灵敏的警示作用。
5、轴承的更换与维修及扭矩的恢复①检查发现油中有铁末和沙粒时,要仔细检查轴承,一般都要更换轴承;②滚动体、外圈滚道、内圈滚道上有大于2×2mm面积剥落时,应更换轴承;③轴承滚柱的大端崩块,应更换轴承;④轴承内外圈断裂或有裂痕时,应更换轴承;⑤轴承外圈滚道产生波状变形(用手触摸检查外圈滚道时,有明显的波状感)、检测隔离环厚度以调整轴承扭矩时百分表跳动大于0.15mm,这两种情况都应更换轴承;⑥刀具轴承预紧的转动扭矩修复轴承的预紧扭矩正、边刀为40—80N.m,中心为60—120 N.m。
控制扭矩用隔离环的厚度,根据百分表测得的数据,经查表可得,磨制时,应控制平行度,偏差不应超过0.015mm。
经过使用运转后的刀具,扭矩一般要降低。
拆卸检查刀具时,要检测隔离环厚度,一般是减薄隔离环,以增加扭矩,恢复刀具轴承的预紧度。
6、刀体的维修①刀具严重偏磨,刀体外表面 6、4严重损坏时应报废;②边刀刀体的刀圈轴向定位挡肩部位1被磨损,在高度小于3mm时,应报废;③表面5变形,若变形不大,可用手砂轮打磨或车床加工修复,变形大者则应报废;④2表面为端面密封橡胶圈安装座,由于轴承保持架损坏后,刮伤其表面,也有的产生与表面5相连的变形,一般可用手砂轮打磨修复;⑤表面3为与轴承外圈配合面,拉毛时,经打磨后可使用。
若外圈压入时失去紧度,应进行缩径(可暂时用冲子打若干麻点以增加预紧,最好进行刷镀)后再使用;⑥B部磨损后,不便仰装密封环,应改变安装顺序使该侧向上;⑦表面4是与刀圈内孔的静配合面。
热装新刀圈前,只能对该表面拉伤凸出点进行打磨;⑧中心刀刀体两侧环状密封面(宽度为3—4mm)有锈蚀及伤痕时,要进行研磨修复。
研磨不能修复的要送工厂修理。
7、正、边刀刀盖的损坏与维修①A 部的局部磨损,一般的情况下可继续使用。
拆检刀具时,可将边刀刀盖换装到正刀上,或将外侧刀盖换至内侧装配,磨损严重者,送工厂维修;②1表面外圆周磨损,不严重者,可继续使用,拆检刀具时也可左右交换安装;③1表面的C 部的局部变形,和刀体的表面5的变形同时产生,一般经修理校正后可使用;④2表面由于轴承保持架损坏后被拉伤,可修磨后使用;⑤刀轴受力时,产生弯曲变形,将刀盖孔3表面的D 部咬伤,修磨后可以使用;⑥B 部和刀体B 损坏的修理方式相同,应改变安装顺序以便安装密封环;⑦4表面为M24螺孔,一般的损伤是螺纹有变形,可用丝攻修理。
螺纹损坏两牙以上时,不能使用;螺纹孔内有断螺栓不能取出时,无法使用。
8、中心刀端盖及轴的损坏与修理掘进中,在轴承受力的情况下,端盖左右摆动,使端盖和轴在A.B 两部位磨损。
轻者在不影响“O ”型橡胶圈圈密封性能的前提下,可以使用。
9、正、边刀刀轴的损坏与维修刀轴与端盖内孔接触部位被挤伤,修磨后使用,装配时,按原部位旋转90度装配。
刀轴两端M16螺孔内有断螺栓不能取出者,不能使用。
10、刀具的报废刀具的报废以刀体的报废为依据。
刀具上除刀体以外的其它零件损坏失效后都可更换,但刀体报废后,该编号的刀具作报废处理。
用新刀体组装的一把新刀,要给该刀一个新的编号,使用时建立记录该工作履历的使用卡片。
对购进的新刀,有编号者,应检查刀号是否重复,无编号者,应进行编号。
四、刀具检查与维修的工艺过程刀具检查与维修的工艺过程见附图。
五、刀具拆卸检查与维修中的注意事项①对解体拆卸的刀具零件应进行仔细清洗,留用零件按刀号成组保存;端面浮封环成对保存;拆卸轴承时,应检查标记,按标记成对保存;新轴承经检测隔离环厚度后,应作配对标记,AB成对存放;②对留用待装零件,应仔细去除毛刺后方可组装。
刀轴与刀盖孔进行试装后再进入组装;③一套轴承中报废一件(内圈或外圈)则全套报废。
一把刀具中,两套轴承应同时更换;④拆卸刀具应更换所有橡胶圈;⑤加入润滑油、异味剂不可超量;⑥对扭矩大的刀具(新刀、旧刀),一定要拆卸检查原因,禁止用刀具跑合来降低扭矩;⑦安装和拆卸时一般不使用锤击;⑧正、边刀组装后,对刀盖上的M16、M24螺孔用丝攻(二攻)进行清理,攻入深度要达到使用要求;⑨刀具检查维修过程的重点环节是维修前的检查与维修程序的制定、刀具解体时的检查、轴承的检查及更换、扭矩的调整、滑动密封的检查与更换,因而在检修过程中必须予以高度重视。
实践证明,完善后的刀具检修工艺,完全能够满足TBM施工要求,只要严格按照此工艺执行,即可确保掘进过程中不会出现掘进操作错误以外的非正常损坏,对减少刀具更换时间、争取掘进时间、提高TBM利用率、降低隧道施工成本等方面作出了巨大贡献。