橡胶工业助剂配方袖珍手册
橡胶工业手册第三册配方与基本工艺

上篇配方设计第一章配方设计第一节概述天然橡胶和合成橡胶的纯胶性能都比较差,无法满足制品的使用要求,加入多种配合剂后才能获得改善。
橡胶、配合剂及其配比的方案,即为橡胶配方。
根据制品各种性能要求,制定橡胶配方,通过试验、调整和验证,最后确定胶料的各种组分及其配比的过程,即称谓橡胶配方设计。
橡胶性能配方,主要研究配方组分与硫化胶及混炼胶性能之间的关系,探求组分对橡胶各种性能的影响和贡献。
橡胶制品配方则主要研究硫化橡胶物理机械性能和化学性能与橡胶只怕你实际使用性能之间的关系,探求硫化橡胶性能对制品使用性能的影响和贡献。
这两类配方所研究的对象和内容虽然不同,但又互相联系,不可分割,由此形成橡胶配方设计体系。
一、配方设计的变迁和发展一、配方组成的多样化现代配合组分可分为五个体系:1.主体材料:生胶、再生胶2.硫化体系:硫化机、促进剂、活性剂、防焦剂。
3.操作体系:增塑剂(化学增塑剂、物理增塑剂)。
4.性能体系:补强剂、防老剂、着色剂、发泡剂、芳香剂、增硬剂。
5.成本体系:填充剂、增容剂。
一个具有实际意义的配方通常含有不同体系二、配合剂品种的专用化适合氯丁橡胶的硫脲类促进剂不适合于其他类型的橡胶。
适合天然橡胶的植物系物理增塑剂并不适合合成橡胶。
三、配合效果的提高四、配方设计过程的简化科学的数理方法用于配方设计:等高线法、实验设计法、三角坐标法及电子计算机法等。
用计算机进行配方试验的数据处理、优选配方,可以通过少量试验获得大量有用的信息,使配方设计发生了根本性变化。
二、配方设计的基本要求和配方分类为获取最佳的共和平衡性能,三个目的1.改善橡胶使用性能。
2.改进橡胶的工艺性能。
配以操作助剂。
3.不影响或少影响性能的前提下,配入填充材料,降低成本。
橡胶配方按其作用分为:试验(或检验)配方、性能配方和制品配方。
试验(或检验)配方。
通用橡胶基础配方:三、橡胶配合中出现的反常现象1.实验室得到的配方,在生产中不一定有满意结果。
橡胶助剂及经典配方(重要)
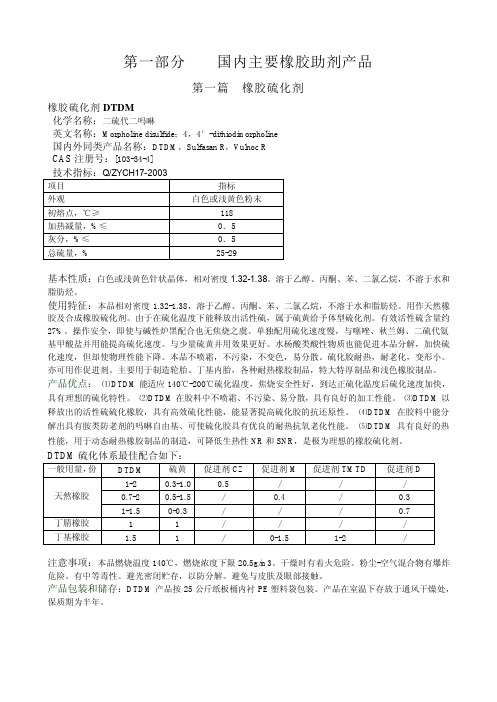
第一篇 橡胶硫化剂
橡胶硫化剂 DTDM 化学名称:二硫代二吗啉
英文名称:Morpholine disulfide;4,4′-dithiodimorpholine 国内外同类产品名称:DTDM,Sulfasan R,Vulnoc R CAS 注册号:[103-34-4] 技术指标:Q/ZYCH17-2003
≤0.30
挥发份(105℃) %
≤0.20
基本性质:在 常 温 下 性 能 十 分 稳 定,可 长 期 在 室 温 下 贮 存 。TAIC 的 功 能 团 为 三 个 烯 丙 基 ,
具有脂肪族烯 烃的一般通性 ,如多种加成反应 ,均 聚 和 共 聚 反 应、Prins 反 应 等。 在过 氧 化 物 引 发 下 ,TAIC 较 其 他 烯 丙 基 更 易 发 生 聚 合 反 应 ,在 空 气 中 加 热 到 140 ℃以 上 即 发 生 自 聚 反 应 , 成 为 透 明 、 质 硬 的 均 聚 物 。 熔点 24~26°C,室温(25°C)为无色液体或六方片状 结晶体,比重 1.155(30°C),沸点 144°C/3mmHg,297°C/760mmHg,闪点 355°C ,粘度 83 ±3 厘泊(30°C) 。溶 解 度 不溶于水,微溶于烷烃,全溶于芳烃,乙醇、丙酮、卤化烃和环戌烯烃等。
0.05
0.05
0.50
0.50
0.10
0.10
99.8
99.8
IS-HS-8010 黄色不飞扬粉
90.0±1.0 90.0 75.0
10.0±1.0 0.05 0.50 0.10 99.8
IS-HS-7020 黄色不飞扬粉
80.0±1.0 90.0 75.0
特种橡胶助剂系列产品说明书

氟胶骨架粘合剂 3290-1/512/5150 未硫化氟橡胶与各种金属、塑料与织物纤维,耐水、盐雾、油脂、溶剂、化学品以及其他苛刻环境,耐高温,防锈性能优良 1kg/8kg/25kg
橡胶抗撕裂剂 抗撕裂压缩变形粘结牢、耐油耐磨耐高低温、提高强度硬度特殊补强、橡胶耐热性提高及抗疲劳性好等特点 20kg
外脱模剂PE-40 肯天公司出品,氟胶专用,具有易脱模、提高产品合格率及表面光洁度,保护模具不受污染等特点 25kg
氟橡胶粘合促进剂L-08N 蜡状固体,熔点低易熔化分散均匀,用于增强氟橡胶和金属的粘接性,改善氟橡胶与非氟橡胶组合物形成的非氟橡胶层的粘接性,并且该增粘剂与双酚AF搭配使用时可部分或完全代替硫化促进剂BPP,增强氟橡胶抗撕裂性 25kg
高性能AF、BPP硫化剂母炼胶 采用杜邦公司最新技术精致而成含有硫化剂及国外高性能氟胶加工助剂的预母炼胶料,从而有效避免了AF、BPP分散不好及粉料飞扬问题,具有撕裂性能好、强度高、低压变、易分散,混炼简单、减少炼胶强度,是高端制品氟胶制品的首选 5kg
新型氟橡胶硫化剂-氟联-5# 氟橡胶硫化剂品种。熔点低于100℃、在炼胶过程中分散性好、与各种牌号的氟橡胶以及填料的相溶性非常好。制品性能好、废品率低, 避免了使用双酚、BPP粉剂时不熔而使炼出的胶质量不均匀的缺陷 500g
EPDM促进剂 EG3M-75GE在胶料中之分散性佳,能提高EPDM的硫化速率,在橡胶制品中可以避免吐霜的現象,建议用量为2~5PHR,可依配方需求自行调整(可不添加其他促进剂只需EG3M-75GE与硫磺并用即可 25kg
硅烷偶联剂SI69/A-172 本品是一种双功能分子,它既可和无机填料反应,也可和有机高分子反应。可用作多种矿物填充聚合物的粘合促进剂、增塑剂以改善填料的物理性能和和加工性能,可用于天然橡胶三元乙丙胶、丁腈胶、氢化丁腈胶异戊二烯橡胶、丁苯胶、丁二烯橡胶、丁酯胶、氯丁胶、丁基橡胶、以及这些橡胶的充油胶 25kg
(完整版)常用的橡胶促进剂大全

常用的橡胶促进剂大全根据化学结构的不同,促进剂分可以为噻唑类、秋兰姆类、次磺酰胺类、胍类、二硫代氨基甲酸盐类、醛胺类、黄原酸盐类和硫脲类等八大类。
一、噻唑类这是有机促进剂中较早的品种。
属于酸性促进剂。
其特点是具有较高的硫化活性,能赋予硫化胶良好的耐老化性能和耐疲劳性能。
所以在橡胶工业中应用比较广泛,耗用量较大。
主要品种有如下两种。
(1)2硫醇基苯并噻唑商品名称为促进剂M。
本品为淡黄色粉末,味极苦,无毒,贮藏稳定。
为通用型促进剂,对天然橡胶及二烯类通用合成橡胶具有快速促进作用,硫化平坦性较好,硫化临界温度为125℃,混炼时有脑炎烧的可能。
在橡胶中容易分散,不污染,但不适于食品用橡胶制品。
用作第一促进剂的用量为1~2份,作第二促进剂的用量为0.2~0.5份。
还可用于天然橡胶的塑解剂。
(2)二硫化二苯并噻唑商品名称为促进剂DM。
本品为淡黄色粉末,味苦,无毒,贮藏时稳定。
其特性和用途与M相似,但硫化临界温度为130℃。
140℃以上活性增大,有较好的后效性,硫化操作安全。
常与其它促进剂并用以提高其活性。
二、秋兰姆类这类促进剂呈酸性。
属于超速促进剂。
包括一硫化秋兰姆、二硫化秋兰和多硫化秋兰。
二硫化秋兰姆可用于无硫黄硫化有硫化剂。
作为促进剂一般用作第二促进剂,与噻唑类和次磺酰胺类促进剂并用以提高硫化速度。
与次磺酰胺类促进剂并用时,能延迟胶料开始反应的时间,硫化开始以后反应又能进行得特别快,硫化胶的硫化程度也比较高。
这种产用体系在低硫硫化中特别重要。
采用秋兰姆促进剂的硫化胶的物理机械性能和耐老化性能受促进剂和硫黄用量比例的影响。
一般来讲,硫黄用量正常,硫化胶的定伸强度较高,其它物理机械性能也比较好;当硫黄用量较低,促进用量较大时,则硫化胶的耐热老化性能可以得到改善。
秋兰姆类促进剂最常用的品种是二硫化四甲基秋兰姆,商品名称为促进剂TMTD,简称促进剂TT。
它既可作促进剂使用,也可作硫化剂使用。
用作促进剂时用量一般为0.2~0.3份。
【收藏】橡胶常用助剂说明!
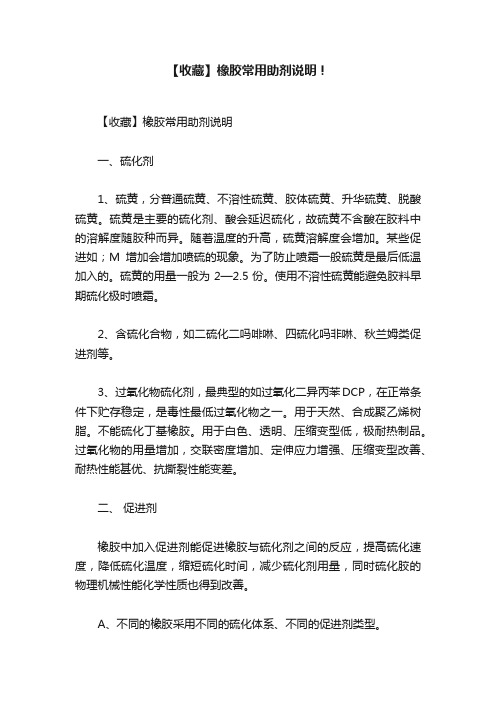
【收藏】橡胶常用助剂说明!【收藏】橡胶常用助剂说明一、硫化剂1、硫黄,分普通硫黄、不溶性硫黄、胶体硫黄、升华硫黄、脱酸硫黄。
硫黄是主要的硫化剂、酸会延迟硫化,故硫黄不含酸在胶料中的溶解度随胶种而异。
随着温度的升高,硫黄溶解度会增加。
某些促进如;M增加会增加喷硫的现象。
为了防止喷霜一般硫黄是最后低温加入的。
硫黄的用量一般为2—2.5份。
使用不溶性硫黄能避免胶料早期硫化极时喷霜。
2、含硫化合物,如二硫化二吗啡啉、四硫化吗非啉、秋兰姆类促进剂等。
3、过氧化物硫化剂,最典型的如过氧化二异丙苯DCP,在正常条件下贮存稳定,是毒性最低过氧化物之一。
用于天然、合成聚乙烯树脂。
不能硫化丁基橡胶。
用于白色、透明、压缩变型低,极耐热制品。
过氧化物的用量增加,交联密度增加、定伸应力增强、压缩变型改善、耐热性能甚优、抗撕裂性能变差。
二、促进剂橡胶中加入促进剂能促进橡胶与硫化剂之间的反应,提高硫化速度,降低硫化温度,缩短硫化时间,减少硫化剂用量,同时硫化胶的物理机械性能化学性质也得到改善。
A、不同的橡胶采用不同的硫化体系、不同的促进剂类型。
B、促进剂对焦烧性能起着决定性的影响,正确的促进剂选择有助于胶料的混炼、压延、压出及操作安全性。
一般模压硫化需有一定的焦烧时间,而无模硫则不需过长的焦烧时间。
C、促进剂的抗焦烧性能与其临界温度有关,超过临界温度促进剂迅速活化,多种促进剂的配合使用时,有些促进剂会受到抑制,有些促进剂在临界温度下也会出现较大的活性。
D、促进剂的搭配应使胶料具有宽广的硫化平坦性。
橡胶是热不良导体,胶料表面内部受热情况并不一至,宽广的硫化平坦性是避免过硫,并使制品各部份硫化均匀的保证。
E、促进剂的合理搭配还能改善硫化胶的老化性能,有一定的塑解作用,可改善胶料的加工性能。
缺点,促进剂分散性差、污染性、目前使用的促进剂一般是没有毒的。
促进剂的介绍1、二硫代氨基甲酸盐类,最常用的如PZ适用于要求压缩变型低的丁基橡胶、耐老化性能优良的丁睛橡胶、三元乙丙橡胶。
橡胶手册001

表 5 同样表明在过去的几十年间加工助剂的数量得以迅速地增长。
从本世纪五十年代开始,加工助
加工助剂的发展演化
剂才得以显著发展。正是在这一 时 期 , 1954 年 SCHILL & SEILACHER 注 册 了 STRUKTOL® 作 为 Schill & Seilacher 产品的商标名注册, 至此这一商标几乎成为了加工 助剂的代名词。
引言
传统上,使用加工助剂以改善加工性能的方法并不被人们普遍接受。然而今天,现代化的加 工助剂已被看作是提高橡胶产品生产效率的推动力。
除传统的、化学结构相当明确的抗氧化剂和促进剂之外,早期用于改善难以加工的橡胶化合 物的混合助剂往往缺乏通用性,因此也得不到太多的认可。使用者只有在万不得已时才会使 用这类助剂,配方师也很难了解其作用机理。 这种状况与混有硫化促进剂的交联反应或抗氧化剂的反应有很大的不同。
4
8
1995 13
塑解剂
14
21
30
(物理、化学)
润滑剂及其他助剂
82
167
来源:蓝皮书(橡胶世界)市场上产品的数量 表4
10
286 加工助剂的历史
This is trial version
这些增长反映了橡胶产品制造过程中,加工助剂对于现代加工工艺的迅速发展和不断提高的 质量要求起了重要作用。
为“油包水”型的乳液增塑剂。 表 5
在此类产品中包括非常著名的 STRUKTOL WB 212(一种基于脂肪酸酯的乳聚增塑剂)。
如今 STRUKTOL 加工助剂的产品列表上包括了大量的品种(表 5),而且仍然在不断地增 长。
加工助剂的历史
橡胶工业手册02配合剂修订版
REBAR的各类用法2.2.3 概念增强筋用途:在膜、壳和面单元顶用于概念单项增强层。
通过在主实体单元中插入面或膜单元来添加增强层在standard中能够采纳beam单元来模拟离散的增强筋不能用于热传导分析和质点发散分析,可是可用于热力耦合分析中。
在热力耦合分析中,增强筋单元没有热传导和比热特性。
能够拥有和其主单元不一样的特性。
概念REBAR LAYER 的4种方式:1), ELSET=memb_set_name 概念膜单元2), ELSET=shell_set_name 概念壳单元3), ELSET=surf_set_name 概念面单元rebar layer name 概念增强层的名字4), HOST ELSET=solid_set_name 在实体单元中直接概念rebar memb_set_name or surf_set_nameREBAR 的几何特性概念1)其定位老是参照局部坐标系2)其几何尺寸能够是常数,也能够是关于圆柱坐标系的径向位置函数,也能够采纳轮胎充气公式来概念。
可是等效的rebar厚度=面积A/间距S。
3)关于壳单元,必需概念rebar在壳厚度方向上与壳中面的距离。
若是壳的厚度通过节点厚度来概念,该距离将按系数(结点厚度/壳截面厚度)缩放;若是壳厚通过单元属性概念,该距离将按系数(单元属性概念厚度/壳截面厚度)缩放。
等间距REBAR的概念, GEOMETRY=CONSTANT间距关于圆柱坐标系的径向位置函数的rebar的概念:角度间距值也能用于非径向rebar和非零定位角的rebar。
这些rebar中定位角可不能发生改变。
角度间距值只用于计算rebar之间的间距(=S×rebar 从旋转中心开始的径向半径)。
若是这种rebar用于三维实体,必需概念局部坐标系。
, GEOMETRY=ANGULAR采纳轮胎充气公式概念rebar要紧考虑轮胎充气前的rebar角度不同于充气后轮胎上rebar的角度,而充气前的角度能够精准取得。
橡胶助剂实用手册
橡胶助剂实用手册摘要:一、橡胶助剂实用手册简介1.橡胶助剂的定义与作用2.橡胶助剂的分类二、橡胶助剂的主要品种1.硫化剂2.硫化促进剂3.防老剂4.补强剂5.填充剂6.软化剂7.其他助剂三、橡胶助剂的应用领域1.轮胎制造2.橡胶制品生产3.胶鞋制造4.橡胶电缆5.其他橡胶制品四、橡胶助剂的选择与使用1.依据橡胶制品性能需求选择2.助剂的配比与混合3.助剂加入时机与方法4.助剂对橡胶制品性能的影响五、橡胶助剂的发展趋势1.环保型助剂的研究与应用2.高性能助剂的开发3.橡胶助剂行业的挑战与机遇正文:橡胶助剂实用手册是一本关于橡胶助剂的综合性参考书籍,旨在为橡胶制品生产企业和相关从业人员提供橡胶助剂方面的实用技术信息。
本文将对橡胶助剂实用手册进行简要介绍,包括橡胶助剂的定义与作用、分类,以及主要品种、应用领域、选择与使用等方面的内容。
橡胶助剂是指在橡胶制品生产过程中,为改善橡胶的加工性能、物理机械性能和化学性能而加入的一类化学物质。
橡胶助剂对橡胶制品的性能起着至关重要的作用,可以提高制品的使用寿命、安全性能和美观度。
橡胶助剂按照作用原理和性能可分为硫化剂、硫化促进剂、防老剂、补强剂、填充剂、软化剂等。
其中,硫化剂用于改善橡胶的硫化程度和物理性能;硫化促进剂可以提高硫化速率,缩短硫化时间;防老剂能够延缓橡胶制品的老化过程,提高其使用寿命;补强剂可以提高橡胶的强度和硬度;填充剂主要用于改善橡胶的耐磨性、耐老化性和降低成本;软化剂则用于改善橡胶的柔软性和可塑性。
橡胶助剂广泛应用于轮胎制造、橡胶制品生产、胶鞋制造、橡胶电缆等领域。
在选择和使用橡胶助剂时,需要根据橡胶制品的性能需求进行合理配比,选择合适的加入时机和方法。
此外,还要注意助剂对橡胶制品性能的影响,以确保制品的质量和性能达到预期目标。
随着环保意识的日益增强,橡胶助剂行业正面临着环保型助剂的研究与应用、高性能助剂的开发等挑战与机遇。
橡胶加工助剂
橡胶加工助剂轮胎工一999年第l9卷⑤2孑3z橡胶加工助剂廖聪隆(美国耀星国际暇份有限公司北京办处110f150~5c,-;(StructotC~mpanyofAmerica)/Lrsen捕妻介绐丁橡胶加工助荆的发展史.一般分类及化学性质.对不同种类的助剂进行性能分析,对比.同时列举r橡胶加工助剂在腔料中的作用及对腔抖物理性能的影响在混炼腔中适当加八橡胶打口j|励剂.可提高腔料的操作性能.对腔料的物理性能无不良影响关键词塾壁~助暴j加工助剂是一种材料,在橡胶胶料中少量添加加工助剂可提高胶料的操作性能,对胶料的物理性能无不良影响.很难讲清楚谁首次有意识地采用加工助剂改善NR或SR的加工性能.1865年.AIexanderParks获得包括脂肪链甘油,油,树胶和焦油在内的多种材料用于润滑硝化纤维素的专利;1870年,John与IsaiahHyatt获得樟脑用于硝化纤维素的专利;1858年,HallHL在马萨诺塞州获得属于Beverly橡胶公司的美国220242专利,应用沥青,煤焦油,树脂和硬沥青软化硬的交联橡胶,使之成为可甩于制成有用制品的软材料.此后,橡胶用加工助剂不断发展,品种和用量日益增加.1分类与品种表I列出对加工助荆的要求,包括混炼,压遥,挤出,成型和模压等方面.一些加工助剂对应的分类与相应的品种如下:抗静电剂抗结团剂成型用助荷分散剂均匀剂腚一级酰胺交联植物油脂脐酸金属皂蜡脂肪醇烃树脂脂肪酸衍生物作者简介杨卫国男.32工程师.1988年毕业F+E京化工学院(1{It化E大学)高分子系主要从夺橡胶助】的直用推rT作润特jfI1塑炼助剂补强荆增粘jfI1酚醛树脂盘属皂脂肪醢胺(盐】脂肪醢酯相对分子质量低的烃芳基对磺酰胺五氯硫酚不饱和脂肪酸锌皂磺酸聚台物助剂酚醛l对脂酚醛树脂烃娄树脂表l对加工助剂的要求注:Y表l”是所璺求的”l姐程两填料甘戢性是改善质培所要求的最近一期蓝皮书(BlueBook:materials, compoundingingredients,machineryandsevices fortherubberindustrv)将加工助剂分为均匀剂,塑耩剂,操作助剂,增牯荆,增塑剂及软化剂.近年来,加工助剂的品睥数量发展很快(见表2).配方工程师在设计配方时应认真选择第12期杨卫国等.橡胶加1==助剂表21980~1997年加工助剂的品牌数量个弹性体体系,补强剂,防老剂,促进剂和硫化剂,以充分展现胶料的特性.与此同时,为了提高胶料的加工质量.降低成本,也应注意加工助剂的选择.现就增塑削/软化剂,均匀削和塑解剂等橡胶加工助剂作-介绍.2增塑剂和软化剂增塑剂和软化剂是相对不挥发的助剂,加入弹性体或树脂后,可改善成型或加工性能,扩展或转换内在性能,特别能改善低温环境下柔顺性和嘭胀性.2.1烃类油烃类油为石油产品,是橡胶配合中用量最大的品种.与其它品种的比例为4:1.该油类普遍用于提高胶料流动性和加工性能,同时降低最终产品的成本.石油产品系的烃类油包括烷烃,环烷烃和芳烃油,其不同用途及相应比例如表3所示.表3油类应用比例‰2.2煤焦油和松焦油(1)煤焦油.煤焦油是炼焦的副产物.是许多组分的复杂混合物.为无色,浅白色到浅黄色液体,兼有相容性和增塑性.煤焦油首先被橡咬工程师用来软化橡胶,但很快被石油系油替代.这里还包括低相对分子质量的苯并呋喃一茚混合物.(2)松焦油.配方中添加松焦油可得到粘而软的胶料,有提高胶料流动性和增加润湿的作用.但近年松焦油的产量已逐渐减少,市售天然松焦油很少见到.2.3酯酯且有使多种聚合物软化的特点.主要用于极性橡胶(如CR和NBR).提高混炼胶低温和高温性能或获得特种耐油性,耐有机溶剂性能.聚酯还具有特高粘度并且相对分子质量高达8000酯.特别是多元醇酯.比脂肪酸或金属皂更易与橡胶相混容.用精细的无水硅胶作载体的自由滑动粉末酯易于操作,且易溶于混炼胶中.酯除用于改善胶料的工艺性能外.常用来提高炭黑及非炭黑填料与橡胶的相容性.图1用点划线表明聚合物分子问力.静态的聚合物分子问力强并保持材料形状.在加工过程中,为使材料流动或成型.剪切力必须超过分子问力.填料和补强剂加入橡胶中会增大胶料的流动阻力.加工助剂作为流动助剂可使胶料较易流动.通常,剪切速率越高,工艺助剂的性能表现越好.天然的脂肪,油(除了矿物油)和多数蜡为酯的混合物.当制作高模量,高硬度的NBR注射件时,很难使胶料充满模腔.评估过许多选择方案,包括低门尼粘度橡胶和采用添加加工助剂以及增大操作油的用量方法,但这均会降低胶料的硬度和模量许多混炼胶制备常采用低门尼粘度橡胶和添加加工助剂的方法,高门尼粘度的NBR流变性能删试结果见图2低门尼粘度橡圈l聚台物分子问力剪切应力/Pa圈2高门尼粘度韵NBR混炼胶的瀛变性能第12期扬卫国等橡胶加工助荆7312.7.1聚乙烯蜡聚乙烯蜡是由乙烯聚合而成的,除相对分子质量低外,化学陛质与聚乙烯树脂相似.相对分子质量,支化度和支化类型是决定聚乙烯蜡性质的重要因素.相对分子质量越高,蜡的粘性和粘稠性越大.聚乙烯蜡与其它碳氢化合物蜡性能对比如表4所示.由于聚乙烯聚合物多方面的适应性,相对分子质量低的带有一系列乙烯基共聚单体的共聚物亦可制造.此外,聚己烯或共聚物蜡聚合后(经过反应)可氧化,接枝聚合或以各种其它化学反应改性.系列聚乙烯蜡的性能对比如表5所示.表4聚乙烯蜡与其它碳氢化舍物蜡的性能对比表5系列聚乙烯蜡的性能对比项目均化蜡霎纂翳嚣密度/(Mg?m.)088~093085~l00+93~096092~093硬度/dram05~98<05~9020~5040~80落球温度/℃)~12088~14076~10575~102官彘团无棱基(酸5%~18%6%~26%己值5~41)丙烯酸基酸乙烯酯基2.7.2石油蜡90%的商用蜡是从石油的脱蜡润滑油浆液中回收的.石油蜡通常分固体石蜡,微晶蜡和石蜡油3种主要类型.所有类型产品广泛用作加工助剂.石蜡是纯的直链混合物,熔点为44--66℃.固体石蜡系从石油中萃取沉淀析出的.固体石蜡的纯化方法包括化学处理,吸附剂脱色和精馏分的蜡蒸馏分离,再结晶.雪白,比石油固体蜡硬的合成蜡具有独特的特性和高纯度,适合替代植物蜡作为石油蜡和许多如聚乙烯等塑料的改良品.微晶蜡与固体石蜡的区别在于,微晶蜡含有更细粉末和少量特别的晶体,并具有更高的熔解温度和粘度.与固体石蜡相比,微晶蜡有更广泛的适应性,包括可用于原油资源,精制方法和精制度.许多蜡是柔软的,如同蜂蜡;有些是硬而脆的;有些是处理时易碎的.微晶蜡的熔点比固体石蜡更高,其商用品级的熔点温度为63~93℃3均匀剂均匀剂是相对分子质量较低的聚合树脂的混合物,有助于混炼胶中的极宽的不相容成分互混,并混炼成均匀,均一加工的胶团.每种类型的弹性体有一种或多种能降低粘度和软化弹性体的增塑剂.与弹性体的溶解度参数和极性相近的增塑剂增塑效果最有效.其溶解度参数和牯度相差越远,生产均匀混台物越困难.与易溶于不同橡胶的增塑剂并用,可有效提高混炼胶的均匀性.用于均化的增塑剂混合物有易迁移和喷霜的酞陷,为解决迁移问题井同时获得均化功能,均匀剂常含有增塑剂的相对分子质量高的同系物(如树脂).均匀树脂混合物含有混炼胶中弹性体的易溶于包括脂肪烃/环烷烃/芳香烃的链段,有湿润性且可减少混炼能耗,使不相容的组分互混4塑解剂自19世纪NR可用开炼机塑炼后发现,氧在开炼机有效塑炼时是必不可少的.塑解剂通常是自由基的接受体或氧化触媒,可在开炼或混炼工艺中有效地消除自由基的形成.此过程可避免再次交联而确保塑解剂对聚台物的作用.硫酚,芳烃硫化物和铁,钴,铜和锰的螯台物对许多弹性体具有催化热氧老化的作用.磺化酯对NR也有极强的塑解作用.当今市场上有效的塑解剂如下:Ak~hemPeptizer66活性荤甲酰胺邻苯二甲酸二硫化物承载在惰性载体上Pepton44活性苯甲酰胺一邻笨二甲酸二硫化物承载在惰性薮体上Pepton80I音性苯甲酰胺邻苹二甲酸::硫化物承载在惰轮胎工业1999年第i9卷性载悻上Renacit11活性二荤甲酰胺.邻苯二甲酸二硫化物承载在惰性载体上Strukt~A95活性五氰硫酚承载在惰性载体上Aktipl~t8活性脂肪酸,脂肪酸皂和脂肪醇的混合物Aktipl~tF活性高相对分子质量,主要古不饱和脂肪馥锌皂的混合物Aktiph~tM活性高相对分子质量.主要含不饱和脂肪酸锌皂的混合物Reaadt8活性不饱和脂肪酸混合物StruktolAS0活性高相对分子质量脂肪酸混合物StruktolA82活性脂肪酸皂混合物StruktolA91活性脂肪酸锌皂混合物St~uktolA86有机金属幌合物加分散剂St~uktolA88有机金属混合物加分散剂AkrochemPepertizer9344芳香胺,烃娄混台物AkrochemPepertizer9349改性烷基烃硫化物的混合物AkrochemProaidPep相对分子质量高的脂肪酸锌皂Reogen石油与磺化石油混合物Bondosen石油与磺化石油混合物Peptizer701ON石油与磺化石油混合物V~nplastPL石油与磺化石油谩台物VanplastR石油与磺化石油混合物5影响选用的因素(1)有限相容性.产品喷霜到混炼胶表面并作为在胶料和金属设备之间的外润滑剂产生润滑.(2)中到低的相容性.低于一定浓度时,材料作为内润滑剂在流动的混炼胶聚集态之间引起润滑.若溶解度超过一定值,材料则作为外润滑剂使用.(3)高相容性.无喷霜发生并且材料因如下某种机理.用作胶体粘度改善剂:分子间作用——减少聚合物分子间缠结:塑解作用.分子内作用——膨胀聚合物分子并软化:增塑作用.(4)多重作用.粘着/润滑/表面活性.此外,在橡胶制品及轮眙加工业中广泛存在分散,润滑,均匀和均一及脱模等问题,这就要求配方工程师在设计配方时必须添加加工助剂,更新传统的设计观念.因此,不仅要考虑胶料的物理性能,更要考虑加工工艺性能和综合经济性能.炼胶,成型及硫化用的隔离/脱模等问题的解决方法是.根据工艺情况适时补充使用诸如DARMEX轮胎内外隔离剂和Struktol P10脱模剂等助剂.6结语目前国内已广泛应用橡胶加工助剂,特别是近几年.随着橡胶加工业引进技术的增多与推广,物理增塑剂,均匀剂以及白炭黑用于环保轮胎及橡胶制品加工用的分散剂(如Struktol EF44等)显示出了高的性能价格比.橡胶加工助剂是一种可提高混炼胶加工性能且对其物理性能无不良影响的理想添加材料.第十届全国轮胎技术研讨会论文米其林重占大轮胎公司排名鳌头英国《欧洲橡胶杂志)1999年181卷9期3l页报道:在1999年度轮胎公司排名榜上,米其林集团公司又升到普利司通公司前面.在这场肉搏战中,汇率变化再次起了重要的作用.两家公司的轮眙经营基本上是并驾齐驱,在过去的两年中每年都在更换领跑地位.尽管加上Sara轮眙公司和日本巨人(Nip—pon’Giant)公司的销售额,固特异仍然保持排名第3.而且到2000年.在排名榜上它的名次可能还不会变化.但是到2001年4月,固特异可能持有住友轮胎公司在北美和欧洲的大部分股份,加上这部分销售额,固特异将排到其它两家公司前面,以占全球20%的轮胎销售额跃居第1位.和1998年一样,由于美元坚挺,加上亚洲国家货币疲软,使全球轮胎总销售额下降了3%左右.由1997年的694亿美元降至673.83 亿美元.米其林和普利司通各占全球轮胎总销售额的l9%,固特异占l7%.这三大公司的销售额占世界轮胎工业总销售额的55%,而十大公司的销售额占世界轮胎工业总销售额的8O%.(涂学忠摘译)。
橡胶工业助剂配方袖珍手册
橡胶工业助剂配方袖珍手册内容简介1.促进剂DM:在NR及SR中硫化速度中等,硫化特性平坦。
可适用于大多数通用橡胶。
在“白色”胶料中无污染不退色。
在NR传统硫化系统中,硫磺用量约2.5份。
在NR 半有效硫化系统中,硫磺用量降至1.0份左右,可获得良好的抗老化和抗返原性能。
2.促进剂DZ(作单用促进剂)尤其适用于直接与黄铜表面或有黄铜镀层的钢丝配方。
与其它次磺酰胺促进剂相比,焦烧安全性能最好。
在NR配方中用量为0.7-2.0份,对应的硫磺用量位2.5-1.5份,在钢丝帘布胶料配方中硫磺用量普遍在4份左右。
高湿度/高温度会引起产品分解从而导致焦烧时间缩短。
本产品不能存放在不溶性硫磺附近,从本产品释放的胺类挥发物会导致不溶性硫磺返原为普通硫磺。
3.促进剂NOBS:是一种通用型主促进剂,在所有(中等)快速硫化次磺酰胺促进剂中,其加工安全性能最好,硫化速率中等,可以较好地提高硫化胶模量。
在NR中的用量为0.5-1.5份,随着NOBS的用量增大,硫磺用量相应减少。
本产品不能存放在不溶性硫磺附近,从本产品释放的胺类挥发物会导致不溶性硫磺返原为普通硫磺。
4.促进剂TBBS:是一种伯胺基通用型主促进剂,硫化速度快,焦烧安全性好,可以极好地提高硫化胶的模量。
在NR…SBR…BR及其并用胶中,TBBS的用量降低10%时,能获得CZ及NOBS相同的模量。
TBBS与CTP并用能够代替NOBS ,既可以避免人们所关注的亚硝胺问题,又可以满足相同的胶烧安全性能和更快的硫化速率的需要。
5.促进剂DPTT:在大多数硫磺硫化弹性体中用作主或助促进剂或硫磺给予体。
无污染性,特别适用于浅色胶料。
其有效硫的含量位28%,因而更适用于半有效及有效硫化系统。
在EPDM中,DPTT在“三个8”组成的系统中,(DPTT 0.8份.TDEC 0.8份TMTM0.8份.MBT 1.5 份.硫磺.2.0份)作助促进剂用。
在其它助促进剂系统中DPTT的用量为0.5—1.5之间。
- 1、下载文档前请自行甄别文档内容的完整性,平台不提供额外的编辑、内容补充、找答案等附加服务。
- 2、"仅部分预览"的文档,不可在线预览部分如存在完整性等问题,可反馈申请退款(可完整预览的文档不适用该条件!)。
- 3、如文档侵犯您的权益,请联系客服反馈,我们会尽快为您处理(人工客服工作时间:9:00-18:30)。
橡胶工业助剂配方袖珍手册内容简介1.促进剂DM:在NR及SR中硫化速度中等,硫化特性平坦。
可适用于大多数通用橡胶。
在“白色”胶料中无污染不退色。
在NR传统硫化系统中,硫磺用量约2.5份。
在NR 半有效硫化系统中,硫磺用量降至1.0份左右,可获得良好的抗老化和抗返原性能。
2.促进剂DZ(作单用促进剂)尤其适用于直接与黄铜表面或有黄铜镀层的钢丝配方。
与其它次磺酰胺促进剂相比,焦烧安全性能最好。
在NR配方中用量为0.7-2.0份,对应的硫磺用量位2.5-1.5份,在钢丝帘布胶料配方中硫磺用量普遍在4份左右。
高湿度/高温度会引起产品分解从而导致焦烧时间缩短。
本产品不能存放在不溶性硫磺附近,从本产品释放的胺类挥发物会导致不溶性硫磺返原为普通硫磺。
3.促进剂NOBS:是一种通用型主促进剂,在所有(中等)快速硫化次磺酰胺促进剂中,其加工安全性能最好,硫化速率中等,可以较好地提高硫化胶模量。
在NR中的用量为0.5-1.5份,随着NOBS的用量增大,硫磺用量相应减少。
本产品不能存放在不溶性硫磺附近,从本产品释放的胺类挥发物会导致不溶性硫磺返原为普通硫磺。
4.促进剂TBBS:是一种伯胺基通用型主促进剂,硫化速度快,焦烧安全性好,可以极好地提高硫化胶的模量。
在NR…SBR…BR及其并用胶中,TBBS的用量降低10%时,能获得CZ及NOBS相同的模量。
TBBS与CTP并用能够代替NOBS ,既可以避免人们所关注的亚硝胺问题,又可以满足相同的胶烧安全性能和更快的硫化速率的需要。
5.促进剂DPTT:在大多数硫磺硫化弹性体中用作主或助促进剂或硫磺给予体。
无污染性,特别适用于浅色胶料。
其有效硫的含量位28%,因而更适用于半有效及有效硫化系统。
在EPDM中,DPTT在“三个8”组成的系统中,(DPTT 0.8份.TDEC 0.8份TMTM0.8份.MBT 1.5 份.硫磺.2.0份)作助促进剂用。
在其它助促进剂系统中DPTT的用量为0.5—1.5之间。
6.促进剂TBzTD:用作快速硫化主促进剂或助促进剂。
在氯丁胶中用作延迟剂。
无污染性不引起变色。
TMTD相比,TBzTD具有更长的焦烧时间。
无.污染性、变色性。
重叠堆放和/或温度超过35℃会导致产品非正常压缩。
7.促进剂TMTD:在与噻唑类、次磺酰胺类等促进剂并用时,用作主或助(超)促进剂。
TMTD在大多数硫磺硫化弹性体中也可以用作硫化剂(硫磺给予体)。
考虑到分散性,建议在软胶料中使用TMTD粉料,而不是TMTD的结晶状粉料。
无污染性,并且不引起变色。
含13%的有效硫磺(作硫磺给予体时)。
TMTD与次磺酰胺类促进剂并用时,用0.1份TMTD代替0.3份的次磺酰胺便可以获得相同的硫化特性。
1.0份TMTD、1.0份CBS、1.0份DTDM并用,胶料的加工安全性与物理特性都较好,并且胶料不喷霜。
8.促进剂DPG:在大多数硫磺硫化弹性体中,它与噻唑类及次磺酰按类促进剂并用,作助促进剂。
可获得良好的硫化协同效应、较高的物理机械性能及较快的硫化速度。
DPG 硫化速度较慢并且易较烧,一般不单用。
会引起变色,不用于浅色胶料。
用DPG活化的配方比用秋兰姆及二硫代氨基甲酸盐类促进剂活化的配方,硫化速度快,具有良好的抗返原性、抗屈挠性、以及更好的储存稳定性。
其用量超过1.0-2.0份时,会引起浅色胶料褪色。
9.防老剂6PPD:是一种强效型抗氧剂,适用于天然胶与合成胶的配方,同时也可以用作合成聚合物稳定剂。
能防止静态及动态操作条件下的疲劳降解。
用量超过2.0份时可能会引起喷霜。
会使胶料变色,引起严重的接触变色。
由于具有强效抗氧化和抗臭氧特性,因而赋予橡胶极好的抗高温疲劳与屈挠性能。
因其特有的分子结构及其在橡胶中的溶解能力,使其受环境(如:热.淋.洗)影响小,所以具有更好的耐久性能。
它具有良好的抗铜及其它重金属催化降解性能。
它的用量在2.0份以下时,不影响胶料与织物或钢帘线的粘合性能;用量超过2.0份时,可能会引起喷霜,影响层间及胶层与帘线间的黏合性能。
它的最佳用量为0.5份(最佳抗氧性能)。
在表面层其最低用量为1.0份,否则会产生臭氧裂吻,导致严重损坏。
它重叠堆放和/或温度超过35℃会导致产品非正常压缩。
10. 防老剂77PD:高效抗臭氧剂,适用于天然胶与合成弹性体胶料,尤其适用于无防护蜡静态使用的胶料。
10.对于胶料来说常见的问题就是填充剂的分散。
分散不良常常会导致物理性能降低,外观难看,产品缺陷和无法使用。
一般可分为:质量差,橡胶和/或填充剂不达标;填充剂结块;各组份混炼顺序不对;混炼方法不正确;设备问题。
一般都同意在橡胶中分散很细的填充剂的最好办法是在混炼周期的开始就添加进去,那时的剪切应力最大。
但是对于其它的组分的最佳加料顺序还没有一致意见。
加料顺序:橡胶—氧化锌—碳黑—操作油—促进剂—硬脂酸—硫磺(针对天然胶和丁苯胶的混炼)。
有人认为:碱性材料与酸性材料不能同时加入,因此硬脂酸与氧化锌不能一起加入,否则氧化锌的分散肯定不好;而且能够观察到填充剂在转子上结块。
某些促进剂.防老剂和硫磺在混炼温度下在橡胶中不溶解,这会导致分散问题,并且在硫化剂的作用下会在最后产品里形成局部过硫点,即所谓的“起疙瘩”。
显然硫化体系的良好分散是获得高质量的关键,由于这些材料均在邻近混炼周期完成前才加入,所以经常会发生分散不良,这被认为是工厂混炼的胶料性能总比实验室的炼胶料差的原因。
11.碳黑分散不好的影响:拉伸和撕裂强度显著下降,而模量和硬度对分散性的变化不敏感。
12.决定混炼质量的因素:除开炼胶的一般规则外,每批的投料量.转子的速度.上顶栓的压力等13.喷霜:喷霜出现在橡胶的表面,最好被描述为一种模糊的灰尘似的污染物。
几乎都是由于使用橡胶助剂的量超过其在橡胶中溶解度导致的。
某些情况下,该现象被作为优点加以利用,如在胶料中混合过量的蜡,就会在表面喷霜,有助于防止臭氧和气候老化。
喷霜的条件取决于配方和环境情况而在很大范围内改变。
解决喷霜的唯一的永久解决方法是减少这种配合剂的用量或用另外一种组分代替。
除了硫磺还有许多助剂能导致喷霜,如:某些促进剂尤其是秋兰姆类和二硫代氨基甲酸脂类;某些防老剂,如DPP D;酸类防焦剂以及PVI的反应产物;增粘剂如间苯二酚。
14.子午胎胎恻:天然胶/50.0,顺丁胶/50.0,碳黑N326/50.0,芳烃油/10.0,氧化锌/3.5,硬脂酸/1.0,防护蜡/2.5,防老剂6PPD/3.0,促进剂TBBS/1.0,硫磺IS-7020/2.5。
白胎侧:天然胶/50.0,三元乙丙胶Vitaion4068/25.0,SBR1502/25.0,氧化锌/5.0,硬脂酸/1.0,滑石粉/20.0,二氧化钛/50.0,无水硅酸铝/30.0,轻质氧化镁MagliteK/0.5,群青/0.2,TBMC/1.0,TBBS/1.0,硫磺HIS-7020/2.5。
15.轮胎气密层:天然胶/63.0,丁基胶HT-1068/37,硬脂酸/1.0,通用炉黑/65.0,PolythleneAC617A/3.0,环烷烃油Sunthene4240/20.0,FlectolTMQ/2.0,氧化锌/6.0,二硫化烷基苯酚Vultac5/1.25,PerkacitMBTS/0.75,硫磺/1.0。
16.丁基内胎:丁基胶268/100.0,通用炉黑/70.0,硬脂酸/1.0,氧化锌/5.0,石蜡油/25.0,MBTS/0.5,TMTD/1.0,硫磺/2.0,Perkalink900/0.75。
17.翻新胎胎面胶(天然胶):天然胶/100.0,HAF碳黑/45.0,芳烃油/3.0,氧化锌/3.5,硬脂酸/2.0,Santoflex6PPD/2.0,Flectol TMQ/1.0,TBBS/0.7,HIS-7020/2.75。
1)记录100份橡胶的配方2)只考虑橡胶.软化剂和填充剂3)对每种填料和软化剂要在基本硬度上加硬度改变20. 对100.0份橡胶基本的硬度计硬度氯丁橡胶和丁晴橡胶 (44)天然橡胶和冷聚合橡胶 (40)热聚合橡胶 (37)丁基橡胶 (35)充油25份的冷的聚合橡胶 (31)充油37.5份的冷聚合橡胶 (26)20.碳黑表面积对硫化橡胶性能的影响(在碳黑结构不变的情况下)21.22. 有效和半有效硫化体系的介绍提高橡胶制品的硫化温度和适应更苛刻使用条件的要求,导致不断深入进行对天然胶和丁苯胶耐更高温度和抗硫化返原的配方的研究。
一种方法是使用大量的强力抗氧剂,第二种方法是对硫化体系进行调整。
众所周知,用硫磺硫化的弹性体包含大量起作用和不起作用的硫磺改性体,它们的化学和热稳定性能变化范围很大。
这些结构都有进一步发生化学变化的趋势,从而解释了老化后物理性能劣化的原因。
在讨论硫化体系的调整之前,让我们是、先看一下传统的硫化天然橡胶交联键的各种变形结构(天然胶100.0份,促进剂CZ0.6份),对硫化胶的分析表明,基本上没有单硫的结构,20%是二硫化物,80%是三硫或多硫化物(聚硫)。
相当一部分硫磺都消耗在主链变形体上,如悬垂的硫-促进剂基团和环形的硫化物。
单硫或二硫化物的交联有相对较高的化学和热稳定性,而多硫交联和主链变形体是有反应活性的,在老化过程中会发生化学变化,从而导致硫化物的物理性能改变。
传统的天然胶胶料老化时,多硫交联数量减少,单硫交联数量增加,而且网络中的环状硫键增加,由于发生这些分子链的改变,致使弹性体骨架结构被氧化和分子链被剪断,从而导致物理性能的丧失,如拉伸强度和扯断伸长率的下降。
1.天然胶有效硫化体系由于认识到多硫交链键和主链变形体的硫,如环状和悬垂的促进剂,具有化学和热的不稳定型,可从逻辑上假定,如果硫化主要是单硫和二硫交联,则老化前后各种性能的保持性应该非常好。
实际情况也是如此。
这种体系被称为“有效硫化”或有效体系。
有效这个词是从提高硫磺使用效率也就是缩短交联键,减少主链变形体,只是很少的硫磺就能达到有效的交联键数量。
有效体系是通过使用硫给予体全部替代硫磺或使用非常高的促进剂/硫磺比例来获得的。
早期开发的有效体系是基于TMTD的,这种体系因可以提供绝对的单.双硫化交联而得名。
但这种方法所需的TMTD含量通常会导致严重的喷霜和焦烧等不够理想的情况出现。
实践中,有效体系经常TMTD加上喷霜的硫磺给予体如硫化剂DTDM(二硫代二吗啡啉),或采用非常高的促进剂/硫磺比例。
表1显示的是传统硫化体系与两种完全有效体系的比较。
要注意耐老化和耐返原性能的显著改进,以及疲劳性能的显著下降。
由于疲劳性能太差,天然胶有效体系的应用受到极大的限制。
表一.天然胶传统体系与有效体系的对比由于半有效硫化体系表现出耐.返原.老化和疲劳的良好组合性能,故应用广泛。
半有效硫化体系可通过用硫磺给予体部分取代硫磺或适度调整硫磺/促进剂比例来实现。