催化裂化基础能耗计算
催化裂化计算公式
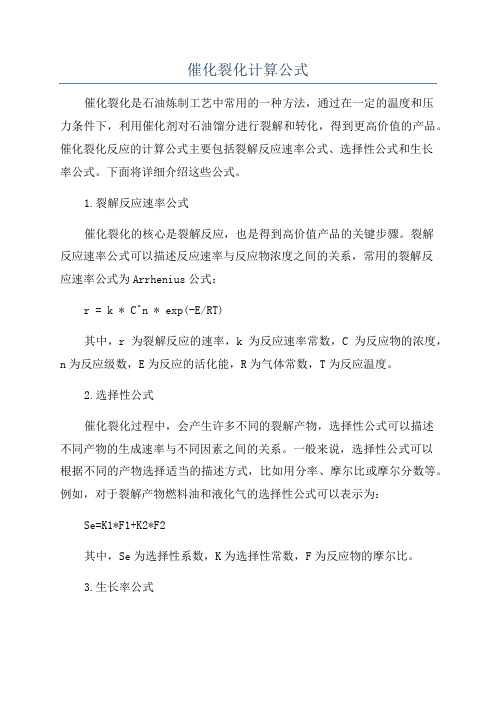
催化裂化计算公式催化裂化是石油炼制工艺中常用的一种方法,通过在一定的温度和压力条件下,利用催化剂对石油馏分进行裂解和转化,得到更高价值的产品。
催化裂化反应的计算公式主要包括裂解反应速率公式、选择性公式和生长率公式。
下面将详细介绍这些公式。
1.裂解反应速率公式催化裂化的核心是裂解反应,也是得到高价值产品的关键步骤。
裂解反应速率公式可以描述反应速率与反应物浓度之间的关系,常用的裂解反应速率公式为Arrhenius公式:r = k * C^n * exp(-E/RT)其中,r为裂解反应的速率,k为反应速率常数,C为反应物的浓度,n为反应级数,E为反应的活化能,R为气体常数,T为反应温度。
2.选择性公式催化裂化过程中,会产生许多不同的裂解产物,选择性公式可以描述不同产物的生成速率与不同因素之间的关系。
一般来说,选择性公式可以根据不同的产物选择适当的描述方式,比如用分率、摩尔比或摩尔分数等。
例如,对于裂解产物燃料油和液化气的选择性公式可以表示为:Se=K1*F1+K2*F2其中,Se为选择性系数,K为选择性常数,F为反应物的摩尔比。
3.生长率公式催化裂化反应中,一些分子会通过生长过程生成更大的分子,这些生长过程可以通过生长率公式描述。
一般来说,生长率公式可以基于碳原子的增长数量表示。
G=A*C^m其中,G为生长率,A为生长常数,C为反应物的浓度,m为生长度。
需要注意的是,上述公式只是催化裂化反应计算中的常用公式,实际应用中还需要结合具体的反应机理和实验数据进行修正和拟合。
此外,催化裂化反应过程中还涉及到反应器设计、催化剂选择、操作参数优化等多方面的问题,需要综合考虑才能得到准确的计算结果。
催化裂化计算方法
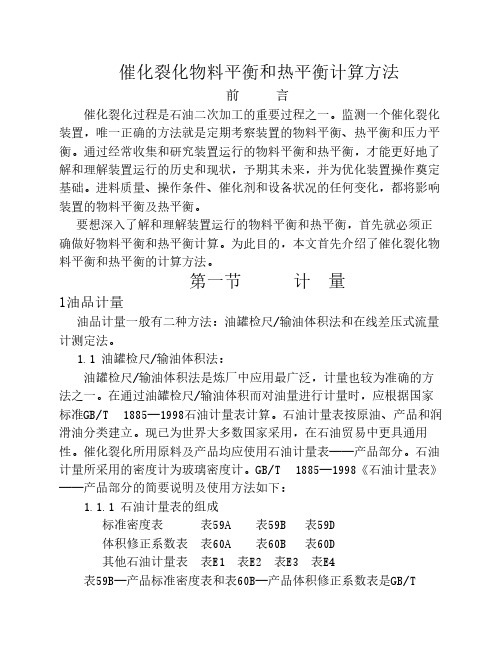
催化裂化物料平衡和热平衡计算方法前 言催化裂化过程是石油二次加工的重要过程之一。
监测一个催化裂化装置,唯一正确的方法就是定期考察装置的物料平衡、热平衡和压力平衡。
通过经常收集和研究装置运行的物料平衡和热平衡,才能更好地了解和理解装置运行的历史和现状,予期其未来,并为优化装置操作奠定基础。
进料质量、操作条件、催化剂和设备状况的任何变化,都将影响装置的物料平衡及热平衡。
要想深入了解和理解装置运行的物料平衡和热平衡,首先就必须正确做好物料平衡和热平衡计算。
为此目的,本文首先介绍了催化裂化物料平衡和热平衡的计算方法。
第一节 计 量1油品计量油品计量一般有二种方法:油罐检尺/输油体积法和在线差压式流量计测定法。
1.1 油罐检尺/输油体积法:油罐检尺/输油体积法是炼厂中应用最广泛,计量也较为准确的方法之一。
在通过油罐检尺/输油体积而对油量进行计量时,应根据国家标准GB/T 1885—1998石油计量表计算。
石油计量表按原油、产品和润滑油分类建立。
现已为世界大多数国家采用,在石油贸易中更具通用性。
催化裂化所用原料及产品均应使用石油计量表——产品部分。
石油计量所采用的密度计为玻璃密度计。
GB/T 1885—1998《石油计量表》——产品部分的简要说明及使用方法如下:1.1.1 石油计量表的组成标准密度表 表59A 表59B 表59D体积修正系数表 表60A 表60B 表60D其他石油计量表 表E1 表E2 表E3 表E4表59B—产品标准密度表和表60B—产品体积修正系数表是GB/T1885—1998《石油计量表》的组成部分之一。
表59B用于润滑油以外的石油产品,由已知试验温度下的视密度(密度计读数)查取标准密度(20℃温度下的密度)。
表60B用于润滑油以外的石油产品,由标准密度和计量温度查取由计量温度下体积修正到标准体积(20℃温度下体积)的体积修正系数(VCF20)。
1.1.2 产品计量产品按空气中的质量计算数量。
催化裂化基础能耗计算

催化裂化装置基准能耗中石化炼油事业部节能中心2004.121 适用范围本基准能耗适用于国内各种类型、处理各种原料、任何生产方案的大中型(≥50×104t/a)催化裂化装置(包括ARGG,MGD,MIP,FDFCC等)。
本方法计算的基准能耗包括反应、再生、分馏、吸收稳定、主风机和烟气透平、余热锅炉、气压机、余热回收站等部分,但不包括水处理和产品精制部分。
2基准能耗主要修订内容(1)鉴于目前催化裂化装置正常生产几乎都不使用加热炉,因此取消原基准能耗中的加热炉能耗项。
(2)根据目前在催化裂化装置中重油催化裂化占绝大多数,仅用掺渣比来衡量催化裂化原料的轻与重并不确切。
因此,在新的基准能耗中计算化学焓差能耗(即反应热)不采用以掺渣比来作为对原料轻重的区别,而采用原料的主要性质(比重、残炭、平均沸点、分子量)来评判原料的轻重,反应热采用分子膨胀法来计算。
(3)原基准能耗中余热锅炉的排烟温度是按250℃考虑的。
鉴于目前有些装置的余热锅炉排烟已降至180℃,故新的基准能耗再生烟气排烟能耗按180℃考虑。
(4)原基准能耗中散热能耗是用装置焦炭产率和回炼比来关联的。
考虑到散热能耗仅与原设计的设备尺寸有关,而与实际操作条件变化和处理量变化关系不大,故新的基准能耗、散热能耗以装置原设计时的处理量和焦炭产率来关联,而与其它无关。
(5)统计多套数据表明,增压机能耗很难找出与之关联的参数,也是装置能耗计算中最不确定的能耗项。
鉴于此,新的基准能耗对增压机能耗采用以实耗的办法来解决。
(6)新的基准能耗中再生烟气排烟能耗以排烟温度和大气温度差来计算能耗,而在主风机能耗项中,主风的温升作为主风机的有效功来考虑。
(7)考虑到目前许多装置采用注终止剂或回炼汽油,故新的基准能耗新增终止剂或回炼汽油能耗项。
(8)针对ARGG、MGD、MIP、FDFCC等各种方案的不同对能耗的影响,重新修订工艺排弃能耗和冷却介质能耗。
(9)蒸汽能耗项中,除考虑雾化蒸汽比例对耗汽的影响外,也考虑回炼比不同对雾化蒸汽量的影响。
催化裂化装置基准能耗修订解析

催化裂化装置基准能耗修订汇报提纲中国石化集团洛阳石油化工工程公司2005-04-23汇报内容1、前言2、主要修订内容3、基础条件4、计算方法5、基准能耗的校正和评价指标6、基准能耗计算举例一、前言节能技术中心组织有关专家编制了催化裂化装置基准能耗的计算方法 计算原理原料油、生产方案、操作条件变化较大计算装置范围适用范围二、主要修订内容加热炉能耗反应热能耗再生器烟气排烟能耗散热能耗增压机能耗主风机能耗终止剂和回炼汽油能耗工艺排弃能耗和冷却介质能耗蒸汽能耗三、基础条件1、再生烟气组成;2、焦炭组成;3、原料油;4、压力降;5、产品进出装置条件;6、余热锅炉的排烟温度;7、主风机组配置;8、工艺用汽;9、分馏塔循环回流取热;10、低温热温位;11、分馏塔顶油气、压缩富气、补充吸收剂及稳定塔顶油气均按冷却至40℃考虑;12、气压机组;13、干气、液化石油气、汽油组成14、泵驱动形式;15、冷却方式;16、余热锅炉;17、终止剂和回炼汽油;18、预提升介质四、计算方法1、输入项混合原料性质;产品收率;回炼比;原料雾化蒸汽比例;主风机出口压力、气压机出口压力和反应压力设计焦炭产率装置公称处理量装置实际处理量终止剂或回炼汽油量2、基准能耗计算方法化学焓差能耗E1;再生烟气排烟能耗E2;工艺排弃能耗E3;主风机能耗E4;气压机能耗E5;工艺用蒸汽能耗E6;泵及其它用电能耗E7;散热能耗E8冷却介质能耗E9终止剂或回炼汽油能耗E10其他能耗E11化学焓差能耗E1原计算公式:E1=(6.7G+16.75S)(Y F+Y L+Y G)分子膨胀法:M C - M PE1=C R•M C•M PS&W公司修正计算方法M PE1=13.45 +530Y CM C上炼3#催化装置标定值计算比较:1、M P计算方法干气:17;液化石油气:50;汽油:100;轻柴油:200;油浆及重柴油:350。
2、M C计算方法M C=42.97·exp(2.10×10 -4T-7.79×D+2.09×10 -3×T×D)×T1.26×D4.98再生烟气排烟能耗E2计算公式:E2=24.8·y C工艺排弃能耗E3计算公式:E3=42.97·y F+17.66·y L+6.42·y G+1.46·y LO+0.19·y H-91.81工艺物流分顶油气;顶循;轻柴油;贫吸收油;重柴油和产品油浆。
催化裂化装置设计工艺计算方法

1.3.3稀相段直径
稀相段中点压力=0.3315MPa 稀相段温度=675+273=946K 气体体积流率=46.84m3/s 取稀相直径=9.7m 稀相线速=0.62m/s
1.3.4稀相段高度 取稀相段高度为12m
1.3.5过渡段高度 取过渡角为45度
1.3.6催化剂的停留时间
过渡段高度为1.25m
195973.42
1.3.1密相床直径
取密相床密度300kg/m3稀相段平均密度25kg/m3 密相段高度为9m 稀相段高度为12 m 密相段中点压力=0.3465MPa 密相段温度=273+671=943k 气体体积流率=44.67m3/s 取密相段线速为1.1m/s
密相段直径=7.19m
1.3.2 密相段的高度 再生器密相床体积==222cm3 密相段高度==5.45m
1.2.13再生器物料平衡
入方 kg/h
I段干烟气
174422.8
II段干烟气
37492.1
待生剂待入烟 1080 气
I段主风带水 汽
3488.5
II段主风带水 670.8 汽
I段松动吹扫 汽
1500
II段松动吹扫 500 汽
焦炭
17000
循环催化剂 1010000
合计
1250100
出方kg/h
I段干烟气
1.1.2理论干空气量的计算
Ⅰ段碳燃烧生成二氧化碳需O2量706.1×1=706.1kmol/h Ⅰ段碳燃烧生成一氧化碳需O2量413.7×0.5=206.9kmol/h Ⅰ段氢燃烧生成水需O2量595×0.5=297.5kmol/h 理论需O2量=706.1+206.9+297.5=1210.5kmol/h=38736kg/h 理论需N2量=1210.5×79/21=4553.8kmol/h=127506.4kg/h Ⅰ段理论干空气量=O2+N2 =5764.3kmol/h=166242.4kg/h Ⅱ段碳燃烧生成CO2需O2量=197.6kmol/h=6323.2kmol/h Ⅱ段碳燃烧生成CO2需N2=197.6×79/21=743.4kmol/h=20813.9kg/h Ⅱ段碳燃烧生成CO2需N2== O2+ N2=941kmol/h=23137.1kg/h 1.1.3 实际干空气量
催化裂化催化剂单耗计算公式

催化裂化催化剂单耗计算公式概述催化裂化是石油炼制中的一项重要工艺,而催化剂则是催化裂化过程中的关键因素之一。
催化剂的单耗计算对于优化生产过程、降低生产成本具有重要意义。
本文将介绍催化裂化催化剂单耗的计算公式及其应用。
催化剂单耗计算公式催化剂单耗计算公式是通过对催化剂的消耗量进行量化来评估催化裂化生产中的资源利用效率。
下面给出催化剂单耗计算公式的详细描述:公式一:单耗计算催化剂单耗=(进料中催化剂质量-出料中催化剂质量)/进料质量公式二:燃烧热值校正催化剂单耗(修正)=催化剂单耗*燃烧热值修正系数催化剂单耗计算示例为了更好地理解催化剂单耗计算公式的应用,我们将通过一个实际的示例来展示其计算过程。
示例假设某炼油厂使用的催化裂化装置进料中含有1000kg的催化剂,在经过催化裂化反应后,出料中含有800kg的催化剂。
催化过程中,进料总质量为10000k g。
燃烧热值修正系数为0.95。
根据公式一,可得:催化剂单耗=(1000k g-800kg)/10000k g=0.02k g/kg根据公式二,可得:催化剂单耗(修正)=0.02k g/kg*0.95=0.019k g/kg因此,该催化裂化装置的催化剂单耗为0.019kg/k g。
催化剂单耗计算的意义催化剂单耗计算的结果能够反映催化裂化装置中催化剂的利用效率,对生产过程进行优化具有重要意义。
通过计算催化剂单耗,可以评估催化裂化装置的状态,判断催化剂的耗用情况,并及时采取调整措施,以提高生产效益和降低生产成本。
总结本文介绍了催化裂化催化剂单耗计算公式及其应用。
催化剂的单耗计算对于优化生产过程、降低生产成本具有重要意义。
通过计算催化剂单耗,可以评估催化裂化装置的状态,提高资源利用效率。
同时,我们还通过一个示例展示了催化剂单耗计算公式的具体应用过程。
注意:在进行催化剂单耗计算时,需要准确获取催化剂的进料和出料质量,并根据实际情况进行燃烧热值的修正。
只有在真实数据的基础上进行计算,才能得到准确的催化剂单耗结果。
催化裂化节能降耗技术
催化裂化装置的用能特点
可回收利用的能数量大、质量高 催化裂化有高温高压烟气压力能、高达600℃以上的再
生器余热和再生烟气显热、高于300℃的油品显热。 反应热随催化剂的不同而不同,而且变化较大
无定形催化剂(560—630kJ/kg)改为沸石催化剂 (185—465kJ/kg)后,反应热减少,但是新一代的超 稳沸石(420kJ/kg)反应热又上升。 催化裂化装置节能的关键,最主要的途径一是减少总
催化裂化生产用能分析
散热损失 散热损失是不可避免的,主要受保温厚度设计、 装置规模及保温工程质量的影响。 近年来受再生器及烟气管线等露点腐蚀的影响, 再生器外壁温度在设计时不但要考虑节能的需要, 还要考虑露点腐蚀的问题,热损失略有增加。 其它设备管线的保温要符合规范要求,需要规范 施工质量。
典型装置用能分析
1069678 48.13
2009 年 70.46 0.01 1.92 1.42 7.22 -20.49 -13.67 -34.16 0 -4.94 845113 41.93
典型装置用能分析
从表-1中可以知道催化裂化装置能耗主要分 为烧焦、电耗、水耗、蒸汽消耗和低温输出热等 几个主要方面。从表-1可知,烧焦产生的能耗是 影响装置能耗的主要方面,占装置能耗的130% 以上,因此如何降低生焦是降低装置能耗的主要 途径。
典型装置用能分析
焦炭的分类 1、催化焦:是在酸性中心上由催化裂化反应生成的焦炭, 与剂油比成正比。 2、附加焦:也称为原料焦,它是由原料中高沸点、高碱 性化合物在催化剂表面吸附,经过缩合反应生成的焦炭。 (可看成稠环芳烃的缩合物)产率和原料残炭有关。 3、污染焦:由于镍、钒等重金属沉积在催化剂表面上造 成催化剂中毒,促使脱氢和缩合反应加剧。 4、剂油比焦:也称为可汽提焦,因汽提不完全而残留在 催化剂上的重质烃类。
催化裂化工艺计算与技术分析
催化裂化工艺计算与技术分析[例4-1] 已知某催化裂化装置操作条件、产品分布等数据(见表4-6),求提升管油气停留时间。
解:(1)计算提升管入口油气流率,如表4-7所示。
= 26887m 3/h= 7.5 m 3/s(2) 计算提升管出口处油气流率,如表4-8所示。
1011401012732735204.22986+⨯+⨯⨯=i V= 54821m 3/h = 15.2m 3/s (3)计算油气线速 提升管横截面积:F = 0.25 πD 2= 0.25×3.14×1.22= 1.13 m 2计算入口油气流速: U i = V i /F = 7.5/1.13 = 6.6 m/s 计算出口油气流速: U o =V o /F = 15.2/1.13 = 13.5 m/s提升管内油气平均流速= 9.6 m/s(4) 计算油气平均停留时间 t = L / U m = 25 / 9.6 = 2.6 sYc =∆C k ·Rc(1+R F ) ( 4-3) 式中:∆C k ——催化剂的焦炭差,%(重);R F ——回炼比。
流量计有多种,应根据不同的流量计要求,进行校正。
(1)质量流量计是目前为许多炼厂所采用的先进的流量计,这种流量计不受检测点条件变化的影响,可以直接取得总通过量,前后数据相减即可。
(2)差压式流量计是利用流体流经节流装置时所产生的压力差实现流量测量的。
应用最广泛的节流1011161012732734931874+⨯+⨯=o V )6.65.13ln(6.65.13ln-=-=io i o m U U U U U装置是孔板,其次是喷嘴。
使用差压式流量计时,液体体积流量可用下式表示:V 实= C △实Pρ (5-1)式中:V 实—流体体积流量, m 3/h;△P —孔板前后压差,Pa ;ρ实—操作条件下流体的密度,m 3/kg ; C —常数。
流体质量流量可表示为:P CG △实实⋅=ρ (5-2)G 实——液体质量流量,t/h 。
催化裂化烟机功率计算
三机组计算公式1、核算效率公式:(1)主风机主风机多变效率:ηpol=Kt-1/K1×lg(P2/P1)/lg(T2/T1)式中:P1——主风机进口压力Mpa(abc)P2——主风机出口压力Mpa(abc)T1——主风机进口温度,KT2——主风机进口温度,KK1——绝热指数:为空气时K1=1.4例1:空气绝热指数取 1.4,主风机入口压力0.096MPa,主风出口压力0.39 MPa,风机入口温度8℃即281K,主风出口温度167℃即440Kηpol=k-1k* =[(1.4-1)/1.4]*[lg(0.39/0.096)]/[lg(440/281)=89.3%(2)烟气轮机η=△T/T1[1-(P2/P1)(K-1)/K]式中:△T——实际温度差,△T=T1-T2 K,K——烟气平均绝热指数T1:实测入口温度,KT2:实测出口温度,KP1:入口压力,Mpa(abc)P2:出口压力,Mpa(abc)注意:若烟气轮机入口在测量时有蒸汽喷入,应对出口温度进行修正。
(参见“烟气能量回收机组的现场标定”,《炼油设计》86年第3期),否则误差较大。
例2:烟机入口温度692℃即965K,烟机出口温度497℃即770K,进气压力0.318MPa,,排气压力0.105 MPa,绝热质数按 1.308计算,烟机效率η=[(T1-T2)/ T1]/[1-(P2/P1)(K-1)/K]=87.9%2 回收功率的核算由于本设计中未安装烟气流量计(因为烟气催化剂粒子流实际为气固两相流,上前还没有合格的计算公式可用)。
帮采用功率平衡方程式来计算(识破差较大)。
Ne=Nc+Ng1+Ng2+Nco式中:(1) Ne——烟气轮机回收功率,KW(2) Nc——主风机所需轴功率,KWNc=16.0132×P1×V1×K1/(K1—1)×[ε(K1-1)/ k1×ηpoc-1-1]/ η式中:P1——主风机进口压力Mpa(abc)P1=0.098(P0-P1`)/735P0——当地大气压mmHgP1`——主风机入口真空度。
催化裂化装置节能操作与设计建议
催化裂化装置节能操作与设计建议(一)、再生及烟气能量回收1、在设计选型时,单段再生优于两段再生;在单段再生型式中,两器高低并列优于两器同轴,建议尽量选用两器高低并列、单段逆再生型式。
由于两段再生形式烟气能量利用不理想,从能耗利用角度出发新装置设计时尽量少采用并列式两段再生工艺。
对现有的两段再生装置中,一再不回收CO化学、二再烟气不进烟机的装置应适时予以改造,回收二再烟气的能量,做到烟气全部进烟机;2、优化特殊工艺装置的操作,降低DCC工艺装置能耗。
安庆DCC工艺裂化深度大,裂化反应热高达888.6kJ/kg,是装置能耗较高的原因之一。
该设计上也存在缺陷,由于在设计时没有考虑分馏塔顶循环回流,塔顶温度采用冷回流控制,增加了反应回路的压降;塔顶油气完全采用循环水冷却,相当于顶循和塔顶油气的低温余热都没有回收;烟气系统没有烟机,烟气能量没有充分回收,综合起来看,如果能量回收手段完善,DCC工艺本身的能耗不至于太高。
3、优化再生操作,控制合理的耗风指标。
对完全再生型式,以再生器为边界线,控制耗风指标不高于12.0Nm3/kg焦炭;对不完全再生装置,优化CO锅炉的焚烧配风比例,监测锅炉后烟气氧含量,控制补风比例不严重过剩;4、改善再生[wiki]催化剂[/wiki]溢流口设计,控制循环催化剂烟气携带量。
催化剂脱气不理想,将造成富气中的氮含量升高,增加气压机和吸收稳定的能耗,也是安全隐患。
建议监测控制干气中的空气含量不高于20%(v),严重时必须改善脱气设计,提高脱气效果;5、在装置(改造)设计中,选择与主风机能力匹配的烟机,避免由于烟机选型过大,导致烟机常不能发电,或者选型过小,烟气部分排空;6、设计烟机时应充分考虑使烟机能力完全与装置能力匹配,在加工量低于设计工况时,采用改小叶片、减小围带面积等办法,增加烟机本体压力降,减小其入口蝶阀的压力降,提高能量回收率;在满负荷生产的工况时使用原设计的大叶片和围带,使烟机能保持在最佳工况点附近运行。
- 1、下载文档前请自行甄别文档内容的完整性,平台不提供额外的编辑、内容补充、找答案等附加服务。
- 2、"仅部分预览"的文档,不可在线预览部分如存在完整性等问题,可反馈申请退款(可完整预览的文档不适用该条件!)。
- 3、如文档侵犯您的权益,请联系客服反馈,我们会尽快为您处理(人工客服工作时间:9:00-18:30)。
表 4 计算基准能耗与标定核算能耗对比
序号 1 2 3 4 5 6 7 8 9 10 11 项目 E1 E2 E3 E4 E5 E6 E7 E8 E9 E10 E11 EB EF 计算基准能耗 423.84 206.34 654.77 -330.97 168.81 440.24 50 341.58 74.18 5.82 45 2079.60 1.233 标定核算能耗 418.68 251.05 695.31 -119.40 262.57 538.99 51 350 64.64 5.82 45 2563.65 差值 -5.16 44.71 40.61 211.57 93.76 98.75 1 8.42 -9.54 0 0 484.05
1
(5)产品进出装置条件见表 1。 表 1 产品进出装置条件
名称 干气 液化气 汽油 相态 气态 液态 液态 温度 40℃ 40℃ 40℃ 名称 轻柴油 重柴油 油浆 相态 液态 液态 液态 温度 60℃ 90℃ 90℃
(6)余热锅炉的排烟温度以 180℃计。 (7)主风机组按主风机—烟机—电机三机组配置,主风机为轴流风机。若烟机回收动力不足以驱动 主风机时以电力补足;若回收率大于 1 时,也以电力计入基准能耗。 (8)工艺用汽等级为 1.0MPa,扫线、伴热、抽空、采暖及其它间断用汽不计入基准能耗。 (9)分馏塔采用塔顶循环回流,不采用冷回流。另设一中、二中及循环油浆共三个循环回流取热。 (10)分馏塔顶油气中≥90℃部分按低温热回收考虑,<90℃部分按冷却考虑。其余物流中≥100℃部 分按低温热回收考虑,<100℃部分按冷却考虑。 (11)分馏塔顶油气、压缩富气、补充吸收剂及稳定塔顶油气均按冷却至 40℃考虑。 (12)气压机为带中间冷却器的两段离心式压缩机,动力为 3.5MPa 蒸汽背压透平,排汽压力为 1.0MPa。 (13)干气中 C3+按<1v%考虑,液化气中≥C5 组分按<1v%考虑,≤C2 组分按≤0.5v%考虑。稳定塔 按深度稳定考虑,汽油中≤C4 组分按≤1m%考虑。 (14)泵均以电力驱动考虑。 (15)冷却方式均以水冷考虑,水的温升为 10℃。 (16)余热锅炉按不补燃考虑。 (17)回炼汽油为装置自产的粗汽油。如果回炼汽油为来自装置外的粗汽油,要求在粗汽油泵出口分 出同样流量的粗汽油返至装置外。 (18)预提升介质为蒸汽,不考虑干气作为预提升介质。
2 基准能耗主要修订内容
(1)鉴于目前催化裂化装置正常生产几乎都不使用加热炉,因此取消原基准能耗中的加热炉能耗项。 (2)根据目前在催化裂化装置中重油催化裂化占绝大多数,仅用掺渣比来衡量催化裂化原料的轻与 重并不确切。因此,在新的基准能耗中计算化学焓差能耗(即反应热)不采用以掺渣比来作为对原料轻 重的区别,而采用原料的主要性质(比重、残炭、平均沸点、分子量)来评判原料的轻重,反应热采用 分子膨胀法来计算。 (3)原基准能耗中余热锅炉的排烟温度是按 250℃考虑的。 鉴于目前有些装置的余热锅炉排烟已降至 180℃,故新的基准能耗再生烟气排烟能耗按 180℃考虑。 (4)原基准能耗中散热能耗是用装置焦炭产率和回炼比来关联的。考虑到散热能耗仅与原设计的设 备尺寸有关,而与实际操作条件变化和处理量变化关系不大,故新的基准能耗、散热能耗以装置原设计 时的处理量和焦炭产率来关联,而与其它无关。 (5)统计多套数据表明,增压机能耗很难找出与之关联的参数,也是装置能耗计算中最不确定的能 耗项。鉴于此,新的基准能耗对增压机能耗采用以实耗的办法来解决。 (6)新的基准能耗中再生烟气排烟能耗以排烟温度和大气温度差来计算能耗,而在主风机能耗项中, 主风的温升作为主风机的有效功来考虑。 (7)考虑到目前许多装置采用注终止剂或回炼汽油,故新的基准能耗新增终止剂或回炼汽油能耗项。 (8)针对 ARGG、MGD、MIP、FDFCC 等各种方案的不同对能耗的影响,重新修订工艺排弃能耗和 冷却介质能耗。 (9)蒸汽能耗项中,除考虑雾化蒸汽比例对耗汽的影响外,也考虑回炼比不同对雾化蒸汽量的影响。
6 基准能耗的校正
在装置负荷率与设计能力相差较多时,需对计算所得到的基准能耗用下式进行近似校正。 EC=[E2+ E4+E6+E8+E9+E11+L(E1+ E3+ E5+E7+E10)]/L 式中:EC—近似的校正后的能耗,MJ/t; L—装置负荷率,分率。
7 建议的能耗评价指标
由于各个装置的具体条件差别较大,用能耗的绝对值对各装置进行比较是不合适的。因此,用能耗 因数 EF 来评价各装置的能量利用水平,可比性相对要强一些。 EF=E/EC 式中:EC—计算的基准能耗; E—装置的实际能耗,MJ/t。 EF 值越大,表示装置实际能耗与基准能耗的差距越大,能量利用水平越低,节能潜力越大。EF 值 越接近 1,表示能量利用水平越高。在设计完善的装置,EF 值小于 1 也是可能的。
对表 4 所列数据逐项分析,可以看出装置节能的潜力所在之处,有助于节能工作的深入进行。逐项 分析如下: (1)再生烟气排烟能耗 E2 排烟温度为 218.8℃,较基准温度高。 (2)工艺排弃能耗 E3 装置的低温热回收比较充分,分馏塔顶换热至 70℃,顶循换热至 95℃,稳定汽油换ቤተ መጻሕፍቲ ባይዱ至 62℃, 排弃能都较基准能耗少,轻柴油换热至 99℃,和基准能耗相当,一中段油采用循环水后冷,而基准能 耗为全回收。综合以上几项,总的工艺排弃能较基准能耗少,但是实际能耗计算中回收的低温热按 60% 可利用计,另有 40%计入排弃能,因此总和较排弃能稍高。 (3)主风机能耗 E4 基准能耗计算中主风机出口至烟机入口压降按 0.09MPa 考虑,实际主风机出口至烟机入口压降为 0.117MPa。烟机回收功率减少。 (4)气压机能耗 装置气压机组配置为汽轮机-电动/发电机-气压机,标定期间,装置产中压蒸汽压力为 2.1MPa(A) , 气压机耗电 2700kW,因此气压机能耗较基准能耗高。 (5)蒸汽能耗 E6 解吸塔底采用低压蒸汽作为热源,总的蒸汽消耗量加大。 (6)冷却介质能耗 E9 低温热回收比较充分,循环水耗量降低,冷却介质能耗有所下降。
5
8 基准能耗计算举例
下面用实例说明基准能耗计算方法的使用。 例:以上海高桥分公司 140 万 t/a 催化裂化装置 1998 年 8 月 26 日标定数据为例。 表 2 上海高桥分公司 140 万 t/a 催化裂化装置 1998 年 8 月 26 日标定数据
序号 1 原料 进料量 残炭 T50 2 产品收率 干气 液化气 汽油 轻柴油 油浆 焦炭 3 回炼比 (终止剂+回炼粗汽油)/ 新鲜原料 4 原料雾化蒸汽比例 反应压力 主风机出口压力 气压机出口压力 5 装置标定能耗 m% MPa(绝) MPa(绝) MPa(绝) MJ/t m% m% m% m% m% m% 3.63 16.44 40.6 26.62 3.93 8.32 0.02577 0.0038 4.94 0.3 0.393 1.28 2563.65 t/h m% ℃ 178 4.11 455 项 目 单 位 数值
催化裂化装置基准能耗
中石化炼油事业部节能中心 2004.12
0
1 适用范围
本基准能耗适用于国内各种类型、处理各种原料、任何生产方案的大中型(≥50×104t/a)催化裂 化装置(包括 ARGG,MGD,MIP,FDFCC 等) 。 本方法计算的基准能耗包括反应、再生、分馏、吸收稳定、主风机和烟气透平、余热锅炉、气压机、 余热回收站等部分,但不包括水处理和产品精制部分。
表 3 上海高桥分公司 140 万 t/a 催化裂化装置 1998 年 8 月 26 日标定数据计算结果
序号 1 2 3 4 5 6 7 E1=423.84 E2=206.34 E3=654.77 E4=-330.97 E5=168.81 E6=440.24 E7=50 计 算 结 果 序号 8 9 10 11 计 算 结 果 E8=341.58 E9=74.18 E10=5.82 E11=45.00 EB=2079.60 EC=EB EF=1.233
EB= 式中:E1~E11 分别见下述。 (1)化学焓差能耗 E1(MJ/t) E1=CR 式中:CR—与原料性质有关的系数; CR =58066D + 957C - 6539 , kJ/kmol;
∑
i =1
11
Ei
Mc − Mp McMp
MC—原料平均分子量,若有该数据按实际数据输入,若无该数据按下式估算, MC=42.97exp(2.10×10 -4T-7.79D+2.09×10 -3TD)T1.26D4.98; Mp—产品平均分子量; Mp=(yH + yLO + yG + yL + yF)/(2.86×10 -3yH +5×10 -3yLO +0.01yG +0.02yL +5.88×10 -2yF)
计算结果表明:虽然上海高桥分公司 140 万 t/a 催化裂化装置的能耗在国内处于领先地位,但 EF 仍高达 1.233。
9 生产装置标定数据校核及节能潜力分析
同样以上海高桥分公司 140 万 t/a 催化裂化装置 1998 年 8 月 26 日标定数据为例,分析其能耗与基 准能耗的差距并分析其节能潜力。
4
E8=5.76y`C-0.58q +396.9 式中:y`C—装置原设计焦炭产率 m%; q—装置原设计的处理量(新鲜原料进料量)t/h。 (9)冷却介质能耗 E9(MJ/t) E9= 10.9yF +1.54yL+0.55yG+0.12yLO+0.018yH-16.3 (10)终止剂或回炼汽油能耗 E10(MJ/t) E10=1549R2 式中:R2 —终止剂或回炼汽油回炼比(对新鲜进料量) 。 (11)其他能耗 E11(MJ/t) E11=45
3
式中:yH—油浆及重柴油产率,m%; yLO—轻柴油产率,m%; yG—汽油产率,m%; yL—液化气产率,m%; yF—干气产率,m%。 T= T50 T50—新鲜混合原料油恩氏蒸馏 50%点温度,K; C—新鲜混合原料残炭,m%; D—新鲜混合原料油比重,d15.615.6。 (2)再生烟气排烟能耗 E2(MJ/t) E2=24.8yC 式中:yC—焦炭产率 m%。 (3)工艺排弃能耗 E3(MJ/t) E3=42.97yF+17.66yL+6.42yG+1.46yLO+0.19yH-91.81 (4)主风机能耗 E4(MJ/t) E4=(207.86P1-0.32) yC(2.43+16.09P12-13.03P1) -0.133yC(432P1+11.7)+Ne 式中:P1—主风机出口压力 MPa(绝) ; Ne—增压机能耗:无增压机 Ne=0,有增压机时按增压机实际耗功计; Ne=11.84N/W N=增压机实际耗功,kW; W=装置实际处理量,t/h。 (5)气压机能耗 E5(MJ/t) E5=(2.16P2+3)[2.46-4.55(P3-0.08)](yF+yL) 式中:P2—气压机出口压力 MPa(绝) ; P3—反应压力 MPa(绝) 。 (6)工艺用蒸汽能耗 E6(MJ/t) E6=279+31.82a(1+R1) 式中:a—雾化蒸汽比例; R1—回炼比。 (7)泵及其它用电能耗 E7(MJ/t) E7=50 (8)散热能耗 E8(MJ/t)