基于先进传感器技术的航空材料无损检测进展
无损检测技术的新进展
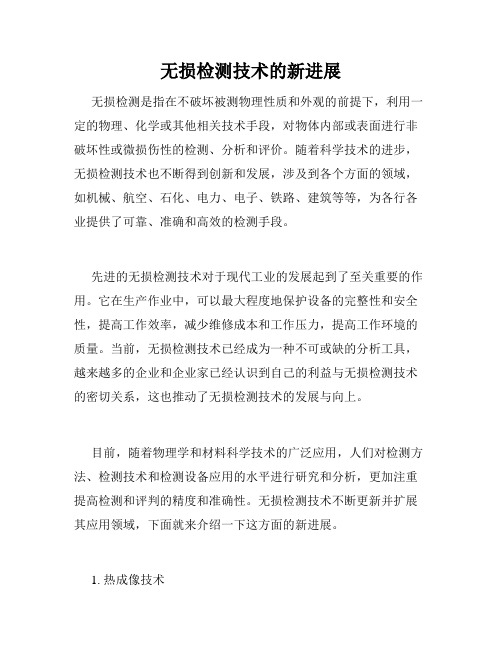
无损检测技术的新进展无损检测是指在不破坏被测物理性质和外观的前提下,利用一定的物理、化学或其他相关技术手段,对物体内部或表面进行非破坏性或微损伤性的检测、分析和评价。
随着科学技术的进步,无损检测技术也不断得到创新和发展,涉及到各个方面的领域,如机械、航空、石化、电力、电子、铁路、建筑等等,为各行各业提供了可靠、准确和高效的检测手段。
先进的无损检测技术对于现代工业的发展起到了至关重要的作用。
它在生产作业中,可以最大程度地保护设备的完整性和安全性,提高工作效率,减少维修成本和工作压力,提高工作环境的质量。
当前,无损检测技术已经成为一种不可或缺的分析工具,越来越多的企业和企业家已经认识到自己的利益与无损检测技术的密切关系,这也推动了无损检测技术的发展与向上。
目前,随着物理学和材料科学技术的广泛应用,人们对检测方法、检测技术和检测设备应用的水平进行研究和分析,更加注重提高检测和评判的精度和准确性。
无损检测技术不断更新并扩展其应用领域,下面就来介绍一下这方面的新进展。
1. 热成像技术热成像技术是一种基于红外光谱的无损检测技术,它能够检测物体表面或内部的温度变化,将热学信息转化成可视的图像或视频。
这种技术不仅可以用于诊断机器设备表面的缺陷和故障,也能应用于监测建筑物和结构物的温度变化,引入越来越广泛的应用领域,例如医学、卫生、保健、生产和维护等。
2. 超声波技术超声波是一种无声或低声的声波,是通过探头向被测物发射声波,利用物体的反射、吸收、穿透和散射等特性得到被测物材料的内部结构变化。
超声波技术广泛应用于工业非破坏检测、质量控制检测、医学和生物检测等领域。
3. 光学成像技术随着近年来光学成像技术的发展,利用光学方法对材料进行无损检测,已经成为一种广泛应用的技术手段之一。
例如激光断层扫描技术(LDS)可以检测物体表面和内部缺陷,并能够精确测量检测到的缺陷和裂纹的尺寸和位置,以及X射线成像技术和拉曼光谱技术等都已广泛应用到材料科学领域。
无损检测技术的未来发展趋势和改进方向

无损检测技术的未来发展趋势和改进方向随着科技的不断进步和工业化程度的提高,无损检测技术在工业领域中的应用逐渐受到重视。
无损检测技术是一种非破坏性检测方法,它能够在不破坏被测对象的情况下,通过测量、分析和判断,检查被测物体的内部和表面缺陷、材料性能以及工作状态。
未来的发展趋势和改进方向将涵盖以下几个方面。
首先,在技术发展方面,无损检测技术将更加智能化和自动化。
随着人工智能和机器学习的快速发展,无损检测技术可以通过人工智能算法和模式识别技术,对大量的数据进行处理和分析,从而能够更准确地判断和预测被测物体的状态。
此外,无损检测技术也将更多地结合无线通信、云计算等技术,实现远程监测和实时数据传输,提高检测的效率和灵活性。
其次,设备和传感器的发展将推动无损检测技术的不断进步。
目前,无损检测技术主要依靠各种传感器来获取被测对象的信号,并通过信号分析来进行判断和诊断。
随着新型传感器技术的不断涌现,如MEMS传感器、光纤传感器等,将为无损检测技术提供更灵敏、更准确、更可靠的测量手段。
同时,新材料的推出,如纳米材料和复合材料,将为无损检测技术提供更适合的测试对象,进一步拓宽技术的应用范围。
第三,无损检测技术将更加注重环境友好性和可持续发展。
在工业生产过程中,无损检测技术往往需要使用辐射、超声波、磁场等能量源来进行检测。
因此,如何降低能源的消耗和减少环境污染将成为今后技术改进的重要方向。
例如,使用低能量的X射线源,研发更环保的检测液体和材料,减少对环境的影响等,将是无损检测技术未来的发展趋势。
此外,无损检测技术还将更加注重实用性和通用性。
目前,无损检测技术在航空航天、汽车、电子、石油和石化等行业得到广泛应用。
未来,随着技术的不断革新和普及,无损检测技术将进一步推广到更多的领域,如医疗保健、农业、矿业等。
为了实现这一目标,需要进一步提高技术的稳定性和可靠性,降低设备的成本和体积,方便使用和维护。
最后,标准化和规范化建设也是无损检测技术发展的方向。
无损检测技术的未来发展趋势和改进方向

无损检测技术的未来发展趋势和改进方向无损检测技术是一种重要的材料检测方法,用于检测材料内部的缺陷和损伤,而无需破坏材料的完整性。
这种技术在许多领域得到广泛应用,如航空航天、汽车制造、建筑工程和能源领域。
随着科学技术的进步和社会的发展,无损检测技术也在不断演进和改进。
本文将讨论无损检测技术的未来发展趋势和改进方向。
首先,无损检测技术的未来发展趋势之一是基于人工智能的应用。
随着人工智能的快速发展和应用,其能力在图像识别和分析方面已经远远超过人类。
将人工智能与无损检测技术结合,可以提高缺陷的检测和诊断效率。
例如,通过训练神经网络来识别和分类不同类型的缺陷,可以减少主观判断的误差,提高检测的准确性和可靠性。
其次,无损检测技术的未来发展趋势之一是以微纳技术为基础的新型传感器的应用。
随着微纳技术的发展,传感器的尺寸越来越小,功能越来越强大。
微纳传感器可以更加灵敏地探测材料的微小缺陷,并可以在高温、高压等恶劣环境下工作。
此外,微纳传感器还可以实现对多个参数的同时检测,提高检测的效率和精度。
第三,无损检测技术的未来发展趋势之一是多模式检测的应用。
传统的无损检测技术通常只能检测一种或几种缺陷类型,而实际工程中往往存在多种类型的缺陷。
因此,发展同时具备多种检测模式的无损检测技术具有重要意义。
例如,结合超声波和磁力学等多种检测模式,可以实现对材料中不同类型缺陷的全面检测。
此外,无损检测技术的未来发展还需要解决以下几个方面的问题:首先是改进检测的灵敏度和分辨率。
当前的无损检测技术在检测微小缺陷和低对比度缺陷方面仍然存在一定的困难。
因此,需要研发更加灵敏和具有高分辨率的无损检测技术,以满足工程应用领域对高精度检测的需求。
第二是提高无损检测技术的可靠性和稳定性。
对于可靠性要求高的领域,如航空航天和核电行业,无损检测技术必须具备高度的稳定性和准确性。
因此,需要加强对测试仪器和设备的质量控制,并改进检测算法和数据处理方法,减小误差和漏诊的概率。
论航空无损检测技术发展现状及挑战

论航空无损检测技术发展现状及挑战航空无损检测技术是航空制造和维护领域的重要工具之一,其发展对于保障飞行安全和延长飞机使用寿命具有重要意义。
随着航空业的快速发展和飞机制造技术的不断提升,航空无损检测技术也在不断地发展和完善。
本文将对航空无损检测技术的发展现状和面临的挑战进行探讨,希望能够为相关研究和实践提供一定的参考。
1. 传统无损检测技术早期的航空无损检测技术主要是使用X射线、超声波、涡流等方法来进行检测,这些方法具有检测速度快、效果准确等优点,能够对金属和非金属材料进行有效的检测。
X射线和超声波技术常被用于对飞机结构、引擎零部件等进行检测,能够有效地发现裂纹、疏松、气孔等缺陷。
而涡流技术则主要用于对铝合金和不锈钢等导电材料的损伤进行检测,具有检测速度快、适用范围广等特点。
随着航空制造材料的不断更新和飞机结构的复杂化,传统无损检测技术在某些方面已经显现出一定的局限性。
近年来,航空无损检测技术向着先进无损检测技术发展。
红外热像技术被广泛应用于飞机表面温度分布检测,能够对机翼等部位的温度分布情况进行全面地监测。
激光干涉和光栅投影等技术也在飞机结构检测中得到了广泛应用,这些方法能够在更大范围内实现无损检测和测量。
随着航空电子设备和自动化技术的不断发展,机载无损检测技术也逐渐成为航空检测领域的研究热点。
通过在飞机上搭载相应的无损检测设备,能够实现对飞机结构和零部件的实时监测,从而及时发现缺陷和故障。
这种技术具有无需停飞、无需拆机、减少维修成本的优点,已经被广泛应用于不同类型的飞机中。
二、航空无损检测技术面临的挑战1. 复杂飞机结构的无损检测随着飞机结构的不断复杂化,传统无损检测技术在某些情况下已经无法满足需求。
对于碳纤维复合材料等新型材料的无损检测,传统的X射线和超声波技术在应用过程中会存在一定的局限性。
如何开发新的无损检测技术,以适应复杂飞机结构的实际需要,是航空无损检测技术发展中的一个重要挑战。
2. 高精度、高效率的无损检测要求航空无损检测技术在实际应用中需要具备高精度和高效率的要求。
无损检测技术在航空维修中的实际应用案例分享
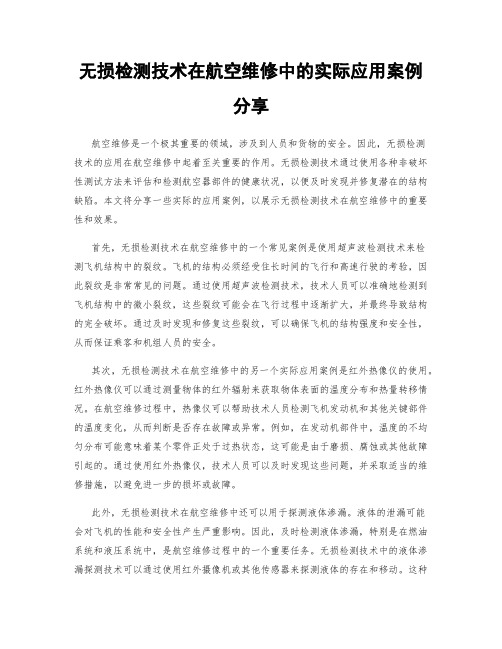
无损检测技术在航空维修中的实际应用案例分享航空维修是一个极其重要的领域,涉及到人员和货物的安全。
因此,无损检测技术的应用在航空维修中起着至关重要的作用。
无损检测技术通过使用各种非破坏性测试方法来评估和检测航空器部件的健康状况,以便及时发现并修复潜在的结构缺陷。
本文将分享一些实际的应用案例,以展示无损检测技术在航空维修中的重要性和效果。
首先,无损检测技术在航空维修中的一个常见案例是使用超声波检测技术来检测飞机结构中的裂纹。
飞机的结构必须经受住长时间的飞行和高速行驶的考验,因此裂纹是非常常见的问题。
通过使用超声波检测技术,技术人员可以准确地检测到飞机结构中的微小裂纹,这些裂纹可能会在飞行过程中逐渐扩大,并最终导致结构的完全破坏。
通过及时发现和修复这些裂纹,可以确保飞机的结构强度和安全性,从而保证乘客和机组人员的安全。
其次,无损检测技术在航空维修中的另一个实际应用案例是红外热像仪的使用。
红外热像仪可以通过测量物体的红外辐射来获取物体表面的温度分布和热量转移情况。
在航空维修过程中,热像仪可以帮助技术人员检测飞机发动机和其他关键部件的温度变化,从而判断是否存在故障或异常。
例如,在发动机部件中,温度的不均匀分布可能意味着某个零件正处于过热状态,这可能是由于磨损、腐蚀或其他故障引起的。
通过使用红外热像仪,技术人员可以及时发现这些问题,并采取适当的维修措施,以避免进一步的损坏或故障。
此外,无损检测技术在航空维修中还可以用于探测液体渗漏。
液体的泄漏可能会对飞机的性能和安全性产生严重影响。
因此,及时检测液体渗漏,特别是在燃油系统和液压系统中,是航空维修过程中的一个重要任务。
无损检测技术中的液体渗漏探测技术可以通过使用红外摄像机或其他传感器来探测液体的存在和移动。
这种技术能够将液体渗漏的位置和严重程度清楚地显示出来,从而帮助技术人员快速定位和修复问题,以确保飞机的正常运行和安全性。
最后,无损检测技术在航空维修中的一个关键应用案例是使用X射线或γ射线检测技术来评估金属结构的完整性和质量。
无损检测技术在航空航天领域中的应用与发展趋势

无损检测技术在航空航天领域中的应用与发展趋势航空航天领域的无损检测技术是确保航空器和航天器安全可靠性的重要手段,它可以帮助检测和评估航空器和航天器中的缺陷、损伤和疲劳等问题,从而及时采取修复或替换措施,保障乘客和航天员的安全。
本文将探讨无损检测技术在航空航天领域中的应用以及发展趋势。
首先,无损检测技术在航空航天领域中的应用非常广泛。
在飞机制造过程中,无损检测技术可以帮助检测飞机结构零件中的缺陷,如裂纹、夹杂物和气孔等。
通过使用超声波、射线、涡流和磁粉等多种无损检测方法,可以对飞机结构进行全面、准确的检测。
此外,无损检测技术还可以应用于航空发动机、航空电子设备和飞机液体系统等关键组件的检测和评估。
在航天器制造和发射过程中,无损检测技术也发挥着重要作用,例如在火箭发动机推力器中检测热应力裂纹、评估航天器外壳的完整性等。
其次,航空航天领域中的无损检测技术正处于不断发展的阶段。
随着航空航天技术的不断前进,新材料的应用以及飞机和航天器结构的复杂性增加,对无损检测技术提出了更高的要求。
一方面,无损检测技术需要发展更精确、快速和全面的检测方法和设备。
近年来,越来越多的无损检测方法开始采用计算机辅助技术,提高了检测的准确性和效率。
例如,利用计算机图像处理技术、机器学习和深度学习等人工智能技术,可以更好地分析和识别无损检测的数据,提高检测的可靠性。
另一方面,无损检测技术还需要不断适应新材料和结构的发展。
例如,碳纤维复合材料已经广泛应用于飞机结构中,其无损检测技术相对于传统金属结构更为复杂,需要不断研究和发展更适应新材料的无损检测方法。
此外,随着航空航天领域的发展,无损检测技术还面临着一些挑战和机遇。
首先,航空航天器的无损检测要求越来越高,对无损检测设备和方法提出了更高的要求。
例如,对于飞机结构的检测要求越来越高的分辨率和检测速度,对无损检测设备的性能提出了更高的要求。
其次,航空航天器无损检测技术还面临着航天器复杂性和可靠性的挑战。
论航空无损检测技术发展现状及挑战

论航空无损检测技术发展现状及挑战航空无损检测技术是航空工程中关键的一环,它能确保飞机零部件和结构的安全性,从而保障飞行安全。
随着航空业的不断发展和飞机的更新换代,无损检测技术也在不断演进。
本文将就航空无损检测技术的发展现状以及面临的挑战进行探讨。
1.传统无损检测技术的发展航空无损检测技术的起步可以追溯到上世纪40年代,当时主要采用的是X射线检测技术。
随着科学技术的不断进步,超声波检测、涡流检测、磁粉检测等传统无损检测技术相继得到应用,并取得了一定的成果。
这些技术在检测飞机结构和零部件的裂纹、缺陷等方面发挥了重要作用,确保了飞行安全。
2.先进无损检测技术的广泛应用随着科学技术的不断进步,一些先进的无损检测技术也开始在航空领域得到应用。
红外热波成像技术可以检测飞机表面的隐形缺陷,非接触性的光学相干断层扫描技术可以对复杂结构进行全方位的检测。
这些先进技术的应用,可以为航空领域的无损检测提供更多的选择和更高的效率。
3.智能化无损检测技术的发展随着人工智能和大数据技术的不断发展,智能化无损检测技术也开始逐渐应用于航空领域。
通过利用机器学习和深度学习等技术,可以对大量的无损检测数据进行分析和处理,提高检测的准确性和效率。
智能化无损检测技术也为航空维修提供了更多的可能性,可以实现更加精准的故障诊断和预测。
二、航空无损检测技术发展面临的挑战1.安全性和可靠性要求的提升随着航空业的不断发展,飞机的运行环境和运行要求也越来越严格,飞机零部件和结构的安全性和可靠性要求也在不断提升。
这就对无损检测技术提出了更高的要求,需要能够更加精准、全面地检测飞机结构和零部件的裂纹、疲劳等隐患,确保飞机的飞行安全。
2.多材料组合结构的检测难题随着航空材料科技的不断进步,飞机结构的材料也越来越多样化和复杂化,多材料组合结构的出现给无损检测技术带来了新的挑战。
传统的无损检测技术对于复合材料、新型金属合金等材料的检测能力有限,需要针对不同材料的特性进行技术革新和突破。
航空装备无损检测技术现状及发展趋势

军方视角VISUAL ANGLE中国军转民54摘要:无损检测技术在航空装备的生产、制造、使用、维修、无损检验等领域中发挥着重要的作用。
为了使无损检验技术得到可持续发展,必须倡导新的检测观念和方法。
以健康监测、综合检测、数据整合、数字化、影像化、信息化等为代表的绿色无损检测技术,将成为今后有意义的检测技术。
关键词:航空装备;无损检测;现状0引言无损检测 (NDT)技术是一种具有低投入、高产出的典型工程应用技术。
它能够提高飞机、太空、发电站、船舶、汽车和建筑物的可靠性。
无损检测技术是一项应用非常广泛的技术,它与国家的重点项目建设密切相关,是我国目前急需解决的重大安全问题。
1航空装备无损检测工作的主要特点航空设备的无损试验存在着以下问题:①结构复杂,多数情况下,自动化装置并不能起到很好的效果。
②材料广泛。
包括铝合金、钛合金、高强度钢、复合材料等。
以复合材料为例,其失效现象较为独特,主要存在着分层、基体开裂、纤维断裂等缺陷,同时由于声学各向异性以及声波衰减系数较高,使得传统的超声波探测难以进行。
钛合金是非磁性材料,但为粗晶态,在超声波、涡流探测等方面均遇到了新问题。
③目标的复杂性。
无论是老式飞机,还是新机型,在许多场合下,其探测能力都较差,尤其是叶片、压气机盘、涡轮盘等部件,更是使检验工作十分困难。
④在某些特定部位、特殊区域和可能的故障探测方面,必须事先进行相关的研究。
由于缺乏有关数据,这一工作常常基于已有的试验经验进行大量的前期研究,因此其危险性很高。
2我国航空装备无损检测工作现状在国内,航空航天领域的研究已成为最普遍、最活跃的一个领域。
在进行航空设备无损检验时,必须坚持找到最合适、最有效的途径,不要盲目地走高、精、尖的路线,选择“对”的,不要盲目地去追求“贵”的!比如,在民航的无损检查中,视觉(包括通过仪器的目视)可以占据70%以上的无损伤检查,而可视化和常规检查则有超过90%。
当然,由于飞机的特殊和安全需要,目前最先进的探测技术(结构健康监测、脉冲涡流、激光、红外图像)已被广泛应用。
- 1、下载文档前请自行甄别文档内容的完整性,平台不提供额外的编辑、内容补充、找答案等附加服务。
- 2、"仅部分预览"的文档,不可在线预览部分如存在完整性等问题,可反馈申请退款(可完整预览的文档不适用该条件!)。
- 3、如文档侵犯您的权益,请联系客服反馈,我们会尽快为您处理(人工客服工作时间:9:00-18:30)。
智能检测技术Automatic Testing and Measurement Technology2009 年第4 期·航空制造技术51在苛刻的工作环境条件下,飞机结构对疲劳裂纹、腐蚀损伤和冲击缺陷非常敏感,容易导致关键结构件的失效,甚至发生灾难性事故。
无损检测(N D T)能够尽早发现飞机结构缺陷并采取适当的维修措施,保证结构基于先进传感器技术的航空材料无损检测进展齐共金工学博士,毕业于国防科技大学航天与材料工程学院,现供职于北京航空工程技术研究中心。
主要研究方向:航空无损检测。
先后参加国家973项目“光子/声子晶体”等多项重大科研项目,以第一作者身份在国内外刊物上发表学术论文30余篇,其中被SCI 收录14篇。
北京航空工程技术研究中心 齐共金 雷 洪 景 鹏S H M 是一种新的预警范例,可以用来防止灾难性失效,明确修补策略,减少维修成本,提高飞机安全。
最有前途的S H M 技术需要先进的智能化传感器,例如小型P Z T 传感器和光纤传感器,使之容易嵌入或粘接到重要的飞机结构上。
基于实时原位S H M 的视情维修将是飞机无损检测和维修理论的未来发展方向。
Progress of Non -destructive Testing for Aviation Materials Based on AdvancedSensor Technology完整性和飞行安全,延长飞机,特别是老旧飞机的服役寿命。
从飞机结构设计、制造到后来的维修,直至最后的结构失效或退役,N D T 都发挥着重要作用。
迄今为止,除了常规的超声、涡流、磁粉、渗透和射线检测之外,人们开发了各种先进的无损检测方法。
无损检测的发展依赖于很多关键技术,其中包括先进的传感器技术,用来监控或检测温度、磁场、应变、振动和位移等等。
这些传感器具有不同的工作原理、类型、灵敏度、阵列、位置、成本、尺寸、重量和数量,决定了整个检测系统的灵敏度、效率和安全性。
近年来,航空无损检测及其相关传感器技术进步很快,本文介绍基于先进传感器技术的航空材料无损检测的最新进展,包括光学检测(热成像、激光剪切散斑成像)、微波检测、振动监控、磁共振检测和敲击检测技术,涉及光学传感器、微波传感器、振动传感器等等。
基于先进传感器技术的航空材料无损检测1 光学检测及其传感器技术近年来,光学检测技术在航空材料领域中的研究和应用越来越多,典型的有红外热成像和激光剪切散斑成像技术,所采用的传感器技术包括热辐射传感器和C C D 传感器等,通过这些传感器捕捉信号,经过处理后最终对材料和结构进行成像。
FORUM52航空制造技术·2009 年第4 期(1)红外热成像及其红外传感器。
物体有无缺陷时所产生的红外热波场不同,通过红外热成像检测这种热波场并用图像显示出来,可以达到对物体内缺陷进行检测和识别的目的。
它是一种快速、非接触的无损检测方式,在航空、航天和许多工业领域都有十分广阔的应用前景。
红外热成像系统的关键部件之一是热像仪。
热像仪是一种光电设备,目标物体的热辐射穿过空气被热像仪接收,经过物镜使热辐射聚焦到热辐射传感器(或称为红外探测器)上,红外探测器再把入射的辐射转换成电信号,进而处理成可见图像,即热图。
由此可见,红外探测器将不可见的红外辐射转换成可测量的信号,是红外热像仪的关键部件,直接影响红外热成像检测的灵敏度。
红外探测器已经发展到焦平面阵列阶段,探测单元数大大增加。
从材料组成和原理分类,高精度红外测温传感器包括I n S b、I n G a A s、非本征硅等量子探测器,以及B S T、多晶硅和非晶硅等热探测器。
英国B a t h 大学材料研究中心和希腊I R T 研究人员[1-2]利用便携式Thermoscope 脉冲热成像系统,对飞机复合材料结构表面和近表面成像。
该系统采用具有InSb 探测器的Indigo Merlin 中波(3~5μm)红外相机,帧频60H z,焦平面阵列格式320×256像素。
不仅能够清晰地检测铝或C F R P 复合材料蒙皮下的模拟分层和孔缺陷,而且可以提供不同类型和厚度蒙皮下固定构件的亚表面特征和位置信息,有利于装配过程中的精确自动操作。
美国T e x a s R e s e a r c h International 公司和加拿大航空航天研究所等机构合作[3],对两层A l 2024-T3铝合金板铆接样品的疲劳磨蚀损伤进行脉冲热成像检测,用来模拟机身连接部件隐藏接触面的主动磨蚀损伤。
他们采用Echotherm红外热成像系统,配备了F l i r 公司T h e r m a C A M S C 3000型红外相机,该相机是量子阱红外照片探测器(QWIP),具有320×240单元的焦平面阵列探测器,303K 下的热灵敏度为20m K,光谱响应为8.0~8.8 μm。
结果发现,热成像可以鉴别磨蚀损伤,疲劳磨蚀最初在铆钉/孔界面发生,然后向接触面扩散。
采用超声短脉冲(一般小于1s)会引起疲劳裂纹面摩擦或碰撞,导致摩擦生热和温度升高,用红外相机检测成像后,背景为暗场,而裂纹附近温度升高呈现为明亮的红外源,这种检测方法称为声红外成像。
美国圣地亚国家实验室和Wayne 州立大学[4]将声红外技术用于飞机结构检测,代替常用的磁粉或渗透检测,以减少除漆、清洁、工艺评价时间,降低地面空间要求和缓解环境污染问题。
他们采用40kHz 超声传感器和InSb 阵列Indigo Phoenix 红外相机(320×256像素),检查各种裂纹部件疲劳裂纹,包括JT-8D 飞机发动机涡轮叶片,Boeing 767机轮等等。
(2)激光剪切散斑成像及其CCD 传感器。
激光剪切散斑成像是一种干涉光学检测方法,采用激光源照射物体,与计算机相连的视频剪切散斑摄像头用于记录和处理数字信号,提供表面和亚表面缺陷的散斑图像。
摄像头的主要部件之一是C C D 图像传感器,其性能直接决定最终的图像质量。
德国B r e m e n 应用波束技术研究所开发了一种综合的剪切散斑装置[5],该装置采用两个相干激光源照射,能够成功检查飞机机翼和机身的层状和蜂窝结构,对表面和亚表面缺陷进行无损检测。
美国北卡罗来纳州州立大学利用剪切散斑技术[6],检测G R I D -L O C K 金属构件的结合缺陷。
激光源产生干涉图像,通过C CD 相机得到面外位移梯度(散斑成像),可清楚检测脱粘和弱结合等缺陷。
2 微波检测及其波导传感器微波(例如厘米波和毫米波)可以穿透蜂窝复合材料等低损耗介电材料,并与内部结构发生相互作用,对于介电性能变化和边界界面变化比较敏感。
所以,微波成像技术可以非接触快速检测复合材料中介电性能发生变化的夹杂和腐蚀等亚表面缺陷。
阿联酋Sharjah 美国大学微波成像和无损评价实验室[7]开发了微波和多层结构之间相互作用的理论成像模型,展示了该方法检测多层复合材料亚表面夹杂的潜力。
利用K 波段(25.5GHz 或26GHz)末端开口矩形波导作为成像传感器,120°相位动态范围,x 和y 方向分辨率为1mm,从而获得近场微波图像。
美国Missouri-Rolla 大学应用微波无损检测实验室与波音公司、空军研究实验室A F R L、T e xa s 研究所合作[8-11],对微波技术检测飞机材料和结构进行了系统的研究。
利用具有末端开口矩形波导探头,工作频率在V 波段 (50~75G H z )和W 波段 (75~110G H z ),通过近场毫米波反射计输出直流电压信号并经过信号处理成像,成功检测油漆下和钢/铝金属层底漆下的腐蚀产物。
以铝板上的激光模拟蚀坑(直径和深度为200~400μm)为研究对象,利用相位敏感反射计和孔径1m m × 0.5m m 的介电波导探头(V 波段,50~75G H z),最终得到高分辨光栅扫描毫米波图像,用于估计坑的直径和深度。
微波检测无需耦合剂,便携式、廉价小型的毫米波探头适用于飞机的快速在线实时检测。
单探头利用末端开口波导孔径产生图像,空间分辨率高,对油漆下的腐蚀和提离变化非常敏感。
为此,Missouri-Rolla智能检测技术Automatic Testing and Measurement Technology2009 年第4 期·航空制造技术53大学开发了一种新型差动探头,由1个毫米波源、1个3d B 电源分配器、2个相同的波导孔径探头、1个电源合成仪和1个探测器组成,探头输出代表了每个孔径获得的反射信号和不受提离影响的相干差异。
因为大面积结构腐蚀不是均匀的,敏感的差动探头不仅可以探测腐蚀区域的边界,还可探测腐蚀的内部。
3 振动监控及其光纤传感器结构健康监控(S H M)有多种方法,振动监控是有效方法之一,可用于飞机机翼等结构的检测。
当复合材料出现分层或脱粘时,结构的动力学振动特征会发生变化,分析振动信号可进行监控。
振动传感器有很多,如标准应变计、压电换能器和光纤传感器等。
英国Cranfield 大学[12]开发了一种基于光纤传感器的智能结构系统,进行飞机结构的损伤监控。
该系统采用直径200/230μm 的多模光纤振动传感器,可将其固定在铝样品表面,或嵌入碳纤维/环氧树脂复合材料样品来进行空间光斑检测的理论分析和试验测试。
当连续光射入多模光纤时,光纤末端会获得光斑的木纹状干涉图像;当结构发生损伤时,外部扰动施加到光纤上时,散斑会发生变化(总强度保持不变),由此对结构损伤状况进行评价。
研究结果显示,这种多模光纤传感器可通过振动监控进行智能材料的无损评价,有效地进行服役状态下的SHM。
与传统的电子传感器技术相比,光纤传感器很多优点:重量轻,体积小,价格低;不受电磁干扰,无电流放电和闪电现象;对很多参数敏感,可调节在纤维内部传输的光的强度、频率、偏振或相位。
正因为传感器重量轻、体积小,可方便地嵌入飞机结构或固定在表面,不影响结构完整性和嵌入材料内部等性能,可以在监控振动特性的同时不破坏飞机结构。
此外,光纤传感器灵敏度高,传感距离长,传感面积大,与复合材料相容性好,可检测机翼等大型结构的振动和损伤状况。
嵌入光纤传感器的智能复合材料结构可以监控服役条件下的结构健康状态。
4 磁共振检测及其NMR 传感器飞机机翼等部位通常为蜂窝夹层结构,在潮湿或雨水环境下容易吸潮进水,长期作用下会导致分层或脱粘,影响结构完整性,容易引发事故。
核磁共振(N M R )是交变磁场与物质相互作用的一种物理现象,用感应线圈磁场传感器检测核磁共振信号,经数据处理后可以获取物质的内部结构图像。
加拿大M o n c t o n 大学和N e w B r u n s w i c k 大学等单位合作[13-14],提出了一种基于核磁共振N M R 的方法来检测夹层板进水。