20CrMoH齿轮弯曲疲劳强度研究
齿轮弯曲疲劳强度试验方法

齿轮弯曲疲劳强度试验方法全文共四篇示例,供读者参考第一篇示例:齿轮在机械设备中起着至关重要的作用,它们通过齿轮传动来实现机械运动,比如汽车的变速箱、风力发电机和其他机械设备都离不开齿轮。
齿轮在长时间运作中会受到各种力的作用,容易发生疲劳断裂,因此对齿轮的疲劳强度进行测试是非常重要的。
本文将介绍一种关于齿轮弯曲疲劳强度试验方法,以帮助读者了解如何对齿轮进行有效的疲劳强度测试。
一、试验原理齿轮在实际工作中常常处于扭转状态,因此齿轮齿面上会受到交替弯曲负载,导致齿轮的疲劳断裂。
齿轮弯曲疲劳强度试验就是通过加载一定应力的齿轮样品,进行一定次数的循环载荷,观察齿轮在经过一定循环次数后是否发生疲劳断裂,从而得到齿轮的弯曲疲劳强度数据。
二、试验步骤1. 制备齿轮样品:根据要测试的齿轮种类和规格,选择合适的齿轮样品进行测试。
确保齿轮样品的质量和尺寸符合要求。
2. 振动应力加载:将齿轮样品安装在试验设备上,施加振动应力加载进行弯曲疲劳试验。
根据所需的循环次数和载荷大小,设定试验参数。
3. 观察齿轮状态:在试验过程中,定期观察齿轮的状态,包括表面裂纹、变形等情况。
一旦发现齿轮有异常情况,立即停止试验,并对齿轮进行检查和修复。
4. 记录数据:记录齿轮样品在每个循环周期后的疲劳情况,包括疲劳寿命、发生裂纹的次数等数据。
5. 分析结果:根据试验数据分析齿轮的疲劳断裂情况,计算出齿轮的弯曲疲劳强度指标,评估齿轮的使用寿命和安全性。
三、试验注意事项1. 选用合适的试验设备和工具,确保试验过程中的准确性和可靠性。
2. 控制试验参数,包括载荷大小、循环次数等,确保试验结果具有可靠性。
3. 在试验过程中定期检查齿轮的状态,及时发现问题并采取措施修复。
4. 根据试验结果对齿轮进行评估和改进,提高其疲劳强度和使用寿命。
通过以上介绍,相信读者已经对齿轮弯曲疲劳强度试验方法有了一定的了解。
要保证齿轮的安全可靠运行,进行疲劳强度测试是非常关键的。
20crmnti弯曲疲劳极限 -回复

20crmnti弯曲疲劳极限-回复弯曲疲劳是材料在反复加载和卸载的循环荷载作用下导致的疲劳失效。
具体来说,当材料受到周期性的弯曲应力时,其内部会出现应力集中和微裂纹的形成。
随着循环次数的增加,微裂纹会逐渐扩展,最终导致材料的断裂。
掌握材料的弯曲疲劳极限有助于提高材料的使用寿命和安全性能。
在工程实践中,对材料的弯曲疲劳极限进行评估具有重要意义。
一般来说,评估弯曲疲劳极限需要进行以下步骤:第一步:确定试样的几何形状和尺寸。
试样的几何形状和尺寸应符合具体的工程要求和标准。
通常使用悬臂梁试样或屈服悬臂式试样进行疲劳弯曲实验。
第二步:确定试验加载方式和频率。
疲劳试验是通过施加特定的应力或应变水平来模拟实际工作条件下的循环载荷。
根据实际工况和试验目的,确定试验加载方式和频率非常重要。
第三步:进行预试验和应力水平选择。
预试验是为了确定合适的应力水平进行后续的疲劳弯曲试验。
在进行预试验的过程中,记录试样的载荷-应变曲线和弯曲疲劳寿命曲线。
第四步:疲劳试验。
按照预设的加载方式和频率进行疲劳试验。
在试验过程中,记录试样的应力-循环次数曲线和应力-挠度曲线。
第五步:数据处理和分析。
根据试验获得的数据,绘制应力-循环次数曲线和应力-挠度曲线。
通过对曲线上的数据进行拟合和分析,得到弯曲疲劳极限。
第六步:评估和使用寿命预测。
根据弯曲疲劳极限,评估材料的疲劳性能和使用寿命。
基于研究和试验得到的数据,可以预测材料在实际工况下的使用寿命,以确保材料能够安全可靠地工作。
总之,弯曲疲劳极限的评估是工程实践中不可或缺的一环。
通过合理选择试样的几何形状和尺寸、确定试验加载方式和频率、进行预试验和应力水平选择、进行疲劳试验,并通过数据处理和分析以及使用寿命预测,可以获得准确的弯曲疲劳极限,提高材料的使用寿命和安全性能。
齿轮弯曲疲劳强度试验方法
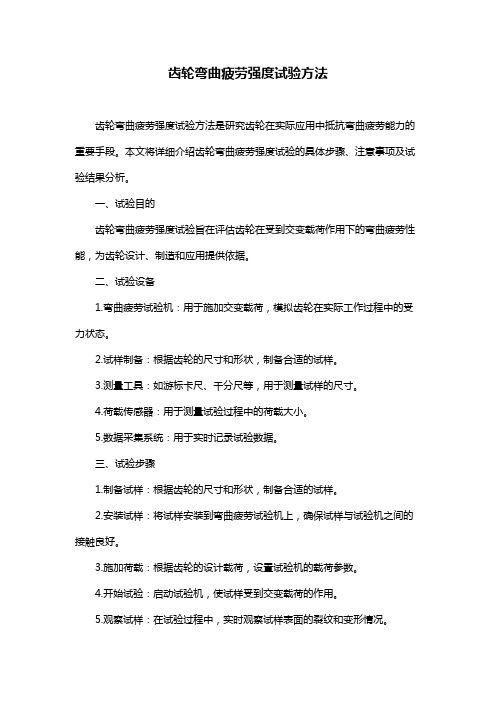
齿轮弯曲疲劳强度试验方法齿轮弯曲疲劳强度试验方法是研究齿轮在实际应用中抵抗弯曲疲劳能力的重要手段。
本文将详细介绍齿轮弯曲疲劳强度试验的具体步骤、注意事项及试验结果分析。
一、试验目的齿轮弯曲疲劳强度试验旨在评估齿轮在受到交变载荷作用下的弯曲疲劳性能,为齿轮设计、制造和应用提供依据。
二、试验设备1.弯曲疲劳试验机:用于施加交变载荷,模拟齿轮在实际工作过程中的受力状态。
2.试样制备:根据齿轮的尺寸和形状,制备合适的试样。
3.测量工具:如游标卡尺、千分尺等,用于测量试样的尺寸。
4.荷载传感器:用于测量试验过程中的荷载大小。
5.数据采集系统:用于实时记录试验数据。
三、试验步骤1.制备试样:根据齿轮的尺寸和形状,制备合适的试样。
2.安装试样:将试样安装到弯曲疲劳试验机上,确保试样与试验机之间的接触良好。
3.施加荷载:根据齿轮的设计载荷,设置试验机的载荷参数。
4.开始试验:启动试验机,使试样受到交变载荷的作用。
5.观察试样:在试验过程中,实时观察试样表面的裂纹和变形情况。
6.记录数据:记录试验过程中的荷载、循环次数等数据。
7.停止试验:当试样出现明显的裂纹或达到预定的循环次数时,停止试验。
四、注意事项1.试样的制备应严格按照齿轮的实际尺寸和形状进行,以保证试验结果的准确性。
2.确保试验机与试样之间的接触良好,避免因接触不良导致的试验误差。
3.在试验过程中,应密切关注试样的裂纹和变形情况,及时记录数据。
4.遵循试验机的操作规程,确保试验安全、顺利进行。
五、试验结果分析1.对比不同齿轮材料的弯曲疲劳强度,为齿轮选材提供依据。
2.分析齿轮设计参数(如模数、齿数等)对弯曲疲劳强度的影响,为优化设计提供参考。
3.研究齿轮制造工艺对弯曲疲劳性能的影响,为改进制造工艺提供指导。
4.通过试验结果,评估齿轮在实际应用中的弯曲疲劳寿命。
总之,齿轮弯曲疲劳强度试验是确保齿轮质量、提高齿轮应用性能的重要手段。
20CrMnTiH凸轮轴惰齿轮及曲轴齿轮失效分析及应对措施

20CrMnTiH凸轮轴惰齿轮及曲轴齿轮失效分析及应对措施杨锴【摘要】通过光学显微镜、扫描电镜、洛氏硬度计及维氏硬度计对失效的20crMnTiH材质的凸轮轴惰齿轮和曲轴齿轮分别进行了微观组织、表面断裂形貌、表面硬度、心部硬度的分析.结果表明,失效的主要原因为热处理过程中渗碳层深超深及心部硬度超标.在采取措施控制渗碳层深及降低心部硬度后,发动机齿轮的服役寿命得以延长.【期刊名称】《金属加工:热加工》【年(卷),期】2010(000)017【总页数】3页(P22-24)【作者】杨锴【作者单位】东风汽车有限公司刃量具厂技术开发部,湖北十堰,442002【正文语种】中文我厂为某主机厂大功率发动机供应相关齿轮。
一次发动机在使用过程中出现故障,经过服务人员拆卸检查发现,发动机内部的凸轮轴惰齿轮和曲轴齿轮断齿严重,而与之相配合的高压油泵惰齿轮和油泵齿轮也遭殃及。
凸轮轴惰齿轮和曲轴齿轮模数均为3.175,材料为20CrMnTiH,技术条件要求为:渗碳淬火,有效硬化层深DC=0.51~1.27mm;带磨量为DC=0.71~1.47mm;表面硬度57~62HRC,心部硬度25~45HRC;马氏体(或残留奥氏体)级别≤3级,碳化物级别≤3级。
我厂委托技术中心根据国家标准GB/T 13298-1991进行检测。
检测条件为31℃,湿度52%RH。
将凸轮轴惰齿轮和曲轴齿轮进行解剖,在LE0 1450VP扫描电子显微镜下观测断口形貌。
1.凸轮轴惰齿轮凸轮轴惰齿轮有7个齿断齿,其中有3个齿断口上可见面积较大的疲劳弧线,其余断齿断口较为粗糙,如图1、图2所示。
3个带有可见面积较大的疲劳弧线的断口SEM形貌如图3所示,其余4个粗糙断口SEM形貌主要为韧窝形貌(如图4所示),说明凸轮轴惰齿轮既有疲劳断齿也有韧性断齿。
对于失效的凸轮轴惰齿轮进行线切割取样,所取得的齿形试样保留有两个完整的齿以方便检测。
使用0LYMPUS GX71金相显微镜进行观测。
20CrMnMo齿轮弯曲承载能力对比试验

循环次数 N × 342 102 × 355 102 × 358 102 × 391 102 × 473 102
>3×106 >3×106
备注 轮齿断裂 轮齿断裂 轮齿断裂 轮齿断裂 轮齿断裂 轮齿未断裂 轮齿未断裂
—2—
57.5
>3×106
轮齿未断裂
57.5
>3×106
轮齿未断裂
57.5
>3×106
2.1 对比试验齿轮的材质 试验齿轮材料分别为: 1 号齿轮材料是 20CrMnMo 是抛丸处理,2 号齿轮
材料是 20CrMnMo 磨齿后再强力喷丸。
2.2 齿轮弯曲疲劳强度的成组寿命对比法实验结果
为了了解在每个应力水平上六种齿轮疲劳寿命的高低,采取成组对比实验
法进行对比实验研究,即在相同的载荷级(或应力水平)上进行双齿脉动加载
轮齿未断裂
2.3 20CrMnMo(抛丸处理)材料齿轮
有限寿命区试验齿轮用恒定应力水平试验法获得的四个应力水平的失效寿
命列于表 2 中。
表 2 试验齿轮失效寿命(按寿命长短排序)
双齿载荷(kN) 应力水平(MPa)
寿命(次)
57.5
835.52MPa
× 342 102 × 355 102 × 358 102 × 391 102 × 473 102
可以看出, 20CrMnMo(磨齿后再强力喷丸)材料齿轮齿根弯曲疲劳极限 远高于正常状态下齿轮齿根弯曲疲劳极限。
—3—
3、结论
通过本项目的试验研究及数理统计分析,我们可以得出以下结论: (1)采用成组对比实验法进行了有限寿命下齿轮的齿根弯曲疲劳试验,每 种状态齿轮采用了四个应力水平,每个应力水平选取了 5 个实验点,获得了每 个应力水平下威布尔分布的位置参数、特征参数和形状参数,从而为不同可靠 度下疲劳曲线的确定奠定了良好的理论基础。 (2)对于抛丸处理的 20CrMnMo 材料齿轮,当载荷增加到 50KN 左右时, 会在齿根产生弯曲疲劳破坏;对于磨齿后再强力喷丸状态下 20CrMnMo 材料齿 轮,当载荷增加到 65KN 左右时,才会在齿根产生弯曲疲劳破坏;由此可见, 对于 20CrMnMo 材料齿轮,磨齿后再强力喷丸的齿根弯曲疲劳强度比普通状态 下的齿根弯曲疲劳强度增大 19.23%。 (3)建议:在某些重要场合,可采用磨齿后再强力喷丸的方法来提高齿轮 的疲劳强度和可靠度。
20CrMnTi硬齿面齿轮弯曲疲劳试验分析

20CrMnTi硬齿面齿轮弯曲疲劳试验分析杨文龙【摘要】为了获得20CrMnTi材料齿轮的弯曲疲劳特性,基于Miner线性损伤累积假设理论,利用疲劳试验机,采用疲劳极限快速测定法,较快地得出被测齿轮的弯曲疲劳极限应力值,能为齿轮设计时提供准确的弯曲疲劳极限应力值.【期刊名称】《机械管理开发》【年(卷),期】2012(000)002【总页数】2页(P65-66)【关键词】20CrMnTi;齿轮;弯曲疲劳;快速测定法【作者】杨文龙【作者单位】中国重汽集团大同齿轮有限公司技术中心,山西大同037305【正文语种】中文【中图分类】TG113.25+50 引言齿轮设计中,齿轮材料的疲劳寿命是关键因素。
齿轮疲劳特性曲线是实现变速器齿轮传动系统有限寿命设计、可靠性设计的关键数据。
特别是汽车变速器设计中,疲劳极限应力尚未获得,给齿轮设计带来较大困难,所以要对其进行疲劳试验研究。
通常,齿轮寿命分布依据大样本的概率试验才能获得,但这造成资源消耗、噪声污染,并且投入资金高,实验时间长,工程中不能广泛应用,因此,本文基于Miner线性损伤累积假设理论,采用罗卡提[1]快速试验方法进行疲劳试验的研究。
与标准试验方法相比较,这种方法只用了有限个试件齿轮,花费较少的时间,就可求出疲劳极限应力,且其相对误差4%左右。
1 试验理论Miner损伤累积假设是罗卡提快速试验法的基础[2]。
该理论认为金属材料在交变应力下,每受一次交变应力就造成小量的损伤,当这些损伤逐渐累积在一起,就达到与其寿命相当的时间。
假设试验齿轮在不稳定的变应力下工作,N1、N2…NK为各应力σl、σ2…σk对应的材料发生疲劳时的各个循环次数,n1、n2…nk为各应力作用下的工作循环次数,可在σ-N坐标上建立。
材料发生疲劳时的循环次数与各应力的对应关系,见图1。
图1 不稳定变应力根据Miner理论,疲劳损伤取决于变形功的作用,因此,在不同的应力水平下工作,就可对相同试验齿轮进行疲劳极限应力快速测定。
汽车齿轮钢弯曲疲劳性能分析研究
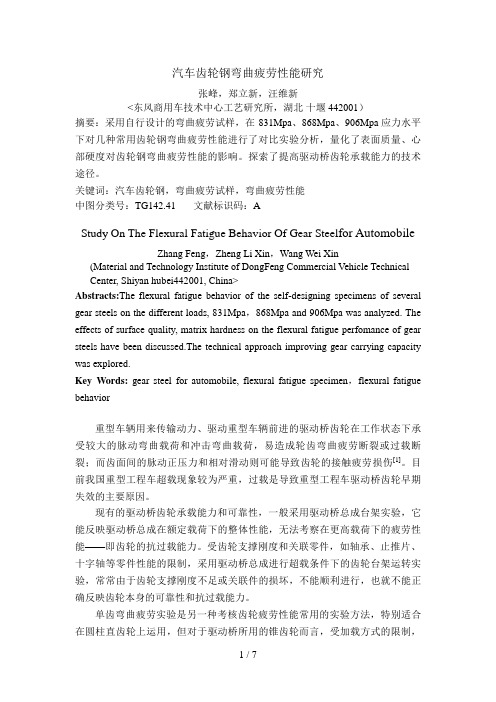
汽车齿轮钢弯曲疲劳性能研究张峰,郑立新,汪维新<东风商用车技术中心工艺研究所,湖北十堰 442001)摘要:采用自行设计的弯曲疲劳试样,在831Mpa、868Mpa、906Mpa应力水平下对几种常用齿轮钢弯曲疲劳性能进行了对比实验分析,量化了表面质量、心部硬度对齿轮钢弯曲疲劳性能的影响。
探索了提高驱动桥齿轮承载能力的技术途径。
关键词:汽车齿轮钢,弯曲疲劳试样,弯曲疲劳性能中图分类号:TG142.41 文献标识码:AStudy On The Flexural Fatigue Behavior Of Gear Steel for AutomobileZhang Feng,Zheng Li Xin,Wang Wei Xin(Material and Technology Institute of DongFeng Commercial Vehicle Technical Center, Shiyan hubei442001, China>Abstracts:The flexural fatigue behavior of the self-designing specimens of several gear steels on the different loads, 831Mpa,868Mpa and 906Mpa was analyzed. The effects of surface quality, matrix hardness on the flexural fatigue perfomance of gear steels have been discussed.The technical approach improving gear carrying capacity was explored.Key Words:gear steel for automobile, flexural fatigue specimen,flexural fatigue behavior重型车辆用来传输动力、驱动重型车辆前进的驱动桥齿轮在工作状态下承受较大的脉动弯曲载荷和冲击弯曲载荷,易造成轮齿弯曲疲劳断裂或过载断裂;而齿面间的脉动正压力和相对滑动则可能导致齿轮的接触疲劳损伤[1]。
20CrMoH齿轮接触疲劳强度研究
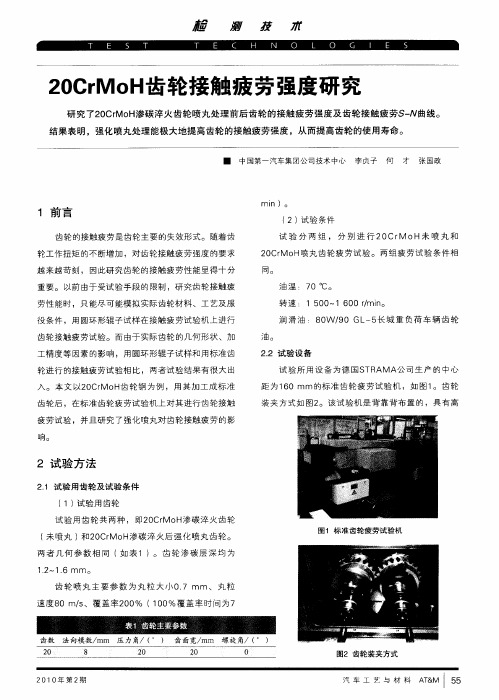
由表 3 可知 , 当齿 轮 工作 扭 矩 增 加 到 2 3 0 Nm 0
时齿 轮 断齿 ,即在高 应 力 区没等 发生 齿轮 接触 疲 劳 失 效 就 先发 生齿 轮弯 曲疲 劳 。用升 降法 求 出齿 轮接 触疲 用 升 降 法 求 出喷 丸 齿 轮 接 触 疲 劳 强 度 为2 0 9 6
获 得在试验 应 力下 的1 个寿命 数据 ,即1 个试 验点 。完
成一 条齿 轮 接触 疲劳S一 ~曲线 ,至 少应 选择3 应 力 个 水平 ,最高 应力 级中应 力循环 次数 不少于 1×1 。 , O次 应力增量 一般取 5 %~1 % ,每个应 力水平 取2 4 0 ~ 个试
H C 残余压应=为9 0MP。2 cM H R, ! 8 a 0 r o 齿轮材料 ]
( 试 验 用齿 轮 1)
试 验 用齿 轮共 两 种 ,即2 Cr H渗碳 淬 火 齿 轮 0 Mo
( 喷丸 ) D 0 H 未  ̄ 2 C Mo 渗碳 淬 火 后 强 化 喷丸 齿 轮 。 r
两 者 几 何 参 数 相 同 ( 表 1)。 齿 轮 渗 碳 层 深 均 为 如
12-1 6 m m 。 .
■
中 国第一 汽车 集 团公 司技术 中 心 李 贞子 何 才 张 国政
mi n)。
1 前 言
齿 轮 的接触 疲劳 是齿 轮主 要 的失 效形 式。 随着 齿 轮工作 扭矩 的不断 增加 ,对齿 轮接 触疲 劳 强度 的要 求 越 来越 苛 刻 ,因此研 究 齿 轮的 接触 疲劳 性 能显 得十 分
裣
渤 技 7 l t
2 C Mo 0 r H齿轮接触 疲劳 强度研究
研 究 了2 Cr H 碳淬 火齿 轮喷 丸处理 前后 齿轮 的接触疲 劳 强度及齿 轮接触 疲 劳S一\ 0 Mo 渗 /曲线。 / 结果表 明 ,强化喷丸处理 能极大 地提高齿轮 的接触疲劳 强度 ,从 而提高齿轮 的使用寿命 。