制动系统匹配计算讲义
制动系统匹配设计计算分解
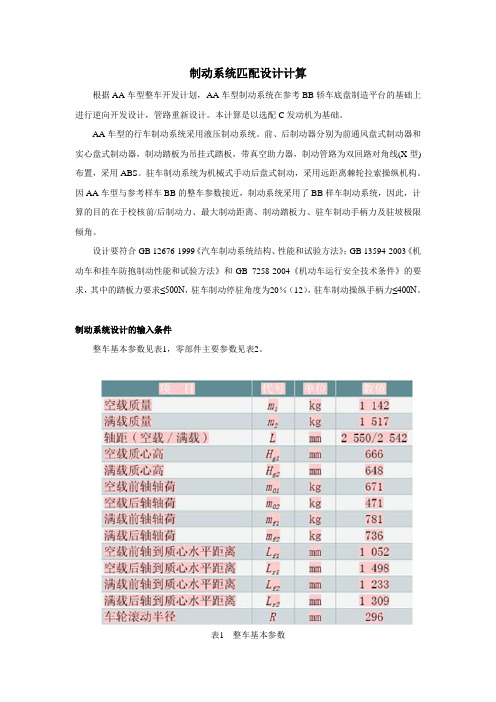
制动系统匹配设计计算根据AA车型整车开发计划,AA车型制动系统在参考BB轿车底盘制造平台的基础上进行逆向开发设计,管路重新设计。
本计算是以选配C发动机为基础。
AA车型的行车制动系统采用液压制动系统。
前、后制动器分别为前通风盘式制动器和实心盘式制动器,制动踏板为吊挂式踏板,带真空助力器,制动管路为双回路对角线(X型)布置,采用ABS。
驻车制动系统为机械式手动后盘式制动,采用远距离棘轮拉索操纵机构。
因AA车型与参考样车BB的整车参数接近,制动系统采用了BB样车制动系统,因此,计算的目的在于校核前/后制动力、最大制动距离、制动踏板力、驻车制动手柄力及驻坡极限倾角。
设计要符合GB 12676-1999《汽车制动系统结构、性能和试验方法》;GB 13594-2003《机动车和挂车防抱制动性能和试验方法》和GB 7258-2004《机动车运行安全技术条件》的要求,其中的踏板力要求≤500N,驻车制动停驻角度为20%(12),驻车制动操纵手柄力≤400N。
制动系统设计的输入条件整车基本参数见表1,零部件主要参数见表2。
表1 整车基本参数表2 零部件主要参数制动系统设计计算1.地面对前、后车轮的法向反作用力地面对前、后车轮的法向反作用力如图1所示。
图1 制动工况受力简图由图1,对后轮接地点取力矩得:式中:FZ1(N):地面对前轮的法向反作用力;G(N):汽车重力;b(m):汽车质心至后轴中心线的水平距离;m(kg):汽车质量;hg(m):汽车质心高度;L(m):轴距;(m/s2):汽车减速度。
对前轮接地点取力矩,得:式中:FZ2(N):地面对后轮的法向反作用力;a(m):汽车质心至前轴中心线的距离。
2.理想前后制动力分配在附着系数为ψ的路面上,前、后车轮同步抱死的条件是:前、后轮制动器制动力之和等于汽车的地面附着力;并且前、后轮制动器制动力Fm1、Fm2分别等于各自的附着力,即:根据式(1)、(2)及(3),消去变量ψ,得:由(1)、(2)、(3)及此时=zg,z=ψ=ψ0,可得:前轴:后轴:由此可以建立由Fu1和Fu2的关系曲线,即I曲线。
制动系统匹配计算讲义
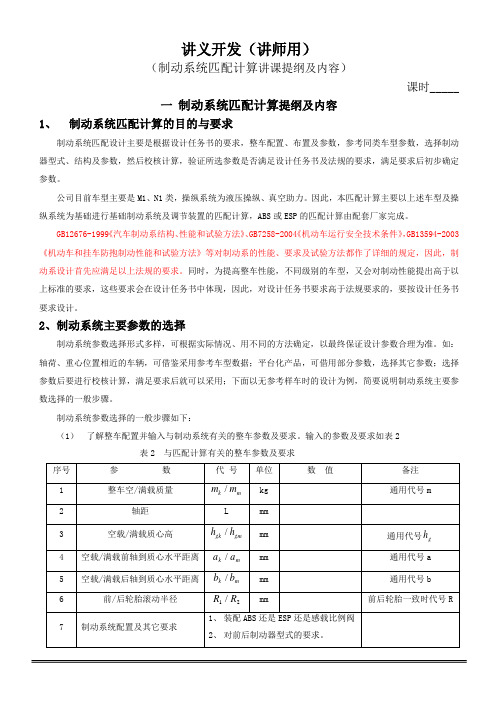
GB12676-1999《汽车制动系结构、性能和试验方法》、GB7258-2004《机动车运行安全技术条件》,GB13594-2003《机动车和挂车防抱制动性能和试验方法》等对制动系的性能、要求及试验方法都作了详细的规定,因此,制动系设计首先应满足以上法规的要求。同时,为提高整车性能,不同级别的车型,又会对制动性能提出高于以上标准的要求,这些要求会在设计任务书中体现,因此,对设计任务书要求高于法规要求的,要按设计任务书要求设计。
Fμ=Tμ/R………………………………………………………(2-3)
式中:Tμ—制动器对车轮作用的制动力矩,即制动器的摩擦力矩,其方向与车轮旋转方向相反。
R—车轮有效半径。
(3)理想的前、后制动器制动力分配
在附着系数为 的路面上,前、后车轮同步抱死的条件是:前、后轮制动器制动力之和 等于汽车与地面附着力 ;并且前、后轮制动器制动力 分别等于各自的附着力 ,即:
制动系统参数选择的一般步骤如下:
(1)了解整车配置并输入与制动系统有关的整车参数及要求。输入的参数及要求如表2
表2与匹配计算有关的整车参数及要求
序号
参 数
代 号
单位
数ቤተ መጻሕፍቲ ባይዱ值
备注
1
整车空/满载质量
kg
通用代号m
2
轴距
L
mm
3
空载/满载质心高
mm
通用代号
4
空载/满载前轴到质心水平距离
mm
通用代号a
5
空载/满载后轴到质心水平距离
制动系统计算说明书
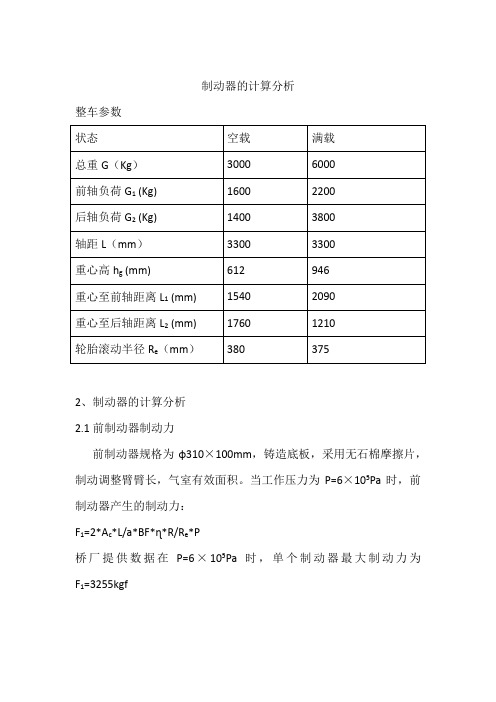
制动器的计算分析整车参数2、制动器的计算分析2.1前制动器制动力前制动器规格为ɸ310×100mm,铸造底板,采用无石棉摩擦片,制动调整臂臂长,气室有效面积。
当工作压力为P=6×105Pa时,前制动器产生的制动力:F1=2*A c*L/a*BF*ɳ*R/R e*P桥厂提供数据在P=6×105Pa时,单个制动器最大制动力为F1=3255kgf以上各式中:A c—气室有效面积L—调整臂长度a—凸轮基圆直径BF—制动器效能因数R—制动鼓半径R e—车轮滚动半径ɳ—制动系效率P—工作压力2.2后制动器制动力后制动器规格为ɸ310×100mm,铸造底板,采用无石棉摩擦片,制动调整臂臂长,气室有效面积。
当工作压力为P=6×105Pa时,前制动器产生的制动力:F2=2*A c*L/a*BF*ɳ*R/R e*P桥厂提供数据在P=6×105Pa时,单个制动器最大制动力为F2 =3467kgf2.3满载制动时的地面附着力满载制动时的地面附着力是地面能够提供给车轮的最大制动力,正常情况下制动气制动力大于地面附着力是判断整车制动力是否足够的一个标准。
地面附着力除了与整车参数有关之外,还与地面的附着系数有关,在正常的沥青路面上制动时,附着系数ϕ值一般在0.5~0.8之间,我们现在按照路面附着系数为0.7来计算前后地面附着力:F ϕ前=G 满1×ϕ+G hgL×ϕ2=2200×0.7+6000×6123300×0.72=2002kgfF ϕ后=G 满2×ϕ-GhgL×ϕ2=3800×0.7-6000×9463300×0.72=1487kgf因为前面计算的前后制动器最大制动力分别为F1=3255kgfF2=3467kgf3、制动器热容量、比摩擦力的计算分析 3.1单个制动器的比能量耗散率的计算分析 前制动器的衬片面积A 1=2×πR 1×w1180×L 1=mm 2式中(L 1=100mm 摩擦片的宽度 w 1=110°) 后制动器的衬片面积A 2=2×πR 2×w2180×L 2=mm 2式中(L 2=100m m 摩擦片的宽度 w2=) 比能量耗散率e 1=GV 124tA 1β= e 2=GV 124tA 2β=上式中:G —满载汽车总质量V 1—制动初速度,计算时取V 1=18m/s β—满载制动力分配系数 t —制动时间,计算时取t=3.06s鼓式制动器的比能量耗散率以不大于1.8W/mm 2为宜,故该制动器的比能量耗散率满足要求。
(整理)制动系统匹配计算讲义
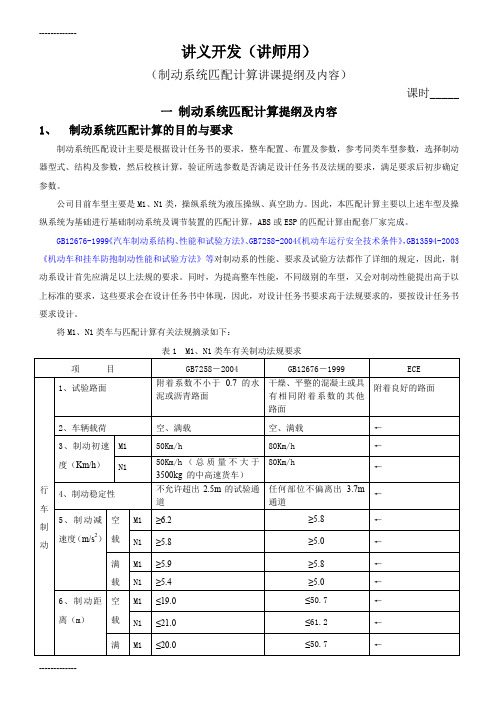
讲义开发(讲师用)(制动系统匹配计算讲课提纲及内容)课时_____一制动系统匹配计算提纲及内容1、制动系统匹配计算的目的与要求制动系统匹配设计主要是根据设计任务书的要求,整车配置、布置及参数,参考同类车型参数,选择制动器型式、结构及参数,然后校核计算,验证所选参数是否满足设计任务书及法规的要求,满足要求后初步确定参数。
公司目前车型主要是M1、N1类,操纵系统为液压操纵、真空助力。
因此,本匹配计算主要以上述车型及操纵系统为基础进行基础制动系统及调节装置的匹配计算,ABS或ESP的匹配计算由配套厂家完成。
GB12676-1999《汽车制动系结构、性能和试验方法》、GB7258-2004《机动车运行安全技术条件》,GB13594-2003《机动车和挂车防抱制动性能和试验方法》等对制动系的性能、要求及试验方法都作了详细的规定,因此,制动系设计首先应满足以上法规的要求。
同时,为提高整车性能,不同级别的车型,又会对制动性能提出高于以上标准的要求,这些要求会在设计任务书中体现,因此,对设计任务书要求高于法规要求的,要按设计任务书要求设计。
将M1、N1类车与匹配计算有关法规摘录如下:表1 M1、N1类车有关制动法规要求项目GB7258-2004 GB12676-1999 ECE行车制动1、试验路面附着系数不小于0.7 的水泥或沥青路面干燥、平整的混凝土或具有相同附着系数的其他路面附着良好的路面2、车辆载荷空、满载空、满载←3、制动初速度(Km/h)M1 50Km/h 80Km/h ←N150Km/h(总质量不大于3500kg 的中高速货车)80Km/h←4、制动稳定性不允许超出2.5m的试验通道任何部位不偏离出 3.7m通道←5、制动减速度(m/s2)空载M1 ≥6.2≥5.8←N1 ≥5.8 ≥5.0 ←满载M1 ≥5.9≥5.8←N1 ≥5.4 ≥5.0 ←6、制动距离(m)空载M1 ≤19.0≤50.7 ←N1 ≤21.0≤61.2 ←满M1 ≤20.0≤50.7 ←载N1 ≤22.0≤61.2 ←7、液压制动脚踏板力(N)空载M1 ≤400≤500←N1 ≤450≤700←满载M1 ≤500≤500←N1 ≤700≤700←8、液压制动踏板行程要求踏板行程不应大于踏板全行程的3/4;装有自动调整间隙装置时不应大于踏板全行程的4/5,且乘用车不应大于120 mm ,其它机动车不应大于150 mm。
制动系统匹配计算98页PPT

41、学问是异常珍贵的东西,从任何源泉吸 收都不可耻。——阿卜·日·法拉兹
42、只有在人群中间,才能认识自 己。——德国
制动系统配计算
21、没有人陪你走一辈子,所以你要 适应孤 独,没 有人会 帮你一 辈子, 所以你 要奋斗 一生。 22、当眼泪流尽的时候,留下的应该 是坚强 。 23、要改变命运,首先改变自己。
24、勇气很有理由被当作人类德性之 首,因 为这种 德性保 证了所 有其余 的德性 。--温 斯顿. 丘吉尔 。 25、梯子的梯阶从来不是用来搁脚的 ,它只 是让人 们的脚 放上一 段时间 ,以便 让别一 只脚能 够再往 上登。
43、重复别人所说的话,只需要教育; 而要挑战别人所说的话,则需要头脑。—— 玛丽·佩蒂博恩·普尔
44、卓越的人一大优点是:在不利与艰 难的遭遇里百折不饶。——贝多芬
45、自己的饭量自己知道。——苏联
制动系统匹配设计
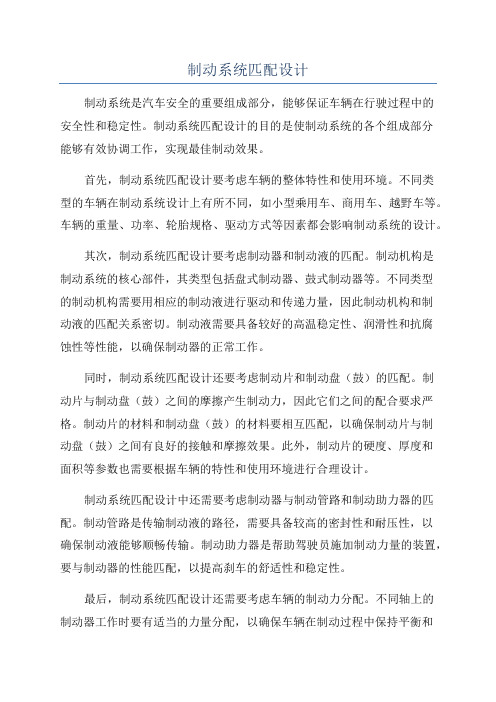
制动系统匹配设计制动系统是汽车安全的重要组成部分,能够保证车辆在行驶过程中的安全性和稳定性。
制动系统匹配设计的目的是使制动系统的各个组成部分能够有效协调工作,实现最佳制动效果。
首先,制动系统匹配设计要考虑车辆的整体特性和使用环境。
不同类型的车辆在制动系统设计上有所不同,如小型乘用车、商用车、越野车等。
车辆的重量、功率、轮胎规格、驱动方式等因素都会影响制动系统的设计。
其次,制动系统匹配设计要考虑制动器和制动液的匹配。
制动机构是制动系统的核心部件,其类型包括盘式制动器、鼓式制动器等。
不同类型的制动机构需要用相应的制动液进行驱动和传递力量,因此制动机构和制动液的匹配关系密切。
制动液需要具备较好的高温稳定性、润滑性和抗腐蚀性等性能,以确保制动器的正常工作。
同时,制动系统匹配设计还要考虑制动片和制动盘(鼓)的匹配。
制动片与制动盘(鼓)之间的摩擦产生制动力,因此它们之间的配合要求严格。
制动片的材料和制动盘(鼓)的材料要相互匹配,以确保制动片与制动盘(鼓)之间有良好的接触和摩擦效果。
此外,制动片的硬度、厚度和面积等参数也需要根据车辆的特性和使用环境进行合理设计。
制动系统匹配设计中还需要考虑制动器与制动管路和制动助力器的匹配。
制动管路是传输制动液的路径,需要具备较高的密封性和耐压性,以确保制动液能够顺畅传输。
制动助力器是帮助驾驶员施加制动力量的装置,要与制动器的性能匹配,以提高刹车的舒适性和稳定性。
最后,制动系统匹配设计还需要考虑车辆的制动力分配。
不同轴上的制动器工作时要有适当的力量分配,以确保车辆在制动过程中保持平衡和稳定。
制动力分配的主要方式有前后轮制动力分配和左右轮制动力分配两种。
综上所述,制动系统匹配设计是一个综合性的工程任务,需要综合考虑车辆的整体特性、使用环境和制动系统的各个组成部分之间的匹配关系。
只有进行合理的匹配设计,才能实现制动系统的最佳性能和安全效果。
制动系统选择与计算
制动系统选择与计算制动系统对于车辆的安全性和性能至关重要。
选择合适的制动系统并进行正确的计算是设计车辆制动系统的关键步骤。
本文将介绍制动系统选择的因素和制动系统计算的方法。
制动系统选择因素选择适合的制动系统需要考虑以下因素:1. 车辆类型:不同类型的车辆需要不同类型的制动系统。
例如,乘用车通常采用液压制动系统,而大型货车可能采用气压制动系统。
2. 车辆质量:车辆的质量将影响制动系统的选择。
较重的车辆可能需要更强大的制动系统来确保安全和效果。
3. 驾驶样式:驾驶员的驾驶样式也是制动系统选择的考虑因素之一。
一些驾驶员可能采用急刹车的方式驾驶,这将需要更高性能的制动系统。
4. 驾驶环境:不同的驾驶环境也需要不同类型的制动系统。
例如,山区驾驶可能需要更强大的制动系统来应对陡峭的坡道。
制动系统计算方法制动系统计算的目标是确定合适的制动力和制动装置。
以下是一些常用的计算方法:1. 制动力计算:根据车辆的质量和设计要求,计算所需的制动力。
制动力通常以车辆质量的百分比来表示。
2. 制动装置计算:根据制动力和制动功率的要求,选择合适的制动装置。
制动装置包括制动盘、制动片、制动液等。
3. 制动力分配:根据车辆的重心位置和轮胎的附着力,将制动力分配到各个轮胎上,以保证车辆的稳定性和安全性。
4. 制动系统参数计算:根据车辆的设计要求和制动装置的特性,计算出制动系统的参数,例如制动管路的直径、制动盘的尺寸等。
总结制动系统选择与计算是设计车辆制动系统的重要步骤。
合适的制动系统选择和正确的计算有助于提高车辆的安全性和性能。
在选择制动系统和进行计算时,需要考虑车辆类型、车辆质量、驾驶样式和驾驶环境等因素,并使用合适的计算方法来确定制动力和制动装置。
制动系统匹配设计计算
制动系统匹配设计计算制动系统是车辆上非常重要的一个系统,它通过施加力来减缓车辆的速度或完全停止车辆。
它可保证车辆在紧急情况下快速停车,同时也可以提供稳定的制动性能给驾驶员。
制动系统的设计计算是为了确定合适的制动力大小以及有效的制动距离。
以下是制动系统匹配设计计算的一些重要内容。
1.车辆质量:首先需要确定车辆的总质量,包括车身质量、人员质量、货物质量等。
车辆质量越大,所需制动力也将越大。
2.制动力计算:制动力取决于摩擦力、制动系数、轮胎质量、制动器效率等因素。
通常使用下面的公式计算制动力:制动力=车辆质量*加速度其中加速度可以根据制动器、轮胎等因素进行调整。
3.制动距离计算:制动距离取决于车辆的速度、制动力以及路面情况。
常用的计算公式如下:制动距离=(速度^2)/(2*制动力*道路摩擦系数)可以根据实际情况调整道路摩擦系数的数值。
4.制动器的选择:根据制动力和制动距离的计算结果,确定合适的制动器类型和规格。
常见的制动器包括液压制动器、电子制动器和气动制动器等。
选择适当的制动器类型和规格可以保证系统的可靠性和安全性。
5.制动系统的平衡:制动系统中的前轮制动力和后轮制动力需要进行合理的分配,以确保车辆能够稳定停止。
通常,前轮制动力应约为总制动力的70%,后轮制动力约为总制动力的30%。
在进行制动系统匹配设计计算时,还需要考虑以下几个因素:1.道路情况:不同路面的摩擦系数有所不同,需要根据实际道路情况调整计算中的摩擦系数。
2.制动器或刹车片的磨损:制动器磨损会导致制动力的减小,因此需要考虑磨损对制动力的影响。
3.轮胎的状态:轮胎的状况会影响制动力的传递效果,因此需要保证轮胎的状态良好。
4.驾驶员的反应时间:制动系统设计中需要考虑到驾驶员的反应时间,通常取2秒。
综上所述,在进行制动系统匹配设计计算时,需要考虑车辆质量、制动力、制动距离、制动器选择以及系统平衡等多个因素。
通过合理的计算可以确保制动系统满足安全性和可靠性的要求,并提供稳定的制动性能给驾驶员。
中重型商用车制动系统匹配计算
Science &Technology Vision科技视界0前言目前,国内车辆制动系统相关标准主要有GB12676-1999《汽车制动系统结构、性能和试验方法》和GB7258-2004《机动车运行安全技术条件》。
但作为国内主机厂研发人员设计的依据主要为GB12676,且GB12676的主要内容是引用欧洲的主要制动法规ECE R13,因此有广泛的使用性和实用性。
根据机动车型分类,中重型商用车应划分为N2、N3和O 类车辆。
因此本规范主要是为了符合GB12676对N2、N3和O 类车辆的制动性能的规定。
同时为了使车辆的制动性能满足我国路况,要求在匹配计算过程中充分考虑用户试验数据,使设计车辆制动性能实用性更好,满足客户使用需求。
1制动系统匹配计算图1制动时的车辆受力图1.1制动匹配计算相关参数的确立1.1.1整车质量m(kg)由于国内中重型商用车超载现象比较普遍,因此需根据国情把超载考虑进去。
定义:空载质量m 1;满载质量质量m 2;超载质量m 31.1.2车辆轴距L(m)对于双前桥或双后桥,由于制动时载轴转移计算复杂,为简化起见,将双前桥或双后桥合并为一桥,轴距测量点为两桥中心点。
1.1.3车辆质心距后轴距离质心距后轴距离可在整车三维数模上得出,但为了数据准确,可以对空载车辆各轴称重,得出L 21;L 22,L 23通过公式(1-1)、(1-2)得出:L 22=m 1L 21+(m 2-m 1)L 24m 2(1-1)L 23=m 1L 21+(m 3-m 1)L 24m 3(1-2)L 21、L 22、L 23———空载、满载、超载质心距后轴距离(m)L 24———载货质心距后轴距离(m)1.1.4车辆质心高h g (m)空载质心高h g1可在整车三维数模上得出,也可以通过悬吊法测得。
而h g2和h g3通过公式(1-3)、(1-4)得出:h g2=m 1h g 1+(m 2-m 1)h g 4m 2(1-3)h g3=m 1h g 1+(m 3-m 1)h g 4m 3(1-4)h g1、h g2、h g3———空载、满载、超载质心高(m)h g4———载货质心高m(m)1.1.5轴荷m L (kg)空载前后轴荷可通过称重获得,而满载和超载前后轴荷可通过公式(1-5)、(1-6)、(1-7)、(1-8)得出:m L21=m 2L 22L(1-5)m L22=m 2-m L21(1-6)m L31=m 3L23L(1-7)m L32=m 3-m L31(1-8)m L11、m L12———空载前、后轴荷;m L21、m L22———满载前、后轴荷;m L31、m L32———超载前、后轴荷。
制动系统匹配设计
制动系统匹配设计制动系统是汽车的重要安全装置之一,在车辆行驶过程中发挥着关键作用。
制动系统匹配设计是指根据车辆的性能和使用需求,选择合适的制动器、制动液、制动盘、制动片、制动盘与制动片之间的配合关系等,使得整个制动系统达到最佳的制动效果和使用寿命。
首先,制动器的匹配是制动系统匹配设计的基础。
制动器的选择应考虑车辆的重量、最大承载能力、行驶速度等因素。
一般来说,重型货车或客车需要更强大的制动力,因此通常采用液压制动器,而轻型汽车则可以采用盘式制动器或鼓式制动器。
此外,还需要考虑制动器的稳定性和可靠性,以确保在各种复杂路况下都能够正常工作。
其次,制动液的选择也是制动系统匹配设计的重要环节。
制动液一般分为矿物油和合成液两种,其性能和使用寿命不同。
矿物油具有较高的抗氧化性和耐磨性,但容易吸湿,导致制动系统生锈和腐蚀。
而合成液具有更好的耐温性和稳定性,但价格较高。
根据车辆的使用环境和经济性需求,可以选择合适的制动液进行匹配设计。
此外,制动盘和制动片之间的配合关系也需要进行匹配设计。
制动盘一般由刚性材料制成,能够承受高温和高压力。
制动片则通常由摩擦材料制成,以产生摩擦力来实现制动效果。
制动盘和制动片之间的摩擦系数、缓冲性能和使用寿命等都需要进行合理的匹配。
过高的摩擦系数可能导致制动力过大,过低的摩擦系数则会影响制动效果。
此外,制动盘和制动片之间的配合要紧密,以避免造成刹车异响或剧烈震动等问题。
最后,制动系统匹配设计还需要考虑车辆的整体性能和使用需求。
例如,高性能的跑车通常需要更强大的制动力和更能耐高温的制动系统,而普通家用车则可以采用较为经济实用的制动系统。
此外,制动系统还需要满足各种环境的需求,例如雨天、雪天等复杂路况下的制动效果。
综上所述,制动系统匹配设计是一个复杂而重要的工作,需要考虑车辆的性能、使用需求以及各个零部件之间的配合关系。
只有合理匹配设计,才能确保制动系统能够安全可靠地工作,提供优秀的刹车效果和使用寿命。
- 1、下载文档前请自行甄别文档内容的完整性,平台不提供额外的编辑、内容补充、找答案等附加服务。
- 2、"仅部分预览"的文档,不可在线预览部分如存在完整性等问题,可反馈申请退款(可完整预览的文档不适用该条件!)。
- 3、如文档侵犯您的权益,请联系客服反馈,我们会尽快为您处理(人工客服工作时间:9:00-18:30)。
讲义开发(讲师用)(制动系统匹配计算讲课提纲及内容)课时_____一制动系统匹配计算提纲及内容1、制动系统匹配计算的目的与要求制动系统匹配设计主要是根据设计任务书的要求,整车配置、布置及参数,参考同类车型参数,选择制动器型式、结构及参数,然后校核计算,验证所选参数是否满足设计任务书及法规的要求,满足要求后初步确定参数。
公司目前车型主要是M1、N1类,操纵系统为液压操纵、真空助力。
因此,本匹配计算主要以上述车型及操纵系统为基础进行基础制动系统及调节装置的匹配计算,ABS或ESP的匹配计算由配套厂家完成。
GB12676-1999《汽车制动系结构、性能和试验方法》、GB7258-2004《机动车运行安全技术条件》,GB13594-2003《机动车和挂车防抱制动性能和试验方法》等对制动系的性能、要求及试验方法都作了详细的规定,因此,制动系设计首先应满足以上法规的要求。
同时,为提高整车性能,不同级别的车型,又会对制动性能提出高于以上标准的要求,这些要求会在设计任务书中体现,因此,对设计任务书要求高于法规要求的,要按设计任务书要求设计。
将M1、N1类车与匹配计算有关法规摘录如下:表1 M1、N1类车有关制动法规要求注:以上数据为发动机脱开的O型试验要求。
2、制动系统主要参数的选择制动系统参数选择形式多样,可根据实际情况、用不同的方法确定,以最终保证设计参数合理为准。
如:轴荷、重心位置相近的车辆,可借鉴采用参考车型数据;平台化产品,可借用部分参数,选择其它参数;选择参数后要进行校核计算,满足要求后就可以采用;下面以无参考样车时的设计为例,简要说明制动系统主要参数选择的一般步骤。
制动系统参数选择的一般步骤如下:(1) 了解整车配置并输入与制动系统有关的整车参数及要求。
输入的参数及要求如表2 表2 与匹配计算有关的整车参数及要求(2) 初步选择系统主要参数。
(3) 制动器及相关参数选择及计算。
(4) 操纵系统主要参数选择及计算。
2.1初步选择系统主要参数在确定制动器参数之前,需初步选择同步附着系数、制动力分配系数及液压系统工作压力。
根据整车提供的参数,绘出理想制动力分配I 曲线,参考同类车型、根据ABS 或比例阀的一般要求,可以确定空载或满载时的同步附着系数,然后,计算出制动器制动力分配系数,绘出β线。
将I 、β曲线进行分析比较,初步选择合适的制动力分配系数。
2.1.1 理想制动力分配曲线绘制1、制动时地面对前、后车轮的法向反作用力不考虑制动时的空气阻力、滚动阻力、轴承摩擦力、传动系阻力、坡度等,制动时地面作用于前、后车轮的法向反作用力如图3-1所示:由图3-1,对后轮接地点取力矩得:g z h dtdumGb L F +=1 ……………………………………………(2-1) 式中:1z F ——地面对前轮的法向反作用力,N ;G ——汽车重力,N ;b ——汽车质心至后轴中心线的水平距离,mm ;m ——汽车质量,kg ; g h——汽车质心高度,mm ;L——轴距,mm;dtdu——汽车减速度,m/s2。
图1 制动工况受力简图对前轮接地点取力矩,得:gzhdtdumGaLF-=2………………………………………………………(2-2)式中:2zF——地面对后轮的法向反作用力,N;a——汽车质心至前轴中心线的距离,m。
2理想的前、后制动器制动力分配曲线—I曲线(1)、地面制动力F B:地面作用于车轮上的制动力,即地面与轮胎之间的摩擦力,其方向与车轮旋转方向相反。
(2)、制动器制动力Fμ:轮胎周缘克服制动器摩擦力矩所需的力,又称制动周缘力。
与地面制动力方向相反,当车轮角速度ω>0时,大小亦相等,且Fμ仅由制动器结构参数决定。
即Fμ及取决于制动器的结构型式、结构尺寸、摩擦副的摩擦系数及车轮有效半径等,并与制动踏板力即制动系的液压或气压成正比。
Fμ=Tμ /R………………………………………………………(2-3)式中:Tμ—制动器对车轮作用的制动力矩,即制动器的摩擦力矩,其方向与车轮旋转方向相反。
R—车轮有效半径。
(3)理想的前、后制动器制动力分配在附着系数为ϕ的路面上,前、后车轮同步抱死的条件是:前、后轮制动器制动力之和)(21μμFFFu+=等于汽车与地面附着力)(21φφφFFF+=;并且前、后轮制动器制动力21μμFF、分别等于各自的附着力21φφFF、,即:⎪⎭⎪⎬⎫⋅===⋅===⋅==+=+222211112121zBzBBBFFFFFFFFGFFFFFϕϕϕφμφμφμμ…………………………………………………(2-4)在上述条件下,g mF F dt du ⋅=+=ϕμμ21,由(2-1)、(2-2)、(2-4)可得以下公式: ϕϕμ)(1g h b L GF +=…………………………………………………(2-5) ϕϕμ)(2g h a LGF -= …………………………………………………(2-6) )]2(4[211122μμμF h GbF GL h b h G F gg g+-+=……………………………(2-7) 式中:21μμF F 、-前、后轴车轮的制动器制动力; 21B B F F 、-前、后轴车轮的地面制动力; ф-附着系数;21F φφ、F —前、后轴附着力将(2-7)可绘成以F μ1 、F μ2为坐标的曲线,即为理想的前后、轮制动器制动力分配曲线,简称I 曲线。
根据式(2-4)的第一式,按不同ф值作图,得到一组与坐标轴成45°的平行线,绘在I 曲线图上,以便分析使用。
2.1.2同步附着系数及制动器制动力分配系数的初步选择 1、同步附着系数同步附着系数φ0是汽车制动时前、后轮同时抱死时的路面附着系数。
同步附着系数的选择首先要满足制动稳定性的要求,然后要有高的制动效率并满足应急制动等的要求,见表1。
对制动稳定性的法规进行分析:附着系数在0.2-0.8之间时除个别很小的区段外,均要求前轮先抱死,所以同步附着系数应≥0.8,但满足此要求后,制动时前轴负荷较大,制动效率低,所以一般都要加装制动力调节装置。
另外,同步附着系数的选择还要结合整车的使用条件、轴荷分配、管路布置、配置综合考虑。
经常在良好的路面上使用且车速较高的车辆,为保证制动时的稳定性,同步附着系数可选的大一点。
对管路布置为II 型的制动系统,要考虑单回路失效的应急制动效能;制动系统配置ABS 时要满足ABS 匹配的基本要求。
对装ABS 的车辆同步附着系数满足ABS 匹配要求即可,一般应在0.5-1.0为宜。
K1无ABS 时的同步附着系数:空载0.48,满载0.65。
CH071参考车:空载0.60,满载0.81装感载比例阀时,拐点后的空、满载同步附着系数应≥0.8。
K1配感载比利阀时的同步附着系数:空载0.97,满载0.85。
K2配感载比利阀时的同步附着系数:空载1.04,满载1.30。
2、制动器制动力分配系数前制动器制动力与汽车总的制动器制动力之比,称为制动器制动力分配系数。
由于在附着条件所限定的 范围内,地面制动力在数值上等于相应的制动周缘力,因此β又通称为制动力分配系数。
2111μμμμμβF F F F F +==…………………………………………………(2-8)3、制动器制动力分配系数的初步选择根据已作出的I 曲线图、法规要求、制动效率初步选择空、满载同步附着系数,然后计算制动器制动力分配系数。
I 曲线由整车参数确定,45°的平行线反映的是在某一附着系数下的前、后地面制动力间的关系。
如果选定一个同步附着系数,与这一附着系数对应的45°的平行线与I 曲线的交点,也应是I 曲线与β线的交点,过交点与原点的直线即为无制动力调节装置时的β曲线;β线与I 曲线所包围的面积反映制动效率的高低,包围面积越小,效率越高。
装感载比例阀时,制动力分配曲线如下图2,可以参考同类车型、法规要求选择拐点前的制动力分配线并确定拐点;再选择拐点后的空载(或满载)同步附着系数,作出拐点后的空载(或满载)β线,一般空、满载拐点后的β线平行,所以可作出拐点后的另一条β线,再根据45°的平行线就可以确定满载(或空载)的同步附着系数,拐点后的空、满载同步附着系数应≥0.8,且要使制动效率尽量高。
通过作图试选,结合法规要求,初步选择制动力分配系数。
不装制动力调节装置时,同步附着系数由式(2-5)及(2-8)推导得:Lh b g⋅+=0φβ …………………………………………………(2-9)装感载比例阀时,拐点以前的制动力分配同上式。
2.1.3系统工作压力的确定管路压力越高,制动轮缸或主缸直径就越小,但对系统密封、管路尤其是制动软管及管接头则提出了更高的要求,对软管的耐压性、强度以及接头的密封性的要求就更加严格。
因此,一般路面上制动时,管路压力不要超过10Mpa ,同时,考虑到传动效率、制动力调节装置等的影响等,选择管路压力还要适当减小。
目前开发的轿车,图2 K2制动力分配曲线管路压力一般在4.5-8MPa 。
2.2制动器主要参数的计算及选择首先,需要确定前、后轴地面极限制动力,满载及路面附着系数最大时,前后轴制动力最大。
考虑到制动效能试验时对路面附着系数的要求,初选参数时可以以满载工况同步附着系数计算。
然后,选择管路工作压力、制动器型式;并根据制动器形式及轮辋规格,选择制动器制动半径及效能因数;由前后轴制动力,确定轮缸直径;最后重新计算制动力分配系数。
对装感载比例阀的系统,以满载前后轴同时抱死工况计算前轴制动力,选择前制动器参数;再根据拐点以前的前后制动力分配关系,选择后制动器参数。
并确定前后轮缸液压关系。
2.2.1前、后轴制动力确定假定车辆在满载时,前后轮同时抱死,由式(2-5)计算前轴制动力。
ϕϕμ)(1g h b LGF +=…………………………………………………(2-5) 无制动力调节装置的后轴制动力为:121u F F ββμ-=…………………………………………………(2-10)2.2.2制动器型式的确定制动器型式选择要结合总布置共同确定,盘式制动器由于其热稳定性、水稳定性、制动稳定性好等优点,广泛用于轿车和部分客车和载货汽车的前轮。
而后轮采用鼓式制动器较容易地附加驻车制动的驱动机构,兼作驻车制动器之用。
所以,采用前盘后鼓制动器能够达到一般制动性能要求,而且成本较低。
高性能轿车前后轮均采用盘式,主要是为了保持制动力分配系数的稳定;同时,配备ESP 时,一般鼓式制动器不能满足ESP 的需求(博士新开发的IDE 鼓式制动器可以配备ESP ),所以采用盘式制动器。
2.2.3制动半径的确定在有关的整车总布置参数和制动器的结构型式确定后,即可参考已有的同类型、同等级汽车的同类制动器,轮辋尺寸,对制动器的结构参数进行初选。